七、铝的电化学氧化法
铝及铝合金的电化学氧化
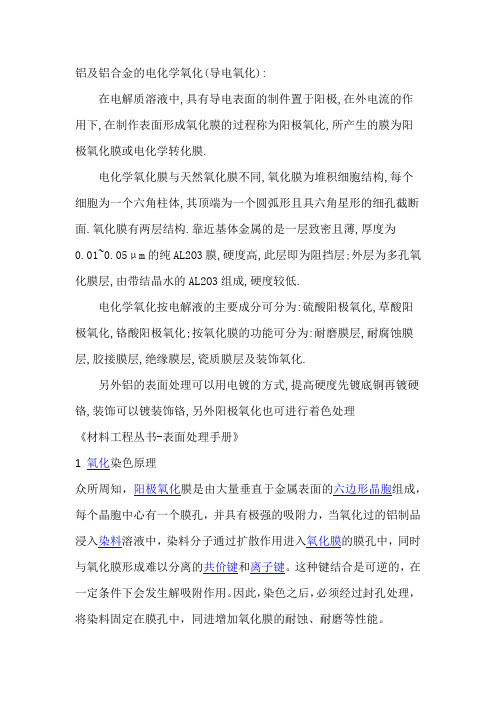
铝及铝合金的电化学氧化(导电氧化):在电解质溶液中,具有导电表面的制件置于阳极,在外电流的作用下,在制作表面形成氧化膜的过程称为阳极氧化,所产生的膜为阳极氧化膜或电化学转化膜.电化学氧化膜与天然氧化膜不同,氧化膜为堆积细胞结构,每个细胞为一个六角柱体,其顶端为一个圆弧形且具六角星形的细孔截断面.氧化膜有两层结构.靠近基体金属的是一层致密且薄,厚度为0.01~0.05μm的纯AL2O3膜,硬度高,此层即为阻挡层;外层为多孔氧化膜层,由带结晶水的AL2O3组成,硬度较低.电化学氧化按电解液的主要成分可分为:硫酸阳极氧化,草酸阳极氧化,铬酸阳极氧化;按氧化膜的功能可分为:耐磨膜层,耐腐蚀膜层,胶接膜层,绝缘膜层,瓷质膜层及装饰氧化.另外铝的表面处理可以用电镀的方式,提高硬度先镀底铜再镀硬铬,装饰可以镀装饰铬,另外阳极氧化也可进行着色处理《材料工程丛书-表面处理手册》1 氧化染色原理众所周知,阳极氧化膜是由大量垂直于金属表面的六边形晶胞组成,每个晶胞中心有一个膜孔,并具有极强的吸附力,当氧化过的铝制品浸入染料溶液中,染料分子通过扩散作用进入氧化膜的膜孔中,同时与氧化膜形成难以分离的共价键和离子键。
这种键结合是可逆的,在一定条件下会发生解吸附作用。
因此,染色之后,必须经过封孔处理,将染料固定在膜孔中,同进增加氧化膜的耐蚀、耐磨等性能。
2 阳极氧化工艺对染色的影响在氧化染色整个流程中,因为氧化工艺原因造成染色不良是比较普遍的。
氧化膜的膜厚和孔隙均匀一致是染色时获得均匀一致颜色的前提和基础,为获得均匀一致的氧化膜,保证足够的循环量,冷却量,保证良好的导电性是举足轻重的,此外就是氧化工艺的稳定性。
硫酸浓度,控制在180—200g/l。
稍高的硫酸浓度可促进氧化膜的溶解反应加快,利于孔隙的扩张,更易于染色;铝离子浓度,控制在5—15 g/l。
铝离子小于5g/l,生成的氧化膜吸附能力降低,影响上色速度,铝离子大于15g/l时,氧化膜的均匀性受到影响,容易出现不规则的膜层。
铝合金防氧化的方法

铝合金的防氧化方法有多种,以下是几种常见的方法:
1. 氧化膜形成:铝合金表面会自然形成一层氧化膜,这层氧化膜能够提供一定
的防腐蚀和防氧化保护。
你可以通过定期清洁铝合金表面,确保其光洁度和整洁度,有助于维持氧化膜的完整性。
2. 电化学氧化:电化学氧化是一种常见的表面处理方法,通过在铝合金表面施
加电流,使铝表面形成坚硬的氧化膜。
这种氧化膜不仅能提供防腐蚀和防氧化的保护,还可以增加铝表面的硬度和耐磨性。
3. 防腐涂层:在铝合金表面涂覆一层防腐涂层可以提供额外的保护。
常用的防
腐涂层包括有机涂层和无机涂层。
有机涂层如油漆和涂层能够形成一个障碍层,阻隔空气和水分对铝合金的侵蚀。
无机涂层如阳极氧化涂层则能够在铝表面形成坚硬的保护层。
4. 阳极氧化:阳极氧化是一种常用的铝合金表面处理方法,通过在电解液中将
铝合金作为阳极,在电流的作用下形成致密的氧化膜。
这种氧化膜具有较高的硬度和耐腐蚀性,能够有效地防止氧化。
