火力发电厂轴瓦的补焊工艺及无损检测
电厂发电机轴瓦损坏原因分析及无损检测方法的探讨

2012年3月内蒙古科技与经济March 2012 第6期总第256期Inner Mongolia Science T echnology &Economy No .6Total No .256电厂发电机轴瓦损坏原因分析及无损检测方法的探讨X王永亮,霍凤仙(内蒙古国电电力工程技术研究院,内蒙古呼和浩特 010080) 摘 要:简要介绍了电厂用汽轮机、发电机轴承轴瓦类型、优点及损坏原因,对于轴瓦上合金与基体脱开的探伤方法进行了探讨,并对几种探伤方法的优缺点进行了对比。
关键词:轴瓦;合金;超声波;探伤;电厂;发电机 中图分类号:T K263.6+4 文献标识码:A 文章编号:1007—6921(2012)06—0115—021 电厂汽轮机、发电机用轴承合金简介电厂汽轮机、发电机用轴承可分为滑动轴承和滚动轴承两大类,滑动轴承与滚动轴承相比,承压面积大,工作平稳,无噪声及装拆方便,因此,在机械设备上广泛使用。
滑动轴承一般由轴承体和轴瓦构成,轴瓦直接支托着转动的轴,为了提高轴瓦的强度和耐磨性及保护转动的轴,往往在轴瓦(钢质轴瓦、铸钢轴瓦、铸铁轴瓦)的内侧表面上堆焊上一层巴氏合金或浇注上一层巴氏合金,巴氏合金国内常称为乌金。
国内常见的轴承合金有锡基、铅基轴承合金(巴氏合金)、铜基轴承合金和铝基轴承合金。
锡基、铅基轴承合金是目前使用最多的一种轴承合金。
锡基、铅基巴氏合金组织为软基体内分布着硬质点(一般为化合物,其体积占15%~30%),当轴转动时软的基体很快被磨损掉而凹下去,硬的质点比较抗磨,便突出于表面以承受载荷,并抵抗自身的磨损,凹下去的地方可以储存润滑油,保证有较低的摩擦系数,同时,软的基体有较好的磨合性及抗冲击和减震性。
锡基巴氏合金(含锡量为80%左右)能担负较大的负载,硬度较大,传热性能好,耐冲击,耐振动,耐磨损,耐腐蚀及有良好的韧性,但是粘附性差,成本较高。
2 轴瓦烧毁的原因分析轴瓦的烧毁有乌金碎裂和乌金碾压2种情况,可能引起烧毁的原因有以下几种:转轴相对振动较大引起轴瓦损坏;轴瓦抗震性能降低引起轴瓦损坏;乌金温度高(润滑不良)引起轴瓦损坏;润滑油脏污造成碾压和碎块,引起轴瓦损坏;润滑油含水危害油膜的形成,引起轴瓦损坏。
火力发电厂金属部件无损检测质量控制办法

火力发电厂金属部件无损检测质量控制办法摘要:本文主要对火力发电厂金属部件的无损检测问题进行了相关分析,同时探讨了金属部件无损检测的相关标准,由此集中对其质量控制办法进行了阐述。
通过了解火力发电厂金属部件的表面缺陷危害及检测要求,明确了在实际检测过程中应注意的问题及质量控制办法。
关键词:火力发电厂;金属部件;无损检测;质量控制随着中国经济发展水平不断提高,中国工业发展取得了显著成就,火力发电厂是中国重要能源企业,在发电、配电、输电等方面有非常重要的作用。
火力发电厂的金属部件不仅运行工况较为恶劣,且制造工艺复杂。
在制造、安装、运行过程中,金属部件均有可能产生缺陷,这些缺陷对于金属部件的安全运行危害很大,对于火电厂机组的安全稳定运行产生重大影响。
因此,对于金属部件的检验检测变得尤为重要。
在整个金属部件检测工作中,无损检测是最基础,同时也是最为实用的检测方法。
1火力发电厂金属部件的主要缺陷缺陷的形式和类型很多,原材料中的缺陷主要有发纹、分层、金属夹杂、缩孔、气孔等。
焊接过程中的主要缺陷有焊接裂纹、气孔、夹渣、未焊透、未融合等。
