冶金炉热平衡
重有色冶金炉窑热平衡的测定与计算方法
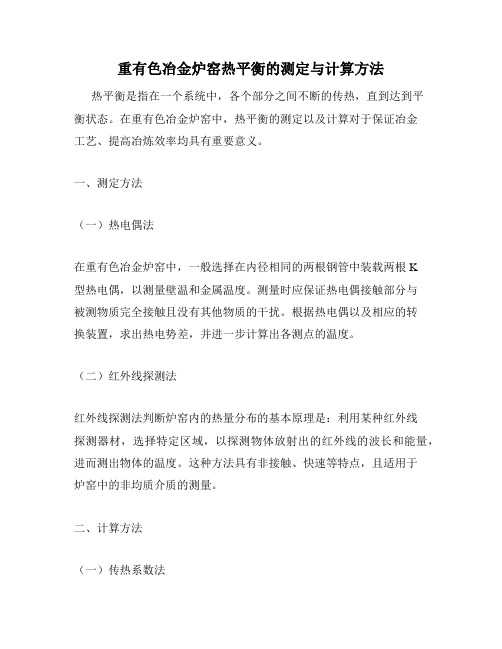
重有色冶金炉窑热平衡的测定与计算方法热平衡是指在一个系统中,各个部分之间不断的传热,直到达到平
衡状态。
在重有色冶金炉窑中,热平衡的测定以及计算对于保证冶金
工艺、提高冶炼效率均具有重要意义。
一、测定方法
(一)热电偶法
在重有色冶金炉窑中,一般选择在内径相同的两根钢管中装载两根K
型热电偶,以测量壁温和金属温度。
测量时应保证热电偶接触部分与
被测物质完全接触且没有其他物质的干扰。
根据热电偶以及相应的转
换装置,求出热电势差,并进一步计算出各测点的温度。
(二)红外线探测法
红外线探测法判断炉窑内的热量分布的基本原理是:利用某种红外线
探测器材,选择特定区域,以探测物体放射出的红外线的波长和能量,进而测出物体的温度。
这种方法具有非接触、快速等特点,且适用于
炉窑中的非均质介质的测量。
二、计算方法
(一)传热系数法
重有色冶金炉窑中能量的收支可按照如下方法计算:Q=Q1+Q2,其中
Q表示能量收支平衡;Q1表示辐射和传导各个方向上的净传热量之和;Q2表示物料反应带来的净热释放量。
其中,Q1的计算需要涉及到传热系数的计算。
(二)基于数学模型的计算
数学建模是最通用、最迅速的方法之一,它可以通过一组方程式描述
系统,并采用有理机构进行研究。
通过对炉窑内传热方程式的建模,
可以获得整个炉窑内的温度场分布等信息。
综上所述,尽管不同的测定方法和计算方法有各自的不同优势与适用
范围,但在实际应用中,我们应根据具体的炉窑条件和需要,选择合
适的方法进行热平衡的测定和计算,进而更好地实现重有色冶金的高效、安全、可靠的生产。
富氧侧吹熔池熔炼炉冶金炉窑热平衡的测定与计算

富氧侧吹熔池熔炼炉冶金炉窑热平衡的测定与计算富氧侧吹熔池熔炼炉冶金炉窑热平衡的测定与计算一、引言富氧侧吹熔池熔炼炉是炼钢过程中常用的设备,其热平衡的测定与计算对于炉冶金炉窑的操作和生产至关重要。
本文将对富氧侧吹熔池熔炼炉冶金炉窑热平衡的测定与计算进行深入探讨,并分享个人观点和理解。
二、富氧侧吹熔池熔炼炉的热平衡1. 热平衡的概念富氧侧吹熔池熔炼炉的热平衡是指在冶炼过程中炉内各部分热量的平衡状态。
熔炼炉内存在着多种热量的流动和转换,如化学热、辐射热、对流热等,而热平衡即是在这些热量之间达到平衡状态,确保炉内温度和热量的稳定。
2. 热平衡的测定与计算要准确测定和计算富氧侧吹熔池熔炼炉的热平衡,需要考虑炉内各部分的热量输入和输出。
首先是炉料和燃料的热量输入,其次是废气和废渣的热量输出,还需要考虑炉壁和炉底的热量损失等。
