气体分馏装置的技术改造设计
气体分馏及MTBE装置技术 共92页

气体分馏及 MTBE装置技术
催化车间 2019年5月
目
录
一、气体分馏技术介绍 二、先进的生产技术及设备 三、科学规范的现场管理 四、MTBE装置技术
2
一、气体分馏技术介绍
石油炼制过程中,特别是二次加工进行重质油轻质 化过程中,产生大量气体,除了催化重整产生的气体是以 氢气为主外,其他装置产气主要为C1(甲烷)至C4(丁 烷、丁烯等)的气态烃以及少量杂质等,其中催化裂化装 置加工量大,气体产量大,气体中的烯烃也最多。因此, 催化裂化气体是气体分馏装置的主要来源。
1.油雾润滑
油雾润滑是一种能够产生、传输并自动为 工业机械和设备中的轴承、齿轮箱等提供润滑 的集中润滑系统。
油雾润滑的核心部件是油雾发生器,他利 用压缩空气作为动力源产生(1-3毫米)的小油 滴,产生的小油滴悬浮在空气中,通过分配管 道网络到机泵需要润滑的地方。
23
二、先进的生产技术及设备
n 惠炼油雾发生器
利用催化装置的低温热水是因为 催化装置分馏塔顶气温度为120℃左 右,冷凝冷却时消耗大量的循环水和 电能,而丙烯塔底温度为55℃左右, 所以利用分馏塔顶气产生的90℃的低 温热水,作为丙烯精馏塔塔底的热源 ,降低了蒸汽消耗。
气体分馏装置的基本原理及工艺流程

气体分馏装置的基本原理及工艺流程作者:董兴鑫来源:《中国科技博览》2014年第11期一气体分馏的重要性炼厂气是石油化工过程中,特别是破坏加工过程中产生的各种气体的总称。
包括热裂化气、催化裂化气、催化裂解气、重整气、加氢裂化气等,炼厂气的产率一般占所加工原油的5~10%。
这些气体的组成较为复杂,主要有C1~C4的烷烃和烯烃,其中有少量的二烯烃和C5以上重组分,此外还有少量的非烃类气体,如:CO、H2、CO2、H2S和有机硫(RSH、COS)等。
炼厂气过去大多是用作工业和民用燃料,少部分加工成为高辛烷值汽油和航空汽油的组成,随着石油化学工业的发展,炼厂气已成为宝贵的化工原料。
炼厂气作为化工原料,必须进行分离,分离的方法很多,就其本质来说可以分为两类,一类是物理分离法,即利用烃类的物理性质的差别进行分离。
如:利用烃类的饱和蒸汽压、沸点不同而进行气体分离过程,有些合成过程对气体纯度要求较高时,则需要高效率的气体分离,如吸附、超精馏、抽提精馏、共沸蒸馏等;另一类方法是化学方法,既利用化学反应的方法将它们分离,如化学吸附和分子筛分离。
目前,我国绝大多数炼油厂采用气体分离装置对炼厂气进行分离,以制取丙烷、丁烷、异丁烷,可以说是以炼油厂气为原料的石油化工生产的重要装置。
一、气体分馏的基本原理炼厂液化气中的主要成分是C3、C4的烷烃和烯烃,即丙烷、丙烯、丁烷、丁烯等,这些烃的沸点很低,如丙烷的沸点是—42.07℃,丁烷为—0.5℃,异丁烯为—6.9℃,在常温常压下均为气体,但在一定的压力下(2.0MPa以上)可呈液态。
由于它们的沸点不同,可利用精馏的力法将其进行分离”所以气体分馏是在几个精馏塔中进行的。
由于各个气体烃之间的沸点差别很小,如丙烯的沸点为—47.7℃.比丙烷低4.6℃,所以要将它们单独分出,就必须采用塔板数很多(一般几十、甚至上百)、分馏精确度较高的精馏塔。
二、气体分馏的工艺流程气体分馏装置中的精馏塔一般为三个或四个,少数为五个,实际中可根据生产需要确定精馏塔的个数。
15万吨年气体分馏装置的优化设计

