QS9000-1质量体系标准
QS9000品质系统体系
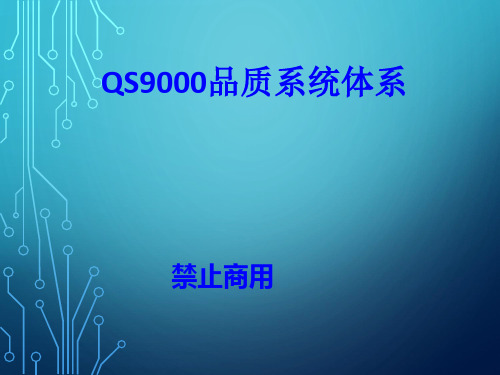
由于全球对QS9000业务需求之殷切,NAASG 工作小组收集执行QS9000的最新之资讯,并特别 纳入北美三大汽车公司的欧洲公司所推荐的改进建 议,于1995年2月发行QS9000第二版,并首次做 全球性发行。
NAASG工作小组在广纳各方意见后,将 QS9000第二部分之汽车业共通性的要求4.2整合, 德国VDA6.1、法国EAQF94及意大利AVSQ94等 标准的差异部分略有加入强化整合性,并于1998 年4月发行第三版,原先的第二版于1999年1月1 日停止使用,有关IASG曾经不定期发行的说明资 料亦停止使用。
(3)通用(GM)的采购诱因
o 每年超过700亿美金的全球采购金额 o 评鉴分数:75-100亚主地区采购网络、100以上全球采购网络
QS9000的核心工具
APQP 产品质量先期策划和控制计划
产品质量策划是一种结构化的方法,用来 确定和制定确保某产品使用权顾客满意所需的 步骤。产品质量策划的目标是促进与所涉及的 每一个人的联系,以确保所要求的步骤按时完 成。有效的产品质量策划依赖于公司高层管理 者对努力达到使顾客满意这一宗旨的承诺。产 品质量 策划有如下的益处:
QS9000对三大汽车厂供应商的好处
(1)三大车厂的限期要求
o GM通用汽车公司:1997.12.31 o FORD福特汽车公司:1998.12.31 o CHRYSLER克莱斯勒公司:1997.7.31
(2)审核效益
o 三大车厂全球共同接受的单一汽车业品质系统 o 单一评鉴(第三者审核)节省人力、时间 o 汽车业的共同沟通语言
QS9000品质系统体系
禁止商用
QS9000简介
1987年以前,美国三大汽车厂通用、福特、克 莱斯勒分别发展了他们各自所期望的品质系统要 求,以应用于供应商品质系统和相关文件方面评 鉴;这些品质系统分别为:
QS9000体系简介资料讲解
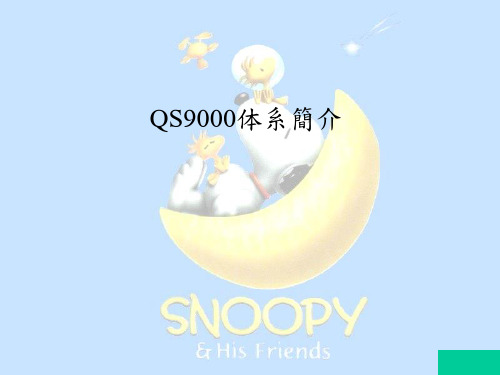
QS-9000質量体系要求
•管制特性(CC&SC)-4.2.3.2
當顧客的設計紀錄標出特殊特性符號時,供方的過 程控制指南上(如FMEAS,控制計划,作業指導書)必 須標上顧客特殊特性符號(或等效符號)以表明對特 殊特性有影響的那些過程步驟.
QS-9000質量体系要求
• 可行性評審-4.2.3.3
QS-9000質量体系要求
• b)确認和記錄與產品﹑過程和質量体系有關的問題
• C)通過規定的渠道﹐采取推荐或提出解決方法 • d)驗証解決辦法的實施效果 • e)控制不合格品的進一步加工﹑交付或安裝﹐直至缺
陷或不滿足要求的情況得到糾正﹒ • f)在闡述QS9000要求時(如選擇特殊特性﹐确定質量
•質量体系-要素4.2 •總則-4.2.1
• 供應商應建立﹑書面訂定﹐並維持其品質制度﹐以确 保產品符合規定的要求﹒
• 供應商應備有品質手冊﹐以涵蓋本國際標准之各項要 求﹒
• 此項品質手冊應包含或對照連接至本品質制度中之各 項書面程序﹐以及网要式列出本品質制度所使用之文 件架構
QS-9000質量体系要求
夾具,所有生產資源與技術之鑒別與獲得. • c)确保設計,製程,安裝,服務,檢驗與測試程序以及使
用文件之相容性. • d)必要時,得更新品質管制,檢驗及測試技術,包括開發
新儀器.
