甲醇合成工艺常出现的问题及解决办法
甲醇合成过程中的问题及解决方法

甲醇合成过程中的问题及解决方法作者:柏小龙王海娟来源:《E动时尚·科学工程技术》2019年第07期摘要:甲醇是不可或缺的工业原料之一,在印染、医药、化工等方面的需求量很大。
目前甲醇的工艺流程都属于大同小异,要不断提高催化剂的活性,提高甲醇合成的效率。
文中分析了甲醇合成工藝过程,阐述了合成工艺过程的问题,提出了合成工艺过程的优化措施,为企业产出更多高精度的甲醇提供独到的见解。
关键词:甲醇;工艺流程;催化剂;解决方法1 甲醇合成工艺过程1.1 甲醇合成原理气体原料H2和CO在不相同的合成工艺和催化剂的作用下,产生一系列化学反应,包含甲醇合成的主反应和很多副反应,主反应的化学式为CO+2H2=CH3OH,标准焓变为ΔHθ298=-90.64kJ/mol;CO2+3H2=CH3OH+H2O,标准焓变为ΔHθ298=-49.45kJ/mol。
两个主反应的特点是都属于可逆反应、体积在反应中变小、放热反应,需要优质的催化剂增加甲醇合成的反应速度,更好的控制反应方向等一系列问题[1]。
影响甲醇合成化学反应的平衡有三个因素:在反应的过程中,根据化学反应平衡的一些理论,反应方向从CO和H2向合成甲醇的方向移动,需要不间断的往反应物中加入原料,同时不间断的取出甲醇。
合成甲醇的过程是一个可逆的放热反应,升高温度,反应方向向逆方向移动,同时反应温度提高副反应的数量也增多,为了保证甲醇的转化比例,时刻保持比较低的温度。
在甲醇的合成过程中是一个体积变小的过程,甲醇的压缩性比H2和CO的压缩性好,压力升高时,反应方向向正方向不断移动[2]。
综上所述,合成甲醇的反应中要在高压、低温的条件下进行,同时将活性较高的催化剂放置在高压和低温的条件下进行反应。
1.2 甲醇合成工艺流程合成甲醇工艺工程的种类特别多,工艺流程的线路比较长。
虽然工艺不同但是整体的流程差别不大,可以分为合成气的生成和净化的过程,制取粗甲醇、提纯粗甲醇的过程等[3]。
甲醇合成中常见故障及处理方法

甲醇合成中常见故障及处理方法发布时间:2021-06-10T11:04:34.307Z 来源:《中国科技信息》2021年7月作者:刘瑜1 魏汶辰2[导读] 工艺的运行状态对化工生产过程的可靠性及高效性起着决定性作用。
在甲醇合成工艺当中,合成系统的运行状态直接决定和最终产率的高低,此过程中一旦出现故障,就会对整个系统造成非常严重的影响,甚至导致系统全面瘫痪,且其加工制造难度大、周期长、价格昂贵,因此,甲醇合成塔使用状况良好与否至关重要。
1陕西省榆林市神木化学工业有限公司刘瑜1 7193192内蒙古鄂尔多斯市内蒙古中煤远兴能源化工有限公司魏汶辰2 017399摘要:工艺的运行状态对化工生产过程的可靠性及高效性起着决定性作用。
在甲醇合成工艺当中,合成系统的运行状态直接决定和最终产率的高低,此过程中一旦出现故障,就会对整个系统造成非常严重的影响,甚至导致系统全面瘫痪,且其加工制造难度大、周期长、价格昂贵,因此,甲醇合成塔使用状况良好与否至关重要。
关键词:甲醇合成;常见故障;处理方法引言甲醇是重要的化工材料,其生产及发展在我国国民经济中占据重要地位。
随着甲醇工艺的发展,甲醇合成塔应运而生。
甲醇合成塔为绝热管壳复合式,内部储存甲醇催化剂。
