机械设计制造及其自动化-外文翻译-外文文献-英文文献-液压支架的最优化设计
机械设计制造及自动化中英文对照外文翻译文献
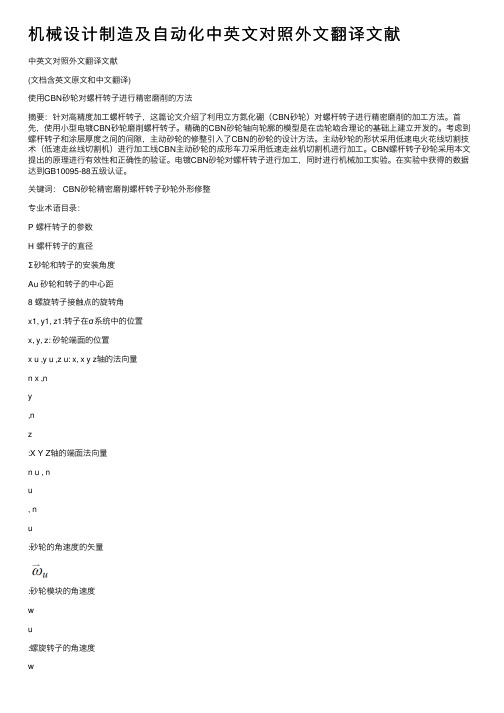
机械设计制造及⾃动化中英⽂对照外⽂翻译⽂献中英⽂对照外⽂翻译⽂献(⽂档含英⽂原⽂和中⽂翻译)使⽤CBN砂轮对螺杆转⼦进⾏精密磨削的⽅法摘要:针对⾼精度加⼯螺杆转⼦,这篇论⽂介绍了利⽤⽴⽅氮化硼(CBN砂轮)对螺杆转⼦进⾏精密磨削的加⼯⽅法。
⾸先,使⽤⼩型电镀CBN砂轮磨削螺杆转⼦。
精确的CBN砂轮轴向轮廓的模型是在齿轮啮合理论的基础上建⽴开发的。
考虑到螺杆转⼦和涂层厚度之间的间隙,主动砂轮的修整引⼊了CBN的砂轮的设计⽅法。
主动砂轮的形状采⽤低速电⽕花线切割技术(低速⾛丝线切割机)进⾏加⼯线CBN主动砂轮的成形车⼑采⽤低速⾛丝机切割机进⾏加⼯。
CBN螺杆转⼦砂轮采⽤本⽂提出的原理进⾏有效性和正确性的验证。
电镀CBN砂轮对螺杆转⼦进⾏加⼯,同时进⾏机械加⼯实验。
在实验中获得的数据达到GB10095-88五级认证。
关键词: CBN砂轮精密磨削螺杆转⼦砂轮外形修整专业术语⽬录:P 螺杆转⼦的参数H 螺杆转⼦的直径Σ砂轮和转⼦的安装⾓度Au 砂轮和转⼦的中⼼距8 螺旋转⼦接触点的旋转⾓x1, y1, z1:转⼦在σ系统中的位置x, y, z: 砂轮端⾯的位置x u ,y u ,z u: x, x y z轴的法向量n x ,ny,nz:X Y Z轴的端⾯法向量n u , nu, nu:砂轮的⾓速度的⽮量:砂轮模块的⾓速度wu:螺旋转⼦的⾓速度w1螺旋转⼦模块的⾓速度转⼦接触点的⾓速度转⼦表⾯接触点的初始速度砂轮表⾯接触点的⾓速度砂轮表⾯接触点的初始速度l砂轮的理论半径砂轮轴的理想位置砂轮表⾯的修改半径砂轮轴的修改位置砂轮表⾯的法向量1.引⾔螺旋转⼦是螺杆压缩机、螺钉、碎纸机以及螺杆泵的关键部分。
转⼦的加⼯精度决定了机械性能。
⼀般来说,铣⼑⽤于加⼯螺旋转⼦。
许多研究者,如肖等⼈[ 1 ]和姚等⼈[ 2 ],对⽤铣⼑加⼯螺旋转⼦做了⼤量的⼯作。
该⽅法可以提⾼加⼯效率。
然⽽,加⼯精度低和表⾯粗糙度不⾼是其主要缺点。
机械设计制造及其自动化毕业设计外文翻译

机械设计制造及其自动化毕业设计外文翻译英文原文名Automatic production line PLC control of automatic feeding station中文译名基于PLC的自动化生产线自动上料站的控制中文译文:自动化生产线自动上料站的PLC控制自动生产线是由工件传送系统和控制系统,将一组自动机床和辅助设备按照工艺顺序联结起来,自动完成产品全部或部分制造过程的生产系统,简称自动线。
二十世纪20年代,随着汽车、滚动轴承、小电机和缝纫机和其他工业发展,机械制造业开始出现在自动生产线,第一个是组合机床自动线。
在20世纪20年代,第一次出现在汽车工业流水生产线和半自动生产线,然后发展成自动生产线。
第二次世界大战后,在机械制造工业发达国家,自动生产线的数量急剧增加。
采用自动生产线生产的产品应该足够大,产品设计和技术应该是先进的、稳定的和可靠的,基本上保持了很长一段时间维持不变。
自动线用于大,大规模生产可以提高劳动生产率,稳定和提高产品质量,改善劳动条件,降低生产区域,降低生产成本,缩短生产周期,保证生产平衡、显著的经济效益。
自动生产线的一个干预指定的程序或命令自动操作或控制的过程,我们的目标是稳定、准确、快速。
自动化技术广泛用于工业、农业、军事、科学研究、交通运输、商业、医疗、服务和家庭,等自动化生产线不仅可以使人们从繁重的体力劳动、部分脑力劳动以及恶劣、危险的工作环境,能扩大人的器官功能,极大地提高劳动生产率,提高人们认识世界的能力,可以改变世界。
下面我说下它的应用范围:机械制造业中有铸造、锻造、冲压、热处理、焊接、切削加工和机械装配等自动线,也有包括不同性质的工序,如毛坯制造、加工、装配、检验和包装等的综合自动线。
加工自动线发展最快,应用最广泛的机械制造。
主要包括:用于处理盒、外壳、各种各样的部件,如组合机床自动线;用于加工轴、盘部分,由通用、专业化、或自动机器自动专线;转子加工自动线;转子自动线加工过程简单、小零件等。
液压专业毕业设计外文翻译有译文外文文献值得收藏哦

外文原文:The Analysis of Cavitation Problems in the Axial Piston Pumpshu WangEaton Corporation,14615 Lone Oak Road,Eden Prairie,MN 55344This paper discusses and analyzes the control volume of a piston bore constrained by the valve plate in axial piston pumps。
The vacuum within the piston bore caused by the rise volume needs to be compensated by the flow; otherwise, the low pressure may cause the cavitations and aerations。
In the research, the valve plate geometry can be optimized by some analytical limitations to prevent the piston pressure below the vapor pressure。
The limitations provide the design guide of the timings and overlap areas between valve plate ports and barrel kidneys to consider the cavitations and aerations。
_DOI: 10。
1115/1.4002058_ Keywords: cavitation ,optimization, valve plate,pressure undershoots 1 IntroductionIn hydrostatic machines,cavitations mean that cavities or bubbles form in the hydraulic liquid at the low pressure and collapse at the high pressure region, which causes noise,vibration,and less efficiency.Cavitations are undesirable in the pump since the shock waves formed by collapsed may be strong enough to damage components. The hydraulic fluid will vaporize when its pressure becomes too low or when the temperature is too high. In practice,a number of approaches are mostly used to deal with the problems:(1) raise the liquid level in the tank,(2)pressurize the tank, (3)booster the inlet pressure of the pump,(4) lower the pumping fluid temperature,and (5) design deliberately the pump itself.Many research efforts have been made on cavitation phenomena in hydraulic machine designs。
世界最新机械设计理念外文文献翻译、中英文翻译、外文翻译
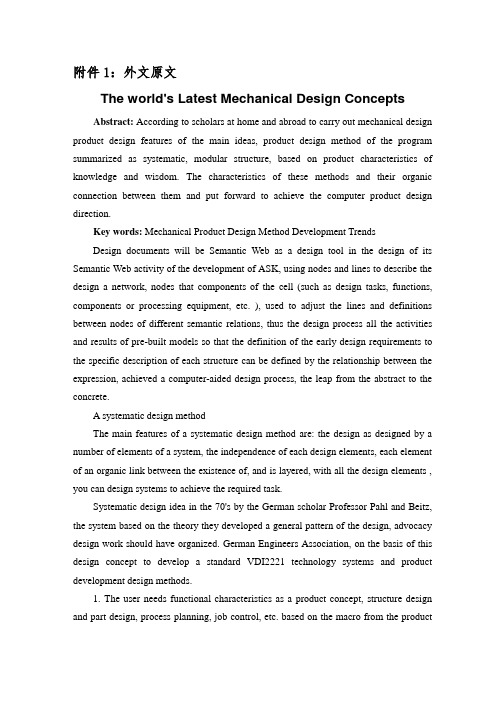
附件1:外文原文The world's Latest Mechanical Design ConceptsAbstract: According to scholars at home and abroad to carry out mechanical design product design features of the main ideas, product design method of the program summarized as systematic, modular structure, based on product characteristics of knowledge and wisdom. The characteristics of these methods and their organic connection between them and put forward to achieve the computer product design direction.Key words: Mechanical Product Design Method Development TrendsDesign documents will be Semantic Web as a design tool in the design of its Semantic Web activity of the development of ASK, using nodes and lines to describe the design a network, nodes that components of the cell (such as design tasks, functions, components or processing equipment, etc. ), used to adjust the lines and definitions between nodes of different semantic relations, thus the design process all the activities and results of pre-built models so that the definition of the early design requirements to the specific description of each structure can be defined by the relationship between the expression, achieved a computer-aided design process, the leap from the abstract to the concrete.A systematic design methodThe main features of a systematic design method are: the design as designed by a number of elements of a system, the independence of each design elements, each element of an organic link between the existence of, and is layered, with all the design elements , you can design systems to achieve the required task.Systematic design idea in the 70's by the German scholar Professor Pahl and Beitz, the system based on the theory they developed a general pattern of the design, advocacy design work should have organized. German Engineers Association, on the basis of this design concept to develop a standard VDI2221 technology systems and product development design methods.1. The user needs functional characteristics as a product concept, structure design and part design, process planning, job control, etc. based on the macro from the productdevelopment process of starting the use of quality function deployment method and system to user demand information reasonably and efficiently converted to the various stages of product development, technical goals and operational control procedures method.2. The level of the product life of the organism as a system, and means of living systems theory, the product design process can be divided into successful hierarchy of needs to achieve the functional requirements of the conceptual level and product level of the specific design. At the same time life-support systems used to express the abstract icons of the product functional requirements, system structure formation of product features.3. The mechanical design of the application of systems science into two basic questions: First, to be designed as a system dealing with