铝合金焊接接头产生裂纹特征及产生机理分析
铝合金焊接接头产生裂纹特征及产生机理
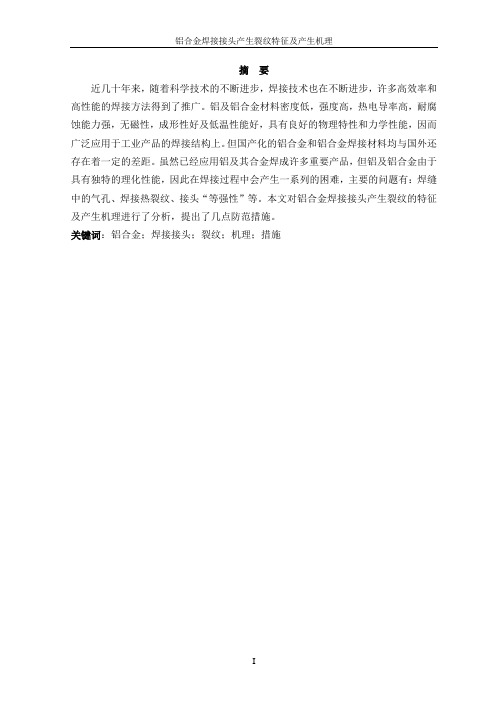
(8)焊接接头的耐腐蚀性能低于母材
热处理强化铝合金(如硬铝)接头的耐腐蚀性的降低很明显,接头组织越不均匀,耐蚀性越易降低。焊缝金属的纯度或致密性也影响接头耐蚀性能。杂质较多、晶粒粗大以及脆性相析出等,耐蚀性就会明显下降,不仅产生局部表面腐蚀而且经常出现晶间腐蚀,此外对于铝合金,焊接应力的存在也是影响耐蚀性的一个重要因素。 为了提高焊接接头的耐蚀性,主要采取以下几个措施[5]:1、改善接头组织成分的不均匀性。主要是通过焊接材料使焊缝合金化,细化晶粒并防止缺陷;同时调整焊接工艺以减小热影响区,并防止过热,焊后热处理。2、消除焊接应力,如局部表面拉应力可以采用局部锤击办法来消除。3、采取保护措施,如采取阳极氧化处理或涂层等。
浅议铝合金焊接接头裂纹产生及防治

I剖 酱 辘 | 庶 苷 ) 詹 瞬弃 , 问 鼓7
() 4 必要 时, 实施切割导轨 工程; 以释放导轨 内部积聚 的应 力; 提高安全性及乘搭舒适感 。 () 5 导轨切割主要步骤: ① 拆 除 导 轨 底 部 固定 支 架 。 ⑦ 设 定 切 割 高度 。 切割 高度= 力释放距离 (0 3mm + 应 2 ~ 0 ) 导轨底座 高度 ( 约为 5mm + 0 ) 预留距 离 ( 约为 8mm 0 ) ③按设定高度切割导轨 。
萌 生和 发 展 有 密 切 联 系 的冶 金 因素 。 力 学 因素 方 面 看 , 接 热 从 焊
最 靛 裙 况
f 连 度变 ,导 f # 高 麦 , 井 高 靶 轨 , 遣 度 化 辩 )
支 位 , 点 轨 截 压 再造 路 进 泉 移 遣 蓐 轻 路轨 , 成 轨
图 1
。 \
一/
f
—
L- =一
c =
/ 匕=
匕 =
/
_
_
④割短低端导轨后 , 瞬问释放 了一部分 内应 力。( 图 1步 如 :
骤 4 )
面保持一定间隙。
⑤对于没有支架 的, 加装导轨底支架 。 需在 日常保养 时,经 常确 认导轨底部和 调整螺栓 项面保持
一
产生重大影响,而本研究试验 中却发现焊缝拉伸试样中同时存 在着 由夹杂和气 孔诱发微裂纹 的现象 。气孔诱发微裂纹的现象 是否只是一种居次要地位 的伴生现象 ,还是引起焊缝拉伸强度 大幅度下 降的主要因素之一 , 亦还有待进一步的研究。
2 热裂纹产 生的过程
通常人们将脆性温度 区间的大小及在此温度 区间内具有 的 延性值称为产生焊接热裂纹 的冶金 因素 ,而把脆性温度区 内金 属的变形率大小称为力学因素 。焊接过程是一系列不平衡 的工 艺过程 的综合,这种特征从本质上与焊接接头金属断裂的冶金 因素和力学因素发生重要 的联系 ,如焊接工艺过程与冶金过程 的产物 即物理的 、 化学的与组织上 的不均匀性 、 熔渣 与夹杂物 、 气 体元 素 与 处 于 过饱 和 浓 度 的空 位 等 。 所有 这 些 , 都是 与裂 纹 的
增材制造铝合金过程中裂纹发生与发展的机理

增材制造铝合金过程中裂纹发生与发展的机理
在增材制造过程中,铝合金的裂纹发生与发展主要与以下几个因素有关:
