注塑成型中产品变形与不平衡流动
注塑成型制品不良现象及解决办法

注塑成型制品不良现象及解决办法一、塑料制品充填不满1、成因:主要是缺料和注射压力与速度不妥(包括阻力造成压力过于耗损)。
2、解决措施:(1)机台方面:机台的塑化量或加热功率不定,应选用塑化量与加热功率大的机台;螺杆与料筒或过胶头等的磨损造成回料而出现实际充模量不中;热电偶或发热圈等加热系统故障造成料筒的实际温度过低;注射油缸的密封元件磨损造成漏油或回流,而不能达到所需的注射压力;射嘴内孔过小或射嘴中心度调节不当造成阻力过大而使压力消耗。
(2)模具方面:①模具局部或整体的温度过低造成入料困难,应适当提高模温;②模具的型腔的分布不平衡。
制件壁厚过薄造成压力消耗过磊而且充模不力。
应增加整个制件或局部的壁厚或可在填充不足处的附近,设置辅助流或浇口解决。
③模具的流道过小造成压力损耗;过大时会出现射胶无力;过于粗糙都会造成制件不满。
应适当设置流道的大小,主流道与分流道,浇口之间的过渡或本身的转弯处应用适当的圆弧过渡。
④模具的排气不良。
进入型腔的料受到来不及排走的气体压力的阻挡而造成充填不满。
可以充分利用螺杆的缝隙排气或降低锁模力利用分型面排气,必要时要开设排气沟道或气孔。
(3)制件不满反复出现的原因:①塑料原料粒度大小悬殊不均时会使加料份量不定。
②螺杆的过胶头、过胶圈及过胶垫圈的磨损过大,使熔料可能在螺杆处经与料筒内之间滑行及回流造成不满。
③入流口的冷却系统失效,使下料量不稳定。
④料筒调定的注料量不足,即缓冲垫过小会使射料时多时少而出现制件不满。
二、飞边1、成因:又称溢边、披锋、毛刺等,大多发生在模具的分合位置上,如动模和静模的分型面,滑块的滑配部位、镶件的绝隙、顶杆孔隙等处,飞边在很大程度上是由于模具或机台锁模力失效造成。
2、解决措施:(1)机台的最高锁模力不够应选用锁模力够的机台。
锁模机铰磨损或锁模油缸密封元件磨损出现滴油或回流而造成锁模力下降。
加温系统失控造成实际温度过高应检查热电偶、加热圈等是否有问题。
注塑生产中常见的问题

注塑生产中常见的问题1. 刚开机时产品跑披锋,生产一段时间后产品缺胶的原因及解决方案。
刚开机时注塑机料管内的熔胶由于加热时间长,熔胶粘度低,流动性好,产品易跑披锋,生产一段时间后由于熔胶不断把热量带走,造成熔胶不足,粘度大,流动性差,使产品缺胶。
在生产一段时间后,逐渐提高料管温度来解决。
2. 在生产过程中,产品缺胶,有时增大射胶压力和速度都无效,为什么?解决方法?是因为生产中熔胶不断把热量带走,造成熔胶不足,胶粘度大,流动性差,使产品缺胶。
提高料管温度来解决。
3. 产品椭圆的原因及解决方法。
产品椭圆是由于入胶不均匀,造成产品四周压力不匀,使产品椭圆,采用三点入胶,使产品入胶均匀。
4. 精密产品对模具的要求。
要求模具材料刚性好,弹变形小,热涨性系数小。
5. 产品耐酸试验的目的产品耐酸试验是为了检测产品内应力,和内应力着力点位置,以便消除产品内应力。
6. 产品中金属镶件受力易开裂的原因及解决方法。
产品中放镶件,在啤塑时由于热熔胶遇到冷镶件,会形成内应力,使产品强度下降,易开裂。
在生产时,对镶件进行预热处理。
7. 模具排气点的合理性与选择方法。
模具排气点不合理,非但起不到排气效果,反而会造成产品变形或尺寸变化,所以模具排气点要合理。
选择模具排气点,应在产品最后走满胶的地方和产品困气烧的地方开排气。
8. 产品易脆裂的原因及解决方法。
产品易脆裂是产品使用水口料和次料太多造成产品易脆裂,或是料在料管内停留时间过长,造成胶料老化,使产品易脆裂。
