SKD32.82.62.62 电动液压阀门执行器说明书_英文版
电动阀门执行器出口英文使用说明书
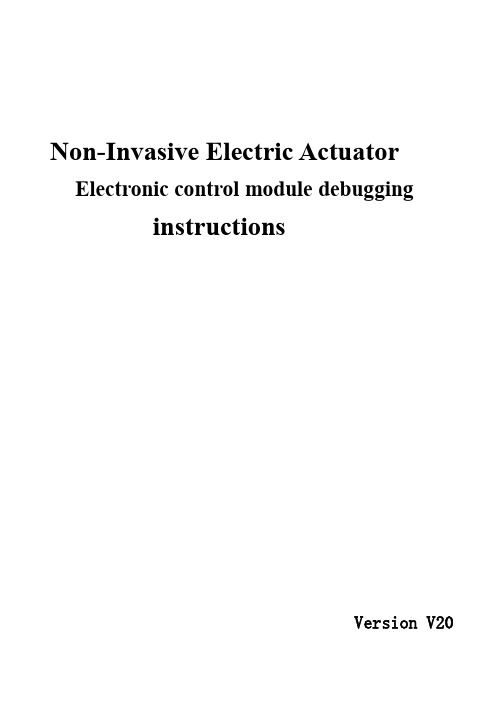
Non-Invasive Electric Actuator Electronic control module debugginginstructionsVersion V201SummaryThis component can receive the DCS system on-off signals (passive dry contact of active, active 24 v, 220 v, keep running can switch) or analog signals (DC4-20 ma, 0 to 10 v, etc.), direct drive electric actuators switch action or adjust the action. Output DC4-20 ma feedback current and contact/remote control state instructions. The component integration the servo control unit, solid-state drive unit, liquid crystal display unit, knobs and other ancillary units and aluminum shell assembly operation.The product operates as a fool camera is simple, like intelligent perfect protection function.2Operating Instructions2.1Knob Operating InstructionsThe red knob is the mode button, can be switched between Local/Stop/Remote. Or in a set state, to save the menu contents (from the stop bit screwed to the site) or to exit the menu(from the stop bit screwed into the remote).Black knob for the operating button can be opened or closed operation at the local.Or to plus or minus in the set state.With button operation, short time effect for the inching mode. When the operation button is effective for more than 3 seconds, in the lower right corner of the LCD, the bc is displayed automatically entered into the hold mode. When actuator movement, click the action button reverse rotation or spin mode button to Stop, the actuator Array stops.2.2 setting tool description (setting tool are optional, needto please when ordering special instructions)"Up" button = Open calibration key, "Down" button = close calibrationkey, "Enter" button = Confirm key or Save key"Stop" button = stop key, "Open" button = open key, "Close" button =close key.When mode button at Local location, press "Open" button to performopen, press "Close" button to perform off. In the action, press the"Stop" button to stop the move, short press "Close" to stop the openingprocess, short press "Open" to stop the closing process.In local mode, even by three "Up" key to enter the open position calibration status, "Open", "Close" and "Stop" keys to control the electric actuator to open, close and stop, "Enter" key to save the trip, "Stop "key is used to return.In local mode, even by three "Down" key to enter the closed position calibration status, like the rest of the operation as above.3Signal query (LCD lower left corner for a signal check area) 3.1 Remote control signal inquiryWhen the mode button is screwed into the Remote, the remote control signal received is displayed in the lower-left corner of the LCD. Switch type: show OP represents a open signal, show CL represents a close signal, show BC represents a keep signal (multi state of coexistence of alternate display). Regulating type: to display the received control current value or voltage value.3.2 Valve position signal queryWhen the mode button is screwed onto the Local, the LCD shows the valve position signal in lower left corner. When using a potentiometer, show the percentage of resistance (d01 ~ d99); When using 12 encoder, shows the percentage of the encoder (b01 ~ b99); When using 18 encoder, display micrometer ratio of the encoder (001 to 999).4 4 Stroke calibrations4.1 Calibration for close limit:The mode button at the Stop position, the rotary operation knob to the Close position for about 3 seconds, until the letter L is flashing of the LCD to release operation button, then the mode button to the Local position, now letter L no longer flashes and the system into the closed position calibration status. The actuator can open or close by the operating button. When the actuator operates to the closed position, then the mode button to spin the Stop position, and back to the Local position, at this time the red LED flashing two times said the closed position calibration is completed. If the mode button is screwed to the Remote position from Stop position, that exit travel calibration.4.2 Calibration for open limitThe mode button at the Stop position, the rotary operation knob to the Open position for about 3 seconds, until the letter H is flashing of the LCD to release operation button, then the mode button to the Local position, now letter H no longer flashes and the system into the open position calibration status. The actuator can open or close by the operatingmode button to spin the Stop position, and back to the Local position, at this time the green LED flashing two times said the open limit position calibration is completed. If the mode button is screwed to the Remote position from Stop position, that exit travel calibration.Note: When you save a stroke, display Fu or Fn characters on the LCD, please re-adjust potentiometer or rotary encoder range, and recalibrate the trip.5Feedback current trimming5.1 Feedback current 4mA trimmingThe mode button at the Stop position, the rotary operation knob to the Open position for about 10 seconds, until the letter LF is flashing of the LCD to release operation button, then the mode button to the Local position and back to the Stop position, and the system into the 4mA current trimming status. At this point,the size of the output current can be adjusted by the operating button. When adjusting the output current reaches 4mA, then mode button to spin the Local position, this time the red LED flashes three times, said 4mA output current trim is complete. If the mode button to Stop position from Remote position, which exit status of the output current trim.5.2 Feedback current 20mA trimmingThe mode button at the Stop position, the rotary operation knob to the Open position for about 10 seconds, until the letter HF is flashing of the LCD to release operation button, then the mode button to the Local position and back to the Stop position, and the system into the 20mA current trimming status. At this point,the size of the output current can be adjusted by the operating button. When adjusting the output current reaches 4mA, then mode button to spin the Local position, this time the green LED flashes three times, said 20mA output current trim is complete. If the mode button to Stop position from Remote position, which exit status of the output current trim.6About dead zoneThe dead zone to adapt automatically, without setting can ensure that in any conditions without oscillation, and the positioning precision is higher.7Alarm description (error code displayed on the LCD in the lower right corner) FaultcodeFault informationFA Actuator running direction errorFu V alve position potentiometer or encoder Angle is too largeFn V alve position potentiometer or encoder Angle is too smallFP Power phaseFF Broken valve position potentiometer, rotary to blind or pick the wrong line, or encoder failure.FC Over closed torqueFO Over open torqueFH Remote control signals to open and close signals exist (only on-off type)FS Control current signal is lost (only positioning)Fb Current control signal calibration error(only positioning)Fd Stall or other causes the valve position does not changeFL Limit contact line or torque contact line reversedFE The motor is too hot or the torque public terminal is openNOTE: The green LED is the open limit position light on the screen, the red LED is closed position light on the screen.8Advanced SettingsNOTE: All the Advanced Settings can be set after the mode button in the "Local" position. Advanced settings must open the electrical box cover and you can operate. The Close Key and Open Key mentioned below are in the electronic control board.8.1 Action when the control current loss:(Only positioning type, default: Remain in Situ)8.1.1 To press the “Close Key” and power up for 3 seconds until the red LED on the board is lit. And you release the key, then the red LED flashes three