镁合金文献综述
镁合金论文

AZ91粉末状镁合金的氢化处理及组织演变摘要镁合金是目前最轻的金属结构材料具有比强度高、比刚度高、耐腐蚀、切削加工性能好、易于回收利用等一系列的优点,因而有着极其重要的应用价值与广阔的应用前景。
但是,现有镁合金常温下的塑性变形能力和塑性加工性能仍然较低,限制了其应用。
因此,提高各类镁合金的强度,改善其塑性,是拓展镁合金应用领域推动镁合金发展的关键。
通过细化晶粒制备纳米晶镁合金,能够提高现有各类镁合金材料的强度和塑性,是发展镁合金的有效途径。
当镁合金粉末经氢化—歧化—脱氢—重组工艺处理后,粉末的微观组织被大幅度细化到纳米级。
进一步研究发现,当粉末经脱氢重组后,其晶粒虽有所长大,但仍可保持在纳米级,这一过程被称为HDDR处理。
本文主要研究粉末状镁合金的氢化过程及温度、氢压对氢化过程的影响。
本研究选择应用广泛的AZ91镁合金。
采用“镁合金氩气中磨制成粉末→氢化处理→真空脱氢→组织性能分析测试”的工艺路线,来研究粉末状镁合金的氢化脱氢过程,对其微观结构,相组成的变化进行研究。
利用X 射线衍射(XRD)和扫描电子显微镜(SEM)对镁中MgH2的体积分数和表面形貌的变化进行分析。
由于实验仪器出了故障,本次试验需先将仪器修理完善。
关键词:AZ91镁合金,HDDR处理,氢化反应,晶粒细化,纳米晶材料HYDROGEN PROCESSING AND MICROSTRUCTURE EVOLUTION OF AZ91 MAGNESIUM ALLOYABSTRACTMagnesium alloys is the lightest metallic structural material. Due to the unique properties, such as high specific strength and rigidity, easy to recycle and so on, they have great potential for structural applications. However, because of the plastic deformability of magnesium alloys is quite poor at room-temperature, which is an intrinsic drawback to limit their applications. So, enhancing the strength and deformability of magnesium alloy is the key to expand their applications and promote the development of magnesium alloy industry. Grain refinement is the effectual way to enhancing the strength and deformability of Mg alloy.When the magnesium alloy material was treated by hydrogenation- disproportionation-dehydrogenation-restructuring process, the microstructure of the material has been substantially refined to the nanoscale. Further studies shows that the material has been treated by dehydrogenation and restructuring process, its grains would grow up, but still remained at the nanoscale, which is called HDDR processing. The paper mainly studies how the surface of block magnesium alloy is hydrogenated and how the temperature and hydrogenpressure effect to the hydrogenation.In this study, AZ91 has been used, which is currently the most popular magnesium alloy. We study the hydrogenation and dehydrogenation process of the block magnesium alloys, its microstructure, phase composition and surface morphology by “magnes ium alloy ingotslices polishing–hydrogenated–vacuum dehydrogenation–organizations perf ormance analysis test” process. The volume fraction of MgH2 in Mg and changes of the surface topography were analyzed using X-ray diffraction and scanning electronmicroscopy analysis, respectively.KEY WORDS: AZ91 magnesium alloy, HDDR processing, hydrogenation, grain refinement, nanocrystalline materials目录第一章绪论 (1)1.1 引言 (1)1.2 镁及镁合金的概述 (1)1.2.1 镁合金的优异性能 (3)1.3 镁合金的发展及应用 (4)1.3.1 镁合金的发展 (4)1.3.2 镁合金在国防、航空航天工业及汽车中的应用 (5)1.4 镁合金材料的分类及研究状况 (6)1.4.1 细晶镁合金的制备工艺及发展现状 (7)1.4.2 强应变塑性变形晶粒细化技术 (8)1.4.3 快速凝固粉末冶金细晶工艺技术 (9)1.4.4 氢化处理细晶强化镁合金工艺技术 (10)1.5 本课题的目的及意义 (11)1.6 本文的研究内容 (12)第二章实验材料、设备及方法 (13)2.1 实验材料 (13)2.2 实验主要设备 (14)2.3 试样的制备 (15)2.4 组织结构分析 (15)2.4.1 射线衍射分析 (16)2.4.2 金相显微镜分析 (16)2.4.3 扫描电镜分析 (17)2.5 实验工艺方法与过程 (17)2.5.1 试验工艺方法的确定 (17)2.5.2 试验操作流程 (18)第三章氢化处理粉末状镁合金的氢化反应机理 (20)3.1 引言 (20)3.2 镁合金的氢化反应机理 (20)3.2.1 氢分子在镁合金表面的解离吸附 (20)3.2.2 氢离子在镁合金内的扩散与反应 (21)3.3 镁合金氢化过程的影响因素 (21)3.3.1 镁合金自身因素对氢化反应的影响 (21)3.3.2 外界因素对氢化反应的影响 (23)3.3.3 AZ91镁合金氢化处理后的组织演变及分析 (23)3.3.4 镁合金氢化处理前后的组织结构 (24)第四章结论 (27)参考文献 (28)致谢 (30)附录一外文文献原文 (32)附录二外文文献翻译 (36)第一章绪论1.1 引言镁是地壳中分布最广的元素之一,占地壳重量的2.77%,为第四个最丰富的金属元素(位于Al、Fe、Ca)之后。
文献综述

TCP/Mg-Zn-Ca生物复合材料的体外降解特性研究姓名:邓凯倩学号:20100892摘要从2l世纪初开始,以生物可降解镁合金为主要代表的具有生物可降解特性的新一代医用金属材料的研发展迅速,受到了人们的特别关注。
这类新型医用金属材料改变人们通常将金属植入材料作为生物惰性材料使用的传统思想,巧妙地利用镁基金属材料在人体环境中易发生腐蚀(降解)的特性,来实现金属植入物在体内逐渐降解直至最终消失的医学临床目的。
关键词:镁合金力学性能生物相容性可降解性可降解支架耐腐蚀性正文:一、Mg合金生物医用材料的概述:镁是人体必需的宏量元素之一,在机体所含众多金属离子中镁的含量居第四位,在细胞内居第一位,是仅次于钾的细胞内正离子。
镁催化或激活机体300多种酶系,参与体内所有能量代谢。
通常永久性金属材料植入体内,由于材料的腐蚀或磨损而导致有毒性金属离子或粒子的释放,从而引发炎症反应,降低材料的生物相容性。
用镁及镁合金作植入材料,在一定镁离子释放量的范围内,不但不用考虑微量金属离子对细胞的毒性,而且植入材料中的镁离子对人体的微量释放还是有益的。
此外,由于镁与镁合金的密度为117g/ cm3 左右,在所有结构材料中密度最小,与人体密质骨的密度( 1175 g/ cm3 ) 相近, 而且其弹性模量(45GP) 与人体骨组织极为接近,从而有效缓解了应力遮挡效应对骨生长的负面影响。
因此镁合金作为血管支架及骨钉骨板材料具有不可比拟的优越性。
下图分别为骨钉骨板和血管支架:Mg合金作为可降解支架的材料满足下列要求:①具有足够的强度,在足够的径向力作用下能够完全扩张以达到成功植入及防止血管弹性回缩的作用;②合适的降解速度(过快的降解可能伴发炎症反应)及维持时间;③具有较好的组织、血液相容性;④材料本身及其降解产物无毒。
二、Mg在人体中的降解方式⑴电池作用腐蚀电池作用腐蚀通常被看做是镁合金靠近阴极区域的严重腐蚀,阴极可能是内部的,即第二相或者杂质相;也可能是外部的,与镁接触的其它金属,具有低氢过点位的金属组成镁的阴极,引起严重的电池作用腐蚀。
镁合金文献
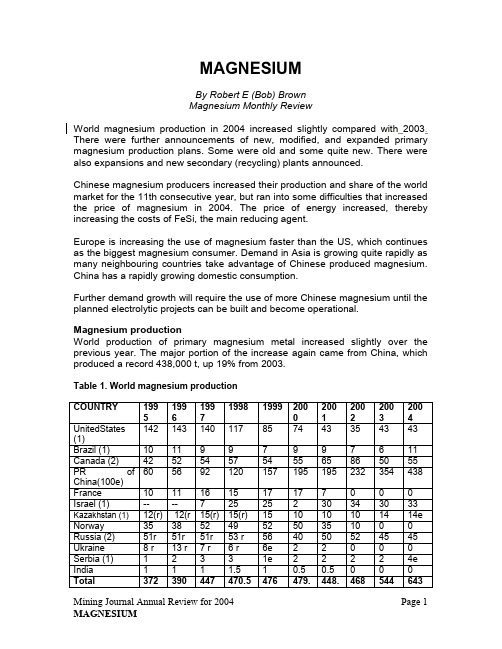
MAGNESIUMBy Robert E (Bob) BrownMagnesium Monthly ReviewWorld magnesium production in 2004 increased slightly compared with2003. There were further announcements of new, modified, and expanded primary magnesium production plans. Some were old and some quite new. There were also expansions and new secondary (recycling) plants announced.Chinese magnesium producers increased their production and share of the world market for the 11th consecutive year, but ran into some difficulties that increased the price of magnesium in 2004. The price of energy increased, thereby increasing the costs of FeSi, the main reducing agent.Europe is increasing the use of magnesium faster than the US, which continues as the biggest magnesium consumer. Demand in Asia is growing quite rapidly as many neighbouring countries take advantage of Chinese produced magnesium. China has a rapidly growing domestic consumption.Further demand growth will require the use of more Chinese magnesium until the planned electrolytic projects can be built and become operational.Magnesium productionWorld production of primary magnesium metal increased slightly over the previous year. The major portion of the increase again came from China, which produced a record 438,000 t, up 19% from 2003.Table 1. World magnesium productionCOUNTRY 1995 199619971998 1999 2002001200220032004UnitedStates(1)142 143 140 117 85 74 43 35 43 43 Brazil (1) 10 11 9 9 7 9 9 7 6 11 Canada (2) 42 52 54 57 54 55 65 86 50 55 PR ofChina(100e)60 56 92 120 157 195 195 232 354 438 France 10 11 161517 17 7 0 0 0 Israel (1) -- -- 725 25 2 30 34 30 33 Kazakhstan (1) 12(r) 12(r 15(r) 15(r) 15 10 10 10 14 14e Norway 35 38 52 49 52 50 35 10 0 0 Russia (2) 51r 51r 51r 53 r 56 40 50 52 45 45 Ukraine 8r13 r 7 r 6 r 6e 2 2 0 0 0 Serbia (1) 1 2 3 3 1e 2 2 2 2 4e India 1 1 1 1.5 1 0.5 0.5 0 0 0 Total 372 390 447 470.5 476 479.448.468 544 6435 5Source: USGS, IMA, CMA, Author estimatese = estimate, r = revision, ( ) = number of operating plants in the countryUnited StatesPrimary magnesium production in the US was estimated as 43,000 t. The only remaining US magnesium producer continues to be US Magnesium Llc(formerly MagCorp).US Magnesium operated its plant at the Great Salt Lake, near Salt Lake City, Utah, with the same management and workforce. The 30 new electrolytic cells and plant modifications are nearly four years old. Cell-life estimates for the new cells have been nearly doubled.US Magnesium Llc announced in September 2004 that it would initiate a further expansion of its magnesium production capabilities. The nameplate capacity of the facility will be increased to 51,000 t/y, utilising the highly efficient electrolytic technology developed by US Magnesium that has proven to reduce energy and labor unit costs significantly. New metal production will be available in July 2005. The expansion will also increase the amount of by-product