汽车电源设计的六项基本原则
汽车电源设计的六项基本原则

汽车电源设计的六项基本原则大多数汽车电源架构需要遵循六项基本原则: 1.输入电压VIN范围:12V电池电压的瞬变范围决定了电源转换IC的输入电压范围。
典型的汽车电池电压范围为9V至16V,发动机关闭时,汽车电池的标称电压为12V;发动机工作时,电池电压在14.4V左右。
但是,不同条件下,瞬态电压也可能达到±100V。
ISO7637-1行业标准定义了汽车电池的电压波动范围。
图1和图2所示波形即为ISO7637标准给出的部分波形,图中显示了高压汽车电源转换器需要满足的临界条件。
除了ISO7637-1,还有一些针对燃气发动机定义的电池工作范围和环境。
大多数新的规范是由不同的OEM厂商提出的,不一定遵循行业标准。
但是,任何新标准都要求系统具有过压和欠压保护。
2.散热考虑:散热需要根据DC-DC转换器的最低效率进行设计。
空气流通较差甚至没有空气流通的应用场合,如果环境温度较高(>30°C),外壳存在热源(>1W),设备会迅速发热(>85°C)。
例如,大多数音频放大器需要安装在散热片上,并需要提供良好的空气流通条件以耗散热量。
另外,PCB材料和一定的覆铜区域有助于提高热传导效率,从而达到最佳的散热条件。
如果不使用散热片,封装上的裸焊盘的散热能力限制在2W至3W(85°C)。
随着环境温度升高,散热能力会明显降低。
将电池电压转换成低压(例如:3.3V)输出时,线性稳压器将损耗75%的输入功率,效率极低。
为了提供1W的输出功率,将会有3W的功率作为热量消耗掉。
受环境温度和管壳/结热阻的限制,将会明显降低1W最大输出功率。
对于大多数高压DC-DC转换器,输出电流在150mA至200mA范围。
汽车DCDC芯片EMC设计要点资料精

高频电流环路主要存在于电流切换的支路,开关管和连接在开关端两端的电容组成了高频电流回路。
The Future of Analog IC Technology®
开关节点dv/dt的阻抗通常是K 欧姆级,呈现近场电场特性
近场和远场干扰
近场源在距离大于λ/2π,变成远场源
高频开关环路di/dt的阻抗通常是 毫欧至欧姆级,呈现近场磁场特 性
高频电流环路形成的磁场大小取决于环路面积和电流大小
The Future of Analog IC Technology®
正确的找出高频电流环路
各种拓扑的高频电流环路
存在于开关回路和滤波电容之间,电感电流是连续的三角波波形,相对而言不是关注的重点
©Christian Kueck &Jens Hedrich
汽车测试标准
OEM标准:GM,Ford, BMW,VW,Daimler 全球性标准:ISO,CISPR 美国标准:SAE 中国标准:GB 欧洲标准:2004/104/EEC
对于汽车零部件来说,电磁兼容测试(EMC)是汽车电子所有测试中很重要的一部分内容
The Future of Analog IC Technology®
静电放电实验
ISO 7637-2
7637-2 7637-3 11452-7 11452-4
11452-2 11452-3 11452-5 11452-8
10605
CISPR
CISPR25 CISPR25 CISPR25 CISPR25