增加新料的比例,减少水口料回收使用次数,一般不能超过三次,避免胶料在料管内长时间停留。
9. 加玻纤产品易出现泛纤的原因及解决方法是由于熔胶温度低或模具温度低,射胶压力不足,造成玻纤在胶内不能与塑胶很好的结合,使纤泛出。
加高熔胶温度,模具温度,增大射胶压力。
10. 进料口温度对产品的影响。
进料口温度的过高或过低,都会造成机器回料不稳定,使加料量不稳定,而影响产品的尺寸和外观。
注塑缺陷原因分析与解决方案
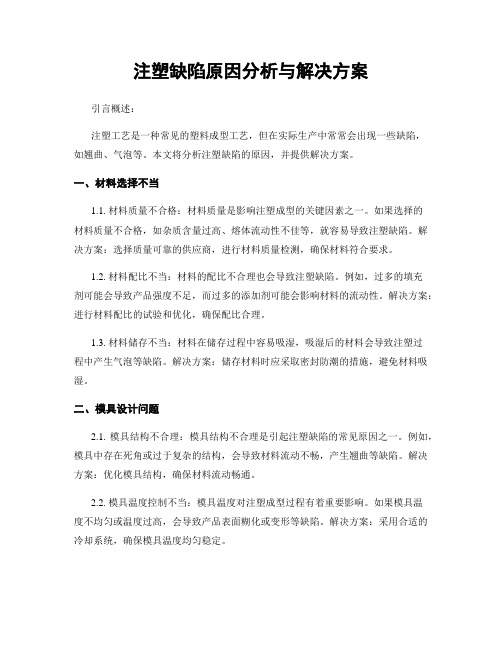
注塑缺陷原因分析与解决方案引言概述:注塑工艺是一种常见的塑料成型工艺,但在实际生产中常常会出现一些缺陷,如翘曲、气泡等。
本文将分析注塑缺陷的原因,并提供解决方案。
一、材料选择不当1.1. 材料质量不合格:材料质量是影响注塑成型的关键因素之一。
如果选择的材料质量不合格,如杂质含量过高、熔体流动性不佳等,就容易导致注塑缺陷。
解决方案:选择质量可靠的供应商,进行材料质量检测,确保材料符合要求。
1.2. 材料配比不当:材料的配比不合理也会导致注塑缺陷。
例如,过多的填充剂可能会导致产品强度不足,而过多的添加剂可能会影响材料的流动性。
解决方案:进行材料配比的试验和优化,确保配比合理。
1.3. 材料储存不当:材料在储存过程中容易吸湿,吸湿后的材料会导致注塑过程中产生气泡等缺陷。
解决方案:储存材料时应采取密封防潮的措施,避免材料吸湿。
二、模具设计问题2.1. 模具结构不合理:模具结构不合理是引起注塑缺陷的常见原因之一。
例如,模具中存在死角或过于复杂的结构,会导致材料流动不畅,产生翘曲等缺陷。
解决方案:优化模具结构,确保材料流动畅通。
2.2. 模具温度控制不当:模具温度对注塑成型过程有着重要影响。
如果模具温度不均匀或温度过高,会导致产品表面糊化或变形等缺陷。
解决方案:采用合适的冷却系统,确保模具温度均匀稳定。
2.3. 模具磨损严重:模具长时间使用后会出现磨损,磨损严重的模具会导致产品尺寸不准确或表面粗糙等缺陷。
解决方案:定期检查和维护模具,及时更换磨损严重的模具部件。
三、注塑工艺参数设置不当3.1. 注射压力过高或过低:注射压力是影响注塑成型的关键参数之一。
如果注射压力过高,会导致产品变形或开裂,而注射压力过低则会导致产品表面光洁度不高。
解决方案:根据产品要求和材料特性,合理设置注射压力。
3.2. 注射速度不合理:注射速度对产品的充填和冷却过程有着重要影响。
如果注射速度过快,会导致产品内部产生气泡或短射,而注射速度过慢则会导致产品表面瑕疵。
注塑产品变形怎么调机【秘籍】
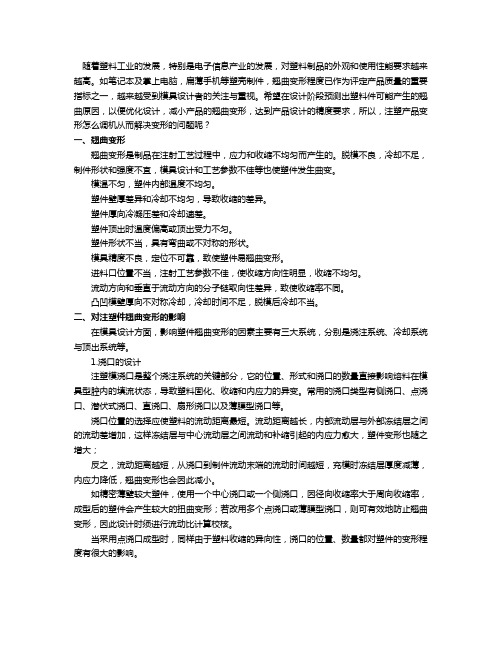
随着塑料工业的发展,特别是电子信息产业的发展,对塑料制品的外观和使用性能要求越来越高。
如笔记本及掌上电脑,扁薄手机等塑壳制件,翘曲变形程度已作为评定产品质量的重要指标之一,越来越受到模具设计者的关注与重视。
希望在设计阶段预测出塑料件可能产生的翘曲原因,以便优化设计,减小产品的翘曲变形,达到产品设计的精度要求,所以,注塑产品变形怎么调机从而解决变形的问题呢?一、翘曲变形翘曲变形是制品在注射工艺过程中,应力和收缩不均匀而产生的。
脱模不良,冷却不足,制件形状和强度不宜,模具设计和工艺参数不佳等也使塑件发生曲变。
模温不匀,塑件内部温度不均匀。
塑件壁厚差异和冷却不均匀,导致收缩的差异。
塑件厚向冷凝压差和冷却速差。
塑件顶出时温度偏高或顶出受力不匀。
塑件形状不当,具有弯曲或不对称的形状。
