含铜废水回收
铜氨废液中铜回收的新工艺流程

铜氨废液中铜回收的新工艺流程铜氨废液是一种常见的含铜废水,通常产生于电镀、冶炼和化学制剂生产等工业过程中。
传统的铜氨废液处理方法主要是通过化学还原、溶解、电析和电积等步骤将废液中的铜回收。
然而,这些方法存在着许多问题,包括操作复杂、设备投资高、产生大量废物等。
为了解决这些问题,近年来出现了一种新的铜回收工艺流程,该工艺使用离子液体作为溶剂,并借助离子液体的独特性质实现高效的铜回收。
离子液体是一类由有机阳离子和无机阴离子组成的液体。
其具有低熔点、广阔的电化学窗口、优异的溶解性能和良好的可重复使用性等特点,因此在废液处理等领域具有广泛的应用前景。
对于铜氨废液处理而言,离子液体可以替代传统的有机溶剂,与废液中的铜离子发生配位反应并形成络合物,实现铜的有效回收。
基于离子液体的铜回收工艺流程一般包括以下几个步骤:1. 提取:首先将铜氨废液与适量的离子液体混合,通过相分离技术将铜络合物从废液中提取到离子液体相中。
2. 洗涤:将离子液体相中的铜络合物用水或酸性溶液进行洗涤,去除其中的杂质和离子液体残留。
3. 脱水:通过蒸发或其他适当方法将洗涤后的溶液中的水分脱除,得到含有高浓度铜络合物的浓缩液。
4. 还原:将浓缩液与适量的还原剂反应,将铜络合物转化为可溶性的金属铜。
5. 结晶/电积:通过结晶或电积等方法将金属铜从溶液中回收,得到高纯度的铜产品。
可以看出,基于离子液体的铜回收工艺流程相比传统的方法具有以下优势:1. 高效:离子液体作为溶剂,能够与废液中的铜离子快速发生配位反应,并形成稳定的络合物,提高了铜的提取效率。
2. 环保:离子液体具有低挥发性和低溶解性有机物的特点,因此在铜回收过程中几乎没有挥发物和废气排放,达到了绿色环保的要求。
3. 经济:离子液体的可重复使用性和稳定性很高,可以降低处理成本,并减少废物的产生。
4. 高纯度:离子液体的溶解性能良好,可以实现对铜的高效分离和纯化,得到高纯度的铜产品。
总结起来,基于离子液体的铜回收工艺流程是一种具有广泛应用前景的新型工艺。
废水中重金属电化学法回收实验报告

6 废水中重金属电化学法回收化工、印染、电镀、有色冶炼、有色金属矿山开采、电子材料漂洗废水、染料生产等过程中常产生含有大量铜离子的废水。
铜是工业废水中非常常见的重金属,若不经适当的处理直接排入环境中,会严重威胁水生态系统健康,并通过食物链危害人体健康。
目前处理含铜废水的方法主要有化学絮凝、离子交换、电解法等。
本实验主要采用电解法处理含铜废水,电解法可直接得到金属铜并且具有操作简单、易实现自动化和设备化控制等优点。
6.1实验目的(1) 了解电解法处理含铜废水的原理和方法;(2) 计算不同电流密度条件下得到铜的电流效率。
6.2实验原理电解法基本原理是当电流通过电解质溶液时,溶液中的阳离子发生离子迁移和电极反应,即废水中的阳离子向阴极迁移,并在阴极上产生还原反应,使金属沉积。
电流效率是电解生产过程中的一项重要的技术经济指标。
电流效率是指电解时在电极上实际沉积或溶解的物质的量与按理论计算出的析出或溶解量之比,通常用符号η表示。
其中铜的电化当量为1.185g/A∙h。
6.3实验设备及条件6.3.1 实验装置电解实验装置如图6.1 所示。