chemicals such as chlorine, that the company will have available to market. Further expansion to 59,000 t/y and eventually to 73,000 t/y is being studied.It was also noted in a Salt Lake newspaper that “word of US Magnesium increasing production once would have caused an outcry among environmentalists. But this project has not incited objections, largely because the new electrolytic technology has drastically reduced chlorine emissions released while extracting magnesium from the Great Salt Lake's brackish waters”. The new cell technology also cuts energy demand by 25%.Advanced Magnesium Alloy Corp (Amacor), the company that bought the former Xstrata Magnesium recycling plant in Anderson, Indiana, continued to operate its specially designed 25,000 t/y magnesium scrap melting operation through 2004. The plant was hit with a fire on January 14, 2005, and the scrap receiving warehouse area was severely damaged. The special magnesium recycling equipment also suffered some damage. The plant will be rebuilt, repaired and put back into operation.In Alabama, Remag’s idled recycling plant was hit by Hurricane Ivan in September 2004 and was completely destroyed. MagReTech, the newer plant developed by Garfield Alloys, continued to recycle Class 1 magnesium die-casting scrap. Halaco, the recycling plant in California, which had declared bankruptcy, was closed and was due to be liquidated at the end of the year.A new secondary magnesium plant is being installed in a vacant foundry in Camden, Tennessee. MagPro, a Tennessee-chartered company, will be the owner and operator. The foundry was previously owned by Citation Corp., which produced castings and assembled components for the automobile industry. MagPro is owned by John Haack and family. The Haack family, which previouslyran Halaco, has been in the secondary magnesium business for many years, and has developed an innovative magnesium recovery technology that can efficiently and safely recycle magnesium dross, skimming, and Class 1 scrap.Nuclear Regulatory Commission staff held a public meeting in July 2004, in Bay City, Michigan, to discuss the NRC’s clean-up and decommissioning requirements for two nearby sites that have low levels of thorium, a naturally-occurring radioactive material. The sites, located at Kawkawlin, contain thorium contamination resulting from the production of a magnesium-thorium metal alloy by a company that has gone out of business.Thorium-contaminated waste material at the two sites is encapsulated, with a clay cover and walls to prevent the movement of groundwater through the wastes. Other hazardous chemical wastes are also present at the sites but there are no immediate radiological hazards. (Magnesium-thorium alloys were used in castings and in rolled sheet during the 1950-60s and much of the rolled sheet that was used in rocket construction was magnesium-thorium. It was melted and cast as just another alloy in magnesium sand foundries. Those employees who worked with the melting and casting wore film badges to check the amount of exposure. The radiation was quite small.)Bioconvergence, Inc.continues to operate a magnesium alloy turnings recycling plant in Niagara Falls, NY, and is continuing to look at melting the scrap and pouring magnesium ingots.CanadaGossan Resources Ltd has entered into an agreement with Hatch Engineering of Montreal for the first in a series of studies that, collectively, would embody a preliminary feasibility study for its Inwood magnesium project. Currently, an initial economic assessment utilizing Mintek of South Africa's new atmospheric silicothermic magnesium extraction process is under way. The Manitoba Government's Trade and Investment office is providing some assistance to the project.Mintek is developing an advanced thermal magnesium extraction process based on silicothermic reduction of calcined dolomite. The technology is potentially superior to both the Pidgeon and the Magnetherm conventional vacuum processes as it operates at atmospheric pressure and at slightly higher temperatures for better recoveries and throughputs. This new continuous process technology will likely provide for substantially larger production units than the Magnetherm process, with expected improvements to capital and operating costs. Manitoba Hydro's low-cost industrial electricity rates could also provide this energy-intensive project with a significant cost advantage.Timminco Ltd decided to delay the announced four-month closure of its magnesium furnaces at Haley, Ontario. This decision was made because of anunanticipated increase in customer demand for its ultra high-purity magnesium. The closure, originally planned for August through November 2004, is still being deferred.Timminco was exempted from antidumping duties during the original findings of the US Commerce Department many years ago. Timminco produces magnesium using the Pidgeon silicothermic reduction process (small batch type of horizontal retorts.) This is the same process predominantly used in China. Its Haley plant has great historic significance in that it was the site of the first silicothermic magnesium production plant built under the direction of Dr Lloyd M Pidgeon, the man who developed the commercial silicothermic process.Leader Mining International Inc’s management has reported continuing progress on the Cogburn magnesium project in southwestern British Columbia. Activities are now being conducted under North Pacific Alloys Ltd, a BC-registered corporation and a wholly owned subsidiary of Leader Mining. The company continues to work to develop a US$1.24 billion integrated magnesium quarry and smelter operation. Plant size in the original feasibility study by Hatch Engineering was 131,000 t/y of magnesium and magnesium alloys.Nichromet Extraction Inc signed an agreement with LAB Chrysotile concerning the construction of an industrial pilot plant that will extract nickel and magnesium compounds from chrysotile tailings located in Thetford Mines, Quebec. The past production of chrysotile in Quebec has resulted in producing tailings containing approximately 0.25% Ni and 37-40% MgO. The tailings project is a JV between Nichromet and LAB, and there are an estimated 750 Mt containing nickel worth US$10 billion at current prices.Nichromet is a private Montreal-based company and has been testing hydrometallurgical processes over the past five years. These are targeted towards the extraction of mineral that is refractory to conventional processes. Nichromet has developed technology that is patent pending in Canada and many other countries. This technology allows for the simultaneous extraction of nickel and various magnesium compounds (chloride oxide). According to the agreement between LAB and Nichromet, Nichromet will be responsible for financing the cost of the pilot plant to be located within the LAB premises in Thetford Mines. Nichromet will also be responsible for financing a full feasibility study on the project to be concluded within the next 24 months. The Nichromet technology is a hydrometallurgical process based on chloridation. The operation is