模具精度不良,定位不可靠,致使塑件易翘曲变形。
进料口位置不当,注射工艺参数不佳,使收缩方向性明显,收缩不均匀。
流动方向和垂直于流动方向的分子链取向性差异,致使收缩率不同。
凸凹模壁厚向不对称冷却,冷却时间不足,脱模后冷却不当。
二、对注塑件翘曲变形的影响在模具设计方面,影响塑件翘曲变形的因素主要有三大系统,分别是浇注系统、冷却系统与顶出系统等。
1.浇口的设计注塑模浇口是整个浇注系统的关键部分,它的位置、形式和浇口的数量直接影响熔料在模具型腔内的填流状态,导致塑料固化、收缩和内应力的异变。
常用的浇口类型有侧浇口、点浇口、潜伏式浇口、直浇口、扇形浇口以及薄膜型浇口等。
浇口位置的选择应使塑料的流动距离最短。
流动距离越长,内部流动层与外部冻结层之间的流动差增加,这样冻结层与中心流动层之间流动和补缩引起的内应力愈大,塑件变形也随之增大;反之,流动距离越短,从浇口到制件流动末端的流动时间越短,充模时冻结层厚度减薄,内应力降低,翘曲变形也会因此减小。
如精密薄壁较大塑件,使用一个中心浇口或一个侧浇口,因径向收缩率大于周向收缩率,成型后的塑件会产生较大的扭曲变形;若改用多个点浇口或薄膜型浇口,则可有效地防止翘曲变形,因此设计时须进行流动比计算校核。
常见注塑缺陷及解决方案
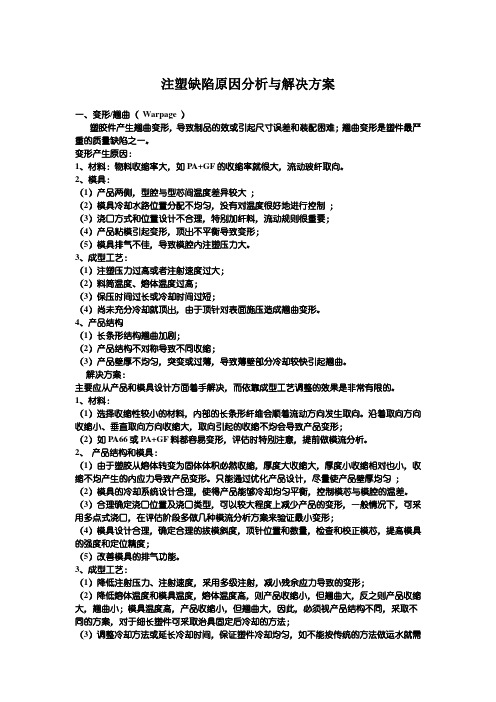
注塑缺陷原因分析与解决方案一、变形/翘曲(Warpage )塑胶件产生翘曲变形,导致制品的效或引起尺寸误差和装配困难;翘曲变形是塑件最严重的质量缺陷之一。
变形产生原因:1、材料:物料收缩率大,如PA+GF的收缩率就很大,流动玻纤取向。
2、模具:(1)产品两侧,型腔与型芯间温度差异较大;(2)模具冷却水路位置分配不均匀,没有对温度很好地进行控制;(3)浇口方式和位置设计不合理,特别加纤料,流动规则很重要;(4)产品粘模引起变形,顶出不平衡导致变形;(5)模具排气不佳,导致模腔内注塑压力大。
3、成型工艺:(1)注塑压力过高或者注射速度过大;(2)料筒温度、熔体温度过高;(3)保压时间过长或冷却时间过短;(4)尚未充分冷却就顶出,由于顶针对表面施压造成翘曲变形。
4、产品结构(1)长条形结构翘曲加剧;(2)产品结构不对称导致不同收缩;(3)产品壁厚不均匀,突变或过薄,导致薄壁部分冷却较快引起翘曲。
解决方案:主要应从产品和模具设计方面着手解决,而依靠成型工艺调整的效果是非常有限的。
1、材料:(1)选择收缩性较小的材料,内部的长条形纤维会顺着流动方向发生取向。
沿着取向方向收缩小、垂直取向方向收缩大,取向引起的收缩不均会导致产品变形;(2)如PA66或PA+GF料都容易变形,评估时特别注意,提前做模流分析。
2、产品结构和模具:(1)由于塑胶从熔体转变为固体体积必然收缩,厚度大收缩大,厚度小收缩相对也小,收缩不均产生的内应力导致产品变形。
只能通过优化产品设计,尽量使产品壁厚均匀;(2)模具的冷却系统设计合理,使得产品能够冷却均匀平衡,控制模芯与模腔的温差。
(3)合理确定浇口位置及浇口类型,可以较大程度上减少产品的变形,一般情况下,可采用多点式浇口,在评估阶段多做几种模流分析方案来验证最小变形;(4)模具设计合理,确定合理的拔模斜度,顶针位置和数量,检查和校正模芯,提高模具的强度和定位精度;(5)改善模具的排气功能。
塑料制品的翘曲变形分析

一、引言翘曲变形是指注塑制品的形状偏离了模具型腔的形状,它是塑料制品常见的缺陷之一。
随着塑料工业的发展,人们对塑料制品的外观和使用性能要求越来越高,翘曲变形程度作为评定产品质量的重要指标之一也越来越多地受到模具设计者的关注与重视。