随着我国煤化工产业的不断发展,甲醇的单元产量不断增加,其核心设备甲醇合成塔的规格不断增大,对其设计、材料、制造及检修等各方面都提出了更高要求。
下面就甲醇合成塔常见故障及处理方法进行简要分析。
1甲醇合成塔常见故障1.1石蜡形成及带来的危害1.1.1对催化剂生产及使用过程中造成一定危害在甲醇合成的过程中,存在多种化学反应;(1)主反应: CO+2H2=CH3OH+QCO2+3H2=CH3OH+H2O+Q(2)副反应: 2CO+4H2=CH3OCH3+H2O+QCO+3H2=CH4+H2O+Q4CO+8H2=C4H9OH+3H2O+QCO2+H2=CO+H2O-QnCO+2nH2=(CH2)n+nH2O+Q当入塔气中H/C降低时有利于二甲醚生成,H/C=2.0时,二甲醚含量很快增加,当触媒中含有钾、钠等碱金属时会促进高级醇生成,合成气中CO含量过高时易与设备上的铁生成亚羟基铁。
关于煤制甲醇工艺问题的探讨
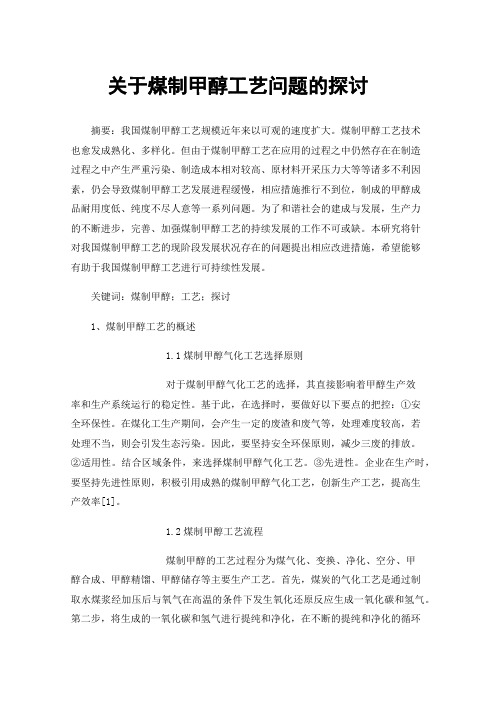
关于煤制甲醇工艺问题的探讨摘要:我国煤制甲醇工艺规模近年来以可观的速度扩大。
煤制甲醇工艺技术也愈发成熟化、多样化。
但由于煤制甲醇工艺在应用的过程之中仍然存在在制造过程之中产生严重污染、制造成本相对较高、原材料开采压力大等等诸多不利因素,仍会导致煤制甲醇工艺发展进程缓慢,相应措施推行不到位,制成的甲醇成品耐用度低、纯度不尽人意等一系列问题。
为了和谐社会的建成与发展,生产力的不断进步,完善、加强煤制甲醇工艺的持续发展的工作不可或缺。
本研究将针对我国煤制甲醇工艺的现阶段发展状况存在的问题提出相应改进措施,希望能够有助于我国煤制甲醇工艺进行可持续性发展。
关键词:煤制甲醇;工艺;探讨1、煤制甲醇工艺的概述1.1煤制甲醇气化工艺选择原则对于煤制甲醇气化工艺的选择,其直接影响着甲醇生产效率和生产系统运行的稳定性。
基于此,在选择时,要做好以下要点的把控:①安全环保性。
在煤化工生产期间,会产生一定的废渣和废气等,处理难度较高,若处理不当,则会引发生态污染。
因此,要坚持安全环保原则,减少三废的排放。
②适用性。
结合区域条件,来选择煤制甲醇气化工艺。
③先进性。
企业在生产时,要坚持先进性原则,积极引用成熟的煤制甲醇气化工艺,创新生产工艺,提高生产效率[1]。
1.2煤制甲醇工艺流程煤制甲醇的工艺过程分为煤气化、变换、净化、空分、甲醇合成、甲醇精馏、甲醇储存等主要生产工艺。
首先,煤炭的气化工艺是通过制取水煤浆经加压后与氧气在高温的条件下发生氧化还原反应生成一氧化碳和氢气。
第二步,将生成的一氧化碳和氢气进行提纯和净化,在不断的提纯和净化的循环过程中,使得生成的一氧化碳和氢气达到一定的纯度。
第三步,将一氧化碳和氢气按1:2比例进行甲醇的合成反应,控制相关工艺条件提高反应收率。
第四步,生成的甲醇进行精馏精制,将生成的粗甲醇在精馏塔内进行精馏处理,使粗甲醇达到国家规定的成品标准[2]。
2、煤制甲醇工艺存在的问题2.1在制造过程中存在严重污染煤制甲醇工艺在生产甲醇的过程之中,并不能够完全净化煤自身原本带有的污染性。
煤制甲醇合成工艺常见问题方法探究
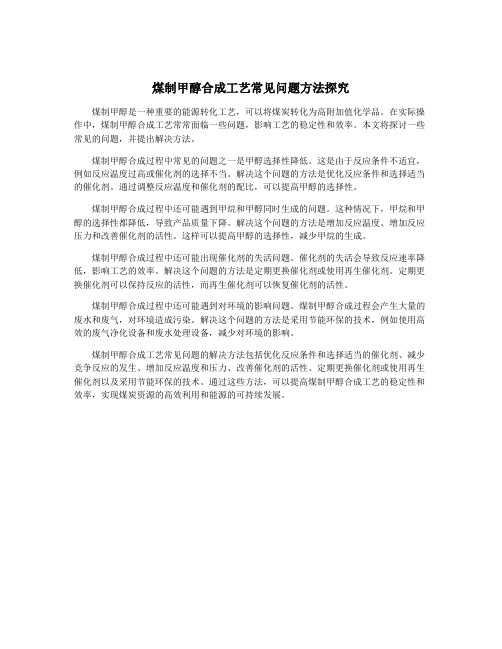
