现场改善培训课程
IE现场改善实务培训课程

IE现场改善实务培训课程介绍IE(Indicator of excellence)程序是一种在生产环境中提高效率和质量的方法论。
IE现场改善实务培训课程是为希望掌握IE技巧的生产人员设计的一门培训课程。
本课程旨在帮助学员理解IE的核心概念,并通过实践案例和团队讨论,培养学员在实际生产环境中运用IE方法的能力。
课程内容第一模块:IE概述和原理(150字)•IE的定义和作用•IE的原理和基本原则•IE在生产中的重要性和应用第二模块:IE工具和技术(300字)•5S方法(整理、整顿、清扫、清洁和素养)•VSM(价值流图)分析•标准化工作流程和作业练习•设备故障分析和预防第三模块:改善项目管理(200字)•改善项目的特点和目标•PDCA(Plan-Do-Check-Act)循环•改善项目的团队管理和评估•持续改进的文化和方法第四模块:实战案例和团队讨论(350字)•学员将以小组形式对实际生产中的问题进行讨论和分析•案例将涵盖不同行业和情境,包括制造、物流和服务业•学员将运用IE的方法和工具,提出改善方案并进行实施第五模块:IE实施和评估(200字)•在生产现场中实施IE方法的挑战和解决方案•IE指标的设计和评估•改善效果的测量和监控•员工培训和绩效管理学习目标本课程的学习目标包括:1.理解IE的核心概念和原则;2.掌握IE工具和技术,如5S方法、VSM分析和标准化工作流程;3.学习改善项目管理的基本原则和技巧;4.运用IE方法解决实际生产中的问题,并提出改善方案;5.熟悉IE的实施和评估过程,包括员工培训和改善效果评估。
学员要求参加IE现场改善实务培训课程的学员应具备以下条件:1.对生产管理和流程改善感兴趣;2.有一定的生产工作经验;3.具备团队合作和问题解决的能力。
课程安排本课程为期2天,共计16学时。
具体课程安排如下:•第一天–上午:IE概述和原理–下午:IE工具和技术•第二天–上午:改善项目管理–下午:实战案例和团队讨论–晚上:IE实施和评估培训师资本课程的培训师均为经验丰富的IE专家,他们将通过实践案例和互动讨论,帮助学员理解IE的实际应用和挑战。
现场改善培训课程
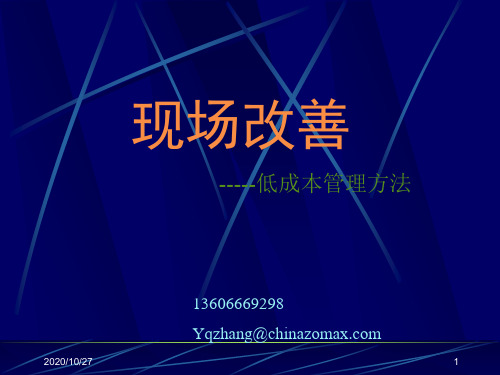
●产距时间( Takt Ti m e):生产一个产品 的目标时间
●周期时间(Cycle Ti m e )
2020/10/27
22
●一个流( O n e - P i e c e F l o w ●后拉式生产(Pull Production) ●自动化( A u t o n o m a t i o n ) ●U型细胞式生产线 ●缩短换模时间。
10
新的工作流程
任何一个新的工作流程,在初期都是呈 不稳定的状态。
开始进行P D C A改善时,必须先将任 何现有的流程稳定下来。此一稳定的过程 称之为:标准化( S t a n d a r d i z e )→执行 (Do)→查核(Check)→处置(Action)SDCA的 循环。
2020/10/27
方针展开、质量保证体系的建立、标准化、 教育训练、成本管理和质量圈。
2020/10/27
19
TQC/TQM的含义
Q表示质量,具有其优先性,但仍含有其他的 目标—即成本与交期。
T在T Q C / T Q M中,意味着“全面的”,包 含组织内每一个人,从最高阶层经中间管理阶层、 现场督导人员,以及现场的作业人员,更进一步延 伸至供应商、经销商及批发商。T也意含着最高管 理部门的领导及绩效,是TQC/TQM推行成功的要 素。
源投资于新技术或设备,而产生戏剧
性的变化的改进。
2020/10/27
金钱
6
目标
改善
努力 士气 沟通 训练 团队 参与 自律
2020/10/27
7
结果 关键
最高管理部门的承诺和参与
