轮胎工艺资料
轮胎制造密炼工艺全程介绍

----老配方 下位机选择、确认
•
混炼----母炼、再炼、终炼
•
出片
挤出机出片: 单螺杆/双螺杆
开炼机出片: 单台/双台
•
胶片冷却----胶片冷却联动线,
•
收胶与标识
•
检验与放行
母炼:门尼;
终炼:硬度、比重、门尼、硫变仪等。
3、密炼原理:
3.1、密炼机的基本构造
工作系统 ----密炼室 ----上顶栓 ----转子 ----卸料门 ----加热冷却系统 辅助系统 ----润滑系统 ----密封系统 ----电机传动装置
1、概述:
密炼工艺:通过在密闭式炼胶机及适当的加工条件下,将配 合剂与生胶均匀混合在一起,制成质量均一、满足后续加工 的混合物,完成这一加工操作的工艺过程即为胶料密炼工艺, 简称密炼。
2、密炼作业流程:
原材料仓库
发料
配方调用
送炭黑油
烘切胶 小粉料品种及总重
检
料
测
生胶
细料
炭黑与油料的称 量
混炼与排 胶
6) 出片装置: 功能:将主机排出的物料压成连续的薄片。 主要装备:挤出机或开炼机。
7) 胶片冷却系统: 功能:胶片悬挂、冷却、收取。 主要装备:胶片冷却系统。
5、影响密炼机混炼效果的因素:
• 混炼容积
填充系数大,容量过大,胶料翻转困难,使上顶拴位置不当,使一部分胶
料在加料口颈处发生滞留,从而使胶料混合不均匀,混炼时间长,并容易导 致设备超负荷,能耗大生热大,散热困难,升温快;
(2 ) 分散 通过密炼机转子突棱和室壁间产生的剪切作用, 使炭黑附聚体搓碎变 小,分散到生胶中, 并进一步生成结合橡胶。由于搓碎炭黑附聚体使消耗的能 量增加, 结合橡胶的生成使胶料弹性增加, 所以功率曲线回升, 出现第二个峰 值 (d点) 。
轮胎生产流程生产工艺
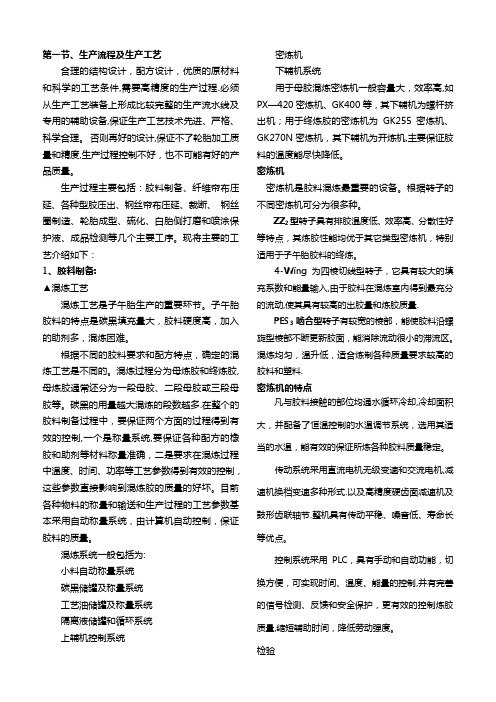
第一节、生产流程及生产工艺合理的结构设计,配方设计,优质的原材料和科学的工艺条件,需要高精度的生产过程.必须从生产工艺装备上形成比较完整的生产流水线及专用的辅助设备,保证生产工艺技术先进、严格、科学合理。
否则再好的设计,保证不了轮胎加工质量和精度,生产过程控制不好,也不可能有好的产品质量。
生产过程主要包括:胶料制备、纤维帘布压延、各种型胶压出、钢丝帘布压延、裁断、钢丝圈制造、轮胎成型、硫化、白胎侧打磨和喷涂保护液、成品检测等几个主要工序。
现将主要的工艺介绍如下:1、胶料制备:▲混炼工艺混炼工艺是子午胎生产的重要环节。
子午胎胶料的特点是碳黑填充量大,胶料硬度高,加入的助剂多,混炼困难。
根据不同的胶料要求和配方特点,确定的混炼工艺是不同的。
混炼过程分为母炼胶和终炼胶,母炼胶通常还分为一段母胶、二段母胶或三段母胶等。
碳黑的用量越大混炼的段数越多.在整个的胶料制备过程中,要保证两个方面的过程得到有效的控制,一个是称量系统,要保证各种配方的橡胶和助剂等材料称量准确,二是要求在混炼过程中温度、时间、功率等工艺参数得到有效的控制,这些参数直接影响到混炼胶的质量的好坏。