conducted at a low temperature with the recycling of water. The solid rejects are inert and insoluble. In these conditions the process respects government norms with regards to the environment.Norsk Hydro is the largest primary magnesium metal producer in Canada, using magnesite imported from China and Australia to produce approximately 43,000 t/y of primary magnesium by a special electrolytic process at Becancour,Quebec. The plant also operates a 10,000 t/y recycling facility. Hydro plans to upgrade the magnesium plant. Production will increase by 7,000 t/y to 58,000 t/y of cast primary metal.Work to expand the plant will start in early 2005 and will take 1½ years to complete. The programme will consist principally of improvements in the dehydration section of the plant and the addition of four electrolytic cells. The plant had been incrementally upgraded from its original 43,000 t/y capacity by debottlenecking and other process improvements.Noranda has no plans to restart its idled Magnola primary magnesium plant in Quebec, despite higher magnesium prices and the US Commerce Dept revoking the antidumping duty order on pure magnesium from Canada, retroactive to August 1, 2000, the effective date of the original full sunset review. The rate had applied to Magnola since it started production in 1999. Magnola ceased production in 2003 after reaching only 60% of its 58,000 t/y capacity because of weak market conditions. Noranda said the revocation is a secondary consideration. The plant was shut down temporarily two years ago and will remain shut down. Noranda's primary focus is on market conditions, such as supply and demand and the Canadian dollar versus the US dollar. Recent currency appreciation hurt as revenues are in US dollars. Noranda had discussions near the end of 2004 with Minmetals Group from China, which is interested in purchasing the total corporation. No specific reference was made at that time to the magnesium operations.Magnesium Alloy Corp of Halifax, Nova Scotia. announced that MagEnergy Inc, a wholly owned energy subsidiary, has signed a preliminary agreement with Soc Nationale d'Electricite (SNEL), the owner and manager of the Inga hydroelectric facility in the Democratic Republic of the Congo. MagEnergy's principal endeavour is to allocate part of the electricity generated by the dam to MagAlloy's Kouilou magnesium project located 200 km west of Inga at the deepwater port city of Pointe-Noire in the Republic of the Congo. SNEL’s management committee and board of directors have approved the agreement. MagEnergy -- together with Rusal, SNC-Lavalin, Eskom, IDC and others – is negotiating with SNEL and the Minister of Mines and Energy, and hopes shortly to conclude this comprehensive agreement for the rehabilitation of all the turbines currently installed at Inga 1 and 2. Besides supplying electricity to MagAlloy's Kouilou plant, electricity sales are also being considered to supply demand in Cabinda (Angola), the Republic of Congo and other neighbouring countries.The Inga hydroelectric site currently consists of the Inga 1 station, which consists of six turbines totalling 351 MW, and the Inga 2 station that consists of eight turbines totalling 1,402 MW. The Inga stations have been highlyunderused since their construction more than 20 years ago. The Inga site, located on the Congo River, represents one of the largest hydroelectric sites in the world that can be expanded at a low cost and without any significant environmental impact.MagEnergy entered into an agreement whereby a consortium called the CTEI (Consortium pour le Transport d'Energy d'Inga) was established. The CTEI targets the construction of a new electrical transmission line to connect Inga with MagAlloy's Kouilou magnesium plant site at Pointe-Noire.Spectra Premium Industries Inc (SPI) has signed an agreement in principle to proceed with the acquisition of 90% of Trimag, a limited partnership headquartered in Boisbriand, Quebec. Investissement Quebec will own the other 10% in Trimag, which is one of the most important North American manufacturers of high-pressure die-cast magnesium alloy parts used in the automotive industry. Created in 1995, Trimag was acquired in 2001 by Soc de Developpement du Magnesium, a limited partnership held by three institutional investors, namely Soc Generale de Financement, Sofinov, a subsidiary of Caisse de Depot et Placement du Quebec, and Solidarity Fund QFL.Trimag has two plants, one in Boisbriand, which began operations in 2002, and the other in Haley, Ontario. At present, nearly all of Trimag's revenues are generated as a Tier 2 supplier in reference to vehicles manufactured by General Motors.The new Boisbriand plant is equipped with two 3,500-t presses, which makes Trimag one of the few companies in North America having the infrastructure to produce large magnesium parts, such as instrument panel beams. The plant will operate at full capacity as of the summer of 2005, as a new supply contract for instrument panel beams for a General Motors plant located in China will have entered into production. Trimag anticipates investing between C$10-million to C$15 million for the expansion and for the acquisition of new equipment.United KingdomMagnesium Elektron, a division of Luxfer, has continued to produce secondary magnesium at its plant in the Manchester area.Birmingham-based Advanced Powder Technology won the Queen's Award for Enterprise for its new, high-yield process for manufacturing atomised magnesium powder. Over the past three years, APT's turnover has more than doubled to £800,000. The company produces powder used in countermeasures against heat-seeking missiles. Using an innovative process to produce the powder has significantly improved the previously expensive and low-yield system.BrazilBrasmag has continued to run its special process silicothermic plant at Bocaiuva. The plant is estimated to have produced 11,000 t in 2004. The plant uses a special modified silicothermic (Bolzano) process developed by Ravelli. The company has been investigating other technologies but by the end of 2004 no decisions had been made.NorwayNorsk Hydro continues to run the magnesium casting operations at the plant in Porsgrunn, rated at 20,000 t/y. The plant remelts scrap and some imported pure magnesium. Norsk Hydro has expanded its recycling plant at Bottrop in Germany to 15,000 t/y from 7,500 t/y.The NetherlandsAntheus Magnesium has formed a JV with Remag of Austria to build and operate a 10,000 t/y magnesium recycling plant in northern Holland. Scrap is obtained from the various magnesium-casting operations in Europe. The plant is owned 40% by the Northern Netherlands Development Agency (NOM), 40% by Remag Recycling Gmbh and 20% by a private owner. It was reported to be struggling at the end of 2004.IcelandMagnesium production continued to remain on hold. Australian Magnesium Investments holds a 40% stake in the Icelandic Magnesium project.SerbiaBella Sterna operates a Magnetherm process plant and is estimated to have produced 4000 t in 2004.GermanyIMCO Recycling Inc’s German subsidiary VAW-IMCO