热处理工艺总结
钢厂热处理年度总结

一、前言时光荏苒,岁月如梭。
转眼间,本年度的热处理工作已接近尾声。
在过去的一年里,我厂热处理车间在厂领导的正确指导下,全体员工的共同努力下,紧紧围绕生产任务,不断优化工艺流程,提高生产效率,确保了产品质量,为公司的稳定发展做出了积极贡献。
现将本年度热处理工作总结如下:二、工作回顾1. 生产任务完成情况本年度,我厂热处理车间共完成各类热处理产品XX万吨,同比增长XX%。
其中,关键部件热处理完成XX万吨,同比增长XX%;一般部件热处理完成XX万吨,同比增长XX%。
生产任务的顺利完成,为公司的整体生产提供了有力保障。
2. 工艺优化与技术创新(1)针对部分产品热处理工艺存在能耗高、效率低的问题,我们积极开展工艺优化,通过调整加热温度、保温时间等参数,降低了能耗,提高了生产效率。
(2)针对部分新产品、新材料的热处理需求,我们积极引进新技术、新设备,如真空热处理、氮化处理等,满足了市场对高性能产品的需求。
(3)开展技术攻关,解决生产过程中遇到的难题,如解决某型号产品热处理变形问题,提高了产品质量。
3. 设备管理与维护(1)加强设备日常保养,确保设备正常运行,降低故障率。
(2)针对关键设备,制定专项维护保养计划,确保设备使用寿命。
(3)开展设备改造,提高设备自动化水平,降低人工成本。
4. 安全管理(1)加强安全教育培训,提高员工安全意识。
(2)严格执行操作规程,确保生产安全。
(3)开展安全隐患排查,及时消除安全隐患。
三、工作亮点1. 成功开发某新型热处理工艺,提高了产品性能,降低了生产成本。
2. 通过设备改造,提高了生产效率,降低了人工成本。
3. 安全生产无事故,实现了安全生产目标。
四、存在问题1. 部分产品热处理工艺仍存在能耗高、效率低的问题。
2. 部分设备自动化程度较低,影响了生产效率。
3. 部分员工安全意识有待提高。
五、改进措施1. 深入开展工艺优化,降低能耗,提高生产效率。
2. 加大设备改造力度,提高设备自动化水平。
热处理个人总结范文

时光荏苒,转眼间,我在热处理领域的工作已满一年。
在这一年的时间里,我经历了从理论到实践,从摸索到熟练的过程。
在此,我对自己过去一年的工作进行总结,以便更好地规划未来。
一、工作成果1. 熟悉热处理基本原理和工艺流程。
通过学习,我掌握了热处理的基本原理,了解了各种热处理工艺的适用范围和特点。
2. 熟练操作热处理设备。
我能够熟练地操作各类热处理设备,如退火炉、正火炉、淬火炉等,确保设备正常运行。
3. 参与热处理工艺优化。
根据生产需求,我参与了多个热处理工艺的优化工作,提高了产品质量和生产效率。
4. 解决生产中遇到的问题。
在热处理生产过程中,我多次成功解决了生产中遇到的问题,保证了生产进度。
二、工作不足1. 理论知识掌握不够深入。
虽然对热处理基本原理和工艺流程有所了解,但在实际应用中,对于一些复杂的热处理问题,我仍然感到力不从心。
2. 实践经验不足。
虽然参与了一些热处理工艺优化工作,但总体来说,实践经验还不够丰富。
3. 沟通协调能力有待提高。
在与其他部门沟通时,有时因表达不够清晰,导致工作效率降低。
三、改进措施1. 加强理论学习。
