表面粗糙度设定规范
混凝土表面粗糙度评定标准

混凝土表面粗糙度评定标准混凝土表面粗糙度评定标准一、引言混凝土表面粗糙度评定是指对混凝土表面平整度的评估。
它是建筑工程中非常重要的检验项目之一,因为表面平整度直接关系到建筑物的外观、强度和耐久性等方面。
因此,制定一套科学合理、实用可行的混凝土表面粗糙度评定标准,对于确保建筑物的质量和安全具有重要意义。
二、标准依据1.《建筑结构验收规范》(GB 50205-2001)2.《混凝土结构工程质量验收规范》(GB 50204-2002)3.《混凝土工程施工质量检验规程》(GB 50203-2011)4.《混凝土工程施工与验收》(GB 50200-2017)三、粗糙度评定方法混凝土表面粗糙度评定方法通常有以下两种:1. 视觉法视觉法是通过人眼直接观察混凝土表面的平整度,根据视觉感受对其进行评定。
这种方法简单直观,但受主观因素影响较大,评定结果不够准确。
视觉法通常适用于表面要求不高的建筑物,如工业厂房、仓库等。
2. 仪器法仪器法是通过使用专业的仪器对混凝土表面进行测量,以达到更为准确的评定结果。
常用的仪器有平板仪、激光仪、光学传感器等。
这种方法对专业人员的要求较高,但评定结果相对准确,适用于表面要求较高的建筑物,如办公楼、商场等。
四、粗糙度等级混凝土表面粗糙度等级通常按照表面平整度进行划分,一般分为以下几个等级:1. 一级表面平整度最高,表面粗糙度小于0.2mm,适用于要求非常高的建筑物,如大型商场、高档写字楼等。
2. 二级表面平整度较高,表面粗糙度在0.2-0.5mm之间,适用于要求较高的建筑物,如高档住宅、酒店等。
3. 三级表面平整度一般,表面粗糙度在0.5-1.0mm之间,适用于要求一般的建筑物,如学校、医院等。
4. 四级表面平整度较差,表面粗糙度在1.0-1.5mm之间,适用于要求较低的建筑物,如工厂、仓库等。
5. 五级表面平整度最差,表面粗糙度大于1.5mm,适用于表面要求非常低的建筑物,如停车场、仓储场等。
表面粗糙度标注原则
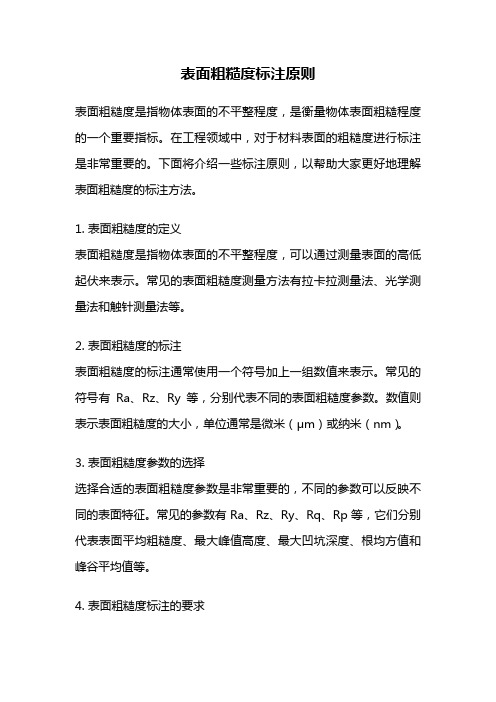
表面粗糙度标注原则表面粗糙度是指物体表面的不平整程度,是衡量物体表面粗糙程度的一个重要指标。
在工程领域中,对于材料表面的粗糙度进行标注是非常重要的。
下面将介绍一些标注原则,以帮助大家更好地理解表面粗糙度的标注方法。
1. 表面粗糙度的定义表面粗糙度是指物体表面的不平整程度,可以通过测量表面的高低起伏来表示。
常见的表面粗糙度测量方法有拉卡拉测量法、光学测量法和触针测量法等。
2. 表面粗糙度的标注表面粗糙度的标注通常使用一个符号加上一组数值来表示。
常见的符号有Ra、Rz、Ry等,分别代表不同的表面粗糙度参数。
数值则表示表面粗糙度的大小,单位通常是微米(μm)或纳米(nm)。
3. 表面粗糙度参数的选择选择合适的表面粗糙度参数是非常重要的,不同的参数可以反映不同的表面特征。
常见的参数有Ra、Rz、Ry、Rq、Rp等,它们分别代表表面平均粗糙度、最大峰值高度、最大凹坑深度、根均方值和峰谷平均值等。
4. 表面粗糙度标注的要求表面粗糙度标注应符合一定的规范,以确保标注的准确性和可读性。
标注应该清晰、整洁,并且不应重复。
标注的位置通常选择在图纸的视图图上,以便于查看和理解。
5. 表面粗糙度标注的示例下面是一个表面粗糙度标注的示例:在图纸的视图图上,使用Ra 符号标注了一个数值为0.4μm的表面粗糙度。
这表示该物体表面的平均粗糙度为0.4微米。
6. 表面粗糙度的影响因素表面粗糙度受到多种因素的影响,包括材料的性质、加工方法、切削速度和切削深度等。
不同的因素会对表面粗糙度产生不同的影响,因此在进行表面粗糙度标注时需要考虑这些因素。
7. 表面粗糙度的测量方法常见的表面粗糙度测量方法有拉卡拉测量法、光学测量法和触针测量法等。
