可塑成型
陶瓷工艺学

二、滚压成形
滚压成型是由旋压成形方法发展而得的 新工艺。这种方法把扁平的型刀改变为尖 锥形或圆柱形的回转体——滚压头。成型 时,盛放着泥科的模型和该压头分别绕自 己的轴线以一定速度旋转。滚压头一面转 动一面压紧泥料。这种方法广泛用于成型 日用陶瓷器皿。
生产能力:
14—16吋盘 240件/h 18—20吋盘 120件/h 成形范围:Φ ≤508mm
一、旋压成形
旋压成形也称刀压成形。它是利用型 刀和石膏模型进行成形的一种方法。 刀口的工作弧线形状与模型工作 面的形状构成了坯体的内外表面, 而型刀口与模型工作面的距离即为 坯体的厚度。
旋压成型操作
向旋转的石膏模中,投入泥料。 然后将型刀慢慢压入泥料。 多余的泥料则贴附于型刀排泥板上, 并用手清除 同时割除模型口沿处余泥。
属护套,以增大强度
檐沟的作用
1、容纳翅片状余泥 2、限制泥料外溢,防止制品成型腹腔 内泥料不足,保证制品充填情况良好 3、限、模具的影响 2、檐沟设计的影响 3、塑压模内水分排除的影响 4、成型压力与塑性泥料的关系
A:泥料含水率高时,成型压力应降低。 B:可塑性愈好的泥料脱水性能愈差,加压停
石蜡作粘结剂的特点
熔化后粘度小,易填满模型;
有润滑性,对模具不会磨损,生坯光洁度高, 冷却凝固后坯体有一的强度; 熔点低故热压铸工作为70~80 ℃; 冷却后体积收缩约为7~8%,易脱模;
(5)模型中泥料被主轴带动旋转,要受到离心 力的作用,如果离心力大于泥料与模型间的 粘附力,泥料就要甩出,产生所谓“飞泥” 的现象,有时局部泥料被拉断而甩出,这都 使成形操作无法进行。
生产效率高
主轴转速高时 飞模 飞泥
第四章 陶瓷工艺学 成型
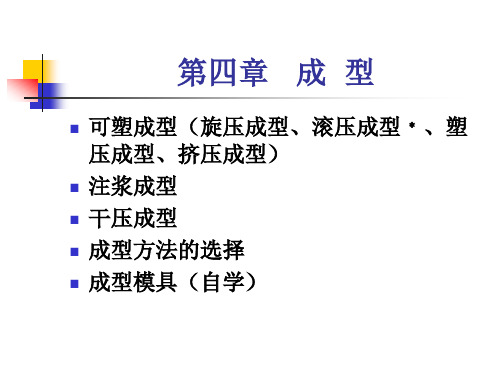
滚压过程的要求
滚压过程是指滚压头从开始接触泥料至离开坯体 表面的一段过程。这一过程所经过的时间只有几秒钟。 通常把这一短暂过程分为3个阶段,而各个阶段对压泥 的要求并不相同。
滚压过程的三个阶段:
布泥阶段:滚压头从开始接触泥料至定压前。泥料在模型 工作面上展布,要求滚压头的动作要轻,压泥速度要适当, 一般以6~7mm/s 为宜。如动作太重或速度过快则会压坏 模型或引起“鼓气”。若下压太慢,泥料容易粘住滚头。
成型就是将制备好的坯料用各种方法加工成具有一 定形状和尺寸的坯件(生坯)半成品。成型工序应满足 以下要求:
形状、尺寸(根据收缩率经过放尺后的尺寸); 一定的机械强度,以保证后继工序的进行; 结构均匀,有一定的致密度; 成型过程应能多、快、好、省的组织生产。
成型是陶瓷生产过程的一个重要步骤。在成 型过程中形成的某些缺陷(如不均匀性等)仅靠烧结 工艺的改进是难以克服的。成型工艺已经成为制备 高性能陶瓷材料的关键技术,它对提高陶瓷材料的 均匀性、重复性和成品率,降低陶瓷制造成本具有 十分重要的意义。
水量小些;
• 阳模滚压:水分少些、延伸性好(即变形量大些) • 阴模滚压:可塑性可稍差些,水分稍多 • 冷滚压:水分要少,可塑性要好 • 热滚压:要求不严
滚压头的温度:冷滚压和热滚压(120℃左右)
热滚和冷滚的工艺特点