1.热处理:热处理是增材制造过程中必不可少的环节,然而,不当的热处理工艺可能导致铝合金内部出现裂纹。
例如,冷却速度过快或加热温度过高可能导致铝合金的晶粒粗大,降低材料的力学性能,增加裂纹的风险。
2.残余应力:增材制造过程中,由于金属粉末的熔化凝固和冷却等过程,会在制件内部产“生残余应力。
这些残余应力在制件使用过程中可能导致裂纹的产“生和扩展。
3.金属粉末质量:金属粉末的质量对裂纹的产生也有很大影响。
如果金属粉末中含有杂质氧化物或其他非金属夹杂物,可能会在制件中形成裂纹源。
4.工艺参数:增材制造过程中的工艺参数如激光功率、扫描速度、层厚度等也会影响裂纹的产生。
当工艺参数选择不当,如激光功率过高或扫描速度过快时,可能导致金属粉末熔化过度,冷却速度过快,从而增加裂纹的风险。
5.基板预处理:在增材制造过程中,基板预处理不当或不进行预处理也可能导致铝合金制件内部产生裂纹。
例如,基板表面未进行充分预热或预热温度过低,可能导致熔化的金属粉末与基板之间的热膨胀系数差异增大,从而在制件中产“生裂纹。
综上所述,增材制造铝合金过程中裂纹的发生与发展涉及多个因素,
需要从多个方面进行研究和优化,以减少裂纹的产“生和提高制件的性能。
铝合金部件焊接接头裂纹分析
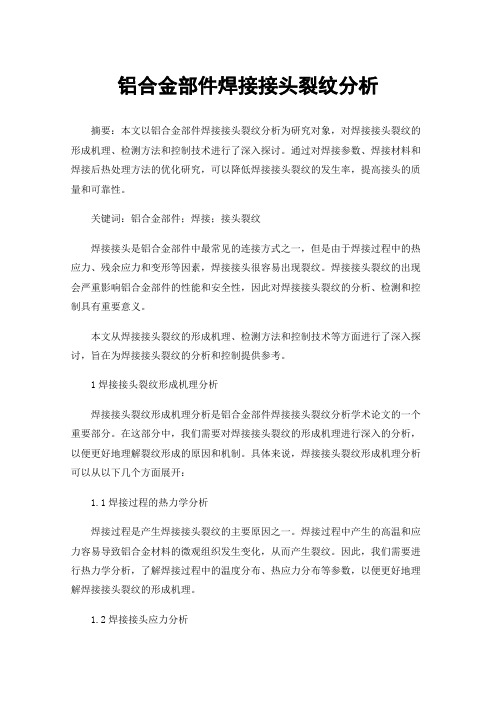
铝合金部件焊接接头裂纹分析摘要:本文以铝合金部件焊接接头裂纹分析为研究对象,对焊接接头裂纹的形成机理、检测方法和控制技术进行了深入探讨。
通过对焊接参数、焊接材料和焊接后热处理方法的优化研究,可以降低焊接接头裂纹的发生率,提高接头的质量和可靠性。
关键词:铝合金部件;焊接;接头裂纹焊接接头是铝合金部件中最常见的连接方式之一,但是由于焊接过程中的热应力、残余应力和变形等因素,焊接接头很容易出现裂纹。
焊接接头裂纹的出现会严重影响铝合金部件的性能和安全性,因此对焊接接头裂纹的分析、检测和控制具有重要意义。
本文从焊接接头裂纹的形成机理、检测方法和控制技术等方面进行了深入探讨,旨在为焊接接头裂纹的分析和控制提供参考。
1焊接接头裂纹形成机理分析焊接接头裂纹形成机理分析是铝合金部件焊接接头裂纹分析学术论文的一个重要部分。
在这部分中,我们需要对焊接接头裂纹的形成机理进行深入的分析,以便更好地理解裂纹形成的原因和机制。
具体来说,焊接接头裂纹形成机理分析可以从以下几个方面展开:1.1焊接过程的热力学分析焊接过程是产生焊接接头裂纹的主要原因之一。
焊接过程中产生的高温和应力容易导致铝合金材料的微观组织发生变化,从而产生裂纹。
因此,我们需要进行热力学分析,了解焊接过程中的温度分布、热应力分布等参数,以便更好地理解焊接接头裂纹的形成机理。
1.2焊接接头应力分析焊接接头的应力是产生焊接接头裂纹的另一个主要原因。
焊接接头在焊接后会受到内部应力的影响,这些应力会导致接头的变形和裂纹。
因此,我们需要进行应力分析,了解焊接接头中各个部位的应力情况,以便更好地预测焊接接头裂纹的形成位置和形态。
1.3焊接接头金相组织分析铝合金部件的微观组织是决定其力学性能和耐腐蚀性能的重要因素。
焊接接头的金相组织分析可以帮助我们了解焊接接头中的晶粒结构、相组成、缺陷分布等信息,从而更好地理解焊接接头裂纹的形成机理。