模具设计者希望在设计阶段预测出塑料件可能产生翘曲的原因,以便加以优化设计,从而提高注塑生产的效率和质量,缩短模具设计周期,降低成本。
本文主要对在注塑模具设计过程中影响注塑制品翘曲变形的因素加以分析。
二、模具的结构对注塑制品翘曲变形的影响在模具设计方面,影响塑件变形的因素主要有浇注系统、冷却系统与顶出系统等。
1.浇注系统的设计注塑模具浇口的位置、形式和浇口的数量将影响塑料在模具型腔内的填充状态,从而导致塑件产生变形。
流动距离越长,由冻结层与中心流动层之间流动和补缩引起的内应力越大;反之,流动距离越短,从浇口到制件流动末端的流动时间越短,充模时冻结层厚度减薄,内应力降低,翘曲变形也会因此大为减少。
图1为大型平板形塑件,如果只使用一个中心浇口(如图1a所示)或一个侧浇口(如图1b所示),因直径方向上的收缩率大于圆周方向上的收缩率,成型后的塑件会产生扭曲变形;若改用多个点浇口(如图1c所示)或薄膜型浇口(如图1d所示),则可有效地防止翘曲变形。
a)中心浇口 b) 侧浇口 c)多点浇口 d) 薄膜型浇口图1 浇口形式对塑料件变形的影响当采用点浇进行成型时,同样由于塑料收缩的异向性,浇口的位置、数量都对塑件的变形程度有很大的影响。
图2为一箱形制件在不同浇口数目与分布下的试验图。
a)直浇口 b)10个点浇口 c)8个点浇口d)4个点浇口 e) 6个点浇口 f) 4个点浇口图2 实验浇口的设置由于采用的是30%玻璃纤维增强PA6,而得到的是重量为4.95kg的大型注塑件,因此沿四周壁流动方向上设有许多加强肋,这样,对各个浇口都能获得充分的平衡。
实验结果表明,按图f设置浇口具有较好的效果。
注塑成型保压参数对塑件翘曲变形的影响
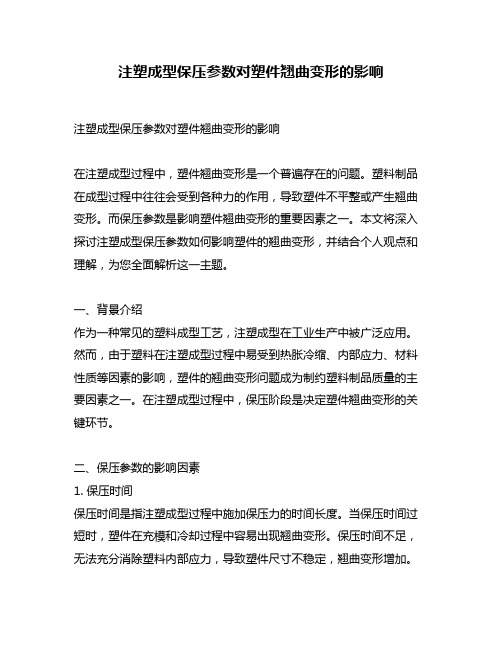
注塑成型保压参数对塑件翘曲变形的影响注塑成型保压参数对塑件翘曲变形的影响在注塑成型过程中,塑件翘曲变形是一个普遍存在的问题。
塑料制品在成型过程中往往会受到各种力的作用,导致塑件不平整或产生翘曲变形。
而保压参数是影响塑件翘曲变形的重要因素之一。
本文将深入探讨注塑成型保压参数如何影响塑件的翘曲变形,并结合个人观点和理解,为您全面解析这一主题。
一、背景介绍作为一种常见的塑料成型工艺,注塑成型在工业生产中被广泛应用。
然而,由于塑料在注塑成型过程中易受到热胀冷缩、内部应力、材料性质等因素的影响,塑件的翘曲变形问题成为制约塑料制品质量的主要因素之一。
在注塑成型过程中,保压阶段是决定塑件翘曲变形的关键环节。
二、保压参数的影响因素1. 保压时间保压时间是指注塑成型过程中施加保压力的时间长度。
当保压时间过短时,塑件在充模和冷却过程中容易出现翘曲变形。
保压时间不足,无法充分消除塑料内部应力,导致塑件尺寸不稳定,翘曲变形增加。
2. 保压压力保压压力是指注塑成型过程中施加在模具上的力大小。
保压压力过大,容易导致塑料流动受阻,造成局部过度压缩而引发变形。
相反,保压压力过小则无法有效地充实塑料料管,产生不均匀的塑件密度分布,进而引发塑件翘曲变形。
3. 保压速度保压速度是指注塑成型过程中注射速度的快慢。
保压速度过快会导致注塑材料充模不充分,形成空洞或气泡,降低塑件的密度,从而增加塑件翘曲变形的风险。
相对应的,保压速度过慢会延长注射时间,使塑料在注射过程中过度热胀冷缩,增加内应力,增加塑件翘曲变形的可能性。
三、个人观点和理解保压参数对于塑件翘曲变形的影响是复杂而微妙的。
