滚压工艺
滚压工艺简介

滚压工艺简介冷弯成形(Cold Roll Forming)是一种节材、节能、•高效的金属成形新工艺、新技术。
冷弯成形是通过顺序配置的多道次成形轧辊,把卷材、带材等金属板带不断地进行横向弯曲,以制成特定断面的型材。
在辊式冷弯成型过程中只有弯曲变形。
除坯料弯曲角局部有轻微减薄外,变形材料的厚度在成型过程中保持不变。
这种加工方法特别适合于外形纵长、批量较大的高精度产品的加工。
钢门窗料型采用辊式连续冷弯成型工艺,成型时前一卷带材的尾部与后一卷带材的头部经对齐对焊,使坯料带材连续不断地进入成型机进行成型。
这种成型工艺高效、高产、通用。
这种成型工艺的主要优点是:(1)带卷成本低、切损少,因而降低了材料总成本。
(2)可以加工形状复杂的型材。
(3)型材的头尾部扭曲及张开度减小。
(4)由于操作几乎是连续的,因而生产率得到提高。
冷弯成形的产品用于建筑、汽车制造、矿山机械制造、农业及轻工机械制造、造船及交通运输、石油化工电力工业、仪器仪表、集装箱、纺织机械、高速公路、金属货架、民用电器及日常用品制造等各个领域,在经济发展中起着很重要的作用。
尽管采用冷弯成形工艺已达到很大的生产量,但它仍被普遍认为是一种“未掌握的艺术”(Blank Art),还未上升为科学。
主要原因是冷弯成形作为一种金属成形加工新技术,本身具有的特点和规律尚未被人们完全掌握和认识。
彩板门窗型材的成型绝大多数采用辊式冷弯成型。
这是因为这种工艺的生产效率高(成型速度10-30m/min)、成型精度高(尺寸控制精度0.2-0.5mm)、大批量生产的成本低(成型加工费1000元/t左右)。
图5-1 塞柯(SERCONSULT)公司的彩色门窗型材轧机我国自1986年从意大利塞柯(SERCONSULT)公司引进彩色门窗生产线,目前已有70多条门窗型材生产线,生产能力达到15万吨足以满足门窗行业的需要。
目前国内钢门窗型材生产厂家所采用的成型机,基本上和塞柯公司的类似。
滚压加工工艺

滚压加工工艺简介滚压加工工艺是一种常见的金属加工方法,通过滚压设备对金属材料进行形变加工,使其获得所需的形状和尺寸。
滚压加工技术广泛应用于汽车制造、航天航空、机械制造等领域。
本文将从滚压加工的原理、工艺流程、设备和应用等方面进行详细探讨。
原理滚压加工是通过在金属材料表面施加大压力,将其塑性变形至所需形状的一种加工方法。
滚压过程中,金属材料处于塑性变形的温度范围,使其分子间结构发生变化,从而改变材料的形状和尺寸。
滚压加工可以通过改变滚轮形状、滚轮排列方式和滚压力度等参数,对金属材料进行精确的控制,以获得满足要求的成品。
工艺流程滚压加工的主要工艺流程包括预处理、滚压加工和后处理三个步骤。
1. 预处理预处理是滚压加工的第一步,其目的是为了提高金属材料的可塑性,减少滚压过程中的应力和能量消耗。
预处理可以采用热处理、化学处理和机械处理等方法,使金属材料达到适合滚压加工的状态。
2. 滚压加工滚压加工是整个工艺的核心步骤,该步骤通过滚压设备对金属材料进行形变加工。
滚轮的形状和排列方式决定了金属材料的变形方式,滚压力度决定了加工的变形程度。