综上所述,焊接接头裂纹形成机理分析是铝合金部件焊接接头裂纹分析学术论文的重要内容之一。
铝合金焊接常见缺陷的产生原因及质量控制分析

铝合金焊接常见缺陷的产生原因及质量控制分析摘要:铝合金材料在现代装备制造业中应用广泛,铝合金材料的可焊性较差,焊接过程中会出现很多缺陷,主要是气孔和裂纹较多。
分析了铝合金焊接过程中造成气孔和裂纹的因素,提出减少气孔和裂纹的质量控制措施。
关键词:铝合金;焊缝;缺陷;措施1 焊接性能简介(1)氧化能力强。
Al与O2在空气中结合生成致密的Al2O3薄膜,厚度约为0.1μm,熔点高达2050℃,密度大,在焊接过程中氧化膜会阻碍金属之间的良好结合,并且容易造成夹渣,氧化膜还会吸附水分,焊接时易生成焊缝气孔。
(2)铝的比热大,导热速度快。
因导热快,散热也快,焊接一般采用能量集中功率大的焊接热源,有时还需预热,才能获得高质量的焊接接头。
(3)线膨胀系数大。
铝及铝合金线膨胀系数大,金属凝固时体积收缩率也大,易产生焊接变形。
(4)容易形成气孔。
H2是铝及铝合金焊接时产生气孔的主要原因,H2主要来源于焊接材料(母材、焊丝、保护气体)吸附的水分。
(5)合金元素蒸发和烧损。
铝合金的某些合金元素,在高温下容易蒸发烧损,从而改变了焊缝金属的化学成份,降低了焊接接头的性能。
(6)铝及铝合金熔化时无色泽变化。
铝及铝合金焊接时,由固态转变为液态时,没有明显的颜色变化,给焊接操作带来一定困难。
2 TIG焊常见缺陷及防止措施铝及铝合金TIG焊的各种缺陷,既有与其他电弧焊相同的,也有一些是其特有的。
铝及铝合金TIG焊的焊接质量与焊前准备情况、保护气体纯度、焊接参数的正确性、电极材料的质量、操作技术的熟练程度、焊接电源等因素有关。
其常见缺陷产生原因及对策阐述如下。
2.1气孔在焊接过程中,熔池中的气体未在金属凝固前逸出,残存于焊缝中的空穴被称为气孔。
气孔是比较多见的焊接缺陷,在焊缝的各个位置都可能发现气孔。
铝合金焊接时生成气孔的气体主要是氢气,氢气主要来自电弧周围的空气,母材和焊丝表面的杂质,如油污,水分等的分解燃烧。
气孔是铝合金焊接时最容易出现的一种体积型缺陷,气孔的存在减少了焊缝的受力截面,有些针形气孔会使焊缝疏松,从而降低了接头的强度,还有就是降低了焊缝的力学性能。
5A06铝合金焊接接头裂纹失效分析

2 7
5 A0 6铝 合 金 焊 接 接 头裂 纹 失效 分 析
Fa i l u r e An a l y s i s o f 5 A0 6 Al u mi n u m Al l o y We l d i n g J o i n t Cr a c k
Mi c r o — f r a c t ur e a n d ma c r o f r a c t u r e a r e a n a l y z e d by SEM a nd f o un d t ha t t h e r e a r e s e c o nd a r y c r a c ks i n t he f r a c t u r e ,a n d t he f r a c t u r e wa s b r i t t l e f r a c t u r e .