本实验采用烧杯盛装铜离子废水溶液,极板间距20 mm。
实验中采用DH1765-1 型程控直流稳压稳流电源(35 V,3A),采用磁力搅拌器对溶液进行搅拌,以使电解液在反应器内分散均匀。
磁力加热搅拌器图6.1 实验装置图6.3.2仪器及化学试剂仪器:电子天平,精度为万分之一克;烘箱;磁力搅拌器;直流稳压电源;pH计。
实验材料:实验中阳极采用石墨板、阴极均采用铁板,极板尺寸为115 mm ×65 mm × 2 mm ( 有效面积68 cm2 )。
化学试剂:硫酸铜;去离子水;器皿:500ml烧杯;搅拌子;6.4实验步骤(1)配置模拟实验废水:用天平称取一定量CuSO4∙5H2O加入到去离子水中,使Cu2+初始浓度保持在C(Cu2 +) = 40 mg∙L-1置于烧杯中,用硫酸调整溶液pH为5。
乳状液膜法回收酸性含铜废水中的铜

t h e P 2 o 4 v o l u me f r a c t i o n wa s 5 9 / 6 ,t h e S p a n 8 0 v o l u me f r a c t i o n wa s 3 9 / 6 , t h e R 0 j w a s 1:1 ,a c i d c o n c e n t r a —
H0U Xi n - g a n g .YI N Ha o - l i a n g
( 1 .Col l e g e o f Ma t e r i a l s S c i e n c e a n d En g i n e e in r g,L a n z h ou Un i v .o f Te c l  ̄ ,La n z h o u 7 3 0 0 5 0,Ch i n a;2 .S t a t e Ke y La b o r a t o r y o f Ga n s u Ad—
离子交换法处理含铜废水试验
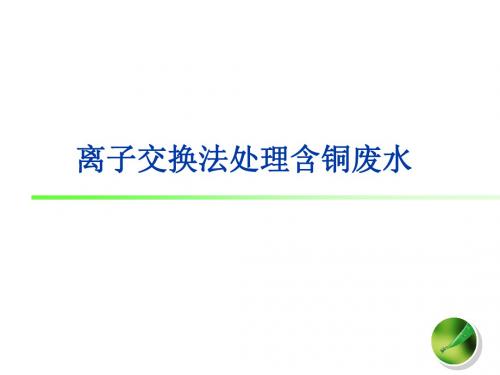
1mL,新铜试剂1mL,用去离子水稀释至刻度, 摇匀后静置5分钟,在可见分光光度计上于457 nm,用2 cm玻璃比色皿比色。以试剂空白作参 比测定溶液吸光度,以吸光度-铜含量(μg)绘制 标准曲线
铜含量的计算
定时( 0,5,10,20,30,45,60,90分钟)收集
出水,吸取2mL到刻度试管,其它试剂加入同标准 溶液测定 水样中铜离子含量Y(μg/mL)的计算 Y=A*X/V 式中: A 从标准曲线查得的铜离子含量,微克; X 稀释倍数; V 测定时取处理后水样的体积,毫升。
子交换柱,不同时间在出水口收集出水
采用比色法测定出水中铜离子浓度
显色反应
盐酸羟胺+Cu2+
Cu+
新铜试剂 +Cu+
黄色
样品分析- 新铜试剂比色法
准确吸取铜标准溶液0,0.2,0.4,0.8,1.0,1.6,
2.0mL分别放入7支10 mL具塞比色管中,加水 至5mL
依次加入10%盐酸羟胺0.5mL,柠檬酸钠溶液
剂、盐酸羟胺分别起什么作用?试剂加入顺
序是随机的还是有序的?
六、思考题
3. 比色反应中参比溶液是水,还是包含柠
檬酸钠、新铜试剂、盐酸羟胺的溶液?
4. 比色法和火焰原子吸收法在原理和分析
过程中有什么差别? 5. 新树脂的活化过程是怎样的?污染树脂 的再生过程是怎样的?
