气 分 装 置
气体分馏装置节能降耗措施探究

气体分馏装置节能降耗措施探究发布时间:2021-12-16T02:33:46.346Z 来源:《科技新时代》2021年10期作者:黄琦琳[导读] 辽河石化公司气体分馏装置在2012装置大检修时对改装置的热水循环系统进行了优化改造,改造前装置使用的热水是由供水车间直接输送,经过装置1.0MPa蒸汽加热器进行加热一般要求加热至95℃以上,然后由装置热水输送机泵送至各个换热设备,经换热后再用机泵直接送出装置进入热水管网。
中国石油天然气集团有限公司辽河石化分公司规划计划处辽宁省盘锦市 124010摘要为了降低气分装置的运行能耗提高装置经济效益,运行部在两次设备工艺大检修时对装置进行了优化改造,改造过程中充分考虑装置节能降耗问题。
关键词气体分馏节能降耗优化改造降耗措施1.前言气分装置在日常生产过程中实际运行能耗比设计时的能耗高很多,每年该装置的能耗费用所占的比例相对较高。
为了降低气分装置能耗,运行部先后对装置的热水循环系统及换热流程进行优化改造。
并对装置各塔的加热流程进行了重新优化,如在脱丙烷塔底增设了一台重沸器该重沸器利用了催化裂化装置分馏塔顶循环油为热源,这样联合改造不仅使催化装置循环油温度得到了降低还充分节约了气分装置大量蒸汽降低了装置能耗。
接下来本文将对气体分馏装置技术改造过程中的一些节能降耗措施进行探讨。
2.气体分馏装置技术改造过程中的一些节能降耗措施2.1 改造循环热水系统,充分利用低温余热辽河石化公司气体分馏装置在2012装置大检修时对改装置的热水循环系统进行了优化改造,改造前装置使用的热水是由供水车间直接输送,经过装置1.0MPa蒸汽加热器进行加热一般要求加热至95℃以上,然后由装置热水输送机泵送至各个换热设备,经换热后再用机泵直接送出装置进入热水管网。
改造前的热水循环系统会由于热水经过换热以后直接送出装置造成热水低温余热的浪费,为了装置的节能降耗运行部对热水循环系统进行了优化改造。
改造后装置增设了一个热水储罐,具体流程为热水储罐的热水先经过低温热水泵将70℃左右的低温热水经系统管网送至催化和常压装置进行换热,换热后热水温度可升高至84.8℃左右,然后进入气分装置在经过1.0MPa蒸汽加热器加热至95℃以上送至气分装置各个冷换设备,经换热后返回热水储罐,当热水储罐水位过低时可向其补充除盐水。
气体分馏装置的能耗分析与节能措施研讨
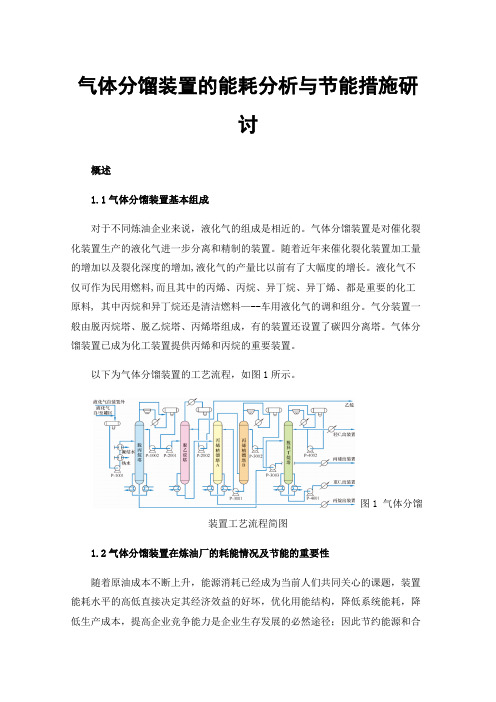
气体分馏装置的能耗分析与节能措施研讨概述1.1气体分馏装置基本组成对于不同炼油企业来说,液化气的组成是相近的。
气体分馏装置是对催化裂化装置生产的液化气进一步分离和精制的装置。
随着近年来催化裂化装置加工量的增加以及裂化深度的增加,液化气的产量比以前有了大幅度的增长。
液化气不仅可作为民用燃料,而且其中的丙烯、丙烷、异丁烷、异丁烯、都是重要的化工原料, 其中丙烷和异丁烷还是清洁燃料—--车用液化气的调和组分。
气分装置一般由脱丙烷塔、脱乙烷塔、丙烯塔组成,有的装置还设置了碳四分离塔。
气体分馏装置已成为化工装置提供丙烯和丙烷的重要装置。
以下为气体分馏装置的工艺流程,如图1所示。
图1 气体分馏装置工艺流程简图1.2气体分馏装置在炼油厂的耗能情况及节能的重要性随着原油成本不断上升,能源消耗已经成为当前人们共同关心的课题,装置能耗水平的高低直接决定其经济效益的好坏,优化用能结构,降低系统能耗,降低生产成本,提高企业竞争能力是企业生存发展的必然途径;因此节约能源和合理利用能源为大势所趋,势在必行。