在今后的工作中,我将深入学习热处理理论知识,提高自己的业务水平。
2. 积累实践经验。
通过多参与生产实践,提高自己的动手能力和解决问题的能力。
3. 提高沟通协调能力。
加强与同事、上级的沟通,提高工作效率。
4. 关注行业动态。
关注热处理行业的发展趋势,紧跟行业步伐。
四、未来展望在新的一年里,我将继续努力,不断提升自己的业务水平,为我国热处理事业贡献自己的力量。
具体目标如下:1. 深入学习热处理理论知识,提高自己的专业素养。
2. 积极参与生产实践,提高自己的动手能力和解决问题的能力。
3. 加强与同事、上级的沟通,提高团队协作能力。
4. 关注行业动态,紧跟行业步伐,为我国热处理事业的发展贡献自己的力量。
总之,过去的一年,我在热处理领域取得了一定的成绩,但也存在不足。
在新的一年里,我将以更加饱满的热情投入到工作中,为实现个人和团队的目标而努力。
热处理工年终总结范文(精选5篇)
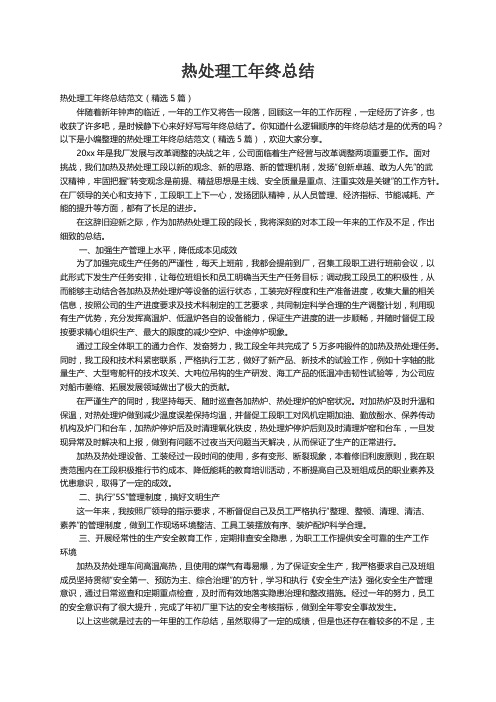
热处理工年终总结热处理工年终总结范文(精选5篇)伴随着新年钟声的临近,一年的工作又将告一段落,回顾这一年的工作历程,一定经历了许多,也收获了许多吧,是时候静下心来好好写写年终总结了。
你知道什么逻辑顺序的年终总结才是的优秀的吗?以下是小编整理的热处理工年终总结范文(精选5篇),欢迎大家分享。
20xx年是我厂发展与改革调整的决战之年,公司面临着生产经营与改革调整两项重要工作。
面对挑战,我们加热及热处理工段以新的观念、新的思路、新的管理机制,发扬“创新卓越、敢为人先”的武汉精神,牢固把握“转变观念是前提、精益思想是主线、安全质量是重点、注重实效是关键”的工作方针。
在厂领导的关心和支持下,工段职工上下一心,发扬团队精神,从人员管理、经济指标、节能减耗、产能的提升等方面,都有了长足的进步。
在这辞旧迎新之际,作为加热热处理工段的段长,我将深刻的对本工段一年来的工作及不足,作出细致的总结。
一、加强生产管理上水平,降低成本见成效为了加强完成生产任务的严谨性,每天上班前,我都会提前到厂,召集工段职工进行班前会议,以此形式下发生产任务安排,让每位班组长和员工明确当天生产任务目标;调动我工段员工的积极性,从而能够主动结合各加热及热处理炉等设备的运行状态,工装完好程度和生产准备进度,收集大量的相关信息,按照公司的生产进度要求及技术科制定的工艺要求,共同制定科学合理的生产调整计划,利用现有生产优势,充分发挥高温炉、低温炉各自的设备能力,保证生产进度的进一步顺畅,并随时督促工段按要求精心组织生产、最大的限度的减少空炉、中途停炉现象。
通过工段全体职工的通力合作、发奋努力,我工段全年共完成了5万多吨锻件的加热及热处理任务。
同时,我工段和技术科紧密联系,严格执行工艺,做好了新产品、新技术的试验工作,例如十字轴的批量生产、大型弯舵杆的技术攻关、大吨位吊钩的生产研发、海工产品的低温冲击韧性试验等,为公司应对船市萎缩、拓展发展领域做出了极大的贡献。
热处理心得体会
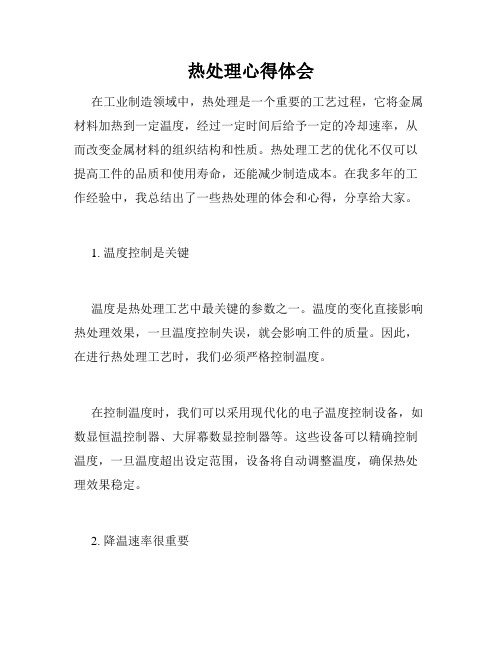