在注塑成型中,保压参数需要根据具体的塑料材料、模具结构和塑件要求进行调整。
作为文章撰写者,笔者认为保压时间的控制至关重要。
恰当的保压时间能够平衡塑料在注塑过程中的热胀冷缩现象,降低内部应力,从而减少塑件翘曲变形的风险。
笔者认为保压压力的选择也是关键。
过大的保压压力会导致塑件过度压缩,从而提高翘曲变形的风险。
注塑成型中一模两腔流道平衡优化设计(论)

第38卷第8期 2015年8月合肥工业大学学报(自然科学版)JOURNALOFHEFEIUNIVERSITYOFTECHNOLOGYVol.38No.8 Aug.2015 收稿日期:2014‐06‐27基金项目:教育部科学技术研究重大资助项目(311025)作者简介:周 香(1988-),女,湖南隆回人,合肥工业大学硕士生;陈文琳(1963-),女,安徽安庆人,博士,合肥工业大学教授,硕士生导师.doi:10.3969/j.issn.1003‐5060.2015.08.007注塑成型中一模两腔流道平衡优化设计周 香, 陈文琳, 王晓花(合肥工业大学材料科学与工程学院,安徽合肥 230009)摘 要:具有配合关系的2个塑件一模两腔注塑成型时,容易产生填充、压力及温度不平衡等问题。
文章通过理论计算和实验相结合的方法,分析了玩具电脑A、B面壳成型中存在的翘曲、飞边等缺陷,采用浇口平衡设计理论和有限元变截面法对该浇注系统进行优化设计。
模拟结果表明,充填时间不平衡率控制在0畅61%,充填压力不平衡率控制在3畅87%,且翘曲值有所减小。
优化后塑件缺陷分析结果表明,塑件飞边得到解决,翘曲有明显改善,从而说明流道平衡对改善塑件质量有较好的效果。
关键词:一模两腔;浇注系统;有限元;流道平衡;塑件质量中图分类号:TQ320畅662 文献标识码:A 文章编号:1003‐5060(2015)08‐1036‐05Runnerbalanceoptimizationdesignindouble‐cavitymoldinjectionZHOUXiang, CHENWen‐lin, WANGXiao‐hua(SchoolofMaterialsScienceandEngineering,HefeiUniversityofTechnology,Hefei230009,China)Abstract:Thetwoplasticpartswithcooperativerelationshipareapttotheproblemssuchasunbal‐ancedfilling,pressureandtemperatureindouble‐cavitymoldinjectionprogress.Inthispaper,thedefectsoftoycomputerAandBshellsformingincludingwarpandflasharediscussedthroughthecombinationoftheoreticalcalculationandexperimentalmethod.Furthermore,thedesigntheoryofrunnerbalanceandthefiniteelementmethodofvariablesectionareappliedtooptimizingthegatingsystem.Thesimulationresultsshowthatthefillingtimeimbalancerateandthefillingpressureimbal‐ancerateshouldbecontrolledat0畅61%and3畅87