风力机叶片动力学响应分析
风力发电机叶片的动力学分析
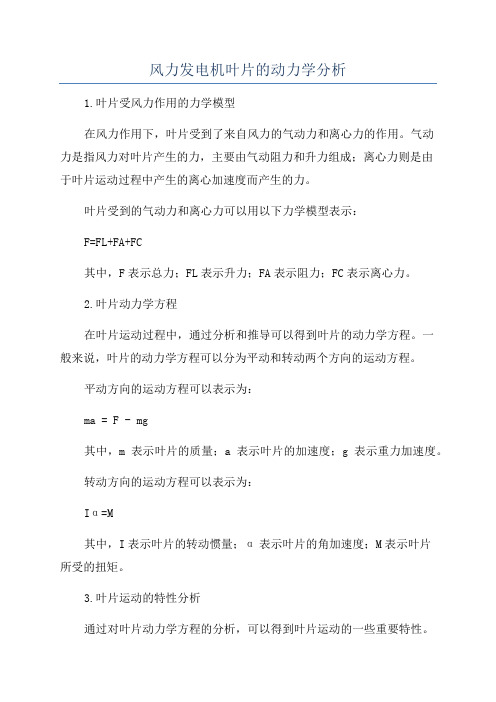
风力发电机叶片的动力学分析1.叶片受风力作用的力学模型在风力作用下,叶片受到了来自风力的气动力和离心力的作用。
气动力是指风力对叶片产生的力,主要由气动阻力和升力组成;离心力则是由于叶片运动过程中产生的离心加速度而产生的力。
叶片受到的气动力和离心力可以用以下力学模型表示:F=FL+FA+FC其中,F表示总力;FL表示升力;FA表示阻力;FC表示离心力。
2.叶片动力学方程在叶片运动过程中,通过分析和推导可以得到叶片的动力学方程。
一般来说,叶片的动力学方程可以分为平动和转动两个方向的运动方程。
平动方向的运动方程可以表示为:ma = F - mg其中,m表示叶片的质量;a表示叶片的加速度;g表示重力加速度。
转动方向的运动方程可以表示为:Iα=M其中,I表示叶片的转动惯量;α表示叶片的角加速度;M表示叶片所受的扭矩。
3.叶片运动的特性分析通过对叶片动力学方程的分析,可以得到叶片运动的一些重要特性。
首先,叶片的运动速度和加速度是随风速和叶片位置的变化而变化的。
当风速较大时,叶片的运动速度和加速度较大;当风速较小时,叶片的运动速度和加速度较小。
其次,叶片的运动也与叶片的质量和刚度有关。
叶片质量越大,惯性力就越大,叶片的运动速度和加速度也会随之增大;叶片刚度越大,叶片的弯曲程度就越小,叶片的运动速度和加速度也会随之减小。
另外,叶片的机械结构和几何形状也会影响叶片的运动特性。
例如,增加叶片的长度和宽度可以增加叶片的弯曲刚度,减小叶片的弯曲程度,从而减小叶片的运动速度和加速度。
最后,叶片的动力学特性还与风力发电机系统的特性相互关联。
例如,当风力发电机系统的负荷增加时,风力发电机叶片所受的力和扭矩也会增加,从而改变叶片的运动特性。
综上所述,风力发电机叶片的动力学分析是对叶片在风力作用下的运动规律和力学特性进行研究的过程。
通过对叶片受力和运动方程的分析,可以了解叶片运动的特性和影响因素,从而为风力发电机叶片的设计和优化提供指导。
风力发电机叶片动力学研究与分析

ce sn ld r i g l e r a ig b a e wo k n f . i
Ke r s ld ft e w n u b n y wo d :b a e o d t ie;mo e a ay i ;v b ai n h i r d n ss i r t l o
图 1 叶型弯扭耦合模 型
单 片 转动 位叶 的 惯量: :f ( Ydd - J + ) y , i f p x
同理 可求 得单 位 叶片 的势 能为 :
叶 片主要 振源 之 一 。 因而 对 风力 机 叶片 进行 振 动 稳 定性 分 析 , 论是 对风 力机 的设计 还是 对风 力机 的运 不 行都 将是 非 常重要 的。
』 h q
L2 = 0 q
() 1
() 2
2 叶片 的运动微分 方程
现采 用 如 图 1 示 的弹 簧 阻尼 质 量 系统 来 研 究 所
风 机叶 片 的动力学 问题 。
y
由图 1 以得 到叶型 任意 点 的垂直 位移 为 : 可
h =一h—x O 所 以单位 叶片 振动 时 的动 能就 为 :
1
0
: i
~ j0
I
:
m
走+ _ 2 ,
() 3
其中:
单 位叶片 质量: J d y 的 m=f x d I p