不同的测量方法适用于不同的表面特征,选择合适的测量方法可以提高测量的准确性和可靠性。
8. 表面粗糙度的控制方法对于精密加工和高要求的产品,控制表面粗糙度是非常重要的。
常见的控制方法包括选择合适的加工工艺、使用合适的刀具和切削参数、进行表面处理等。
表面粗糙度国家标注

10/9/2019
a 上限或下限符号U或L b 滤波器类型“x”。标准滤波器是高斯滤波器(GB/T 18777)。
以前的标准滤波器是2RC滤波器。将来也可能对其他的滤波器 进行标准化。在转换期间,在图样上标注滤波器类型对某些公 司比较方便。滤波器类型可以标注为“高斯滤波器”或 “2RC"。滤波器名称并没有标准化,但这里所建议的标注名 称是明确的,无争议的。
和 GB/T18778.32006 定义) 。 其中轮廓参数是我国机械图样中目前最常用的,
轮廓算术平均偏差 Ra、轮廓最大高度 Rz 中的两 个高度为最多。粗糙度轮廓也称 R 轮廓。
10/9/2019
R轮廓(粗糙度参数)
(1)轮廓算术平均偏差Ra(幅度参数)
在取样长度内,被测实际轮廓上各点至轮 廓中线距离绝对值的平均值,即:
10/9/2019
10/9/2019
(3)轮廓单元的平均宽度RSm(间距 参数)
在一个取样长度范围内所有轮廓单元的宽度 Xsi的平均值。
1 m
R Sm m i1 Xsi
10/9/2019
10/9/2019
二、表面粗糙度(评定参数及数值)的选择
1 评定参数的选择:如无特殊要求,一般仅选 用幅度参数。推荐优先选用Ra值,因为Ra能 充分反映零件表面轮廓的特征。以下情况下例 外:
能、导电导热性能和胶合强度等也有着 不同程度的影响。
10/9/2019
有关检验规范的基本术语
1 取样长度和评定长度 取样长度——测量表面粗糙度轮廓时,测量限制的一
段足够短的长度,以限制或减弱波纹度、排除形状误 差对表面粗糙度轮廓测量的影响。(详见P134表5-1) 评定长度默认为 5 个取样长度, 否则应注明个数。 例如Rz0.4、Ra3 0.8、Rz1 3.2 分别表示评定长度 为 5 个( 默认) 、3个、1 个取样长度。
表面粗糙度的标注方法有了新规定

表面粗糙度的标注方法有了新规定——华科大教师团队内部资料表面粗糙度是工程图样和技术文件中的重要内容,GB/T 131‐2006《产品几何技术规范(GPS)技术产品文件中表面结构的表示法》等同采用国际标准,于2007‐02‐01 起代替GB/T131‐1993。
一、表面粗糙度在工程图样中的标注方法1. 新标准规定,当表面粗糙度有单一要求和补充要求时,应使用长边上有一条横线的完整图形符号,完整符号有三种(见图1)。
(a)允许任何工艺(b)去除材料(c)不去除材料图1表面粗糙度各项要求标注的位置如图2 所示:图2单一要求:a ——第一个表面粗糙度要求(传输带/取样长度参数代号数值)b ——第二个表面粗糙度要求(传输带/取样长度参数代号数值)补充要求:c ——加工方法(车、铣、磨、涂镀等)d ——表面纹理和方向e ——加工余量例1(见图3):图3含义:上限值Ra=50μm;下限值Ra=6.3μm;U 和L 分别表示上限值和下限值,当不会引起歧义时,也可不标注U、L;极限值规则均为“16%规则”;两个传输带均为0.008mm—4mm(其中4mm 为取样长度);评定长度中含有5 个取样长度(默认),5×4mm = 20 mm;加工方法为铣;表面纹理符号c(表示表面纹理呈近似同心圆,且圆心与表面中心相关);加工余量为3mm。
例2(见图4):图4含义:第一个表面粗糙度要求Ra 的上限值为1.6μm(符合16%规则),其取样长度为0.8mm;第二个表面粗糙度要求Rz 的上限值为12.5μm(符合最大规则),其取样长度为2.5mm,Rz 的下限值为3.2μm(符合最大规则),其取样长度为2.5mm,其中U、L 在不会引起歧义时也可不标注。