Guss und Recycling Gmbh started operations at a new 15,000 t/y facility that will melt, refine and cast magnesium ingots from scrap. About 90% of the output of the plant, which is located next to the IMCO Toeging facility, will be provided to the European auto industry. The plant will start at a rate of 5,000 t/y.Norway's Hydro Magnesium has doubled magnesium recycling at Bottrop to 15,000 t/y after opening two new reprocessing lines. The company expanded Bottrop in order to meet growing demand from the domestic and regional automobile sector. The new lines, together with Hydro's Porsgrunn plant in Norway, have made the company the largest recycler of remelt magnesium in Europe, with a total production of 35,000 t/y.IsraelDead Sea Magnesium(DSM), the 65% Israeli-owned company continued to produce magnesium in 2004 and the output was 33,000 t of which half was alloy.Volkswagen of Germany continues to own 35% of DSM. Higher magnesium prices in 2004 enabled the plant to operate at a profit for the first time since starting operation.Czech RepublicMagnesium Elektron Ltd (MEL) is operating a 10,000 t/y magnesium recycling plant northwest of Prague. The plant is toll-melting magnesium scrap for customers across Europe.RussiaSolikamsk Magnesium Works(SMZ) is a large magnesium producer with a 20,000 t/y plant. Solikamsk is Russia's second-biggest magnesium producer and exports almost all of its rare-earth metal products and about 60% of its magnesium and alloys. Silvinit, which owns 56.7% of SMZ, will put close to US$10 million into the construction of two fluidised bed furnaces, with a capacity of 300 t/d of dehydrated carnallite at the SMZ plant. Construction of the furnaces will begin in 2005 and be completed in 2006. SMZ currently takes in 260,000 t/y of enriched carnallite from Silvinit and tolls 10,000 t/y of dehydrated carnallite from Avisma (in the Perm region). The modifications will boost output of magnesium and its alloys from 15,000 to 32,000 t/y to keep up with growing market demand. The new dehydrating furnaces will make it possible to cover SMZ's magnesium electrolysis capacity and produce an additional 40,000-45,000 t/y of dehydrated carnallite.The general designer on the project will be the Galurgia Institute in Perm. The two furnaces are expected to yield benefits of about Rb130 million, according to the feasibility study.Construction of the Asbest magnesium plant, which will produce magnesium from asbestos tailings, is planned to begin at the end of 2005 in the Sverdlovsk region town of Asbest. Representatives of Switzerland's Minmet Financing, one of the founders of the plant, announced the plan at a meeting in Yekaterinburg with Sverdlovsk’s Regional Governor Eduard Rossel on September 30 2004. The main investor in the project is Minmet Financing Co, which holds a controlling interest in the plant, which was set up in April 2004. Anatoly Shchelkonogov, a prominent specialist in magnesium mining and processing who has been named general director of the venture, said that the plant would require about US$300 million of investment to achieve design capacity of 60,000 t/y of magnesium. Mr Shchelkonogov said construction would be split into three stages, with the first producing 20,000 t/y.Avisma’s magnesium operations continued in 2004. The company produced over 30,000 t of magnesium, of which more than 50% was recycled magnesium that is re-used to produce titanium sponge. Avisma is located at Berezniki in the Perm region. It is Russia’s largest producer of magnesium and the world’s largest producer of titanium sponge, with about 30% of the global output.Rusal, Russia’s biggest aluminum producer, will build a plant capable of producing 40,000 t/y of metallic magnesium in the Volgograd region. The company will carry out further exploration at a bischofite field this year and will complete a feasibility study for the magnesium plant. Rusal-Bishofit won a public tender in December 2004 for the right to develop the estimated 50 Mt field in the Gorodnishchensky district of Volgograd region. Rusal will use the magnesium to produce aluminum alloys. Rusal is planning to increase the amount of alloy that it produces by up to 50%. Output of cast-house alloys rose 33.5% to 740,000 t in 2003 and accounted for 27.8% of total aluminium output. Rusal produces more than 80 aluminium alloys.UkraineThe Ukraine has two magnesium plants, Zaporoshe and Kalush. The former has a rated capacity of 40,000 t/y and the latter 10,000 t/y. Both plants were shut down during 2004. However, restoration work was proceeding at the magnesium reduction plant at Kalush, with plans to produce 500 t/mth in early 2005.ONVI is a small company producing magnesium granules from scrap magnesium.KazakhstanThe Ust Kamenogorsk magnesium plant produced an estimated 14,000 t in 2004. The plant in eastern Kazakhstan, produces high-quality titanium sponge and magnesium. Belgium's Specialty Metals owns 66% and ZAO Central Securities Depository 7.3%.South AfricaMintek and its consortium partners, Anglo American plc, power utility Eskom Holdings, and South Africa’s Department of Science and Technology, has been working on the Mintek Thermal Magnesium Project for three years. The objective is to develop a continuous thermal process so as to minimise the number of operators required and to achieve efficiency gains.AustraliaMagnesium International Ltd (MIL) of Australia has confirmed Egypt as the location for a 88,000 t/y magnesium smelter. It will be owned and operated by a special purpose company, Egyptian Magnesium Co (Emag) that is currently being established by MIL and Amiral Investments (MIL’s partner in Egypt, under Egyptian investment laws). The specific site will be inside the new port at Ain Sokhna on the Gulf of Suez Sokhna is a relatively new port but is already the most efficient port in Egypt, with high operating standards. The port operator is Sokhna Port Development Co (SPDC), an affiliate of Amiral. As a port, Sokhna has the ability to handle and rapidly unload large bulk carriers (up to 150,000 dwt) for delivery of magnesite ore, and to ship magnesium in containers worldwide.LaTrobe Magnesium(formerly Rambora Technologies Ltd.) continues to work on a process to produce magnesium metal from ash produced at the LaTrobe Valley power generation plants in Victoria. Latrobe Magnesium decided to ‘change technology ships’, and will abandon plans to use magnesium smelting processes owned by Alcan and replace them with methods developed in Russia. The switch would lower the cost of a bankable feasibility study from US$32 million to US$15.5 million and reduce the time taken for the study from 29 months to 23 months. The process is in use at four magnesium production facilities around the world and eliminates the requirement to construct an expensive pilot-plant facility in Australia. La Trobe would use an existing pilot plant in Russia rather than building one.Sydney-based Quay Magnesium Ltd is building a new 30,000 t/y magnesium alloy plant in China. The plant is being built on the premise that the majority of Chinese primary