气分装置总能耗一般占全厂总能耗的15-17%,其用能水平直接关系到整个炼厂的经济效益,因此气分装置的节能降耗工作意义重大。
1.3气体分馏装置的能耗组成及用能分析1.3.1气体分馏装置的用能形式;目前国内气体分馏装置用能有4种形式,分别为;1)采用蒸汽作为气分再沸器热源气体分馏塔塔底再沸器多用0.45 MPa蒸汽作热源。
该形式流程简单,但能耗高,适宜小型装置或复杂系数较低的炼厂。
2)采用其它装置工艺物流的低温余热催化裂化装置与气体分馏装置就近联合布置,同步开停工,实现装置间的热联合是节能降耗的有效途径。
催化裂化分馏塔顶循环回流的低温热足以作为气体分馏装置的低温热源。
其利用方式有2种。
①直接采用顶循油气作为气体分馏塔热源;②利用软化水与顶循换热,热水作为气体分馏塔热源,可大大减少蒸汽的消耗。
后者相比操作可靠,安全性好;直接换热可减少换热器投资,但对设备的性能要求较高,存在一定的运行风险。
气体分馏装置操作规程

气体分偕装置操作规程目录第一章气分岗位操作规程1.1岗位划分及岗位职责 (8)1.2 工艺系统说明 (9)1.3装置开工方案............................... (10 )1.4装置开工吹扫流程.. (12)1.5装置开工水冲洗 (12)1.6 蒸汽吹扫贯通 (15)1.7氮气气密试压 (16)1.8氮气置换 (19)1.9烧置换................................. (12 )1.10开工步骤 (24)1.11气分岗位操作法 (26)1.12 停工 (30)1.13紧急停工 (35)1.14事故处理 (35)1.15 盲板表 (38)第二章产品精制岗位操作规程2.1产品精制岗位任务 (39)2.2工艺技术说明 (39)2.3装置开工方案 (45)2.4吹扫试压 (54)2.5开工步骤 (54)2.6进料开工 (56)2.7 正常运行操作 (57)2.8非正常操作 (61)2.9 停工 (63)2.10 紧急停工 (65)2.11仪表位号 (69)第三章液化气液膜脱硫醇及碱液氧化再生装置操作规程。
工艺原理、工艺特点 (70)1.1.1 概述 (70)1.1.2 工艺原理 (70)1.1.3 工艺特点 (71)1.2操作变量分析 (71)1.2.1 原料及产品质量技术指标 (71)1.2.2 主要工艺操作条件 (71)2.1液化气脱硫醇单元 (72)2.1.1 液膜脱硫醇反应器 (72)2.1.2 精细过滤器 (73)2.2液化气液膜水洗单元 (74)2.3碱液高效氧化再生单元 (75)2.3.1 碱液氧化塔 (76)2.3.2 尾气水洗塔 (78)2.3.3 氧化后碱液气提塔 (78)2.3.4 二硫化物储罐 (79)3. 开车准备工作程序 (80)3.1设备安装 (80)3.2系统冲洗与吹扫 (80)3.3系统管线冲洗与吹扫 (80)3.4设备冲洗与吹扫 (80)3.5设备调试验收 (80)4. .............................................................................. 