例3(传输带/取样长度为默认值,评定长度中所含取样长度的个数不是默认的5,而是含有3 个取样长度,见图5):图5含义:传输带/取样长度为默认值;评定长度为3 个取样长度;默认Rz 为上限值要求,Rz = 6.3μm,符合最大规则。
表面粗糙度的标注方法有了新规定

表面粗糙度的标注方法有了新规定——华科大教师团队内部资料表面粗糙度是工程图样和技术文件中的重要内容,GB/T 131‐2006《产品几何技术规范(GPS)技术产品文件中表面结构的表示法》等同采用国际标准,于2007‐02‐01 起代替GB/T131‐1993。
一、表面粗糙度在工程图样中的标注方法1. 新标准规定,当表面粗糙度有单一要求和补充要求时,应使用长边上有一条横线的完整图形符号,完整符号有三种(见图1)。
(a)允许任何工艺(b)去除材料(c)不去除材料图1表面粗糙度各项要求标注的位置如图2 所示:图2单一要求:a ——第一个表面粗糙度要求(传输带/取样长度参数代号数值)b ——第二个表面粗糙度要求(传输带/取样长度参数代号数值)补充要求:c ——加工方法(车、铣、磨、涂镀等)d ——表面纹理和方向e ——加工余量例1(见图3):图3含义:上限值Ra=50μm;下限值Ra=6.3μm;U 和L 分别表示上限值和下限值,当不会引起歧义时,也可不标注U、L;极限值规则均为“16%规则”;两个传输带均为0.008mm—4mm(其中4mm 为取样长度);评定长度中含有5 个取样长度(默认),5×4mm = 20 mm;加工方法为铣;表面纹理符号c(表示表面纹理呈近似同心圆,且圆心与表面中心相关);加工余量为3mm。
例2(见图4):图4含义:第一个表面粗糙度要求Ra 的上限值为1.6μm(符合16%规则),其取样长度为0.8mm;第二个表面粗糙度要求Rz 的上限值为12.5μm(符合最大规则),其取样长度为2.5mm,Rz 的下限值为3.2μm(符合最大规则),其取样长度为2.5mm,其中U、L 在不会引起歧义时也可不标注。
例3(传输带/取样长度为默认值,评定长度中所含取样长度的个数不是默认的5,而是含有3 个取样长度,见图5):图5含义:传输带/取样长度为默认值;评定长度为3 个取样长度;默认Rz 为上限值要求,Rz = 6.3μm,符合最大规则。
表面粗糙度标注原则
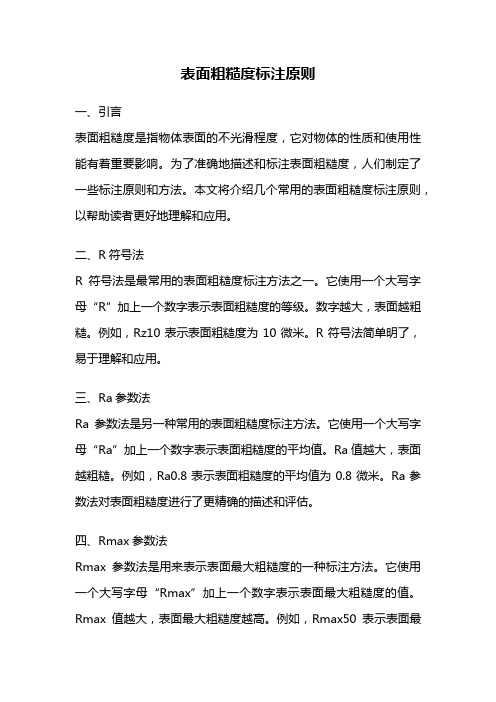
表面粗糙度标注原则一、引言表面粗糙度是指物体表面的不光滑程度,它对物体的性质和使用性能有着重要影响。
为了准确地描述和标注表面粗糙度,人们制定了一些标注原则和方法。
本文将介绍几个常用的表面粗糙度标注原则,以帮助读者更好地理解和应用。
二、R符号法R符号法是最常用的表面粗糙度标注方法之一。
它使用一个大写字母“R”加上一个数字表示表面粗糙度的等级。
数字越大,表面越粗糙。
例如,Rz10表示表面粗糙度为10微米。
R符号法简单明了,易于理解和应用。
三、Ra参数法Ra参数法是另一种常用的表面粗糙度标注方法。
它使用一个大写字母“Ra”加上一个数字表示表面粗糙度的平均值。
Ra值越大,表面越粗糙。
例如,Ra0.8表示表面粗糙度的平均值为0.8微米。
Ra参数法对表面粗糙度进行了更精确的描述和评估。
四、Rmax参数法Rmax参数法是用来表示表面最大粗糙度的一种标注方法。
它使用一个大写字母“Rmax”加上一个数字表示表面最大粗糙度的值。
Rmax值越大,表面最大粗糙度越高。
例如,Rmax50表示表面最大粗糙度为50微米。
Rmax参数法对表面粗糙度的极值进行了标注。
五、其他标注方法除了上述常用的标注方法外,还有一些其他的表面粗糙度标注方法。
例如,使用符号“λ”表示表面波纹度,使用符号“Δ”表示表面峰谷高度差等。