1 马永红、钱洪、袁立.有效的信息共享是供应链管理的基石[J] .化工管理;2003(6).
VMI的优点体现在两个方面:其一,有效地 消除了长鞭效应,并可提高服务水平和库存周转; 其二,对分销商角色的变革,使之从传统的赚取买 卖差价向提供高质量的服务转变,共同为目标客户 服务。
4结束语 化工企业的设备及设备零配件的库存管理占整
个化工企业运行成本的较大比率,在这一领域提高 服务水平,降低成本大有可为。在生产原材料的供 应中,运用先进的供应链管理的理念已很普遍,但 在技术物资供应领域却实施得不够,在这方面加强 管理、开展合作,前景将会是很好的。
该装置为连续化生产装置,年开工周期为 8400小时。
装置的设计规模按处理原料液化石油气的能力 为15万吨/年,操作弹性60~120%。 2.2原料液化石油气的组成数据:
原料的组成Irod%)
2.3产品要求 该装置的主要产品为: ①精丙烯纯度≥99。6%(m01%),经进一步脱
水干燥、精制后满足工业用精丙烯的质量指标 万方数据
精丙烯塔A、B在工艺模型中为l台精馏塔, 但由于塔板数多达200层,在实际工程制造中无法 实现,因此精丙烯塔采用双塔流程,即精丙烯塔A 与精丙烯塔B。精丙烯塔A为精馏塔的提馏段与精 馏段、精丙烯塔B则全部为精馏段,用工艺管道 与机泵设备实现两塔之间的物料传递。
2分馏装置设计参数的确定 2.1设计规模
万方数据
化学工程与装备
2007年
第5期
·35 ·
塔板上的液面梯度。塔板上存在液面梯度。将使汽 体分布不均匀。此外,塔板上除含有矩形导向浮阕 外,还含有适当配比的梯形导向浮阀(组合导向浮 阀塔板上梯形导向浮阀数与塔板上的浮阀总数之 比,称为组合配比,简称配比,以K表示)。当液 流强度较大或液体流路较长时,K值适当增大,反 之,K值适当减小,以适应消除塔板上的液面梯度 的需要。
25万吨气体分馏装置工艺管道施工方案
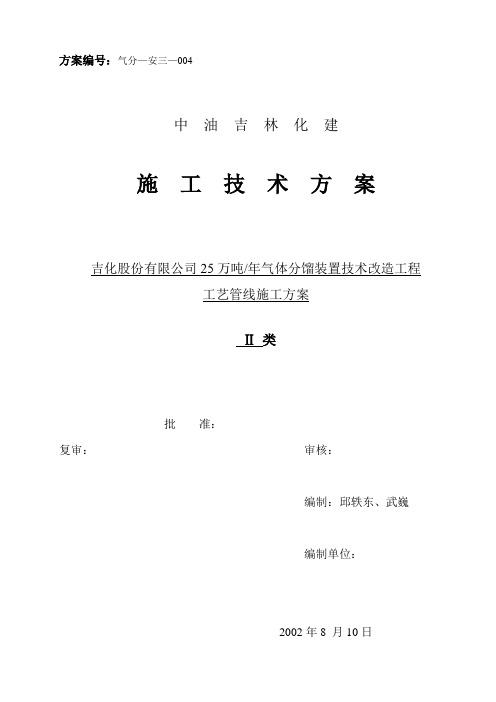
方案编号:气分—安三—004中油吉林化建施工技术方案吉化股份有限公司25万吨/年气体分馏装置技术改造工程工艺管线施工方案Ⅱ类批准:复审:审核:编制:邱轶东、武巍编制单位:2002年8 月10日目录一、编制说明二、编制依据三、工程概况四、施工准备五、施工方法及技术要求六、施工技术组织措施计划七、资源需求计划八、施工进度计划一、编制说明本方案仅适用于吉化股份有限公司炼油厂25万吨/年气体分馏装置技术改造工程中工艺管道施工。
二、编制依据1.25万吨/年气体分馏装置设计文件2.《工业安装工程质量检验评定统一标准》GB50252—943.《工业金属管道工程质量检验评定标准》GB50184—934.《工业金属管道工程施工及验收规范》GB50235—975.《现场设备、工业管道焊接工程施工及验收规范》GB50236—986.《石油化工剧毒、可燃介质管道工程施工及验收规范》SH3501—977.《石油化工工程焊接工艺评定标准》SHJ509—888.《石油化工钢制管道工程施工工艺标准》SHJ517—919.《阀门检验与管理规程》SHJ518—9110.《石油化工施工安全技术规程》SH3505—199911.中油吉林化建《安全技术操作规程》Q/JH121.11004—92三、工程概况本工程建设单位为吉化股份有限公司炼油厂,由中国石油天然气华东勘察设计院炼油厂分院设计,中油吉林化建安装三公司施工。
四、施工准备1.设置暂设,组织材料及加工件;2.组织准备参加施工的劳动力、工机具以及手段用料;3.施工图审核;4.根据施工图编制施工技术方案,下发技术交底和施工图。
五、施工方法1.施工程序现场配管管道预制2.施工方法及技术要求2.1 材料验收材料包括管道组成件、管道支承件和焊接材料2.1.1 材料必须具有制造厂的质量证明书,其质量不得低于国家现行标准的规定。
2.1.2 材料的材质、规格、型号、质量应符合设计文件的规定,并应按国家现行标准进行外观检验,不合格者不得用;a 材料无裂纹、缩孔、夹渣、折叠、重皮等缺陷;b 锈蚀、凹陷及其它机械损伤的深度,不应超过产品相应标准允许的壁厚负偏差;c 检验合格的材料按照规定分门别类摆放,并设有明显标识。
炼油厂气体分馏装置用能的集成和优化

