人工装配线
简述装配线平衡的步骤

简述装配线平衡的步骤1. 确定装配线的目标和要求装配线平衡的第一步是确定目标和要求,需要明确生产线的产量需求、工作时间、产品质量要求等。
这些目标和要求将指导后续的工作,确保装配线平衡的过程能够满足生产需求。
2. 分析产品的工艺流程在装配线平衡的过程中,需要对产品的工艺流程进行详细分析。
这包括产品的组成结构、各个部件之间的装配关系、装配的顺序等。
通过对产品工艺流程的分析,可以了解到每个工位需要完成的具体工作内容。
3. 收集工序的时间数据为了进行装配线平衡,需要收集各个工序的时间数据。
这些数据可以通过直接观察和测量,或者通过历史数据的分析来获取。
收集到的时间数据将用于后续的分析和计算。
4. 计算工位的工作时间和负荷根据收集到的时间数据,可以计算每个工位的工作时间和负荷。
工作时间是指完成某个工序所需的时间,而工作负荷是指工作时间与总工作时间的比值。
通过计算工位的工作时间和负荷,可以评估每个工位的工作量大小。
5. 进行装配线平衡的优化在计算了工位的工作时间和负荷之后,可以开始进行装配线平衡的优化。
优化的目标是使各个工位的工作负荷相对平衡,从而提高生产效率和产品质量。
具体的优化方法包括调整工作内容、改变工序的顺序、增加或减少工位等。
6. 验证装配线的平衡效果在完成装配线平衡的优化之后,需要验证装配线的平衡效果。
这可以通过模拟实际生产过程或者在实际生产中进行观察和测量来完成。
验证的目的是确保装配线平衡的效果能够满足生产需求,并且达到预期的目标和要求。
7. 持续改进和优化装配线平衡是一个持续改进的过程,需要不断地进行优化和调整。
通过不断地收集和分析数据,评估装配线的平衡效果,并根据实际情况进行调整,可以不断提高生产效率和产品质量。
以上就是装配线平衡的步骤的简要介绍。
通过合理安排工位上的工作内容和工作时间,装配线平衡能够提高生产效率和产品质量,为企业的发展提供支持。
在实际应用中,需要根据具体情况进行调整和优化,以适应不同的生产需求。
装配线如何合理布局
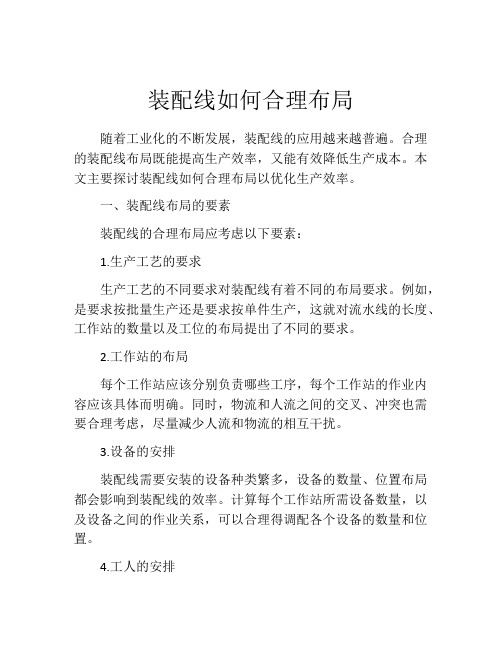
装配线如何合理布局随着工业化的不断发展,装配线的应用越来越普遍。
合理的装配线布局既能提高生产效率,又能有效降低生产成本。
本文主要探讨装配线如何合理布局以优化生产效率。
一、装配线布局的要素装配线的合理布局应考虑以下要素:1.生产工艺的要求生产工艺的不同要求对装配线有着不同的布局要求。
例如,是要求按批量生产还是要求按单件生产,这就对流水线的长度、工作站的数量以及工位的布局提出了不同的要求。
2.工作站的布局每个工作站应该分别负责哪些工序,每个工作站的作业内容应该具体而明确。
同时,物流和人流之间的交叉、冲突也需要合理考虑,尽量减少人流和物流的相互干扰。
3.设备的安排装配线需要安装的设备种类繁多,设备的数量、位置布局都会影响到装配线的效率。
计算每个工作站所需设备数量,以及设备之间的作业关系,可以合理得调配各个设备的数量和位置。
4.工人的安排工人的数量和分配也是装配线布局时需要考虑的要素。
要考虑各个工作站的作业强度、需要的工人数量以及工人之间的工作协调关系,从而确定工人的数量和岗位。
二、装配线布局的优化方案1.流程图和工艺分析在装配线布局之前,必须先进行流程图和工艺分析。
制定出工序流程图和作业分析图可以帮助检查各个流程是否合理、工序的缺陷以及各个工艺节点的要求等。
基于这些分析,可以优化各个工序之间的联系,以及分析哪些工序可以合并到一个工作站,哪些工序需要拆分到不同的工作站。
