悬架的设计计算.doc
汽车悬架构件的设计计算

汽车悬架构件的设计计算前言第一章汽车悬架的基本知识第一节汽车悬架构件一、导向机构二、弹性元件三、梯形机构四、阻尼元件五、稳定装置第二节汽车悬架型式一、悬架的基本要求二、悬架的分类(一)按功能原理划分(二)按导向机构划分(三)按弹性元件划分第三节汽车悬架型式的发展一、导向机构悬架型式的发展(一)单臂悬架的发展(二)从单臂到双臂(三)麦弗逊悬架(四)平衡悬架二、弹性元件悬架型式的发展(一)钢板弹簧悬架(二)螺旋弹簧悬架(三)扭杆弹簧悬架(四)空气弹簧悬架(五)油气弹簧悬架第二章汽车悬架的基础理论第一节汽车悬架术语和力矩中心一、特定术语二、力矩中心(一)定义(二)相关定理(三)悬架的侧倾力矩中心(四)悬架的纵倾力矩中心第二节多轴汽车的特性参数一、特性参数(一)外心距(二)组合线刚度(三)中性面(四)内心距(五)换算线刚度二、角刚度与角刚度比(一)角刚度(二)角刚度比第三节汽车平顺性的评价指标一、IS0263l标准二、常用评价指标第四节汽车操纵稳定性的评价指标一、定义及研究对象二、评价指标三、车身稳定性第三章汽车悬架构件的设计计算第一节汽车导向机构一、车轮定位参数(一)轮距(二)车轮外倾角(三)前束二、麦弗逊悬架的导向机构(一)悬架中心和力矩中心(二)换算线刚度和角刚度(三)受力分析三、半拖臂悬架的导向机构(一)相关参数(二)线刚度与角刚度(三)设计要点四、双横臂悬架的导向机构(一)空间模型(二)运动学特性(三)弹性元件受力(四)换算线刚度与角刚度(五)摆臂临界角五、单纵臂悬架的导向机构六、钢板弹簧悬架的导向机构(一)对称板簧的运动特性(二)非对称板簧的运动特性(三)中心扩展法的作图步骤及其修正方法(四)两点偏转法的作图步骤及其修正方法第二节汽车弹性元件一、钢板弹簧(一)普通钢板弹簧(二)变断面钢板弹簧(三)渐变刚度钢板弹簧(四)非对称钢板弹簧二、螺旋弹簧(一)普通压缩螺旋弹簧(二)变参数压缩螺旋弹簧(三)变节距压缩螺旋弹簧(四)变圈径等节距压缩螺旋弹簧(五)等螺旋角圆锥压缩螺旋弹簧(六)变丝径等内径压缩螺旋弹簧三、扭杆弹簧(一)端部结构和相关参数(二)变形及刚度(三)扭杆直径的确定(四)容量与容量比(五)材料和应力四、空气弹簧(一)空气弹簧的特点(二)空气弹簧的类型(三)空气弹簧的刚度计算五、油气弹簧六、橡胶弹簧(一)橡胶弹簧的类型和弹性特性(二)橡胶弹簧的静刚度计算第三节汽车稳定装置一、稳定装置的设计规范二、稳定装置的设计计算三、结构及布置四、普通型杆体变形公式的推导第四节汽车梯形机构一、普通梯形机构(一)内外轮转角关系(二)转弯半径的计算(三)梯形机构的转向特性(四)转向机构附加牵动轮转向二、断开式梯形机构(一)机构的设计(二)内外轮转角关系(三)侧倾牵动车轮偏转角第五节汽车阻尼元件一、汽车阻尼元件的分类及发展(一)减振器的分类(二)减振器的发展二、汽车阻尼元件的选用设计(一)阻尼特性(二)阻尼比(三)阻尼系数(四)最大卸荷力(五)工作缸直径的确定(六)合理的布置位置附表附表l 变丝径等圈径等螺旋角压缩螺旋弹簧附表2 等丝径变节距等圈径压缩螺旋弹簧附表3 