机械优化设计三个案例
机械优化设计案例

机械优化设计案例:某生产线自动送料机构的改进
在制造领域,生产线上的自动送料机构是确保生产流程顺畅、高效的关键环节。
然而,传统的自动送料机构往往存在效率低下、易损坏、维护成本高等问题。
为了解决这些问题,我们采用了机械优化设计的方法,对某生产线上的自动送料机构进行了改进。
该自动送料机构的主要任务是将原材料从存储区输送到生产线,并确保每次输送的数量准确。
但是,在长时间使用后,传统的送料机构常常出现卡顿、输送不准确等问题。
经过分析,我们发现这些问题主要是由于机构中的某些部件设计不合理,导致机械效率降低。
为了解决这些问题,我们采用了以下优化策略:
结构优化:利用拓扑优化技术,对送料机构的主体结构进行了重新设计,使其在满足强度和刚度的同时,减轻了重量,从而减少了动力消耗。
传动系统优化:采用了新型的齿轮和链条传动系统,减少了传动过程中的摩擦和能量损失,提高了传动效率。
控制系统优化:引入了PLC和传感器技术,实现了对送料过程的精确控制,确保了每次输送的数量准确。
维护性优化:设计了易于拆卸和维护的结构,减少了维护时间和成本。
经过上述优化后,新的自动送料机构的性能得到了显著提升。
与传统的送料机构相比,新的机构在输送速度、准确性、使用寿命和维护成本等方面都有了显著的优势。
经过实际生产验证,新的自动送料机构不仅提高了生产效率,还降低了生产成本,为企业带来了显著的经济效益。
第八章机械优化设计应用实例

最优值 上面的最优解是连续性的,需进一步离散化处理,从略。
1,确定设计变量
铰链四杆机构按主从动连架杆给定的角度对应关系进行 设计时,各杆长度按同一比例缩放并不影响主,从动杆转 角的对应关系。因此可把曲柄长度作为单位长度,即令 L1=1,其余三杆表示为曲柄长度的倍数,用其相对长度l2, L3,l4作为变量。一般考虑,本问题与初始角 , 也有 关系,所以变量本应为l2,l3,l4, 和 五个。但是两 转角变量并不是独立变量,而是杆长的函数。写出如下式
D:
二,选择优化方法及结果分析
该题维数较低,用哪一种优化方法都适宜。这里选用约束 坐标轮换法。
计算时,曾用若干组不同的初始数据进行计算,从中选出 其中三组。见课本表8.1
由其中的计算结果可以看出,第二次计算结果应为最优解。
, 为相对杆长。最后,根据机构的结构设计需要按一定 的比例尺求出机构实际杆长L1,L2,L3,L4。
由余弦定理a图
整理得约束条件 同理由上页b图传动角最小位置写出 整理得约束条件
⑵按曲柄存在条件建立约束条件 写成约束条件有
用全部约束条件画成次下图所示的平面曲线,则可见, g3(x)~g7(x)均是消极约束。而可行域D实际上只是由g1(x) 与g2(x)两个约束条件围成的。综合上述分析,本题的优 化数学模型如下
输 出 角 函 数 图
对于该机构设计问题,可以取机构输出角的平方偏差 最小为原则建立目标函数。为此,将曲柄转角为
的区间分成n等分,从动摇杆输出角也有相对
应的分点。若各分点标号记作i,以各分点输出角的偏差 平方和作为目标函数,则有
式中的有关参数按如下步骤及公式计算 ①曲柄各等分点的转角
②期望输出角 ③实际输出角
机械优化设计范例(共9张PPT)
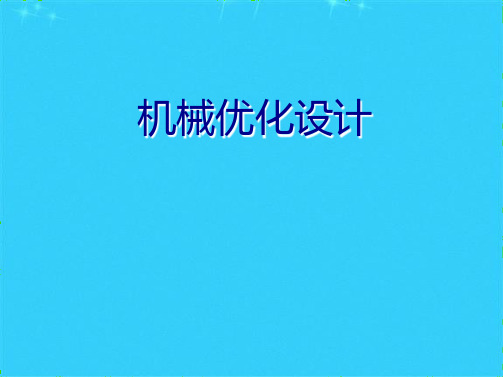
设计变量
现设 甲矿运往东站x万吨
乙矿运往东站y万吨
则甲矿运往西站200-x万吨
乙矿运往西站260-y万吨 令x=x1,y=x2
所以:X43;1.5(200-x1)+0.8x2+1.6(260-x2) =716-0.5x1-0.8x2(万元)
所以:Min f(X)= 716-0.5x1-0.8x2
约束条件
- x1 ≤0 X1-200 ≤0 -x2 ≤0 x2 - 260 ≤ 0
x1+x2-280≤ 0 100-x1-x2≤0
求解结果
x2 280 260
100
Z
(20,260)
x1=20 x2=260
Minf(X)= 498万元
100
200 280
x1
所以: 乙矿运往西站260-y万吨
Mx2in-f(26X0)≤ =0 498万元 则令甲x=矿x1运,y=往x2西站200-x万吨