5. 化学处理:化学处理是利用化学方法对铝合金表面进行处理,以形成保护层。
例如,可以使用酸洗或碱洗等方法去除铝表面的氧化层,并在处理后立即进行涂层或阳极氧化,以增加铝表面的防氧化性能。
需要注意的是,选择适当的防氧化方法应根据具体的应用需求和铝合金的使用环境来决定。
在实际应用中,可能会采用多种方法的组合来达到更好的防氧化效果。
建议在使用之前咨询专业人士或参考相关技术文献,以确保选择适合的防氧化方法。
铝合金表面阳极氧化处理

铝合金表面阳极氧化处理铝合金表面阳极氧化处理是一种常见的表面处理技术,也被称为电化学氧化或阳极处理。
它是通过在铝合金表面形成一层氧化膜来改善其耐腐蚀性、硬度和耐磨性。
这种氧化膜通常具有良好的耐热性、耐磨性、绝缘性和美观性,因此广泛应用于航空、汽车、建筑、电子等行业。
铝合金表面阳极氧化处理的过程是将铝合金制品作为阳极,置于电解质溶液中,通电时在表面形成一层氧化膜。
电解质溶液通常是含有硫酸、草酸、硫酸铬等成分的溶液。
在电解质溶液中通电时,阳极表面的铝原子会与氧离子结合形成氧化物,这些氧化物会在阳极表面形成一层致密的氧化膜。
这种氧化膜的厚度、硬度和颜色等特性可以通过调整电解质溶液的成分、温度、电流密度等参数来控制。
铝合金表面阳极氧化处理的优点包括:1.提高耐腐蚀性:通过形成致密的氧化膜,可以有效地提高铝合金的耐腐蚀性,使其在恶劣环境下更加耐用。
2.提高硬度和耐磨性:氧化膜的硬度可以达到200-500HV,比铝合金本身的硬度高出数倍,因此可以有效地提高铝合金的耐磨性和耐划伤性。
3.美观性好:氧化膜的颜色可以根据需要进行调整,可以制成金色、银色、黑色、蓝色等不同颜色的氧化膜,从而提高铝合金制品的美观性。
4.绝缘性好:氧化膜具有良好的绝缘性能,可以用于制作电子器件、电解电容器等。
铝合金表面阳极氧化处理的缺点包括:1.成本较高:阳极氧化处理需要专门的设备和工艺,成本较高。
2.氧化膜厚度不易控制:氧化膜的厚度受到多种因素的影响,不易精确控制,可能会导致产品质量不稳定。
3.容易受到机械损伤:氧化膜的硬度虽然很高,但容易受到机械损伤,因此需要注意保护。
总的来说,铝合金表面阳极氧化处理是一种有效的表面处理技术,可以提高铝合金制品的耐腐蚀性、硬度和美观性,广泛应用于航空、汽车、建筑、电子等行业。
铝合金化学导电氧化最佳配方

铝合金化学导电氧化最佳配方铝合金化学导电氧化,这听起来好像是个高大上的话题,其实说白了就是让铝合金表面变得更耐用、更好看,同时还能提升它的导电性。
哎,咱们先把这话说清楚。
铝合金就是那种轻便又结实的金属材料,常常用在飞机、汽车,还有各种家电上。
可惜了,原本这么好的材料,要是表面没处理好,时间一长就容易氧化、变色,真是可惜。
想要让铝合金焕发第二春,化学导电氧化就是一个好办法,听起来是不是就觉得特别牛?什么是化学导电氧化呢?这可不是说随便往铝合金上撒点东西就行的哦。
这里面可是有一套讲究的。
简单来说,就是利用化学反应让铝合金表面形成一层保护膜。
这层膜不仅可以抵抗腐蚀,还能增强导电性,真是一举两得。
想象一下,你家的电器用上这样的铝合金,是不是就像是给它穿上了一层铠甲?再也不用担心外面的环境会对它造成伤害,心里可踏实多了。