times; the “FullClose” setup is completed.8.1.2 To press the “Open Key” and power up for 3 seconds until the green LED on the board is lit. And you release the key, then the green LED flashes three times; the “Full Open” setup is completed.8.1.3 Simultaneously press two keys and power up for 3 seconds until the green and red LEDs on the board are lit. And you release the two keys simultaneously, then the two LEDs flashes three times; the “Remain in Situ” setup is completed.8.2 Control current calibration:(Only positioning type)8.2.1 To send 4mA control current to the module from the outside, press the “Close Key” and power up for 10 seconds until the red LED on the board is lighted second times. And you release the key, then the red LED flashes three times; and the4mA calibration is completed.8.2.2 To send 20mA control current to the module from the outside, press the “Open Key” and power up for 10 seconds until the green LED on the board is lighted second times. And you release the key, then the green LED flashes three times; and the20mA calibration is completed.8.3 Polarity for the control current:(Only positioning type)20mA = Full Open /4mA = Full Open (default:20mA = Full Open) Simultaneously press “Open Key” and “Close Key” and then power up for 10 seconds. To release the key after the red LED and green LED second lights up. Short press “Open Key” or “Close Key” to alternately lit red LED or green LED. The red LED light represents “20mA = Full Open”, the green LED light represents “4mA = Full Open”. Simultaneously press “Open Key” and “Close Key” for 3 seconds. To release two keys after the two LEDs lights up. Then corresponding LED flashes three times, the polarity for the control current setup is complete.8.4 Two-Wire Control:(Only on-off type)Disable or Open First or Close First (default: Disable)8.4.1Close FirstYou press “Close Key” and then power up for 10 seconds. The key is released after the red LED second light up. And the red LED flashes three times, this setup is complete. This Close First refers to the actuator close operation when voltages signal on the “Remote Close” terminal of the actuator. But no voltage signal, actuators open operation. When wiring, “Remote Open” terminal connected to 24V +.8.4.2Open FirstYou press the “Open Key” and then power up for 10 seconds. The key is released after the green LED second light up. And the green LED flashes three times, this setup is complete.This Open First refers to the actuator open operation when voltages signal on the “Remote Open” terminal of the actuator. But no voltage signal, actuators close operation. When wiring, “Remote Close” terminal connected to 24V +.8.4.3 DisableYou press the two keys simultaneously and then power up for 10 seconds. The key is released after the two LEDs second lights up. Then the two LEDs flashes three times, this setup is complete.8.5 Close direction:Clockwise /Anti-clockwise (default:Clockwise)You press the “Open Key” and “Close Key” simultaneously and then power up for 20 seconds. The keys are released after the red LED and green LED third lights up. Short press “Open Key” or “Close Key” to alternately lit red LED or green LED. Red LED light represents “Clockwise”, green LED light represents “Anti-clockwise”. You press the two keys simultaneously for 3 seconds. The keys is released after the two LEDs light up. Then corresponding LED flashes three times, the Close direction setup is complete.9Common problems to deal withPower LED is not lit or digital display does not show 1. Power is not actually access. 2. voltage is too low 3. Wiring fault. 4. Module badLEDs and digital display abnormal 1. See fault code.2. Query information.3. Replace the moduleAfter power on ,actuator can be not control in the LOCAL and REMOTE mode 1. Wiring fault or loose wiring. 2. Fault Protection.3. Motor bad or stuck.4. Bad start capacitor.5. module badLOCAL mode work is normal but the REMOTE mode can't control 1. No signal or junction anti- , 2. Bad or no knob plate in Remote3. Positive / reaction set wrong.4. Module badREMOTE mode work is normal but the LOCAL mode can't control 1. Not in LOCAL mode. 2. Knobs board bad or not at the scene mode. 3. Operation button is not properly screwed in placeActuator can open but not close or can close but not open 1. Torque wiring fault or loose wiring. 2. to limit position or over torque3. Motor bad or stall or wiring fault.4. Module badThe action immediately after power on 1. Wiring fault. 2. control signal is present3. Implementation the action when the control current loss4. Set the wrong.5. module badThe middle position can move but to the limit position does not move 1. Reverse limit switch line. 2. Motor bad or loose wiring 3. Module badThe direction of movement is the anti 1. Motor lines reversed. 2. Anti valve calibration.3. Signal Reverse4. Polarity for the control current or closing direction set wrong.No output current or sometimes no 1. The output wiring fault or bad. 2. Module bad 3. potentiometer wiring fault or loose wiringFeedback current is larger or smaller or unchanged 1.Potentiometer failure. 2. Calibration error.3. module bad4. potentiometer meshing with drive gear not wellNote: Please strictly in accordance with the wiring diagram electrical wiring connection.Like has the change, without notice。
电动阀门电动驱动器说明书
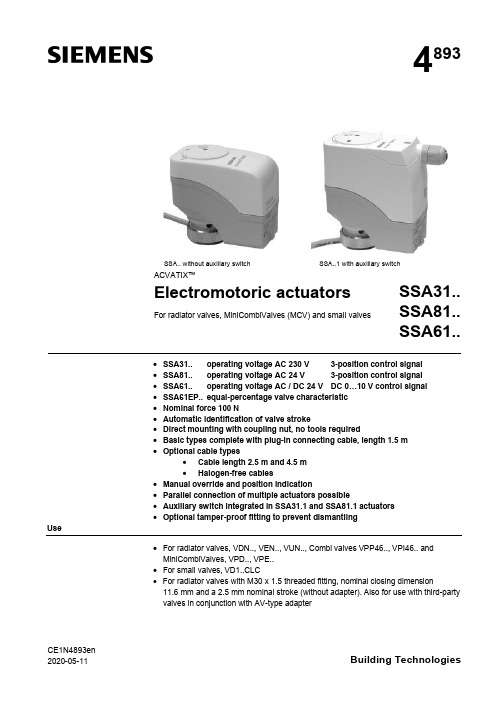
CE1N4893en 2020-05-11Building Technologies4893SSA.. without auxiliary switch SSA..1 with auxiliary switchACVATIX™Electromotoric actuatorsFor radiator valves, MiniCombiValves (MCV) and small valvesSSA31..SSA81..SSA61..·SSA31.. operating voltage AC 230 V 3-position control signal ·SSA81.. operating voltage AC 24 V 3-position control signal ·SSA61.. operating voltage AC / DC 24 V DC 0…10 V control signal ·SSA61EP.. equal-percentage valve characteristic ·Nominal force 100 N·Automatic identification of valve stroke·Direct mounting with coupling nut, no tools required·Basic types complete with plug-in connecting cable, length 1.5 m ·Optional cable types·Cable length 2.5 m and 4.5 m ·Halogen-free cables·Manual override and position indication·Parallel connection of multiple actuators possible·Auxiliary switch integrated in SSA31.1 and SSA81.1 actuators ·Optional tamper-proof fitting to prevent dismantlingUse·For radiator valves, VDN.., VEN.., VUN.., Combi valves VPP46.., VPI46.. and MiniCombiValves, VPD.., VPE..·For small valves, VD1..CLC· For radiator valves with M30 x 1.5 threaded fitting, nominal closing dimension11.6 mm and a 2.5 mm nominal stroke (without adapter). Also for use with third-party valves in conjunction with AV-type adapter2/10SiemensCE1N4893enSmart InfrastructureBuilding Technologies2020-05-11· For modulating or 3-position control in heating systems, chilled ceilings and terminal units.Type summaryTypereference Operating voltage Run time at 50 HzControl signalConnecting cableAuxiliary switchSSA31AC 230 V150 s3-position1.5 m SSA31/001)no cable SSA31.1 1.5 m YesSSA81AC 24 V1.5 m SSA81/001)no cable SSA81.1 1.5 m YesSSA61AC / DC 24 V 34 s DC 0...10 V1.5 m SSA61/001)no cable SSA61EP 2) 1.5 m SSA61EP/002)no cable1)For available cable lengths or terminal block connectors refer to "Accessories", page 42)With equal-percentage valve characteristicTypereference DescriptionOperating voltage Control signalASY3L25Connecting cable 2.5 mAC 230 V3-positionASY3L45Connecting cable 4.5 m ASY8L25Connecting cable 2.5 m AC 24 V ASY8L45Connecting cable 4.5 mASY8L45HF Connecting cable 4.5 m, halogen-free, VDE 0207-24ASY6L25Connecting cable 2.5 m AC / DC 24 V DC 0...10 V ASY6L45Connecting cable 4.5 m ASY6L45HF Connecting cable 4.5 m, halogen-free, VDE 0207-24ASY98Retaining screw for terminal block connectors. Included in ASY99 and ASY100.ASY99Terminal block connector for 3-position actuators SSA81../00ASY100Terminal block connector for DC 0…10 V modulating actuators SSA61/00AL40Tamper-proof fitting to prevent dismantling of actuators Adapter typefor third-party valves Adapter type for third-party valves AV51Beulco old (M30x1.0)AV56Giacomini AV522)Comap AV57Herz AV53Danfoss RA-N (RA2000)AV58Oventrop old (M30x1.0), till 2002AV54Danfoss RAVL AV592)Vaillant AV55Danfoss RAV AV60TA, till 20021)AV61Markaryd (MMA)1) No adapter required for type TBV-C 2)While stocks lastOrdering Type Stock no.DescriptionQuantity SSA81/00SSA81/00Electromotoric actuator 2ASY8L45ASY8L45Connecting cable2Actuators, valves and accessories are packed separately. Items are suppliedindividually packed.Overview tables, see page 9.AccessoriesExample:DeliveryRev.