Flexsim仿真案例
flexsim建模案例
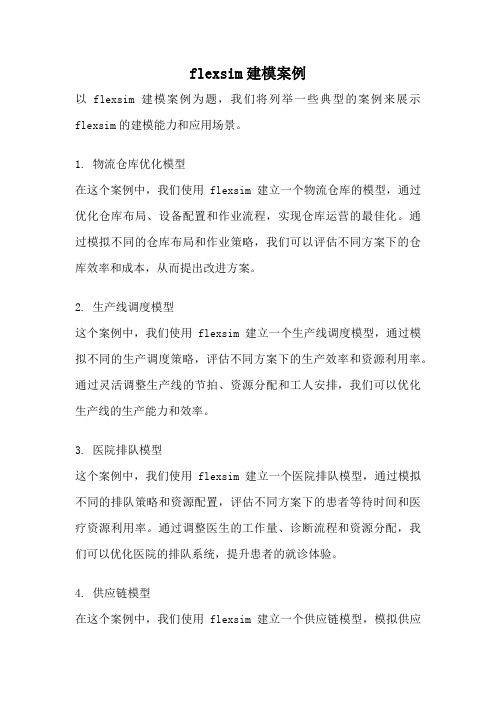
flexsim建模案例以flexsim建模案例为题,我们将列举一些典型的案例来展示flexsim的建模能力和应用场景。
1. 物流仓库优化模型在这个案例中,我们使用flexsim建立一个物流仓库的模型,通过优化仓库布局、设备配置和作业流程,实现仓库运营的最佳化。
通过模拟不同的仓库布局和作业策略,我们可以评估不同方案下的仓库效率和成本,从而提出改进方案。
2. 生产线调度模型这个案例中,我们使用flexsim建立一个生产线调度模型,通过模拟不同的生产调度策略,评估不同方案下的生产效率和资源利用率。
通过灵活调整生产线的节拍、资源分配和工人安排,我们可以优化生产线的生产能力和效率。
3. 医院排队模型这个案例中,我们使用flexsim建立一个医院排队模型,通过模拟不同的排队策略和资源配置,评估不同方案下的患者等待时间和医疗资源利用率。
通过调整医生的工作量、诊断流程和资源分配,我们可以优化医院的排队系统,提升患者的就诊体验。
4. 供应链模型在这个案例中,我们使用flexsim建立一个供应链模型,模拟供应链中不同环节的物流流程和库存管理。
通过优化供应链中的运输路线、库存水平和订单处理流程,我们可以降低供应链的成本,提高供应链的响应速度和灵活性。
5. 机场运营模型这个案例中,我们使用flexsim建立一个机场运营模型,模拟机场的航班调度、旅客流动和行李运输。
通过优化航班的调度安排、旅客的流动路径和行李的运输流程,我们可以提高机场的运营效率和旅客的出行体验。
6. 货物分拣系统模型在这个案例中,我们使用flexsim建立一个货物分拣系统模型,模拟货物的分拣流程和设备利用率。
通过优化货物的分拣路径和设备的配置,我们可以提高分拣系统的效率和准确率,降低分拣成本。
7. 铁路调度模型这个案例中,我们使用flexsim建立一个铁路调度模型,模拟列车的运行和交路调度。
通过优化列车的运行路径、发车间隔和交路安排,我们可以提高铁路的运行效率和安全性,减少列车的延误和碰撞风险。
Flexsim建模案例-(4)复习进程
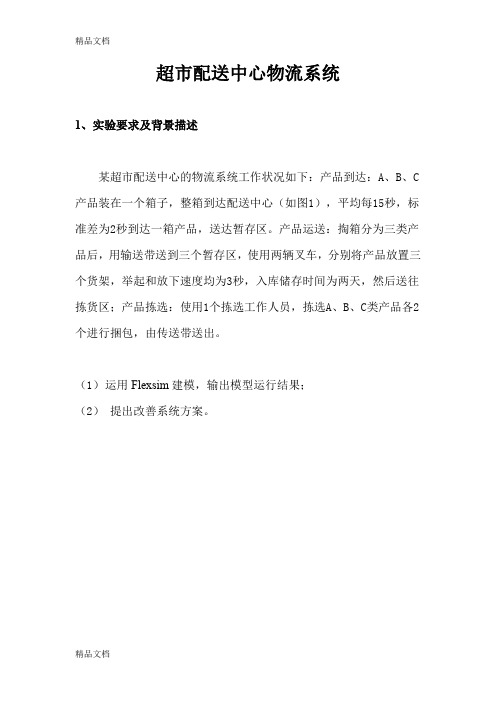
超市配送中心物流系统1、实验要求及背景描述某超市配送中心的物流系统工作状况如下:产品到达:A、B、C 产品装在一个箱子,整箱到达配送中心(如图1),平均每15秒,标准差为2秒到达一箱产品,送达暂存区。
产品运送:掏箱分为三类产品后,用输送带送到三个暂存区,使用两辆叉车,分别将产品放置三个货架,举起和放下速度均为3秒,入库储存时间为两天,然后送往拣货区;产品拣选:使用1个拣选工作人员,拣选A、B、C类产品各2个进行捆包,由传送带送出。
(1)运用Flexsim建模,输出模型运行结果;(2)提出改善系统方案。