煤制甲醇合成工艺常见问题方法探究煤制甲醇是一种重要的能源转化工艺,可以将煤炭转化为高附加值化学品。
在实际操作中,煤制甲醇合成工艺常常面临一些问题,影响工艺的稳定性和效率。
本文将探讨一些常见的问题,并提出解决方法。
煤制甲醇合成过程中常见的问题之一是甲醇选择性降低。
这是由于反应条件不适宜,例如反应温度过高或催化剂的选择不当。
解决这个问题的方法是优化反应条件和选择适当的催化剂。
通过调整反应温度和催化剂的配比,可以提高甲醇的选择性。
煤制甲醇合成过程中还可能遇到甲烷和甲醇同时生成的问题。
这种情况下,甲烷和甲醇的选择性都降低,导致产品质量下降。
解决这个问题的方法是增加反应温度、增加反应压力和改善催化剂的活性。
这样可以提高甲醇的选择性,减少甲烷的生成。
煤制甲醇合成过程中还可能出现催化剂的失活问题。
催化剂的失活会导致反应速率降低,影响工艺的效率。
解决这个问题的方法是定期更换催化剂或使用再生催化剂。
定期更换催化剂可以保持反应的活性,而再生催化剂可以恢复催化剂的活性。
煤制甲醇合成过程中还可能遇到对环境的影响问题。
煤制甲醇合成过程会产生大量的废水和废气,对环境造成污染。
解决这个问题的方法是采用节能环保的技术,例如使用高效的废气净化设备和废水处理设备,减少对环境的影响。
煤制甲醇合成工艺常见问题的解决方法包括优化反应条件和选择适当的催化剂、减少竞争反应的发生、增加反应温度和压力、改善催化剂的活性、定期更换催化剂或使用再生催化剂以及采用节能环保的技术。
通过这些方法,可以提高煤制甲醇合成工艺的稳定性和效率,实现煤炭资源的高效利用和能源的可持续发展。
合成甲醇过程中结蜡的原因及预防处理措施

合成甲醇过程中结蜡的原因及预防处理措施甲醇是一种重要的化工原料,广泛应用于化学、医药、建材等领域。
而合成甲醇的工艺流程中,常会遇到结蜡现象,不仅降低了产量和质量,还会增加生产成本和操作难度。
因此,针对合成甲醇过程中结蜡的原因及预防处理措施进行深入研究具有重要意义。
一、合成甲醇过程中结蜡的原因1. 杂质的存在合成甲醇的原料中常含有各种杂质,例如硫、氧、硅等,这些杂质在反应过程中会导致甲醇过饱和和析出,使得产物结蜡。
同时,还会影响反应的速率和选择性,降低甲醇的产量和质量。
2. 温度的变化合成甲醇反应需要在一定的温度下进行,温度的变化会直接影响反应物质的平衡状态和固态化的温度点,从而导致产物结蜡。
此外,温度过高还会使得甲醇氧化成为二氧化碳和水,进一步降低产量和质量。
3. 压力的变化合成甲醇反应还需要在一定的压力条件下进行,压力的变化也会影响反应平衡状态和结蜡情况。
高压下容易产生结蜡现象,而低压下则不利于反应物的稳定性和流动性。
4. 催化剂的性质催化剂是合成甲醇过程中不可或缺的重要组成部分,其选择和使用也直接影响合成甲醇的质量和效率。
若催化剂的特性不匹配或活性过高,容易导致产物结蜡。
二、预防处理结蜡的措施1. 清除杂质合成甲醇的原料中含有的硫、氧、硅等杂质是结蜡的主要原因之一,因此必须进行严格的筛选和清除。
可以通过升华、蒸馏和干燥等方法进行降低杂质的含量,以保证原料的纯度。
2. 控制温度温度的控制是合成甲醇反应过程中防止结蜡的关键因素之一。
需要根据反应物的特性和反应条件进行合理的控制,不过度升高温度,避免产物过饱和和固态化。
