滑动轴承计算
滑动轴承间隙计算

滑动轴承间隙计算
滑动轴承的间隙计算方法可以根据轴承的类型和使用要求而有所不同。
以下是一种常见的间隙计算方法:
1. 确定滑动轴承类型:常见的滑动轴承类型有径向滑动轴承和推力滑动轴承。
根据具体的使用要求选择相应的轴承类型。
2. 确定负荷条件:根据实际应用中的负荷条件,包括径向负荷和推力负荷,确定轴承的工作负荷。
3. 计算轴承间隙:根据轴承的类型和工作负荷,使用滑动轴承间隙计算公式计算轴承的间隙。
- 对于径向滑动轴承,一般采用以下公式计算轴承间隙:间隙= ε × √(负荷/ (π × d × L × μ))
其中,ε为系数(一般为0.2-1.0),d为轴承内径,L为轴承长度,μ为润滑油的黏度。
- 对于推力滑动轴承,一般采用以下公式计算轴承间隙:间隙= ε × √(负荷/ (π × d × L × μ))
其中,ε为系数(一般为0.2-1.0),d为轴承内径,L为轴承长度,μ为润滑油的黏度。
4. 根据实际要求调整间隙:根据实际应用要求,对计算得到的间隙进行调整。
一般来说,间隙过小会导致润滑不良,间隙过大则会导致轴承的振动和松动。
需要注意的是,以上的计算方法只是一种常见的方法,实际应用中还需要考虑其他因素,如温度、工作速度等。
最好咨询专业的轴承制造商或工程师来进行具体的间隙计算。
滑动轴承实用标准尺寸与公差
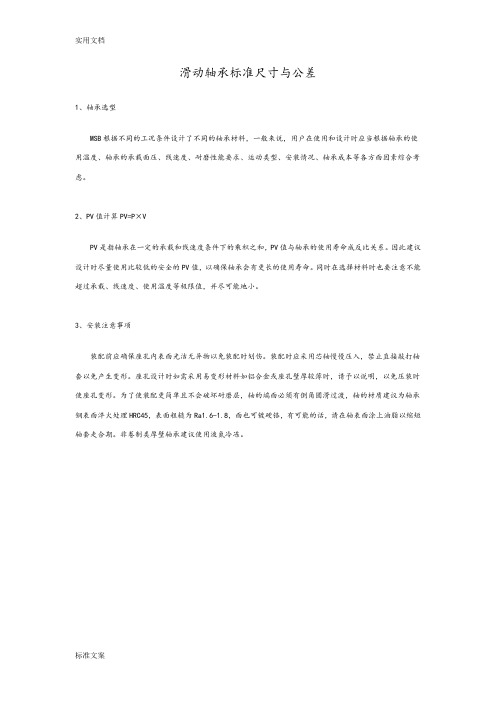
滑动轴承标准尺寸与公差1、轴承选型MSB根据不同的工况条件设计了不同的轴承材料,一般来说,用户在使用和设计时应当根据轴承的使用温度、轴承的承载面压、线速度、耐磨性能要求、运动类型、安装情况、轴承成本等各方面因素综合考虑。
2、PV值计算PV=P×VPV是指轴承在一定的承载和线速度条件下的乘积之和,PV值与轴承的使用寿命成反比关系。
因此建议设计时尽量使用比较低的安全的PV值,以确保轴承会有更长的使用寿命。
同时在选择材料时也要注意不能超过承载、线速度、使用温度等极限值,并尽可能地小。
3、安装注意事项装配前应确保座孔内表面光洁无异物以免装配时划伤。
装配时应采用芯轴慢慢压入,禁止直接敲打轴套以免产生变形。
座孔设计时如需采用易变形材料如铝合金或座孔壁厚较薄时,请予以说明,以免压装时使座孔变形。
为了使装配更简单且不会破坏耐磨层,轴的端面必须有倒角圆滑过渡,轴的材质建议为轴承钢表面淬火处理HRC45,表面粗糙为Ra1.6-1.8,面也可镀硬铬,有可能的话,请在轴表面涂上油脂以缩短轴套走合期。
非卷制类厚壁轴承建议使用液氮冷冻。
SF-1标准轴承尺寸及配合公差SF-1翻边轴承尺寸及配合公差表SF-2标准轴承尺寸及配合公差表JDB标准轴套尺寸FZ钢球保持架标准尺寸公差滑动轴承与座孔的装配SF轴承在装配前宜先用煤油或柴油清洗干净,然后在机油内浸油、沥干。
轴承与座孔装配时,即要保证轴承在座孔中不发生转动和轴向移动,要使轴承外表面与座孔充分接触,一般应保证接触面积大于70%以上,以利于承受载荷和传导摩擦热,SF轴承内表面是自润滑塑料,外表面是铜背,钢对钢的摩擦系数比钢对塑料的摩擦系数大,因此采用较轻盈配合,既保证使用时衬衫套不会在座孔内发生相对移动,又不会使衬套外径过大致使衬套内孔变形较大。