目前各种物料的称量和输送和生产过程的工艺参数基本采用自动称量系统,由计算机自动控制,保证胶料的质量。
混炼系统一般包括为:小料自动称量系统碳黑储罐及称量系统工艺油储罐及称量系统隔离液储罐和循环系统上辅机控制系统密炼机下辅机系统用于母胶混炼密炼机一般容量大,效率高,如PX—420密炼机、GK400等,其下辅机为螺杆挤出机;用于终炼胶的密炼机为GK255密炼机、GK270N密炼机,其下辅机为开炼机,主要保证胶料的温度能尽快降低。
密炼机密炼机是胶料混炼最重要的设备。
根据转子的不同密炼机可分为很多种。
ZZ2型转子具有排胶温度低、效率高、分散性好等特点,其炼胶性能均优于其它类型密炼机,特别适用于子午胎胶料的终炼。
4-Wing为四棱切线型转子,它具有较大的填充系数和能量输入,由于胶料在混炼室内得到最充分的流动,使其具有较高的出胶量和炼胶质量.PES3啮合型转子有较宽的棱部,能使胶料沿螺旋型棱部不断更新胶面,能消除流动很小的滞流区。
半钢轮胎生产工艺
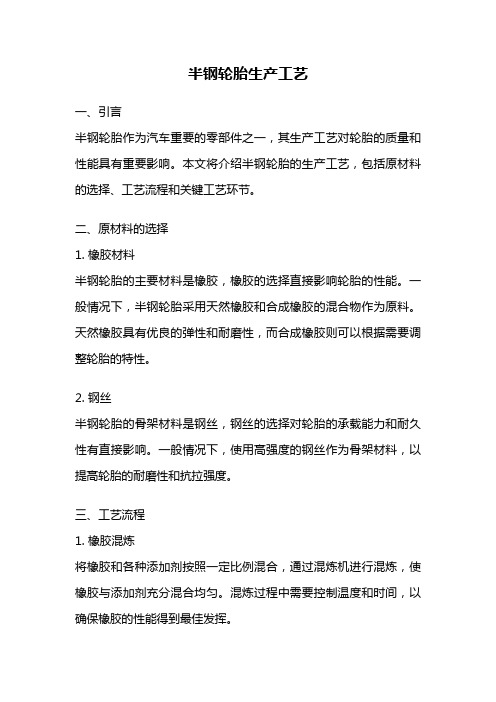
半钢轮胎生产工艺一、引言半钢轮胎作为汽车重要的零部件之一,其生产工艺对轮胎的质量和性能具有重要影响。
本文将介绍半钢轮胎的生产工艺,包括原材料的选择、工艺流程和关键工艺环节。
二、原材料的选择1. 橡胶材料半钢轮胎的主要材料是橡胶,橡胶的选择直接影响轮胎的性能。
一般情况下,半钢轮胎采用天然橡胶和合成橡胶的混合物作为原料。
天然橡胶具有优良的弹性和耐磨性,而合成橡胶则可以根据需要调整轮胎的特性。
2. 钢丝半钢轮胎的骨架材料是钢丝,钢丝的选择对轮胎的承载能力和耐久性有直接影响。
一般情况下,使用高强度的钢丝作为骨架材料,以提高轮胎的耐磨性和抗拉强度。
三、工艺流程1. 橡胶混炼将橡胶和各种添加剂按照一定比例混合,通过混炼机进行混炼,使橡胶与添加剂充分混合均匀。
混炼过程中需要控制温度和时间,以确保橡胶的性能得到最佳发挥。
2. 每层胶片的制作将混炼好的橡胶通过挤出机或压延机制成胶片,每层胶片的厚度根据轮胎的要求而定。
每层胶片的制作需要控制温度和压力,以保证胶片的质量。
3. 钢丝骨架的制作将钢丝经过清洗和拧绞等工艺处理,使其表面光滑且具有一定的强度。
然后将钢丝编织成骨架,骨架的形状和结构根据轮胎的要求而定。
4. 胎体的制作将每层胶片和钢丝骨架按照一定的工艺顺序叠合在一起,经过成型机的加热和压制,形成轮胎的胎体。
成型过程需要控制温度、压力和时间,以确保胎体的质量。
5. 胎纹的制作通过模具将胎体的胎纹部分进行冷挤压成型,形成轮胎的胎纹。
胎纹的形状和花纹根据轮胎的用途和性能要求而定。
6. 硫化将成型好的轮胎放入硫化机中进行硫化处理。
硫化过程中需要控制温度和时间,使橡胶与硫化剂充分反应,形成硫化交联结构,提高轮胎的强度和耐磨性。
7. 后处理经过硫化处理的轮胎需要进行后处理,包括修边、动平衡、外观检查等工艺。
修边是将轮胎边缘的多余材料去除,使轮胎边缘光滑。
动平衡是通过在轮胎上安装配重块,使轮胎在高速旋转时保持平衡。
外观检查是对轮胎的外观质量进行检查,确保轮胎没有明显的缺陷和损伤。