2、实验布局逐步添加离散实体: 5个发生器(3个用于生产产品;2个用于生产托盘);4个暂存区;8条传送带(4条进货,4条出货);2条分拣传送带;2个合成器;1个分解器;1个吸收器;1个操作员;3个货架;1个分配器;5辆叉车,如图1、2。
图1(主视图)图2(左视图)3、设计思路及建模步骤产品到达:A、B、C产品装在一个箱子,整箱到达配送中心(如图3)。
图3 图4掏箱分为三类产品后,用输送带送到三个暂存区(如图4)。
使用两辆叉车,分别将产品放置三个货架(如图5)。
图5入库储存时间为两天,然后送往拣货区(如图6)图6使用1个拣选工作人员,拣选A、B、C类产品各2个进行捆包,由传送带送出。
(如图7)图74、散实体连接。
按照不同的逻辑关系,采用A 连接和S 连接, 逐一对模型内的实体进行连接,应注意各个端口的连接顺序, ( 输入端口,输出端口,中间端口)。
5、参数设置图8图9图10此处已经完成模型设计的第一环节:A 、B 、C3类产品装在一个箱子,整箱到达配送中心,平均每15秒,标准差为2秒到达一箱产品,送达暂存区。
图11图12图13图14此处已经完成模型设计的第二个环节:掏箱分为三类产品后,用输送带送到三个暂存区。
图15图16此处已经完成模型设计的第三和第四个环节:使用两辆叉车,分别将产品放置三个货架;入库储存时间为两天,然后送往拣货区。
立体仓库flexsim仿真模拟

立体仓库仿真模拟业务流程描述某仓储企业欲新建一个立体仓库,仓库长80米,宽50米,高20米,占地面积为4000平方米。
企业与客户预签订了仓储外包合同,仓库建成后,客户将按合同定时定量进行送货,按市场需求不定期取货,并支付货物装卸费和仓储管理费。
立体仓库的基本业务流程如下:客户需要仓库存储4种不同类型的货物,类型分别为1,2,3,4。
其中1,2种货物为小型包装货物;3,4种为大型包装货物。
每天客户按照约定在不同的时间将不同类型的整车货物运抵仓库卸货口,货物均为单个包装运输(非托盘化运输),仓库负责卸货(人工或叉车),并将货物堆放在某个临时存储区等待入库。
入库前所有货物需要进行验货并贴条形码标签,由验货标签设备一次性完成。
验货标签设备分为两种:小型设备和大型设备,前者用于小型货物的验货和贴条形码标签;后者用于大型货物的验货和贴条形码标签。
由于1,2种货物为小型货物,验货后还需要码放在托盘上才能入库,这种处理由托盘码放设备完成。
完成码放后,货物与托盘一并入库(巷道堆垛机或叉车),每托盘货物占用一个货位。
3,4种货物可直接入库(巷道堆垛机或叉车),每件货物占用一个货位。
每个货架只能存储一种类型的货物。
货物的出库由市场需求决定,每个货物的库存时间平均为一天,且符合正态分布。
出库的货物堆放在某个临时存储区,仓库负责进行装货(人工或叉车),其中1,2种货物进行托盘化搬运和装货。
