碳化硅工艺过程简述
碳化硅工艺过程

生产技术一、生产工艺1.碳化硅原理:通过石英砂、石油胶和木屑为原料通过电阻炉高温冶炼而成,主要反应机理是SiO2+3C----SiC+2CO。
碳化硅电阻炉制炼工艺:炉料装在间歇式电阻炉内,电阻炉两端端墙,近中心处是石墨电极。
炉芯体连接于两电极之间。
炉芯周围装的是参加反应的炉料,外部则是保温料。
冶炼时,给电炉供电,炉芯温度上升,达到2600~2700℃。
电热通过炉芯表面传给炉料,使之逐渐加热,达到1450℃以上时,即发尘化学反应,生成碳化硅,并逸出一氧化碳。
随着时间的推移,炉料高温范围不断扩大,形成碳化硅愈来愈多。
碳化硅在炉内不断形成,蒸发移动,晶体长大,聚集成为—个圆筒形的结晶筒。
结晶筒的内壁因受高温,超过2600℃的部分就开始分解。
分解出的硅又与炉料中的碳结合而成为新的碳化硅。
破碎:把碳化硅砂破碎为微粉,国内目前采用两种方法,一种是间歇的湿式球磨机破碎,一种是用气流粉末磨粉机破碎。
我公司已由气流粉末磨碎机代替湿式球磨机破碎。
湿式球磨机破碎时用是用湿式球磨机将碳化硅砂磨成微粉原料,每次需磨6-8小时。
所磨出的微粉原料中,微粉约占60%左右。
磨的时间越长,则微粉所占的比例越大。
但过粉碎也越严重,回收率就会下降。
具体的时间,应该与球磨比、球径给配、料浆浓度等工艺参数一起经实验优选确定。
该方法最大的优点就是设备简单,缺点是破碎效率较低,后续工序较复杂。
雷蒙磨粉机工作原理是:颚式破碎机将大块物料破碎到所需的粒度后,由提升机将物料输送到储料仓,然后由电磁振动给料机均匀连续地送到主机的磨腔内,由于旋转时离心力作用,磨辊向外摆动,紧压于磨环,铲刀与磨辊同转过程中把物料铲起抛入磨辊与辊环之间,形成填料层,物料在磨辊与磨环之间进行研磨。
粉磨后的粉子随风机气流带到分级机进行分选,不合要求的粉子被叶片抛向外壁与气流脱离,粗大颗粒在重力的作用F落入磨腔进行重磨,达到细度要求的细粉随气流经管道进入大旋风收集器,进行分离收集,再经卸料器排出即为成品粉子,气流由大旋风收集器上端回风管吸入鼓风机。
cvd碳化硅工艺流程
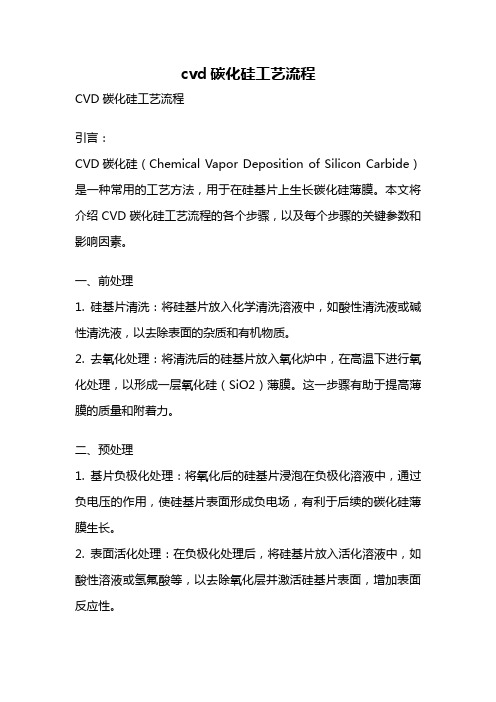
cvd碳化硅工艺流程CVD碳化硅工艺流程引言:CVD碳化硅(Chemical Vapor Deposition of Silicon Carbide)是一种常用的工艺方法,用于在硅基片上生长碳化硅薄膜。
本文将介绍CVD碳化硅工艺流程的各个步骤,以及每个步骤的关键参数和影响因素。
一、前处理1. 硅基片清洗:将硅基片放入化学清洗溶液中,如酸性清洗液或碱性清洗液,以去除表面的杂质和有机物质。
2. 去氧化处理:将清洗后的硅基片放入氧化炉中,在高温下进行氧化处理,以形成一层氧化硅(SiO2)薄膜。
这一步骤有助于提高薄膜的质量和附着力。
二、预处理1. 基片负极化处理:将氧化后的硅基片浸泡在负极化溶液中,通过负电压的作用,使硅基片表面形成负电场,有利于后续的碳化硅薄膜生长。
2. 表面活化处理:在负极化处理后,将硅基片放入活化溶液中,如酸性溶液或氢氟酸等,以去除氧化层并激活硅基片表面,增加表面反应性。