管理部门的承诺和参与,必须 适时地、持续地表现出来,以确保 在“改善”的过程中获得成功。
精选生产现场改善力提升培训

FTF生产管理培训咨询
பைடு நூலகம்
No:16
要点十:标示管理与目视管理
标识 部门 人员 状态 区位 限位 提示 指向 警示 流向 音响 透明化 容量 油位 水位指示透明化
FTF生产管理培训咨询
No:14
要点八:工具物料拿取方便
愚巧化:改善工具,使“愚人”能象 “巧匠”一样工作。
手工配钥匙需要很高的技巧,用一台仿 形机任何人都能把它做得又快又好。
用手数小螺钉又慢又差,做一个定数器 就能数得又快又好。
FTF生产管理培训咨询
No:15
要点九:看板管理
让所有人一看就知道怎样做
No:8
要点二:划线定位,规定区域
◆通道线 ◆斑马线 ◆止步线
◆停放线 ◆隔离栏
FTF生产管理培训咨询
No:9
要点三:调整位置,单向流动
按工序顺序流动 关键工序先行 避免往复迂回运输 先进先出
FTF生产管理培训咨询
No:10
要点四:定置管理
定置 箱、柜、框、桌、椅位置不动 定位 周转箱车、工件、材料位置固定 定量 不多不少、按规定数量盛放 定点 货架上、箱柜内物品定点放置
FTF生产管理培训咨询
No:30
项目 整顿
判定重点 41.不良品放置场地应设置在明显的地方 42.修理品应放置在生产线外 43.零件放置场所的标识表示应完备 44.塑胶箱、捆包材料上应标明品名 45.作业工具的放置位置不能走路或弯腰才能放置 46.应下工夫大概在放置位置放手就能放置作业工具 47.作业工具放置处应有余量 48.治具、工具架上应有编码管理及有品目表示 49.在架子前应能清楚辨明上面的编码 50.治具、工具架應導入用不同顏色標識區分 51.治具是否按使用频率放置,使用频率越高的放置越近 52.治具、工具应按成品类别成套放置 53.成品的放置应该按機種型号区分开 54.成品的放置场地的通路和放置场所应画线表示区分 55.成品上应有编码(番号)、数量的表示 56.包装材料和成品的堆放高度应做出规定 57.治具架应采取容易取出的放置方法 58.不能使用未被认定的不良测量工具(精密度检查颜色用标贴表示) 59.测定具应采取防尘、防锈的放置方法 60.私用杯子应按规定放置于杯架上 61.测定具在托盘下面应使用橡胶之类的缓冲材料
现场改善手法干部培训课程
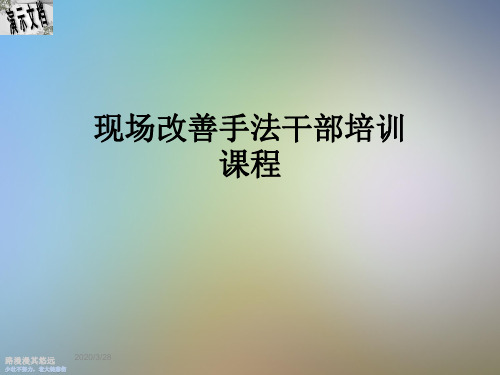
•课 程 简 介
•一、动作分解与标准化作业 •二、生产线平衡分析与瓶颈改 善 •三、 JIT之现场物流改善
•四、 JIT之切换效率改善
路漫漫其悠远
•一、动作分解与标准化作业
1.1 作业标准
•O S peration tandard•作业标 准
•定义:作业标准是为保证产品质量和生产效率,在标准 工时内完成作业的标准作业方法。其内容包括:
•动作浪费
为“地下工厂”。
•加工浪费
•库存浪费
•制造过多(过早)浪费
•缺货损失
路漫漫其悠远
•等 •待 •浪•费
•一、动作分解与标准化作业
•等待不创造价值
•常见的等待现象:
•☆ 物料供应或前工序能力不足造成待料
• ☆ 监视设备作业造成员工作业停顿
• ☆ 设备故障造成生产停滞
•
☆ 质量问题造成停工
•
☆ 型号切换造成生产停顿
现场改善手法干部培训 课程
路漫漫其悠远 2020/3/28
•前 言
•导致生产效率低下的主要原因:
•1、新员工多,员工操作慢,员工(班、组长)对现产品生产工 艺(设备)不熟悉 ;(人) •2、机器不稳定,工具不好用;(机) •3、物料跟不上,且来料不良率高;物料须再加工后才能使用; (物) •4、提供的作业方法不实用,员工操作不习惯;(方法) •5、车间太热、太挤了,风扇都不够爽;拿物料太远了,且物料 要搬来搬去的,累死人啦!(环境) •6、转拉多;(其它) •……….