客户送货与发货时刻:客户的送货车辆每次只能在仓库停留15分钟,要求仓库对于任意货物的卸货时间不超过15分钟。
(代表车厢的暂存区实体最大停留时间stats_staytimemax小于等于900秒)送货时刻与送货数量如下表:客户的接货车辆每天按照一定时间到达仓库发货区(详见发货时间表),客户要求的装货时间也不超过15分钟。
(通过控制发货暂存区的输出流来实现)仿真时间假定仓库每天运转10小时,上午8:00到下午18:00,每天的运营时间为36000秒,一周运营时间为252000秒。
flexsim建模案例
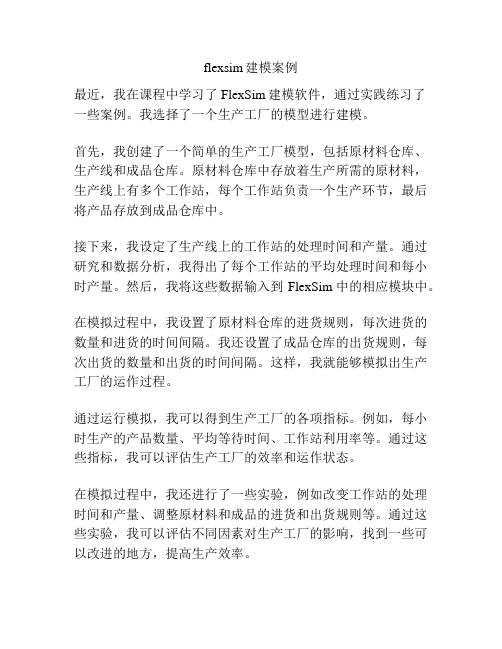
flexsim建模案例最近,我在课程中学习了FlexSim建模软件,通过实践练习了一些案例。
我选择了一个生产工厂的模型进行建模。
首先,我创建了一个简单的生产工厂模型,包括原材料仓库、生产线和成品仓库。
原材料仓库中存放着生产所需的原材料,生产线上有多个工作站,每个工作站负责一个生产环节,最后将产品存放到成品仓库中。
接下来,我设定了生产线上的工作站的处理时间和产量。
通过研究和数据分析,我得出了每个工作站的平均处理时间和每小时产量。
然后,我将这些数据输入到FlexSim中的相应模块中。
在模拟过程中,我设置了原材料仓库的进货规则,每次进货的数量和进货的时间间隔。
我还设置了成品仓库的出货规则,每次出货的数量和出货的时间间隔。
这样,我就能够模拟出生产工厂的运作过程。
通过运行模拟,我可以得到生产工厂的各项指标。
例如,每小时生产的产品数量、平均等待时间、工作站利用率等。
通过这些指标,我可以评估生产工厂的效率和运作状态。
在模拟过程中,我还进行了一些实验,例如改变工作站的处理时间和产量、调整原材料和成品的进货和出货规则等。
通过这些实验,我可以评估不同因素对生产工厂的影响,找到一些可以改进的地方,提高生产效率。
通过这个建模案例,我深入了解了FlexSim建模软件的使用方法,并学会了如何应用它来解决实际问题。
通过建模和模拟,我可以更好地理解生产工厂的运作过程,以及如何通过优化和改进来提高生产效率。
总的来说,通过对FlexSim建模软件的学习和实践,我不仅提高了自己的技能,还拓宽了自己的视野,了解了生产工厂的运作过程和优化方法。
我相信这些经验将对我未来的工作和学习都有很大的帮助。
flexsim建模案例

flexsim建模案例FlexSim建模案例。
在物流领域,模拟仿真技术被广泛应用于优化生产流程、提高效率和降低成本。
FlexSim作为一款领先的仿真软件,为用户提供了强大的建模和分析工具,能够帮助用户快速、准确地模拟和分析各种复杂的生产和物流系统。
本文将通过一个实际案例,介绍FlexSim在物流建模中的应用。
案例背景。
某电子产品制造公司的仓储物流系统存在一些问题,包括库存过多、拣货效率低下、物料周转周期长等。
