合成氨催化剂的生产和技术
合成氨的工艺流程
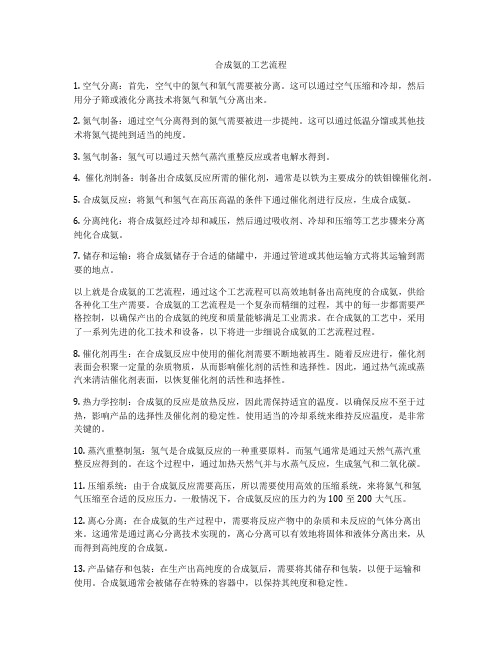
合成氨的工艺流程1. 空气分离:首先,空气中的氮气和氧气需要被分离。
这可以通过空气压缩和冷却,然后用分子筛或液化分离技术将氮气和氧气分离出来。
2. 氮气制备:通过空气分离得到的氮气需要被进一步提纯。
这可以通过低温分馏或其他技术将氮气提纯到适当的纯度。
3. 氢气制备:氢气可以通过天然气蒸汽重整反应或者电解水得到。
4. 催化剂制备:制备出合成氨反应所需的催化剂,通常是以铁为主要成分的铁钼镍催化剂。
5. 合成氨反应:将氮气和氢气在高压高温的条件下通过催化剂进行反应,生成合成氨。
6. 分离纯化:将合成氨经过冷却和减压,然后通过吸收剂、冷却和压缩等工艺步骤来分离纯化合成氨。
7. 储存和运输:将合成氨储存于合适的储罐中,并通过管道或其他运输方式将其运输到需要的地点。
以上就是合成氨的工艺流程,通过这个工艺流程可以高效地制备出高纯度的合成氨,供给各种化工生产需要。
合成氨的工艺流程是一个复杂而精细的过程,其中的每一步都需要严格控制,以确保产出的合成氨的纯度和质量能够满足工业需求。
在合成氨的工艺中,采用了一系列先进的化工技术和设备,以下将进一步细说合成氨的工艺流程过程。
8. 催化剂再生:在合成氨反应中使用的催化剂需要不断地被再生。
随着反应进行,催化剂表面会积聚一定量的杂质物质,从而影响催化剂的活性和选择性。
因此,通过热气流或蒸汽来清洁催化剂表面,以恢复催化剂的活性和选择性。
9. 热力学控制:合成氨的反应是放热反应,因此需保持适宜的温度。
以确保反应不至于过热,影响产品的选择性及催化剂的稳定性。
使用适当的冷却系统来维持反应温度,是非常关键的。
10. 蒸汽重整制氢:氢气是合成氨反应的一种重要原料。
而氢气通常是通过天然气蒸汽重整反应得到的。
在这个过程中,通过加热天然气并与水蒸气反应,生成氢气和二氧化碳。
11. 压缩系统:由于合成氨反应需要高压,所以需要使用高效的压缩系统,来将氮气和氢气压缩至合适的反应压力。
一般情况下,合成氨反应的压力约为100至200大气压。
合成氨的工艺流程

合成氨的工艺流程
合成氨是一种重要的化工原料,广泛应用于化肥、医药、塑料等多个领域。
其工艺流程主要包括氮气和氢气的催化反应,下面将详细介绍合成氨的工艺流程。
首先,合成氨的工艺流程是通过哈伯-玻斯曼过程实现的。
在工业上,通常采用铁-铝催化剂进行合成氨的催化反应。
反应的化学方程式为N2 + 3H2 → 2NH3。
在反应过程中,氮气和氢气在催化剂的作用下发生反应,生成氨气。
其次,合成氨的工艺流程需要高温高压条件。
反应温度通常在400-500摄氏度,压力在100-200大气压。
高温高压条件有利于提高反应速率和转化率,从而提高合成氨的产率。
然后,合成氨的工艺流程需要进行氮气和氢气的预处理。
氮气通常来自空分设备,需要进行脱氧、脱水等处理,以保证氮气的纯度和干燥度;而氢气通常来自重整装置,也需要进行脱氧、脱硫等处理,以保证氢气的纯度和干燥度。
此外,合成氨的工艺流程还需要进行氨气的分离和净化。
合成
氨反应产生的氨气中通常伴随着少量的氮气、氢气、水蒸气和杂质气体,需要进行分离和净化,以得到高纯度的合成氨产品。