1.6 标准作业•一、动作分与标准化作业•S O tandard peration •标准作
业
•
标准作业是对周期性的人—机作业中将有关人的作业动作程序
现场改善培训课件

SDCA 循環 標準化-執行-查核-處置
UMAX
主要的改善活動
一﹒全面品質管理 ( TQM ) 二﹒及時生產方式 ( JIT ) 三﹒全員生產保全 ( TPM ) 四﹒方針展開 五﹒提案建議制度 六﹒小集團活動 ( QCC )
UMAX - QC
現場改善 第二章
現場改善
主講人
侯建平
UMAX - QC
活動必需要長久、持續地做下去,這不是一年、二年
之事,而是一輩子的事。
UMAX - QC
日本式改善活動 ~ 「五心」
一﹒信心:相信這些改善活動會帶給你好處。 二﹒決心:下定決心趕快去做,不要猶豫不決。 三﹒耐心:要永遠持續做下去,成果自然呈現。 四﹒關心:對員工表示出你的關懷及重視之意。 五﹒愛心:多用鼓勵的方式來鼓舞員工士氣。
UMAX - QC
現場管理的金科玉律
1.當問題(異常)發生時,要先去現場 2.檢查現物(有關的物件) 3.當場採取暫行處置措施 4.發掘真因並將之排除 5.標準化以防止再發生
UMAX - QC
現場改善 第三章
如何管理現場的品質﹑成本和交 期
主講人
彭文彬
UMAX - QC
品質~不僅是指[結果面的品質]而已
標
準
※ 企業的日常事務,應依據某種已達成共識的程序來運作,
把這些程序清楚地寫下來,就成為標準。
維持和改進標準。
作業標準。
標準的主要特徵。
豐田工機公司。
改善事例(Kaizen Story)。
改善/ISO 9000/QS 9000。
UMAX - QC
維持和改進標準
用改進的術語來說,管理人員應當推行標準化─執行─
六﹒全員現場改善﹝Gemba Kaizen﹞
现场改善培训课程
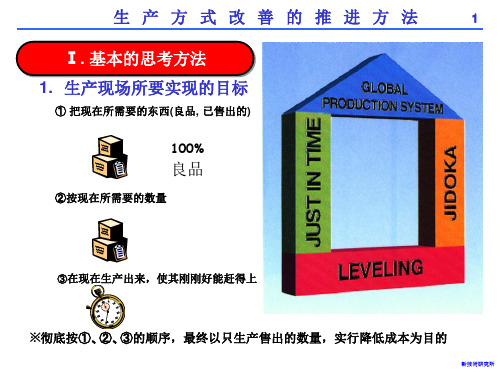
① (a)
1分 1分
24
②
③
④
⑤
⑥
切削加工
完成时间2分钟 完成时间 分钟 ① (b)
1分
① 下工件 ② 检查 ③ 去毛刺 ④ 装箱 ⑤ 安工件 ⑥ 启动
⑤
⑥
②
③
④ 完成时间1分 秒 完成时间 分30秒 缩短30秒 (缩短 秒)
16
B: 需要多技能员工 (3) 标准在制品
装在机器上的, 传送带上的, 需要冷却的等东西,指为了使作业能按同一步骤 装在机器上的 传送带上的 需要冷却的等东西 指为了使作业能按同一步骤 且反复进行而需要的最少限度的在制品
标准作业在制品的原则
