化学镀镍工艺
化学镀镍工艺
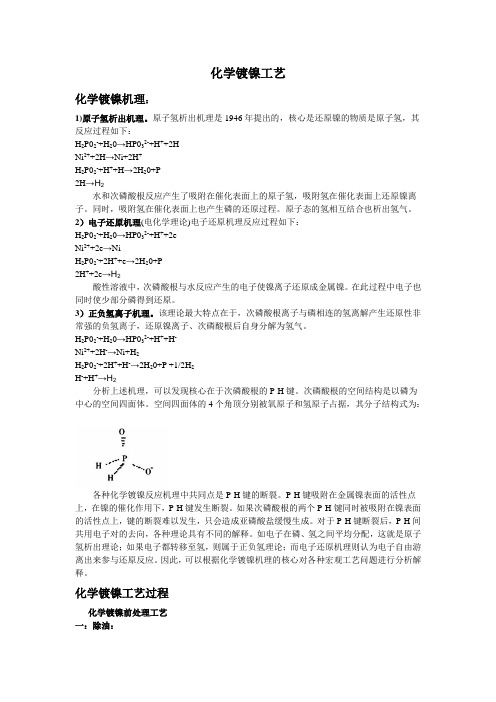
化学镀镍工艺化学镀镍机理:1)原子氢析出机理。
原子氢析出机理是1946年提出的,核心是还原镍的物质是原子氢,其反应过程如下:H2P02-+H20→HP032-+H++2HNi2++2H→Ni+2H+H2P02-+H++H→2H20+P2H→H2水和次磷酸根反应产生了吸附在催化表面上的原子氢,吸附氢在催化表面上还原镍离子。
同时,吸附氢在催化表面上也产生磷的还原过程。
原子态的氢相互结合也析出氢气。
2)电子还原机理(电化学理论)电子还原机理反应过程如下:H2P02-+H20→HP032-+H++2eNi2++2e→NiH2P02-+2H++e→2H20+P2H++2e→H2酸性溶液中,次磷酸根与水反应产生的电子使镍离子还原成金属镍。
在此过程中电子也同时使少部分磷得到还原。
3)正负氢离子机理。
该理论最大特点在于,次磷酸根离子与磷相连的氢离解产生还原性非常强的负氢离子,还原镍离子、次磷酸根后自身分解为氢气。
H2P02-+H20→HP032-+H++H-Ni2++2H-→Ni+H2H2P02-+2H++H-→2H20+P +1/2H2H-+H+→H2分析上述机理,可以发现核心在于次磷酸根的P-H键。
次磷酸根的空间结构是以磷为中心的空间四面体。
空间四面体的4个角顶分别被氧原子和氢原子占据,其分子结构式为:各种化学镀镍反应机理中共同点是P-H键的断裂。
P-H键吸附在金属镍表面的活性点上,在镍的催化作用下,P-H键发生断裂。
如果次磷酸根的两个P-H键同时被吸附在镍表面的活性点上,键的断裂难以发生,只会造成亚磷酸盐缓慢生成。
对于P-H键断裂后,P-H间共用电子对的去向,各种理论具有不同的解释。
如电子在磷、氢之间平均分配,这就是原子氢析出理论;如果电子都转移至氢,则属于正负氢理论;而电子还原机理则认为电子自由游离出来参与还原反应。
因此,可以根据化学镀镍机理的核心对各种宏观工艺问题进行分析解释。
化学镀镍工艺过程化学镀镍前处理工艺一:除油:(1)有机溶剂除油常用溶剂有:三氯乙烯、四氯乙烯、三氯乙烷(2)碱性除油常用的碱:氢氧化钠、碳酸钠、磷酸三钠、乳化剂和表面活性剂(3)电化学除油阴极除油、阳极除油、交替电解除油二:酸洗(1)化学酸洗盐酸、硫酸、硝酸、磷酸(2)电解酸洗在酸的溶液中采用阴极、阳极,阳极阴极联合(PR)电解酸洗比单纯得浸蚀酸洗速率快,特别是溶液除去那些附着紧密的氧化皮,而且允许酸的浓度有较大变化三:镀液组成以次磷酸盐为还原剂的酸性化学镀镍液溶液组成及其作用1:镍盐最常用的镍盐有硫酸镍和氯化镍,硫酸镍价格低廉,容易制成纯度较高的产品,别人为是镍盐的最佳选择次磷酸镍是镍离子的最理想的来源镀液中镍离子浓度不宜过高,镍液中镍离子过多会降低镀液的稳定性,容易形成粗糙的镀层镍离子浓度较低时,速率随浓度升高而上升,达到一定浓度后速度不再改变。
