铜冶炼水淬渣中铜的资源化利用研究
铜渣的处理与资源化
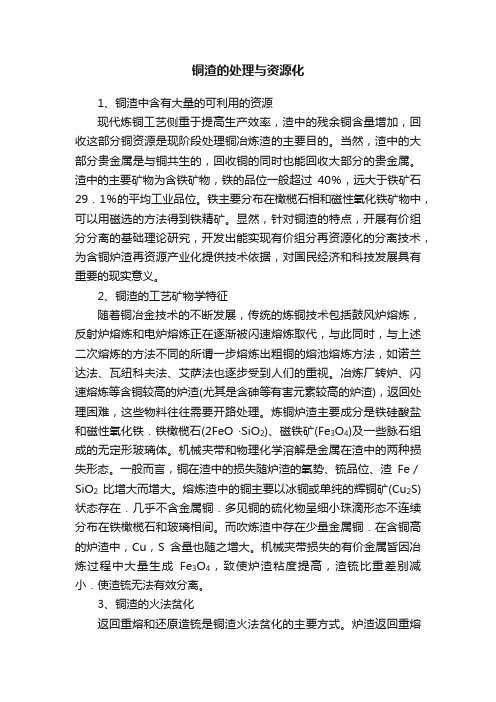
铜渣的处理与资源化1、铜渣中含有大量的可利用的资源现代炼铜工艺侧重于提高生产效率,渣中的残余铜含量增加,回收这部分铜资源是现阶段处理铜冶炼渣的主要目的。
当然,渣中的大部分贵金属是与铜共生的,回收铜的同时也能回收大部分的贵金属。
渣中的主要矿物为含铁矿物,铁的品位一般超过40%,远大于铁矿石29.1%的平均工业品位。
铁主要分布在橄榄石相和磁性氧化铁矿物中,可以用磁选的方法得到铁精矿。
显然,针对铜渣的特点,开展有价组分分离的基础理论研究,开发出能实现有价组分再资源化的分离技术,为含铜炉渣再资源产业化提供技术依据,对国民经济和科技发展具有重要的现实意义。
2、铜渣的工艺矿物学特征随着铜冶金技术的不断发展,传统的炼铜技术包括鼓风炉熔炼,反射炉熔炼和电炉熔炼正在逐渐被闪速熔炼取代,与此同时,与上述二次熔炼的方法不同的所谓一步熔炼出粗铜的熔池熔炼方法,如诺兰达法、瓦纽科夫法、艾萨法也逐步受到人们的重视。
冶炼厂转炉、闪速熔炼等含铜较高的炉渣(尤其是含砷等有害元素较高的炉渣),返回处理困难,这些物料往往需要开路处理。
炼铜炉渣主要成分是铁硅酸盐和磁性氧化铁.铁橄榄石(2FeO ·SiO2)、磁铁矿(Fe3O4)及一些脉石组成的无定形玻璃体。
机械夹带和物理化学溶解是金属在渣中的两种损失形态。
一般而言,铜在渣中的损失随炉渣的氧势、锍品位、渣Fe/SiO2比增大而增大。
熔炼渣中的铜主要以冰铜或单纯的辉铜矿(Cu2S)状态存在.几乎不含金属铜.多见铜的硫化物呈细小珠滴形态不连续分布在铁橄榄石和玻璃相间。
而吹炼渣中存在少量金属铜.在含铜高的炉渣中,Cu,S含量也随之增大。
机械夹带损失的有价金属皆因冶炼过程中大量生成Fe3O4,致使炉渣粘度提高,渣锍比重差别减小.使渣锍无法有效分离。
3、铜渣的火法贫化返回重熔和还原造锍是铜渣火法贫化的主要方式。
炉渣返回重熔是回收铜的传统方法,产生的冰铜返主流程。
针对炉渣的钴、镍回收,采取在主流程之外的单独还原造锍。
废杂铜冶炼渣中铜资源有效回收方案
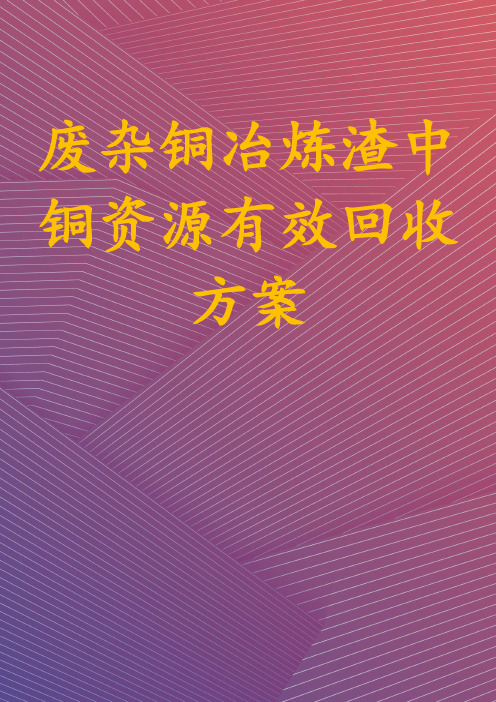
废杂铜冶炼渣中铜资源有效回收方案废杂铜冶炼渣中铜资源有效回收方案废杂铜冶炼渣中含有一定量的铜资源,有效回收这些资源可以减少资源浪费,并且对环境具有积极作用。
下面将逐步介绍废杂铜冶炼渣中铜资源的有效回收方案。
第一步:渣料预处理首先,需要对废杂铜冶炼渣进行预处理。
这包括对渣料进行筛分和磁选,以去除其中的杂质和磁性物质。
筛分可以将较大颗粒的渣料分离出来,而磁选可以去除含有磁性物质的渣料,使得后续步骤更为高效。
第二步:酸浸提取接下来,将经过预处理的渣料进行酸浸提取。
这一步骤可以利用酸性溶液中铜与渣料中的铜发生反应,将铜离子溶解在溶液中。
