影响紧固件磷化原因分析
磷化工艺中的各种影响因素

磷化工艺的影响因素磷化膜的质量直接影响与有机膜、涂层的附着力和防护性,影响磷化工件的耐磨、耐微动力磨损和抗擦伤性,以及磷化膜能否成为润滑剂的载体。
磷化膜质量的高低,取决于磷化所采用的工艺是否恰当,磷化过程是否符合工艺要求,因此要十分注意影响磷化工艺的因素。
影响磷化工艺的主要因素有:材质及表面状态、磷化前处理、磷化后处理、磷化液的化学成分等。
下面试就影响磷化工艺的主要因素作一分析。
(一)材质及表面状态。
同是钢铁工件,受含有的其它元素不同,表面晶格是否遭受腐蚀等因素的影响,形成的磷化膜颜色、均匀性、抗腐蚀能力不一样。
低碳钢容易磷化,膜的结晶致密,颜色较浅;中、高碳钢和低合金钢比较容易磷化,结晶有变粗的倾向,磷化膜颜色深;含有较多铬、钼、钨、钒、硅等元素的钢材不容易磷化。
磷化膜随钢材中碳化物含量和分布的不同存在差异,因此,不同钢材应选用不同的磷化工艺和相应的磷化产品。
(二)前处理。
磷化前的表面处理程度是影响磷化质量的重要因素。
因此,要求除净所有的锈迹、油污。
具体要求是,脱脂后的工件,不应有油脂、乳浊液等污物,其表面应能被水完全湿润;酸洗后的工件,不应有目视可见的氧化物、锈及过腐蚀现象.为防止过腐蚀,减轻氢脆,应在酸洗液中加入缓蚀剂.为防止酸雾,酸洗液中可加入酸雾抑制剂;喷抛丸清理后的工件,不应有漏喷、磨料粘附、锈蚀及油污,其表面应露出金属本色.从除油后到磷化前这一过程,工件不允许直接接触手或有油的污物。
经强酸、强碱处理后的钢铁件,一般会增大结晶粒度,增加膜的重量。
水洗是将工件表面从前道处理工序中带出来的残留化学成分除去,防止对下道处理工序的影响。
除油后的不良水洗会使油污再沉积,更多地消耗酸,造成不均匀的酸洗,形成不均匀的磷化膜;酸洗后的不良水洗,导致磷化槽液游离酸度升高,形成稀疏、不均匀的磷化膜,甚至磷化后的工件生锈。
要保证水洗质量,应保持清水的特定pH值或更有效的导电率,延长清洗时间和次数。
(三)后处理。
钢铁零件磷化缺陷原因分析及解决方案
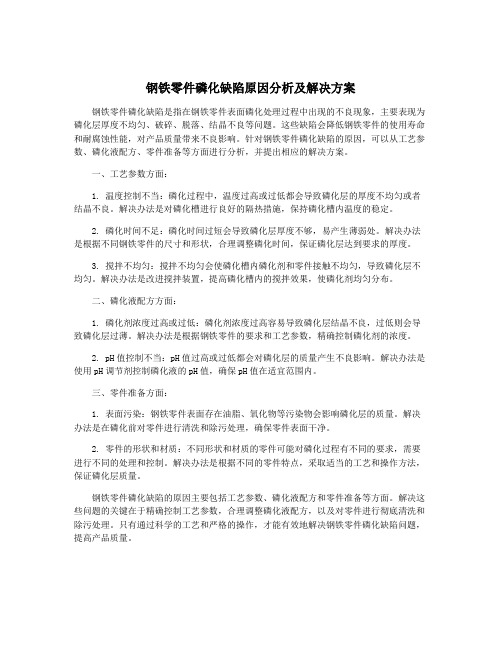
钢铁零件磷化缺陷原因分析及解决方案钢铁零件磷化缺陷是指在钢铁零件表面磷化处理过程中出现的不良现象,主要表现为磷化层厚度不均匀、破碎、脱落、结晶不良等问题。
这些缺陷会降低钢铁零件的使用寿命和耐腐蚀性能,对产品质量带来不良影响。
针对钢铁零件磷化缺陷的原因,可以从工艺参数、磷化液配方、零件准备等方面进行分析,并提出相应的解决方案。
一、工艺参数方面:1. 温度控制不当:磷化过程中,温度过高或过低都会导致磷化层的厚度不均匀或者结晶不良。
解决办法是对磷化槽进行良好的隔热措施,保持磷化槽内温度的稳定。
2. 磷化时间不足:磷化时间过短会导致磷化层厚度不够,易产生薄弱处。
解决办法是根据不同钢铁零件的尺寸和形状,合理调整磷化时间,保证磷化层达到要求的厚度。
