煤炭液化技术课程论文
煤炭液化论文

煤液化多联产技术概述(辽宁科技大学化学工程学院煤化09-*)摘要:煤炭液化技术是把固体煤炭通过化学加工过程,使其转化成为液体燃料、化工原料和产品的先进洁净煤技术。
根据不同的加工路线,煤炭液化可分为直接液化和间接液化两大类:直接液化和间接液化。
直接液化是在高温(400℃以上)、高压(10MPa以上),在催化剂和溶剂作用下使煤的分子进行裂解加氢,直接转化成液体燃料,再进一步加工精制成汽油、柴油等燃料油,又称加氢液化。
间接液化技术是先将煤全部气化成合成气,然后以煤基合成气(一氧化碳和氢气)为原料,在一定温度和压力下,将其催化合成为烃类燃料油及化工原料和产品的工艺,包括煤炭气化制取合成气、气体净化与交换、催化合成烃类产品以及产品分离和改制加工等过程。
关键词:煤直接液化、煤间接液化、多联产、生产模式Guo WeiLiaoning University of Science and Technology, School of ChemicalEngineering coalification 09-4General introduction of co- production system for coal liquefaction Abstract:Give a simple introduction todirect coal liquefaction andindirect coal liquefaction, and multi-combinative production, and theapplication of the technology of multi-combinative production in coal liquefaction and its types of produce,and its development in China.Key word: direct coal liquefaction; indirect coal liquefaction; multi-combinative production; types of produce.据有关资料统计,2010年,中国消耗煤炭总量33亿t,消耗石油4.2亿t,其中本国生产石油1.81亿t,从国外进口2.39亿t,即54%的石油依赖进口,进口量已超过国内总需求的一半,预计到2020年,石油的对外依存度有可能接近70%,如此大规模的石油进口,增加了我国对国外资源的依赖程度,国际市场的波动和变化将直接影响到国内经济乃至政治的安全与稳定。
煤液化技术研究

煤液化技术研究一、煤炭液化在我国有很大的发展空间(一)我国的煤炭资源丰富从世界范围看,煤炭是一种储量丰富的化石能源,在一次能源中占31%。
众所周知,我国是一个富煤、少油、有气的国家。
据报道,我国煤炭的预测资源量达到5万亿t,探明资源储量约1万亿t,可采储量2000多亿t。
煤炭在中国一次能源结构中所占比例曾高达90%,目前为66%左右。
相比之下,我国油气资源贫乏,每平方公里国土面积的资源量、累计探明可采储量、剩余可采储量,都明显低于世界平均水平,石油剩余可采储量仅占世界剩余可采储量的1.8%。
(二)我国能源消耗量日趋增大随着我国国民经济的高速发展,能源消费将持续增长。
目前,我国已是世界第二大石油消耗国。
这就使我国在能源结构上对国外有很强的依赖性,据报道,我国的石油进口量已超过消费总量的40%。
而且对国外进口能源的依存度有逐年上升的趋势,这很不利于我国的进一步发展。