为了解决这些问题,公司决定引入FlexSim仿真软件,对仓储物流系统进行建模分析,找出问题所在并提出优化方案。
建模过程。
首先,我们需要收集仓储物流系统的相关数据,包括物料流动情况、人员操作流程、设备利用率等。
然后,利用FlexSim软件搭建仓储物流系统的仿真模型,包括仓库布局、货架设置、拣货站点、运输设备等。
在建模过程中,需要考虑到系统的实际运行情况,尽可能还原真实的物流环境。
模拟分析。
完成建模后,我们可以对仓储物流系统进行模拟分析。
通过设定不同的参数和场景,可以模拟出不同的运作情况,并对系统的运行效率、吞吐量、人员利用率等指标进行评估。
通过模拟分析,我们可以直观地看到系统的瓶颈和问题所在,为后续的优化提供依据。
优化方案。
根据模拟分析的结果,我们可以提出针对性的优化方案。
比如,对仓库布局进行调整,优化拣货路径,提高货架利用率,优化人员作业流程等。
在FlexSim软件中,我们可以通过调整模型参数,模拟不同的优化方案,并对比各方案的效果,找出最优的方案。
实施效果。
经过优化方案的实施,仓储物流系统的运作效率得到了显著提升。
库存周转周期缩短,拣货效率提高,人员利用率得到了优化。
通过FlexSim软件的建模分析,我们成功地解决了仓储物流系统存在的问题,为公司节约了成本,提高了生产效率。
结论。
FlexSim作为一款强大的仿真软件,在物流建模中有着广泛的应用前景。
通过本案例的介绍,我们可以看到FlexSim在物流建模中的重要作用,它不仅可以帮助我们发现问题,提出解决方案,还可以帮助我们评估方案的效果,为实际生产运营提供决策支持。
flexsim仿真案例
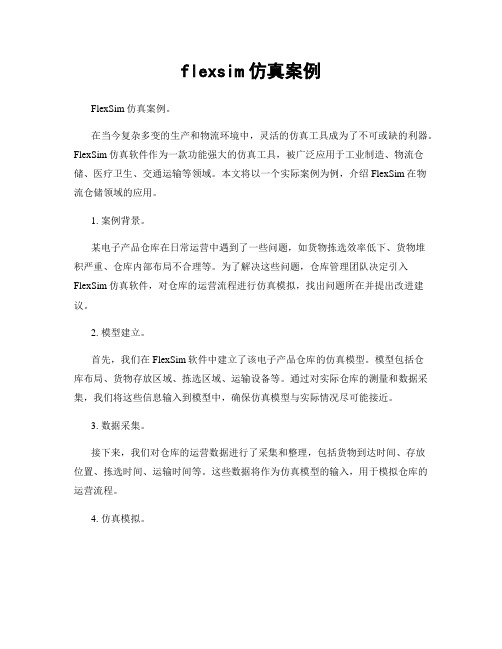
flexsim仿真案例FlexSim仿真案例。
在当今复杂多变的生产和物流环境中,灵活的仿真工具成为了不可或缺的利器。
FlexSim仿真软件作为一款功能强大的仿真工具,被广泛应用于工业制造、物流仓储、医疗卫生、交通运输等领域。
本文将以一个实际案例为例,介绍FlexSim在物流仓储领域的应用。
1. 案例背景。
某电子产品仓库在日常运营中遇到了一些问题,如货物拣选效率低下、货物堆积严重、仓库内部布局不合理等。
为了解决这些问题,仓库管理团队决定引入FlexSim仿真软件,对仓库的运营流程进行仿真模拟,找出问题所在并提出改进建议。
2. 模型建立。
首先,我们在FlexSim软件中建立了该电子产品仓库的仿真模型。
模型包括仓库布局、货物存放区域、拣选区域、运输设备等。
通过对实际仓库的测量和数据采集,我们将这些信息输入到模型中,确保仿真模型与实际情况尽可能接近。
3. 数据采集。
接下来,我们对仓库的运营数据进行了采集和整理,包括货物到达时间、存放位置、拣选时间、运输时间等。
这些数据将作为仿真模型的输入,用于模拟仓库的运营流程。