metal requires further refining and beneficiation to meet high quality European alloy specifications for use in automotive and aeronautical applications. The alloying plant will be built in Nanjing and will produce high quality magnesium alloys. Quay plans to source primary magnesium metal from a number of local Chinese producers, thereby reducing capital costs and technical risks, whilst satisfying a higher end value die-casting market.Quay's plant is relatively simple and features a molten salt refining furnace, rather than the more typical steel crucible furnace, providing for a purer alloy. There is no chemical change involved with the alloying metals and the only physical changes are those associated with the heating and cooling of magnesium metal and its alloys. Quay's primary business will be as a manufacturer and marketer of magnesium alloys, a rapidly growing market. The company plans to produce high-quality European specification alloys that are keenly sought by die-casting companies targeting the automobile and aeronautical industries. .Hella Australia, has designed the Hella HydroLUX FF 1000 Submersible Driving Lamp System to meet the needs of mining, military and emergency services vehicles, as well as rugged off-road sport-utilities and pickup trucks. The new HydroLUX is the only light of its kind on the market to use Hella's Free Form reflector technology, which features a magnesium reflector, the same material used in Formula 1 racing cars and aerospace applications. The durable and fully submersible driving light is built to withstand the most extreme conditions.JapanJapan produced no magnesium in 2004, but had a number of industries producing fabricated parts from magnesium alloys. Kasatani Co has begun mass producing electronic equipment parts using magnesium alloys and recently began shipping parts for personal digital assistants. The new business will make use of existing facilities in Osaka.. It is initially making 10,000 components per month for portable digital assistants, with plans to raise output to 100,000 unitsper month by the end of 2005 to meet anticipated demand for mobile phone and personal computer components. The company targets magnesium alloy parts sales of 300 million yen in the first year. It aims to raise sales in the business to ¥1.2 billion yen in the year ending March 2007.Asahi Tec Corp has begun mass-producing magnesium steering members for supply to Nissan Motor Co. The steering member is part of the instrument panel, which in turn is part of the cockpit module fitted in the car. Steering members made from magnesium are around 40% lighter than those made from iron. Asahi Tec is mass-producing these parts at its Yokochi plant. The plant is making the steering members at a rate of around 5,000 units/mth and shipping them to Calsonic Kansei Corp. where they are used in the assembly of cockpit modules for Nissan's new luxury Fuga.ChinaChina must be given a more definitive treatment since it now produces 68% of the world’s magnesium. The Chinese Magnesium Association (CMA) has developed a reporting system that enables us better to understand the operation of the magnesium industry in China.China's magnesium production reached about 438,000 t in 2004, up 23% from the 354,000 t reported the previous year. China's magnesium exports were also on the rise last year, owing to the increase in output. Output growth in China has been strong. China exported about 383,748 t of magnesium in 2004, up from about 280,000 t reported in 2003. Most exports were to Europe, with a total of about 120,000 t, followed by Asian countries, including Japan and Korea, which accounted for around 65,000 t. Exports to the US from China were down to about 30,000 t in 2004, compared with 42,000 t in 2003. This decrease was due to the large preliminary antidumping duties placed on Chinese magnesium imports. China's domestic consumption reached about 80,000 t in 2004.Table 2: China’s magnesium capacity and production in 20003-04(’000 tonnes)2003 2004 Change% (Y-O-Y) Capacity 600 750 25182 248 36Primary Magnesium IngotoutputMagnesium Alloy 98.8 107 8.3Magnesium Granule (Powder) 68.5 78 13.9Others 4.7 5 6.3Total magnesium output 354 438 23.7Source: Antaike CMA。
镁合金研究现状及发展趋势

镁合金研究现状及发展趋势摘要:镁合金作为21世纪的绿色环保工程材料之一,近年来已成为学术界的一个研究热点。
本文主要综述了镁合金的研究进展和应用,介绍了耐热、耐蚀、阻燃和高强高韧等高性能镁合金材料的最新发展。
还介绍了镁合金成型技术的研究成果,最后展望了高性能镁合金的发展前景。
关键词:镁合金;高强高韧;成型技术;应用1.引言镁(Mg)是地球上储量最为丰富的元素之一,在陆地、湖泊和海洋中都广为分布,例如,其在地壳表层金属矿资源中的含量达2.3%,仅次于占8.1%的铝和5%的铁,居第三位;海水中的镁含量达到2.1×1015吨,可以认为是取之不尽、用之不竭的元素[1]。
此外,我国的白云石矿储量、菱镁矿以及原镁的产量位列世界镁资源储量首位[2]。
同时,随着当前钢铁行业中铁矿石等资源的日趋紧张,开发和利用镁作为替代材料是必然的趋势。
被誉为“二十一世纪绿色金属结构工程材料”的镁合金是目前所知金属结构材料中最轻的,与其他同类材料相比,它具有密度小,比强度、比刚度较高,可以回收再利用且机加工性能优异,阻尼减震性好,电磁屏蔽效果佳等一系列优点,因此在交通运输(如汽车、摩托车、自行车等工业)、航空航天、武器装备、计算机通讯和消费电子产品等领域具有广阔的应用前景[3],但其使用量与铝合金和塑料相比还相当少[4]。
目前,从全球镁合金研发状况看,发展方向如图1所示[5],我国在镁合金材料的应用研究与产业化方面也己取得重大进展,形成了从高品质镁材料生产到镁合金产品制造的完整产业链,为我国实现由镁资源大国向镁应用强国的跨越奠定了坚实的基础。
图1 镁合金的研发方向[5]Fig. 1 Directions of Mg alloy development2.镁合金的特点及分类通过在纯镁中添加其他化学元素,可显著改善镁的物理、化学和力学性能。
但镁合金同时存在着显著的缺点,下面对镁合金的优缺点进行简要的阐述。
2.1镁合金的优点[6 ~ 8]1)密度小、质量轻。
镁合金表面浸锌技术文献综述

镁合金表面浸锌技术现状和发展趋势1 镁及镁合金的特性镁属于元素周期表上的IIA族碱土金属元素。
其结构为密排六方晶格,无同素异构转变;熔点648.8℃,沸点1107℃ ,密度1.74 g/cm3。
镁是继氧、硅、铝、铁、钙之后地壳中第六位富有的元素,约占地壳重量的2.3%,镁的含量相当丰富[1]。
镁及镁合金具有银白色光泽,略有延展性。
并且镁及镁合金具有密度小、比强度和比刚度高、阻尼减震性和电磁屏蔽性好、易机械加工和再回收利用[2]。
与铝、锌、锆和稀土等构成的合金及热处理后强度大大提高。
其减震、降噪性能好,比强度高于铝合金和某些高强度钢。
其中,AZ31B更是以其抗冲击、减震性能好,可铸造性强,尺寸稳定性好,以及较好的机械性能和良好的电磁屏蔽性等优点脱颖而出[3]。
2 镁合金的应用现状镁基材料被誉为世纪最富于开发和应用潜力的“绿色材料”被广泛应用于航空航天、军事、交通及3C产品等领域中[4]。
交通工具轻量化成为当今发展趋势,镁合金是实际应用中最轻的金属结构材料。
非常适用于交通运输领域,是生产重量轻、油耗低、环保的新一代交通工具的最佳材料[5]。
目前,镁合金应用主要有以下三个方面:(1)汽车、摩托车等交通类产品用镁合金世界各大汽车公司已经将镁合金制造零件作为重要发展方向。
在欧美国家中,各国的汽车厂商正极力争取采用镁合金零件的多少来作为自身车辆领先的标志,大众、奥迪、菲亚特汽车公司纷纷使用镁合金[6]。
美、欧、日等发达国家投入大量人力和物力,实施多项大型联合研究发展计划,研究用镁合金制造汽车零部件。
这些研究开发计划促进了镁合金在汽车上应用的发展。
目前,镁合金压铸汽车零部件至少已超过90种,例如,已经使用要快速推广的零部件有轮毂、仪表盘、座椅框架、变速箱壳体、转向系统、汽缸盖、大的车体外部件、支撑柱、发动机箱体、油底盘。
其中,安装安全气囊的汽车都开始改用镁合金方向盘,这既可减重,又可降低震动,在发生意外撞击时,镁合金可吸收更多的能量,有利于保证驾驶员的安全。
镁合金资料文献

镁合金资料文献镁合金是实际应用中最轻的金属结构材料,它具有比重轻,比强度和比刚度高,阻尼性,导热性、切削加工型、铸造性能好,电磁屏蔽能力强,尺寸稳定,资源丰富,容易回收等一系列优点,所以,镁合金广泛应用也汽车工业,通讯电子业和航空航天业等领域,近年来镁合金产量在全球的年增长率高达20%,有极大的应用前景。
由于镁合金有极大的应用前景,所以在国内外掀起了一股研究镁合金的热潮。
在我国,镁资源及其丰富,我国是原镁生产大国,约占全球总产量的67%,而且是镁金属最大的出口国。
近年来,我国镁合金的研究和应用取得了举世瞩目的成绩,在高性能镁合金研究、加工装备开发以及镁合金深加工产品的开发应用方面都取得了很大的进展。
从镁产业的角度来讲,已经形成了从原材料到深加工一直到应用的完整产业链;从没研究开发的角度来讲,已经初步形成了从基础研究到应用研究一直到产品开发的完整科研开发体系,正从镁生产大国向镁研发和应用强国迈进。
但是,我国的镁工业仍然存在着很多问题:1)原镁生产技术落后,质量不稳定,镁中夹杂着大量有害元素,不满足很多生产工艺的技术要求;2)出口产品绝大多数是廉价的纯镁锭,利润低;3)原创性的研究成果太少。
镁合金产品加工中的关键技术和装备大部分靠国外引进。
2003年3月,科技部启动了“镁合金开发应用及产业化的前期战略研究,联合了4个研究院所,7所高校,20多家企业直接参与,建立了具有国际竞争力的镁合金高新技术产业群,将镁资源优势转化为经济优势!在863计划中,开展了包括耐热压铸镁合金及其应用技术,高强高韧镁合金及其技术开发,高性能变形镁合金及其应用技术,镁合金先进焊接技术,镁合金冲锻成型技术,镁合金锻造轮毂技术等研究。
而且,镁合金现在广泛应用于汽车行业。
国外的发展状态:北美、欧洲和日本等发达国家相继加大对镁合金开发和应用研究的投入。
德国1997年由联邦政府政府出资2500万马克的MADICA(Magnesium Die Casting)镁合金研究开发计划,主要研究压铸镁合金工艺、快速原型化与工具制造技术、切削加工技术,连接技术和半固态成形工艺。
镁合金文献综述
金属镁及其镁合金的制备与应用摘要:本文评述了金属镁的制备,镁合金的种类,以及镁及其镁合金的应用。
关键词镁镁合金制备应用镁是最轻的金属元素,其比重只有1.74,仅相当于铝的2/3,铁的1/4。
而且镁资源特别丰富,占地壳总重量的2.1%,海水中的o.13%,可谓取之不尽,用之不竭。
金属镁及其合金具有密度小、比强度和比刚度高、导电导热性能较好、阻尼减震和电磁屏蔽性能良好、易于加工成型、废料容易回收等优点[1],广泛应用于航天航空、交通运输、电子技术、光学器材、精密机械、日用商品等领域。
由此镁及镁合金获得“21世纪的绿色工程材料”的美誉[2]。