通过对这些因素的测定和计算,可以得出炉内热平衡的状态,有助于调整冶炼过程,提高炉窑热效率。
三、富氧侧吹熔池熔炼炉的热平衡测定方法1. 热量输入的测定炉料和燃料的热量输入是熔炼过程中最主要的能量来源,其测定是热平衡计算的关键。
可以通过测定燃料的热值和炉料的热容来计算其输入的热量,确保炉内能量充足,保证冶炼过程的稳定进行。
2. 热量输出的测定废气和废渣的热量输出是熔炼炉的热平衡中的重要组成部分。
通过测定废气和废渣的温度、流量等参数,可以计算其带走的热量,进而更好地控制炉内热平衡状态。
3. 热量损失的估算在熔炼炉的运行过程中,热量损失是不可避免的。
炉壁和炉底的散热、辐射热等都会导致热量的损失。
通过对炉壁和炉底的材料和结构进行分析,可以估算热量损失,从而更好地维持炉内热平衡。
四、热平衡的重要性及个人观点热平衡的合理测定和计算对于富氧侧吹熔池熔炼炉的生产和操作至关重要。
只有保持炉内的热平衡状态,才能确保熔炼过程的稳定性和高效性。
通过有效地测定和计算热平衡,可以更好地控制熔炼过程,提高冶金炉窑的生产效率和质量。
冶炼热平衡计算
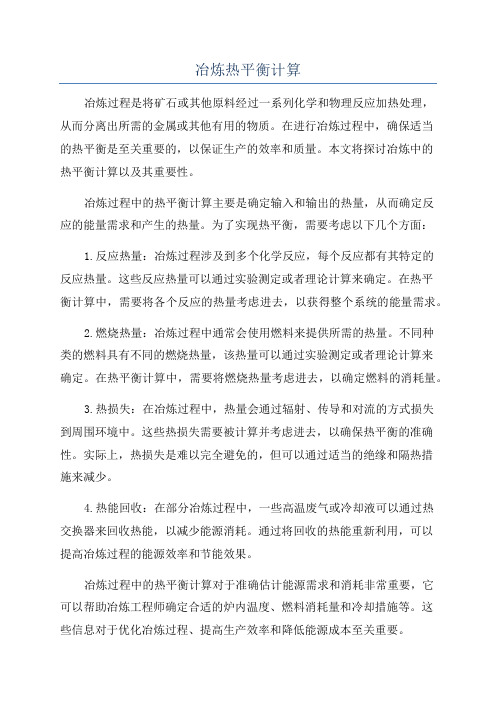
冶炼热平衡计算冶炼过程是将矿石或其他原料经过一系列化学和物理反应加热处理,从而分离出所需的金属或其他有用的物质。
在进行冶炼过程中,确保适当的热平衡是至关重要的,以保证生产的效率和质量。
本文将探讨冶炼中的热平衡计算以及其重要性。
冶炼过程中的热平衡计算主要是确定输入和输出的热量,从而确定反应的能量需求和产生的热量。
为了实现热平衡,需要考虑以下几个方面:1.反应热量:冶炼过程涉及到多个化学反应,每个反应都有其特定的反应热量。
这些反应热量可以通过实验测定或者理论计算来确定。
在热平衡计算中,需要将各个反应的热量考虑进去,以获得整个系统的能量需求。
2.燃烧热量:冶炼过程中通常会使用燃料来提供所需的热量。
不同种类的燃料具有不同的燃烧热量,该热量可以通过实验测定或者理论计算来确定。
在热平衡计算中,需要将燃烧热量考虑进去,以确定燃料的消耗量。
3.热损失:在冶炼过程中,热量会通过辐射、传导和对流的方式损失到周围环境中。
这些热损失需要被计算并考虑进去,以确保热平衡的准确性。
实际上,热损失是难以完全避免的,但可以通过适当的绝缘和隔热措施来减少。
4.热能回收:在部分冶炼过程中,一些高温废气或冷却液可以通过热交换器来回收热能,以减少能源消耗。
通过将回收的热能重新利用,可以提高冶炼过程的能源效率和节能效果。
冶炼过程中的热平衡计算对于准确估计能源需求和消耗非常重要,它可以帮助冶炼工程师确定合适的炉内温度、燃料消耗量和冷却措施等。