QS-9000質量体系要求
•產品質量先期策划-4.2.3.1
供方應建立和實施先期產品品質規劃的流程,須召集內 部跨工能小組為新產品或更改產品進行生產准備,這些 小組須采用規定在先期產品品質規劃和管制計劃參考 手冊的各种適當的技術.但也可采用能達成本項意圖的 類似技術. 小組工作必須包括: • 各項管制特性的發展定案 • 各項失效模式與效應分析的發展和檢討 • 制定行動方案以降低高風險优先指數的潛在失效模式 • 各項管制計劃的發展和檢討
QS9000车辆工业质量管理体系
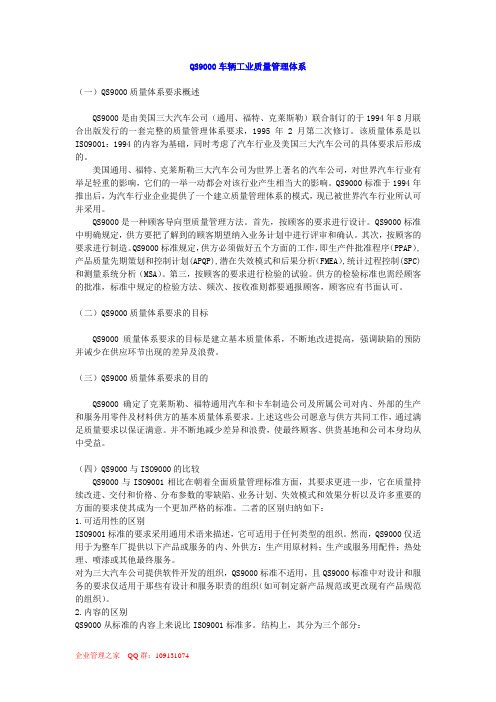
QS9000车辆工业质量管理体系(一)QS9000质量体系要求概述QS9000是由美国三大汽车公司(通用、福特、克莱斯勒)联合制订的于1994年8月联合出版发行的一套完整的质量管理体系要求,1995年2月第二次修订。
该质量体系是以ISO9001:1994的内容为基础,同时考虑了汽车行业及美国三大汽车公司的具体要求后形成的。
美国通用、福特、克莱斯勒三大汽车公司为世界上著名的汽车公司,对世界汽车行业有举足轻重的影响,它们的一举一动都会对该行业产生相当大的影响。
QS9000标准于1994年推出后,为汽车行业企业提供了一个建立质量管理体系的模式,现已被世界汽车行业所认可并采用。
QS9000是一种顾客导向型质量管理方法。
首先,按顾客的要求进行设计。
QS9000标准中明确规定,供方要把了解到的顾客期望纳入业务计划中进行评审和确认。
其次,按顾客的要求进行制造。
QS9000标准规定,供方必须做好五个方面的工作,即生产件批准程序(PPAP),产品质量先期策划和控制计划(APQP),潜在失效模式和后果分析(FMEA),统计过程控制(SPC)和测量系统分析(MSA)。
第三,按顾客的要求进行检验的试验。
供方的检验标准也需经顾客的批准,标准中规定的检验方法、频次、按收准则都要通报顾客,顾客应有书面认可。
(二)QS9000质量体系要求的目标QS9000质量体系要求的目标是建立基本质量体系,不断地改进提高,强调缺陷的预防并诫少在供应环节出现的差异及浪费。
(三)QS9000质量体系要求的目的QS9000确定了克莱斯勒、福特通用汽车和卡车制造公司及所属公司对内、外部的生产和服务用零件及材料供方的基本质量体系要求。
上述这些公司愿意与供方共同工作,通过满足质量要求以保证满意。
并不断地减少差异和浪费,使最终顾客、供货基地和公司本身均从中受益。
(四)QS9000与ISO9000的比较QS9000与ISO9001相比在朝着全面质量管理标准方面,其要求更进一步,它在质量持续改进、交付和价格、分布参数的零缺陷、业务计划、失效模式和效果分析以及许多重要的方面的要求使其成为一个更加严格的标准。
qs9000-2001质量体系要求(中文第三版)
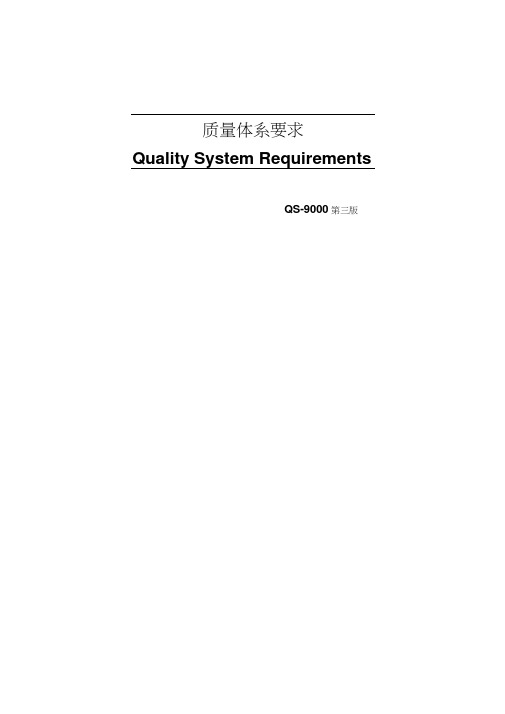
