典型钻床夹具的设计
钻床夹具设计
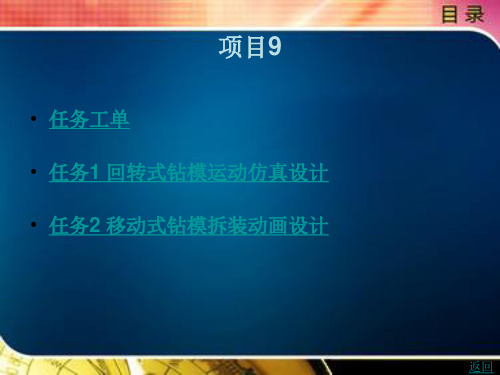
任务1 回转式钻模运动仿真设计
• 2. 运动仿真 • (1)进入机构设计环境(图Ⅸ−42、图Ⅸ−43) • (2)建立伺服电动机 • 如图Ⅸ−44~图Ⅸ−46 所示,建立3 个伺服电动机。 • 3. 运动分析 • (1)设置机构运动参数(图Ⅸ−47) • (2)运动回放及动画捕捉(图Ⅸ−48)
• ① 为营销展示、管理会议或设计审查生成高质量的动画。 • ② 将装配、拆卸及维护顺序创建成动画。 • ③ 创建复杂的合成动画。
下一页 返回
任务2 移动式钻模拆装动画设计
• 利用“设计动画”应用程序完成移动式钻模的拆装动画可以形象地展 示钻模的组成及装配过程。
• 9.2.2 移动式钻模拆装动画设计思路
上一页
返回
任务2 移动式钻模拆装动画设计
• 9.2.1 移动式钻模拆装动画设计分析
• 移动式钻模(图Ⅸ−49)用于加工中、小型工件同一表面上的多个孔 ,加工中通过移动钻模,找正钻头相对钻套的位置,对不同的孔进行 加工。
• Creo 使用“设计动画”应用程序可定义和调整动画序列的元件,并 可回放动画,从而可以完成以下功能:
• 移动式钻模拆装动画设计思路如图Ⅸ−50 所示。
• 9.2.3 移动式钻模拆装动画设计过程
• 1. 动画设计准备工作 • (1)设计零件并装配(图Ⅸ−51) • (2)创建合适的分解视图(图Ⅸ−52) • (3)创建合适的视图(图Ⅸ−53)
上一页 下一页 返回
任务2 移动式钻模拆装动画设计
• 请读者自行重复上面的过程,建立多个合适的视角。 • (4)创建合适的样式(图Ⅸ−54) • 2. 动画设计 • (1)进入动画设计模块(图Ⅸ−55) • (2)创建新动画(图Ⅸ−56) • (3)定义主体(图Ⅸ−57) • (4)定义快照 • ① 定义快照1,如图Ⅸ−58 所示。 • ② 定义快照2,如图Ⅸ−59 所示。
15钻床夹具设计

LOGO
一、钻床夹具的主要类型
2.移动式钻模
移动式钻模用在立式钻床上,先后钻销工件同一表面上的多个孔, 属于小型夹具。移动的方法有两种:一种是自由移动,另一种是定向移 动,用专门设计的轨道和定程机构来控制移动的方向和距离。
定向移动
自由移L动OGO
一、钻床夹具的主要类型
3.回转式钻模
回转式钻模的结构形 式按其转轴的位置可分为 立轴式,卧轴式和斜轴式 三种。这类钻模的引导元 件-钻套,一般是固定不 动的,为了实现工件在一 次安装中进行多工位加工 的目的,钻模一般采用回 转式分度装置。
LOGO
一、或 安装工件位置与钻孔位置不同
特点:使用时,工件和夹 具整体一起翻转。
这类钻模是一种小型夹具, 在操作过程中,需要用人工进 行翻动,为了减轻工人的劳动 强度,这类钻模的总质量最好 不要超过10KG,对于稍大一 些的工件用翻转钻模时,必须 设计专门的托架。
5. 因焊接应力 不能彻底消除,精度不能长期保持,故一般只在工 件孔距公差要求不高(大于±0.15mm)时,才采用焊接结构 的钻模板和夹具体。
6. 当工件被加工孔与定位基准的孔距公差小于0.05mm时,宜采 用固定式钻模和。
7. 在大型工件上加工位于同一平面上的孔时,为简化夹具结构, 可采用盖板式钻模。
套时,就应视具体情况设计各种形式的特种钻套。
孔距过近时
15
起钻表面特殊时
LOGO
二、钻床夹具设计要点
钻套与钻夹具实物:
Page 16
LOGO
二、钻床夹具设计要点
2.钻套尺寸设计:
内径:
孔径基本尺寸取刀具最大直径d刀max
公差钻、扩孔取F7,粗铰时取G7,
。
精铰时取G6。
16孔单工位组合钻床夹具设计

山西大同大学本科生毕业设计中文题目:16孔单工位组合钻床夹具设计英文题目:The Design of Simplex 16 Hole Combination Drilling Machine Fixture 学院:姓名:学号:专业:机械设计制造及其自动化班级:指导教师:职称:助教完成日期:2014 年6月 3 日摘要论文从现实出发,发现在生产小型拖拉机前盖上的16孔时,都是用普通车床进行加工,比较复杂,精度不易保证。