4. 仿真模拟。
在数据准备完成后,我们开始对仓库的运营流程进行仿真模拟。
通过设定不同的参数和场景,我们可以模拟出不同的运营情况,如高峰时段的货物拣选、不同拣选策略的比较、仓库布局的优化等。
5. 问题分析。
通过对仿真模拟结果的分析,我们发现了一些问题,如拣选区域的瓶颈、货物存放位置的不合理、拣选人员的工作效率等。
这些问题导致了仓库运营效率的低下和成本的增加。
6. 改进建议。
基于仿真模拟结果的分析,我们提出了一些改进建议,如优化拣选区域的布局、调整货物存放策略、改进拣选流程、提高人员培训等。
这些改进建议将有助于提高仓库的运营效率,降低成本,提升客户满意度。
7. 结论。
通过FlexSim仿真软件的应用,我们成功地发现了仓库运营中存在的问题,并提出了有效的改进建议。
这些改进建议得到了仓库管理团队的认可,并已经开始逐步实施。
flexsim案例背景及步骤

flexsim案例背景及步骤FlexSim是一种基于离散事件模拟技术的仿真软件,可以用于各种领域的仿真建模和分析,如制造、物流、医疗、公共服务等。
下面针对一个典型的FlexSim案例,介绍该案例的背景及步骤。
案例背景:某电子厂需要优化其生产线的生产效率,以提高产品的生产率和质量。
该生产线由多个工作站组成,每个工作站有不同的生产能力和工作速度。
产品从原材料到成品的生产过程包括多个工序,并且在生产过程中有不同的等待时间和工作停顿时间。
步骤:1. 定义模型元素:对生产线的整体结构进行建模,包括所有工作站、生产过程、等待区和其他需要仿真的要素。
确保所有的元素都正确定义,并与实际生产线的结构相匹配。
2. 定义产出物流:根据生产线的产出物品,建立合适的物流模型,并确定每个工序和每个工作站的成品输出点。
同时,根据生产线的标准流程和实际生产情况进行优化调整。
3. 定义工作流程:为每个工作站和每个工序定义相应的工作流程,包括工作顺序、加工时间、等待时间和可能的故障时间等。
根据实际生产线的统计数据确定工作周期。
4. 定义数据收集:确定需要收集的数据类型和参数,如生产速率、工作效率、工作停顿时间等。
为每个工作站和每个工序设置数据收集点,并将所有数据集中到一个数据管理模型中。
5. 进行仿真分析:运行仿真模型,获取生产线的性能指标和数据。
对数据进行统计分析,如仿真结果的可靠性和偏差程度等。
根据仿真结果,分析生产线的优化方案并进行比较和评估。
6. 模型优化:基于仿真分析结果,对模型进行优化。
优化方案包括调整工作流程、调整工作站设备和工作时间,并根据实际情况进行调整和改进。
7. 验证和验证:验证和验证仿真模型的准确性和可信度,并确定模型的适用范围和有效性。
8. 分析和性能评估:分析并评估生产线优化实施后的性能,确定是否达到预期的改进效果。
9. 改进和优化:持续监测生产线的性能,并根据实际情况进行改进和优化,以确保持续不断的生产线优化。