3. 搅拌不均匀:搅拌不均匀会使磷化槽内磷化剂和零件接触不均匀,导致磷化层不均匀。
解决办法是改进搅拌装置,提高磷化槽内的搅拌效果,使磷化剂均匀分布。
二、磷化液配方方面:1. 磷化剂浓度过高或过低:磷化剂浓度过高容易导致磷化层结晶不良,过低则会导致磷化层过薄。
解决办法是根据钢铁零件的要求和工艺参数,精确控制磷化剂的浓度。
2. pH值控制不当:pH值过高或过低都会对磷化层的质量产生不良影响。
解决办法是使用pH调节剂控制磷化液的pH值,确保pH值在适宜范围内。
三、零件准备方面:1. 表面污染:钢铁零件表面存在油脂、氧化物等污染物会影响磷化层的质量。
解决办法是在磷化前对零件进行清洗和除污处理,确保零件表面干净。
2. 零件的形状和材质:不同形状和材质的零件可能对磷化过程有不同的要求,需要进行不同的处理和控制。
解决办法是根据不同的零件特点,采取适当的工艺和操作方法,保证磷化层质量。
钢铁零件磷化缺陷的原因主要包括工艺参数、磷化液配方和零件准备等方面。
解决这些问题的关键在于精确控制工艺参数,合理调整磷化液配方,以及对零件进行彻底清洗和除污处理。
只有通过科学的工艺和严格的操作,才能有效地解决钢铁零件磷化缺陷问题,提高产品质量。
钢铁零件磷化缺陷原因分析及解决方案
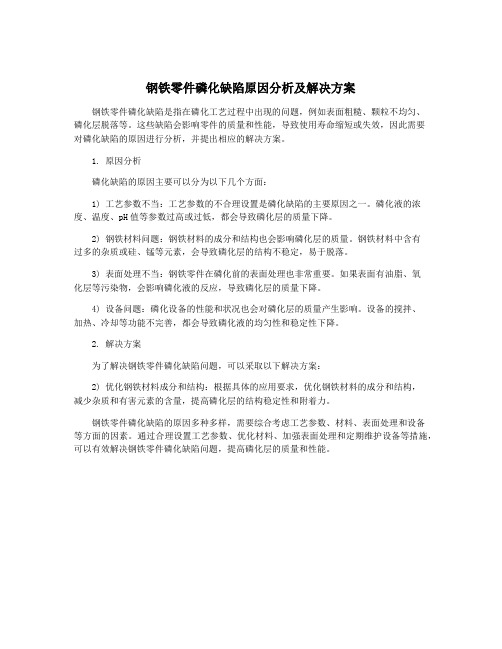
钢铁零件磷化缺陷原因分析及解决方案
钢铁零件磷化缺陷是指在磷化工艺过程中出现的问题,例如表面粗糙、颗粒不均匀、
磷化层脱落等。
这些缺陷会影响零件的质量和性能,导致使用寿命缩短或失效,因此需要
对磷化缺陷的原因进行分析,并提出相应的解决方案。
1. 原因分析
磷化缺陷的原因主要可以分为以下几个方面:
1) 工艺参数不当:工艺参数的不合理设置是磷化缺陷的主要原因之一。
磷化液的浓度、温度、pH值等参数过高或过低,都会导致磷化层的质量下降。
2) 钢铁材料问题:钢铁材料的成分和结构也会影响磷化层的质量。
钢铁材料中含有
过多的杂质或硅、锰等元素,会导致磷化层的结构不稳定,易于脱落。
3) 表面处理不当:钢铁零件在磷化前的表面处理也非常重要。
如果表面有油脂、氧
化层等污染物,会影响磷化液的反应,导致磷化层的质量下降。
4) 设备问题:磷化设备的性能和状况也会对磷化层的质量产生影响。
设备的搅拌、
加热、冷却等功能不完善,都会导致磷化液的均匀性和稳定性下降。
2. 解决方案
为了解决钢铁零件磷化缺陷问题,可以采取以下解决方案:
2) 优化钢铁材料成分和结构:根据具体的应用要求,优化钢铁材料的成分和结构,
减少杂质和有害元素的含量,提高磷化层的结构稳定性和附着力。
钢铁零件磷化缺陷的原因多种多样,需要综合考虑工艺参数、材料、表面处理和设备
等方面的因素。
通过合理设置工艺参数、优化材料、加强表面处理和定期维护设备等措施,可以有效解决钢铁零件磷化缺陷问题,提高磷化层的质量和性能。
影响磷化的工艺因素