-No.3/10SiemensCE1N4893en Smart Infrastructure2020-05-11Equipment combinationsk vs = nominal flow rate of cold water (5...30 °C) through the fully open valve (H 100)at a differential pressure of 100 kPa (1 bar)V & = Nominal volume flow at 0.5 mm strokeTo ensure trouble-free operation of third-party valves with the SSA.. actuator, the valves must satisfy the following requirements:·Threaded connections with coupling nut M30 x 1.5·Nominal force F £ 100 N ·Dimension x x > 9.0 mm ·Dimension y y £ 14.5 mmFunction / mechanical designWhen the actuator is driven by DC 0…10 V control voltage or by a 3-position signal, it produces a stroke which is transmitted to the valve stem.The description of operation in this document applies to the valve versions which are fully open when de-energized (NO).·Voltage at Y1:Stem retracts Valve opens ·Voltage at Y2:Stem extends Valve closes ·No voltage at Y1 and Y2:Actuator maintains its current position· The valve opens / closes in proportion to the control signal at Y.· At DC 0 V, the valve is fully closed (A à AB).· When power supply is removed, the actuator maintains its current position.1)Actuator is calibrated to 2.5 mm stroke of VPI46.15.L06S t r o k e 2,5 m m ((c a l i b r a t e d )1)22.51.510.500246810control signal Y [V]Type reference Valve type k vs [m 3/h]V&[l/h]PN class Data sheet VDN.., VEN.., VUN..Radiator valves 0.09…1.41PN 10N2105, N2106VPD.., VPE..MCV radiator valves 25…483N2185VD1..CLC Small valves 0.25…2.60N2103VPP46.., bi valves 30…4001PN 25N4855For other radiator valves with type AV.. adapters refer to "Type summary / accessories"Radiator valves (M30 x 1.5) from other manufacturers, without adapter:· Heimeier · Crane D981..· TA-Type TBV-C · Oventrop M30 x 1.5 (from 2001)· MNG · Junkers · Honeywell-Braukmann · Cazzaniga · Beulco (new)Valves from othermanufacturers3-position control signalSSA31.. / SSA81..DC 0...10 V control signalSSA61, SSA61/004/10SiemensCE1N4893enSmart InfrastructureBuilding Technologies2020-05-11Combi valves VPI46../VPP46.. in combination with SSA61EP.. have an equal-percentage characteristics.· The valve opens / closes in equal percentage ratio to the control signal at Y.· At DC 0 V, the valve is fully closed (A à AB).· When power supply is removed, the actuator maintains its current position.1)Actuator is calibrated to 2.5 mm stroke of VPI46.15L06S t r o k e 2,5 m m (c a l i b r a t e d )1)2.42.51.510.500246810control signal Y [V]·Plastic housing·Locking-proof, maintenance-free gear train·Manual override with hexagonal socket wrench 3 mm ·Reduced power consumption in the holding positions·Load-dependent switch-off in the event of overload and in stroke end positions·Parallel operation of 6 SSA31.., 24 SSA81.. and 10 SSA61..possible, provided the controllers’ output is sufficient ·Terminal block connectors for customer made cables available (only for use with AC 24 V and AC / DC 24 V actuators)·Connecting cables with AC 24 V and AC 230 V connectors cannot be mixed up·Halogen-free cables availableAccessoriesAdapter types AV51 to AV61 are available for mounting the SSA.. actuators on third-party radiator valves as shown under "Type summary/accessories", page 2.1xtighten gentlyType ASY98 to secure the cable connector. Included in ASY99 and ASY100.The cable connector snaps into position,but can be additionally secured with the retaining screw.DC 0...10 V control signal SSA61EP,SSA61EP/00Features and advantagesAdapter type AV.. for third-party valves Tamper-proof fitting AL40Retaining screw ASY985/10SiemensCE1N4893en Smart Infrastructure2020-05-11For special cable lengths of the AC / DC 24 V actuators.·Type ASY99 for 3-position actuators SSA81../00·Type ASY100 for DC 0…10 V modulating actuators SSA61/00The terminal block connectors are supplied complete with mounting instructions (74 319 0385 0).Notes The actuators must be electrically connected in accordance with local regulations (refer to "Connection diagrams", page 9).Regulations and requirements to ensure the safety of people and property must be observed at all times!The permissible temperatures (refer to "Technical data", page 7) must be observed.The connecting cable of the actuator may come into contact with the hot valve body,provided the temperature of the valve body does not exceed 80 °C.Actuator types SSA 31.1 and SSA81.1 have a built-in auxiliary switch. The switch cannot be fitted in other actuators later.Mounting instructions (Ref. 74 319 0497 0) are enclosed in the product packaging.The actuator and valve are assembled with the coupling nut; no tools or adjustments are required.The actuator must be fitted in position 1 with the power disconnected (refer also to "Manual override", page 6):·Position the actuator and tighten the coupling nut manually ·Do not use any tools such as wrenches·Avoid lateral pressure or (cable) tension on the mounted actuator!In the case of actuators without a connecting cable (SSA../00), the separately orderedCrimp ferrule on stripped wire of connecting cable.When commissioning, check the wiring and the functioning of the actuator and auxiliary switch, if fitted.·Actuator stem extends (from position 1 to 0): Valve closes ·Actuator stem retracts (from position 0 to 1): Valve opens During commissioning and whenever the operating voltage is switched on,the SSA61.. runs a self-calibration routine. (Valve stroke 0® Max.stroke ® Setpoint).Never intervene manually in this process.ON0 %EngineeringMountingOrientationInstallationCommissioningTerminal block connectors ASY99ASY1006/10SiemensCE1N4893enSmart InfrastructureBuilding Technologies2020-05-11The second or third attempt at calibration occurs automatically after an 8-minute delay.After three failed calibration attempts the actuator stem remains in the extended position and the radiator valves are closed.For valves with strokes < 1.5 mm, the actuator/valve combination locks after three failed calibration attempts.The new Siemens type VDN.., VEN.. and VUN.. radiator valves have in all 1.5 mm stroke.A 3 mm hexagonal socket wrench can be used to move the actuator to any position.However, if a control signal from the controller is present, then this takes priority in determining the position.To retain the manually set position, unplug the connecting cable or switch off the operating voltage and the control signal.2.5 mm stroke5.5 mm strokeThe actuators are maintenance-free.When carrying out service work on the plant, following must be noted:·Turn power off (e.g. remove the plug)·If necessary, disconnect electrical connections from the terminals·The actuator must be commissioned only with a correctly mounted valve in place!SSA.. actuators cannot be repaired; the complete unit must be replaced.DisposalWarrantyThe technical data given for these applications is valid only when the actuators are used with the Siemens valves listed under "Equipment combinations", page 2.The use of the SSA.. actuators in conjunction with third-party valves invalidates any warranty offered by Siemens Building Technologies / HVAC Products.Note: Correctcalibration is only possible ·with valve·stroke > 1.5 mmOperationNoteManual overrideMaintenance!Repair7/10SiemensCE1N4893en Smart Infrastructure2020-05-11Technical dataPower supplyControlFunctional dataElectrical connectionsNorms and directivesDimensions /weight Housing colors 1)Provided the controller output is sufficient2)The documents can be downloaded from /bt/download8/10SiemensCE1N4893enSmart InfrastructureBuilding Technologies2020-05-11General ambient conditionsOperation EN 60721-3-3Transport EN 60721-3-2Storage EN 60721-3-1Environmental conditions Class 3K3Class 2K3Class 1K3Temperature +1...