Flexsim建模案例 (4)
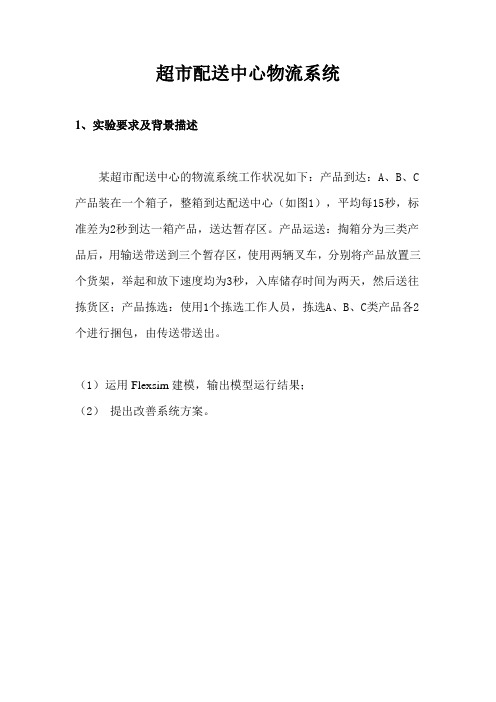
超市配送中心物流系统1、实验要求及背景描述某超市配送中心的物流系统工作状况如下:产品到达:A、B、C 产品装在一个箱子,整箱到达配送中心(如图1),平均每15秒,标准差为2秒到达一箱产品,送达暂存区。
产品运送:掏箱分为三类产品后,用输送带送到三个暂存区,使用两辆叉车,分别将产品放置三个货架,举起和放下速度均为3秒,入库储存时间为两天,然后送往拣货区;产品拣选:使用1个拣选工作人员,拣选A、B、C类产品各2个进行捆包,由传送带送出。
(1)运用Flexsim建模,输出模型运行结果;(2)提出改善系统方案。
2、实验布局逐步添加离散实体: 5个发生器(3个用于生产产品;2个用于生产托盘);4个暂存区;8条传送带(4条进货,4条出货);2条分拣传送带;2个合成器;1个分解器;1个吸收器;1个操作员;3个货架;1个分配器;5辆叉车,如图1、2。
图1(主视图)图2(左视图)3、设计思路及建模步骤产品到达:A、B、C产品装在一个箱子,整箱到达配送中心(如图3)。
图3 图4掏箱分为三类产品后,用输送带送到三个暂存区(如图4)。
使用两辆叉车,分别将产品放置三个货架(如图5)。
图5入库储存时间为两天,然后送往拣货区(如图6)图6使用1个拣选工作人员,拣选A、B、C类产品各2个进行捆包,由传送带送出。
(如图7)图74、散实体连接。
按照不同的逻辑关系,采用A连接和S 连接,逐一对模型内的实体进行连接,应注意各个端口的连接顺序,(输入端口,输出端口,中间端口)。
5、参数设置图8 图9发生器参数设置11、临时实体种类设置为Box2、发生器1、2、3的物品类型分别设置为1、2、3。
3、到达时间间隔设置为“统计分布:normal(15,2)。
4、其余为默认值如图8发生器参数设置21、发生器4和5的临时实体种类设置为Pallet。
2、到达时间间隔设置为“统计分布:normal(15,2)。
3、其余为默认值如图9合成器参数设置1、在合成器选项卡中合成模式设置为Pack。
- 1、下载文档前请自行甄别文档内容的完整性,平台不提供额外的编辑、内容补充、找答案等附加服务。
- 2、"仅部分预览"的文档,不可在线预览部分如存在完整性等问题,可反馈申请退款(可完整预览的文档不适用该条件!)。
- 3、如文档侵犯您的权益,请联系客服反馈,我们会尽快为您处理(人工客服工作时间:9:00-18:30)。
备注
产线生产——设备需求
来料 治具 OK品 品 治具 品 来料 治具 来料
拆装线
CNC1
CCD
治具
来料
CNC3
治具 OK品
CNC2
说明:(1)拆装线前端为将加工OK之产品从治具拆除,治具沿流水线流动并装加来料继续生产. (2)拆装线11人作业,即要保证每条流水线至少有11个治具.
