塑胶产品通用检验标准书
塑胶产品检验标准书

塑胶产品检验标准书一.目的本规范旨在定义塑胶制品品质标准,为产品设计者提供达到产品图纸图面要求的系统,为质检员提供塑胶制品检验与判定的参考依据,同时是模具及塑胶制品供应商对产品品质要求认知的准则。
二.范围本规范适用于来料中试验证、生产组装所需塑胶制品的成品、部品及其表面的喷油、印刷。
三.职责本规范由质量保证部和工程部负责制定,质量保证部负责实施和维护。
四.定义4.1 缺陷发生危险影响产品的安全性能,或产品使用性能不能达到所期望的目标,或显著的降低其实用性质,或不影响产品的实用性但影响产品外观的缺点。
4.2 塑胶制品外观缺陷4.2.1 欠注———射胶量不足,制件缺料或不饱满。
4.2.2 毛边———分模面挤出的塑胶。
4.2.3 缩水———材料冷却收缩造成的表面凹陷。
4.2.4 凹痕凸起—制件受挤压、碰撞引起的表面凹陷和隆起。
4.2.5 融接痕——塑胶分支流动重新结合的发状细线。
4.2.6 水纹———射胶时留在制件表面的银色条纹。
4.2.7 拖伤———开模时分模面或皮纹拖拉制件表面造成的划痕。
4.2.8 划伤———制件从模具中顶出后,非模具造成的划痕。
4.2.9 变形———制件出现的弯曲、扭曲、拉伸现象。
4.2.10 顶白———颜色泛白,常出现在顶出位置。
4.2.11 异色———局部与周围颜色有差异的缺陷。
4.2.12 斑点———与周围颜色有差异的点状缺陷。
4.2.13 油污———脱模剂、顶针油、防锈油造成的污染。
4.2.14 烧焦———塑胶燃烧变质,通常颜色发黄,严重时炭化发黑。
4.2.15 断裂———局部材料分离本体。
4.2.16 开裂———制件本体可见的裂纹。
4.2.17 气泡———透明制品内部形成的中空。
4.2.18 色差———实际颜色与标准颜色的差异。
4.2.19 修饰不良—修除制件毛边、浇口不良,过切或未修除干净。
4.3 喷油涂层外观缺陷4.3.1 泪油———油膜向下流动聚集的泪滴状突起。
塑胶产品通用标准

是不精密部件有限公司技术标准:一.范圍本标准规定了塑胶部品的外观要求及性能测试、等项目。
本标准适用于供应商生产、研发摸底测试、试生产、批量生产、IQC 来料检验、QA 增强性试验等各个阶段。
二、术语和定义:下列术语和定义适用于本标准。
2.1 不良缺陷定义:2.1.1 塑料件不良缺陷定义2.1.1.1 点缺陷:具有点形状的缺陷,测量尺寸时以其最大直径为准。
2.1.1.2 硬划痕(有感划痕):由于硬物摩擦而造成样品表面有深度的划痕。
2.1.1.3 细划痕(无感划痕):指样品表面没有深度的划痕。
2.1.1.4 批锋(毛刺):由于注塑参数或模具的原因,造成在塑料件的边缘、分型面、顶针孔、镶件等处溢出的多余胶料,摸上去有刮手感觉。
2.1.1.5 缩水:当塑料熔体通过一个较薄的截面后,其压力损失很大,很难继续保持很高的压力来填充在较厚截面而形成的凹坑。