等丝径等节距圆锥压缩螺旋弹簧附表4 等丝径等螺旋角圆锥压缩螺旋弹簧附表5 变丝径等簧径变节距变螺角压缩螺旋弹簧附表6 变丝径等节距变圈径压缩螺旋弹簧附表7 变丝径等螺角圆锥压缩螺旋弹簧附表8 变丝径等螺旋角圆锥压缩螺旋弹簧附表9 变丝径变节距变螺角圆锥压缩螺旋弹簧附表10 变丝径等螺角中凹双圆锥压簧,变丝径变节距中凸变圈径压缩螺旋弹簧附表11 无簧圈叠压变丝径等螺角圆锥压缩螺旋弹簧附表12 变丝径等螺角上直下锥压缩螺旋弹簧附表13 变丝径等内径组合式压缩螺旋弹簧附表14 各种截面形状的扭杆弹簧的设计计算公式。
悬架系统计算报告样本

悬架系统计算报告项目名称:03月编号:版本号:V1.0修订记录目次1 概述 (1)1.1 计算目的 (1)1.2 悬架系统基本方案介绍 (1)1.3 悬架系统设计的输入条件 (2)2 悬架系统的计算 (3)2.1 弹簧刚度 (3)2.2 悬架偏频的计算 (3)2.2.1 前悬架刚度计算 (4)2.2.2 前悬架偏频计算 (4)2.2.3 后悬架刚度计算 (5)2.2.4 后悬架偏频计算 (6)2.3 悬架静挠度的计算 (6)2.4 侧倾角刚度计算 (7)2.4.1 前悬架的侧倾角刚度 (7)2.4.2 后悬架的侧倾角刚度.......... 错误! 未定义书签。
2.5 整车的侧倾角计算 (10)2.5.1 悬架质量离心力引起的侧倾力矩 (11)2.5.2 侧倾后, 悬架质量引起的侧倾力矩 (12)2.5.3 总的侧倾力矩 (12)2.5.4 悬架总的侧倾角刚度 (12)2.5.5 整车的侧倾角 (12)2.6 纵倾角刚度 (12)2.7 减振器参数 (13)2.7.1 减振器平均阻力系数的确定错误! 未定义书签。
2.7.2 压缩阻尼和拉伸阻尼系数匹配 (16)2.7.3 减震器匹配参数 (16)3 悬架系统的计算结果 (17)4 结论及分析 (18)参考文献 (18)1概述1.1 计算目的经过计算,求得反映MA02-ME10Q纯电动车悬架系统性能的基本特征,为零部件开发提供参考。
计算内容主要包括悬架刚度、悬架侧倾角刚度、刚度匹配、悬架偏频、静挠度和阻尼等。
1.2 悬架系统基本方案介绍MA02-ME10 0纯电动车前悬架采用麦弗逊式独立悬架带横向稳定杆结构,后悬架系统采用拖曳臂式非独立悬架结构。
前、后悬架系统的结构图如图1、图2:图1前悬架系统图2后悬架系统1.3 悬架系统设计的输入条件悬架系统设计输入参数如表1:表1悬架参数列表22.1 弹簧刚度根据KC试验数据分析,选定弹簧刚度:前悬架弹簧刚度为:C sf 20N/mm;后悬架弹簧刚度为:C sr 21.7N/mm;2.2 悬架偏频的计算悬架系统将车身与车轮弹性的连接起来,由此弹性元件与它所支承的质量组成的振动系统决定了车身的固有频率,这是影响汽车行驶平顺性的重要性能指标之一。
悬架偏频计算公式
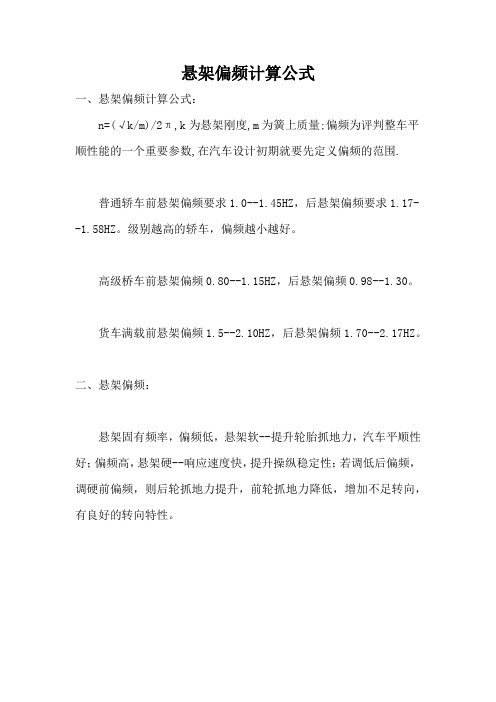
悬架偏频计算公式
一、悬架偏频计算公式:
n=(√k/m)/2π,k为悬架刚度,m为簧上质量;偏频为评判整车平顺性能的一个重要参数,在汽车设计初期就要先定义偏频的范围.