轮胎工艺知识点总结
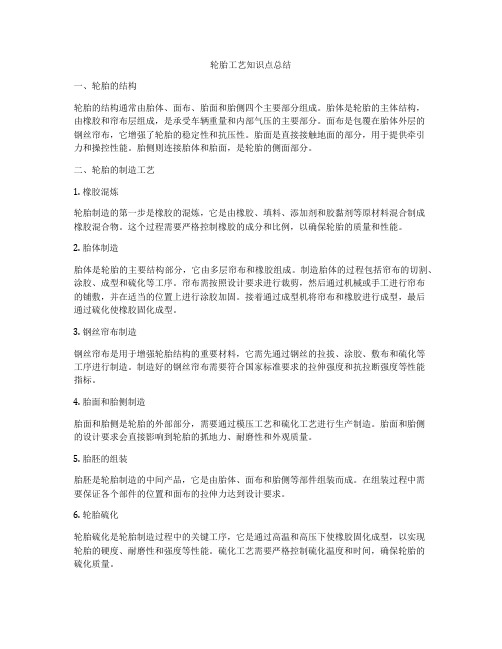
轮胎工艺知识点总结一、轮胎的结构轮胎的结构通常由胎体、面布、胎面和胎侧四个主要部分组成。
胎体是轮胎的主体结构,由橡胶和帘布层组成,是承受车辆重量和内部气压的主要部分。
面布是包覆在胎体外层的钢丝帘布,它增强了轮胎的稳定性和抗压性。
胎面是直接接触地面的部分,用于提供牵引力和操控性能。
胎侧则连接胎体和胎面,是轮胎的侧面部分。
二、轮胎的制造工艺1. 橡胶混炼轮胎制造的第一步是橡胶的混炼,它是由橡胶、填料、添加剂和胶黏剂等原材料混合制成橡胶混合物。
这个过程需要严格控制橡胶的成分和比例,以确保轮胎的质量和性能。
2. 胎体制造胎体是轮胎的主要结构部分,它由多层帘布和橡胶组成。
制造胎体的过程包括帘布的切割、涂胶、成型和硫化等工序。
帘布需按照设计要求进行裁剪,然后通过机械或手工进行帘布的铺敷,并在适当的位置上进行涂胶加固。
接着通过成型机将帘布和橡胶进行成型,最后通过硫化使橡胶固化成型。
3. 钢丝帘布制造钢丝帘布是用于增强轮胎结构的重要材料,它需先通过钢丝的拉拔、涂胶、敷布和硫化等工序进行制造。
制造好的钢丝帘布需要符合国家标准要求的拉伸强度和抗拉断强度等性能指标。
4. 胎面和胎侧制造胎面和胎侧是轮胎的外部部分,需要通过模压工艺和硫化工艺进行生产制造。
胎面和胎侧的设计要求会直接影响到轮胎的抓地力、耐磨性和外观质量。
5. 胎胚的组装胎胚是轮胎制造的中间产品,它是由胎体、面布和胎侧等部件组装而成。
在组装过程中需要保证各个部件的位置和面布的拉伸力达到设计要求。
6. 轮胎硫化轮胎硫化是轮胎制造过程中的关键工序,它是通过高温和高压下使橡胶固化成型,以实现轮胎的硬度、耐磨性和强度等性能。
硫化工艺需要严格控制硫化温度和时间,确保轮胎的硫化质量。
7. 轮胎检验和包装轮胎制造完成后需要进行严格的质量检验,包括外观质量、尺寸测量、硫化性能和性能测试等。
合格的轮胎在包装之前还需要进行气密性试验和动平衡试验等。
三、轮胎的检验和测试轮胎制造过程中的检验和测试是确保轮胎质量的重要环节。
轮胎生产工艺及流程
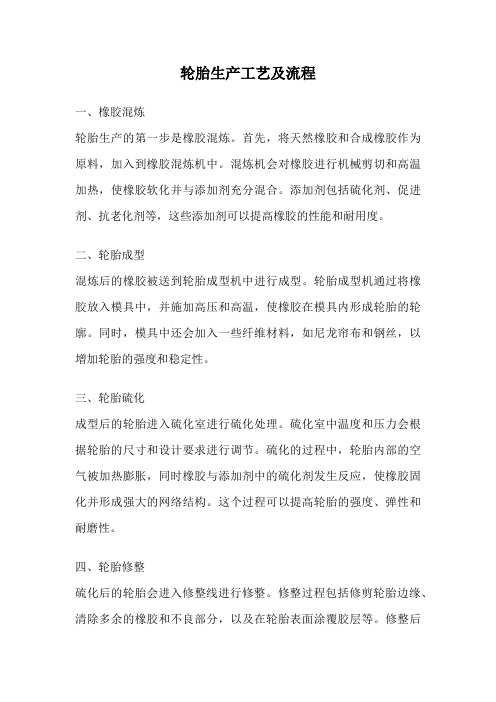
轮胎生产工艺及流程一、橡胶混炼轮胎生产的第一步是橡胶混炼。
首先,将天然橡胶和合成橡胶作为原料,加入到橡胶混炼机中。
混炼机会对橡胶进行机械剪切和高温加热,使橡胶软化并与添加剂充分混合。
添加剂包括硫化剂、促进剂、抗老化剂等,这些添加剂可以提高橡胶的性能和耐用度。
二、轮胎成型混炼后的橡胶被送到轮胎成型机中进行成型。
轮胎成型机通过将橡胶放入模具中,并施加高压和高温,使橡胶在模具内形成轮胎的轮廓。
同时,模具中还会加入一些纤维材料,如尼龙帘布和钢丝,以增加轮胎的强度和稳定性。
三、轮胎硫化成型后的轮胎进入硫化室进行硫化处理。
硫化室中温度和压力会根据轮胎的尺寸和设计要求进行调节。
硫化的过程中,轮胎内部的空气被加热膨胀,同时橡胶与添加剂中的硫化剂发生反应,使橡胶固化并形成强大的网络结构。