三、碳源供应1. 碳源选择:CVD碳化硅工艺中常用的碳源为甲基三氯硅烷(MTS),其分解产生的甲基自由基可在硅基片表面与硅原子结合形成碳化硅薄膜。
2. 碳源输送:将甲基三氯硅烷通过气体输送系统引入反应室,确保碳源的稳定供应和适量流量控制。
四、生长薄膜1. 反应室控制:将硅基片放入CVD反应室中,并保持一定的反应温度和压力。
通常,反应温度在1000℃至1400℃之间,反应压力在10 Torr至100 Torr之间。
2. 生长碳化硅薄膜:甲基三氯硅烷分解后,甲基自由基与硅基片表面的硅原子结合,逐渐形成碳化硅薄膜。
反应时间通常在几十分钟至几小时之间。
五、后处理1. 薄膜冷却:在生长完碳化硅薄膜后,将反应室温度逐渐降低到室温,以确保薄膜的稳定性和附着力。
2. 气体清洗:将反应室内的气体通过净化系统进行清洗,以去除其中的有害物质和杂质。
3. 薄膜检测:使用表面形貌分析仪、扫描电子显微镜等工具对生长的碳化硅薄膜进行检测,评估其质量、厚度和均匀性。
碳化硅陶瓷制作工艺
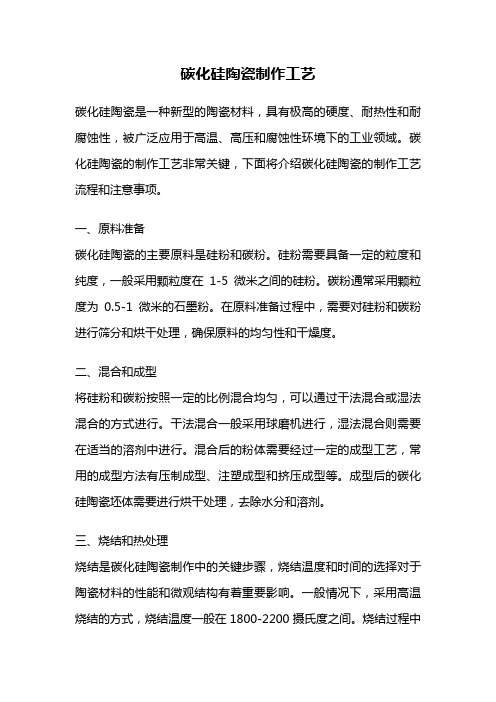
碳化硅陶瓷制作工艺碳化硅陶瓷是一种新型的陶瓷材料,具有极高的硬度、耐热性和耐腐蚀性,被广泛应用于高温、高压和腐蚀性环境下的工业领域。
碳化硅陶瓷的制作工艺非常关键,下面将介绍碳化硅陶瓷的制作工艺流程和注意事项。
一、原料准备碳化硅陶瓷的主要原料是硅粉和碳粉。
硅粉需要具备一定的粒度和纯度,一般采用颗粒度在1-5微米之间的硅粉。
碳粉通常采用颗粒度为0.5-1微米的石墨粉。
在原料准备过程中,需要对硅粉和碳粉进行筛分和烘干处理,确保原料的均匀性和干燥度。
二、混合和成型将硅粉和碳粉按照一定的比例混合均匀,可以通过干法混合或湿法混合的方式进行。
干法混合一般采用球磨机进行,湿法混合则需要在适当的溶剂中进行。
混合后的粉体需要经过一定的成型工艺,常用的成型方法有压制成型、注塑成型和挤压成型等。
成型后的碳化硅陶瓷坯体需要进行烘干处理,去除水分和溶剂。
三、烧结和热处理烧结是碳化硅陶瓷制作中的关键步骤,烧结温度和时间的选择对于陶瓷材料的性能和微观结构有着重要影响。
一般情况下,采用高温烧结的方式,烧结温度一般在1800-2200摄氏度之间。
烧结过程中需要注意控制温度升降速率和保持时间,以避免过烧或不完全烧结。
烧结后的陶瓷坯体需要进行热处理,以提高其硬度和耐热性能。
四、加工和修整烧结后的碳化硅陶瓷坯体需要进行加工和修整,以获得所需的形状和尺寸。
常用的加工方法包括机械加工、电火花加工和激光加工等。
加工过程中需要注意避免过度加工和损坏陶瓷材料的表面质量。
修整是指对陶瓷材料进行表面处理,去除表面的瑕疵和不均匀性,以提高其外观和质量。
五、性能测试和质量控制制作完成的碳化硅陶瓷需要进行性能测试和质量控制。
常用的测试方法包括硬度测试、抗压强度测试、热膨胀系数测试和化学稳定性测试等。
通过这些测试可以评估碳化硅陶瓷的性能和质量是否符合要求。
同时,还需要进行质量控制,包括对原料、工艺和产品的各个环节进行监控和管理,确保产品的一致性和稳定性。