咱们接下来聊聊最佳配方,这可是关键中的关键。
咱们得选择适合的化学药剂。
这可不是随便买瓶什么药水就能搞定的,得根据铝合金的成分和要求来定。
一般来说,硫酸铝和氟化铝都是不错的选择。
这两种材料能帮助铝合金形成一层致密的氧化膜,效果杠杠的。
哎,这里边可得注意浓度问题,浓度高了,反应速度快,但也容易损伤铝合金的表面;浓度低了,反应太慢,效果也不明显,真是有点儿让人头疼。
然后就是温度和时间,这俩也是不能忽视的因素。
温度过高,化学反应迅速,但容易让膜层不均匀,甚至起泡;温度太低,又反应慢,膜层太薄,根本达不到预期的效果。
一般来说,控制在20到30摄氏度之间最为合适。
时间方面,通常在20到60分钟之间,具体还得根据铝合金的厚度和预期效果来调整,真是个细致活儿啊。
咱们还得考虑到后处理。
化学氧化完了,可不是就完事了,后续处理也得跟上。
洗涤、干燥、封闭这些步骤不能少,这样才能确保膜层的质量。
很多人以为这步骤随便搞搞就行,实际上,细节决定成败,做得好,膜层才能更加耐磨、耐腐蚀,还能提升导电性。
想象一下,这样的铝合金就像一位运动员,经过严格的训练,最终迎来了辉煌的时刻。
铝与铝合金的氧化处理一般知识介绍

铝与铝合金的氧化处理铝及铝合金在大气中虽能自然形成一层氧化膜,但膜薄(40- 50A)而疏松多孔,为非晶态的、不均匀也不连续的膜层,不能作为可靠的防护、装饰性膜层。
随着铝制品加工工业的不断发展,在工业上越来越广泛地采用阳极氧化或化学氧化的方法,在铝及铝合金制件表面生成一层氧化膜,以达到防护、装饰的目的。
一、经化学氧化处理获得的氧化膜,厚度一般为~4um,质软、耐磨和抗蚀性能均低于阳极氧化膜。
所以,除有特殊用途外,很少单独使用。
但它有较好的吸附能力,在其表面再涂漆,可有效地提高铝制品的耐蚀性和装饰性。
二、经阳极氧化处理获得的氧化膜,厚度一般在5-20um,硬质阳极氧化膜厚度可达60- 250um。
其膜层还具有以下特性:(1)硬度较高。
纯铝氧化膜的硬度比铝合金氧化膜的硬度高。
通常,它的硬度大小与铝的合金成份、阳极氧化时电解液的技术条件有关。
阳极氧化膜不仅硬度较高,而且有较好的耐磨性。
尤其是表面层多孔的氧化膜具有吸附润滑剂的能力,还可进一步改善表面的耐磨性能。
(2)有较高的耐蚀性。
这是由于阳极氧化膜有较高的化学稳定性。
经测试,纯铝的阳极氧化膜比铝合金的阳极氧化膜耐蚀性好。
这是由于合金成分夹杂或形成金属化合物不能被氧化或被溶解,而使氧化膜不连续或产生空隙,从而使氧化膜的耐蚀性大为降低。
所以,一般经阳极氧化后所得的膜必须进行封闭处理,才能提高其耐蚀性能。
(3)有较强的吸附能力。
铝及铝合金的阳极氧化膜为多孔结构,具有很强的吸附能力,所以给孔内填充各种颜料、润滑剂、树脂等可进一步提高铝制品的防护、绝缘、耐磨和装饰性能。
(4)有很好的绝缘性能。
铝及铝合金的阳极氧化膜,已不具备金属的导电性质,而成为良好的绝缘材料。
(5)绝热抗热性能强。
这是因为阳极氧化膜的导热系数大大低于纯铝。
阳极氧化膜可耐温1500℃左右,而纯铝只能耐660℃。
