模具问题点解决方案表
常见模具问题改善方法

偏大1、凹凸模间隙太松加大凸模或减少凹模2、成形块直身太浅、R太大加高成形块减小R位3、压筋压太少追加压筋4、凹模顶底弹力太小加大弹力5、角度偏大研磨角度6、凸凹模未锁紧紧固螺丝或定位7、凸凹模边多边少重新调整间隙8、凸模深度不够调整凸模高度偏小1、凸凹间隙太紧加大间隙2、成形块直身太深R位太小减少成形块直身或加大R位3、压筋压得太深降低压筋4、凹模顶底力太小加大顶底顶力5、凹凸角位偏小调整角度6、凸凹模未固定固定凸凹模7、凸凹间隙边多边少重新调整间隙8、凸凹深度未到位调整深度偏高1、成形R位太小加大R位2、压筋太小加深压筋3、定位太松固定定位4、凸凹间隙太紧放松间隙5、剪口落料太多减少开料尺寸6、凸模压得太深把凸模上升7、凸凹不垂直调整凸凹垂直度偏低1、成形R位太大缩小R位2、压筋太少加大压筋3、定位太紧研磨定位4、凸凹间隙太松调整间隙5、剪口落料不够增加开料尺寸6、凸模压得不够调整凸模深度7、凸凹不垂直调整凸凹垂直度不脱料1、缺少或顶料力不够增加顶料或加大顶料力2、冲孔冲头太长缩短冲头3、外脱或内脱太紧或太低调整间隙增高内外脱4、未退磁或油类太多太浓退磁或更换油类5、冲头变形修理或更换冲头6、角度偏小或让位不够调整角度加大让位孔径不良1、冲头同镶件间隙不符调整冲头同镶件间隙2、冲孔后变形成形后冲孔3、冲头同镶件材质不够硬更换或调整冲头同镶件4、压料未到位调整压料5、烧公烧镶件省或更换公同镶件6、冲头或镶件崩角研磨或更换冲头同镶件拉料1、压料不够增加压料力或追加压筋2、余料太多减少余料3、冲头同镶件加钝研磨冲头同镶件4、间隙不符调整间隙产品擦伤1、光洁度太粗省光洁度2、间隙太紧调整间隙3、油类不够增加油类4、有异物去除异物5、凹模有印省光洁度6、米位不够省R位产品压印1、顶料销太利省顶料销光洁度2、压得太深压力太大调整压力3、顶料销孔螺丝孔销钉孔不够光滑省顶料销螺丝销钉孔4、凸凹模上有压印省平压卯5、凸凹模上有异物/产品有异物去除异物正批锋1、间隙不符调整间隙2、硬度不够更换或调整硬度3、铲模研磨刀口或更换刀口4、烧公或烧模省烧公或烧模、研磨,烧公或烧模更换公同镶件5、油类不够增加油类6、单剪口调整间隙,研磨刀口7、崩角研磨或更换刀口8、刀口钝研磨刀口反批锋1、外脱料太高弹力太大降低外脱料减少弹力2、间隙太大调整间隙拉深起皱1、弹簧力不够增加弹簧力2、R位不够光省R位3、走料不够增加走料4、间隙不符调整间隙5、油类不当更换油类6、压力不够增加压力7、转速太快减少转速拉深破裂1、R位不够增大R位2、光滑不够抛光3、拉深行程太多减少拉深行程4、间隙不符调整间隙5、边多边少调整间隙6、拉深油不当更换拉深油7、弹簧力不够增加弹簧力8、转速太快减少转速9、材质太硬更换材质10、拉深力太小增加拉深力平面度不良1、压力不够调整压力2、脱料不均调整脱料3、材质不当更换材质V折模可能产生的不良现象1、角度偏大偏小调整角度深度2、V折边有印省V折模边3、平面度超差硬成型冲及凹模取放料物方便性探讨1、非特别材料:模具要退磁2、连续模的落料:不是直接掉料的应加吹气或磨斜度3、导柱的设计应考虑取放材料及材料宽窄4、材料卸压及顶料的平面度5、模具应有材料固定位冲头折断分析1、塞屎2、冲头直身太长3、冲头无固定4、冲头小材料厚5、间隙不符6、刀口不对7、内脱料让位不够8、冲头太脆或不够硬9、冲头变形折弯角度不良(偏大、偏小)1、成形间隙大调整成形间隙为合理状态2、成形深度不够加深成形浓度不合理状态3、顶针顶料不顺修正顶针与轧弯距离,修正弹力大小不均4、R圆角过大减小R圆角,不良结果:会有拉伤偏小原因同偏大问题点修正对策相反折弯边高度不良偏高:1、设计展开2.