从作业顺序来看 相对于加工顺序) (相对于加工顺序) 从机器是否能 自动送料来看
③ 降低质量的不良
(A) 实行不良对策 不良, 异常发生时, · 不良 异常发生时 立即停线 中加入品质检查, · 在标准作业中加入品质检查 确保品质 · 改善品质检查作业
新技術研究所
生 产 方 式 改 善 的 推 进 方 法
· 拆分检查作业 · 缩短检查作业 反复问“为什么” · 反复问“为什么” 考虑对策、 · 考虑对策、实施 经常跟进( 追究根本原因) · 经常跟进(用5W追究根本原因) 追究根本原因 (B)建立容易掌握原因的体系 “单件流” )建立容易掌握原因的体系 单件流” · 在相同条件下进行反复作业 单件流, ·不改变生产作业 ― 流线化作业 ― 单件流 顺序生产 生产的Lead-Time · 加工后马上检查 ― 生产的 最理想的是做的人来检查 考虑Pokayoke, 用检具来控制 · 考虑
2-2 标准作业的 要素 标准作业的3要素
(1) Takt-Time 一天的工作时间(固定时间 小时 一天的工作时间 固定时间: 8小时) 固定时间 小时) 一天的销售数量(平均每日需要生产数) 平均每日需要生产数 一天的销售数量 平均每日需要生产数)
【培训课件】现场改善培训教材
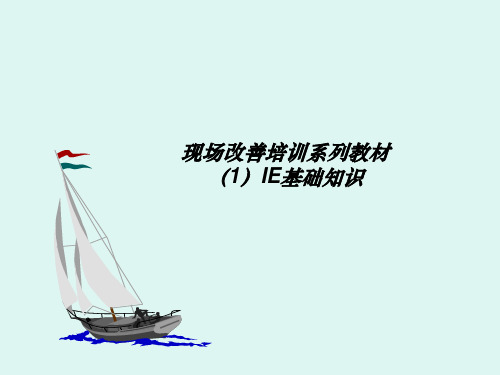
现场改善培训系列教材
Industrial Engineering
4. 标准产能计算的依据
依照各产品的标准工时,将每天的工作时間来计算各 产品的标准产能。
考题: 现装配、充填、固化、基片检验、加硬的标准工时分别为:10秒、 15秒、 8秒、 20秒、 1.5秒。共人装配工10人、充填工12人、固化炉
35
30
29
26 25 20
25 22
白色部份为平衡损失时间
生产节拍=33
29
26 24
27
瓶颈时间=29
23
15 1 2 3 456 7 8 9
时间 26 29 25 22 24 26 29 27 23
现场改善培训系列教材
Industrial Engineering
8. 人员需求计划 将标准工时所计算出的产能来安排作业人员,再将全
Industrial Engineering
一、时间分析与研究
小测试:
1、现在你正驾驶一部小车从丹阳驶向南京,假设从丹阳 到南京的距离为100公里,请问需要多长时间?
1、现在你正驾驶一部小车从丹阳驶向南京,假设从丹阳
到南京的距离为100公里, 车速为80公里/小时,请问需要多
长时间?
标准!
现场改善培训系列教材
否能满足计划需求?
