蒸发器尺寸设计
满液式蒸发器的设计

满液式蒸发器的设计3 满液式蒸发器的设计3.1 制冷剂流量的确定制冷剂压焓图:图 3.1由蒸发温度t0 5℃,t k 40 ℃,t g 5℃,附表13(P341)和附图5(P373)查得:h1 407.143kJ /(kg.K) ,h2 430.050kJ /(kg.K ) ,h3单位制冷量:制冷剂流量:选用φ10×1低螺纹铜管,取水流速度u 1.2m/ s , 则每流程的管子数Zh3 h4 242.963kJ/(kg.K) , 1 340.3556 10 3 m 3 3 /kg , 2 17.9876 3310 m /kg3 0.88392 10 3m3/kg ,4 9.0003 10 3m3 /kg根据文献1《制冷原理及设备》h4 249.686kJ /(kg.K)q0 h1 h4 407.143 242.963 164.180kJ/(kg.K) (P31)(3.1)qmQ0 70 0.4263kg / sq0 164.180P31) (3.2)3.2 载冷剂流量的确定qvs70Qc p(t s1 t s2) 1000 4.187 5333.3436 10 3m3/ s (P246)(3.3)Z4dq i v 2su 3.144(130.3423)26 1100 6 1.255.46根(3.4)圆整后, Z=56 根。
实际水流速度3u4dq i v 2sZ 3.144(130.3423)62 1100 6 56 1.1884m/s 1.2m/s3.4 管程与有效管长假定热流密度 q=6600W /m 2, 则所需的传热面积3Q k 70 1032F 0 k10.61m 2 0q 6600管子与管子有效长度的乘积采用管子成正三角形排列的布置方案,管距 s=14mm 对, 不同流程数 N ,有效单管长l c ,总根数 NZ,壳体直径 D 及长径比 l c /D 进行组合计算,组合计算结果表 3.1 不同流程数 N 对应的管长 l c 及l c /D4 3.3436 10 36(3.6)NI c10.61 F06.03md 0Z 3.14 0.01 56(3.7)(3.5)如表 3.1 所示:表 3.1 组合计算结果3.5 传热系数的确定 3.5.1蒸发器中污垢的热阻由文献 1《制冷原理及设备》表 9-1 可知: 管外热阻 0 9 10 5m 2?0 C/W 管内热阻 i 4.5 10 5m 2?0 C/W3.5.2平均传热温差平均传热温差:(3.8)3.5.3管内换热系数查饱和水物性表得:3ud i =1.2 8 1063 =78951.216 10 6假设壁温 t w 为 8.5℃,查水的物性表,得 Pr w 11.75 ,假设管长为 1.8m ,t s1 t s2mt t s1 0 lnt s2 t 056.17 ℃ ln 94(3.9)管内强制对流换热系数由文献 5《传热学》(P 248)公式 (f / 8)(Re 1000) Pr f 2/ 31 12.7 f /8(Pr f1 (d )2/31) l其中(Pr f )0.01 (Pr w )(1.82 lg Re 1.64)冷却水的定性温度 t s :t t s1 t s2 14 9 ts s2 211.5℃(6-21a)式可知:ctddi(3.10)999.25kg / m 3 ,1.216 106m 2 / s58.15 210 2W /(m k) ,Pr f 8.77则: Re =5146.53.5.5壁温和热流密度的估算传热过程分为两部分:第一部分是传热量经过制冷剂的传热过程;第二部 分是传热量经过污垢层、管壁、管内污垢层以及冷却水的传热过程。
蒸发器的设计计算
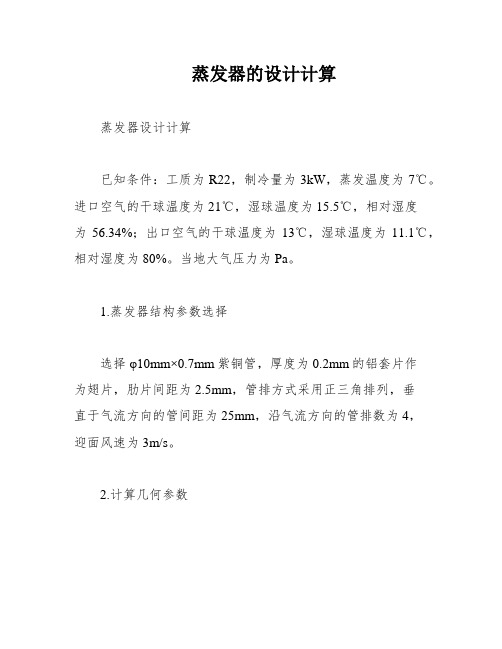
蒸发器的设计计算蒸发器设计计算已知条件:工质为R22,制冷量为3kW,蒸发温度为7℃。
进口空气的干球温度为21℃,湿球温度为15.5℃,相对湿度为56.34%;出口空气的干球温度为13℃,湿球温度为11.1℃,相对湿度为80%。
当地大气压力为Pa。
1.蒸发器结构参数选择选择φ10mm×0.7mm紫铜管,厚度为0.2mm的铝套片作为翅片,肋片间距为2.5mm,管排方式采用正三角排列,垂直于气流方向的管间距为25mm,沿气流方向的管排数为4,迎面风速为3m/s。
2.计算几何参数翅片为平直套片,考虑套片后的管外径为10.4mm,沿气流方向的管间距为21.65mm,沿气流方向套片的长度为86.6mm。
设计结果为每米管长翅片表面积为0.3651m²/m。
每米管长翅片间管子表面积为0.03m²/m。
每米管长总外表面积为0.3951m²/m。
每米管长管内面积为0.027m²/m。
每米管长的外表面积为0.m²/m。
肋化系数为14.63.3.计算空气侧的干表面传热系数1)空气的物性空气的平均温度为17℃。
空气在下17℃时的物性参数为:密度为1.215kg/m³,比热容为1005kJ/(kg·K)。
2)空气侧传热系数根据空气侧传热系数的计算公式,计算得到空气侧的干表面传热系数为12.5W/(m²·K)。
根据给定的数据,蒸发器的尺寸为252.5mm×1mm×10.4mm。
空气在最窄截面处的流速为5.58m/s,干表面传热系数可以用小型制冷装置设计指导式(4-8)计算得到,计算结果为68.2W/m2·K。
在确定空气在蒸发器内的变化过程时,根据进出口温度和焓湿图,可以得到空气的进出口状态点1和点2的参数,连接这两个点并延长与饱和气线相交的点w的参数为hw25kJ/kg。
dw6.6g/kg。
tw8℃。
2吨双效蒸发器
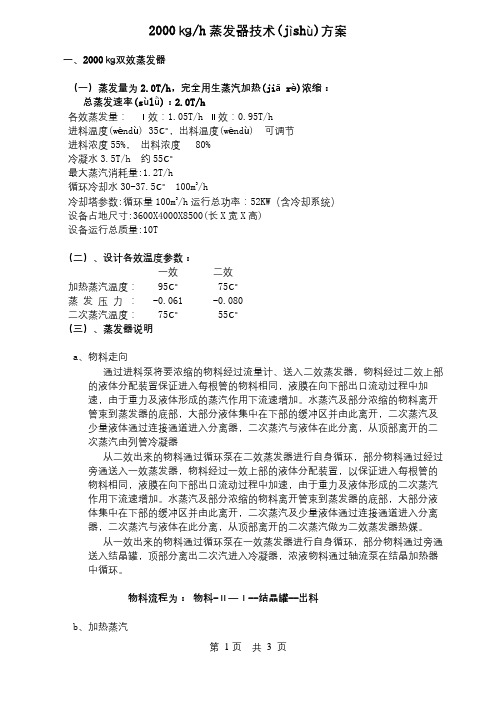
2000㎏/h蒸发器技术(jìshù)方案一、2000㎏双效蒸发器(一)蒸发量为2.0T/h,完全用生蒸汽加热(jiā rè)浓缩:总蒸发速率(sùlǜ):2.0T/h各效蒸发量:Ⅰ效:1.05T/h Ⅱ效:0.95T/h进料温度(wēndù) 35℃,出料温度(wēndù) 可调节进料浓度55%,出料浓度 80%冷凝水3.5T/h 约55℃最大蒸汽消耗量:1.2T/h循环冷却水30-37.5℃ 100m3/h冷却塔参数:循环量100m3/h运行总功率:52KW(含冷却系统)设备占地尺寸:3600X4000X8500(长X宽X高)设备运行总质量:10T(二)、设计各效温度参数:一效二效加热蒸汽温度: 95℃ 75℃蒸发压力: -0.061 -0.080二次蒸汽温度: 75℃ 55℃(三)、蒸发器说明a、物料走向通过进料泵将要浓缩的物料经过流量计、送入二效蒸发器,物料经过二效上部的液体分配装置保证进入每根管的物料相同,液膜在向下部出口流动过程中加速,由于重力及液体形成的蒸汽作用下流速增加。
水蒸汽及部分浓缩的物料离开管束到蒸发器的底部,大部分液体集中在下部的缓冲区并由此离开,二次蒸汽及少量液体通过连接通道进入分离器,二次蒸汽与液体在此分离,从顶部离开的二次蒸汽由列管冷凝器从二效出来的物料通过循环泵在二效蒸发器进行自身循环,部分物料通过经过旁通送入一效蒸发器,物料经过一效上部的液体分配装置,以保证进入每根管的物料相同,液膜在向下部出口流动过程中加速,由于重力及液体形成的二次蒸汽作用下流速增加。
水蒸汽及部分浓缩的物料离开管束到蒸发器的底部,大部分液体集中在下部的缓冲区并由此离开,二次蒸汽及少量液体通过连接通道进入分离器,二次蒸汽与液体在此分离,从顶部离开的二次蒸汽做为二效蒸发器热媒。
从一效出来的物料通过循环泵在一效蒸发器进行自身循环,部分物料通过旁通送入结晶罐,顶部分离出二次汽进入冷凝器,浓液物料通过轴流泵在结晶加热器中循环。
蒸发器设计
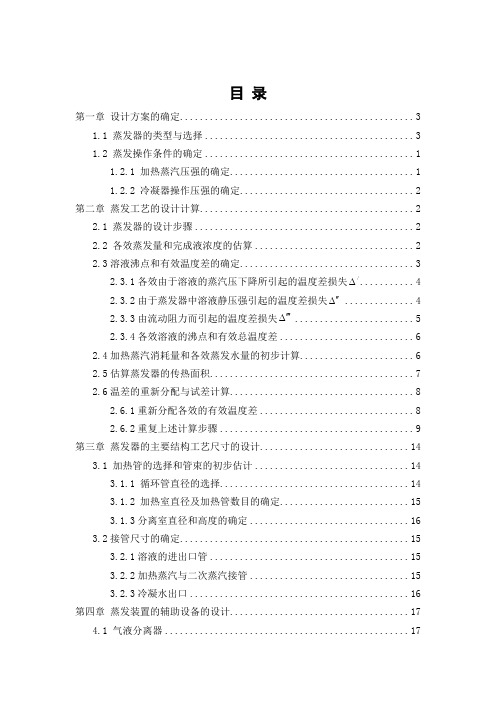
目录第一章设计方案的确定 (3)1.1 蒸发器的类型与选择 (3)1.2 蒸发操作条件的确定 (1)1.2.1 加热蒸汽压强的确定 (1)1.2.2 冷凝器操作压强的确定 (2)第二章蒸发工艺的设计计算 (2)2.1 蒸发器的设计步骤 (2)2.2 各效蒸发量和完成液浓度的估算 (2)2.3溶液沸点和有效温度差的确定 (3)2.3.1各效由于溶液的蒸汽压下降所引起的温度差损失∆/ (4)2.3.2由于蒸发器中溶液静压强引起的温度差损失∆'' (4)2.3.3由流动阻力而引起的温度差损失∆''' (5)2.3.4各效溶液的沸点和有效总温度差 (6)2.4加热蒸汽消耗量和各效蒸发水量的初步计算 (6)2.5估算蒸发器的传热面积 (7)2.6温差的重新分配与试差计算 (8)2.6.1重新分配各效的有效温度差 (8)2.6.2重复上述计算步骤 (9)第三章蒸发器的主要结构工艺尺寸的设计 (14)3.1 加热管的选择和管束的初步估计 (14)3.1.1 循环管直径的选择 (14)3.1.2 加热室直径及加热管数目的确定 (15)3.1.3分离室直径和高度的确定 (16)3.2接管尺寸的确定 (15)3.2.1溶液的进出口管 (15)3.2.2加热蒸汽与二次蒸汽接管 (15)3.2.3冷凝水出口 (16)第四章蒸发装置的辅助设备的设计 (17)4.1 气液分离器 (17)4.2蒸汽冷凝器主要类型 (17)4.3蒸汽冷凝器的设计与选用 (19)4.3.1工作水量的计算 (19)4.3.2喷射器结构尺寸的计算 (19)4.3.3射流长度的决定 (22)第五章设计结果一览表 (22)结束语.............................................. 错误!未定义书签。
主要参考文献........................................ 错误!未定义书签。
蒸发器技术规范书

蒸发器技术规范书-标准化文件发布号:(9456-EUATWK-MWUB-WUNN-INNUL-DDQTY-KII蒸发器技术规范书1.技术规范1 总则1.1 本规范书专用于皇明洁能控股有限公司太阳能光热项目蒸发器技术规范书,它包括蒸发器本体及辅助设备的功能设计、结构、性能、安装和试验等的技术要求。
1.2 设备生产厂家具备一二类或者以上压力容器制造和设计资质;1.3 在签订合同之后,需方有权提出因规范标准和规程发生变化而产生的一些补充要求,具体项目由供、需双方共同商定。
2 设计要求(注:未填写内容由供货厂家填写)2.1 蒸发器技术规范书2.1.1 型号:2.1.2 型式:卧式2.1.3 蒸发器尺寸:2.1.4 蒸汽进管径: mm2.1.5 水进出口管径: mm2.1.6蒸发器(水侧)阻力:2.1.7 设备台数:1台2.1.8 高温油侧:供油300℃,回油:180℃,油量:5.8t/h2.1.9蒸汽侧:蒸发器出口温度:200℃,给水温度:60℃,蒸汽流量:0.5t/h 2.1.10 蒸发器 (油侧)工作压力:0.2MPa2.1.11蒸发器(水侧)工作压力:1.2Mpa2.1.12 蒸汽换热后导热油温度:低于180℃3 技术要求3.1 设备说明本期蒸发器都应有结构上独立的本体。
3.2 技术性能要求3.2.1 蒸发器换热能力蒸发器应在需方提供的设计条件下能达到保证换热能力,并有不低于20%的余量。
3.2.2 在正常工作条件下,不出现任何渗漏。
3.2.3 蒸发器汽侧设计压力2.5Mpa。
3.2.4 蒸发器汽侧设计温度200℃。
3.2.5 各接口法兰详细的连接尺寸及接口方位应与设计院协商后确定,法兰应符合HG20592-97系列标准。
3.3 液温控制系统温度控制由人工设定,电动调节阀完成。
推荐选用西门子品牌。
3.4 设备制造要求设备制造应按《中华人民共和国国家标准》蒸发器有关标准进行。
4 质量保证及考核试验4.1 设备产品设计、制造应遵照的规范和标准4.1.1 有新版本实施时应采用最新版本。
蒸发器的设计
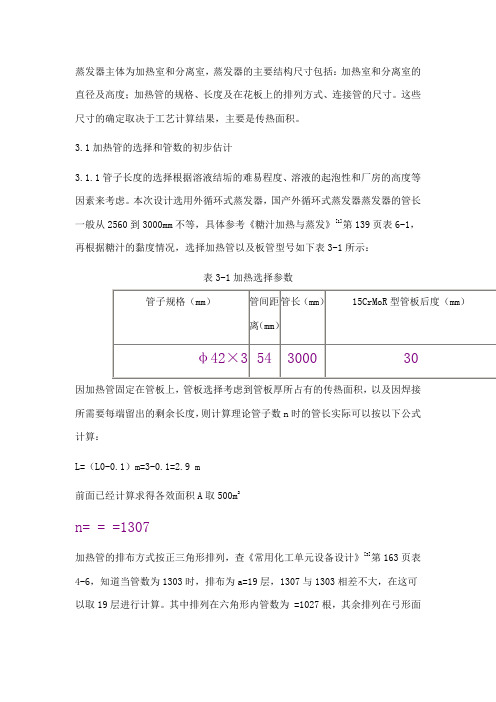
蒸发器主体为加热室和分离室,蒸发器的主要结构尺寸包括:加热室和分离室的直径及高度;加热管的规格、长度及在花板上的排列方式、连接管的尺寸。
这些尺寸的确定取决于工艺计算结果,主要是传热面积。
3.1加热管的选择和管数的初步估计3.1.1管子长度的选择根据溶液结垢的难易程度、溶液的起泡性和厂房的高度等因素来考虑。
本次设计选用外循环式蒸发器,国产外循环式蒸发器蒸发器的管长一般从2560到3000mm不等,具体参考《糖汁加热与蒸发》[1]第139页表6-1,再根据糖汁的黏度情况,选择加热管以及板管型号如下表3-1所示:表3-1加热选择参数因加热管固定在管板上,管板选择考虑到管板厚所占有的传热面积,以及因焊接所需要每端留出的剩余长度,则计算理论管子数n时的管长实际可以按以下公式计算:L=(L0-0.1)m=3-0.1=2.9 m前面已经计算求得各效面积A取500m2n= = =1307加热管的排布方式按正三角形排列,查《常用化工单元设备设计》[3]第163页表4-6,知道当管数为1303时,排布为a=19层,1307与1303相差不大,在这可以取19层进行计算。
其中排列在六角形内管数为 =1027根,其余排列在弓形面积内,如果按标准间距即管间距离54mm排列,则有四根管排不下,四根管的总面积为:A3=3.1415926×0.042×2.9×3=1.53 m2鉴于前面已经取1.11的安全系数,如果现在取1303根管,则总面积为:=500-1.53=498.47 安全系数为 K= =1.108在安全系数范围内,所以可以不要三根管,取1303根。
3.1.2加热壳体的直径计算D=t(b-1)+2eD-----壳体直径,m;t------管间距,m;b-----沿直径方向排列的管子数目;,在此取 e-----外层管的中心到壳体内壁的距离,一般取e=(1.0~1.5)d1.5。
b =2a-1=2×19-1=37D=0.054×(37-1)+2×1.5×0.042=2.07m参考《糖厂技术准备第三册》[6]第198页表9-2,本次设计常用标准形式的外循环式蒸发器,型号为TWX-550,有关参数如下表所示取标准的壳体直径为2400mm,具体参数如下表3-2-1,3-2-2所示:表3-2-1外循环管蒸发器有关技术参数表3-2-2 管蒸发器有关技术参数3.3 分离室直径与高度的校核分离室的直径取决于分离室的体积,而分离室体积又与二次蒸汽的体积流量及蒸发体积强度有关。
蒸发器尺寸设计
蒸发器尺寸设计集团文件版本号:(M928-T898-M248-WU2669-I2896-DQ586-M1988)蒸发器工艺尺寸计算加热管的选择和管数的初步估计1加热管的选择和管数的初步估计蒸发器的加热管通常选用38*2.5mm无缝钢管。
加热管的长度一般为0.6—2m,但也有选用2m以上的管子。
管子长度的选择应根据溶液结垢后的难以程度、溶液的起泡性和厂房的高度等因素来考虑,易结垢和易起泡沫溶液的蒸发易选用短管。
根据我们的设计任务和溶液性质,我们选用以下的管子。
可根据经验我们选取:L=2M,38*2.5mm可以根据加热管的规格与长度初步估计所需的管子数n’,=124(根)式中S=----蒸发器的传热面积,m2,由前面的工艺计算决定(优化后的面积);d0----加热管外径,m; L---加热管长度,m;因加热管固定在管板上,考虑管板厚度所占据的传热面积,则计算n’时的管长应用(L—0.1)m.2循环管的选择循环管的截面积是根据使循环阻力尽量减小的原则考虑的。
我们选用的中央循环管式蒸发器的循环管截面积可取加热管总截面积的40%--100%。
加热管的总截面积可按n’计算。
循环管内径以D1表示,则所以mm对于加热面积较小的蒸发器,应去较大的百分数。
选取管子的直径为:循环管管长与加热管管长相同为2m。
按上式计算出的D1后应从管规格表中选取的管径相近的标准管,只要n和n’相差不大。
循环管的规格一次确定。
循环管的管长与加热管相等,循环管的表面积不计入传热面积中。
3加热室直径及加热管数目的确定加热室的内径取决于加热管和循环管的规格、数目及在管板撒谎能够的排列方式。
加热管在管板上的排列方式有三角形排列、正方形排列、同心圆排列。
根据我们的数据表加以比较我们选用三角形排列式。
管心距t为相邻两管中心线之间的距离,t一般为加热管外径的1.25—1.5倍,目前在换热器设计中,管心距的数据已经标准化,只要确定管子规格,相应的管心距则是定值。
6平方薄膜蒸发器参数
6平方薄膜蒸发器是一种常用的传热设备,广泛应用于化工、制药、食品等行业。
它通过在薄膜表面形成液膜,使液体在薄膜上形成薄膜层流,从而提高传热效率和传质效率。
下面将详细介绍6平方薄膜蒸发器的参数。
一、结构参数1. 蒸发器尺寸:6平方薄膜蒸发器的有效蒸发面积为6平方米,通常采用长方形或圆柱形结构。
2. 材料选择:常见的材料包括不锈钢、玻璃钢等,具有良好的耐腐蚀性和传热性能。
3. 薄膜厚度:薄膜的厚度通常在0.1mm-0.3mm之间,可以根据具体工艺要求进行选择。
二、操作参数1. 进料流量:进料流量是指单位时间内进入蒸发器的液体流量,通常以升/小时为单位。
进料流量的大小会影响薄膜层的稳定性和传热效果,需要根据具体工艺条件进行调整。
2. 进料浓度:进料浓度是指进入蒸发器的液体中所含溶质的质量百分比。
进料浓度的高低会影响薄膜层的稳定性和传质效果,需要根据具体工艺要求进行调整。
3. 蒸汽压力:蒸汽压力是指蒸发器内部的蒸汽压力,通常以帕斯卡(Pa)为单位。
蒸汽压力的大小与传热效率密切相关,需要根据具体工艺要求进行调整。
4. 出料浓度:出料浓度是指从蒸发器中排出的液体中所含溶质的质量百分比。
出料浓度的高低受进料浓度、进料流量和蒸汽压力等参数的影响,需要根据具体工艺要求进行调整。
三、传热参数1. 传热系数:传热系数是指单位面积上单位时间内传递的热量,通常以瓦特/平方米·开尔文(W/(m²·K))为单位。
传热系数的大小与薄膜表面的温度差、薄膜厚度、薄膜材料和流体性质等因素有关,可以通过实验或计算进行确定。
2. 温差:温差是指薄膜表面和进料液体之间的温度差,通常以摄氏度(℃)为单位。
温差的大小对传热效果有着重要影响,需要根据具体工艺要求进行调整。
四、其他参数1. 清洗方式:薄膜蒸发器的清洗方式有物理清洗和化学清洗两种,具体选择取决于薄膜材料和工艺要求。
2. 能耗:能耗是指单位时间内薄膜蒸发器所消耗的能量,通常以千瓦时(kWh)为单位。
蒸发器制作有关数据
蒸发器制作有关数据:《蒸发管面积计算》1:单效蒸发器《蒸发强度:Kg/m²./h》 80~100Kg。
2:双效蒸发器《蒸发强度:Kg/m²./h》 30~32Kg。
吗3;三效蒸发器《蒸发强度:Kg/m²./h》 18~20Kg。
4:四效蒸发器《蒸发强度:Kg/m²./h》 14~15Kg。
5:五效蒸发器《蒸发强度:Kg/m²./h》 9~12Kg。
蒸发器蒸汽耗量参考数据1:单效蒸发器:蒸发1吨水分需蒸汽: 920~1050Kg2: 双效蒸发器:蒸发1吨水分需蒸汽: 490~530Kg3: 三效蒸发器:蒸发1吨水分需蒸汽: 320~350Kg4: 四效蒸发器:蒸发1吨水分需蒸汽: 220~250Kg5: 五效蒸发器:蒸发1吨水分需蒸汽: 160~180Kg蒸发器各效配管面积参考双效蒸发器:Ⅰ效:66% Ⅱ效:34 %三效蒸发器:Ⅰ效:41% 。
Ⅱ效:37.5 %。
Ⅲ效:21.5% 四效蒸发器:Ⅰ效:34%。
Ⅱ效:27 %。
Ⅲ效:20%。
Ⅳ效:19 %。
五效蒸发器:Ⅰ效:36% Ⅱ效:26 % Ⅲ效:21%Ⅳ效:16 %。
Ⅴ效:11 %。
蒸发器管板孔距参考:管直径加15~18毫米蒸发管面积计算是按管子外径计算。
蒸发器管板分配管数参考数据:蒸发管在管板上的分配是按等边六角形的结构分配,在大型蒸发器的管板上,六边形以外在不影响管板圆结构的基础上,还可以排相当数量的管子,为方便计算各效的管径与管板尺寸。
可参考表1。
六角形的边行数中心行数可布管数量3 5 194 7 375 9 616 11 91 - 977 13 127 - 1338 15 169 - 1979 17 217 - 23510 19 271 - 29511 21 331 - 35512 23 397 - 42713 25 469 - 51114 27 549 - 60115 29 631 - 68516 31 721 - 82317 33 784 - 91618 35 919 - 111719 37 990 - 115220 39 1141 - 1300计算管板直径: D =中心管数x (管径+边距)+60效体与分离器直径比例参考数据:效体 1 比 1.25 – 1.4 蒸发量计算:湿物料总:G1物料含水率:W1。
空调蒸发器设计计算方法
计算过程1)空气进出口状态:进气:干球温度t1=27℃,湿球温度t1s=19℃,h1=54 KJ/Kg.干出气:干球温度t12=14℃,湿球温度t12s=12℃,h12=35.8 KJ/Kg.干肋管外表面平均温度:tss=10.8℃,hss=31 KJ/Kg.干2)单位管长参数值管间距p1=0.0254;排间距p2=0.022;铜管外径d0=0.00952;铜管内径di=0.00882;片厚δf=0.00011;片距e1=0.0016;铝箔导热系数λ=204 w/m.k每米管长肋片外表面积:AF=(p1*p2-πd0²/4)*2*1/e1 =0.61每米管长肋片基管外表面积:AP=πd0*(e1-δf)*1/e1 =0.027每米管长内表面积:Ai = π* di * 1 =0.0276每米管长总外表面积:AFP = AF + AP =0.637肋化系数:τ=AFP / Ai =23肋通系数:a =AFP / (p1 * 1) =25净面比:ε=(p1 - d0) * (e1 -δf) / (p1 * e1) =0.582)计算干工况下空气侧换热系数α选迎面风速:Va=1.7 m/s最窄截面处流动速度:Vmax=Va/ε选取管排数:N=2沿气流方向肋片长度:L=N*p2当量直径:de= 2 * (p1 - d0) * (e1 -δf) / ((p1 - d0) + (e1 -δf)) =2.72mm雷诺数:Re = 1.2 * Vmax * de / (1.815 * 10 ^ (-5)) =525.9干工况下空气侧换热系数α= c1 * c2 * (2.568 * 10 ^ (-2) / de) * ((L / de) ^ (N)) * (Re ^ (m)) =56.7 (只适用于Re>=500)α1=1.1*α=62.4 (铜管错排)c1 = 1.36 - 0.24 * Re / 1000c2 = 0.518 - (2.315 * 10 ^ (-2) * (L / de)) + (4.25 * 10 ^ (-4) * (L / de) ^ 2) - (3 * 10 ^ (-6) * (L / de) ^ 3)3)冷却效率η= (h1 - h12) / (1.005 * (h1 - hss)) =0.7874)校核管排数η=1- Exp(-α* a* N’ / (1005 * 1.2 * Va))=0.784(N’=3)|N’-N|<0.5,调整迎风面积|N’-N|>0.5,增减排数求满足η5)计算湿工况下空气侧换热系数αe析湿系数:ξ= (h1 - h12) / (1.005 * (t1 - t12)) =1.39计算肋片效率m = (2 *ξ* α/ (204 * 0.00011)) ^ (0.5)l=(1.065*p1/2-d0/2)*(1+0.805lg((1.065*p1/2)/(d0/2))ηf=th(m*l)/(m*l)湿工况下空气侧放热系数αe=ξ*α1*((ηf*AF+AP)/AFP) =676)初估迎风面积、总传热面积空气流量Ma=Q/(h1-h12)=0.275迎风面积Fa=Ma/(1.2*Va) =0.135总传热面积Ft= Fa * a * N =6.767)制冷剂侧放热系数热流密度q0=Q/(Ft*τ) =17025制冷剂质量流速q0>10000 时Vr=210 kg/(㎡.s)确定通路数n=Mr/(Vr*πd0²/4) =3实际制冷剂质量流速Vrm= Mr/(n*πd0²/4) =184.4制冷剂管内放热系数B = 1.22 + ((1.54 - 1.22) / 20 * (10 + t0))式中:t0是蒸发温度。
- 1、下载文档前请自行甄别文档内容的完整性,平台不提供额外的编辑、内容补充、找答案等附加服务。
- 2、"仅部分预览"的文档,不可在线预览部分如存在完整性等问题,可反馈申请退款(可完整预览的文档不适用该条件!)。
- 3、如文档侵犯您的权益,请联系客服反馈,我们会尽快为您处理(人工客服工作时间:9:00-18:30)。
蒸发器工艺尺寸计算?
加热管的选择和管数的初步估计
1加热管的选择和管数的初步估计
蒸发器的加热管通常选用38*2.5mm无缝钢管。
加热管的长度一般为0.6—2m,但也有选用2m以上的管子。
管子长度的选择应根据溶液结垢后的难以程度、溶液的起泡性和厂房的高度等因素来考虑,易结垢和易起泡沫溶液的蒸发易选用短管。
根据我们的设计任务和溶液性质,我们选用以下的管子。
可根据经验我们选取:L=2M,38*2.5mm
可以根据加热管的规格与长度初步估计所需的管子数n’,
=124(根)
式中S=----蒸发器的传热面积,m2,由前面的工艺计算决定(优化后的面积);
d0----加热管外径,m;????? L---加热管长度,m;? 因加热管固定在管板上,考虑管板厚度所占据的传热面积,则计算n’时的管长应用(L—0.1)m.
2循环管的选择
???? 循环管的截面积是根据使循环阻力尽量减小的原则考虑的。
我们选用的中央循环管式蒸发器的循环管截面积可取加热管总截面积的40%--100%。
加热管的总截面积可按n’计算。
循环管内径以D1表示,则
所以mm
对于加热面积较小的蒸发器,应去较大的百分数。
选取管子的直径为:循环管管长与加热管管长相同为2m。
按上式计算出的D1后应从管规格表中选取的管径相近的标准管,只要n和n’相差不大。
循环管的规格一次确定。
循环管的管长与加热管相等,循环管的表面积不计入传热面积中。
3加热室直径及加热管数目的确定
?? 加热室的内径取决于加热管和循环管的规格、数目及在管板撒谎能够的排列方式。
?? 加热管在管板上的排列方式有三角形排列、正方形排列、同心圆排列。
根据我们的数据表加以比较我们选用三角形排列式。
管心距t为相邻两管中心线之间的距离,t一般为加热管外径的1.25—1.5倍,目前在换热器设计中,管心距的数据已经标准化,只要确定管子规格,相应的管心距则是定值。
我们选用的设计管心距是:????
确定加热室内径和加热管数的具体做法是:先计算管束中心线上管数nc,管子安正三角形排列时,nc=1.1* ;其中n为总加热管数。
初步估计加热室Di=t(nc-1)+2b’,式中b’=(1—1.5)d0.然后由容器公称直径系列,试选一个内径作
为加热室内径并以该内径和循环管外景作同心圆,在同心圆的环隙中,按加热管的排列方式和管心距作图。
所画的管数n必须大于初值n’,若不满足,应另选一设备内径,重新作图,直至合适。
由于加热管的外径为38mm,可取管心距为48mm;以三角形排列计算,
b’=(1—1.5)d0=1.5*d0,
Di=t(nc-1)+2b’=48*(13-1)+2*38*1.5=690mm,选取加热室壳体内径为800mm鄙厚为12mm;
4分离室直径与高度的确定
分离室的直径与高度取决于分离室的体积,而分离室的体积又与二次蒸汽的体积流量及蒸发体积强度有关。
分离室体积V的计算式为:
式中V-----分离室的体积,m3;???????? W-----某效蒸发器的二次蒸汽量,kg/h;
??? P-----某效蒸发器二次蒸汽量,Kg/m3 ,U-----蒸发体积强度,m3/(m3*s);
即每立方米分离室体积每秒产生的二次蒸汽量。
一般用允许值为U=1.1~1.5 m3/(m3*s)
根据由蒸发器工艺计算中得到的各效二次蒸汽量,再从蒸发体积强度U的数值范围内选取一个值,即可由上式算出分离室的体积。
一般说来,各效的二次蒸汽量不相同,其密度也不相同,按上式计算得到的分离室体积也不会相同,通常末效体积最大。
为方便起见,各效分离室的尺寸可取一致。
分离室体积宜取其中较大者。
确定了分离室的体积,其高度与直径
符合关系,确定高度与直径应考虑一下原则:
(1)分离室的高度与直径之比H/D=1~2。
对于中央循环管式蒸发器,其分离室一般不能小于1.8m,以保证足够的雾沫分离高度。
分离室的直径也不能太少,否则二次蒸汽流速过大,导致雾沫夹带现象严重。
(2)在条件允许的情况下,分离室的直径尽量与加热室相同,这样可使结构简单制造方便。
(3)高度和直径都适于施工现场的安放。
现取分离室中U=1.2m3/(m3*s);
m3。
H=1.8m,,D=1.2m
2接管尺寸的确定
流体进出口的内径按下式计算
式中? -----流体的体积流量m3/s??? ;U--------流体的适宜流速?? m/s ,
估算出内径后,应从管规格表格中选用相近的标准管。
1溶液进出口??
于并流加料的三效蒸发,第一效溶液流量最大,若各效设备尺寸一致的话,根据第一效溶液流量确定接管。
取流体的流速为0.8 m/s;
所以取ф57X3.5mm规格管。
2加热蒸气进口与二次蒸汽出口???
?各效结构尺寸一致二次蒸汽体积流量应取各效中较大者。
所以取ф76X3.5mm规格管。
3冷凝水出口?
冷凝水的排出一般属于液体自然流动,接管直径应由各效加热蒸气消耗量较大者确定。
所以取ф65X3.5mm规格管。