开车程序(81)4.1脱硫醇单元开工过程 (81)4.1.1 新鲜水置换 (81)4.1.2 氮气置换 (81)4.1.3 新鲜水与碱液置换 (81)4.1.4 液化气置换 (82)4.2水洗单元开工过程 (82)4.2.1 除盐水置换 (82)4.2.2 液化气置换 (82)4.3建立正常操作循环 (82)4.4碱液氧化单元开工过程 (82)5. ................................................................................... 正常停车程序(83) 5.1正常停车. (83)5.2临时停车 (83)5.3紧急停车和故障排查 (83)6. ................................................................................ 事故处理原则(84)7. .............................................................................. 催化剂装卸(86)8. 采样 (86)9. 工艺危险因素分析及控制措施 (87)9.1液化气 (87)9.1.1 液化气组成 (87)9.1.2 液化气物理化学性能 (87)9.1.3 安全注意事项 (88)9.2 碱液 (89)9.2.1 碱液成分 (89)9.2.2 碱液物理化学性能 (89)9.2.3 碱液安全使用措施 (89)9.3二硫化物 (89)9.3.1 二硫化物来源 (89)9.3.2 二甲基二硫物理化学性质 (89)第四章装置安全规程 (90)4.1人身安全十大禁令 (90)4 .2 防火防爆十大禁令 (90)4.3装置开工及正常生产安全规程 (91)4.4装置停工安全规程 (93)4.5装置检修安全规程 (94)4.6装置安全常识 (96)4.7酸碱操作规定 (98)一、气分岗位职责范围精制液态烧通过气分装置处理,分离出丙烯、丙烷和碳四。
气分装置节能降耗优化措施

气分装置节能降耗优化措施在全球经济一体化和世界经济的迅速发展的背景下,节约能源,降本增效,是一项长期而紧迫的战略任务,也是未来可持续发展的必然选择。
气体分馏装置的主要作用是将催化裂化装置来的液化烃分离出丙烯、丙烷及混合碳四作为聚丙烯与MTBE装置的原料。
分离过程采用精馏方式,能量使用密集,降低装置能耗。
分析气体分馏装置单位能耗偏高的原因,找出不合理因素,采用优化操作参数、方案及换热流程优化等措施,在保证产品质量与生产效率的同时,降低能耗。
因此,几个重要操作参数进行调整,优化工艺条件,有效提高了丙烯产品的收率和纯度,提升了装置运行平稳率,降低了成本和能耗,增加了经济效益。
标签:气分装置;节能降耗;优化措施气分装置虽然具有以下优势:工艺流程简单,生产运行易于控制,但是,降低气分装置能耗,已成为目前国内同类装置面临的一个共同课题。
能源作为人类社会生存和社会经济发展的重要物质基础,随着全球经济一体化和世界经济的迅速发展,资源已是全人类共同关心的重要问题和面临的严峻挑战。
节约能源,降本增效,是一项长期而紧迫的战略任务,也是未来可持续发展的必然选择。
1 装置简介我们中海油东方石化有限责任公司,气体分馏装置设计加工量60万t/年,采用常规三塔流程,原料液态烃来自上游催化装置,由脱丙烷塔分离成碳二、碳三和碳四馏分。
碳二、碳三馏分经脱乙烷塔脱除碳二后,进入丙烯精馏塔分离出丙烯和丙烷馏分。
丙烷馏分外销,碳四馏分和丙烯作为聚丙烯和MTBE装置原料。
主要能源消耗是塔底热源(蒸汽、低温热)和机泵耗能。