对于工作压力较高的场合为避免轴套走外圆,推荐用以下二方法:1、加大轴套外径尺寸,内孔变形用较正芯棒校正。
2、安装时,座孔涂ZY801厌氧胶,增强轴套与座孔的结合强度。
机械设计 10-5 液体动压滑动轴承的设计计算
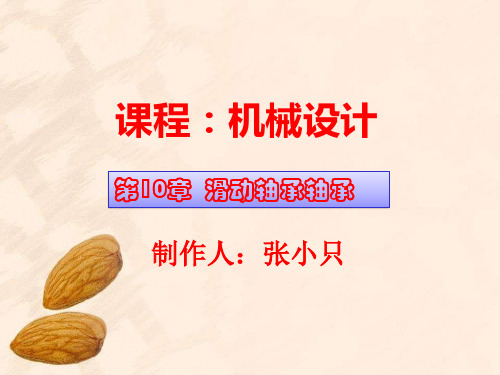
Uh0 2
油膜压力 最大处的 油膜厚度
p 6 ηU 3 [ h( x ) h0 ] x h ( x )
——一维雷诺方程
p 6 ηU 3 [h( x ) h0 ] x h ( x )
U
U
F
U
h0 h
形成动压油膜的必要条件:
1.两表面必须构成楔形; 2.两表面必须有一定的相对速度, 使大口带入油,小口带出油; 3.两表面间必须连续充满润滑剂。
五、轴承的热平衡计算
热平衡条件:摩擦功耗产生热量=轴承的散热量
摩擦功(发热量): H
fFv
ti
散热量: 润滑油带走的热量: H1 Qcto ti
轴承表面散发的热量: H 2 a sπ dBto ti
一次积分: 求任意位置 处油膜压力p
a
F
dp p ( )d 1 d
1
求单位轴承宽度承载力py
2
1
2
py = p r d cos(180o-( + a))
B/2
B/2
F =
z
z
B 2 B 2
2z 2 C '[1 ( ) ] py dz B
z y
y
U( h - y) y (h y ) p u h 2 x
剪切流
压力流
F
p 0 x
U
油压 p 的分布
x
U
h
y
2 润滑油的流量:z=1
Q
h
0
U (h y ) y (h y ) p ]dy udy 0 [ h 2 x
h
Uh h p 2 12 x
完整的轴承选型计算方法
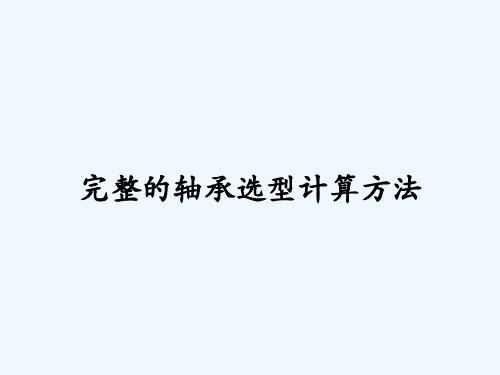
轴瓦得材料
减摩性:材料副具有较低得摩擦系数。 耐磨性:材料得抗磨性能,通常以磨损率表示。 抗咬粘性(胶合):材料得耐热性与抗粘附性。 摩擦顺应性:材料通过表层弹塑性变形来补偿轴承滑动表面初始配合 不良得能力。
嵌入性:材料容纳硬质颗粒嵌入,从而减轻轴承滑动表面发生刮伤 或磨粒磨损得性能。
磨合性:轴瓦与轴颈表面经短期轻载运行后,形成相互吻合得表面形 状与粗糙度得能力(或性质)。
§7-4 非液体摩擦滑动轴承得设计
一、失效形式
1、磨损
导致轴承配合间隙加大,影响轴得旋转精度,甚至使 轴承不能正常工作。
2、胶合
高速重载且润滑不良时,摩擦加剧,发热多,使轴承上 较软得金属粘焊在轴颈表面而出现胶合。
二、设计准则
B
Fr
1、限制轴承得压强 p :
d
目得 — 防止轴瓦过度磨损。
平均压强: p Fr [ p] MPa dB
(5)、根据调心性能 轴刚性差、轴承座孔同轴度差或多点支承
—— 选调心轴承( “1” 类 或 “2” 类 );
§11-5 滚动轴承得寿命计算
一、滚动轴承得载荷分析
Qi
各滚动体上得受力情况如何?
