金属腐蚀研究报告方法
金属腐蚀实验方法

金属腐蚀实验方法金属腐蚀是指金属在与周围环境接触时,由于化学反应而逐渐受到破坏的过程。
为了研究金属腐蚀的机理以及寻找有效的防腐措施,科学家们进行了大量的金属腐蚀实验。
下面将介绍几种常见的金属腐蚀实验方法。
1.大气腐蚀实验:大气中的氧气、水蒸气和气体等对金属具有一定程度的腐蚀作用。
通过将金属样品置于模拟大气环境中,观察金属表面的变化,可以评估金属腐蚀的速度和方式。
实验可以在实验室内进行,使用加速腐蚀试验装置模拟多种大气环境条件。
2.氧化腐蚀实验:金属的氧化腐蚀是指金属与氧气反应生成金属氧化物的过程。
常用的方法是将金属样品置于模拟氧化环境中,如水蒸气或热空气中,观察金属表面的颜色变化、表面形貌变化等。
也可以使用电化学方法测量氧化膜的阻抗、厚度等参数。
3.电化学腐蚀实验:电化学腐蚀实验是通过在电解质溶液中通过金属样品与参比电极之间施加不同的电位,研究金属在不同电位下的电流响应、电化学反应和腐蚀速度等。
常用的电化学腐蚀实验方法包括极化曲线、交流阻抗谱和电位动力学等。
4.加速腐蚀实验:为了研究腐蚀过程中的变化规律,科学家们通常采用加速腐蚀实验方法,通过人为增加腐蚀速率的方式,缩短实验时间。
常用的加速腐蚀实验方法包括盐雾腐蚀实验、酸腐蚀实验、碱腐蚀实验等。
5.微观腐蚀实验:微观腐蚀实验主要通过电子显微镜和原子力显微镜等技术,观察金属表面的微观形貌和成分变化。
这些实验方法可以研究腐蚀产物的形成规律、腐蚀与材料微观结构的关系等。
总之,金属腐蚀实验方法多种多样,可以从不同角度对腐蚀过程进行研究。
这些实验方法不仅有助于了解金属腐蚀的机理,还可以为防腐材料的研发和应用提供参考。
金属的腐蚀实验

金属的腐蚀实验金属的腐蚀实验是一种常见的科学实验,旨在研究金属在特定条件下受到腐蚀的情况,以便分析金属材料的性能及其在特定环境中的适用性。
本文将介绍金属腐蚀实验的背景、实验方法、结果分析和实验应用,以及对腐蚀防护的探讨。
一、背景腐蚀是指金属在特定环境中与外界介质的相互作用下产生的化学或电化学反应。
腐蚀会导致金属材料的破坏和性能下降,影响工业设备的正常运行和寿命。
了解金属腐蚀现象对于材料科学和工程实践至关重要。
二、实验方法1. 实验材料本次实验选择了钢铁、铝、铜和镀锌板作为研究对象。
这些金属在现实应用中被广泛使用,对其腐蚀性能的研究具有实际意义。
2. 实验装置采用恒温水槽,确保实验条件的一致性。
在水槽内设置腐蚀试样的支架,以保持试样的稳定和相对位置的一致。
3. 实验步骤(1) 准备试样:将金属试样进行充分抛光和清洗,确保试样表面干净光滑。
(2) 安装试样:将试样固定在试样支架上,并将其放入恒温水槽中。
(3) 添加介质:向恒温水槽中加入腐蚀介质,如盐水或酸溶液,保证介质的浓度和温度的一致性。
(4) 实验观测:在规定的时间段内,记录试样的质量变化和表面形态变化。
三、结果分析通过一定时间的实验观测,得出如下结果:1. 不同金属材料的腐蚀程度不同。
在相同的实验条件下,铝和铜的腐蚀程度明显低于钢和镀锌板。
2. 相同金属材料在不同腐蚀介质中也会有差异。
在盐水中,腐蚀程度较大,而在酸溶液中,腐蚀程度较小。
3. 腐蚀程度随时间的推移而加剧。