20世纪70年代后发生过两次石油危机,使各国普遍开始重新认识未来能源中煤炭的战略地位,制定了相应法规和政策,并明显加大了煤炭作为原料和燃料利用技术的开发力度。
这在我国更是有着特殊的意义和价值。
(三)传统煤炭能源的使用有很多弊端虽然我国的煤炭资源丰富。
但也有着一些不利因素的存在。
首先,就是环境污染问题。
烟煤型污染已经给生态环境带来严重问题。
大部分煤直接燃烧生成CO2、SO2、NO2、烟雾等,在许多地区形成“酸雨”和“温室效应”,严重污染环境,造成的经济损失每年达100亿元以上,使我国成为世界上因大气污染排放造成损失最大的国家之一。
其次,传统的工艺对煤炭能源的利用率不高,造成资源的严重浪费。
另外,我国能源分布不均,重心偏西偏北。
而经济发达区域偏南偏东。
常规能源需要长途运输才能满足需求。
煤炭的运输从某种意义上说没有液体燃料方便。
二、煤炭的液化技术(一)煤炭直接液化技术。
该技术是把煤先磨成粉,再和自身产生的液化重油(循环溶剂)配成煤浆,在高温(430℃~465℃)和高压f17MPa~30NPa)下直接加氢,将煤转化成汽油、柴油等石油产品。
探析当今煤直接液化技术及标准论文
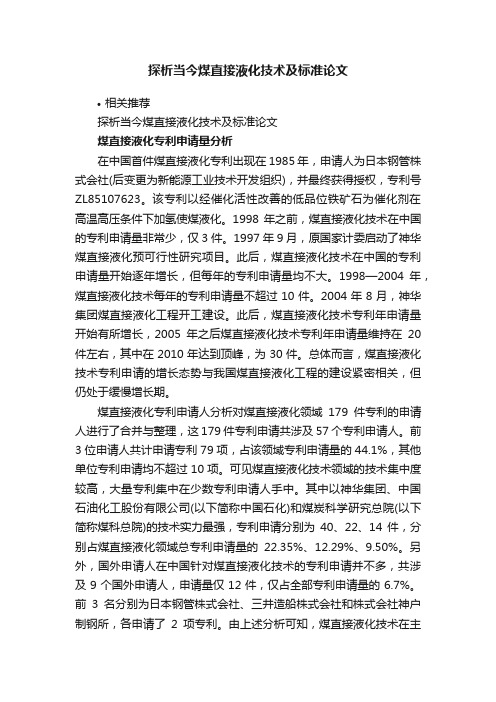
探析当今煤直接液化技术及标准论文•相关推荐探析当今煤直接液化技术及标准论文煤直接液化专利申请量分析在中国首件煤直接液化专利出现在1985年,申请人为日本钢管株式会社(后变更为新能源工业技术开发组织),并最终获得授权,专利号ZL85107623。
该专利以经催化活性改善的低品位铁矿石为催化剂在高温高压条件下加氢使煤液化。
1998年之前,煤直接液化技术在中国的专利申请量非常少,仅3件。
1997年9月,原国家计委启动了神华煤直接液化预可行性研究项目。
此后,煤直接液化技术在中国的专利申请量开始逐年增长,但每年的专利申请量均不大。
1998—2004年,煤直接液化技术每年的专利申请量不超过10件。
2004年8月,神华集团煤直接液化工程开工建设。
此后,煤直接液化技术专利年申请量开始有所增长,2005年之后煤直接液化技术专利年申请量维持在20件左右,其中在2010年达到顶峰,为30件。
总体而言,煤直接液化技术专利申请的增长态势与我国煤直接液化工程的建设紧密相关,但仍处于缓慢增长期。
煤直接液化专利申请人分析对煤直接液化领域179件专利的申请人进行了合并与整理,这179件专利申请共涉及57个专利申请人。
前3位申请人共计申请专利79项,占该领域专利申请量的44.1%,其他单位专利申请均不超过10项。
可见煤直接液化技术领域的技术集中度较高,大量专利集中在少数专利申请人手中。
其中以神华集团、中国石油化工股份有限公司(以下简称中国石化)和煤炭科学研究总院(以下简称煤科总院)的技术实力最强,专利申请分别为40、22、14件,分别占煤直接液化领域总专利申请量的22.35%、12.29%、9.50%。
另外,国外申请人在中国针对煤直接液化技术的专利申请并不多,共涉及9个国外申请人,申请量仅12件,仅占全部专利申请量的6.7%。
前3名分别为日本钢管株式会社、三井造船株式会社和株式会社神户制钢所,各申请了2项专利。
由上述分析可知,煤直接液化技术在主要专利都掌握在我国企业手中,国外企业并未针对中国市场展开大规模的专利布局。
煤炭的煤炭液化与煤制气技术研究进展

煤炭的煤炭液化与煤制气技术研究进展煤炭液化与煤制气技术研究进展煤炭作为一种重要的能源资源,在人类社会发展中扮演着重要的角色。