拉料3、折弯R过大产品不脱料1、弹力太小加大弹簧力度2、冲头太紧重新修正过紧位置3、顶针孔到轧弯边距离太大修正顶针孔到边的距离4、角度小调整气压,骨位降低5、间隙紧调整成形间隙为合理状态6、脱料力不平衡修正平衡力度孔径不良孔过大:1、拉料孔变形、变大加大弹弓力度,减小拉料,加刻印2、冲头研磨不标准、过大按标准重新研磨3、冲针不圆修正重磨孔过小:1、压线太深,孔挤小减低压线2、冲头研磨过小重新研磨拉料现象1、单边折弯有拉料做档块结构2、成形力度不够,弹力过小,成形会拉料加大上下弹力产品擦伤1、间隙不合理、偏小调整间隙2、模板硬度不够加硬3、R角不够圆滑研磨R4、板件表面光洁度达不到要求产品压印1、与产品接触面凸起位修正光滑且圆角过度批锋正批锋:1、间隙过大2、间隙过小3、刀口不利反批锋:1、内脱高模面太多2、产品分离不顺畅拉伸起皱1、凸凹模不够光滑抛光凸凹模2、上下模压力太小加大上下模弹弓、气顶力度3、凸凹模间隙配对不均匀重新调整间隙4、周边无压料筋加压筋拉深破裂1、R角不够大、光滑2、压料力太大3、R角位硬度不够平面度不良1、下模脱料,压力不够大加大脱料力为气顶,弹力胶2、上模脱料不均匀,产品变形更改上模脱料结构V曲可能产生不良现象1、角度大调整啤机上升调整V曲深度变浅2、角度偏小与上述相反3、V曲时擦伤严重加大R位不良影响角度取放料的方便性探讨1、管位直身位要高顶针面二个料厚,管位尽量不采用管轧弯边冲头折断分析1、冲孔堵屎2、冲针在孔里摩擦不顺3、冲针太小无加强4、脱料不顺操作规程1、上落模操作规程上模前:首先检查啤机闭合高度是否够,模具螺丝是否紧固下模前:详细填写好模具调试管制单。
模具问题点 原因分析 解决对策

模具问题点原因分析解决对策1.废料跳穴a.冲头长度不够按冲头刃口切入凹模一个料厚加1mm更换冲头b.凹模间隙过大割入子减少间隙或用披覆机减小间隙c.冲头或模板未去磁将冲头或模板用去磁器去磁2.废料堵穴a.落料孔小或落料孔偏位加大落料孔,使落料顺畅b.落料孔有倒角加大落料孔去除倒角c.刀口未放锥度线割锥度或反面扩充孔减小直壁位长度d.刀口直壁位过长反面钻孔,使刀口直壁位缩短e.刃口崩,造成披锋大,堵料重新研磨刃口3.披锋不良a.刃口崩,造成披锋过大重新研磨刃口b.冲头与凹模间隙过大线割入块,重新配间隙c.凹模刀口光洁度差抛光刀口直壁位d.冲头与凹模间隙过小重新省模,配间隙e.顶料力过大,反向拉出披锋换弹簧,减小顶料力4.切边不齐a.定位偏移调整定位b.有单边成型,拉料加大压料力,调整定位c.设计错误,造成接刀不平重新线割切边刀口镶块d.送料不准调整送料器e.送料步距计算有误重新计算步距,重定接刀位5.冲头易断a.闭合高度过低,冲头切入刀口部位过长调整闭合高度b.材料定位不当,造成冲孔冲头切单边,调整定位或送料装置因受力不均断裂c.下模废料堵死刀口,造成冲头断重新钻大落料孔,使落料顺畅d.冲头的固定部位(夹板)与导向部位修配或重新线割入块使冲头上下顺畅(打板)偏移e.打板导向不良,造成冲头单边受力重新修配打板间隙f.冲头刀口太短,与打板干涉重换冲头,增长刀口部分长度g.冲头固定不好,上下窜动重新固定冲头使之不能上下窜动h.冲头刃口不锋利重新研磨刃口I.冲头表面拉伤,脱料时受力不均重新换冲头j.冲头过细,过长,强度不够重新换冲头类型k.冲头硬度过高,冲头材质不对更换冲头材质,调整热处理硬度6.铁屑a.压筋错位重新计算压筋位置或折弯位置b.折弯间隙过小,挤出铁屑重新调整间隙,或研磨成型块,或研磨成型冲头c.折弯凸模太锋利修R角d.接刀口材料太少重新接刀口e.压筋太窄重新研磨压筋7.抽芽不良a.抽芽底孔中心与抽芽冲子中心不重合造确定正确中心位置,或移动抽芽冲子位置,或移成抽芽-边高-边低甚至破裂动预冲孔位置,或调整定位b.凹模间隙不均匀,造成抽芽-边高-边修配抽芽间隙低甚至破裂c.抽芽底孔不符合要求,造成抽芽高度及重新计算底孔孔径,预冲孔增大或减少直径偏差,甚至破裂8.成型不良a.成型模凸模太锋利,造成材料拉裂成型凸模修R角,刀口处适当修R角b.成型冲头长度不够,造成未能成型计算冲头正确长度调整冲头实际长度以达成型要求c.成型冲头过长,成型处材料压变形,甚确定冲头正确长度,调整冲头实际长度以达到要求至冲头断裂d.成型处材料不够造成拉裂计算展开材料,或修R角,或降低成型高度e.定位不良,造成成型不良调整定位或送料装置f.成型间隙太小造成拉裂或变形调配间隙9.折弯尺寸a.模具没调到位造成角度误差导致尺寸偏调整闭合高度不良或角度差不良 b.