? 28800÷14.4=2000PCS
一台修边机加工2PCS镜片的标准时间为28.8秒.现计划下单
2000PCS,请问这台机器是否能满足计划需求? 28800÷(28.8÷2)=2000PCS
现场改善培训系列教材
现场改善的培训

踢/换 培訓/推
不知
引导/沟通
利用不同的方法/手段,达到目的
思想篇
改善
改善的经历
3)合作
1)怀疑
2)了解
負面對抗
正面對抗
改善 改善
----是须要有勇气否定現狀
思想篇
改善须要我们----1)勇气
2)吸收 3)抛弃 4)创新
思想篇
放大问题
思想篇
不可能,不可能……
改 变
第一步,第二步……
持续改善
思想篇
技能篇
5Why
1) 1Why~4Why是原因 2) 第5个Why才是真因
解决问题的根本方法
技能篇 7种方法
开发创意。大但提出你的任何方案
老板 满意
演讲完毕,谢谢观看!
思想篇 目标
5 4 3 2 1
現狀
1)主动 完成的
過程
转变----1)主动
2)被动
2)被逼 达成的
時間
思想篇
• 什么是转变?------- 转变就是改变现状
• 最坏的转变,不是不变,而是变得更坏
– 不进则退 – 进退两难 – 往后的一成不变
• 所以我们须要的是
正面改善
负面改善
思想篇
不愿意 不能
现场改善系列培训 ---基层管理
课程内容
1) 前言 2) 现场改善理念 3) 认识浪费 4) 改善的基本原则 5) 改善的基本方法
思想篇
?
改喜 改善
放大
5Why
动手
成就感
1)---动手 2)---变化
思想篇
变化
1)等变化 2)创造变化
思想篇
思维
是什么?
态度
- 1、下载文档前请自行甄别文档内容的完整性,平台不提供额外的编辑、内容补充、找答案等附加服务。
- 2、"仅部分预览"的文档,不可在线预览部分如存在完整性等问题,可反馈申请退款(可完整预览的文档不适用该条件!)。
- 3、如文档侵犯您的权益,请联系客服反馈,我们会尽快为您处理(人工客服工作时间:9:00-18:30)。
加工
流程A
流程B
流程C
下一流程就是顾客
内部 外部
绝不将不合格品或不正确 信息,往下一流程传送。
学习改变观念,观念改变行动,行动改变命运
第2章 推行改善活动
建立改善观念后,更重要的在于落实,推行改善 活动。日本工业界的管理实务,值得我们实践。
• 全面质量控制/ 全面质量管理。 • 及时生产方式(丰田生产体系)。 • 全员生产保全。 • 方针展开。 • 提案建议制度和小量控制/全面质量管理
TQC:着重在流程上的质量控制。 TQM:不仅仅是流程上,而且包 含
所有的管理层面。
T Q C / T Q M活动的内容: 方针展开、质量保证体系的建立、标准化、 教育训练、成本管理和质量圈。
TQC/TQM的含义
Q表示质量,具有其优先性,但仍含有其他的 目标—即成本与交期。
团队导向
提案建议制度:鼓励员工多提出建议,无论 他们的建议有多小。培养、开发具有改善意识 及自律化的员工。
小集团活动:是指在工作现场的环境里,在 公司内以非正式、自愿性质组成团体,去执行 特定的工作任务。
第3章 走进改善舞台--现场
创新 改善 维持
改善 ( K a i z e n ):是由于持续不断的努 力,所产生的诸多的小步伐改进,而 逐次累积而成。
创新 ( I n n o v a t i o n ):则是借助大笔资 源投资于新技术或设备,而产生戏剧 性的变化的改进。
改善
目
标
努力 士气 沟通 训练 团队 参与 自律
关
最高管理部门的承诺和参与
所以S D C A的目的,就是在标准化和稳定 现有的流程,而P D C A的目的则是在提高流 程的水准。
质量是企业的生命。 但管理人员经常会因屈服交期和 降低成本的压力,而对质量妥协让步, 因此,便冒着牺牲质量和危及企业生 命的风险。
为了能正确地了解及解决问题,首先必 须收集及分析相关的资料,以确定问题的真 象。没有确实的资料,就去尝试解决一个问 题,与凭借感觉及预感是没什么两样的,这 并不是科学或客观的方法。搜集现状资料, 有助于了解目前专注的地方,以此作为改善 的出发点。