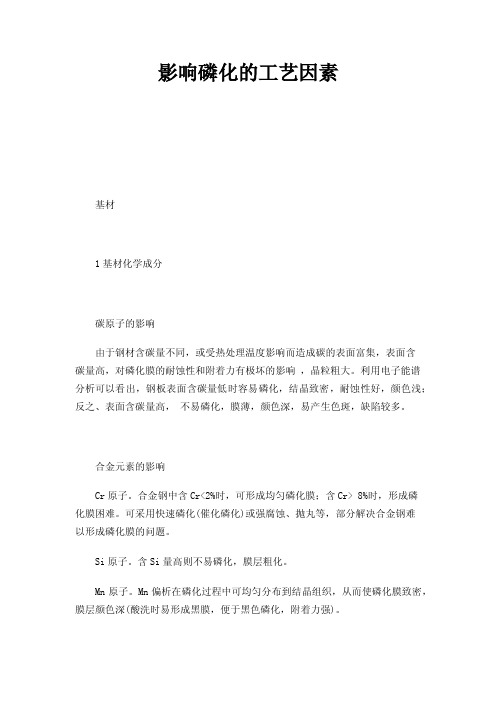
影响磷化的工艺因素基材1基材化学成分碳原子的影响由于钢材含碳量不同,或受热处理温度影响而造成碳的表面富集,表面含碳量高,对磷化膜的耐蚀性和附着力有极坏的影响,晶粒粗大。
利用电子能谱分析可以看出,钢板表面含碳量低时容易磷化,结晶致密,耐蚀性好,颜色浅;反之、表面含碳量高,不易磷化,膜薄,颜色深,易产生色斑,缺陷较多。
合金元素的影响Cr原子。
合金钢中含Cr<2%时,可形成均匀磷化膜;含Cr> 8%时,形成磷化膜困难。
可采用快速磷化(催化磷化)或强腐蚀、抛丸等,部分解决合金钢难以形成磷化膜的问题。
Si原子。
含Si量高则不易磷化,膜层粗化。
Mn原子。
Mn偏析在磷化过程中可均匀分布到结晶组织,从而使磷化膜致密,膜层颜色深(酸洗时易形成黑膜,便于黑色磷化,附着力强)。
Ni原子。
含Ni材质经热处理后,合金组织发生变化,磷化困难,且易出现缺陷。
活性冷轧钢板的活性大小对磷化效果产生不同的影响。
即活性小的冷轧钢板磷化效果好;而活性大的磷化效果差。
生产表明,几种冷轧钢板的活性大小顺序:宝钢板2030>日本板>宝钢1550。
需要钢板生产厂家,降低钢板活性。
表面状态粗糙度在相同磷化条件下,磷化工件表面光洁度越高,磷化过程进行越缓慢,获得的膜层薄而致密,且颜色浅。
反之,表面粗糙,磷化反应快,膜层厚而疏松,均匀性差,颜色深。
可以解释为:光洁度高的表面比粗糙的表面电位正,基体表面在磷化液中不易被酸蚀所致。
所以,光洁度高的工件,磷化前必须进行充分预处理(抛丸或酸蚀)。
锈蚀度。
锈蚀钢板会影响磷化质量(无论采用何种涂锈方法,其磷化膜耐蚀性差)。
况且由于酸洗造成工件表面黑白不均匀,同样影响磷化效果(白色部位较难磷化)。
因此,尽量不要选用锈蚀的钢板加工工件。
特别要防止采用不同厂家、不同批次的钢板来加工同一工件(如汽车车身等)。
否则。
因钢板的差异而造成磷化质量不一样。
同时要注意加工过程中尽量不要破坏钢板防锈膜和加工后长时间存放(采取防锈措施)。
磷化处理影响因素及常见问题
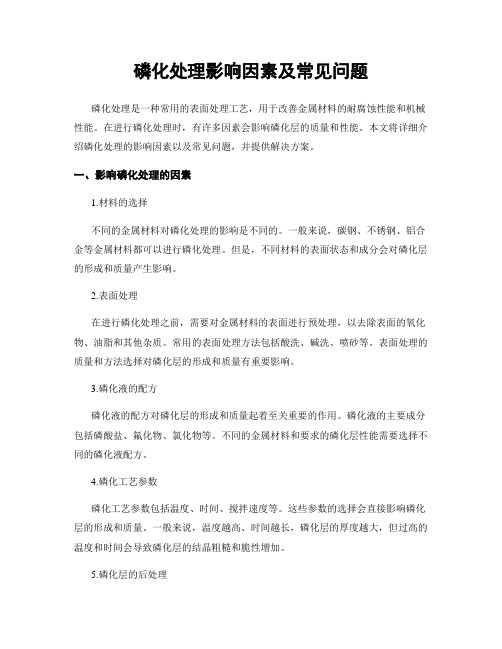
磷化处理影响因素及常见问题磷化处理是一种常用的表面处理工艺,用于改善金属材料的耐腐蚀性能和机械性能。
在进行磷化处理时,有许多因素会影响磷化层的质量和性能。
本文将详细介绍磷化处理的影响因素以及常见问题,并提供解决方案。
一、影响磷化处理的因素1.材料的选择不同的金属材料对磷化处理的影响是不同的。
一般来说,碳钢、不锈钢、铝合金等金属材料都可以进行磷化处理。
但是,不同材料的表面状态和成分会对磷化层的形成和质量产生影响。
2.表面处理在进行磷化处理之前,需要对金属材料的表面进行预处理,以去除表面的氧化物、油脂和其他杂质。
常用的表面处理方法包括酸洗、碱洗、喷砂等。
表面处理的质量和方法选择对磷化层的形成和质量有重要影响。