热处理心得体会在工业制造领域中,热处理是一个重要的工艺过程,它将金属材料加热到一定温度,经过一定时间后给予一定的冷却速率,从而改变金属材料的组织结构和性质。
热处理工艺的优化不仅可以提高工件的品质和使用寿命,还能减少制造成本。
在我多年的工作经验中,我总结出了一些热处理的体会和心得,分享给大家。
1. 温度控制是关键温度是热处理工艺中最关键的参数之一。
温度的变化直接影响热处理效果,一旦温度控制失误,就会影响工件的质量。
因此,在进行热处理工艺时,我们必须严格控制温度。
在控制温度时,我们可以采用现代化的电子温度控制设备,如数显恒温控制器、大屏幕数显控制器等。
这些设备可以精确控制温度,一旦温度超出设定范围,设备将自动调整温度,确保热处理效果稳定。
2. 降温速率很重要在金属材料热处理时,降温速率对材料的性能也有很大的影响。
对于一些要求高强度、高硬度的零件,降温速率应尽可能快,以保证零件的硬度和强度。
而对于一些要求高韧性的零件,则需要较低的降温速率,以保证零件的韧性。
在降温的过程中,我们可以采用自然冷却、强制空气冷却等方式来控制降温速率。
特别是对于较大尺寸的工件,一定要采取强制冷却的方式,以保证工件的热处理效果。
3. 选择合适的热处理介质热处理介质也是影响热处理效果的一个重要因素。
一般情况下,金属材料的热处理介质可分为气体介质、液体介质和固体介质三大类。
气体介质主要用于淬火工艺中,如采用淬火油、水等液体介质,可以使金属材料表面硬度增加,但容易产生变形和裂纹等缺陷。
而固体介质则以盐类为主,它的优点是产生的变形比液体介质小,对于一些要求高精度的工件,使用固体介质更为合适。
4. 过度热处理会产生负面影响有些人认为经过强化处理后的金属零件硬度高,应该更耐用。
其实并不完全正确。
如果经过过度热处理,会导致材料的晶粒过度长大,从而破坏了材料的均匀性和强度。
因此,在进行热处理工艺时,要根据实际情况选择合理的工艺,并严格控制热处理参数,避免出现过度热处理的情况。
热加工实训总结

热加工实训总结热加工是一种重要的金属加工方式,它通过加热金属材料,使其软化,然后进行塑性变形或切削加工,从而得到所需的形状和尺寸。
在工业生产中,热加工广泛应用于各种金属制品的生产和加工,如汽车零部件、机械零件、航空航天部件等。
为了提高学生的热加工技能,我校开设了热加工实训课程,让学生在实践中掌握热加工的基本原理和技术。
在热加工实训中,我们主要学习了以下几个方面的内容:一、热处理工艺热处理是热加工的重要环节,它可以改变金属材料的组织结构和性能,使其具有更好的机械性能和耐腐蚀性能。
在实训中,我们学习了常见的热处理工艺,如退火、正火、淬火、回火等。
通过实际操作,我们了解了每种热处理工艺的原理和适用范围,掌握了热处理的基本技能。
二、热加工设备热加工设备是实现热加工的关键,它包括热处理炉、热加工机床、热喷涂设备等。
在实训中,我们学习了各种热加工设备的结构和工作原理,了解了设备的使用方法和注意事项。
通过实际操作,我们掌握了设备的操作技能,提高了设备的使用效率和安全性。
三、热加工工艺热加工工艺是实现热加工的关键,它包括热加工的基本原理、加工工艺和加工参数等。
在实训中,我们学习了各种热加工工艺的原理和适用范围,了解了加工参数的选择和调整方法。