当轴承仅受到纯轴向力 Fa 作用时:
Fa
载荷由各滚动体平均分担,即:
Qi = Qj
Qj
当轴承仅受到纯径向力 Fr 作用时: 接触点产生弹性变形,内圈下沉δ,
此外还应有足够得强度与抗腐蚀能力、良好得导热性、工艺性与经 济性。
常用轴瓦材料有: 金属材料 —轴承合金(巴氏合金、白合金)就是由锡、铅、锑、铜等组成得合金 —铜合金 分为青铜与黄铜两类。 —铸铁 有普通灰铸铁、球墨铸铁等。
粉末冶金材料 —由铜、铁、石墨等粉末经压制、烧结而成得多孔隙轴瓦材料。
环宇轴瓦滑动轴承选型计算手册
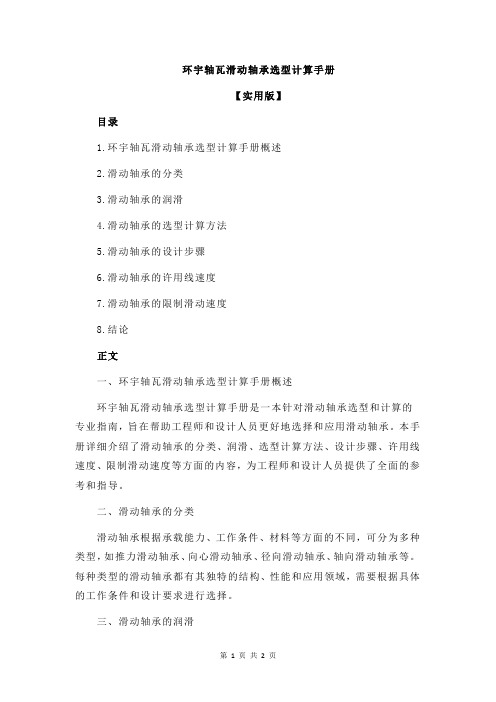
环宇轴瓦滑动轴承选型计算手册【实用版】目录1.环宇轴瓦滑动轴承选型计算手册概述2.滑动轴承的分类3.滑动轴承的润滑4.滑动轴承的选型计算方法5.滑动轴承的设计步骤6.滑动轴承的许用线速度7.滑动轴承的限制滑动速度8.结论正文一、环宇轴瓦滑动轴承选型计算手册概述环宇轴瓦滑动轴承选型计算手册是一本针对滑动轴承选型和计算的专业指南,旨在帮助工程师和设计人员更好地选择和应用滑动轴承。
本手册详细介绍了滑动轴承的分类、润滑、选型计算方法、设计步骤、许用线速度、限制滑动速度等方面的内容,为工程师和设计人员提供了全面的参考和指导。
二、滑动轴承的分类滑动轴承根据承载能力、工作条件、材料等方面的不同,可分为多种类型,如推力滑动轴承、向心滑动轴承、径向滑动轴承、轴向滑动轴承等。
每种类型的滑动轴承都有其独特的结构、性能和应用领域,需要根据具体的工作条件和设计要求进行选择。
三、滑动轴承的润滑润滑是滑动轴承正常工作和延长使用寿命的关键。
滑动轴承的润滑方式主要有油润滑、脂润滑和固体润滑等。
选择润滑方式时,需要考虑轴承的工作环境、负荷、转速等因素,以确保润滑效果和轴承的性能。
四、滑动轴承的选型计算方法滑动轴承的选型计算主要包括轴承类型的选择、轴承尺寸的选择、轴承的承载能力计算等。
在选型计算过程中,需要根据工作条件、设计要求和轴承性能参数等因素,进行综合分析和比较,以确保选择的轴承能够满足工作要求。
五、滑动轴承的设计步骤滑动轴承的设计步骤主要包括确定轴承结构、选择轴承类型、计算轴承尺寸、校核轴承承载能力等。
在设计过程中,需要根据工作条件、设计要求和轴承性能参数等因素,进行综合分析和比较,以确保设计的轴承能够满足工作要求。
六、滑动轴承的许用线速度许用线速度是指滑动轴承在正常工作条件下允许达到的最高线速度。
选择许用线速度时,需要考虑轴承的工作环境、负荷、转速等因素,以确保滑动轴承在工作过程中的稳定性和寿命。
七、滑动轴承的限制滑动速度限制滑动速度是为了防止滑动轴承在工作过程中因滑动速度过高而引起的磨损。
轴承的摩擦系数及摩擦力矩计算04.03

轴承的摩擦系数
为便于与滑动轴承比较,滚动轴承的摩擦力矩可按轴承内径由下式计算:M=uPd/2
这里,
M:摩擦力矩,
u:摩擦系数,表1
P:轴承负荷,N
d:轴承公称内径,mm
摩擦系数u受轴承型式、轴承负荷、转速、润滑方式等的影响较大,一般条件下稳定旋转时的摩擦系数参考值如表1所示。
对于滑动轴承,一般u=,有时也达。
各类轴承的摩擦系数u
轴承型式摩擦系数u
深沟球轴承
角接触球轴承
调心球轴承
圆柱滚子轴承
满装型滚针轴承
带保持架滚针轴承
圆锥滚子轴承
调心滚子轴承
推力球轴承
