对铆接疲劳裂纹产生机理的探讨
金属材料的疲劳与断裂机制

金属材料的疲劳与断裂机制随着科学技术的不断发展,金属材料在我们的生活中扮演着越来越重要的角色。
无论是制作机器、建筑结构还是汽车、航空航天等领域,金属材料都是不可或缺的材料之一。
与此同时,金属材料的疲劳与断裂问题也越来越引起人们的关注。
在本文中,我们将探讨金属材料的疲劳与断裂机制。
首先,我们需要明确什么是疲劳及其机制。
疲劳是指材料在交替载荷循环下,出现的渐增裂纹扩展和终至断裂的现象。
简单来讲,就是材料长时间的受外力而发生的老化现象,最终造成材料损坏甚至断裂。
而疲劳的机制则是由于金属材料中晶界(晶粒之间的交界面)会在多次反复受载荷下产生微小的位移,从而使晶界附近的原子缺陷不断累积,导致晶界上的裂纹扩展和终于断裂。
那么,如何预测和延缓金属材料的疲劳断裂呢?这时就需要了解金属材料断裂的机理。
材料断裂涉及到多个层面,从宏观到微观逐步深入。
宏观上,断裂的形式可以分为脆性断裂和塑性断裂两种。
脆性断裂指材料在受到载荷时,很快就突然断裂了,而塑性断裂指在受到载荷时,材料逐渐失去强度向外延伸,最终断裂。
微观上,材料的断裂机制主要由原子、晶粒等层面的力学和物理因素所控制。
为了预测和延缓金属材料的疲劳断裂,我们可以采取多种措施。
一是降低工作环境中的载荷大小、频率和气温等,从而降低材料的应力水平;二是在金属材料预制过程中,添加特殊的合金元素,如铬、锰等,来增强材料的抗疲劳性能;三是定期检查和维护设备,避免设备老化或失修导致疲劳断裂等。
另外,金属材料的疲劳与断裂问题也给材料科学家带来了创新的机会。
如今,新型材料的研究和开发正在不断向前推进。
有些新型材料如高韧性合金、纳米材料等,通过调整其内部结构和力学性质,可以使其具有更好的疲劳抗性和延展性,更适合于特定的应用场合。
同时,理论模拟计算技术的不断发展也为对金属材料疲劳与断裂机制进行基础研究提供了新的研究手段。
总之,金属材料的疲劳与断裂问题对我们日常生活和工业生产都有重要的影响。
焊缝疲劳裂纹的原因

焊缝疲劳裂纹的原因一、疲劳裂纹的概念和特征疲劳裂纹是指材料在受到交变或重复载荷作用下,在无外界力的情况下产生的由于疲劳所致的裂纹。
疲劳裂纹通常以一定的周期性或规律性扩展,直至超过材料的疲劳强度而导致破坏。
疲劳裂纹的存在可能严重影响结构的可靠性和使用寿命。
二、焊缝疲劳裂纹的原因2.1 形成焊缝疲劳裂纹的基本原因焊缝疲劳裂纹的形成主要受到以下几个因素的影响:1.组织不均匀性:焊缝内的组织不均匀性是疲劳裂纹形成和扩展的一个重要原因。
焊接过程中,焊缝区域受到高温和热应力的影响,会导致晶粒的过度长大和组织的变化,使得焊缝区域在受到交变载荷的情况下更容易发生裂纹。
2.应力集中:焊接过程中,焊缝周围的材料经历了复杂的热循环和相变过程,会产生应力集中现象。
焊缝本身就是一个应力集中的区域,如果设计不合理或施工不当,就会导致焊缝的应力集中进一步加剧,从而促使疲劳裂纹的形成和扩展。
3.缺陷和不良现象:焊接过程中,可能会出现不均匀的焊缝几何形状、焊接缺陷(如气孔、夹渣等)、内部应力、残余变形等不良现象。
这些缺陷和不良现象会导致焊缝的强度降低,从而促使焊缝疲劳裂纹的形成。
2.2 不同焊接方法对焊缝疲劳裂纹的影响不同的焊接方法对焊缝疲劳裂纹的形成和扩展有着不同的影响。
下面以常见的几种焊接方法为例进行讨论:1.电弧焊:电弧焊是一种常用的焊接方法,其焊接过程中产生的较高温度可能导致焊缝周围材料的相变和组织变化,从而增加了焊缝疲劳裂纹形成的风险。