最后,合成氨的工艺流程还需要进行废气处理。
合成氨反应产生的废气中含有一定量的氮气、氢气和氨气,以及少量的催化剂粉尘和有机物,需要进行处理,以达到环保排放标准。
综上所述,合成氨的工艺流程是一个复杂的化学过程,需要高温高压条件下进行氮气和氢气的催化反应,同时进行氮气和氢气的预处理,以及氨气的分离和净化,最终进行废气处理。
这一工艺流程的稳定运行对设备的稳定性和操作技术都有较高要求,但合成氨作为重要的化工原料,其生产工艺的不断改进和优化将对化工行业的发展起到积极作用。
合成氨的工艺流程
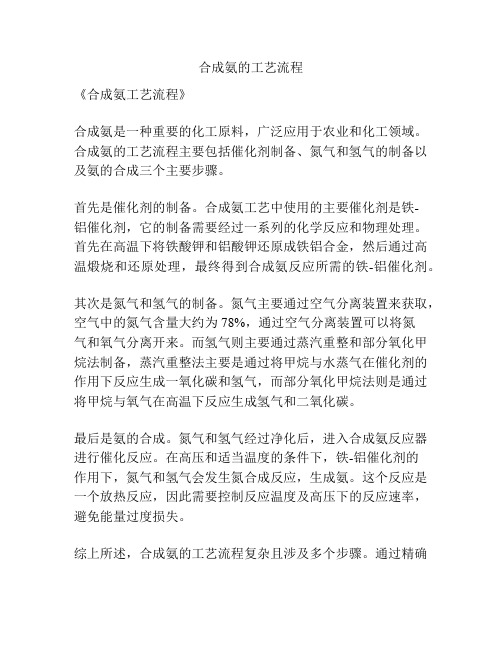
合成氨的工艺流程
《合成氨工艺流程》
合成氨是一种重要的化工原料,广泛应用于农业和化工领域。
合成氨的工艺流程主要包括催化剂制备、氮气和氢气的制备以及氨的合成三个主要步骤。
首先是催化剂的制备。
合成氨工艺中使用的主要催化剂是铁-
铝催化剂,它的制备需要经过一系列的化学反应和物理处理。
首先在高温下将铁酸钾和铝酸钾还原成铁铝合金,然后通过高温煅烧和还原处理,最终得到合成氨反应所需的铁-铝催化剂。
其次是氮气和氢气的制备。
氮气主要通过空气分离装置来获取,空气中的氮气含量大约为78%,通过空气分离装置可以将氮
气和氧气分离开来。
而氢气则主要通过蒸汽重整和部分氧化甲烷法制备,蒸汽重整法主要是通过将甲烷与水蒸气在催化剂的作用下反应生成一氧化碳和氢气,而部分氧化甲烷法则是通过将甲烷与氧气在高温下反应生成氢气和二氧化碳。
最后是氨的合成。
氮气和氢气经过净化后,进入合成氨反应器进行催化反应。
在高压和适当温度的条件下,铁-铝催化剂的
作用下,氮气和氢气会发生氮合成反应,生成氨。
这个反应是一个放热反应,因此需要控制反应温度及高压下的反应速率,避免能量过度损失。
综上所述,合成氨的工艺流程复杂且涉及多个步骤。
通过精确
控制每个步骤的条件和参数,可以确保生产安全高效地进行,从而满足氨的需求并为化工及农业领域提供丰富的原料。
合成氨催化剂的生产和技术

合成氨催化剂的生产和技术发布时间:2023-01-04T05:52:04.717Z 来源:《中国科技信息》2023年17期作者:张鹏[导读] 合成氨广泛用于工业硝酸、盐铵和化肥的生产过程,间接促进了国民经济的发展。
与此同时,有关工业对氨的需求以吨计有所增加,这是工业建设和化学发展的基本原料之一。
张鹏陕西黄陵煤化工有限责任公司陕西延安 727307摘要:合成氨广泛用于工业硝酸、盐铵和化肥的生产过程,间接促进了国民经济的发展。
与此同时,有关工业对氨的需求以吨计有所增加,这是工业建设和化学发展的基本原料之一。
但是,作为工业发展和国民经济的重要参与者,传统的合成氨往往消耗更多的能源,产生较少的效益。
因此,对合成氨催化剂的研究开发不断进行推导。
本文介绍了合成氨催化剂的研究开发,讨论了最新的合成氨研发趋势,供参考。
关键词:合成氨;催化剂;新技术;研究进展前言作为合成氨化工的重要原料,在中国工业建设和经济生产中发挥着十分重要的作用,合成氨相关催化剂的开发也是化工发展的重要组成部分。
但是,我们还必须认识到,合成氨工业在实际生产中也消耗大量能源在全球气候日益受到灾害威胁的时候,化学研究人员必须加倍努力,改进现有的催化剂,以提高合成氨工业的总体效率。