3. 调节压力合成甲醇的反应需要在一定的压力范围内进行,成分和流动性不同的反应物有着不同的压力范围。
需要进行合理的压力选择和调节,尽可能减少结蜡现象的发生。
4. 优化催化剂催化剂的优化和使用是合成甲醇过程中提高产量和质量的关键因素之一。
可以通过选择合适的催化剂种类和控制催化剂的使用量和反应时间等方式,降低产物的结蜡情况。
煤制甲醇合成工艺常见问题方法探究

煤制甲醇合成工艺常见问题方法探究煤制甲醇是一种常用的化学合成方法,其工艺过程中会遇到一些常见问题。
本文将探讨一些常见问题,并提供解决方法。
1. 煤种选择问题:不同种类的煤对甲醇的产量和质量会有不同影响。
在选择煤炭原料时需要考虑煤的种类和质量,以确保甲醇的产量和质量达到预期目标。
可以通过实验室试验和前期工艺优化来确定最适合的煤种。
2. 煤气化问题:煤经过气化反应产生的合成气是合成甲醇的关键原料。
在煤气化过程中,常见的问题包括煤气化温度、气化剂选择、气化反应条件等。
通过优化气化反应条件可以提高煤气化效率和甲醇产率。
3. 合成催化剂选择问题:合成催化剂对甲醇的合成反应具有重要影响。
常见的催化剂包括氧化锌、铜锌、铝锌等。
在选择催化剂时需要考虑其活性、稳定性和抗毒性等因素。
可以通过实验室试验和工艺优化来选择最合适的催化剂。
4. 反应温度和压力问题:反应温度和压力是影响甲醇合成反应速率和反应平衡的重要因素。
合适的反应温度和压力可以提高甲醇产率和减少副产品的生成。
通过实验室试验和工艺优化可以确定最佳的反应温度和压力条件。
5. 催化剂失活问题:由于反应条件的变化和催化剂的使用,催化剂可能会失活。
常见的催化剂失活原因包括颗粒堵塞、催化剂中毒和烧结等。
对于催化剂的失活问题,可以采取适当的催化剂再生和更换方法来恢复催化剂的活性。
6. 产品分离和净化问题:合成甲醇反应产生的气相和液相产物需要进行分离和净化。
常见的问题包括气液分离、除水、除杂质等。
可以通过蒸馏、吸附、膜分离等方法来进行产品的分离和净化。
煤制甲醇工艺中常见的问题包括煤种选择、煤气化、催化剂选择、反应温度和压力、催化剂失活以及产品分离和净化等。
通过适当的材料选择、反应条件优化和工艺改进,可以解决这些问题,提高甲醇的产率和质量。
需要进行系统的实验和工程验证,以确保工艺稳定和可行性。
合成工段问题处理 甲醇生产
处理方法: 1 增加循环量; 2 调节汽包压力值之恢复正常值, 必要时可加大排污量或用调整循环 量的办法使温度降下来,如果出现 干锅应立即采取果断措施,以免事 故扩大;
原因分析: 1 生产负荷过大 2 催化剂活性下降 3 氢碳比高 4 循环气惰性组分高 5 垮温
处理方法: 1 2 3 4 5
调整负荷 降负荷或停车处理 调整新鲜气组分 增加弛放气的排放量 减量生产或重新升温
原因分析: 1 分离器分离效果差 2 水冷器水冷效果差 3 负荷过大 4 分离器液位过高
3 与前系统联系,使CO含量调整至正常 值,并适当增加H2/CO比与惰性气含 量,使温度尽快恢复正常; 4 及时调整循环量或汽包压力,使之与 负荷相适应; 5 精心操作,细心调节各工艺参数,尽 量避免波动过大; 6 根据床层温升情况,适当降低系统压 力,必要时卸掉合成压力按紧急停车 事故处理。
原因分析: 1 循环量突然增加; 2 汽包压力下降; 3 新鲜气组成发生变化,CO含量降 低,总硫含量超标;