近 年来 , 铝、 镁 等 轻 质 合 金 由 于其 节 约 能 源 、 减 少 废气 排 放 等特 点 , 在 海事 用 途 ( 如船 舶 ) 、 汽 车、 飞
摘 要 :针 对 5 A 0 6 铝 合 金 焊 缝 附 近 出 现 的 裂 纹 进 行 了分 析 。5 A 0 6铝 合 金 母 材 、 焊缝及 热影响区组织分析结果 表明 , 材 料
成 型 后 的组 织 不 均 匀 , 并且存在夹杂物 , 晶 内 和 晶 界 有 析 出相 出 现 。采 用 光 学 显 微 镜 对 裂 纹 的 扩 展 特 征 进 行 分 析 , 结 果
d o i :1 0 . 3 9 6 9 / j . i s s n . 1 0 0 1 — 4 3 8 1 . 2 0 1 3 . 0 3 . 0 0 6 中图 分 类 号 : TG1 4 6 . 2 1 文献 标 识 码 : A 文 章 编 号 :1 0 0 1 — 4 3 8 1 ( 2 0 1 3 ) 0 3 — 0 0 2 7 - 0 5
铝合金焊接裂纹产生的原因和预防措施李修鹏谭长波
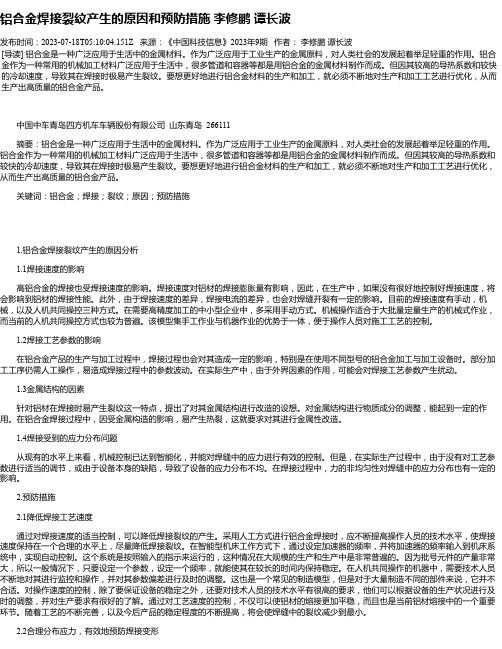
铝合金焊接裂纹产生的原因和预防措施李修鹏谭长波发布时间:2023-07-18T05:10:04.151Z 来源:《中国科技信息》2023年9期作者:李修鹏谭长波[导读] 铝合金是一种广泛应用于生活中的金属材料。
作为广泛应用于工业生产的金属原料,对人类社会的发展起着举足轻重的作用。
铝合金作为一种常用的机械加工材料广泛应用于生活中,很多管道和容器等都是用铝合金的金属材料制作而成。
但因其较高的导热系数和较快的冷却速度,导致其在焊接时极易产生裂纹。
要想更好地进行铝合金材料的生产和加工,就必须不断地对生产和加工工艺进行优化,从而生产出高质量的铝合金产品。
中国中车青岛四方机车车辆股份有限公司山东青岛 266111摘要:铝合金是一种广泛应用于生活中的金属材料。
作为广泛应用于工业生产的金属原料,对人类社会的发展起着举足轻重的作用。
铝合金作为一种常用的机械加工材料广泛应用于生活中,很多管道和容器等都是用铝合金的金属材料制作而成。
但因其较高的导热系数和较快的冷却速度,导致其在焊接时极易产生裂纹。
要想更好地进行铝合金材料的生产和加工,就必须不断地对生产和加工工艺进行优化,从而生产出高质量的铝合金产品。
关键词:铝合金;焊接;裂纹;原因;预防措施1.铝合金焊接裂纹产生的原因分析1.1焊接速度的影响高铝合金的焊接也受焊接速度的影响。
焊接速度对铝材的焊接膨胀量有影响,因此,在生产中,如果没有很好地控制好焊接速度,将会影响到铝材的焊接性能。
此外,由于焊接速度的差异,焊接电流的差异,也会对焊缝开裂有一定的影响。
目前的焊接速度有手动,机械,以及人机共同操控三种方式。
在需要高精度加工的中小型企业中,多采用手动方式。
机械操作适合于大批量定量生产的机械式作业,而当前的人机共同操控方式也较为普遍。
该模型集手工作业与机器作业的优势于一体,便于操作人员对施工工艺的控制。
1.2焊接工艺参数的影响在铝合金产品的生产与加工过程中,焊接过程也会对其造成一定的影响,特别是在使用不同型号的铝合金加工与加工设备时。
受电弓用5083铝合金焊接裂纹分析