化学镀镍一般工艺
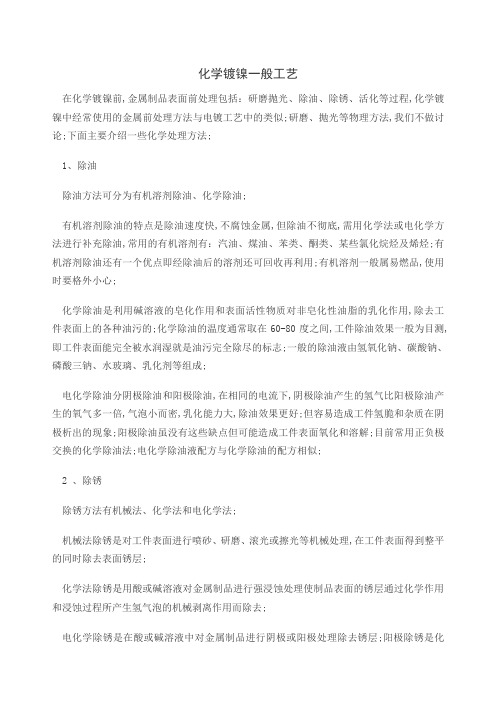
化学镀镍一般工艺在化学镀镍前,金属制品表面前处理包括:研磨抛光、除油、除锈、活化等过程,化学镀镍中经常使用的金属前处理方法与电镀工艺中的类似;研磨、抛光等物理方法,我们不做讨论;下面主要介绍一些化学处理方法;1、除油除油方法可分为有机溶剂除油、化学除油;有机溶剂除油的特点是除油速度快,不腐蚀金属,但除油不彻底,需用化学法或电化学方法进行补充除油,常用的有机溶剂有:汽油、煤油、苯类、酮类、某些氯化烷烃及烯烃;有机溶剂除油还有一个优点即经除油后的溶剂还可回收再利用;有机溶剂一般属易燃品,使用时要格外小心;化学除油是利用碱溶液的皂化作用和表面活性物质对非皂化性油脂的乳化作用,除去工件表面上的各种油污的;化学除油的温度通常取在60-80度之间,工件除油效果一般为目测,即工件表面能完全被水润湿就是油污完全除尽的标志;一般的除油液由氢氧化钠、碳酸钠、磷酸三钠、水玻璃、乳化剂等组成;电化学除油分阴极除油和阳极除油,在相同的电流下,阴极除油产生的氢气比阳极除油产生的氧气多一倍,气泡小而密,乳化能力大,除油效果更好;但容易造成工件氢脆和杂质在阴极析出的现象;阳极除油虽没有这些缺点但可能造成工件表面氧化和溶解;目前常用正负极交换的化学除油法;电化学除油液配方与化学除油的配方相似;2 、除锈除锈方法有机械法、化学法和电化学法;机械法除锈是对工件表面进行喷砂、研磨、滚光或擦光等机械处理,在工件表面得到整平的同时除去表面锈层;化学法除锈是用酸或碱溶液对金属制品进行强浸蚀处理使制品表面的锈层通过化学作用和浸蚀过程所产生氢气泡的机械剥离作用而除去;电化学除锈是在酸或碱溶液中对金属制品进行阴极或阳极处理除去锈层;阳极除锈是化学溶解、电化学溶解和电极反应析出的氧气泡的机械剥离作用而去除;阴极除锈是化学溶解和阴极析出氢气的机械剥离作用而去除;用于化学镀镍前处理除锈工艺基本与电镀的除锈工艺相同;3 、活化活化是使零件能获得充分活化的表面,这种酸蚀对于不同材质的零件所用的酸液是不同的;一般钢铁件的活化可用10%的硫酸或1:1的盐酸进行,活化的标准一般为工件表面冒出细小均匀的气泡;不锈钢件的活化可加大酸的浓度,并且加热进行酸蚀;严格讲,不锈钢的化学镀镍应该进行闪镀后再进行化学镀镍,也就是先打一个电解镍或电解铜的底层;。
第三章化学镀镍工艺

pH 值对沉积速率的影响
pH 值对镀层含磷量的影响
(二)温度
温度是影响化学镀镍反应活化能的主要参数。 化学镀工作时有一个启镀的温度,特别是酸性 化学镀镍,温度必须高于50℃时才能以明显的 速率进行。酸性次亚磷酸盐体系镀液的操作温 度一般为 80℃-95℃,温度过高镀液不稳定, 容易分解;温度过低,反应不进行。