SAE J1113-42 J1113-41 J1113-41 J1113-41 J1113-41 J1113-11 J1113-12 J1113-3 J1113-4 J1113-2 J1113-21 J1113-24
汽车线束要点

汽车线束汽车线束是汽车电路的网络主体,没有线束也就不存在汽车电路。
在目前,不管是高级豪华汽车还是经济型普通汽车,线束编成的形式基本上是一样的,都是由电线、联插件和包裹胶带组成。
汽车电线又称低压电线,它与普通家用电线是不一样的。
普通家用电线是铜质单蕊电线,有一定硬度。
而汽车电线都是铜质多蕊软线,有些软线细如毛发,几条乃至几十条软铜线包裹在塑料绝缘管(聚氯乙烯)内,柔软而不容易折断。
汽车线束内的电线常用规格有标称截面积 0.5、0.75、1.0、1.5、2.0、2.5、4.0、6.0 等平方毫米的电线,它们各自都有允许负载电流值,配用于不同功率用电设备的导线。
以整车线束为例:1、0.5 规格线适用于仪表灯、指示灯、门灯、顶灯等;2、0.75 规格线适用于牌照灯,前后小灯、制动灯等;3、1.0 规格线适用于转向灯、雾灯等;4、1.5 规格线适用于前大灯、喇叭等;5、主电源线如发电机电枢线、搭铁线等要求 2.5 至 4 平方毫米电线。
这只是指一般汽车而言,关键要看负载的最大电流值,例如蓄电池的搭铁线、正极电源线则是专门的汽车电线单独使用,它们的线径都比较大,起码有十几平方毫米以上,这些“巨无霸”电线就不会编入主线束内。
在排列线束前要事先绘制线束图,线束图与电路原理图是不一样的。
电路原理图是表述各个电气部分之间关系的图像,它不反映电气件彼此之间怎样连接,不受各个电气元件的尺寸形状和它们之间距离的影响。
而线束图则必须要顾及各个电气元件的尺寸形状和它们之间的距离,也要反映出电气件彼此之间是如何连接的。
线束厂的技术员根据线束图做成线束排线板后,工人就按照排线板的规定来截线排线了。
整车主线束一般分成发动机(点火、电喷、发电、起动)、仪表、照明、空调、辅助电器等部分,有主线束及分支线束。
一条整车主线束有多条分支线束,就好象树杆与树支一样。
整车主线束往往以仪表板为核心部分,前后延伸。
由于长度关系或装配方便等原因,一些汽车的线束分成车头线束(包括仪表、发动机、前灯光总成、空调、蓄电池)、车尾线束(尾灯总成、牌照灯、行李箱灯)、篷顶线束(车门、顶灯、音响喇叭)等。
汽车电源分配的基本设计方法

汽车电源分配的基本设计方法贾承前;宋海健;顾越;付文刚;吴祥凤;曹丞【摘要】The correct design flow and method is introduced here, aiming at the power distribution of electrical devices in the electrical development of whole vehicle.%针对整车电气开发过程中存在的电器设备的电源合理分配问题。
详细讲述正确的设计流程和方法。