1.金属镁的制备金属镁的制备方法可分为两大类:电解法和热还原法。
1.1电解法炼镁[3-5]电解法的原理是电解熔融的无水氯化镁,使之分解成金属镁和氯气。
依据所用原料及处理原料的方法不同,可细分为以下具体的方法:道乌法、氧化镁氯化法、诺斯克法和光卤石法等[6]。
以下主要介绍氧化镁氯化法和光卤石法。
1.1.1 氧化镁氯化法利用天然菱镁矿,在700~800℃下煅烧,80%得到活性较好的轻烧氧化镁。
氧化镁的粒度要小于0.144mm ,然后与碳素混合制团,团块炉料在竖式电炉中氯化,制得无水氯化镁,直接投入电解槽,最后电解得金属镁。
制备MgCL2的程式为:2MgO+2CL2+C=2Mgcl2+CO2。
1.1.2 光卤石法将光卤石(Mgcl2·kcl ·6H2O )脱水后,直接电解制取金属镁。
光卤石脱水时水解反应不像Mgcl2那样严重,但也有一定的水解,因而在无水化的处理过程中,也需要氯化过程,由于加入了,需要经常清理电解槽。
1.1.3 电解法制镁存在的问题制备无水Mgcl2困难:在氯化镁的脱水过程中,由一水氯化镁脱水制取结晶氯化镁的过程极易水解,产生碱式氯化镁[Mg (OH )CL ]和氧化镁,生产工艺较难控制;在HCL 气氛下,水氯镁石脱水需要较高的温度(一般约为450℃),能耗大,设备腐蚀严重。
镁合金的组织结构、特性及应用综述
中国镁合金的组织结构、特性及应用2003/01/24摘自:新型材料的特性及其应用牌号热处理制度组织结构特性及应用MB2M状态:冷轧退火300~350ºC,300minα(镁基固溶体)+ Mn-Al 化合物质点+Mg17Al12 (片状)。
热压棒、型材为再结晶组织,退火均为再结晶组织是一种不可热处理强化的变形镁合金(Mg -Al –Zn系);它的热塑性良好,切削加工性、焊接性好,应力腐蚀倾向小,主要用于航空发动机零件以及其他复杂的锻件等制品MB3M状态:板材退火温250~300ºC,300min合金中Al、Mn含量偏高,板材易产生锰的偏析物(Al- Mn化合物),它对合金的力学性能无明显影响,但使抗蚀性能下降,正常的微观组织为中等晶粒再结晶组织,晶界残存Mg17Al12属于不可热处理强化的Mg -Al –Zn系变形镁合金,室温强度较高,切削性良好,焊接性合格。
但有应力腐蚀倾向,故必须表面氧化处理及涂漆防护。
合金以冷(热)轧退火状态供应。
主要制造导弹蒙皮和壁板,长期工作温度:150ºC,短期200ºCMB8R状态:热轧、热挤压、热锻状态M状态:冷轧板退火:300ºC,300minY2状态:半冷作硬化,240ºC,300min合金中锰含量偏高,易出现锰的偏析物,其结构为ßMn及含有Fe、Al 等杂质。
微观组织中因Ce含量少,难以见到Mg9 Ce属于Mg-Mn系不可热处理强化的变形镁合金;添加铈可细化晶粒和改善力学性能;它的切削加工性及焊接性良好,没有应力腐蚀倾向。
用于制作飞机蒙皮、壁板及汽油和滑油系统附件MB15S状态:热挤压后人工时效,170ºC,10h,空冷,热锻后人工时效,150ºC,合金中加入锆,晶粒组织细密。
铸态高倍组织的晶界区为亮灰色镁锌化合物。
局部区域有时也出现锆的偏析物(Zn-是Mg-Zn-Zr系,可热处理强化的高强度变形镁合金,它的强度高,其σb、、σs、δ 、αh 优于其他镁合金,综合性能好,切削性能优良,24h,空冷Zr化合物)。
Mg-Gd系镁合金的研究进展
Mg-Gd系镁合金的研究进展98材料导报:综述篇20O9年6月(上)第23卷第6期Mg-Gd系镁合金的研究进展孙明h,吴国华,王玮,侯正全.,陈斌.,丁文江h(1上海交通大学轻合金精密成型国家工程研究中心,上海200240;2上海交通大学金属基复合材料国家重点实验室,上海200240;3上海航天精密机械研究所,上海201600)摘要Mg-Gd系镁合金由于具有高比强度,优良的室温强度和抗蠕变性能而成为研究的热点.介绍了其合金化基础,组织特性;总结了主要稀土合金元素,非稀土元素的影响作用,包括Gd,Y,Nd,La,Ce,Mn,Zr,Zn,Ag等;讨论了合金系的时效行为.在综述国内外研究现状的基础上,对其未来发展进行了展望.关键词Mg-Gd镁合金时效ResearchProgressofMg-GdAlloySUNMing,WUGuohua,WANGWei,HOUZhengquan.,CHENBin..DINGWenjiang'(1NationalEngineeringResearchCenterofLightAlloyNetForming,ShanghaiJiaotongUni versity,Shanghai200240;2StateKeyLaboratoryofMetalMatrixComposites,ShanghaiJiaotongUniversity,Shangha i200240;3ShanghaiInstituteofAerospacePrecisionMachinery,Shanghai201600) AbstractItisreportedthatMg-Gdalloysbecomepopularinrecentyearsbecauseofhighspecif icstrengthat bothroomandelevatedtemperaturesandgoodcreepresistance.Thealloyingbasisandmicro structurecharacteristicareintroduced.TheeffectofmainalloyingdementssuchasGd,Y,Nd,La,Ce,Mn,Zr,Zn,Agetc.aresumma—rizedaccordingtoresearchduringrecentyears.BasedoncurrentstateofresearchonMg-Gdal loy,thedevelopmentprospectispresented.KeywordsMg-Gd,magnesiumalloys,aging0引言镁合金作为最轻的金属结构材料,在汽车工业,通讯电子业和航空航天业等领域正得到日益广泛的应用_1.].Mg}-Gd系合金具有较稳定的低蠕变速率和较高的蠕变抗力,其优异的室温和高温力学性能甚至超过成功的商用WE43和QE22合金[3"],得到了国内外研究者的广泛关注,例如Mg-10Gd_5Y-O.5Mn合金和Mg-10Gd-3Y-0.4Zr合金,其室温和高温比强度,耐热,蠕变抗力均优于传统的A1,Mg合金_5].本文综述了近年来国内外关于Mg-Gd镁合金的研究状况.1简单的Mg-Gd二元合金稀土元素Gd的相对原子质量为157.25,密度为7.89g/cm3,熔点为1312℃,是重稀土元素的代表.Gd在镁中的平衡固溶度相当高,548℃时原子固溶度为4.53(质量固溶度为23.5%),形成熔点为640℃的共晶相MgGd,而且强化相在250℃时仍然具有较高的热稳定性_6],因此加入稀土Gd的镁合金具有优异的固溶强化效应和耐热性.并且随着温度的降低,其平衡固溶度呈指数迅速降低,200℃时原子固溶度仅为0.61(质量固溶度为3.82),形成理想的析出强化体系.根据Mg-Gd二元相图,Mg与Gd形成的化合物有MgGd,Mg.Gd,MgGd和MgGd4种,它们在平衡凝固时的形成温度分别为658℃,720℃,756℃,868℃.如果合金在平衡凝固条件下凝固,Mg-Gd合金的室温凝固组织就应为旷Mg固溶体+MgGd析出相.但由于实际凝固时,凝固速度较快,溶质原子来不及再分配,故凝固过程是在非平衡状态下进行的,其实际凝固组织也要偏离平衡组织.合金在非平衡凝固过程中有可能偏析形成MgaGd,MgzGd,MgGd等相[7].Jakub的研究表明,挤压铸造Mg-15Gd合金中过饱和富Gd固溶体的分解序列为:(Do.)一p(cbco)--~(fcc),其中亚稳B相的形成引起了强化,位错促进了析出相的形核.2稀土元素对Mg-Gd系合金组织与性能的影响2.1GdGd是提高镁合金耐热性能的有效元素.Mg-Gd系具有较好的高温蠕变抗力,在挤压,淬火及时效硬化下,均发现室温和高温抗拉强度随Gd含量的增加而提高.然而,Gd的*国家973资助项目(2007CB613701);上海市优秀学科带头人计划(08XD14020) 孙明:男,1982年生,博士研究生,从事镁合金研究E-mail:****************** Mg—Gd系镁合金的研究进展/孙明等?99?质量分数低于1O的二元Mg-Gd合金在等温时效或等时时效过程中,过饱和固溶体仅仅显示出较微弱的时效强化效应,甚至无时效强化效应;而增大Gd的质量分数至2O可提高合金的硬度和强度l8].合金在150~250℃时效,Gd的质量分数越高,最大硬度越大,且达到最大硬度的时间也越短,15Gd和20Gd合金时效硬化显着.RokhlinL6]和Ka—madoE]发现Mg-20(质量分数)Gd合金的高温强度优于传统耐热镁合金wE54A.通过适宜的热处理,Mg.Gd合金有望发展成为新型轻质,超强耐热镁合金.图1为200℃,一6OMPa时Mg—Gd二元合金的蠕变速率与WE43,QE22T6的对比图j.1E尝1E§0誊1E盆1E.734.1jIE.【E一1O隰hf'1.21E—l0圉一图1Mg-Gd二元合金蠕变速率与WE43,QE22的对比Fig.1ComparisonofthesecondarystrainrateforbinaryMg-Gdalloys图2为不同Gd含量Mg-xGd-3Y-0.5Zr合金的400倍光学组织,其中图2(a)一6,(b)z一10,(c):12,(d)为A点第二相EDS.由图2可知,Gd添加量对合金的晶粒尺寸没有明显的影响,只是随着稀土总含量的增加,晶界上第二相体积分数明显增大,第二相组成是Mg2(Gd,Y)(bcc,晶格常数a一11.2A)[1.gA点:Mg.Gd-YElementwt/%at/%:器GdL34.017.90Total1O0.0010o.00Y,.图2Mg-xGd-3Y-0.5Zr合金的显微组织Fig.2MicrostructureofMg-xGd-3Y-0.5ZralloysChangDz~对峰时效后的Mg-xGd-3"2"-0.4Zr合金进行腐蚀研究表明,随Gd含量由6增加到1O,合金的腐蚀抗力逐渐降低,但随Gd含量由1O增加到12,合金的腐蚀抗力又逐渐增加,耐腐蚀性的不同是因为时效析出的B相含量不I司.2.2YGd,Y与Mg同属密排六方晶体结构,二者在镁中的质量固溶度分别为23.50A,12.O.虽然Gd具有比Y更高的时效硬化特性,但单纯加Od的镁合金成本太高,密度更大,室温延伸率过低E133.2O世纪8O年代DritsE"在Mg-10Gd_ 0.6Mn合金中加入6的Y,使合金的室温强度由340MPa提高到440MPa,300℃的强度由17OMPa提高到23OMPa. Rokhlin等[1明使用了价格较便宜,密度较小,在镁中固溶度较低的Y代替部分Gd,发展了Mg-G&Y合金.三元Mg-Gd-Y 合金的铸态组织由基体a-Mg-t-l~-网状枝晶组成,不同稀土含量并没有造成合金微观组织本质上的区别,口是MgGd,MgY以及由这两者构成的连续固溶体Ll"].随着稀土含量的增加,枝晶之间和晶界上的这些富溶质相比例增大.增加Y含量能增强时效硬化作用,提高拉伸强度E17,183.Mg-7Gd-3Y合金具有较好的时效硬化响应和高的力学性能[1.Mg-10Gd-5Y-0.4Zr合金在峰时效表现出的最大抗拉强度和屈服强度分别为:室温时302MPa,289MPa,250℃时340MPa,267MPa_1.Mg-10Gd-0.6Mn-Y合金随着Y含量增加至8,强度一直提高,延伸率却一直下降,8Y合金的延伸率下降到未加Y时的5O%,为了保持强度和延伸率的结合,Mg-10Gd-0.6Mn-Y合金的Y含量最好为4~6[】43.对Mg-8Gd-0.6Zr-xNd-yY(x+一3)合金的研究表明,Y主要提高韧性,Nd提高硬度,随着Y含量的增加,沿着晶界的共晶区域增大u.2.3Nd稀土元素Nd是La系中比较活泼的元素之一,是轻稀土元素的代表,Nd在镁中的固溶度非常小,最大质量固溶度仅为3.6(原子固溶度为0.63),随温度降低,Nd在镁中的固溶度迅速减小.与Gd类似,Nd与Mg形成的化合物也可在低温时效析出.Mg-Gd-Nd在250~C时具有高的时效硬化响应与Do.结构的相有关.Mg-8G&0.6Zr-xNd(—O,1,2,3)铸态显微硬度随着Nd含量的增加而提高,加Nd后时效硬化行为和力学性能显着增强[2引.2.4其他稀土元素Ho对Mg-8Gd-0.6Zr-xHo(x一1,3,5)合金的研究表明,co(Ho)一3时峰时效硬度最高,高出Mg-8Od-0.6Zr合金3O,达到最大抗拉强度和屈服强度:室温时为279MPa, 175MPa,250℃时为191MPa,131MPa.强度提高是由于细小BMg(Gd,Ho).亚稳析出相的出现[2.Sc添加Sc至Mg-10G&0.6Mn合金中,使300℃时的强度增加[1.La,CeMg-8Gd-0.6Zr添加1的La或Ce减小了枝晶臂间距,轻微提高了力学性能和时效硬化响应.在峰时效硬度下Mg-8Gd_0.6Zr-lCe合金显示出最大屈服强度和抗拉强度,室温时为146MPa,17OMPa,250℃时为90MPa,135MPa,高出Mg-8Gd-0.6Zr合金1O.力学性能的提高是因为亚稳~'-Mg15RE3(RE=Ce/C_,,d),O-MgsRE,13-Mg2RE 析出相的出现_2.100?材料导报:综述篇2009年6月(上)第23卷第6期3非稀土元素对Mg-Gd系合金组织性能影响3.1MnMn元素能提高镁合金的耐热性,耐腐蚀性[1,含Mn的Mg_Gd-Y合金室温力学性能优异,Mn与稀土元素可能形成金属间相,在镁合金热加工的组织结构演变中发挥作用.含Mn变形镁合金适宜通过T6处理来提高其综合拉伸力学性能[26].Rokhlin开发了Mg-10Gd-5Y-0.5Mn合金,其力学性能较好,但在挤压T5态下室温延伸率只有4[1.肖阳发现Mg-9G&4Y-0.6Mn合金在400℃时产生超塑性现象,延长率达266(见表1).在Cast-T5,Cast-T6,Rolled-T5和Rolled—T6的4种热处理状态中,Rolled—T5态的硬度最高[2.3.2ZrZr作为镁合金的晶粒细化剂,发展了一系列重要的商用镁合金,包括砂型铸造抗蠕变汽车发动机部件.2O世纪90年代,Kamado在Mg-Gd-Y合金中使用Zr代替Mn设计了Mg-10Gd-4Y一0.4Zr,其力学性能优异n.3.表2为Mg-Gd-YZr合金的性能.表1Mg-9Gd-4Y-O.6Mn合金Rolled-T5态的拉伸性能Table1TensilepropertiesofMg-9Gd一4Y-0.6Mnrolle&T5alloy性能测试温度/℃25250300350400对Mg-9Gd-4Y-0.6Zr合金高温拉伸超塑性的研究表明,在温度高于623K时的延展性归因于基面和非基面位错滑移.673K超塑性变形包括3个阶段:第1阶段是由位错滑移和孪生引起的塑形变形;第2阶段是由动态再结晶控制的晶粒细化;第3阶段包括2个过程,即晶粒细化过程和细晶生长过程.表2Mg-Gd-Y-Zr合金的性能Table2TensilepropertiesofMg-Gd-Y-Zralloy3.3ZnSuzuki指出,Zn加入到镁合金中降低了堆垛层错能及位错的可动性,使位错限制在基面滑移,在55O~600K高温时可抑制非基面滑移,有利于提高合金的蠕变强度[3.Zn的加入产生了长周期结构(LPS),LPS结构是富Y,Zn层的周期性堆垛,Y和Zn富集在相同的基面,降低了Y原子周围的应力集中,LPS相是强化相,对强度有贡献[3.Nie[3]在Mg-6Gd-Zr合金中加入1%~2%(质量分数)的Zn,显着提高了室温强度和175℃时的蠕变强度,这与加入Zn后使得Mg5Gd分布相致密均匀有关.Mg-Gd-Y合金加入Zn后,降低了Gd,Y的固溶度,使得第二相的体积分数增加,由骨骼状变为相互连结的网状[3.Mg-12G&4Y-1Zn-0.5Zr经370℃热挤压后200℃×70h 时效,在挤压态显微组织发现2种分别呈层片状和块状的非平衡相,为Mg(Gd,Zn)和Mg(Gdo.,Y0.),室温抗拉强度显着提高,且具有良好的延伸率[3.u[3]在Mg-10Gd-3Y-0.5Zr合金中加入1的Zn,大大提高了时效强化效果,力学性能和耐热性,加入Zn前后的力学性能对比如表3所示.