1 铁基催化剂的研究1.1铁系氨合成催化剂A-110-1催化剂是一种以铁-氨为基础的合成催化剂,主要由磁铁矿的传统熔炼形成。
为了提高催化剂活性和稳定性,结构催化剂如Al2O3、K2O、CaO、BaO等。
已添加到准备中。
其作用是利用这些高熔点折射氧化物作为活性物质的α-Fe晶体的绝缘材料,防止容易发生摩擦的微晶接触,从而提高催化剂体的热稳定性。
SiO2 _ 2通常是从磁铁矿原料引入的,其适当存在类似于Al2O3,它可以稳定铁颗粒,提高催化剂的热阻和水的毒性。
催化剂的组成和含量在熔化状态下相互作用,影响催化剂的活性和热稳定性。
尤其是还原催化剂表面化学成分对催化剂的活性和稳定性起着重要作用。
合成氨工艺催化剂

合成氨工艺催化剂引言合成氨是一种重要的化工原料,广泛应用于农业肥料、塑料、石油化工等领域。
在合成氨的生产过程中,催化剂起着关键作用。
本文将详细介绍合成氨工艺催化剂的种类、性能以及制备方法。
催化剂种类合成氨工艺催化剂主要分为三类,分别为铁基催化剂、铁铅共催化剂和铜铁催化剂。
铁基催化剂铁基催化剂是合成氨工艺中最常用的催化剂之一。
它使用铁作为主要活性组分,通常与铝、钛、硅等辅助载体配合使用。
铁基催化剂具有良好的催化性能和稳定性,能够在相对较低的温度下即可实现合成氨的转化。
铁铅共催化剂铁铅共催化剂是在铁基催化剂的基础上进行改进的一种催化剂。
它通过铅的引入,可以进一步提高催化剂的催化活性和选择性。
铁铅共催化剂在工业生产中有广泛应用,并取得了良好的效果。
铜铁催化剂铜铁催化剂是近年来发展起来的一类新型催化剂。
相比于传统的铁基催化剂,铜铁催化剂具有更高的催化活性和选择性。
这得益于铜与铁之间的协同作用,能够加速反应速率并改善催化剂的稳定性。
催化剂性能合成氨工艺催化剂的性能主要包括催化活性、选择性和稳定性。
催化活性催化活性是指催化剂对于反应底物的转化能力。
合成氨的生产过程是一个高温高压的反应过程,因此催化剂需要具备较高的催化活性,才能保证反应的效果和产量。
选择性选择性是指催化剂在反应过程中对不同反应产物的选择性。
对于合成氨工艺而言,目标产物是氨气,因此催化剂需要具备高的选择性,以避免产生过多的副产物。
稳定性稳定性是催化剂的另一个重要性能指标。
由于合成氨反应条件的严苛性,在长时间的反应过程中,催化剂会受到高温高压等因素的影响,容易发生失活。
因此,稳定性是评价催化剂性能的关键指标之一。
催化剂制备方法合成氨工艺催化剂的制备方法多种多样,常见的方法包括物理混合法、浸渍法和共沉淀法。
物理混合法物理混合法是最简单的制备方法之一,它将催化活性组分与载体物理混合,通过高温煅烧使其形成均匀分散的催化剂颗粒。
物理混合法制备的催化剂成本较低,但催化活性和稳定性相对较差。
合成氨的生产流程

合成氨的生产流程合成氨是一种广泛应用于农业和化工领域的重要化学品,它用作肥料和原材料,在现代社会具有重要的意义。
本文将深入探讨合成氨的生产流程,帮助读者更好地理解这一过程的关键步骤和技术。
一、引言合成氨是一种通过将氮气和氢气合成而成的无色气体。
它被广泛应用于农业领域,用于制造氨水肥料,也是合成其他化学品的重要原料。
合成氨的生产流程主要由催化剂反应、气体净化和氨合成等步骤组成。