(五)稳定剂 在正常条件下,化学镀镍溶液较稳定。但在 镀液受到污染、存在有催化活性的固体颗粒、 装载量过大或过小、pH值过高等异常情况下, 化学镀镍溶液会自发分解,会在整个溶液内生 成金属镍的颗粒,镀液迅速分解失效。为了防 止上述情况的发生,溶液中通常需要加入稳定 剂。稳定剂阻止或推迟了化学镀镍液的自发分 解,稳定镀液,有时还能加速反应,影响化学 镀镍层的磷含量以及内应力。
常用的有机溶剂有汽油(易燃)、甲基乙基 酮(易燃)、丙酮(易燃)、苯(易燃、有毒)、 溶剂石脑油(易燃、不经济)、四氯化碳(有腐 蚀性)。 这些溶剂除特殊情况外目前均不主张使用。 目前常使用的是氯化烃系溶剂,其中主要有三氯 乙烯、四氯乙烯、三氯乙烷。
(二)碱性除油
碱性除油是指用含有碱性化学药剂的处理液 除去表面油污的方法。这种方法实质是靠皂化和 乳化作用除油。碱性化学除油通常有下列组分: 氢氧化钠、碳酸钠、磷酸三钠、乳化剂。
(七)光亮剂
化学镀镍是一种功能性镀层,通常为半光亮 外观,然而近年来人们对化学镀镍的光亮性的要 求越来越高。
初级光亮剂一般可由萘、苯、甲苯、炔-烃化合物、 萘胺的磺酸、磺酸盐或它们的氨磺酰产物等组成, 如丁炔二醇及它们与环氧乙烷和环氧丙烷的醚化 产物、邻甲苯磺酰胺、苯二磺酸钠、糖精、对氨 酰基苯酚等。次级光亮剂由镉、硒、锑、钼、硫、 硫脲等金属离子或硫类化合物组成,如乙酸铅、 硫代硫酸钠、硫酸镉等。
化学镀镍工艺
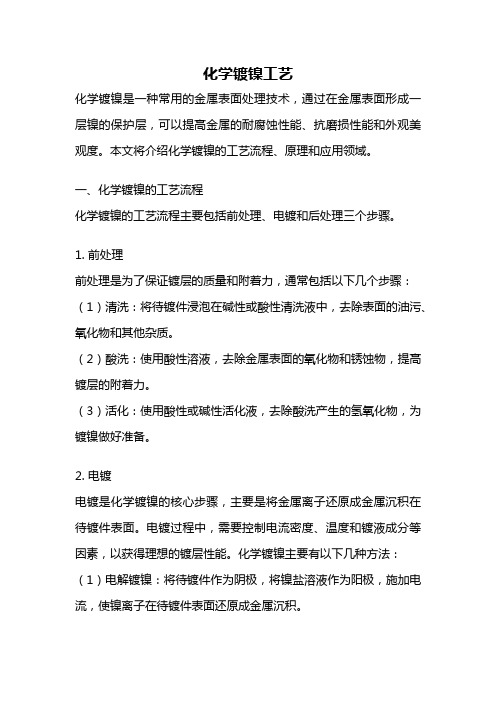
化学镀镍工艺化学镀镍是一种常用的金属表面处理技术,通过在金属表面形成一层镍的保护层,可以提高金属的耐腐蚀性能、抗磨损性能和外观美观度。
本文将介绍化学镀镍的工艺流程、原理和应用领域。
一、化学镀镍的工艺流程化学镀镍的工艺流程主要包括前处理、电镀和后处理三个步骤。
1. 前处理前处理是为了保证镀层的质量和附着力,通常包括以下几个步骤:(1)清洗:将待镀件浸泡在碱性或酸性清洗液中,去除表面的油污、氧化物和其他杂质。
(2)酸洗:使用酸性溶液,去除金属表面的氧化物和锈蚀物,提高镀层的附着力。
(3)活化:使用酸性或碱性活化液,去除酸洗产生的氢氧化物,为镀镍做好准备。
2. 电镀电镀是化学镀镍的核心步骤,主要是将金属离子还原成金属沉积在待镀件表面。
电镀过程中,需要控制电流密度、温度和镀液成分等因素,以获得理想的镀层性能。
化学镀镍主要有以下几种方法:(1)电解镀镍:将待镀件作为阴极,将镍盐溶液作为阳极,施加电流,使镍离子在待镀件表面还原成金属沉积。
(2)化学还原镀镍:利用化学反应将镍离子还原成金属沉积在待镀件表面,无需外加电流。
3. 后处理后处理是为了提高镀层的质量和外观,通常包括以下几个步骤:(1)酸洗:将镀层浸泡在酸性溶液中,去除表面的氢氧化物和杂质。
(2)抛光:使用机械或化学方法,提高镀层的光亮度和平整度。
(3)清洗:将镀件浸泡在清水中,去除残留的酸洗液和其他杂质。
(4)干燥:将镀件进行烘干,确保镀层完全干燥。