普通轿车前悬架偏频要求1.0--1.45HZ,后悬架偏频要求1.17--1.58HZ。
级别越高的轿车,偏频越小越好。
高级桥车前悬架偏频0.80--1.15HZ,后悬架偏频0.98--1.30。
货车满载前悬架偏频1.5--2.10HZ,后悬架偏频1.70--2.17HZ。
二、悬架偏频:
悬架固有频率,偏频低,悬架软--提升轮胎抓地力,汽车平顺性好;偏频高,悬架硬--响应速度快,提升操纵稳定性;若调低后偏频,调硬前偏频,则后轮抓地力提升,前轮抓地力降低,增加不足转向,有良好的转向特性。
悬架的参数计算公式
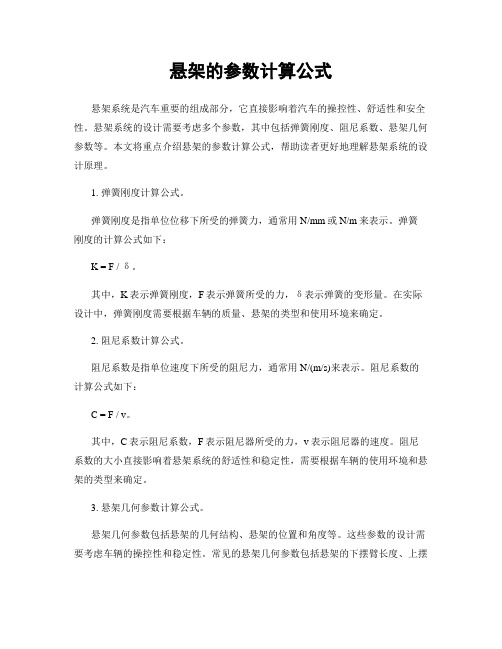
悬架的参数计算公式悬架系统是汽车重要的组成部分,它直接影响着汽车的操控性、舒适性和安全性。
悬架系统的设计需要考虑多个参数,其中包括弹簧刚度、阻尼系数、悬架几何参数等。
本文将重点介绍悬架的参数计算公式,帮助读者更好地理解悬架系统的设计原理。
1. 弹簧刚度计算公式。
弹簧刚度是指单位位移下所受的弹簧力,通常用N/mm或N/m来表示。
弹簧刚度的计算公式如下:K = F / δ。
其中,K表示弹簧刚度,F表示弹簧所受的力,δ表示弹簧的变形量。
在实际设计中,弹簧刚度需要根据车辆的质量、悬架的类型和使用环境来确定。
2. 阻尼系数计算公式。
阻尼系数是指单位速度下所受的阻尼力,通常用N/(m/s)来表示。
阻尼系数的计算公式如下:C = F / v。
其中,C表示阻尼系数,F表示阻尼器所受的力,v表示阻尼器的速度。
阻尼系数的大小直接影响着悬架系统的舒适性和稳定性,需要根据车辆的使用环境和悬架的类型来确定。
3. 悬架几何参数计算公式。
悬架几何参数包括悬架的几何结构、悬架的位置和角度等。
这些参数的设计需要考虑车辆的操控性和稳定性。
常见的悬架几何参数包括悬架的下摆臂长度、上摆臂长度、悬架的前后距离等。
这些参数的计算需要结合车辆的设计要求和悬架的类型来确定。
4. 悬架系统的动力学模型。
悬架系统的动力学模型包括悬架的质量、弹簧、阻尼器等参数,可以用来描述悬架系统的运动规律。
常见的悬架系统动力学模型包括单自由度模型、双自由度模型等。
这些模型可以用来分析悬架系统的振动特性和响应特性,对悬架系统的设计和优化具有重要的意义。
5. 悬架系统的优化设计。
悬架系统的优化设计需要考虑多个参数的综合影响,包括弹簧刚度、阻尼系数、悬架几何参数等。
优化设计的目标通常包括提高车辆的操控性、舒适性和安全性。
在实际设计中,可以利用计算机辅助设计软件来进行悬架系统的优化设计,通过多次模拟和分析来确定最佳的参数组合。
总结。
悬架系统的设计需要考虑多个参数,包括弹簧刚度、阻尼系数、悬架几何参数等。
悬架各工况受力计算公式表

悬架各工况受力计算公式表悬架各工况受力计算公式表是汽车设计师们必备的一份文档,因为悬架是汽车上最重要的零部件之一,它直接关系到汽车的运行性能和安全性。
本文将详细介绍悬架各工况受力的计算公式表,以帮助读者更好地理解。
首先,悬架是一个复杂的系统,由若干个部件组成,包括弹簧、减震器、传动轴、控制臂、节流阀等。
在实际工作过程中,悬架各部件都会承受不同的受力状态,如纵向加速、横向转向、制动、加速、刹车等。
而悬架各部件所承受的受力状态也是不同的,因此,针对不同的受力状态,悬架各部件的受力计算公式也是不同的。