【期刊名称】《汽车电器》【年(卷),期】2012(000)003【总页数】4页(P12-15)【关键词】汽车;电器件;电源分配;熔断器;继电器【作者】贾承前;宋海健;顾越;付文刚;吴祥凤;曹丞【作者单位】上海世科嘉车辆技术研发有限公司,上海201209;上海世科嘉车辆技术研发有限公司,上海201209;上海世科嘉车辆技术研发有限公司,上海201209;上海世科嘉车辆技术研发有限公司,上海201209;上海世科嘉车辆技术研发有限公司,上海201209;上海世科嘉车辆技术研发有限公司,上海201209【正文语种】中文【中图分类】U463.63随着汽车工业的飞速发展,汽车的配置也越加丰富,其中车载电器设备的数量也越来越多,因此对整车的电气电路系统的性能、可靠性的要求也就更高。
如何安全又合理地对众多的电器设备的电源进行有效的管理和分配,对于整车电气系统开发来讲,成为非常重要的一项工作。
本文分三部分对汽车的电源分配的设计进行详细的分析和研究。
1 电源分配设计流程图1是基于整车开发大背景下定义的电源分配系统开发的流程。
以下分别就流程中的6个过程进行详细的解析。
图1 电源分配设计流程2 电源分配设计内容2.1 配置表分析第一步进行配置表的分析。
主要内容是提取所有和电气相关的配置,为其后的工作进行范围的界定。
配置表描述了开发车型的各项配置和功能,对整车项目的开发进行了全方位的定义和定位。
汽车应急启动电源设计的基本原则
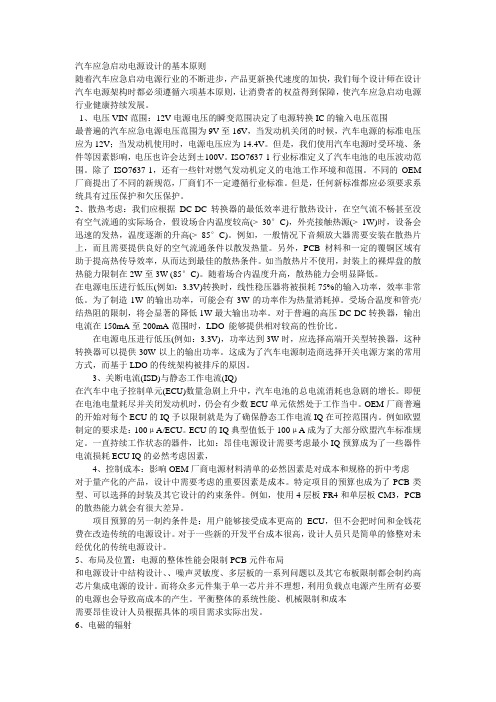
汽车应急启动电源设计的基本原则随着汽车应急启动电源行业的不断进步,产品更新换代速度的加快,我们每个设计师在设计汽车电源架构时都必须遵循六项基本原则,让消费者的权益得到保障,使汽车应急启动电源行业健康持续发展。
1、电压VIN范围:12V电源电压的瞬变范围决定了电源转换IC的输入电压范围最普遍的汽车应急电源电压范围为9V至16V,当发动机关闭的时候,汽车电源的标准电压应为12V;当发动机使用时,电源电压应为14.4V。
但是,我们使用汽车电源时受环境、条件等因素影响,电压也许会达到±100V。
ISO7637-1行业标准定义了汽车电池的电压波动范围。
除了ISO7637-1,还有一些针对燃气发动机定义的电池工作环境和范围。
不同的OEM 厂商提出了不同的新规范,厂商们不一定遵循行业标准。
但是,任何新标准都应必须要求系统具有过压保护和欠压保护。
2、散热考虑:我们应根据DC-DC转换器的最低效率进行散热设计,在空气流不畅甚至没有空气流通的实际场合,假设场合内温度较高(> 30°C),外壳接触热源(> 1W)时,设备会迅速的发热,温度逐渐的升高(> 85°C)。
例如,一般情况下音频放大器需要安装在散热片上,而且需要提供良好的空气流通条件以散发热量。
另外,PCB材料和一定的覆铜区域有助于提高热传导效率,从而达到最佳的散热条件。
如当散热片不使用,封装上的裸焊盘的散热能力限制在2W至3W (85°C)。
随着场合内温度升高,散热能力会明显降低。
在电源电压进行低压(例如:3.3V)转换时,线性稳压器将被损耗75%的输入功率,效率非常低。
为了制造1W的输出功率,可能会有3W的功率作为热量消耗掉。
受场合温度和管壳/结热阻的限制,将会显著的降低1W最大输出功率。
对于普遍的高压DC-DC转换器,输出电流在150mA至200mA范围时,LDO 能够提供相对较高的性价比。
在电源电压进行低压(例如:3.3V),功率达到3W时,应选择高端开关型转换器,这种转换器可以提供30W以上的输出功率。
第六章电动汽车充电站设计
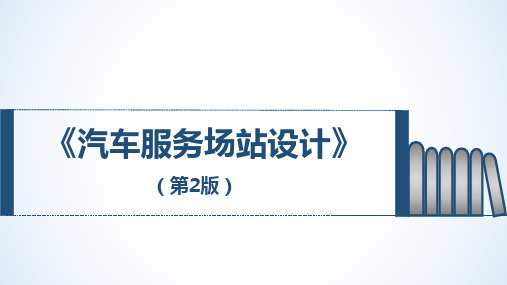