二、催化剂反应在合成氨的生产过程中,第一步是制备催化剂。
常用的催化剂是铁或铑基催化剂。
这些催化剂具有高度的活性和选择性,能够促使氮气和氢气发生反应。
2.1 清洁气体合成氨的生产过程开始之前,必须先准备清洁的氮气和氢气。
这些气体通常来自裂解炉或氢氟酸生产工艺中的副产品。
在这一步骤中,气体被送入净化系统,去除其中的杂质和不纯物质。
2.2 压力调节氮气和氢气经过净化后,需要将其压力进行调节。
调节后的压力必须与催化剂反应器的工作压力相匹配,以保证反应的正常进行。
2.3 催化剂载体合成氨的催化剂是由催化剂载体和催化剂活性组分组成。
催化剂载体通常是铝、硅和稳定剂等物质的混合物,用于支撑和固定催化剂活性组分。
2.4 催化剂的还原催化剂在装配后,必须进行还原处理。
这一步骤的目的是去除催化剂中的氧化物,提高其活性。
催化剂通常置于高温下,并与一个还原剂(如氨气)反应,还原催化剂的金属离子。
2.5 反应区域设计在合成氨的生产过程中,催化剂反应器的设计十分关键。
反应器通常是由多层催化剂床组成,以提高反应效率。
而且,反应器会在压力、温度和流量等方面进行控制,以确保最佳的反应条件。
三、气体净化在通过催化剂反应产生氨气后,我们需要对气体进行净化处理,以去除催化剂的残留物和其他杂质。
3.1 氨气冷却合成氨反应产生的气体含有大量热量。
在净化处理之前,需要通过冷却处理降低气体的温度,使其达到适合净化的温度范围。
3.2 气体压力调节与催化剂反应步骤类似,氨气也需要在净化过程中进行气压的调节。
合成氨催化剂
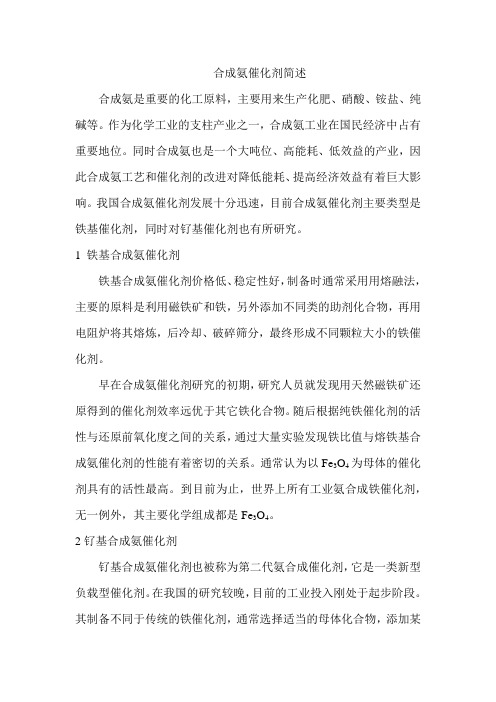
合成氨催化剂简述合成氨是重要的化工原料,主要用来生产化肥、硝酸、铵盐、纯碱等。
作为化学工业的支柱产业之一,合成氨工业在国民经济中占有重要地位。
同时合成氨也是一个大吨位、高能耗、低效益的产业,因此合成氨工艺和催化剂的改进对降低能耗、提高经济效益有着巨大影响。
我国合成氨催化剂发展十分迅速,目前合成氨催化剂主要类型是铁基催化剂,同时对钌基催化剂也有所研究。
1 铁基合成氨催化剂铁基合成氨催化剂价格低、稳定性好,制备时通常采用用熔融法,主要的原料是利用磁铁矿和铁,另外添加不同类的助剂化合物,再用电阻炉将其熔炼,后冷却、破碎筛分,最终形成不同颗粒大小的铁催化剂。
早在合成氨催化剂研究的初期,研究人员就发现用天然磁铁矿还原得到的催化剂效率远优于其它铁化合物。
随后根据纯铁催化剂的活性与还原前氧化度之间的关系,通过大量实验发现铁比值与熔铁基合成氨催化剂的性能有着密切的关系。
通常认为以Fe3O4为母体的催化剂具有的活性最高。
到目前为止,世界上所有工业氨合成铁催化剂,无一例外,其主要化学组成都是Fe3O4。
2钌基合成氨催化剂钌基合成氨催化剂也被称为第二代氨合成催化剂,它是一类新型负载型催化剂。
在我国的研究较晚,目前的工业投入刚处于起步阶段。
其制备不同于传统的铁催化剂,通常选择适当的母体化合物,添加某种促进剂,采用浸渍法负载在载体上,经一定条件还原活化处理后,转化成活性组分。
催化剂中母体化合物、载体、促进剂对所制备的催化剂的活性具有很大影响。
经历了近—个世纪的研究,合成氨催化剂技术可以说已相当成熟,但是传统的熔铁催化剂不符合低能耗的发展趋势,而钌基合成氨催化剂的价格昂贵,又不容易普及。