这个过程可以提高轮胎的强度、弹性和耐磨性。
四、轮胎修整硫化后的轮胎会进入修整线进行修整。
修整过程包括修剪轮胎边缘、清除多余的橡胶和不良部分,以及在轮胎表面涂覆胶层等。
修整后的轮胎表面更加平整光滑,外观更加美观。
五、轮胎质检修整后的轮胎会经过严格的质检程序。
质检人员会对轮胎进行外观检查、尺寸检测以及性能测试。
外观检查包括检查轮胎表面是否有明显的瑕疵或缺陷,尺寸检测则是确保轮胎的尺寸符合设计要求。
性能测试包括耐磨性测试、抗滑性测试、抗爆破性测试等,以确保轮胎的质量和性能达到标准。
六、包装和出厂质检合格的轮胎会被包装起来,准备出厂。
包装通常使用塑料薄膜,以保护轮胎免受污染和损坏。
然后,轮胎会被装载到货车或集装箱中,准备运往销售渠道或客户。
轮胎的生产工艺及流程包括橡胶混炼、轮胎成型、轮胎硫化、轮胎修整、轮胎质检以及包装和出厂等环节。
每个环节都至关重要,只有每个步骤都严格把控,才能生产出质量可靠的轮胎产品。
轮胎作为汽车的重要组成部分,对行驶安全和舒适性具有重要影响,因此轮胎生产过程中的每一个细节都需要被精心处理和管理。
自行车轮胎生产工艺
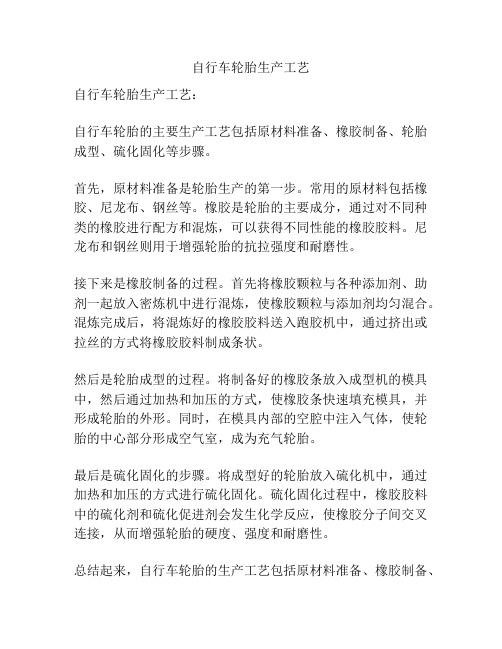
自行车轮胎生产工艺
自行车轮胎生产工艺:
自行车轮胎的主要生产工艺包括原材料准备、橡胶制备、轮胎成型、硫化固化等步骤。
首先,原材料准备是轮胎生产的第一步。
常用的原材料包括橡胶、尼龙布、钢丝等。
橡胶是轮胎的主要成分,通过对不同种类的橡胶进行配方和混炼,可以获得不同性能的橡胶胶料。
尼龙布和钢丝则用于增强轮胎的抗拉强度和耐磨性。
接下来是橡胶制备的过程。
首先将橡胶颗粒与各种添加剂、助剂一起放入密炼机中进行混炼,使橡胶颗粒与添加剂均匀混合。
混炼完成后,将混炼好的橡胶胶料送入跑胶机中,通过挤出或拉丝的方式将橡胶胶料制成条状。
然后是轮胎成型的过程。
将制备好的橡胶条放入成型机的模具中,然后通过加热和加压的方式,使橡胶条快速填充模具,并形成轮胎的外形。
同时,在模具内部的空腔中注入气体,使轮胎的中心部分形成空气室,成为充气轮胎。
最后是硫化固化的步骤。
将成型好的轮胎放入硫化机中,通过加热和加压的方式进行硫化固化。
硫化固化过程中,橡胶胶料中的硫化剂和硫化促进剂会发生化学反应,使橡胶分子间交叉连接,从而增强轮胎的硬度、强度和耐磨性。
总结起来,自行车轮胎的生产工艺包括原材料准备、橡胶制备、
轮胎成型和硫化固化等步骤。
这些工艺环节的精细控制和协调配合能够保证生产出质量优良的自行车轮胎。
轮胎行业工艺流程

轮胎行业工艺流程
《轮胎行业工艺流程》
轮胎作为车辆的重要零部件,其制造工艺流程非常复杂。
以下是轮胎行业工艺流程的简要介绍:
1. 布胎:轮胎的制作是从内部开始的,首先是将胎体的骨架结构通过一定的工艺手段进行排布,形成布胎。
布胎的设计和制作需要考虑轮胎的尺寸、荷载和速度等因素。
2. 胶料制备:轮胎的胎体和胎面需要使用各种不同类型的橡胶,其中包括天然橡胶、合成橡胶等材料。