机组运行过程中容易产生疲劳裂纹,蠕变裂纹和腐蚀裂纹。
在火力发电厂金属部件中,管子及焊缝的主要缺陷有管材缺陷,管材质量不好,如重皮、过大的加工直道、机械碰伤等,在高温高压下工作,会产生较大的应力集中,造成管子开裂。
管子对接焊缝存在焊接缺陷,或是焊缝成形不良,造成过大的应力集中,产生裂纹。
2火力发电厂金属部件无损检测通过以上分析,发现火力发电厂金属部件表面的最主要缺陷就是裂纹缺陷,无论何种原因,裂纹缺陷所导致的金属部件运行隐患必然存在。
因此,金属部件表面检测重点主要在于裂纹检测。
金属部件表面裂纹检测方法很多,针对不同情况,相关检测人员应采取不同检测方法。
目前普遍采用的五大常规无损检测方法为:超声检测;射线检测;涡流检测;磁粉检测;渗透检测。
2.1质量控制方法2.1.1提高人员的专业素质人员的控制检验人员是检验的主体,是决定检验质量的客观条件,但同时,人的主观意识对检验结果的判定起主导作用,所以检验人员的素质是至关重要的。
浅谈火电厂无损检测质量控制

浅谈火电厂无损检测质量控制摘要:火电事业推动着国民经济、社会的发展和进步,也是我国电力的主要来源。
在火电厂建设过程中,无损检测是控制安装质量和焊接质量的重要手段。
可以说无损检测的实施效果直接关系到工程质量的好坏。
如何利用好无损检测技术成为确保工程质量的关键。
本文通过对无损检测技术进行概述,进一步提出了无损检测质量保证体系以及质量控制的具体方法和措施。
关键词:火力发电厂;无损检测;质量控制;方法和措施引言目前我国为确保火力发电厂建设的工程质量,主要采用无损检测方法对建造、维修过程进行质量控制。
随着社会的进步和科技的发展,电厂建设过程中所采用的材料逐渐被高合金、高强钢等特殊材料所取代。
这就对无损检测的实施提出了更高的要求,如何利用好无损检测技术,提高无损检测的实施效果成为确保工程质量的关键。
1 无损检测技术概述1.1 无损检测的概念及主要方法无损检测技术以不损害被检验对象的实用性能为前提,应用物理、化学原理,对各种工程材料、零部件、结构件等进行有效的检验和测试,进而评价它的连续性、完整性、安全可靠性。
无损检测包括:检验材料的材质,探测材料、构件或焊缝中是否存在缺陷(铸造缺陷、加工缺陷、焊接缺陷等),并对缺陷的形状、大小、方位、取向、分布和内含物等情况进行判断,还能提供组织分布、应力状态以及某些机械和物理量等信息。
目前,火力发电厂安装工程中的无损检测通常包括射线检测(分为X射线检测和γ射线检测)、超声检测、磁粉检测和渗透检测,光谱分析等。
1.2 无损检测的主要功能和价值无损检测技术是火力发电厂安装过程中实施金属技术监督的重要组成部分,是检验焊接质量的重要检测手段。
将无损检测技术运用到火力发电厂安装工程中,不仅可以提高工程效率,保障工程质量,而且可以有效降低工程成本,产生一定的经济价值。
无损检测技术的主要功能体现在以下三个方面。
(1)无损探伤:对电厂质量作出评价,无论是锻件、铸件、焊接件、钣金件或机加件都能用无损检测技术找出它的表面或内部缺陷,并能对缺陷进行定性及定量分析。
火力发电厂安装过程中无损检测与焊接管理-精品文档
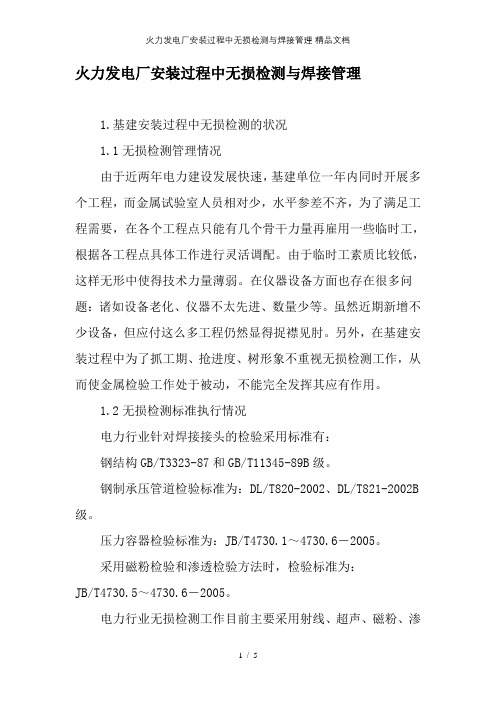
火力发电厂安装过程中无损检测与焊接管理1.基建安装过程中无损检测的状况1.1无损检测管理情况由于近两年电力建设发展快速,基建单位一年内同时开展多个工程,而金属试验室人员相对少,水平参差不齐,为了满足工程需要,在各个工程点只能有几个骨干力量再雇用一些临时工,根据各工程点具体工作进行灵活调配。