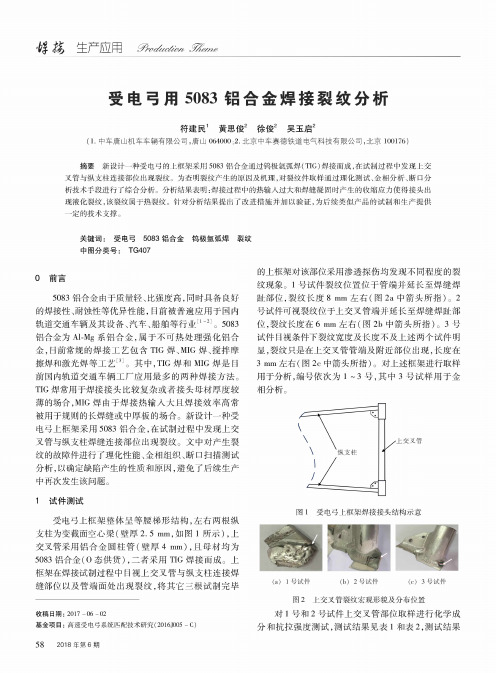
生产1应用 S/%e/受电弓用5083钼合金焊接裂纹分析符建民1黄思俊2徐俊2吴玉启2(1.中车唐山机车车辆有限公司,唐山064000;2.北京中车赛德铁道电气科技有限公司,北京100176)摘要新设计一种受电弓的上框架采用5083铝合金通过钨极氩弧焊(TIG)焊接而成,在试制过程中发现上交 叉管与纵支柱连接部位出现裂纹。
为查明裂纹产生的原因及机理,对裂纹件取样通过理化测试、金相分析、断口分析技术手段进行了综合分析。
分析结果表明:焊接过程中的热输人过大和焊缝凝固时产生的收缩应力使得接头出现液化裂纹,该裂纹属于热裂纹。
针对分析结果提出了改进措施并加以验证,为后续类似产品的试制和生产提供一'定的技术支撑。
关键词:受电弓5083铝合金钨极氩弧焊裂纹中图分类号:TG407〇前言5083铝合金由于质量轻、比强度高,同时具备良好 的焊接性、耐蚀性等优异性能,目前被普遍应用于国内 轨道交通车辆及其设备、汽车、船舶等行业[1_2]。
5083 铝合金为A l-M g系铝合金,属于不可热处理强化铝合 金,目前常规的焊接工艺包含T IG焊、M IG焊、搅拌摩 擦焊和激光焊等工艺[3]。
其中,T IG焊和M IG焊是目 前国内轨道交通车辆工厂应用最多的两种焊接方法。
T IG焊常用于焊接接头比较复杂或者接头母材厚度较 薄的场合,M IG焊由于焊接热输人大且焊接效率高常 被用于规则的长焊缝或中厚板的场合。
新设计一种受 电弓上框架采用5083铝合金,在试制过程中发现上交 叉管与纵支柱焊缝连接部位出现裂纹。
文中对产生裂 纹的故障件进行了理化性能、金相组织、断口扫描测试 分析,以确定缺陷产生的性质和原因,避免了后续生产 中再次发生该问题。
1试件测试受电弓上框架整体呈等腰梯形结构,左右两根纵 支柱为变截面空心梁(壁厚2.5 mm,如图1所示),上 交叉管采用铝合金圆柱管(壁厚4 mm),且母材均为 5083铝合金(0态供货),二者采用T IG焊接而成。
- 1、下载文档前请自行甄别文档内容的完整性,平台不提供额外的编辑、内容补充、找答案等附加服务。
- 2、"仅部分预览"的文档,不可在线预览部分如存在完整性等问题,可反馈申请退款(可完整预览的文档不适用该条件!)。
- 3、如文档侵犯您的权益,请联系客服反馈,我们会尽快为您处理(人工客服工作时间:9:00-18:30)。
虽然已经应用铝及其合金焊成许多重要产品,但实际焊接生产中并不是没有困难,主要的问题有:焊缝中的气孔、焊接热裂纹、接头“等强性”等。
由于铝及其合金的化学活泼性很强,表面极易形成氧化膜,且多具有难熔性质(如Al2O3的熔点为2050℃,MgO熔点为2500℃),加之铝及其合金导热性强,焊接时容易造成不熔合现象。
由于氧化膜密度同铝的密度极其接近,所以也容易成为焊缝金属中夹杂物。
同时,氧化膜(特别是有MgO存在的,不很致密的氧化膜)可以吸收较多水分而常常成为焊缝气孔的重要原因之一。
此外,铝及其合金的线胀系数大,导热性又强,焊接时容易产生翘曲变形。
这些也都是焊接生产中颇感困难的问题。
下面,对在试验过程中产生比较严重的裂纹进行深入的分析。