质量体系要求Quality System RequirementsQS-9000第三版以ISO 9000 为基础的要求内容组成管理职责——要素4.1质量体系——要素4.2合同评审——要素4.3设计控制——要素4.4文件和资料控制——要素4.5采购——要素4.6顾客提供产品的控制——要素4.7产品标识和可追溯性——要素4.8过程控制——要素4.9检验和试验——要素4.10检验、测量和试验设备的控制——要素4.11检验和试验状态——要素4.12不合格品的控制——要素—要素4•13纠正和预防措施——要素—要素4.14搬运、贮存、包装、防护和交付——要素4.15 质量记录的控制——要素4.16 内部质量审核——要素4.17 培训——要素4.18 服务——要素4.19 统计技术——要素4.20管理职责一要素4.1质量方针---4.1.1 负有执行职责的供方管理者,应规定质量方针,包括质量目标和对质量的承诺,并形成文件。
质量方针应体现供方的组织目标以及顾客的期望和需求。
供方应确保其各级人员都理解质量方针,并坚持贯彻执行。
组织---4.1.2 职责与权限---4.1.2.1 对从事与质量有关的管理、执行和验证工作的人员,特别是对需要独立行使权力开展以下工作的人员,应规定其职责、权限和相互关系,并形成文件:a)采取措施,防止出现与产品、过程和质量体系有关的不合格;注:如需要纠正质量问题,建议负责质量的人员有权停止生产。
b)确认和记录与产品、过程和质量体系有关的问题;0通过规定的渠道,采取、推荐或提出解决办法;d)验证解决办法的实施效果;e)控制不合格品的进一步加工、交付或安装,直至缺陷或不满足要求的情况得到纠正。
f)在阐述QS-9000要求时,说明顾客对内部职能部门的需求(如选择特殊特性,确定质量目标、培训、纠正和预防措施,产品设计与开发)。
资源---4.1.2.2 对管理、执行工作和验证活动(包括内部质量审核),供方应确定资源要求并提供充分的资源,包括委派经过培训的人员(见4.18)。
qs9000体系文件
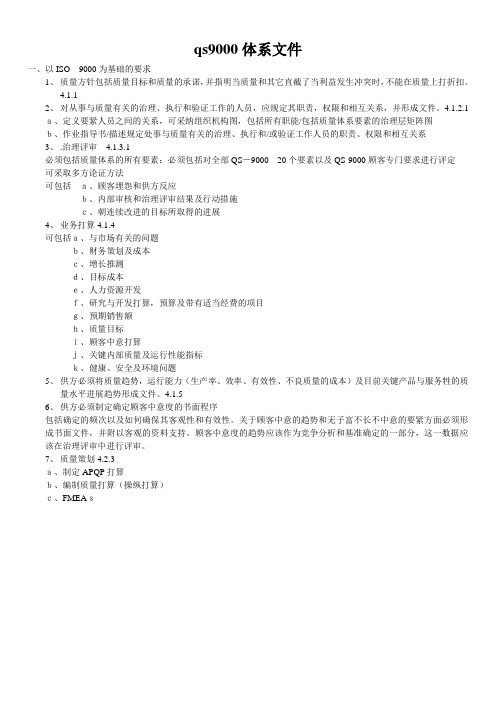
qs9000体系文件一、以ISO9000为基础的要求1、质量方针包括质量目标和质量的承诺,并指明当质量和其它直截了当利益发生冲突时,不能在质量上打折扣。
4.1.12、对从事与质量有关的治理、执行和验证工作的人员,应规定其职责,权限和相互关系,并形成文件。
4.1.2.1a、定义要紧人员之间的关系,可采纳组织机构图,包括所有职能/包括质量体系要素的治理层矩阵图b、作业指导书/描述规定处事与质量有关的治理、执行和/或验证工作人员的职责、权限和相互关系3、.治理评审 4.1.3.1必须包括质量体系的所有要素:必须包括对全部QS-900020个要素以及QS-9000顾客专门要求进行评定可采取多方论证方法可包括a、顾客埋怨和供方反应b、内部审核和治理评审结果及行动措施c、朝连续改进的目标所取得的进展4、业务打算4.1.4可包括a、与市场有关的问题b、财务策划及成本c、增长推测d、目标成本e、人力资源开发f、研究与开发打算,预算及带有适当经费的项目g、预期销售额h、质量目标i、顾客中意打算j、关键内部质量及运行性能指标k、健康、安全及环境问题5、供方必须将质量趋势,运行能力(生产率、效率、有效性、不良质量的成本)及目前关键产品与服务牲的质量水平进展趋势形成文件。
4.1.56、供方必须制定确定顾客中意度的书面程序包括确定的频次以及如何确保其客观性和有效性。
关于顾客中意的趋势和无子富不长不中意的要紧方面必须形成书面文件,并附以客观的资料支持。