二、化学镀镍的原理化学镀镍的原理是利用电化学反应将金属离子还原成金属沉积在待镀件表面。
在电镀过程中,镍离子在电解液中发生还原反应,得到金属镍,并沉积在待镀件表面。
镀层的厚度可以通过控制电镀时间来调节。
化学镀镍的镀液主要由镍盐、镉盐和其他添加剂组成。
镀液中的镍离子和镉离子通过电解反应分别还原成金属镍和金属镉,镀液中的添加剂可以调节镀层的成分、结构和性能。
三、化学镀镍的应用领域化学镀镍广泛应用于装饰、防腐和电子等领域。
化学镀镍

化学镀镍ENP简介化学镀镍技术是采用金属盐和还原剂,在材料表面上发生自催化反应获得镀层的方法。
到目前为止,化学镀镍是国外发展最快的表面处理工艺之一,且应用范围也最广。
化学镀镍之所以得到迅速发展,是由于其优越的工艺特点所决定。
一、化学镀镍层的工艺特点1. 厚度均匀性厚度均匀和均镀能力好是化学镀镍的一大特点,也是应用广泛的原因之一,化学镀镍避免了电镀层由于电流分布不均匀而带来的厚度不均匀,电镀层的厚度在整个零件,尤其是形状复杂的零件上差异很大,在零件的边角和离阳极近的部位,镀层较厚,而在内表面或离阳极远的地方镀层很薄,甚至镀不到,采用化学镀可避免电镀的这一不足。
化学镀时,只要零件表面和镀液接触,镀液中消耗的成份能及时得到补充,任何部位的镀层厚度都基本相同,即使凹槽、缝隙、盲孔也是如此。
2. 不存在氢脆的问题电镀是利用电源能将镍阳离子转换成金属镍沉积到阳极上,用化学还原的方法是使镍阳离子还原成金属镍并沉积在基体金属表面上,试验表明,镀层中氢的夹入与化学还原反应无关,而与电镀条件有很大关系,通常镀层中的含氢量随电流密度的增加而上升。
在电镀镍液中,除了一小部分氢是由NiSO4和H2PO3反应产生以外,大部分氢是由于两极通电时发生电极反应引起的水解而产生,在阳极反应中,伴随着大量氢的产生,阴极上的氢与金属Ni-P合金同时析出,形成(Ni-P)H,附着在沉积层中,由于阴极表面形成超数量的原子氢,一部分脱附生成H2,而来不及脱附的就留在镀层内,留在镀层内的一部分氢扩散到基体金属中,而另一部分氢在基体金属和镀层的缺陷处聚集形成氢气团,该气团有很高的压力,在压力作用下,缺陷处导致了裂纹,在应力作用下,形成断裂源,从而导致氢脆断裂。
氢不仅渗透到基体金属中,而且也渗透到镀层中,据报道,电镀镍要在400℃×18h或230℃×48h的热处理之后才能基本上除去镀层中的氢,所以电镀镍除氢是很困难的,而化学镀镍不需要除氢。
化学镀镍的工艺流程

化学镀镍的工艺流程
首先,进行表面处理。
表面处理是化学镀镍工艺中至关重要的
一步,它直接影响着后续的镀镍质量。
表面处理的主要目的是去除
基材表面的油污、氧化物和其他杂质,使基材表面变得清洁和粗糙,以利于镀液的附着和镀层的结合力。
表面处理一般包括除油、酸洗、水洗、活化和化学镀前处理等步骤。
其次,进行镀镍操作。
在表面处理完成后,就可以进行镀镍操
作了。