弹力不够造成角度不良导致尺寸偏差换弹簧c.材质不符合要求造成角度不良导致尺寸换材料或重新调整间隙偏差d.材料厚度偏差引起角度不良导致尺寸偏确定料厚,换材料或重新调整间隙差e.定位不当导致尺寸偏差调整定位使尺寸OKf.设计或加工错误造成折弯公拼块间有间補焊研磨,消除拼块间的间隙隙,导致折弯尺寸小g.成型公无R角,在角度及其他正常情况成型公修R角下折弯高度偏小h.两边折弯尺寸偏大加压筋I.单边折弯拉料造成尺寸不稳定加大弹簧力,调整定位j.间隙不合理,引起角度不良和尺寸偏差修配间隙k.折刀高度不够,折弯冲头合入折刀太短增加折刀高度,使折弯冲头尽可能合入折刀部队位造成角度不良多一些l.折弯时速度太快,造成折弯根部变形调整速比控,选择合理转速m.结构不合理,折刀未镶入固定模板,重新铣槽,将折刀镶入模板冲压时,造成间隙变大n.成型公热处理硬度不够,造成压线崩或重制成型公压线打平10.不卸料a.定位不当或送料不当调整定位或送料装置b.避位不够修磨避位c.内导柱拉伤,造成打板活动不畅更换内导柱d.冲头拉伤或表面不光滑更换冲头e.顶料销摆布不合理重新摆布顶料销位置f.顶料力不够,或脱料力不够更换顶料弹簧或脱料弹簧g.冲头与夹板打板配合不顺畅修配打板和夹板使冲头配合顺畅h.成型滑块配合不畅修整滑块与导向槽使之配合顺畅I.打板热处理不适,冲压一段时间后变形重新研磨打板,矫正变形j.冲头过长或顶料销长度不够增加顶料销长度或换用长度合适之冲头k.冲头断更换冲头l.模板未云磁,工件往上带给模板去磁11.送料不顺a.模具没架正,导致料带与送料器及模具重架模具或调整送料器不在同一条直线上b.料带不平调整校平机或更换材料c.不卸料造成送料不顺参照不卸料解决对策d.定位太紧调整定位e.导正销太紧或直壁位太长调整导正销f.冲头固定不好或太长与料带干涉换长度合适之冲头重新固定g.顶料销太短,料带与成型入块相干涉调整顶料销长度,避免干涉h.浮升块位置排配不当调整浮升块位置12.铆合不良a.模具闭合高度不当铆合不到位调整闭合高度b.工件未放到位,定位偏差调整定位c.铆合前工件不良确认抽芽孔,参考抽芽孔不良解决对策处理确认铆合孔是否倒角,如无倒角则增加倒角d.铆合冲头长度不够换用长度合适之冲头e.铆合冲头不符合要求确认并用符合要求之铆合冲头13.漏装或装a.不小心组立时细心错冲子b.冲子无方向标记有方向性的冲子做上记号14.装错螺丝a.不知道模板的厚度了解模板的厚度太长或太短 b.不够细心,经验不足选用适当的螺丝15.拆装模具a.销钉孔没有擦干净将销孔,销钉擦干净,拆模时应先拆定位销,时容易损坏装模时,应先用螺丝导正,后打定位销销钉孔 b.装拆模具程序不对打落销钉时不要碰伤销钉孔16.定位销a.孔壁拉毛,刮伤致使太紧组模时,细心检查销钉孔是否拉毛,否则应将打不出来销孔重新铰孔b.销孔偏位或下面没有逃孔追加定位销逃孔17.弹簧太长a.没有注意弹簧孔深度量好弹簧孔深度,算好弹簧的压缩量,重新选择无法下压到 b.不够细心,经验不足合适的弹簧下死点。
模具常见问题分析及其解决方法

模具常见问题分析及其解决方法概述模具是工业生产中常用的一种工具,它在各个行业中被广泛应用。
然而,随着使用时间的增加,模具也会出现各种问题。
本文将详细分析模具常见问题,并提供相应的解决方法,以帮助读者更好地应对模具问题。
问题一:模具磨损严重模具磨损是使用寿命过程中常见的问题之一。
其主要表现为模具表面磨损或凹陷。
磨损的原因可能是: - 使用材料硬度较高 - 使用时间较长 - 模具润滑不足 - 模具设计不合理解决方法: - 使用耐磨性能更好的模具材料,如优质钢材 - 定期进行模具保养和维护,及时更换磨损严重的部件 - 在使用过程中保持适当的模具润滑,减少磨损 - 对模具进行优化设计,减少出现磨损的可能性问题二:模具尺寸偏差大模具尺寸偏差大是另一个常见问题。
这可能导致生产出的产品尺寸不准确,影响产品质量。