这些橡胶材料需要经过一系列的工艺流程,包括混炼、压片、硫化等步骤,制备成适合轮胎生产的胶料。
3. 成型:成型是轮胎制造的关键环节,通过在模具内注入胶料并施加压力和热力,使其在模具内形成具有特定轮胎花纹和轮胎轮廓的成品。
成型过程需要严格控制温度、压力和时间等参数。
4. 硫化:硫化是将成型后的轮胎在高温和压力条件下进行固化和交联的过程。
这一步骤是轮胎工艺流程中至关重要的环节,能够提高轮胎的耐磨性和耐老化性能。
5. 检测和质量控制:轮胎生产完成后,需要进行严格的检测和质量控制,确保轮胎符合相关的安全和性能标准。
这些检测包括轮胎的尺寸、硬度、韧性、耐磨性等各项指标。
以上是轮胎行业的工艺流程的主要环节,轮胎的制造需要精密的设备和严格的工艺管理,以确保轮胎的安全性和性能可靠性。
随着技术的不断发展,轮胎制造工艺也在不断创新和改进,以满足市场和消费者的需求。
子午线轮胎生产工艺
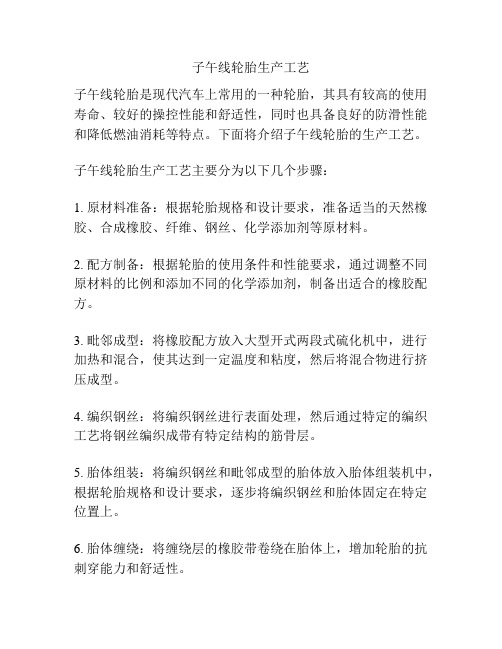
子午线轮胎生产工艺子午线轮胎是现代汽车上常用的一种轮胎,其具有较高的使用寿命、较好的操控性能和舒适性,同时也具备良好的防滑性能和降低燃油消耗等特点。
下面将介绍子午线轮胎的生产工艺。
子午线轮胎生产工艺主要分为以下几个步骤:1. 原材料准备:根据轮胎规格和设计要求,准备适当的天然橡胶、合成橡胶、纤维、钢丝、化学添加剂等原材料。
2. 配方制备:根据轮胎的使用条件和性能要求,通过调整不同原材料的比例和添加不同的化学添加剂,制备出适合的橡胶配方。
3. 毗邻成型:将橡胶配方放入大型开式两段式硫化机中,进行加热和混合,使其达到一定温度和粘度,然后将混合物进行挤压成型。
4. 编织钢丝:将编织钢丝进行表面处理,然后通过特定的编织工艺将钢丝编织成带有特定结构的筋骨层。
5. 胎体组装:将编织钢丝和毗邻成型的胎体放入胎体组装机中,根据轮胎规格和设计要求,逐步将编织钢丝和胎体固定在特定位置上。
6. 胎体缠绕:将缠绕层的橡胶带卷绕在胎体上,增加轮胎的抗刺穿能力和舒适性。
7. 成型硫化:将胎体放入硫化机中,根据特定的温度、时间和压力要求,进行硫化加工,使橡胶与钢丝、编织层等材料紧密结合,形成轮胎的整体结构。
8. 后处理:将成型硫化后的轮胎进行修边、去毛刺、喷漆等处理,使其外观更加美观。
9. 质量检测:对每一只轮胎进行严格的质量检测,如外观质量、尺寸测量、性能测试等,确保轮胎的质量符合标准要求。
10. 包装出厂:将符合质量要求的轮胎进行包装,并做好相应的标识和记录,然后出厂销售。
子午线轮胎的生产工艺需要借助先进的设备和技术,以确保轮胎的质量和性能符合规定标准。
在整个生产过程中,需要严格控制原材料的质量、配方的准确性以及操作的规范性,以确保子午线轮胎具有优良的使用性能和安全性。
通过持续的技术创新和工艺改进,子午线轮胎的生产工艺也在不断提升,以满足不同车辆和路况的需求。
- 1、下载文档前请自行甄别文档内容的完整性,平台不提供额外的编辑、内容补充、找答案等附加服务。