然而,传统的煤炭利用方式存在着严重的环境污染问题,因此煤炭液化与煤制气技术的研究进展成为了当前能源领域的热点之一。
一、煤炭液化技术煤炭液化是将固态煤转化为液体燃料的过程,其主要目的是提高煤炭能源的利用效率,降低对环境的污染。
传统的煤炭液化技术主要采用煤浆化和煤泥化的方法,通过热解、气化和加氢等步骤将煤转化为液体燃料。
然而,这些传统的液化技术存在着工艺复杂、能耗高和环境污染等问题。
近年来,煤炭液化技术得到了新的突破。
一种被广泛关注的技术是直接煤液化技术,其通过高温高压条件下将煤直接转化为液体燃料。
这种技术具有工艺简单、能耗低和环境友好等优势,被认为是未来煤炭液化的发展方向之一。
此外,还有一些新型的催化剂和溶剂被应用于煤炭液化过程中,能够提高液化效率和产物质量。
二、煤制气技术煤制气技术是将煤转化为合成气的过程,合成气主要由一氧化碳和氢气组成,可用于发电、制造化学品和合成燃料等领域。
传统的煤制气技术主要采用煤气化和煤炭燃烧两种方式,但这些方法存在着煤气净化困难、热效率低和环境污染等问题。
近年来,煤制气技术也取得了一系列的研究进展。
一种被广泛研究的技术是煤炭气化与气体分离一体化技术,其通过将煤气化和气体分离两个步骤结合起来,能够提高煤制气的效率和纯度。
此外,还有一些新型的气化剂和催化剂被应用于煤制气过程中,能够提高气化效率和减少污染物排放。
三、煤炭液化与煤制气技术的应用前景煤炭液化与煤制气技术的研究进展为煤炭资源的高效利用提供了新的途径。
这些技术不仅能够降低煤炭的环境污染,还能够提高能源利用效率,减少对传统能源的依赖。
尤其是在能源转型和碳减排的背景下,煤炭液化与煤制气技术具有重要的应用前景。
目前,煤炭液化与煤制气技术已经在一些国家和地区得到了广泛的应用。
例如,中国是世界上最大的煤炭生产和消费国,煤炭液化与煤制气技术在中国的应用已经取得了显著的成果。
煤炭资源的清洁高效液化技术研究
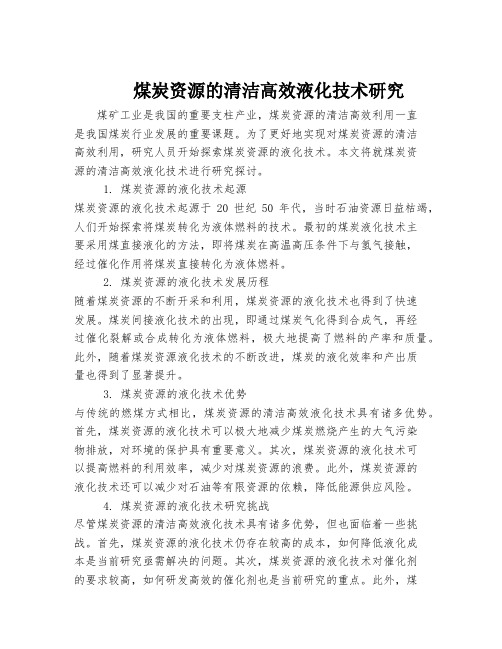
煤炭资源的清洁高效液化技术研究煤矿工业是我国的重要支柱产业,煤炭资源的清洁高效利用一直是我国煤炭行业发展的重要课题。
为了更好地实现对煤炭资源的清洁高效利用,研究人员开始探索煤炭资源的液化技术。
本文将就煤炭资源的清洁高效液化技术进行研究探讨。
1. 煤炭资源的液化技术起源煤炭资源的液化技术起源于20世纪50年代,当时石油资源日益枯竭,人们开始探索将煤炭转化为液体燃料的技术。
最初的煤炭液化技术主要采用煤直接液化的方法,即将煤炭在高温高压条件下与氢气接触,经过催化作用将煤炭直接转化为液体燃料。
2. 煤炭资源的液化技术发展历程随着煤炭资源的不断开采和利用,煤炭资源的液化技术也得到了快速发展。
煤炭间接液化技术的出现,即通过煤炭气化得到合成气,再经过催化裂解或合成转化为液体燃料,极大地提高了燃料的产率和质量。
此外,随着煤炭资源液化技术的不断改进,煤炭的液化效率和产出质量也得到了显著提升。
3. 煤炭资源的液化技术优势与传统的燃煤方式相比,煤炭资源的清洁高效液化技术具有诸多优势。
首先,煤炭资源的液化技术可以极大地减少煤炭燃烧产生的大气污染物排放,对环境的保护具有重要意义。
其次,煤炭资源的液化技术可以提高燃料的利用效率,减少对煤炭资源的浪费。
此外,煤炭资源的液化技术还可以减少对石油等有限资源的依赖,降低能源供应风险。
4. 煤炭资源的液化技术研究挑战尽管煤炭资源的清洁高效液化技术具有诸多优势,但也面临着一些挑战。
首先,煤炭资源的液化技术仍存在较高的成本,如何降低液化成本是当前研究亟需解决的问题。