综上所述,铝和铝合金经化学氧化处理,特别是阳极氧化处理后,在其表面形成的氧化膜具有良好的防护、装饰等特性。
铝阳极氧化工艺原理

铝阳极氧化工艺原理铝阳极氧化是一种常用的表面处理工艺,用于提高铝材的防腐蚀性能、硬度和耐磨性。
其原理是在铝材表面形成一层致密的氧化膜,该膜具有良好的耐腐蚀性能,并能增加材料的硬度。
铝阳极氧化工艺主要包括预处理、阳极氧化和封孔三个步骤。
第一步,预处理。
在进行阳极氧化之前,需要对铝材进行预处理,以去除表面的污垢和氧化层。
常用的预处理方法有碱洗和酸洗两种。
碱洗可以去除表面的油污和有机物,酸洗则可去除表面的氧化层和金属杂质。
第二步,阳极氧化。
阳极氧化是指将铝材作为阳极,通过直流电流的作用,在电解液中形成一层氧化膜的过程。
电解液通常是硫酸、草酸或硫酸铬等,其中硫酸电解液是最常用的。
在阳极氧化过程中,阳极和阴极通过电解液相互连接,形成电流回路。
当电流通过阳极时,阳极表面的铝材会与电解液中的氧发生反应,形成氧化膜。
氧化膜的厚度和性能可以通过调节电流密度、电解液浓度和温度等参数来控制。
第三步,封孔。
阳极氧化后的氧化膜表面存在微小的气孔,这些气孔会影响氧化膜的耐腐蚀性能。
因此,在阳极氧化后需要进行封孔处理,以提高氧化膜的致密性。
封孔的方法通常是将氧化膜浸泡在热水或镁盐溶液中,使氧化膜中的孔隙被填充。
铝阳极氧化工艺的原理是利用电化学反应,在铝材表面形成一层致密的氧化膜。
这层氧化膜具有良好的耐腐蚀性能,能够保护铝材不受外界环境的侵蚀。
同时,阳极氧化还能增加氧化膜的硬度,提高铝材的耐磨性。
这使得铝材在工业生产中被广泛应用于制造各种耐腐蚀、耐磨损的部件和产品。
在实际应用中,铝阳极氧化工艺可以根据不同需求进行调整和改进。
例如,可以通过改变电解液的配方和工艺参数来控制氧化膜的颜色和厚度,以满足不同外观和性能要求。
此外,还可以采用阳极氧化与其他表面处理工艺相结合,如着色、电泳涂装等,以进一步改善铝材的表面性能和装饰效果。
铝阳极氧化工艺利用电化学反应在铝材表面形成致密的氧化膜,提高了铝材的防腐蚀性能、硬度和耐磨性。
该工艺简单易行,成本低廉,广泛应用于各个领域,为铝材的加工和应用提供了有效的解决方案。
铝氧化处理方法
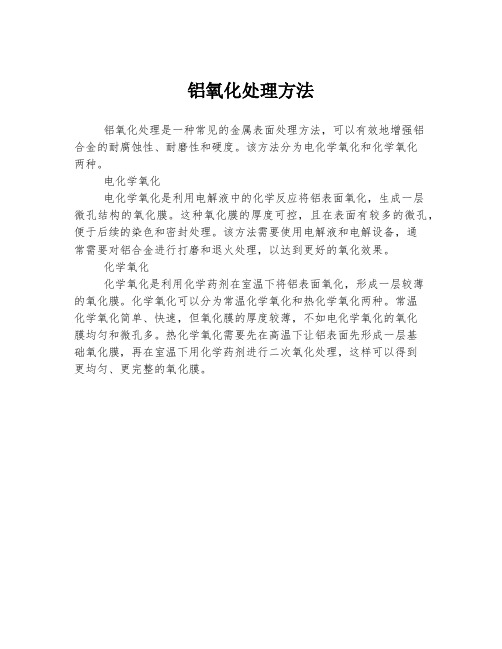
铝氧化处理方法
铝氧化处理是一种常见的金属表面处理方法,可以有效地增强铝
合金的耐腐蚀性、耐磨性和硬度。
该方法分为电化学氧化和化学氧化
两种。
电化学氧化
电化学氧化是利用电解液中的化学反应将铝表面氧化,生成一层
微孔结构的氧化膜。
这种氧化膜的厚度可控,且在表面有较多的微孔,便于后续的染色和密封处理。
该方法需要使用电解液和电解设备,通
常需要对铝合金进行打磨和退火处理,以达到更好的氧化效果。
化学氧化
化学氧化是利用化学药剂在室温下将铝表面氧化,形成一层较薄
的氧化膜。
化学氧化可以分为常温化学氧化和热化学氧化两种。
常温
化学氧化简单、快速,但氧化膜的厚度较薄,不如电化学氧化的氧化
膜均匀和微孔多。
热化学氧化需要先在高温下让铝表面先形成一层基
础氧化膜,再在室温下用化学药剂进行二次氧化处理,这样可以得到