元分析软件 对风机叶 片模型进行振 动模 态分析 , 计算 了叶片的固有频率、 阶振 型 图, 各 为避 免叶 片发 生共振 、 提 高叶片使 用寿命提供 了分析 方法。
关键 词 : 力机 叶 片 ; 态分 析 ; 动 风 模 振
, 文章编号 :06—4 1 ( 00 0 0 5 — 2 10 4 4 2 1 ) 5— 0 1 0
风力发电机叶片的动力学分析

风力发电机叶片的动力学分析□冯锦飞□顾永强□贾宝华□朱文彬内蒙古科技大学土木工程学院内蒙古包头014010摘要:旋转是叶片的主要工作方式,叶片轴向力与切向力的大小随叶片的旋转而时刻发生变化,导致重力对叶片每个旋转位置有不同程度的影响。
应用A N S Y S 软件建立旋转状态下叶片的有限元模 型,对其进行动力学分析。
分析结果表明:叶片的最大变形量为0.327 mm ,位于叶尖附近,远小于玻璃钢 叶片的最大弯曲变形要求;叶片的最大应力值为1.04 MPa ,远小于玻璃钢的抗拉强度。
通过分析确认,重 力对风力发电机叶片的整体力学性能影响较小。
关键词:风力发电机叶片动力学分析中图分类号:T H 113.2;T M 315 文献标志码:B文章编号:1000-4998(2019)12-0056-04Abstract : Rotation is the main working mode of the blade. The axial force and tangential force of the blade are changing with the rotation of the blade, which causes the gravity to have different degrees of influence on each rotating position of the blade. The finite element model of the blade in the rotating state was established by ANSYS software, and the kinetic analysis was carried out. The analysis results show that the maximum deformation of the blade is 0.327 mm, which is located near the tip of the blade, which is much smaller than the maximum bending deformation requirement of the FRP blade. The maximum stress value of the blade is 1.04 MPa, which is much smaller than the tensile strength of FRP. It is confirmed by analysis that gravity has little effect on the overall mechanical properties of the blade of wind turbine.Key W ords : Wind Turbine Blade Kinetics Analyses1研究背景能源危机席卷全球,环境保护迫在眉睫,新型清洁 能源的发展势在必行。