3.磷化液的配方磷化液的配方对磷化层的形成和质量起着至关重要的作用。
磷化液的主要成分包括磷酸盐、氟化物、氯化物等。
不同的金属材料和要求的磷化层性能需要选择不同的磷化液配方。
4.磷化工艺参数磷化工艺参数包括温度、时间、搅拌速度等。
这些参数的选择会直接影响磷化层的形成和质量。
一般来说,温度越高、时间越长,磷化层的厚度越大,但过高的温度和时间会导致磷化层的结晶粗糙和脆性增加。
5.磷化层的后处理磷化层形成后,需要进行后处理,以提高磷化层的耐腐蚀性能和机械性能。
常用的后处理方法包括中和、封闭、涂覆等。
后处理的质量和方法选择对磷化层的性能有重要影响。
二、常见问题及解决方案1.磷化层不均匀磷化层不均匀可能是由于磷化液的搅拌不均匀、材料表面存在油脂或氧化物等杂质、磷化液配方不合理等原因造成的。
解决方法包括加强搅拌、提高表面处理质量、优化磷化液配方等。
2.磷化层结晶粗糙磷化层结晶粗糙可能是由于磷化液温度过高、时间过长、磷化液配方不合理等原因造成的。
解决方法包括控制磷化液的温度和时间、优化磷化液配方等。
3.磷化层附着力差磷化层附着力差可能是由于材料表面存在油脂、氧化物等杂质、磷化液配方不合理等原因造成的。
解决方法包括提高表面处理质量、优化磷化液配方等。
钢铁零件磷化缺陷原因分析及解决方案
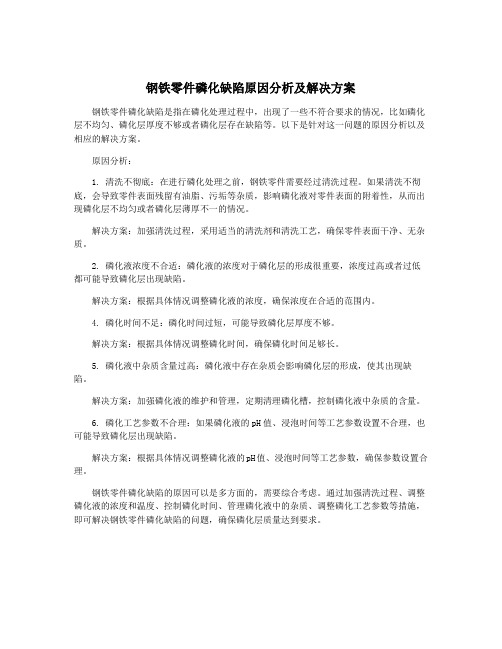
钢铁零件磷化缺陷原因分析及解决方案
钢铁零件磷化缺陷是指在磷化处理过程中,出现了一些不符合要求的情况,比如磷化层不均匀、磷化层厚度不够或者磷化层存在缺陷等。
以下是针对这一问题的原因分析以及相应的解决方案。
原因分析:
1. 清洗不彻底:在进行磷化处理之前,钢铁零件需要经过清洗过程。
如果清洗不彻底,会导致零件表面残留有油脂、污垢等杂质,影响磷化液对零件表面的附着性,从而出现磷化层不均匀或者磷化层薄厚不一的情况。
解决方案:加强清洗过程,采用适当的清洗剂和清洗工艺,确保零件表面干净、无杂质。
2. 磷化液浓度不合适:磷化液的浓度对于磷化层的形成很重要,浓度过高或者过低都可能导致磷化层出现缺陷。
解决方案:根据具体情况调整磷化液的浓度,确保浓度在合适的范围内。
4. 磷化时间不足:磷化时间过短,可能导致磷化层厚度不够。
解决方案:根据具体情况调整磷化时间,确保磷化时间足够长。
5. 磷化液中杂质含量过高:磷化液中存在杂质会影响磷化层的形成,使其出现缺陷。
解决方案:加强磷化液的维护和管理,定期清理磷化槽,控制磷化液中杂质的含量。
6. 磷化工艺参数不合理:如果磷化液的pH值、浸泡时间等工艺参数设置不合理,也可能导致磷化层出现缺陷。
解决方案:根据具体情况调整磷化液的pH值、浸泡时间等工艺参数,确保参数设置合理。
钢铁零件磷化缺陷的原因可以是多方面的,需要综合考虑。
通过加强清洗过程、调整磷化液的浓度和温度、控制磷化时间、管理磷化液中的杂质、调整磷化工艺参数等措施,即可解决钢铁零件磷化缺陷的问题,确保磷化层质量达到要求。