其次,煤炭资源的液化技术对催化剂的要求较高,如何研发高效的催化剂也是当前研究的重点。
此外,煤炭资源的液化技术还存在着燃烧产生的副产品处理难题,如何有效处理液化副产品对环境造成的影响也是亟需解决的问题。
5. 煤炭资源的液化技术未来展望随着我国经济的快速发展和环境保护意识的提高,煤炭资源的清洁高效液化技术将会迎来更广阔的发展空间。
煤的液化的原理范文
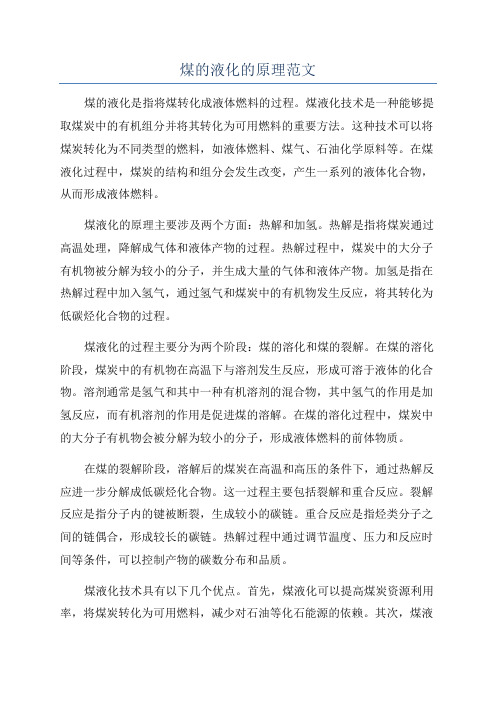
煤的液化的原理范文煤的液化是指将煤转化成液体燃料的过程。
煤液化技术是一种能够提取煤炭中的有机组分并将其转化为可用燃料的重要方法。
这种技术可以将煤炭转化为不同类型的燃料,如液体燃料、煤气、石油化学原料等。
在煤液化过程中,煤炭的结构和组分会发生改变,产生一系列的液体化合物,从而形成液体燃料。
煤液化的原理主要涉及两个方面:热解和加氢。
热解是指将煤炭通过高温处理,降解成气体和液体产物的过程。
热解过程中,煤炭中的大分子有机物被分解为较小的分子,并生成大量的气体和液体产物。
加氢是指在热解过程中加入氢气,通过氢气和煤炭中的有机物发生反应,将其转化为低碳烃化合物的过程。
煤液化的过程主要分为两个阶段:煤的溶化和煤的裂解。
在煤的溶化阶段,煤炭中的有机物在高温下与溶剂发生反应,形成可溶于液体的化合物。
溶剂通常是氢气和其中一种有机溶剂的混合物,其中氢气的作用是加氢反应,而有机溶剂的作用是促进煤的溶解。
在煤的溶化过程中,煤炭中的大分子有机物会被分解为较小的分子,形成液体燃料的前体物质。
在煤的裂解阶段,溶解后的煤炭在高温和高压的条件下,通过热解反应进一步分解成低碳烃化合物。
这一过程主要包括裂解和重合反应。
裂解反应是指分子内的键被断裂,生成较小的碳链。
重合反应是指烃类分子之间的链偶合,形成较长的碳链。
热解过程中通过调节温度、压力和反应时间等条件,可以控制产物的碳数分布和品质。
煤液化技术具有以下几个优点。
首先,煤液化可以提高煤炭资源利用率,将煤炭转化为可用燃料,减少对石油等化石能源的依赖。
其次,煤液化可以降低燃料的污染性,减少大气污染和温室气体排放。
此外,煤液化还可以生产出更多的高附加值化学产品,提高煤炭综合利用的经济和环境效益。
总之,煤液化是一种可以将煤炭转化为液体燃料的重要技术。
通过热解和加氢两个过程,煤炭中的有机组分可以转化为液体化合物,形成液体燃料的前体物质。
煤液化技术有望成为未来能源领域的重要发展方向,为可持续能源的发展做出贡献。
煤液化技术的重要性

煤液化技术的重要性煤液化技术是指将固态的煤炭转化为液态燃料或化学品的过程。
这项技术对于能源产业和经济发展具有重要的意义。
煤是世界上最丰富的化石能源之一,但一般来说,燃煤会排放大量的二氧化碳、二氧化硫等有害气体,对环境和人类健康都造成极大的损害。
相对于原油资源的逐渐枯竭和国际能源形势的愈发严峻,发展煤液化技术具有重要的振兴煤炭工业、增加能源供给等方面的意义。
首先,在资源保障方面,煤液化技术有助于解决石油资源的不足和不平衡的问题。
近年来,发展煤液化技术成为国际上一项热门的研究课题,许多国家都开始大力支持和投入重资发展煤液化产业。
我国是煤炭资源大国,而且资源丰富分布广泛,发展煤液化产业可以更好地开发和利用煤炭资源,增加石化产业的供给。
此外,由于我国地广人多,能源需求量大,发展煤液化产业有助于增加我国能源类型的多样性,减少对外部能源的依赖,稳定国家能源供给,提高能源安全保障能力。
其次,在经济发展方面,发展煤液化技术有助于实现经济增长和就业创造。
随着科技不断发展和进步,液化煤产业逐渐成为一个风险较小、利润较高的支柱产业。