热滚的滚头内部有电阻丝加热,用调压器调节温度, 加热的滚头与坯泥接触,能在表面产生一层蒸汽膜, 避免坯泥粘附滚头。滚头材料大都采用铸铁和普通 碳素钢,耐磨性较好,但滚头结构较复杂,维修操 作较麻烦,工人操作条件差,这是它的不足之处。
注射成型(Injection Molding)
注射成型可成型尺寸精度高、形状比较复杂的陶瓷部 件,易于自动化和大规模生产。
陶瓷生产技术及设备-3

成 型
3.1 器形的合理设计
陶瓷制品的器形设计讲究 “实用、美观、可加工、高生产效率” 的原则。
3.2 成型方法的分类与选择
一、成型方法的分类
半干压法:坯料含水率 8~15%
1. 压制法成型
普通压制法成型
等静压法成型
干压法:坯料含水率 3~7%
2. 可塑法成型:雕塑、拉坯、印坯、盘筑、旋坯、滚压、车坯、 挤出、注塑、轧膜法等。坯料含水率 18~26 %。 常压注浆(石膏模) 3. 注浆法成型 中高压注浆(多孔树脂模) 坯料含水率 28~35% 流延法成型(金属模) 热压铸法注浆(金属模)
● 轧膜成型适于轧制 1mm以下 的坯片,通常是 0.15mm左右, 最薄可达 0.05mm。
3.3 可塑成型
八、其他手工可塑成型方法
1. 雕塑
一般雕塑
雕塑
镂空雕塑 堆贴雕塑
● 镂空雕塑
3.3 可塑成型
八、其他手工可塑成型方法
1. 雕塑
● 堆贴雕塑
3.3 可塑成型
八、其他手工可塑成型方法
2. 盘筑(围筑)塑形
3.3 可塑成型
三、挤压(出)成型
挤出成型主要适用于管状、棒状、截面和中孔一致的制品的成型。 坯体外形由挤出机机嘴的内表面形状确定,坯体长度则根据尺寸 要求进行切割。
3.3 可塑成型
四、车坯成型
● 主要设备:立式或卧式车坯机;模具:金属车刀 车坯成型适合用来成型外形复杂的圆柱状制品,如各种瓷质绝 缘件。所采用的坯料为经真空练泥机挤出的塑性泥段。有湿式 车坯和干式车坯二种。 湿式车坯:坯料含水率16~18%,成型坯体精度较差且易 变形,但刀具磨损小,无粉尘产生。 干式车坯:坯料含水率 6~11%,成型坯体精度高,但刀 具磨损大,粉尘大。
木材的可塑性和成型能力
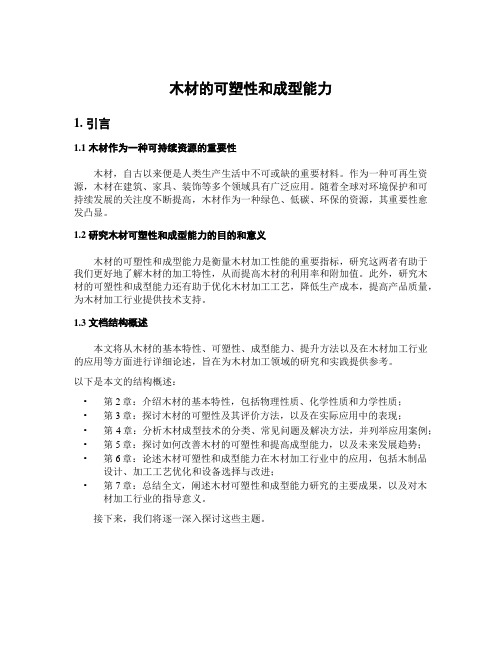
木材的可塑性和成型能力1. 引言1.1 木材作为一种可持续资源的重要性木材,自古以来便是人类生产生活中不可或缺的重要材料。
作为一种可再生资源,木材在建筑、家具、装饰等多个领域具有广泛应用。
随着全球对环境保护和可持续发展的关注度不断提高,木材作为一种绿色、低碳、环保的资源,其重要性愈发凸显。
1.2 研究木材可塑性和成型能力的目的和意义木材的可塑性和成型能力是衡量木材加工性能的重要指标,研究这两者有助于我们更好地了解木材的加工特性,从而提高木材的利用率和附加值。
此外,研究木材的可塑性和成型能力还有助于优化木材加工工艺,降低生产成本,提高产品质量,为木材加工行业提供技术支持。
1.3 文档结构概述本文将从木材的基本特性、可塑性、成型能力、提升方法以及在木材加工行业的应用等方面进行详细论述,旨在为木材加工领域的研究和实践提供参考。
以下是本文的结构概述:•第2章:介绍木材的基本特性,包括物理性质、化学性质和力学性质;•第3章:探讨木材的可塑性及其评价方法,以及在实际应用中的表现;•第4章:分析木材成型技术的分类、常见问题及解决方法,并列举应用案例;•第5章:探讨如何改善木材的可塑性和提高成型能力,以及未来发展趋势;•第6章:论述木材可塑性和成型能力在木材加工行业中的应用,包括木制品设计、加工工艺优化和设备选择与改进;•第7章:总结全文,阐述木材可塑性和成型能力研究的主要成果,以及对木材加工行业的指导意义。