行的。在处理之前,一般先用活性炭去除水中的
可溶性有机碳(DOC),防止对铜吸附的干扰。
二、实验原理
常用阳离子交换树脂处理含铜废水,首先 将001阳离子交换树脂转型为H型树脂。 树脂活化:NaCl;盐酸;氢氧化钠 离子交换所遵循的原则和顺序
含铜废水处理、回收实验报告

重金属处理剂实验报告--------2013.12.31一:方法提要用晨源生产的重金属处理剂吸附水体中的重金属离子,并保持稳定;在磁场作用下,使重金属处理剂与铜离子的复合物定向移动,进行分离,从而达到铜离子去除的目的。
同时考察了负载了重金属离子的吸附材料用酸溶液处理后循环利用的吸附效率,以及处理剂将重金属离子吸附后转移并释放从而达到回收重金属的能力。
二:试剂和材料1硫酸铜溶液:(铜离子含量100ppm)。
2重金属处理剂:自备。
3稀硫酸:1%。
4氢氧化钠溶液:1%。
三:仪器和设备1、火焰原子吸收光谱仪中空阴极灯管分析波长324.7nm,光普通带宽带0.5nm,灯电流4mA,燃烧器高度 5.0nm,乙炔气流量 1.1L/min,原子化方法空气-乙炔火焰法,背景校正氘灯2、超声仪3、烧杯、量筒、试管、镊子、移液管、容量瓶等。
四:实验步骤1、配置浓度为100ppm的实验铜离子水样2、取400ml水样于烧杯中,分别用硫酸和NaOH调节PH至7、83、加入重金属处理剂后,室温下超声震荡2h4、磁力分离底部沉淀,上清液用原子吸收光谱仪测量所含金属离子的浓度。
5、取底部沉淀(重金属处理剂吸附重金属),经磁分离干燥后,加酸酸化调节PH至3,超声30min,测量溶液重金属浓度6、重复上述步骤测量重金属处理剂二次吸附和解吸附、三次吸附和解吸附的重金属浓度7、计算。
根据实验结果,计算磁性纳米材料去除铜离子效率。
铜离子去除效率根据如下方程计算:q=(Co-C1)/Co式中,Co:溶液中金属离子的初始浓度,mg/L;C1:溶液中金属离子的平衡浓度,mg/L。
五:实验数据编号重金属处理PH重金属浓度(ppm)重金属回收率重金属去除率剂用量1(空白)0N/A112.853520.04g(100ppm)70.255699.77%3(一次解吸附)3109.384296.93%4(二次吸附)70.302099.72%5(二次解吸附)3104.478595.52%6(三次吸附)7 4.940898.14%附注:1#为所配置的原铜离子水样的浓度2#为经过添加重金属处理剂处理后的铜离子浓度3#为将2#水样经重金属处理剂处理后,取下层经磁分离后的重金属沉淀重新加酸酸化后释放出的重金属浓度4#为重金属处理剂经回收后的二次处理重金属浓度5#为二次处理后吸附的重金属沉淀重新加酸酸化后释放出的重金属浓度6#为重金属处理剂经回收后的三次处理重金属浓度六:实验结论:1、晨源生产的重金属处理剂在PH为7时,对铜离子有较大的吸附效率,可达99.77%;2、负载了重金属铜离子的处理剂经酸化至PH为3时,可将所携带的重金属重新释放出来,一次回收率达96.93%,二次回收率达95.52%3、重新回收利用的重金属处理剂在三次使用中,铜离子去除率有微小的减小,三次重金属处理率分别为99.77%,99.72%,98.14%,处理能力均保持在98%以上。
络合铜废水处理工艺

络合铜废水处理工艺络合铜废水处理工艺是一种用于处理含有铜离子的废水的技术。
铜是一种常见的金属元素,广泛应用于电子、电镀、冶金等行业,但其废水排放对环境造成严重污染。
因此,开发一种高效、经济的络合铜废水处理工艺具有重要意义。
络合铜废水处理工艺的核心原理是利用络合剂与铜离子形成络合物,使其从废水中被吸附或沉淀下来,达到去除铜离子的目的。
经过多次试验和实践,科研人员发现了多种有效的络合剂,如有机酸、有机胺和螯合剂等。
这些络合剂具有良好的络合性能,能够与铜离子迅速发生络合反应,形成稳定的络合物。
在络合铜废水处理过程中,首先需要对废水进行预处理,去除其中的悬浮物和有机物。
然后,将络合剂加入废水中,与铜离子发生络合反应。
经过一段时间的反应,络合物会逐渐形成,并沉淀到底部。
最后,通过沉淀、过滤等工艺,将络合物与废水分离,得到清洁的废水。
络合铜废水处理工艺具有许多优点。
首先,它可以高效去除废水中的铜离子,使废水达到国家排放标准。
其次,络合剂使用量少,成本低廉,适用于大规模生产。
再次,该工艺操作简便,易于控制,适用于各种工业废水的处理。
最重要的是,络合铜废水处理工艺对环境友好,能够减少对水资源的污染,保护生态环境。
然而,络合铜废水处理工艺也存在一些问题和挑战。
首先,选择合适的络合剂对于工艺的成功至关重要。
不同的废水成分可能需要不同的络合剂,因此需要进行充分的实验和研究。
其次,处理废水所需的时间较长,需要一定的耐心和耐久性。
此外,处理后的废水中可能仍含有微量的铜离子,需要进一步处理。
络合铜废水处理工艺是一种有效的废水处理技术,能够高效去除废水中的铜离子。
通过合理选择络合剂、优化工艺参数,可以实现废水的高效处理和资源回收利用。
在今后的工程实践中,我们应该进一步探索和创新,提高络合铜废水处理工艺的效率和可行性,为保护环境、减少污染作出更大的贡献。
铜矿废水的处理及铜的回收

膜提高一级浓缩的效率 ; 二级浓缩时 , 在 由于浓缩倍 数很高 , 膜表面溶 液的离子浓度大幅升高, 容易 出现结 晶浑浊 , 卷式膜 的结构流道易被结 晶物堵塞的特点 , 决定 了它不适合作 为二级浓缩 , 因此本试验选取管式 纳滤膜进行二级浓缩 。
3处 理 效 果分 析 .