%respectively,andthewarpvaluedecreasestoacertainextent.Finally,thepartsdefectsareanalyzedthroughoptimizedexperiment.Theresultsshowthatplasticflashissolvedandthewarpisimprovedsignificantly,whichindicatesthatrunnerbalancehasgoodeffectinimprovingthequalityofplasticparts.Keywords:double‐cavitymold;gatingsystem;finiteelement;runnerbalance;plasticpartquality 一模多腔模具结构是一种能充分利用生产力资源,减少模具数量,提高企业生产效率和经济性的模具形式,在小型塑件、配合塑件及颜色相同塑件上具有广泛的应用。
- 1、下载文档前请自行甄别文档内容的完整性,平台不提供额外的编辑、内容补充、找答案等附加服务。
- 2、"仅部分预览"的文档,不可在线预览部分如存在完整性等问题,可反馈申请退款(可完整预览的文档不适用该条件!)。
- 3、如文档侵犯您的权益,请联系客服反馈,我们会尽快为您处理(人工客服工作时间:9:00-18:30)。
注塑成型中产品变形与不平衡流动
技术中心 林科松 模流分析师
C & B CONFIDENTIAL
1/26
大纲
13 模流分析的重要性与目的 232 模流分析的作用 3 分析类型 4 流道尺寸设计 5 案例解答(不平衡流动) 6 案例解答(产品变形)
C & B CONFIDENTIAL
2/26
C & B CONFIDENTIAL
11/26
3.进胶口设计
• A、浇口的作用 • 浇口是分流道和型腔之间的连接部分,也是注塑模具浇注系统的最后部分,
通过浇口直接使熔融的塑胶进入型腔内。浇口的作用是使从流道来的熔融塑胶 以较快的速度进入并充满型腔,型腔充满塑胶后,浇口能迅速冷却封闭,防止 型腔内还未冷却的热胶回流。 • 塑胶制品的缺陷如困气、缩水、夹水纹、分解、变形等往往都是由于浇口设 计不合理而造成的。 • B、浇口位置的确定 • 浇口位置的选择,一般应注意以下问题: • 1)、浇口位置应设在制品最大壁厚处,使塑胶从厚壁流向薄壁,并保持浇口 至型腔各处的流程基本一致。 • 2)、防止浇口处产生喷射而在充填过程中产生夹水纹。 • 3)、浇口位置应设在制品的主要受力方向上,因为塑胶的流动方向上所承受 的拉应力和压应力特别高,特别是带填料的增强塑胶,这种情况更加明显。 • 4)、在选择浇口位置时应考虑制品的尺寸要求,因为塑胶经浇口充填型腔 时,在塑胶的流动方向与垂直于流动方向上的收缩不尽相同,所以应考虑到变 形和收缩的方向性。 • 5)、选择浇口位置时,浇口不能直接开在外观面并考虑修正浇口时在塑胶制 品上不留痕迹,以保证制品外观。 • 6)、在浇口位置选定后,可用MOLDFLOW进行模流分析,再确认浇口的位 置是否合理。
在使用时出现很多问题。
• 第一:在顶出制品时由于顶出不在模具中心,顶针固定板容易顶偏,造 成顶针折断,制品变形或损坏。
• 第二:由于主流道不在中心,会造成单面批锋过大。
上述问题虽然可以采用三板模结构来解决,但这样会使模具成本提高。
所以在上述情况下,采用倾斜式主流道的设计可以避免或改进其不足。