推力调心滚子轴承由轴承摩擦引起的轴承功率损失可用以下计算公式得出
NR = 1,05 x 10-4 Mn
其中
NR = 功率损失,W
M = 轴承的总摩擦力矩,Nmm
n = 转速,r/min
电机扭矩公式:T=9550*P/n
T:电机转矩
P:电机功率KW
n:转速r/min。
滑动轴承的计算
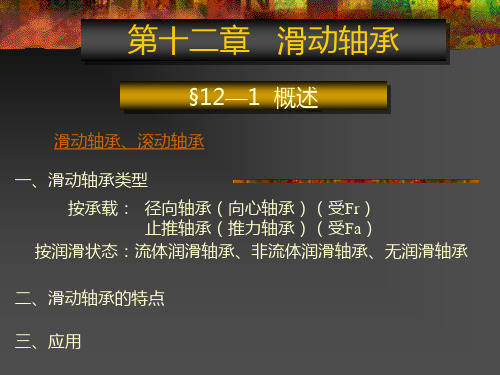
t t m t1 2
先给定tm,再按上式求出Δt,再求t1=35℃~45℃ a) 若t1>>(35~45)℃, 热平衡易建立,则应降低tm,再行计算。 b) 若t1<(35~45) ℃,不易达到热平衡状态→降低粗糙度→重新计算 c) t2>80℃→易过热失效,→改变相对间隙和油的粘度→重新计算
dp f ( , ) d
z
从压力区起始角 1 至任意角 进行积分,得任意角处的压力 再求压力在外载荷方向上的分量
py
将上式在压力区内积分(求和),得到轴承单位宽度上的油膜 承载能力 2Z 2 引入修正系数A,考虑端泄的影响 p y p y A1 B
第十二章
滑动轴承
§12—1 概述
滑动轴承、滚动轴承 一、滑动轴承类型 按承载: 径向轴承(向心轴承)(受Fr) 止推轴承(推力轴承)(受Fa) 按润滑状态:流体润滑轴承、非流体润滑轴承、无润滑轴承 二、滑动轴承的特点 三、应用
§12—2 径向滑动轴承的主要类型
一、整体式径向滑动轴承
如图,由轴承座、整体轴 套、油孔等组成
(1)粘度↓→间隙改变,使轴承的承载能力下降
(2)会使金属软化→发生抱轴事故 热平衡条件:单位时间内 摩擦产生的热量H = 端泄润滑油所带走热量H1 + 轴承散发热量H2
( )P t t 2 t1
f
S Q c ( ) Bd v
(C )
润滑油平均温度tm 为保证承载要求tm<75℃
v
h0
移动件
p max
O
x
移动件
静止件
v
h0
h>h0 y p x >0 p x =0
动载滑动轴承轴心轨迹计算

动载滑动轴承轴心轨迹计算在往复式机械中,作用在连杆大小端及曲轴的滑动轴承上的载荷,无论大小和方向都随时间作周期性变化。
动载轴承由于油膜动压受旋转效应和挤压效应的综合作用,其轴心轨迹是变化的。
在正常的工况下,其轴心轨迹收敛于固定的轨迹曲线。
动载轴承的轴心轨迹的计算可以估计出轴承的失效形式及失效位置,从而在设计时可作有效的预防。
对轴心轨迹的计算,不能用稳态下的计算方法来确定,这是因为其油膜动压涉及挤压效应和旋转效应的综合作用,因而要采用非稳态下的计算方法才能确定。
本文主要采用Holland方法并通过计算机模拟进行计算。
图1 轴承模型示意图1.建立模型在进行轴心轨迹的计算之前,对有限宽的动载轴承作以下假设:(1)轴承的间隙中充满润滑油介质,流动服从雷诺方程,不考虑润滑油的涡动现象;(2)整圆轴承,轴承的轴线和轴颈平行;(3)轴承外表面光整;(4)不考虑温度场变化引起的油粘度变化。
求解轴心轨迹的基本思路如下,在油膜力和载荷互相平衡的情况下(由于轴颈惯性力相对较小,因此可以忽略不计),轴心都会逐渐收敛于一个确定的轨迹,所以可在轴颈的任意初始位置上根据力平衡关系确定轴心变化速度。
由此得到经过一微小时间间隔后的新的轴颈位置。
从这个位置再确定新的轴心变位速度,又得到另一时间间隔后的另一个轴颈位置。