这些标注方法在特定领域和特定要求下得到了应用。
六、标注原则在进行表面粗糙度标注时,应遵循以下几个原则:1. 标注方法应符合国家和行业标准,以确保标注的准确性和可比性;2. 标注应尽量简洁明了,避免使用过多的符号和术语,以便于理解和使用;3. 标注应尽量具体,精确描述表面粗糙度的特征和数值,避免歧义和误解;4. 标注应与设计和制造要求相匹配,以保证产品的质量和性能;5. 标注应尽量规范整洁,避免混乱和错误。
七、应用实例表面粗糙度的标注在各个领域和行业都有广泛应用。
例如,在机械加工中,标注表面粗糙度可以帮助操作人员选择合适的刀具和工艺参数,以提高加工质量和效率。
表面粗糙度的评定标准及方法
表面粗糙度的评定标准及方法当钢材表面经喷射清理后,就会获得一定的表面粗糙度或表面轮廓。
表面粗糙度可以用形状和大小来进行定性。
经过喷射清理,钢板表面积会明显增加很多,同时获得了很多的对于涂层系统有利的锚固点。
当然,并不是粗糙度越大越好,因为涂料必须能够覆盖住这些粗糙度的波峰。
太大的粗糙度要求更多的涂料消耗量。
一般的涂料系统要求的粗糙度通常为 Rz40~75微米.1.粗糙度的定义对表面粗糙度的定义有以下几种:hy:在取样长度内,波峰到波谷的最大高度, ISO8503—3(显微镜调焦法)Ry:在取样长度内,波峰到波谷的最大高度,ISO8503—4(触针法)Ra:波峰和波谷到虚构的中心线的平均距离, ISO 3274Ry5:在取样长度内,五个波峰到波谷最大高度的算术平均值,ISO8503—4(触针法)有关 Rz的表述与 Ry5其实是相同的,Rz的表述来自于德国标准 DIN 4768-1.Ra和 Rz 之间的关系是 Rz相当于 Ra 的 4~6倍。
2. 表面粗糙度的评定标准为了测定钢板表面粗糙度,不同的标准规定了相应的仪器可以使用,测量值以微米(µm)为单位。
国际标准分 ISO 8503 成五个部分在来说明表面粗糙度:ISO8503—1:1995表面粗糙度比较样块的技术要求和定义ISO8503-2:1995喷射清理后钢材表面粗糙度分级―样板比较法ISO8503-3:1995 ISO基准样块的校验和表面粗糙度的测定方法―显微镜调焦法ISO8503—4:1995 ISO基准样块的校验和表面粗糙度的测定方法,触针法ISO8503-5:2004表面轮廓的复制胶带测定法我国的国家标准 GB/T 13288-91《涂装前钢材表面粗糙度等级的评定(比较板块法)》,参照 ISO8503所制订。
3。
比较样块法评定表面粗糙度在涂装现场较为常用的粗糙度评定方法是比较样块法。
常用的粗糙度比较块有英国易高elcometer125,荷兰TQC LD2040、LD2050以及英国PTE R2006、R2007等。
表面粗糙度检测标准规定
标题:粗糙度检验规范文件编号:WI/ZB版本:A修订履历表1.0目的对来自于外购模具、工装、治具、夹具等零配件、本厂加工的模具、工装、治具、夹具等零配件按要求进行表面粗糙度检验,以确保模具、工装、治具、夹具等零配件满足预期的要求。
2.0范围适用于所有组成模具、工装、治具、夹具的零配件,包括委外和内部加工的零配件。
3.0定义3.1表面粗糙度:表面粗糙度是指加工表面具有的较小间距和微小峰谷不平度。
无论采用哪种加工方法所获得的零件表面,都不是绝对平整和光滑的,放在显微镜(或放大镜)下观察,都不得可以看到微观的峰谷不平痕迹,一般是受刀具与零件间的运动、摩擦,机床的振动及零件的塑性变形等各种因素的影响而形成的。
表面上所具有的这种较小间距和峰谷所组成的微观几何形状特征,称为表面粗糙度。
3.2表面粗糙度对工件的影响:3.2.1表面粗糙度影响零件的耐磨性。
表面越粗糙,配合表面间的有效接触面积越小,压强越大,磨损就越快。
3.2.2表面粗糙度影响配合性质的稳定性。