这些信息对于优化冶炼过程、提高生产效率和降低能源成本至关重要。
在热平衡计算中,可以使用各种数学模型和计算工具。
其中最常用的是热平衡计算软件,这些软件通常基于物理和化学原理构建模型,并使用数值计算方法来求解热平衡方程。
通过输入相关参数和反应热量,软件可以计算出热平衡所需的热量输入和输出,从而确定冶炼过程的热平衡状态。
总之,热平衡计算在冶炼过程中具有重要的意义。
它可以帮助冶炼工程师确定冶炼过程所需的热量输入和燃料消耗量,并提供合理的温度控制和热能回收方案。
行业标准《重有色冶金炉窑热平衡测定与计算方法(吹炼转炉)》编制说明
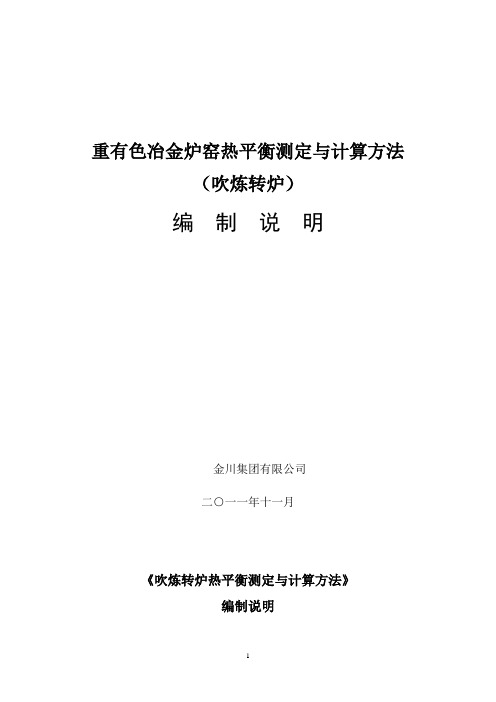
重有色冶金炉窑热平衡测定与计算方法(吹炼转炉)编制说明金川集团有限公司二○一一年十一月《吹炼转炉热平衡测定与计算方法》编制说明1、工作简况1.1 任务来源根据中国有色金属协会以有色标委会[2010]21号文件下达的标准编制任务,其中附件1《2010年第一批有色金属行业标准项目计划表》计划编号为2010-0497T-YS,《重有色冶金炉窑热平衡测定与计算方法(吹炼转炉)》行业标准由金川集团有限公司负责起草修订。
1.2 主要工作过程2010年3月至2010年5月开展国内外调研、资料收集和方案制定;2010年6月开始测试准备工作;2010年8月完成铜转炉和镍转炉生产现场热平衡测试;2011年4月形成标准讨论稿;2011年5月全国“有色重标委”组织专家对标准进行了讨论,并形成改进意见;2011年9月完成标准送审初稿,金川集团公司专家初审,形成修改意见;2011年10月由金川集团公司和中南大学共同进行专家评审,并提出改进意见;2011年11月提出标准送审稿。
2、标准的编制和修改原则2.1 修订理由卧式转炉主要用于有色冶金生产中处理铜锍或低镍锍,产品为粗铜或高镍锍。
伴随冶金技术和装备水平的提升,转炉热平衡测定标准也需要加以完善,以满足生产实际的要求。
通过热平衡标准的修定,为进一步制定能耗定额标准或能耗分级标准打下基础,促进企业的节能改造和科研机构的技术创新。
2.2 编制原则1)以GB/T 13338作为编制的基础。
2)编制中充分考虑了国内行业发展的现状,综合考虑了炉型、工艺原理和耗能情况。
3)依据镍闪速熔炼炉的特点,规定具体的体系划分和考核范围、工艺参数基准、测试项目和测试方法,以及当无法测量时的理论计算方法等。
4)编制中充分考虑到实际操作中会出现具体问题的处理方法,编制人员大多来自生产一线,实现了理论与实际的结合,保证其可操作性。
5)编制中充分考虑到不但能反映出能耗的高低,更利于找出能耗高低的原因和途径。
转炉物料平衡与热平衡计算.