2.气保焊:气保焊是一种在保护气体的环境下进行的焊接方法,其焊接过程中产生的保护气体可以有效地减少焊缝周围材料的氧化和污染,从而减少了焊缝疲劳裂纹形成的概率。
3.点焊:点焊是一种通过电阻热来实现焊接的方法,其焊接过程中产生的高温和热应力可能导致焊缝周围材料的晶粒长大和组织变化,从而增加了焊缝疲劳裂纹形成的风险。
4.激光焊:激光焊是一种高能量密度的焊接方法,其焊接过程中产生的高温和应力可能导致焊缝周围材料的熔化和凝固,从而对焊缝疲劳裂纹的形成和扩展产生影响。
疲劳裂纹论文
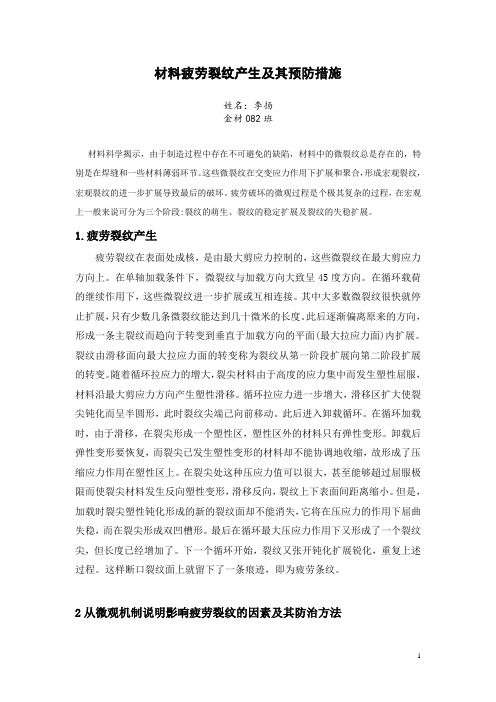
材料疲劳裂纹产生及其预防措施姓名:李扬金材082班材料科学揭示,由于制造过程中存在不可避免的缺陷,材料中的微裂纹总是存在的,特别是在焊缝和一些材料薄弱环节。
这些微裂纹在交变应力作用下扩展和聚合,形成宏观裂纹,宏观裂纹的进一步扩展导致最后的破坏。
疲劳破坏的微观过程是个极其复杂的过程,在宏观上一般来说可分为三个阶段:裂纹的萌生、裂纹的稳定扩展及裂纹的失稳扩展。
1.疲劳裂纹产生疲劳裂纹在表面处成核,是由最大剪应力控制的,这些微裂纹在最大剪应力方向上。
在单轴加载条件下,微裂纹与加载方向大致呈45度方向。
在循环载荷的继续作用下,这些微裂纹进一步扩展或互相连接。
其中大多数微裂纹很快就停止扩展,只有少数几条微裂纹能达到几十微米的长度。
此后逐渐偏离原来的方向,形成一条主裂纹而趋向于转变到垂直于加载方向的平面(最大拉应力面)内扩展。
裂纹由滑移面向最大拉应力面的转变称为裂纹从第一阶段扩展向第二阶段扩展的转变。
随着循环拉应力的增大,裂尖材料由于高度的应力集中而发生塑性屈服,材料沿最大剪应力方向产生塑性滑移。
循环拉应力进一步增大,滑移区扩大使裂尖钝化而呈半圆形,此时裂纹尖端己向前移动。
此后进入卸载循环。
在循环加载时,由于滑移,在裂尖形成一个塑性区,塑性区外的材料只有弹性变形。
卸载后弹性变形要恢复,而裂尖已发生塑性变形的材料却不能协调地收缩,故形成了压缩应力作用在塑性区上。
在裂尖处这种压应力值可以很大,甚至能够超过屈服极限而使裂尖材料发生反向塑性变形,滑移反向,裂纹上下表面间距离缩小。
但是,加载时裂尖塑性钝化形成的新的裂纹面却不能消失,它将在压应力的作用下屈曲失稳,而在裂尖形成双凹槽形。
最后在循环最大压应力作用下又形成了一个裂纹尖,但长度已经增加了。
下一个循环开始,裂纹又张开钝化扩展锐化,重复上述过程。
这样断口裂纹面上就留下了一条痕迹,即为疲劳条纹。
2从微观机制说明影响疲劳裂纹的因素及其防治方法1从循环应力方面直接观测表明,在循环应力作用下,疲劳裂纹尖端附近产生明显的塑性滑移带。
机械材料的疲劳断裂行为与失效机理研究

机械材料的疲劳断裂行为与失效机理研究疲劳断裂是机械材料在长期应力循环作用下产生失效的一种常见方式。
疲劳失效的发生对于许多工程结构的可靠性和寿命都产生着重要的影响。
因此,研究机械材料的疲劳断裂行为与失效机理具有重要的工程实际意义。
疲劳断裂行为主要通过疲劳寿命和裂纹扩展速率来描述。
疲劳寿命是指在给定的应力循环条件下,材料能够承受多少次应力循环而不发生疲劳断裂。
裂纹扩展速率是指裂纹在疲劳断裂过程中的扩展速度,它是刻画疲劳寿命的重要参数。
疲劳断裂的失效机理可以分为微观和宏观两个层面。
在微观层面上,疲劳断裂是由于材料内部的细小缺陷在应力循环加载下逐渐扩展形成裂纹,最终导致断裂失效。