最少的运费为498万元 x令1x+=xx21-2,y8=0x≤20
己 x1知+x甲2-、28乙0≤两0煤矿每年的产量分别为200万吨和260万吨,需经过东、西两个车站运外地。 M甲i煤nf(矿X运)往=东49站8和万西元车站的运费价格分别为1元/吨和1.5元/吨,乙煤矿运往东车站和西车站的运费价格分别为0.8元/吨和1.6元/吨 所。以:Min f(X)= 716-0. 煤乙矿应 运怎往样东编站制y万调吨运方案才能使总运费最少? 己x1知+x甲2-、28乙0≤两0煤矿每年的产量分别为200万吨和260万吨,需经过东、西两个车站运外地。 xM1i+nfx(2-X2)80=≤ 4098万元 现甲设煤矿甲运矿往运东往站东和站西x万车吨站的运费价格分别为1元/吨和1.5元/吨,乙煤矿运往东车站和西车站的运费价格分别为0.8元/吨和1.6元/吨 所 。以:X = [ x1, x2 ]T
机械设计中的案例分析与实例讲解

机械设计中的案例分析与实例讲解在机械设计领域中,案例分析和实例讲解是非常重要的学习方法和实践工具。
通过案例分析和实例讲解,可以加深对机械设计原理和应用的理解,掌握解决实际问题的能力。
本文将通过几个案例来分析和讲解机械设计中的关键问题和解决方法。
案例一:轴承选择与设计在机械设计过程中,轴承是不可或缺的重要组件。
选择和设计合适的轴承对于确保机械设备的正常运行至关重要。
在某公司的一个机械设计项目中,设计师面临着选择和设计轴承的问题。
首先,设计师需要根据机械设备的工作条件和要求来确定所需承载能力、转速范围等参数。
然后,根据这些参数和轴承的性能指标表,筛选出合适的轴承型号。
在选择轴承型号后,设计师还需要对轴承进行设计,确定轴承的几何尺寸和安装方式,以确保其在特定工作条件下的可靠性和寿命。
通过这个案例,我们可以看到,在机械设计中,轴承的选择和设计是一个复杂而关键的环节。
合适的轴承选择和设计可以提高机械设备的性能和可靠性。
案例二:零件强度分析与优化在机械设计中,零件的强度是一个重要的设计指标。
在某公司的一个机械结构设计项目中,设计师需要对一个零件进行强度分析和优化。
首先,设计师需要根据零件的工作条件和受力情况,确定零件的受力分析模型,并据此计算零件的应力和变形。
然后,根据零件的材料特性和载荷条件,对零件的强度进行评估。
如果发现零件的强度不满足要求,设计师需要通过调整材料选择、几何尺寸等参数来优化零件的强度。
通过这个案例,我们可以看到,在机械设计中,零件的强度分析和优化是关键的设计环节。
通过对零件的强度进行分析和优化,可以确保零件在工作条件下的安全可靠性,提高机械设备的性能。
案例三:机构设计与运动模拟在机械设计中,机构的设计和运动模拟是一项重要任务。
在某公司的一个机械运动机构设计项目中,设计师面临着设计和优化运动机构的问题。
首先,设计师需要根据机械设备的功能和要求,确定机构的类型和布置方式。
然后,设计师需要进行机构的几何设计,确定机构的连杆比例、驱动方式等参数。
机械优化设计实例
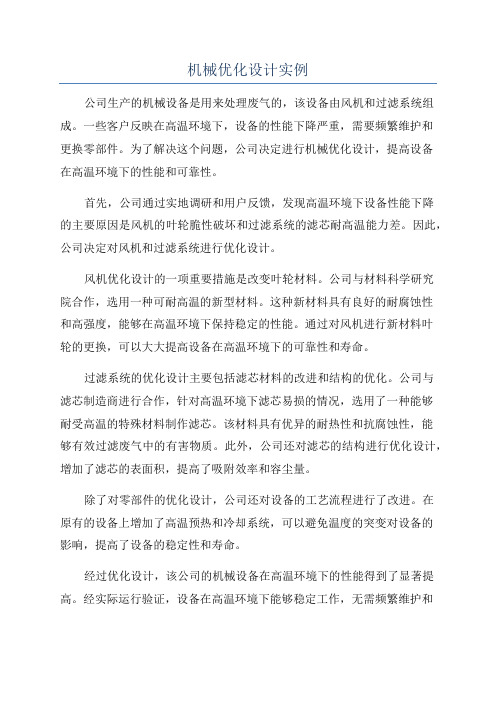
机械优化设计实例公司生产的机械设备是用来处理废气的,该设备由风机和过滤系统组成。
一些客户反映在高温环境下,设备的性能下降严重,需要频繁维护和更换零部件。
为了解决这个问题,公司决定进行机械优化设计,提高设备在高温环境下的性能和可靠性。
首先,公司通过实地调研和用户反馈,发现高温环境下设备性能下降的主要原因是风机的叶轮脆性破坏和过滤系统的滤芯耐高温能力差。
因此,公司决定对风机和过滤系统进行优化设计。
风机优化设计的一项重要措施是改变叶轮材料。
公司与材料科学研究院合作,选用一种可耐高温的新型材料。
这种新材料具有良好的耐腐蚀性和高强度,能够在高温环境下保持稳定的性能。
通过对风机进行新材料叶轮的更换,可以大大提高设备在高温环境下的可靠性和寿命。
过滤系统的优化设计主要包括滤芯材料的改进和结构的优化。
公司与滤芯制造商进行合作,针对高温环境下滤芯易损的情况,选用了一种能够耐受高温的特殊材料制作滤芯。
该材料具有优异的耐热性和抗腐蚀性,能够有效过滤废气中的有害物质。
