管道机器人(英文)
双轮链平面管道检测机器人外文文献翻译、中英文翻译、外文翻译
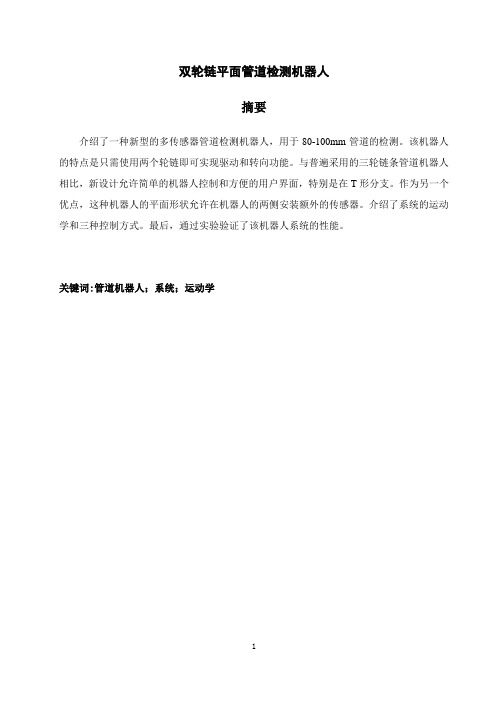
双轮链平面管道检测机器人摘要介绍了一种新型的多传感器管道检测机器人,用于80-100mm管道的检测。
该机器人的特点是只需使用两个轮链即可实现驱动和转向功能。
与普遍采用的三轮链条管道机器人相比,新设计允许简单的机器人控制和方便的用户界面,特别是在T形分支。
作为另一个优点,这种机器人的平面形状允许在机器人的两侧安装额外的传感器。
介绍了系统的运动学和三种控制方式。
最后,通过实验验证了该机器人系统的性能。
关键词:管道机器人;系统;运动学I.绪论管道检测机器人的功能可以描述为驱动、转向、检测和检索。
而用于直径小于100mm管道检测的机器人,在设计紧凑的转向机构和安装磁探头、超声波探头等传感器检测裂纹、破裂、泄漏等方面存在特殊困难。
管道机器人机构在机器人技术领域有着悠久的发展历史,按其运动模式可分为几种基本形式。
它们有轮式、尺蠖式、腿式、螺旋式、履带式和被动式。
其中轮式管道检测机器人最为流行,[1]-[8]。
然而,它们不适合在垂直路径或在t分支操作。
近10年来,人们对差动驱动型机构[9]-[11]进行了较为深入的研究。
差动驱动类型通常有三个动力轮链。
通过独立控制每个链条的速度,机器人可以通过肘部和t型分支。
然而,当只使用一个机器人模块时,有时会在T支[9]处发生奇异运动。
为了解决这一问题,已经开发了几种方法,如主动转向关节机构[12-13]或两个机器人模块[9]协作。
然而,整个机器人系统的体积变得庞大。
使用三个动力轮链的另一个缺点是没有足够的空间在机器人体内安装更多的传感器,因为三个轮链占据了管道的大部分横截面积,特别是直径小于100mm的管道。
目前,机器人身体前只安装了一个摄像头。
T. Okad等[14-16]开发了平板式管道检测机器人。
然而,他们的设计是复杂的,并用于大型管道。
针对这些因素,我们提出了一种双动力轮链的管道检测机构。
两个轮链以180度的角度分开布置,所以可以在机器人身体的两侧附加传感器。
各轮采用两台电机控制;一种用于驾驶,另一种用于驾驶。
管道机器人控制及通讯系统和管道检测共3篇

管道机器人控制及通讯系统和管道检测共3篇管道机器人控制及通讯系统和管道检测1管道机器人控制及通讯系统和管道检测管道机器人控制是指使用控制系统控制管道机器人的运动、操作等行为,使其能够在管道内完成各种任务。
管道机器人通讯系统则是指管道机器人与外部设备或中央控制系统之间的通讯方式,以便实现远程监控和数据传输等功能。
管道检测是指使用各种工具和设备,对管道进行检测、评估和监测,以找出管道内的问题和隐患,以及及时进行维修和保养。
管道机器人控制系统主要分为硬件和软件两部分。
硬件主要包括电机、传感器、阀门、液压系统、机器人外壳、控制面板等。
软件主要是控制系统的软件程序,它可以控制机器人的运动、操作、状态等。
电机是管道机器人完成各种动作的驱动力,传感器可以实现对环境的感知与控制,阀门用于控制管道内的流量和压力,液压系统可以驱动机器人的动作和操作,机器人外壳可以保护机器人的安全和稳定性,控制面板是人机交互的中心,可以实现对机器人的远程控制。
管道机器人的通讯系统主要包括,数据采集、数据存储、数据传输以及远程监控等方面。
数据采集可以通过传感器和控制系统来实现。
数据存储可以在机器人内部的存储设备中实现,也可以通过无线云端的方式进行存储。
数据传输可以通过有线或者无线等通讯方式实现,远程监控可以通过网络或者云端进行实现。
管道检测是指利用工具或设备,对管道进行检测和监测,以找出管道内的问题和隐患,及时进行维修和保养。
管道检测的主要方法包括:摄像头检测、超声波检测、磁探测等方法。
摄像头检测是指在机器人上搭载摄像头,利用其进行拍摄和检测。
超声波检测是利用超声波探头,对管道内部和外部进行探测和检测。
磁探测可以检测管道内或者表面上的磁性材料,判断管道内是否存在隐患或者故障。
以上内容是管道机器人控制及通讯系统和管道检测方面的简单介绍,管道机器人的相关技术还有很大的研究空间和发展潜力。
随着社会的不断发展和进步,管道机器人技术将得到进一步应用和推广,为人们的生产生活带来更多的便利和舒适。
管道机器人技术指标

管道机器人技术指标1.引言1.1 概述概述部分的内容:管道机器人技术是以机器人技术为基础,应用于管道行业的一项创新技术。
随着管道行业的快速发展和复杂化需求的增加,传统的人工维修和巡检方式已经无法满足现代化管道行业的需求。
管道机器人技术的出现填补了这一空白,为管道行业的维修、巡检和监测工作提供了全新的解决方案。
管道机器人技术指标是对管道机器人在技术性能和综合能力方面的评估指标。
这些指标涵盖了机器人的外观、尺寸、自主导航和控制能力、运动稳定性、承载能力、耐高温、耐腐蚀、图像处理和数据传输等方面。
通过对这些指标的评估,可以客观地了解管道机器人的优势和不足,从而为其进一步的优化和改进提供依据。
在管道机器人技术指标中,外观和尺寸是最为基础的指标之一。
由于管道的形状和尺寸各异,机器人需要具备足够的灵活性和适应性,能够适应各类管道的形状和尺寸,并能在狭小的空间中自由移动和操作。
自主导航和控制能力是保证机器人能够准确无误地进行巡检和维修工作的重要指标,这需要机器人具备高精度的定位、路径规划和避障能力。
运动稳定性和承载能力是保证机器人在管道内安全运行和进行维修工作的重要指标。
机器人需要具备稳定的运动性能,以防止在运动过程中出现意外情况。
同时,机器人需要能够承载各类传感器、工具和设备,在维修过程中能够完成各类操作。
耐高温和耐腐蚀是针对部分特殊工况的指标,对于一些高温和腐蚀性较强的管道,机器人需要具备相应的防护和耐用能力,以确保机器人在极端环境下的正常运行和工作。
图像处理和数据传输是保证管道机器人能够实时获取并传输巡检和维修数据的关键指标,这需要机器人具备快速准确的图像处理和数据传输能力。
总之,管道机器人技术指标对于评估和优化管道机器人的性能和能力起到了重要的作用。
随着技术的不断进步和完善,相信管道机器人将在未来的管道行业中发挥越来越重要的作用。
1.2 文章结构文章结构部分的内容可以参考如下:在本文中,我们将按照以下结构来阐述管道机器人技术指标的相关内容。
简单结构管道检测机器人(有出处)687--中英文翻译

中文翻译:简单结构管道检测机器人本文介绍了管道检测机器人的原始架构。
该机器人由包含两个万向节铰接部分。
一部分是沿管道平行移动的轴车轮盘,而另一部分则是被迫遵循与螺旋运动有关的轴线旋转的车轮倾斜管。
单台电动机被放置在两个机构之间产生的运动。
所有车轮安装在悬架上,以适应不断变化的曲线管道。
该机器人有其自己的电池和无线链路。
四种不同管径分别为的170,70和40毫米。
对于较小的直径,电池,无线电接收器,可放置在其他额外的机构中。
这种架构非常简单,其旋转运动可以被利用来进行擦洗或检验任务。
关键词:自主移动机器人,在管道检测,螺旋运动管道检测机器人已经被研究了很长一段时间,许多原来的运动观念被提出来解决在管道直径,曲线和能源供应变化中有关的许多技术困难。
虽然一个详尽的文献回顾是不可能的,根据有限的可用空间,几大类别,可确定几大类别:1对于小规模,许多项目遵循蚯蚓原则:中央部分组成轴向移动,而两端连接的设备具有阻隔管道。
这一概念已经提出气动版本(如[1]),但他们需要电力脐带。
对于较小的直径(10毫米或更小),根据尺蠖的原则,或根据惯性运动由锯齿波电压驱动[2],或使用与微分摩擦系数振动鳍[3],则采用压电驱动。
2对于各种中型管道,根据直径的适应性和转弯能力古典机电系统已提出各种涉及车轮和轨道运动学结构。
3对于大型管道,管道爬行走路也已提出[6]。