镀镍操作是化学镀镍工艺的核心环节,主要是将含有镍离子
的镀液中的镍离子还原成纯镍沉积在基材表面上。
镀液中的主要成
分包括镍盐、缓冲剂、还原剂和复合添加剂等。
镀液的配方和镀镍
条件的控制对镀层的质量有着重要影响。
镀液的搅拌、温度、PH值、电流密度等参数都需要严格控制,以获得致密、光亮的镀层。
最后,进行后处理。
镀镍完成后,还需要进行后处理工序。
后
处理主要包括水洗、中性化处理、烘干和包装等环节。
水洗是为了
去除镀液残留在镀层表面的杂质,中性化处理是为了中和镀液残留
在镀层上的酸碱成分,烘干是为了去除水分,包装是为了保护镀层
免受外界环境的影响。
总的来说,化学镀镍的工艺流程是一个复杂而严谨的过程,需要严格控制各个环节,以确保镀层的质量和性能。
通过合理的工艺流程和严格的操作控制,可以获得均匀、致密、光亮、耐腐蚀的镍镀层,提高基材的使用性能和寿命。
化学镀镍工艺在电子、航空、汽车等领域有着广泛的应用,对于提高产品质量和降低成本具有重要意义。
工艺技术化学镀镍详解

工艺技术:化学镀镍详解一、化学镀镍层的工艺特点1.厚度均匀性厚度均匀和均镀能力好是化学镀镍的一大特点,也是应用广泛的原因之一,化学镀镍避免了电镀层由于电流分布不均匀而带来的厚度不均匀,电镀层的厚度在整个零件,尤其是形状复杂的零件上差异很大,在零件的边角和离阳极近的部位,镀层较厚,而在内表面或离阳极远的地方镀层很薄,甚至镀不到,采用化学镀可避免电镀的这一不足。
化学镀时,只要零件表面和镀液接触,镀液中消耗的成份能及时得到补充,任何部位的镀层厚度都基本相同,即使凹槽、缝隙、盲孔也是如此。
2.不存在氢脆的问题电镀是利用电源能将镍阳离子转换成金属镍沉积到阳极上,用化学还原的方法是使镍阳离子还原成金属镍并沉积在基体金属表面上,试验表明,镀层中氢的夹入与化学还原反应无关,而与电镀条件有很大关系,通常镀层中的含氢量随电流密度的增加而上升。
在电镀镍液中,除了一小部分氢是由NiSO4和H2PO3反应产生以外,大部分氢是由于两极通电时发生电极反应引起的水解而产生,在阳极反应中,伴随着大量氢的产生,阴极上的氢与金属Ni-P合金同时析出,形成(Ni-P)H,附着在沉积层中,由于阴极表面形成超数量的原子氢,一部分脱附生成H2,而来不及脱附的就留在镀层内,留在镀层内的一部分氢扩散到基体金属中,而另一部分氢在基体金属和镀层的缺陷处聚集形成氢气团,该气团有很高的压力,在压力作用下,缺陷处导致了裂纹,在应力作用下,形成断裂源,从而导致氢脆断裂。
氢不仅渗透到基体金属中,而且也渗透到镀层中,据报道,电镀镍要在400℃×18h或230℃×48h的热处理之后才能基本上除去镀层中的氢,所以电镀镍除氢是很困难的,而化学镀镍不需要除氢。
3.很多材料和零部件的功能如耐蚀、抗高温氧化性等均是由材料和零部件的表面层体现出来,在一般情况下可以采用某些具有特殊功能的化学镀镍层取代用其他方法制备的整体实心材料,也可以用廉价的基体材料化学镀镍代替有贵重原材料制造的零部件,因此,化学镀镍的经济效益是非常大的。