常用的酸浸剂包括硫酸和盐酸。
酸浸提取的条件如溶液浓度、反应时间和温度等需要根据具体情况进行优化调节,以提高铜的溶解效率。
第三步:溶液处理经过酸浸提取后,得到含有铜离子的溶液。
为了进一步提取和回收铜资源,需要对溶液进行处理。
常见的处理方法包括电解、溶剂萃取和水热法等。
电解是最常用的方法之一,通过在电解槽中施加电场,使得铜离子在阳极上还原成纯铜。
溶剂萃取则是利用有机溶剂将溶液中的铜离子萃取出来,然后通过脱溶剂和再溶剂两个步骤将铜离子从有机相转移到水相,最终得到纯铜。
而水热法则是利用水热条件下的化学反应,通过添加特定试剂将溶液中的铜离子转化成稳定的铜化合物或纳米颗粒,然后通过过滤或离心等操作得到纯铜。
第四步:铜产品制备最后,通过对溶液进行干燥、熔炼等处理,可以得到纯度较高的铜产品。
这些铜产品可以进一步加工,例如铸造成铜坯、制备铜粉等,以满足不同的应用需求。
通过以上步骤,废杂铜冶炼渣中的铜资源可以得到有效回收。
这不仅可以减少资源浪费,降低环境污染,还可以提高资源利用效率,促进可持续发展。
因此,对废杂铜冶炼渣中的铜资源进行有效回收具有重要的经济和环境意义。
从炼铜水淬渣中浮选回收铜的试验研究
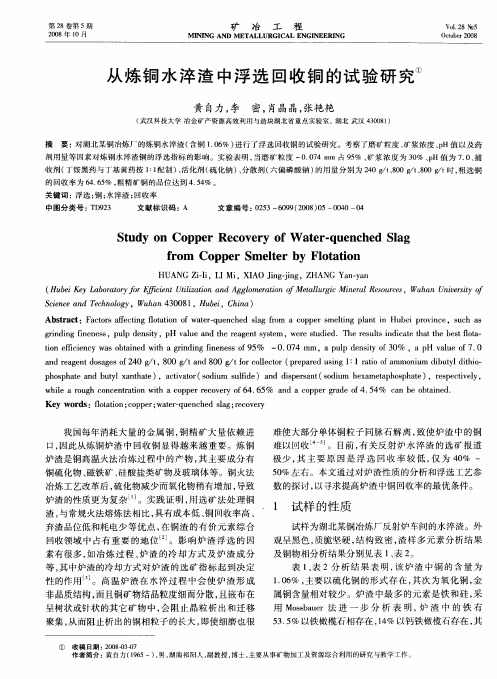
我 国每年 消耗 大量 的 金 属铜 ,铜 精 矿 大 量依 赖 进 口,因此从 炼铜 炉渣 中 回收 铜显 得 越来 越重 要 。炼 铜 炉渣 是铜 高温火 法 冶炼 过 程 中 的产 物 ,其 主 要成 分 有 铜硫 化物 、磁铁 矿 、硅 酸盐类 矿物 及玻璃 体 等 。铜 火法 冶炼 工艺 改革后 ,硫化 物减 少而 氧化物 稍有 增加 ,导致 炉 渣 的性 质更 为复 杂 ¨J。实 践证 明 ,用 选 矿 法处 理 铜 渣 ,与常 规火法 熔炼 法相 比 ,具有 成本 低 、铜 回收率高 、 弃 渣 品位 低和耗 电少等 优 点 ,在 铜 渣 的有 价 元 素综 合 回收领 域 中 占有 重 要 的地 位 。影 响 炉 渣 浮 选 的 因 素 有很 多 ,如 冶 炼 过 程 、炉 渣 的冷 却 方 式 及 炉 渣 成 分 等 ,其 中炉渣 的冷却 方 式对 炉渣 的选矿 指 标 起 到决 定 性 的作 用 。高 温 炉 渣 在 水 淬 过 程 中会 使 炉 渣 形 成 非晶质结构 ,而且铜矿物结晶粒度细而分散 ,且嵌布在 呈树 状 或针状 的其 它矿 物 中 ,会 阻 止 晶粒 析 出和 迁 移 聚集 ,从 而阻止 析 出 的铜 相粒 子的 长大 ,即使 细磨也 很
and reagent dosages of 240 g/t,800 g/t and 800 g/t for collector(prepared using 1:1 ratio of ammonium dibutyl dithio— phosphate and butyl xanthate),activator(sodium sulf ide)and dispersant(sodium hexametaph0sphate),respectively,