对间隙配合来说,表面越粗糙,就越易磨损,使工作过程中间隙逐渐增大;对过盈配合来说,由于装配时将微观凸峰挤平,减小了实际有效过盈,降低了联结强度。
3.2.3表面粗糙度影响零件的疲劳强度。
粗糙零件的表面存在较大的波谷,它们像尖角缺口和裂纹一样,对应力集中很敏感,从而影响零件的疲劳强度。
3.2.4表面粗糙度影响零件的抗腐蚀性。
粗糙的表面,易使腐蚀性气体或液体通过表面的微观凹谷渗入到金属内层,造成表面腐蚀。
3.2.5表面粗糙度影响零件的密封性。
粗糙的表面之间无法严密地贴合,气体或液体通过接触面间的缝隙渗漏。
3.2.6表面粗糙度影响零件的接触刚度。
接触刚度是零件结合面在外力作用下,抵抗接触变形的能力。
3.2.7影响零件的测量精度。
零件被测表面和测量工具测量面的表面粗糙度都会直接影响测量的精度,尤其是在精密测量时。
3.3表面粗糙度比较样块定义及检验要求:3.3.1定义:表面粗糙度比较样块是检查加工后工件表面的一种对比量具,他的使用方法是以样块工作面的表面粗糙度为标准,凭触觉(如手摸)或视觉(可借助放大镜、比较显微镜等)与待检查的工件表面进行比对,从而判别被检查表面的表面粗糙度是否合乎要求,这是一种定性的检查工具。
表面粗糙度标注新规
表面粗糙度的标注方法新规表面粗糙度是工程图样和技术文件中的重要内容,GB/T 131‐2006《产品几何技术规范(GPS)技术产品文件中表面结构的表示法》等同采用国际标准,于2007‐02‐01 起代替GB/T131‐1993。
一、表面粗糙度在工程图样中的标注方法1. 新标准规定,当表面粗糙度有单一要求和补充要求时,应使用长边上有一条横线的完整图形符号,完整符号有三种(见图1)。
(a)允许任何工艺(b)去除材料(c)不去除材料图1表面粗糙度各项要求标注的位置如图2 所示:图2单一要求:a ——第一个表面粗糙度要求(传输带/取样长度参数代号数值)b ——第二个表面粗糙度要求(传输带/取样长度参数代号数值)补充要求:c ——加工方法(车、铣、磨、涂镀等)d ——表面纹理和方向e ——加工余量例1(见图3):图3含义:上限值Ra=50μm;下限值Ra=6.3μm;U 和L 分别表示上限值和下限值,当不会引起歧义时,也可不标注U、L;极限值规则均为“16%规则”;两个传输带均为0.008mm—4mm(其中4mm 为取样长度);评定长度中含有5 个取样长度(默认),5×4mm = 20 mm;加工方法为铣;表面纹理符号c(表示表面纹理呈近似同心圆,且圆心与表面中心相关);加工余量为3mm。
例2(见图4):图4含义:第一个表面粗糙度要求Ra 的上限值为1.6μm(符合16%规则),其取样长度为0.8mm;第二个表面粗糙度要求Rz 的上限值为12.5μm(符合最大规则),其取样长度为2.5mm,Rz 的下限值为3.2μm(符合最大规则),其取样长度为2.5mm,其中U、L 在不会引起歧义时也可不标注。
例3(传输带/取样长度为默认值,评定长度中所含取样长度的个数不是默认的5,而是含有3 个取样长度,见图5):图5含义:传输带/取样长度为默认值;评定长度为3 个取样长度;默认Rz 为上限值要求,Rz = 6.3μm,符合最大规则。
GB/T1031-2009《产品几何技术规范(GPS)表面结构轮廓法表面粗糙度参数及其数值》介绍
踩 寸 寸躲 距 ∞0 0 .l
机 械
工
业
标
准
化 与 质
量
GB T 1 3 - 2 0 产 品几何技术规 0 0 9《 / 1 - 范 ( GP S)表 面 结构 轮廓 法 表 面 粗糙度参数及其数值》介绍
0 1 m~ 5 m)推荐优 先 选 用 。根据 表 面功 .u 2 p 能 的需 要 ,除 表 面粗 糙度 高 度参 数 ( a R ) R 、 z 外 可选 用轮 廓单 元 的平均 宽度—— , 和轮 廓 7 7