由于临时工素质比较低,这样无形中使得技术力量薄弱。
在仪器设备方面也存在很多问题:诸如设备老化、仪器不太先进、数量少等。
虽然近期新增不少设备,但应付这么多工程仍然显得捉襟见肘。
另外,在基建安装过程中为了抓工期、抢进度、树形象不重视无损检测工作,从而使金属检验工作处于被动,不能完全发挥其应有作用。
1.2无损检测标准执行情况电力行业针对焊接接头的检验采用标准有:钢结构GB/T3323-87和GB/T11345-89B级。
钢制承压管道检验标准为:DL/T820-2002、DL/T821-2002B 级。
压力容器检验标准为:JB/T4730.1~4730.6―2005。
采用磁粉检验和渗透检验方法时,检验标准为:JB/T4730.5~4730.6―2005。
电力行业无损检测工作目前主要采用射线、超声、磁粉、渗透、涡流五种检测方法。
而磁粉、渗透、涡流主要用于检测工件或焊缝的表面及近表面缺陷,在基建安装过程中焊接质量控制主要采用射线和超声波两种方法。
《火力发电厂焊接技术规程》DL/T869-2012代替原有DL5007―92,成为现在电力行业无损检测的依据。
它规定了钢制压力容器及承压管道焊缝必须执行的无损检测标准合格级别、各部件应采用的无损检测方法和检验比例。
在DL/T869―2012规程中我们可以看到以下几个特点:1.随着机组压力参数提高,I类焊接接头检验比例明显的提高(超临界机组锅炉的I类焊接接头为100%无损检测);2.Ⅱ、Ⅲ类焊接接头检验比例为抽检; 3.对应采用何种检验方法也作了明确规定,并强调了超声波与射线检测之间的相互重叠。
质量工艺手册(轴瓦检修)

安全质量标准化
—轴瓦检修关键工艺
1、轴瓦的检查:
关键质量工艺要求:
1
对所检修的轴瓦首先进行外观检查,是否存在气孔、裂纹等缺陷,并进行详细的记录。
2
检查轴瓦尺寸是否正确,轴瓦乌金是否脱胎或局部脱落(可浸煤油实验、超声波探伤等方法)。
3
乌金面上轴颈磨擦痕迹所占的位置是否正确,该处的刮研刀花是否被磨亮,有无划伤,损坏和磨蚀。
4
垫铁承力面或球面上有无磨损和磨蚀,垫铁螺钉是否松动以及垫铁是否完好。
5 检查轴承各部份间隙是否符合要求,如轴瓦处有磨得发
亮,变硬,要进行修刮,以免损伤轴颈。
6 检查轴颈有无损伤,并用金相砂纸打磨轴颈。
检查轴瓦是
否存在脱
胎、气孔等
缺陷 乌金磨擦痕
迹所占位置
是否正确 打磨轴颈,检查有无损
伤
2、更换轴瓦所进行的检查:
关键质量工艺要求:
1 新的轴瓦首先进行外观检查,是否存在气孔、裂纹等缺陷,并进行详细的记录。
2 检查轴瓦尺寸是否正确,轴瓦乌金是否脱胎或局部脱落(可浸煤油实验、超声波探伤等方法)。
3 对新轴瓦进行初步修刮,使轴与轴瓦之间出现部分间隙,但一般不超过正常间隙的2/3。
3、下轴瓦的初步修刮:
4、下轴瓦的精刮:
5、上轴瓦的研刮:。
火力发电厂焊接技术一般规定

火力发电厂焊接技术一般规定「总的要求1.1.1焊接工程应按DL/T868进行焊接工艺评定,编制焊接工艺、作业指导书,必要时应编制焊接施工措施文件。
1.1.2焊接接头质量检验应根据部件工况条件和质量要求分类。
1.1.3焊接人员考核应符合有关规程的规定。
1.1.4焊接工程质量验收,应符合DL/T5210.5的规定。