+50 °C –25...+70 °C –5...+50 °C Humidity 5...85 % r.h.< 95 % r.h. 5...95 % r.h.Connecting cableConnection terminalsY2Y1G4864Z 15Control signal CLOSE Control signal OPENSystem potential AC 24 VG0Y G4864Z 16System neutralControl signal DC 0...10 V System potential AC/DC 24 VFactory setting: 50 %0...50 % Q11® Q1250...100 % Q11® Q14The switching point can be adjusted by turning the switching cam with a screwdriver (see Mounting Instructions).Recommended connecting cable: H03VV-F, 2x0.5…0.75 mm 2.ASY3L.. with SSA31..ASY8L.. with SSA81..ASY6L.. with SSA61..ASY99for SSA81..ASY100for SSA61..Terminals for auxiliary switchesSSA31.1, SSA81.19/10SiemensCE1N4893en Smart Infrastructure2020-05-11Connection diagramsN Controller Y ActuatorL System potential AC 230 V NSystem neutralY1, Y2Control signal OPEN, CLOSE Q1, Q2Controller contactsN Controller YActuatorSP, G System potential AC 24 V SN, G0System neutralY1, Y2Control signal OPEN, CLOSE Q1, Q2 Controller contactsN Controller YActuatorSP, G System potential AC 24 V SN, G0System neutral Y Control signalSSA31..SSA81..SSA61..10/10SiemensCE1N4893enSmart InfrastructureBuilding Technologies2020-05-11DimensionsDimensions in mm8377484893M 0172.59M30 x 1,54893M 0298.5834889.5M30 x 1,59Revision numbersType reference Valid from Rev.-No.Type reference Valid from Rev.-No.SSA31K SSA61K SSA31/00K SSA61/00KSSA31.1K SSA81K SSA81/00K SSA81.1KActuator without auxiliary switch SSA31..SSA81..SSA61..Actuator with auxiliary switch SSA31.1..SSA81.1..Issued bySiemens Switzerland LtdBuilding Technologies Division International Headquarters Theilerstrasse 1a 6301 Zug SwitzerlandTel. +41 41-724 24 24/buildingtechnologies © Siemens Switzerland Ltd, 2005Technical specifications and availability subject to change without notice.。
SKD…U电子阀门驱动器安装说明说明书
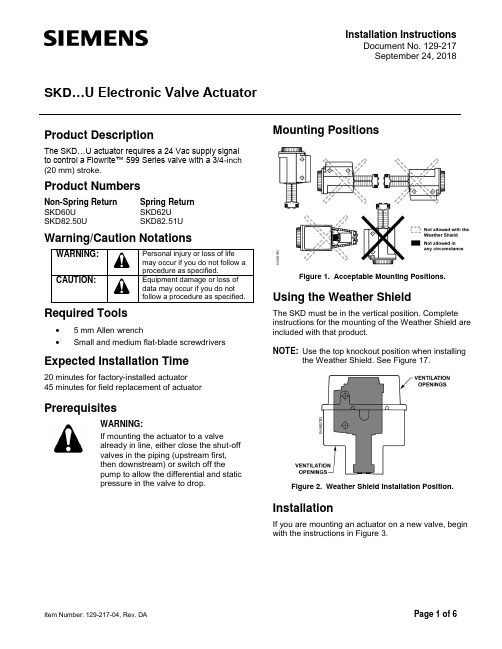
Installation InstructionsDocument No. 129-217 September 24, 2018SKD …U Electronic Valve ActuatorItem Number: 129-217-04, Rev. DAPage 1 of 6Product DescriptionThe SKD…U actuator requires a 24 Vac supply signal to control a Flowrite™ 599 Series valve with a 3/4-inch (20 mm) stroke.Product NumbersNon-Spring Return Spring Return SKD60U SKD62U SKD82.50USKD82.51UWarning/Caution NotationsWARNING:Personal injury or loss of life may occur if you do not follow a procedure as specified.CAUTION:Equipment damage or loss of data may occur if you do not follow a procedure as specified.Required Tools• 5 mm Allen wrench•Small and medium flat-blade screwdriversExpected Installation Time20 minutes for factory-installed actuator 45 minutes for field replacement of actuatorPrerequisitesWARNING:If mounting the actuator to a valvealready in line, either close the shut-off valves in the piping (upstream first, then downstream) or switch off the pump to allow the differential and static pressure in the valve to drop.Mounting PositionsFigure 1. Acceptable Mounting Positions.Using the Weather ShieldThe SKD must be in the vertical position. Complete instructions for the mounting of the Weather Shield are included with that product.NOTE: Use the top knockout position when installingthe Weather Shield. See Figure 17.Figure 2. Weather Shield Installation Position.InstallationIf you are mounting an actuator on a new valve, begin with the instructions in Figure 3.Document No. 129-217 Installation Instructions September 24, 2018Page 2 of 6 Siemens Industry, Inc.Removing the Actuator from the Valve1. Remove the actuator cover.2. Disconnect the wires and conduit, if installed.3. Loosen the valve stem retainer using a 5 mm Allenwrench and lower the valve stem into the valve. 4. Loosen the yoke nuts using a 5 mm Allen wrenchin the actuator yoke.5. Remove the actuator from the valve, being carefulnot to damage the valve stem.Continue with Mounting an Actuator to a Valve .Figure 3. Preparing a new Valve.Mounting an Actuator to a Valve.NOTE: Install the stem heating element,(P/N ASZ6.6), if used, before proceeding.Figure 4.NOTE: Ensure the yoke nuts are loose enough toallow the actuator to slip over the bonnet. See Figure 5.Figure 5.Figure 6.NOTE: Hold the stem retainer in place as you tightenit around the valve stem. See Figure 6.Figure 7.NOTE: Position the actuator to accommodate thewiring. Hold the actuator in place while tightening the yoke nuts. See Figure 7.Figure 8.1234 567Document Number: 129-217Installation Instructions September 24, 2018Siemens Industry, Inc. Page 3 of 6WiringCAUTION:Use care when removing the knockout. Do not damage the circuit board.Do not use autotransformers. Use earth ground isolating step-down Class 2 transformers.Determine supply transformer rating by summing total VA of all actuators used. The maximum rating for a Class 2 power supply circuit is 100 VA.ActuatorPower ConsumptionActuators Per Class 2 Supply Circuit* (80% of Transformer VA)S KD6…U 17 VA 4 SKD82.50U 13 VA 8 SKD82.51U18 VA5* Operating more actuators requires additional transformers or separate 100 VA power supplies.Wiring DiagramsSKD60U/SKD62U Figures 9 and 10 SKD82.50U/51UFigures 11 through 13SKD6…U12Figure 9. SKD6…U. DIP Switches1Selection of Control Signal 2Selection of Flow Characteristic ON 4 to 20 mAModified*OFF(Factory Setting)0 to 10 Vdc Default*Changing the default setting will modify an equalpercentage valve to a linear flow characteristic. When set to default, the flow characteristic is determined by the valve body.Figure 10.Connecting Terminals24 VacG System Potential (SP) G0 System Neutral (SN)Y Control Input: 0 to 10 Vdc or 4 to 20 mA(DIP switch selectable) Z Override Control(See Technical Instructions 155-180P25) M Measuring NeutralU Output for 0 to 10 Vdc or 4 to 20 mAmeasuring voltage. It will match the input signal type. The position output signal U will switch from 0 to 10 Vdc to 4 to 20 mA when a 4 to 20 mA input signal is selected and used on the terminal.Wiring for SKD82…UFigure 11. Location of Terminals.Document No. 129-217 Installation Instructions September 24, 2018Page 4 of 6 Siemens Industry, Inc.Wiring for SKD82…U , ContinuedFigure 12. Non-Spring Return SKD82.50U.Connecting Terminals G System Potential 24 Vac (+)Y1 Outward movement of coupling piece (0 to 1) Y2 Inward movement of coupling piece (1 to 0) Cm1 Limit switch for 100% strokec1 ASC9.3DU double auxiliary switch c2ASC9.3DU double auxiliary switch 1000 ΩASZ7.3 potentiometerThe diagram shows all possible connections. How many and which are used depend on the application.Figure 13. Spring Return SKD82.51U.Connecting TerminalsG System Potential 24 Vac (+) 21 System Neutral (SN) Y1 Outward movement of coupling piece (0 to 1) Y2 Inward movement of coupling piece (1 to 0) Cm1 Limit switch for 100% stroke c1 ASC9.3DU double auxiliary switch c2 ASC9.3DU double auxiliary switch 1000 Ω ASZ7.3 potentiometermany and which are used depend on the application.Start-UpCheck the wiring for proper connections.Consult Flowrite 599 Series SKD6xU Electronic Valve Actuators 24 Vac Proportional Technical Instructions 155-180P25 for detailed commissioning information.Normally Closed ValveActuator pressure cylinder moves: • Outward (0 to 1): Valve opens. •Inward (1 to 0): Valve closes.Normally Open ValveActuator pressure cylinder moves:• Outward (0 to 1): Valve closes. •Inward (1 to 0): Valve opens.Document Number: 129-217Installation Instructions September 24, 2018Siemens Industry, Inc. Page 5 of 6Three-Way ValveActuator pressure cylinder