的支承 长度率—— r( )附加 参数 。 C
R z相当于 旧标准中高度参数 尺 ,数值保持不变。
表 3 轮 廓 单 元 的 平 均 宽 度 R m 的 数 值 s
00 6 .o O0l 5 . 2
Rs m
m m
16 . 32 . 63 .
l . 25
01 . 02 . 04 .
08 .
00 5 .2
0. 05
表 4 轮 廓 的 支承 长度 率 R mr ( )的数 值 c
中附加评 定参 数 。即轮廓 微观 不 平度 的平均 间
13—19 《 面 粗糙 度 0 1 95 表
参 数 及 其 数 值》
( 简称 I标 准 ) t 3 。新 标准 依据 GBT3 0 - 2 0 / 5 5 0 9
《 品 几何 技术 规 范 ( S 表 面 结构 轮 廓 产 GP )
表 5R a的 补 充 系列 值
00 8 .0
R0 001 . 0
x I m
2O .
- 1、下载文档前请自行甄别文档内容的完整性,平台不提供额外的编辑、内容补充、找答案等附加服务。
- 2、"仅部分预览"的文档,不可在线预览部分如存在完整性等问题,可反馈申请退款(可完整预览的文档不适用该条件!)。
- 3、如文档侵犯您的权益,请联系客服反馈,我们会尽快为您处理(人工客服工作时间:9:00-18:30)。
粗糙度设定规范目录1.粗糙度的定义-----------------------------------------------------------------22.内容-----------------------------------------------------------------------------24.1粗糙度介绍--------------------------------------------------------------24.1.1粗糙度产生的原因-------------------------------------------------24.1.2粗糙度的评价标准-------------------------------------------------34.1.3表面粗糙度代(符)号及其注法------------------------------64.2表面粗糙度的选用----------------------------------------------------114.2.1表面粗糙度的选用原则-----------------------------------------114.2.2表面粗糙度参数值的适用表面--------------------------------124.2.3轴和孔的表面粗糙度参数推荐值-----------------------------134.2.4各种常用加工方法可能达到的表面粗糙度-----------------144.2.5座椅常用部品粗糙度设定--------------------------------------154.3表面粗糙度的检测方法----------------------------------------------163.相关文件---------------------------------------------------------------------174.实施要求---------------------------------------------------------------------175.附件---------------------------------------------------------------------------173 定义粗糙度:加工表面上具有的间距很小(小于1mm)的微小峰谷所形成的微观几何形状特征。