作为世界人口最多的农业大国和世界最大产氨国,合成氨工业对于我国国民经济的发展具有重要的战略和现实意义。
虽然国内对铁基催化剂的研究方面投入了大量的人力物力,但钌基合成氨催化剂的研究方面起步较晚,对于催化剂的作用机理也未进行深入研究,与国际先进水平的差距较大,这与我国是最大的产氨大国极不相称,因此我们合成氨这种高能耗产业的节能降耗还很漫长。
合成氨工艺流程详解
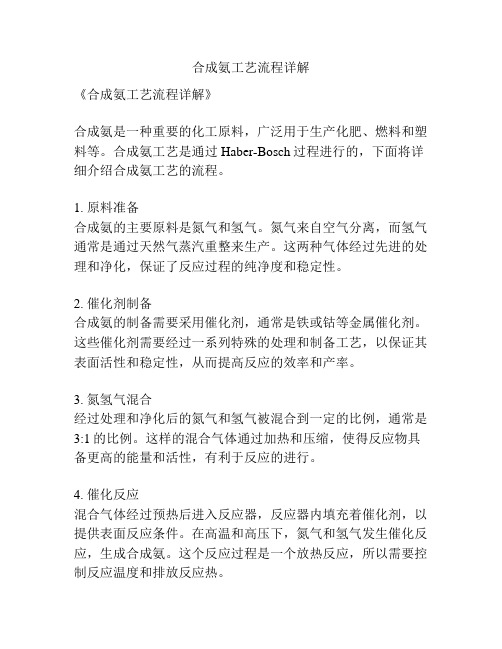
合成氨工艺流程详解
《合成氨工艺流程详解》
合成氨是一种重要的化工原料,广泛用于生产化肥、燃料和塑料等。
合成氨工艺是通过Haber-Bosch过程进行的,下面将详细介绍合成氨工艺的流程。
1. 原料准备
合成氨的主要原料是氮气和氢气。
氮气来自空气分离,而氢气通常是通过天然气蒸汽重整来生产。
这两种气体经过先进的处理和净化,保证了反应过程的纯净度和稳定性。
2. 催化剂制备
合成氨的制备需要采用催化剂,通常是铁或钴等金属催化剂。
这些催化剂需要经过一系列特殊的处理和制备工艺,以保证其表面活性和稳定性,从而提高反应的效率和产率。
3. 氮氢气混合
经过处理和净化后的氮气和氢气被混合到一定的比例,通常是3:1的比例。
这样的混合气体通过加热和压缩,使得反应物具备更高的能量和活性,有利于反应的进行。
4. 催化反应
混合气体经过预热后进入反应器,反应器内填充着催化剂,以提供表面反应条件。
在高温和高压下,氮气和氢气发生催化反应,生成合成氨。
这个反应过程是一个放热反应,所以需要控制反应温度和排放反应热。
5. 分离和提纯
产生的混合气体经过冷却后进入分离装置,将产生的合成氨和未反应的氮氢气体进行分离。
分离得到的合成氨会进一步进行脱水和提纯处理,使其符合工业用途的级别。
通过以上的工艺流程,合成氨可以有效地得到,而且具有较高的产率和纯度。
这个工艺流程成为了化工工业中的一种重要生产方式,为生产化肥和其他化工产品提供了重要的原料支持。
- 1、下载文档前请自行甄别文档内容的完整性,平台不提供额外的编辑、内容补充、找答案等附加服务。
- 2、"仅部分预览"的文档,不可在线预览部分如存在完整性等问题,可反馈申请退款(可完整预览的文档不适用该条件!)。
- 3、如文档侵犯您的权益,请联系客服反馈,我们会尽快为您处理(人工客服工作时间:9:00-18:30)。
合成氨催化剂的生产和技术钱伯章(金秋石化科技传播工作室,上海200127)摘 要 介绍了世界合成氨催化剂发展历程、新开发的合成氨催化剂种类,同时评述了我国化肥催化剂研发和生产近况,对我国化肥催化剂性能进行了评价。
关键词 合成氨 催化剂 化肥 生产 技术 进展收稿日期:2003-07-14。
作者简介:钱伯章,高级工程师,1963~1996年任职于中国石化上海高桥分公司,2001年创立金秋石化科技传播工作室,从事石油化工技术和经济信息调研和传播工作,获各种各级荣誉奖60余项,出版著作3部,发表论文500余篇。
1 合成氨催化剂的开发历程世界需求氮肥(折氮量)将从2001年11060亿吨增加到2003年11112亿吨,世界氮肥(折氮量)能力现为11327亿吨/年(合成氨能力116亿吨/年)。
2005年前,全世界将有约6150Mt/a 合成氨装置投产。