1.1.5汽包、汽轮机铸钢件、汽轮机叶片、轴颈、轴瓦巴氏合金、阀门等重要部件焊接或焊接修复应分别符合DL/T734、DL/T753、DL/T905>DL/T1927、DL/T1621的规定。
1.1.6电力钢结构、母线、凝汽器管板焊接应分别符合DL/T 678、DL/T754、DL/T1097的规定。
1.1.7焊接工作应遵守国家和行业的安全、环保规定和其他专项规定。
1.2企业及焊接人员1.2.1承担火力发电厂焊接工程的施工、监理、检修和相关工作的单位应具备下列条件:a)具有国家认可的与承担工程相适应的单位资质,具备相应的质量保证体系;b)企业质量体系中应对焊接工程管理有明确的规定,焊接工程中,质量体系应有效运行,确保焊接工程的质量;c)指定焊接专业负责人,负责本专业的技术、质量及安全工作;d)具备与工程规模相适应的焊接施工、检验装备和人力资源条件;e)施工和监理企业应经常组织焊接人员参加专业技术培训。
1.2.2承担火力发电厂焊接工程的焊接人员应具备的条件1.2.2.1焊接技术人员应具备下列条件:a)焊接技术人员应经过专业技术培训,取得相应的证书;b)焊接技术人员应有不少于1年的专业技术实践;0焊接工程中担任管理或技术负责人的焊接技术人员应取得相应专业中级或以上专业技术资格。
1.2.2.2 焊接质量检查人员应具备下列条件:a)焊接质量检查人员应具有初中及以上的文化程度,具有3年及以上实践经验;b)焊接质量检查人员应经过专门技术培训,具备相应的质量管理知识,并取得相应的证书。
1.2.2.3焊接检验、检测人员应具备下列条件:a)无损检测人员应按照DL/T675的规定参加考核并取得相应的技术资格;b)从事金相、光谱、力学性能检测的人员,应按照相关的规定取得相应的资格;c)焊接检验、检测人员的证书应在有效期内;d)评定检测结果,签署检测报告的人员应具备中级及以上资格。
火力发电厂焊接技术规程 (2)

火力发电厂焊接技术规程1. 引言火力发电厂是一种以燃煤、燃油或天然气等燃料为能源,通过燃烧产生热能进而转化为电能的发电设施。
在火力发电厂的建设和运行中,焊接是不可或缺的工艺之一。
为了确保焊接质量,提高工程质量,制定火力发电厂焊接技术规程非常重要。
本文档旨在规范火力发电厂焊接工程的施工过程,明确焊接质量和安全要求,保证焊接工作的稳定运行。
2. 参考标准本文档以以下标准为参考:1.GB 50305-2001 焊接施工质量检验规范2.GB/T 985.1-2001 金属焊接术语3.GB/T 196-2003 焊接术语4.GB/T 2651-2008 电弧焊用螺旋缝焊条(电极)5.GB/T 5117-2012 船用电焊条6.GB/T 8110-2008 钢管焊接焊缝强度试验方法3. 焊接设备要求为了确保焊接工作的顺利进行,火力发电厂应配备先进、可靠的焊接设备。
焊接设备应符合以下要求:•焊接设备应具备稳定的电源,能满足预定焊接电流和电压的要求;•焊接设备应具备良好的温度控制系统,避免过热和过冷现象发生;•焊接设备应具备防止漏电的保护装置,确保焊工的人身安全;•焊接设备应具备适当的调节和控制功能,以满足不同焊接工艺的要求。
4. 焊接工艺要求4.1 焊接材料选择火力发电厂焊接工程中常使用的焊接材料有焊条、焊丝和焊剂等。
选择适当的焊接材料对于焊接质量的提高至关重要。