尺寸偏差大的原因包括: - 模具制造过程中的测量误差 - 模具材料膨胀或收缩不均匀 - 模具结构设计不合理解决方法: - 提高模具制造过程中的测量精度,并进行多次验证 - 选择合适的模具材料,控制材料膨胀或收缩的影响 - 对模具结构进行优化设计,避免尺寸偏差的产生问题三:模具易生锈模具易生锈是模具在使用过程中常见的问题之一。
模具生锈不仅影响外观,还可能导致模具损坏。
模具易生锈的原因可能是: - 环境湿度较高 - 模具存放不当 - 模具润滑不足解决方法: - 控制使用环境湿度,尽量保持干燥 - 对模具进行正确的存放,避免受潮或受酸碱腐蚀 - 在使用过程中,保持模具的适度润滑,防止生锈问题四:模具易断裂模具易断裂是一种严重的问题,可能导致模具报废,造成生产线停机。
模具易断裂的原因包括: - 模具结构设计不合理 - 模具材料不合格或强度低 - 模具使用过程中发生过载解决方法: - 对模具结构进行优化设计,提高其受力性能 - 选择合适的模具材料,确保其强度和韧性满足要求 - 在使用过程中,避免过载操作,及时发现并处理异常情况问题五:模具易堵塞模具易堵塞是模具在使用过程中常见的问题,特别是对于塑料注塑模具。
注塑模具常见缺陷、产生原因和调整方法表

制件பைடு நூலகம்量不好:
1.有飞边
2.有缺料
3.有顶白
4.有拖花
5.变形大
6.级位大
7.溶接线明显
1.配合间隙过大;
2.走胶不畅, 困气;
3.顶针过小, 顶出不均匀;
4.斜度过小, 有毛刺, 硬度不足;
5.注塑压力不均匀, 产品形态强度不足;
6.加工误差;
7.离浇口远, 模温低。
注塑模具常见缺陷、产生原因和调整方法表
注塑模
装配缺陷
产 生 原 因
调 整 方 法
模具开闭
顶出复位
动作不顺
1.模架导柱、导套滑动不顺,配合过紧
2.斜顶、顶针滑动不顺。
3.复位弹簧弹力或预压量不足。
1修配或者更换导柱、导套。
2检查并修配斜顶、顶针配合。
3增加或者更换弹簧。
模具与注塑
机不匹配
1.定位环位置不对、尺寸过大或过小。
1.合理调整间隙及修磨工作部分分型面;
2.局部加胶, 加排气;
3.加大顶针, 均匀分布;
4.修毛刺, 加斜度, 氮化;
5.修整浇口, 压力均匀, 加强产品强度;
6.重新加工;
7.改善浇口, 加高模温。
2.模具的限位行程不够,模具的抽芯行程不够,模具的顶出行程不够;
1.检查浇注系统各段流道和浇口,修整有关零件;
2.检查各限位、抽芯、顶出行程是否符合设计要求,调整不符合要求的行程;
模具运水
不通或漏水
1模具运水通道堵塞,进出水管接头连接方式错误。
2封水胶圈和水管接头密封性不够。
1.检查冷却系统进出水管接头连接方式及各段水道,修整有关零件;
模具问题点解决方案

5.冲头易断-2
d.冲头的固定部位(夹板)与导向部位 修配或 重新线割入块使冲头上下顺畅(打板)偏移 e.打板导向不良,造成冲头单边受力 重新修配 打板间隙 f.冲头刀口太短,与打板干涉 重换冲头,增长 刀口部分长度
5.冲头易断-3
g.冲头固定不好,上下窜动 重新固定冲头使之 不能上下窜动 h.冲头刃口不锋利 重新研磨刃口
I.冲头表面拉伤,脱料时受力不均 重新换冲头
5.冲头易断-4
j.冲头过细,过长,强度不够 重新换冲头类型
k.冲头硬度过高,冲头材质不对 更换冲头材质, 调整热处理硬度
6.铁屑-1
a.压筋错位 重新计算压筋位置或折弯位置
b.折弯间隙过小,挤出铁屑 重新调整间隙,或 研磨成型块,或研磨成型冲头 c.折弯凸模太锋利 修R角
模具问题点
--解决方案
1.废料跳穴
a.冲头长度不够 按冲头刃口切入凹模一个料厚 加1mm更换冲头 b.凹模间隙过大 割入子减少间隙或用披覆机减 小间隙 c.冲头或模板未去磁 将冲头或模板用去磁器去 磁
2.废料堵穴-1
a.落料孔小或落料孔偏位 加大落料孔,使落料 顺畅
b.落料孔有倒角 加大落料孔去除倒角 c.刀口未放锥度 线割锥度或反面扩充孔减小直 壁位长度 d.刀口直壁位过长 反面钻孔,使刀口直壁位缩 短
6.铁屑-2
d.接刀口材料太少 重新接刀口
e.压筋太窄 重新研磨压筋
7.抽芽不良-1
a.抽芽底孔中心与抽芽冲子中心不重合造 确定 正确中心位置,或移动抽芽冲子位置,或移成 抽芽-边高-边低甚至破裂动预冲孔位置,或 调整定位