一旦煤液化生产线能够投入生产,它将会带来巨大的经济效益和社会效益。
一方面,煤液化技术可实现对所有煤种的利用,提高资源利用率,降低成本操作成本,对经济发展提供了更多的支撑和保障。
另一方面,发展煤液化技术还将带来新的就业机会,增加农村劳动力的就业渠道,促进农民就业,提高居民收入水平,改善民生福祉。
最后,在环境保护方面,煤液化技术有助于减少环境污染和温室气体排放。
液化煤产业可解决煤炭燃烧所产生的大量环境污染问题,同时也使排放温室气体的量大大减少。
液化煤技术的发展使得煤炭能够逐渐从一个相对短暂、不可持续的能源向一个更为可持续、环保的能源转型。
这样,在保护环境方面,煤液化技术的应用和发展也为我们国家的长远发展提供了更多的保障。
总之,煤液化技术是一个重要的科技领域,具有巨大的发展潜力和应用空间。
它的应用和发展有助于解决石油资源不足、对外部依赖以及环境污染等各种问题,提高了能源的利用效率、经济发展水平和环境质量,具有重要的经济、社会和环境意义。
化工学科前沿结课论文 (3)
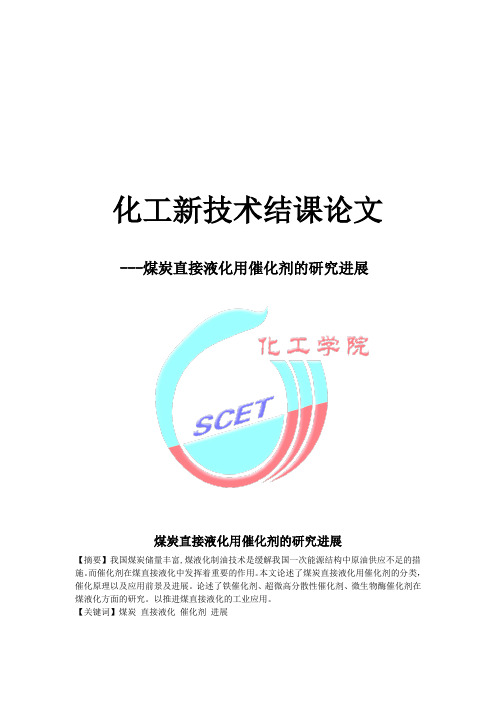
化工新技术结课论文---煤炭直接液化用催化剂的研究进展煤炭直接液化用催化剂的研究进展【摘要】我国煤炭储量丰富,煤液化制油技术是缓解我国一次能源结构中原油供应不足的措施。
而催化剂在煤直接液化中发挥着重要的作用。
本文论述了煤炭直接液化用催化剂的分类,催化原理以及应用前景及进展。
论述了铁催化剂、超微高分散性催化剂、微生物酶催化剂在煤液化方面的研究。
以推进煤直接液化的工业应用。
【关键词】煤炭直接液化催化剂进展0.引言世界上煤的储量比石油丰富得多,有可能成为未来燃料的主要来源[1]。
煤直接液化能够提供分子量比原煤低,H/C原子比比原煤高的液体燃料, 仍是广泛研究的从煤制备洁净液体材料的重要途径[2] , 公认的比较成功的煤直接液化工艺有两段或多段工艺和煤油共处理工艺,近年来还有铁基催化剂、超微高分散性催化剂、微生物酶催化剂、煤与废塑料在直接液化应用中的研究。
从某种程度上来讲,一种煤直接液化工艺开发的成功与否, 取决于其采用的催化剂。
根据煤直接液化工艺的特点, 可将煤液化催化剂分为两大类: 一类用于从煤直接生成液化油, 另一类用于将液化油进一步提质制备满足市场需要的运输燃料油。
1.煤直接液化的原理煤直接液化是煤在一定温度、压力和催化剂的作用下加氢转化的过程[3],煤分子中的一些键能较小的化学键发生热断裂,成较小分子的自由基。
在加氢反应中所使用的循环油通常采用H/ C较高的饱和烃,在加压时又有相当量的气相氢溶于循环油中,两者均提供使自由基稳定的氢源。
由于C—H键比H—H键活泼而易于断裂。
因此,循环油是主要的供氢载体,催化剂的功能是促进溶于液相中的氢与脱氢循环油间的反应,使脱氢循环油加氢并再生。
在直接液化过程中,煤的大分子结构首先受热分解,而使煤分解成以结构单元缩合芳烃为单个分子的独立的自由基碎片。
在高压氢气和催化剂存在下,这些自由基碎片又被加氢,形成稳定的低分子物。
自由基碎片加氢稳定后的液态物质可分成油类、沥青烯和前沥青烯等三种不同成分,对其继续加氢,前沥青烯即转化成沥青烯,沥青烯又转化为油类物质。
- 1、下载文档前请自行甄别文档内容的完整性,平台不提供额外的编辑、内容补充、找答案等附加服务。
- 2、"仅部分预览"的文档,不可在线预览部分如存在完整性等问题,可反馈申请退款(可完整预览的文档不适用该条件!)。
- 3、如文档侵犯您的权益,请联系客服反馈,我们会尽快为您处理(人工客服工作时间:9:00-18:30)。