2.优化工作站的数量和布局制定合理的工作站数量和布局对提升生产效率起到了非常重要的作用。
应该考虑到每个工作站所需的人手、物料和设备等情况,以及应考虑人员流动路线速度和交通安排,使得流程达到最优状态。
优化之后,可以有效提高生产速度和产品质量。
3.设备的优化和协调设备的选择和优化也非常重要。
应该试图在每个工作站中使用自动化设备,减少人工操作,加速生产速度。
还应该考虑设备之间的协调性,以避免设备之间的冲突或阻塞。
适当地增加不同的设备,可以提高产品的生产速度,并保证高质量的生产。
拖拉机智能制造柔性装配线平衡问题研究

拖拉机智能制造柔性装配线平衡问题研究1. 引言1.1 研究背景拖拉机是农业生产中的重要机械设备,对农业生产起着至关重要的作用。
随着现代农业的发展,人们对拖拉机的需求越来越大,生产效率和质量要求也越来越高。
传统的拖拉机制造采用人工装配线的方式,存在着效率低、精度不高、生产效率低等问题,迫使人们不得不寻求新的解决方案。
智能制造技术的不断发展为拖拉机制造行业带来了新的希望。
智能制造技术可以提高生产效率、降低生产成本、改善产品质量,为拖拉机制造业的发展提供了新的动力。
在实践中,拖拉机制造中的柔性装配线平衡问题成为了一个亟待解决的难题。
如何利用智能制造技术解决拖拉机制造中的装配线平衡问题,提高生产效率和产品质量,成为了当前研究的重要课题。
有必要对拖拉机智能制造柔性装配线平衡问题进行深入研究,为拖拉机制造行业的发展提供新的思路和方法。
1.2 研究目的研究的目的是为了探讨拖拉机智能制造柔性装配线平衡问题,通过深入分析现有的技术和应用情况,解决在拖拉机制造过程中出现的装配线不平衡问题,提高生产效率和产品质量。
通过本研究,可以为拖拉机制造企业提供有效的解决方案和实施策略,帮助企业实现智能制造技术的应用,提升市场竞争力。
本研究还将通过实际案例和数据分析,为拖拉机制造企业提供可行的实施策略和建议,促进产业升级和转型,推动拖拉机制造行业的可持续发展。
通过本研究,不仅可以为拖拉机制造行业的发展提供参考和借鉴,还可以为智能制造领域的研究和实践做出贡献。
1.3 研究意义拖拉机智能制造柔性装配线平衡问题研究的意义在于提高生产效率、降低生产成本、优化资源利用、提升产品质量。
随着智能制造技术的不断发展,传统的生产模式无法满足市场需求的变化和生产效率的要求。
研究拖拉机智能制造柔性装配线平衡问题,探讨如何在生产过程中实现灵活性和高效性的平衡,对于提高整个制造企业的核心竞争力具有重要意义。
通过解决拖拉机制造中存在的平衡问题,可以有效提升生产线的稳定性和生产效率,缩短生产周期,减少生产过程中的浪费,降低生产成本,提高企业的市场竞争力。
基于人工智能的自动化装配线的设计与优化
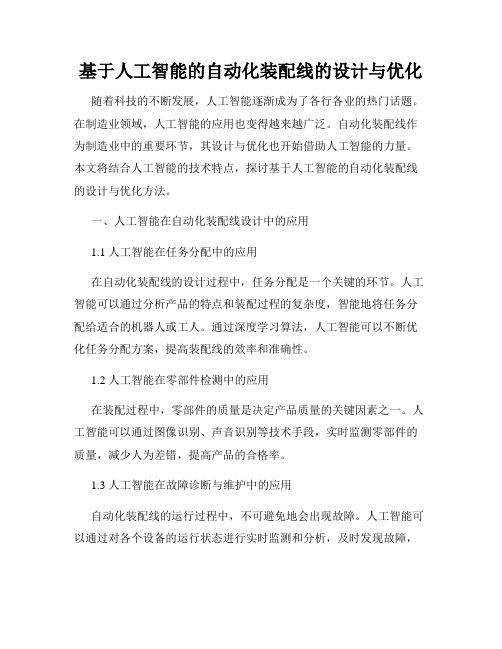
基于人工智能的自动化装配线的设计与优化随着科技的不断发展,人工智能逐渐成为了各行各业的热门话题。
在制造业领域,人工智能的应用也变得越来越广泛。
自动化装配线作为制造业中的重要环节,其设计与优化也开始借助人工智能的力量。
本文将结合人工智能的技术特点,探讨基于人工智能的自动化装配线的设计与优化方法。
一、人工智能在自动化装配线设计中的应用1.1 人工智能在任务分配中的应用在自动化装配线的设计过程中,任务分配是一个关键的环节。
人工智能可以通过分析产品的特点和装配过程的复杂度,智能地将任务分配给适合的机器人或工人。