1铝合金焊接接头中的裂纹及其特征在铝合金焊接过程中,由于材料的种类、性质和焊接结构的不同,焊接接头中可以出现各种裂纹,裂纹的形态和分布特征都很复杂,根据其产生的部位可分为以下两种裂纹形式:(1)焊缝金属中的裂纹:纵向裂纹、横向裂纹、弧坑裂纹、发状或弧状裂纹、焊根裂纹和显微裂纹(尤其在多层焊时)。
(2)热影响区的裂纹:焊趾裂纹、层状裂纹和熔合线附近的显微热裂纹。
按裂纹产生的温度区间分为热裂纹和冷裂纹,热裂纹是在焊接时高温下产生的,它主要是由晶界上的合金元素偏析或低熔点物质的存在所引起的。
根据所焊金属的材料不同,产生热裂纹的形态、温度区间和主要原因也各有不同,热裂纹又可分为结晶裂纹、液化裂纹和多边化裂纹3类。
热裂纹中主要产生结晶裂纹,它是在焊缝结晶过程中,在固相线附近,由于凝固金属的收缩,残余液体金属不足不能及时填充,在凝固收缩应力或外力的作用下发生沿晶开裂,这种裂纹主要产生在含杂质较多的碳钢、低合金钢焊缝和某些铝合金;液化裂纹是在热影响区中被加热到高温的晶界凝固时的收缩应力作用下产生的。
在试验过程中发现,当填充材料表面清理不够充分时,焊接后焊缝中仍存在较多的夹杂和少量的气孔。
在三组号试验中,由于焊接填充材料为铸造组织,其中夹杂为高熔点物质,焊接后在焊缝中仍将存在;又,铸造组织比较稀疏,孔洞较多,易于吸附含结晶水的成分和油质,它们将成为焊接过程中产生气孔的因素。
当焊缝在拉伸应力作用下时,这些夹杂和气孔往往成为诱发微裂纹的关键部位。
通过显微镜进一步观察发现,这些夹杂和气孔诱发的微观裂纹之间有明显的相互交汇的趋势。
然而,对于夹杂物在此的有害作用究竟是主要表现为应力集中源从而诱发裂纹,还是主要表现为脆性相从而诱发裂纹,尚难以判断。
此外,一般认为,铝镁合金焊缝中的气孔不会对焊缝金属的拉伸强度产生重大影响,而本研究试验中却发现焊缝拉伸试样中同时存在着由夹杂和气孔诱发微裂纹的现象。
气孔诱发微裂纹的现象是否只是一种居次要地位的伴生现象,还是引起焊缝拉伸强度大幅度下降的主要因素之一,亦还有待进一步的研究。
2热裂纹产生的过程目前关于焊接热裂纹理论,国内外认为较完善的是普洛霍洛夫理论。
概括地讲,该理论认为结晶裂纹的产生与否主要取决于以下3方面:脆性温度区间的大小;在此温度区间内合金所具有的延性以及在脆性温度区间金属的变形率大小。
通常人们将脆性温度区间的大小及在此温度区间内具有的延性值称为产生焊接热裂纹的冶金因素,而把脆性温度区内金属的变形率大小称为力学因素。
焊接过程是一系列不平衡的工艺过程的综合,这种特征从本质上与焊接接头金属断裂的冶金因素和力学因素发生重要的联系,如焊接工艺过程与冶金过程的产物即物理的、化学的与组织上的不均匀性、熔渣与夹杂物、气体元素与处于过饱和浓度的空位等。
所有这些,都是与裂纹的萌生与发展有密切联系的冶金因素。
从力学因素方面看,焊接热循环特定的温度梯度与冷却速度,在一定的拘束条件下,将使焊接接头处于复杂的应力-应变状态,从而为裂纹的萌生与发展提供必要的条件。
在焊接过程中,冶金因素和力学因素的综合作用将归结为两个方面,即是强化金属联系还是弱化金属联系。