4 甲醇分离器液位高或假液位使得大量 甲醇带入合成塔; 5 操作失误,调节幅度过大。 处理方法: 1 适当减少循环量; 2 提高汽包压力,使之恢复正常值; 3 与前系统联系,调整气体成分,使CO 含量恢复正常指标,如果总硫超标, 切断气源,待分析合格后再导气;
4 应开大甲醇放出阀,使液位恢复 正常,同时减少循环量,控制温度, 用塔后放空控制系统压力不得超压, 联系仪表检查连锁与液位指示; 5 精心操作,细心调节各工艺参数, 尽量避免波动过大。
谢谢!!
煤制甲醇合成工艺常见问题方法探究
煤制甲醇合成工艺常见问题方法探究煤制甲醇是一种重要的合成工艺,由于煤资源丰富且分布广泛,因此煤制甲醇具有很大的应用前景。
在实际生产中,煤制甲醇合成工艺常常会遇到一些问题,这些问题可能会影响甲醇的质量和产量,甚至会导致生产过程中的安全事故。
探究煤制甲醇合成工艺常见问题的方法,对于保障生产的稳定性和提高生产效率具有非常重要的意义。
一、煤制甲醇合成工艺常见问题及其原因1. 甲醇产率低甲醇产率低是煤制甲醇合成工艺中常见的问题之一。
这可能是由于催化剂失活、反应器内部污染、反应条件不合适等多种原因造成的。
2. 甲醇质量不稳定在煤制甲醇合成过程中,甲醇的质量不稳定也是一个常见问题。
这可能会导致产品质量不达标、无法满足市场需求。
3. 能源消耗高煤制甲醇合成工艺涉及到大量的能源消耗,如果能源消耗过高会导致生产成本增加,降低企业的竞争力。
1. 提高催化剂的稳定性和活性催化剂是煤制甲醇合成工艺中至关重要的一环,催化剂的稳定性和活性直接影响到甲醇的产率和质量。
提高催化剂的稳定性和活性是解决甲醇产率低和质量不稳定的关键。
在实际生产中,可以通过改进催化剂的制备工艺、提高催化剂的结构稳定性等方法来提高催化剂的稳定性和活性。
及时清理和更换失活的催化剂也是保障甲醇产率和质量的重要手段。
2. 加强反应器内部的清洁和维护反应器是煤制甲醇合成工艺中的核心设备,反应器内部的污染和积碳会严重影响甲醇的产率和质量。
加强反应器内部的清洁和维护是保障甲醇产率和质量的重要方法。
在生产中,可以定期对反应器进行清洁、维护和检修,及时清除污物和积碳,保持反应器内部的清洁状态,以确保甲醇的产率和质量。
3. 优化反应条件反应条件的优化对于提高甲醇产率和质量具有非常重要的意义。
在生产实践中,可以通过调整反应温度、压力、催化剂用量、气体流速等参数,优化反应条件,提高甲醇的产率和质量。
合理选择反应器的类型和结构,优化反应器的工艺流程也是提高甲醇产率和质量的有效途径。
煤制甲醇合成工艺常见问题方法探究
煤制甲醇合成工艺常见问题方法探究煤制甲醇是一种重要的化工工艺,通过将煤气化产物气体转化成甲醇,可以充分利用煤炭资源,减少对石油等非可再生能源的依赖。
煤制甲醇工艺常见问题的解决对于提高工艺的稳定性和经济效益具有重要意义。
本文将从煤制甲醇合成工艺的常见问题出发,探讨解决方法,为工程技术人员提供参考和借鉴。
煤制甲醇合成工艺常见问题之一是催化剂失活。
催化剂在长时间的运行中会发生失活现象,主要是由于催化剂表面积和活性位点的减少,导致反应活性降低。
解决方法可以通过提高反应器的操作温度和压力,以增加催化剂表面积和活性位点的利用率;定期进行催化剂再生和更换,恢复催化剂的活性。