文中提出的四个移动机器人属于第二类,他们的管直径从40到170mm,该设计尝试使用单一驱动器减少机器的复杂性实现沿管的的流动性,即使我们的研究可看作一个独立努力地结果。
但此螺旋论似乎已经被研究过。
体系结构图1该机器人主要分为两部分,定子和转子,包括一个DC 连接,马达与减速机,万向节。
定子配备了一套轮子,有助于运动平行; 在这种情形下,定子约束沿着管轴,而转子的车轮只能沿着螺旋轨迹,该机器人之间的轴向速度和旋转速度的关系 αtg R w v ∙∙=其中R 为管道半径, a 是车轮倾斜角度。
机器人专业英语词汇学习 2.1

66
20 boolean(布尔型) 67
21
bracket(支架)
68
22 brake(制动器,闸) 69
23
button(按钮)
70
24 cabinet(机箱,柜子) 71
25
cable(线缆)
72
26 calculate(计算) 73
27 calibration(标定,校准) 74
28 cartesian(笛卡尔) 75
207
TRUE(真)
208
unit(部件)
209
unload(卸载)
210
upper(较高的)
211
value(数值)
212 variable(变量)
213
via(导通孔)
214
vision(视觉)
215 visual(视觉的)
216
voltage(电压)
217
warning(警告)
218 warranty(保证,授权)
161
receive(接收)
118
metal(金属)
162 reference(参考)
119
method(方法)
163 relative(相对的)
120 minimum(最小值) 164
relay(继电器)
121
mode(代码)
165
release(释放)
122
module(模块)
166 remove(除去,拆卸)
10 arm(手臂,装备) 57
11
array(数组)
58
12
attach(附加)
59
13 automatic(自动的) 60
管道机器人(英文)

A SIMPLE ARCHITECTURE FOR IN-PIPE INSPECTION ROBOTS Mihaita HORODINCA, Ioan DOROFTEI, Emmanuel MIGNON, André PREUMONTActive Structures LaboratoryUNIVERSITE LIBRE DE BRUXELLESAv. F. D. Roosevelt 50, cp 165/42, Brussels, BelgiumPhone: (32)2-6504663 Fax: (32)2-6504660e-mail: andre.preumont@ulb.ac.beAbstract: The paper presents an original robot architecture for in-pipe inspection. Therobot consists of two parts articulated with a universal joint. One part is guided along thepipe by a set of wheels moving parallel to the axis of the pipe, while the other part isforced to follow an helical motion thanks to tilted wheels rotating about the axis of thepipe. A single motor is placed between the two bodies to produce the motion. All thewheels are mounted on a suspension to accommodate for changing tube diameter andcurves in the pipe. The robot is autonomous and carries its own batteries and radio link.Four different prototypes have been constructed for pipe diameters of 170, 70 and 40mm, respectively. For smaller diameters, the batteries and the radio receiver may beplaced on an additional body attached to the others. The autonomy of the prototypes isabout 2 hours. This architecture is very simple and the rotary motion can be exploited tocarry out scrubbing or inspection tasks.Keywords: Autonomous mobile robot, In-pipe inspection, Helical motionIntroductionPipe inspection robots have been studied for a long time, and many original locomotion concepts have been proposed to solve the numerous technical difficulties associated with the change in pipe diameter, curves and energy supply. Although an exhaustive review of the literature is impossible due to the limited space available, a few broad categories can be identified:(i) For small size, many projects follow the earthworm principle consisting of a central partmoving axially while the two end parts are provided with blocking devices connectedtemporarily to the pipe. Pneumatic versions of this concept have been proposed (e.g. [1]),but they require an umbilical for power. For smaller diameter (10 mm or less), apiezoelectric actuation has been considered, according to the inchworm principle, oraccording to an inertial locomotion driven by a saw-tooth wave voltage [2], or usingvibrating fins with differential friction coefficients [3].(ii) For medium size piping, classical electromechanical systems have been proposed with various architectures involving wheels and tracks, with more or less complicatedkinematical structures, depending on the diameter adaptability and turning capability (e.g.