叶片空气动力学特性研究及其在风电系统中的应用
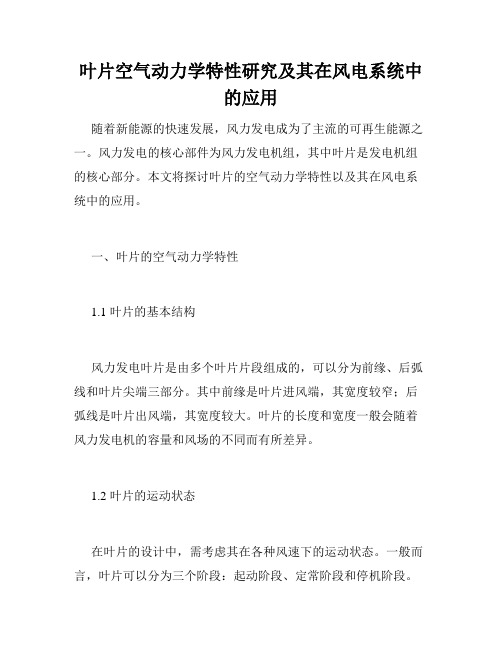
叶片空气动力学特性研究及其在风电系统中的应用随着新能源的快速发展,风力发电成为了主流的可再生能源之一。
风力发电的核心部件为风力发电机组,其中叶片是发电机组的核心部分。
本文将探讨叶片的空气动力学特性以及其在风电系统中的应用。
一、叶片的空气动力学特性1.1 叶片的基本结构风力发电叶片是由多个叶片片段组成的,可以分为前缘、后弧线和叶片尖端三部分。
其中前缘是叶片进风端,其宽度较窄;后弧线是叶片出风端,其宽度较大。
叶片的长度和宽度一般会随着风力发电机的容量和风场的不同而有所差异。
1.2 叶片的运动状态在叶片的设计中,需考虑其在各种风速下的运动状态。
一般而言,叶片可以分为三个阶段:起动阶段、定常阶段和停机阶段。
在高速风区,叶片处于起动阶段;在设计风速区,叶片处于定常阶段;在极端风区,叶片处于停机阶段。
针对不同风速下的运动状态,需要对叶片进行不同的设计。
1.3 叶片的空气动力学特性叶片的空气动力学特性是指叶片在风场中运动时所受到的空气阻力和动力。
叶片的对流和湍流效应,以及翼型、叶片倾角、攻角和扭曲角等因素都会影响叶片的空气动力学特性。
因此,在设计叶片时,需要对这些因素进行深入研究。
二、叶片的材料和制造工艺在叶片的制造中,需要选择合适的材料和制造工艺。
传统的叶片材料有玻璃钢、碳纤维等,而新型复合材料也逐渐被应用到叶片的制造中。
制造工艺一般包括手工铺装、模压、挤出和复合等方式。
制造工艺的选择对叶片的质量、成本等方面都会有影响。
三、叶片在风电系统中的应用叶片是风力发电机组的核心部分,其空气动力学特性的优化对提高发电效率至关重要。
针对叶片的优化,可以采用数值模拟、试验等方法进行研究和优化。
此外,还可以通过改变叶片的长度、倾角、翼型等方式来提升叶片的性能。
除了优化叶片设计外,叶片在风电系统中还可以发挥其他作用。
例如,在风电场运行中,风向和风速会不断变化,需要根据实际情况调整叶片的姿态角度以获取最佳风能发电效果。
此外,还可以通过安装监测设备来实现对叶片状态的远程监测和管理,从而提高叶片的使用寿命和安全性能。
风力涡轮机叶片动态结构研究

风力涡轮机叶片动态结构研究随着能源需求的不断增加和环境保护意识的加强,风能逐渐被人们所认知和使用。
而风力涡轮机作为转化风能的重要设备,其性能如何提升,成为解决能源问题的重要课题。
而风力涡轮机叶片,作为核心部件之一,其结构是否合理、动态响应是否稳定,直接关乎着机组的运行效率和寿命,因此对其进行动态结构研究显得尤为重要。
一、叶片动态响应的原因风力涡轮机叶片在运行过程中,会受到气动力、离心力、重力和惯性力等多种作用力的影响,从而引起叶片的动态响应。
其中气动力是导致叶片振动最主要的原因。
1. 拍动振动风力涡轮机在运行时,气流会因为旋转的涡轮机叶片而分别从正面和背面流过,并产生交替的高压区和低压区。
在这个过程中,因为叶片表面压力产生的作用力和弹性产生的反作用力不断地变化,使得叶片发生类似于机翼不稳定的“buffetting”现象,即叶片交替地在正反两面振荡,造成拍动振动。
2. 纵向弯曲振动风力涡轮机叶片也存在纵向弯曲振动的现象。
当叶片表面的气流速度和压强产生变化时,叶片弯曲形成梁的形式。
当叶片在运行过程中产生的转动惯量大于弯曲振动引起的回复力时,叶片向相反方向运动,造成纵向弯曲振动。