摘要:论述了甲醇制汽油( MTG) 技术的工艺特点,并对固定床工艺和流化床工艺的优缺点及国内外MTG 技术的发展现状进行了详细分析。
从能源需求、工艺发展、技术优势、甲醇过剩等方面分析,得出甲醇转化为汽油技术相对成熟、简单、容易实现,且能缓解中国甲醇过剩和石油紧缺的矛盾,具有较好的经济性和实用性。
最后提出了中国发展MTG 技术的必要性,MTG 技术符合中国国情,具有广阔的应用前景,并提出项目能否正常运营取决于原料甲醇和产品汽油的价格。
关键词:MTG,甲醇制汽油,固定床工艺,流化床工艺,应用前景。
引言:近年来,在石油价格高位运行背景下,煤制油(CTL)研究不断升温,而甲醇制汽油(MTG)作为CTL 后半段的核心技术之一,也再次受到青睐。
MTG 工艺是在Mobil 公司开发的甲醇在ZSM-5 分子筛上转化为芳烃的基础上发展而来———以煤或天然气作原料生产合成气,再以合成气制甲醇,最后将粗甲醇转化为高辛烷值汽油。
Mobil 法MTG 技术首次公开于1976年,历经30 多年的改进和创新后,该工艺技术有了很大的进步,与石油炼制生产汽油路线的竞争力也越来越强,这对我国来说尤为重要。
国内自主创新,开发了具有自主知识产权的“一步法”工艺。
一步法甲醇转化制汽油新工艺已经申报中国发明专利,具有完全自主知识产权。
1 MTG工艺特点:(1)因为采用了ZSM-5沸石分子筛,所以Mobil法基本上不生成碳数为11 以上的烃类。
如果将沸石进行改性, 并适当改变反应条件, 生成物的组分分布就会发生变化。
将这一反应的产物油用作石化工业裂解的原料时, 可提高乙烯和丙烯的收率。
(2)对原料的纯度要求不高。
无需将粗甲醇中其他含氧化合物除去, 就可以用作MTG 工艺的原料。
(3)副产物价值高。
该工艺产生的少量副产物是液化石油气和高热值燃料气。
(4)产物性能优良。
产物油作为汽油使用时, 性能非常优良。
其生成物中, 一部分为芳香族烃, 其中大部分被甲基化; 另一部分是脂肪族烃类, 其中支链烃类占多数。
在无四乙基铅的情况下, 产物汽油的辛烷值为90~ 95。
比较而言, 目前用F-T 合成法得到的烃类主要是直链的烯烃和烷烃, 且碳数分布范围较广, 产物中有半数是蜡, 裂解后主要是柴油。
2 Mobil甲醇制汽油工艺过程:甲醇制汽油的转化反应是急剧的反应,最佳反应温度为370 ~430 ℃,在采用绝热反应器时,温升达到600 ℃左右。
因此,甲醇制汽油实现工业化的主要工程问题是如何传递反应热。
Mobil 公司为此先后开展了甲醇制汽油的固定床反应器、流化床反应器和多管式反应器3 种工艺。
2.1固定床法工艺:该工艺的优点是容易从中试结果进行工业化放大,放大研究的工作量最少; 但是严重的缺点是,催化剂特别容易老化失活。
同时,为了有效解决反应热的问题,固定床工艺通常采用两段式反应器,脱水反应器和转化反应器。
在固定床法工艺过程中,第一个反应是原料甲醇的脱水反应,在Cu /Al2O3催化剂的作用下,甲醇脱水而生成二甲醚。
未反应的甲醇、二甲醚、水从脱水反应器出来,与汽油分离塔中出来的压缩循环气进行混合,进入转化反应器,甲醇混合气在ZSM-5 分子筛催化剂的作用下,转化为汽油。
从转化反应器出来的气体,一部分用来预热原料甲醇,另一部分则用来与循环气换热,其余的部分则到达汽油分离塔,分离成液态烃、气态烃和水。
此时,如果从反应产物中检测出没有发生反应的甲醇,那么可以采用空气-N2混合气体燃烧的方法,将催化剂表面的焦炭去除掉,使催化剂再生。