以下是悬架各工况受力计算公式表:1. 纵向加速时,控制臂承受的力矩计算公式为:M = ma / FZ,其中m是汽车质量,a是车辆纵向加速度,FZ是轮胎垂直载荷。
2. 横向转向时,控制臂承受的力矩计算公式为:M = Fy * h,其中Fy是横向力,h是控制臂与地面垂直距离。
3. 制动时,制动力矩的计算公式为:M = W * (R - r) / 2,其中W是车辆重量,R是轮胎半径,r是制动器半径。
4. 加速时,驱动轴承受的力矩计算公式为:M = T /i * η * r,其中T是发动机输出扭矩,i是变速器传动比,η是传动效率,r是驱动轴半径。
5. 刹车时,制动器受到的压缩应力计算公式为:σ =F / A,其中F是制动力,A是制动器面积。
6. 路面颠簸时,减震器吸收的能量计算公式为:E = 1 / 2 * k * δ^2,其中k是减震器弹簧刚度,δ是减震器伸缩位移。
以上是悬架各工况受力计算公式表的部分内容,这些公式可以帮助汽车设计师了解悬架各部件在不同工况下所承受的受力情况,从而优化设计方案,提高汽车的性能和安全性。
总之,悬架各工况受力计算公式表是非常重要的一个文档,它涉及到汽车设计的方方面面,设计师们应该积极学习和掌握这些公式,以更好地提高汽车的性能和安全性。
悬架系统设计计算报告
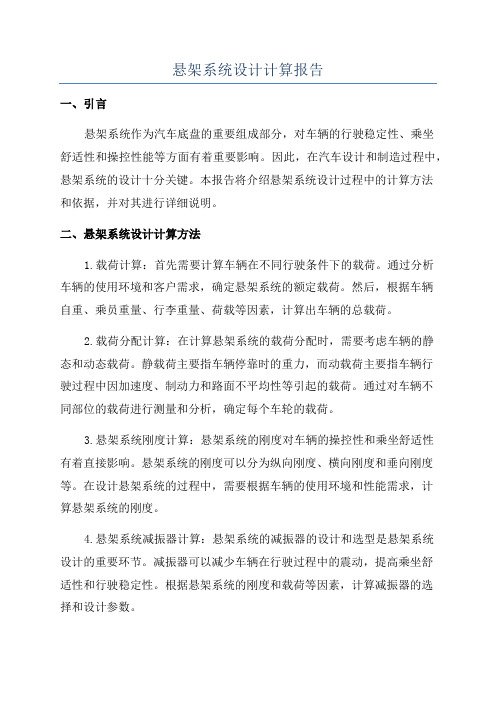
悬架系统设计计算报告一、引言悬架系统作为汽车底盘的重要组成部分,对车辆的行驶稳定性、乘坐舒适性和操控性能等方面有着重要影响。
因此,在汽车设计和制造过程中,悬架系统的设计十分关键。
本报告将介绍悬架系统设计过程中的计算方法和依据,并对其进行详细说明。
二、悬架系统设计计算方法1.载荷计算:首先需要计算车辆在不同行驶条件下的载荷。
通过分析车辆的使用环境和客户需求,确定悬架系统的额定载荷。
然后,根据车辆自重、乘员重量、行李重量、荷载等因素,计算出车辆的总载荷。
2.载荷分配计算:在计算悬架系统的载荷分配时,需要考虑车辆的静态和动态载荷。
静载荷主要指车辆停靠时的重力,而动载荷主要指车辆行驶过程中因加速度、制动力和路面不平均性等引起的载荷。
通过对车辆不同部位的载荷进行测量和分析,确定每个车轮的载荷。
3.悬架系统刚度计算:悬架系统的刚度对车辆的操控性和乘坐舒适性有着直接影响。
悬架系统的刚度可以分为纵向刚度、横向刚度和垂向刚度等。
在设计悬架系统的过程中,需要根据车辆的使用环境和性能需求,计算悬架系统的刚度。
4.悬架系统减振器计算:悬架系统的减振器的设计和选型是悬架系统设计的重要环节。
减振器可以减少车辆在行驶过程中的震动,提高乘坐舒适性和行驶稳定性。
根据悬架系统的刚度和载荷等因素,计算减振器的选择和设计参数。
5.悬架系统运动学计算:悬架系统的运动学计算是为了确定悬架系统在不同行驶状态下的主要参数,以便进行悬架系统的设计和调整。
通过对车辆的几何尺寸、运动学参数和悬架结构的分析和计算,确定悬架系统的工作范围和参数。
三、计算依据在悬架系统设计计算中,需要依据以下相关标准和原则进行设计:2.汽车悬架系统设计手册:根据汽车制造商提供的相关手册和技术资料,对悬架系统设计进行指导和计算。
3.数学和工程力学原理:在悬架系统设计计算过程中,需要运用数学和工程力学的相关原理和方法,如力学平衡、弹性力学、振动理论等,进行悬架系统的计算。