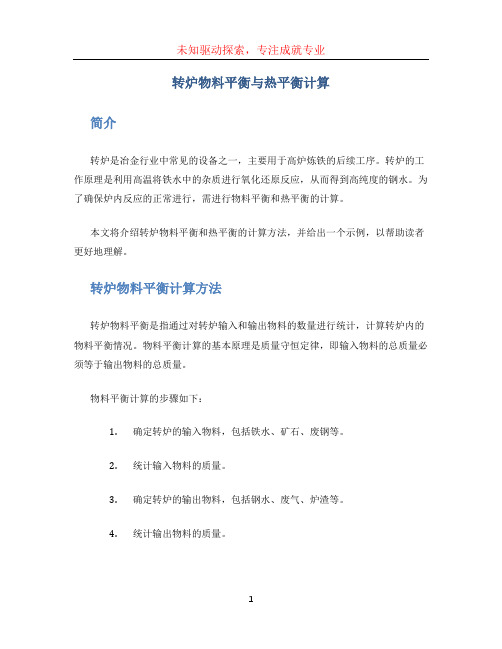
转炉物料平衡与热平衡计算简介转炉是冶金行业中常见的设备之一,主要用于高炉炼铁的后续工序。
转炉的工作原理是利用高温将铁水中的杂质进行氧化还原反应,从而得到高纯度的钢水。
为了确保炉内反应的正常进行,需进行物料平衡和热平衡的计算。
本文将介绍转炉物料平衡和热平衡的计算方法,并给出一个示例,以帮助读者更好地理解。
转炉物料平衡计算方法转炉物料平衡是指通过对转炉输入和输出物料的数量进行统计,计算转炉内的物料平衡情况。
物料平衡计算的基本原理是质量守恒定律,即输入物料的总质量必须等于输出物料的总质量。
物料平衡计算的步骤如下:1.确定转炉的输入物料,包括铁水、矿石、废钢等。
2.统计输入物料的质量。
3.确定转炉的输出物料,包括钢水、废气、炉渣等。
4.统计输出物料的质量。
5.比较输入物料的总质量和输出物料的总质量,若两者相等,则物料平衡成立;若不相等,则存在物料的损失或增加。
下面以一个具体的例子来说明转炉物料平衡的计算过程。
假设一个转炉的输入物料包括1000kg的铁水、200kg的矿石和100kg的废钢。
经过转炉反应后,得到800kg的钢水、400kg的废气和100kg的炉渣。
通过统计计算,我们可以得到输入物料的总质量为1000kg + 200kg + 100kg = 1300kg,输出物料的总质量为800kg + 400kg + 100kg = 1300kg。
两者相等,说明物料平衡成立。
转炉热平衡计算方法转炉热平衡是指通过对转炉内的能量输入和输出进行统计,计算转炉的热平衡情况。
热平衡计算的基本原理是能量守恒定律,即输入能量的总量必须等于输出能量的总量。
热平衡计算的步骤如下:1.确定转炉的输入能量,包括燃料的热值、还原剂的热值等。
2.统计输入能量的总量。
3.确定转炉的输出能量,包括钢水的热值、废气的热值等。
4.统计输出能量的总量。
5.比较输入能量的总量和输出能量的总量,若两者相等,则热平衡成立;若不相等,则存在能量的损失或增加。
5冶金炉热能的合理利用
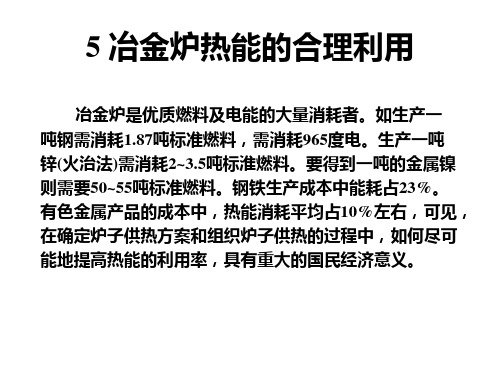
5.1 炉子能源的合理选择
确定冶金炉能源时,应从以下原则出发: (1) 满足工艺过程技术上的要求:如温度水平, 杂质含量,温度控制的精确程度等; (2) 从能源生产、输送及使用各个过程出发,保 证最高的热利用率(称为能量总利用率); (3) 国家资源的综合利用; (4) 减轻劳动强度,便于操作的机械化和自动化。
•
4、越是无能的人,越喜欢挑剔别人的 错儿。 02:00:4 302:00: 4302:0 0Wednesday, September 09, 2020
炉子的热平衡可以用图形表示出来(如图5—2)。
2、燃料的节约
节约燃料的一些基本途径:即提高空气(及煤气) 的预热温度,提高燃料的发热量,改善燃料和传热 条件以减少废气带走的热量,减少炉子的热损失, 确定合理的热负荷等。
A、余热回收
炉尾废气带走的热量,一般占热平衡支出的 40~50%,充分利用这部分热量有巨大的潜力。首 先应该用来预热空气或煤气(或炉料)将这部分热量 回收到炉内,其次才生产蒸汽或其它用途。
•
1、有时候读书是一种巧妙地避开思考 的方法 。20.9. 920.9.9 Wedne sday, September 09, 2020
•
2、阅读一切好书如同和过去最杰出的 人谈话 。02:0 0:4302: 00:4302 :009/9/ 2020 2:加自命不凡。 20.9.90 2:00:43 02:00S ep-209-Sep-20
把炉膛作为一个区域。凡进入这个 区域的热量都是炉膛的热收入,而离开 的都是热支出(参看图5—1)。这样得到 的热平衡,便是炉膛热平衡,它是炉子 备区域热平衡中最主要的一环