初始阶段腐蚀缓慢,随着时间的推移,腐蚀速度逐渐增加。
四、实验应用金属腐蚀实验的结果可以为材料科学、工程设计和工业制造提供参考:1. 材料科学:通过研究金属腐蚀现象,科学家可以深入了解金属材料的特性和行为,为新材料的研发提供依据。
2. 工程设计:在设计工程结构时,需要考虑金属材料的腐蚀问题。
金属腐蚀实验可以帮助工程师选择适合特定环境的材料,并优化设计方案。
3. 工业制造:在工业生产中,金属材料常受到潮湿、酸碱等环境的影响。
金属的腐蚀与防护实验报告
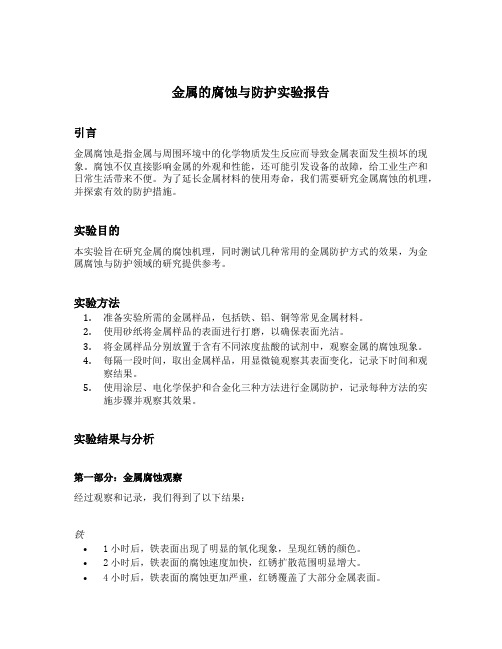
金属的腐蚀与防护实验报告引言金属腐蚀是指金属与周围环境中的化学物质发生反应而导致金属表面发生损坏的现象。
腐蚀不仅直接影响金属的外观和性能,还可能引发设备的故障,给工业生产和日常生活带来不便。
为了延长金属材料的使用寿命,我们需要研究金属腐蚀的机理,并探索有效的防护措施。
实验目的本实验旨在研究金属的腐蚀机理,同时测试几种常用的金属防护方式的效果,为金属腐蚀与防护领域的研究提供参考。
实验方法1.准备实验所需的金属样品,包括铁、铝、铜等常见金属材料。
2.使用砂纸将金属样品的表面进行打磨,以确保表面光洁。
3.将金属样品分别放置于含有不同浓度盐酸的试剂中,观察金属的腐蚀现象。
4.每隔一段时间,取出金属样品,用显微镜观察其表面变化,记录下时间和观察结果。
5.使用涂层、电化学保护和合金化三种方法进行金属防护,记录每种方法的实施步骤并观察其效果。
实验结果与分析第一部分:金属腐蚀观察经过观察和记录,我们得到了以下结果:铁•1小时后,铁表面出现了明显的氧化现象,呈现红锈的颜色。
•2小时后,铁表面的腐蚀速度加快,红锈扩散范围明显增大。
•4小时后,铁表面的腐蚀更加严重,红锈覆盖了大部分金属表面。
铝•在盐酸溶液中,铝表面发生了化学反应,产生了大量气泡。
•经过1小时的观察,铝表面的气泡逐渐减少,但仍有气泡产生。
•经过2小时的观察,铝表面的气泡完全消失,金属表面变得光滑。
铜•铜在盐酸中的腐蚀速度较慢,经过4小时的观察,铜表面仅有少量的氧化现象。
•铜的腐蚀速度与盐酸浓度相关,浓度越高,腐蚀速度越快。
第二部分:金属防护方案测试涂层1.清洁金属表面,确保无杂质。
2.使用喷涂或刷涂等方式将防腐涂层均匀地涂抹在金属表面。
3.经过一段时间的观察,发现涂层能够有效阻隔外界环境对金属的腐蚀作用。
电化学保护1.在金属样品上加入电解质溶液,并连接一个外部电源。
2.电流经过金属样品时,形成一个保护性的氧化物膜,防止氧气和水分进一步腐蚀金属。
3.经过实验证明,电化学保护能够显著减缓金属的腐蚀速度。
腐蚀调研报告

腐蚀调研报告腐蚀调研报告一、研究背景腐蚀是指金属或其他材料在一定条件下与周围环境发生化学或电化学反应而导致表面破坏的现象。
腐蚀不仅会导致材料性能下降,甚至会引发事故,造成巨大的经济损失和人员伤亡。
因此,对于腐蚀问题的调研具有重要的意义。
二、调研目的本次调研的目的是了解腐蚀的相关情况,包括腐蚀的分类、腐蚀的成因、腐蚀的预防和保护等方面的情况,以便更好地预防和控制腐蚀现象的发生。
三、调研方法本次调研采用文献调研和实地调查相结合的方法进行。