更均匀、更完整的氧化膜。
铝件导电氧化和阳极氧化

铝件导电氧化和阳极氧化铝是一种常见的金属材料,因其轻质、强度高、耐腐蚀等特点,广泛应用于电子、汽车、航空航天、建筑等行业中。
然而,铝面临的一个问题是,其表面容易氧化,导致其导电性变差,从而影响其使用效果。
因此,铝件的导电氧化和阳极氧化技术得到了广泛的研究和应用。
本文将介绍铝件的导电氧化和阳极氧化过程及其应用。
一、导电氧化技术导电氧化技术是通过在铝材表面形成一层氧化膜,使其具有较好的导电性能,从而实现对铝件表面的防腐蚀和增强其结构性能的目的。
目前常用的导电氧化工艺有紫外线辐射法、微波辐射法、脉冲电解法、电化学氧化法等。
1.紫外线辐射法紫外线辐射法是一种新兴的导电氧化技术,其主要原理是在紫外光照射下,铝材表面形成自组织氧化膜。
它的优点在于加工时间短、工艺简单、能耗低、成本较低,同时所形成的氧化膜均匀、致密,具有较好的导电性能。
2.微波辐射法微波辐射是在高频电场的作用下,利用铝与氧化还原剂反应得到氧化膜的方法。
其优势在于导电性能优异,且氧化膜表面平整光洁,粗糙度低,表面孔洞少,防腐蚀性能较好。
另外,微波辐射法的工艺稳定,操作简单,但其成本较高。
3.脉冲电化学氧化法脉冲电化学氧化法是一种新型的导电氧化技术,其主要原理是在铝材表面施加脉冲电流,由于脉冲电流存在间歇性,因此能够形成致密均匀的氧化膜,且导电性能好。
脉冲电化学氧化法对处理铝材的厚度、形状、大小、数量等几乎没有限制,优点在于工艺可控性好,操作简单,加工速度快。
4.电化学氧化法电化学氧化法是较常见的一种导电氧化技术,其通过电解处理,在铝材表面生成含Al2O3的氧化膜,从而实现防腐蚀和导电的目的。
电化学氧化法具有操作简单、成本低、处理效果好等优点。
但其缺点在于钝化剂、电压、电解质的选择必须谨慎,并且加工时间较长。
二、阳极氧化技术阳极氧化技术是一种特殊的电化学氧化技术,它通过加强电压,使氧化膜生成速度大幅提高,从而得到更厚、更硬的氧化膜。
相比于导电氧化技术,阳极氧化技术所形成的氧化膜硬度高,耐用性好,防腐蚀性强。
- 1、下载文档前请自行甄别文档内容的完整性,平台不提供额外的编辑、内容补充、找答案等附加服务。
- 2、"仅部分预览"的文档,不可在线预览部分如存在完整性等问题,可反馈申请退款(可完整预览的文档不适用该条件!)。
- 3、如文档侵犯您的权益,请联系客服反馈,我们会尽快为您处理(人工客服工作时间:9:00-18:30)。
七、铝的电化学氧化法在工业生产中,采用电化学氧化主要的电解液有三种:硫酸、草酸、和铬酸。
根据电解条件的不同,在这些电解液里,可以获得不同厚度的、具有不同机械和物理—化学性能的氧化膜。
电化学铝氧化机理:以硫酸为例,硫酸在水溶液中以离子状态存在:H2SO4↔2H+SO42-水本身也有一部分离解为H+和OH-。
在外加电压的作用下,阳离子[H+]移向阴极并在阴极还原发生氢气。
H++e↔H→H2↑阴离子[OH-]和[SO42-]移向阳极。
在氧化工艺条件下,保持只有OH-的放电,而未达到SO4-放电电位,这是因为OH-容易失去电子的缘故。