这些缺陷包括晶界、夹杂物、位错和间隙等。
晶界是指不同晶体之间的界面,当应力循环加载时,晶界处容易形成新的裂纹,并引起裂纹的扩展。
夹杂物是指材料中的非金属物质,如氧化物、硫化物等,这些夹杂物在应力循环加载下也容易形成裂纹。
位错是材料内部的晶格缺陷,应力循环加载容易使位错和裂纹相互作用,导致裂纹扩展。
间隙是指材料中的空隙或孔洞,这些空隙会在应力循环加载下形成新的裂纹。
在宏观层面上,疲劳断裂的失效机理主要与应力和形变有关。
材料在应力循环加载下,会产生应力和形变的变化。
当应力和形变超过一定阈值时,材料易发生塑性变形,易导致裂纹的扩展,最终导致断裂失效。
此外,应力集中也是疲劳断裂的重要机理之一。
如结构中存在缺口、孔洞等几何缺陷,会使应力在这些区域集中,从而增加了材料断裂的风险。
近年来,随着材料科学与工程技术的发展,疲劳断裂的研究得到了广泛的关注。
人们开始尝试利用先进的材料制备技术和表征手段,以提高材料的疲劳寿命和抗疲劳断裂能力。
例如,通过采用新型合金、复合材料和纳米材料等,可以显著提高材料的强度和韧性,从而延长疲劳寿命。
同时,借助先进的表征手段如电子显微镜和原位测量技术,可以更加深入地研究疲劳断裂的微观机理,为材料设计和结构优化提供更精确的参考。
材料疲劳与断裂机理研究

材料疲劳与断裂机理研究材料疲劳与断裂机理是一个重要的研究领域,对于工程材料的设计和使用具有重要意义。
在工程实践中,材料的疲劳与断裂问题经常会导致结构的失效和事故的发生。
因此,深入研究材料疲劳与断裂机理,对于提高材料的性能和安全性具有重要的意义。
材料的疲劳与断裂是由于外界作用下,材料内部的微观缺陷逐渐扩展而导致的。
疲劳是指在外界交变载荷作用下,材料内部的微观缺陷会逐渐扩展,最终导致材料的断裂。
疲劳断裂是一种时间相关的现象,通常需要经过较长时间的循环载荷作用才能发生。
而断裂是指在外界静态或动态载荷作用下,材料内部的微观缺陷会迅速扩展,导致材料的瞬时断裂。
材料的疲劳与断裂机理研究主要包括两个方面:疲劳寿命预测和断裂机制分析。
疲劳寿命预测是指通过实验和理论分析,确定材料在一定载荷下的疲劳寿命。
疲劳寿命预测是工程设计和材料选择的重要依据。
断裂机制分析是指通过实验和理论模型,揭示材料在断裂过程中的微观机制和力学行为。
断裂机制分析可以为工程实践提供指导,帮助设计和制造更可靠的结构。
疲劳寿命预测是材料疲劳与断裂机理研究的重要内容之一。
疲劳寿命预测通常通过实验和数值模拟相结合的方法进行。
实验方法主要是设计疲劳试验,通过对不同载荷下的试样进行疲劳循环加载,测定材料的疲劳寿命。
数值模拟方法主要是建立材料的疲劳损伤模型,通过计算机模拟材料的疲劳寿命。
疲劳寿命预测需要考虑多种因素,如载荷频率、应力幅值、材料的力学性能和微观结构等。
通过研究这些因素对材料疲劳寿命的影响,可以为工程实践提供可靠的疲劳寿命预测方法。
断裂机制分析是材料疲劳与断裂机理研究的另一个重要内容。
断裂机制分析通常通过实验和理论模型相结合的方法进行。
实验方法主要是通过断裂试验,观察材料在断裂过程中的形变和破坏特征,从而揭示材料的断裂机制。
理论模型主要是通过建立材料的断裂力学模型,分析材料在断裂过程中的应力分布和应变分布,从而揭示材料的断裂机制。
断裂机制分析需要考虑多种因素,如应力状态、材料的力学性能和微观结构等。
宏观力学不均质焊接接头疲劳裂纹扩展及裂纹闭合的研究
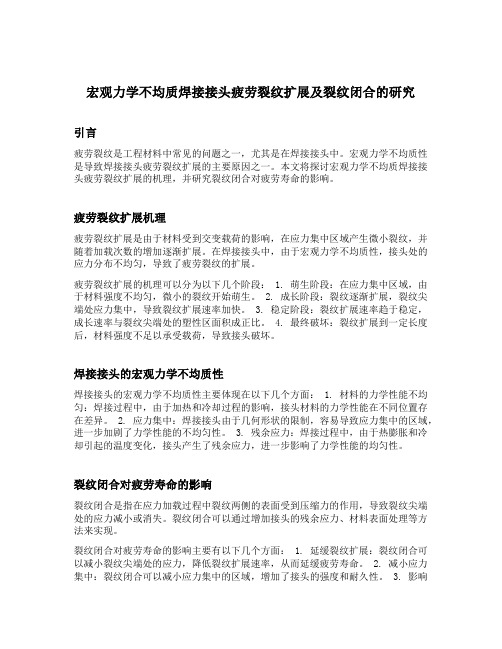