I n t e g r a t i o n a n d Op t i mi z a io t n o f En e r g y Us e i n Ga s Fr a c t i o n a t i o n Pl a n t o f Re in f e r y
1 基本设备概述 Q c 的热量 ,该蒸馏 塔可 由 图上 的 四边形 来表示 。可 以通 本 文 研 究 的气 体 分馏 装 置 由 6 塔和 1 3 个 热 交换 器 组成 。 过 在上 下范 围 内通 过移动 温度 四边形 的从而 改变 面积大 小来 具体 的系统示意 图如 图 1 所示。 增加 或 降低压力 。 已知热效应和冷 加工之 间的传热 温差为 7 2 ~ 1 2 4 " C,较 大的温差可 能会导致 能量损失 较大 。因此可 以使用 多效蒸馏来 降低 温差,从而降低能量损失 。 3 节 能 工 程 在 对应 用过程 中能量集 成技 术的设 备进 行分析 时,通 过 对 以下过程进行修 改,可 以显着改善整个e ,S O i t i s v e y r i mp o r t a n t t o s t u d y t h e e n e r g y s a v i n g o f he t d e v i c e .
化 工 设 计 通 讯
C h e mi c a l En g i n e e r i n g De s i g n Co mmu n i c a t i o n s
工艺与设备
Te c h n o l o g y a n d Eq u i p me n t
第4 3 卷第4 期
2 0 1 7 薤4 , 9
炼 油厂气体 分馏 装置用 能的集成 和优化
李宜蓉 ,张红晨
气体分馏装置能量利用现状及优化措施

气体分馏装置能量利用现状及优化措施摘要:气体分馏装置工作是根据不同种类液体的不同沸点进行分离,在实际工作中由于涉及多组分,因此对精度要求也是各不相同。
所以,实际工作中能量管理仍有很大难度。
例如:催化裂化为实现对非烃气体的分离,实际工作过程中会产生大量的丙烯,造成混合气和原料浪费。
为此,有必要对企业技术创新进行优化,以保证气体分馏装置的高能效。
关键词:气体分馏;能量利用;优化途径前言气体分馏装置对提高能效具有十分重要的意义,针对目前气体分馏技术在国内外的应用情况,对气体分馏装置的基本原理、工艺流程进行分析,并对气体分馏装置的能量利用状况进行分析,进而提出能量利用优化措施。
1、气体分馏装置的基本原理烷烃与烯烃是液化石油气的重要组分,其沸点很低。
由于丙烷沸点为-0℃,所以,一般情况下,液化气为气态,但在一定外界压力下,液化气会转变为液态。
由于液化气中各成分具有不同沸点,因此可以采用蒸馏法将其分离。
由于需要用精馏塔,所以在同样条件下,液体碳氢化合物的沸点是不一样的。
比如:丙烯具有比丙烃更低的沸点。
所以,在对液化气进行精馏时,要尽量选用多个精馏塔。
在此基础上,进一步提高蒸馏试验的精确度,达到精确度要求。
2、气体分馏装置工艺流程的简要概述在进行气体分馏时,要先预备3-4个精馏塔,被分离的气体由 n个单体组成,则至少设置n-1个精馏塔,在实际工作中,可按实际要求作适当调节[1]。
以5种类型的气体为例对工艺流程进行描述:第一,将液化气体用空气泵送入塔中,在高压作用下将其分离出来;第二,经冷凝后的乙烷、丙烷由塔顶排出,多数经低温回流,其余的则由塔顶排出。
在一定的压力条件下,可各组分进行有效分离;第三,将丙烷与丙烯分开后,将剩余的组分送入丙烯塔中,在塔顶对乙烷进行蒸馏,在塔底对丙烷组分进行分离;第四,从脱丙烷塔的塔底放出丁烷、戊烷,而丁烷、戊烷则由塔中除去异丁烷而得到分离。
第五,脱异丁烷的馏分,以戊烷为主,被分离到癸烷塔中。
气体制取装置的改进和创新