四、调研结果1.腐蚀的分类根据腐蚀的机理和作用方式,可以将腐蚀分为化学腐蚀和电化学腐蚀两大类。
化学腐蚀指的是材料与化学物质直接发生反应导致腐蚀,例如金属在强酸或强碱环境中的腐蚀。
电化学腐蚀指的是材料在电解质溶液中发生电化学反应导致腐蚀,例如金属在潮湿的环境中发生氧化还原反应导致腐蚀。
2.腐蚀的成因腐蚀的发生与多种因素有关,包括环境因素和材料因素。
环境因素包括温度、湿度、酸碱度、氧气含量等影响腐蚀的因素;材料因素包括材料的化学成分、晶体结构、氧化膜、应力等影响腐蚀的因素。
3.腐蚀的预防和保护为了预防和控制腐蚀的发生,可以采取以下措施:选择适当的材料,例如具有良好耐蚀性的材料;改变环境条件,例如控制温度、湿度和酸碱度等;采用防腐蚀涂层,例如涂覆保护性涂层或电镀等;电化学保护,例如通过外加电位使金属产生保护性的电位。
五、结论腐蚀是一个严重影响材料性能和安全的问题,对于腐蚀问题的预防和控制具有重要意义。
通过调研发现,腐蚀的分类多样,成因复杂,但可以通过选择适当材料、改变环境条件、采用防腐蚀涂层等方式进行预防和控制。
然而,腐蚀问题仍然存在挑战,需要进一步研究和探索。
金属腐蚀调查报告
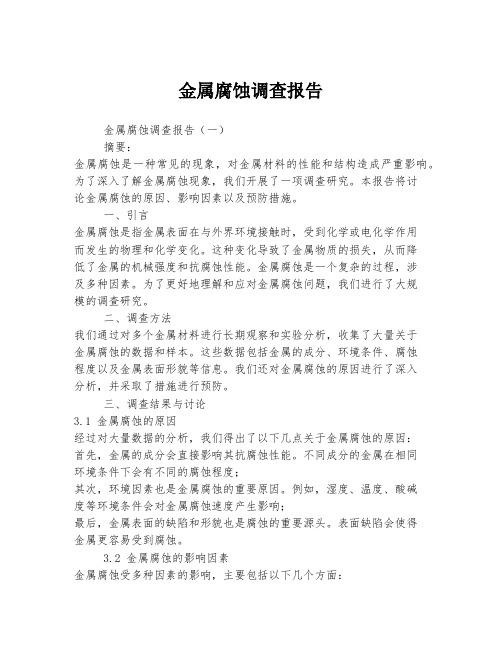
金属腐蚀调查报告金属腐蚀调查报告(一)摘要:金属腐蚀是一种常见的现象,对金属材料的性能和结构造成严重影响。
为了深入了解金属腐蚀现象,我们开展了一项调查研究。
本报告将讨论金属腐蚀的原因、影响因素以及预防措施。
一、引言金属腐蚀是指金属表面在与外界环境接触时,受到化学或电化学作用而发生的物理和化学变化。
这种变化导致了金属物质的损失,从而降低了金属的机械强度和抗腐蚀性能。
金属腐蚀是一个复杂的过程,涉及多种因素。
为了更好地理解和应对金属腐蚀问题,我们进行了大规模的调查研究。
二、调查方法我们通过对多个金属材料进行长期观察和实验分析,收集了大量关于金属腐蚀的数据和样本。
这些数据包括金属的成分、环境条件、腐蚀程度以及金属表面形貌等信息。
我们还对金属腐蚀的原因进行了深入分析,并采取了措施进行预防。
三、调查结果与讨论3.1 金属腐蚀的原因经过对大量数据的分析,我们得出了以下几点关于金属腐蚀的原因:首先,金属的成分会直接影响其抗腐蚀性能。
不同成分的金属在相同环境条件下会有不同的腐蚀程度;其次,环境因素也是金属腐蚀的重要原因。
例如,湿度、温度、酸碱度等环境条件会对金属腐蚀速度产生影响;最后,金属表面的缺陷和形貌也是腐蚀的重要源头。
表面缺陷会使得金属更容易受到腐蚀。
3.2 金属腐蚀的影响因素金属腐蚀受多种因素的影响,主要包括以下几个方面:首先,金属材料的使用条件会影响其腐蚀程度。
例如,在潮湿的环境中,金属腐蚀速度更快;其次,金属材料的成分和微观结构也会对腐蚀产生影响。
不同成分的金属腐蚀程度不同,而细粒度的金属更容易发生腐蚀;最后,金属的表面处理和保护措施也会对腐蚀产生影响。
例如,对金属表面进行涂层处理可以有效延缓腐蚀进程。
3.3 金属腐蚀的预防措施为了有效预防金属腐蚀,我们提出了以下几点建议:首先,根据具体情况选择合适的金属材料。
在具有较高腐蚀倾向的环境条件下,选择抗腐蚀性能好的金属;其次,加强对使用环境的控制。