4.仿真和试验数据:通过对悬架系统的仿真分析和试验测试,获取悬架系统的相关参数和性能数据,为悬架系统的设计计算提供依据。
悬架系统计算报告..
修订记录目次1 概述 (1)1.1 计算目的 (1)1.2 悬架系统基本方案介绍 (1)1.3 悬架系统设计的输入条件 (1)2 悬架系统的计算 (2)2.1 弹簧刚度 (2)2.2 悬架偏频的计算 (2)2.2.1 前悬架刚度计算 (3)2.2.2 前悬架偏频计算 (4)2.2.3 后悬架刚度计算 (4)2.2.4 后悬架偏频计算 (5)2.3 悬架静挠度的计算 (5)2.4 侧倾角刚度计算 (6)2.4.1 前悬架的侧倾角刚度 (6)2.4.2 后悬架的侧倾角刚度 (8)2.5 整车的侧倾角计算 (9)2.5.1悬架质量离心力引起的侧倾力矩 (9)2.5.2侧倾后,悬架质量引起的侧倾力矩 (9)2.5.3总的侧倾力矩 (10)2.5.4悬架总的侧倾角刚度 (10)2.5.5整车的侧倾角 (10)2.6 纵倾角刚度 (10)2.7 减振器参数 (11)2.7.1 减振器平均阻力系数的确定 (11)2.7.2 压缩阻尼和拉伸阻尼系数匹配 (13)2.7.3 减震器匹配参数 (13)3 悬架系统的计算结果 (14)4 结论及分析 (15)参考文献 (15)1 概述1.1 计算目的通过计算,求得反映MA02-ME100纯电动车悬架系统性能的基本特征,为零部件开发提供参考。
计算内容主要包括悬架刚度、悬架侧倾角刚度、刚度匹配、悬架偏频、静挠度和阻尼等。
1.2 悬架系统基本方案介绍MA02-ME100纯电动车前悬架采用麦弗逊式独立悬架带横向稳定杆结构,后悬架系统采用拖曳臂式非独立悬架结构。
前、后悬架系统的结构图如图1、图2:图1 前悬架系统图2 后悬架系统1.3 悬架系统设计的输入条件悬架系统设计输入参数如表1:表1 悬架参数列表2 悬架系统的计算 2.1 弹簧刚度根据KC 试验数据分析,选定弹簧刚度: 前悬架弹簧刚度为: mm N C sf /20=; 后悬架弹簧刚度为: mm N C sr /7.21=; 2.2 悬架偏频的计算悬架系统将车身与车轮弹性的连接起来,由此弹性元件与它所支承的质量组成的振动系统决定了车身的固有频率,这是影响汽车行驶平顺性的重要性能指标之一。
悬架系统计算报告
修订记录目次1 概述 (1)1。
1 计算目的 (1)1。
2 悬架系统基本方案介绍 (1)1.3 悬架系统设计的输入条件 (1)2 悬架系统的计算 (2)2。
1 弹簧刚度 (2)2。
2 悬架偏频的计算 (2)2。
2。
1 前悬架刚度计算 (3)2.2.2 前悬架偏频计算 (4)2。
2。
3 后悬架刚度计算 (4)2。
2。
4 后悬架偏频计算 (5)2.3 悬架静挠度的计算 (5)2.4 侧倾角刚度计算 (6)2.4。
1 前悬架的侧倾角刚度 (6)2.4.2 后悬架的侧倾角刚度 (8)2.5 整车的侧倾角计算 (9)2.5.1悬架质量离心力引起的侧倾力矩 (9)2.5.2侧倾后,悬架质量引起的侧倾力矩 (9)2。
5.3总的侧倾力矩 (10)2。
5.4悬架总的侧倾角刚度 (10)2。
5.5整车的侧倾角 (10)2.6 纵倾角刚度 (10)2.7 减振器参数 (11)2.7。
1 减振器平均阻力系数的确定 (11)2.7。