4.内容4.1粗糙度介绍4.1.1粗糙度产生的原因:由于切削过程中的刀痕,切屑分离时的塑性变形,刀具与工件表面之间的摩擦以及工艺系统的高频振动等原因所形成。
4.1.2 粗糙度的评价标准:4.1.2.1评定表面粗糙度的基本规定实际轮廓:一个指定平面与实际表面相交所得的轮廓(实际表面指物体与周围介质分离的表面)。
取样长度:在X 轴方向判别被评定轮廓不规则特征的长度。
评定长度:用于评定被评定轮廓的X 轴方向上的长度(注:评定长度包含一个或几个取样长度)。
中线:具有几何形状并划分轮廓的基准线。
4.1.2.2表面粗糙度的评定参数为了定量评定表面粗糙度轮廓,必须用参数及其数值来表示表面粗糙度轮廓的特征。
包括:(1)微小峰、谷的幅度;(2) 间距的大小;通常采用下列幅度参数和间距参数: 轮廓算术平均偏差Ra在一个取样长度内纵坐标Z(x)绝对值的算术平均值:ini a Z n R ∑==11轮廓最大高度Rz在取样长度内,最大轮廓高与最大轮廓谷深之和。
轮廓单元的平均宽度RSm一个轮廓峰与相邻的轮廓谷的组合叫做轮廓单元。
在取样长度lr 范围内,中线与各个轮廓单元相交线段的长度叫做轮廓单元的宽度,用符号Xsi 表示。
vp z Z Z R +=轮廓单元的平均宽度是指在一个取样长度lr 范围内所有轮廓单元的宽度Xsi 的平均值。
轮廓支承长度率Rmr(c)在给定水平截面高度c 上轮廓的实体材料长度与评定长度的比率。
轮廓支承长度率Rmr(c) 与零件的实际轮廓形状有关,是反映零件表面耐磨性的指标。
其他条件相同时,Rmr(c) 越大,支承面积越大,接触刚度越高,耐磨性能越好。
轮廓水平截距c 为轮廓峰顶线与平行与它的截线之间的距离。
可用μm 表示,也可用轮廓最大高度Rz 的百分数表示。
Rmr(c)数值用百分数表示。
在给Rmr(c)值时, 必须同时给出轮廓水平截距c 。
simi m X m RS ∑==11nc i mi l lc Rmr )(1)(∑==对于上述四种评定参数:⒈与高度特性有关的评定参数是基本评定参数,通常只给出Ra或Rz 及允许值:(1)参数Ra 的概念直观, Ra 值反映表面粗糙度轮廓特性的信息量大,且Ra 值用触针式轮廓仪测量比较容易,普遍采用。
(2)对于极光滑的表面和粗糙表面,采用Rz 作为评定参数。
粗糙度在Ra 为0.025~6.3μm , Rz 为0.1~25μm范围内,推荐优先选用Ra参数。
⒉与间距和形状特性有关的参数RSm或Rmr(c)是附加评定参数,在有特殊要求时才选用。
4.1.3表面粗糙度代(符)号及其注法:4.1.3.1 表面粗糙度的符号4.1.3.2 表面粗糙度的代号为了表示表面结构的要求,除了标注表面结构参数和数值外,必要时应标注补充要求,包括传输带、取样长度、加工工艺、表面纹理及方向、加工余量等。
这些要求在图形符号中的注写位置:位置a ──注写表面结构的单一要求(该要求不能省略)标注表面 结构参数代号、极限值和传输带或取样 长度; 位置a 和b(同时存在)──注写两个或多个表面结构要求; 在位置a 注写第一个表面结构要求,方法同a 。
在位置b 注写第二个表面结构要求。
如果要注写第三个或更多个 表面结构要求,图形符号应在垂直方向扩大,以空出足 够的空间。
扩大图形符号时,a 和b 的位置随之上移。
位置c ──注写加工方法、表面处理、涂层或其他加工工艺要求等。
如车、磨、镀等加工表面;位置d ──注写所要求的表面纹理和纹理的方向,如“=”、“X”、“M”;位置e──注写所要求的加工余量,以毫米为单位给出数值。
以下为表面粗糙度的单一要求标注示例:①上限或下限的标注:表示双向极限时应标注上限符号“U”和下限符号“L”。
如果同一参数具有双向极限要求,在不引起歧义时,可省略“U”和“L” 的标注。