•焊条的选用应符合GB/T 2651-2008标准的要求,焊条的种类、牌号应根据焊接材料的性能要求和焊接工艺进行选择;•焊丝的选用应符合GB/T 983-2008标准的要求,焊丝的种类、牌号应根据焊接材料的性能要求和焊接工艺进行选择;•焊剂的选用应符合GB/T 3429-2017标准的要求,焊剂应具有良好的润湿性和除氧性。
4.2 焊接工艺选择根据焊接材料、焊接位置和焊接工艺要求,确定合适的焊接工艺。
常见的焊接工艺有手工电弧焊、埋弧焊、气体保护焊等。
根据不同场合的要求选择合适的工艺应用于焊接工程中。
火力发电厂工程金属检测方法概述

火力发电厂工程金属检测方法概述
火力发电厂工程金属检测是指对火力发电厂工程中使用的金属材料进行质量检测的方法。
火力发电厂工程中使用的金属材料通常包括钢材、铜材、铝材等。
以下是火力发电厂工程金属检测的常见方法概述:
1. 无损检测:无损检测是一种非破坏性检测方法,可用于检测金属材料表面和内部的缺陷,如裂纹、气孔、夹杂物等。
常用的无损检测方法包括超声波检测、X射线检测、磁粉检测等。
2. 化学分析:化学分析可用于检测金属材料中的化学成分,以确定其是否符合要求的标准。
常用的化学分析方法有光谱分析、质谱分析、原子吸收光谱等。
3. 物理性能测试:物理性能测试可用于评估金属材料的力学性能、物理性能和热学性能等。
常用的物理性能测试方法有硬度测试、拉伸测试、冲击测试等。
4. 金相分析:金相分析是一种显微观检测方法,可用于观察金属材料的晶体结构、组织形态和缺陷情况。
金相分析通常需要进行金属样品的切割、打磨、腐蚀等前处理工序,然后使用显微镜观察和分析。
5. 电化学测试:电化学测试可用于评估金属材料的腐蚀性能和抗腐蚀能力。
常用的电化学测试方法包括极化曲线法、交流阻抗法等。
以上是火力发电厂工程金属检测的常见方法概述,通过这些方法可以对金属材料进行全面的检测和评估,确保其质量符合要求,以提高火力发电厂工程的安全和可靠性。
- 1、下载文档前请自行甄别文档内容的完整性,平台不提供额外的编辑、内容补充、找答案等附加服务。
- 2、"仅部分预览"的文档,不可在线预览部分如存在完整性等问题,可反馈申请退款(可完整预览的文档不适用该条件!)。
- 3、如文档侵犯您的权益,请联系客服反馈,我们会尽快为您处理(人工客服工作时间:9:00-18:30)。
浅谈火力发电厂轴瓦的补焊工艺及无损检
测
汽轮机轴瓦运行中会出现局部脱落现象,整体更换价格昂贵,
常用局部补焊的方法进行修复。
汽轮机轴瓦在传统上常用渗透来检
验乌金复合层的复合情况,这种检验方式对于非开口性的脱层无法
检验,已越来越不适应我公司大功率、高参数机组轴瓦检验的要求。
利用渗透检验和超声波检验两种方法对轴瓦进行综合检测,不但具
有较高的检测灵敏度而且具有较高的发现缺陷的能力,可有效的保
证发电厂的安全运行,可广泛地用于汽轮机轴瓦缺陷的检测。
1、轴瓦的类型及应用
汽轮机轴承合金为巴氏合金,巴氏合金按化学成分分为两类,即锡基轴承合金和铅基轴承合金。
锡基轴承合金是以Sn为基础,加入少量Sb、Cu所组成的合金,典型的牌号为:ZChSnSb11-6,常用于浇注重载高速和抗蚀要求高的轴瓦,如汽轮机和发电机的主轴瓦;铅基轴承合金是以Pb为基础加入Sn、Sb、Cu等所组成的合金,典型的牌号为ZChPbSbl6—16—2,常用来制造低中载荷和低中速设备的轴承,如泵、风机、磨煤机和电动机的轴承衬。