样本28个,均值4.32 5.56 5.34 5.27 5.57 5.97 5.36 7.54 6.14 6.77 4.47 5.29
gamma( 4.331564, 0.622312, 2.961961) 7.44 交换 7.40 7.82 7.76 7.84 7.36 7.44 loglaplace( loglaplace( 0.000000, 7.440000, 16.007083) 对位 MARK 4.62 5.01 4.91 5.37 5.55 4.71 5.39 4.77 4.19 4.25 4.84 4.17 5.16 4.71 6.56 7.33 9.39 7.91 8.22 6.70 6.49
2批/天有通道 2批/天无通道 3批/天 4批/天 5批/天 6批/天 随到随走 7.1 6.1 4.7 4.1 3.1 2.8 0.2 平均WIP
项目绩效
项目时间﹕2007/12/15-2008/01/07 人力投入﹕2 项目绩效:有形绩效为 650W(NTD)/MON。同时WIP显著降低、 Leadtime 和工令结案时间明显缩短、资金周转率得到很大提升。 仿真绩效:仿真人员贡献的绩效占整个项目的30%,其中有形绩效为 195W(NTD)/MON,同时为SMT、装配一体化动态排程项目人员提供了技 术支持和决策依据。
样本27个,均值6.17 7.81 6.75 7.50 7.76 7.36 6.69
样本20个,均值7.47 5.16 3.64 4.24 3.94 4.51 4.75
johnsonbounded( johnsonbounded( 2.888928, 6.181216, -0.248686, 1.463819) 28 画检 24 23 14 30 28 25 14 21 24 21 16 28 33 26 20 24 23 21 30 33 34 23 16 23 31 25 20 26 26 33 16 24 22 21 17 21 27 24 24
样本20个,均值7.47 28 27 20 21 22 27 22 14 20 23 24 21 25 28 15 27 19 20 19 20
gamma( 0.000000, 1.050779, 22.221603)
样本20个,均值7.47
仿真时间5小时
经多次反复实验,改善前两站UPH之和与改善后 两站UPH之和差异不大,一般在-3~+3之间变 化,因此可知改善方案是可行的。 另外,改善后LOAD/UNLOAD作业员的时间利用 率59.9%左右(因目前数据是在改善前工站采集 的,时间较宽松,所以改善后的利用率应不超过 59.9%),画检作业员时间利用率65.5%.