如果忽略物料在炉内的放热或吸热反 应,通常火焰炉炉膛热平衡包括以下各 项:
物料平衡 热平衡 转炉
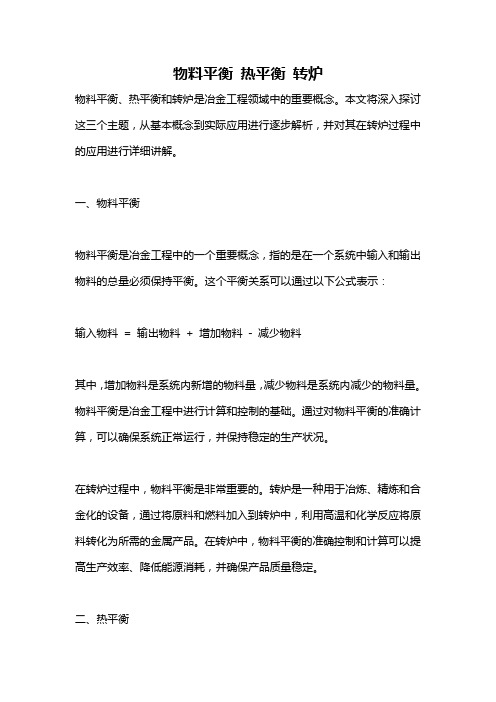
物料平衡热平衡转炉物料平衡、热平衡和转炉是冶金工程领域中的重要概念。
本文将深入探讨这三个主题,从基本概念到实际应用进行逐步解析,并对其在转炉过程中的应用进行详细讲解。
一、物料平衡物料平衡是冶金工程中的一个重要概念,指的是在一个系统中输入和输出物料的总量必须保持平衡。
这个平衡关系可以通过以下公式表示:输入物料= 输出物料+ 增加物料- 减少物料其中,增加物料是系统内新增的物料量,减少物料是系统内减少的物料量。
物料平衡是冶金工程中进行计算和控制的基础。
通过对物料平衡的准确计算,可以确保系统正常运行,并保持稳定的生产状况。
在转炉过程中,物料平衡是非常重要的。
转炉是一种用于冶炼、精炼和合金化的设备,通过将原料和燃料加入到转炉中,利用高温和化学反应将原料转化为所需的金属产品。
在转炉中,物料平衡的准确控制和计算可以提高生产效率、降低能源消耗,并确保产品质量稳定。
二、热平衡热平衡是指系统中输入和输出的热量必须保持平衡。
一个系统中的热平衡可以通过以下公式表示:输入热量= 输出热量+ 产生热量- 消耗热量其中,产生热量是系统内产生的热量,消耗热量是系统内消耗的热量。
热平衡的准确计算和控制是保证系统正常运行和能量效率的关键。
在转炉过程中,热平衡是非常重要的。
在转炉内,燃料燃烧产生的热量被用于原料的冶炼、精炼和合金化。
同时,热量还会通过系统的一些其他途径(如散热、冷却等)被消耗。
通过准确计算和控制热平衡,可以提高能源利用率,降低能源消耗,确保系统高效稳定地运行。
三、转炉转炉是一种非常重要的冶金设备,广泛应用于钢铁和有色金属冶炼工业中。
通过转炉,原料和燃料被加入到设备中,利用高温和化学反应将原料转化为所需的产品。
在转炉过程中,物料平衡和热平衡是两个非常重要的概念。
通过准确计算和控制物料平衡,可以确保输入和输出物料的平衡,保证生产过程的稳定性和产品质量的一致性。
通过准确计算和控制热平衡,可以提高能源利用率,降低能源消耗,保证系统的高效运行。
电炉普通铁合金冶炼过程中热平衡分析与调控

电炉普通铁合金冶炼过程中热平衡分析与调控热平衡是电炉普通铁合金冶炼过程中关键的参数之一。
合理控制冶炼过程的热平衡可以确保铁合金的质量,提高冶炼效率和能源利用率。
本文将通过对电炉普通铁合金冶炼过程中热平衡进行分析,并探讨如何调控热平衡,从而提高铁合金的生产效益。
在电炉普通铁合金冶炼过程中,热平衡是指冶炼系统中热量的输入和输出之间的平衡状态。
一个良好的热平衡状态可以使铁合金的冶炼温度稳定,并确保合金中的合金元素得到充分的溶解和分散。
同时,热平衡还与冶炼炉体的寿命、电能消耗和环境排放等因素密切相关,因此在铁合金冶炼过程中,必须特别重视热平衡的分析和调控。
首先,进行热平衡分析时,需要考虑到炉体和冶炼过程中的热损失,这是影响热平衡的重要因素之一。
冶炼炉体的外壳和衬里的材料导热系数、厚度和温度梯度等因素都会影响热损失的大小。
此外,冶炼过程中的废气和废热也是热平衡分析的重要内容,合理回收和利用废气和废热可以减少热损失,提高热平衡。
其次,调控热平衡主要涉及到热量的输入和输出的平衡。
冶炼过程中,热量的输入主要来自电能和燃料燃烧产生的热能。
电能通过电极和炉料的电阻加热产生热能,可以通过调节电极的电流强度和电极位置来控制热量的输入。
而燃料燃烧产生的热能主要由燃料的燃烧效率和燃烧温度决定,通过控制燃料的供给量和氧气的流量来调节燃烧产生的热量。
除了热量的输入之外,还需要考虑热量的输出,即冶炼过程中冶炼系统中的热损失。
通过合理设计冶炼设备的外壳和衬里材料、加强冶炼炉体的保温措施等方式可以减少热损失。
此外,还可以通过回收和利用废气和废热来降低热损失,以提高热平衡水平。