接下来,我们将逐一深入探讨这些主题。
2 木材的基本特性2.1 木材的物理性质木材作为一种天然的生物材料,其物理性质具有独特的特点。
首先,木材具有较好的隔热性,这是因为木材的多孔结构和其中的空气能够有效阻止热量传递。
其次,木材的密度较低,使得其重量轻便,易于搬运和加工。
此外,木材的吸湿性较强,能够吸收空气中的水分,但也容易导致木材的膨胀和收缩。
2.2 木材的化学性质木材主要由纤维素、半纤维素和木质素组成。
这些成分赋予木材良好的化学稳定性,使其在一定条件下能够抵抗生物、真菌和化学品的侵蚀。
陶瓷工艺学

原料的分类根据工艺特性:可塑性原料,非可塑性原料(瘠性),熔剂性原料。
根据用途:坯用原料,釉用原料,色料和彩料。
根据矿物组成:粘土原料,硅质原料,长石原料,钙质原料,镁质原料等。
根据原料的获得方式:天然矿物原料,化工原料,工业废渣原料等。
粘土的组成:粘土的性能取决于粘土的组成,包括粘土的矿物组成、化学组成和颗粒组成。
粘土:粘土很少由单一矿物组成,而是多种微细矿物的混合体。
因此,粘土所含各种微细矿物的种类和数量是决定其工艺性能的主要因素。
粘土的工艺性质:可塑性、结合性、离子交换性、触变性、膨化性、收缩、烧结性能、耐火度等。
石英的晶型转化类型有两种:(1)高温型的缓慢转化(2)低温型的快速转化石英的工艺性质:(1)石英是瘠性原料,可对泥料的可塑性起调节作用。
(2)提供了生坯中水分快速排出的通道,可缩短干燥时间,减少干燥收缩(3)烧成过程中,石英的体积膨胀可以补偿坯体的收缩(4)高温下石英会部分熔解而提高液相的粘度,未熔化的石英可作为坯体的骨架,起到增强的作用(5)冷却时石英晶型转化的体积效应使坯体内产生相当大的内应力,导致裂纹产生,从而影响陶瓷的抗热振性和机械强度(6)釉料中的石英对其性能有很大影响。
长石:是陶瓷生产中的主要熔剂性原料。
钾长石:异成分熔融,高温下熔体粘度大。
钾长石的熔融温度不是太高,且其熔融温度范围宽。
高温下钾长石熔体的粘度很大,且随着温度的增高其粘度降低的较慢,在陶瓷生产中有利于烧成控制和防止变形。
钠长石:同成分熔融,高温熔体的粘度小。
钠长石的开始熔融温度比钾长石低,熔化时没有新的晶相产生,液相组成和未熔长石的组成相似,但液相的粘度较低。
钠长石的熔融范围较窄,且其粘度随温度的升高而降低的速度较快,因而在烧成过程中易引起产品的变形。
长石在陶瓷生产中的作用:1. 长石是熔剂性原料,高温下熔融形成粘稠的玻璃熔体,是坯料中碱金属氧化物的主要来源,能降低陶瓷坯体组分的熔化温度,有利于成瓷和降低烧成温度。
特种陶瓷的成型方法

¾ 干压等静压成型的特点:
¾ 干式等静压更适合于生产形状简单的长形、壁薄、 管状制品。
¾ 这种方法可连续操作,操作周期短,适用于成批生 产。但产品规格受限制,因为加压塑性模不能经常 更换。
目前大量使用的主要是湿袋法。
3.热等静压成型
热等静压也称为高温等静压,是用金属箔代替橡皮 模,用气体代替液体,使金属箔内的粉料均匀受压。 通常所用的气体为氦气、氩气等惰性气体。结。