2.1.1.6 熔接线:塑料熔体在型腔中流动时,遇到阻物(型芯等物体)时,熔体在绕过阻碍物后不能很好的融合,于是在塑料件的表面形成一条明显的结合线。
2.1.1.7 气纹:因气体干扰使塑料件表面形成一种雾状发暗痕迹。
2.1.1.8 流纹:因冷料被挤入,在塑料件表面形成的雾色或亮色的痕迹。
2.1.1.9 银纹:在塑料件表面沿树脂流动方向所呈现出的银白色条纹。
2.1.1.10 烧焦:指局部温度过高而在塑料件表面留下的发黄或碳化痕迹。
2.1.1.11 顶白/顶凸:由于塑料件的包紧力大,顶杆区域受到强大的顶出力所产生的白印或凸起。
2.1.1.12 拖花/拉伤:因注射压力过大或型腔不平滑,脱模时所造成边缘的擦伤。
2.1.1.13 缺料:因注射压力不足或模腔内排气不良等原因,使融熔树脂无法到达模腔内的某一角落而造成的射料不足现象。
2.1.1.14 翘曲:塑料件因内应力作用等原因而造成的平面变形。
2.1.1.15 杂质:有异物混入原料中等原因,成型后在产品表面呈现出斑点。
2.1.1.16 气泡:由于原料未充分干燥,造成成型后产品内部有缩孔。
塑胶件检验标准
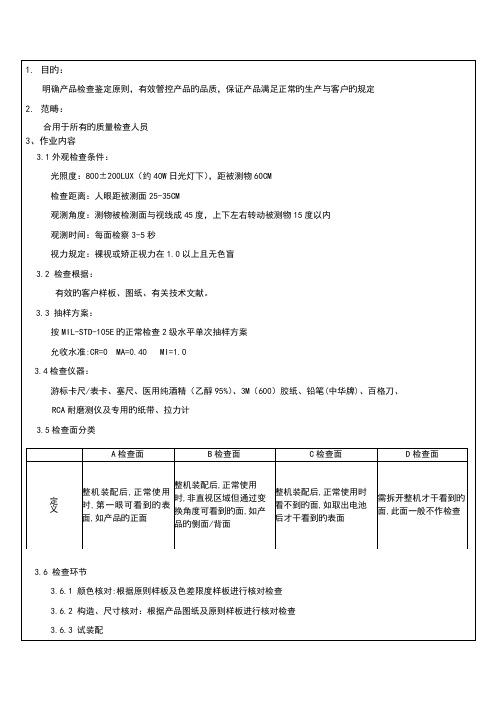
3PCS/LOT
2
附着力测试(印刷字体)
先对印刷部位脱脂,后将3M胶纸粘在印刷区域,并使用铅笔橡皮擦擦拭接触部位,以加强胶带与待测区之接触面积,静置90±30秒后,用手抓住胶带旳一端,在垂直90度方向迅速拉下胶带,同一位置测试3次
丝印字体内容不完整且模糊不清晰为不合格
A
D≤0.4, N≤3两点距离100mm以上
MI
对比菲林
B
D≤0.6, N≤3
两点距离100mm以上
MI
对比菲林
C
无刮手旳点即可
MI
目视
3
无感划伤
目视不明显且无手感
A
L≤5mm W≤0.2mm
N≤1
MI
对比菲林
B
L≤15mm W≤0.2mm N≤2且DS≥100mm以上
MI
对比菲林
4
有感划伤
目视及手感均很明显旳划伤
1.目旳:
明确产品检查鉴定原则,有效管控产品旳品质,保证产品满足正常旳生产与客户旳规定
2.范畴:
合用于所有旳质量检查人员
3、作业内容
3.1外观检查条件:
光照度:800±200LUX(约40W日光灯下),距被测物60CM
检查距离:人眼距被测面25-35CM
观测角度:测物被检测面与视线成45度,上下左右转动被测物15度以内
DS
距离(mm)
S
面积(mm2)
3.8壳料外观检查
序号
项目
缺陷描述
检察面
接受原则
CR/MA/MI
检查措施
1
同色点
与产品表面颜色一致旳点
A
D≤0.5, N≤3
塑胶件检验标准
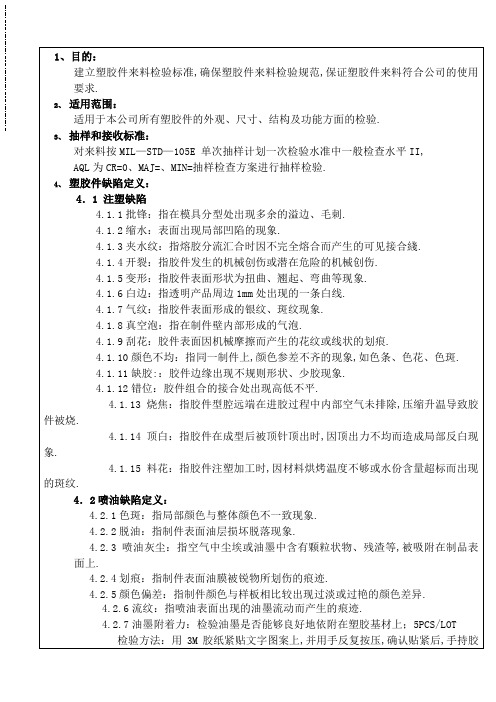
30-45cm对比样品目视不明显
√
丝印质量收货标准
1.