顾客中意度的趋势应该作为竞争分析和基准确定的一部分,这一数据应该在治理评审中进行评审。
7、质量策划4.2.3a、制定APQP打算b、编制质量打算(操纵打算)c、FMEAs。
QS9000 质量体系评定说明及指南 含 检查清单

质量体系评定评定说明和指南目的本质量体系评定(QSA)用以确定体系是否符合QS—9000质量体系要求。
正确使用QSA可以确保所有要求均被说明,并有助于确定QS—9000符合性的部门与人员一致性。
适用范围QSA可以根据顾客和供方需要,在下列几种情况下使用:——第一方一供方对质量体系进行自我评定,至少使用带(*)和(**)的问题。
——第二方一顾客对供方质量体系进行评定(包括第一层次供方对分供方的评定),应使用所有的问题和子问题。
某些顾客至少会使用标有双星号(**)的问题。
——第三方一由质量体系认证/注册机构用采作为编制审核检查表的输入,至少使用带(*)和(**)的问题。
评定程序在QS—9000附录A中规定了QSA程序。
QSA中问题的顺序并不意味着审核的顺序。
评定方法评定方法由三个主要阶段组成:阶段I——质量体系文件审核确定质量手册(包括所要求的支持性文件)是署符合QS—9000的所有要求。
使用QSA的问题0.1文件审核。
阶段Ⅱ——现场审核这一阶段是确定供方现场及外部场所质量体系实施的程度和有效性。
阶段Ⅲ——分析和报告对上述两阶段的结果进行评审,以确定供方是否符合QS—9000要求。
审核总结的方式审核员/顾客可采用以下两种方法之一对审核做出结论:—推荐/不推荐—计分法每一个要素都可以按顾客的要求选用下述两种方法之一进行评定:—合格/一般不合格/严重不合格;—每个要素可得0~l0分,见“使用计分法的评定过程”。
定义严重不合格是指出现下述情况之一:—质量体系缺项或完全不符合QS—9000要求。
若对于某项要求出现多个一般不合格,而使整个体系无法运行,则同样视为严重不合格;—任何有可能使不合格产品装运的不合格。
任何可能导致产品或服务失效或预期的使用性能严重降低的不合格;—审核员根据经验和判断表明很可能导致质量体系失效或严重降低对产品和过程控制能力的不合格。
一般不合格是指不符合QS—9000要求,但根据经验和判断不太可能导致出现下列结果的不合格:—质量体系失效;—降低对过程的控制能力;—不合格产品可能被装运。
制程管理-QS9000-1
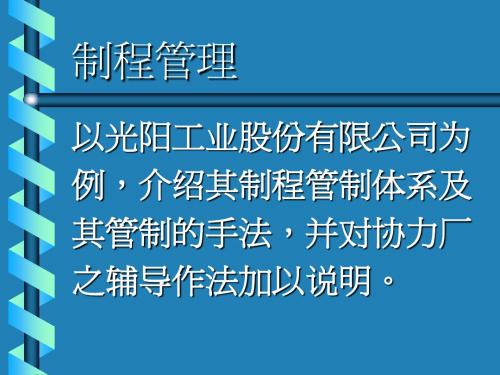
(8)建议行动: 主要目的为减少严重性、发 生性、侦测性或任何这三种 状况之组合。
1.降低严重性:要做设计变更。 2.降低发生性:去除或控制潜在 失效因素、机械结构。 3.降低侦测性:改善、增加设计 管制行动将建议行动及负责建议 行动的人与部门及预估完成日期 填入FMEA表中。
(9)采取行动: 建议行动完成后,列出简略 的 采取行动及完成日期,填于 FMEA表中。 (10)RPN结果:采取行动后,再 次 评估其严重性、发生性、侦 测性及重新计算新的RPN。
工程标准
图面管理
检查基准书、标准样品
工程计划、工程质量管理表
治、检具管理 检查成绩表 作业标准、标准工时
目视管理
部品识别、不良品标识
区域规划
量检具颜色管理 生产管制显示广告牌
初物管理
新设计、新厂商之部品