工人劳动强度高,工步多,生产出来的废品也比较多,对工人的操作也比较严格,浪费了许多时间和不必要的损耗。
本次设计通过分析工件结构,设计出一种组合钻床,解决了加工速度慢的问题,能够较方便的通过一个工序完成零件各孔的加工,减少了工人的劳动时间,也减少了没必要的设备,为工厂节约了大笔资金,降低产品的成本。
设计还运用了变位齿轮传动,并采用了滚针轴承,解决了常规方法不能完成的排箱问题,减少了主轴箱的尺寸,也减轻了主轴箱的重量,节约了成本,提高了机床的可靠性。
同时也采用了新型的夹具,解决了定位困难,夹紧费时的问题,降低了工人的劳动强度。
设计过程都根据国家标准规定,先对机床进行总体设计,在进行主轴箱设计,包括主轴箱设计原始依据图,主轴箱传动系统的设计及计算,主轴箱零件的选择,以及传动轴承的选用和总图设计,最后进行夹具设计。
关键词:变位齿轮;滚针轴承;组合钻床;夹具设计ABSTRACTPaper embarks from the reality, found in the production of small tractors before 16 hole on the cover, is conducted using ordinary lathe processing, is more complex, precision is difficult to guarantee.Workers labor intensity is high, the working step, also produce waste more, are more strict to the operation of the workers, waste a lot of time and unnecessary losses.This design by analyzing the workpiece structure, design a combination drilling machine, solves the problems of slow processing, can be convenient to make the hole through a process of finished parts processing, reducing the labor time and also reduce the unnecessary equipment, saves a lot of money for the factory, reduce the cost of the products.Design also uses the modified gear transmission, and use the needle roller bearing, solve the problem of the conventional methods cannot finish line box, reducing the size of the spindle box, and to reduce the weight of the spindle box, to save the cost and improve the reliability of the machine tool.Also adopted a new type of fixture, solves the location difficulty, the clamping time-consuming problem, reduces the labor intensity of workers.Design process according to