3. 扭曲振动由于叶片的形状不规则,因此在风力涡轮机运行过程中,会存在扭曲振动。
当叶片表面的气流速度和压强不均匀时,将会引起叶片发生扭曲,当旋转惯量和扭曲力产生的力矩不平衡时,叶片将会发生扭曲振动。
二、叶片结构的优化为了减少风力涡轮机叶片的动态响应,需要从叶片结构方面进行优化。
在叶片结构设计和制造时,需要考虑到以下几个方面:1. 减少结构复杂度叶片的结构越复杂,就越容易出现动态响应问题。
因此,在叶片设计中,要尽量简化叶片的结构,减少复杂度。
2. 提高叶片刚度叶片刚度是指叶片抵抗弯曲和扭曲振动的能力。
当叶片刚度越高时,其抵抗振动的能力也越强。
因此,在设计和制造叶片时,需要考虑到叶片的材料、横截面积等因素,来提高叶片的刚度。
3. 减少材料的疲劳损伤叶片在长时间运行后会发生疲劳损伤。
风力发电机组的动态响应特性分析
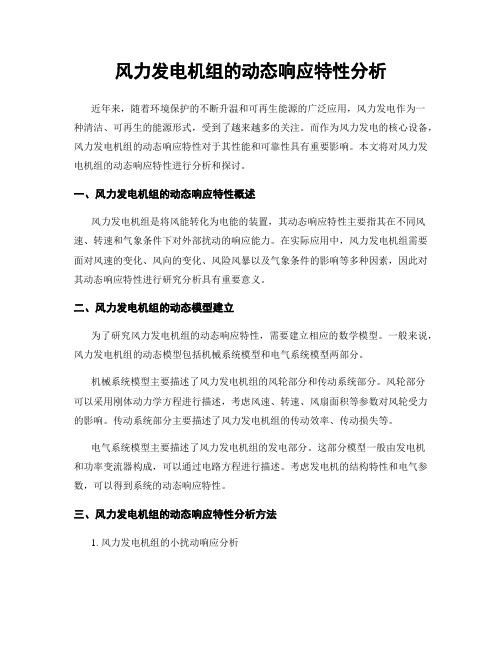
风力发电机组的动态响应特性分析近年来,随着环境保护的不断升温和可再生能源的广泛应用,风力发电作为一种清洁、可再生的能源形式,受到了越来越多的关注。
而作为风力发电的核心设备,风力发电机组的动态响应特性对于其性能和可靠性具有重要影响。
本文将对风力发电机组的动态响应特性进行分析和探讨。
一、风力发电机组的动态响应特性概述风力发电机组是将风能转化为电能的装置,其动态响应特性主要指其在不同风速、转速和气象条件下对外部扰动的响应能力。
在实际应用中,风力发电机组需要面对风速的变化、风向的变化、风险风暴以及气象条件的影响等多种因素,因此对其动态响应特性进行研究分析具有重要意义。
二、风力发电机组的动态模型建立为了研究风力发电机组的动态响应特性,需要建立相应的数学模型。
一般来说,风力发电机组的动态模型包括机械系统模型和电气系统模型两部分。
机械系统模型主要描述了风力发电机组的风轮部分和传动系统部分。
风轮部分可以采用刚体动力学方程进行描述,考虑风速、转速、风扇面积等参数对风轮受力的影响。
传动系统部分主要描述了风力发电机组的传动效率、传动损失等。
电气系统模型主要描述了风力发电机组的发电部分。
这部分模型一般由发电机和功率变流器构成,可以通过电路方程进行描述。
考虑发电机的结构特性和电气参数,可以得到系统的动态响应特性。
三、风力发电机组的动态响应特性分析方法1. 风力发电机组的小扰动响应分析小扰动响应分析是研究风力发电机组对风速和风向变化的响应能力。
通过线性化模型和小信号分析方法,可以得到系统的频率响应特性、振荡特性等。
2. 风力发电机组的非线性动态响应分析非线性动态响应分析考虑了更为复杂的工况,如大风、风暴等。
这种情况下,风力发电机组的动态响应特性可能不再是线性的,因此需要采用非线性动力学模型进行分析。
通过数值模拟方法,可以研究系统在不同工况下的动态响应特性。
四、影响风力发电机组动态响应特性的因素1. 风速的变化风速的变化是最直接的影响因素之一。
低风速环境下风力发电叶片的动态特性分析与优化设计

低风速环境下风力发电叶片的动态特性分析与优化设计1. 引言随着环境保护意识的增强和可再生能源的重要性日益凸显,风力发电作为一种清洁、可持续的能源形式得到了广泛发展。
在风力发电系统中,风力发电叶片作为最核心的组成部分,起着将风能转化为机械能的关键作用。
本文将针对低风速环境下风力发电叶片的动态特性进行分析与优化设计。