碳化硅陶瓷的制作工艺包括原料准备、混合和成型、烧结和热处理、加工和修整、性能测试和质量控制等多个环节。
碳化硅工艺过程简述

碳化硅工艺过程简述碳化硅(Silicon Carbide, SiC)是一种极具应用潜力的新型半导体材料,具有高温、高电压、高频率和高能量等特性。
碳化硅在电力电子、光电子、能源和材料等领域具有广泛的应用前景。
碳化硅工艺过程是制造碳化硅器件的关键步骤,下面对其进行详细的描述。
剥离硅衬底是将硅衬底从碳化硅薄膜上剥离的过程。
首先,在硅衬底上形成一层释放层,如氧化物或氮化物。
然后,将碳化硅薄膜通过热剥离或化学剥离的方式与硅衬底分离,从而获取自支撑的碳化硅薄膜。
悬浮硅衬底是将碳化硅薄膜转移到另一张辅助衬底上的过程。
通常使用临时性的辅助衬底,如石墨或其他材料,使碳化硅薄膜能够在后续加工步骤中更方便地处理。
表面处理是对碳化硅薄膜表面进行化学处理或物理处理,以提高表面质量和粗糙度。
常见的表面处理方法包括湿法化学处理和干法物理处理。
湿法处理可以使用酸或碱溶液来去除表面的污染物或提高表面平整度。
干法处理可以通过离子轰击、等离子体处理或蒸发沉积等方式改善表面的质量和结构。
薄膜生长是在表面处理后,在碳化硅薄膜上沉积所需的层状材料。
常见的薄膜生长方法包括化学气相沉积(Chemical Vapor Deposition, CVD)、物理气相沉积(Physical Vapor Deposition, PVD)和分子束外延(Molecular Beam Epitaxy, MBE)等。
这些方法可以在高温或低温条件下生长碳化硅薄膜,控制薄膜的厚度和组分。
沉积是将所需的材料通过化学气相沉积或物理气相沉积等方法直接沉积到碳化硅薄膜上。
沉积可以用于制备导电薄膜、隔离层或表面保护层等。
常见的沉积材料包括金属、高介电常数材料和对碳化硅有特殊功能的材料。
刻蚀是通过化学溶液或等离子体等方式将碳化硅薄膜局部去除的过程。
刻蚀是制造碳化硅器件中非常重要的一步,可以用于形成通道、电极或微结构等。
常见的刻蚀方法包括干法刻蚀和湿法刻蚀。
干法刻蚀常使用氧气、氟化物或氯化物等气体,湿法刻蚀则通常使用酸或碱溶液。
碳化硅mosfet工艺制备过程

碳化硅MOSFET工艺制备过程1. 碳化硅简介碳化硅(Silicon Carbide,SiC)是一种半导体材料,具有优异的物理和化学性质,被广泛应用于各种高温、高电压和高频率的电子器件中。
碳化硅MOSFET是一种基于碳化硅材料制备的金属-氧化物-半导体场效应晶体管。
2. 制备过程概述碳化硅MOSFET的制备过程可以概括为以下几个步骤:1.硅衬底制备:选择高质量的硅衬底(Substrate),通常采用氮化硅或者氮化铝作衬底材料。
2.基底表面处理:对硅衬底进行化学处理,去除表面的氧化物和杂质,使基底表面变得干净平整。
3.硅衬底清洗:采用酸碱处理方法对硅衬底进行清洗,去除表面的有机和无机杂质,并提高衬底的电学性能。
4.硅衬底极柱制备:在硅衬底表面通过光刻和化学腐蚀等工艺步骤制备出硅衬底极柱(epi layer),用于形成MOSFET的源极和漏极。