斜角a主要与塑胶性能有关,如PE、PP、PA、POM等塑胶,其倾斜角a 最大可达30°;HIPS、ABS、PC等塑胶,其倾斜角a最大可达20°。 SAN、PMMA不能用倾斜式主流道。倾斜式主流道的其他设计参数与垂
圆形截面分流道的塑胶与模具的接触面积为最小,因此其压力损失及温度损失 小,有利于塑 胶的流动及压力传递。其缺点是圆形截面分流道必须在动模及定 模上分别加工。 • 改良梯形截面分流道兼顾了减小压力损失及温度损失和加工便利。 • C、分流道的修正 • 1)、在同一模具上成型两种大小不同的塑胶制品,为了保证在注塑时,塑胶能 同时充满模具上大小。 • 2)、不同的型腔,这时单使用修正浇口大小,不一定能达到充填平衡效果,必 须对分流道进行修正才能达到预期效果。
C & B CONFIDENTIAL
4/26
二.模流分析的作用
• 是通过电脑仿真产品在注塑成型过程中的具体情况,有人把 它很形象的比比喻成万能注塑机。可以通过它来判断注塑成 型的各种缺陷如:填充情况、压力、结合线、缩水、冷凝层、
波前温度、产品变形等。
C & B CONFIDENTIAL
5/26
三.分析类型
• 7、能顺利地引导熔融的塑胶填充各个部位,并在填充过程中不致产 生塑胶涡流、紊乱现象,使型腔内的气体顺利排出模外。
• 8、在成批塑胶制品生产时,在保证产品质量前提下,要缩短冷却时 间及成型周期。
• 9、尽量避免使制品产生结合线,或使结合线产生在制品不重要的部 位。
C & B CONFIDENTIAL
C & B CONFIDENTIAL
12/26
4.胶口类型
C & B CONFIDENTIAL
13/26
五.案例解答(不平衡流动)
• 1、理论上平衡,但由于加工原因而实际生产中形成不平衡 流动现象。
C & B CONFIDENTIAL
14/26
填充动画
请打开附件 填充动画
C & B CONFIDENTIAL
模流分析流程
设计提供模流分析文件包
2D
3D
DFM模流分析执行单
做模流分析
出模流分析报告
发送到相关人员手中
客户回复资料
进胶变更 水路分析 调节夹线 产品变更
模流报告变更
出工艺卡
参加试模实践
解决成型缺陷
C & B CONFIDENTIAL
3/26
一.模流分析重要性与目的
• Mold Flow(模流分析)它是塑胶模具最具有代表性CAE (Computer aided engineering 计算机辅助工程)分析软件, 真正突了传统思维的限制,帮助生产过程实现合理化与人性 化。CAE与CAD和CAM一起,已日渐成企业自身市场竟争 力和争取更大利润的必备工具。
• C.成型材料影响变形:进胶方式相同,但材料牌号不同对产品变形影 响很大。如下图建议方案材料用POM(Hostaform C 9021 K)产品变形 很小。
• D.成型参数影响变形:下面再对建议方案再进行成型参数的调节得出 下列变形结果。
• 从上述结果得出结论:前后模温温差控制不当,变形反而加大;流道加 大对变形影响很小;加长保压时间与注射时间变形反而加大原因是产品 出现过度填充,出现膨胀现象,产品内部产生内应力加大,从而造成变 形加大。
C & B CONFIDENTIAL
7/26
浇注系统设计的基本要点
•
浇注系统的设计包括主流道的选择,分流道截面型状及尺寸的确
定,浇口位置的选择,浇口形式及浇口截面尺寸的确定。
• 在设计浇注系统时应遵循以下原则:
• 1、设计浇注系统时,流道应尽量减少弯折,表面粗糙度为Ra1.6Ra0.8um。
• 2、设计浇注系统时,应考虑到模具是一模一腔还是一模多腔,浇注 系统应按型腔布局设计,尽量与模具中心线对称。