选用高效能设备
采用高效能压缩机、涡轮 机等设备,提高设备效率, 降低能耗。
智能化控制
通过智能化控制技术,实 时监测和控制气体制取过 程,实现能源的优化利用。
提高效率
改进工艺流程
优化气体制取的工艺流程, 减少不必要的环节和损失, 提高制气效率。
选用高性能催化剂
采用新型高性能催化剂, 降低反应活化能,提高反 应速率,从而提高制气效 率。
作用
气体制取装置在科学研究、工业生产 、环境保护等领域具有广泛的应用, 对于满足气体需求、推动科技进步和 经济发展具有重要意义。
气体制取装置的种类和原理
种类
根据不同的制气原理和应用需求,气体制取装置有多种类型 ,如化学反应制气装置、气体分离装置、生物发酵制气装置 等。
原理
不同类型的制气装置具有不同的制气原理。化学反应制气装 置基于化学反应产生气体,气体分离装置则利用各种物理或 化学方法将混合气体中的不同组分进行分离,生物发酵制气 装置则是利用微生物发酵产生气体。
06
未来展望
技术发展趋势
1 2 3
自动化与智能化
随着人工智能和自动化技术的发展,气体制取装 置将更加智能化,能够实现自动控制、智能监测 和故障诊断等功能。
高效与环保
随着环保意识的提高,气体制取装置将更加注重 高效和环保,采用新型的分离技术和节能技术, 降低能耗和排放。
定制化与个性化
根据不同用户的需求,气体制取装置将更加定制 化和个性化,能够满足不同用户的特殊需求。
推广价值
该装置具有较高的推广价值,可应用于其他类似的气体生产过程中, 提高整个行业的生产效率和产品质量。
成功案例二
创新点
该装置利用生物质废弃物作为原料,通过生物发酵技术制备气体,实现了废弃物的资源化 利用。
气分MTBE装置技术讲座.

名 称
单耗 /吨原料
设 计
1996年 (标定)
2000年 (标定)
循环水
t/t
61.19
94.00
108.04
电
Kw.h(度)/t
11.84
9.15
5.276
1.0Mpa蒸汽
t/t
0.23
0.90
0.905
110℃热水
t/t
1分馏装置的任务是以液化石油气为原料生产合格的精丙烯、丙烷和混合C4馏分,从原料到产品这些物质具有闪点低、引烃能量小、爆炸下限低、爆炸范围大等特点,一旦发生泄漏,遇着火源就有燃烧、爆炸的危险,所以它们均属于易燃易爆危险品。根据国家有关规定,本装置属于甲A类火灾危险的场所。
五、装置工艺原则流程图
C2.C3 C2 C=3 C2C3C4C5 C3 C4C5 CO3
二、装置的工艺特点
2、采用低醇烯比将有利于减少DME(付反应产物)的生成以满足下游装置进料的要求。 3、降低醇烯比还有利于减少甲醇回收系统的设备尺寸及能耗。
三、装置的基本原理
MTBE(甲基叔丁基醚)是用于生产新配方汽油的优良调和组分,是实施汽油无铅化的重要手段之一。它可以代替四乙基铅作为高辛烷值汽油的添加剂,其马达法 辛烷值101,研究法辛烷值118。 MTBE的合成是在催化剂的作用下,混合C4中的异丁烯和甲醇反应制得的。 具体反应过程如下,其反应是一个可逆放热反应。 CH3OH + (CH3)C=CH2 === CH3O-C(CH3)3
六、装置的工艺控制指标 1、原料及产品质量控制指标
项 目
设计指标
实际控制
碳二含量%(重)