moves:• Outward: Valve opens between port NC and C. •Inward: Valve opens between ports NO and C.NOTE: The valve body assembly determines thecomplete assembly action.ReferenceTechnical InstructionDocument Number Flowrite EA599 Series SKD Electronic Valve Actuator Proportional Control155-180P25 Flowrite EA599 Series SKDElectronic Valve Actuator 3-position (Floating) Control155-181P25Manual OperationFigure 14. Manual Override in Manual and AutomaticPosition.Each complete revolution (360°) is equal to 3/32-inch (2.5 mm) stroke.Figure 15. Valve Stem Travel Indication.DimensionsFigure 16. Dimensions of the 599-10071 Weather Shield in Inches (Millimeters).Document No. 129-217Installation InstructionsSeptember 24, 2018Information in this publication is based on current specifications. The company reserves the right to make changes in specifications and models as design improvements are introduced. Flowrite is a trademark of Siemens Industry, Inc. Other product or company names mentioned herein may be the trademarks of their respective owners. © 2018 Siemens Industry, Inc.Siemens Industry, Inc. Building Technologies Division 1000 Deerfield Parkway Buffalo Grove, IL 60089-4513 USATel. +1 847-215-1000 Your feedback is important to us. If you havecomments about this document, please send themto ***************************************Document No. 129-217Printed in the USAPage 6 of 6Dimensions, ContinuedCAUTION:Be careful when removing the knockout. Do notdamage the circuit board.NOTE: Use the top knockout position when installing theWeather Shield.SERVICE ENVELOPEMINIMUM ACCESSSPACE RECOMMENDED4 inches (100 mm)8 inches (200 mm)Figure 17. SKD…U Dimensions in Inches (Millimeters).。
AUMA说明书中英文对照文稿

AUMA说明书中英文对照文稿操作说明手册的封面内容翻译(中英文对照):Multi-turn actuators万向驱动装置SA07.1-SA48.1 (产品型号)SAR 07.1-SAR 30.1 (产品型号)AUMA NORM (AUMA是这个阀门生产厂的品牌名称)AUMA标准Operation instructions (操作手册)目录内容:Scope of these instructions:本手册内容介绍的范围包括:These instructions are valid for multi-turn actuators for Open-close duty, SA 07.1-SA 48.1 ,and multi-turn actuators for modulating duty, SA07.1-SA 30.1.本手册的说明适应型号为SA 07.1-SA 48.1、具有开启-关闭功能系列的万向驱动装置和型号为SA07.1-SA 30.1、具有调节功能系列的万向驱动装置有效。
These operations instructions are only valid for “clockwise closing”, i.e. driven shaft turns clockwise to close the valve.这些操作说明只对"顺时针关闭"有效,即:驱动轴顺时针转动关闭阀门。
.Safety instructions (安全说明 )1.1 Range of application (应用的范围) AUMQ multi-turn actuators are designed for the operation of industrial valves, e.g, globe valves, butterfly valves and ball valves. For other applications, please consult us. AUMA is not liable for any applications. Such risk lies entirely with the user. AUMQ万向驱动装置是为工业用阀所设计的,例如:工业生产常用球瓣阀,蝶阀和球阀。
亚瑟 美国92系列电动阀门驱动器操作和维护手册说明书
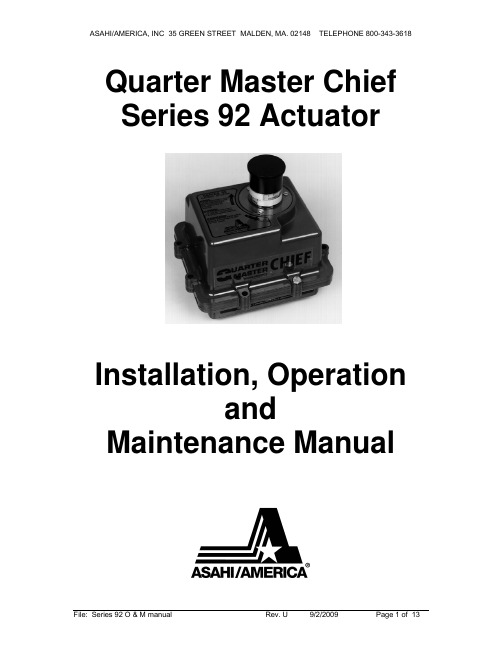
Quarter Master Chief Series 92 ActuatorInstallation, Operationand Maintenance ManualTable of ContentsSeries 92 Electric Actuator Introduction (3)Description (3)Electrical Requirement (3)Installation (4)Electrical (4)Type 21 Ball Valve (4)Type 23 Ball Valve (3-way) (5)Type 57 / 57L Butterfly Valves (5)Actuator Mounting Dimensions (6)Operation (7)Manual Override Operation (7)Setting Limit Switches (7)Options (8)Single Limit Switch (8)Double Limit Switch (8)Heater and Thermostat (8)Mechanical Brake (9)Feedback Potentiometer (9)Series 92 Options Codes for Serial # Tags (10)Troubleshooting (10)Maintenance (12)ATEX Requirements (12)Spare Parts (13)Series 92 Electric Actuator IntroductionDescriptionThe Series 92 electric actuators feature a reversing,capacitor run motor, with a permanently lubricated gear train, and hardened steel spur gears. These actuators are equipped with integral thermal overload protection (AC models) with automatic reset, independently adjustable limit switches, declutchable manual override, beacon position indication, baked powder epoxy coating with stainless steel trim, ISO bolt circle, and 2 (two) ½” NPT conduit entries.Standard models are offered in 115 VAC, feature a combination enclosure of Nema-4X, 7 & 9, and, provide up to 2000 in-lbs. of output torque.Various options are available such as operating voltages, additional limit switches, heater and thermostat, feedback potentiometers, etc.Please see page 8 regarding these options.Electrical RequirementWARNING: Do not open actuator cover while circuits are energized.CAUTION: Proper voltage must be supplied to actuator or damage will result.CAUTION: If 115vac & 220vac models are PLC driven, output contacts of PLC should be rated at a minimum of 1.5 times required input voltage of actuatorNOTE: To conform to various electrical codes, a green grounding screw has been provided (on the baseplate) inside of actuator.Terminal Strip Wiring: 75° C Copper Supply Wires up to #14 AWG, wired as per the attached diagrams or the wiring diagram affixed inside of actuator cover. Control Wiring shall be insulated with conductors rated 105° C, 300 V minimum.Torque Terminal Strip Wiring to 5 in-lbs.115 Vac 230 Vac 12 Vdc 24 Vdc 12 Vac 24 Vac Cycle Timeper 90 Model Torque Amp Duty Amp Duty Amp Duty Amp Duty Amp Duty Amp DutyDegrees (in/lbs) Draw Cycle Draw Cycle Draw Cycle Draw Cycle Draw Cycle Draw Cycle (seconds) S92 400 0.5 100% 0.4 100% 2.075% 4.075% 2.075% 3.0 75% 10A92 700 0.8 75% 0.6 75% 2.075% 4.075% 2.075% 3.0 75% 10B92 1100 0.5 100% 0.4 100% 2.075% 4.075% 2.075% 3.0 75% 25C92 2000 1.0 50% 0.6 50% 2.075% 4.075% 2.075% 3.0 75% 25 NOTE: Amp rating is considered locked rotor.Duty cycles are for ambient temperature (73°F)InstallationElectricalReference Drawing #289S92Models S-92, A92, & B921A. To gain access to terminal strip (Part #24) it is necessary to remove manual override knob (Part #18) by loosening slotted setscrew (Part #39). Remove 2 cover screws and cover; the remaining 6 cover screws are packaged inside the actuator. Torque cover/base screws to 120 in-lbs.Note: Failure to properly tighten cover/base flange fasteners to 120 in/lbs may compromise the certified safety factors of the actuator.Model C921B. To gain access to terminal strip it is necessary to remove manual override hand wheel (Part #18A) by loosening slotted setscrew (Part #39). Remove cam (Part #51) by loosening 2 set screws (Part #52). Remove 2 cover screws and cover; the remaining 6 cover screws are packaged inside the actuator.Torque cover/base screws to 120 in-lbs.All Models2. Make electrical connections to terminal strip as shown on wiring schematiclocated inside the cover (per various electrical codes there is a green screw on the actuator base plate for grounding purposes). Terminals are suitable for up to #14 AWG wire. All units are completely calibrated prior to shipment, and no internal adjustments should be required.3. For United States units, Install 1/2" NPT conduit fitting(s) to actuator base.For ATEX Certified European Union units, Install M20 x 1.5 conduit fitting(s) to actuator base.Note: Proper conduit fitting must be used to maintain enclosure rating and not compromise the certified safety factors of the actuator(weatherproof, explosion proof or combination weather proof/explosion proof). NOTE: We recommend sealing conduit openings on units installed outdoors or exposed to large temperature swings (15ºF or more).We also recommend the Heater and Thermostat option in these applications. 