the national standard, to the overall design of machine tool, first in the headstock design, including the design of spindle box original according to the figure, the spindle box of transmission system design and calculation, the choice of the spindle box parts, and the choice of drive bearing and general layout design, fixture design finally.Keywords:modified gear; needle roller bearing; combination drilling machine; fixture design目录1 组合机床概述 (1)1.1组合机床组成及其特点 (1)1.2组合机床应用范围及加工精度 (2)1.2.1组合机床的应用范围 (2)1.2.2组合机床孔加工精度 (3)1.3组合机床的通用部件 (3)1.4组合机床的国内、外现状 (4)1.4.1国内组合机床现状 (4)1.4.2国外组合机床现状 (6)2 组合钻床的总体设计 (8)2.1制定工艺方案 (8)2.216孔组合机床配置型式及结构方案的确定 (9)2.3主参数的计算 (9)2.3.1确定切削用量计算各主轴转速 (9)2.3.2 确定切削力F切削转矩M切削功率P (11)2.4组合机床的总体设计 (11)2.4.1被加工零件工序图 (12)2.4.2加工示意图 (12)2.4.3机床联系尺寸图的绘制 (17)3 主轴箱的设计 (21)3.1绘制主轴箱设计原始依据图 (21)3.2主轴箱传动系统的设计计算 (22)3.2.1传动思路 (23)3.2.2传动树形图 (23)3.2.3 合理分配各级传动比确定传动轴位置确定齿数 (24)3.2.4主轴箱各通用部件的选择 (26)3.2.5绘制主轴箱传动系统图 (27)3.3变位齿轮计算和滚针轴承的选用 (28)3.3.1变位齿轮计算 (28)3.3.2轴承的选用 (29)4 夹具设计 (33)4.1定位系统的设计 (33)4.1.1定位系统的设计原则 (33)4.1.2定位支承元件及其布置 (34)4.2导向装置设计 (35)4.2.1导向装置的作用 (35)4.2.2导向装置的类型选择 (35)4.2.3固定式导套的设计 (35)4.2.4固定钻模板结构设计 (36)4.3夹紧机构设计 (37)4.3.1夹紧方案的确定 (37)4.3.2螺栓的选用和夹紧力的计算 (37)4.3.3定位套的校核 (38)4.4夹具体底座及钻模板总成结构 (40)5 16孔单工位机床设计的结论 (41)参考文献 (43)致谢 (44)1 组合机床概述1.1组合机床组成及其特点组合机床是以系列化、标准化的通用部件为基础,配以少量的专用部件所组成的专用机床。
夹具设计(钻孔)说明书
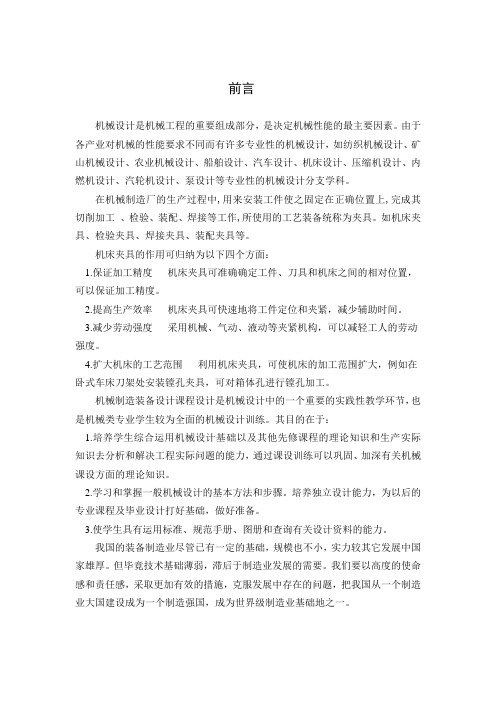
前言机械设计是机械工程的重要组成部分,是决定机械性能的最主要因素。
由于各产业对机械的性能要求不同而有许多专业性的机械设计,如纺织机械设计、矿山机械设计、农业机械设计、船舶设计、汽车设计、机床设计、压缩机设计、内燃机设计、汽轮机设计、泵设计等专业性的机械设计分支学科。
在机械制造厂的生产过程中,用来安装工件使之固定在正确位置上,完成其切削加工、检验、装配、焊接等工作,所使用的工艺装备统称为夹具。
如机床夹具、检验夹具、焊接夹具、装配夹具等。
机床夹具的作用可归纳为以下四个方面:1.保证加工精度机床夹具可准确确定工件、刀具和机床之间的相对位置,可以保证加工精度。
2.提高生产效率机床夹具可快速地将工件定位和夹紧,减少辅助时间。