[4,5]).(iii) For large pipes, walking tube crawlers have also been proposed [6].The four mobile robots presented in this paper belong to the second category, they span a tube diameter from 40 to 170 mm. The design results from an attempt to reduce the electromechanical complexity through the use of a single actuator to achieve mobility along the tube. Although our study can be regarded as an independent effort, it appears that the “spiral wheel” strategy was explored before [7].ArchitectureThe robot consists of two main parts, a stator and rotor, connected by an active joint including a D.C. motor with reducer and, in some cases, a universal joint. The stator is equipped with a set of wheels which allow the motion parallel to the tube axis; the rotor is equipped with wheels tilted with a small angle with respect to the plane perpendicular to the tube axis (Fig. 1. a). In this way, the stator is constrained to move along the tube axis while the wheels of the rotor can only move along helical trajectories, and the rotation of the rotor with respect to the stator generates the axial motion. The relation between the axial velocity v of the robot and the rotation velocity ωof the rotor is:αωtg R v ⋅⋅=where R is the radius of the pipe and α is the tilting angle of the wheels of the rotor, taken as 10° throughout this project. The wheels on the stator and on the rotor must be located in order to guarantee the overturning stability, to assure a sufficient contact force between the robot and the pipe, to adapt to small changes in the pipe diameter and obstacles, and to allow travelling in curved pipes. For the larger robot (D-170), the robot is rigidly connected to the axis of the motor and three pairs of wheels on both the rotor and the stator are sufficient for stability. For smaller diameters, curved pipes require more degrees of freedom, because the connection between the rotor and the stator does not stay on the tube axis during turning. This is achieved with a universal joint provided with some axial backlash along the two axes of the joint; overturning stability requires the doubling of the number of wheels on the stator.Two-body architecture for larger diameter (D-170) (b) Three-body architecture for small diameter (D-40).(a) (b)For diameter above 70 mm, the robot is provided with 9 batteries (AA NiCd 600 mAh) which are distributed around the motor on the stator. Tests have shown that they give a reasonable autonomy of the order of 2 hours. For smaller diameters, this configuration is no longer possible and the robot is made of three bodies separated by two universal joints (Fig. 1. b): the first one consists of the rotor with the tilted wheels; the second one includes the motor and reducer, and the third one is the stator with the axial wheels, the energy supply and the telecom.(a)(a) The motor and the batteries are mounted on the stator.(b) The motor and batteries are mounted on the rotor.