开工投产以来,装置运行平稳,丙烯纯度≥99.6%,主要技术经济指标达到设计要求,装置已通过采用高效浮阀塔盘、应用屏蔽泵、干气密封泵、表面蒸发式空冷等新技术新设备,充分利用装置内部热源给原料液态烃换热、与催化装置进行热联合等措施,有效降低装置能耗。
但受上游装置生产方案及市场影响,投产后相当长时间液态烃加工量仅为设计能力的68%左右,投产当年加工量更仅有设计能力的62%,处于装置加工弹性范围60%~110%的下限。
气分MTBE及品精制装置基本原理概述

产品精制、气体分馆及MTBE装置基本原理概述2010年4月30日第一章第二章第三章第四章第五章总述干气、液化气脱硫轻油、液化气脱硫醇气体分MTBE合成第一章总述1・1双脱装置作用:1)处理来自催化装置的干气,脱除其中的硫化氢,脱硫后的气体去燃料气管网和制氢装置;2)处理来自催化装置的液化气,脱除其中的硫化氢和硫醇,为下游气体分憎装置提供原料;3)处理来自催化装置的汽油,脱除汽油中的硫醇硫,满足汽油质量对硫醇硫的要求。
1.2气分装置作用:来自催化装置并经过脱硫、脱硫醇装置精制后的液化气经过气体分憎装置精憎后,生产丙烯和丙烷产品。
混合碳四作为下游MTBE装置的原料。
1.3MTBE装置作用:来自气分装置的混合碳四与外购甲醇经过MTBE装置处理后主要产品为MTBE产品,MTBE纯度>98% (重)(含C5),该产品辛烷值高,且调合性能优良,可用作高辛烷值无铅车用汽油的添加组分,乂是汽油中所需氧含量的最重要来源。
装置的副产品为未反应C4憎分,用作民用液化气燃料。
第二章干气、液化气脱硫2.1基本原理:吸收与解吸炼油生产过程产生的炼厂气是多种组分的混合物,并可能含有杂质。
只有将它们分离、提纯、精制,才能进人下一道炼制工序或作为化工原料和其他用途。
为实现分离过程,炼油厂广泛采用吸收和解吸的方法。
2.1.1基本概念(1)物系的相在物质体系中,具有相同物理和化学性质的均匀部分,称为相。
其分散度达到分子大小的数量级。
相与相之间有明确的分界面。
如装在压力容器内的液化石油气,上部的气体称为气相,下部的液体称为液相。
由浮在水面上的冰块及水、蒸汽所组成的物系,冰块称为固相,水称为液相,上部蒸汽则称为气相。
这三者虽具有相同的化学性质,但物理性质却不一样,因此是三个相。
由油和水组成的物系,如果分了层,上面油的部分称为油相,下面水的部分称为水相。
虽然都是液体,但属于不同的相。
乂如两种或两种以上的物质组成的溶液,因其任何部分都是均匀的,所以整个溶液就是一个相。
气体分馏装置的基本原理及工艺流程

气体分馏装置的基本原理及工艺流程作者:董兴鑫来源:《中国科技博览》2014年第11期一气体分馏的重要性炼厂气是石油化工过程中,特别是破坏加工过程中产生的各种气体的总称。
包括热裂化气、催化裂化气、催化裂解气、重整气、加氢裂化气等,炼厂气的产率一般占所加工原油的5~10%。
这些气体的组成较为复杂,主要有C1~C4的烷烃和烯烃,其中有少量的二烯烃和C5以上重组分,此外还有少量的非烃类气体,如:CO、H2、CO2、H2S和有机硫(RSH、COS)等。
炼厂气过去大多是用作工业和民用燃料,少部分加工成为高辛烷值汽油和航空汽油的组成,随着石油化学工业的发展,炼厂气已成为宝贵的化工原料。
炼厂气作为化工原料,必须进行分离,分离的方法很多,就其本质来说可以分为两类,一类是物理分离法,即利用烃类的物理性质的差别进行分离。