5.氧化层形成:在硅衬底表面形成一层氧化层(Oxide Layer),通常采用湿法或干法氧化方法。
6.金属栅极制备:在氧化层表面通过物理气相沉积(PECVD)或热蒸发等方法,沉积金属薄膜,形成金属栅极(Gate Electrode)。
7.掩膜形成:通过光刻和蒸发等技术,制备出用于定义源极和漏极等结构的金属掩膜。
8.掺杂处理:采用离子注入或物理气相沉积等方法,向硅衬底中引入杂质,形成源极、漏极和通道区域,从而改变材料的导电性质。
9.金属电极制备:沉积金属薄膜并通过光刻和蒸发等工艺步骤制备源极和漏极等电极结构。
10.金属化层制备:通过蒸发和光刻等工艺,制备出金属化层,用于连接MOSFET的各个电极。
3. 制备过程详解3.1 硅衬底制备碳化硅MOSFET的制备过程通常从硅衬底的选择开始。
硅衬底材料应具有良好的晶体质量和电学性能,以确保器件的稳定性和性能。
目前常用的硅衬底材料有氮化硅和氮化铝。
选择合适的硅衬底材料是确保碳化硅MOSFET制备成功的关键。
3.2 基底表面处理硅衬底经过切割和打磨等工艺后,表面可能存在一些氧化物和杂质。
sic 工艺流程

sic工艺流程一、原料准备原料准备是SIC工艺流程的第一步,包括采购和储存高质量的原材料,如碳化硅(SiC)粉末、氮化硼(BN)粉末等。
这些原材料将用于后续的化学气相沉积(CVD)和外延生长等工艺。
二、化学气相沉积(CVD)在SIC工艺中,化学气相沉积是一种关键技术,用于在基底上沉积一层薄膜。
该过程主要涉及将原材料在高温下与惰性气体混合,然后通过化学反应在基底上沉积一层薄膜。
此步骤将多次重复进行,以逐渐增加薄膜的厚度。
三、外延生长外延生长是SIC工艺中另一个重要的步骤,它是在已沉积的薄膜上生长出新的薄膜。
这个过程需要控制温度、压力和气体的流量,以保证新生长的薄膜与基底具有良好的附着力,同时具有所需的晶体结构和电学特性。
四、掺杂掺杂是将杂质引入SIC薄膜中的过程,以改变其导电类型和电学特性。
掺杂的目的是为了调节薄膜的电阻率和迁移率等电学性能。
常见的掺杂剂包括氮(N)、磷(P)和硼(B)等元素。
五、薄膜制备薄膜制备是将SIC粉末通过加热和加压的方式转化为致密的SIC 薄膜。
这个过程通常采用热压法或反应烧结法等工艺。
在制备过程中需要控制好温度、压力和烧结时间等参数,以保证制备出的薄膜具有高的致密度、纯度和结晶质量。
六、刻蚀刻蚀是去除多余的SIC材料并形成所需图案的过程。
刻蚀方法包括干法刻蚀(如等离子刻蚀)和湿法刻蚀(如化学刻蚀)。
根据需要,还可以采用光刻技术来控制刻蚀的图案和深度。
刻蚀后的SIC材料将用于制造各种器件,如二极管、晶体管和集成电路等。
七、热处理热处理是SIC工艺流程中一个重要的步骤,它有助于改善薄膜的质量和性能。
通过热处理可以消除薄膜中的缺陷、提高晶格常数稳定性并降低薄膜内部的残余应力。
同时,热处理还可以促进薄膜与基底之间的附着力,为后续的器件制造提供更好的基础。
八、检测与分析在完成SIC工艺流程后,需要对制备出的薄膜进行检测和分析,以确保其满足设计和性能要求。