若为单向下限值,则必需加注“L” 。
②传输带和取样长度的标注:传输带是指两个滤波器的截止波长值之间的波长范围。
长波滤波器的截止波长值就是取样长度ln。
传输带的标注时,短波在前,长波在后,并用连字号“—”隔开。
在某些情况下,传输带的标注中,只标一个滤波器,也应保留连字号“—”,来区别是短波还是长波。
③参数代号的标注:参数代号标注在传输带或取样长度后,它们之间用“/”隔开。
④评定长度的标注:如果默认的评定长度时,可省略标注。
如果不等于5lr时,则应注出取样长度的个数。
⑤极限值判断规则和极限值的标注:极限值判断规则的标注如图中所示上限为“16%规则”,下限为“最大规则”。
为了避免误解,在参数代号和极限值之间插入一个空格。
⏹16%规则: 运用本规则时, 当被检表面测得的全部参数值中,超过极限值的个数不多于总个数16%时, 该表面是合格的。
⏹最大规则: 运用本规则时, 被检的整个表面上测得的参数值一个也不应超过给定的极限值。
(16%规则是所有表面结构要求标注的默认规则。
即当参数代号后未标注写“max”字样时, 均默认为应用16%规则(例如Ra0.8) 。
反之, 则应用最大规则( 例如Ramax0.8) )4.1.3.3 Ra、Rz的参数值国标GB/T1031-2009中,规定了Ra、Rz的参数值。
Ra参数值:Rz参数值4.1.3.4 表面粗糙度的标注示例4.2表面粗糙度的选用4.2.1表面粗糙度的选用原则:(1)在满足零件表面使用功能的前提下,表面粗糙度的要求尽可能低,即尽量选用大的参数值(除Rmr(c)外),以减小加工难度,降低制造成本。
(2)在同一个零件上,非工作表面比工作表面的表面粗糙度值大。
(3)受循环载荷的表面及容易引起应力集中的表面(如圆角、沟槽),表面粗糙度值要小。
(4)配合性质相同时,尺寸小的零件比尺寸大的表面粗糙度值小;同一公差等级,小尺寸比大尺寸、轴比孔的表面粗糙度值要小。
(5)运动速度高、单位压力大的摩擦表面比运动速度低、单位压力小的非摩擦表面的表面粗糙度值小。
(6)一般情况下,尺寸和表面形状要求精确程度高的表面,表面粗糙度值要小。
4.2.2表面粗糙度参数值的适用表面:4.2.3 轴和孔的表面粗糙度参数推荐值4.2.4 各种常用加工方法可能达到的表面粗糙度注:对于钣金类的冲裁在普通冲裁中,材料都是从模具刃口处产生裂纹而剪切分离,制件尺寸精度低(<IT11),断面粗糙(Ra=12.5~6.3μm),不平直,断面有一定斜度,往往不能满足零件较高的技术要求,有时还需再进行多道后续的机械加工。
精密冲裁是使材料呈纯剪切的形式进行冲裁,是通过改进模具来提高精度和改善断面质量的,制件尺寸精度可达到IT6~ IT9,断面粗糙度Ra=1.6~0.4μm,断面垂直度可达89°30′或更佳。
4.3表面粗糙度的检测方法比较法比较法是用已知其高度参数值的粗糙度样板与被测表面相比较,通过人的感官,亦可借助放大镜、显微镜来判断被测表面粗糙度的一种检测方法。
光切法光切法是利用“光切原理”来测量零件表面粗糙度的方法。
光切显微镜(又称双管显微镜)就是应用这一原理设计而成的。
光切显微镜干涉法干涉法是利用光波干涉原理测量表面粗糙度的一种方法。
干涉显微镜针描法针描法又称触针法,是一种接触测量表面粗糙度的方法。
电动轮廓仪(又称表面粗糙度检查仪)就是利用针描法来测量表面粗糙度。
电动轮廓仪5 相关文件GB/T1031-2009产品几何技术规范(GPS)表面结构轮廓法表面粗糙度参数及其数值GB/T131-2006 产品几何技术规范(GPS)技术产品文件中表面结构的表示法GB/T131-2006产品几何技术规范(GPS)_表面结构_轮廓法_评定表面结构的规则和方法GB/T3505-2009产品几何技术规范(GPS)_表面结构_轮廓法_术语、定义及表面结构参数。