设计变更或改善后之部品
加工方式或制造设备变更之
部品 实施每日首件检查
Report Analysis , Corrective Action System): 指质量设计执行时,有一种制度, 可以提出文书报告,分析失效, 拟定改善对策,矫正与预防处理 循环不已的操作系统。
RPN是用来评估设计风险的,
从1~1000其数字乃指示设计 风险之严重顺序,将数据填 入FMEA表中。
(5)制程能力评价与解析
(1)图示法:以次数分配图、直方图、 散布图、管制图表示之。 (1-1)直方图、散布图用以解析数据是 否为常态分布与发现原因和结果间 之关系。 (1-2)用以调查各时间的质量变化与规 格之比较,适用之计量值管制 (2)数值法:以Ca值(制程准确度)、Cp 值(制程精密度)、Cpk值(制程能力 指数)来表示之。
量测系统是指由人员、量具、操 作程序及其他设备或软件集合组 成皆称为量测系统。
QS9000标准要求条款

QS9000标准要求条款1. 引言QS9000是一种供汽车行业使用的质量管理系统标准。
该标准由国际质量管理系统注册机构〔IATF〕和三个主要汽车制造商——克莱斯勒、福特和通用汽车共同开发。
QS9000标准的目的是确保供给商能够提供符合汽车行业质量要求的产品和效劳。
2. 质量管理体系要求QS9000标准要求供给商建立和维护一套有效的质量管理体系。
以下是相关要求条款:2.1 质量方针供给商应该制定并实施一套质量方针,明确质量目标和责任。
质量方针应该与组织的目标相一致,并向相关方提供清晰的质量承诺。
2.2 质量方案供给商应该制定质量方案,以确保产品和效劳符合要求。
质量方案应包括质量目标、质量活动、资源需求和时间表等内容,并与相关方进行沟通和确认。
2.3 质量手册供给商应编制质量手册,详细说明质量管理体系的结构和运作。
质量手册应包括质量政策、程序、工作指南和记录要求等内容,并向相关方提供。
2.4 质量目标达成供给商应采取有效措施,确保质量目标得到达成。
这应包括设定和跟踪关键绩效指标,识别和纠正质量问题,并进行持续改良。
2.5 产品/过程设计与开发供给商应采用系统化的方法进行产品和过程的设计与开发。
该方法应包括产品规格的制定、设计验证、过程评估和强制性工具的使用等步骤,以确保产品和过程的可靠性和可重复性。
2.6 供货管理供给商应建立和维护有效的供货管理程序。
该程序应覆盖供给商选择、评估和审核、供货合同管理、物料接收和检验、供给商反响和改良等流程,并与相关方进行沟通和确认。
2.7 过程控制供给商应采取措施,确保产品和过程的可控。
这应包括过程标准的制定、设备维护、监控和测量以及记录和数据分析等活动,以及作为结果的产品合格性确认。
2.8 持续改良供给商应积极主动地进行持续改良。
这应包括收集并分析质量数据、进行异常管理、培训和教育以及质量管理体系的审查和改良等活动,以提高质量管理能力和客户满意度。
3. 结论QS9000标准要求供给商建立和实施一套有效的质量管理体系,以确保产品和效劳符合汽车行业的质量要求。
- 1、下载文档前请自行甄别文档内容的完整性,平台不提供额外的编辑、内容补充、找答案等附加服务。
- 2、"仅部分预览"的文档,不可在线预览部分如存在完整性等问题,可反馈申请退款(可完整预览的文档不适用该条件!)。