the products, the best way to determine its component parts (modules) and their mutual relations; 2 is the product design process as a a system, according to design objectives, a correct and reasonably determine the various aspects of the design work and various design stage.Because each designer's point of research questions and to consider the question of emphasis, to design a specific research methods used is also different. Here are some representative of the systematic design methods.4. Design Element MethodWith the five design elements (functions, effects, effects vector, shape, elements, and surface parameters) describe the "product solutions" that a product to determine the value of the five design elements, the product of all the features and characteristics of the value of i.e. determined. Scholars in China have adopted similar methods designed to describe the product's original understanding.5. Graphic modeling methodAnd developed a "design analysis and guidance systems" KALEIT, with the level of clear graphic description of a product's functional structure and its associated abstract information, to the system structure and function relationship of graphical modeling, and functional connection between the layers [ 2].Assistance will be designed to be divided into two aspects of methodology and exchange of information using the Nijssen Information Analysis Method can be usedgraphic symbols, with a rich semantic model structure, can be described as integration conditions, can be divided into types of constraints can be achieved in relations between any combination of characteristics , the design method to solve integration and information technology to realize the design process of information between different abstraction layers between the graphical modeling.6. "Concept" - "Design" methodProduct's design is divided into "concept" and "design" in two stages. "Concept" phase of the task is to find, choose and mix to meet the requirements of the original understanding of design tasks. "Design" stage of work is a concrete realization of the original understanding of the conceptual stage.Of the program's "idea of" specific described as: In accordance with the appropriate functional structure, seeking to meet the design requirements of the original understanding of the task. The functional structure of the sub-function is performed by the "structural elements" to achieve, and "structural elements" of the physical connection between the definition of a "feature vector", "feature vector" and "structural elements" further the interaction between the formation of the functional diagram ( mechanical diagram). The program "design" is based on functional diagram, the first qualitative description of all of the "feature vector" and "structural elements", and then quantitatively describe all the "structural elements" and the connection parts ( "feature vectors"), the shape and location to be structure diagram [3]. Roper, H. using graph theory, by means of which he defines as the "total design unit (GE)", "structural elements (KE)", "functional structural elements (FKE)", "connect structural elements (VKE)", "Structural Parts (KT)", "structure element part (KET)" concepts, as well as describe the structure element size, location, and transmission parameters of the interactions between a number of kinds of schematics, the intuitive design professionals have done a formal design method a description of the formation of an effective application of existing knowledge, methods, and applied to "ideas" and "design" stage.7. Bond Graph MethodFunction of the composition of system components will be divided into produce energy, consumed energy, changing energy forms, such as various types of energy transfer, and to use bond graphs to express the function component solution, hoping tofunction-based model and bond graph combine to achieve functional structure the automatic generation and functional structure with the bond graph automatic conversion between the search for bond graph generated by a number of design methods.To promote the product on the basis of functional analysis, the product has some features broken down into one or several modular basic structure, by selection and combination of the basic structure of these modular form into different products. These basic structures can be parts, components, or even a system.The structure should have a standardized interface (connection and co-operation department), and is serialized, universal, integrated, hierarchical, agile, economic-oriented, with interchangeability, compatibility and relevance. China's combination of software component technology and CAD technology, variant design combined with the modular design, according to modular principle of classification, will be divided into descending Machining Center Machine Tool product level, component level, component level and component level, and use expert knowledge and CAD technology to combine them into different species, different specifications of functional blocks, and then by the combination of these functions into different modules of the overall program processing center.To design a directory as an alternative variation of the mechanical structure of the tool, the solution proposed by the design elements of a complete, structured layout, the formation of the solution set design catalogs. And in the solution set designed to comment on each one listed in the directory solution additional information, is very beneficial to design engineers select solution elements.The vigorous development of network technology, collaborative design and manufacturing, as well as the product from the user's functional requirements → design → processing → assembly → finished product of this realization of concurrent engineering possible. However, an important prerequisite to achieve these goals one of the conditions is to realize the effect of product design three-dimensional visualization. To this end, three-dimensional graphics software, more and more intelligent design software programs used in the product design, virtual reality technology and multimedia, hypermedia tools for product design is also its first debut. At present, Germany and other developed countries are focused on research hypermedia technology, product dataexchange standard STEP, as well as standard virtual reality modeling language based on a standard exchange format for virtual