固定床法工艺可以生产出抗爆性能良好的汽油,汽油中烃类的组成与常用汽油非常相似,而且汽油中没有硫和氯等组分,但催化剂老化失活现象较严重。
2.2 流化床法工艺:流化床法工艺是美国Mobil公司和德国联合褐煤公司共同开发的,该项目得到了美国能源部和西德研究和工艺部的财政资助。
主要装置包括: 流化床反应器、再生塔和冷却器。
将甲醇原料和水按照一定的比例配料先进行汽化,过热至177 ℃后便进入流化床反应器。
反应产物从流化床反应器的顶部出来,除去夹带的催化剂,对反应产物进行冷却,分离为水、稳定的汽油和轻组分。
流化床中的反应是急剧的放热反应,必须采用冷却器及时将热量移走,可以采用在流化床内安装传热盘管,也可以使催化剂通过外部冷却器循环来回收该反应放出的热量。
可是,不管采用哪一种热量去除办法,为了将催化剂表面的积炭去除,都不得不将一部分催化剂循环至再生塔进行再生。
流化床法工艺的特点主要有以下几方面: 一是甲醇转化比较完全,汽油的收率以及汽油的辛烷值都要比固定床法工艺高; 二是在操作过程中,反应热比较容易移去,当然也可以利用反应热来生产高压蒸汽; 三是通过催化剂再生以及补充新鲜催化剂,使得催化剂的活性相对比较稳定。
缺点就是操作不太方便。
2.3多管式反应器:多管式反应器是Lurgi 公司与Mobil 公司协作开发的,与固定床法工艺不同的是,该方法是在一台反应器中将甲醇转化为烃的。
反应器出来的气体与原料甲醇和循环气进行热交换,将原料温度调整到适宜的反应温度。
气体与甲醇混合物从上部进入多管式反应器中,在催化剂作用下,催化转化为烃。
反应热则由多管式反应器壳程循环的熔融盐带入蒸汽发生器中,从而产生高压蒸汽。
从多管式反应器出来的反应生成物则通过热交换器冷却至常温。
甲醇制汽油的反应温度约为400 ℃,该工艺采用熔融盐冷却,不能保证高压蒸汽均匀分布,此外,由于在单位反应器中,催化剂的装载量较少,催化剂再生过程中的高温,对于机械也有很大的损害。
2.4国内MTG一步法:Mobil 公司的MTG 工艺是采用两段反应,一段采用改性的氧化铝为催化剂,实现甲醇脱水到二甲醚的目的,甲醇的转化通常达到平衡转化率。
二段采用改性的ZSM -5 分子筛催化剂,完成甲醇、二甲醚( 和水) 混合物到汽油组分的转化。
中国科学院山西煤炭化学研究所从20 世纪80 年代开始关注甲醇转化制汽油的MTG 过程。
在工艺方面,山西煤炭化学研究所与赛鼎工程有限公司( 原化学工业第二设计院) 合作,自主创新,开发了具有自主知识产权的“一步法”工艺。
其特征是甲醇到汽油和LPG 的转化仅需要一段反应,无须再进行甲醇到二甲醚的转化反应,不仅缩短了工艺流程,而且避免了两段法工艺由于两段催化剂寿命不匹配所带来的诸多麻烦。
一步法甲醇转化制汽油新工艺已经申报中国发明专利,具有完全自主知识产权。
表1 为一步法工艺与两步法工艺比较。
其主要区别在于,一步法工艺将甲醇脱水制二甲醚和甲醇/二甲醚脱水制汽油两步反应在同一台反应器和同一个催化剂作用下完成,使工艺过程简化,设备投资得到降低。
在反应指标方面,一步法工艺具有反应条件温和,汽油选择性高,催化剂单程寿命长,汽油辛烷值高,单位重量汽油消耗的催化剂量小等优点。
表一一步法工艺与二步法工艺的比较项目一步法工艺二步法工艺反应器入口温度/℃315 350 ~366反应器出口温度/℃430 415反应器入口压力/MPa 1.6 ~1.8 1.9 ~2.3反应器出口压力/MPa 1.6 1.6物料循环比6~9 ~6催化剂单程寿命( t 甲醇/t 催化剂) 500 500催化剂总寿命( t 甲醇/t 催化剂) 10000 8000汽油收率(W) /%36 33LPG 收率(W) /% 5 8研究法辛烷值/RON 93 92马达法辛烷值/MON 84.3 823 MTG项目前景分析:3.1 可行性分析:(1)有助于缓解中国石油短缺的紧张局面随着经济的快速发展,能源紧缺的问题日益突出。