常见模具问题改善方法

偏大1、凹凸模间隙太松加大凸模或减少凹模2、成形块直身太浅、R太大加高成形块减小R位3、压筋压太少追加压筋4、凹模顶底弹力太小加大弹力5、角度偏大研磨角度6、凸凹模未锁紧紧固螺丝或定位7、凸凹模边多边少重新调整间隙8、凸模深度不够调整凸模高度偏小1、凸凹间隙太紧加大间隙2、成形块直身太深R位太小减少成形块直身或加大R位3、压筋压得太深降低压筋4、凹模顶底力太小加大顶底顶力5、凹凸角位偏小调整角度6、凸凹模未固定固定凸凹模7、凸凹间隙边多边少重新调整间隙8、凸凹深度未到位调整深度偏高1、成形R位太小加大R位2、压筋太小加深压筋3、定位太松固定定位4、凸凹间隙太紧放松间隙5、剪口落料太多减少开料尺寸6、凸模压得太深把凸模上升7、凸凹不垂直调整凸凹垂直度偏低1、成形R位太大缩小R位2、压筋太少加大压筋3、定位太紧研磨定位4、凸凹间隙太松调整间隙5、剪口落料不够增加开料尺寸6、凸模压得不够调整凸模深度7、凸凹不垂直调整凸凹垂直度不脱料1、缺少或顶料力不够增加顶料或加大顶料力2、冲孔冲头太长缩短冲头3、外脱或内脱太紧或太低调整间隙增高内外脱4、未退磁或油类太多太浓退磁或更换油类5、冲头变形修理或更换冲头6、角度偏小或让位不够调整角度加大让位孔径不良1、冲头同镶件间隙不符调整冲头同镶件间隙2、冲孔后变形成形后冲孔3、冲头同镶件材质不够硬更换或调整冲头同镶件4、压料未到位调整压料5、烧公烧镶件省或更换公同镶件6、冲头或镶件崩角研磨或更换冲头同镶件拉料1、压料不够增加压料力或追加压筋2、余料太多减少余料3、冲头同镶件加钝研磨冲头同镶件4、间隙不符调整间隙产品擦伤1、光洁度太粗省光洁度2、间隙太紧调整间隙3、油类不够增加油类4、有异物去除异物5、凹模有印省光洁度6、米位不够省R位产品压印1、顶料销太利省顶料销光洁度2、压得太深压力太大调整压力3、顶料销孔螺丝孔销钉孔不够光滑省顶料销螺丝销钉孔4、凸凹模上有压印省平压卯5、凸凹模上有异物/产品有异物去除异物正批锋1、间隙不符调整间隙2、硬度不够更换或调整硬度3、铲模研磨刀口或更换刀口4、烧公或烧模省烧公或烧模、研磨,烧公或烧模更换公同镶件5、油类不够增加油类6、单剪口调整间隙,研磨刀口7、崩角研磨或更换刀口8、刀口钝研磨刀口反批锋1、外脱料太高弹力太大降低外脱料减少弹力2、间隙太大调整间隙拉深起皱1、弹簧力不够增加弹簧力2、R位不够光省R位3、走料不够增加走料4、间隙不符调整间隙5、油类不当更换油类6、压力不够增加压力7、转速太快减少转速拉深破裂1、R位不够增大R位2、光滑不够抛光3、拉深行程太多减少拉深行程4、间隙不符调整间隙5、边多边少调整间隙6、拉深油不当更换拉深油7、弹簧力不够增加弹簧力8、转速太快减少转速9、材质太硬更换材质10、拉深力太小增加拉深力平面度不良1、压力不够调整压力2、脱料不均调整脱料3、材质不当更换材质V折模可能产生的不良现象1、角度偏大偏小调整角度深度2、V折边有印省V折模边3、平面度超差硬成型冲及凹模取放料物方便性探讨1、非特别材料:模具要退磁2、连续模的落料:不是直接掉料的应加吹气或磨斜度3、导柱的设计应考虑取放材料及材料宽窄4、材料卸压及顶料的平面度5、模具应有材料固定位冲头折断分析1、塞屎2、冲头直身太长3、冲头无固定4、冲头小材料厚5、间隙不符6、刀口不对7、内脱料让位不够8、冲头太脆或不够硬9、冲头变形折弯角度不良(偏大、偏小)1、成形间隙大调整成形间隙为合理状态2、成形深度不够加深成形浓度不合理状态3、顶针顶料不顺修正顶针与轧弯距离,修正弹力大小不均4、R圆角过大减小R圆角,不良结果:会有拉伤偏小原因同偏大问题点修正对策相反折弯边高度不良偏高:1、设计展开2.