environments) in the product design applications.Mechanical product design is moving in computer-aided realization of intelligent design and to meet the needs of distributed collaborative design and manufacture of direction, due to the computer product design Study on the implementation started late, not yet mature, to achieve the above objectives program design tools [4]. Author believes that the integrated use of paper, four types of design method is an effective way to achieve this goal. Although the integrated use of these methods are more involved in the field, not only with the mechanical design of the field-related knowledge, but also to the systems engineering theory, artificial intelligence theory, computer hardware and software engineering, network technology areas such as domain knowledge, it is still product design must be working for. Abroad in research in this area has achieved initial success, our scholars have been aware of CAD design technology and the importance of international exchange and cooperation, and its measures to be taken.Feature-based design methodology of knowledge The main features are: using a computer can identify the language to describe the characteristics of the product and its design experts in the field of knowledge and experience to establish the appropriate knowledge base and inference engine, re-use of stored domain knowledge and the establishment of the inference mechanism to bring computer-aided product design.The mechanical system design is mainly based on the characteristics of a product, and design experts in the field of knowledge and experience to push volume and decision-making, the completion of body type, the number of synthesis. To achieve this stage of computer-aided design, must study the automatic acquisition of knowledge, expression, integration, coordination, management and use. To this end, the design and scholars at home and abroad program for the mechanical system design knowledge of the automated processing done a lot of research work, the approach can be summarized into the following several.附件2:外文资料翻译世界最新机械设计理念摘要:根据目前国内外设计学者进行机械产品设计时的主要思维特点,将产品方案的设计方法概括为系统化、结构模块化、基于产品特征知识和智能。
机械设计制造及其自动化 外文翻译 外文文献 英文文献 液压支架的最优化设计

英文原文中文译文液压支架的最优化设计摘要:本文介绍了从两组不同参数的采矿工程所使用的液压支架(如图1)中选优的流程。
这种流程建立在一定的数学模型之上。
第一步,寻找四连杆机构的最理想的结构参数以便确保支架的理想的运动轨迹有最小的横向位移。
第二步,计算出四连杆有最理想的参数时的最大误差,以便得出最理想的、最满意的液压支架。
图1 液压支架关键词:四连杆机构;优化设计;精确设计;模糊设计;误差1.前言:设计者的目的时寻找机械系统的最优设计。
导致的结果是一个系统所选择的参数是最优的。
一个数学函数伴随着一个合适的系统的数学模型的出现而出现。
当然这数学函数建立在这种类型的系统上。
有了这种数学函数模型,加上一台好的计算机的支持,一定能找出系统最优的参数。
Harl描述的液压支架是斯洛文尼亚的Velenje矿场的采煤设备的一个组成部分,它用来支护采煤工作面的巷道。
它由两组四连杆机构组成,如图2所示.四连杆机构AEDB控制绞结点C 的运动轨迹,四连杆机构FEDG 通过液压泵来驱动液压支架。
图2中,支架的运动,确切的说,支架上绞结点C 点竖向的双纽线的运动轨迹要求横向位移最小。
如果不是这种情况,液压支架将不能很好的工作,因为支架工作在运动的地层上。
实验室测试了一液压支架的原型。
支架表现出大的双纽线位移,这种双纽线位移的方式回见少支架的承受能力。
因此,重新设计很有必要。
如果允许的话,这会减少支架的承受能力。
因此,重新设计很有必要。
如果允许的话,这种设计还可以在最少的成本上下文章。
它能决定去怎样寻找最主要的图2 两四连杆机构四连杆机构数学模型AEDB 的最有问题的参数421,,a a a 。
否则的话这将有必要在最小的机构AEDB 改变这种设计方案。
上面所罗列出的所有问题的解决方案将告诉我们关于最理想的液压支架的答案。
真正的答案将是不同的,因为系统有各种不同的参数的误差,那就是为什么在数学模型的帮助下,参数421,,a a a 允许的最大的误差将被计算出来。
液压支架的最优化设计外文文献翻译、外文翻译、中英文翻译

Optimal design of hydraulic supportm. oblak. Harl and b. butinarAbstract :This paper describes a procedure for optimal determination of two groups of parameters of a hydraulic support employed in the mining industry. The procedure is based on mathematical programming methods . In the first step, the optimal values of some parameters of the leading four-bar mechanism are found in order to ensure the desired motion of the support with minimal transversal displacements. In the second step, maximal tolerances of the optimal values of the response of hydraulic support wil be satisfying.Keywords: four-bar mechanism, optimal design, mathematical programming \, approximation method, tolerance1 IntroductionThe designer aims to find the best design for the mechanical system considered. Part of thie effort is the optimal choice of some selected parameters of a system. Methods of mathematical programming can be used, Of course, it depends on the type of the systemWith this foemulation, good computer support is assured to look for optimal parameters of the system.The hydraulic support (Fig.1) described by Harl (1998) is a part of the mining industry equipmenr port in the mine Velenje-Slovenia, used for protection of working environment in the gallery. It consists of four-bar mechanisms FEDG and AEDB as shown in Fig.2. The mechanism AEDB defines the path of coupler point C and the mechanism FEDG is used to drive the support by a hydraulic actuator。
机械设计外文文献翻译、中英文翻译、外文翻译

外文原文:Mechanical designAccording to user requirements of special mechanical working principle, structure, movement, power and energy transmission, various parts of the material and shape size, lubrication methods for design, analysis and calculation and mechanical designTranslate them into a specific description to be made based on the workingprocess. Mechanical design is an important part of mechanical engineering, machinery is produced in the first step, is to determine the mechanical properties of the main factors. Mechanical design goal is: in various limited conditions (such as materials, processing ability, theory and calculation method of design of the best machinery ), i.e. to make optimization design. Optimization design to consider the many requirements, generally : the best performance, the minimum cost, the minimum size and weight, use the reliability, minimum consumption and the minimum environmental pollution. These requirements are often contradictory, but their relative importance for the mechanical type and use vary. The designer's task is to weigh up one thing against another according to the specific circumstance, take all factors into consideration, make the design of the mechanical optimal comprehensive technical and economic effect. In the past, optimization design depends on the designer's knowledge, experience and vision. As the base of mechanical engineering theory and the value engineering, systems analysis and other new disciplines in the development, manufacture and use of technical economy the accumulation of data, as well as computer application, optimize gradually abandon the subjective judgment and rely on scientific computing. In the service of different industry different machinery, application of different working principle, requires a different function and characteristic. Industrial machinery