还可以通过改进催化剂的配方和制备工艺,提高催化剂的稳定性和耐受性,延长其使用寿命。
煤制甲醇合成工艺常见问题之二是产物纯度不稳定。
甲醇是一种重要的有机化工产品,其纯度对于下游产品的质量影响极大。
产物纯度不稳定可能导致产品质量不稳定,影响工艺的经济效益。
解决方法可以通过优化反应器的操作条件,如温度、压力和进料气体比例,以提高产物的选择性和纯度;采用离心分离、蒸馏和结晶等方法对产物进行精制,去除杂质,提高产品的纯度和稳定性。
煤制甲醇合成工艺常见问题之三是催化剂的选择和制备。
催化剂的选择和制备直接关系到工艺的效率和成本。
不同的催化剂对于甲醇合成的活性和选择性有着不同的影响,选用合适的催化剂对于提高工艺的稳定性和产物的纯度至关重要。
解决方法可以通过对不同催化剂的活性和选择性进行评价,选择最适合的催化剂;优化催化剂的制备工艺,控制催化剂的晶粒大小和分布,提高催化剂的活性和稳定性。
煤制甲醇合成工艺常见问题之四是再循环气体的处理。
甲醇合成过程中产生的再循环气体含有大量的杂质和有害物质,需要进行处理和回收利用。
再气体的处理对于降低生产成本和减少环境污染具有重要意义。
解决方法可以通过采用吸附、膜分离和化学吸收等方法对再气体进行处理,去除其中的二氧化碳、硫化物和氨等有害物质,回收其中的甲醇和氢气,提高资源利用率和环境友好度。
煤制甲醇合成工艺常见问题方法探究
煤制甲醇合成工艺常见问题方法探究煤制甲醇合成工艺是一种将天然煤气转化为甲醇的重要工艺,能够实现对煤炭资源的高效利用,并为我国能源结构的调整提供有力支撑。
在实际生产中,煤制甲醇合成工艺也存在着一些常见问题,比如低转化率、高能耗、催化剂寿命短等。
本文将就煤制甲醇合成工艺的常见问题进行探究,并提出相应的解决方法。
1. 低转化率低转化率是煤制甲醇合成工艺中常见的问题之一。
主要体现在煤气转化率低、甲醇产率不高等方面。
造成这一问题的原因有很多,比如反应条件不合适、催化剂活性不高、废气回收不完善等。
解决方法:(1)调整反应条件:通过调整反应温度、压力、催化剂种类和质量等参数,改变反应条件,提高反应的效率和产率。
(2)改进催化剂:研发新型高效催化剂,增加催化剂的活性和稳定性,提高反应的选择性和转化率。
(3)完善废气回收系统:合理设计废气回收系统,充分利用废气中的可回收物质,减少资源的浪费,提高反应的综合利用率。
2. 高能耗煤制甲醇合成工艺的能耗问题一直备受关注。
高能耗不仅加大了生产成本,也给环境造成了一定的负担。
造成高能耗的原因主要包括设备老化、工艺不合理、能源利用不合理等。
解决方法:(1)更新设备:及时更换老化的设备,采用新型高效节能设备,提高生产效率,降低能耗。
(2)优化工艺:通过工艺优化,减少不必要的能源消耗,提高能源利用效率,降低生产成本。
(3)综合利用能源:利用余热余压等废能源,进行能源综合利用,降低能耗,减少资源浪费。
3. 催化剂寿命短催化剂寿命短是煤制甲醇合成工艺的另一个常见问题。
催化剂的寿命直接影响了生产成本和工艺稳定性,所以延长催化剂寿命一直是工艺改进的重点。
解决方法:(1)改进催化剂制备工艺:优化催化剂的制备工艺,提高催化剂的稳定性和活性,延长催化剂的寿命。
(2)改进反应条件:通过调整反应条件,减少催化剂的热变形和失活,延长催化剂的使用寿命。