31 . 浓缩过 程的结 晶现象 由于浓缩 液的结晶盐析出对卷式膜 的正 常运行有较大 的影响 , 在 工业 系统 中必须避免出现 。因此 , 在本 试验过程 中, 一旦 发现浓缩液 出 现浑浊 , 即视为浓缩终点 。具体情况如表 2 。 表 2浓缩倍数与浑浊现象 操作批次
一
浓缩液 C ( gL um/)
项目
p H
级反渗透
批次 1
23 l
1.4 1 6
批次 2
2 92 5.
77 .5
批次3
2 24 4.
3 3
平均值
28 3
8
进料液 C ( /) u mgL
透 析 液 C ( gL um/)
TS D 电 导 率 F e C U C a N a ( mg ) ( s r ( / ) ( / ) ( / ( /) / m / r mgL mgL mg L c L) mg L
2 8 10
浓缩倍数
1 6
浓缩液外观
有 沉 淀 析 出
级R O批 次 I
一
级R O批 次 2 级R O 8
浑浊少量沉淀 浑浊少量沉淀
一
由于试验设备 限制 , 试验 出现浓缩液结 晶浑浊时 , 无法及时停机检 测, 因此导致浓缩终点 的浓缩倍数不尽相 同。由表 2批次 2和批次 3的 数据可以看出 ,浓缩 至 8倍 时,浓缩液开始 出现浑浊并有少量沉淀析 出 。 因此 , 可推 测 浓 缩 极 限 为 8 。 倍 32一级 R . O浓 缩 的通 量 变 化 试验中采用反渗透 4 O 进行一级浓缩 , FI 运行温度控制在 1~2 ℃, 9 2 运行压力控制在 1br共进行 了三个批次 的运行试验 。图 2是一级反 7 a, 渗透膜运行通量与运行时间的关系图。 从图 中反渗透的运行通量来看 , 在浓缩终点前 , 反渗透保持较高 的运行通量且通量较为稳定 ,反渗透 4O F I的平 均 通量 为 3 .L 3O MH。
含铜废水处理方法
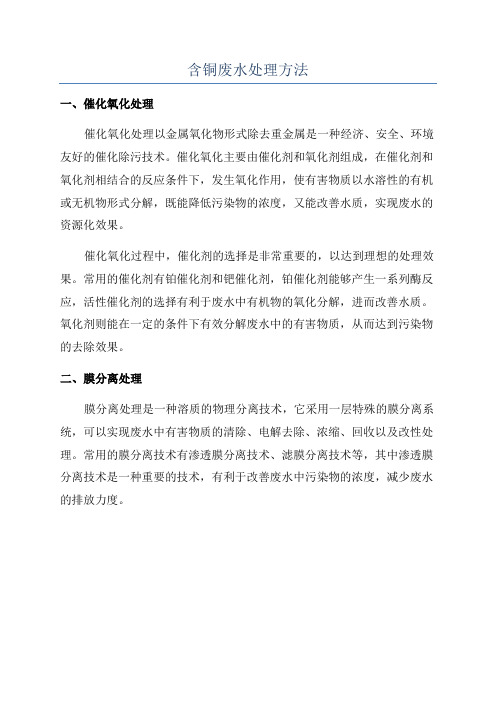
含铜废水处理方法
一、催化氧化处理
催化氧化处理以金属氧化物形式除去重金属是一种经济、安全、环境友好的催化除污技术。
催化氧化主要由催化剂和氧化剂组成,在催化剂和氧化剂相结合的反应条件下,发生氧化作用,使有害物质以水溶性的有机或无机物形式分解,既能降低污染物的浓度,又能改善水质,实现废水的资源化效果。
催化氧化过程中,催化剂的选择是非常重要的,以达到理想的处理效果。
常用的催化剂有铂催化剂和钯催化剂,铂催化剂能够产生一系列酶反应,活性催化剂的选择有利于废水中有机物的氧化分解,进而改善水质。
氧化剂则能在一定的条件下有效分解废水中的有害物质,从而达到污染物的去除效果。
二、膜分离处理
膜分离处理是一种溶质的物理分离技术,它采用一层特殊的膜分离系统,可以实现废水中有害物质的清除、电解去除、浓缩、回收以及改性处理。
常用的膜分离技术有渗透膜分离技术、滤膜分离技术等,其中渗透膜分离技术是一种重要的技术,有利于改善废水中污染物的浓度,减少废水的排放力度。
- 1、下载文档前请自行甄别文档内容的完整性,平台不提供额外的编辑、内容补充、找答案等附加服务。
- 2、"仅部分预览"的文档,不可在线预览部分如存在完整性等问题,可反馈申请退款(可完整预览的文档不适用该条件!)。
- 3、如文档侵犯您的权益,请联系客服反馈,我们会尽快为您处理(人工客服工作时间:9:00-18:30)。