特种陶瓷的主要成型方法可分为: ① 压力成型方法,如干压成型、冷等静压成型、干袋式
等静压成型等。 ② 可塑成型方法,如可塑毛坯挤压、轧膜成型等。 ③ 浆料成型方法,如料浆浇注、离心浇注、流延成型、
热压铸等。 ④ 注射成型。 ⑤ 其他成型方法。如压滤法、固体自由成型制备技术、
直接凝固注模成型、温度诱导成型、电泳沉积成型等。
挤压成型时将真空练制的泥 料放入挤制机内,这种挤制 机一头可以对泥料施加压力, 另一头装有机嘴即成型模具。 通过更换机嘴,能挤出各种 形状的坯体。也有将挤制嘴 直接安装在真空练泥机上, 成为真空练泥挤压机,挤出 的制品性能更好。
棒和管材的挤压成型
Á 挤压机适合挤制棒状、管状(外形可以是圆形成多 角形,但上下尺寸大小一致)的坯体,然后待晾干 后,可以再切割成所需长度的制品。一般常用挤 制φl~30 mm的管、棒及壁厚可小至0.2mm左右细 管等。随着粉料质量和泥料可塑性的提高,也用 来挤制长100~200mm,厚0.2~3mm片状坯膜,半 干后再冲制成不同形状的片状制品,或用来挤制 100~200孔/cm2的蜂窝状或筛格式穿孔瓷制品。
3 4~ 12 14 17 18 20 25 30 40 50 10
0. 0.3 0.4 0.5 0.6 1.0 2.0 2.5 3.5 5.5 7.5 2
陶瓷成型方法
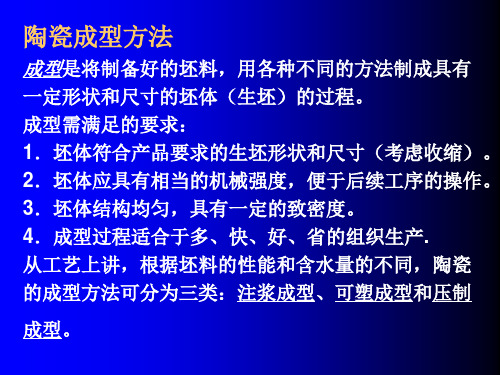
2、热压铸成型工艺
3、热压铸成型工艺 主要工艺参数:
(1) 腊浆温度:60~75℃,温度升 高,则腊浆的粘度下降,坯体致 密,但冷却收缩相应大。温度过 低,则易出现欠注、皱纹等缺陷。 (2) 钢模温度。决定坯体冷却凝固 的速度。一般为20~30℃。 (3) 成型压力:与浆桶深度、料浆 性能有关。压力升高,坯体的致 密度增加,坯体的收缩程度下降。 一般可以采用0.3~0.5 MPa。
3、强化注浆成型方法
(注浆方法的改进)
在注浆过程中人为地施加外力,加速注浆过程的进行,使吸浆 速度和坯体强度得到明显改善的方法。 1) 真空注浆 模具外抽真空,或模具在负压下成型,造成模具内外压力差, 提高成型能力,减小坯体的气孔和针眼。
2)
离心注浆
使模型在旋转情况下进浆,料浆在离心力的作用下紧靠 模壁形成致密的坯体。气泡较轻,易集中在中间最后破 裂排出,故可提高吸浆速度与制品质量。要求:泥浆中 的颗粒分布范围窄,否则大颗粒集中在靠近模型的坯体 表面,而小颗粒集中在坯体内面,造成坯体组织不均匀, 收缩不一致。
2. 滚压成型的主要控制因素 (1) 对泥料的要求:水分低、可塑性好。成型时模具 既有滚动,又有滑动,泥料主要受压延力的作用。要求有 一定的可塑性和较大的延伸量。可塑性低,易开裂;可塑 性高,水分多易粘滚头。阳模滚压和阴模滚压对泥料的要 求有差别。阴模滚压受模型的承托和限制,可塑性可以稍 低,水分可稍多。 (2) 滚压过程控制:分压下(轻)、压延(稳)、抬起 (慢)阶段。 (3) 主轴转速(n1)和滚头转速(n2) :控制生产效率; 对坯料的施力形式,控制坯体的密度均匀和表面光洁。 滚压头的温度热滚压:100~130℃,在泥料表面产生一 层气膜,防止粘滚头,坯体表面光滑。冷滚压:可用塑料 滚压头,如聚四氟乙烯。