在具体的调控操作中,还需要根据冶炼过程的实际情况和要求来确定合理的热量输入和输出。
例如,在铁合金冶炼过程中,合金元素的溶解温度是一个重要的参数。
通过调节电极电流强度和电极位置等参数,可以控制炉内的温度分布,从而确保合金元素得到充分的溶解。
同时,要特别注意电极与炉料的接触情况,保证电极与炉料的紧密接触,以减少电阻和电热效应的损失。
- 1、下载文档前请自行甄别文档内容的完整性,平台不提供额外的编辑、内容补充、找答案等附加服务。
- 2、"仅部分预览"的文档,不可在线预览部分如存在完整性等问题,可反馈申请退款(可完整预览的文档不适用该条件!)。
- 3、如文档侵犯您的权益,请联系客服反馈,我们会尽快为您处理(人工客服工作时间:9:00-18:30)。
冶金炉热平衡冶金炉热平衡1、热平衡原则⑴热平衡是以热力学第一定律为基础,遵守能量守衡原则, 研究体系的能量进、出平衡关系,反映能量消耗和有效利用、能量损失之间的平衡⑵冶金热平衡是指冶金炉体系热量收、支平衡,能量消耗和有效利用、能量损失之间的平衡关系。
是冶金炉热工常用的分析方法。
⑶热平衡结果,可用热平衡方程、热平衡表及热流图表示。
2、冶金炉热平衡计算的目的:(1)通过现场测试,编制热平衡表,分析炉子的热工作,判断热量的利用是否合理,找出提高热效率的途径;在设计炉子时,通过计算编制热平衡表,热平衡关系中找出燃料消耗量等未知量。
把热收入及热支出各项与现有炉子进行比较,帮助设计者判断设计方案的优缺点。
3、冶金炉热平衡主要内容热平衡区域划定热平衡计算中热量收、支的项目是随选取的热平体系所决定的,所以必须首先划定热平衡体系区域,把进入该区域的热量作为热收人.反之为热支出。
热平衡区域的划分视需要而定,通常有炉膛区域、预热区域及全炉区域。
有时,可将炉子某一特定区域作为热平衡计算所划定的区域,例如可以将炉膛沿炉长方向划定几个区域分别作区域热平衡计算。
划定的区域不同,热收入及热支出项就有所不同。
例如:某炉炉膛及空气换热器两部分组成,如图所示。
图热平衡区域的划分图全炉子热平衡模型炉膛区域热平衡式为:QDw+ Qα= Qs+ QCP+ Qω 其中热量收入项QDw---燃料的燃烧热Qα---空气预热所带入的物理热热量支出项Qs ---加热炉料的有效热QCP ---烟气所带走的热Qω---炉膛内各项热损失换热器域热平衡式为:QCP= Q P+ Qα+ QCω 其中热量收入项QCP ---炉堂烟气所带入的热热量支出项QP ---空气预热的物理热Qα---换热器各项热损失QCω---烟气所带走的热全炉热平衡式为:QDw= Qs+ QP + 其中:---全炉热损失项不难看出炉膛热平衡与全炉热平衡的差别。
于区域不同,对炉膛来说Qα是热收入;但对全炉来说,热收入不包括Qα,是其内部的循环热量,因为供给炉子的是冷空气,Qα是来自换热器从炉膛烟气回收的热,而不是另外供给的热。
全炉子热平衡模型如图示意。
3.2 热平衡中热量的表示方法热平衡中热量的表示方法常有几种不同情况:1)连续工作的炉子,通常以单位时间为基准进行计算,热量单位:为kJ/h。
2) 周期工作的炉子则以周期为基准进行计算3)用单位产品的质量为基准进行计算。
无论基准如何选定,在同一个热平衡计算中,各项热收入及热支出的单位应一致。
热平衡计算中的基准温度热平衡计算中的基准温度通常有多种取法。
如0℃、25℃大气温度和环境温度。
我国热工设备能量平衡通则国家标准规定采用环境温度作为基准温度。
环境温度是指在环境温度下的干球温度,可直接测得。
采用环境温度比较符合实际,并且计算较为简单,因为通常工质、燃料物料等都处于环境温度。
物料平衡物料平衡是热平衡的前提。
在进行热平衡时,首先应进行物料平衡。
物料平衡一般与冶金炉生产的产品以及产品工艺有关。