(a) (b) (c) (d)Figure 3: HELI-PIPE family portrait. (a) D-170, (b) D-70/1, (c) D-70/2, (d) D-40Two design alternatives have been investigated for a diameter of 70 mm (Fig. 2). In the first one, the motor and the batteries are mounted on the stator while in the second one they are mounted on the rotor; this second alternative is not acceptable if the robot is used with a tether for power supply. Table1 gives the main characteristics of the various robots; by “payload”, it is meant the maximum allowed axial force in addition to the weight when the robot is moving upwards in a vertical position.References[1] C. Anthierens, C. Prelle, A., Jutard, M. Bétemps, “Pneumatic Actuated Microrobot for In-Pipe Locomotion”, 4th Japan-France / 2nd Asia-Europe Congress on Mechatronics, Kitakyushu, Japan, 6-8 october, 1998.[2] H. Nishikawa, T. Sasaya, T. Shibata, T. Kaneko, N. Mitumoto, S. Kawakita and N. Kawahara, DENSO CORPORATION, Japan, “In-Pipe Wireless Micro Locomotive System”, in Proc. International Symposium on Mechatronics and Human Science (MHS ’99), Nagoya, Japan, Nov. 24-26,1999.[3] S. Aoshima , T. Tsujimura, T.,Yabuta , “A Miniature Mobile Robot Using Piezo Vibration for Mobility in a Thin Tube” Transactions of ASME, Journal of Dynamic Systems, Measurements and Control, Vol. 115, pp. 270-278, June 1993.[4] K. Suzumori, T. Miyagawa, M. Kimura, Y. Hasegawa, “Micro Inspection Robot for 1-in Pipes” in IEEE/ASME Transactions on Mechatronics, vol. 4, No. 3, pp. 286-292. September 1999.[5] S. Hirose, H. Ohno, T. Mitsui, K. Suyama, “Design of In-Pipe Inspection Vehicles for ø25, ø 50, ø 150 Pipes”, Journal of Robotics and Mechatronics 12, 3, pp. 310-317, 2000.[6] F. Pfeiffer, T. Rossmann, “Control of a Tube Crawler”, Proceedings of the Fourth International Conference on Motion and Vibration Control, Movic’ 98,Zurich, 1998, pp. 889-894, Vol. 3, Switzerland, August 25-28.[7] JGC Corporation, “Inspection Robots in Nuclear Power Plants” Robotics in Nuclear Facilities, Special issue for the exhibition of the 11th International Conference on Structural Mechanics in Reactor Technology (SMIRT II), Tokyo, August 1991.。
国外管道机器人3

Manufacturertele rob Gesellschaft fuer Fernhantierungstechnik mbH Vogelsangstrasse 8Base unit with different equipmentwith manipulatorwith barrel gripperwith hydraulic chiselwith shovel and bucketwith log gripperwith hydraulic shears concrete mill and crusherControl equipmentmanipulator operator, control centremobile control centretele rob ’s Rem ote I ntervention S ystem (REMIS) bases on the idea of having a wide range of equipment to approach all imaginable types of situations from a safe distance as it is necessary for jobs to be carried out in hazardous environments. The handling equipment is brought in position by an excavator-like track based vehicle which makes the system as independent as possible to the terrain to work in.An onboard video and audio system allows the operator to be virtually present when working from the control centre.Manufacturertele rob Gesellschaft fuer Fernhantierungstechnik mbH Vogelsangstrasse 8Carrying system:Remote controlled track chassis with articulated arm, similar to an excavator (see pictures above). It is hydraulically driven and powered by a diesel engine. The carrying system is controlled via a wireless link carrying the RC-signals and also feedback information about the vehicle status.Technical data: Height appx 1850 mm (6’ 1”) Length (outriggers up) appx 4000 mm (13’ 2”) Length (outriggers down) appx 5000 mm (16’ 5”)Width (track gage adjustable) appx 1500 … 1950 mm (4’ 11” … 6’ 5”) Width of