无机非金属材料工学 成型

六、触变性与反触变性
定义:粘土泥浆或可塑泥团受到振动或搅拌时,粘度会降低 而流动性增加静置后能恢复原来状态。反之,相同泥浆放置一段 时间后,在维持原有水分的情况下会增加粘度,出现变稠和固化 现象,上述现象可重复无数次,统称为触变性。
触变环曲线 a-正触变环;b-负触变环
成型泥料要有一定的触变性,但不要太大。
第三节 浆料的成型
一、成型的工艺原理
多属于粘塑性体,其中液相是连续的(如水泥砂浆、混
凝土浆、陶瓷泥浆、耐火材料浇注料等)。
成型基本过程: 流动→充满模型→具有模型的形状→脱水或水化→坯体 →脱模→干燥或水化→完全的固体(弹性体)。 控制浆体的流动度
触变性是指在剪切应力保持一定时,表观粘度将随着剪切应 力作用时间的持续而减小,剪切应变速率将不断增加的性质。或 者,当剪切应变速率保持不变时,剪切应力将逐渐下降。具有这 种性质的材料称为正触变材料。 反触变性:表观粘度随着应力作用的时间而增加。
触变性的大小可用触变环的大小和方向来表示:逆时针走向 的是正触变,顺时针走向的代表反触变。
Na-粘土+CaSO4+Na2SiO4 Ca—粘土+CaSiO3+Na2SO4
使得靠近石膏模表面的一层Na-粘土变为Ca-粘土,泥浆由悬 浮状态转为聚沉。石膏起着絮凝剂的作用,促进泥浆絮凝硬化, 颗粒成棚架结构,有利于排水,减少泥坯的阻力,缩短成坯时 间。
3.成型速度 成型速度可由阿德柯克推导出来的吸浆速度公式来计算: 吸浆速率: 将上式移项积分得:
(2)压力注浆可以减少坯体的干燥收缩 常压下注浆时,与坯体表面平行方向上的干燥收缩约 为3%,与坯体表面垂直方向上的干燥收缩为2%。在7MPa 压力注浆时,上述二方向上的收缩分别减小至0.8%及0.3 %。 (3)压力注浆可降低坯体脱模后留存的水分 常压注浆时,坯体平均留存水分约19.5%,在7MPa压 力下成型的坯体只含17%水分。
- 1、下载文档前请自行甄别文档内容的完整性,平台不提供额外的编辑、内容补充、找答案等附加服务。
- 2、"仅部分预览"的文档,不可在线预览部分如存在完整性等问题,可反馈申请退款(可完整预览的文档不适用该条件!)。
- 3、如文档侵犯您的权益,请联系客服反馈,我们会尽快为您处理(人工客服工作时间:9:00-18:30)。
二、塑压成型
►
►
将可塑泥料放在模型中在 常温下压制成型的方法。 常温下压制成型的方法。 模型:蒸压型的α 模型:蒸压型的α-半水石 膏,内部盘绕多孔性纤维 管,用以通压缩空气或抽 真空。 真空。成型压力与坯泥的 含水量有关。 含水量有关。坯体的致密 度较旋坯法、滚压法都高。 度较旋坯法、滚压法都高。 因此,需要提高模型强度: 因此,需要提高模型强度: 采用多孔性树脂模、 采用多孔性树脂模、多孔 金属模。 金属模。
陶瓷可塑成型法
陶瓷成型技法之一
► 可塑法成型是用各种不同的外力对具有可塑
性的坯料(泥团)进行加工,迫使坯料在外 力作用下发生可塑变形而制成生坯的成型方 法。 ► 可塑成型方法是古老的一种成型方法。我国 古代采用的手工拉坯(景德镇古窑厂仍采用 此方法)就是最原始的可塑法。
一、滚压成型
►பைடு நூலகம்