通过实际操作,我们掌握了热加工的基本技能,提高了加工效率和质量。
四、热喷涂技术热喷涂技术是一种新型的热加工技术,它可以在金属表面形成一层坚硬的涂层,提高金属的耐磨性和耐腐蚀性。
在实训中,我们学习了热喷涂技术的原理和适用范围,了解了喷涂设备的结构和工作原理。
通过实际操作,我们掌握了热喷涂的基本技能,提高了涂层的质量和稳定性。
热加工实训是一种非常重要的实践教学方式,它可以让学生在实践中掌握热加工的基本原理和技术,提高学生的实际操作能力和创新能力。
在今后的学习和工作中,我们将继续发扬实践精神,不断提高自己的热加工技能,为国家的工业发展做出更大的贡献。
热处理总结
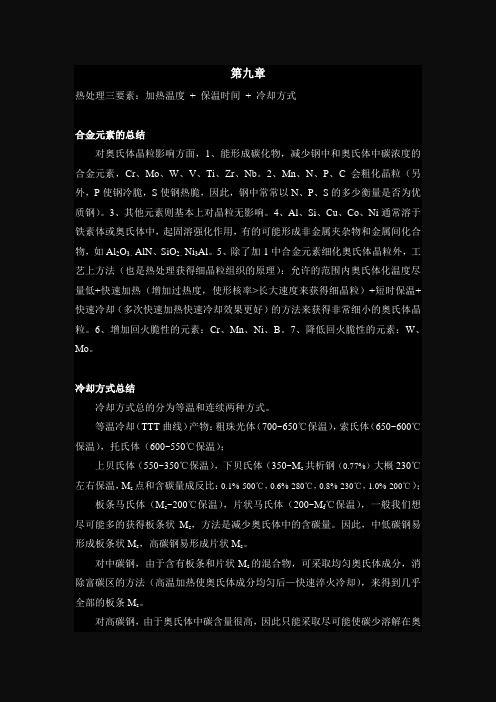
淬火:将钢加热到Ac3或Ac1以上一定温度(得到细小的奥氏体为依据),保温后以大于临界冷却速度冷却得到马氏体(或下贝氏体)的热处理工艺。
回火:将淬火钢加热到A1以下,使其转变为稳定的回火组织,并以适当的方式冷却的工艺过程。
均匀化退火:(Ac3或Acm以上150~300℃)。碳钢一般为1100~1200℃,合金钢一般为1200~1300℃,保温时间一般为10~15h,采用炉冷。当加热温度高、成本高,除非成分有区域偏析或较大的枝晶偏析才用,后加正火补充。
完全退火:(Ac3+20~30℃),保温时间:T= K•D min(K为1.5~2min/mm,D为工件有效厚度),采用炉冷,室温组织:铁素体+珠光体。用于消除魏氏组织(针片状)、带状组织,细化晶粒(相对组织而言);亚共析钢的预备热处理,均匀成分,消除加工硬化,降低硬度,为下一步切削加工做准备。
常见钢的编号(P307)
碳素结构钢(Q)低合金高强度钢(Q)碳素工具钢(T)
滚动轴承钢(G)焊接用钢(H)易切削钢(Y)
铸钢(ZG)锅炉用钢(g)桥梁用钢(q)
沸腾钢(F)半镇静钢(b)镇静钢(z)
机器零件、构件用钢,包括:渗碳钢(表层高强度硬度、耐磨性、抗疲劳强度,心部高强韧性,主要用于齿轮;低碳合金钢表面渗碳,淬火低温回火)、调质钢(综合性能高,主要用于轴类、连杆,中碳钢,调质处理)、弹簧钢(高碳钢,淬火350℃回火)、轴承钢(高强度硬度、耐磨性、抗疲劳强度高碳钢;淬火低温回火)。
常见的工程结构钢:型材、棒材、板材、管材、带材,由于他们都需要冷变形和焊接,采用低碳低合金钢;由于尺寸大、形状复杂,不能进行整体淬火回火,因此大部分工为热轧空冷(正火),室温组织:铁素体加少量珠光体。
热处理工作总结7篇
热处理工作总结7篇第1篇示例:热处理是一种通过控制金属材料的加热、保温和冷却过程来改变其结构和性能的工艺。
作为热处理工程师,我们在日常工作中需要根据不同金属材料的性质和加工要求,选择合适的工艺参数和设备,进行热处理操作,以达到提高材料硬度、强度、耐磨性以及改善其工艺性能等目的。
在过去一段时间的工作中,我深刻体会到热处理工作的重要性和复杂性,也积累了一些经验和教训,下面我将就此进行总结。
热处理工作需要严格遵守操作规程和安全措施。
在进行热处理操作时,要严格按照工艺流程和规范操作,避免出现操作失误或疏忽造成材料受损或设备事故的情况。