3.减少劳动强度采用机械、气动、液动等夹紧机构,可以减轻工人的劳动强度。
4.扩大机床的工艺范围利用机床夹具,可使机床的加工范围扩大,例如在卧式车床刀架处安装镗孔夹具,可对箱体孔进行镗孔加工。
机械制造装备设计课程设计是机械设计中的一个重要的实践性教学环节,也是机械类专业学生较为全面的机械设计训练。
其目的在于:1.培养学生综合运用机械设计基础以及其他先修课程的理论知识和生产实际知识去分析和解决工程实际问题的能力,通过课设训练可以巩固、加深有关机械课设方面的理论知识。
2.学习和掌握一般机械设计的基本方法和步骤。
培养独立设计能力,为以后的专业课程及毕业设计打好基础,做好准备。
3.使学生具有运用标准、规范手册、图册和查询有关设计资料的能力。
我国的装备制造业尽管已有一定的基础,规模也不小,实力较其它发展中国家雄厚。
但毕竟技术基础薄弱,滞后于制造业发展的需要。
我们要以高度的使命感和责任感,采取更加有效的措施,克服发展中存在的问题,把我国从一个制造业大国建设成为一个制造强国,成为世界级制造业基础地之一。
1.3零件工艺分析本次课设是要为此图1-1-3中的端盖设计一个钻3-φ9孔的夹具,最终实现将工件定位,更加精确和方便的完成钻孔工作,并保证能夹紧工件,夹紧力要适中,不要使工件变形,又能保证工件所要求的加工精度。
操纵杆支架加工工艺及钻床夹具设计(钻底面孔系)

操纵杆支架加工工艺及钻床夹具设计(钻底面孔系)一、操纵杆支架加工工艺操纵杆支架是用于安装控制杆的零部件,其制作需要采用精细的加工工艺。
下面介绍一种常见的操纵杆支架加工工艺:1. 材料准备首先,需要准备好所需的材料,这一步比较简单,只需要进货时检查材料质量即可。
2. 加工准备接着,需要进行加工准备,具体包括:•测量材料长度和宽度,确定需要加工的尺寸;•设计加工工艺路线和操作顺序;•准备加工设备。
3. 加工操作具体的加工操作包括:•使用铣床或加工中心,按照设计好的工艺路线进行粗加工和精加工;•使用钻床对操纵杆支架进行钻孔;•使用切割机对操纵杆支架进行切割;•对操纵杆支架进行表面处理,包括打磨、喷漆等。
4. 检验工艺最后,需要对操纵杆支架进行检验,确保其符合设计要求和相关的质量标准。
二、钻床夹具设计(钻底面孔系)钻床夹具的设计一直是制造业中比较重要的一环,好的钻床夹具设计不仅可以提高工作效率,还能保证钻孔的质量。
本文主要介绍一种适用于钻底面孔系的夹具设计,具体如下:1. 夹具结构钻底面孔系的夹具主要由四个部分组成:夹具主体、夹紧装置、定位装置和调整装置。
其中,夹具主体由底座和夹紧臂组成,底座为整体结构,夹紧臂为可移动结构,通过螺旋调节杆进行调节。
夹紧装置包括三爪夹具和可调紧钳,用于夹紧工件。
定位装置包括定位块和定位铣刀,用于保证工件在夹具中的定位精度。
调整装置由螺旋调节杆组成,用于调节夹紧臂位置和夹具夹紧力度。
2. 夹具使用在使用过程中,需要注意以下几点:•使用前需检查夹具部件是否完好;•按照工艺进行定位、夹紧和加工顺序;•加工后需清理夹具,确保夹紧和定位部件不受损坏。
综上所述,操纵杆支架的加工工艺和钻床夹具的设计对提高制造业的生产效率和质量有着至关重要的作用,需要在实际应用中加以重视和应用。
25钻床夹具设计总结

25钻床夹具设计总结一、引言钻床夹具是一种用于加工工件的专用夹具,广泛应用于机械制造行业。
它能够固定工件,使得钻床在进行钻孔、镗孔等加工过程中保持工件的位置稳定,从而提高加工精度和效率。
本文主要对钻床夹具的设计进行总结与分析,总结关键点、注意事项等。
二、钻床夹具设计的关键点1.适应性:钻床夹具的设计应该能够适应不同种类、尺寸的工件,具有一定的通用性。
可以通过设计可调节的夹具结构、可更换的夹具部件等方式实现。
2.刚性:钻床夹具在加工过程中需要具备足够的刚性,以保证工件的位置稳定。
可以通过选用高硬度、高强度材料,增加夹具的结构强度来实现。
另外,还可以增加夹具的支撑点、减小夹具部件的长度等方式来提高夹具的刚性。