滚压过程中需要对滚轮、工件和润滑液进行充分的冷却和润滑,以降低摩擦和热量的产生,提高加工效果和生产效率。
后处理是滚压加工的最后一步,其目的是对加工后的成品进行整形、调整和修整。
后处理可以采用热处理、机械加工和表面处理等方法,使成品达到所需的精度、表面光洁度和机械性能要求。
设备滚压加工依靠专用的滚压设备进行实施,主要包括滚轮、滚床和润滑系统等组成部分。
1. 滚轮滚轮是滚压设备的核心部件,其形状和排列方式直接决定了加工成品的形状和尺寸。
滚轮可以分为单排滚轮、双排滚轮和多排滚轮等不同形式,根据加工要求选择合适的滚轮类型。
2. 滚床滚床是用于支撑和定位金属材料的装置,保证滚轮对工件的加工精度和一致性。
滚床的结构和刀具的改变,可以实现对不同形状和尺寸的工件进行滚压加工。
3. 润滑系统润滑系统主要用于降低滚压过程中的摩擦和热量产生,提高加工效果和生产效率。
试述内孔滚压工艺原理

关 键词 : 内孔 ; 压 ; 艺 滚 工 中图分 类号 :G 7 T 3
引言
文献 标识 码 : A
滚 压加 工是 将 高硬 度 且光 滑 的滚 柱与 金 属表 面滚压 接触 ,使 其 表 面层 发生 局 部微 量 的塑 性 变形 后得 到 改善 表 面粗糙 度 的 塑性 加 工法 的 ,通 过滚 压方 法 不仅 能 提 高 内孑表 面 L 粗糙 度 f 1,同 时也 提 高零 件 内孔 表 面质 图 ) 量, 是一 种高 效 的 内孔加 工方 法 , 经 济效 而且
摘 要 : 重机械 是被 广 泛地应 用 于各种 物料 的起 重 、 输 、 卸 、 装等 作业 中, 现代 工业 生产 不 可缺 少的设 备 。其广 泛地 应 用在 起 运 装 安 是 室内外仓 库 、 厂房 、 头和露 天贮料 场 等处 。通过 对起 重机械 现场 检验 案例 的分 析 , 出现 场检验 顺序 的 重要 性 及 解决方 法 码 提 关键 词 : 重机 械 ; 场检 验 ; 起 现 顺序 中 图分类 号 :H 1 T 2 文献 标识 码 : A
滚 压 内孔 时滚 柱 在 内孔 工 件 表 面 上作 1 ~ O 以上 。 O5 倍 b 优 质 一 次进 给实 现 R 0 501m 的 无 滑动 的滚 动 ,使 内孔表 面 层金 属 产生 塑性 . a. .. 0一 u
以 , 后 的零件 表 面质量 好 。 加工 滚珠 滚压 通常 可 获 得 很 低 的 表 面 粗 糙 度 ( a. m~ R0 2 01 ,在其余工艺参数匹配的条件下 , . m) 0 还 能达 到 R 0 5 m,被滚 压 零件 表 面质 量好 。 a. / 0x 同时 ,由于滚珠 与 工件 表 面 的接触 面 相对 较 小, 因此 , 同样 单 位压 力 的情 况 下能 减小 总 在 压力 , 滚压 时较 轻快 , 其 适合 于小 型 细长 精 尤 密零件 的外 表 面及 薄壁 零件 的内孔 滚 压 。滚 压 工 具 结构 简单 、 便 , 轻 当滚 珠 磨 损 后 , 采 可 用 价格 低 的外购 标 准滚 珠 ,一定 程 度上 可 以 降低成本。 其不足之处是滚珠使用寿命过低 , 通 常连 续使 用 1h 1h即需更 换 。 0一2 2. .2滚柱 滚压 2 滚 柱滚 压不 仅 可 以像 滚 珠滚 压 一样 得到 较好 的表 面 粗糙 度 ,又克 服 了滚 珠 寿命低 的 缺 点 ,还 可 以采 用 大 的 进 给 量 ,通 常 采 用 O 5 mr08m /进行 滚 压 , 其 生产 效 率 . m / . mr 7 一 0 故 高。