宏观力学不均质焊接接头疲劳裂纹扩展及裂纹闭合的研究引言疲劳裂纹是工程材料中常见的问题之一,尤其是在焊接接头中。
宏观力学不均质性是导致焊接接头疲劳裂纹扩展的主要原因之一。
本文将探讨宏观力学不均质焊接接头疲劳裂纹扩展的机理,并研究裂纹闭合对疲劳寿命的影响。
疲劳裂纹扩展机理疲劳裂纹扩展是由于材料受到交变载荷的影响,在应力集中区域产生微小裂纹,并随着加载次数的增加逐渐扩展。
在焊接接头中,由于宏观力学不均质性,接头处的应力分布不均匀,导致了疲劳裂纹的扩展。
疲劳裂纹扩展的机理可以分为以下几个阶段: 1. 萌生阶段:在应力集中区域,由于材料强度不均匀,微小的裂纹开始萌生。
2. 成长阶段:裂纹逐渐扩展,裂纹尖端处应力集中,导致裂纹扩展速率加快。
3. 稳定阶段:裂纹扩展速率趋于稳定,成长速率与裂纹尖端处的塑性区面积成正比。
4. 最终破坏:裂纹扩展到一定长度后,材料强度不足以承受载荷,导致接头破坏。
焊接接头的宏观力学不均质性焊接接头的宏观力学不均质性主要体现在以下几个方面: 1. 材料的力学性能不均匀:焊接过程中,由于加热和冷却过程的影响,接头材料的力学性能在不同位置存在差异。
2. 应力集中:焊接接头由于几何形状的限制,容易导致应力集中的区域,进一步加剧了力学性能的不均匀性。
3. 残余应力:焊接过程中,由于热膨胀和冷却引起的温度变化,接头产生了残余应力,进一步影响了力学性能的均匀性。
裂纹闭合对疲劳寿命的影响裂纹闭合是指在应力加载过程中裂纹两侧的表面受到压缩力的作用,导致裂纹尖端处的应力减小或消失。
裂纹闭合可以通过增加接头的残余应力、材料表面处理等方法来实现。
裂纹闭合对疲劳寿命的影响主要有以下几个方面: 1. 延缓裂纹扩展:裂纹闭合可以减小裂纹尖端处的应力,降低裂纹扩展速率,从而延缓疲劳寿命。
2. 减小应力集中:裂纹闭合可以减小应力集中的区域,增加了接头的强度和耐久性。
3. 影响疲劳裂纹的形态:裂纹闭合可以改变疲劳裂纹的形态,使其更加平缓,减小了应力集中的程度。
金属材料疲劳断裂机理研究与性能评估
金属材料疲劳断裂机理研究与性能评估金属材料在使用过程中,存在着疲劳断裂的问题。
疲劳断裂是材料在反复应力下发生的微裂纹扩展,最终导致材料的失效。
在工程设计与制造中,对材料的疲劳性能评估至关重要,因为它直接关系到材料的使用寿命和安全性。
本文旨在探讨金属材料疲劳断裂的机理研究和性能评估。
一、金属材料疲劳断裂机理研究1.1 疲劳断裂的基本概念疲劳断裂是指材料在循环载荷下出现的裂纹扩展失效现象。
它具有以下特点:循环载荷、应力水平远低于极限强度时,材料仍会断裂;无论是否有缺陷、裂纹,材料都会发生疲劳断裂;其裂纹扩展方向始终垂直于载荷方向,且遵循马克斯威尔-亚明原理。
1.2 疲劳断裂机理在循环载荷下,金属材料表面的微缺陷、塑性区内部分布的位错、各向异性等因素都会引起材料内部的应力集中。
当材料表面的应力达到局部塑性极限时,就会在此处产生裂纹。
裂纹形成后,由于裂纹尖端处应力集中,会使应力比裂纹尖端位置低的位置高,裂纹尖端处的应力即达到材料的局部塑性极限,裂纹尖端就会继续扩展。
当裂纹长度达到一定值时,就会致使材料的断裂失效。
1.3 影响因素金属材料疲劳断裂是受到诸多因素的影响,如应力水平、循环次数、裂纹扩展方向、腐蚀等因素都会对材料的疲劳性能产生影响。
二、金属材料疲劳性能评估2.1 疲劳寿命测试疲劳寿命测试是评估金属材料疲劳性能的主要方法之一。
在寿命测试中,样品在不同的循环载荷下进行断裂试验,经过统计分析得到样品的疲劳寿命曲线和疲劳极限值。