4. Replace actuator (gasket if removed) cover, and install 8 cap screws suppliedand tighten securely to 120 in/lbs. For outdoor or wet locations it isrecommended prior to replacing the cover that the top shaft seal be cleaned and coated with silicone grease. Also clean shaft and lightly coat seal area of shaft with silicone grease. Unit is now ready for operation.Type 21 Ball ValvePosition the valve and the actuator to corresponding positions (either OPEN or CLOSED). The flats on the actuator shaft extension indicate valve positionType 21 Ball Valves (See Drawing #0107BV sizes ½” – 2”)Install mounting bracket #3 to actuator #2 using bolts #8 and washers #9. Insert coupling #4 on stem of valve #1 and then bolt valve #1 to mounting bracket #3 using bolts #5, nuts #7, and washers #6.Note: All bolts should be snug and not excessively over tightened.Type 21 Ball Valves (See Drawing #0113BV sizes 2-1/2” - 4")Install mounting bracket #3 to actuator #2 using bolts #8 and washers #9. Insert coupling #4 on stem of valve #1 and then bolt valve #1 to mounting bracket #3 using bolts #5, nuts #7, and washers #6.Note: All bolts should be snug and not excessively over tightened.Type 23 Ball Valve (3-way)Position the valve and the actuator to corresponding positions (either OPEN or CLOSED). The flats on the actuator shaft extension indicate valve positionType 23 Ball Valves (3-way): (See Drawing #0130BV, sizes ½” - 4”)Install mounting bracket #3 to actuator #2 using bolts #8 and washers#9. Insert coupling #4 on stem of valve #1 and then bolt valve #1 tomounting bracket #3 using bolts #5, nuts #7, and washers #6.Type 57 / 57L Butterfly ValvesCAUTION: If valve is in line, system must be shut down and have no line pressure before removing throttle plate and retaining washer.Position the valve and the actuator to corresponding positions (either OPEN or CLOSED). The flats on the actuator shaft extension indicate valve position Butterfly Valves (See Drawing # 0200BF57 sizes 1-1/2” - 6”)No specially machined stem or valve body drilling required. Remove handle (remove handle cap and hex head bolt) to expose throttle plate screws. Remove throttle plate and retaining washer to expose existing bolt pattern.Mount bracket #3 to actuator #2 with bolts #8 and washers #9 and tighten evenly. Insert coupling #4 into actuator #2.Install valve #1 onto mounting bracket #3 and align stem of valve to engage with coupling. (Line scribed on top of stem indicates disc orientation). Install bolts #5, washers #6 and nuts #7 and tighten evenly. Flats on actuator shaft indicate valve position. (Disc Orientation)Butterfly Valves (See Drawing #0168BF57 8” size)No specially machined stem or valve body drilling required. Remove gear operator by removing 4 thru bolts in body of valve to gear operator and lift off. Mount bracket #2 to actuator #10 using bolts #7 and washers #8. Insert actuator shaft adapter #9 into actuator #10. Install valve #1 to mounting bracket #2 and align stem of valve to engage with coupling. (Line scribed on top of stem indicates disc orientation). Install bolts #3, washers #4 & #5 and nuts #6 and tighten evenly. Flats on actuator shaft indicate valve position. (Disc Orientation) CAUTION: If mounted unit is installed other than straight up, the actuator should be supported independently to prevent side loading and loosening up ofOperationManual Override OperationReference Drawing #289S92Models S-92, A92, & B92Pull up the declutching knob (Part #18) and apply a 5/8" open end wrench to exposed flats and rotate within labeled limits as indicated by arrows.To re-engage simply rotate actuator shaft in the opposite direction until declutching knob drops back down into position.Model C92Push down on hand wheel (Part #18A) and rotate within labeled limits.To re-engage simply rotate actuator hand wheel until it moves up and re-engages.CAUTION: The manual override should only be used when there is no power applied to actuator. When power is restored the actuator will automatically resume normal operation.Setting Limit SwitchesReference Drawing #289S92Open Travel Limit Switch (Top Switch Part #25):Using declutchable manual override, move the valve into a full open position. Then loosen set screws on top cam (Part #40) and rotate cam (CCW) into limit switch arm until a click is heard, this designates the switch circuit has opened and defines a full open position. Tighten 2 set screws (Part #40) on cam.Close Travel Limit Switch (Bottom Switch Part #25):Using declutchable manual override, move the valve to a full closed position, loosen set screws on bottom cam (Part #40) and rotate cam (CW) into limit switch arm until a click is heard, this designates the switch circuit has opened and defines a full closed position. Tighten 2 set screws (Part #40) on cam.Manually position valve to midstroke. Reapply power to actuator and drive to open or closed position. Actuator motor will run. The shaft will not turn until drivepins (Part #7) reseat in drive gear. This could take up to 25 seconds.OptionsModels S92, A92, B92, C92Single Limit SwitchInstall additional limit switch on posts on opposite side of standard limit switches using screws provided.Wiring for switch is as follows:Pink = Common to Terminal #6Purple = NC to Terminal #7Blue = NO to Terminal #8Cam must be set so that this switch is tripped just ahead of Closed limit switch. Wire tie loose wiring and check operation before installing cover.Double Limit SwitchInstallation and wiring is the same as for the single limit switch, with the additionof wiring of the second switch as follows:Brown = Common to Terminal #9Green = NC to Ternimal #10Orange = NO to Terminal #11Cam must be set so that this switch is tripped just ahead of Open limit switch. Wire tie loose wiring and check operation before installing cover.Heater and ThermostatModels S92 & A92Install Heater into threaded hole located between actuator base gasket andmotor module.Wiring is as follows:Heater lead = Terminal #12Thermostat lead = Terminal #13Wire tie loose wiring and check operation before installing cover.Models B92 & C92Install Heater into threaded hole located between actuator shaft and motor module.Wiring is as follows:Heater lead = Terminal #12Thermostat lead = Terminal #13Wire tie loose wiring and check operation before installing cover.Mechanical BrakeLoosen two (2) motor screws diagonally from each other and install bracket with tabs facing upward. Tighten screwsInstall hexagonal adapter over armature shaft and tighten set screws.NOTE: The adapter should be resting on the step of the armature shaft.Install brake assembly onto hexagonal adapter making sure that the brake assembly is sitting flush on the bracket. Tighten with supplied screws.Remove motor leads “A” & “B” from capacitor and install “piggy back connectors to capacitor, the re-install motor leads to their original locations.Connect brake leads to piggy back connectors on capacitor (orientation does not matter)Wire tie loose wiring and check operation before installing cover.Feedback PotentiometerUsing 4-40 x 3/8 hardware, install potentiometer and bracket on standoffs by limit switches, with potentiometer gear facing output shaft.Install drive gear face down over output shaft.Wiring for potentiometer as follows:#1 on potentiometer (black) #14 on terminal strip.#2 on potentiometer (white) #15 on terminal strip.