高濃度含銅廢水資材化處理技術之探討吳俊毅1陳偉聖1蕭庭哲2胡紹華3蔡敏行41國立成功大學資源再生及管理研究中心暨永續環境科技研究中心研究助理國立成功大學資源工程學系博士生2國立成功大學資源再生及管理研究中心暨永續環境科技研究中心助理研究員3大漢技術學院環境資源管理學系副教授4國立成功大學資源工程學系研究教授暨台灣資源再生協會理事長摘 要本處理技術係在提供一種高濃度含銅廢水資材化處理方法,主要是將高濃度含銅重金屬廢水加入鹼性浸漬槽中進行攪拌,並適當地添加氯化鐵並控制三價鐵離子與銅離子之莫耳比以及維持溶液pH值在高鹼環境下,進行第一階段礦化反應,待反應完成後,再適當地添加氯化亞鐵並控制二價鐵離子與銅離子之莫耳比並維持溶液初始pH值仍在高鹼環境下,進行第二階段磁化反應,待反應完成後,可利用磁性分選進行固液分離;如此,不僅濾液中銅離子濃度可以符合放流水排放標準,且固體產物中銅離子溶出濃度也符合TCLP毒性特性溶出試驗標準,降低業者的處理負荷及對於環境的危害;此外,由於固體產物具有磁性及銅金屬離子均勻分佈特性可作為磁性材料、塗(顏)料、觸媒與吸收劑等資材化再利用。
關鍵詞:含銅廢水、礦化、磁化、鐵氧磁體、資材化壹、前言傳統上含銅重金屬廢水大都以化學混凝沈降法處理,其程序為在含銅廢水中先加入多元氯化鋁(PAC)或硫酸亞鐵(FeSO4)等混凝藥劑後,此溶液中的pH值大約在2~3左右,再快混添加氫氧化鈉提高溶液中pH值至鹼性範圍為6~9間,使其形成不溶性金屬氫氧化物,如圖1金屬氫氧化物中溶液中平衡常數(c Ksp)與pH安定領域圖所示,化學式如式(1)所示,與廢水達到分離效果。
Cu(OH)2(S) Cu2++2OH--------------(1) K=10-20.4資源與環境學術研討會, 2007, 花蓮圖1 金屬氫氧化物中溶液中平衡常數(c K sp)與pH安定領域圖由於業者為達較快速又明顯的沈降分離效果,故一般皆添加高分子凝集劑(polymer)進行處理。
其中,上澄液雖符合放流水排放標準,分析結果如表1所示,然而後續經板框式壓濾機固液分離之後所產生固體產物(污泥餅),因無法通過TCLP溶出試驗仍視為有害事業廢棄物,分析結果如表2所示,因此業者必須委託清除處理污泥,遂造成龐大的處理負擔。
其次,針對重金屬廢水處理尚可利用濕法冶金法中鐵氧磁體技術(1)-(4),然現行之鐵氧磁體法仍無法妥善處理含銅濃度超過100 mg/L之重金屬廢水。
由於鐵氧磁體法處理含銅廢水程序,在廢水中先加入硫酸亞鐵等二價鐵藥劑後,此時溶液中的pH值大約在2~3,再緩慢加入氫氧化鈉提高溶液中pH值為10.0以上,再進行攪拌、加熱與曝氣等操作步驟,然而在鹼性領域的氧化過程中因溶液中氧化銅(CuO)的迅速形成,成為Fe(OH)2(氫氧化亞鐵)之成長晶核,而促進Fe(OH)2之晶相成長。
另一方面,由於CuO之存在也促成Jahn-Teller效應,遂使Fe(OH)2和H2O分子所形成的八面體配位結構之對稱性受到嚴重扭曲,而降低其晶格穩定性(5)。
另外如表2分析結果所示,檢視經鐵氧磁體法處理後的固體產物中以TCLP試驗之銅離子溶出濃度皆超過法規標準,顯示溶液中的銅離子大部分仍未進入鐵氧磁體的結晶構造內而以氧化銅晶相存在,由此可知氧化銅在酸性環境中不安定,容易被酸所溶解的特性,造成固體產物在TCLP溶出試驗中銅離子大量溶出的主要原因,因此以鐵氧磁體法處理高濃度含銅廢水所產生之固體廢棄物仍視為有害事業廢棄物。