采集数据的概率拟合分析
UNLOAD
4.06 4.28
3.9 6.1
3.87 5.3
5.23 2.91
5.96 3.44
4.33 3.39
5.34 3.29
4.96 2.81
6.14 3.27
4.89 3.24
4.99 3.25
5.09 3.65
6.06 3.05
5.18 3.19
weibull( 2.806805, 1.600534, 1.205378) 服从分布weibull( 5.67 LOAD 6.36 6.81 5.47 7.45 5.17 5.57 5.08 5.94 5.05 8.06 5.80 6.80 7.92 6.57 7.00 7.89 7.18
仿真说明
主要评价指标: � 各线体WIP变化 � 总共产品数 � 在线暂存区利用率 � 最优批次(ロット) � 送入烤箱千层架数量变化 � 烤箱利用率 � 静置区利用率 � 堵塞情况
生产物流——产线生产
批次 静置区原利用率 原对应时数 静置区新利用率 新利对应时数 2 55.12% 12 55.12% 12 3 57.97% 12 69.85% 14.5 4 58.35% 12 64.47% 13 5 57.42% 12 72.24% 15 6 57.78% 12 74.01% 15.5 随到随走 60.25% 12 82.17% 17
生产物流——产线生产
生产物流——产线生产
1.当前问题:该车间一共有 12条生产线H1~H12,其中 H1﹑H2线外借,部门可用的产线只有 10条,分别进行 不同种类的产品的加工。另外由于产品加工特点,车 间还有烤箱(焼き入れ),静置区等区域,分别对产品进 行不同的处理 2.项目目的:在于通过对产品加工的整个流程进行分 析,找出瓶颈处和可以改进的工序,分析造成瓶颈的 原因,找到相应的解决措施。 通过仿真优化达到以下目的:降低产在线的 WIP,提高 烤箱的利用率,优化产品运输路线
Flexsim仿真案例之
——生产/物流篇
北京创时能科技发展有限公司
目录
设施规划(ライン新設 工程設計) 生产物流 产线生产(ライン運用) 其他仿真(その他)
(ライン新設、工程設計) Laຫໍສະໝຸດ out设施规划——车间布置
设施规划——车间布置
1.当前问题: SMT 生产流程“锡膏印刷-锡膏AOI-贴片-回焊-焊点AOI”,实际 中﹐每印刷一片板子的单位时间是 15~20S,印刷机擦拭一次的时间是 30~55S, 当印刷机在擦拭时﹐对生产造成的影响是显著 2.项目目的:分析印刷机在执行擦拭动作时﹐对后面的AOI及整条产线 所造成的影响﹐以及探讨让整条产线可以高效生产的最佳配置。 3.有形绩效: 以P455为例﹐6月份产量60K﹐印刷机每次擦拭等待时间为 30s﹐通过参 数优化﹐使AOI的每次等待时间减少 10S﹐则6月份AOI工作时间增加 60000/20*10/3600=8.3H ,如果每片板子的利润是 30元﹐则每月增加收 益:8.3*180*30=44820元 无形绩效: 得出不同条件下﹐"印刷机-AOI"两机间的最佳配置参数﹐用具体数字量化 出来。反过来指导设置最佳的机器参数以及产线 Layout.
产线生产——物流自动线
产线生产——物流自动线
其他仿真
�
建厂规划
其他仿真
�
线边仓建立
其他仿真
�
废气回收再利用
其他仿真
�
人力评估
其他仿真
�
Cell线生产
其他仿真
�
仓库模型
结束语
创时能科技 � 创时能Flexsim仿真咨询团队 �
�
产线生产——人力配置
产线生产——人力配置
仿真说明: 1.工站作业时间单元分为:unload,load,传片, 对位,画检。其中, unload,load两时间单元 为合并时间单元(便于现场测量工时),包含作 业员取片、移动及放片时间。 仿真条件设定﹕ 1﹑投料及时稳定,作业员作业时间稳定﹔ 2﹑生产线连续正常运作﹐无异常﹔
(3)治具运送方式:物流员以小车运送,每装满8PCS(或16PCS)即从拆装线装运往CNC1机台,同时收集CNC1加工 完成 之产品运往CNC2,依此类推.直到产品加工完成
4.客户需求:假设来料及良品输出不制约整个生产过程,评估现有状况下生产系统(虚线部分)中 1)在物料员每次运送8PCS或16PCS两种情况下各所需EROWA治具数量; 2)物流线路长度
产线生产——设备需求
产线生产——设备需求
治具评估需求数据
1.机加日工作时间以20小时计 机台分布 1F 2F 2.工时 工序名称 单片产品 工时(S/PC) 模穴数 嫁动率 工序1 EROWA子 治具拆装 3S 工序2 CNC1 50S 1出1 95% 工序3 CCD 20.25S 1出2 工序4 CNC2 120S 1出1 工序5 CNC3 200S 1出1 每套EROWA治具维修时 间20MIN/周 备注 EROWA子 治具拆装线 2 3 产能 CNC1 30 49 CCD 12 20 CNC2 72 118 CNC3 119 197 42K 70K