如此不断进行下去,直到收敛于一个封闭的轴心轨迹。
分析动载轴承轴心轨迹的具体方法有Holland法、和Hahn法和移动率(Mobility)法。
为了克服对动载Reynolds方程在数学上求通解的困难,采用Holland法进行分析。
图1为物理模型的受力关系示意。
图中,F为动载荷,γ为动载荷与Y轴的方向角,δ为偏位角,Ωb为轴承角速度,Ωj为轴颈角速度,轴颈中心O j绕轴承中心O b的回转变位角速度为δ’,偏心率随时间的增长速率为ε’,R为轴承的内径。
P D是由轴颈和轴承相对油楔的旋转角速度引起的油膜动压,P V是由轴颈与轴承之间的挤压引起的油膜动压,称为挤压油压。
- 1、下载文档前请自行甄别文档内容的完整性,平台不提供额外的编辑、内容补充、找答案等附加服务。
- 2、"仅部分预览"的文档,不可在线预览部分如存在完整性等问题,可反馈申请退款(可完整预览的文档不适用该条件!)。
- 3、如文档侵犯您的权益,请联系客服反馈,我们会尽快为您处理(人工客服工作时间:9:00-18:30)。
滑动轴承计算第十七章滑动轴承基本要求及重点、难点滑动轴承的结构、类型、特点及轴瓦材料与结构。
非液体摩擦轴承的计算。
液体动压形成原理及基本方程,液体动压径向滑动轴承的计算要点。
多油楔动压轴承简介。
润滑剂与润滑装置。
基本要求:1) 了解滑动轴承的类型、特点及其应用。
2) 掌握各类滑动轴承的结构特点。
3) 了解对轴瓦材料的基本要求和常用轴瓦材料,了解轴瓦结构。
4) 掌握非液体摩擦轴承的设计计算准则及其物理意义。
5) 掌握液体动压润滑的基本概念、基本方程和油楔承载机理。
6) 了解液体摩擦动压径向润滑轴承的计算要点(工作过程、压力曲线及需要进行哪些计算)。
7) 了解多油楔轴承等其他动压轴承的工作原理、特点及应用。
8) 了解滑动轴承采用的润滑剂与润滑装置。
重点:1) 轴瓦材料及其应用。
2) 非液体摩擦滑动轴承的设计准则与方法。
3) 液体动压润滑的基本方程及形成液体动压润滑的必要条件。
难点:液体动压润滑的基本方程及形成液体动压润滑的必要条件。
主要内容:一:非液体润滑轴承的设计计算。
二:形成动压油膜的必要条件。
三:流体动压向心滑动轴承的设计计算方法,参数选择§17-1概述:滑动轴承是支撑轴承的零件或部件,轴颈与轴瓦面接触,属滑动摩擦。
一 分类:1. 按承载方向径向轴承(向心轴承。
普通轴承)只受. 推力轴承: 只受 组合轴承: ,. 2. 按润滑状态 液体润滑: 摩擦表面被一流体膜分开(1.5—2.0以上)表面间摩擦为液体分子间的摩擦 。
例如汽轮机的主轴。
rF aF a F rF m非液体润滑:处于边界摩擦及混合摩擦状态下工作的轴承为非液体润滑轴承。
关于摩擦干:不加任何润滑剂。
边界:表面被吸附的边界膜隔开,摩擦性质不取决于流体粘度,与边界膜的表面的吸附性质有关。
液体:表面被液体隔开,摩擦性质取决于流体内分子间粘性阻力。
混合:处于上述的混合状态.相应的润滑状态称边界、液体、混合、润滑。
3.液体润滑按流体膜形成原理分:1)流体动压润滑轴承:靠摩擦表面几何形状相对运动并借助粘性流体动力学作用产生力。
平衡外载。
2)流体静压润滑轴承:靠外部提供压力流体,借助流体静压力平衡外载荷。
但开始启动时处于干摩擦,逐渐转换的,表明滑动轴承摩擦状态转化过程滑动轴承摩擦特性曲线。