钢铁零件磷化缺陷原因分析及解决方案

钢铁零件磷化缺陷原因分析及解决方案钢铁零件磷化缺陷是钢铁制品表面处理过程中的一种常见问题。
磷化是通过对钢铁表面进行磷酸盐处理来提高其腐蚀抗性和润滑性。
然而,在磷化过程中,会出现一些缺陷,如不均匀磷化、磷化质量低劣、磷化层厚度不均等问题。
本文将重点讨论钢铁零件磷化缺陷的原因分析以及解决方案。
一、原因分析1. 前处理不当:前处理是钢铁磷化过程中的重要步骤,它会影响到后续磷化质量。
如果前处理不当,如清洗不彻底或清洗液过期,会导致表面极性不足,防锈效果降低,磷化效果也会受到影响。
2. 磷酸盐浓度不合适:磷酸盐溶液的浓度对磷化的效果有着很大的影响。
如果浓度过低,会导致磷化不彻底,磷化层厚度不均,磷化后表面容易生锈。
而浓度过高则会导致磷化剂的使用量增加,磷化质量降低,磷酸盐沉淀堵塞喷嘴等问题。
3. 磷酸盐处理时间过长:磷化处理时间的长短也会影响磷化层的均匀性和质量。
如果磷化时间过长,会导致表面结晶过度,出现磷化皮层厚度不均、磷化结晶不完整等缺陷。
5. 设备设施不足:磷化过程中,设备的自动化程度和设施的完善程度也会影响磷化质量。
如果设备不足或者过于陈旧,会导致工艺不稳定,磷化后表面质量不稳定等问题。
二、解决方案1. 加强前处理:在前处理过程中,应当使用专用清洗剂,充分清洗表面,确保表面无污垢和油脂。
并且,清洗剂的浓度和使用次数也要把握好,并及时更换和补充。
2. 控制磷酸盐浓度:在磷酸盐溶液配制时应该控制好浓度,浓度不宜过高或过低,最好依据工艺要求合理配制。
同时,应该定时检测溶液的浓度并进行调整,以免磷化质量受到影响。
3. 控制磷酸盐处理时间:磷酸盐沉积时间的长短会直接影响磷化层的质量,因此应该依照实际情况调整时间。
如果时间过长,应该考虑更换磷酸盐处理剂。
4. 控制磷酸盐处理温度:磷酸盐处理温度的控制也极为关键,在生产过程中应该随时监测温度,并进行适当调整。
在调整温度时,应该按照工艺条例和设备规范来操作,避免产生翻样或者温度不稳定的情况。
钢铁零件磷化缺陷原因分析及解决方案

钢铁零件磷化缺陷原因分析及解决方案钢铁材料作为工业生产中常用的原材料之一,广泛应用于汽车、机械、航空航天等领域。
而在钢铁材料进行加工过程中,为了提高其表面的防腐性能和使用寿命,通常会进行磷化处理。
磷化过程中出现的缺陷问题一直困扰着生产制造企业。
本文将对钢铁零件磷化缺陷的原因进行分析,并提出解决方案,以期能够解决这一难题,提高产品质量和生产效率。
1. 工艺参数不当:在钢铁零件的磷化处理过程中,如果磷化剂的浓度、温度、PH值等工艺参数控制不当,就会导致磷化层的均匀度不佳,甚至出现斑驳、脱落等缺陷。
2. 钢铁材料质量不良:钢铁材料的表面质量不良,如存在氧化皮、油污等杂质,会影响磷化剂与基体金属的反应,导致磷化层的质量不达标,出现缺陷。