(3)改进废物处理方式:合理处理反应废物,减少对催化剂的污染,延长催化剂的寿命。
- 1、下载文档前请自行甄别文档内容的完整性,平台不提供额外的编辑、内容补充、找答案等附加服务。
- 2、"仅部分预览"的文档,不可在线预览部分如存在完整性等问题,可反馈申请退款(可完整预览的文档不适用该条件!)。
- 3、如文档侵犯您的权益,请联系客服反馈,我们会尽快为您处理(人工客服工作时间:9:00-18:30)。
2.3 结蜡问题
任何甲醇生产(高压法、中压法、低压法)的 大中小型的单醇或联醇装置都存在着不可避 免的或多或少的蜡生成的现象。石蜡是多种 高级烷烃的混合物,即脂肪烃类,分子式为 CnH2n+2,比重0.786~0.800。低压法甲醇 装置生成蜡状物以C18~C20为主,中压法 蜡状物以C20~C25为主,高压法蜡状物以 C35~C42。C18-C20蜡质熔点75~80℃。以 H2和CO为原料,使用不同催化剂或同一种
的主要方法是排放粗甲醇分离器后的气。
目前许多单位为了减少甲醇合成有效气体 CO、H2的损失,采用氢回收的方法,对甲 醇合成粗甲醇分离器后的放空气进行氢气 回收,回收放空气中的氢气后然后做为燃 料气供其它工序使用。如果循环气中惰性 气体含量比较高,此时可以适当增大氢回 收的量,待惰性气体含量降低后再适当减 小氢回收的量,以免造成过多甲醇合成有 效气体CO、H2的损失。
而影响甲醇的精馏及精甲醇的产品质量。一般 而言,氢碳比控制太低,副反应增加,催化剂 活性衰退加快,还容易引起积碳反应;氢碳比 控制太高,影响产量并引起能耗等消耗定额增 加。
2.1.3 氢碳比失调后的处理方法
由氢碳比的公式可以看出,影响氢碳比的主要 因素是合成气中H2、CO2、CO的含量,而合 成气中CO2的含量是由净化工序决定的,其通 常相对较为稳定,一般控制在2.5%~3.0%
从反应式可以看出,H2与CO合成甲醇的物 质量比为2:1,与CO2合成CH3OH的物质 量比为3:1,当CO与CO2 都有时,对原料 气中氢碳比(f)用以下表达方法表示:
f=(H2-CO2)/(CO+CO2)=2.05~2.15
2.1.2 氢碳比失调的危害
氢碳比在2.05~2.15之间,对甲醇合成反应 最为有利。当氢碳比偏离这个指标时,不 仅会影响甲醇合成反应的进行,影响甲醇 的产量;而且还会造成副反应的增多,进
调节CO含量的副线,此时可以采用调节CO 含量的副线进行调节,如果没有调节CO含量 的副线,此时可以通过调节水汽比的方法 (具体就是调节添加蒸汽的流量)进行调节。 调节时要缓慢,防止出现大起大落的情况。
2.2 循环气中惰性气体含量高
2.2.1 循环气中惰性气体含量高的危害
循环气中的惰性气体通常为甲烷、氮气及氩。 这些气体不参与甲醇合成的反应,但会在合 成系统中逐渐积累而增多。循环气中的惰性 气体的增多会降低CO、CO2、H2的有效分
催化剂在不同工艺条件下(温度、压力、气 体成分),会生成不同的产品。
2.3.1 结蜡产生的原因
2.3.1.1 Fe(C0)5、Ni(C0)4 及少量Mo(CO)4是 生成CH4的催化剂。它们的存在使反应急剧 放热,对催化剂有害,同时生成会少量高级 烷烃类蜡质。当系统有过多铁锈杂质时,在 130~150℃可生成Fe(C0)5 。Fe(C0)5 易挥发 成气态的物质,随着工艺气进入催化剂,在 250℃下分解成元素铁,进而堵塞催化剂微 孔使之过早失活。