tracks appx 400 mm (15”) Weight appx 6.5 tons(metric) Payload at tool flange appx 1400 kg (3100 lb)The operating distance by a handheld control unit (direct view) is appx 300m (1000’).Driven from the control centre an operating distance of up to 1 km (2/3 miles) is possible. If an additional antenna mast is applied the distance can be increased to several miles.Video equipment:Fix cameras on each corner of the chassis for driving, 2 zoom cameras sideways of the arm on tiltable, extentable booms with tilt-swivel head. The viewing area of the cameras is illuminated as well as the working area of the adapted tools. There is also a stereoscopic camera system available as well as a video multiplexing unit to transmit more than one picture per video link.Transportation devices:• Carrying system, manipulators, toolsThe carrying system with the tools and manipulators can be transported on a trailer or lorry. • Control centreThe whole control centre can be located in a 4-wheel drive-lorry with box body where the control cubicles for the manipulator arms and their master arms as well as control desks and video monitors are fix installed. An on board generator provides sufficient power to supply the manipulators independently from mains supply. The control room can be air conditioned.The whole control centre can also be installed into a container.Manufacturertele rob Gesellschaft fuer Fernhantierungstechnik mbH Vogelsangstrasse 8Adaptable equipment:• Force reflecting-manipulators (tele rob EMSMs):Cable controlled, up to 300m(1000’). The cables are managed by a cable management system located inside the control vehicle. EMSM2b, single or double armPayload 24kg/45kg (53lb/100lb) continuous/short term per arm Purpose: sensitive handling of with “extended hands”EMSM3, single armPayload 60kg/100kg (130lb/220lb) continuous/short term per arm Purpose: powerful handling of with “remote hands”The base of the manipulators can be equipped with a tool rack which is accessible with the gripper.A combination of each an EMSM2b and an EMSM3 manipulator arm may cover a wide range of tasks, this arrangement can be improved by an additional cantilevered chain hoist to handle material, slinging happens with themanipulators. The payload of the hoist depends on the remaining payload of the carrying system.• Hydraulically driven equipment Controlled via carrying system• parallel finger gripper, 250 kg (550 lb) payload, for material handling• Hydraulically driven barrel gripper, 3-finger gripper to handle waste drums safely (formclose)• Further hydraulically driven grippers like concrete crushers, scrab gripper or log gripper or other robust tongs and grippers • Excavator shovel and bucketAll equipment is coupled to the arm by means of a universal tool flange, whereby hydraulic connections are coupled inside the tool flange. Force Reflecting-Manipulators stay plugged to their umbilical cables on the tool support unitOptionally the above tools can be set on a (mobile) tool support unit.Detailed data sheets for the various types of equipment are available.Manufacturertele rob Gesellschaft fuer Fernhantierungstechnik mbH Vogelsangstrasse 8Operational envelope:。
管道机器人总体方案设计机械类的

摘要管道运输在我国运用比较普遍,管道长期处于压力大的恶劣环境中,受到水、油混合物、硫化氢等有害气体的腐蚀。
这些管道受蚀后,管壁变薄,容易产生裂缝,造成漏油的问题,存在重大安全生产隐患和济济损失。
因此研究工程应用中的管道机器人具有很高的实用价值和学术价值。