要时刻注意工作场所的通风情况和防护设施的完好性,确保操作人员的安全。
在进行热处理操作前,要对设备进行检查和保养,确保设备运行正常,避免因设备故障导致操作中断或事故发生。
热处理工作需要具备良好的专业知识和技能。
热处理工程师需要了解不同金属材料的性质和特点,掌握各种热处理工艺参数的调节方法,以及相关设备的操作原理和维护技巧。
只有具备扎实的专业知识和技能,才能正确选择合适的热处理工艺方案,确保热处理效果达到预期目标。
要不断学习和提升自己的专业水平,跟上行业技术的发展动态,为工作提供更加有力的支持。
热处理工作需要注重团队合作和沟通。
在实际工作中,热处理工程师需要与生产、质检、技术等部门密切合作,共同制定热处理方案和解决实际问题,保障产品质量和生产进度。
要建立良好的团队合作精神,积极参与工作讨论和交流,及时沟通和协调各方需求,确保工作的顺利进行。
热处理工作需要不断总结经验和教训,持续改进和完善工作流程。
在实际操作中,可能会出现各种问题和挑战,比如材料变形、裂纹产生等,我们要及时总结经验教训,找出问题原因并寻求解决方案,避免类似问题再次发生。
要关注热处理工艺技术的发展动态,引进新技术、新设备,不断改进和完善工作流程,提高工作效率和质量。
热处理工作是一项重要而复杂的工作,需要我们不断学习和提升自己,保持专业水平和团队合作精神,不断总结经验和完善工作流程,以确保工作顺利进行并达到预期效果。
2024年热处理年度工作总结范例(2篇)
2024年热处理年度工作总结范例尊敬的领导、同事们:您们好!我是热处理部门的一名普通员工,在过去的2024年里,我一直在这个岗位上努力工作,不断学习和提升自己。
经过一年的努力,我将我的工作总结如下。
一、指导思想在工作中,我始终坚持“追求卓越,责任至上”的原则。
每一项工作,我都严格要求自己,力求做到最好,以实际行动践行“质量第一、用户至上”的工作理念。
二、工作成果在2024年,我们热处理部门完成了各项工作任务,取得了一系列骄人的成绩:1. 提升工艺水平:我积极参与技术培训和学习,不断提升自己的知识和技能。
通过调研和参考优秀企业的先进经验,我们优化了热处理工艺流程,提高了产品的质量和工艺效率。
2. 技术创新:针对某些特殊材料的热处理难题,我积极与同事合作,开展技术攻关工作。
通过不断摸索和实践,我们克服了一系列技术难题,为公司的产品提供了更好的热处理解决方案。
3. 质量管理:我积极参与质量管理工作,认真执行各项质量标准和操作规程,严格控制产品的质量。
公司在2024年度的质量检查中,热处理部门被评定为优秀,得到了领导的表扬和肯定。
4. 安全生产:我始终把安全生产放在首要位置,严格按照相关规定和操作流程进行操作,积极参与安全培训和演练活动。
在2024年,热处理部门未发生任何安全事故,为公司的安全生产工作做出了贡献。
三、存在问题在本年度的工作中,我也发现了一些问题和不足:1. 学习不够深入:虽然我积极参加了技术培训和学习,但有时候对一些复杂技术的理解还不够深入,需要进一步加强学习,提升自己的专业水平。
2. 沟通不够顺畅:由于工作中的需要,我们经常需要与其他部门进行协作,但有时候沟通上存在一些问题,需要提高自己的沟通能力和团队合作精神。