滚压工艺流程
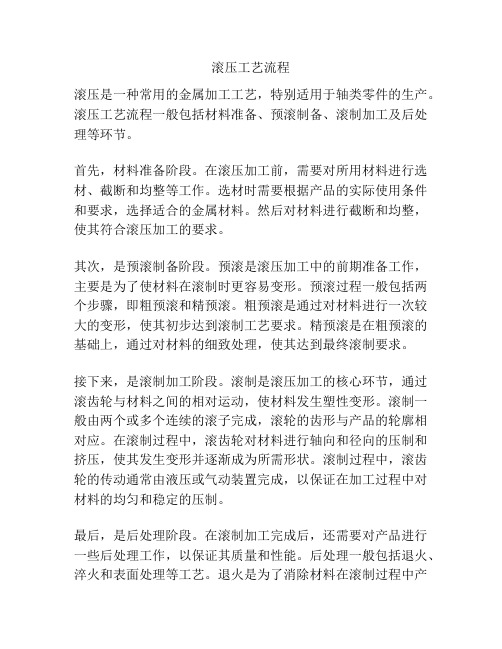
滚压工艺流程滚压是一种常用的金属加工工艺,特别适用于轴类零件的生产。
滚压工艺流程一般包括材料准备、预滚制备、滚制加工及后处理等环节。
首先,材料准备阶段。
在滚压加工前,需要对所用材料进行选材、截断和均整等工作。
选材时需要根据产品的实际使用条件和要求,选择适合的金属材料。
然后对材料进行截断和均整,使其符合滚压加工的要求。
其次,是预滚制备阶段。
预滚是滚压加工中的前期准备工作,主要是为了使材料在滚制时更容易变形。
预滚过程一般包括两个步骤,即粗预滚和精预滚。
粗预滚是通过对材料进行一次较大的变形,使其初步达到滚制工艺要求。
精预滚是在粗预滚的基础上,通过对材料的细致处理,使其达到最终滚制要求。
接下来,是滚制加工阶段。
滚制是滚压加工的核心环节,通过滚齿轮与材料之间的相对运动,使材料发生塑性变形。
滚制一般由两个或多个连续的滚子完成,滚轮的齿形与产品的轮廓相对应。
在滚制过程中,滚齿轮对材料进行轴向和径向的压制和挤压,使其发生变形并逐渐成为所需形状。
滚制过程中,滚齿轮的传动通常由液压或气动装置完成,以保证在加工过程中对材料的均匀和稳定的压制。
最后,是后处理阶段。
在滚制加工完成后,还需要对产品进行一些后处理工作,以保证其质量和性能。
后处理一般包括退火、淬火和表面处理等工艺。
退火是为了消除材料在滚制过程中产生的应力和变形,提高产品的力学性能。
淬火是为了提高产品的硬度和强度,同时增加其耐磨和耐腐蚀性能。
表面处理可以采用镀锌、镀铬、喷涂等方法,以提高产品的外观和耐用性。
总之,滚压工艺流程包括材料准备、预滚制备、滚制加工及后处理等多个环节。
每个环节都对产品的质量和性能有着重要影响,需要经过精细的设计和操作,才能得到满足要求的产品。
滚压工艺的应用广泛,不仅可以用于生产轴类零件,还可以在汽车、机械、航空航天等领域得到广泛应用,为各行各业的发展提供重要的支撑。
滚压加工工艺
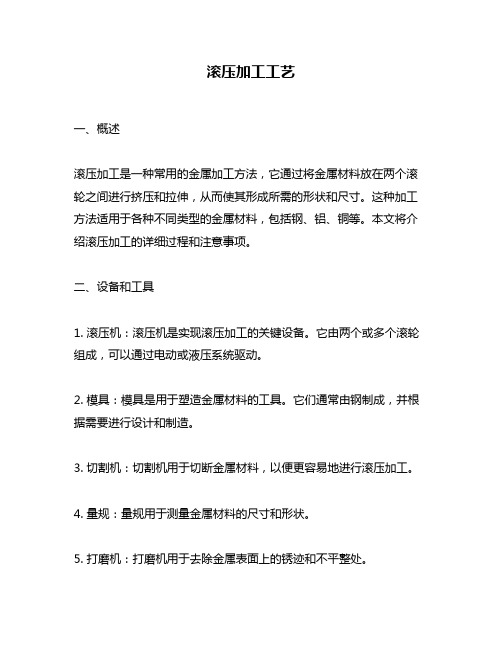
滚压加工工艺一、概述滚压加工是一种常用的金属加工方法,它通过将金属材料放在两个滚轮之间进行挤压和拉伸,从而使其形成所需的形状和尺寸。
这种加工方法适用于各种不同类型的金属材料,包括钢、铝、铜等。
本文将介绍滚压加工的详细过程和注意事项。
二、设备和工具1. 滚压机:滚压机是实现滚压加工的关键设备。
它由两个或多个滚轮组成,可以通过电动或液压系统驱动。
2. 模具:模具是用于塑造金属材料的工具。
它们通常由钢制成,并根据需要进行设计和制造。