根据这些问题,我们设计一种新的行走机构并分析了其总体机械结构。
本文进一步介绍了当前国内外的管道机器人的发展现状并提出了一种新的管内行走机构。
它利用一个电机同时驱动均布在机架上并与管内壁用弹簧力相封闭的六个行进轮,从而实现了可以轴向直进全驱动的管内行走。
接着本论文重点对直进轮式管道机器人的运动机理和运动特征进行了分析和介绍。
根据管道机器人的设计要求选择电机,介绍了电机选择过程,对其中关键的机械部件如蜗轮蜗杆传动部件、齿轮等进行了设计。
该机器人具有较大的承载能力,可以在较高的速度下实现连续移动,由于该机构采用弹性装置支撑,所以该机构的管径适应性增大,是一种具有实用价值的移动机构形式。
关键词:管道机器人;行走机构;弹性装置AbstractIn our country, pipeline transportation is very universal, and pipeline is in high pressure circumstance. Because pipes are corroded by the water, the oil mixture, the hydrogen sulfide, the noxious gas corrosion and so on. When these pipelines were corroded, their walls would become thin and result in cracks and oil leak, there is safety incipient fault in production and economic loss. So the key technology and further research development trend of in-pipe robot are discussed.According to these problems, we designed a new mobile mechanism and analyzed its machine structure. In this paper, the current states of in-pipe robot are described and a new type of mobile robot mechanism moving in pipe is presented. It uses two motor to drive six wheels which distribute symmetrically on the robot body and a wheels are pushed on the wall of pipe by spring force,so that the six driving wheels move along the axis of pipe. This kind of mobile robot mechanism has high efficiency,simple structure and easy to manufacture and to mount.Then the papers focus on direct pipeline into the wheeled robot's movement and the movement of an analysis and presentation. According to the pipeline robot design requirements choose Motors, introduced the motor selection process, of which the key mechanical components such as worm transmission parts, such as a gear design. The robot with the larger carrying capacity, can achieve higher speeds for mobile, as the agencies adopt a flexible device support, the agency increased the diameter of adaptability, is a kind of practical value in the form of body movement.Keywords: In-pipe Robot; Mobile mechanism; Flexible device目录摘要 (I)Abstract ........................................................................................ I I 1绪论 (IV)1.1本课题的研究目的和意义................................ 错误!未定义书签。
- 1、下载文档前请自行甄别文档内容的完整性,平台不提供额外的编辑、内容补充、找答案等附加服务。
- 2、"仅部分预览"的文档,不可在线预览部分如存在完整性等问题,可反馈申请退款(可完整预览的文档不适用该条件!)。
- 3、如文档侵犯您的权益,请联系客服反馈,我们会尽快为您处理(人工客服工作时间:9:00-18:30)。
A SIMPLE ARCHITECTURE FOR IN-PIPE INSPECTION ROBOTS Mihaita HORODINCA, Ioan DOROFTEI, Emmanuel MIGNON, André PREUMONTActive Structures LaboratoryUNIVERSITE LIBRE DE BRUXELLESAv. F. D. Roosevelt 50, cp 165/42, Brussels, BelgiumPhone: (32)2-6504663 Fax: (32)2-6504660e-mail: andre.preumont@ulb.ac.beAbstract: The paper presents an original robot architecture for in-pipe inspection. Therobot consists of two parts articulated with a universal joint. One part is guided along thepipe by a set of wheels moving parallel to the axis of the pipe, while the other part isforced to follow an helical motion thanks to tilted wheels rotating about the axis of thepipe. A single motor is placed between the two bodies to produce the motion. All thewheels are mounted on a suspension to accommodate for changing tube diameter andcurves in the pipe. The robot is autonomous and carries its own batteries and radio link.Four different prototypes have been constructed for pipe diameters of 170, 70 and 