检测方法包括光学显微镜观察、扫描电子显微镜(SEM)分析、X射线衍射(XRD)分析以及电学性能测试等。
碳化硅制作工序

碳化硅的制作工序主要包括以下几个步骤:
1. 原料准备:通常使用硅砂和碳粉作为主要原料。
硅砂经过筛选、清洗等处理,以去除杂质。
碳粉可以是木炭、石墨或其他含碳物质。
2. 配料:将硅砂和碳粉按照一定比例混合,以确保最终产品的化学成分符合要求。
3. 反应:将混合好的原料放入高温反应炉中,在一定的温度和压力条件下进行反应。
在这个过程中,硅砂和碳粉会发生化学反应,生成碳化硅。
4. 提纯:反应生成的碳化硅中可能会含有杂质,需要通过提纯步骤去除。
这可以通过物理方法(如浮选、磁选等)或化学方法(如酸洗等)来实现。
5. 粒度调整:根据最终产品的要求,可以对提纯后的碳化硅进行粒度调整。
这可以通过破碎、研磨等方式来实现。
6. 包装:将调整好粒度的碳化硅进行包装,以方便储存和运输。
以上是碳化硅制作的一般工序,具体的生产过程可能会因厂家和产品要求的不同而有所差异。
碳化硅生产工艺流程

碳化硅生产工艺流程碳化硅是一种重要的无机材料,广泛应用于电子、化工、冶金等领域。
其生产工艺流程主要包括原料准备、炉料制备、炭素化反应、物理处理和产品制取等步骤。
一、原料准备碳化硅的主要原料为高纯度的石墨和硅质原料。
石墨一般需要进行氧化、还原等处理,使其纯度达到要求。
硅质原料一般采用高纯度的二氧化硅或硅金属。
同时还需要准备一定量的助熔剂和添加剂,以提高碳化硅的性能。
二、炉料制备将高纯度的石墨和硅质原料按一定比例混合,并加入助熔剂和添加剂。
然后通过粉碎、混合、压制等步骤制备成炉料。
同时,需要进行炉料的筛选和质量检测,确保炉料的均匀性和质量。
三、炭素化反应将炉料装入电阻炉、高频感应炉或电弧炉等反应器中,通过加热至高温下进行炭素化反应。
炭素化反应是指在高温下,石墨碳和硅形成碳化物SiC的反应。
反应温度通常在2000-2500℃之间,反应时间较长,一般需要12-36小时。
在反应过程中,需要控制好反应温度、气氛和反应时间等参数,以确保反应的顺利进行。
四、物理处理炭化反应结束后,需要将反应产物进行冷却和分级处理。
首先将反应产物经过冷却设备冷却至室温。
然后进行粉碎、筛分和磁选等步骤,以得到所需要的粒度和纯度的碳化硅产品。
同时还需要对产物进行质量检测,以确保产品的合格率。
五、产品制取在物理处理后,还需要对碳化硅进行进一步的成型和烧结,以得到所需要的成品。
碳化硅可通过压制、注射成形、蒸汽沉积等工艺制成所需形状的产品。
然后将制好的成品放入烧结炉中,在高温下进行烧结,将碳化硅的颗粒互相结合,形成致密的块体。
烧结温度一般在2100-2300℃之间,烧结时间也较长。
烧结后的产品还需要进行表面处理和质量检测,以提高其性能和质量。
碳化硅生产工艺流程涉及到多个步骤和设备,需要掌握一定的化工和冶金技术,同时还需要严格控制各个环节的工艺参数,确保产品的质量和性能达到要求。
随着技术的不断进步和创新,碳化硅生产工艺也在不断改进和优化,以提高产品的品质和生产效率。
- 1、下载文档前请自行甄别文档内容的完整性,平台不提供额外的编辑、内容补充、找答案等附加服务。