3.稳定性:钻床夹具在加工过程中需要保持稳定的位置,以减小加工误差。
可以通过设计稳定的夹具支撑面、采用深度固定夹具等方式来提高夹具的稳定性。
4.精度:钻床夹具需要保证加工工件的精度,应尽量减小夹具本身的加工误差。
可以通过采用精密加工工艺、优化夹具结构、提高夹具部件的精度等方式来提高夹具的精度。
三、钻床夹具设计的注意事项1.安全性:钻床夹具设计应注意避免夹具在加工过程中发生意外脱离或松动,以确保操作人员的安全。
2.耐用性:钻床夹具设计应注意材料的选择和处理,以提高夹具的耐用度。
应尽量选择耐磨、耐腐蚀、耐疲劳的材料,并对夹具部件进行适当的表面处理。
3.便于操作:钻床夹具设计应考虑到操作人员的操作习惯和人体工程学要求,使得夹具易于调整、装卸工件,并能够快速、准确地定位工件。
4.可维护性:钻床夹具设计应注意方便夹具的维护和修理。
应选择易于购买和更换的标准件,设计合理的夹具结构和拆卸方式。
四、钻床夹具设计中的工程案例1.通用钻床夹具设计:通过设计可调节的夹具结构,采用可更换的夹具部件等方式,使得夹具适用于不同尺寸的工件,提高了夹具的适应性。
2.高精度钻床夹具设计:通过采用精密加工工艺,优化夹具结构,提高夹具部件的精度等方式,使得夹具本身的加工误差减小到最小,保证了加工工件的精度。
钻床夹具设计

夹具课程设计说明书学院:机电工程学院班级:09机械2班姓名:学号:指导老师:夹具课程设计说明书一、 工件加工工艺性分析工件钢套已加工0.021020720H φφ+=,外圆及两端面。
设计要求:一,小孔中心线与B 端面为200.1±mm 二,大孔的中心线与B 端面的垂直度误差为0.02 三,小孔中心线的对称度误差为0.1。
工序图如下:二,确定夹具的结构方案 一, 确定定位方案,选择定位元件加工小孔的工序基准是B 端面。
从基准重合的原则出发,定位基准为B 端面和的轴线。
采取一凸面一孔定位。
结下图所示:二,确定夹具导引方式,选择导引元件为能迅速,准确地确定刀具与夹具的相对位置,钻夹具上都应设置引导刀具的元件——钻套。
钻套一般安装在钻模板上,钻模板与夹具体连接,钻套与工件之间留有排屑空间,如下图所示。
三,确定加紧方案由于工件批量小,宜用简单的手动夹紧装置。
钢套的轴向刚度比径向刚度好,因此夹紧力应指向限位台阶面。
如下图所示,采用带开口垫圈的螺旋夹紧机构。
四,夹具体的设计为了保证位置精度,这里选择铸造件具体,因为铸造夹具体的优点是:制造工艺性好,可以铸造各种复杂的外形,铸件的抗压强度、刚度和抗振性比较好,且采用适当的时效方式可以消除残余应力,长期保持尺寸的稳定性,能够保证位置精度。
该夹具是小型夹具,因此选择铸铝件ZL110材料,这样的话铸造时消耗的能量比铸铁低。
定向键选择:根据立式钻床的T型槽尺寸,查手册取B=22n6的定向键,定向键与夹具体槽形的配合方式是:22H7/n6,固定螺钉选618M⨯的螺钉。
结果如下:五,误差分析1、孔距误差分析(1)孔距误差定位误差δ1定位:由工序图知,钢套内孔轴线对端面B的垂直度误差为0.02mm,因此孔距定位误差为:301=+=0+0.02=0.02m m<0.20.067303m mδδδ⨯⨯=1定位不重位置,满足要求(2)对定误差δ1对定:固定钻套与定位平面距离公差:为了减小对定误差取TL=0.03mm,钻套与钻头的最大配合间隙为:1∆=0.022+0.030=0.052mm,单边间隙E=1/25 4.290.0520.05318B h H m mH++++∆=⨯=,钻套外圆与内孔的同轴度误差取:1e =0.01mm ,于是对定误差为:2222222211T e 0.030.0520.0530.010.081L E mmδ=+∆++=+++=1对定0.067m m >,不满足要求。
钻床夹具设计剖析

3.辅助装置
(1)钻套 从国家标准中选用。
(2)钻模板
4.夹具体
五、绘制夹具总图
二、定位方案与定位元件