2009 年,中国石油消耗量跃居世界第2,中国石油对外依存度达到了50%,按照目前经济发展速度和能源的消耗速度,寻找新的可替代能源已迫在眉睫,而MTG 是缓解中国石油紧张的重要途径之一。
(2)丰富了煤制油路线煤基制油技术在中国正面临着良好的发展机遇和长远的发展前景。
MTG 技术是以煤或天然气作原料生产合成气,再用合成气制甲醇,最后将粗甲醇转化为高辛烷值、无硫无氯的高品质汽油。
由于MTG 技术相对简单,MTG 有可能成为甲醇的后继产业链,实现由煤到甲醇,再到油品的路线,为当前中国煤制油工业提供了一个与煤炭直接液化和费-托合成平行的可供选择的技术路线,具有非常广阔的应用前景。
(3)缓解当前国内甲醇过剩局面,延伸煤化工产业链近年来,甲醇项目受到诸多企业的青睐,大批甲醇项目争相上马,导致甲醇产能过剩,企业纷纷寻找甲醇深加工技术,延伸产品链。
流化床MTG 技术可以有效缓解甲醇产能过剩局面,延伸煤化工产业链,促进煤化工产业健康,持续发展。
(4)技术相对简单,容易实现MTG 技术与甲醇制烯烃技术、甲醇制丙烯技术相比,在反应器技术、油品后处理技术及油品品质等方面都有一定的优势。
特别是MTG 技术的产品汽油,不含S、N,经简单处理可以直接使用。
过剩等方面分析,发展MTG 技术是十分必要的,是符合中国国情的重要措施。
3.2 经济性分析:目前,中国甲醇产能严重过剩,甲醇主要下游产品对甲醇需求不足,预计甲醇价格低位运行将成为未来较长时期内的市场现状,以甲醇成本1700元/t 计算,生产每吨汽油原料外的成本费用( 包括折旧和摊销费用) 600 元计算,根据美孚公司提供的数据( 每100 t 甲醇可生产汽油37. 76 t,液化石油气4. 89 t,燃料气1. 27 t,火炬气0. 04 t) ,可以得到汽油成本为5102 元/t。
中国汽油价格受国际原油价格的影响,长期处于高位,未来3 a 内预测的90 号汽油的年平均批发价格将为6800 ~7300 元/t,93 号汽油的年平均批发价格将为7350 ~7850 元/t。
由此可见,用市场价格的甲醇通过MTG 工艺生产汽油的成本与93 号汽油批发价格相比,可见MTG 利润空间比较稳定。
如果甲醇是自备生产装置,甲醇价格以成本计算,则利润空间将进一步扩大。
由于石油资源的不可再生性,随着国际油价的回升,MTG 项目的经济性将进一步加强。
结论:(1) MTG 技术具有优良的产品组合( 高品质汽油和LPG) ,灵活的装置规模和较小的投资金额,但此项目的可实施性取决于原料甲醇和产品汽油的价格;(2) MTG 项目在国外有着成熟的商业运营经验,国内技术也已具备工业化运行条件,如采用国内技术,经济效益更加显著;(3) MTG 工艺丰富了煤制油路线。
由于MTG技术相对简单,MTG 有可能成为甲醇的后继产业链,实现由煤到甲醇,再到油品的路线,为当前中国煤制油工业提供了一个与煤炭直接液化和费-托合成平行的可供选择的技术路线,具有非常广阔的应用前景。
参考文献:1 煤化工工艺学郭树才化学工业出版社2006.42 中国知网甲醇制汽油( MTG) 技术应用实践介绍尹丽夏3 中国知网甲醇制汽油发展现状及前景分析王毅4 中国知网甲醇制汽油工艺概述刘于英原丰贞赵霄鹏。