3. 磷化剂配方问题:磷化液的配方中,磷化剂、促进剂、缓蚀剂等成分比例不合理,或者使用的磷化液质量不合格,都会在磷化过程中引起问题,导致磷化层质量不佳。
4. 磷化处理工艺控制不严:在磷化处理过程中,处理时间、温度、浸泡性等工艺控制不严,会导致磷化层的厚度、致密性、结晶度等不达标,形成磷化缺陷。
5. 配件形状设计不当:有些钢铁零件的形状复杂、结构特殊,不易达到均匀的磷化处理,容易形成磷化缺陷。
1. 严格控制磷化工艺参数:制定科学合理的磷化工艺流程,严格控制磷化液的浓度、温度、PH值等参数,确保每一道工序都按照标准操作,避免出现磷化缺陷。
2. 提高钢铁材料表面质量:在进行磷化处理前,对钢铁材料的表面进行清洗、脱脂、除锈等处理,确保表面质量良好,避免表面杂质影响磷化效果。
5. 针对特殊零件设计特殊处理方案:对于形状复杂的钢铁零件,可以采用特殊的固液分离设备,或者采用局部涂覆、喷涂等方式进行磷化处理,以保证磷化的均匀性和质量。
钢铁零件磷化缺陷问题的解决需要全面考虑原材料质量、工艺参数控制、磷化处理方法等方方面面的因素。
只有在生产制造过程中严格控制每一个环节,优化工艺流程和磷化液配方,才能够有效地解决钢铁零件磷化缺陷问题,提高产品质量和生产效率。
- 1、下载文档前请自行甄别文档内容的完整性,平台不提供额外的编辑、内容补充、找答案等附加服务。
- 2、"仅部分预览"的文档,不可在线预览部分如存在完整性等问题,可反馈申请退款(可完整预览的文档不适用该条件!)。
- 3、如文档侵犯您的权益,请联系客服反馈,我们会尽快为您处理(人工客服工作时间:9:00-18:30)。
影响紧固件磷化原因分析
本文从磷化紧固件耐腐蚀的影响因素分析,总结出如何提高磷化紧固件耐腐蚀性能。
1、存在的问题
磷化膜耐蚀性按GB11376-1989进行中性盐雾试验,90min不产生锈蚀。
汽车紧固件其耐中性盐雾试验不合格率达45%,磷化膜外观、色泽不一致,结晶粗大,挂灰多。
2、影响因素
2.1、溶液成分配比不佳
溶液的组成与配比对磷化质量有很大的影响,采用自调整的钙盐磷化液进行生产时,工件表面形成的磷化膜结晶粗大、挂灰多,产品外观质量差,该方案配制的黑色磷化液生产时产生的沉淀相对较多,基本上每日都需要打涝沉渣。
经多种磷化液比较,采用PF-MIAM和PF-MIAR磷化液。
该磷化液调整简单、磷化膜结晶细密,使汽车紧固件耐蚀性能得到较大提高,而且工件挂灰少、溶液沉淀少。
其磷化效果基本能满足汽车钢质紧固件黑色磷化要求。
2.2、酸比不正确
酸比是指游离酸度(Tb)与总酸度(Ta)的关系。
游离酸度过高,与钢铁件的作用快,会大量析氢,使界面层磷酸盐不易饱和,导致晶核形成困难,膜层结晶粗大、疏松多了孔,搞蚀性能降低,而且合磷化时间延长;游离酸度过低,磷化膜薄、甚至没有磷化膜生成。
总酸度过高会使膜层过薄,总酸度过低会使膜层疏松粗糙。
所以,总酸度一般控制在85 ̄140点。
2.3、磷化前处理方式的影响