40mm, respectively. For smaller diameters, the batteries and the radio receiver may beplaced on an additional body attached to the others. The autonomy of the prototypes isabout 2 hours. This architecture is very simple and the rotary motion can be exploited tocarry out scrubbing or inspection tasks.Keywords: Autonomous mobile robot, In-pipe inspection, Helical motionIntroductionPipe inspection robots have been studied for a long time, and many original locomotion concepts have been proposed to solve the numerous technical difficulties associated with the change in pipe diameter, curves and energy supply. Although an exhaustive review of the literature is impossible due to the limited space available, a few broad categories can be identified:(i) For small size, many projects follow the earthworm principle consisting of a central partmoving axially while the two end parts are provided with blocking devices connectedtemporarily to the pipe. Pneumatic versions of this concept have been proposed (e.g. [1]),but they require an umbilical for power. For smaller diameter (10 mm or less), apiezoelectric actuation has been considered, according to the inchworm principle, oraccording to an inertial locomotion driven by a saw-tooth wave voltage [2], or usingvibrating fins with differential friction coefficients [3].(ii) For medium size piping, classical electromechanical systems have been proposed with various architectures involving wheels and tracks, with more or less complicatedkinematical structures, depending on the diameter adaptability and turning capability (e.g.[4,5]).(iii) For large pipes, walking tube crawlers have also been proposed [6].The four mobile robots presented in this paper belong to the second category, they span a tube diameter from 40 to 170 mm. The design results from an attempt to reduce the electromechanical complexity through the use of a single actuator to achieve mobility along the tube. Although our study can be regarded as an independent effort, it appears that the “spiral wheel” strategy was explored before [7].ArchitectureThe robot consists of two main parts, a stator and rotor, connected by an active joint including a D.C. motor with reducer and, in some cases, a universal joint. The stator is equipped with a set of wheels which allow the motion parallel to the tube axis; the rotor is equipped with wheels tilted with a small angle with respect to the plane perpendicular to the tube axis (Fig. 1. a). In this way, the stator is constrained to move along the tube axis while the wheels of the rotor can only move along helical trajectories, and the rotation of the rotor with respect to the stator generates the axial motion. The relation between the axial velocity v of the robot and the rotation velocity ωof the rotor is:αωtg R v ⋅⋅=where R is the radius of the pipe and α is the tilting angle of the wheels of the rotor, taken as 10° throughout this project. The wheels on the stator and on the rotor must be located in order to guarantee the overturning stability, to assure a sufficient contact force between the robot and the pipe, to adapt to small changes in the pipe diameter and obstacles, and to allow travelling in curved pipes. For the larger robot (D-170), the robot is rigidly connected to the axis of the motor and three pairs of wheels on both the rotor