例如,保持适当的湿度和温度,避免暴露在强酸、强碱等腐蚀性环境中;最后,加强金属材料的表面处理和保护措施。
腐蚀调研报告

腐蚀调研报告
《腐蚀调研报告》
在工业生产中,腐蚀是一个普遍存在的问题,对于各种金属材料和设备都可能会造成严重的损坏。
因此,本次调研旨在了解腐蚀现象的发生原因、对策和预防措施。
首先,我们对腐蚀现象进行了详细的描述和分析。
腐蚀是一种表面改变,通常由化学反应引起。
在工业生产中,常见的腐蚀类型包括金属腐蚀、水腐蚀、化学腐蚀等。
我们通过实地调研和实验,详细了解了各种腐蚀现象的特点和影响。
其次,我们对腐蚀的原因进行了深入研究。
经过调研发现,腐蚀的原因多种多样,包括环境因素、化学因素、温度因素等。
了解腐蚀的原因有助于我们更好地制定预防措施和应对策略。
最后,我们对腐蚀的预防措施进行了总结和归纳。
我们认为,要防止腐蚀的发生,首先要在材料选择和生产工艺上下功夫。
其次,定期维护和保养也是非常重要的。
此外,采用防腐蚀涂料和添加腐蚀抑制剂也是有效的预防措施。
通过本次调研,我们对腐蚀现象有了更深入的了解,也积累了丰富的应对经验。
希望通过我们的工作,能够对腐蚀问题的解决起到一定的指导作用。
腐蚀极化实验报告
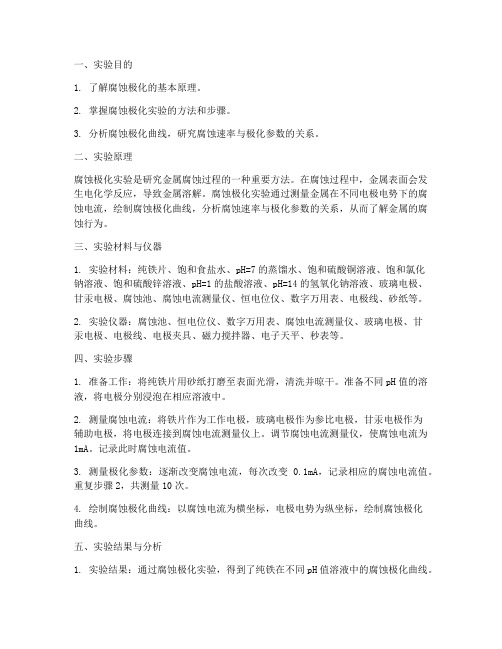
一、实验目的1. 了解腐蚀极化的基本原理。
2. 掌握腐蚀极化实验的方法和步骤。
3. 分析腐蚀极化曲线,研究腐蚀速率与极化参数的关系。
二、实验原理腐蚀极化实验是研究金属腐蚀过程的一种重要方法。
在腐蚀过程中,金属表面会发生电化学反应,导致金属溶解。
腐蚀极化实验通过测量金属在不同电极电势下的腐蚀电流,绘制腐蚀极化曲线,分析腐蚀速率与极化参数的关系,从而了解金属的腐蚀行为。
三、实验材料与仪器1. 实验材料:纯铁片、饱和食盐水、pH=7的蒸馏水、饱和硫酸铜溶液、饱和氯化钠溶液、饱和硫酸锌溶液、pH=1的盐酸溶液、pH=14的氢氧化钠溶液、玻璃电极、甘汞电极、腐蚀池、腐蚀电流测量仪、恒电位仪、数字万用表、电极线、砂纸等。
2. 实验仪器:腐蚀池、恒电位仪、数字万用表、腐蚀电流测量仪、玻璃电极、甘汞电极、电极线、电极夹具、磁力搅拌器、电子天平、秒表等。
四、实验步骤1. 准备工作:将纯铁片用砂纸打磨至表面光滑,清洗并晾干。
准备不同pH值的溶液,将电极分别浸泡在相应溶液中。
2. 测量腐蚀电流:将铁片作为工作电极,玻璃电极作为参比电极,甘汞电极作为辅助电极,将电极连接到腐蚀电流测量仪上。
调节腐蚀电流测量仪,使腐蚀电流为1mA。
记录此时腐蚀电流值。
3. 测量极化参数:逐渐改变腐蚀电流,每次改变0.1mA,记录相应的腐蚀电流值。
重复步骤2,共测量10次。
4. 绘制腐蚀极化曲线:以腐蚀电流为横坐标,电极电势为纵坐标,绘制腐蚀极化曲线。
五、实验结果与分析1. 实验结果:通过腐蚀极化实验,得到了纯铁在不同pH值溶液中的腐蚀极化曲线。
2. 结果分析:(1)腐蚀速率与电极电势的关系:在腐蚀极化曲线上,腐蚀电流随电极电势的增大而减小,说明腐蚀速率与电极电势呈负相关。
(2)腐蚀速率与pH值的关系:在pH=7的溶液中,腐蚀速率最小;在pH=1和pH=14的溶液中,腐蚀速率较大。
这表明金属在弱酸性或弱碱性溶液中腐蚀速率较小,而在强酸性或强碱性溶液中腐蚀速率较大。