沙特阿拉伯化肥公司(SAFCO)(沙特基础工业公司子公司)兴建的世界最大单系列合成氨装置将于2005年投产,该装置能力为3kt/d(约110Mt/a),它比现有的最大装置大50%。
另外,4kt/d 规模的装置也已完成初步设计。
现在,世界最大单系列新建装置为阿根廷Profertil 公司的2105kt/d 装置,采用海尔德-托普索技术。
印度尼西亚博廷拥有2kt/d 装置。
巴斯夫在比利时拥有2106kt/d 装置,由乌德公司建设。
KBR 公司在特立尼达建有3套1185kt/d 装置,第4套装置正在建设中,第3套装置由加勒比氮肥公司运作,产能已达2kt/d,所有这几套装置都采用KBR 公司KAAP 技术(KB R 先进合成氨工艺)用于氨合成。
大型装置可实现经济规模,单系列装置规模翻番,可减少投资费用约20%,按照当今技术,放大到313kt/d 也是可行的。
KBR 己设计了4kt/d 装置,除主转化器和氨转化器为并列设置外,所有其他设备均为单系列。
世界大约10%的能源用于合成氨生产,所以,合成氨工艺和催化剂的改进将对矿物燃料的消费量产生重大影响。
自上个世纪80年代后期以来,合成氨技术继续向前发展,并建设了规模更大的装置,每吨合成氨生产的能耗也降到了28GJ 。
一种铁钴催化剂引入了ICI 公司的LC A 流程,LC A 工艺中合成内件的操作压力为8MPa 。
1992年,第一个无铁的氨合成催化剂由凯洛格公司(现KB R 公司)应用于其KAAP(Kellogg 高级氨合成工艺)工艺中。
这种钌催化剂以一种石墨化的碳作为载体。
据称其活性是传统的熔铁催化剂的10~20倍。
在反应中,这种催化剂具有不同的动力学特征,内件可在低于化学计量的氢/氮比及约9MPa 压力下操作。
自从Haber 和Mittasch 研究之后,几乎没有发现高活性的催化剂,因此熔铁催化剂仍是广泛应用的催化剂。
它具有高内在活性,长使用寿命和高密度特点,除这些优点外,它最公认的优点是价格便宜。
尽管熔铁催化剂有很多优点,但人们一直在努力开发新型催化剂,并对无铁类催化剂产生了浓厚兴趣。
上个世纪70~80,日本积极寻求开发钌基催化剂。
继在ICI AMV 和LCA 工艺中推出铁-钴系催化剂后,在KAAP 工艺中采用的以碳为载体的钌催化剂推动了氨合成催化剂的发展。
完全不含铁、不含钌的催化剂(如Cs/Co 3Mo 3N 催化剂),其活性介于熔铁类和钌系催化剂之间,活性低于钌系催化剂。
Cs/Co 3Mo 3N 催化剂、KM1R 催化剂(托普索的熔铁催化剂)和以碳为载体的含钡6%、含钌617%的催化剂在氢/氮比各为3B 1和1B 1的工艺条件下作出的对比可以看出,Cs/Co 3Mo 3N 催化剂的动力学特征介于熔铁和钌基催化剂之间,但它在600e 空气中焚烧时可再生成氧化性的粒子。
钌是贵重金属,其含量甚至比铂还稀少,1844年首次由俄国的Klaus提炼出来。
在Mittasch早期发现钌催化剂之后,钌系催化剂的开发一直没有进展,直到1970年,以硅藻土为载体的钌系催化剂在氨合成反应上的动力学研究引进日本,日本的研究者继续研究了大量的以钾促进的金属(C o、Ni、Re、Mo、Fe、Ru、Os)在碳载体上的活性,发现钌比传统的双金属铁催化剂活性更高。