压,对CH3OH的合成不利,影响粗甲醇产量, 而且增加了压缩机的动力消耗。但在系统中 又不能排放过多,否则会引起有效气体的大 量损失 。
2.2.2 循环气中惰性气体含量高的处理办法
惰性气体的含量一般控制原则为:在催化剂 使用初期活性较好,或者合成塔的负荷较轻、 操作压力较低时,可将循环气中的惰性气体 含量控制在20% ~25%左右,反之控制在15 % ~20%左右。控制循环气中惰性气体含量
主讲:陈玉民 2020年6月21日
来自净化工序的总硫含量小于0.1ppm, (H2-CO2)/(CO+CO2)=2.05-2.15的新 鲜气,与循环气压缩机加压后的循环气在缓 冲罐混合,出缓冲罐的混合气进入入塔气 预热器的壳程,被来自合成塔反应后的出 塔热气体加热至约225℃后,进入合成塔顶 部。
合成塔为立式绝热——管壳型反应器。
管内装有低压甲醇合成催化剂。当合成气 进入催化剂床层后,在5.3MPa、220~
260℃下,CO、CO2与H2反应生成甲醇和微 量的水,同时还有微量的其他有机杂质生成。 合成甲醇的两个主反应都是强放热反应,反 应释放出的热量大部分由合成塔壳程的沸腾 水带走。通过控制汽包压力来控制催化剂床 层温度及合成塔出口温度。从合成塔出来的 热反应气进入入塔气预热器的管程与入塔合 成气逆流换热,被冷却到90℃左右,此时有 一部分甲醇被冷凝成液体。该气液混合物再 经甲醇水冷器进一步冷凝,然后进入甲醇分 离器分离出粗甲醇。
分离出粗甲醇后的气体,压力约为4.8MPa~ 5.0MPa,温度约为40℃,返回甲醇循环气压 缩机,经加压后送至油分离器分离油水,分 离油水后的循环气送至缓冲罐。为了防止合 成系统中惰性气体的积累,要连续从系统中 排放少量的气体。这部分弛放气经水洗塔洗 涤甲醇后送氢回收系统回收氢气,整个合成 系统的压力由调节阀来控制。
2.3.1.2 甲醇合成气中含有少量H2S,它们会 对管道及设备腐蚀产生铁锈,铁锈的存在促 使羰基化反应的发生。原始开车前系统吹扫 不彻底,设备及管道留下的残余的铁锈会加 速羰基化反应的发生,生成Fe(C0)5、 Ni(C0)4 及少量Mo(CO)4,进而促使结蜡反 应的进行。
由甲醇分离器分离出的粗甲醇,进入甲 醇膨胀槽进行减压闪蒸,以除去溶解在粗甲 醇中的大部分气体,然后送往粗甲醇储罐。
甲醇膨胀槽的压力控制在0.4MPa。膨胀气送 往燃料气管网。水洗塔塔底排出的粗甲醇也 排至甲醇膨胀槽中。 2甲醇合成工艺常出现的问题 2.1氢碳比失调 2.1.1氢碳比的定义及指标 甲醇是由CO、CO2和H2反应生成,反应式如 下: CO+2H2=CH3OH CO2+3H2=CH3OH+H2O
之间较为适宜;而合成气中CO的含量是由 变换工序来控制的,许多变换工艺设置有 专门调节CO含量的副线,变换出口CO一 般控制在20%左右。甲醇合成的氢碳比一 般通过调节变换出口CO的含量来调节氢碳 比,而净化工序的CO2含量相对较为稳定, 不作为氢碳比的调节手段。甲醇合成工序 一旦发现氢碳比偏离了工艺指标之后,要 及时与变换工序联系(一般是通过生产调 度进行联系),变换工序的操作人员要根 据情况及时进行调整,如果变换工艺有专