金属腐蚀和防护的实验报告
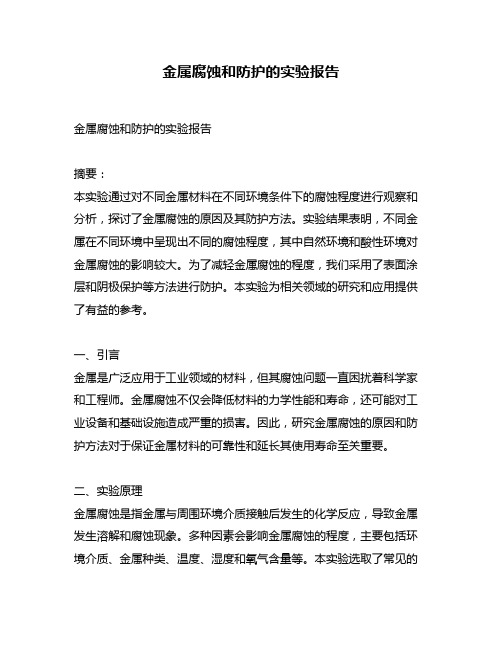
金属腐蚀和防护的实验报告金属腐蚀和防护的实验报告摘要:本实验通过对不同金属材料在不同环境条件下的腐蚀程度进行观察和分析,探讨了金属腐蚀的原因及其防护方法。
实验结果表明,不同金属在不同环境中呈现出不同的腐蚀程度,其中自然环境和酸性环境对金属腐蚀的影响较大。
为了减轻金属腐蚀的程度,我们采用了表面涂层和阴极保护等方法进行防护。
本实验为相关领域的研究和应用提供了有益的参考。
一、引言金属是广泛应用于工业领域的材料,但其腐蚀问题一直困扰着科学家和工程师。
金属腐蚀不仅会降低材料的力学性能和寿命,还可能对工业设备和基础设施造成严重的损害。
因此,研究金属腐蚀的原因和防护方法对于保证金属材料的可靠性和延长其使用寿命至关重要。
二、实验原理金属腐蚀是指金属与周围环境介质接触后发生的化学反应,导致金属发生溶解和腐蚀现象。
多种因素会影响金属腐蚀的程度,主要包括环境介质、金属种类、温度、湿度和氧气含量等。
本实验选取了常见的钢铁、铝和铜等金属材料,将其置于自然环境和酸性环境中,观察并比较其腐蚀程度。
三、实验步骤1. 准备金属试样:分别选取同一尺寸和形状的钢铁、铝和铜试样,保证其表面光洁。
2. 自然环境观察:将金属试样暴露在自然环境中,每隔一段时间观察试样表面的变化,并记录下来。
3. 酸性环境观察:将金属试样置于酸性溶液中,每隔一段时间观察试样表面的变化,并记录下来。
4. 分析实验结果:根据观察记录,比较不同金属试样在不同环境中的腐蚀程度,并进行结果分析。
四、实验结果与分析根据实验观察,在自然环境中,铁表面出现了明显的锈斑,而铝和铜表面没有明显腐蚀现象。
这是由于铁在湿氧气环境下容易氧化生成铁锈,而铝和铜具有更好的抗氧化性能。
在酸性环境中,铁和铝表面均出现了腐蚀现象,与自然环境下相比,腐蚀速度更快。
铜的腐蚀程度较轻,表面仅有些微变化。
这是由于酸性溶液中的氢离子和氧气能够加速金属的腐蚀反应。
为了减轻金属腐蚀的程度,我们可以采用表面涂层和阴极保护等方法进行防护。
- 1、下载文档前请自行甄别文档内容的完整性,平台不提供额外的编辑、内容补充、找答案等附加服务。
- 2、"仅部分预览"的文档,不可在线预览部分如存在完整性等问题,可反馈申请退款(可完整预览的文档不适用该条件!)。
- 3、如文档侵犯您的权益,请联系客服反馈,我们会尽快为您处理(人工客服工作时间:9:00-18:30)。
金属腐蚀研究方法院(系):材料科学与工程学院专业班级:金材1101班学生姓名:卢阳学号:9完成日期:2014年11月16日金属腐蚀研究方法——缝隙腐蚀的研究缝隙腐蚀是在电解质溶液(特别是含有卤族离子的介质)中,在金属与金属或金属与非金属表面之间狭窄的缝隙内,溶液的移动受到阻滞,当缝隙内溶液中的氧耗竭后,氯离子从缝隙外向缝隙内迁移,金属氯化物的水解酸化过程发生,导致钝化膜的破裂而产生与自催化点腐蚀相类似的局部腐蚀。
缝隙腐蚀现象非常普遍,对一些耐蚀金属材料的危害尤其明显[1]。
1、缝隙腐蚀的机理[2]缝隙腐蚀可分为初期阶段和后期阶段。