1972年,日本报道了以石墨为载体的钌系氨合成催化剂的第一次应用,BP公司在1979年真正将其推向生产。
此后凯洛格公司接受BP公司的催化剂技术转让,共同开发并将这种催化剂应用在KAAP工艺中。
1992年加拿大的Ocelot氨生产公司在其工业化装置上第一个装填了钌系催化剂,此后其他两个工厂改造也装填了这种催化剂。
1998年首次采用KAAP工艺的两个工厂在Point Lisas和Trinidad地区建成投产,生产能力为1185kt/d。
KB R公司KAAP氨合成工艺在4个床层的3个床层中采用以活性炭为载体的钌催化剂,其活性比标准的熔铁催化剂高得多。
较高的活性使反应可在9MPa下进行,而常规技术为20MPa,因而可降低投资和能耗。
钌催化剂用于后面三个床层,可使合成氨产率提高到18%以上。
传统的合成氨原料氢/氮化学计量比为3B1,而由于含促进剂的钌催化剂的特性,所需原料氢/氮比较低,内件操作压力也较低,而产量较高。
但从热动力学观点,石墨在氨合成工业条件下很不稳定,而且钌对石墨加氢生成甲烷具有催化作用。
钡在较大程度上能抑制甲烷形成,但也不能完全避免。
对无促进剂和有促进剂的钌系催化剂有了较为详细的认识后,出现了几种改进型钌系催化剂,如Ruhler等开发了Ba-Ru/MgO催化剂具有较高的活性和稳定性,丹麦托普索(Tops<e)公司也开发了含钌的氨合成催化剂。
在这些研究中,镁铝尖晶石和高表面积石墨为载体的钌系催化剂显示出较好的活性。
然而,在工业条件下,它的稳定性还存在一定问题。
最近,以Ba促进BN(氮化硼)为载体的钌催化剂开发成功,它具有前所未有的活性和稳定性。
B N(以白石墨著称)对于钌系氨合成催化剂是很有潜力的载体材料,它与石墨几乎有相似的结构(除了在单层上面叠层稍有不同之外),与石墨不同的是,它在所有的加氢反应下都很稳定。
同时,它以高温电阻而闻名,与石墨相反,它是一种绝缘材料。
开发的Ba-Ru/B N催化剂在81m2/g载体上含有516%的Ba和617%的Ru,业已证明在5000h,10MPa,550e以及氢氮比为3B1的平衡条件下稳定性很好。
在特定的反应条件(温度、压力、氢/氮比、氨浓度等)下可选择适当的氮化硼表面积、钌浓度、助剂及浓度、颗粒大小及密度,以获得最佳的Ru/ B N催化剂的催化活性。
而且,可采用类似于处理Ba-Ru/MgO催化剂的方法来回收Ba-Ru/B N催化剂中有用的Ba、Ru、B混合物。
2新开发的合成氨催化剂丹麦哈尔多托普索研究实验室的研究人员研制成功可替代传统铁催化剂的系列产品。
研究人员发现,在工业装置操作条件下,三元氮化物,如Fe3Mo3N、C o3Mo3N和Ni2Mo3N用作合成氨催化剂时活性高,稳定性好。
另外,如果在Co3Mo3N催化剂中加入铯,则活性将高于目前使用的铁催化剂。
据报道,在相同操作条件下,如温度400e、压力20MPa、氢氮比3B1,以铯为助催化剂的Co3Mo3N 的活性为传统铁催化剂活性的2倍。
德国鲁尔(Ruhr)大学开发了一种氨催化剂。
这种催化剂由金属钡、金属钌和氧化镁组成。
据称,它比现有的合成氨催化剂产氨更多,寿命更长。
据报道,这种钡-钌催化剂活性比传统的铁基催化剂或者其他类型的钌基催化剂活性高2~ 4倍,研发的这种钡-钌催化剂与铈-钌催化剂相比,可以产生双倍的氨产量。