由德国科学家Stribeck通过实验做出的。
3.按润滑材料分液体润滑轴承(油、水)气体润滑轴承(空气、氦、氮)塑料体润滑轴承(脂、半夜体金属、、) 固体润滑轴承 (、、石墨,玻璃) 自润滑轴承(粉末冶金)二 :主要特点:1.平稳, 可靠, 噪音小,高旋转精度2.承载力大,耐冲击(油膜缓冲阻尼作用),用于高速3.启动阻力大。
§17--2 径向滑动轴承的主要类型整体式:结构简单,低速、载荷不大 , 间歇机器无法调间隙,轴颈只能从端部装入。
剖分式 : 见教材P334图17.1-17.2。
§17—3滑动轴承材料:即轴瓦与轴承衬材料。
一:对材料要求:1. 强度塑性 顺应性 嵌藏性2. 磨合性减摩性 耐磨性磨合性 材料消除表面不平度而使轴瓦表面和轴颈表面相互吻合的性质减摩性:材料具有较低摩擦阻力的性质。
耐磨性:材料具有抵抗磨粒磨损和胶合磨损的性质。
b P n S nI b P nS s m v /303.良好的导热性、工艺性 、经济性。
二:常用材料:1. 材料分类:金属材料粉末冶金材料非金属材料2. 常用材料简介:1) 巴氏合金(轴承合金)、、、合金 ,以、为基础,悬浮锑锡及铜锡的硬晶粒,均匀的分布于基体内,硬晶粒起抗磨作用软基体则增加材料的塑性。
2)轴承青铜:粉末冶金:金属粉末加石墨高压成型再经高温烧制而成的多空隙结构材料。
孔隙率占总体积的15-35%,可预先浸满油或脂,又称含油轴承。
3)塑料:耐水耐酸耐碱,但导热性差耐塑性差。
详见p355表17.1u C n S b P b S n S b P 110P ZCuSn§17—7 滑动轴承的条件性计算用于低速轻载不重要轴承,也用于流体润滑的初算。
非液体润滑轴承计算缺乏系统理论,用一些条件性的验算来进行计算。
失效形式:磨损(主要)无合适公式胶合(次要)点蚀(更次要)一、径向轴承。
1. 限制平均压强P 即限制磨损失效。
(17.2)F------ 轴承径向载荷----轴颈直径及有效宽mm----许用比压Mpa 表17.4 P3422.限制值即限制胶合因发热量有摩擦功率损失而来,与功率损失成正比,因而限制值就可以限制发热量,进而限制了胶合。
发热量[]P B d F P ≤⋅=N dB []P pv pv pv v p d B f s m v F f H ⋅⋅⋅⋅=⋅⋅=)/(式中f —摩擦系数; F —力(); —速度上式中B 、d 一定,f 一定,为变值、可控制此项即可限制胶合失效。
(17-3)3.限制滑动速度:有时由于安装误差或轴的弹性变形,使轴径与轴承局部接触,此时即使平均比压较小,及皆小于许用值,但也可能由于轴颈圆周速度较高,而使轴承局部过度磨损或胶合。
因此安装精度较差、轴的弹性变形较大和轴承宽径比较大时,还需验算轴径的圆周速度。
(17-4)材料的pv 及v 见教材表17.4二、推力轴承(见教材P342页,略)§17—8液体动压润滑的基本方程用润滑油把摩擦表面完全分割开的摩擦成为液体摩擦,此时摩擦性质取决于润获的黏度,而与两摩擦表面间的材料无关。
一:润滑油粘度N v pv []s m Mp pv B n F dn Bd F pv a /2000100060⋅≤⋅⋅=⨯⋅=πv p p pv v []s m v dnv /100060≤⨯=π1.润滑油在运动过程中产生内部摩擦阻力的性质叫粘性,粘性大小称粘度。
粘度是表征流体流动中内摩擦性能的。