所以在阳极OH-失去电子生成水和新生态氧;2 OH- -2e→H2O+[O]在这一过程中,从反应式可以看出硫酸是没有消耗的,而新生态氧[O]则是由H2O分子离解除的OH-放电产生的。
新生态氧的氧化能力很强,可以和AL反应生成Al2O3的氧化膜:2Al+3[O] →Al2O3(阳极)由于硫酸对金属铝和氧化膜都有溶解作用,所以在氧化过程中,还存在在以下二个化学反应:2Al+3H2SO4→Al2(SO4)3+3H2↑Al2O3+3H2SO4→Al2(SO4)3+3H2O↑从以上可知,而整个电解反应中,存在着电化学反应和化学反应两个过程。
电化学反应是膜的生产过程,化学反应式膜的溶解过程。
只有当生成速度大于溶解速度时氧化膜才能生长,并保持一定厚度。
在通电时,与电解接触的表面首先形成无孔,而绝缘一层薄膜(内层)本来膜不会再生长,因为该膜将底金属与电解液隔绝,但在内层形成的同时,膜就开始溶解而呈不均一性。
某些薄的地方电阻较小,电流就集中在这里,把膜击穿,使电解液能通过膜孔而继续与底金属作用,而生成新的内层。
原来的内层,由于电解液的溶解作用,生成多孔性的外层。
内层的生成和溶解在整个氧化过程中是不断进行的:当膜在一定厚度时,膜的溶解速度小于生成速度,以致使膜不断增厚,因此阳极氧化所取得膜是整片玻璃状的无水氧化铝(Al2O3)组成的,其厚度始终变化不大,一般在0.01~0.1微米之间。
而膜的外层较软,是由氧化铝(Al2O3*H2O)组成,多孔,孔呈毛细管形圆锥状,其小孔所占的区域占膜总体积约10~15%,这些小孔就是染色时吸附染料的地方。
阳极氧化处理方法和类型:1.硫酸氧化工艺:硫酸氧化法目前广泛应用在防护装饰性的阳极氧化处理方面。
硫酸氧化法工艺有以下优点:(1)膜层较厚,表面色泽为透明无色,吸附能力好,有利于染着各种鲜艳的色彩。
(2)本工艺操作简单,电能消耗较小,不需要高压电源。
(3)生成效率高,氧化时间短。
(4)槽液毒性小,槽液价格便宜。
(5)溶液温度,生产操作易掌握。
(6)适用范围广,故在工业上得到广泛应用。
它的缺点:(1)氧化温度一般控制在15~25℃,在氧化过程中,由于产生大量的热量,使电解液温度很快升高,因此在生产中必须有冷却装置。
(2)不适合松孔度大的铸件,点焊件或铆接的组合件。
表9 硫酸氧化工艺配方与操作条件硫酸氧化液配置方法:先计算电解槽的容积和所需硫酸量,加入3/4容积的蒸馏水或去离子水,然后打开搅拌设备,将所需的硫酸在强力的搅拌下缓缓加入槽液中,然后加水至规定容积,冷却至工艺规范,化学分析电解液后试生产。
硫酸规格最好采用试剂硫酸或电池硫酸,如用工业硫酸配制,配制后可加入1毫升/升双氧水。
配制硫酸氧化液时不可将水加入硫酸中,否则会引起爆炸。
硫酸氧化液中成份作用及操作条件影响:(1)硫酸浓度的影响:硫酸浓度对氧化膜有一定的影响。
通常采甩15~20%的硫酸组成电解液,在浓的溶液里,膜的溶解速度快,但在实际生产中,开始氧化时膜的成长速度,在浓溶液中要比稀溶液快,随着时间的延长,浓溶液中的成长速度要比稀溶液成长速度缓慢,一般在高浓度硫酸中氧化膜层的溶解速度越快,孔隙率高,透明度好,容易染色,但膜的硬度,耐磨性等较差。