如果在冷却时,焊接接头金属中正在建立强度联系,在一定刚性拘束条件下能够顺从地应变,焊缝与近缝区金属能够承受外加拘束应力与内在残余应力的作用时,裂纹就不容易产生,焊接接头的金属裂纹敏感性低,反之,当承受不住应力作用时,金属中强度联铝合金焊接接头产生裂纹特征及产生机理分析谢辉(广东省第二农机厂,广东广州512219)摘要:近40年来,由于焊接技术的进步,高效率和高性能的焊接方法得到了推广,铝及铝合金在车辆、船舶、建筑、桥梁、化工机械、低温工程和宇航工业等各种结构方面的应用在不断扩大,但国产化的铝合金和铝合金焊接材料均还存在着一定的差距。
对铝合金焊接接头产生裂纹的特征及产生机理进行了分析,提出了几点防范措施。
关键词:铝合金;焊接接头;裂纹;机理—116—系容易中断,就会产生裂纹。
在这种情况下,焊接接头金属的裂纹敏感性较高。
焊接接头金属从结晶凝固的温度开始,以一定的速度冷却到室温,其裂纹敏感性决定于变形能力和外加应变的对比以及变形抗力与外加应力的对比。
然而在冷却过程中,在不同的温度阶段,由于晶间强度与晶粒强度增长的情况不同、变形在晶粒间和晶粒内部的情况分布不同、由应变所诱导的扩散行为不同、应力集中的条件以及导致金属脆化的因素不同,焊接接头具体的薄弱环节以及它弱化的因素和程度也是不同的。
导致焊接接头金属产生裂纹的冶金因素和力学因素有着较为密切的联系,力学因素中的应力梯度和热循环特征所确定的温度梯度有关,而后者与金属的导热性密切相关,如金属的热塑性变化特征、热膨胀性以及组织转变等构成的冶金因素,在很大程度上对焊接接头金属所处的应力-应变状态起到重要作用,此外,随着温度的降低与冷却速度的变化,冶金因素和力学因素也都是在变化着的,在不同的温度区间对焊接接头金属的强度联系作用各不相同,如结晶温度区间大,固相线温度低,在晶粒间残存的低熔液态金属处,更容易引起应力集中,导致固相金属产生裂纹;同样,随着温度降低,如果收缩量较大,特别是在快速冷却条件下,当收缩应变速率高,应力-应变状态比较苛刻时也容易产生裂纹等等。
在铝合金焊接时焊缝金属凝固结晶的后期,低熔共晶体被排挤在晶体交遇的中心部位,形成一种所谓的“液态薄膜”,此时由于在冷却时收缩量较大而得不到自由收缩产生较大的拉伸应力,这时候液态薄膜就形成了较为薄弱的环节,在拉伸应力的作用下就可能在薄弱地带开裂而形成裂纹。
3热裂纹产生的机理为了研究铝合金焊接时那个时候最容易产生热裂纹,把铝合金焊接时焊接熔池的结晶分为3个阶段。
第一个阶段是液固阶段,焊接熔池从高温冷却开始结晶时,只有很少数量的晶核存在。
随着温度的降低和冷却时间的延长,晶核逐渐长大,并且出现新的晶核,但是在这个过程中液相始终占有较多的数量,相邻晶粒之间不发生接触,对还未凝固的液态铝合金的自由流动不形成阻碍。
在这种情况下,即使有拉伸应力存在,但被拉开的缝隙能及时地被流动着的铝合金液态金属所填满,因此在液固阶段产生裂纹的可能性很小。
第二阶段是固液阶段,在焊接熔池结晶继续进行时,熔池中固相不断增多,同时先前结晶的晶核不断长大,当温度降低到某一数值时,已经凝固的铝合金金属晶体相互彼此发生接触,并且不断倾轧在一起,这时候液态铝合金的流动受到阻碍,也就是说熔池结晶进入了固液阶段。
在这种情况下,由于液态铝合金金属较少,晶体本身的变形可以强烈发展,晶体间残存的液相则不容易流动,在拉伸应力作用下产生的微小缝隙都无法填充,只要稍有拉伸应力的存在就有产生裂纹的可能性。