在初期阶段,发生金属的溶解和阴极的氧还原为氢氧离子的反应:阳极:M→M++e 阴极:O2+2H2O+4e→4OH-阳极阴极此时金属和溶液之间电荷是守恒的,金属溶解产生的电子立即被氧还原消耗掉。
在经过一段时间后,缝内的氧消耗完后,氧的还原反应不再进行。
这时缝内缺氧,缝外富氧,形成了氧浓差电池,金属M在缝内继续溶解,缝内溶液中M+过剩,为了保持电荷平衡,缝隙外部迁移性大的阴离子(如氯离子)迁移到缝内,同时阴极过程转到缝外。
缝内已形成金属的盐类(包括氯化物和硫酸盐)发生水解:M+CI+H2O→MOH↓+H+CI-结果使缝内pH值下降,可达2至3,这就促使缝内金属溶解速度增加,相应缝外邻近表面的阴极过程,即氧的还原速度也增加,使外部表面得到阴极保护,而加速了缝内金属的腐蚀。
而Myer等人认为,至少还有氢离子、中性盐和缓蚀剂的浓差电池存在于缝隙腐蚀过程中,Brown以水解后局部酸化引起局部腐蚀的依据,提出了闭塞腐蚀电池(occluded corrosion cell)的概念。
另外,Fontana和Rosefeld等人,指出了蚀孔或缝隙闭塞电池的自催化理论。
缝内外溶液的对流和扩散受阻,导致闭塞区贫氧,缝隙外仍然富氧,造成的氧浓差电池使缝隙内金属的电位低于缝隙外金属的电位,pH值的降低以及H+和Cl-的作用(HCl)使金属处于活化状态,促进闭塞区内金属的溶解,形成二次腐蚀产物Fe(OH)3在缝口,造成正电荷过剩,Cl-迁入。
而氯化物在水中发生水解,使缝隙内介质(H+离浓度增加)酸化,pH值下降,因此,加速了阳极的溶解。
阳极的加速溶解,又引起更多的Cl-离子迁入,氯化物浓度又增加,氯化物的水解又使介质进一步酸化,如此反复循环,形成了一个闭塞电池内的自催化效应。
2、缝隙腐蚀试验方法在相对闭塞的狭小缝隙中存留的溶液容量甚微,因此必须设计一些特殊的研究方法才能有效地研究缝隙腐蚀行为。
迄今为止采用的研究方法可归纳为三类,真实缝隙中的测量、数学模拟法、模拟缝隙测量。
真实缝隙中的测量又分为原位测量法和取样分析法,可是无论是原位测量还是取样分析都会因缝隙狭小,测量和取样困难而影响实验精度。
数学模拟法目前模型尚未统一。
模拟缝隙测量的方法采用较多,有的已形成国家标准,主要分为浸泡试验和电化学试验两大类。
浸泡试验法中有三氧化铁试验(GB/T 10127-2002.),多缝隙试样试验,临界缝隙腐蚀温度试验,活性炭加速试验等。
电化学测试法(GB/T 13671-1992.)中有临界(再钝化)电位测试法,去钝化pH 值比较法,稳态pH 值与去钝化pH 值比较法等。
3、22Cr 双相不锈钢缝隙腐蚀[3]国内外对22Cr 双相不锈钢缝隙腐蚀的研究结果表明,其缝隙腐蚀性能优于18 -5Mo 型双相不锈钢,与316L 奥氏体不锈钢相当,但低于25Cr 型同样含钼量的双相不锈钢,在流动的海水中有轻微的缝隙腐蚀。
3.1试验材料试验所用材料为00Cr22Ni5Mo3N 双相不锈钢,其化学成分见表3-1。
表3-1 00Cr22Ni5Mo3N 双相不锈钢化学成分 (wt%) 成分 C Mn Si Cr Ni Mo N S P 含量0.0211.520.3721.475.553.040.130.0030.00143.2化学浸泡法①三氯化铁实验试验方法试验依据GB/T 10127-2002[4]不锈钢三氯化铁缝隙腐蚀试验方法进行。