如:利用烃类的饱和蒸汽压、沸点不同而进行气体分离过程,有些合成过程对气体纯度要求较高时,则需要高效率的气体分离,如吸附、超精馏、抽提精馏、共沸蒸馏等;另一类方法是化学方法,既利用化学反应的方法将它们分离,如化学吸附和分子筛分离。
目前,我国绝大多数炼油厂采用气体分离装置对炼厂气进行分离,以制取丙烷、丁烷、异丁烷,可以说是以炼油厂气为原料的石油化工生产的重要装置。
一、气体分馏的基本原理炼厂液化气中的主要成分是C3、C4的烷烃和烯烃,即丙烷、丙烯、丁烷、丁烯等,这些烃的沸点很低,如丙烷的沸点是—42.07℃,丁烷为—0.5℃,异丁烯为—6.9℃,在常温常压下均为气体,但在一定的压力下(2.0MPa以上)可呈液态。
由于它们的沸点不同,可利用精馏的力法将其进行分离”所以气体分馏是在几个精馏塔中进行的。
由于各个气体烃之间的沸点差别很小,如丙烯的沸点为—47.7℃.比丙烷低4.6℃,所以要将它们单独分出,就必须采用塔板数很多(一般几十、甚至上百)、分馏精确度较高的精馏塔。
二、气体分馏的工艺流程气体分馏装置中的精馏塔一般为三个或四个,少数为五个,实际中可根据生产需要确定精馏塔的个数。
气体分离装置工艺流程简介-刘兴金教材

V402 V403
T
F 4
混 合 器
F 4
F 4 0 1
4 0 3
0 0 1 A 2
V 4 0 1
C4 泵
C4 外送泵
B
甲醇泵
MTBE 外送泵
汽油脱硫醇工艺原理
工艺原理:利用含有催化剂(磺化酞菁钴) 的碱液萃取汽油中硫醇的过程。以使汽油 含硫到达小于150PPM。
汽油系统工艺流程图
谢 谢!
胺脱工艺流程说明
1、含硫干气进入干气分液罐(V101A)分离出杂质及所携带的部分轻油进入干 气脱硫塔(T101A)下部,与自塔顶上部引入的温度为40℃左右的乙醇胺溶 液(贫液)逆向接触,乙醇胺吸收气体中的H2S和CO2,气体得到精制,净 化后的气体自塔顶进入净化分离罐(V102A),分离出携带的胺液后出装置 含硫液态烃进入液态烃脱硫塔(T102A)下部,与自塔顶部引入的40℃左右的乙 醇胺溶液逆向接触,乙醇胺吸收液态烃中的H2S和CO2,液态烃得到精制, 净化后的液态烃经缓冲罐(V108A)分离出携带的胺液后出装置。 自T101A、T102A底引出的乙醇胺溶液(富液)借助再生塔的压力自塔底压出, 经过富液过滤器除去杂质后与贫富液换热器(E101A)换热后进入溶剂再生 塔上部。在再生塔内与下部上来的酸性气直接接触,再生塔底重沸器( E102A)提供热源,富液在115℃左右时,酸性气分离出来酸性气自塔顶排 出经塔顶冷却器(E103A)冷却后进入酸性气分液罐(V105A),在分离罐 分离出液体,液体再经酸性水回流泵加压送回塔内打回流,分离出的酸性气 至火炬。 自再生塔底重沸器引出的贫液经贫富液换热器(E101)与富液换热后再经贫液 冷却器(E104)冷却后返回溶剂罐(V103),经贫液泵(P101)打入吸收 塔循环使用。 新鲜乙醇胺溶液经抽空器抽入V104(乙醇胺配制罐)经P103打入V103,注入一 定量的水,即可得一定浓度的乙醇胺液。 乙醇胺溶液的浓度通常为8-15%;浓度越低,溶液的“发泡”现象越不易发生 。
二气分装置概况(九江石化)

II套气分(30万吨/年气体分馏装置)流程简介1、车间简介1.6×105t/a气体分馏装置于1998年2月26日投料试车一次成功,3月4日拿出合格产品,同年5月经过标定,装置操作参数、产品质量、能耗、环保指标全部达到设计要求。