3. 切割机:切割机用于切断金属材料,以便更容易地进行滚压加工。
4. 量规:量规用于测量金属材料的尺寸和形状。
5. 打磨机:打磨机用于去除金属表面上的锈迹和不平整处。
三、准备工作1. 准备好所需的设备和工具,并确保它们都处于良好状态。
2. 检查金属材料的尺寸和形状是否符合要求,并在必要时进行切割和打磨。
3. 根据需要,设计和制造所需的模具。
4. 将模具安装到滚压机上,并调整滚轮之间的距离,以便适应所需的加工形状。
5. 调整滚压机的速度和压力,以便实现所需的加工效果。
四、滚压加工过程1. 将金属材料放置在滚压机上,并将其夹住以防止移动。
2. 启动滚压机,并将金属材料通过滚轮之间的空隙拉伸和挤压,直到其达到所需形状和尺寸为止。
3. 在加工过程中,注意控制滚压机的速度和压力,以避免过度挤压或拉伸导致金属材料损坏或变形。
4. 在完成加工后,使用量规检查金属材料的尺寸和形状是否符合要求。
如果需要进一步处理,则可以使用打磨机去除表面上的锈迹或不平整处。
五、注意事项1. 在进行滚压加工时,必须注意安全。
操作人员必须戴上适当的保护设备,如手套、护目镜等。
2. 在进行滚压加工前,必须仔细检查金属材料的尺寸和形状是否符合要求,并在必要时进行切割和打磨。
3. 在进行滚压加工时,必须注意控制滚压机的速度和压力,以避免过度挤压或拉伸导致金属材料损坏或变形。
4. 在进行滚压加工后,必须使用量规检查金属材料的尺寸和形状是否符合要求,并在必要时使用打磨机去除表面上的锈迹或不平整处。
【精品】滚压工艺简介

滚压工艺简介冷弯成形(ColdRollForming)是一种节材、节能、•高效的金属成形新工艺、新技术.冷弯成形是通过顺序配置的多道次成形轧辊,把卷材、带材等金属板带不断地进行横向弯曲,以制成特定断面的型材.在辊式冷弯成型过程中只有弯曲变形。
除坯料弯曲角局部有轻微减薄外,变形材料的厚度在成型过程中保持不变。
这种加工方法特别适合于外形纵长、批量较大的高精度产品的加工.钢门窗料型采用辊式连续冷弯成型工艺,成型时前一卷带材的尾部与后一卷带材的头部经对齐对焊,使坯料带材连续不断地进入成型机进行成型。
这种成型工艺高效、高产、通用。
这种成型工艺的主要优点是:(1)带卷成本低、切损少,因而降低了材料总成本。
(2)可以加工形状复杂的型材。
(3)型材的头尾部扭曲及张开度减小。
(4)由于操作几乎是连续的,因而生产率得到提高。
冷弯成形的产品用于建筑、汽车制造、矿山机械制造、农业及轻工机械制造、造船及交通运输、石油化工电力工业、仪器仪表、集装箱、纺织机械、高速公路、金属货架、民用电器及日常用品制造等各个领域,在经济发展中起着很重要的作用。
尽管采用冷弯成形工艺已达到很大的生产量,但它仍被普遍认为是一种“未掌握的艺术”(BlankArt),还未上升为科学。
主要原因是冷弯成形作为一种金属成形加工新技术,本身具有的特点和规律尚未被人们完全掌握和认识.彩板门窗型材的成型绝大多数采用辊式冷弯成型。
这是因为这种工艺的生产效率高(成型速度10—30m/min)、成型精度高(尺寸控制精度0。
2—0.5mm)、大批量生产的成本低(成型加工费1000元/t左右)。