铜冶炼渣的资源化利用
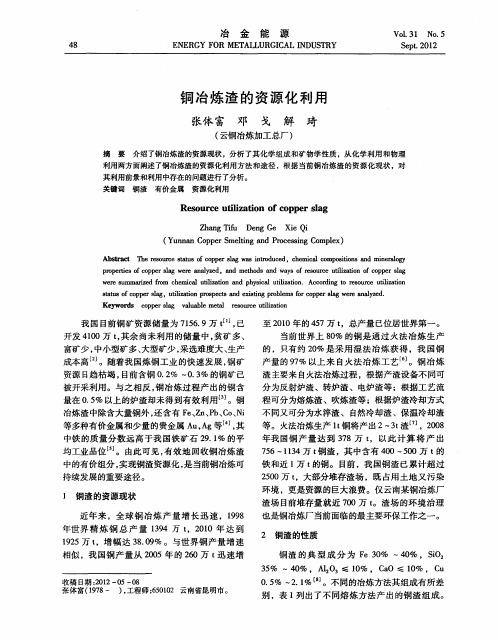
Z agTf D n e X eQ hn i e gG i i h
( u n nC p e me iga dPoes gC m l ) Y n a op rS ln n rcsi o pe t n x
Ab ta t Th e o r e sau fc p e 1g wa n r d c d,c e c l c mp st n n n r o y sr c e rs u c tt s o o p r s s i t u e a o h mia o o i o s a d mi e a g i l p o r e fc p rsa r n y e rp t s o o p lg wee a a z d,a d me h d n a s o s u c t z f n o o p r sa e i e l n t o s a d w y f r o re u H a o c p lg e i i f e
5 %降低到 03 % 以下。王学文等¨ 人在真空条 .5 训
件 下研究 了真空 度 、温度 、处理 时间 、渣型 及添
z 等 用 “ a 氧化浸出 一 萃取”法从铜渣 中回收
有价金属 ,在常压下用 H s . H O 混合溶液 2O 和 2 2 对铜渣进行氧化浸 出,再用萃取剂分步萃取浸 出 液 得到有 价 金 属 ,C 、C Z u O n回收 率 分 别 达 到 8 %、9 %、9 %。蒋镜宇等人采用碳铵 一 0 0 0 氨水 体系浸取黄铜熔 炼渣 ,黄铜熔炼渣经稀碱洗 涤 后 ,在碳铵 一 氨水体系中浸出,铜、锌的浸出率
形玻璃体 引,其 中铜主要 以辉铜矿 ( uS 、金 C:)
表 1 典型熔炼炉渣的化 学成分
3 铜渣 的资源 化利 用
间 2 , 属铜 的 回收率 达到 8 % 以上 。 h金 5
铜渣综合利用的研究情况与难点及新技术论文
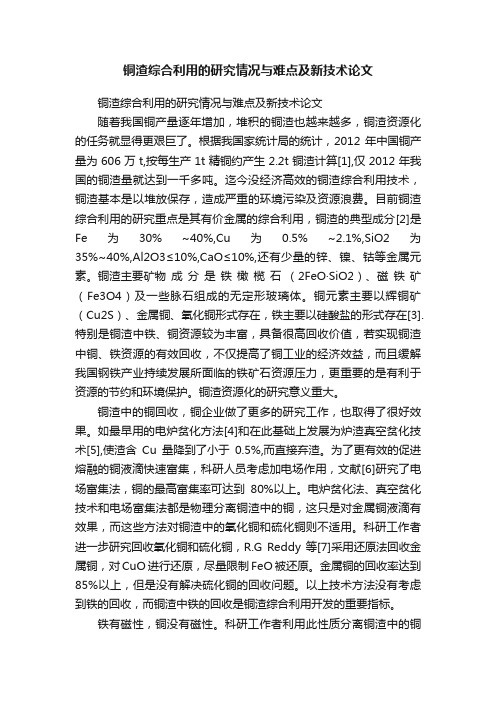
铜渣综合利用的研究情况与难点及新技术论文铜渣综合利用的研究情况与难点及新技术论文随着我国铜产量逐年增加,堆积的铜渣也越来越多,铜渣资源化的任务就显得更艰巨了。
根据我国家统计局的统计,2012年中国铜产量为606万t,按每生产1t精铜约产生2.2t铜渣计算[1],仅2012年我国的铜渣量就达到一千多吨。
迄今没经济高效的铜渣综合利用技术,铜渣基本是以堆放保存,造成严重的环境污染及资源浪费。
目前铜渣综合利用的研究重点是其有价金属的综合利用,铜渣的典型成分[2]是Fe为30% ~40%,Cu为0.5% ~2.1%,SiO2为35%~40%,Al2O3≤10%,CaO≤10%,还有少量的锌、镍、钴等金属元素。