表3GW103和GWZ1031的室温力学性能Table3TensilepropertiescomparisonsbetweenGW103 andGWZ1031alloysatroomtemperature温度性能GW103合金UrSTYSELMPaMPa%GWZ1031合金UTSISELMPlaMPa%As-extruded2901921334723l1lCast—T6.225℃34823733642532Extruded—T5.250℃341228l13822559Extruded—T5.225oC38326194062856Extmded—T5.200℃39731154283394T5,secondaryageing39529774213216Tip:UTS=Ultimatetensilestrength;TYS=Yieldtensilestrength;EL=Elongation3.4其它合金元素分别添加si,,Sn,CA至Mg-10Gd-o.6Mn合金,经过2OO~C时效24h,测试20~C和300oc的力学性能,发现使室温强度增加的元素为:CA,含量大于0.6的Zn,含量大于0.1%的Sn;使300"C强度增加的元素为:含量大于0.1AI:"].Mg-Gd系镁合金的研究进展/孙明等?1O1?添加Ag可提高Mg-Nd合金力学性能,发展了商用QE22(Mg-2.5Ag-2Nd-0.7Zr)合金,但在Mg-Gd合金中添加Ag的报道则不多.Nie在Mg-6Gd-0.6Zr合金中添加Ag,或联合添加Ag+Zn使时效硬化效果得到显着增强,硬度峰值出现在200~250℃等温时效Mg-6Gd-2Ag-lZn-0.6Zr合金,这归因于纳米级析出相的致密均匀分布[3.添加0.4Ca至Mg-10Gd-3Y-O.5Zr合金,对铸态组织和晶粒尺寸影响甚微,对强度影响也较小,但会严重恶化延伸率;对合金挤压后的强度也没有提高,反而使合金脆化_1.4合金固溶和时效行为的研究早期对于二元Mg-Gd合金时效析出序列研究为"三阶段析出序列":过饱和固溶体(s.s.S.S.)一(Do.)一p(cb—eo)-+13(MgGd,fcc),不同于Mg-Y合金的过饱和固溶体(S.S.s.S.)一(cbco)--~(cbco)一8(Mg24Ys,bcc)_3.Kama—do[13]指出Mg-Gd-Y-Zr合金"三阶段析出序列"为(S.S.S. S.)一(DO19)一p(cbco)--~(bcc),类似于二元Mg-Y合金.Nie[s9]在WE54合金250℃等温时效时发现B一p转变之间存在中间相(fec),p同样在时效Mg-Gd-Nd合金中存在.最近,Honma等_4叩使用原子探针分析Mg-Gd-Y_Zr析出相化学成分,发现相成分;~JMg.X,p相成分为Mgx(其oex=Gd+Y).合金固溶一时效行为是近年来研究的热点,表4为部分文献的研究结果.最近,何上明l_1系统地研究了Mg-Gd—Y_Zr 合金铸态,T4态,T6态,挤压一T5态的组织演变,性能和断裂行为,由铸态到T4态再到T6态组织变化为:固溶体+共晶相一过饱和固溶体+方块相一固溶体+B析出相+方块相,其时效硬化曲线和力学性能如图3所示,指出,对于高稀土含量的Mg-10Gd-3Y-0.5Zr和Mg-13Gd-3Y-0.5Zr合金, 250℃时效可以在牺牲部分强度指标的情况下获得较高的强度和延伸率组合;若只要求强度指标时,低稀土含量的Mg-6Gd-3Y-0.5Zr和Mg-8Gd一3Y-0.5Zr合金的最优时效温度是200℃,而高稀土含量的Mg-10Gd-3Y-0.5Zr和M13Gd一3Y_ 0.5Zr合金的最优时效温度是225℃.在250~300℃时效,Mg-7Gd-2.25Nd-0.6Zr比Mg-4Y-2.25Nd-0.6Zr,Mg-TDy-2.25Nd-0.6Zr具有更快更强的300℃时效硬化响应_2.Peng系统研究了Mg-Gd-Nd合金的组织与性能,如表5所示.表4Mg-Gd-X合金固溶,时效组织演化Table4Solid-solutionandagingbehaviorsaboutMg-Gd-Xalloys合金固溶+时效条件时效抗拉强度和屈服强度强化因素文献Mg-Gd-Nd合金在时效过程中主要生成,p,和p析出相l7引,典型析出相的TEM如图4所示.在这些析出相中,,p和pt相均为亚稳相而p相为平衡相.细微片状或棒状析出相在镁基体的{1120)面族析出,为DO.超结构,晶格常数口一2a~=0.64nm,C—c№一0.52nm在已有的析出相上形成的球形析出J3为底心立方结构(bco),晶格常数a=2a~=0.64nm,b一2.2rim,C一№一0.52nm,与镁基体取向的关系为[OO1]8,//[0001],[010]~//[10i0],{100}#//{ll2O},在{1010)面析出并存在3种方向变体.进一步时效,在镁基体的{1010}面形成具有面心立方结构的片状析出口相,其晶格常数为0.74nm,这与Nie和Muddle在102?材料导报:综述篇2009年6月(上)第23卷第6期WE54(Mg-Y-Nd)合金中观察到的B相的特征一致.Apps[21]认为p的形核与和p有关,延长时效时间,则p.以和p为代价生长.同时观察到向平衡相p发生原位转变,2个不同析出相的区域分界明晰可见,并通过微衍射进一步确定其分别为p和B.平衡相p具有面心立方(fcc)结构,晶格常数为2.2nm[7]..12OlOO8O60.GW123K—GW103K+0.4Ga-一G15K—-—一GWlO3K-e-GW83K.-,e-GW63K—W8KJsl-quenched~.fl专日Agingtime/h(a)MG—Gd-Y-zr台金200~C的时效硬化曲线日400譬∽:300200o100(b)峰时效Mg一10Gb一3Y-0.36Zr~金的室温力学性能图3Mg-Gd-Y-Zr合金的时效硬化曲线与力学性能Fig.3a#ngClll~es(a)andmechanicalproperties(b)OfMg-GY-Zralloy(a)300~Cx48h时效B析出相(b)30O℃×30min时效p析出相图4Mg-7Gd-2.25Nd-0.6Zr合金时效析出相分布Fig.4PrecipitatedistributioninMg-7Gd-2.25Nd-0.6ZralloyZhengE研究了预变形对Mg-11Gd-2Nd-0.5Zr合金时效特性和力学性能的影响,预变形试样在200~C表现出快速时效动力,在200~C时效24h,不仅在基体有多种析出相,而且在孪晶界有多种析出相;预变形提高了强度,但降低了韧性.5结束语Mg-Gd系合金作为耐高温镁合金,在航空航天,武器装备等领域具有广阔的应用前景.但高含量的重稀土元素将提高材料的密度和增大成本,故应优化合金成分,加强研究合金元素对Mg-Gd合金组织与性能的影响;优化合金制备工艺,减少稀土的损耗;Zr有着细化晶粒的作用,但其收得率低,且价格较贵,应深入研究Zr在熔体中的行为;时效析出相对合金的高强度化,耐热化起着重要作用,应加强热处理, 热加工,固态成型等过程研究;研究合金在高温环境的服役情况,为应用提供参考.参考文献1张丁非,彭建,丁培道,等.镁及镁合金的资源,应用及其发展现状[J].材料导报,2004,18(4):722WangYingxin,GuanShaokang,XiaoqinZeng.eta1.Effects ofREonthemicrostructureandmechanicalpropertiesofMg-8Zn-4AImagnesiumalloy[J].MaterSciEngA,2006,416(1-2):1093MordikeBL.Creep-resistantmagnesiumalloys[J].Mater SciEngA,2002,324(1-2):1034SmolaB,StulikovdI,V onBuchF.eta1.Structuralaspects ofhighperformanceMgalloysdesign[J].MaterSciEngA,2002,324(1—2):1135Y angZ,LiJP,GuoYC,eta1.Precipitationprocessand effectonmechanicalpropertiesofMg-9Gd-3Y-0.6Zn-O.5Zr alloy[J].MaterSciEngA,2007,454—455:2746RokhlinLL.Magnesiumalloyscontainingrareearthmetals [M].London:TaylorandFrancis,20037谢中柱.Mg-Gd-Nd系合金析出相的电子显微研究[D].北京:北京工业大学,20078JakubCi~ek,IvanProchdzka,BohumilSmola,eta1.Inf- luenceofdeformationonprecipitationprocessinMg-15wt%Gdalloy[J].JAlloysCompd,2007,430(1-2):929蒋浩.Mg-Gd-Y耐热镁合金材料及其热处理研究[D].长沙:中南大学,200610KamadoS,1wasawaS,Ohuchi,K.eta1.Aginghardening characteristicsandhightemperaturestrengthofMg-GdandMg-Tballoys[J].JJphInstLightMetals,1992,42(12):72711何上明.Mg-Gd—Y-Zr(一Ca)合金的微观组织演变,性能和断裂行为研究[D3.上海:上海交通大学,200712ChangJianwei,GuoXingwu,HeShangming,eta1.Investi—gationofthecorrosionforMg-xGd-3Y-0.4Zr(一6,8,10,12wt)alloysinapeak-agedcondition[J].CorrosSci,2008,50(1):16613KarnadoS,KojimaY,NinomiyaR,eta1.Agingcharacteri- sticsandhightemperaturetensilepropertiesofmagnesium alloyscontainingheavyrareearthelements[C]//LorimerGW.Proceedingsofthe3rdInternationalMagnesiumConfe-renc~Manchester:InstituteofMaterials,1997:32714DritsME,SviderskayaZA,RokhlinLL,eta1.Effectof alloyingonthepropertiesofMg-Gdalloys[J].MetallSci HeatTreat,1979,21(11):88715RokhlinLL,NikitinaNLMagnesium-gadoliniumandmag—nesiurn-gadolinium-yttriumalloys[J].zMetallkd,1994,85:Mg-Gd系镁合金的研究进展/孙明等?1O3?8l916赵娟.Mg-Gd-Y系合金相图的热力学计算验证及其应用ED].西安:西安工业大学,200717PengQM,WuYM,FangDQMicrostructuresandpro- pertiesofMg-7GdalloycontainingY[J].JAlloysCompd,2007,430(1-2):25218WangJun,MengJian,ZhangDeping.eta1.EffectofYfor enhancedagehardeningresponseandmechanicalproperties ofMg-Gd-Y-Zralloys[J].MaterSciEngA,2007,456(1—2):7819PengQiuming,WangJianli,WuY aoming,eta1.Micro—structuresandtensilepropertiesofMg-8Gd_0.6Zr-xNd-yY (+一3,mass%)alloys[J].MaterSciEngA,2006,433(1-2):13320AppsPJ,KarimzadehH,KingJF,eta1.Precipitationre.a- ctionsinmagnesium-rareearthalloyscontainingyttrium, gadoliniumordysprosium[J].SetMater,2003,48(9):1023 21AppsPJ,Karim_zadehH,KingJF,eta1.Phasecomposi—tionsinmagnesium-rareearthalloyscontainingyttrium, gadoliniumordysprosium[J].ScrMater,2003,48(5):475 22NegishiY,NishimuraT,KiryuuM,eta1.Phasediagrams ofmagnesium-richportion,agingcharacteristicsandtensile propertiesofMg-heavyrareearthmetal(Gd,Dy)一Ndalloys [J].JJpnInstLightMetals,1995,45(2):5723PengQiuming,WuY aoming,FangDaqing,eta1.Micro—structuresandmechanicalpropertiesofMg-8Gd-0.6Zr-xNd (一0,1,2and3mass)alloys[J].JMaterSci,2007,42 (11):390824PengQiuming,DongHanwu,WangLidong,eta1.Aging behaviorandmechanicalpropertiesofMg-Cd-Hoalloys[J]. MaterCharact,2008,59(8):98325PengQiuming,WangJianli,WuY aoming,eta1.Theeffect ofLaorCeonageingresponseandmechanicalpropertiesof castMg-Gd-Zralloys口].MaterCharact,2008,59(4):435 26张新明,陈健美,邓运来,等.Mg-Gd-Y-(Mn,Zr)合金的显微组织和力学性fl~EJ].中国有色金属学报,2006,16(2): 21927肖阳,张新明,陈健美,等.Mg-9Gd-4Y-0.6Mn合金的微观组织与力学性能[J].材料热处理学报,2007,28(2):4428童炎,王渠东,高岩,等.Mg-13Gd-3Y-0.4Zr合金热处理工艺优化及其性能[J].轻金属,2007,(3):4529肖阳,张新明,陈健美,等.高强耐热Mg-9Gd-4Y-0.6Zr合金的性能[J].中南大学学报(自然科学版),2006,37(5): 85030HeSM,ZengXQ,PengLM,eta1.Microstructureand strengtheningmechanismofhighstrengthMg-10Gd一2Y_ 0.5Zralloy[J].JAlloysCompd,2007,427(1-2):316,)(上接第97页)3OKimSH,Y ouBS,YimCD,eta1.Textureandmicrostruc—turechangesinasymmetricallyhotrolledAZ31magnesium alloysheets[J].MaterLett,2005,59(29—30):387631WatanabeH,MukaiT,IshikawaK.Effectoftemperatureof differentialspeedrollingonroomtemperaturemechanical31XiaoY ang,ZhangXinming,DengYunlai,eta1.Superplas—ticityofMg-Gd-Y alloyintensiletestatelevatedtempera—tureEJ].TransNonferrousMetSocChina,2007,17(6):s37232SuzukiM,KimuraT,KoikeJ,eta1.Strengtheningeffect ofZninheatresistantMg-Y-Znsolidsolutionalloys[J]. ScrMater,2003,48(8):99733HonmaT,OhkuboT,KamadoS,eta1.EffectofZnaddi—tionsontheage-hardeningofMg-2.0Gd-1.2Y-0.2Zralloys[J3.ActaMater,2007,55(12):413734NieJF,GaoX,ZhuSMEnhancedagehardeningresponseandcreepresistanceofMg-GdalloyscontainingZnEJ].Scr Mater,2005,53(9):104935李杰华,介万奇,杨光昱,等.