通过深度学习算法,人工智能可以不断优化任务分配方案,提高装配线的效率和准确性。
1.2 人工智能在零部件检测中的应用在装配过程中,零部件的质量是决定产品质量的关键因素之一。
人工智能可以通过图像识别、声音识别等技术手段,实时监测零部件的质量,减少人为差错,提高产品的合格率。
1.3 人工智能在故障诊断与维护中的应用自动化装配线的运行过程中,不可避免地会出现故障。
人工智能可以通过对各个设备的运行状态进行实时监测和分析,及时发现故障,并给出故障诊断和维护的建议。
这可以大大减少因故障导致的停机时间,提高装配线的稳定性和生产效率。
二、基于人工智能的自动化装配线设计与优化方法2.1 数据采集与处理在设计自动化装配线之前,我们首先需要收集大量的装配线相关数据,并对这些数据进行有效的处理。
人工智能的数据处理能力可以帮助我们从海量数据中发现规律和模式,为装配线设计提供科学依据。
2.2 智能决策与优化算法基于人工智能的自动化装配线设计与优化,核心在于智能决策和优化算法的应用。
通过建立适当的数学模型,并结合人工智能算法,可以实现对装配线布局、任务分配、工时安排等方面的智能决策和优化。
例如,可以运用遗传算法、神经网络等方法,不断优化装配线的效率和生产成本。
2.3 过程监控与改进在装配线运行的过程中,我们需要通过实时监控和数据分析,了解装配线的状态和效率。
汽车智能制造案例

汽车智能制造案例汽车智能制造是指通过应用先进的信息技术和智能化设备,实现汽车生产过程的自动化、智能化和柔性化,提高生产效率和产品质量的一种制造模式。
下面将列举10个与汽车智能制造相关的案例。
1. 智能机器人装配线:传统汽车生产中,大量的装配工作需要人工完成,容易出现疲劳、误差等问题。
而智能机器人装配线能够实现自动化装配,提高生产效率和产品质量。
2. 智能无人搬运车:在汽车生产过程中,需要大量的物料搬运工作。
使用智能无人搬运车可以实现物料的自动化搬运,减少人力成本和工作风险。
3. 智能质检系统:传统的质检过程需要大量的人力和时间,容易出现漏检和误检等问题。
而智能质检系统利用机器视觉和人工智能技术,可以实现对产品的自动化检测,提高质检效率和准确性。
4. 智能物流管理系统:在汽车生产过程中,需要对物料和零部件进行管理和配送。
智能物流管理系统可以实现对物料和零部件的自动化管理和配送,提高物流效率和准确性。
5. 智能制造执行系统:智能制造执行系统是汽车智能制造的核心技术之一,它能够实时监控和控制生产过程,提高生产调度的灵活性和响应速度。
6. 人机协作生产系统:传统的汽车生产线上,人工和机器之间的协作相对独立,容易出现不协调和浪费。
而人机协作生产系统通过智能感知和控制技术,实现人机之间的紧密协作,提高生产效率和灵活性。
7. 智能供应链管理系统:在汽车生产过程中,需要对供应链进行管理和协调。
智能供应链管理系统利用大数据和物联网技术,可以实现对供应链的实时监控和调度,提高供应链的效率和可靠性。
8. 虚拟现实技术在汽车设计中的应用:虚拟现实技术可以帮助汽车设计师在虚拟环境中进行设计和模拟,减少实际样车的制作和测试成本,提高设计效率和产品质量。
9. 3D打印技术在汽车零部件制造中的应用:3D打印技术可以实现对汽车零部件的快速制造和个性化定制,减少库存和物流成本,提高制造灵活性和响应速度。
10. 智能驾驶技术在汽车生产中的应用:智能驾驶技术可以帮助汽车制造商实现对汽车生产过程的自动化和智能化,提高生产效率和产品质量。
装配生产线(3篇)