1.确定定位方案
2.选用定位元件
三、夹紧方案及夹紧装置的设计
夹紧机构
四、夹具结构设计
1.定位装置
(1)销轴
(2)可调支承钉 可调支承钉在GB JB/T 8026.1-1999(六角头支承)中 选取M8×40-S。
(3)辅助螺旋支承
2.夹紧装置
(1)夹紧 选用M10螺纹以满足强度要求。 (2)开口垫圈
钻床夹具设计
一、明确设计任务
设计在摇臂钻床上加工杠杆臂零件上孔φ10
0.1 0
mm和
φ13mm的钻夹具。
1.杠杆臂零件图
2.杠杆臂加工工艺分析
(1)加工要求
(2) 加工工艺
该工件的结构形状比较不规则,臂部刚性不足,加 工孔φ10 mm位于悬臂结构处,且该孔精度和表面粗糙度 要求高,故工艺规程中分钻、扩、铰多个工序。由于该 工序中两个孔的位置关系为相互垂直,且不在同一个平 面里,要钻完一个孔后翻转90°再钻削另一个孔,因此 要设计成翻转式钻夹具。
- 1、下载文档前请自行甄别文档内容的完整性,平台不提供额外的编辑、内容补充、找答案等附加服务。
- 2、"仅部分预览"的文档,不可在线预览部分如存在完整性等问题,可反馈申请退款(可完整预览的文档不适用该条件!)。
- 3、如文档侵犯您的权益,请联系客服反馈,我们会尽快为您处理(人工客服工作时间:9:00-18:30)。
典型钻床夹具的设计摘要:主要技术指标能保证工件的加工精度、提高生产效率、工艺性好和使用性好。
我们在设计专用夹具时为了能满足工件的加工精度要求,考虑了合理的定位方案、合适的尺寸、公差和技术要求,并进行了必要的精度分析。
由于是中批量生产,采用了回转式钻床夹具,提高了生产效率。
在工艺性方面使这种夹具的结构简单、合理、便于加工、装配、检验和维修。
在使用性方面这种夹具的操作简便、省力、安全可靠,排屑也方便,必要时可设置排屑结构。
通过对钻床夹具设计的制作,进一步巩固和所学基本知识并使所学知识得到综合运用。
学会查阅和收集技术资料,提高运用计算机辅助设计的能力,树立正确的设计思想和严谨的工作作风。
关键词:夹具的基本概念,分度装置,零件分析,精度分析,零件的加工工艺目录引言 (3)第1章夹具的基本概念 (4)1.1夹具的概念 (4)1.2夹具的组成 (4)第2章分度装置的设计 (4)第3章零件分析 (6)3.1工艺分析 (6)3.2零件工艺规程设计 (6)第4章典型夹具的设计 (7)4.1典型夹具的设计要点 (7)4.2夹具的设计 (8)4.3夹紧力的确定 (10)4.4夹紧表面的选择 (10)4.5夹紧元件的确定 (12)第5章夹具设计精度分析 (12)5.1定位误差的分析与计算 (12)5.2螺栓的公称直径 (13)5.3夹具加工精度的分析 (15)第6章夹具各零件的加工工艺 (19)6.1底板加工工艺路线 (19)6.2支撑板加工工艺路线 (20)6.3钻模板加工工艺路线 (22)6.4轴加工工艺路线 (23)6.5分度盘的加工工艺路线 (23)6.6定位端盖的加工路线 (24)6.7定位销的加工工艺路线 (25)机械加工工艺过程卡片 (25)结论 (27)【参考文献】 (28)致谢 (29)引言毕业设计是对学生在学完本专业的课程之后进行的一次综合考察,是对学到基本理论、基本原理付诸于实践,经培养其分析问题和解决总是的能力。
它是一次对学生是知识结构、理论水平、实践经验、操作技能、创作思维能力的培养和训练。
我的毕业设计课题典型钻床夹具的设计。
主要内容是:制定被加工工件的工艺规程,并对其尺寸精度进行分析,确定定位基准,设计的夹具并行进行夹具的制作。
夹具设计不仅是新产品投产的重要工艺措施,也是老厂技术改革提高生产率和保证产品质量的主要技术途径。
机床夹具主要有四项功用:1、保证加工精度2、提高生产率降低成本3、扩大机床工艺范围4、减轻工人劳动强度,保证生产安全。
为了适应现代机械工业各向高、精、尖方向发展的需要和多品种、中小批量生产的特点,机床夹具发展方向表现为:精密化、高效化、自动化、标准化、通用化。