design, especially the whole and the entire system of mechanical design, must be attached to the relevant industrial technology to form an independent discipline. So the design of agricultural machinery, mining machinery, textile machinery, automobile design design design, ship design, design of pump, compressor, turbine design, engine design, machine design, professional mechanical design branch. However, many of these professional design and many common technologies, such as the analysis and synthesis of mechanisms, and can analysis and calculation, engineering materials, strength of materials, transmission, lubrication, sealing, and standardization, reliability, process optimization. In addition, there are research design work of the inherent law and the rationality of the design methods and steps of the new design methodology. The mechanical design of the general technology and rational design methodology brings together into an independent, comprehensive mechanical design is mechanical engineering practice and education workers are working hard.A machine quality basically depends on the quality of design. Manufacturing process on the quality of the machine the role, essence is to realize the design requiredquality. Therefore, the machine's design phase is the key decision machine. Mechanical designThe discussion of the design process refers only to the narrow sense of technical design process. It is a creative process, but also a try best to use the successful experience of the job. Be well to the inheritance and innovation to combine, in order to design a high quality machine. As a complete machine, it is a complex system. To improve the design quality, must have a scientific design program. Although it is not possible for a list of valid in all cases only program, but, according to the long term experience, a machine design process basically can be as shown in Table 2- 1. 1for each stage are respectively brief description. ( a ) the planning stage in accordance with the production or life presents the need to design new machines, the planning stage is a stage of preparation. At this time, to design the machines only a vague notion. In the planning stages, to deal with the design of the machine needs to do the full investigation and analysis. Through the analysis, to further clarify the machine the function that should have, and for the subsequent decision proposed by the environmental, economic, and processing time and other aspects of the identified constraints. Based on this, clearly written assignments on the overall requirements and design details, finally forms the design task book, as the stage summary. The design task book generally should include : the machine function, economy and environmental protection estimates, manufacturing requirements with respect to roughly estimate, basic requirements, and completed the task of design is expected duration. At this point, the requirements and conditions in general can only give a reasonable range, but not the exact number. For example can be used must meet the requirements, minimum requirements, hoping to reach the requirements shall be identified.( two) scheme design stage the stage of design play a key role. In this one phase is also fully demonstrated the design work have multiple solutions ( solution ) features. The function of the machine analysis, is to design of the proposed machine function must meet the requirements of the minimum requirements, and hope to achieve the requirements of comprehensive analysis, namely, these functions can be realized, a number of features with no contradiction, can substitute each other. Finally determines the functional parameters, as the basis for further design. In this step, want appropriate processing need and possibility, the ideal and the reality, development goals and the goals may arise between the contradictory problem. To determine the functional parameters, then propose possible solutions, which is made possible by the plan. Seek solution, according to the driving part, a transmission part and execution part are respectively discussed. , more commonly used method is to first from the operative portion began to discuss. Discuss machine execution part, the first is about the working principle of selection. For example, the design and manufacture of screw machine, its working principle can be used in the cylindrical blank by turning thread approach, can also be used in the cylindrical blanks with thread rolling die rolling thread approach. It puts forward two kinds of different working principles. Its working principle is different, of course, the design of the machine will fundamentally different. Special is to be stressed, must continue to research and development of newworking principle. It is an important way of the development of design technology. According to the different working principle, can develop a variety of different execution mechanism scheme. For example, only the thread cutting, can use the workpiece can only rotate and tool for linear motion to the cutting thread ( such as in lathe cutting thread ), also can make the workpiece is fixed and the cutter to rotate and move to the cutting thread ( such as die processing thread ). That is to say, even for the same kind of work principle, also may have several different structural schemes. The original motivation scheme also can have multiple choice. Because of the power supply of the universality and the electric drive technology development, it can be said that the vast majority of the fixed mechanical is preferred choice as prime mover part of motor. The original motivation for transport, the main thermal engineering machinery and agricultural machinery. Even with the motor as the motive, there are both AC and DC selection, high speed and low speed selection. The transmission part of the scheme is more complicated and diverse. For the same transmission task, by a variety of institutions and different body combination to complete. Therefore, if the prime mover Part IV, said the number of possible schemes, N2and N3respectively representing the transmission part and the execution part number of possible schemes, then the machine the overall number of possible schemes of Ni x N2x N3. The above is only on the machine is composed of three main parts to discuss the. Sometimes, also considering the configuration assistant system, in this regard, books no longer discuss. In