- 3、如文档侵犯您的权益,请联系客服反馈,我们会尽快为您处理(人工客服工作时间:9:00-18:30)。
判定基準(書面、圖例或標準 樣品)
設備維護
特殊製程的規定(操作條件、 人員資格、記錄)
製程管制系統
光陽體系目前雖有約160家協力 廠商承製各種零組件,但中心 工廠本身尚保有若干關鍵性零 件之製造,如引擎(engine)、
變 速箱(gear box)、車架
工程標準
圖面管理 檢查基準書、標準樣品 工程計劃、工程品質管理表
偵測性:目前之設計管制,在零 件、配件開始量產前
偵 測潛在因素之能力,
數 據填入FMEA表中。
嚴重性:在一個零件、系統、分 系統或客戶發生失效
之 潛在影響程度之分級
, 數據填入FMEA表中。
發生性:特定原因、機械結構失 效發生之機會,數據
FRACAS(Failure Report Analysis , Corrective Action System):
治、檢具管理 檢查成績表 作業標準、標準工時
目視管理
部品識別、不良品標識 區域規劃 量檢具顏色管理 生產管制顯示看板
初物管理
新設計、新廠商之部品 設計變更或改善後之部品 加工方式或製造設備變更之 部品 實施每日首件檢查
製程品管
依據各製程不同的製造方式如 圖。
環境品質
5S活動 公害防治 睦鄰活動
QS9000-1质量体系标 准
製程管理內容
製程管制的原則、中心廠的 製程管制系統、衛星工廠之 品質提昇。
製程管制的原則:
依據ISO 9001,1994年版,條款 4.9有關製程管制的要點有:
製程的規劃 書面作業標準 適切之生產、設備、環境
符合有關的標準/法規、品 質計劃及程序 各項品質參數/特性之檢測 製程及設備的核准
量具再現性及再生性(R&R)評價結果:
若誤差在30%以下則量測系統可 接受。
若誤差超過30%則量測系統需加 以改進。
貳、能力分析
為調查分析各工程之製造品質能 力,以建立工程品質重點與管制 方法,確保產品質穩定。
適用時機:
(1 法、機具、人具之作業標準 。
(3)工程規格或其他生產因素變 更前後品質的確認。
(4)某種製程發生不良,需製程 能力研判時。
(3)製程能力指數(Cpk)之評價, 為
綜合Ca與Cp兩者之指數。
製程能力改善與處置
再標準化: (1)將其最佳條件、管制方法,反應
入相關作業標準書內 (2)上列標準化完成後,應列入教育
訓練內容,並排定時間實施教育 訓練。
再生性與再現性
為能了解量具之量測品質,通 用範圍:包含各種量具、儀器 設備、檢具及試驗機。
(1)確認系統、分系統之任務 :
(2)作成可靠性方塊圖:
(3)選定有效之潛在失效模式 :
(4)推定原因之記入: (5)失效之潛在影響: (6)目前設計管制: (7)風險領先指標:
(8)建議行動: 主要目的為減少嚴重性、發 生性、偵測性或任何這三種 狀況之組合。
1.降低嚴重性:要做設計變更。
2.降低發生性:去除或控制潛在 失效因素、機械結構。
執行量測系統前之準備事項 :
所研究之主要變異型態對象決定 。
基於統計之考量,配合實際之製 程,選擇適當之作業人數、樣本 數及重複測試次數。
執行研究:
將作業者分為A、B、C三者零件 10個,但作業者無法看到零件號 碼。