根据这些数据,可以评估材料的疲劳性能以及使用寿命。
2.2 应力集中系数法应力集中系数法是根据裂纹尖端处的应力集中系数计算材料的疲劳寿命。
它通过测量样品的应变值和载荷值,计算应变幅和载荷幅值的变化,得出应力集中系数,据此推算出样品的疲劳寿命。
2.3 断裂韧性检测对于金属材料的应用,除了考虑疲劳寿命外,在材料设计中,还要关注其断裂韧性。
在断裂韧性检测中,样品进行双头缺口试验,并计算得出其裂纹扩展的临界应力强度因子,据此评估材料的断裂韧性。
金属材料疲劳与断裂行为的研究与分析
金属材料疲劳与断裂行为的研究与分析引言:金属材料在工程领域中扮演着至关重要的角色,然而,其长期受力与损伤的过程中,金属可能会经历疲劳与断裂行为。
疲劳与断裂是金属材料失效的主要形式之一,对金属材料的可靠性和耐久性提出了严峻的挑战。
因此,深入了解金属材料的疲劳与断裂行为是非常重要的。
本文将从疲劳机制、疲劳寿命预测和断裂行为分析三个方面进行讨论,以便提供关于金属材料疲劳与断裂行为的综合研究与分析。
一、疲劳机制:疲劳是由金属受到交替应力加载后,在相对较小的应力水平下发生的失效过程。
疲劳失效是由汇集的微观损伤逐渐积累形成裂纹并扩展最终导致材料断裂。
金属疲劳过程中的微观损伤主要包括晶体内部的位错累积和裂纹的扩展。
位错的累积导致了晶体结构的畸变,使材料内部出现了一系列的变形和塑性变化。
裂纹的扩展是疲劳过程中的关键步骤,裂纹的扩展速率与应力强度因子和材料的断裂韧性密切相关。
二、疲劳寿命预测:疲劳寿命预测是确定金属材料在一定应力水平下能够承受多少次应力循环才会发生断裂的关键问题。
常见的疲劳寿命预测方法主要包括基于应力和应变的疲劳寿命预测和基于损伤评估的疲劳寿命预测。
基于应力和应变的疲劳寿命预测方法主要根据试验得到的应力和应变历程来计算相应的疲劳寿命。
而基于损伤评估的疲劳寿命预测方法则基于损伤累积理论,将微观损伤累积与宏观疲劳寿命进行关联。
这些方法可以通过模拟疲劳试验、应用损伤累积模型以及进行试验验证,对金属材料的疲劳寿命进行预测。
三、断裂行为分析:金属材料在疲劳过程中的断裂行为对于工程结构的安全和可靠性至关重要。
断裂行为的分析需要考虑到断裂的机制和断裂韧性。
断裂机制主要包括韧突和韧面断裂两种形式。
韧突断裂是由于材料的塑性行为导致断裂过程中发生大量能量的耗散,形成一个粗糙的表面。
而韧面断裂则是由于材料的脆性行为导致断裂过程中几乎没有能量的耗散,形成一个相对平滑的断口。
断裂韧性则是描述材料抵抗断裂的能力。
通常使用断裂韧性指标如塞克斯克曼断裂韧性来评估材料的断裂行为。
焊接接头的疲劳断裂机理研究
焊接接头的疲劳断裂机理研究随着工业的发展和技术的进步,焊接接头在各个领域中得到了广泛应用。
然而,焊接接头的疲劳断裂问题一直是工程界关注的焦点。
本文将探讨焊接接头的疲劳断裂机理,并分析其中的原因和解决方案。
焊接接头是将两个或多个金属部件通过熔合的方式连接在一起的工艺。
焊接接头的疲劳断裂是指在循环载荷作用下,焊接接头出现裂纹并最终断裂的现象。
疲劳断裂对于工程结构来说是非常危险的,因为它往往是突然发生的,而且很难被察觉到。
因此,研究焊接接头的疲劳断裂机理对于预防事故的发生至关重要。
焊接接头的疲劳断裂机理可以分为两个方面:焊缝区域的疲劳断裂和热影响区的疲劳断裂。
焊缝区域的疲劳断裂是由于焊接过程中产生的缺陷和应力集中导致的。
焊接过程中,由于焊接材料的熔化和凝固,焊缝中会产生气孔、夹杂物和裂纹等缺陷。