将试样加工成50 mm ×25 mm ×3 mm 的薄片,试样的6个表面依次用180#、240#、400#、600#和800#金相砂纸逐级打磨,然后测量尺寸、计算总表面积、用无水乙醇洗净、干燥,称重(精确到0. 001 g)后置于干燥器中备用。
试验溶液是将100 g 分析纯三氯化铁( FeCl 3 ▪6H 2O ) 溶解在用优级纯盐酸和蒸馏水或去离子水配制成的900mL 、0. 05mo l/ L 的盐酸水溶液中。
试验温度分别为22℃±1℃、35℃±1℃、50℃±1℃和75℃±1℃。
试样两侧用2个聚四氟乙烯圆柱夹紧,并用低硫( S ≤0. 02% ) 橡胶带十字形捆好; 12. 7 m m ×1 2. 7 mm 的聚四氟乙烯圆柱顶部加工有宽、深均为1. 6 mm 的垂直槽,防止橡胶带滑动,如图3.2。
本试验共4组,每组试验取三片平行试样,每次试验使用新的试验溶液。
在烧瓶中注入配制好的试验溶液300 m L ,盖上玻璃塞后放入恒温槽装置中将试验溶液加热 到规定温度,之后,将试样水平放在溶液中的支架上,连续进行72h 的浸泡试验,试验1-聚四氟乙烯圆柱;2-试样;3-低硫橡胶带图3.2 FeCl 3溶液缝隙腐蚀试验装置示过程中试验容器要密,以防溶液蒸发。
试验结束后,取出试样在流水中用尼龙刷清除试样上的腐蚀产物,用无水乙醇洗净、干燥并在干燥器中放置数小时后称重[3]。
②试验结果分析图3.3为平均腐蚀速率与试验温度的关系。
从图中可以看出,随着温度的升高,22Cr 双相不锈钢的缝隙腐蚀程度越来越严重,尤其是温度大于35 ℃时,其腐蚀速率急剧上升。
3.3电化学方法 ①试验方法试验依据GB/ T 13671-1992不锈钢缝隙腐蚀电化学试验方法进行。
图3.4所示为由绝缘树脂、塑料管和Φ 10mm ×3 mm 双相不锈钢片镶嵌制成的试样,其中1 cm 2 的试验表面裸露。
试验时将试验表面用砂纸逐级打磨至800 #,然后冲洗, 丙酮除油、干燥。
图3.5为用规定的有机玻璃夹具将1 cm 2的试样表面与尼龙网构成人工缝隙的装配图。
电化学测试由EG& 公司的M237A 恒电位仪和M 5210锁相放大器完成。
电解池采用EG& G 公司的1L 容积的玻璃电解池,辅助电极采用大面积石墨惰性电极,参比电极采用饱和甘汞电极。
扫描速率为1mV / s 。
试验溶液为3.5% NaCl, 试验温度分别为 30℃±1℃,40℃±1℃, 60℃±1℃,80℃±1℃。
电化学阻抗测试的频率范围为10 mHz~ 100 kHz ,阻抗测量信号采用幅值为5mV 的正弦波。
试验介质为3.5% NaCl 溶液,试验温度分别为30℃、40℃、60℃和80 ℃。
②试验结果分析试验结束后,测得22Cr 双相不锈钢在30℃、40℃、60℃和80 ℃的缝隙腐蚀极化曲线如图3.6所示。
从图3.6可以观察到,22Cr 双相不锈钢的自腐蚀电位随着温度的升图3.3 平均腐蚀速率与试验温度关系1-试样;2-绝缘树脂;3-塑料管;4-导线图3.4 镶嵌式样1-有机玻璃夹;2-玻璃珠;3-聚四氟乙烯垫片;4-镶嵌的试样图3.5 人工缝隙装置高向负方向移动,表明自腐蚀倾向增大;并且钝化区宽度变窄,塔菲尔斜率减小,表明电极的极化率随温度升高而变小,电极反应过程阻力变小,腐蚀速率增大。