拉料3、折弯R过大产品不脱料1、弹力太小加大弹簧力度2、冲头太紧重新修正过紧位置3、顶针孔到轧弯边距离太大修正顶针孔到边的距离4、角度小调整气压,骨位降低5、间隙紧调整成形间隙为合理状态6、脱料力不平衡修正平衡力度孔径不良孔过大:1、拉料孔变形、变大加大弹弓力度,减小拉料,加刻印2、冲头研磨不标准、过大按标准重新研磨3、冲针不圆修正重磨孔过小:1、压线太深,孔挤小减低压线2、冲头研磨过小重新研磨拉料现象1、单边折弯有拉料做档块结构2、成形力度不够,弹力过小,成形会拉料加大上下弹力产品擦伤1、间隙不合理、偏小调整间隙2、模板硬度不够加硬3、R角不够圆滑研磨R4、板件表面光洁度达不到要求产品压印1、与产品接触面凸起位修正光滑且圆角过度批锋正批锋:1、间隙过大2、间隙过小3、刀口不利反批锋:1、内脱高模面太多2、产品分离不顺畅拉伸起皱1、凸凹模不够光滑抛光凸凹模2、上下模压力太小加大上下模弹弓、气顶力度3、凸凹模间隙配对不均匀重新调整间隙4、周边无压料筋加压筋拉深破裂1、R角不够大、光滑2、压料力太大3、R角位硬度不够平面度不良1、下模脱料,压力不够大加大脱料力为气顶,弹力胶2、上模脱料不均匀,产品变形更改上模脱料结构V曲可能产生不良现象1、角度大调整啤机上升调整V曲深度变浅2、角度偏小与上述相反3、V曲时擦伤严重加大R位不良影响角度取放料的方便性探讨1、管位直身位要高顶针面二个料厚,管位尽量不采用管轧弯边冲头折断分析1、冲孔堵屎2、冲针在孔里摩擦不顺3、冲针太小无加强4、脱料不顺操作规程1、上落模操作规程上模前:首先检查啤机闭合高度是否够,模具螺丝是否紧固下模前:详细填写好模具调试管制单。
注塑模具常见问题解决方案
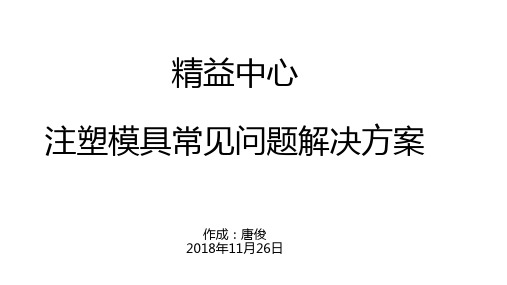
顶出机构设计不合理
圆筒、深腔类产品、深筋位、孔纹、气泡
原因分析
进浇口尺寸太小
进浇点位置设计不合理 模具困气
解决对策
大水口侧进浇厚度不能太薄,一般不小于主体壁厚1/2,潜筋位进浇口,筋位 适当加宽、浇口可做椭圆形改善进浇口表面困气不良。
进胶点的位置布置应充分考虑气体能顺利排出型腔,型腔的充填压力最小。 产品周圈分型面和熔胶未端需要加强排气、深筋、深柱超过6-8mm以上需要 做排气镶件。 PC、PMMA等透明部件防止冷料进入型腔而产生流痕必须做“S”形流道。
顶机构设计不合理 热量集中冷却不足 冷却不均
6.缩水
原因分析
产品胶位太厚 加强筋太厚 流道偏小 浇口偏小 产品走胶困难 浇口位置设计不合理 热量集中冷却不足 冷却不均
解决对策
模具设计前期应考虑产品避免局部胶位太厚,主体壁厚造型需均匀,拐角部位圆 角过渡。 加强筋厚度在模具设计时不超过主体壁厚的1/2,太厚产品表面会缩水,BOO柱根 部需做火山口减胶,深度0.3T,坡度为30º 比如PC、PC+ABS、玻纤类材料流行性不好,试模后可适当加大流道直径。 比如PC、PC+ABS、玻纤类材料流行性不好,试模后可适当加大浇口直径。 浇口数量的设计要考虑塑每种材料的流长比(L/T),产品深筋、薄避充填过程 容易产生滞留而导致缩水,产品、模具设计前期需要重点考虑。 浇口应设计在产品胶位较厚且容易走胶的部位,进胶压力损失少,利于充填。 深腔胶位、深骨类区域热量较集中,冷却缓慢,应该考虑增加水井加强冷却。 水路设计需随形产品胶位,水路直径D一般取数为6、8、10,具体根据模具规格 来调整,距离产品胶位10-20之间,水路间距等于5D,不小于30mm。
解决对策
碰穿面与插穿面,公模面负公差控制-0.015-0mm;母模面正公差控制+0.015-0
模具毛病及解决方法

挤压料变薄 2.凸凹模间隙过小 角半径 2.修正凸凹模间隙 5 凹形件底部不平 凹模内无顶料装置 增加顶料装置或校正 6 制件端面鼓起或不平 弯曲时材料外表面在圆周方向受拉产生收缩变形,内表面在圆周方向受压产生伸长变形,因而沿弯曲方向出现挠曲端面产生鼓起现象 1.制件在冲压最后阶段凸凹模应有足够压力 2.做出与制件外圆角相应的凹模圆角半径 3.增加工序完善 7 弯曲引起孔变形 采用弹压弯曲并以孔定位时弯臂外侧由于凹模表面和制件外表面摩擦而受拉,使定位孔变形 1.采用V形弯曲 2.加大顶料板压力 3.在顶料板上加麻点格纹,以增大摩擦力防止制件在弯曲时滑移 8 弯曲后不能保证孔位置尺寸精度 1.制件展开尺寸不对 2.材料回弹引起 3.定位不稳定 1.准确计算毛坯尺寸 2.增加校正工序或改进弯曲模成型结构 3.改变工艺加工方法或增加工艺定位 9 弯曲后两边对向的两孔轴心错移 材料回弹改变弯曲角度使中心线错移 1.增加校正工序 2.改进弯曲模结构减小材料回弹 10 弯曲线与两孔中心联机不平行 弯曲高度小于最小弯曲极限高度时弯曲部位出现外胀现象 1.增加折弯件高度尺寸 2.改进折弯件