化学镀镍工艺流程
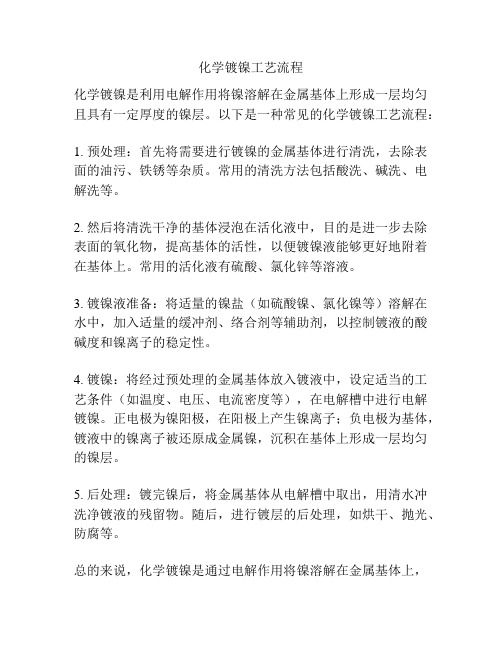
化学镀镍工艺流程
化学镀镍是利用电解作用将镍溶解在金属基体上形成一层均匀且具有一定厚度的镍层。
以下是一种常见的化学镀镍工艺流程:
1. 预处理:首先将需要进行镀镍的金属基体进行清洗,去除表面的油污、铁锈等杂质。
常用的清洗方法包括酸洗、碱洗、电解洗等。
2. 然后将清洗干净的基体浸泡在活化液中,目的是进一步去除表面的氧化物,提高基体的活性,以便镀镍液能够更好地附着在基体上。
常用的活化液有硫酸、氯化锌等溶液。
3. 镀镍液准备:将适量的镍盐(如硫酸镍、氯化镍等)溶解在水中,加入适量的缓冲剂、络合剂等辅助剂,以控制镀液的酸碱度和镍离子的稳定性。
4. 镀镍:将经过预处理的金属基体放入镀液中,设定适当的工艺条件(如温度、电压、电流密度等),在电解槽中进行电解镀镍。
正电极为镍阳极,在阳极上产生镍离子;负电极为基体,镀液中的镍离子被还原成金属镍,沉积在基体上形成一层均匀的镍层。
5. 后处理:镀完镍后,将金属基体从电解槽中取出,用清水冲洗净镀液的残留物。
随后,进行镀层的后处理,如烘干、抛光、防腐等。
总的来说,化学镀镍是通过电解作用将镍溶解在金属基体上,
形成一层均匀且具有一定厚度的镍层。
这一工艺流程需要经过预处理、镀镍、后处理等多个步骤,工艺条件的控制和辅助剂的添加都对镀液的稳定性和镀层的质量有着重要影响。
化学镀镍具有镀层硬度高、抗腐蚀性好、外观美观等优点,广泛应用于金属制品的表面处理和装饰。
- 1、下载文档前请自行甄别文档内容的完整性,平台不提供额外的编辑、内容补充、找答案等附加服务。
- 2、"仅部分预览"的文档,不可在线预览部分如存在完整性等问题,可反馈申请退款(可完整预览的文档不适用该条件!)。
- 3、如文档侵犯您的权益,请联系客服反馈,我们会尽快为您处理(人工客服工作时间:9:00-18:30)。
化学镀镍工艺——镀前处理需知
化学镀镍的对象是具体的工件,进厂待镀的工件状况,包括工件材质、制造或维护方法,工件尺寸和最终使用情况是不同的;因此前处理方法应有所不同。
在确定正确的前处理工艺流程时,必须对工件善有充分的了解。
合金类型为保证镀层足够的结合力以及镀层质量,必须鉴定基体材质。
某些含有催化毒性合金成分的材料在镀前处理时加以表面调整,保证除去这些合金成分后才能进行化学镀镍。
例如:铅(含铅钢)、硫(含硫钢)、过量的碳(高碳钢)、碳化物(渗碳钢)等。
因为这些物质的残留会产生结合力差和起泡问题。
而且,在未除净这些物质的表面、镀层会产生针孔和多孔现象。
另一种处理方法是在镀前采用预镀的方法隔离基体才料中有害合金元素的影响。
在不清楚待镀工件材质而且又不可能进行材料分析的情况下,必须进行预先试验,试合格后方可处理工作。