第1篇随着科技的飞速发展,制造业在生产效率、产品质量和生产成本等方面对装配生产线提出了更高的要求。
装配生产线作为现代制造业的核心环节,其高效、稳定和智能化的特点,已成为推动产业升级的重要力量。
本文将从装配生产线的定义、组成、特点以及发展趋势等方面进行阐述。
一、装配生产线的定义装配生产线是指按照产品组装工艺流程,将原材料、零部件等经过一系列加工、组装、检测等工序,最终形成成品的生产线。
它具有自动化、连续化、模块化、柔性化等特点,是实现产品大批量、高效率生产的基础。
二、装配生产线的组成1. 设备:包括各种自动化设备、手动设备、检测设备等,如数控机床、机器人、输送带、自动化检测设备等。
2. 工具:包括用于组装、调试、维修等工序的各种工具,如扳手、螺丝刀、量具等。
3. 辅助设备:包括用于提高生产效率、改善工作环境的设备,如输送设备、周转车、工具柜等。
4. 人员:包括生产线操作人员、管理人员、维修人员等。
5. 软件系统:包括生产管理系统、设备控制系统、质量控制系统等。
三、装配生产线的特点1. 自动化:装配生产线采用自动化设备,实现了生产过程的自动化,提高了生产效率。
2. 连续化:生产线上的设备、工装、物料等按照一定的工艺流程进行连续生产,减少了生产过程中的停顿和等待时间。
3. 模块化:生产线上的设备、工装等可根据产品需求进行灵活配置,便于生产线的扩展和升级。
4. 柔性化:装配生产线可适应不同产品的生产需求,实现多品种、小批量生产。
5. 精细化:装配生产线采用高精度设备、工装和检测设备,确保产品质量。
6. 环保节能:装配生产线采用节能设备、环保材料,降低生产过程中的能耗和污染。
四、装配生产线的应用1. 汽车制造:汽车生产线是典型的装配生产线,包括车身焊接、涂装、总装等环节。
2. 电子产品:电子产品生产线包括元器件加工、组装、测试等环节,实现电子产品的批量生产。
3. 家用电器:家电生产线涵盖冰箱、洗衣机、空调等产品的组装、检测等环节。
装配线发展历程

装配线发展历程
装配线的发展历程可以追溯到工业革命时期。
以下是装配线的主要发展阶段:
1. 手工装配阶段:在早期工业革命阶段,产品的生产主要依赖于手工劳动。
工人在生产线上按照顺序完成各个工序,如零件加工、组装等。
2. 传送带系统的引入:为了提高生产效率和降低成本,传送带系统被引入,使得零件和产品可以沿着一条线进行运输。
这种系统的使用大大提高了生产效率,减少了工人的劳动强度。
3. 首次应用自动化技术:随着自动化技术的出现和发展,工厂开始使用自动化设备来替代人工劳动。
自动化设备可以完成重复性工作,并且具有更高的精度和效率。
4. 产业机器人的出现:产业机器人的出现标志着装配线的进一步发展。
这些机器人可以完成更加复杂和精细的任务,如焊接、喷涂和装配等。
它们的使用提高了生产线的灵活性和生产效率。
5. 智能制造和物联网的应用:随着信息技术和物联网的快速发展,智能制造概念开始被广泛应用于装配线中。
通过传感器和数据分析技术,装配线可以实现实时监测和远程控制,提高生产线的自动化程度和生产效率。
6. 柔性生产线的兴起:柔性生产线是指具有快速转换能力和适应性的生产线。
它可以根据需求快速更改生产流程和产品组合,
提高生产线的灵活性和客户定制能力。
总的来说,装配线的发展历程经历了从手工劳动到自动化设备和机器人的应用,再到智能制造和柔性生产的阶段。
每个阶段都以提高生产效率、降低成本和提升产品质量为目标。
随着科技的不断进步,装配线的发展也将继续推动工业生产的革新。
什么是纯作业人工数?什么是附带作业人工数?