如果对钡与钌比率进行优化,还能进一步增加氨产量。
3我国研发和生产合成氨催化剂近况中国是世界最大产氨国,年需各类制氢催化剂约20kt,预计2010年需要量为27kt,现有装置能力已能满足。
规模及原料的多样性使我国万吨氨的催化剂单耗高于国外平均值,但大型氨厂催化剂的使用已达到国际先进水平。
我国大型化肥企业使用催化剂总体水平较高,催化剂的使用呈现出国产化率逐年提高、催化剂的使用消耗量逐步降低、使用催化剂的种类和总量进一步减少以及新型催化剂的应用不断增多等特点。
目前,全国正在运行的引进大型制氨装置(年产300kt/a合成氨、520kt/a尿素)共29套,对这些装置催化剂使用情况的调查结果显示,2001年我国大化肥催化剂国产化率已达到93197%,国产催化剂无论在品种上,还是在质量上均能满足不同流程制氨装置的要求。
近年各类制氨催化剂需求量见表1。
表1近年各类制氨催化剂需求量t催化剂2000年2001年加氢转化130170净化剂1)45001800蒸汽转化2)8001040铁系高变1120011400铁钼宽变23002500铜系低变12001400甲烷化450500氨合成51605360合计25740271701)包括氧化锌脱硫剂、氧化铁脱硫剂、脱氯剂、脱砷剂等;2)包括一段转化、轻油转化、二段转化。
我国合成氨催化剂涉及脱毒剂、烃类蒸汽转化、变换、甲烷化和氨合成5大类,以高(中)温变换和氨合成催化剂消耗量最大,约占合成氨催化剂总消耗量的70%。
我国合成氨年产量已超过34Mt,按万吨氨平均耗催化剂6126t计算,年需要催化剂211284kt。
(1)有机硫加氢转化催化剂有机硫加氢转化催化剂主要有钴钼催化剂和铁钼催化剂2种,该类催化剂在大型合成氨装置平均使用寿命已超过10年,使用技术已达国外先进水平。
降低床层阻力、堆密度及使用温度,提高活性,实现器外预硫化是今后的发展趋势。
南京化学工业公司催化剂厂积极参与国际石油化工市场竞争,加速推出新产品。
该厂与安庆石化、金陵石化合作开发的NC9802型炼厂气加氢催化剂,使炼厂气代替石脑油作为大化肥制氢原料变为现实,大幅度地降低制氢成本。
鉴定认为,该项技术填补了国内空白,具有国际先进水平。
NC9802型加氢催化剂具有高空速、耐低硫、自然硫化等特性,用于大化肥原料路线改变,以焦化干气代替石脑油生产合成氨,可有效降低生产成本。
金陵石化公司在年处理60kt炼厂气装置上使用,催化剂的活性、选择性和稳定性良好。
(2)脱硫剂及其他净化剂脱硫剂主要有氧化锌脱硫剂、铁锰脱硫剂和氧化铁脱硫剂,高温复合氧化物脱硫剂是今后的发展趋势。
其他净化剂主要有脱氯剂、脱砷剂等。
氧化锌脱硫剂是以ZnO为主要组分,添加CuO、MnO、Al2O3等促进剂的精细脱硫剂,因其脱硫精度高、使用简便、性能稳定可靠、硫容高而占据着重要地位,广泛应用于合成氨、制氢、合成甲醇、煤化工、石油炼制、饮料生产等行业,以脱除天然气、石油馏分、油田气、炼厂气、合成气(H2+ CO)、二氧化碳等原料中的硫化氢及某些有机硫。
由于氧化锌脱硫剂可将原料气(油)中的硫脱除到015~01l L g/g以下,从而保证了下游工序的蒸汽转化、低变、甲烷化、甲醇、低压联醇、羰基合成等含镍、铜、铁及贵金属催化剂免于硫中毒。