#3 on potentiometer (red) #16 on terminal strip.Using multimeter set at 2k ohms, calibrate potentiometer with leads from meter connected to terminals #15 and #16. With actuator in closed position multimeter should read between 95 and 100 ohms.Rotate actuator 90 degrees (open position).Connect leads from multimeter to terminal #14 and #15; multimeter should read 95 to 100 ohms.If necessary adjust open limit switch cam so that multimeter will read 95-100 ohms.Series 92 Options Codes for Serial # TagsExample 1: S92HTP XWJHeater & thermostat and feedback potentiometer installed.Example 2: A92BRM1XWJMechanical brake and 1 extra limit switch installed.Troubleshooting WARNING: Do not open actuator cover while circuits are energized.Q: What if there is no output, but the motor runs?A: Manual override possibly engaged.When the manual override is engaged, the motor will run, but no output will be observed until the manual override re-engages with the output shaft.A: Valve stem broken. When the valve stem is broken, there will not be a change in fluid movement, making it seem as if the actuator has no output..Q: What if valve does not cycle?A: No power source to actuator. Check for power.A: Power source disconnected. Check for broken wire, loose connection or no connection as per appropriate wiring diagram.A: Low or wrong power source. Check for proper voltage.A: Mechanical Brake jammed or misaligned. Check alignment of brake assembly.This could occur during installation when someone would rest their hand on the Mechanical Brake to steady themselves. M1 1 extra limit switchM2 2 extra limit switches HT Heater & thermostat P Feedback potentiometer DP Dual feedback potentiometers C1 4-20 mA Positioner C3 4-20mA Output Transmitter BR Mechanical brake L2 2-Position Indicating Lights CO Center offCL Cycle length control 2W 2-wire control FS Failsafe Battery Pak A4 4-12mA Input Signal Positioner B12 Split Range Positioner ASI AS-I Bus Network CardQ: What if there is water and/or moisture inside of the unit?A: Conduit fitting installed improperly. Re-install correctly.A: Cover and/or base seal damaged. Replace damaged seal(s).A: Base gasket damaged or installed improperly. Check gasket and replace if necessary.A: Temperature swings of more than 15 degrees F. Install heater and thermostat to eliminate condensation.When these temperature swings occur, the unit will “sweat” on the inside causing internal corrosion unless the actuator is equipped with a heater and thermostat to keep a constant temperature inside of the housing.A: Unit has been submerged. Raise unit above liquid level.An actuator that is to be submerged MUST meet NEMA 6 for the proper protection of the actuator and the elimination of a potential hazard. We do not recommend submerging the Series 92 Actuator as the electrical rating does not meet NEMA 6.Q: What if unit is oscillating?A: Valve torque exceeds output torque of actuator. Check for chemical compatibility of valve, and flange torque.Q: What if thermal overload frequently cuts out motor?A: Frequency of operation exceeds duty cycle rating. Check cycling period.A: Unit is oscillating. Refer to above.Q: What if motor hums and no output is observed?A: Foreign material caught in valve. Remove material and inspect valve for damaged and/or worn parts. Replace parts as necessary.A: Unit wired incorrectly (simultaneously powering open and closed). Check wiring as per appropriate wiring diagram.A: Capacitor worn. Replace.Q: What if actuator “over-shoots” limit switches without stopping?A: Actuator wired in parallel to each other. Please note that each actuator requires it’s own set of switch contacts.MaintenanceDisconnect power!WARNING: Do not open actuator cover while circuits are energized. ArrayCAUTION: It is imperative for reducing the chance of electrical shock, and to prevent ignition of hazardous atmospheres that youDisconnect powerbefore any maintenance or repairs are performed.Series 92 actuators are virtually maintenance free. We do however, recommend that periodic checks are made to ensure that all fasteners are tight and properly torqued to extend the life of the actuator and valve.Series 92 Actuators are manufactured with factory lubricated grease in the gear case and gearbox. In most cases, this lubricant should never have to be replenished, however if deemed necessary, we recommend using Aeroshell Grease #33 MS, mfg. by Shell Oil Co.Consult our technical department before replenishing lubricant.For outdoor or wet locations keep top and bottom seals coated with a silicone based grease.ATEX RequirementsATEX Standard EEx d IIB Directive II 2 G Certified UnitsService/Maintenance/Inspection RequirementsAbove directive for hazardous location service electric actuators, for use throughout the European Union.All electric actuators are to be used for remote operation of a valve to open or closed positions. Any other uses are not approved by Asahi/America, Inc.Every 250,000 cycles or 10 years whichever comes first, the actuator must be removed from service and sent back to Asahi/America, Inc. for inspection of wear of bearings as they relate to joints and gaps in accordance with above directive. Any units not within normal tolerances, will need to be re-built or replaced at theusers expense.Spare PartsReference Drawing #289S92We recommend that the following be kept on hand as spare parts.1 --- Limit Switch (Part #25)1 --- Capacitor (Part #27 or #28)NOTE: When ordering replacement motor parts and/or options specify model # and voltage.Attachments:9 drawings: 0043EL, 0044EL, 0042EL, 0107BV, 0113BV,0130BV, 0168BF57, 0200BF57, 289S92。
电动蝶阀使用说明书(中英文)

电动蝶阀使用说明书(中英文)电动蝶阀Electric Butterfly Valve使用说明书Operation Manual一、用途Ⅰ.Application本系列蝶阀适用于冶金、矿山、建材、石化、造纸、纺织等行业的工业管道中。
它对气体半流体等管道中的介质按不同的信号,改变其流量的大小,从而达到自动调整风量,实现自动控制。
体阀采用优质钢板焊接结构,具有传动轻巧灵活,密封性能好,开闭时间短,切断速度快,能可靠的杜绝事故的发生。
This series butterfly valve is suitable to use in the industry pipe of metallurgical, ore building material. Paper textile and so on, Accord to the different signal in the pipes of the gas half fluid medium. Change the flow volume, and adjust the fan volume automatically. It can realize automatic control. The valve is used good welding structure. It is characterized by light, nimble good sealing, short open time, fast speed broken and dependable.二、结构及工作原理Ⅱ.The structure and Working principle1、电动蝶阀由电动执行机构和蝶阀组成,有关电动执行机构作用原理,使用维护等参阅电动执行机构说明书。
1、The electric butterfly valve is composed of electric executestructure and butter fly valve. The relative electric execute. Working principle and main is refer to the operation manual of electric executor.2、电动蝶阀按作业方式可分为电开式和电关式两种。
SKD32[1].62.82电动液压阀门执行器
![SKD32[1].62.82电动液压阀门执行器](https://img.taocdn.com/s3/m/54bfb0758e9951e79b8927ca.png)
5/10 Siemens Building Technologies HVAC Products 电动-液压阀门执行器 CM1N4561CN 12. 2002
安装位置
允许 允许 允许 允许 不允许 阀门安装指南与执行器同时提供。附件安装指南与所需附件同时提供。 调试注意事项 在调试过程中,进行接线和功能检查。另外,检查或对辅助开关、电位计和行程限位器 进行所需设置。
0 1
0 1
4561Z12
0 1
0 1
4561Z13
连接件完全收缩
连接件完全伸出
如果手动旋钮逆时针方向旋转到最终位置,阀门 VVF…, VVG…, VPF…, VXF…和 VXG…型号系列关闭(行程 = 0%)。
01330a
01330b
? MAN
? AUTO
手动运行 流量特征的出厂设置 维护注意事项
自动运行
仅适用于 SKD62 和 SKD62U:等百分比。
对于执行器的维护工作: • 停泵并切断电源,关闭阀门。系统管路减压使阀门冷却,如果需要,拆下电气连接。 • 如果执行器正确连接时,只需要重新调试阀门。 保证 执行器技术数据(Δpmax、ΔPs、泄露率、噪声水平、使用寿命)只适用于配套西门子 阀门(组合设备表).。 使用第三方设备应注意符合安全要求 技术数据 电源 工作电压 SKD32… SKD82… SKD62…
流量0 % 等百分比流量特性 (出厂设定) 线性流量特性
型号概览 标准版本
型号 SKD32.50 SKD32.51 SKD32.21 SKD82.50 SKD82.51 SKD62 型号 SKD82.50U
2/10 Siemens Building Technologies HVAC Products 电动-液压阀门执行器 CM1N4561CN 12. 2002
A-T CONTROLS 电动阀门和阻尼器阀门驱动器产品说明说明书

Confirmation of Product Type ApprovalCompany Name:A-T CONTROLSAddress:9955INTERNATIONAL BOULEVARD OH45246United StatesProduct:Actuator,Electric for Valves and DampersModel(s):KE-440,KE-880,KE-1700,KE-3500Endorsements:Certificate Type Certificate Number Issue Date Expiry DateProduct Design Assessment(PDA) Manufacturing Assessment(MA) Product Quality Assurance(PQA)23-2343935-PDA22-5418453NA31-JAN-202318-AUG-2022NA30-JAN-202820-AUG-2027NATier3-Type Approved,unit certification not requiredIntended ServiceMarine&Offshore ApplicationDescriptionOn-Off or Modulating service electrical operated actuator fitted with manual override,anti-condensation heater and thermostat for valves&dampers and other quarter-turn devices;Option Configurations:Convex lens visual position indicator.RatingsVoltage:110/220VAC,Single Phase,50/60Hz,12VDC(440&880models only)/24VDC;Operating Temperature:-4ºF to+140ºF(-20ºC to+60ºC);Enclosure IP rating:IP67;Actuator torque output;(i).KE-440,440In-Lbs.,50NM;(ii).KE-880,880In-Lbs.,100NM;(iii).KE-1700,1700In-Lbs.,200NM;(iv).KE-3500,3500In-Lbs.,400NM.Service Restrictions1.Unit Certification is not required for this product.If the manufacturer or purchaser request an ABS Certificate for compliance with a specification or standard,the specification or standard,including inspection standards and tolerances,must be clearly defined;2.Suitable for Non-hazardous area