我设计的夹具是按工件的某道工序加工,便于成批加工的扇形、圆周上钻孔,保证尺寸精度孔所用的专用夹具。
由于我的水平和经验有限,出现错误请各位老师提出批评和指教。
第1章夹具的基本概念1.1夹具的概念机床夹具是在机床上用以装夹工件的一种装置,其作用是使工件相对于机床或刀具有一个正确的位置,并在加工过程中保持这个位置不变。
1.2夹具的组成1、定位元件及定位装置;2、夹紧元件及夹紧装置(或称夹紧机构);3、夹具体;4、对刀、导引元件及装置(包括刀具导向元件、对刀装置及靠模装置等);5、动力装置;6、分度、对定装置;7、其它元件及装置(包括夹具各部分相互连接用的以及夹具与机床相连接用的紧固螺钉、销钉、健和各种手柄等)。
第2章分度装置的设计回转分度装置由固定部分、转动部分、分度对定控制机构、抬起锁紧结构以及润滑部分等组成。
(一)固定部分它是分度装置的基体,其功能相当于夹具体。
通常采用经过时效处理的灰铸铁制造,精密基体则可以选择孕育铸铁。
孕育铸铁有较好的耐磨性、吸振性和刚度。
(二)转动部分转动部分包括回转盘、衬套和转轴等。
回转盘通常用45钢经淬火至40-45HRC或20钢经渗碳淬火至58-63HRC加工制成。
转盘工作平面的平行度公差为0.01mm,圆端面的圆跳动公差0.01-0.015mm,工作面对底面的平行度公差为0.01-0.02mm.。
轴承的间隙一般在0.005-0.008mm之间,以减少分度误差。
如图2—1所示。
图2—1衬套(三)分度对定机构及控制机构分度对定机构由分度盘和对定销组成。
其作用是在转盘转位后,使其相对于固定部分定位。
分度对定机构的误差会直接影响分度精度,因此是分度装置的关键部分。
设计时应根据工件的加工要求,合理选择分度对定机构的类型。
如图2—2所示。
图2—2分度盘(四)抬起锁紧机构分度对定后,应将转动部分锁紧,以增强分度装置工作时的刚度。
(五)各个结构的材料分度盘的材料用20钢,渗碳淬火,回火HRC 58-64,定位元件的材料用T8A,淬火HRC 55-60夹紧零件材料用45钢淬火,回火HRC40-45。
第3章零件分析3.1工艺分析该零件材料为45号调质钢,具有较高的强度、耐热性、耐磨性及减振性,适用承受较大的压力,要求耐磨的零件。
该零件的加工尺寸为φ160、角度为60度圆形面上钻3个深孔,深度为20±0.05,分度精度和装配误差将影响孔的尺寸精度。
因此,在加工中,保证分度精度和装配很重要。
为了减小定位误差,应保证零件和各项尺寸及相对于零件中心的垂直度和同轴度要求3.2零件工艺规程设计1、定位基准的确定:该项零件是以工件的中心为设计基准的。
根据粗、精基准选择原则,选择转动轴作为定位基准,以保证孔与转动轴轴心线的垂直度及孔的尺寸20±0.05,再以其右端的定位端盖为基准保证圆上孔的位置。
2、确定工艺方案,拟订工艺路线:根据先加工基准面后加工其他表面,先粗加工后精加工的原则,根据各加工面的要求和各种加工方法能达到的经济精度,确定各表面的加工方法,拟订编写机械工艺过程卡片。
第4章典型夹具的设计4.1典型夹具的设计要点1、钻模类型的选择钻模类型很多,在设计钻模时,首先需要根据工件的尺寸、质量、加工要求和批量来选择钻模的结构类型。
选择时注意以下几点:(1)被钻孔直径大于10mm时,(特别是加工钢件),宜采用固定式钻模。
(2)翻转式钻模使适用于加工中小件,包括工件在内的总质量不宜超过10kg。
(3)肖加工分布不在同心圆周上的平行孔系时,如工件和夹具的总质量超过期15 kg,宜采用固定钻模在摇臂钻床上加工,如生产批量大,则可在立式钻床上采用。
(4)对于孔的垂直孔心距离要求不高的中小型工件,宜优先采用滑柱钻模。
如孔的垂直度公差小于0.1mm,孔距集团公差δ小于±0.15mm时,一般不宜采用这类钻模。
(5)钻模板和夹具体为焊接式的钻模板,因焊接应力不能彻底消除,精度不能长期保持,故一般在工件孔距公差要求不高(δ≥±0.15mm)时才用。