3. 工作效率有待提高:由于工作量较大,我有时候会感到压力较大,可能会影响我的工作效率,需要进一步提高自己的工作效率和时间管理能力。
四、改进措施为了进一步提高自己的工作质量和效率,我制定了以下改进措施:1. 提高学习深度:我将利用业余时间加强学习,阅读更多的专业书籍和文献,参加更多的技术培训和学习交流活动,不断提升自己的专业水平。
热处理专业年度质量总结(3篇)
第1篇一、前言热处理作为材料加工的重要环节,在工业生产中发挥着至关重要的作用。
本年度,我国热处理行业在技术创新、质量管理、市场拓展等方面取得了显著成果。
现将本年度热处理专业质量工作总结如下:二、工作回顾1. 技术创新(1)研发新型热处理工艺:本年度,我国热处理行业在技术研发方面取得了丰硕成果,成功研发出新型热处理工艺,如真空热处理、激光热处理等,提高了产品质量和生产效率。
(2)优化现有热处理工艺:针对现有热处理工艺中存在的问题,通过优化工艺参数、改进设备等措施,降低了能耗,提高了热处理质量。
2. 质量管理(1)完善质量管理体系:本年度,我国热处理企业不断完善质量管理体系,严格执行ISO9001质量管理体系标准,确保产品质量。
(2)加强过程控制:在热处理过程中,严格控制工艺参数,确保产品质量稳定可靠。
同时,加强设备维护保养,降低设备故障率。
(3)提升员工素质:通过开展员工培训、技能竞赛等活动,提高员工的质量意识和操作技能,为产品质量提供有力保障。
3. 市场拓展(1)拓展国内外市场:本年度,我国热处理企业积极拓展国内外市场,与多家国内外知名企业建立了合作关系,产品远销欧美、东南亚等地区。
(2)参加行业展会:积极参加国内外热处理行业展会,展示企业实力,提升品牌知名度。
三、存在的问题及改进措施1. 存在问题(1)部分企业质量管理意识薄弱,质量管理体系不完善。
(2)热处理工艺水平有待提高,部分企业仍采用传统热处理工艺。
(3)市场竞争激烈,企业面临成本压力。
2. 改进措施(1)加强质量管理,完善质量管理体系,提高产品质量。
(2)加大技术研发投入,提高热处理工艺水平。
(3)优化生产流程,降低生产成本,提高企业竞争力。
四、展望展望未来,我国热处理行业将继续秉持“质量第一”的原则,以技术创新为动力,以市场为导向,不断提升产品质量,为我国制造业的发展贡献力量。
总之,本年度我国热处理专业在技术创新、质量管理、市场拓展等方面取得了显著成果。
热处理年度工作总结(2篇)
热处理年度工作总结热处理基础知识培训—学____结一、热处理定义热处理是将金属材料放在一定的介质内加热、保温、冷却,通过改变材料表面或内部的金相____结构,来控制其性能的一种金属热加工工艺。
二、热处理工艺的特点金属热处理是机械制造中的重要工艺之一,与其他加工工艺相比,热处理一般不改变工件的形状和整体的化学成分,而是通过改变工件内部的显微____,或改变工件表面的化学成分,赋予或改善工件的使用性能。
其特点是改善工件的内在质量,而这一般不是肉眼所能看到的。
为使金属工件具有所需要的力学性能、物理性能和化学性能,除合理选用材料和各种成形工艺外,热处理工艺往往是必不可少的。