- 2、"仅部分预览"的文档,不可在线预览部分如存在完整性等问题,可反馈申请退款(可完整预览的文档不适用该条件!)。
- 3、如文档侵犯您的权益,请联系客服反馈,我们会尽快为您处理(人工客服工作时间:9:00-18:30)。
耐龟裂性 气密性好
化学稳定性 链烯烃化学反应,返原及老化
耐溶剂性 耐酸碱良,耐油及燃料油差
耐寒性 耐寒性好,耐材料
易塑炼,易包热辊,塑性大, 易于压出,加工性能良好
C=C)。
3)在正常的SBR中,苯乙烯含量为23.5%(重量%),摩尔比为1:6。
4)按聚合方法分类,SBR有乳液聚合(E-SBR)、溶液聚合(S-SBR)。
5)SBR较NR耐磨耗、湿地抓着力高,但生热高,加工困难。 6)溶聚较乳聚有较低的滚动阻力,高的抗湿滑性及良好的综合性能。
Study
SBR的分类区分
Study
主体材料介绍——SR
合成橡胶(SR): 合成橡胶是人们采用化学加工方法由相关单体制作的具有橡 胶特征的高弹性聚合物材料。
如SBR是由丁二烯与苯乙烯经化合而成的高弹聚合体。 常见的SR有:异戊橡胶(IR)、丁苯橡胶(SBR)、顺丁橡胶 (BR)、丁基或卤化丁基橡胶(IIR、X-IIR)、乙丙橡胶(EPM、 EPDM)等。其中各不同种类又有不同牌号的商品。
骨架材料
金属织物类:钢丝帘线,包括有纬及无纬两种,常用到的为无纬钢丝帘 线,按帘线的构成上分,又有OC、CC、普通分类,按强度上分又
有普强(NT)、高强(HT)、超高强(UT)等。
胎圈钢丝
作为轮胎受力的主要部位胎圈的主体,直径及强度不同有不同的分类。
CONTENTS
1 主体材料
5 增塑软化
6 配合其它
Study
BR的简单介绍
BR:poly Butadiene Rubber,高顺式聚丁二烯橡胶。
轮胎行业主要使用高顺式的聚丁二烯橡胶。
Study
BR的特点及使用
BR因为其分子链不含侧基,分子链的柔性好,所以具有以下特点: 1)良好的弹性和优异的耐寒性,很低的玻璃化温度。 2)耐磨耗性好,耐老化性能好,但老化后变硬且易崩花。 3)动态生热低,但湿动抓着力不好。
公司用:SBR1712、SBR1500、SBR1721、SBR1502、 BR9000、IR、EPDM、Br_IIR等。
Study
SBR(丁苯胶料)简介
SBR:Styrene-Butadiene Rubber SBR的基本情况
1)丁苯胶是世界产量、用量最大的合成胶,且70%用于轮胎制造业。 2)SBR单体为丁二烯(C=C-C=C)、苯乙烯(
4)耐曲挠性良好,但抗刺穿性不佳。
在轮胎行业BR的使用: 1)S/W部,与NR并用,以改善耐曲挠、耐O3老化性能。 2)T/D部,与NR/SBR并用,增加胶料的耐磨耗性,保持良好的 热稳定性及低的行驶温度。
Study
IIR的简单介绍
IIR:丁基橡胶,异丁烯橡胶。由异丁烯与少量异戊二烯聚合。前者是 主体材料,后者是用于提供可交联的双键。IIR具有高饱合度。
Study
白炭黑的简介 Silica
白炭黑:拥有一定的补强性的一种白色的无机填加剂。 使用演变:Rx(SiO3)y (1957年以前) → SiO2 • nH2O