2. 低风速环境下风力发电叶片的动态特性分析低风速环境下,叶片所受到的风力较弱,这对风力发电系统的效率和稳定性提出了更高的要求。
为了准确分析低风速环境下风力发电叶片的动态特性,我们可以采用数值模拟方法,如计算流体力学(CFD)仿真。
首先,我们需要建立一个准确的数学模型,包括叶片的几何形状、材料特性、风速分布等。
然后,利用CFD软件对风力发电叶片进行流场仿真,得到叶片表面的压力分布、气动力、风速分布等相关数据。
通过对这些数据的分析,可以得到低风速环境下叶片的气动特性和动态响应性能。
在分析低风速环境下风力发电叶片的动态特性时,需要考虑以下几个方面:2.1 风速分布对叶片的影响低风速环境下,风速分布不均匀是一个普遍存在的问题。
在动态特性分析中,我们需要关注风速的峰值、起始时间、持续时间等参数。
通过对风速分布的分析,可以确定叶片在不同时刻所受到的风力大小和方向,进而研究叶片的振动特性、变形情况等。
2.2 叶片质量与刚度对动态特性的影响低风速环境下,叶片的质量和刚度对其动态响应有重要影响。
质量分布不均匀和刚度不足会导致叶片的振动和形变过大,从而影响风力发电系统的工作效率和寿命。
因此,在优化设计叶片时,需要合理分配叶片的质量,并提高其刚度。
2.3 流态特性对叶片的影响低风速环境下,流态特性对风力发电叶片的动态特性有显著影响。
流场的湍流程度、流速梯度等因素决定了叶片表面的压力分布和气动力大小。
因此,优化叶片的流态特性可以提高叶片的功率输出和稳定性。
3. 风力发电叶片的优化设计基于对低风速环境下风力发电叶片动态特性的分析,我们可以进行优化设计,以提高风力发电系统的效率和稳定性。
基于ANSYS的风电机组叶片动态响应分析与优化设计

基于ANSYS的风电机组叶片动态响应分析与优化设计风电机组是目前广泛应用于清洁能源领域的一种发电设备,其核心部件之一是叶片。
叶片的设计与优化对于提高风电机组的发电效率、减少结构疲劳损伤具有重要意义。
本文将基于ANSYS软件,对风电机组叶片的动态响应进行分析,并提出优化设计方法。
一、叶片动态响应分析叶片在工作过程中会受到风力的作用而发生弯曲和振动,因此需要进行动态响应分析。
首先,我们需要建立叶片的有限元模型。
通过ANSYS的建模工具,可以将叶片的几何形状进行三维建模,并使用适当的材料属性对叶片进行参数化描述。
在建立有限元模型后,我们需要给予风电机组施加载荷。
根据风力的特性和叶片的运行条件,可以采用风力加载模块对叶片进行施加风载。
该模块可以模拟风力的作用,计算叶片所受的风载大小和方向,并将其作为载荷输入到有限元模型中。
接下来,通过ANSYS的动态分析功能,对叶片的振动响应进行计算。
动态分析将考虑材料的刚度、阻尼和质量等因素,得出叶片在不同工况下的振动情况。
通过分析叶片的振动频率和振型,可以评估叶片的结构是否合理,是否存在共振问题。
二、叶片优化设计在进行叶片的优化设计时,我们可以通过ANSYS的参数化设计功能来实现。
首先,我们需要确定需要优化的设计变量,如叶片的几何参数、材料参数等。
然后,通过定义参数和参数范围,可以使得ANSYS自动地进行参数组合和计算。
通过进行多次模拟计算和优化迭代,可以得到不同设计变量组合下的叶片性能。
根据设定的优化目标,如最小化叶片的振动响应或最大化叶片的发电效率,可以选取最优的设计变量组合作为最终的优化设计方案。
另外,对于叶片的优化设计,还可以考虑使用拓扑优化方法。
拓扑优化可以根据预设的约束条件和目标函数,在给定的设计空间内调整叶片的材料分布,使得叶片的结构更加均衡和优化。