式中:
——电动汽车动力蓄电池的串联电池单体数量;
——充电机输出电压裕度系数,宜取1.0~1.1;
——单体电池最高电压(V)。
第三节 充电站充电系统设计
(4)充电机直流输出电压范围宜从电压优选范围中选择一组最高电压大于或等于的等级确定。 2.非车载充电机输出额定电流的选择 (1)根据电动汽车动力蓄电池的容量和充电速度以及供电能力和设备性价比,在确保安全、可靠充电的情况下确定最大充电电流。 (2)充电机输出的直流额定电流应优先采用以下值:10A、20A、50A、100A、160A、200A、315A和400A。 (3)充电机的输出直流额定电流可按式(6-2)计算:
第三节 充电站充电系统设计
(6-2)
式中:
——充电机输出电流裕度系数,宜取1.00~1.25;
——电动汽车动力蓄电池最大允许持续充电电流(A)。
(4)应从电流优选值中选择一个大于或等于的数值确定为充电机直流输出额定电流。
3.非车载充电机的功能要求 (1)具有根据电池管理系统提供的数据动态调整充电参数、自动完成充电过程的功能。 (2)具有判断充电机与电动汽车是否正确连接的功能,当检测到电接口连接异常时,应立即停止充电。
第二节 充电站选址及平面布置
一.充电站选址 1.影响电动汽车充电站选址的因素 (1)运行经济性。 (2)电网安全性。 (3)交通便利性。 (4)区域发展性。 ①人口数量。 ②居民消费习惯。
第二节 充电站选址及平面布置
2.充电站选址 充电站是中低压配电网的重要组成部分,站址选择应兼顾电网规划的要求,并与电网规划、建设与改造紧密结合,以满足电力系统对电力平衡、供电可靠性、电能质量、自动化等方面的要求,并结合变配电设施的建设、改造进行科学、合理的选址。 (1)充电站的选址应结合城市电动汽车发展规划统筹考虑,并与配电网现状和近远期规划紧密结合,以满足充电站对供电可靠性、电网对充电站电能质量和自动化的要求。充电站的站址应接近供电电源端,并便于供电电源线路的进出。 (2)公共充电站应选择在进出车便利的场所,充电站进出口宜与城市次干道路相连,便于车辆通行,不宜选择在城市干道的交叉路口和交通繁忙路段附近。
汽车电路原理
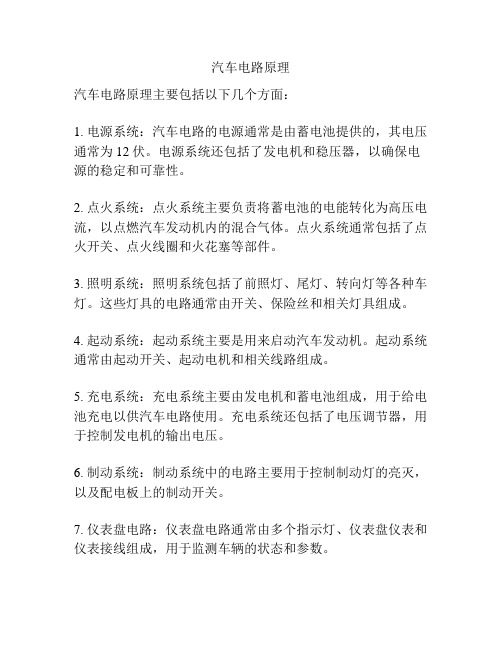
汽车电路原理
汽车电路原理主要包括以下几个方面:
1. 电源系统:汽车电路的电源通常是由蓄电池提供的,其电压通常为12伏。
电源系统还包括了发电机和稳压器,以确保电源的稳定和可靠性。
2. 点火系统:点火系统主要负责将蓄电池的电能转化为高压电流,以点燃汽车发动机内的混合气体。
点火系统通常包括了点火开关、点火线圈和火花塞等部件。
3. 照明系统:照明系统包括了前照灯、尾灯、转向灯等各种车灯。
这些灯具的电路通常由开关、保险丝和相关灯具组成。
4. 起动系统:起动系统主要是用来启动汽车发动机。
起动系统通常由起动开关、起动电机和相关线路组成。
5. 充电系统:充电系统主要由发电机和蓄电池组成,用于给电池充电以供汽车电路使用。
充电系统还包括了电压调节器,用于控制发电机的输出电压。
6. 制动系统:制动系统中的电路主要用于控制制动灯的亮灭,以及配电板上的制动开关。
7. 仪表盘电路:仪表盘电路通常由多个指示灯、仪表盘仪表和仪表接线组成,用于监测车辆的状态和参数。