铜渣主要矿物成分是铁橄榄石(2FeO·SiO2)、磁铁矿(Fe3O4)及一些脉石组成的无定形玻璃体。
铜元素主要以辉铜矿(Cu2S)、金属铜、氧化铜形式存在,铁主要以硅酸盐的形式存在[3].特别是铜渣中铁、铜资源较为丰富,具备很高回收价值,若实现铜渣中铜、铁资源的有效回收,不仅提高了铜工业的经济效益,而且缓解我国钢铁产业持续发展所面临的铁矿石资源压力,更重要的是有利于资源的节约和环境保护。
铜渣资源化的研究意义重大。
铜渣中的铜回收,铜企业做了更多的研究工作,也取得了很好效果。
如最早用的电炉贫化方法[4]和在此基础上发展为炉渣真空贫化技术[5],使渣含Cu量降到了小于0.5%,而直接弃渣。
为了更有效的促进熔融的铜液滴快速富集,科研人员考虑加电场作用,文献[6]研究了电场富集法,铜的最高富集率可达到80%以上。
电炉贫化法、真空贫化技术和电场富集法都是物理分离铜渣中的铜,这只是对金属铜液滴有效果,而这些方法对铜渣中的氧化铜和硫化铜则不适用。
科研工作者进一步研究回收氧化铜和硫化铜,R.G Reddy等[7]采用还原法回收金属铜,对CuO进行还原,尽量限制FeO被还原。
金属铜的回收率达到85%以上,但是没有解决硫化铜的回收问题。
铜渣综合利用的研究情况与难点及新技术论文

铜渣综合利用的研究情况与难点及新技术论文铜渣是铜冶炼过程中产生的一种含铜固体废弃物。
传统上,铜渣被视
为废弃物,只能用于填埋或堆放。
然而,随着资源的日益紧缺和环境意识
的提高,对于铜渣的综合利用研究变得越来越重要。
下面将介绍铜渣综合
利用的研究情况、难点以及新技术论文。
铜渣综合利用的研究最早起源于20世纪80年代,主要集中在两个方面:铜渣中铜的回收和铜渣的资源化利用。
铜渣中铜的回收是指将废渣中
的有价金属回收利用,目前主要方法包括浮选、磁选和火法冶炼等;而资
源化利用则是指将铜渣转化为可利用的材料,主要包括水泥、陶瓷、制砂、铜渣掺合料等。
随着研究的深入,人们开始探索更加高效、环保的铜渣综
合利用方法,如高效回收、废渣中有价金属的回收、废渣中的环境污染物
处理等。
铜渣综合利用面临一些困难和挑战。
首先,铜渣成分复杂,含有大量
的非金属元素,如硫、砷、锌等,这些元素会对环境造成污染,并且会影
响废渣的再利用。
其次,铜渣中的有价金属元素含量相对较低,所以如何
高效回收这些金属也是一个难题。
另外,废渣回收利用技术的研究需要考
虑到经济利益和环境效益的平衡,要确保技术的可行性和经济性。
此外,
废渣的后处理也是一个难题,需要针对废渣中的污染物设计合适的处理方法。
废杂铜冶炼渣中铜资源回收技术

废杂铜冶炼渣中铜资源回收技术废杂铜冶炼渣中铜资源回收技术随着工业化的发展,废弃物的处理和资源回收变得尤为重要。
废杂铜冶炼渣中含有丰富的铜资源,因此开发高效的铜回收技术对于环境保护和资源利用具有重要意义。