C & B CONFIDENTIAL
26/26
直式主流道的设计相同。
C & B CONFIDENTIAL
9/26
C & B CONFIDENTIAL
10/26
2.分流道设计
• A、分流道设计要求 • 1)、塑胶流经分流道时的压力损失及温度损失要小。 • 2)、分流道的固化时间应稍后于制品的固化时间,以利于压力的传递及保压。 • 3)、保证塑胶迅速而均匀地进入各个型腔。 • 4)、分流道的长度应尽可能短,其容积要小。 • 5)、要便于加工及刀具选择。 • 6)、每节流道要比下一节分流道大10-20%左右。 • B、对分流道截面的分析 • 圆形截面分流道的优点是表面积与体积之比为最小。在容积相同的分流道中
8/26
1.主流道设计要求
•
主流道是指连接注塑机喷嘴与分流道的塑胶通道,是熔料注入模具
最先经过的一段流道其形状,大小会直接影响塑胶的流动速度和注塑时
间。
• A、垂直式主流道(图A)
• B、倾斜式主流道(图B)
• 在设计模具时,往往由于受制品及模具结构的影响,或者由于浇注系统 及腔数的限制,使主流道偏离模具中心,有时这一距离很大,造成模具
15/26
• 2、流体在剪切流动过程中形成不平衡流动现象。
C & B CONFIDENTIAL
16/26
下图为流变学证明不平衡流动的原因
C & B CONFIDENTIAL
17/26
六、案例解答(产品变形)
• 产品变形是成型中最常见又最难解决的成型不良现象。直接影响试模次数与模 具制造周期的重要因素。善于解决其现象减少不必要的试模次数,节省了多次 试模花费的人力与物力,提高工作效率,降低公司的生产成本,实现模具正常 出货。变形是由很多因素造成,现在概括为三大影响因素:如下图可看出解决 变形只是从调节胶口是很不客观的做法。
• 该产品出模后与模流分析变形结果不同,只要是由于产品黏模严重,在 顶出的过程中把产品顶变形,顶针位置出现严重顶高现象。
C & B CONFIDENTIAL
21/26
3、多种因素影响变形案例
• A.流动方向影响变形:试模方案进胶为垂直方向流动,方 案一为平行方向流动,平板产品为了减少产品变形,最好使 用平行流动进胶。
• 一套模具生产成本与生产周期有太部分是花费于试模这一环 节,不能及时时走模,都是由于试模次数过多而造成。近年 来,随着国内塑料模具工业的不断发展,以Moldflow为代表 的塑胶模具CAE模流分析软件的价值得到越来越广泛的信赖 与肯定。通过Moldflow软件的效应,众多企业成功地达到了 节省成本和提升行业内综合竟争力的目的。
PS、PE=0.6 PP、POM=0.7 PA、PMMA=0.8 PVC 、PC=0.9。
• 以上参数只供参考!在流道设计时一定要从流动平衡与流程最 短出发,上一级流尺寸一定要比下一级大0.5以上这样有利于压
力的传递,减少压力的损耗。尽量少使用潜顶针方案进胶,该 方式进胶压力损耗较大,容易造成成型不良 。
C & B CONFIDENTIAL
22/26
C & B CONFIDENTIAL
23/26
• B.胶口位置影响变形:方案二进胶形式不变,但位置变更后变形将有 所减少。浇口位置应设在制品的主要受力方向上,因为塑胶的流动方向 上所承受的拉应力和压应力特别高,特别是带填料的增强塑胶,这种情 况更加明显。胶品的位置是产品应力最容易集中的地方,当变形大的地 方尽量避免放置胶口,如方案二偏离变形大的位置进胶变形减少。
• 3、塑胶制品投影面积较大时,在设计浇注系统时,应避免在模具的 单面开设浇口,否则会造成注塑时受力不均。