大型轴承在使用过程中会经常碰到轴瓦瓦面合金损坏的情况,比如脱胎、裂纹、局部脱落或磨损以及腐蚀等,产生的原因较多,如制造时浇注质量问题、运行操作因素、检修安装方面的因素等,大型轴瓦价格昂贵,为减少经济损失,一般采取补焊修复的方式来解决该问题。
2、补焊修复工艺
2.1 修复方法的选择
轴瓦的修复有两种方法,即整体浇铸和局部补焊。
整体浇注的质量容易保证,但工艺复杂、技术要求高,需有浇注的专用设备、费用较高、工期相对较长。
局部补焊的工艺简单、费用低、工期短、工作量小、在现场可以直接实施,但补焊时温度较难掌握,易产生二次脱胎和其它质量问题。
从经济原则考虑,乌金轴瓦现场修复采用氧乙炔火焰进行局部补焊的方法。
2.2补焊工艺
2.2.1清理瓦胎
1)判断脱胎部位,然后用尖铲、錾子把脱胎部分彻底剔除;2)用钢丝刷将轴瓦的凹面清理干净,露出金属光泽;3)用热碱水(10%氢氧化钠或氢氧化钾)清洗数次,再用清水清洗;4)用氧乙炔火焰(氧化焰)把瓦面烧一遍,以清除残留在细孔的石墨和油垢,并用白布轻擦表面。
2.2.2挂锡
挂锡的目的是要增加轴承合金对瓦胎的附着力,使其紧密地结合在一起。
通常采用工艺性能好的锡铅合金焊锡作为挂锡材料。
1)把锡加工成直径4~6mm的条状;2)在瓦胎表面涂上一层盐酸,数分钟后用清水冲洗并用白布擦干净;3)用氧乙炔火焰(中性焰或轻微碳化焰)将瓦胎均匀加热到250~270℃,加热时,瓦胎要保持清洁;4)在加热中用锡条在瓦胎面上轻轻摩擦,锡条能熔化表示已达到挂锡所需要的温度;5)加热后,在瓦胎面上均匀地涂上一层氯化
锌溶液(ZnC1),随即用细铜丝刷用力来回刷瓦面,一边刷一边加锡条,直到全部瓦面挂均匀为止;6)挂好锡的瓦胎表面应是发亮的暗银色,如果出现淡黄色或黑色的斑点,则说明挂锡质量不合格,必须返工,重新再挂;7)挂锡后,应及时补焊乌金,不可放置时间过长以免氧化。
2.2.3 补焊轴承合金准备
1)轴承合金的选择:轴承合金是一种摩擦系数和摩擦消耗功率都比较低的灰白色合金,铅基合金可塑性较差,所以一般采用可塑性较强的锡基合金作为堆焊材料;2)补焊前先用一角铁作为模具,把乌金熔化成 5~6mm的条状,以适合补焊时手持操作。
不允许将用过的轴承合金重新再用;3)为了防止堆焊时瓦体过热,导致整个乌金脱胎,补焊时,要控制好温度和选择好轴瓦的放置方向。
2.2.4轴承合金的补焊
1)轴承合金的补焊质量很大程度上取决于轴承合金补焊时的温度,温度过高会增加氧化,使晶粒粗大,合金不同比重的各种金属容易分离,造成组织不均匀;温度过低则结合性能不良。
2)堆焊时,先加热挂锡后的瓦面,并用乌金条摩擦,乌金熔化并能与锡熔在一起即可填加乌金,同时向前移动。
第一遍不宜太厚,以后用同样方法堆焊,直到厚度符合要求为止。
补焊温度以能熔化轴承合金为准(乌金的熔点为240°C左右),焊接速度要快,一定要控制温度,切忌过热。
施焊中,既要保证堆焊区新旧合金熔合,又要保证非堆焊区温度不超过100%,防止发生脱胎和其他问题。
特别是比较小的
轴瓦一定要控制好温度,防止变形过大而无法使用。
3)为了防止瓦
体变形,应采用多层多道补焊。
补焊顺序见图示。
4)补焊轴瓦合金每一层每一道都要清理,用白布轻擦干净。
5)堆焊时一定要使弧坑填满、缓慢收弧,以免产生气孔及裂纹。
6)补焊轴承合金要留够加工余量,最后一层焊道要比轴瓦原始表面略高,并注意在焊道与原始表面交界处避免咬边和未熔合等缺陷。
2.2.5 焊后处理
采用刮削方法恢复其原始尺寸,使修复后的轴瓦达到设计要求。
3 无损检测工艺
3.1 渗透检测