2004年8月,对其进行了扩能改造,改造后装置处理能力可达3×105t/a,塔-301、塔-302由单溢流浮阀塔盘改为高效微分塔盘,塔-303、塔-304由双溢流浮阀塔盘改为高效立体传质塔盘,增设了E-307/5.6.6、E-306/2、E-304/1、增加了化肥低压蒸汽至二气管线,丙烯塔增设了气相色谱仪,丙烯塔操作条件有较大改变,机泵设备规格及性能参数有较多改变。
因塔-303、塔-304塔盘达不到工艺生产要求,2007年11月将原河北工学院的CTST塔盘,更换为南京凯宁公司的复合孔高效塔盘,考虑塔-301顶冷却负荷不足,将塔-302顶E-306/2改为塔-301顶E-305/1,增设了塔-301底去MTBE装置进料线。
2008年9月,装置停工进行低温热利用改造,塔-301底重沸器E-302实现了可用溶脱装置来的高温热媒水加热;增设了蒸汽-热媒水换热器E-300;增设了溴化锂机组M-301/1、2,将17℃除盐水变成7℃冷冻水,用于E-307/2、E307/4、冷-102和焦化车间做冷却介质;E-304/1增加了FIC-347控制阀。
2009年3月增设了塔-301底物料-进料换热器E-301/A。
2011年9月增设溶剂脱沥青装置来的高温热媒水压力控制阀组。
装置现有倒班职工37人(两套气分),(溶脱车间管理人员29人),目前实行五班三倒。
在卓越文化的引领下,溶脱人卓越理念:卓越引领、和谐融通、强基固本、同创一流。
2、装置概况2.1 本装置以催化裂化装置所产液化气为原料,以生产丙烯为主要产品,装置的公称规模为年加工液化气3×105t/a。
本装置主要生产任务是生产聚合级丙烯,由于原料在本装置上游经脱硫化氢和硫醇外,未进一步精制,本装置只能保证产品纯度达99.0%,产品中微量水等在丙烯预精制装置进行再处理。
- 1、下载文档前请自行甄别文档内容的完整性,平台不提供额外的编辑、内容补充、找答案等附加服务。
- 2、"仅部分预览"的文档,不可在线预览部分如存在完整性等问题,可反馈申请退款(可完整预览的文档不适用该条件!)。
- 3、如文档侵犯您的权益,请联系客服反馈,我们会尽快为您处理(人工客服工作时间:9:00-18:30)。
气分装置
• • • • • • • • • • 气分装置工艺参数控制指标 温度: T1顶: 47±1℃ T1底: 105±2℃ T2顶: 46±1℃ T2底: 58±1℃ T3顶: 51±1℃ T3底: 58±1℃ T4顶: 47±0.5℃ T4底: 50±1℃
气分装置
• • • • 压力: T1顶: 1.85±0.05Mpa T2顶: 2.50±0.05Mpa T4顶: 1.85±0.05Mpa
气分装置
• 经脱丙烷塔顶冷却器冷到38℃后,进入脱 丙烷塔回流罐,冷凝液一部分用脱丙烷塔 回流泵抽出,打到T501顶作为塔顶回流, 另一部分作为脱乙烷塔(T502)进料。罐 内不凝气由压控放入高压瓦斯管网。
气分装置
• 2、进入到脱乙烷塔(T502)中的≤C3馏份C1、 /C2馏份及少量C3馏份从塔顶分离出来,经冷 凝器冷凝后,进入脱乙烷塔顶回流罐,罐内不凝 气由灌顶压控调节阀放入高压瓦斯管网回流罐液 相用脱乙烷塔回流泵抽出,作为脱乙烷塔顶回流, 脱乙烷塔底C3馏份经塔底重沸器用催化装置来的 顶循汽油加热到60℃利用热虹吸是原理,汽液混 相返回脱乙烷塔,以提供传质传热所需的热量, 重沸器底部C3馏份作为进料靠自压进入粗丙烯塔 T503.