●改善在每一个人都能为达成目标而工作时, 才能产生最大的效果;而管理部门的职责,就是 要设定这个改善的目标。
目 标:
为维持竞争力,我们 必须降低1 0%的成本。
展 开:
●提高生产力 ●降低库存 ●不合格品 ●改进生产线
最高管理层 中层管理部门
5 提案建议制度和小集团活动
提案建议制度
个人导向
小集团活动
SDCA循环
PDCA循环
改进
AP CD
AP CD
维持
AS CD
SDCA循环
流程发生异常
在当前的流程里,每当发生异常时,便必 须反问自己下列的问题:是否因为没有标准 而发生的?是否因为没有遵守标准而发生的? 或者因为标准不适当而发生的?惟有建立了 标准,并且确实遵守,以将当前的流程稳定 下来,才能再进行下一个PDCA的循环。
现场改善培训课程
路漫漫其悠远
少壮不努力,老大徒悲伤
第1章 建立改善观念
“改善”定义
●一种企业经营理念,用以持续不断地改 进工作方法和人员的效率等。
●意指持续不断地改进。
●“改善”的步伐是一小步一小步、阶梯 式的,但随着时间的演进,它会带来戏剧 性的重大成果。
改善的观念 • 改善与管理。 • 过程与结果。 • 遵循PDCA循环/SDCA循环。 • 把质量放在第一位。 • 用数据说话。 • 下一流程就是顾客。
3 全员生产保全(TPM)
T P M则着重于设备质量的改 进。
T P M是通过总体的预防保 养制度,来延长设备的寿命,以 追求设备效率的最大化。
4 方针展开
●管理部门应设定明确的改善目标,以领导 和指引每一位员工开展所有的改善活动。
●真正具有改善成效的活动,是需要予以密 切地督导推行的。
●没有目标的改善活动,就如同没有终点站 的旅途。
T在T Q C / T Q M中,意味着“全面的”,包 含组织内每一个人,从最高阶层经中间管理阶层、 现场督导人员,以及现场的作业人员,更进一步延 伸至供应商、经销商及批发商。T也意含着最高管 理部门的领导及绩效,是TQC/TQM推行成功的要 素。
C指控制或流程控制。在TQC/TQM中,为了改 进成果,必须对关键的流程加以认定、控制及持续 不断地改进。
或者是再设定新的改进目标。
我再拿出脑图、 清单和流程出来, 我就能当总统啦!
新的工作流程
任何一个新的工作流程,在初期都是呈 不稳定的状态。
开始进行P D C A改善时,必须先将任 何现有的流程稳定下来。此一稳定的过程 称之为:标准化( S t a n d a r d i z e )→执行 (Do)→查核(Check)→处置(Action)SDCA的 循环。
2 及时生产方式(JIT)
JIT的目的:
是要消除各种没有附加价值的动作,同时 达成一个去芜存菁的生产体系,以便更具弹 性地去适应顾客订单的需求变化。
J I T 生产方式奠基于如下的观念:
●产距时间( Takt Ti m e):生产一个产品 的目标时间
●周期时间(Cycle Ti m e )
●一个流( O n e - P i e c e F l o w ●后拉式生产(Pull Production) ●自动化( A u t o n o m a t i o n ) ●U型细胞式生产线 ●缩短换模时间。
管理具有两项主要的功能 维持 ( M a i n t e n a n c e ):是指从事于保持现
有技术、管理及作业上标准的活动,以及 支持这些标准所需的训练和纪律。 改进 ( I m p r o v e m e n t ):则是以改进现有标 准为目标的活动。
维持标准和改进标准 改进
高层管理 中层管理 督导人员 作业人员
管理部门的承诺和参与,必须
键
适时地、持续地表现出来,以确保
在“改善”的过程中获得成功。
结
过
程
果
改善的过程步骤
PDCA循环
计划( P ): 建立改善的目标。
执行( D ):依计划目标推行。
核查( C ):确认是否按计划进度在实行,
以及是否达成预定的计划。
处置( A ):新作业程序的实施及标准化,
以防止原来的问题再次发生,