此外,公司还对滤芯的结构进行优化设计,增加了滤芯的表面积,提高了吸附效率和容尘量。
除了对零部件的优化设计,公司还对设备的工艺流程进行了改进。
在原有的设备上增加了高温预热和冷却系统,可以避免温度的突变对设备的影响,提高了设备的稳定性和寿命。
经过优化设计,该公司的机械设备在高温环境下的性能得到了显著提高。
经实际运行验证,设备在高温环境下能够稳定工作,无需频繁维护和更换零部件,极大地减少了停机时间和维修成本。
同时,设备的可靠性和寿命也得到了显著提升,增强了客户的信任和满意度。
这个实例充分展示了机械优化设计的重要性和成功应用。
通过对机械结构、工艺流程和材料的优化,可以提高机械产品的性能、效率和可靠性,满足客户的需求,提升企业的竞争力。
机械优化设计_经典实例
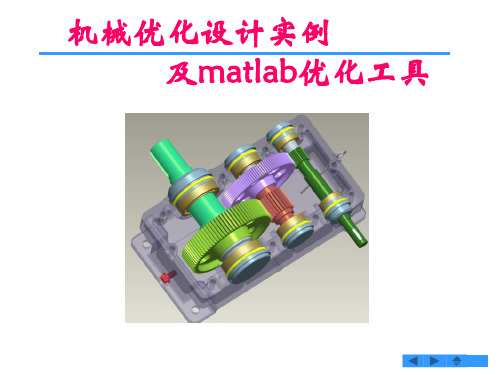
1.5 f max
1
1 321
x1 x22
1
0
g5 (x) x1 0
g6 (x) x2 0
盖板优化实例
f (x) 2 60t 2 0.5h 120 x1 x2
盖板优化实例
g1 ( x)
1
1 4
x2
0
7 g2 (x) 1 45 x1x2 0
目标函数:
f (x) 2 60t 2 0.5h 120 x1 x2
约束:
g1 ( x)
[ ] max
1
1 4
x2
1
0
g2 (x)
[ ] max
1
7 45
x1 x2
1
0
g3 (x)
c max
1
7 45
x13 x2
1
0
g4 (x)
第2部分 优化计算工具
2.1 线性规划优化函数 2.2 无约束非线性优化函数 2.3 约束优化函数
MATLAB解决的线性规划问题的标准形式为:
min cT x s.t. Ax b, x 0
A (aij )mn , x (x1, x2, x3,...xn )T c (c1, c2, )T ,b (b1,b2,...bm )T ,且b 0
a2
1 b2
an
1 bn
(a、b维数必须相同)
1.4 源文件(M-文件)
分为两类: 函数文件和非函数文件 都用扩展名.M
1.4.1 函数文件(相当于子程序)
机械创新设计案例

机械创新设计案例概述机械创新设计是指基于机械原理和工程知识的创新设计过程。
机械创新设计案例是指以机械创新设计为基础,通过解决实际问题和满足需求的方式,创造出新的机械产品或改进现有机械产品的设计案例。
在这篇文章中,我们将介绍一些机械创新设计的案例,并探讨其在工程领域中的应用和意义。
案例一:自动化垃圾分类系统在现代社会中,垃圾分类成为了一个重要的环保问题。
传统的垃圾分类方式需要人工操作,效率低下且容易出错。
为了解决这个问题,某公司设计了一套自动化垃圾分类系统。
该系统通过使用机器视觉技术和机械臂控制系统,能够精准地识别和分拣垃圾。
用户只需将垃圾投放到系统中,系统便能够自动地将不同种类的垃圾分拣到不同的垃圾桶中。
这种自动化垃圾分类系统不仅大大提高了垃圾分类的效率,还减少了人力成本和环境污染。
案例二:智能电动自行车随着城市化进程的不断加快,电动自行车成为了一种常见的交通工具。
然而,传统的电动自行车存在电量不稳定、续航里程不够长等问题。
为了解决这些问题,一家公司开发了一款智能电动自行车。
这款智能电动自行车配备了一套先进的电池管理系统和能量回收系统。
电池管理系统能够根据用户的习惯和行驶条件,智能地控制电池的放电和充电,提高电池的使用寿命和续航里程。
能量回收系统能够将制动过程中产生的能量转化为电能,回馈给电池进行充电,进一步延长续航里程。
这款智能电动自行车不仅解决了传统电动自行车的短板,还提升了用户的乘坐体验。
案例三:无人驾驶汽车无人驾驶汽车是近年来快速发展的机械创新设计领域。
它基于人工智能、传感器和控制系统等技术,能够在无需人类干预的情况下自主行驶。
这种创新设计不仅在交通运输领域中具有重要意义,还对未来的城市规划和交通系统的发展产生了深远的影响。
无人驾驶汽车通过使用激光雷达、摄像头和超声波传感器等技术,能够实时感知周围环境的情况,并做出相应的决策。
它能够通过精确的导航算法和先进的控制系统,安全地驾驶在不同的路况下。
机械优化设计经典实例

机械优化设计经典实例机械优化设计是指通过对机械结构和工艺的改进,提高机械产品的性能和技术指标的一种设计方法。
机械优化设计可以在保持原产品功能和形式不变的前提下,提高产品的可靠性、工作效率、耐久性和经济性。
本文将介绍几个经典的机械优化设计实例。
第一个实例是汽车发动机的优化设计。
汽车发动机是汽车的核心部件,其性能的提升对汽车整体性能有着重要影响。
一种常见的汽车发动机优化设计方法是通过提高燃烧效率来提高功率和燃油经济性。
例如,通过优化进气和排气系统设计,改善燃烧室结构,提高燃烧效率和燃油的利用率。
此外,采用新材料和制造工艺,减轻发动机重量,提高动力性能和燃油经济性也是重要的优化方向。
第二个实例是飞机机翼的优化设计。
飞机机翼是飞机气动设计中的关键部件,直接影响飞机的飞行性能、起降性能和燃油经济性。
机翼的优化设计中,常采用的方法是通过减小机翼的阻力和提高升力来提高飞机性能。
例如,优化机翼的气动外形,减小阻力和气动失速的风险;采用新材料和结构设计,降低机翼重量,提高飞机的载重能力和燃油经济性;优化翼尖设计,减小湍流损失,提高升力系数。
第三个实例是电机的优化设计。
电机是广泛应用于各种机械设备和电子产品中的核心动力装置。
电机的性能优化设计可以通过提高效率、减小体积、降低噪音等方面来实现。
例如,采用优化电磁设计和轴承设计,减小电机的损耗和噪音,提高效率;通过采用新材料和工艺,减小电机的尺寸和重量,实现体积紧凑和轻量化设计。
总之,机械优化设计在提高机械产品性能和技术指标方面有着重要应用。
通过针对不同机械产品的特点和需求,优化设计可以提高机械产品的可靠性、工作效率、耐久性和经济性。
这些经典实例为我们提供了有效的设计思路和方法,帮助我们在实际设计中充分发挥机械优化设计的优势和潜力。
- 1、下载文档前请自行甄别文档内容的完整性,平台不提供额外的编辑、内容补充、找答案等附加服务。
- 2、"仅部分预览"的文档,不可在线预览部分如存在完整性等问题,可反馈申请退款(可完整预览的文档不适用该条件!)。
- 3、如文档侵犯您的权益,请联系客服反馈,我们会尽快为您处理(人工客服工作时间:9:00-18:30)。
机械优化设计案例11. 题目对一对单级圆柱齿轮减速器,以体积最小为目标进行优化设计。
2.已知条件已知数输入功p=58kw,输入转速n=1000r/min,齿数比u=5,1??]=400Mpa。
,许用弯曲应力[ 齿轮的许用应力[=550Mpa]FH3.建立优化模型3.1问题分析及设计变量的确定由已知条件得求在满足零件刚度和强度条件下,使减速器体积最小的各项设计参数。
由于齿轮和轴的尺寸(即壳体内的零件)是决定减速器体积的依据,故可按它们的体积之和最小的原则建立目标函数。
单机圆柱齿轮减速器的齿轮和轴的体积可近似的表示为:222222??)?0.25(b?c)(D?0.25?b(d?ddv?0.25(bd)?d?)22ggzz121222222????d?)?7c?0.258l(dd?dd22z101zzz22222222??)10mb(mzub?d?0?.25b[m?z0b?db?m.z8u1z2z1112222]3228dd?.6d)?d?l.205bd10?0.05b(mzu? m?12z1zz222z1z式中符号意义由结构图给出,其计算公式为d?mz,d?mz2211D?umz?10m1g2d?1.6d,d?0.25(umz?10m?1.6d)2z22g10z c?0.2b由上式知,齿数比给定之后,体积取决于b、z、m、l、d 和d z21 z1六个参数,则设计变量可取为TT]ddl[bzx[xxxxx]m?x?21z2314z5163.2目标函数为222222f(x)?0.785398(4.75xxx?85xxx?85xx?0.92xx?xx?5631323111122222220.8xxxx?1.6xxx?xx?xx?28x ?32x)?min61236541364563.3约束条件的建立z?z?17,得1 )为避免发生根切,应有min10x??17?g(x)21b???????maxmin d的最大值,为齿宽系数齿宽应满足和2 )dmaxmin??,,得和最小值,一般取=1.4=0.9maxmin0(xx)?xg()?0.9?x322101.4??(x)?x(xx)g 3123 3)动力传递的齿轮模数应大于2mm,得02?x?g(x)?34)为了限制大齿轮的直径不至过大,小齿轮的直径不能大于4d,得axm10??300g(x)?xx325d?d?d)齿轮轴直径的范围:5得maxminzzz0gx?)?100?(x560?x??150g(x)570?130?xg(x)?680?)?x?200g(x69d??0.5?b?2ll按结构关系,应满足条件:)轴的支撑距离62minz? =20),得(可取min0??400?x?.5x?x(gx)41106)齿轮的接触应力和弯曲应力应不大于许用值,得7g(x)?1468250(xxx)?550?0123117098?400??0g(x)4222??12)0.85410x?..xxx(0169?06666?10?x221237 098?)(gx?400?04222?13)10177028240(xxx.?.?x10?.0?394x221322??][,得不大于许用值8)齿轮轴的最大挠度axm440??0.003x117x)?.04x(xxx)g(4324145??][不大于许用值,得9)齿轮轴的弯曲应力ww6x1012.85?12240510??5.x)?()?2.4?g(153xxx3526x102.85?112240??5.5)?()?6?10g(x163xxx362 4.优化方法的选择个约束条件的优化设计问题,16由于该问题有6个设计变量,Matlab采用传统的优化设计方法比较繁琐,比较复杂,所以选用函数来求解此非线性优化问题,避免了fmincon优化工具箱中的较为繁重的计算过程。
数学模型的求解5. 该优化设计的数学优化模型表示为:5.1.1将已知及数据代入上式,2222?85xxxx?85xx?0f(x)?.785398(4.75xxmin33211132222x?x.6xxxxxx?0.8xxx?1.092xx?5533461121661222 )xx?28?32?xx6645Subject to:g(x)?17?x?021g(x)?0.9?x(xx)?03212g(x)?x(xx)?1.4?03321g(x)?2?x?034g(x)?xx?300?0352g(x)?100? x?056g(x)?x?150?057g(x)?130?x?06830?xg?200(x)?690??40?x?0.5x?xg(x)410610550?x)?1468250(xx)?g(x1311270980?g(x)?400?4?222?12)?0.6666?10x.x?0854?10(xxx0.1692213270980xg()??400?42?2213).?0394?10177(xxx0.2824?0.?10x x22312440?003xx04x(xx)?0.)g(x?117.43451426x1021.85?12240?10??5.5(g(x)?)?2.4153xxx3256x10852.?1122405.?)?()6?10??5(gx163xxx362优化工具箱对数学模型进行程序求解5.1.2运用Matlabmyfun.m,Matlab首先在优化工具箱中编写目标函数的M文件返回x:处的函数值ffunction f = myfun(x)f=0.785398*(4.75*x(1)*x(2)^2*x(3)^2+85*x(1)*x(2)*x(3)^2-85*x(1)*x(3)^2+0.92* x(1)*x(6)^2-x(1)*x(5)^2+0.8*x(1)*x(2)*x(3)*x(6)-1.6*x(1)*x(3)*x(6)+x(4)*x(5)^2+ x(4)*x(6)^2+28*x(5)^2+32*x(6)^2)由于约束条件中有非线性约束,故需要编写一个描述非线性:文件约束条件的Mmycon.mfunction[c,ceq]=myobj(x)c=[17-x(2);0.9-x(1)/(x(2)*x(3));x(1)/(x(2)*x(3))-1.4;2-x(3);x(2)*x(3)-300;100-x(5);x( 5)-150;130-x(6);x(6)-200;x(1)+0.5*x(6)-x(4)-40;1486250/(x(2)*x(3)*sqrt(x(1)))-550; 7098/(x(1)*x(2)*x(3)^2*(0.169+0.006666*x(2)-0.0000854*x(2)^2))-400;7098/(x(1)* x(2)*x(3)^2*(0.2824+0.00177*x(2)-0.0000394*x(2)^2))-400;117.04*x(4)^4/(x(2)*x( 3)*x(5)^4)-0.003*x(4);(1/(x(5)^3))*sqrt((2850000*x(4)/(x(2)*x(3)))^2+2.4*10^12)-5 .5;(1/(x(6)^3))*sqrt((2850000*x(4)/(x(2)*x(3)))^2+6*10^13)-5.5];ceq=[];里输入:最后在command window给定初始值x0=[230;21;8;420;120;160];%4[x,fval,exitflag,output]=fmincon(@myfun,x0,[],[],[],[],[],[],@myobj,output)%调用优化过程5.1.3最优解以及结果分析运行结果如下图所示:由图可知,优化后的最终结果为x=[123.3565 99.8517 1.7561 147.3157 150.4904129.5096]7 f(x)=2.36e*10由于齿轮模数应为标准值,齿数必须为整数,其它参数也要5 进行圆整,所以最优解不能直接采用,按设计规范,经标准化和圆整后:x=[124 100 2 148 150 130]7 f(x)=6.16 *106.结果对比分析73,而优化后×10mm若按初始值减速器的体积V大约为6.3273,优化结果比初始值体积减少为:mm则为6.16×10 的体积V77)×100%10=2.5%=1-(6.16×10/6.32×Δν所以优化后的体积比未优化前减少了2.5%,说明优化结果相对比较成功。
7.学习心得体会学习机械优化设计课程的心得体会通过将近一学期的学习,对这门课有了初步的了解和认识,学期伊始,浏览全书,发现全是纯理论知识,觉得这门课会很枯燥,但是又回过头来想想,作为21世纪的大学生,要使自己适应社会需求,首先在做任何事之前都应该有正确的态度看待问题,把这些想法作为促使自己进步的动力,再去学习课本知识,效果应该很不一样,有了想法就付诸行动,随着对课本内容的学习跟老师的讲解,发现并不是像自己在学期初想的那样困难,特别是在老师介绍了一些与机械优化设计相关的计算机语言和计算机软件后,真正体会到科学优化设计的强大跟简洁明了,与传统优化设计方法相比较,大大提高了设计效率和质量。
传统设计方法常在调查分析的基础上,参照同类产品通过估算,经验类比或试验来确定初始设计方案,如不能满足指标要求,则进行反复分析计算—性能检验—参数修改,到满足设计指标要求为止。
整个传统设计过程就是人工凑试和定性分析比较的过程,是被动地重复分析产品性能,不是主动设计产品参数。
按照传统设计方法做出的设计方案,有改进余地,但不是最佳设计方案。
而现代化设计工作是借助电子计算机,,应用一些精确度较高的力学数值分析方法,优化软件进行分析计算,找最优设计方案,实现理论设计代替经验设计,用精确计算代替近似计算,用优化设计代替一般的安全寿命可行性设计。
在进行程序求解的过程中,因为是初学Matlab软件,对很多问题的关键点不能够掌握,非线性约束如何书写,上、下限如何选择,函数格式如何书写,变量未定义等等或大或小的问题,但是在一步步排除错误、重新编写程序的过程中,渐渐的对Mtalab熟悉起来,懂得了一些优化方法的简单计算过程和原理,省去了6繁琐复杂的优化计算过程在学完课程之后,反思自己在学习过程中的得失,深深体会到,不论在人生的哪个阶段,都要对自己负责,做任何事都要耐心,细致,“千里之行,始于足下”,学会在物欲横流的社会大潮中,坚持踏踏实实走好人生的每一步。
8.参考文献[1] 孙靖民,梁迎春. 机械优化设计. 北京:机械工业出版社,2006.[2] 濮良贵,纪名刚. 机械设计. 8版. 北京:高等教育出版社,2006.[3] 孙桓,陈作模,葛文杰. 机械原理. 7版. 北京:高等教育出版社,2006.[4]李涛,贺勇军,刘志俭. MATLAB工具箱应用指南—应用数学篇[M].北京:电子工业出版社,2000.7机械优化设计案例2复杂刀具优化设计数学模型的建立及算法改进摘要: 目的建立复杂刀具优化的数学模型,提高优化算法速度.方法采用优化设计与CAD相结合的方法. 结果与结论解决了传统刀具设计的缺点,改进后的算法速度大幅度提高.关键词: 数学模型;优化;算法在传统的刀具设计中,通过查表和经验公式来确定各种结构参数和几何参数,然后,反复计算来得到相对较优的刀具参数.这种方法使设计过程复杂费时,且得不到最优化的参数,设计出的刀具成本高,加工效率低.因而刀具的计算机辅助设计应采用优化设计与CAD相结合的方法,欲进行优化设计,必需首先建立刀具优化设计的数学模型,由于复杂刀具的种类繁多,结构变[1],,因而需分门别类地建立模型此篇仅以轮切式拉刀化多样,优化目标不同.为例1 拉刀优化设计的数学模型在拉刀参数设计过程中需要选择的主要参数有拉削余量A,齿升量a,f齿距t,容屑槽形状和深度h,容屑系数k,同时工作齿数等,这些参数可分为两类,一类是独立参数,如拉削余量和容屑槽形状等,这些参数基本不受其他参数的影响.另一类参数是非独立参数,如齿升量、齿距、容屑槽深度、容屑系数等,这些参数既相互限制又相互依赖,第一类参数的选择比较容易.可以用经验公式和数据库来解决.第二类参数比较复杂,只有通过优化的方法才能得到较好的结果.粗切齿升量的选择是一个比较复杂的问题.增大a可使齿数减少,拉刀f长度变短,但同时又要求容屑槽深度增加.另外齿升量的增加又会引起拉削力的增大,受到拉床和拉刀拉应力的限制.齿距是决定拉刀长度的一个重要因素,t越大,拉刀越长,同时工作齿数越少.这样会在拉削过程中引起振动,生产效率低,降低刀具的使用寿命;t过小,又会使容屑空间变小,从而限制了齿升量的增大.其他参数如同时工作齿数z,容屑槽深度h,容屑系数k都是a和t的fi8函数,只有当a和t选择后才能确定.从上述参数分析可知,a和t是拉刀ff设计的关键,在a和t 之间应有一最佳组合值,使得a在拉床的额定应力和ff拉刀的许用应力范围内达到最高,即使拉刀的长度最小.1.1 目标函数的建立确定以af和t为优化的自变量,A为切削余量.拉刀长度是与拉削生产率、成本及其工艺性能有关的参数,拉刀越短对使用和制造越有利,因而取粗切齿[4]部分长度L作为优化目标F= minL(a,t) =tA/(2a). ff约束条件的建立(1)1.2h- 1.13(kaL )≥0. 2/1制槽1)容屑空间的限fw(2)式中 h是与t有关的参数;k为容屑系数,是与t和af有关的参数;Lw为拉削长度.F-pπD≥0. zcwzi/拉额定力的限制拉2)床e(3)式中 Fe为拉床额定拉力;Dw为拉削后孔直径;p为单位切削力;zi为同时工作齿数,zi=INT(Lw/t)+1;zc为组齿数.[σ] –2pD≥0. 用3)拉刀许拉应力制限的inwzi/zcdm(4)式中 [σ]为拉刀许用拉应力;dmin为拉刀最小直径.11 -z≥0. 时大4)最同工制限数齿作的i(5)9z - 3≥0. 制5)最小同时的限作齿数工i(6)25 -t≥0. 制的6)最大齿距限(7)t- 4≥0. 制限最小齿距的7)(8)8)弧形槽能保证稳定的分屑要求的最大齿升量h-a≥0;f(D,n,z) -a≥0. cffz(9)t- Int(2t)/2 = 0. 倍9)齿距整0.5的数应为(10)1.3 优化模型:a,t;自变量f:F=minL(a,t)=tA/2a; 目标函数ff:g(1)=h-1.13(kafLw)≥0;g(2)=F-pπD≥1/2约束方程wzi/zc e0;g(3)=[σ]-2pD≥0;g(4)=11-z≥0;g(5)=z-3≥wzi/zcdmin ii0;g(6)=25-t≥0;g(7)=t-4≥0;g(8)=h-a≥f0;g(9)=f(D,n,z)-a≥0;g(10)=t-Int(2t)/2=0. cfz2 优化算法102.1 标准算法复合形法是一种采用直接搜索方式求解非线性规划问题的数值计算方法,这个方法可以在N维非线性约束的空间中自动选择并改进设计点,该方法的:]3[2.一般步骤为1)m>n+1{x}(i=1, 2,…,n,n+1,…,m)构在可行域内生成个点i①初始顶点的形成,:可以人工选定,成初始复合形,这里需要注意两个问题②需要检验初始顶点是否满足约束条件,;即检验其可行性;也可随机产生2),f(x)≤将其由小到大的顺序重新编号计算各顶点的目标函数值,1f(x)≤…≤f(x); 2m3)xm-1,即心点点个的中坏点后复合形中其余确定除去最mi?11?;xc=xi1m?1m?4)xxx=x+α(x-x),α为映对中心点确定最坏点的映射点cccamm1.3;~,0.9一般取射系数5)x按则件,约某个束条:的可行性如果违背了射检验映点a(x+x)/2x,xa向中心移动一半距离,反复直至映射点把映射点a ac x;是可行点a6)f(x),x,完成一次计算新的可行点的函数值用它代替最坏点m a;回到第二步,迭代7)f(x)-f(x)<ε直到满足.,则终止以上称为复合形,重复以上过程1m法的“标准算法”,由于该算法的概念简单、容易实现,且能有效灵活地处理不等式约束问题,所以在结构化设计中得到广泛的应用.112.2 存在的问题把上述标准算法应用于工程实际时,就会发现它还存在以下几个问题:1)过多的可行性检验限制了其在优化设计中的有效应用.初始顶点生成和映射点的确定,都要进行可行性检验,在结构优化设计中,可行性检验其实质上就是结构分析过程,其计算量通常要占总工作量的80%以上,因此结构分析次数过多,必然会导致因计算时间过长而降低算法的效率.2)迭代过程中向极值点逼近的速度问题.开始若干次迭代(一次迭代是对于选取一个既满足约束条件又使目标函数值有所改善的新点所需的计算),目标函数值下降得很快,各顶点迅速接近极值点,一般来说,最初的(5~10)次迭代函数值下降得最快.随着迭代次数的增加,函数值的变化却越来越缓慢,也就是说,这时要使目标函数值有微小的改善,都要付出宝贵的计算时间.3)局部最优点问题.用上述算法得到的最优点有可能是局部最优点,虽然可通过多取几个初始点,经计算后得到几个最优点,然后比较得到全局最优点,但这样必然会导致计算工作量的成倍增加.2.3 分层复合形法针对标准算法中存在的问题,采用“分层复合形法”,它是对标准复合形法的改进,其基本思想是:充分利用复合形法开始时目标函数值急剧下降的特点,以迭代次数为控制参数,进行两层优化计算,为避免产生局部最优点,在第一层迭代中,选取多组复合形分别地进行计算,经过若干次有效地迭代,各顶点迅速地逼近最优点,分布在最优点附近.分层复合形法的基本步骤如下:(n )g, (i=1,}…,m)n,n1){x}…, {x(1)个初组初始顶点构成选择ggii n=Int[n/2]+1,n为设计变量数.始复合形,这里只要设计变量所取的值g不太小且相互间离得远些,就可不对初始顶点作可行性检验.2)2)~ 6)步的计算是第一层迭代对各初始复合形标准算法第,取映射率为αn;迭代次数为,t113)n次以后,第一层迭代结束当各复合形都迭代,取两个最好设计点组成t1α(α<α),迭代次数为,取映射率为新的复合形进入第二层迭代221n;.第二层迭代得到的最优点可被认为全局最优点t212分层复合形法有以下几个优点:①迭代次数大大减少;②以迭代次数为停止准则,可根据需要人工控制计算工作量;③第二层迭代能有效地产生全局最优点.3 结论依据本文所述方法,已开发出具有高效率优化CAD系统,证明对传统算法的改进是有效的.参考文献:[1] 唐锡荣. CAD/CAM技术[M].北京:北京航空航天大学出版社, 1994.18-36.[2] 蔡锁章.计算方法[M].北京:中国科学技术出版社, 1993. 54-60.[3] 徐灏.机械设计手册.第二卷[M].北京:机械工业出版社, 1991. 40-41.[4] 吴伏家,刘兆华.圆孔拉刀CAD系统研制[J].华北工学院院报, 1996,(增刊): 74-78.13机械优化设计案例3直齿圆柱齿轮传动的优化设计摘要:一、问题描述:现有一单级渐开线直齿圆柱齿轮减速器,其输入功率N=280kW,输入转速n=980r/min,传动比i=5。