图5-1塞柯(SERCONSULT)公司的彩色门窗型材轧机我国自1986年从意大利塞柯(SERCONSULT)公司引进彩色门窗生产线,目前已有70多条门窗型材生产线,生产能力达到15万吨足以满足门窗行业的需要.目前国内钢门窗型材生产厂家所采用的成型机,基本上和塞柯公司的类似。
这种成型机一般由24—32道水平辊机架和矫直辊机架组成.按型材成型要求配置不同辅助变形辊和立辊。
陶瓷产品滚压工艺
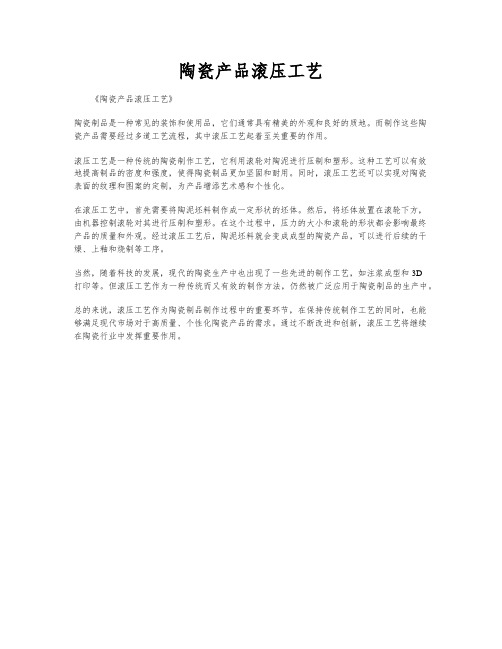
陶瓷产品滚压工艺
《陶瓷产品滚压工艺》
陶瓷制品是一种常见的装饰和使用品,它们通常具有精美的外观和良好的质地。
而制作这些陶瓷产品需要经过多道工艺流程,其中滚压工艺起着至关重要的作用。
滚压工艺是一种传统的陶瓷制作工艺,它利用滚轮对陶泥进行压制和塑形。
这种工艺可以有效地提高制品的密度和强度,使得陶瓷制品更加坚固和耐用。
同时,滚压工艺还可以实现对陶瓷表面的纹理和图案的定制,为产品增添艺术感和个性化。
在滚压工艺中,首先需要将陶泥坯料制作成一定形状的坯体。
然后,将坯体放置在滚轮下方,由机器控制滚轮对其进行压制和塑形。
在这个过程中,压力的大小和滚轮的形状都会影响最终产品的质量和外观。
经过滚压工艺后,陶泥坯料就会变成成型的陶瓷产品,可以进行后续的干燥、上釉和烧制等工序。
当然,随着科技的发展,现代的陶瓷生产中也出现了一些先进的制作工艺,如注浆成型和3D
打印等。
但滚压工艺作为一种传统而又有效的制作方法,仍然被广泛应用于陶瓷制品的生产中。
总的来说,滚压工艺作为陶瓷制品制作过程中的重要环节,在保持传统制作工艺的同时,也能够满足现代市场对于高质量、个性化陶瓷产品的需求。
通过不断改进和创新,滚压工艺将继续在陶瓷行业中发挥重要作用。
滚压工艺流程
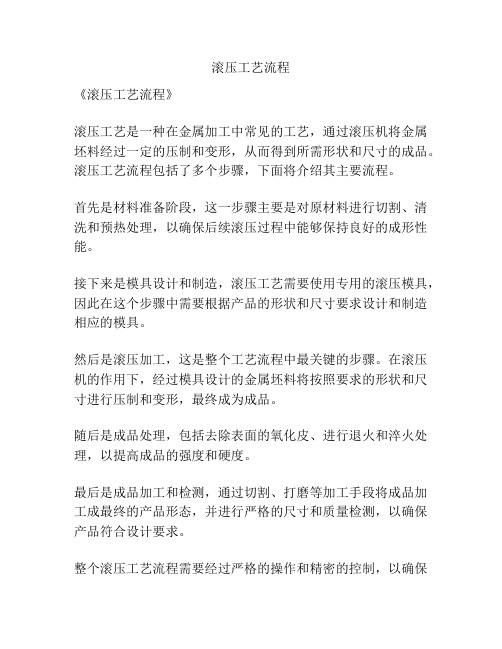
滚压工艺流程
《滚压工艺流程》
滚压工艺是一种在金属加工中常见的工艺,通过滚压机将金属坯料经过一定的压制和变形,从而得到所需形状和尺寸的成品。
滚压工艺流程包括了多个步骤,下面将介绍其主要流程。
首先是材料准备阶段,这一步骤主要是对原材料进行切割、清洗和预热处理,以确保后续滚压过程中能够保持良好的成形性能。
接下来是模具设计和制造,滚压工艺需要使用专用的滚压模具,因此在这个步骤中需要根据产品的形状和尺寸要求设计和制造相应的模具。
然后是滚压加工,这是整个工艺流程中最关键的步骤。
在滚压机的作用下,经过模具设计的金属坯料将按照要求的形状和尺寸进行压制和变形,最终成为成品。
随后是成品处理,包括去除表面的氧化皮、进行退火和淬火处理,以提高成品的强度和硬度。
最后是成品加工和检测,通过切割、打磨等加工手段将成品加工成最终的产品形态,并进行严格的尺寸和质量检测,以确保产品符合设计要求。
整个滚压工艺流程需要经过严格的操作和精密的控制,以确保
成品能够满足客户的需求。
而滚压工艺也因其高效、成本低、生产速度快等优势,受到了广泛的应用和欢迎。
- 1、下载文档前请自行甄别文档内容的完整性,平台不提供额外的编辑、内容补充、找答案等附加服务。