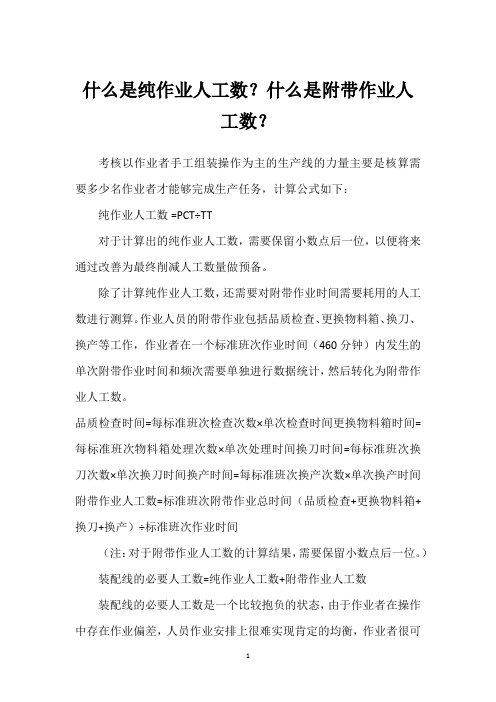
什么是纯作业人工数?什么是附带作业人
工数?
考核以作业者手工组装操作为主的生产线的力量主要是核算需要多少名作业者才能够完成生产任务,计算公式如下:
纯作业人工数=PCT÷TT
对于计算出的纯作业人工数,需要保留小数点后一位,以便将来通过改善为最终削减人工数量做预备。
除了计算纯作业人工数,还需要对附带作业时间需要耗用的人工数进行测算。
作业人员的附带作业包括品质检查、更换物料箱、换刀、换产等工作,作业者在一个标准班次作业时间(460分钟)内发生的单次附带作业时间和频次需要单独进行数据统计,然后转化为附带作业人工数。
品质检查时间=每标准班次检查次数×单次检查时间更换物料箱时间=每标准班次物料箱处理次数×单次处理时间换刀时间=每标准班次换刀次数×单次换刀时间换产时间=每标准班次换产次数×单次换产时间附带作业人工数=标准班次附带作业总时间(品质检查+更换物料箱+换刀+换产)÷标准班次作业时间
(注:对于附带作业人工数的计算结果,需要保留小数点后一位。
)装配线的必要人工数=纯作业人工数+附带作业人工数
装配线的必要人工数是一个比较抱负的状态,由于作业者在操作中存在作业偏差,人员作业安排上很难实现肯定的均衡,作业者很可
能在标准班次内完不成生产任务而需要加班,所以在标准班次之间需要留有2~4小时的缓冲时间来解决各种特别和损失造成的影响,从而保障生产方案和任务的完成。
- 1、下载文档前请自行甄别文档内容的完整性,平台不提供额外的编辑、内容补充、找答案等附加服务。
- 2、"仅部分预览"的文档,不可在线预览部分如存在完整性等问题,可反馈申请退款(可完整预览的文档不适用该条件!)。
- 3、如文档侵犯您的权益,请联系客服反馈,我们会尽快为您处理(人工客服工作时间:9:00-18:30)。
17.5 Line Balancing Algorithms 生產線平衡算法
To distribute the total workload as evenly as possible. 儘可能平均分發總工 作量
w
Minimize (wTs Twc ) or Minimize (Ts Tsi )
-Line pacing生產線步調
- Maintain production rate by a mechanized conveyor. 透過機械化的輸送裝置保持生產率
17.1 Fundamentals of Manual Assembly Lines人工裝配線的基礎
Figure 17.1 (圖17.1)
efficiency
重新定位效率
Er
Ts Tc
Tc Tr Tc
17.4.2 The Line Balancing Problem 生產線平衡問題
Assigning the individual work elements to workstations so that all workers have an equal amount of work. 把個別的工作項目分發到工作站,以便全 部工人有相等的工作量。
Concepts概念
-Minimum rational work elements 最小合理的 工作項目 -Precedence constraints先後順序限制條件
17.4.2 The Line Balancing Problem
Minimum rational work elements
Introduction
Why is it productive?為什麼它是有生產力 的?