渗透检测只能检验表面开口性缺陷。
所以对轴瓦进行渗透检测是检测轴瓦的乌金复合层表面裂纹、气孔等缺陷,以及轴瓦的乌金复合层与基体的接合面的熔合情况。
检测面为乌金瓦表面和侧面乌金复合层与基体的接合面处。
3.2 检测准备
3.2.1 轴瓦的表面光精、平整,不需修磨,完全符合渗透检验要求,但轴瓦表面通常有防护油层,进行渗透检验时必须清洗干净。
3.2.2 在汽轮机安装现场,取水不便,且对环境污染较大,而
且轴瓦检测工作量也不是太大,因此采用溶剂去除型着色探伤法喷罐式探伤剂较为适宜,其检验灵敏度完全可以保证检验质量。
3.3 检测实施
3.3.1 在检验工作前,先用铝合金试块或镀铬试块对渗透探伤剂和检测工艺进行检验。
3.3.2依照预清洗一施加渗透剂一清除表面多余渗透剂一施加显像剂一观察与评定的工作程序对轴瓦进行检测。
3.3.3 若轴瓦乌金复合层有开口性脱层缺陷存在,则接合线处将有明显的显示痕迹产生,可根据显示痕迹的颜色深浅大概判定为缺陷深度太小。
较深的脱层在擦去显示痕迹后再施加显像剂,仍然还可得到较为明显的显示迹痕,显示迹痕的长度即为开口性缺陷的长度。
3.4 超声波检测
3.4.1 轴瓦乌金复合层脱层缺陷是在乌金与基体结合面上平行于乌金表面的平面型缺陷。
由超声波检测原理可知,在进行超声波检测时应尽量使超声波垂直于缺陷表面,这时缺陷回波最高,检验灵敏度、准确率最好,目前常用的超声波探伤方法是纵波直探头法和双晶直探头法,检测面为乌金瓦表面。
3.4.2检测仪选用A型脉冲反射式超声波探伤仪。
由于脱层缺陷平行于乌金检测面,检测时选用纵波直探头。
双晶纵波直探头盲区小,检测灵敏度高,但其探测厚度有限,所以检测探头可选用单直探头探测轴瓦。
由于轴瓦乌金复合层质软易被较
硬物体划伤,宜选用软保护膜探头检验。
3.4.3晶片尺寸选定
由于支持轴承轴瓦的检测筒为弧形,曲率较大,为减小耦合损失,提高探伤耦合性能,要选用小晶片探头;另一方面,小晶片探头近场区小,盲区小,有利于轴瓦探测。
实践证明选用中10mm的探头较为适宜。
3.4.4 检测频率选择
检测频率高,则灵敏度和分辩力也高,并且指向性好。
但频率高时,近场区长度大,会造成盲区大,对探测不利。
所以在能保证探测灵敏度的前提下,要尽量选用较低的检测频率。
实践证明选用2.5~5MHz的检测频率较为适宜。
3.4.5 检测灵敏度的调节
轴瓦检测时,人工缺陷试块的制作较为复杂困难。
所以在轴瓦检测中,常利用轴瓦底波来调节检测灵敏度,如下图(a)所示。
单直探头探测以轴瓦底波等于满幅度的80再增益20dB作为检测灵敏度。
3.4.6 检测实施
依据检测程序对轴瓦进行100%的扫查,相邻两次扫查应有至少10%的重复扫查重叠区。
对于脱层缺陷的面积围使用6dB法(半波高度法)进行测定。
若有下列波型显示,则有脱层缺陷存在:①若无轴瓦底波,只有缺陷波多次相连,则该区域为完全脱层。
②若缺陷波多次相连,轴瓦底波下降,则该区域为不完全脱层。
4 结束语
4.1 渗透检测主要是检验轴瓦乌金复合层边缘开口性脱层缺陷、轴瓦乌金表面裂纹、气孔等缺陷,这也是制造和补焊轴瓦时最易产生的缺陷。
4.2超声波检测则是发现较深的边缘脱层和部脱层缺陷,其灵敏度高、准确性好,并且可以确定脱层的缺陷大小,但由于侧壁衍射等因素的影响,无法对轴瓦边缘的浅层缺陷进行准确的探测。
4.3在实际工作中,利用渗透检验和超声波检验的综合检验可全面地检测轴瓦质量,确保设备安全运行。