工艺原理和特点: 工艺原理和特点:成型时盛放着泥 料的石膏模型和滚压头分别绕自己 的轴线以一定的速度同方向旋转。 的轴线以一定的速度同方向旋转。 滚压头在旋转的同时逐渐靠近石膏 模型,对泥料进行滚压成型。 模型,对泥料进行滚压成型。 优点:坯体致密、组织结构均匀、 优点:坯体致密、组织结构均匀、 表面质量高。阳模滚压(外滚压): 表面质量高。阳模滚压(外滚压): 滚压头决定坯体形状和大小,模型 滚压头决定坯体形状和大小, 决定内表面的花纹。阴模滚压( 决定内表面的花纹。阴模滚压(内 滚压):滚压头形成坯体的内表面。 ):滚压头形成坯体的内表面 滚压):滚压头形成坯体的内表面。
三、旋压成型 四、其他塑性方法 雕塑、印坯、 雕塑、印坯、拉坯
主要用途
► 可塑成型法多用来生
产大型或特别复杂形 耐火制品。
实际操作图
作品赏析一
作品赏析二
再 见
►
滚压成型的主要控制因素
►
(1) 泥料的要求:水分低、可塑性好。成型时模具 泥料的要求:水分低、可塑性好。 既有滚动对,又有滑动,泥料主要受压延力的作用。 既有滚动对,又有滑动,泥料主要受压延力的作用。要求有一定的可塑 性和较大的延伸量。可塑性低,易开裂;可塑性高,水分多易粘滚头。 性和较大的延伸量。可塑性低,易开裂;可塑性高,水分多易粘滚头。 阳模滚压和阴模滚压对泥料的要求有差别。 阳模滚压和阴模滚压对泥料的要求有差别。阴模滚压受模型的承托和限 可塑性可以稍低,水分可稍多。 制,可塑性可以稍低,水分可稍多。 (2) 滚压过程控制:分压下(轻)、压延(稳)、抬起(慢)阶段 滚压过程控制:分压下( )、压延 压延( )、抬起 抬起( 主轴转速(n1)和滚头转速(n2) 控制生产效率; (3) 主轴转速(n1)和滚头转速(n2) :控制生产效率;对坯料的施 力形式,控制坯体的密度均匀和表面光洁。 力形式,控制坯体的密度均匀和表面光洁。 滚压头的温度热滚压:100~130℃ 在泥料表面产生一层气膜, 滚压头的温度热滚压:100~130℃,在泥料表面产生一层气膜,防止 粘滚头,坯体表面光滑。冷滚压:可用塑料滚压头,如聚四氟乙烯等。 粘滚头,坯体表面光滑。冷滚压:可用塑料滚压头,如聚四氟乙烯等。
► ►
滚压成型常见缺陷
► ► ► ► ►
1)粘滚头:泥料可塑性太强或水分过多;滚头转速太快; 粘滚头:泥料可塑性太强或水分过多;滚头转速太快; 滚头过于光滑及下降速度慢;滚头倾角过大。 滚头过于光滑及下降速度慢;滚头倾角过大。 2)开裂:坯料可塑性差;水分太少,水分不均匀;滚头温 开裂:坯料可塑性差;水分太少,水分不均匀; 度太高,坯体表面水分蒸发过快,引起坯体内应力增大。 度太高,坯体表面水分蒸发过快,引起坯体内应力增大。 3)鱼尾:坯体表面呈现鱼尾状微凸起。原因是滚头摆动; 鱼尾:坯体表面呈现鱼尾状微凸起。原因是滚头摆动; 滚头抬离坯体太快。 滚头抬离坯体太快。 4)底部上凸:滚头设计不当或滚头顶部磨损; 滚头安装角 底部上凸:滚头设计不当或滚头顶部磨损; 度不当;泥料水分过低。 度不当;泥料水分过低。 5)花底:坯体中心呈菊花状开裂。原因是模具过干过热; 花底:坯体中心呈菊花状开裂。原因是模具过干过热; 泥料水分少;转速太快;滚头中心温度高;滚头下压过猛; 泥料水分少;转速太快;滚头中心温度高;滚头下压过猛; 新模具表面有油污。 新模具表面有油污。