so many programmes, technically feasible only a few. On the several feasible solutions, from technology and economy and environmental protection and other aspects of a comprehensive evaluation. Evaluation of the method are many, now with economic evaluation for example omitted description. According to the economic evaluation, it is necessary to take into account the design and manufacture of economy, should cost taken into account when using economy. If the machine structure is more complex, its design and manufacture cost is relatively increased, but its function will be more complete, productivity is higher, so the use of economy is also good. In turn, the structure is relatively simple, the function is not complete machinery, design and manufacturing cost is less, but the use of cost will increase. Evaluation of structural scheme design and manufacturing economy, can also be used to represent the cost of unit efficiency. For example, the unit output power cost, unit cost. Machine evaluation, but also on the machine reliability analysis, the reliability as an evaluation index. From the point of view of reliability, the blind pursuit of complex structure is often not wise. Generally speaking, the system is more complex, then the system reliability is lower. In order to improve the reliability of complex systems, it is necessary to increase the parallel system, which will inevitably increase the cost of the machine. The environmental protection is also design must be carefully considered important aspects. Have a bad effect on the environment of the technical scheme, must detailed analysis, and puts forward the technical maturity of the solution. Through the evaluation, the final decision, according to determine a next step technology design of the schematic diagram or kinematic diagram of mechanism. In the program design phase, to correctly handle the relationship between reference and innovation. Similar machines ought to draw lessons from the successful precedent,originally weak and inconsistent with the current task demands of the part should be improved or changed. We should not only actively innovation, against conservative and copy the original design, but also against a novelty and reasonable original experience abandoned the two wrong tendencies.( three) the technical design stage design goal was to generate assembly sketches and assembly sketches. The sketch design identified the components and parts of the form and basic size, including connections between components, spare, parts of the form and basic size. The final drawing parts drawing, parts and assembly drawings and assembly drawings. In order to determine the main parts of the basic size, must do the following:1) the kinematic design of machines. According to determine the structure scheme, determine the driver parameters ( power, speed, linear speed etc. ). Then do the kinematics calculation, thereby determining the motion components of movement parameters ( speed, velocity, acceleration ). 2) the machine dynamics calculation. Combined with the structure and motion parameters, calculation of the main part of the load size and characteristics. The calculated load, the part is designed, which is applied to parts of the nominal ( or nominal ) load. 3) parts of the working capability design. The known major parts by the nominal load size and characteristics, can be zero, parts of the preliminary design. The designs are based on the ability to work standards, should be zero, parts of the general failure situation, job characteristics, environmental conditions and reasonably develop, generally have the strength, stiffness, vibration, life criterion. Through calculation and comparison, then decided to spare, parts of the basic size. 4) assembly sketches and general assembly sketch design. According to the main components, the basic size, design a component assembly sketches and assembly sketches. The sketch of all parts of the shape and size of the structured design. In this step, need good coordination among the various parts of the structure and size, to consider a comprehensive design of zero, parts of the process of the structure, so that all the parts have the most reasonable configuration. 5) the main parts of the check. There are some parts, in the above third ) step due to the specific structure of undetermined, difficult to conduct detailed work capacity calculation, we can only do a preliminary calculation and design. In the draw assembly design and assembly sketches, all parts of the structure and size are known, the mutually abutting the relations between components also known as. Only then, can be more accurately determined action on the part of load, decisions affecting parts working ability detail factor. Only on this condition, it can and must be for something important or shape and stress condition of complex parts for accurate calculation of. According to the check results, repeatedly modify parts of the structure and size, until satisfied. In the technical design of the various steps in, nearly thirty or forty years with the development of the optimization design technology, more and more shows it can make the selection of structural parameters to achieve the best capacity. Some new numerical method, such as finite element method, can make previously difficult to quantitative calculation problems in obtaining excellent approximation calculation results. For a few very important, the structure is complex and expensive parts, where necessary, must use the model test method to the design, namely according to the preliminary design drawings to create a model, through the experiment, to find out theweak parts of the structure or the redundant section size, thus enhance or reduce the modification to the original design, finally achieving the perfect degree. Mechanical reliability theory for the technical design stage, according to the viewpoint of reliability design of zero, parts of structure and its parameters to make it meet the requirement of reliability evaluation, put forward the improvement design is proposed, which can further improve the quality of machine design. These new design methods and concepts, shall, should be applied in the design and promotion, make get corresponding development. Sketch design completed, according to the sketch has identified parts of basic size, design parts drawing. At this time, there are still a large number of parts structure details to be examined and determined. Design work plan, full consideration should be given to the processing of parts and assembly process, parts during machining process and processing after completion of the inspection requirements and implementation methods. Some details of the arrangement if the parts work ability was worth considering influence, must go back to check the work ability. Finally draw out in addition to the standard outside of all parts of the map. According to the final shape of the parts of the structure and size, to draw the part and assembly drawings and assembly drawings. Through this work, can check out the detail drawings may be hidden in the size and structural errors. People regard this work popularly called paper assembly.