installation;3.The actuators are not to be used for valves on tanks containing flammable liquids,fire mains and fire dampers in high fire risk area such as machinery spaces unless fitted with approved insulation to ensure effective closure facility in the event of fire(ABS Marine Vessel Rules4-6-4/13.5.3b),MOU Rules4-2-5/3.9.2.).CommentsThe Manufacturer has provided a declaration about the control of,or the lack of Asbestos in this product;i)Setting and calibration of limit switches are to be in accordance with the manufactures' recommendation;ii)Cables for power supply and signals are to be suitable for intended service and environmental conditions(ABS Marine Vessels Rules4-8-3/9,4-8-4/21,27.9,MOU Rules4-3-3/5&4-3-4/7);iii)Where actuators are remotely controlled and used in propulsion and safety related systems,the complete control system and its associated electrical system for each application are to be submitted to ABS technical office for suitability review(ABS Marine Vessels Rules4-9-5/13.13).Notes,Drawings and DocumentationDocument No.30441,KE Series BOM,Revision:0,Pages:1Document No.KE Dimensional Dwg,KE Dimensional Dwg,Revision:0,Pages:N/ADocument No.No.DoC,KE Series Actuators Declaration of Conformity,Revision:n/a,Pages:1Document No.BST18011046630001Y-1SR-2,IP67Test Report,Revision:0,Pages:10,Dated:20 January2018Document No.0P221213.ZTASU33,ECM Certificate,Issuance dated:13December2022,Expiry date: 12December2027,Document No.WE XE XC KE Actuator Literature,WE XE XC KE Actuator Literature,Revision:0, Pages:N/ADocument No.IOM08069,Installation&Maintenance Manual,Revision:23July2020,Pages:7Term of ValidityThis Product Design Assessment(PDA)Certificate remains valid until30/Jan/2028or until the Rules and/or Standards used in the assessment are revised or until there is a design modification warranting design reassessment(whichever occurs first).Acceptance of product is limited to the"Intended Service"details prescribed in the certificate and as per applicable Rules and Standards.This Certificate is valid for installation of the listed product on ABS units which exist or are under contract for construction on or previous to the effective date of the ABS Rules and standards applied at the time of PDA e of the Product for non-ABS units is subject to agreement between the manufacturer and intended client.ABS RulesThe Rules for Conditions of Classification,Part1,2023Marine Vessels Rules1-1-4/7.7,1-1-A3,1-1-A4, which covers following:2023Marine Vessels Rules:4-8-3/1.3,4-8-3/1.11.1;The Rules for Conditions of Classification-Offshore Units and Structures,2023Mobile Offshore Units Rules:1-1-4/9.7,1-1-A2,1-1-A3which covers the following:2023Rules for Building and Classing Mobile Offshore Units:4-3-1/15.International StandardsN/AEU-MED StandardsN/ANational StandardsEN61000-3-2:2019/A1:2021,EN60947-1:2021.Government StandardsN/AOther StandardsN/ACorporate ABS ProgramsAmerican Bureau of ShippingPrint Date and Time:31-Jan-20233:53 ABS has used due diligence in the preparation of this certificate,and it represents the information on the product in the ABS Records as of the date and time the certificate is printed.If the Rules and/or standards used in the PDA evaluation are revised or if there is a design modification(whichever occurs first), a PDA revalidation may be necessary.The continued validity of the MA is dependent on completion of satisfactory audits as required by the ABS Rules.The validity of both PDA and MA entitles the product to receive a Confirmation of Product Type Approval.Acceptance of product is limited to the“Intended Service”details prescribed in the certificate and as per applicable Rules and Standards.This Certificate is valid for installation of the listed product on ABS units which exist or are under contract for construction on or prior to the effective date of the ABS Rules and standards applied at the time of PDA issuance.ABS makes no representations regarding Type Approval of the Product for use on vessels,MODUs or facilities built after the date of the ABS Rules used for this evaluation.Type Approval requires Drawing Assessment,Prototype Testing and assessment of the manufacturer's quality assurance and quality control arrangements.The manufacturer is responsible to maintain compliance with all specifications applicable to the product design assessment.Unless specifically indicated in the description of the product,certification under type approval does not waive requirements for witnessed inspection or additional survey for product use on a vessel,MODU or facility intended to be ABS classed or that is presently in class with ABS.Due to wide variety of specifications used in the products ABS has evaluated for Type Approval,it is part of our contract that; whether the standard is an ABS Rule or a non-ABS Rule,the Client has full responsibility for continued compliance with the standard.Questions regarding the validity of ABS Rules or the need for supplemental testing or inspection of such products should,in all cases,be addressed to ABS.。
- 1、下载文档前请自行甄别文档内容的完整性,平台不提供额外的编辑、内容补充、找答案等附加服务。
- 2、"仅部分预览"的文档,不可在线预览部分如存在完整性等问题,可反馈申请退款(可完整预览的文档不适用该条件!)。
- 3、如文档侵犯您的权益,请联系客服反馈,我们会尽快为您处理(人工客服工作时间:9:00-18:30)。
B H Montageanleitung H ?l Mounting instructions
Q Instructions de montage
M on te rin g s in s tru k tio n
CD M ontagehandleiding D Istruzioni di montaggio D As© 门nusohjo
Risk for skada vid trasig holje eller kapa Demontera ALDRIG stalldonet fran ventilen (kringflygande delar) Demontera ventil och stalldon som en enhet S kicka till S iem ens fo r analys och skrotning M ontera ny ventil och stalldon enligt m onteringsanvisning_____________________ Letselgevaar bij gebroken huis of deksel Aandrijving nooit van afsluiter demonteren (rondvliegende onderdelen) Afsluiter en aandrijving als geheel demonteren Naar Siem ens sturen voor analyse en verwijdering M onteer nieuwe afsluiter en aandrijving volgens m ontage instructies
Risque de blessure avec la com m ande manuelle ou le couvercle casse. Ne jam ais separer le servom oteur de la vanne (pieces volantes). Dem onter la vanne et le servom oteur comme une unite entiere. Envoyer I'unite entiere a Siem ens pour analyse M onter la nouvelle va nn e et le servom oteur selon les instructions de m ontage.________
1/lHCTpyKUMfl no yciaHOBKe
B 安裝指導
a cva tM
赢
Stellantriebe Actuators Servomoteur Stalldon Servomotoren Servocomandi Toimimoottorit Actuadores Motorer Silowniki
Pericolo di lesioni con custodia o coperchio rotto Non smontare MAI I'attuatore dalla valvola (parti volanti) Sm ontare la valvola e I'attuatore insiem e come se fosse un corpo unico Inviare entrambi a Siemens per I'anaiisi e lo sm altim ento M ontare una nuova valvola e attuatore secondo le istruzioni di m ontaggio______ Loukkaantumisvaara mikali kotelo tai kansi on rikki toimilaitetta El SAA irroittaa venttiilista (lentavat osat) Irroita venttiili ja toimilaite yhtena kappaleena Laheta Siemensille tutkittavaksi ja havitettavaksi Asenna uusi venttiili ja toim ilaite asennusohjeen mukaisesti
Pohony Szelepallito motorok
K iv n T h p £ ?
npuBOflbi
执行器
74 319 0325 0 M3250
SKD32..
C irn o o
o J v D o z ..
SKD62.. SKD60
AA
A Warning
Verletzungsgefahr bei gebrochenem Gehause oder Deckel Stellantrieb NIE vom Ventil demontieren (herumfliegende Teile) VentH-Stellantriebskombination als ganze Einheit demontieren I Siemens zur Analyse und Entsorgung at vorschriftgem ass m ontieren______________________________ Risk of injury with broken housing or cover I NEVER disassemble actuator from valve (flying debris) I D ism o u n t valve an d actuator as a whole unit Send to Siem ens for analysis and disposal M ount new valve and actuator according to mounting instructions
I门struccio 门6S de m ontaje
ES M onteringsvejledning
r a Instrukcja m onta之u m M on tazn 丨navod
nm Szerelesi utm utato
m 0 5 r ) Y ^ ? z \K O n 6 o ia o r\q