通过结合拓扑优化和动态响应分析,可以得到更加高效和可靠的叶片设计方案。
三、实例分析与展望通过基于ANSYS的风电机组叶片动态响应分析与优化设计方法,可以有效地评估叶片的结构性能,并提供优化建议。
- 1、下载文档前请自行甄别文档内容的完整性,平台不提供额外的编辑、内容补充、找答案等附加服务。
- 2、"仅部分预览"的文档,不可在线预览部分如存在完整性等问题,可反馈申请退款(可完整预览的文档不适用该条件!)。
- 3、如文档侵犯您的权益,请联系客服反馈,我们会尽快为您处理(人工客服工作时间:9:00-18:30)。
截面上的应力与弯矩的关系为:
I Yl仃ldAl+l Yl盯2dA2+…=M。
o 4l
o^2
可得:
等.f.。,,jdA。+等』屯y2dAz+…=M。
由此得挠度与弯矩的关系:
肘。=(El,,l+如,,2+…)罟{
代入振动方程得:
习习a(2(E州td,+E2d如++如..+..).+础。型3)2+=p础y-a型t2 等
模型,但Beddoes—Leishman模型考虑非定常效应时使 用二阶微分方程来描述,且需通过叶型试验要确定 的参数较多,因此比较复杂。这里介绍Krenk模型,
Krenk模型是在考虑风力机叶片实际状况的基础上
万方数据
太阳能学报
31卷
对Beddoes.Leishman模型作了适当的简化。 在Krenk模型中用c,。表示定常条件下不考虑
本文采用Marc有限元软件实现风力机叶片动 力学响应计算。选用FORCDT载荷子程序施加气动 载倚。根据Marc子程序的调用特点,在计算的每一 个增量步中,对于每一个将载荷定义成FORCDT子 程序的节点,该子程序都要被调用一次。在静力分 析中,位移向量被传递到子程序中;在动态分析中, 速度和加速度量也被传递过来[2 J。由此可见,只要 将计算叶片气动载荷的方法编成FORCDT子程序, 就可实现在计算中每个增量步互相交换边界条件的 目的。
肼。=(Gl‘+G2缸+…)关
由此得振动方程:
71,订a20=未(G。[pl+G2”…)箬饥
式中,G;——截面各铺层材料的面内剪切模量; ,。;——截面不同材料的极惯性矩。且有:
,,=∑,pi
根据以上的推导,梁单元使用各向同性材料, E、G分别由下式确定:
,;:∑,“EV:I竿F
T可_ ∑,,iE
∑,,iG;
1 叶片动力学响应计算基本思路
在前述的三类方法中,第一类方法由于自身假 设的限制,应用不多,第三类方法由于理论上的难 度,亟待进一步的发展,而第二类方法得到了广泛应 用,该方法在每个时问步交换流体域和固体域的信 息,这样,一个域求解的结果就被当作边界条件施加 到另一个域中,即在每一步将计算得到的流体力施 加到叶片上,得到叶片的新佗置,而叶片的新位置又 被作为新的流固边界去计算下一步的流体力。
是将叶片沿展向分成许多微段,这些微段称为叶素。 假设每个叶素上的流动相互之间没有干扰,即将叶 素看成二维叶型。
风通过风轮后产生漩涡,因而有轴向诱导速度 和环向诱导速度,分别用轴向诱导因子口、环向诱导 因子口’来表示,轴向诱导速度与来流速度相反,环 向诱导速度与叶片旋转方向相反,由此可以得到考 虑诱导速度后气流相对于叶素的速度的大小。由相 对气流速度、准静态升力、阻力和力矩曲线即可求得 叶素上的力和力矩,将作用在每个叶素上的力和力 矩沿叶片展向积分,就可以求得作用在叶片上的力 和力矩。