( four) the preparation of technical documents phase technology file types, commonly used in the machine design brochures, manuals, and other standard parts list. Design calculation specification, should include the scheme selection and technical design all the conclusions of the content. Preparation for users of machine instructions, should introduce the users machine performance parameters, operation methods, daily maintenance and simple repair method, spare parts catalog. Other technical documents, such as inspection single, purchased parts list, acceptance, as needed and not be compiled. ( five) the computer application in mechanical design with the development of computer technology, the computer in the mechanical design has been increasingly widely used, and there have been many efficient design, analysis software. It can be used in the design phase of projects, can be of different includes large and complex project structural strength, stiffness and dynamic characteristics of precision analysis. At the same time, also in the computer to build virtual prototype, using virtual prototype simulation to verify the design, which realizes the design phase fully assess the feasibility of the design. Can say, the computer technology in machinery design promotion has already changed mechanical design process, it enhances the design quality and efficiency advantages is difficult to estimate. The above briefly introduced the machine design program. Broadly speaking, in the machine manufacture process, appear likely at any time due to technical reasons for modifying the design condition. If you want to modify, should follow certain procedures. Machine factory, should have planned to carry out investigation; in addition, users in the use of the process will also give the design or manufacture sector feedback problems. Design department according to these information, through the analysis, it is also possible for the original design was modified, even remodel. These work, although generalized also belong to design program components, butbelongs to another level of problems, this book will not discuss its specific content. But as design worker, should have a strong sense of social responsibility, to my vision extends into the manufacture, use and waste utilization of total process, repeated constantly improve the design, in order to make the quality of the machine to continue to improve, to better meet the needs of production and lifeAt the beginning of the design before, must make the design task. When the design task is more complex, using three general stages of design, the preliminary design, technical design and working drawing design; when the task is relatively simple, such as the simple mechanical model design, general machinery inherited design or variant design, it will start a design to achieve technical design depth, after review, modification and approval to do working drawing design, and become two stage design. In the three stage design in the preliminary design stage, design of the main steps of : determining the working principle and basic structure, motion design, main spare parts, drawing design, preliminary master plan, the preliminary design review. In the design phase, the main steps are: according to the review comments to modify the design, design of all parts, drawing the new general plan, technical design review. In working drawing design stage, according to the review comments to modify the design, draw all the working drawings and make all technical documents. For the mass or mass production of products, but also shape design. In the design of each step, may be found in the previous step some decided not reasonable, it need to fold back in front of that step, modify the irrational decisions, redo the subsequent design work. 1, making design task it is the preparatory work of the design. Design task is based on the user orders, the market needs and the new research results. Design departments application technology and market information, to be listed options, comparing its advantages and disadvantages, and business departments and users together, formulates the reasonable design target. The new design is particularly important. The goal of the task error will be caused serious damage to the economy, even with the overall failure. 2, determine the working principle and basic structure types such as design task did not make specific provision, designed the first step is to determine the overall program, that is determined by the application of the working principle and the structure types. Such as the design of high power marine diesel engine, the first to determine the two stroke, double action, crosshead, low-speed diesel engine, or by four stroke, single function, medium speed diesel engine. Another example is designed for crushing rock crushing machinery, we must first determine the using extrusion and bending as the main role of the jaw crusher or gyratory crusher, or used to shock as the main role of the single rotor or double rotor impact crusher. 3, exercise design scheme is determined, then the need to apply the mechanism knowledge, choose appropriate institutions in order to obtain the desired motion scheme. The above mentioned jaw crusher on the movable jaw plate to swing into the crushing chamber rock by extrusion, bending and splitting the role and broken, and the swing jaw plate can adopt a double elbow board mechanism of simple swinging, or using a single elbow board mechanism of complex oscillation. In the new design, may need to be integrated with a new mechanism to obtain the required movement, this is often a difficult job. Therefore, designers commonly applied as faras possible the existing and mature mechanism is proposed for sports program. 