- 2、"仅部分预览"的文档,不可在线预览部分如存在完整性等问题,可反馈申请退款(可完整预览的文档不适用该条件!)。
- 3、如文档侵犯您的权益,请联系客服反馈,我们会尽快为您处理(人工客服工作时间:9:00-18:30)。
11、加工完毕后,用行车将夹具体吊至托盘上并涂抹润滑油。
在铣槽过程中可根据加工后光圆两侧铣槽的宽度是否相等来略微调整刀具在Z方向的坐标。
名称
图号或型号
数量
注意事项
1、工作台必须清洗干净(否则会给后面工序中的刀具在Z方向对正带来困难)。
2、整个过程需注意防止型材表面划伤。
3、铆:1)、铆时的顺序按照先中间后两边、光圆同一位置处两侧对称铆紧的原则进行操作。
2)、铆操作时的两把工具,一把用于开槽,一把用于收槽。在对型材壁薄的一侧开槽时,开槽的位置应在线内,以防止铆后型材的外侧凸起。
3)、铆紧的程度应为铆后的光圆用手无法将其旋转,在两个铆点之间用手推拉光圆时无明显弯曲变形。铆点间距L一般在230mm~330mm之间。(对于敲击光圆进入型材一侧的型槽在铆时,一般只铆光圆两端的四处位置即可)
5、对正刀具:
(1)将对正用的刀具装到刀杆上(对正定位垫厚度见表1),并将刀具靠近光圆,如图1所示查看距离δ1、δ2大小是否相等,待δ1、δ2相等之后,将Z轴值清零。
(2)将铣槽刀具(中间定位垫厚度见表2)换装到刀杆上(应按照顺铣要求安装铣槽刀具),主轴旋转250r/min,下降到Z0位置,移动Y轴靠近光圆,待铣刀在型材上铣出轻微的切痕时,将Y轴值清零。
C-光圆到型材一端的距离
D-光圆的长度
E-型材的长度
L-两个铆点之间的距离
点划线――铣槽的中心线(或者划线)
一、划线(图1)
1、用专用工具将型材的两个端面倒角、去毛刺。用干净面纱将型材的外表面擦拭干净后放置擦拭后的平台上,依次摆放整齐,准备划线。
2、用高度尺量出尺寸A(表1),一手将型材从顶端往下按紧,一手用高度尺在型材的两个侧面上依次划出尺寸A。同样方法划出尺寸B(表1)。表1单位:mm
尺寸
型号
Φ8光圆
Φ10光圆
A
3.00
5.00
B
15.00
19.00
二、铆(图1)
1、准备:用干净面纱将型材、型槽的外表面擦拭干净后依次摆放置垫有软物的工作台上,将光圆的一端在砂轮机上倒角尺寸1×45º。
2、选配光圆:将光圆倒角的一端涂抹上少许的润滑油后,尝试穿入型材两侧的型槽内,找出型材型槽较紧的一侧并将光圆穿入,符合要求尺寸;倘若用手旋转光圆穿入型槽困难,可用千分尺选出最细的一根光圆再尝试将其穿入型槽内;如果光圆穿入仍困难,可考虑用铁锤、铝板将其敲入型材的型槽内(敲击时必须有人用手扶住型材,同时另一手扶住光圆)。按照上述方法,将所有穿好一侧型槽的型材依次摆放至工作台上。
4)、铆型材两侧光圆时,必须保证图2所示的尺寸A(表2),且其基准面应为同一个端面。表2单位:mm
尺寸
型号
HHM1-750B主臂
XJ600主臂
XJ600副臂
XJ800主臂
XJ800副臂
C
18
10
10
10
10
D
1150
950
1000
1150
1200
E
1180
970