不垂直,使小凸模偏位 3.凸模或导柱安装不垂直 4.平行度误差积累 件块 3.重新装配,保证垂直度 4.重新修磨装配 10 脱料不正常 1.脱料板与凸模配合过紧,脱料板倾斜或其它脱料件装置不当 2.弹簧或橡胶弹力不够 3.凹模落料孔与下模座漏料孔没有对正 4.凹模有倒锥 1.修整脱料伯 2.更换弹簧或橡胶 3.修整漏料孔 4.修整凹模 18如何根据弯曲件的质量分析修整模具? 弯曲件产生缺陷的原因及调整解决办法如下表: 序号 质量问题 原因分析 解决办法 1 制件高度尺寸不稳定 1.高度尺寸太小 2.凹模圆角不对称 1.高度尺寸不能小于最小极限尺寸 2.修正凹模圆角 2 弯曲角有裂缝 1.弯曲内半径太小 2.材料纹向与弯曲线平行 3.毛坯的毛刺一面向外 4.金属可塑性差 1.加大凸模弯曲半径 2.改变落料排样 3.毛刺改在制件内圆角 4.退火或采用软性材料 3 制件外表面有压痕 1.凹模圆角半径太小 2.凹模表面粗糙间隙小 1.增大凹模圆角半径 2.修正凸凹模间隙 4 弯曲表面1.凹模圆角太小 1.增大凹模圆
- 1、下载文档前请自行甄别文档内容的完整性,平台不提供额外的编辑、内容补充、找答案等附加服务。
- 2、"仅部分预览"的文档,不可在线预览部分如存在完整性等问题,可反馈申请退款(可完整预览的文档不适用该条件!)。
- 3、如文档侵犯您的权益,请联系客服反馈,我们会尽快为您处理(人工客服工作时间:9:00-18:30)。
補焊研磨,消除拼块间的间隙
成型公修R角
加压筋 加大弹簧力,调整定位 修配间隙 增加折刀高度,使折弯冲头尽可能合入折刀部队位 多一些 调整速比控,选择合理转速
重新铣槽,将折刀镶入模板
重制成型公
调整定位或送料装置 修磨避位 更换内导柱 更换冲头 重新摆布顶料销位置 更换顶料弹簧或脱料弹簧 修配打板和夹板使冲头配合顺畅 修整滑块与导向槽使之配合顺畅 重新研磨打板,矫正变形 增加顶料销长度或换用长度合适之冲头 更换冲头 给模板去磁
模具问题点解决作业标准
序号 1 2 3 4
5
6 7
问题点 废料跳穴 废料堵穴 披锋不良 切边不齐
冲头易断
铁屑 抽芽不良
原因分析 a.冲头长度不够 b.凹模间隙过大 c.冲头或模板未去磁 a.落料孔小或落料孔偏位 b.落料孔有倒角 c.刀口未放锥度 d.刀口直壁位过长 e.刃口崩,造成披锋大,堵料 a.刃口崩,造成披锋过大 b.冲头与凹模间隙过大 c.凹模刀口光洁度差 d.冲头与凹模间隙过小 e.顶料力过大,反向拉出披锋 a.定位偏移 b.有单边成型,拉料 c.设计错误,造成接刀不平 d.送料不准 e.送料步距计算有误 a.闭合高度过低,冲头切入刀口部位过长 b.材料定位不当,造成冲孔冲头切单边,因 受力不均断裂 c.下模废料堵死刀口,造成冲头断 d.冲头的固定部位(夹板)与导向部位(打 板)偏移 e.打板导向不良,造成冲头单边受力 f.冲头刀口太短,与打板干涉 g.冲头固定不好,上下窜动 h.冲头刃口不锋利 I.冲头表面拉伤,脱料时受力不均 j.冲头过细,过长,强度不够 k.冲头硬度过高,冲头材质不对 a.压筋错位 b.折弯间隙过小,挤出铁屑 c.折弯凸模太锋利 d.接刀口材料太少 e.压筋太窄 a.抽芽底孔中心与抽芽冲子中心不重合造成 抽芽-边高-边低甚至破裂 b.凹模间隙不均匀,造成抽芽-边高-边低 甚至破裂 c.抽芽底孔不符合要求,造成抽芽高度及直 径偏差,甚至破裂 a.成型模偏差引起角度不良导致尺寸偏差
e.定位不当导致尺寸偏差
f.设计或加工错误造成折弯公拼块间有间隙,
导致折弯尺寸小
9
折弯尺寸不良或角度不良
g.成型公无R角,在角度及其他正常情况下折 弯高度偏 小
h.两边折弯尺寸偏大