关键词:风力机叶片;气动弹性;气动阻尼系数
中图分类号:TK83
文献标识码:A
0引 言
随着风力机尺寸的增加,一方面叶片的叶尖切 向速度小断提高,另一方面考虑到重鼍问题,叶片将 越来越细长,在这种趋势下,研究风力机叶片在风载 荷下的动力学响应,从而判断叶片的运动稳定性就 显得越来越霞要。由于叶片处于气流中,流场的流 动对叶片产生的作用力会使叶片产生变形,而叶片 的变形会影响到流场流动,若要较准确的得到叶片 的动力学响应,就必须考虑叶片与流场的这种相互 影响作用,即必须考虑叶片的气动弹性响应问题。
的大小,选用修正的动量叶素理论和梁单元作为流体和结构模型,并将动态失速模型与动虽叶素理论结合计算气
动力;以Marc通用有限元计算程序为基础平台,将气动力计算程序写入子程序中,并根据子程序的调用特点,实现了 在每个增量步中气动和结构边界条件的相互交换。最后给出计算算例,得到的计算结果与实际使用情况相符合。
分离时的升力曲线;C。.表示定常条件下考虑分离时 的升力曲线;下标加d表示对应的非定常条件下的 数值;口为攻角。定义分离系数.厂,物理意义如图3 所示,它表示分离点的位置。
3计算结果及分析
以上面提到的某型750kW风力机叶片为例,计 算了叶片在风速为10~25m/s时的响应,图4~图6 仅绘出25m/s风速下叶尖节点3个方向的响应历 程,另外几种情况下叶尖节点3个方向的响应历程 图形与此类似。
性基本一致。 2.3耦合计算过程
FORCDT子程序计算流程如下:在每一个增量 步,Marc主程序将节点号及弯曲、摆振和扭转方向位 移传给FORCDT载荷子程序,子程序根据节点号得
到截面翼型类型以及该点的初始展向位置,初始安 装角及弦长,根据挥舞、摆振和扭转方向位移修正展 向位置及安装角,并计算攻角,由攻角插值获得升力 系数、阻力系数和力矩系数,根据修正的动量叶素理
万方数据
918
太 阳 能 学报
3l卷
这是因为: 1)风力机叶片由多层玻璃布铺敷而成,铺层十
分复杂,首先是层数多,最多处有30多层,其次每一 层的铺敷范围极不规律,只有极个别的层是全型面 铺设的,图l为部分铺层的示意图【3】。如果选用三 维模型,为描述这种复杂的铺层,就需要尽量多的结 构单元,而一般流体域网格要远大于固体域,因此整 个模型规模很大,导致计算时间不可接受;
由于修正的动量叶素理论是比较常用的方法, 限于篇幅这里不再详细叙述,具体过程和用到的公 式可参见文献[4]。
2.2结构模型[5’6】 与动量叶素理论相配套,叶片结构采用梁单元
模拟。由图l可知叶片铺层层数多且形式复杂,无 论沿弦向还是沿展向材料都不存在均匀性,将叶片 简化成梁后,每个实际截面变成了一个点,梁单元的 材料属性如何给出,才能保证梁单元模型的动力学 特性与真实叶片的动力学特性一致,是需要考虑的 问题。在分析叶片的振动时,根据受力情况,叶片主 要有3个方向的运动,即挥舞振动(Z向,坐标参考 图1),摆振振动(Y向)和扭转振动(绕x轴)。Y向 弯曲振动微分方程为:
编号为l、2、3……16,其中1、2节点之间是圆柱段, 之后各段选用不同的翼型。该叶片的额定工作风速 为14IIl/s。
根据稳态升阻力系数曲线,使用上述模型迭代
计算得到叶片各截面在额定工作风速附近不同风速
下的稳态攻角,如图2所示。
60
3
4
50
f40
\
援30 铎
20
01234
10
节摹节符宵节 点赛点 点 567891lIl 56