- 2、"仅部分预览"的文档,不可在线预览部分如存在完整性等问题,可反馈申请退款(可完整预览的文档不适用该条件!)。
- 3、如文档侵犯您的权益,请联系客服反馈,我们会尽快为您处理(人工客服工作时间:9:00-18:30)。
碳化硅磨料通常以石英、石油焦炭为主要原料。
它们在备料工序中经过机械加工,成为
合适的粒度,然后按照化学计算,混合成为炉料。
磨料调节炉料的透气性,在配炉料时要加适量的木屑。
制炼绿碳化硅时,炉料中还要加适量的食盐。
炉料装在间歇式电阻炉内。
电阻炉两端是端墙,近中心处有石墨电极。
炉芯体即连于两电极之间。
炉芯周围装的是参加反应的炉料,外部则是保温料。
制炼时,电炉供电,炉芯体温度上升,达到2600~2700℃。
电热通过炉芯表面传给炉料,使之逐渐加热,达到1450℃以上时,即发生化学反应,生成碳化硅,并逸出一氧化碳。
随着时间的推移,炉料高温范围不断扩大,形成的碳化硅也越来越多。
它在炉内不断形成,蒸发移动,结晶长大,聚集成为一个圆筒形的结晶筒。
结晶筒的内壁因受高温,超过2600℃的部分就开始分解。
分解出的硅又与炉料中的碳结合而成为新的碳化硅。
炉自送电初期,电热主要部分用于加热炉料,而用以形成碳化硅的热量只是较少的一部分。
送电中期,形成碳化硅所用的热量所占比例较大。
送电后期,热损失占主要部分。
调整送电功率与时间的关系,优选出最有利的停电时间,以期获得最好的电热利用率。
大功率电阻炉通常选择送电时间在24小时左右,以利作业安排。
在此基础上,调整电炉功率与炉子规格的关系。
电阻炉送电过程中,除了形成碳化硅这一基本反应外,炉料中各种杂质也发生一系列化学的和物理的变化,并发生位移。
食盐亦然。
炉料在制炼过程中不断减少,炉料表面变形下沉。
反应所形成的一氧化碳则弥漫于大气中,成为污染周围大气的有害成分。
停电后,反应过程基本结束。
但由于炉子很大,蓄热量就很大,一时冷却不了,炉内温度还足以引起化学反应,因此,炉表面仍继续有少量一氧化碳逸出。
对于大功率电炉来说,延续的残余反应可达3~4小时。
这时的反应比起送电时的反应来说,是微不足道的。
但因为当时
炉表面温度已经下降,一氧化碳燃烧更不彻底。
从劳动保护角度来说,仍应予以足够重视。
停电后经过一段时间冷却,就可以拆除炉墙,然后逐步取出炉内各种物料。
制炼后炉内的物料,从外到里,构成下列各物层:
(1)未经反应的物料
这部分炉料在制炼时未达到反应温度,因而不起反应,只起保温作用,它在炉中所占的位置叫保温带。
保温带炉料与反应带炉料的配制方法、制炼后该部位炉料的利用方法不尽相同。
有一种工艺方法,在保温带的特定区域内装炉时装以新料,制炼后取出配到反应料中去,这就叫做焙烧料。
若将保温带上未反应的料经再生处理,稍加焦炭及适量木屑,配制成保温料重新利用,就称之为乏料。
(2)氧碳化硅层
该层物料实际上是半反应的料,主要是还未反应的碳和二氧化硅,也有一部分为已经反应成的碳化硅(约占20~50%)。
未反应的二氧化硅和碳,其形态已经发生很大变化,因此不同于乏料。
氧碳化硅层的二氧化硅及碳已不现原来的外貌,两者结合成为灰色或黄色的无定形物料。