气分装置
• 馏分中的碳二组分,为下游精分岗位和尾分岗位 的平稳生产创造条件;严格执行本岗位的工艺操 作指标,按生产方案要求,控制合理的塔底温度 和塔顶温度,以及合理的回流比,及时和气体脱 硫装置以及丙烯球罐保持生产联系,以保证原料 量的稳定,保证脱丙烷塔和脱乙烷塔的正常生产; 负责本岗位的开停工和事故处理;确保和二套催 化装置热联合工艺的正常生产;做好本岗位工艺 设备及相关的工艺管线的巡检和日常维护工作, 做好交接班和原始记录;调节过程要认真细致, 避免大幅度波动;完成车间下达的有关生产指令 和任务。
气分装置
• 3、进入到粗丙烯塔T503中的C3馏份在塔 内传质传热进行分离。C3馏份流入塔底经 粗丙烯塔底重沸器用蒸汽加热到63℃左右, 利用热虹吸式原理,汽液混相返回粗丙烯 塔以提供分馏所需的热量,重沸器底部丙 烷馏份通过丙烷冷却器冷却后送到成品罐 区。
气分装置
• 4、粗丙烯塔顶馏份进入精丙烯塔T504底部, 而精丙烯塔T504馏份经塔底泵抽出返回粗 丙烯塔顶部作为顶回流,经过粗丙烯塔 T503.精丙烯塔T504分离出来的丙烯馏份从 精丙烯塔顶流出,经精丙烯塔顶冷凝冷却 器冷却到38℃后,进入精丙烯塔回流罐, 罐内不凝气由罐顶压控调节阀放入高压瓦 斯管网,回流罐内液态丙烯经精丙烯塔回 流泵抽出一部分作为精丙烯塔顶回流,另 一部分送到成品罐区。
气分装置
气分装置
气分装置
气分装置
气分装置
• • • • • 所有液位控制为50±5% T1底: C3=含量不高于0.5% T2顶: C2排放以T4顶不含C2为准 T3底: C3=含量不高于0.5% T4顶: C3=含量不小于99.5%
气分装置
• 三、工艺流程 • 1、自催化碱洗后的液化气,经催化液态烃泵送到 原料缓冲罐.再由脱丙烷塔进料泵抽出,经碳四—原 料换热器,再经原料预热器与从催化装置来的顶循 汽油换热到70度后,进入脱丙烷塔(T-501)中部 进料段.在脱丙烷塔内传质传热进行分离,液态烃中 ≥C4馏份流入塔底,脱丙烷塔底液相经塔底重沸 器用蒸汽加热到105℃左右,利用热虹吸式原理, 一部分汽液混相返回脱丙烷塔以提供传质传热所 需的热量,重沸器底≥C4馏份与原料换热并冷却 后出装置,C2、C3馏份从塔顶分离出去,
气分装置
一、装置简介 松原油化工股份有限公司12×104t /a气体分馏装置采用四塔工艺流程, 比较合理。
气分装置
• 二、生产方法及反应机理: • 本车间原料为低沸点烃类混合物,是利用精馏方 法使混合物得到分离的。其基本原理是利用被分 离的组分具有不同的挥发度,即各组分在同一压 力下具有不同的沸点将其分离的,其实质是不平 衡的汽液两项在塔盘上多次逆向接触,多次进行部 分汽化和部分冷凝,传质传热,使气相中轻组分 浓度不断提高,液相中重组分浓度不断提高,从 而使混合物得到分离初分岗位的任务是将净化液 态烃分离为纯度合格的混合碳二、碳三馏分和混 合碳四、碳五馏分,并分离出纯度合格的混合碳 三