目前求解气弹响应的方法,根据出现的先后顺 序可以分为三大类:第一类是将流体和固体区域解 耦,将流体对结构的作用折算到结构动力学方程中 去,或者反之。这类方法为了能实现将一个区域的 作用效果用另一个区域的参量表示出来,做了许多 假设和限制。第二类方法将流体区域和结构区域的 方程单独求解,但是在每个时间步交换边界条件。 这类方法中一个区域对于另一个区域的响应是滞后 的,只是时间步越小这种滞后的影响越小。第三类 方法用一个统一的方程描述流体域和结构域,结构 和流体运动在每个时间步用同一个求解器同时求 解。由于流体与结构的刚度相差很大,因此这类方 法实现起来比较困难,有待进一步的发展…。
10 12 14 16 18 20 22 24 26 风速/m·8-‘
图2各截面攻角随风速变化 ng.2 Attack锄gle ch粕g嗍with wind spoed 表1中列出了各截面翼型升力系数直线段结束 对应的攻角以及最大升力系数位置对应的攻角,由 图2与表1可以看出,风速在lOm/s时,叶片各截面 还处于升力系数曲线的线性段,随后,各截面逐渐出 现失速,可见在叶片工作过程中,失速现象时有发 生。当叶型进行俯仰振荡运动时,其失速攻角比叶 型静止时的失速攻角要大,另外,叶型空气动力特性 随攻角变化的曲线出现迟滞现象,在攻角增大的过 程中,最大升力系数大于静态值;而在攻角减小的过 程中,则小于静态值,这种现象称之为动态失速。在 对风力机叶片做气动弹性分析时动态失速是一个很 重要的现象,需要重点考虑。 表1升力曲线直线段结束及最大值位置对应攻角 Table 1 attack跗lgle of straight line segment
图3分离函数厂的物理意义 Fig.3 The mea|lillg of sepa_mtion function f 则有如下关系:
c。=(掣)cm
在非定常流中升力曲线的时变性来自于两个方 面,一方面是升力线斜率的时变,另一方面足分离点 位置的时变。
考虑在无分离的条件下升力线斜率的时变性, 当攻角发生小的扰动时,叶型上会暂时性的产生小 的分离,然后气流会重新附体,这一滞后过程导致了 环量的变化,从而导致升力的变化,Krenk模型用脉 冲响应函数来描述这个过程,最终得到升力线的滞 后响应表示如下:
论计算微段的气动升力、气动阻力及气动力矩,并将 其折算到节点位置上,由于Marc主程序要求 FORCDT载荷子程序返回的是载荷增量,因此这里 还需要取出上一增量步的载荷值,从而获得增量值。
Marc主程序根据返回的载荷增量,求解结构的响应, 如此实现反复迭带。
以某型750kW风力机叶片为例,根据以上的思 路,将叶片分成15段,每一段由一个梁单元来表示, 这样每一个节点代表一个截面,由叶根至叶尖分别
叶片为薄壁结构,可得扭转振动微分方程:
71p 3。2。0=券+mI
截面上的剪应力与扭矩的关系为:
可得:
I rI rldAl+I r2 r2dA2+…=M。
o 4l
o^2
鬟(G。,^I r2dA。+G2J.^2 r;dA:力学响应分析
919
由此得到角位移和扭矩的关系:
fdl(t)+ccJI Cl(t)=Al em(t)
{e2(f)+∞2 c2(£)=A2e【o(t)
【CIo.d(t)=Cm(口)一cl(t)一c2(£) 考虑分离点位置的时变性,在分离状态下,当攻 角改变时分离点位置也会改变,而位置的改变滞后 与攻角的改变,用一阶微分方程表示这种滞后关系, 得: