振动疲劳试验与CAE分析(动态播放)
典型结构件的振动疲劳分析
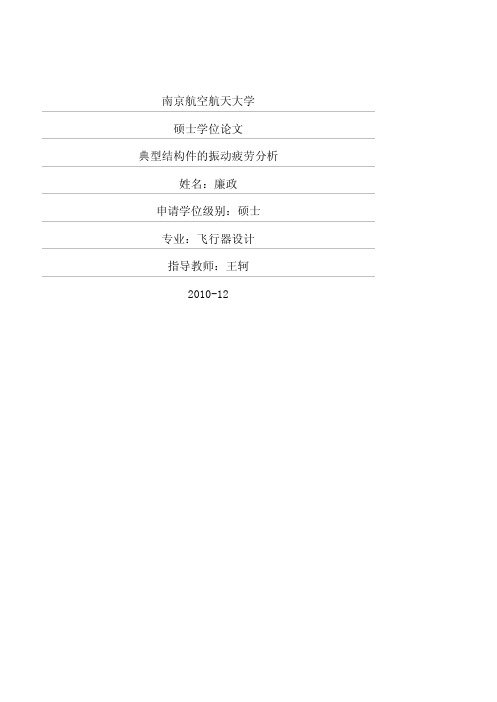
ii
典型结构件的振动疲劳分析
图清单
图 1.1 基础激励振动疲劳试验装置 ........................................................................................ 4 图 1.2 铝合金疲劳裂纹扩展曲线及实物图.............................................................................. 4 图 1.3 复合膜材料疲劳寿命曲线............................................................................................ 5 图 1.4 有机塑料的 S-N 曲线 ................................................................................................... 5 图 1.5 LY12CZ 铝合金动态疲劳 S-N 曲线.........................................................................频率,模型修正,频率变化,裂纹扩展
i
典型结构件的振动疲劳分析
Abstract
At present, the conventional analytical methods of static fatigue has been formed a separate system, and in engineering applications are quite ripe. But in actual environment, the project structure is often working in the environment of the vibration loads, the principal loss of structure is caused by vibration. Only use the idea of static fatigue can not compeletly explain the vibration conditions of failure,because it omits the key role of the changes of frequency . As a result, we take the common typical structure of aircraft as analyzing objects. Futhermore, we use the finite element software of MSC.patran&nastran and fatigue as a platform building dynamic models to study its’dynamic features and fatigue life. This paper put forward a method which considers frequency as a main factor to predict the life of structure. All works of this paper includes: First, we choose unidirectional stiffened plate and linking slab which are widely used in aircraft as objects to complete the structural vibration fatigue experiments under resonant excitation, realizing band motivation of the incentive frequency tracking structure inherent frequency and studying structure life change rule and the dynamic change of natural frequency by the resonance conditions. Results show that structural dynamic characteristics have important influence on fatigue life and nature frequency with the fatigue process is drab degressive. Futhermore, all works Based on the MSC. Patran&nastran platform, establishing the typical structure finite element dynamic model to complete the modal analysis and validate the finite element model is correct. And we use the amended model to analysis structure dynamic response, so as to realize the fatigue life calculation. Moreover, considering frequency variation of structure damage effect, this paper puts forward the frequency as the main parameters of resonance fatigue longevity methods. Through reasonable simplification and assumptions, using the finite element software of ABAQUS to simulate the dynamic structure crack propagation (named frequency of dynamic decreasing process), dynamic analysis is studied on each stages. SN method and damage tolerance are picked to simulate the progress of Adopt SN method, damage tolerance is done by the way under the condition of simulation timely resonance fatigue life. The example shows that the method is simple and reasonable and provides reference for vibration fatigue analysis. Key words : vibration fatigue; typical structure; natural frequency; model modification; frequency change; crack propagation
振动测试与动态信号分析

振动测试与动态信号分析
振动测试是一种重要的工程实验,它可以检测、评估和改进系统的性
能和可靠性。
它主要用于监测和评价物体的结构、动力学和耐久性能。
它
也可以用于诊断故障并提出进一步的维护措施。
振动测试和动态信号分析是振动测试的主要方法之一,它是对系统的
动态性能检测和评估的有效手段。
振动测试可以快速和准确地捕捉原始振
动信号,并将它们可视化。
振动测试还可以检测和分析动态响应,从而从
多个角度了解系统的性能和可靠性。
动态信号分析也是技术测试工作的重要组成部分,它将振动信号进行
信号处理,分析系统的动态行为,可反映系统的状态和性能。
通过这种方法,可以诊断故障类型,指导维护策略,确定不良结构性能,验证设计参数,优化运行状态,等等。
它可以通过模拟检测和实验测试相结合的方式
完成,来获得完整的数据分析和诊断结果,以识别和可靠性评估复杂的机
械系统。
动态信号分析是通过复杂的信号处理方法,对原始振动信号进行分析、可视化和诊断,从而对机械系统的性能和可靠性进行评估。
基于CAE分析的发动机共振问题研究

基于C AE分析的发动机共振问题研究李壮(广西玉柴机器股份有限公司,广西南宁530007)摘要:为解决柴油发动机振动超标问题,分析发动机中的零部件及安装支架等固有频率的同时,需分析发动机总成固 有频率在发动机运行过程中产生的影响,采用C A E分析软件对几种设计方案进行计算分析。
计算结果发现改变整机设计结构,可以提升发动机总成的固有频率,避免发动机常用转速运行过程中产生共振,改善N V H水平。
关键词:柴油发动机;N V H;C A E中图分类号:T K428 文献标识码:A 文章编号:1672-545X( 2021 )03-0156-04〇刖5中国近年来,随着重型卡车技术水平的突飞猛 进,以及道路条件的不断完善,越来越多的商用车辆 选择在高速公路上运送货物。
然而部分车辆在常用 车速行驶时,会出现明显的整车抖动问题。
在长途行 车的过程中,这种异常抖动一方面加剧了驾驶员的 身体疲劳,造成腰肌劳损,令一方面分散驾驶员注意 力,存在安全隐患|1]。
同时随着人们生活水平逐渐提 高,对于驾乘舒适性也提出了更高的要求,尤其是卡 车司机群体呈现年轻化趋势,良好的驾驶体验,也成 为了各个汽车厂产品竞争力的体现,各家商用车企,均在N V H方面投入了大家的研究工作,发动机作为 整车主要的振动噪声来源,动力总成的N V H开发,也成为整车开发的重点工作。
现如今仿真技术的不 断成熟,可代替部分汽车试验,但是仍与实际试验有 部分差异。
同时结合仿真与实际试验,进一步完善试 验步骤,缩小差异,仍需深人了解[\作者针对某款柴油机配套整车,在1300 ~1 400 r/min转速下出现整车共振和车内轰鸣问题,进行原因分析并提出优化设计方案,基于C A E仿真 分析评估优化方案对于发动机及动力总成固有频率 的影响,进而判断优化设计对于整车N V H改进效 果,结果表明对于发动机N V H开发,不单单要考虑 零件本身的固有频率,还需要把整个动力总成看成 整体进行优化设计,提升动力总成的固有频率,避免 在发动机常用转速区域产生共振问题。
随机振动疲劳寿命预测方法研究

随机振动疲劳寿命预测方法研究随机振动疲劳寿命预测方法研究随机振动是指在一定时间内,不同时刻上所发生的振动信号之间存在差异性的振动。
由于许多机械结构都会遭受到不可预测的外界环境干扰,这些外界环境干扰的特性通常被抽象为随机振动。
因此,要准确地预测机械结构的寿命,就必须对其受到的随机振动进行有效的分析和预测。
随机振动分析中的疲劳寿命预测是一个重要的研究内容。
疲劳寿命是指机械结构在设计使用条件下,能够耐受的最大的疲劳应力循环次数或者疲劳应力循环时间。
疲劳寿命预测是指根据机械结构的设计参数和受到的振动信号,预测该机械结构的疲劳寿命。
疲劳寿命预测的方法主要包括:静态疲劳预测方法、静动态耦合疲劳预测方法、单峰值疲劳预测方法和随机振动疲劳预测方法。
由于随机振动疲劳预测方法能更好地反映实际环境,因此,随机振动疲劳预测方法也是最常用的疲劳预测方法之一。
随机振动疲劳寿命预测方法主要依赖于随机振动理论,该理论可以将随机振动过程分解为三个独立的过程:功率谱密度函数、相位移动函数和幅度变化函数。
功率谱密度函数描述了振动的能量分布情况;相位移动函数描述了振动的相位变化;而幅度变化函数则描述了振动的幅度变化。
随机振动疲劳寿命预测的基本原理是:将受到的振动信号转换为功率谱密度函数、相位移动函数和幅度变化函数,然后根据疲劳理论,以及功率谱密度函数、相位移动函数和幅度变化函数作为输入参数,计算出机械结构受到的疲劳应力和应变,从而确定其疲劳寿命。
随机振动疲劳寿命预测可以更加准确地反映机械结构实际的疲劳寿命,尤其是在受到非常复杂的随机振动时,其预测结果更为可靠。
然而,随机振动疲劳寿命预测的计算量较大,而且需要准确的功率谱密度函数、相位移动函数和幅度变化函数,因此,随机振动疲劳寿命预测的可靠性取决于这些函数的准确性。
随机振动疲劳寿命预测方法也可以改进,例如采用改进的功率谱密度函数,改进的相位移动函数,改进的幅度变化函数,以及改进的疲劳理论,以期提高疲劳寿命预测的准确性和可靠性。
电池组随机振动疲劳分析

电池组随机振动疲劳分析本例展示基于功率谱密度曲线(PSD)的电池组疲劳分析,即针对随机振动的疲劳寿命分析。
1 问题设定一块电池组,尺寸为70mm x 175mm x 400mm。
该电池组的两端共有6个端点,分别受到垂直于电池组平面的激励作用,且激励的加速度功率谱密度曲线(ASD)相同。
由于在随机振动基于线性动力学原理,因此电池,PC材料等采用实体建模,其他钣金采用壳单元建模,设定相关的fastener点焊单元,coupling耦合单元和tie约束,建立零件和零件之间相应的连接关系。
两端所对应的PSD谱线如下图。
请注意该曲线的频率截断在200Hz处。
本案例用到的附件包括:battery_SSD.cae 提取前10阶固有模态和扫频分析plate.psd PSD曲线2 分析过程一般来说,针对随机振动的疲劳分析包含两大步。
第一步是在Abaqus中完成固有模态和扫频两个计算;第二步是把这两个计算结果与PSD曲线一起输入fe-safe,运行若干设置后完成疲劳分析,得到相关结果。
2.1 有限元计算需要强调的是,在有限元计算部分,不采用随机振动分析方法,而是采用模态提取和扫频方法。
2.1.1 固有模态分析附件中的battery_SSD.cae第一个step分析步是用于提取固有模态的Abaqus计算文件。
其中的关键设置如下:a) 两端固定b) 提取1~200HZ内的固有模态c) 指定位移U和应力S作为场输出变量2.1.2 扫频分析第二个step分析步是用于扫频分析的Abaqus计算文件。
由于PSD曲线上的最高频率是200Hz,故而扫频分析的最大频率也截断在200Hz。
同时,设定各阶频率对应的阻尼均为2%。
定义单位加速度的base motion激励载荷,用于扫频分析:在输出设定上,对两个扫频分析Step,设定对广义位移GU和GPU的历程输出。
2.2 疲劳计算由前述的固有模态分析和扫频分析,计算得到结果文件:battery_shockZ_fastener.odb。
通过FEA、MBS 和 FEMFAT 对曲轴进行疲劳强度分析

内部节点
接口节点
Author: Robert Wahlmüller
Date: July 2007
7
Component Mode Synthesis 部件模态合成 (Craig Bampton Method)
假定: 柔体具有小的变形 => 部件模态的线性叠加
u
physical coordinates 物理坐标 Modal (Generalized) Coordinates 模态坐标 变换矩阵,包含部件模态
Author: Robert Wahlmüller
Date: July 2007
10
Component Mode Synthesis 部件模态合成 部件模态合成的主要优点:
大大降低了柔体的自由度数量
eg.: dof 100.000
MKK MKI MIK MII
. .K u . .I u
+
. .C q . .N q .. qC .. N q
16
Two Mass Flywheel 双质量飞轮
弹簧和质量系统 (刚性部件) 主要质量通过约束或是刚度进行操纵
齿轮箱 / 试验台轴的影响是主要的
主和次质量的连接通过应用径向约束 (inline) 或是刚度 扭曲和倾斜连接通过应用非线性弹簧(从供应商得到)
M
φ
range 1 range 2 limit stop
= u =
q
C 约束模态Constraint Modes矩阵
q
N 固有模态Normal Modes矩阵
uK
uI
=
I
C
0
N
qC (=uK)
*
qN
机械振动学中的振动与疲劳寿命分析

机械振动学中的振动与疲劳寿命分析机械振动学是研究物体在受到外力或激励下发生振动的学科,通过振动分析可以了解机械系统的动态特性。
在工程实践中,振动分析在设计、优化和故障诊断上起着重要作用。
而振动引起的疲劳破坏也是工程领域中常见的问题。
本文将探讨机械振动学中的振动与疲劳寿命分析,帮助读者更好地理解相关理论和方法。
振动分析是机械系统动态特性分析的重要手段。
振动可以分为自由振动和受迫振动两种情况。
自由振动是指物体在没有外力作用下的振动,其振幅和频率由系统的初始条件确定。
而受迫振动是指物体受到外力作用下的振动,外力的频率与系统的固有频率接近时,会出现共振现象。
通过振动分析,可以得到机械系统的振动模态、频率响应等重要参数,为系统设计和优化提供依据。
疲劳寿命是指机械元件在交变载荷作用下发生疲劳破坏之前可以承受的循环载荷次数。
疲劳破坏是由于材料内部的微观缺陷在循环载荷下逐渐扩展至裂纹并最终导致破坏。
在振动引起的疲劳问题中,振动载荷作用下的应力循环是引起疲劳破坏的主要原因。
疲劳寿命分析是通过计算机模拟或实验手段确定机械元件在特定工况下的疲劳寿命,以预防疲劳破坏的发生。
振动与疲劳寿命之间存在着密切的联系。
振动会引起机械元件受到动态载荷作用,导致应力的集中和变化;而应力的集中和变化则是疲劳破坏的主要因素。
因此,在设计机械系统时,需要综合考虑振动对元件疲劳寿命的影响,采取相应的措施减小振动幅值和频率,提高元件的疲劳寿命。
在实际工程中,振动与疲劳寿命分析是不可或缺的环节。