2 压缩阻尼和拉伸阻尼系数匹配 (13)2。
7.3 减震器匹配参数 (13)3 悬架系统的计算结果 (14)4 结论及分析 (15)参考文献 (15)1 概述1。
1 计算目的通过计算,求得反映MA02—ME100纯电动车悬架系统性能的基本特征,为零部件开发提供参考。
计算内容主要包括悬架刚度、悬架侧倾角刚度、刚度匹配、悬架偏频、静挠度和阻尼等。
1。
2 悬架系统基本方案介绍MA02—ME100纯电动车前悬架采用麦弗逊式独立悬架带横向稳定杆结构,后悬架系统采用拖曳臂式非独立悬架结构。
前、后悬架系统的结构图如图1、图2:图1 前悬架系统图2 后悬架系统1。
3 悬架系统设计的输入条件悬架系统设计输入参数如表1:表1 悬架参数列表2 悬架系统的计算 2。
1 弹簧刚度根据KC 试验数据分析,选定弹簧刚度: 前悬架弹簧刚度为: mm N C sf /20=; 后悬架弹簧刚度为: mm N C sr /7.21=; 2.2 悬架偏频的计算悬架系统将车身与车轮弹性的连接起来,由此弹性元件与它所支承的质量组成的振动系统决定了车身的固有频率,这是影响汽车行驶平顺性的重要性能指标之一。
计算说明书_悬架系统
悬架系统1.整车有关参数1.1 轴距:L=2610mm1.2 轮距:前轮B1=1530mm后轮B2=1510mm1.3 轴荷(kg)1.4 前后轮空满载轮心坐标(Z向)1.4 前、后悬架的非簧载质量(kg):G u1=108kg G u2=92kg1.5 悬架单边簧载质量(kg)悬架单边簧载质量计算结果如下:前悬架:空载单边车轮簧载质量为M01=(795-108)/2=343.5kg 半载单边车轮簧载质量为 M03=(872-108)/2=382kg满载单边车轮簧载质量为M02=(891-108)/2=391.5kg 后悬架:空载单边车轮簧载质量为M1=(625-92)/2=266.5kg半载单边车轮簧载质量为M3=(773-92)/2=340.5kg满载单边车轮簧载质量为M2=(904-92)/2=406kg2、前悬架布置前悬架布置图见图1图1 T21前悬架布置简图3、前悬架设计计算3.1 前悬架定位参数:3.2 前悬架采用麦弗逊式独立悬架,带稳定杆,单横臂,螺旋弹簧,双向双作用筒式减震器。
(1) 空满载时缓冲块的位置和受力情况 空载时,缓冲块起作用,不受力 满载时,缓冲块压缩量为13.8mm ,(由DMU 模拟得知,DMU 数据引自T21 M2数据)。
根据缓冲块的特性曲线,当缓冲块压缩13.8mm 时,所受的力为:125N (2) 悬架刚度计算螺旋弹簧行程杠杆比:1.06悬架刚度为K 1= ((391.5-343.5)*9.8-125/1.06)/(5-(-15))= 17.62N/mm(3)前螺旋弹簧①截锥螺旋弹簧②螺旋弹簧行程杠杆比:1.06③刚度C1=K1*(1.06)2*0.9=17.62*(1.06)2*0.9=17.81N/mm(4)静挠度和空满载偏频计算空载时挠度 f 1= N 1/K 1=( M 01*9.8)/K 1=(343.5*9.8)/17.81=18.9cm静挠度 f 01= f 1 +(5-(-15))/10=20.9 偏频n: 空载为 Hz f n 15.19.18/5/511=== 满载为 Hz f n 09.19.20/5/50101===结论:前悬架偏频在1.00~1.45Hz 之间,满足设计要求。
(完整word版)悬架刚度
5.1。
1悬架的弹性特性和工作行程对于大多数汽车而言,其悬挂质量分配系数:ab =0。
8~1.2,因而可以近似地认为e =1,即前后桥上方车身部分的集中质量的垂向振动是相互独立的,并用偏频21,n n 表示各自的自由振动频率,偏频越小,则汽车的平顺性越好.一般对于采用钢制弹簧的轿车,1n 约为1~1.3Hz (60 — 80次/ min ), 2n 约为1。
17 ~1。
5Hz ,非常接近人体步行时的自然频率.载货汽车的偏频略高于轿车,前悬架约为1.3Hz ,后悬架则可能超过1。
5Hz 。
为了减小汽车的角振动,一般汽车前、后悬架偏频之比约为1n /2n = 0.85~0.95。
具体的偏频选取可参考表5-1:表5-1 汽车悬架的偏频、静挠度和动挠度车满载时偏频 n / Hz满载时静挠度 f c / 满载时动挠度 f d /空载满载1c f 2c f2d f 载货汽车1.0~1.451。
17~1。
6~11 5~9 6~9 6~8由上表选取货车满载时前后悬架的偏频分别为:1n =1.4Hz,2n = 1。
5Hz 所以1n /2n =1。
4 / 1。
5 = 0.93,满足要求。
当ε=1时,汽车前、后桥上方车身部分的垂向振动频率21,n n 与其相应的悬架 刚度1s C 和2s C ,以及悬挂质量1s m 和2s m 之间有如下关系:11111222221212s s s s s s s s C gC n m G C gC n m G ππ⎫==⎪⎪==………………………………………………5-1式中: g ——重力加速度,g =98102/s mm ; 1s C ,2s C ——前、后悬架刚度,N / m ; 1s G ,2s G -—前、后悬架簧载重力,N 。
为了求出前后悬架的垂直刚度,必须先求出前后悬架的簧载质量m s 1 和m s 2 。
而 m s 1 和m s 2 可以通过满载时前后轮的轴荷减去前后非簧载质量得到。
- 1、下载文档前请自行甄别文档内容的完整性,平台不提供额外的编辑、内容补充、找答案等附加服务。
- 2、"仅部分预览"的文档,不可在线预览部分如存在完整性等问题,可反馈申请退款(可完整预览的文档不适用该条件!)。
- 3、如文档侵犯您的权益,请联系客服反馈,我们会尽快为您处理(人工客服工作时间:9:00-18:30)。
3.1 弹簧刚度
弹簧刚度计算公式为:
前螺旋弹簧为近似圆柱螺旋弹簧:前
n 8D Gd 3
14
1
1=
Cs (1)
1
后螺旋弹簧为圆柱螺旋弹簧:后
n 8D Gd 3
24
2
2=
Cs (2)
式中:G 为弹性剪切模量79000N/mm 2
d 为螺旋弹簧簧丝直径, 前螺旋弹簧簧丝直径d 1=11.5mm ,
后螺旋弹簧簧丝直径d 2=12mm ;
1D 为前螺旋弹簧中径,D 1=133.5mm 。
D 2为后螺旋弹簧中径,D 2=118mm 。
n 为弹簧有效圈数。
根据《汽车设计》(刘惟信)介绍的方法,判断前螺旋弹簧有效圈数为4.25圈,即n 前=4.25;后螺旋弹簧有效圈数为5.5圈,即 n 后=5.5。
前螺旋弹簧刚度:
=18.93 N/mm
后螺旋弹簧刚度:
后
n 8D Gd 324
2
2=
Cs =22.6N/mm