3.5冶金炉热平衡计算结果表示1)热平衡表2)热流图3)冶金炉生产热工技术指标如:单位能耗量;冶金炉热效率单位助燃空气量;单位位排烟量;单位冷却水量提出节能降耗措施:[实例] 加热炉炉膛热平衡计算一、收人项计算1.燃料燃烧的化学热QC QC = BQ kJ/h 式中B——燃料消耗量,kg/h;QC——燃料低发热量,kJ/kg;2.燃料预热带入的物理热Q Qf= B C tf= B Kj/H 式中Qf——燃料的平均比热,KJ/h;tf----燃料的预热温度℃if一燃料的热含量,kJ/m 。
于气体燃料各组分的比热不同,应采用下式计算燃料预热的物理热Qf?B?p1c1?p2c2???tf () 式中p1,p2?—气体燃料各组分的体积百分比;c1,c2?—各组分的平均比热。
3. 空气预热代入的物理热Qa Qa?BnL0cata?BLnia?kJ/h?式中n—空气消耗系数;L0—理论空气消耗量,m3/kg(m3);Ln—实际空气消耗量,m3/kg(m3);ta—空气预热温度,℃;ia—空气热含量,kJ/m3。
4.钢料在入炉时代入的物理热Qm 钢料在热装时应计入此项热收入,常温入炉时则不计Qm?Gcmtm?kJ/h?式中G—炉子生产率,kg/h;cm—钢料的比热,kJ/(kg℃);tm—钢料入炉温度,℃。
5.金属氧化所放出之热Q0 Q0?5652Ga?kJ/h?式中a—金属烧损率,一般加热炉中a?~,若小于则可不计;5652—每千克铁氧化时所放出的热量,单位是kJ/kg。
# 6.雾化用蒸汽带入的物理热QH 用油作燃料时,油本身的物理热不计入收入项,用空气做雾化剂时,空气的物理热也不计入热收入项,但用蒸汽做雾化剂时,则蒸汽所带入的物理热应计入,并按下式计算QH?Bn’cHtH?Bn’iH?kJ/h?式中n’—每千克燃油雾化用蒸汽量,kg/kg;cH—蒸汽的比热,kJ/(kg℃);tH—蒸汽的温度,℃;iH—蒸汽热含量,kJ/kg。
二、热支出项计算 1. 钢料加热所需的热—有效热Qs Qs?Gcmtm?kJ/h? 式中tm—钢料出炉时的平均温度。
若钢料为热装,则按下式计算Qs?G?tm,2cm,2?tm,1cm,1??G?i?kJ/h?式中tm,2,tm,1—钢料出炉及入炉温度,℃;cm,2,cm,1—相应温度的平均比热,kJ/(kg℃)。
2. 烟气带走的热Qcp Qcp?BVnccptcp?kJ/h?式中Vn—燃烧产物量,m/kg(m);tcp—出炉烟气温度,℃;ccp—tcp 下烟气的平均比热,kJ/(m3℃)。
3. 燃料化学不完全燃烧的热损失Qtd pH2O??pCO?BVn?QCO?QH???kJ/h 100100??2O33Qtd式中QCO,QH pCO,pH?—CO、H2O…等可燃成分的发热量;2O?—CO、H2O…等可燃成分在烟气中的体积百分含量。
一般情况下,可以认为烟气中每含1%的CO,就会同时含有5%的H2。
这种混合气体折算成1m 3CO时的发热量为18046kJ,所以此项热损失也可见单用下式计算Qtd?18046VnpCO100?kJ/h? 4. 燃料机械不完全燃烧的热损失对烧固体燃料的炉子,此项损失是指炉栅的漏失及清灰渣时夹带而损失的燃料。
对燃油及煤气的炉子,则指泄漏损失。
Qi?KQD??kJ/h?式中K—机械不完全燃烧损失的百分数,可参考下列数据固体燃料K?~;液体燃料K?;气体燃料K?~。
5. 炉壁的散热损失Q? 连续工作的炉子,经过炉壁的散热损失可视为稳定导热过程,按下式计算Q??t1?t2AkJ/h??1?1??2?2????n?n式中A—炉壁面积,m2;t1—炉壁内表面温度,℃;t2—周围大气温度,℃;?1,?2??n—炉壁各层材料的厚度,m;?1,?2,??n—各层材料的导热系数,kJ/(mh℃)。
其中为假设炉壁对空气的总换热系数?等于71 kJ/(mh℃)时,炉壁外表面与空气间的热阻??1??。
71??于炉顶、炉底、炉墙的砌筑厚度、层数及温度均不一样,所以应分别计算热然后相加。