Green Tire
20世纪90年代初,米其林通过用高分散性白炭黑替代胎面胶中的 炭黑创立了低滚动阻力的概念,使节省燃油成为现实,“绿色轮胎” 由此产生。为白炭黑的应用开辟了新的天地。
Study
C/B介绍
C/B是烃类不完全燃烧或热解制得的具有高度分散性的黑色粉末状 的物质,主要由元素C组成。
炭黑按制法的分类: 炉法C/B:烃类在反应炉中不完全燃烧制取的。
槽法C/B:是天然气与油类火焰与槽钢接触制造的。 热裂C/B:由天然气热解制得的。
乙炔C/B:由乙炔放热热解制得。
灯烟C/B:在敞口浅盘中燃烧烃类制取的。 现在轮胎行业使用的C/B主要是炉法C/B。
不利点 界面面积小,与橡胶亲和性差 易结团,不利于混炼的分散 迟缓硫化,易于其它组分作用 易吸附其它配合剂,不利于分散 易脱水形成硅氧基,不利于粘合 结构硬化,贮藏过程粘度增加
区分 No.01 No.02 No.03 No.04 No.05 No.06
采用改性 剂 以调节性 能
当今的世界橡胶行业,改善白炭黑的性能主要以偶联剂为主,而在偶 联剂中又以硅烷偶联剂占用量最大。 在硅烷偶联剂中,公司所采用的是TESPT (Si-69)
2 补强填充
3 硫化体系
7 骨架材料
8 胎圈钢丝
4 防护体系
一
主体材料 - NR - SBR - BR
- IIR
主体材料就是橡胶及其它高分子材 料,决定了制品的性能与用途。 我公司主要使用橡胶材料。
6
Study
主体材料介绍——NR
天然橡胶(NR) 天然橡胶是指从自然界中获得的,主要的采集对象是巴西橡胶树! NR的主要生产国:泰国、马来西亚、印度尼西亚、中国、印度等, NR的种类:烟片胶、颗粒胶(标准胶)、恒粘或低粘等特殊天然胶等。
Study
Silica补强在轮胎中的使用及效果
Tread部位: - 低滚动阻力,高制动性。 - 抗剥离性增加,抗切割性好。
I/L部位: - 与BIIR使用 透气性增加
C/C、Belt部位: - 粘着性增加。
1)轮胎滚动阻力降低,燃料消耗减少; 2)防滑性能和安全性能提高。
Study
白炭黑使用不利点及解决方案
分散能力
胶辊间隙 粘度 焦烧时间 压出收缩率 压出光滑度 压出速度 区分 项目
下降
增加 增加 减小 减小 提高 减小 比表面积↑ I2吸收值↑
提高
增加 增加 减小 减小 提高 变化小 结构增加 DBP吸收值↑
硬度
伸长率 耐磨耗性 搞撕裂性 搞割口增长性 耐屈挠性 弹性
增加
MIN后增加 提高 提高 提高 提高 减小
Study
轮胎用原材料统计
主体材料:是决定硫化胶使用性能及工艺性能的主要因素。
硫化体系:含硫化剂、促进剂、活性剂等,使橡胶通过化学交联,形成 立体网状结构,使可塑的粘弹胶料转变为可使用的高弹硫化胶。
配合体系
补强填充:保证胶料具有要求的力学性能,改善加工工艺并降低成本。 防护体系:提高硫化胶的耐老化性能,对各类型的老化起防护作用,在 一定程度上延长了制品的使用寿命。 软化增塑:改善加工性、耐寒性,也可降低成本。 纤维织物类:尼龙6、尼龙66、聚脂类、人造丝、芳纶等。