通过有限元分析、模态试验等手段,可以对机械系统进行振动模态分析,得到系统的动态响应特性;同时,通过疲劳实验和寿命预测方法,可以评估元件在实际工作条件下的疲劳寿命,为系统的可靠性设计提供依据。
综上所述,机械振动学中的振动与疲劳寿命分析是研究机械系统动态特性和耐久性的重要内容。
通过振动分析和疲劳寿命评估,可以优化机械系统的设计,延长元件的使用寿命,提高系统的稳定性和可靠性。
应用CAE技术进行空调管路的振动分析 (1)
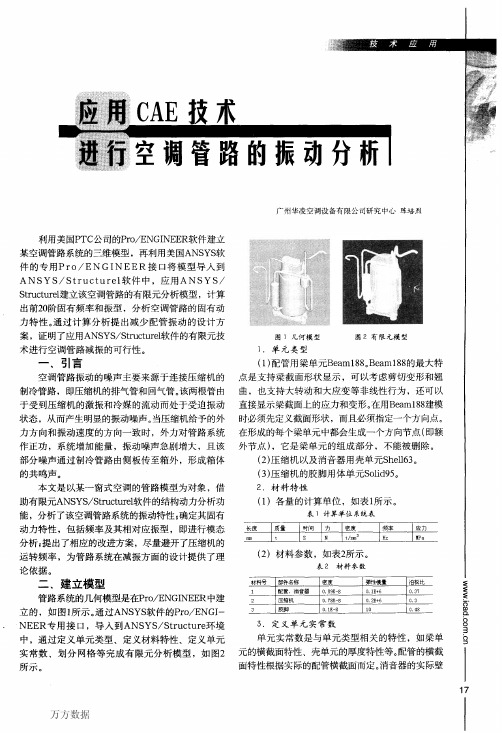
作正功,系统增加能量,振动噪声急剧增大,且该 外节点),它是梁单元的组成部分,不能被删除。
部分噪声通过制冷管路由侧板传至箱外,形成箱体
(2)压缩机以及消音器用壳单元SheⅡ63。
的共鸣声。
(3)压缩机的胶脚用体单元Solid95。
本文是以某一窗式空调的管路模型为对象,借
2.材料特性
助有限元ANSYS/Stnlcturel软件的结构动力分析功
2004(5)
9.赵文龙.张增学.李立斌 有限元技术在空调器管路振动分析及设计优化中的应用[期刊论文]-华南农业大学学报
(自然科学版) 2004(3)
本文链接:/Periodical_cadcamyzzyxxh200201008.aspx
醚羲蠢麓垂薹秘黼豢j篱蠹稳豢粪黧滋溯霸鬻糍囊誓。蕤。 o∞9罄悭。÷l瓣纛矧滔!|垂连冁i谶趟鞫瞧|;||!囊l《瀚鬟黝黼靛黼畿豢豢黼灞藿穗隧嚣龋避i登醚l|:蠹鞫图。i滔戳粒l戳篷i鞘黼麟|||l黼鬣豢潮懑l誊戳j
o o
;i
一i
。
jo];ii。邋露潼透置露逐繁熊l受筮舞瓣裁蠢鬻娥蠢缝瓣糕燧麓谶鬟黻獯襻鞭镳镶麟麓爨麟凝蠹蝴|鬣|||麓Y 浚Ⅵ 镰麓豢纛!嚣灌黍黼羧灏麓麓魏麟.|粼鏊凌燃麓粼攀隧燃稳纛鼗鼗鞫裁粼纛麟终浚溅遴豢羹i|麓||爨|iii
10
O 48
NEER专用接口,导人到ANSYS/Structure环境
3.定义单元实常数
中,通过定义单元类型、定义材料特性、定义单元
单元实常数是与单元类型相关的特性,如梁单
≤ ≤.|c∞Q_corn_c3
实常数、划分网格等完成有限元分析模型,如图2 所示。
元的横截面特性、壳单元的厚度特I生等。配管的横截 面特性根据实际的配管横截面而定。消音器的实际壁
- 1、下载文档前请自行甄别文档内容的完整性,平台不提供额外的编辑、内容补充、找答案等附加服务。
- 2、"仅部分预览"的文档,不可在线预览部分如存在完整性等问题,可反馈申请退款(可完整预览的文档不适用该条件!)。
- 3、如文档侵犯您的权益,请联系客服反馈,我们会尽快为您处理(人工客服工作时间:9:00-18:30)。
5
1.1 应力疲劳与振动疲劳对比
计算流程
6
JS Bendat,1964
1.2 振动疲劳理论发展过程
PSD循环计数
T Dirlik,1985 C Lalanne,1992
1.Rayleigh分布,仅适用于 窄带信号
2.基于Dirlik、Rayleigh、 Gaussian分布,适用于宽 带信号
楔子
什么原因引起? 怎么故障再现? 如何结构优化? 如何快速验证?
3
1.1 应力疲劳与振动疲劳对比
类型
疲劳试验
寿命计算
适用范围
应用举例
应力疲劳 通过迭代技术, S-N法 (时域再现) 对非平稳随机过 E-N法
程的精确描述
振动疲劳 对平稳随机过程 Dirlik模型 (频域再现) 的统计学模拟 Lalanne
振动疲劳试验与CAE分析
•
车身研究院试验检测所
•
毛招凤
•
2014.8.28
CONTENTS
01 振动疲劳概述 02 试验场数据采集与分析 03 台架振动加载谱合成 04 台架振动试验与寿命计算 05 动态响应与疲劳仿真分析
1
1
振动疲劳概述
2
C-9A驾驶室 在挖掘岩石、 破碎锤冲击等 恶劣工况下出 现开裂
PSD 0.01068 0.01898 0.01305 0.08158 0.07755
4
台架振动试验与寿命计算
21
4.1 C-9B驾驶室结构
C-9A
型材骨架
+
C-9B
=
22
4.2 台架振动试验
C-9B驾驶室
23
标准谱1.5倍强度,X方向
16Hz 5Hz
500Hz
台架振动
7Hz 100Hz
综合工况加载谱,X方向
10
2.2 振动数据分析
怠速Z 高速Z 挖掘Z
11
◆ 465挖机在高速行走与挖 掘工况时,发动机转速在 1900RPM 附 近 , 依 此 计 算 发动机的各阶频率。