钢铁是机械工业中应用最广的材料,钢铁显微____复杂,可以通过热处理予以控制,所以钢铁的热处理是金属热处理的主要内容。
另外,铝、铜、镁、钛等及其合金也都可以通过热处理改变其力学、物理和化学性能,以获得不同的使用性能。
三、常见热处理概念1.正火。
将钢材或钢件加热到临界点上的适当温度保持一定时间后在空气中冷却,得到珠光体类____的热处理工艺。
2.退火。
将亚共析钢工件加热至20—____度,保温一段时间后,随炉缓慢冷却(或埋在砂中或石灰中冷却)至____度以下在空气中冷却的热处理工艺。
3.固溶热处理。
将合金加热至高温单相区恒温保持,使过剩相充分溶解到固溶体中,然后快速冷却,以得到过饱和固溶体的热处理工艺。
4.时效。
合金经固溶热处理或冷塑性形变后,在室温放置或稍高于室温保持时,其性能随时间而变化的现象。
5.固溶处理。
使合金中各种相充分溶解,强化固溶体并提高韧性及抗蚀性能,消除应力与软化,以便继续加工成型。
6.时效处理。
在强化相析出的温度加热并保温,使强化相沉淀析出,得以硬化,提高强度。
7.淬火。
将钢奥氏体化后以适当的冷却速度冷却,使工件在横截面内全部或一定的范围内发生马氏体等不稳定____结构转变的热处理工艺。
8.回火。
将经过淬火的工件加热到临界点以下的适当温度保持一定时间,随后用符合要求的方法冷却,以获得所需要的____和性能的热处理工艺。
- 1、下载文档前请自行甄别文档内容的完整性,平台不提供额外的编辑、内容补充、找答案等附加服务。
- 2、"仅部分预览"的文档,不可在线预览部分如存在完整性等问题,可反馈申请退款(可完整预览的文档不适用该条件!)。
- 3、如文档侵犯您的权益,请联系客服反馈,我们会尽快为您处理(人工客服工作时间:9:00-18:30)。
1.退火
将钢件加热到Ac3+30~50度或Ac1+30~50度或Ac1以下的温度后,一般随炉温缓慢冷却。
目的:1.降低硬度,提高塑性,改善切削加工与压力加工性能
2.细化晶粒,改善力学性能,为下一步工序做准备
3.消除冷、热加工所产生的内应力。
应用要点:1.适用于合金结构钢、碳素工具钢、合金工具钢、高速钢的锻件、焊接件以及供应状态不合格的原材料
2.一般在毛坯状态进行退火。
2.正火
将钢件加热到Ac3以上30~50度,保温后以稍大于退火的冷却速度冷却。
目的:1.降低硬度,提高塑性,改善切削加工与压力加工性能
2.细化晶粒,改善力学性能,为下一步工序做准备
3.消除冷、热加工所产生的内应力。
应用要点:正火通常作为锻件、焊接件以及渗碳零件的预先热处理工序。
对于性能要求不高的低碳的和中碳的碳素结构钢及低合金钢件,也可作为最后热处理。
对于一般中、高合金钢,空冷可导致完全或局部淬火,因此不能作为最后热处理工序。
3.淬火
将钢件加热到相变温度Ac3或Ac1以上,保温一段时间,然后在水、硝盐、油、或空气中快速冷却。
目的:淬火一般是为了得到高硬度的马氏体组织,有时对某些高合金钢(如不锈钢、耐磨钢)淬火时,则是为了得到单一均匀的奥氏体组织,以提高耐磨性和耐蚀性。
应用要点:1.一般用于含碳量大于百分之零点三的碳钢和合金钢;2.淬火能充分发挥钢的强度和耐磨性潜力,但同时会造成很大的内应力,降低钢的塑性和冲击韧度,故要进行回