四硫化双(三乙氧基丙基)硅烷
Study
聚合物+偶联剂+白炭黑工作原理
(
C
S i-(C H 2 ) 3 -S -S - (S ) n -
C C C
C C C
C
C C C
C C C C
C
S i-(C H 2 ) 3 -S -S - (S ) n -
)n
PO LYM ER
偶 联 剂
C 2H 5O C 2H 5O
纤维织物帘线
2
3
4
4
3
205/55R16V 04 K407 重量,kg 重量% 区分 4.801 47.69% 胶料 0.732 7.27% 药品 0.220 2.18% 油类 0.528 5.24% 纤维类 1.007 10.00% 钢丝类 2.781 27.62% C/B类 TOTAL 10.068 100.00%
C 2H 5O
OH
O
O
OH
-O -S i-O -S i-O -
S IL IC A
-O -S i-O -S i-O -
此反应强烈依赖于温度的高低
增大
下降 提高 变化小 下降 下降 变化小
实验室检测项目的对应
生热
压缩变形 导电性
增加
变化小 增加
稍增加
变化小 变化小
Study
轮胎行业常用C/B名称统计
我公司现采用的及其它常见C/B统计
C/B检查SPEC ISAF/HS(LH10) ISAF/HS-HP130 ISAF-N220 ISAF-N205 SAF-HP1107 HAF-N330 HAF/LS-N326 HAF/HS-N339 FEF-N550 GPF-N660 SRF-N770 105℃*2hr 1.2↓ 1.2↓ 0.9↓ 1.2↓ 1.2↓ 0.9↓ 0.9(1.2)↓ 0.9↓ 0.85↓ 0.85↓ 0.85↓ I2 - mg/g 108-122 108-122 117-127 117-127 135-145 77-87 77-87 85-95 38-48 30-41 23-33 DBP-ml/g 1.28-1.42 1.28-1.42 1.10-1.20 1.09-1.19 1.25-1.35 0.97-1.07 0.67-0.77 1.17-1.27 1.16-1.28 0.85-0.97 0.66-0.76 325目 0.1%↓ 0.1%↓ 0.1%↓ 0.1%↓ 0.1%↓ 0.1%↓ 0.1%↓ 0.1%↓ 0.1%↓ 0.1%↓ 0.1%↓
Study
Copyright © zzxue
轮胎生产用原材料
Study
原辅材料区分
原材料: 是指以材料原来的形态构成成品或在成品内部维持材料 特性的配合物。 辅材料: 是指在成品制造过程中不能构成产品实体的材料。
Study
从轮胎断面图看轮胎用材料
1
区分 1
材料名称 胶料,包含配合剂
2
金属织物帘线 胎圈钢丝
Study
H_IIR的简单介绍
H_IIR:卤化丁基橡胶,包括氯化、溴化。 目的: 1)提高硫化速度; 2)提高与不饱和橡胶的相溶性。
3)改善自粘性和与其它材料的互粘性;
4)氯化的含氯量为1.1%~1.3%,溴化的含溴量约为2%。
Study