貳、處理技術將高濃度含銅廢水(以銅離子為主的重金屬廢水中,銅離子濃度範圍為100~24,000mg/L)先進行礦化處理後,使其具有特定的礦物組成,再藉由後續的磁化技術,將產物具有磁性以利後續固液分離與固體產物資材化再利用,經由礦化與磁化高濃度含銅廢水資材化處理技術之探討的二階段反應後,其濾液可循環至原處理流程再利用,減少氫氧化鈉添加量或經調整後予以放流;固體產物符合TCLP溶出試驗,有效降低有害重金屬污泥對環境的衝擊,且資材化再生產品因具有磁性、銅金屬離子均勻分佈特性與吸收特性,可應用於磁性材料、塗(顏)料、觸媒與吸收劑等資材化再利用途徑(6)-(7)。
本技術主要目的在提供將高濃度含銅廢水先進行礦化處理後,達到無害化之初始目標,再藉由磁化技術,將產物具有磁性以利後續固液分離與產物資材化再利用,經由礦化與磁化的二階段反應後,其過濾液與固體產物之分析結果如表1與表2所示,由表1中發現含銅廢水經由本技術處理後,其過濾液中重金屬濃度皆符合放流水排放標準,濾液可回原處理流程再利用以減少氫氧化鈉添加量或經調整後予以放流。
此外,藥劑為使用回收廢酸製成的氯化鐵與氯化亞鐵再生產品,進而達到再生產品應用於廢水處理的循環型資源化目標,因此本技術實為兼顧污染防治之高濃度含銅廢水處理技術及資材化再利用。
經由以上說明可知,本技術具有以下優點:1.本技術所提供的資材化處理方法,突破傳統利用化學混凝沈降法處理廢水所產生的含銅污泥為有害事業廢棄物之困境,且將廢水中銅離子處理濃度提昇24,000mg/L,遠勝於傳統化學混凝沈降法與鐵氧磁體法操作處理量的負荷達數倍至數十倍以上。
因此,不但為資材化產物,將原本有害事業廢棄物委託處理費用大幅降低至一般事業廢棄物委託處理費用,由目前一噸至少12,000元降至2,000元左右,大幅節省業者的處理負荷,且在技術處理量上更大幅提昇,可因應生產流程(製程中)突來飇高的重金屬廢水濃度,極具實際應用價值。
2.本技術所提供的資材化處理方法,突破傳統上利用鐵氧磁體無法處理含銅廢水而導致固體物中銅離子溶出濃度無法符合TCLP標準之缺點。
3.本技術可解決目前國內氯化鐵與氯化亞鐵等再生產品生產過剩而苦無出路之困境。
不僅降低因高濃度含銅廢水處理所產生重金屬污泥的環境危害,且達到再生產品應用於廢水處理的循環型資源化目標。
4.本技術由於資材化再生產品因具有磁性與吸收特性,可應用於磁性材料、塗(顏)料、觸媒與吸收劑等資材化再利用途徑。
參、處理流程說明本技術將高濃度含銅廢水利用濕式冶金處理方式,以低溫礦化處理及磁化技術以產生資材化之固體產物,首先將高濃度含銅重金屬廢水導入鹼性浸漬槽中(如:氫氧化鈉溶液)同時進行攪拌,並適當添加氫氧化鈉維持溶液pH值大於12.5以上,再添加三價鐵溶液(藥劑型式如:氯化鐵FeCl3、硫酸鐵Fe2(SO4)3、硝酸鐵Fe(NO3)3、碳酸鐵Fe2(CO3)3等)控制溶液中三價鐵離子與銅離子之莫耳比大於2以上,以及適當添資源與環境學術研討會, 2007, 花蓮加氫氧化鈉維持溶液pH值仍大於12.5以上,保持溶液中的金屬種類皆為離子狀態(Cu(OH)3-、Cu(OH)42-,參閱圖2說明所示),其次將此溶液控制在反應溫度為60~90℃與持續攪拌下進行第一階段礦化反應,待反應完成後,再添加二價鐵溶液(如:氯化亞鐵FeCl2、硫酸亞鐵FeSO4、硝酸亞鐵Fe(NO3)2、碳酸亞鐵FeCO3等)控制此礦化溶液中二價鐵離子與銅離子之莫耳比大於2以上並適當調整溶液pH值仍大於10.0以上,再將此礦化溶液在反應溫度為60~90 ℃、並持續攪拌與曝氣(曝氣量建議大於4 Liter air/min/Liter liquid)下進行第二階段磁化反應,待反應完成後,由於產物具有磁性可利用磁性分選或壓濾進行固液分離;因此,高濃度含銅廢水經由本技術處理,不僅濾液中銅離子濃度可以符合放流水排放標準(3 mg/L以下),同時其固體物中銅離子溶出濃度也符合毒性溶出試驗標準(TCLP標準為15 mg/L以下)為一般事業廢棄物,大幅降低業者的處理負荷及對於環境的危害與衝擊。
圖2 溶液中銅離子濃度與pH關係圖高濃度含銅廢水資材化處理技術之探討圖3 本處理流程圖有關本處理流程參閱圖3之處理流程圖及配合圖4之處理設備圖說明所示,步驟如下:(1)離子化含銅廢液:首先,其係將高濃度含銅廢水置於廢水暫存槽A中,利用幫浦W1抽送至鹼性(氫氧化鈉)浸漬槽B進行快速攪拌,以pH電極D1量測並適當添加鹼劑(如:氫氧化鈉,以維持pH值大於12.5以上),且藉電腦自動記錄器G作監測以維持溶液pH值大於12.5以上,保持溶液中的銅為離子狀態;(2)礦化反應:將浸漬後高pH值的高濃度含銅廢液藉由幫浦W2抽送至反應槽C中,添加氯化鐵,控制廢液中三價鐵離子與銅離子之莫耳比大於2以上並進行攪拌,以pH 電極D2量測並適當添加鹼液(如:氫氧化鈉),以維持廢液pH值大於12.5以上,利用加熱器F使溫度控制在60℃~90℃的條件下進行第一階段礦化反應,並持續攪拌,以ORP電極E量測並由電腦自動記錄器G作監測至ORP值變動幅度達到平衡(跳動不大呈現穩定時),此礦化反應階段之反應時間約0.5~1.5小時完成;(3)磁化反應:完成上一步驟後於反應槽C中添加氯化亞鐵,控制礦化溶液中二價鐵離子與銅離子之莫耳比大於2以上並持續攪拌,以pH電極D2量測並適當添加氫氧化鈉,以維持礦化溶液pH值大於10.0以上,利用加熱器F使槽內溫度維持在60℃~資源與環境學術研討會, 2007, 花蓮90℃以及利用曝氣機H進行曝氣,同時維持曝氣量大於(4 Liter air/min/Liter liquid)的操作條件下進行第二階段磁化反應,並持續攪拌,以ORP電極E量測並由電腦自動記錄器G作監測至ORP值變動幅度達到平衡(跳動不大呈現穩定時),此磁化反應階段之反應時間約0.5~1.5小時完成;(4)固液分離:磁化反應步驟完成後藉由幫浦W3抽送至濃縮槽J,利用自然重力沈降,進行初步地固、液分離,再抽送至第一固液分離裝置K1,經固、液分離後,第一固液分離槽所產生之濾液,可直接回原廢水處理流程作為液鹼添加劑部份補充使用,或經由濾液調整槽L進行pH調整至符合排放標準後予以放流,所得之固體物輸送至水洗槽M,藉由清洗水攪拌水洗以去除固體物中多餘的鹽類與雜質,之後再輸送至第二固液分離裝置K2,第二固液分離槽所得之濾液可收集至濾液調整槽L,所得之固體物則利用烘箱N進行105℃烘乾,以去除水分,後續則利用研磨設備P進行研磨成粉體等資材化產物R,其產物經由JCPDS資料庫進行比對所得的XRD分析結果如圖5所示,顯示為銅系鐵氧磁體結晶構造。