1020
1170
1220
1、铆后的凸起相对于型材平面的高度要小于0.3mm。(防止装配时滚轮与铆后的凸起发生干涉)
(3)将型材无定位螺钉的一端的X坐标清零(铣槽方向从无定位端向另一端铣槽)。
6、铣槽参数:铣槽吃刀量依次是1.4mm,主轴转速250r/min,横向进给速度250mm/min。铣槽完毕。
7、挤压参数:将挤压刀具(中间定位垫厚度见表1)换装到导杆上,原点与铣槽的相同。挤压吃刀量依次是1.00mm、1.20mm、1.35mm、1.40mm。主轴转速15r/min.横向进给速度1800mm/min。挤压完毕。
3、安装型材:将夹具体上型材的定位块用面纱擦拭干净,再将擦拭干净后的型材放到定位块上,一端与夹具体一端的定位螺钉靠近。
4、找正型材:将自制 形垫板(或者150*50胶垫)对应各个压紧块的位置放到型材上,然后用扳手将各个压紧块按照先中间后两边的顺序预紧一下。用百分表沿着X方向将型材侧面靠近光圆处的部分找正(平行度误差在0.04mm以内)后,用扳手将压紧块按照顺序分三次依次拧紧固。
铣槽以及挤压工艺ห้องสมุดไป่ตู้
工艺简图
操作工步
要求
消耗材料
光圆
对正刀具
图1:对正刀具示意图
表1单位:mm
光圆
对正定位垫
中间定位垫
Φ8
8
8
Φ10
10
10
1、清洗工作台:将工作台面清扫干净,并用干净的面纱将其擦拭一边。
2、找正夹具体:将夹具体用行车吊起并用干净面纱将其底面擦拭一边,确保无杂物后将其吊至工作台中间部位。用百分表沿着X方向先将夹具体大体找正(夹具体侧面与机床X方向平行度误差在0.05mm以内),然后用压板将夹具体紧固但不拧紧,再用百分表沿着X方向将夹具体找正(平行度误差在0.02mm以内)后,用扳手将压板的螺钉按照先中间后两边的顺序分三次依次拧紧。
3、整个过程需注意防止型材表面划伤。
更改履历
更改时间
更改内容
更改原因
编制
审核
会签
批准
表号RT42303F01
现场工艺操作指导卡
编号:GYNCJXHHM1-750B
第1页,共1页
第0次修改
生效期:2006.03.01
产品名称
五轴伺服迅捷机械手
适用型号
HHM5-600GHHM1-750B
工序
滚压工艺
本工位名称
更改履历
更改时间
更改内容
更改原因
编制
审核
会签
批准
2、铆时重点在于光圆两端的收槽。收槽后的槽宽相对于原来至少缩短1.0mm。
3、型材两侧光圆所对应的如图2所示的尺寸A必须保证为同一基准面。
名称
图号或型号
数量
。
注意事项
1、划线时,必须保持型材的底面与型台面重合(减小扭拧度对划线的影响)。
2、铆后的凸起相对于型材平面的高度要小于0.3mm。(防止装配时滚轮与铆后的凸起发生干涉)
表号RT42303F01
现场工艺操作指导卡
编号:GYNCJXHHM1-750B
第1页,共1页
第0次修改
生效期:2006.03.01
产品名称
五轴伺服迅捷机械手
适用型号
HHM5-600GHHM1-750B
工序
铆接工艺
本工位名称
划线以及铆的工艺
工艺简图
操作工步
要求
消耗材料
图1:A-距离型材底面的划线尺寸
B-距离型材底面的划线尺寸