这些缺陷会导致焊缝区域的强度降低,从而容易引发疲劳断裂。
此外,焊接接头中的应力集中也会导致焊缝区域的疲劳断裂。
焊接接头中由于材料的不均匀性和焊接过程中的温度变化,会导致应力集中的形成,从而加速了焊缝区域的疲劳断裂。
另一方面,热影响区的疲劳断裂是由于焊接过程中的热输入导致的。
焊接过程中,焊接接头周围的材料会受到高温的影响,从而发生相变和晶粒长大等现象。
这些热输入引起的材料变化会导致热影响区的力学性能发生变化,从而增加了疲劳断裂的风险。
为了解决焊接接头的疲劳断裂问题,可以采取一系列的措施。
首先,焊接过程中应严格控制焊接参数,以减少焊接缺陷的产生。
例如,可以通过优化焊接电流和焊接速度来控制焊接过程中的热输入,从而减少气孔和夹杂物的产生。
其次,可以采用预处理技术来改善焊接接头的力学性能。
例如,可以通过热处理和表面强化等方法来提高焊接接头的强度和韧性,从而延缓疲劳断裂的发生。
此外,还可以通过改变焊接接头的几何形状和结构设计来减少应力集中,从而降低焊接接头的疲劳断裂风险。
总之,焊接接头的疲劳断裂机理是一个复杂而重要的问题。
焊接接头的疲劳损伤与断裂行为研究
焊接接头的疲劳损伤与断裂行为研究焊接接头是工程结构中常见的连接方式,它能够将两个或多个金属构件牢固地连接在一起。
然而,长期以来,焊接接头在使用过程中经常出现疲劳损伤和断裂的问题,给工程结构的安全性和可靠性带来了威胁。
因此,研究焊接接头的疲劳损伤与断裂行为成为了一个重要的课题。
焊接接头的疲劳损伤是指在循环荷载作用下,接头内部产生的微小裂纹逐渐扩展并最终导致断裂的过程。
疲劳断裂是一种隐蔽性较强的断裂形式,常常在无明显预兆的情况下发生,给工程结构带来了巨大的安全隐患。
焊接接头的疲劳损伤与断裂行为受多种因素的影响,其中最重要的是应力水平和循环次数。
应力水平是指接头在循环荷载作用下所承受的最大应力,它对接头的疲劳寿命有着决定性的影响。
循环次数是指接头在循环荷载作用下所经历的循环次数,它也是影响接头疲劳寿命的重要因素。
除此之外,焊接接头的几何形状、焊接质量、材料性能等因素也会对疲劳损伤与断裂行为产生一定的影响。
研究表明,焊接接头的疲劳损伤与断裂行为与接头的微观结构有着密切的关系。
焊接接头的微观结构包括焊缝区域、热影响区和母材区。
焊缝区域是焊接接头中最脆弱的部分,容易发生裂纹的产生和扩展。
热影响区是指焊接过程中受到热影响而发生组织改变的区域,它对接头的疲劳性能有着重要的影响。
母材区是焊接接头中相对较强的部分,但也存在一定的疲劳问题。
因此,研究焊接接头的微观结构对于理解接头的疲劳损伤与断裂行为具有重要意义。
为了研究焊接接头的疲劳损伤与断裂行为,科学家和工程师们采用了多种研究方法和手段。
其中,实验研究是最常用的方法之一。
通过在实验室中设计和搭建相应的实验装置,可以对焊接接头在不同应力水平和循环次数下的疲劳性能进行测试和评估。
此外,还可以通过断口分析、金相显微镜观察等手段,研究焊接接头的断裂行为,并进一步揭示其破坏机制。
除了实验研究外,数值模拟也是研究焊接接头疲劳损伤与断裂行为的重要方法之一。
通过建立适当的数学模型和计算方法,可以模拟焊接接头在不同应力水平和循环次数下的疲劳寿命,并分析其疲劳损伤和断裂行为。
- 1、下载文档前请自行甄别文档内容的完整性,平台不提供额外的编辑、内容补充、找答案等附加服务。
- 2、"仅部分预览"的文档,不可在线预览部分如存在完整性等问题,可反馈申请退款(可完整预览的文档不适用该条件!)。