下面将介绍一种“废杂铜冶炼渣中铜资源回收技术”的步骤。
1. 渣料分析:首先,对废杂铜冶炼渣进行详细的化学成分分析。
通过分析可以确定渣中铜的含量以及其他有害元素的含量,为后续的处理提供基础数据。
2. 磨碎和筛分:将废杂铜冶炼渣进行机械磨碎和筛分,使其颗粒尺寸均匀一致,方便后续处理。
筛分可以将渣中的大颗粒杂质分离出来。
3. 酸浸:将筛选后的冶炼渣放入酸浸槽中,用稀硫酸或盐酸进行浸取。
通过酸浸可以将渣中的铜溶解出来形成铜离子。
4. 溶液过滤:将酸浸后的溶液进行过滤,去除其中的固体杂质和杂质颗粒。
这样可以得到相对纯净的铜离子溶液。
5. 电解:将过滤后的铜离子溶液放入电解槽中进行电解。
电解过程中,铜离子在电极上还原成固体的金属铜,同时释放出电子。
经过电解后,可以得到高纯度的铜。
6. 铜收集和熔炼:将电解后的固体铜收集起来,进行熔炼。
熔炼可以进一步提高铜的纯度,并将其他杂质从铜中分离出来。
熔炼后的铜可以用于再次冶炼或者制作各种铜制品。
需要注意的是,在废杂铜冶炼渣中,可能存在一些有毒有害物质,如重金属等。
因此,在处理过程中应采取相应的防护措施,确保操作人员的安全。
通过上述步骤,废杂铜冶炼渣中的铜资源可以高效回收利用,实现资源的循环利用,降低环境污染。
同时,这种技术还可以为冶炼企业带来经济效益,节约成本。
因此,废杂铜冶炼渣中铜资源回收技术具有重要的应用前景和社会意义。
冶炼水淬渣含铜分析方法改进及应对策略

1 . 2 干 技术 人员 每天 根据 化验 的数 据进 行加 料量 和入 炉矿 料来 控制 硅 铁 比 , 避 免 低 铁 硅 比例 产生 的 大量 大链 硅 酸盐 分 子 , 从 而 使熔 渣 粘度 变 大 。大 多
有 时达 2 ~2 . 2 ,为确 保 化 验分 析 数 据 的 准确 性 , 对
学 特性及 成 分选择 其 冶炼途 径 。传统 的方法是 在 提 取 金属 之前 先改 变 矿 物 的化 学 成 分 , 让 它 们 在 空 气
中进行 焙烧 , 使其 生 成 铅 、 锌 的氧 化 物 , 而 后 在 下 一
阶段对 金 属进行 还 原 , 主要 原 因 是 不能 直 接 用 碳 把 硫化 物 中的金 属 还原 出来 。因此 , 必 须根 据 硫 化 矿
冶 炼 水 淬 渣 含 铜 分 析 方 法 改进 及 应 对 策 略
于 兰 英
( 中 国有 色 集 团 抚顺 红 透 山矿 业 有 限公 司 , 辽宁 抚顺 1 1 3 3 2 1 )
摘 要 : 控 制 铜 冶 炼 最 终产 物 水 淬 渣 的 质 量 是 减 少 冶 炼 生 产 过 程 中铜 流 失 的 主要 渠 道 。为 了提 高 粗 铜 的质 量 , 减 少 冶 炼 生 产 过 程 中铜 的 流失 , 冶 炼 工 艺 中必 须 控 制 水 淬 渣 中的 含 铜 量 。 由
稀 散金 属 常与铅 锌 硫 化 物共 生 , 因此 一 般 的 硫 化 矿 都 是金 属复 合矿 , 具 有 综 合 利 用 的 价 值 。现 代 硫 化 矿 的处 理 主要依 靠 火 法 冶金 , 提 取金 属 的方 法 较 处
理 氧化 矿 复杂 。因 此 , 必 须 根 据 硫 化 矿 物 的 物 理 化
- 1、下载文档前请自行甄别文档内容的完整性,平台不提供额外的编辑、内容补充、找答案等附加服务。
- 2、"仅部分预览"的文档,不可在线预览部分如存在完整性等问题,可反馈申请退款(可完整预览的文档不适用该条件!)。
- 3、如文档侵犯您的权益,请联系客服反馈,我们会尽快为您处理(人工客服工作时间:9:00-18:30)。
铜冶炼水淬渣中铜的资源化利用研究
本文采用湿法冶金技术对我国铜冶炼过程中产生的大量水淬渣进行铜的资
源化利用研究,研究采用氧化氨浸法对铜冶炼水淬渣中铜进行浸取,并考察浸取
时间、浸出温度、过硫酸铵用量、氨水浓度、渣样粒度大小、搅拌转速、液固比对铜浸出率的影响,得出铜浸出的最佳条件。
浸出后的溶液与硫化铵反应,制取硫化铜,并研究硫化铵用量、反应温度、机械搅拌速度、反应时间对浸出液中铜回收率及硫化铜纯度的影响,得出影响浸出液中铜回收率及硫化铜纯度的最佳条件。
具体实验结果如下:(1)取10g渣样,当控制温度为50℃,浸取时间为120min,粒径大小为100目,转速为400r/min,(NH4)2S2O8用量为渣样的0.7倍,NH3·H2O 浓度为10mol/L时考察液固比(m/m)对铜冶炼水淬渣中铜、锌浸出率的影响。
实验结果表明:最佳液固比为4:1(m/m),此时,Cu浸出率为49.1%,Zn浸出率为
0.32%。
(2)取10g渣样,当控制液固比(m/m)为4:1,浸取时间为120min,粒径大小为100目,转速为400r/min,用量为渣样的0.7倍,NH3·H2O浓度为10mol/L时考察温度对铜冶炼水淬渣中铜、锌浸出率的影响。
实验结果表明:最佳温度为35℃,此时,Cu的浸出率为53.5%,Zn的浸出率为0.15%。
(3)取10g渣样,当控制液固比(m/m)为4:1,温度为35℃,粒径大小为100目,转速为400r/min,用量为渣样的0.7倍,NH3·H2O浓度为10mol/L时考察浸取时间对铜冶炼水淬渣中铜、锌浸出率的影响。
实验结果表明:最佳浸取时间为180min,此时,Cu的浸出率为58.3%,Zn的浸出率为0.23%。
(4)取10g渣样,当控制液固比(m/m)为4:1,温度为35℃,浸取时间为180min,转速为400r/min,用量为渣样的0.7倍,NH3·H2O浓度为10mol/L时考察粒径大
小对铜冶炼水淬渣中铜、锌浸出率的影响。
实验结果表明:最佳颗粒粒度为200目,此时,Cu的浸出率为79.2%,Zn的浸出率为0.23%。
(5)取l0g渣样,当控制液固比(m/m)为4:1,温度为35℃,浸取时间为180min,粒径大小为200目,(NH4)2S2O8用量为渣样的0.7倍,NH3·H2O浓度为10mol/L 时考察搅拌速度对铜冶炼水淬渣中铜、锌浸出率的影响。
实验结果表明:最佳搅拌速度为500(r/min),此时,Cu的浸出率为80.6%,Zn的浸出率为0.19%。
(6)取10g渣样,当控制液固比(m/m)为4:1,温度为35℃,浸取时间为180min,粒径大小为200目,转速为500r/min,NH3·H2O浓度为10mol/L时考察(NH4)2S2O8用量对铜冶炼水淬渣中铜、锌浸出率的影响。
实验结果表明:最佳过硫酸铵用量为渣样的0.4倍,此时,Cu浸出率为80.8%,Zn的浸出率为0.27%。
(7)取10g渣样,当控制液固比(m/m)为4:1,温度为35℃,浸取时间为180min,粒径大小为200目,转速为500r/min,(NH4)2S2O8用量为渣样的0.4倍时考察NH3·H2O浓度对铜冶炼水淬渣中铜、锌浸出率的影响。
实验结果表明:最佳氨水的浓度为11mol/L,此时,Cu的浸出率为81.7%,Zn的浸出率为0.13%。
即此时为铜冶炼水淬渣中铜浸出的最佳条件。
(8)铜氨浸出液经火焰原子吸收分光光度计检测得:浸出液中的金属基本为铜,铜含量为85.4mg/L,锌的含量很少,锌含量为1.4mg/L, Cu的浸出率为81.7%,Zn的浸出率为0.13%,检测不出其它金属。
(9)取铜氨浸出液500mL,控制反应温度为25℃,机械搅拌速度为200r/min,反应时间为20min,考察(NH4)2S用量对铜回收率及硫化铜纯度的影响。
实验结果表明:最佳(NH4)2S用量为理论量的1.6倍,此时,铜氨浸出液中铜回收率为90.4%,硫化铜纯度为96.9%,并且硫化铵用量对硫化铜纯度影响不明显。
(10)取铜氨浸出液500mL,控制硫化铵用量为理论量的1.6倍,机械搅拌速度为200r/min,反应时间为20min,考察反应温度对铜回收率及硫化铜纯度的影响。
实验结果表明:最佳反应温度为室温25℃左右,此时,铜回收率为91.1%,硫化铜纯度为98.7%,并且反应温度对硫化铜纯度影响不明显。
(11)取铜氨浸出液500mL,控制硫化铵用量为理论量的1.6倍,反应温度为25℃,反应时间为20min,考察搅拌速度对铜回收率及硫化铜纯度的影响。
实验结果表明:最佳机械搅拌速度为100r/min,此时,铜回收率为91.1%,硫化铜纯度为98.1%,并且搅拌速度对硫化铜纯度影响不明显。
(12)取铜氨浸出液500mL,控制硫化铵用量为理论量的1.6倍,反应温度为25℃,机械搅拌速度为100r/min,考察反应时间对铜回收率及硫化铜纯度影响。
实验结果表明:最佳反应时间为15min,此时,铜回收率为90.9%,硫化铜纯度为97.8%,并且反应时间对硫化铜纯度影响不明显。
即此时为铜氨浸出液中铜回收率及硫化铜纯度的最佳条件,根据公式(4.7)计算得出铜的资源化率为74%。