校正量具。使作業者A依隨機取 樣10個零件,將量測數據分別記 入。
計算
量具再現性及再生性計算如(表 5.8)及(表5.9)為整個研究的數據 表,表5.9為個別項目的記錄和 依規定公式的計算。
指品質設計執行時,有一種制度 ,可以提出文書報告,分析失效 ,擬定改善對策,矯正與預防處 理循環不已的作業系統。
RPN是用來評估設計風險的, 從1~1000其數字乃指示設計 風險之嚴重順序,將數據填 入FMEA表中。
FMEA的準備與實施
組成跨部門小組,小組包含設計 、製造、裝配、品管、售後服務 等部門。 各專業領域中之責任工程師必須 直接參與各領域的工程活動。
(5)需建立經濟有效之製程能力 評價時。
實施步驟
(1)分析對象選定 (2)作業標準化 (3)加工條件予以標準化
(4)數據蒐集30組或個以上之數 據
(5)製程能力評價與解析
(1)圖示法:以次數分配圖、直方圖、 散佈圖、管制圖表示之。
(1-1)直方圖、散佈圖用以解析數據是 否為常態分佈與發現原因和結果間 之關係。
製程分析
失效模式與效應分析(FMEA)─ 為一種預防性之可靠度設計分 析技術,藉由探求失效謀求改 進的活動。
包括:
(1)認識且評估對產品或製程的潛 在失效因素及其對品質及客戶滿 意度之影響。
(2)確認可以避免或降低失效機會 發生之步驟。
(3)將過程文書化。
風險領先指標(RPN)─為偵測性 *嚴重性*發生性之乘積
(1-2)用以調查各時間的品質變化與規 格之比較,適用之計量值管制
(2)數值法:以Ca值(製程準確度)、Cp 值(製程精密度)、Cpk值(製程能力 指數)來表示之。
(1)製程準確度(Capability of Accuracy-Ca)之評價,是以製造 之產品衡量平均值與規格中心值 之一致性。
(2)製程精密度 (Capability of Precision- Cp)之評價,是以製 造出之一品衡量變異寬度與規格 公差符合之程度。
設備管理
全面預防保養(TPM) 刀具管理 量、檢具管理、校正 刀具管理
資料分析
製程能力分析 不良率、不良原因統計 QC七手法運用 品質週/月會報
改善活動
QCC 提案制度 自動化、電腦化、防呆措施
教育訓練
外訓(品管技術師、品管工程 師) 內訓(種子人員培育),訓練 課程內容如表5.2所示 專案改善、優良案例獎
相關定義 :
量具乃一般生產現場上所用的 量具、儀器設備、檢具及試驗 機皆通稱為量具。
量測系統是指由人員、量具、操 作程序及其他設備或軟體集合組 成皆稱為量測系統。
量具再現性是指一量具由同一作業 者,經量測同一零件,其量測特性 值之再現能力,亦即其量測值間變 異。
量具再生性是指不同作業者使用相 同量具量測相同產品之特性時,其 作業者間量測平均值之變異。
3.降低偵測性:改善、增加設計 管制行動將建議行動及負責建議 行動的人與部門及預估完成日期 填入FMEA表中。
(9)採取行動: 建議行動完成後,列出簡略
的 採取行動及完成日期,填於 FMEA表中。
(10)RPN結果:採取行動後,再 次 評估其嚴重性、發生性、偵 測性及重新計算新的RPN。
(11)跟催:設計的責任工程師必 須確定所有建議行動皆有列 出及執行,其確保FMEA之完 整性的方法有:圖面審查、 製程FMEA審查、定期與原始 FMEA小組追蹤會議。