(6)孔距与孔和基面公差小于0.05mm时用用固定式钻模。
2、钻套的选择和设计根据钻套的结构有固定钻套、可换钻套、快换钻套、及特殊钻套四种类型,分别适用不同情况。
3、钻套板的设计钻模板是供安装钻套用的,钻模板多装配在夹具体或支架上,与夹具上的其他元件相连接或夹具体铸成一体。
如图4—1所示。
图4—1钻模板4.2夹具的设计1、夹具方案的选择方案以圆柱凸台和端面为基准,在转动轴和分度盘上定位。
在用一个圆锥销插在分度盘上的以加工好的锥槽里作径向定位,用螺母和开口垫片将工件夹紧在分度盘上手柄拨动分度销来分度。
这样就可以对工件在一次安装中来变更工位,钻出12个φ10的径向孔。
2、定位元件的选择在以转动轴和定位端面定位中,定位的最大特点是:工件是以转动轴的中心和定位端盖的端面定位,不论是经过加工与否或精度的高低,也不论是圆柱面或是圆弧面,它们在经转动轴和定位端盖上定位时,其定位基准(轴线)和一个侧面,始终处于中心位置,即定位性很好。
3、夹具体的选择夹具体是夹具的基础件,如图4—2所示。
要安装组成该夹具所需要的各种元件,机构和装置等,夹具应满足:1)用有足够的强度和刚度。
2)结构简单,具有良好的工艺性。
3)尺寸要稳定。
4)便于排屑。
(1)根据钻床与夹具的固定连接,由钻床工作台T形槽的尺寸设计带U形槽耳座的夹具体。
(2)选择夹具体毛坯结构时,根据结构合理性、工艺性、经济性、标准化的可能性选择装配结构。
(3)根据工件、定位元件、加紧装置、对刀引导元件以及其它辅助机构和装置在总体上的培植,确定夹具体外形尺寸为180×180×120.(4)为了便于排除切屑,不使其聚积在定位元件工作表面上而影响工件正确定位,使钻摸板和工件及定位元件相距5-l0mm。
图4—2夹具体4.夹具辅助支承的选择工件以转动轴定位时,工件在夹具中的位置,主要是由基本支承按定位基本原理来确定的,但是工件在加工过程中,往往由于工件的支承刚性较差,在切削力、夹紧力、或工件本身重力作用下,单由基本支撑定位,仍然可能发生定位不稳定或引起工件加工部位变形,因而这时需要增设辅助支承。
辅助支承不是定位元件,决不能允许它破坏基本支承应起的主要定位作用。
辅助支承也不能使制件的基准面靠牢定位元件表面,所以它不能起夹紧作用,它仅是用以增加制件在加工过程中的刚性的装置。
在此夹具中,采用螺钉——螺母式辅助支承的结构简单,缺点是操作麻烦,效率较低。
辅助支承弹簧设置时应使其弹力适当,不可过强,也不可过弱。
通常以能在螺母松开后维持弹力,而受工件重力作用后又能缩回,并保持与工件接触为宜。
否则便将失去辅助支承的作用。
4.3夹紧力的确定夹紧力包括大小、方向和作用点三个要素,他们的确定是夹紧机构设计中首先要解决的问题。
1、夹紧力方向的选择应遵守以下原则:夹紧力的作用方向有利于工件的准确定位,而不能破坏定位。
为此,一般要求夹紧力应垂直指向主要定位表面。
夹紧力的作用方向应尽量与工件刚度最大的方向相一致,以减小工件变形。
夹紧力的作用方向应尽可能与切削力、工件重力方向一致,以减小所需夹紧力。
2、夹紧力作用点的选择:夹紧力作用点的选择是指在夹紧力方向已定的情况下,确定夹紧元件与工件接触点的位置和接触点数目。
一般应注意以下几点:夹紧力作用点应正对支承元件或位于支承元件所形成的支承面内,以保证工件已获得的定位不变。
夹紧力作用点应处于工件刚性较好的部位,以减小工件的夹紧变形。
夹紧力作用点应尽可能靠近被加工表面,以便减小切削力对工件造成的翻转力矩。
4.4夹紧表面的选择加工前,工件在夹具的定位原上获得正确的位置后,还必须在夹具上设置夹紧机构将工件夹紧,以保证工件在加工过程中不致因受到切削力、惯性力、离心力或重力等外力作用而产生位置偏移和振动,并保持已由定位元件所确定的加工位置。
由此可见夹紧机构在夹具中占有重要的地位。
对夹紧装置的要求:1) 在夹紧过程中应能保持工件在定位时已获得的正确位置。
2) 夹紧应适当和可靠,夹紧机构一般要有自锁作用,保证在加工规程中工件不会产生松动或振动。