火以得到较好的综合力学性能。
4.回火
将淬火后的钢件重新加热到Ac1以下某一温度,经保温后,于空气或油、热水、水中冷却。
目的:1.降低或消除淬火后的内应力,减少工件的变形和开裂;2.调整硬度,提高塑性和
韧性,获得工作所要求的力学性能;3.稳定工件尺寸。
应用要点:1.保持钢在淬火后的高硬度和耐磨性时用低温回火;在保持一定韧度的条件下
提高钢的弹性和屈服强度时用中温回火;以保持高的冲击韧度和塑性为主,又有足够的强
度时用高温回火;2.一般钢尽量避免在230~280度、不锈钢在400~450度之间回火,因为这时会产生一次回火脆性。
5.调质
淬火后高温回火称调质,即将钢件加热到比淬火时高10~20度的温度,保温后进行淬火,然后在400~720度的温度下进行回火。
目的:1.改善切削加工性能,提高加工表面光洁程度;2.减小淬火时的变形和开裂;3.获得良好的综合力学性能。
应用要点:1.适用于淬透性较高的合金结构钢、合金工具钢和高速钢;2. 不仅可以作为各种较为重要结构的最后热处理,而且还可以作为某些紧密零件,如丝杠等的预先热处理,
以减小变形。
6.时效
将钢件加热到80~200度,保温5~20小时或更长时间,然后随炉取出在空气中冷却。
目的:1. 稳定钢件淬火后的组织,减小存放或使用期间的变形;2.减轻淬火以及磨削加工
后的内应力,稳定形状和尺寸。
应用要点:1. 适用于经淬火后的各钢种;2.常用于要求形状不再发生变化的紧密工件,如
紧密丝杠、测量工具、床身机箱等。
7.冷处理
将淬火后的钢件,在低温介质(如干冰、液氮)中冷却到-60~-80度或更低,温度均匀一致后取出均温到室温。
目的:1.使淬火钢件内的残余奥氏体全部或大部转换为马氏体,从而提高钢件的硬度、强度、耐磨性和疲劳极限;2.稳定钢的组织,以稳定钢件的形状和尺寸。
应用要点:1.钢件淬火后应立即进行冷处理,然后再经低温回火,以消除低温冷却时的内应力;2.冷处理主要适用于合金钢制的紧密刀具、量具和紧密零件。
8.火焰加热表面淬火
用氧-乙炔混合气体燃烧的火焰,喷射到钢件表面上,快速加热,当达到淬火温度后立即喷水冷却。
目的:提高钢件表面硬度、耐磨性及疲劳强度,心部仍保持韧性状态。
应用要点:1.多用于中碳钢制件,一般淬透层深度为2~6mm;2.适用于单件或小批量生产的大型工件和需要局部淬火的工件。
9.感应加热表面淬火
将钢件放入感应器中,使钢件表层产生感应电流,在极短的时间内加热到淬火温度,然后喷水冷却。
目的:提高钢件表面硬度、耐磨性及疲劳强度,心部保持韧性状态。
应用要点:1.多用于中碳钢和中堂合金结构钢制件;2.由于肌肤效应,高频感应淬火淬透层一般为1~2mm,中频淬火一般为3~5mm,高频淬火一般大于10mm.
10.渗碳
将钢件放入渗碳介质中,加热至900~950度并保温,使钢件便面获得一定浓度和深度的渗碳层。
目的:提高钢件表面硬度、耐磨性及疲劳强度,心部仍然保持韧性状态。
应用要点:1.用于含碳量为0.15%~0.25%的低碳钢和低合金钢制件,一般渗碳层深度为0.5~2.5mm;2.渗碳后必须进行淬火,使表面得到马氏体,才能实现渗碳的目
的。