在稀的硫酸液中所获得的氧化膜,坚硬耐磨,反光性能好,但孔隙率低只适宜染成淡色。
当硫酸浓度不同时,生成的氧化膜的质量和电解时间的关系如图(10)所示。
交流电氧化由于一半时间处于阴极半周期,所以氧化液的硫酸浓度通常控制在100-150克/升之间,膜的透明度要比直流电氧化差、如图:硫酸浓度对氧化膜成长速度的影响图中1. 5%硫酸曲线2.20%硫酸曲线(2)电解液温度的影响槽温太低氧化膜发脆,槽温高会使氧化膜疏松。
工作温度对氧化膜厚度影响如图:(11)所示。
从图中可见:温度升高,氧化膜厚度减小,例温度由20℃升高到50℃时,膜的厚度减少90%以上,这是由于温度升高加速了膜的溶解所致。
在氧化过程中是放热过程,铝和氧进行化合反应;2A+3[O] →AL203+399卡在生成AL203有大量化合物热放出来,而这一反应集中在孔穴底部,所以热量也聚集在这里,它随着溶液在孔中的流动将热量带给槽中,使整个槽液温度上升。
为此需采用冷却措施,以控制槽温15~25℃范围内。
(3)电流密度的影响:阳极氧化时,提高电流密度,能够增大氧化膜的生长速度,但氧化膜较粗糙,反光性能较差。
在高的电流密度下氧化会导致铝及其表面附近的电解液局部发热,同时膜被腐蚀,一般有较好的冷却系统和搅拌,却不致因产生焦耳热影响而引起氧化膜的腐蚀、对于装饰性阳极氧化的制件宜采用0.5~1安培/分米2的电流密度及低温下进行氧化,才能获得一定厚度,硬度,耐磨性氧化膜、如电流过大,会使染色不均匀着色表面发生花点的缺陷。
(4)氧化时间:氧化时间的选择取决于电解液的硫酸浓度,工作条件,镀液温度。
氧化膜在开始时至一小时内的成长速度几乎时直线上升,速度较快,但随时间的延长而逐步减缓,是由于膜层厚、电阻加大,影响到导电能力、如图(12)所示在20%硫酸溶液中,用1安培/分米2直流电的电流密度于不同时间所获得氧化膜层度曲线、经过长时间实验,得到氧化时间的经验公式为:氧化时间(分)=2.5*(40-t)t=槽温(℃)一般氧化时间控制在40~60分钟。
(5)硫酸氧化槽搅拌:在硫酸中进行铝及其合金的阳极氧化时,由于产生大量热,它将破坏工艺最适宜的温度,导致质量下降,为了保证氧化过程所需求的温度范围,除了有冷却措施,还必须采用搅拌措施。
这对保证电解液温度均匀性,强化冷却效果以及直接从阳极加工的工件表面带走热量非常有效。
生产中采用的搅拌方式采用压缩空气搅拌法。
(6)硫酸氧化液中的杂质影响:阳极氧化液中的杂质对氧化膜影响是很大的。
常见杂质如下:(1)氯离子:氧化槽中氯离子来自自来水和冷却管破裂、试验和生产实践证明氯离子含量应低于0.2克/升,如大于0.2克/升氯离子,膜粗糙而疏松、当其含量达0.5克/升氯离子,制作发生击穿(穿孔)。
(2)铜离子:氧化槽中铜离子来自铝铜合金氧化时的溶解,及铜导电棒溶解,当铜离子含量大于0.02克/升时所生长氧化膜上会出现暗色条纹和斑点。
(3)铝离子:氧化槽中铝离子是逐步增长的,当铝离子含量大于25克/升,往往使制件表面呈现白点或块状白斑,并使膜层的吸附性能下降,造成染色困难。
(4)铁离子:氧化槽中铁离子不允许超过0.2克/升,否则会出现暗色条纹斑点。
(5)铬离子:铬酸根阴离子含量在氧化槽中对氧化膜无不良影响。
氧化槽中存在杂质,经过技术和经济原则综合考虑,一般采取更换电解液、表10 硫酸溶液氧化时的常见故障,产生的原因及排除方法表11交流电硫酸型氧化常见故障现象,产生原因及排除方法2.铬酸氧化工艺铝及其合金用铬酸电解液阳极处理的工艺过程是最先采用的电化学氧化法之一。
铬酸电解液所获得的氧化膜较薄,在一般情况下,氧化膜厚度只有1~3微米。
弹性较好,几乎没有气化,它的抗蚀能力比不封闭的在硫酸液中得到氧化膜强。
但铬酸氧化后膜层具有有透明的灰色或彩虹色,不能很好地染色,一般作为油漆的良好底层。
由于铬酸溶液对铝溶解度小,所以此法用于尺寸容差小和表面光度高的零件加工合适。
所以对一些具有铆钉、铗缝、砂眼的另件,特别对压铸件,浇铸件的阳极氧化较为适用,但对含铜和硅量较高的合金不能用铬酸方法进行氧化处理。
常用的铬酸阳极氧化处理:铬酐CrO350~60克/升温度35±2℃阳极电流密度D A 1.5~2.5A氧化时间60分钟电压0~50伏铬酸氧化电解液配制:首先计算电解槽中所需电解液的体积容量,然后加入五分之四水。
之后再加入需要量的铬酸,向溶液进行加热和搅动,使铬酸完全溶解,再加水到规定容积水平,使温度保持在工艺规范,然后进行化学分析,并进行试生产。
配制电解液所用铬酸内硫酸根(SO42-)含量不应超过0.1%,氯根(Cl)不应越过0.05%。
铬酸氧化电解液中有害杂质为SO4--。
C1--及Cr3+。
当SO42-含量大于0.5克/升,C1--含量大于0.2克/升时氧化膜外观粗糙。
当氧化液中SO42-太多时,可加入氢氧化钡或碳酸钡的方法使SO42-成为BaSO4沉淀通过过滤即可除去。
氧化液中的Cl-太多时,通常用稀释溶液或更换溶液方法来解决之。
Cr+++是由六价铬在阳极上还原所产生。
电解液中Cr+++的积累会使氧化膜变得暗而无光,而且抗蚀性能也降低。
当三价铬含量高时,可采用铅作阳极,钢阴极,控制阳极电流密度为0.25安培/分米2,阴极电流密度为8~10安培/分米2,使其在阳极上重新氧化成六价格。
铬酸浓度影响:铬酸电解槽是否正常,决定溶液中游离铬酸含量,随着氧化过程的进行,铝不断进入电解液内,由于溶解铝与铬酸化合,生成铬酸铝A12(CrO4)3及碱性铬酸铝A1(OH)CrO4,所以游离铬酸含量将随着加工时间延长而减少,於是溶液氧化能力随之下降。
因此,应定时往电解液中补充铬酸。
铬酸阳极氧化操作。
在铬酸阳极氧化的过程中,要留心调整使用的电压,以保证是流密度的稳定。
在电解开始约15分钟内,使电压逐渐由零升至25伏,这一阶段是控制电压以维持阳极电流密度为1.5~2.5安培/分米2。
而且随着氧化过程的进行,电流密度逐步下降,电压逐步上升,尽可能在氧化结束时将电压升至40~50伏时间为45分钟,至氧化完时,中断电流取出工作物。
经水彻底清洗后于60~70℃下干燥15分左右。
铬酸阳极氧化工艺流程:(1)零件上挂具(2)化学除油(3)热水清洗(4)冷水清洗(5)硝酸出光(6)清水清洗(7)铬酸阳极氧化(8)冷水清洗(9)热水洗(10)干燥表12 铬酸溶液氧化铝件时常见故障,产生原因及排除方法。