8. 娱乐系统:娱乐系统包括了音响、收音机、DVD等设备和其相关线路。
在实际应用中,以上电路系统通常会相互连接和影响,以确保汽车的正常运行和安全。
正确理解和操作汽车电路原理对于车主和维修人员来说都是非常重要的。
汽车线束设计及搭铁分析
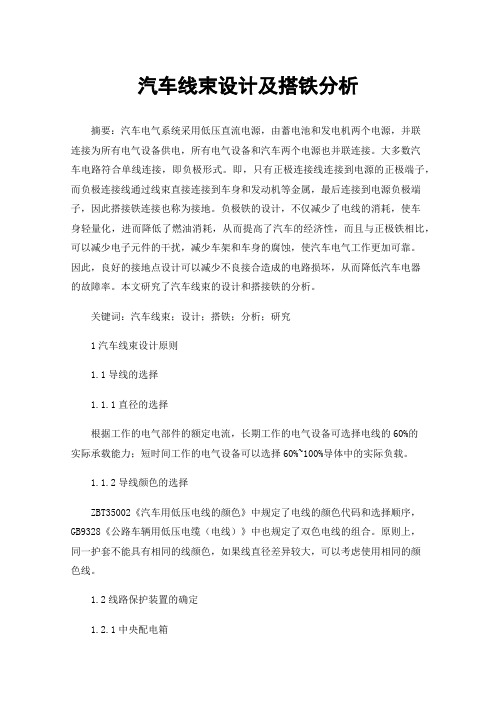
汽车线束设计及搭铁分析摘要:汽车电气系统采用低压直流电源,由蓄电池和发电机两个电源,并联连接为所有电气设备供电,所有电气设备和汽车两个电源也并联连接。
大多数汽车电路符合单线连接,即负极形式。
即,只有正极连接线连接到电源的正极端子,而负极连接线通过线束直接连接到车身和发动机等金属,最后连接到电源负极端子,因此搭接铁连接也称为接地。
负极铁的设计,不仅减少了电线的消耗,使车身轻量化,进而降低了燃油消耗,从而提高了汽车的经济性,而且与正极铁相比,可以减少电子元件的干扰,减少车架和车身的腐蚀,使汽车电气工作更加可靠。
因此,良好的接地点设计可以减少不良接合造成的电路损坏,从而降低汽车电器的故障率。
本文研究了汽车线束的设计和搭接铁的分析。
关键词:汽车线束;设计;搭铁;分析;研究1汽车线束设计原则1.1导线的选择1.1.1直径的选择根据工作的电气部件的额定电流,长期工作的电气设备可选择电线的60%的实际承载能力;短时间工作的电气设备可以选择60%~100%导体中的实际负载。
1.1.2导线颜色的选择ZBT35002《汽车用低压电线的颜色》中规定了电线的颜色代码和选择顺序,GB9328《公路车辆用低压电缆(电线)》中也规定了双色电线的组合。
原则上,同一护套不能具有相同的线颜色,如果线直径差异较大,可以考虑使用相同的颜色线。
1.2线路保护装置的确定1.2.1中央配电箱中央配电箱是车辆电气和电子电路的控制中心。
线路的保护装置,如保险丝和继电器,集中布置在中央配电箱上。
它是车辆电源的核心,也是线路保护的核心。
1.2.2继电器的选择继电器选型的技术要求如下:可靠性好、性能稳定、体积小、寿命长、装配好、成本低。
常用的继电器设备一般包括雨刮器、喇叭、除霜、前照灯、雾灯、风扇、鼓风机和转向灯(闪光灯)等。
常用的继电器为电压型,通常为12V。
1.2.3保险丝的选择1)发动机ECU、ABS等,对车辆的性能和安全性有很大影响,容易受到其他电气设备的干扰。
- 1、下载文档前请自行甄别文档内容的完整性,平台不提供额外的编辑、内容补充、找答案等附加服务。
- 2、"仅部分预览"的文档,不可在线预览部分如存在完整性等问题,可反馈申请退款(可完整预览的文档不适用该条件!)。
- 3、如文档侵犯您的权益,请联系客服反馈,我们会尽快为您处理(人工客服工作时间:9:00-18:30)。
汽车电源设计的六项基本原则大多数汽车电源架构需要遵循六项基本原则:1.输入电压VIN范围:12V电池电压的瞬变范围决定了电源转换IC的输入电压范围。
典型的汽车电池电压范围为9V至16V,发动机关闭时,汽车电池的标称电压为12V;发动机工作时,电池电压在14.4V左右。
但是,不同条件下,瞬态电压也可能达到±100V。
ISO7637-1行业标准定义了汽车电池的电压波动范围。
图1和图2所示波形即为ISO7637标准给出的部分波形,图中显示了高压汽车电源转换器需要满足的临界条件。
除了ISO7637-1,还有一些针对燃气发动机定义的电池工作范围和环境。
大多数新的规范是由不同的OEM厂商提出的,不一定遵循行业标准。
但是,任何新标准都要求系统具有过压和欠压保护。
2.散热考虑:散热需要根据DC-DC转换器的最低效率进行设计。
空气流通较差甚至没有空气流通的应用场合,如果环境温度较高(>30°C),外壳存在热源(>1W),设备会迅速发热(>85°C)。
例如,大多数音频放大器需要安装在散热片上,并需要提供良好的空气流通条件以耗散热量。
另外,PCB材料和一定的覆铜区域有助于提高热传导效率,从而达到最佳的散热条件。
如果不使用散热片,封装上的裸焊盘的散热能力限制在2W 至3W(85°C)。
随着环境温度升高,散热能力会明显降低。
将电池电压转换成低压(例如:3.3V)输出时,线性稳压器将损耗75%的输入功率,效率极低。
为了提供1W的输出功率,将会有3W的功率作为热量消耗掉。
受环境温度和管壳/结热阻的限制,将会明显降低1W最大输出功率。
对于大多数高压DC-DC转换器,输出电流在150mA 至200mA范围时,LDO能够提供较高的性价比。
将电池电压转换成低压(例如:3.3V),功率达到3W时,需要选择高端开关型转换器,这种转换器可以提供30W以上的输出功率。
这也正是汽车电源制造商通常选用开关电源方案,而排斥基于LDO的传统架构的原因。
大功率设计(>20W)对于热管理要求比较严格,需要采用同步整流架构。
为了获得高于单个封装的散热能力,避免封装“发热”,可以考虑使用外部MOSFET驱动器。
3.静态工作电流(IQ)及关断电流(ISD):随着汽车中电子控制单元(ECU)数量的快速增长,从汽车电池消耗的总电流也不断增长。
即使当发动机关闭并且电池电量耗尽时,有些ECU单元仍然保持工作。
为了保证静态工作电流IQ在可控范围内,大多数OEM厂商开始对每个ECU的IQ加以限制。
例如欧盟提出的要求是:100μA/ECU。
绝大多数欧盟汽车标准规定ECU的IQ典型值低于100μA。
始终保持工作状态的器件,例如:CAN收发器、实时时钟和微控制器的电流损耗是ECUIQ的主要考虑因素,电源设计需要考虑最小IQ预算。
4.成本控制:OEM厂商对于成本和规格的折中是影响电源材料清单的重要因素。
对于大批量生产的产品,成本是设计中需要考虑的重要因素。
PCB类型、散热能力、允许选择的封装及其它设计约束条件实际受限于特定项目的预算。
例如,使用4层板FR4和单层板CM3,PCB的散热能力就会有很大差异。
项目预算还会导致另一制约条件,用户能够接受更高成本的ECU,但不会花费时间和金钱用于改造传统的电源设计。
对于一些成本很高的新的开发平台,设计人员只是简单地对未经优化的传统电源设计进行一些简单修整。
5.位置/布局:在电源设计中PCB和元件布局会限制电源的整体性能。
结构设计、电路板布局、噪声灵敏度、多层板的互连问题以及其它布板限制都会制约高芯片集成电源的设计。
而利用负载点电源产生所有必要的电源也会导致高成本,将众多元件集于单一芯片并不理想。
电源设计人员需要根据具体的项目需求平衡整体的系统性能、机械限制和成本。
6.电磁辐射:随时间变化的电场会产生电磁辐射,辐射强度取决于场的频率和幅度,一个工作电路所产生的电磁干扰会直接影响另一电路。
例如,无线电频道的干扰可能导致安全气囊的误动作,为了避免这些负面影响,OEM厂商针对ECU单元制定了最大电磁辐射限制。
为保持电磁辐射(EMI)在受控范围内,DC-DC转换器的类型、拓扑结构、外围元件选择、电路板布局及屏蔽都非常重要。
经过多年的积累,电源IC设计者研究出了各种限制EMI的技术。
外部时钟同步、高于AM调制频段的工作频率、内置MOSFET、软开关技术、扩频技术等都是近年推出的EMI抑制方案。
应用与功率需求大多数系统电源的基本架构选择应从电源要求以及汽车厂商定义的电池电压瞬变波形入手。
对于电流的要求应该反映到电路板的散热设计。
与数字CMOS工艺类似,模拟BiCMOS也在不断地缩小设计的几何尺寸,以求获得最佳的投资回报,降低工艺开发的风险。
但是,工艺优化的方向并不符合汽车应用的需求。
例如:大多数集成工艺针对降低5.5V至6V输入电压范围的器件成本进行优化,但尚未对9V至10V 输入器件的制造工艺进行成本优化。
这也正是设计中需要产生中等电源,进而产生低压的原因。
以下列出了四种常用的电源架构,总结了最近三年汽车领域的典型设计架构。
当然,用户可以通过不同方式实现具体的设计要求,多数方案可归纳为这四种结构中的一种。
方案1该架构为优化DC-DC转换器的效率、布局、PCB散热及噪声指标提供了极大的灵活性。
方案1的主要优势是:增加核设计的灵活性。
设计提供不同的电压选项,以满足特定的设计要求。
即使不是最低成本/最高效率的解决方案,增加一个独立的转换器有助于重复利用原有设计。
有助于合理利用开关电源/线性稳压器。
例如,如果系统中提供为处理器供电的3.3V电源,相对于直接从汽车电池降压到1.8V,从3.3V电压产生1.8V300mA的电源效率更高、成本也更低。
如果新设计中需要更改电源电压,旧的电源模块不再满足要求时,设计人员可以很容易地选择一个替代模块,不会造成任何浪费。
合理分配PCB散热,这为选择转换器的位置及散热提供了灵活性。
允许使用高性能、高性价比的低电压模拟IC,与高压IC相比,这种方案提供了更宽的选择范围。
另外需要注意的是:方案1占用较大的电路板面积、成本相对较高,对于有多路电源需求的设计来说过于复杂。
方案2该方案是高集成度与设计灵活性的折衷,与方案1相比,在成本、外形尺寸和复杂度方面具有一定的优势。
该方案特别适合两路降压输出并需要独立控制的应用。
例如, 3.3V不间断供电电源,而在需要时可以关闭5V电源,以节省IQ电流。
另一种应用是产生中等电源,例如5V,为低压转换器供电,利用这种方案可以省去一个产生8V的boost转换器。
采用外置FET的双输出控制器可以提供与方案1相同的PCB布板灵活性,便于散热。
内置FET的转换器,设计人员应注意不要在PCB的同一位置耗散过多的热量。
方案3这一架构把多路高压转换问题转化成一路高压转换和一个高度集成的低压转换IC,相对于多输出高压转换IC,高集成度低压转换IC成本较低,且容易从市场上得到。
这种方案有助于简化电源设计,可以方便地从不同供应商获得替代器件。
另外,高度集成的低压IC要比多路高压IC的成本低。
如果方案3中的低压PMIC有两路以上输出,那么方案3将存在与方案4相同的缺陷。
方案3的主要劣势是多路电压集中在同一芯片,布板时需要慎重考虑PCB散热问题。
方案4最新推出的高集成度PMIC可以在单芯片上集成所有必要的电源转换和管理功能,突破了电源设计中的诸多限制。
但是,高集成度也存在一定的负面影响。
在高集成度PMIC中,集成度与驱动能力总是相互矛盾。
例如,在产品升级时,原设计中内置MOSFET的稳压器可能无法满足新设计中的负载驱动要求。
把低压转换器级联到高压转换器有助于降低成本,但这种方式受限于稳压器的开/关控制。
例如,如果5V电源关闭时必须开启3.3V电源,就无法将3.3V输入连接到5V电源输出;否则将不能关闭5V电源,造成较高的静态电流IQ。
EMI和负载点转换器可能会制约核心PMIC的使用,电路板布局以及较长的引线可能无法使用PMIC能够提供的电源电压。
Maxim的汽车电源解决方案Maxim的汽车电源IC克服了许多电源管理问题,能够提供独特的高性能解决方案。
电源产品包括过压保护和欠压保护、微处理器监控、开关转换器和线性稳压器等高度集成的多功能PMIC,完全满足汽车信息娱乐系统的供电需求。
Maxim通过了TS16949(汽车质量标准)认证,针对汽车产品配备了专门的支持队伍,提供质量认证、客户服务、本地销售及应用支持,拥有满足汽车市场需求的IC设计资源。
Maxim的电源IC符合汽车级质量认证和生产要求,例如:AECQ100认证、DFMEA、不同的温度等级(包括85°C、105°C、125°C等)、特殊的封装(有引出线的引脚或QFN,带有裸焊盘或不带裸焊盘)要求。
MAX15004/MAX15005为通用的电流模式PWM控制器,能够配制成boost、反激、正激和SEPIC转换器,IC工作在4.5V至40V输入电压范围,允许在15kHz至500kHz范围内调节开关频率。
该款IC还允许同步到一个外部时钟。
电流模式控制架构具有出色的电源瞬态响应特性和逐周期限流,有效简化频率补偿。
可编程斜率补偿进一步简化了设计,60ns快速限流响应时间和低至300mV的限流门限使得该控制器非常适合构成高效、高频DC-DC转换器。
器件包括内部误差放大器和1%精度的基准,便于构成隔离或非隔离型原边稳压器。
保护功能包括逐周期、“打嗝式”限流,输出过压保护和热关断。
MAX15004/MAX15005采用16引脚TSSOP封装,带有裸焊盘或不带裸焊盘。
所有器件工作在-40°C至+125°C汽车级温度范围。
MAX1744为单路输出、汽车级开关稳压器,能够承受4.5V至36V瞬变电压。
器件采用专有的限流控制架构,提供出色的轻载和满负荷效率,无需散热器即可提供50W的输出功率。
MAX1745在关断时仅消耗4μA电流,轻载时消耗90μA电流。
IC 规定工作在+125°C,提供3mm×3mm、16引脚μMAX?封装,带有裸焊盘或不带裸焊盘。
MAX1745可通过外部电阻调节输出电压。
MAX15006/MAX15007为超低静态电流的线性稳压器,能够工作在4V至40V电压范围。
IC 可提供高达50mA的输出电流,空载时仅消耗10μA的IQ。
内置p沟道调整管即使在满负荷时也能保持极低的IQ。
关断时,MAX15007仅消耗3μA电流。
MAX15006A/MAX15007A提供固定3.3V输出,MAX15006B/MAX15007B提供固定5V输出。
MAX15007包括一个使能输入,用于器件的通、断控制。