and the stator are sufficient for stability. For smaller diameters, curved pipes require more degrees of freedom, because the connection between the rotor and the stator does not stay on the tube axis during turning. This is achieved with a universal joint provided with some axial backlash along the two axes of the joint; overturning stability requires the doubling of the number of wheels on the stator.Two-body architecture for larger diameter (D-170) (b) Three-body architecture for small diameter (D-40).(a) (b)For diameter above 70 mm, the robot is provided with 9 batteries (AA NiCd 600 mAh) which are distributed around the motor on the stator. Tests have shown that they give a reasonable autonomy of the order of 2 hours. For smaller diameters, this configuration is no longer possible and the robot is made of three bodies separated by two universal joints (Fig. 1. b): the first one consists of the rotor with the tilted wheels; the second one includes the motor and reducer, and the third one is the stator with the axial wheels, the energy supply and the telecom.(a)(a) The motor and the batteries are mounted on the stator.(b) The motor and batteries are mounted on the rotor.(a) (b) (c) (d)Figure 3: HELI-PIPE family portrait. (a) D-170, (b) D-70/1, (c) D-70/2, (d) D-40Two design alternatives have been investigated for a diameter of 70 mm (Fig. 2). In the first one, the motor and the batteries are mounted on the stator while in the second one they are mounted on the rotor; this second alternative is not acceptable if the robot is used with a tether for power supply. Table1 gives the main characteristics of the various robots; by “payload”, it is meant the maximum allowed axial force in addition to the weight when the robot is moving upwards in a vertical position.References[1] C. Anthierens, C. Prelle, A., Jutard, M. Bétemps, “Pneumatic Actuated Microrobot for In-Pipe Locomotion”, 4th Japan-France / 2nd Asia-Europe Congress on Mechatronics, Kitakyushu, Japan, 6-8 october, 1998.[2] H. Nishikawa, T. Sasaya, T. Shibata, T. Kaneko, N. Mitumoto, S. Kawakita and N. Kawahara, DENSO CORPORATION, Japan, “In-Pipe Wireless Micro Locomotive System”, in Proc. International Symposium on Mechatronics and Human Science (MHS ’99), Nagoya, Japan, Nov. 24-26,1999.[3] S. Aoshima , T. Tsujimura, T.,Yabuta , “A Miniature Mobile Robot Using Piezo Vibration for Mobility in a Thin Tube” Transactions of ASME, Journal of Dynamic Systems, Measurements and Control, Vol. 115, pp. 270-278, June 1993.[4] K. Suzumori, T. Miyagawa, M. Kimura, Y. Hasegawa, “Micro Inspection Robot for 1-in Pipes” in IEEE/ASME Transactions on Mechatronics, vol. 4, No. 3, pp. 286-292. September 1999.[5] S. Hirose, H. Ohno, T. Mitsui, K. Suyama, “Design of In-Pipe Inspection Vehicles for ø25, ø 50, ø 150 Pipes”, Journal of Robotics and Mechatronics 12, 3, pp. 310-317, 2000.[6] F. Pfeiffer, T. Rossmann, “Control of a Tube Crawler”, Proceedings of the Fourth International Conference on Motion and Vibration Control, Movic’ 98,Zurich, 1998, pp. 889-894, Vol. 3, Switzerland, August 25-28.[7] JGC Corporation, “Inspection Robots in Nuclear Power Plants” Robotics in Nuclear Facilities, Special issue for the exhibition of the 11th International Conference on Structural Mechanics in Reactor Technology (SMIRT II), Tokyo, August 1991.。