2.内摩擦阻力的计算:图是为两块平行平板被一层不可压缩的润滑油隔开,下板静止加压力拖动上板,润滑油做层流流动。
沿y 坐标轴油层将以不同速度u 在移动。
流动时内摩擦阻力阻止层流流动,此力称流体内摩擦阻力。
关于内摩擦阻力的大小:速度位置速度梯度,即速度在垂直方向上的变化率。
由理论分析及试验结果剪应力与速度梯度成正比。
因方向取负,负号表示随的增大而减小,当温度、压力一定时,为一常数称为动力粘度。
上述方程称牛顿方程或流体内摩擦定律2. 粘度单位 τv τy u∂∂∝τy u∂∂=ητy u y η1) 动力粘度(绝对粘度):单位为动力学单位,称动力粘度。
国际单位(工程单位):巴斯()长宽高各为1m 的液体如使两平行面a .b 发生1m/s 相对滑动速度所需的力为1N.这样的液体粘度为 物理单位 泊或2) 运动粘度 动力粘度与同温度下该液体的密度的比值称运动粘度。
国际单位:物理单位:斯(Stock ),s Pa ⋅2/1m s N ⋅)(poise P s Pa cP P cm s dyn ⋅===⋅1.0(1001/12厘泊)cPP s Pa 1000101==⋅s m m Kg m ss m Kg m Kg m s N s m /)/(/(2322322=⋅⋅=⋅==ρηγcSt s cm cm g s s cm g cm g cm s dyn St 100/1/)/(/1/123222==⋅⋅=⋅==ρη蒸馏水在20.3摄氏度时运动粘度为1新标准规定机械油牌号为40摄氏度时运动粘度的厘斯数,温度上升,粘度下降;压力升高,粘度上升,超过100Mpa 时压力升高,粘度明显增加。
二:流体动压润滑的形成(润滑油是怎样起作用的,压力如何产生的)(a ) 如图17.14.b 所示:板b 静止,板a以速度v 向右移动,板上无载荷,液体速度图呈三角形分布,板ab 间带进油量等于带出油量,板间油量保持不变,板a 不会下沉。
(b ) 板a 承载,油向两侧溢出,于是板a下沉,不能承载。
cSt(c)如图17.14 a所示,ab板不平行,板间隙沿运动方向由大到小呈收敛的楔形,板a 承受载荷P。
板a运动使两端流体速度图似乎应如虚线所示的三角形分布。
如此进油多出油少,由于实际上液体不可压缩,必将在间隙内拥挤形成压力,迫使进口端的速度图向内凹,出口端速度图形向外凸,使进口油量等与出口带出的油量。
间隙内液体形成压力,即由向上的压力与外载荷平衡,说明在间隙内形成了动压油膜。
归纳起来:获得流体动压润滑的必要条件是:1)相对运动两表面间,必须有沿运动方向由大变小的楔形间隙;2)两表面必须有一定的相对速度3)润滑油有一定粘度,且供油充足。
进一步观察径向轴承形成动压油膜的过程:(1)如图17.16 a所示,制造时轴承孔直径D 大于轴径d,二者之差称直径间隙。
静止时轴处于轴承孔最下方稳定位置。
(2)轴径开始转动时,轴承与轴径为金属相接触,为金属间直接相摩擦。
轴承对轴径的摩擦力方向与轴径表面圆周速度方向相反,迫使轴径向左移动而偏移。
如图17.16 b所示(3)当轴径速度继续增加时,楔形间隙内形成的油膜将轴径推开而与轴承脱离接触,但此情况不持久,因为油膜内各点内压力的合力有向右推动轴径的分力存在,因而轴径向右移动。
(4)随转速的增大,轴径表面圆周速度增大,带入油楔内油量逐渐加多,则金属接触面被润滑油分隔开的面积增大,因而摩擦阻力下降。