工件的制造历史钢件表面状况由于渗碳、渗氮、淬火硬化后提高表面硬度是重要的变化途径之一。
通常化学镀镍在硬度范围HRC58-62的铁件表面上镀层的结合力是难以合格的。
一方面,上述硬度范围的工件必须进行特别的清洗方法,即在含氰化物的溶液中周期换向电解活化或其它合适的电解清洗,以便溶解除去表面的无机物质诸如碳化物。
另一方面,在施镀中产生的表面应力,诸如航天工业用的表面有较高张应力的工件,必须在镀前镀后进行去应力处理,以获得合格的结合力。
在制造过程中工件表面大量通讯以除去的机械润滑油和抛光剂等也必须在镀前清除干净。
工件的维修历史工件维修时为除去表面的有机涂层、铁锈或氧化皮,采用喷砂处理,这种工件是化学镀前最难处理的。
因为这些工件表面不仅嵌进了残留物质,而且腐蚀产物附着得很牢。
在这种情况下,应先采用机械方法清洁表面,以保证后续化学清洗和活化工序的质量。
为除去工件表面嵌进的油脂和化学脏污,有时预先烘工件十分有效,尽管这不是唯一的好用的清除方法。
工件的几何尺寸许多工件的几何赃妨碍了采用某前处理技术,如大尺寸的容器以及内表面积很大的管件就是如此。
通常清洗和活化钢件应包括电解清洗和活化,在上述情况下,应采用机械清洗、化学清洗和活化更为可行。
对于具有盲孔和形状复杂的零件,需要加强清洗工序以解决除去污垢、氢气泡逸出和溶液带出的问题。
在工件吊挂和放置方法上也应考虑解决上述问题。
工件非镀面的阻镀问题许多工件要求局部化学镀镍,因此必须彩屏蔽材料将非镀部分保护起来。
屏蔽材料可用压敏胶带、涂料、专用塑料夹具等。
当然市场上现在有商品的阻镀涂料(或叫保护漆)出售,并且高级一点的,可以镀后轻松除去,用专用溶剂溶解后可以反复使用。
化学清洗浸洗是化学镀前处理的重要步骤之一,其重要的功能在于清除工件表面的污垢,为保证清洗效果,通常使用清洗剂、机械搅拌和加温。
采用碱性清洗剂时必须加热至60-80℃,以便彻底清洗污垢,大多数碱性清洗采取浸洗并且强力搅拌,也可以采用喷淋清洗方式。
市售的浸洗清洁剂的质量和去污能力差异很大,因此根据工件污染程度选用清洁剂是很重要的。
电解清洗电解清洗化学镀镍活化处理前的末道清洗方法,多适用于精密零件。
直流电解清洗即阻极电解清洗的优点在于工件表面产生大量的氢气增加了洗涤效果;其缺点在于工件带负电,因而吸附清洗溶液中的铜、锌和其它金属离子、皂类和某些胶体物质,在工件上形成疏松的电极泥以致带去。
电解清洗时采用周期换向电注,当工件为阳极时,迫使工件表面带正电荷的离子和污垢脱离。
而且工件表面生成的氧气有利于有效地洗涤掉嵌牢在工件上的污垢,由清洗溶液中的清洁剂去润湿污垢,乳化转换掉污垢。
水洗两个前处理工序之间的水洗工序,目的在于防止上道工序带出的溶液对下道工序溶液的污染和从工件表面清除污垢、金属离子污染和电极泥,以保证镀层结合力合格。
水洗工序进行得好坏与设计出一个好的工艺流程是很重要的,应避免共用漂洗,即回头至先前用过的槽中漂洗的现象出现。