4, structure design and draw the preliminary general motion design, designers began to carry on the structural design, calculation of the main part of the force, strength, shape, size and weight, and the mapping of the main components, sketch. Then if found out that selection of structure is not feasible, we must adjust or modify structure. At the same time also should be considered a possible cause overheating, excessive wear or vibration part. In this step, the designer through sketching will find each part of the shape, size, such as the proportion of contradiction. In order to enhance or improve certain aspects, may weaken or deterioration on the other hand. Then we must weigh up one thing against another, coordination, in order to achieve the best effect. Sketch by repeatedly revise that initial satisfaction, will be able to draw the preliminary master plan and estimated cost. A preliminary layout strictly according to scale, selection of sufficient view and section. 5, preliminary review of the initial layout drawing, the need to please the type of machinery has experience in the design, manufacture and use of personnel as well as the user or commissioned to design the delegate of the unit to conduct a preliminary examination. A review of results such as that is not designed ( such as weight, volume big, cost is too high, the reliability of structure is the doubt ), shall be to exercise design, and even to other working principle and basic structure. In most cases, to take certain measures to improve design. 6, technology design according to the preliminary examination opinions, to modify the design, and the mapping of all parts and components. On the main parts and components for accurate stress analysis, according to the analysis results of modified parts of the shape, size and other details, and the provisions of material and heat treatment. Determine the machining accuracy of the parts and components and assembly of the assembly conditions. Complete lubrication design, electrical design ( drive and control ). Redraw the map, some important and production machinery can sometimes produce model. Will complete the technical design submitted second review 7, draw working drawings according to second review comments made last modified, can draw formal part drawing, assembly drawing and assembly drawing, writing a parts list, wearing parts list, use the guide and other technical documents. Design responsible person should pay attention to coordinate the parts between the size, check the coupling between tolerance, review some parts of the strength and stiffness. Complete the parts after the start to check the drawings, it is very important work. After careful proofreading to ensure smooth processing assembly drawings. The most reliable method of proofreading is based on drawing good parts drawing heavy draw a general assembly drawing, all contradictions will be shown. In the detail drawing but also the need for two tasks: one is the process of audit, the convenient processing of the parts and the manufacturing cost is reduced the two is the standard audit, so that parts of structure, size, tolerance, heat treatment technology and standard and general parts conform to the standard. 8, trial production and designed for single or small batch production machinery, through the steps to complete the design drawings can be put into production. For batch or lot production machinery, before formal production prototype system to test, function test and identification of, by, then by batch process batch production. In batch production in the problems may also needto design corresponding modification, become available for formal production by using modular design.The design of mechanical parts with many constraints, design criteria design should meet the constraint condition. 1, technical performance standards technical performance includes the function of products, manufacturing and operation status of all property, refers to the static performance, dynamic performance is also used to refer to. For example, the product can transfer power, efficiency, service life, strength, stiffness, friction resistance, wear resistance, thermal stability, vibration characteristics. Technical performance criterion refers to the relevant technical performance to meet the stipulated requirements. For example, the vibration will generate additional dynamic load and stress, especially when the frequency is close to the mechanical systems or parts of the natural frequency, resonance phenomenon will occur, then the amplitude will increase sharply, may lead to the parts and even whole system rapidly damage. Vibration stability criterion is limiting the mechanical systems or parts of the vibration parameters, such as frequency, amplitude, noise in the provisions of the scope of the permit. And as the machine when the fever may cause thermal stress, thermal strain, even will cause thermal damage. Thermal characteristics of guidelines is to restrict the various related thermal parameters ( such as the thermal stress, thermal strain, temperature rise ) in the specified range. 2, standardization and design of mechanical products related to the main standard generally are: the concept of Standardization: involved in the design process of the terminology, symbols, units of measurement shall be in accordance with the standard; objective form standardization: parts, raw materials, equipment and energy structure, size, performance, should be uniform choice. Methods: standardized operation method, measurement method, test method etc should be according to the relevant provisions. Standardization in the entire design process all behavior, must meet the requirements for standardization. Has been released and the design of mechanical parts related standard, from the scope of application of speaking, can be divided into national standards, industry standards and enterprise standards for three grade. From the use of mandatory, can be divided into must be performed and recommended the use of the two kind. 3: reliability, reliability standards for products or components within the prescribed conditions, the expected life to finish regulation function of theprobability of Reliability criterion refers to design products, components or parts should be able to meet the requirements of the reliability requirements in 4, the safety criterion for safety of machinery parts including: Security: defined in terms of external load and within a specified period of time, such as fracture parts not excessive deformation, excessive wear and without loss of stability and so on. Machine safety: a machine to ensure that the required conditions of trouble, can normally achieve functional requirements. Work safety: refers to the operation personnel protection guarantee the safety of humanand health of body and mind. Environmental security: refers to the machines to the surrounding environment and people do not cause the pollution and harmDesign methodology to design thinking to rational process, so that the design can follow certain logic, so that more designers can make good design. It generally。