-Specialization of labor勞工的專業化
- Learning curve學習曲線
-Interchangeable parts可互換零件 -Work principle工作原則
- Applied to make smooth material handling可應用來 達到平順的物料處理
where Ts = max { Tsi }
-Eb = 0.9 ~0.95
-Balance delay 平衡延遲
d
wTs Twc wTs
Labor efficiency (勞工效率) = E Er Eb Revised number of workers 修正工人的數量
w minimum integer RpTwc Twc Twc 60 EEr Eb Er EbTc EbTs
Mechanized work transport 機械化的工作
運輸
17.1.3 Line Pacing 生產線步調
Rigid pacing 硬性步調
- 固定時間完成工作
Pacing with margin 有範圍的步調
- Allowing queues 允許等候線 - Designing the station to be longer length 設計工作站 有較長的輸送帶長度
-Synchronous transport 同步運輸
- Move simultaneously 同時移動(例如轉盤)
-Asynchronous transport非同步運輸
- Move independently、Small queues 獨立移動、小量等 候
17.1.2 Work Transport Systems 工件運輸系統
人工方法的工件運輸
-Starving and blocking buffers 缺料和阻擋現象 緩衝區
Mechanized work transport 機械化的工作運輸
-Continuous transport 連續的運輸
- Work units may be fixed or removable工件可能是固定 的或可移動的 - 例如輸送帶 (汽車或電子產品)
17.1.4 Coping with Product Variety 對應於產品種類
Single model 單一模型
-No variety
Batch model 批量模型
-Hard variety
Mixed model 混合模型
-Soft variety -Vs. batch model
- No production time lost 沒有生產時間浪費 - Lower inventories 較低的存貨 - Adjustable production rate 可調整的生產率 - Line balancing problem 生產線平衡問題 - difficult scheduling and logistics困難的排程和運籌
17.3 Design for Assembly (DFA) 為方便組裝的設計
During product design:在產品設計階段
- Fewer parts 更少的零件 - Easy to assembly. 容易組裝
General principles 一般通則
- Use the fewest number of parts possible儘可能的使用 最少的零件數量
最小合理的工作項目
-A small amount of work having a specific limited objective (required time: Tek)
ne
Twc
Tek
k 1
ne:number of work elements 工作項目的數量
-The task time at station I 在工作站i 的工作時間
17.4 Analysis of Single Model Assembly Lines
(Hourly) Workload (每小時)工作量
WL Rp Twc
Minimum number of workers 至少工人的數
量
w* WL minimum integer Twc
AT
i 1
subject to (1) Tek Ts
ki
(2) precedencereqirements are obeyed
Tc
-Theoretical formula because of:此乃理論公式因為
- Repositioning losses: 重新定位之損失
- E.g. workers walk from the ending position to the starting position.
- The line balancing problem 生產線平衡問題 - Task time variability 工作時間變化性 - Quality problem品質問題
Da: Annual demand 每年需求
Rp
Da 50SH
plant operates 50 wk/yr 工廠一年運作50週 S:每週班次 H:每班次工作時數
Cycle time週期時間(min/cycle) and cycle rate週期率
(cycles/hr 對於生產線而言)
Tc
60 E Rp
17.4.2 The Line Balancing Problem Example 17.1
Example 17.1
17.4.2 The Line Balancing Problem
Measures of line balance efficiency
Eb
Twc w Ts
生產線平衡效率的測量
workers i
assigned
-Utility workers
- Helping workers - Relieving workers - Maintenance
17.1.2 Work Transport Systems 工件運輸系統
Manual methods of work transport
Assembly workstations 組裝工作站
-Workers stand or sit. 工人站或坐 -Average manning level 平均人工化水準
n
wu wi
M
i1 w
n
n
wu: number of utility workers
wi
:
number of to station
- For fixed work unit with continuous moving.
- Allowing to move beyond the boundaries 允許在邊界 以外移動
No pacing 無步調
- No time limit 沒有時間限制
- Manual transport, removable work unit or asynchronous conveyor. 人工運輸、可移動的工件或非同步輸送帶 - Motivating workers to achieve a certain pace.激勵工人達到一 定步調
17.4.1 Repositioning losses . 重新定位的損失
M大的可允許的服務時間
Ts Max{Tsi} Tc Tr Tr: repositioning time
-Figure 17.4
Repositioning
- Symmetrical features 對稱的特徵
- Avoid parts that tangle 避開纏結的零件
- Less hooks, holes, etc. 較少鉤,洞等等
17.4 Analysis of Single Model Assembly Lines單一模型裝配線的分析