螺旋弹簧刚度试验值: 前螺旋弹簧刚度:18.8N/mm ;
1
螺旋弹簧刚度计算公式,参考《汽车工程手册》设计篇
3
1
41
116n Gd D Cs 前=
后螺旋弹簧刚度:22.78N/mm 。
前螺旋弹簧刚度和后螺旋弹簧刚度计算值与试验值基本相符。
G08设计车型轴荷与参考样车的前轴荷相差<2.0%,后轴荷相差<0.8%。
设计车型直接选用参考样车的弹簧刚度,刚度为:
Cs=18.8 N/mm;
1
Cs=22.6 N/mm。
2
3.5 减震器参数的确定
汽车的悬架中安装减振装置的作用是衰减车身的振动保证整车的行驶平顺性和操纵稳定性。
下面仅考虑由减振器引起的振动衰减,Array不考虑其他方面的影响,以方便对减振器参数的计算。
汽车车身和车轮振动时,减振器内的液体在流经阻尼孔时的摩擦
和液体的粘性摩擦形成了振动阻尼,将振动能量转变为热能,并散发到周围的空气中去,达到迅速衰减振动的目的。
汽车的悬架有了阻尼以后,簧载质量的振动是周期衰减振动,用相对阻尼比ψ来评定振动衰减,相对阻尼比的物理意义是指出减振器的阻尼作用在与不同刚度和不同质量的悬架系统匹配时,会产生不同的阻尼效果。
减振器中的阻力F和速度v之间的关系可以用下式表示:
i
= (10)
Fδ
v
式中:δ为减振器阻尼系数;
i是常数,i=1。
以下是前后减震器阻力-速度特性曲线:
从上图曲线中得到,当前后减振器速度为0.524 m/s时:下面以空载状态分别对前后悬架的相对阻尼比进行计算:
前悬架的减振器安装如图3-6所示:
图3-6 前减振器安装结构图
在上图中,车轮处的阻尼力始终随减振器运动,因此此处不存在杠杆比。
减振器有一个3.0°的空间安装角。
计算得到前悬架的相对阻尼比为:
α为减振器与垂直线所成夹角,单位rad ; m 为簧载质量,单位kg ; n 为偏频,单位Hz ; i 为常数,i=1。
23.04cos 2
2==mni
παδψ前 后悬架的减振器安装如图3-7所示:
图3-7 后减振器安装侧视图
后减振器在侧视图中存在杠杆比i =L 1/L 4=400.2/468.2=0.85, 其与垂直线的空间夹角α是4.4°。
计算得到后悬架的相对阻尼比为:
81.04cos 2
2==mni
παδψ后 1. 前后悬架螺旋弹簧长度校核
悬架在运动过程中,必须验证螺旋弹簧在上下极限位置的长度是否满足使
用要求,弹簧长度应该满足以下要求: 1、上极限位置时螺旋弹簧应该不能并圈。
2、下极限位置时螺旋弹簧长度应该小于弹簧自由长度,以防止弹簧脱落 根据CAE 分析的悬架跳动结果可以确定螺旋弹簧的长度,见表1:
镖1 螺旋弹簧长度列表
400.2
468.2
341.4
由上表可以看出,悬架处于上极限位置时,其长度大于并圈长度,故不会发生并圈;悬架处于下极限位置时,其长度小于自由长度,故弹簧处于被压缩状态,不会脱落。
因此,螺旋弹簧长度符合整车设计要求。
2.前、后减振器长度校核
悬架运动过程中必须校核减振器的工作行程,以判断悬架在运动过程中减振器推杆是否顶死。
5.1 前减振器校核
a)根据厂家提供前减振器图纸可得前减振器极限尺寸,如图19所示。
最长491mm,最短310mm
图19 前减振器极限尺寸
b)前悬架在上极限位置时,前减振器的长度为344.5mm,如图20所示,大于减振器极限最短尺寸,故减振器推杆不会顶死。