因此,这个阶段叫做“脆性温度区”。
第三阶段是完全凝固阶段,熔池金属完全凝固之后所形成的焊缝,受到拉应力时,就会表现出较好的强度和塑性,在这一阶段产生裂纹的可能性相对来说较小。
因此,当温度高于或者低于a-b之间的脆性温度区时,焊缝金属都有较大的抵抗结晶裂纹的能力,具有较小的裂纹倾向。
在一般情况下,杂质较少的金属(包括母材和焊接材料),由于脆性温度区间较窄,拉应力在这个区间作用的时间比较短,使得焊缝的总应变量比较小,因此焊接时产生的裂纹倾向较小。
如果焊缝中杂质比较多,则脆性温度区间范围比较宽,拉伸应力在这个区间的作用时间比较长,产生裂纹的倾向较大。
4铝合金焊接裂纹的防止措施根据铝合金焊接时产生热裂纹的机理,可以从冶金因素和工艺因素两个方面进行改进,降低铝合金焊接热裂纹产生的机率。
在冶金因素方面,为了防止焊接时产生晶间热裂纹,主要通过调整焊缝合金系统或向填加金属中添加变质剂。
调整焊缝合金系统的着眼点,从抗裂角度考虑,在于控制适量的易熔共晶并缩小结晶温度区间。
由于铝合金属于典型的共晶型合金,最大裂纹倾向正好同合金的“最大”凝固温度区间相对应,少量易熔共晶的存在总是增大凝固裂纹倾向,所以,一般都是使主要合金元素含量超过裂纹倾向最大时的合金组元,以便能产生“愈合”作用。
而作为变质剂向填加金属中加入Ti、Zr、V和B等微量元素,企图通过细化晶粒来改善塑性、韧性,并达到防止焊接热裂纹的目的尝试,在很早以前就开始了,并且取得了效果。
图3给出刚性搭接角焊缝的条件下Al-4.5%Mg焊丝中加入变质剂的抗裂试验结果。
试验中加入的Zr为0.15%,Ti+B为0.1%。
可见,同时加入Ti和B可以显著提高抗裂性能。
Ti、Zr、V、B及Ta等元素的共同特点,是都能同铝形成一系列包晶反应生成难熔金属化合物(Al3Ti、Al3Zr、Al7V、AlB2、Al3Ta等)。
这种细小的难熔质点,可成为液体金属凝固时的非自发凝固的晶核,从而可以产生细化晶粒作用。
在工艺因素上,主要是焊接规范、预热、接头形式和焊接顺序,这些方法都是从焊接应力上着手来解决焊接裂纹。
焊接工艺参数影响凝固过程的不平衡性和凝固的组织状态,也影响凝固过程中的应变增长速度,因而影响裂纹的产生。
热能集中的焊接方法,有利于快速进行焊接过程,可防止形成方向性强的粗大柱状晶,因而可以改善抗裂性。
采用小的焊接电流,减慢焊接速度,可减少熔池过热,也有利于改善抗裂性。
而焊接速度的提高,促使增大焊接接头的应变速度,而增大热裂的倾向。
可见,增大焊接速度和焊接电流,都促使增大裂纹倾向。
在铝结构装配、施焊时不使焊缝承受很大的钢性,在工艺上可采取分段焊、预热或适当降低焊接速度等措施。
通过预热,可以使得试件相对膨胀量较小,产生焊接应力相应降低,减小了在脆性温度区间的应力;尽量采用开坡口和留小间隙的对接焊,并避免采用十字形接头及不适当的定位、焊接顺序;焊接结束或中断时,应及时填满弧坑,然后再移去热源,否则易引起弧坑裂纹。
对于5000系合金多层焊的焊接接头,往往由于晶间局部熔化而产生显微裂纹,因此必须控制后一层焊道焊接热输入量。
而根据本文试验所证明,对于铝合金的焊接,母材和填充材料的表面清理工作也相当重要。
材料的夹杂在焊缝中将成为裂纹产生的源头,并成为引起焊缝性能下降的最主要原因。