圖4 處理設備圖主要元件符號說明A:高濃度含銅廢水暫存槽B:鹼性浸漬槽C:反應槽D1、D2:第一、第二pH電極E:ORP電極F:加熱器G:電腦自動記錄器H:曝氣機J:濃縮槽K1、K2:第一、第二固液分離裝置L:濾液調整槽M:水洗槽N:烘箱P:研磨設備W1、W2、W3:第一、第二、第三幫浦高濃度含銅廢水資材化處理技術之探討圖5 處理後固體產物之XRD圖譜肆、處理結果4.1 模擬重金屬廢水處理結果配製不同濃度範圍(600~24,000 mg/L)的高濃度含銅重金屬模擬廢水,比較傳統化學混凝法、鐵氧磁體法與利用本技術之處理結果,不同批次之高濃度含銅重金屬模擬廢水組成與處理後濾液與固體產物分析結果如表1與表2所示;表1 不同批次之模擬廢水組成與處理後之濾液分析結果單位:mg/L No. 批次銅鉻鎳鋅pH 銅濃度600mg/L模擬廢水600 100 200 100 3.06化學混凝法處理後之濾液0.19 0.17 0.11 0.08 7.84 1鐵氧磁體處理後之濾液0.26 0.11 0.13 0.16 10.52本技術處理後之濾液0.16 0.12 0.10 0.13 10.77銅濃度2,000mg/L模擬廢水2,000 100 200 100 3.07化學混凝法處理後之濾液0.13 0.21 0.21 0.15 8.12 2鐵氧磁體處理後之濾液0.29 0.08 0.17 0.10 10.74本技術處理後之濾液0.32 0.15 0.19 0.07 9.94銅濃度6,000mg/L模擬廢水6,000 100 200 100 2.95化學混凝法處理後之濾液0.21 0.16 0.15 0.14 7.88 3鐵氧磁體處理後之濾液0.15 0.23 0.13 0.05 10.48本技術處理後之濾液0.40 0.13 0.22 0.18 10.61資源與環境學術研討會, 2007, 花蓮No.批 次銅 鉻 鎳 鋅 pH 銅濃度 24,000mg/L 模擬廢水24,000100 200 100 3.02 化學混凝法處理後之濾液0.27 0.14 0.04 0.24 7.97 鐵氧磁體處理後之濾液 0.21 0.09 0.18 0.20 10.79 4 本技術處理後之濾液0.31 0.17 0.17 0.16 10.42 放流水標準3.02.01.05.06.0~9.0表2 不同批次之模擬廢水經處理後固體產物之TCLP 分析結果 單位:mg/kgNo. 處理後之固體產物銅 鉻 鎳 鋅 化學混凝法 124.5 25.3 35.7 24.9 鐵氧磁體法 78.6 1.5 1.1 0.6 1模擬廢水 (銅濃度 600mg/L)本處理技術 2.5 1.3 0.7 0.8 化學混凝法 178.8 135.8 67.9 15.6 鐵氧磁體法 217.2 2.4 0.6 0.7 2模擬廢水 (銅濃度 2,000mg/L)本處理技術 4.8 1.9 0.8 1.1 化學混凝法 875.3 389.4 42.77 11.5 鐵氧磁體法 647.2 1.2 0.37 0.3 3模擬廢水 (銅濃度 6,000mg/L)本處理技術 6.1 1.3 0.81 0.6 化學混凝法 978.1 798.3 58.99 17.6 鐵氧磁體法 1,145.51.9 1.01 0.7 4模擬廢水 (銅濃度 24,000mg/L)本處理技術6.7 1.2 0.93 1.2 TCLP 標準15.05.0--4.2 實際電鍍廢水處理結果取南部某家電鍍工廠所產生之含銅重金屬廢水,比較廠內現有處理方式(傳統化學混凝法)與利用本技術處理結果,不同批次之原始廢水組成與處理後濾液之分析結果如表3所示,不同批次之原始廢水經處理後固體產物之TCLP 分析結果如表4所示。