I.单边折弯拉料造成尺寸不稳定
j.间隙不合理,引起角度不良和尺寸偏差
k.折刀高度不够,折弯冲头合入折刀太短造
调整定位或送料装置
重新钻大落料孔,使落料顺畅
修配或重新线割入块使冲头上下顺畅
重新修配打板间隙 重换冲头,增长刀口部分长度 重新固定冲头使之不能上下窜动 重新研磨刃口 重新换冲头 重新换冲头类型 更换冲头材质,调整热处理硬度 重新计算压筋位置或折弯位置 重新调整间隙,或研磨成型块,或研磨成型冲头 修R角 重新接刀口 重新研磨压筋 确定正确中心位置,或移动抽芽冲子位置,或移动 预冲孔位置,或调整定位
重架模具或调整送料器
调整校平机或更换材料 参照不卸料解决对策 调整定位 调整导正销
换长度合适之冲头重新固定 调整顶料销长度,避免干涉 调整浮升块位置 调整闭合高度 调整定位 确认抽芽孔,参考抽芽孔不良解决对策处理;确认铆 合孔是否倒角,如无倒角则增加倒角 换用长度合适之冲头 确认并用符合要求之铆合冲头 组立时细心 有方向性的冲子做上记号 了解模板的厚度 选用适当的螺丝 将销孔,销钉擦干净,拆模时应先拆定位销,装模 时,应先用螺丝导正,后打定位销 打落销钉时不要碰伤销钉孔 组模时,细心检查销钉孔是否拉毛,否则应将销孔 重新铰孔 追加定位销逃孔 量好弹簧孔深度,算好弹簧的压缩量,重新选择 合适的弹簧
b.销孔偏位或下面没有逃孔
17
弹簧太长无法下压到下死点
a.没有注意弹簧孔深度 b.不够细心,经验不足
解决对策 按冲头刃口切入凹模一个料厚加1mm更换冲头 割入子减少间隙或用披覆机减小间隙 将冲头或模板用去磁器去磁 加大落料孔,使落料顺畅 加大落料孔去除倒角 线割锥度或反面扩充孔减小直壁位长度 反面钻孔,使刀口直壁位缩短 重新研磨刃口 重新研磨刃口 线割入块,重新配间隙 抛光刀口直壁位 重新省模,配间隙 换弹簧,减小顶料力 调整定位 加大压料力,调整定位 重新线割切边刀口镶块 调整送料器 重新计算步距,重定接刀位 调整闭合高度
修配抽芽间隙
重新计算底孔孔径,预冲孔增大或减少
成型凸模修R角,刀口处适当修R角
计算冲头正确长度调整冲头实际长度以达成型要求
确定冲头正确长度,调整冲头实际长度以达到要求
计算展开材料,或修R角,或降低成型高度 调整定位或送料装置 调配间隙
调整闭合高度
换弹簧
换材料或重新调整间隙
确定料厚,换材料或重新调整间隙
12
铆合不良
c.铆合前工件不良
d.铆合冲头长度不够
e.铆合冲头不符合要求
13
漏装或装错冲子
a.不小心 b.冲子无方向标记
14
装错螺丝太长或太短
a.不知道模板的厚度 b.不够细心,经验不足
15 拆装模具时容易损坏销钉孔 a.销钉孔没有擦干净 b.装拆模具程序不对
16
定位销打不出来
a.孔壁拉毛,刮伤致使太紧
成角度不良
l.折弯时速度太快,造成折弯根部变形
m.结构不合理,折刀未镶入固定模板,冲压
时,造成间隙变大
n.成型公热处理硬度不够,造成压线崩或压
线打平
a.定位不当或送料不当
b.避位不够
c.内导柱拉伤,造成打板活动不畅
d.冲头拉伤或表面不光滑
e.顶料销摆布不合理
10
不卸料
f.顶料力不够,或脱料力不够 g.冲头与夹板打板配合不顺畅
8
成型不良
b.成型冲头长度不够,造成未能成型
8
成型不良
c.成型冲头过长,成型处材料压变形,甚至 冲头断裂
d.成型处材料不够造成拉裂
e.定位不良,造成成型不良
f.成型间隙太小造成拉裂或变形
a.模具没调到位造成角度误差导致尺寸偏差
b.弹力不够造成角度不良导致尺寸偏差 c.材质不符合要求造成角度不良导致尺寸偏 差
h.成型滑块配合不畅
I.打板热处理不适,冲压一段时间后变形
j.冲头过长或顶料销长度不够
k.冲头断
l.模板未云磁,工件往上带
a.模具没架正,导致料带与送料器及模具不
在同一条直线上
b.料带不平
c.不卸料造成送料不顺
11
送料不顺
d.定位太紧
e.导正销太紧或直壁位太长
11
送料不顺
f.冲头固定不好或太长与料带干涉 g.顶料销太短,料带与成型入块相干涉 h.浮升块位置排配不当 a.模具闭合高度不当铆合不到位 b.工件未放到位,定位偏差