合金化元素Zn对GW系镁合金组织和力学性能的影响EJ].金属学报,2007,43(10): 107736郭永春,刘涛,李建平,等.Mg-12Gd-4Y-1Zn-0.5Zr合金的显微组织和力学性能EJ].西安工业大学学报,2007,27 (3):24237LiuXB,ChenRS,HanEH.Effectsofageingtreatment onmicrostructuresandpropertiesofMg-Gd-Y-Zralloys withandwithoutZnadditions[J].JAlloysCompd,2008,465(1—2):17338GaoX,NieJF,Enhancedprecipitation-hardeninginMg-Gd alloyscontainingAgandZn[J].ScrMater,2008,58(8):61939NieJF.MuddleBC.Characterisationofstrengtheningpre—cipitatephasesinaMg-Y-Ndalloys[J].ActaMater,2000,48(8):169140HonmaT,OhkuboT,HonoK,eta1.Chemistryof nanoscaleprecipitatesinMg-2.1Gd-0.6Y-0.2Zr(at)al—loyinvestigatedbytheatomprobetechnique[J].MaterSci EngA,2005,395(1-2):30141HeSM,ZengXQ,PengLM,eta1.PrecipitationinaMg-10Gd-3Y-0.4Zr(wt0A)alloyduringisothermalageingat250~C[J].JAlloysCompd,2006,421(1—2):30942GaoY an,WangQudong,GuJinhai,etakBehaviorofMg-15Gd-5Y-0.5Zralloyduringsolutionheattreatmentfrom500to540"C[J].MaterSciEngA,2007,459(1—2):11743PengQiuming,HouXiuli,WangLidong,etatMicrostruc—tureandmechanicalpropertiesofhighperformanceMg-Gdbasedalloys[J].MaterDes,2009,30(2):29244ZhengKY,DongJ,ZengXQ,eta1.Effectofpre-defor_ mationonagingcharacteristicsandmechanicalpropertiesof aMg-Gd-N&Zralloy[J].MaterSciEngA,2008,(1-2): 103(责任编辑曾文婷)propertiesandtextureinanAZ31magnesiumalloy[J].J MaterProcTechn,2007,182(1—3):64432WatanabeH,MukaiT,IshikawaK.Differentia1speedrolling ofanAZ31magnesiumalloyandtheresultingmachanical properties[J].JMaterSci,2004,39(4):1477(责任编辑林芳)。
镁合金文献综述
金属镁及其镁合金的制备与应用陈少华(中南大学冶金科学与工程学院,湖南长沙 410012)摘要:本文评述了金属镁的制备,镁合金的种类,以及镁及其镁合金的应用。
关键词镁镁合金制备应用镁是最轻的金属元素,其比重只有1.74,仅相当于铝的2/3,铁的1/4。
而且镁资源特别丰富,占地壳总重量的2.1%,海水中的o.13%,可谓取之不尽,用之不竭。
金属镁及其合金具有密度小、比强度和比刚度高、导电导热性能较好、阻尼减震和电磁屏蔽性能良好、易于加工成型、废料容易回收等优点[1],广泛应用于航天航空、交通运输、电子技术、光学器材、精密机械、日用商品等领域。
由此镁及镁合金获得“21世纪的绿色工程材料”的美誉[2]。
1.金属镁的制备金属镁的制备方法可分为两大类:电解法和热还原法。
1.1电解法炼镁[3-5]电解法的原理是电解熔融的无水氯化镁,使之分解成金属镁和氯气。
依据所用原料及处理原料的方法不同,可细分为以下具体的方法:道乌法、氧化镁氯化法、诺斯克法和光卤石法等[6]。
以下主要介绍氧化镁氯化法和光卤石法。
1.1.1 氧化镁氯化法利用天然菱镁矿,在700~800℃下煅烧,80%得到活性较好的轻烧氧化镁。
氧化镁的粒度要小于0.144mm ,然后与碳素混合制团,团块炉料在竖式电炉中氯化,制得无水氯化镁,直接投入电解槽,最后电解得金属镁。
制备MgCL2的程式为:2MgO+2CL2+C=2Mgcl2+CO2。
1.1.2 光卤石法将光卤石(Mgcl2·kcl ·6H2O )脱水后,直接电解制取金属镁。
光卤石脱水时水解反应不像Mgcl2那样严重,但也有一定的水解,因而在无水化的处理过程中,也需要氯化过程,由于加入了,需要经常清理电解槽。
1.1.3 电解法制镁存在的问题制备无水Mgcl2困难:在氯化镁的脱水过程中,由一水氯化镁脱水制取结晶氯化镁的过程极易水解,产生碱式氯化镁[Mg (OH )CL ]和氧化镁,生产工艺较难控制;在HCL 气氛下,水氯镁石脱水需要较高的温度(一般约为450℃),能耗大,设备腐蚀严重。
- 1、下载文档前请自行甄别文档内容的完整性,平台不提供额外的编辑、内容补充、找答案等附加服务。
- 2、"仅部分预览"的文档,不可在线预览部分如存在完整性等问题,可反馈申请退款(可完整预览的文档不适用该条件!)。
- 3、如文档侵犯您的权益,请联系客服反馈,我们会尽快为您处理(人工客服工作时间:9:00-18:30)。
金属镁及其镁合金的制备与应用摘要:本文评述了金属镁的制备,镁合金的种类,以及镁及其镁合金的应用。
关键词镁镁合金制备应用镁是最轻的金属元素,其比重只有1.74,仅相当于铝的2/3,铁的1/4。
而且镁资源特别丰富,占地壳总重量的2.1%,海水中的o.13%,可谓取之不尽,用之不竭。
金属镁及其合金具有密度小、比强度和比刚度高、导电导热性能较好、阻尼减震和电磁屏蔽性能良好、易于加工成型、废料容易回收等优点[1],广泛应用于航天航空、交通运输、电子技术、光学器材、精密机械、日用商品等领域。
由此镁及镁合金获得“21世纪的绿色工程材料”的美誉[2]。
1.金属镁的制备金属镁的制备方法可分为两大类:电解法和热还原法。
1.1电解法炼镁[3-5]电解法的原理是电解熔融的无水氯化镁,使之分解成金属镁和氯气。
依据所用原料及处理原料的方法不同,可细分为以下具体的方法:道乌法、氧化镁氯化法、诺斯克法和光卤石法等[6]。
以下主要介绍氧化镁氯化法和光卤石法。
1.1.1 氧化镁氯化法利用天然菱镁矿,在700~800℃下煅烧,80%得到活性较好的轻烧氧化镁。
氧化镁的粒度要小于0.144mm,然后与碳素混合制团,团块炉料在竖式电炉中氯化,制得无水氯化镁,直接投入电解槽,最后电解得金属镁。
制备MgCL2的程式为:2MgO+2CL2+C=2Mgcl2+CO2。
1.1.2 光卤石法将光卤石(Mgcl2·kcl·6H2O)脱水后,直接电解制取金属镁。
光卤石脱水时水解反应不像Mgcl2那样严重,但也有一定的水解,因而在无水化的处理过程中,也需要氯化过程,由于加入了,需要经常清理电解槽。
1.1.3 电解法制镁存在的问题制备无水Mgcl2困难:在氯化镁的脱水过程中,由一水氯化镁脱水制取结晶氯化镁的过程极易水解,产生碱式氯化镁[Mg(OH)CL]和氧化镁,生产工艺较难控制;在HCL气氛下,水氯镁石脱水需要较高的温度(一般约为450℃),能耗大,设备腐蚀严重。
在金属镁的生产成本中,大约50%的费用用于Mgcl2脱水。
金属镁的纯度较低:电解法制取的粗镁中主要含有电解质中的氯化物及Fe、Si、Ni、Cr、Mn和K、Na等金属杂质,其存在会降低镁及其合金的耐腐蚀性能,因此需要采取措施,提高镁的纯度。
1.2 热还原法炼镁热还原法的典型代表是皮江法,皮江法是1940年左右发展起来的一种炼镁方法[7],我国目前约98%以上的原镁是由皮江法生产的。
皮江法将煅烧白云岩和硅铁按一定配比磨粉,压成团块,在高温和真空条件下,使煅烧白云岩中的氧化镁还原为镁蒸气,然后冷凝结晶为粗镁,再经精炼制得镁锭。
皮江法的最大问题是严重的环境污染和巨大的能量消耗。
主要能耗与二氧化碳的排放集中在以下3个阶段:①利用硅铁还原煅烧后的白云石矿需要耗能及释放二氧化碳;②生产硅铁消耗大量的电能,电能来源于煤炭;③煅烧白云石矿石消耗煤炭及释放大量的二氧化碳。
随着国际市场对金属镁需求的日益增长,加上自身镁资源的优势,中华大地的镁厂如雨后春笋般涌现出来。
到2001年,国际市场近40%-50%的原镁由中国提供,我国一跃成为世界第一产镁大国和出口大国,在国际镁工业中占据了举足轻重的地位,其中95%的原镁是由皮江法生产的[8]。
1.3 金属镁制备的发展趋势[9-10]近年来,国际上金属镁工业的发展趋势是以盐湖水氯镁石制取无水氯化镁为原料,这将大幅度降低金属镁的生产成本。
随着水氯镁石脱水炼镁技术的进步,带来的是金属镁制造成本的大幅度降低,也促进了金属镁的需求量的不断加大,并将产生巨大的经济效益和社会环境效益。
用CO气体作还原剂氯化煅烧菱镁矿炉料和研究开发一种新的单级电解槽电解氯化镁是电解法主要发展趋势;采用内热法与半连续硅热法技术,应用水煤浆高效能源作为燃料可提高金属镁的还原效率。
2. 镁合金的制备[11-12]根据加工方式的不同,镁合金材料主要分为铸造镁合金与变形镁合金两大类。
前者主要通过铸造获得镁合金产品。
传统的铸造工艺比较成熟,近年来,铸造领域中一些新的生产工艺和技术,如压力铸造技术,半固态成型技术,都被用来开发新型镁合金材料,并取得了很大的进展。
变形镁合金材料的生产主要通过挤压、轧制和锻造等工艺手段实现,由于镁在加工过程中对设备能力、生产条件的要求基本与变形铝合金相同,因此变形镁合金的生产完全可以采用变形铝合金的压力加工设备。
随着科技的进步,大量的镁合金被制备出来用于各个领域。
例如,AZ91D合金作为一种主要的镁合金而被做结构材料[13]。
2.1 耐热镁合金镁合金耐热性差是限制其应用的主要问题之一,提高耐热性可以扩大应用范围。
国内外耐热镁合金的应用对象,主要是轿车/微型车的发动机及其传动机构零部件,如变速箱壳体,汽缸体,汽缸盖,进/排气管等。
因此,它们的使用性能要求满足:工作温度高于120℃:应力范围35 M咿a~70 MPa;室温延伸率>3%;耐腐蚀和加工性能良好;并且易回收。
应用最广泛的耐热镁合金是Mg-AI系列合金,如As台金和AE合金已经过几十年的深入研究,相当成熟。
全世界每年生产镁材约30万吨,其中乐铸材料占90%,变形材料仅占O.5%,用量甚微。
但是,经过挤压、锻造、轧制等工艺制备的镁合金能够提供更多样化的力学性能及可后续热处理,进一步提高韧性、焊接性能等,可以满足更多样化的结构件需求。
因此,研究耐热镁合金的塑性变形非常有意义[14]。
2.2 高性能稀土镁合金稀土元素由于具有独特的核外电子排布,在冶金、材料领域中有独特的作用,具有净化合金溶液、改善合金组织、提高合金室温及高温力学性能、增强合金耐蚀性能等功能。
稀土镁合金具有镁合金的固有优点,如密度小、比强度高、具有金属光泽等,同时又具有耐热强度高、蠕变性能优良的新特点[15]。
2.2.1 Mg-Y系合金Y在镁中具有高的固溶度,能够形成强化相,具有明显的时效硬化特征。
在合金中加入其他合金元素(如:Nd、Zn和zr等)会明显降低Y在镁中的固溶度,但能大幅提高合金中析出相的体积分数,从而进一步提高合金的机械性能。
在含Y 的稀土镁合金中,WE系合金具有较好的浇铸、时效硬化及高温抗蠕变性能,因而被广泛应用于航空航天领域中。
2.2.2 Mg-sc系合金金属钪作为镁合金的强化元素,具有较高的熔点(1541℃),但其在镁合金中的扩散能力相对于其他稀土元素较低,强化作用显著。
钪的密度为39/cm3,比其他稀土元素的密度小,更能体现镁合金低密度的特点;与其他外加合金元素一起能够形成镁、钪和复杂的合金化合物强化相,改善合金的室温和高温性能。
2.2.3 Mg-Gd系合金Gd能提高镁合金的熔点和抗蠕变性能。
早在1974年研究者就发现,经过挤压、调质和时效处理的Mg一15%Gd合金在高温及低温下都具有较高的抗拉强度。
在Mg—Gd合金中加入其他合金元素,如:钪、锰、钇等,能大大提高镁合金的性能,其耐热性要远远高于铝及Mg-Y-Nd-zr(WE54A)等镁合金,高温强度在目前研究的镁合金中也是最高的。
但在镁合金中加入重稀土后会导致镁合金成本增加、密度提高及韧性变低等,因此,M矿Gd—Nd和Mg-Gd—Y合金中的Gd部分被Y及Nd替代。
2.3 泡沫镁合金泡沫金属作为一种新型多功能材料,以其特殊的结构与性能特征,在当前高速发展的科技领域倍受关注。
对泡沫金属的制备、性能以及应用方面的研究近年来越来越广泛和深入。
泡沫镁合金具有良好的阻尼性能、抗冲击性能、电磁屏蔽性能、吸声性能、以及生物相容性能。
不仅在汽车、航空航天、造船业等方面具有广泛的应用,而且在海陆空武器装备、建筑行业、医疗业等方面也有潜在用途。
可用于汽车的车身结构、飞船的起落架、减震器、缓冲器、过滤器、消音器、人体骨骼修复及再生等[16]。
3. 金属镁及其镁合金的应用[17-20]3.1 镁用作化学工业中试剂或添加剂在化学工业上,应用镁的格里纳德反应,通过合成可以制得多种复杂的有机化合物。
在电位序中镁的电极电位比铁和铝更负,镁广泛被用来制作化工容器、地下管道以及船体的防腐蚀部件。
镁的燃烧特性使其可用于爆破装置、照明弹、燃烧弹及焰火等等的生产。
镁还可用于阴极保护以防止其它金属的腐蚀,用作干电池及蓄电池的构件。
3.2 镁用作冶金行业的处理剂在冶金工业上,由于镁对卤素及氧的亲和力强,近年来钢铁工业中用镁粒代替碳化钙作为脱硫剂脱除钢水中的硫,从而得到优质钢。
镁在镍铁合金及铜合金冶炼中作为除氧剂和脱硫剂。
镁是生产钛、锆、铪、铀、钚等金属的还原剂。
镁是生产球墨铸铁的球化剂。
灰口铸铁铸造厂应用镁及镁合金作为烧注前加入铁水包内的添加剂镁使石墨成球状,大大改善了铸铁的性能。
由于薄壁高强度铸件可以实现产品轻量化,因此球墨铸铁件的应用有日益扩大的倾向。
含镁球化剂可以通过熔制法、还原法等制备。
在日本<镁在工业界中的用途主要是铝合金、铸铁的球化剂、钢铁冶金及钛冶金中的还原剂等。
3.3 镁合金的应用3.3.1 用作汽车行业合金材料从20世纪20年代开始,镁制零件就在赛车上应用。
目前在汽车工业方面镁合金主要用来制造离合器壳体、转向柱架、制动器踏板支架、阀盖、阀板、仪表板支架、变速器体、车窗马达壳体、油滤接头、发动机前盖、进气歧管、镜子外罩、辅件托架及照明灯夹持器等零部件。
在今后的20年里汽车工业使用的镁将会超过122/车(车质量的6%)即当前使用量的30倍。
全球每年生产5000万辆汽车,这意味着2020年将需要5X106t金属镁的生产能力。
3.3.2 用作电子通讯领域的合金零件在手机、笔记本电脑、CD机、摄影机、投影仪、MD、录像机等方面利用镁合金,可使之小型轻便化并增强抗电磁干扰能力。
电脑生产厂越来越多地要求它的供应商提供镁合金外壳来替代塑料外壳。
因为镁合金是一种很轻的金属,镁合金电脑外壳为薄壁结构(约1mm),因此比塑料外壳的质量小;另外,在机械的作用下变形很小,镁合金的散热性比塑料好,这样可以使结构更紧凑和变得更小。
日本正在将镁合金的应用从手提电脑扩大到手提电话及数码相机等,日本国内500万像素以上的高档数码相机均用镁合金外壳。
3.3.3 用作航空航天、国防等部门的合金零件[21]镁在航空航天、国防等部门的应用也十分广泛。
目前世界各国将轻质镁合金用作兵器零件。
如欧美生产的Racegun的枪械零件用镁钛合金使重量降低45%,击发时间减少66%;美国军用吉普车M27A1型的车身和桥壳采用镁合金,重量大大减小;法国MK式反坦克枪榴弹部分零件采用镁合金,全弹质量仅为800g美国大口径无后坐力反坦克炮也采用镁合金,大大减小了重量。
3.3.4 用作其它行业的合金零件镁合金在其它领域的应用也非常广泛。
如用作链锯、民用工具、旋转式割草机面板、钓鱼卷线盘、器具盒、便携工具、手电钻、研磨机、真空吸尘器、剪草机、家用搅拌器、地板上光清洗机、血压测试仪、电影放映机、照相机、雷达显示器、卡式录音机、运动器材、计算器、邮资显示表、微型马达、木工和瓦工用水平尺、缝纫机、太阳能电池、雪地汽车和行李箱等等。