于是轴径又向右下方移动(油膜内各点压力的合力有向右推动轴径的分力存在)。
当转速增加到一定大小达到工作转速时,已形成足够油量将金属接触面分开,轴承开始按液体摩擦状态工作。
油压如何计算?通过雷诺方程解决。
三:流体动压润滑的基本方程------雷诺方程如图17.13所示两刚体被润滑油分开,移动件以速度v沿x方向移动,另一刚体静止不动。
假设:1. z 方向无穷大,(润滑油在此方向不流动);2. 润滑油做层流流动,油不可压缩;3. 润滑油粘度不随温度压力变化;4. 忽略油层重力和惯性;5. 由于工作表面吸附牢固,表面油分子随工作表面一同运动或静止。
取单元微体分析,p 为单位压力。
因沿z 方向不流动,因而前后面压强相等。
作用于微元体两侧压力及作用于微元体上下两面压力为及dz pdy ⋅dz dy dx x p p ⋅∂∂+)(dz dx ⋅⋅τdz dx dy dydp ⋅+)(τ分析x 方向受力,因为等速运动,所以受力平衡:代入牛顿定律得:得反过来分析一下平行板的情况: 如图,速度分布为三角形 ,即不能产生压力来支撑外载荷(平行油膜各处油压差等于入口及出口的油压)。
上式积分:再积分:利用边界条件,当y=0时(移动件)得=当时(静止件)得导出:∑=0x 0)()(=⋅∂∂+-⋅⋅+⋅∂∂+-⋅⋅dz dx dy ydz dx dz dy dx x p p dz dy p τττ0=∂∂-∂∂-dydxdz ydxdydz x p τy x p ∂∂-=∂∂∴τy u ∂∂=ητ22y u x p ∂∂=∂∂η常数=∂∂∴y u 0022=∂∂∴=∂∂x p y u ∴111C y dx dp dy x l y u +=∂∂=∂∂⎰ηη212121)1(C y C y x p dy C y x p u ++∂∂=+∂∂=⎰ηηv u =2C v h y =0=u h v h x p C -∂∂-=211η将、代入原式得利用润滑油连续流动的关系得出任一剖面沿x 方向单位宽度流量:[导出: =u (速度)x 截面积=dz=udy (因为单位宽,所以dz=1)==Vh(a )设以表示油膜中油压最大处的间隙(=0)h v h dx dp h v h x p C v h C h x p u C y C y x p u --=-∂∂-=∴++∂∂=∴++⋅∂∂=212121212112212ηηηη1C 2C )(21)()21(21)21)1(22121h y y x p y h h v v y h v y h x p y x p C y C y x p dy C y x p u -∂∂+-=+-∂∂-⋅∂∂=++⋅∂∂=+⋅∂∂=⎰ηηηηη⎰=h x udy q 0xq udy ⎰-∂∂+-h dy h y y x p y h h V 0)](21)([η2213212232h h x p h x p h h V ∂∂-∂∂+-ηη31212h x p V ∂∂-=ηη0h x p ∂∂此截面上 (b )而式(a )应等于式(b ) (因为流量必相等)== (7—7)此为一维雷诺流体动压润滑方程,是计算流体动压润滑的基本方程,从公式可看出油压变化与粘度、速度、间隙有关,利用此公式可求出油膜上各点压力P ,根据油压分布可算出油膜承载能力。