缝隙腐蚀发生后,缝隙内作为阳极区,阴极反应由氧去极化逐渐转化为H+去极化,缝隙内pH值降低,缝隙内金属腐蚀阳极反应加剧,腐蚀电位也逐渐负移[5]。
电化学测量结果如表3-3。
表3-3 电化学测量结果温度/℃自腐蚀电位/mV30 -13640 -17260 -26680 -264图3.6 不同温度下的极化曲线试验条件下,22Cr双相不锈钢的缝隙腐蚀程度随介质温度的升高而急剧上升,同时发现有点腐蚀痕迹。
同时,其自腐蚀电位随温度的升高向负方向移动,自腐蚀倾向增大。
4、Q235钢的缝隙腐蚀采用动电位扫描法研究了碱性条件下氯离子浓度对Q235钢缝隙腐蚀行为的影响。
氯离子对缝隙腐蚀有极强的促进作用,氯离子浓度的增加会导致缝隙腐蚀电位的显著下降,从而大幅度降低了碳钢的抗缝[6]。
4.1试验材料试验材料为Q235钢,试样采用截面为1cm2的Q235钢,焊接铜丝作为导线,用环氧树脂固封焊接处。
每次试验前,将试样用180#到800#的砂纸按顺序进行打磨,试验面磨光后,用去离子水冲洗,再用无水乙醇丙酮脱脂,最后用吹风机吹干。
表4-1 Q235钢的化学成分(wt%)成分 C Si Mn P S含量0.214 0.195 0.644 0.0264 0.02364.2试验方法[6]试验溶液为碱性条件下的NaNO2+NaCI和Na3PO4低+H3PO4+NaCI溶液体系。
在NaNO2+NaCI溶液体系中:通过改变Cl-浓度,配制了0.1mol/L NaNO2+Xmol/L NaCI 的系列溶液,研究Cl-对碳钢缝隙腐蚀的影响。
溶液用去离子水配制,所用试剂均为分析纯。
通过缝隙腐蚀电位来描述材料的缝隙腐蚀敏感性。
缝隙腐蚀电位是指在阳极极化过程中,由于缝隙腐蚀的发生而使电流密度急剧上升时对应的电位。
采用三电极体系,工作电极为试样,参比电极采用饱和甘汞电极(CSE),辅助电极选用铂电极。
为了满足试验要求,使用如图4-2所示的缝隙腐蚀夹具。
缝隙夹具全部由聚四氟乙烯(PDFE)材料制成。
试样按图4-2装好后浸入溶液,采用恒温水槽控温。
温度控制在(30±l)℃范围,自腐蚀电位稳定后,以0.8mV/s的速度进行动电位扫描,从而获得阳极极化曲线。
缝隙腐蚀电位可直接在阳极极化曲线上读取。
缝隙的宽度对缝隙腐蚀有很大影响,所以要尽量保持每次试验中缝隙宽度的一致性。
腐蚀试样被固定在夹具上部的槽中,导线由上部穿出,四个聚四氟乙烯螺栓对称分布于四周,将腐蚀试样紧固于夹具中央,由此产生缝隙,如图4-2所示。
每次安装试样时,通过扭矩扳手调整螺栓以保证每次试验中安装力矩的一致,从而在腐蚀试样和聚四氟乙烯底板间就会产生宽度大致相同的缝隙。
4.3试验结果分析图4-3是Q235钢在不同Cl-浓度的亚硝酸钠溶液中的极化曲线,表4.3是Q235钢在不同Cl-浓度的亚硝酸钠溶液中的自腐蚀电位E corr和缝隙腐蚀电位E cc。
综合图4-3和表4.3可知,随着Cl-浓度的增加,溶液的自腐蚀电位呈下降趋势,从-348mV下降至-608mv,说明Cl-离子对钝化膜有较强的侵蚀性,尤其是在Cl-离子浓度大于0.02mol/L 后,自腐蚀电位下降至-591mV,表明此时Q235钢很难形成自钝化。