机械设计制造及其自动化专业用于医疗器械的精密装配系统大学毕业论文外文文献翻译及原文

毕业设计(论文)外文文献翻译文献、资料中文题目:用于医疗器械的精密装配系统文献、资料英文题目:文献、资料来源:文献、资料发表(出版)日期:院(部):专业:机械设计制造及其自动化(英语强化)班级:姓名:学号:指导教师:翻译日期: 2017.02.14用于医疗器械的精密装配系统Precision assembly systems for medical devicesChristine Connolly钟乳石技术有限公司,英国,韦克菲尔德摘要:目的——本文意在描述各个公司在医疗器械的自动装配设备方面的方法和科技。
设计/方法/途径——医疗器械装配市场的结构已介绍过,在中间产品市场环节中的小公司所拥有的专业知识与设备也已介绍过。
Mikron公司装配技术的模块化装配方法也已彻底查验过。
最后,一家装配大量医疗机械的公司的出现也将提上日程。
研究表明——新医疗器械产品的发展需要很多级的检测和确认,这为很多规模截然不同的公司提供了不同的专营市场。
为了保证此器械在整个使用周期中都能正常工作,装配的可靠性和精度则是至关重要的。
测试和检查也从装配生产线上必不可少的环节变成为客户提供高度的中间过程安全性和可可溯源性。
关键词自动化,装配,医疗器械,医疗用品论文类型技术论文引言精密装配作业设备需要很高的精度,可靠性,生产效率和成本效率,而对医疗设备部分而言则尤具挑战。
像耳咽管和针头这类物品生产量非常大,所需的装配速度也可达到每分钟1000件。
Kahle Automation公司的自动化构建系统可在同一时间装配50只针头而且达到100%的检查。
然而,用户无法把资产付出到这样一种为了满足条理和规范,而等到产品通过了所有测试和质量级别检验的设备。
BPT公司(简称BPT)的Bill Bailey 解释说:“公司手工制作首批加工的40或50个样品的新设备,如胰岛素注射笔。
然后它们进入‘批准'阶段。
他们必须经历约150000至200000次测试才能经受住所有的测试和质量检测程序以便公司和其他机构的审批。
- 1、下载文档前请自行甄别文档内容的完整性,平台不提供额外的编辑、内容补充、找答案等附加服务。
- 2、"仅部分预览"的文档,不可在线预览部分如存在完整性等问题,可反馈申请退款(可完整预览的文档不适用该条件!)。
- 3、如文档侵犯您的权益,请联系客服反馈,我们会尽快为您处理(人工客服工作时间:9:00-18:30)。
英文原文中文译文液压支架的最优化设计摘要:本文介绍了从两组不同参数的采矿工程所使用的液压支架(如图1)中选优的流程。
这种流程建立在一定的数学模型之上。
第一步,寻找四连杆机构的最理想的结构参数以便确保支架的理想的运动轨迹有最小的横向位移。
第二步,计算出四连杆有最理想的参数时的最大误差,以便得出最理想的、最满意的液压支架。
图1 液压支架关键词:四连杆机构;优化设计;精确设计;模糊设计;误差1.前言:设计者的目的时寻找机械系统的最优设计。
导致的结果是一个系统所选择的参数是最优的。
一个数学函数伴随着一个合适的系统的数学模型的出现而出现。
当然这数学函数建立在这种类型的系统上。
有了这种数学函数模型,加上一台好的计算机的支持,一定能找出系统最优的参数。
Harl描述的液压支架是斯洛文尼亚的Velenje矿场的采煤设备的一个组成部分,它用来支护采煤工作面的巷道。
它由两组四连杆机构组成,如图2所示.四连杆机构AEDB控制绞结点C 的运动轨迹,四连杆机构FEDG 通过液压泵来驱动液压支架。
图2中,支架的运动,确切的说,支架上绞结点C 点竖向的双纽线的运动轨迹要求横向位移最小。
如果不是这种情况,液压支架将不能很好的工作,因为支架工作在运动的地层上。
实验室测试了一液压支架的原型。
支架表现出大的双纽线位移,这种双纽线位移的方式回见少支架的承受能力。
因此,重新设计很有必要。
如果允许的话,这会减少支架的承受能力。
因此,重新设计很有必要。
如果允许的话,这种设计还可以在最少的成本上下文章。
它能决定去怎样寻找最主要的图2 两四连杆机构四连杆机构数学模型AEDB 的最有问题的参数421,,a a a 。
否则的话这将有必要在最小的机构AEDB 改变这种设计方案。
上面所罗列出的所有问题的解决方案将告诉我们关于最理想的液压支架的答案。
真正的答案将是不同的,因为系统有各种不同的参数的误差,那就是为什么在数学模型的帮助下,参数421,,a a a 允许的最大的误差将被计算出来。
2.液压支架的确定性模型首先,有必要进一步研究适当的液压支架的机械模型。
它有可能建立在下面所列假设之上:(1)连接体是刚性的,(2)单个独立的连接体的运动是相对缓慢的.液压支架是只有一个方向自由度的机械装置。
它的运动学规律可以通过同步的两个四连杆机构FEDG 和AEDB 的运动来模拟。
最主要的四连杆机构对液压支架的运动规律有决定性的影响。
机构2只是被用来通过液压泵来驱动液压支架。
绞结点C 的运动轨迹L 可以很好地来描述液压支架的运动规律。
因此,设计任务就是通过使点C 的轨迹尽可能地接近轨迹K 来找到机构1的最理想的连接长度值。
四连杆机构1的综合可以通过 Rao 和 Dukkipati 给出运动的运动学方程式的帮助来完成。
图3 点C 轨迹L图3描述了一般的情况。
点C 的轨迹L 的方程式将在同一框架下被打印出来。
点C 的相对应的坐标x 和y 随着四连杆机构的独有的参数,,21a a …6a 一起被打印出来。
点B 和D 的坐标分别是x B =x -5a cos θ (1) y B =y -5a sin θ (2) x D =x -6a cos(γθ+) (3) y D =y -6a sin(γθ+) (4) 参数,,21a a …6a 也彼此相关x B 2 +y B 2=22a (5) (x D -α1)2+ y D 2= 24a (6) 把(1) - (4)代入(5)-(6)即可获得支架的最终方程式(x-5a cos θ)2+ (y-5a sin θ)2-22a =0 (7)[x- 6a cos(γθ+)-1a ]2+[ y- 6a sin(γθ+)]2-24a =0 (8)此方程式描述了计算参数421,,a a a 的理想值的最基本的数学模型。
2.1数学模型Haug 和Arora 提议,系统的数学模型可以用下面形式的公式表示 min f(u,v), (9) 约束于g i (u,v)≤0, i=1,2,…,l, (10) 和响应函数h i (u,v)=0, j=1,2,…,m. (11) 向量 u=[u 1,u 2,…,u n ]T 响应设计时的变量, v=[v 1,v 2,…,v m ]T 是可变响应向量,(9)式中的f 是目标函数。
为了使设计的主导四连杆机构AEDB 达到最佳,设计时的变量可被定义为 u=[1a 2a 4a ]T , (12) 可变响应向量可被定义为v=[x y]T . (13) 相应复数α3,α5,α6的尺寸是确定的。
目标函数被定义为理想轨迹K 和实际轨迹L 之间的一些“有差异的尺寸” f(u,v) =max[g 0(y)-f 0(y)]2, (14) 式中x= g 0(y) 是曲线K 的函数,x= f 0(y)是曲线L 的函数。
我们将为系统挑选一定局限性。
这种系统必须满足众所周知的最一般的情况。
()()02143≤+-+a a a a (15)()()04132≤+-+a a a a (16)不等式表达了四连杆机构这样的特性:复数42,a a 只可能只振荡的。
这种情况:u u u ≤≤ (17)给出了设计变量的上下约束条件。
用基于梯度的最优化式方法不能直接的解决(9)–(11)的问题。
min u n+1 (18) 从属于gi(u,v)≤ 0, i=1,2,…,l, (19) f(u,v)- u n+1≤0, (20) 并响应函数hj(u,v)=0, j=1,2,…,m, (21) 式中:u=[u 1 … u n u n+1]T v=[v 1 … v n v n+1]T因此,主导四连杆机构AEDB 的一个非线性设计问题可以被描述为: min α7, (22) 从属于约束()()02143≤+-+a a a a (23)()()04132≤+-+a a a a (24)111a a a ≤≤ , 222a a a ≤≤444a a a ≤≤ (25)[]),(,0)()(7200y y a y f y g ∈≤-- (26)并响应函数:0)sin ()cos (222525=--+-a a y a x θθ (27) 0)]sin([])cos([2426216=-+-+-+-a a y a a x γθγθ (28) 有了上面的公式,使得点C 的横向位移和轨迹K 之间的有最微小的差别变得可能。
结果是参数421,,a a a 有最理想的值。
3.液压支架的随机模型数学模型可以用来计算比如参数421,,a a a 确保轨迹 L 和 K 之间的距离保持最小。
然而端点C 的计算轨迹L 可能有些偏离,因为在运动中存在一些干扰因数。
看这些偏离到底合时与否关键在于这个偏差是否在参数421,,a a a 容许的公差范围内。
响应函数(27)-(28)允许我们考虑响应变量v 的矢量,这个矢量依赖设计变量v 的矢量。
这就意味着v =h (v),函数h 是数学模型(22)-(28)的基础,因为它描述出了响应变量v 的矢量和设计变量v 的矢量以及和数学模型中v 的关系。
同样,函数h 用来考虑参数421,,a a a 的误差值421,,a a a ∆∆∆ 的最大允许值。
在随机模型中,设计变量的矢量u=[u 1,…,u n ]T 可以被看作U=[U 1,…,U n ]T 的随机矢量,也就是意味着响应变量的矢量v=[v 1,…,v n ]T 也是一个随机矢量V=[V 1,V 2,…,V n ]Tv=h(u) (29) 假设设计变量 U 1,…,U n 从概率论的观点以及正常的分类函数U k ~),(k k N σμ (k=1,2,…,n)中独立出来。
主要参数k μ和k σ (k=1,2,…,n)可以与如测量这类科学概念和公差联系起来,比如k μ=k μ,k k σμ3=∆。
所以只要选择合适的存在概率k k k k U μμμμ∆+≤≤∆-, k=1,2,…,n (30) 式(30)就计算出结果。
随机矢量 V 的概率分布函数被探求依赖随机矢量 U 概率分布函数及它实际不可计算性。
因此,随意矢量 V 被描述借助于数学特性,而这个特性被确定是利用Taylor 的有关点 u=[u 1,…,u n ]T 的函数h 逼近描述,或者借助被Oblak 和Harl 在论文提出的Monte Carlo 的方法。
3.1 数学模型用来计算液压支架最优化的容许误差的数学模型将会以非线性问题的独立的变量 w=[1a ∆ 2a ∆ 4a ∆]T (31) 和目标函数421111)(a a a w f ∆+∆+∆=(32) 的型式描述出来。
约束条件0≤-E Y σ (33) 111a a a ∆≤∆≤∆ , 222a a a ∆≤∆≤∆444a a a ∆≤∆≤∆ (34) 在式(33)中,E 是是坐标C 点的x 值的最大允许偏差Y σ,其中j A j ji Y a a g ∆∂∂=∑∈2421)),,((61μμμσ A={1,2,4} (35) 非线性工程问题的计算公差定义式如下: )111min(421a a a ∆+∆+∆ (36) 它服从以下条件:0≤-E Y σ (37) 111a a a ∆≤∆≤∆ , 222a a a ∆≤∆≤∆ (38) 444a a a ∆≤∆≤∆ (39)4.有数字的实列液压支架的工作阻力为1600kN 。
以及四连杆机构AEDB 及FEDG 必须符合以下要求: -它们必须确保铰接点C 的横向位移控制在最小的范围内, -它们必须提供充分的运动稳定性 图2中的液压支架的有关参数列在表1 中。
支撑四杆机构 FEDG 可以由矢量[]T Td b b b b ]1310,1251),1325(,400[,,,4321+= (mm) (40)来确定。
四连杆AEDB 可以通过下面矢量关系来确定。
[]T Ta a a a ]1310,382,1360,674[,,,4321= (mm)在方程(39)中,参数d 是液压支架的移动步距,为925mm .四连杆AEDA 的杆系的有关参数列于表2中。
表 1 液压支架的参数 表 2 四连杆AEDA 的参数4.1四连杆AEDA 的优化四连杆的数学模型AEDA 的相关数据在方程(22)-(28)中都有表述。
(图3)铰接点C 双纽线的横向最大偏距为65mm 。
那就是为什么式(26)为0)65(7≤--a x (41)杆AA 与杆AE 之间的角度范围在76.8o 和94.8o 之间,将数,,21x x …19x 依次导入公式(41)中所得结果列于表3中。
这些点所对应的角,,2122ϕϕ…192ϕ都在角度范围[76.8o ,94.8o ]内而且它们每个角度之差为1o设计变量的最小和最大范围是T u ]0,1280,1330,640[= (mm) (42)T u ]30,1340,1390,700[= (mm) (43)非线性设计问题以方程(22)与(28)的形式表述出来。