- 3、如文档侵犯您的权益,请联系客服反馈,我们会尽快为您处理(人工客服工作时间:9:00-18:30)。
对铆接疲劳裂纹产生机理的探讨
【摘要】自冲铆接的微裂纹会在铆接孔中产生,这主要是由于材料内部组织的不均匀性及铆接模具的结构、形状造成的。
本文对接疲劳裂纹产生机理进行了探讨研究。
【关键词】自冲铆接;微裂纹;裂纹扩展;疲劳强度
0.引言
自冲铆接技术是采用一个铆钉连接两个或更多部件的方法,它实行冲铆一次完成。
半空心铆钉自冲铆接工艺的铆接过程铆钉在冲头的作用下,穿透上层板料,在凹模和铆钉外形共同作用下空心铆钉尾部在下层金属中张开形成喇叭口形状。
自冲铆接除了可连接上述点焊所难于连接的材料外,自冲铆接和点焊相比还具有许多点焊所不具备的优点:能连接不同材料,能和粘接复合连接,无发光,发热少,疲劳强度较高,快捷等。
1.自冲铆接疲劳破坏方式
自冲铆接的疲劳扩展最易在铆接孔处扩展,且在宏观上裂纹扩展方向垂直于载荷方向,且裂纹宏观方向通过铆接孔中心,在裂纹扩展末期的瞬断时形成剪切唇,剪切唇与载荷成大约45o,这其实是由于强度不足所致。
有的时候自冲铆接疲劳裂纹不在铆接孔发生,而有可能在铆接孔附近靠近铆钉头部的地方萌生和扩展,这主要由于铆钉在受载时会对板料有一个弯曲作用。
在有的时候,比如自冲铆接和粘接复合连接时,或材料缺陷情况下,疲劳萌生和扩展还可能发生在板料的其他部位。
2.自冲铆接微裂纹的产生
铆钉可用钢材或硬铝等制作,一般经热处理来适当提高其韧、硬度,这主要取决于被铆接材料特性如强度、硬度、厚度等。
被铆接的材料常有钢板、铝板或铝合金、塑料、铜或铜合金、高分子材料及复合材料等,一般其硬度不能太高,否则铆钉将难刺穿上板料,若采用更高硬度的铆钉,但这样铆钉在刺入板料和张开时易开裂,且增大了刺入力。
由于铆钉刺进板料时,板料内部强度、硬度、结构、相分布、原子结合力不均,晶粒、晶界性状不一等原因导致板料的铆钉孔孔壁有毛刺、微裂纹,这些将是导致自冲铆接失效的重要扩展源。
下面阐述裂纹不在铆接孔中产生的情况。
金属中常见的有面心立方晶格、体心立方晶格、密排六方晶格等多种结构,它们具有多种滑移系和滑移方向,晶体是各向异性的。
在其受力时可沿着受载最大或最弱的、抗力最小的晶面和晶向滑
移,在每一次滑移时晶面和晶向都有可能不同,这样就有可能导致产生侵入沟、挤出脊、晶格畸变或位错堆积等缺陷,导致出现微裂纹。
由于材料在成形时温度高低不是很均匀、化学成分也不可能非常均匀(如钢中的碳元素)、表面和内部散热不均、化学成分偏析或偏聚也不均匀等原因,可能导致多种晶体结构同时存在,不过可能有一种或几种结构为主,况且材料一般都是含有多种元素,则原子间作用力或键的作用力将不同,其对内、外界环境和作用载荷改变而应力的变化也不同,这也将导致最薄弱处出现微裂纹;每种结构、成分的机械性能(如硬脆度、强度等)和形状、结构就不同,受载时材料内部的微观部分的受力肯定不一样(如应力集中等);那么由以上各原因,经过反复不断的受载则位错或微裂纹将在最薄弱处发生。
一般金属材料都是多晶体构成的,如果结晶时温度不太均匀、散热不均匀、冷却不均匀或其他添加元素、杂质干扰等情况,金属内可能出现两种或多种晶格,微观受载不均就位错增加而出现微裂纹。