小型紧固件采用篮装,工件容易接触,在磷化过程中不能让其充分磷化,接触部位难以形成完整的磷化膜,故耐中性盐雾性能差;若采用挂装或让工件间不接触,使其能充分反应,便对提高耐中性盐雾性能有事半功倍的作用。
2.4、溶液温度的影响
磷化液温度升高,可提高磷化的结合力、硬度、耐蚀性。
但是温度也不宜过高,否则会使Fe2+氧化成Fe3+,并使沉淀物增多,溶液挥发快,导致溶液不稳定。
3、抗蚀性能差的原因及排除对策
磷化紧固件抗腐蚀性能差产生的原因及排除对策
⑴溶液成分配比不佳:改进磷化液配方,采用PL-VM磷化液。
⑵酸比不正确:游离酸性太高,可加碳酸锰等调节:总酸太低,可加主剂调节,总酸控制在85点以上。
⑶溶液主要成分低:补加主液。
⑷溶液主要成分不正确:溶液沉清后,槽温控制在95℃左右。
⑸磷化时间太短:磷化时间控制在10 ̄15min。
⑹溶液中Fe2+含量高:加双氧水等氧化剂调整Fe2+含量,或更换槽液。
⑺溶液里有氧化物:更换槽液,或加强工件前处理酸洗后的清洗。
⑻前处理不干净:采用喷砂或紧固件保持磷化前有较好的表面状况。
⑼装载量过多:采用挂装或减少装载量,使紧固件保持一定空隙,让其能充分反应。
4、结语
⑴根据紧固件不同,分别进行酸洗或喷砂后,再磷化10 ̄15min,基本能达到耐中性盐雾试验90min的要求。
⑵根据紧固件形状、大小,采用不同的装挂方式进行磷化10 ̄15min,基本能达到耐中性盐雾试验要求。
⑶自配磷化液成分控制不好,溶液调整难度大,沉淀多,工件挂灰中,在磷化过程工件易造成过腐蚀。
采用PL-VM磷化液,溶液参数调整简单,沉渣少,工件挂灰,膜层结晶细蜜,其耐中性盐雾时间能有所提高,工件经中性盐雾试验后腐蚀程度小。
磷化常见故障及解决办法
磷化废水处理
汽车磷化处理是对汽车的钢铁零件表面进行的一种化学加工工艺,其废水中含磷量高,超标严重。
磷化废水的处理有多种处理方法,需要通过研究和实验获得最经济和最有效的处理方法。
目前,除磷方法主要有生物法、化学法、物理化学法及其这些方法的综合运用。
化学法和生物法是目前应用比较广泛的方法,其中化学法除磷具有处理效率高、效果稳定、简单易行等优点,是处理高浓度含磷废水的最有效方法之一。
在磷化工序中,磷是以可溶性磷酸盐的形式存在的,去除的最佳途径是使正磷酸根和金属离子形成难溶性物质而产生沉淀。
通常,化学沉淀法是以投加氯化钙来进行沉淀,成本较高;而使用石灰则价格相对低廉、操作简单。
安徽师范大学研究人员采用石灰法处理磷化废水,在适当的pH值条件下能使PO43-达到良好的沉淀效果;同时,通过研究氯化钙处理磷化废水的效果,分析和论证溶液的pH值和钙离子浓度对PO43-根沉淀效果的影响。
为了达到更好的沉淀效果,在工程应用中可采用聚合氯化铝为混凝剂。
通过沉淀过滤、涡流反应池、斜管沉淀池、过滤器以及调节池调节出水的pH值,用酸中和反应过程中多余的碱等程序便可做到达标排放磷化废水。