◆驾驶室安装平台Z 方向在 32 Hz、95 Hz、185 Hz、 295 Hz、601 Hz、898 Hz、 1220 Hz分别为发动机的1阶、 3阶、6阶、9阶及主泵的18 阶、27阶、36阶激励频率;
5.3 疲劳寿命计算
—— 减振前
—— 减振后
12
3
台架振动加载谱合成
13
3.1 载荷谱组合
时域叠加
14
3.2 大挖综合工况
综合工况加载谱合成方案
序号
原始数据
原始时长
1
怠速运行
15s
2
低速行走
35s
3
高速行走
30s
4
挖掘泥土
65s
5
挖掘碎石
50s
6
挖掘矿山
60s
备注:设计寿命以10000h计, 延长倍数=36000000×权重÷原始时长
4.3 局部位置应力分析
7Hz 50Hz
500Hz
再次映证5-100Hz的振动是 造成局部开裂的主要原因,“B 柱上转角”在7-8Hz附近出现应 力峰值,与路面激励8Hz重叠。
8Hz
100Hz
24
4.4 应力疲劳寿命计算流程
25
标准谱1.5倍强度,X方向
4.5 局部位置寿命计算
振动数据时长5min,疲劳 寿命计算累计7.1h,实际 振动2.5h出现开裂
权重
5% 5% 10% 10% 40% 30%
延长倍数
120000 51430 120000 55380 288000 180000
15
3.3 加载谱合成流程
SRS
根据寿命等效原 则将4min15s的振 动外推到10000h
FDS
16
3.3 加载谱合成流程
基于累积寿命等效原则
17
3.3 台架振动加载谱 X
频率(Hz) 20 70 100
PSD 0.00304 0.00304 0.00626
19
3.3 台架振动加载谱 Z
频率(Hz) 3 5 6 11 15
PSD(g2/Hz) 0.00025 0.00452 0.01281 0.02799 0.03226
频率(Hz) 30 38 44 88 100
20
标准谱1.5倍强度
Max
510.97
Min
-841.22
Range
1352.19
Damage 1.17E-2
台架振动
局部损伤计算
综合工况加载谱,X方向
振动数据时长8min,疲劳 寿命计算累计5.4万h,实 际振动10h未出现开裂
26
综合工况加载谱
Max Min Range Damage
94.09 -89.87 183.96 2.46E-06
模型
结构件受力状态明确,激励 铲斗
载荷便于获取,需要用力、 挖机两臂
位移信号加载
轴耦合道路模拟
结构复杂,受力情况复杂, 难于获得准确的受力载荷, 载荷来源于海浪、风力、轮 胎等随机激励,需要大幅度 加速试验或加速计算,可以 用加速度PSD加载
驾驶室 油箱 水箱 散热器支架 座椅 电气安装支架
4
1.1 应力疲劳与振动疲劳对比
5
动态响应与疲劳仿真分析
27
5.1 疲劳分析流程
E、σ、ρ 、SN、表面处理
结构、尺寸、应力集中系数
1. 动态响应分析 MSC.Nastran
2. 寿命预测 nCode Designlife
1.
2.
28
5.2 动态响应分析
SOL 111
29
5.2 动态响应分析
10Hz
37Hz
46Hz
30
75Hz
3.利用Rayleigh、Gaussian 分布按一定的权重比例组 合,适用于宽带信号
7
1.3 振动疲劳问题研究流程
样机 数据采集
CAD模型 有限元模型
数据处理
PSD激励
频率响应分析
合成加载谱
S-N曲线
随机疲劳分析
台架振动试验
疲劳寿命计算
结构优化建议
8
2
试验场数据采集与分析
9
2.1 振动数据采集
频率(Hz)
3 5 7 18
PSD(g2/Hz)
0.00160 0.00567 0.00954 0.00084
频率(Hz)
30 45 55 100
PSD
0.00213 0.00101 0.00192 0.00192
18
3.3 台架振动加载谱 Y Nhomakorabea频率(Hz) 3 5 9
PSD(g2/Hz) 0.00092 0.00556 0.02744
◆高速行走与挖掘工况下, 8 Hz、13Hz的响应频率应 为来自地面激励;
◆ 465高速行走与挖掘工况 的加速度RMS大致相当,约 为 怠 速 工 况 加 速 度 RMS 的 4~5倍。
2.2 振动数据分析
怠速X 怠速Y 怠速Z
◆减振器对100Hz以 上的振动具有较好的 隔振效果。 ◆由于驾驶室的主要 整体模态在100Hz以 下,且 5Hz以下振动 台驱动困难。 ◆建议驾驶室振动试 验与CAE分析的频率 范围设置为5-100Hz, 既能覆盖绝大部分损 伤又能节省计算资源