但它们结合的很松散,冷却后轻轻一压就会成为粉末。
而乏料中的二氧化硅,其粒度大小与形状都与投炉前差不多,只不过透明度变化了。
炭粉也只是烧结成较大的粒,并除去了挥发分而已。
因此,氧碳化硅层是很容易辨认的。
(3)粘合物层
粘合物层是介于氧碳化硅与无定形物层之间的、粘结很紧的物料,含有较多的铁、铝、钙、镁等杂质,其量若用金属氧化物表示的话。
可达5~10%。
粘合物的物相组成,主要是未反应的二氧化硅、碳和所形成的碳化硅(SiC约占40~60%)及铁、铝、钙、镁的硅酸盐类。
这层物料有时很难与氧碳化硅及无定形物加以分辨。
但如果炉内杂质多时,此层就很分明,特别是在黑碳化硅炉内。
(4)无定形物层
无定形物层主要是立方碳化硅(β-SiC),其主要成分为碳化硅(约占70~90%),还有较多的反应不完全的碳及二氧化硅,而铁、铝、钙、镁等金属氧化物含量合计可达2~5%。
该层物料较松散,很容易弄碎使之成为粉末状。
黑碳化硅炉内的无定形物通常呈黑色,绿碳化硅炉内的无定形物多数为黄绿色,也有在外部呈黑色而向内则逐渐呈灰黄、黄绿色的。
无定形物层一般较均匀。
当所用原料二氧化硅颗粒太粗、焦炭中固定碳太低时,无定形物层有时有较多的小泡状空洞。
(5)二级品碳化硅
该层已经成α-SiC,但结晶较小,很脆弱,杂质也较多,碳化硅含量只有90~95%,还不能作磨料用。
二级品与无定形物外观上很易分辨。
无定形物层β-SiC如粉末状,无光泽,而二级品为六方结晶体,晶面清晰,有光泽,如镜面反光。
二级品与一级品无本质上的差别,在结晶筒上分为二级品层与一级品层,完全是人为地按用途及质量要求划分的。
而上述的其他料层,有些则是物料本质不同,外观差别很大;有些则自然粘结成层。
与无定形物一样,二级品层有时也有小泡状空洞。
(6)一级品碳化硅结晶块
这是电阻炉的主要产品,是粗大的α-SiC结晶,SiC含量在96%以上。
其厚度视炉功率及部位不同为50~450mm不等。
结晶粗大紧密,有黑色的或绿色的。
(7)炉芯体石墨
紧靠结晶筒内壁的是碳化硅分解而成的石墨,其外形仍保持原来碳化硅结晶的样子。
分
解石墨层内侧是原先装进炉内的石墨炉芯体,它又经过一炉次高温,石墨化程度更加完全。
但形态上已与原先装入时有所不同。
两种石墨混合回收,作为下一炉次的炉芯体材料。
如果把碳化硅各层物料按其制炼后在炉内的位置描绘下来。
可以得到如图2-1所示制炼后炉子的剖面图。
上述各层物料的分析数据如表2-1、表2-2所示。
生产过程中,以上各种物料是在电炉的不同作业阶段中取出的。
取出的先后次序有时与上述
次序也不一致,而且也不完全按照上述分类来收集。
通常作业分类是,乏料与一部分氧碳化硅统一作为乏料收集;氧碳化硅的一部分和无定形物、二级品一起收集,笼统称为回炉料。
粘合物有时归入回炉料中收集之,有时选出其中一部分较大块而粘结很紧的,含杂质明显较
多的抛弃之。
取得的一级品结晶块,要经过分级,然后再经过粗碎、细碎、化学处理、干燥与筛分、磁选,制成各种粒度的黑碳化硅磨料和绿碳化硅磨料。
对于微粉来说,还要经过水选过程,
制得W5~W40微粉。