每种晶格分别存在一个个小晶体内,这样一些小晶体常排列方向各异,各小晶体间以不规则的、畸变的结构连接,形成晶界或亚晶界,晶界或亚晶界强度和硬度较高,但其方向、排列、结构、强度等各异,且存在位错,在受到交变载荷、冲击载荷、循环载荷、受力不均匀、应力集中等情况时,由于变形不协调、不均匀或附加载荷等,相对较弱的晶界和亚晶界可能发生更大的位错,或小孔洞,甚至破裂成微裂纹;也可能因小晶体内的微观或显微局部强度不够,当载荷长时间作用时,某些小缺陷就不断扩展成微裂纹,然后微裂纹经很多次扩展就穿晶破裂。
金属材料内部常有其他金属或非金属元素。
如钢材中添加的碳、硅、硫、磷、铬、镍等等元素,这些元素往往固溶于基体中(如在钢材中这些元素会固溶于铁晶格中形成固溶体)或形成金属化合物等,且铝合金中可能有α、θ、S等相,铜合金中可能有α、δ、β‘等相,还可形成金属化合物如渗碳体等,载荷在微观不均,位错增加,微裂纹将在薄弱处产生;由于化学成分不完全均匀,各种成分在进行物理化学变化时所处的条件也不完全毫无差别,这些相可能同时存在,且可能方向、位置及形状等较为杂乱,微观受载不均,位错堆积,微裂纹将在薄弱处产生;而且比如常用的退火、正火的钢材由于化学元素是否均匀、是否偏聚偏析、热处理加热快慢、加热是否均匀、降温速度、降温是否均匀等影响可能导致材料中同时存在铁素体、珠光体、渗碳体等各种相、结构,而各种相的强度、硬度、韧性、伸长率等不一,这样当材料受到外载时,在微观中的每个相的各个部分的微观变形及受力就不一样,这使得最薄弱处出现微裂纹;且由于加温、降温等在材料内部和外部差别不一等情况,可导致材料内部应力大小不一,甚至出现有的地方是拉应力而有的地方是压应力,且可能应力大小差别较大,薄弱处也将出现微裂纹;在应力集中或局部受力超过相的强度极限等情况下,相特别是其尖端可能破裂或者和相邻的相之间产生更长更宽的位错以及压破相邻的相,而后出现微裂纹;如渗碳体等硬脆相在应力集中和局部过载时易脆断,或者珠光体等较强韧相压破相邻的弱相,而出现微裂纹;以及在晶界原子结构畸变处累积位错,这样晶界处可能产生微裂纹,特别是那些局部的尖锐的板条状渗碳体;且由于金属材料成形时的相变和温度改变不均等可能造成应力集中或初始位错等。
所有以上情况经反复加载就成了微裂纹。
金属中还有夹杂物如氧化物、硫化物、硅酸盐、耐火材料微末等,可以是球形、片状、有尖角的不规则形状或有圆角的多面体形,杂质间还可以互相连通,杂质和基体的连接强度较弱,这样就把材料基体割裂了,受到一定时间载荷就形成了裂纹。
金属中还可能有气孔、缩孔、有杂质等缺陷,它们中有的即使在轧制时也可能不能压合成一体。
它们的形状各异,在这些缺陷边缘处材料受到一个较大弯矩作用,故容易出现微裂纹。
且在这些缺陷的边缘,特别是垂直于载荷的片状裂纹尖角应力集中,则尖端容易堆积位错而塑性下降,然后撕裂成微裂纹。
3.结语
自冲铆接的微裂纹往往在铆接孔中产生,这主要是由于精品源自地理科材料内部微观组织性能不一致,及材料不均匀和模具的形状决定铆接孔中有毛刺和微裂纹。
对于本文所述,微裂纹在铆接孔外产生的情形,往往由于材料内部的组织、相的物理和力学性能的不一致,如微观组织的微观强度、韧性和塑性等不一致造成的。
微裂纹的扩展主要是由于裂纹受到一个撕裂弯矩,且附加有拉伸力作用,而这些载荷综合作用在裂尖附近的微小区域内,故裂尖附近综合应力很大,当综合应力超过材料微观强度极限时(不同于普通意义上的强度极限,因为那个描述的是材料的平均强度极限),裂纹就扩展。
在铆钉孔中分布力产生的对垂直于载荷的直径与孔边缘交点的弯矩很大,故在铆钉孔中很容易发生疲劳裂纹扩展现象。
由于弯矩的力臂越来越大,弯矩就越来越大,故疲劳裂纹扩展越来越快,故疲劳寿命主要由疲劳裂纹萌生寿命和小裂纹的扩展寿命组成。