6. 炉门、开孔辐射热损失QR 当炉门或窥孔打开时,炉内向炉外高温辐射造成的热损失用下式计算?T?QR????A? kJ/h ?100?4式中T—炉门或窥孔处炉气温度,K;?—综合角度系数,附图查出。
一般而言大炉子??~,中炉子;??~?—炉门或窥孔的开启时间,h。
7. 炉门、开孔溢气热损失Qg 一般炉子底面为零压,故炉膛处于正压,当打开炉门或窥孔时,高温气体将溢出炉外,同时炉子缝隙之处也将有高温气体溢出,从而造成热损失,此项热损失用下式计算。
Qg?V0tgcg? kJ/h式中tg—炉气温度,℃;cg—炉气在tg下的平均比热,kJ/(m℃);3V0—在标准下从炉内溢出的气体量,m/h,按下式计算3因为V0?Vt1??t3600?m/h? 3气体溢出体积按下式计算Vt?23?Hb2gH??a??g???m/s?g 式中?—流量系数,薄壁??;厚壁??;H—炉门开启高度,m;b=炉门宽,m;?g—炉气在tg下的密度,kg/m3;?a—空气在ta下的密度,. kg/m3。
若炉膛为负压,则无此项热损失,但冷空气被吸入炉内造成炉温降低、烟气量增大、金属烧损增加,一般不希望呈现这种情况。
8. 炉子冷却水带走的热损失Qcd 炉子冷却部件中冷却水带走的热量占热支出很大的比例,例如大型连续加热炉此项热损失可达20%,一般用下式计算Qcd?Gc?cctc?c’ct’c??Gc?ic?i’c? kJ/h 式中Gc—冷却水消耗量,kg/h;tc,t’c—冷却水出、进口温度,℃;cc,c’c—冷却出、进口温度下的比热,一般取cc?c’c?,kJ/kg℃;ic,i’c—冷却水出、进口温度下的热焓,kJ/kg;当采用汽化冷却时,此项热损失用下式计算Qcd?G’c?ic,g?ic? kJ/h 式中G’c—蒸汽产量及补给水量,kg/h;ic,g—蒸汽热含量,kJ/kg;ic—补给水热含量,kJ/kg。
9. 其它热损失包括炉体蓄热、加热各种支架、链条、炉辊等所需的热量。
这些热量有时可以计算,有时很难计算,它所占的比例一般来说不算太大,所以除非特殊情况,一般不进行计算。
有时将氧化铁皮带走的热量也计入此项热损失之中。
三、热平衡表的编制及燃料消耗量的确定根据能量平衡定律,热收入项总和等于热支出项总和,列出热平衡方程式为?Qin??Qout 表连续式加热炉热平衡表四、加热炉生产热工技术指标1)加热炉单位能燃料耗量b?BQDGkJ/kgb?1000BQDGkJ/tG---炉子生产率kJ/h2) 加热炉炉底强度d?BQDAkJ/mh22d?1000BQDAkJ/mh2A---炉底面积m3)加热炉热效率是指金属加热所需热量占燃料燃烧的热量??金属加热所需热量Q1,燃料燃烧的化学热Q1?100% 五、提高炉子热效率的措施1)减少烟气带走的热损失2)回收烟气余热预热空、煤气4)减少冷却水带走的热损失5)减少炉体散热6)使燃料燃烧充分,减少不完全燃烧7)加强炉子的热工管理和操作电弧炉冶炼碳素结构钢物料平衡收入项目废钢生铁石灰萤石炉衬耐火材料氧气空气电极铁合金质量750 250 70 10 20 23 92 30 1425 100 1425 100 %项目钢水炉渣炉气铁挥发烟尘支出质量1000 120 125 10 10 %电弧炉冶炼碳素结构钢热平衡表2-3 碳素结构钢热平衡收入项目物理热氧化热和成渣热其中:C氧化si氧化Mn氧气p氧化Al 氧化Fe氧化SiO2成渣P2O5成渣电能热量/kj 3430 58520 13750 9330 900 140 600 29790 3340 670 183220 245170 100 245170 100 %项目钢水物理热炉渣物理热反应吸热炉气物理热烟尘物理热冷却水热变压器系统热其它损失热支出热量139120 24430 7830 16780 2750 20090 14720 19450 %注:1)热平衡以100kg废钢和生铁为基础计算;2)计算的单位耗电量为:/t钢。