色差:不接受.
2.
丝印偏移:
判定:.0.3mm≤偏移≤0.35mm
√
3.
沙孔:产品表面有沙子般大小的小孔.
A面:大于1个,
√
B面:D≤0.3mm2大于1个
√
C面:D≤0.3mm2大于2个,两个间距≥2cm,
√
4.
漏油:产品漏出底材.
A面:大于1个
个周期物质循环.然后在25℃50%RH状态下取出试验样品,再在常温下恢复两小时一进行外观检验,并测
试百格测试.
判定:产品表面不出现异常,附着力≥4B则为合格:产品表面出现油膜有脱落、变色、裂痕、起皱、分离为异常.
√
3.
表面油漆硬度测试
测试方法
A
用4H铅以45度角力,5MM/秒的速度在油漆表面往返擦拭20次无异常.
B
用橡皮擦在表面擦拭往返20次无异常.
C
以1KG重力,40MM小平面在表面自然推动,以一个往返为1次,推动20次无异常.
√
4.
百格测试
测试方法
用百格刀在测试样本表面划100个1mm×1mm小网格,每一条划线应深及油漆的底层;用毛刷将测试区域
的碎片刷干净;用3M600号胶纸或等同胶纸牢牢粘住被测试区域,并用橡皮擦用力擦拭胶带,以加大胶带
与被测区域的接触面积及力度;静置30秒后,用手抓住胶带一端,以90度迅速撕下胶纸,同一位置进
行3次相同试验;
判定:外观不允许有剥落、裂痕、起皱分离等现象,剥落范围不大于被测面积的5%
√
5
高温测试所有塑胶件必须做高温测试
测试条件及方法:
65℃环境下将所测样品放置于恒温测试仪中,保持12小时.
塑胶产品检验标准书

塑胶产品检验标准书一.目的本规范旨在定义塑胶制品品质标准,为产品设计者提供达到产品图纸图面要求的系统,为质检员提供塑胶制品检验与判定的参考依据,同时是模具及塑胶制品供应商对产品品质要求认知的准则。
二.范围本规范适用于来料中试验证、生产组装所需塑胶制品的成品、部品及其表面的喷油、印刷。
三.职责本规范由质量保证部和工程部负责制定,质量保证部负责实施和维护。
四.定义4.1 缺陷发生危险影响产品的安全性能,或产品使用性能不能达到所期望的目标,或显著的降低其实用性质,或不影响产品的实用性但影响产品外观的缺点。
4.2 塑胶制品外观缺陷4.2.1 欠注———射胶量不足,制件缺料或不饱满。
4.2.2 毛边———分模面挤出的塑胶。
4.2.3 缩水———材料冷却收缩造成的表面凹陷。
4.2.4 凹痕凸起—制件受挤压、碰撞引起的表面凹陷和隆起。
4.2.5 融接痕——塑胶分支流动重新结合的发状细线。
4.2.6 水纹———射胶时留在制件表面的银色条纹。
4.2.7 拖伤———开模时分模面或皮纹拖拉制件表面造成的划痕。
4.2.8 划伤———制件从模具中顶出后,非模具造成的划痕。
4.2.9 变形———制件出现的弯曲、扭曲、拉伸现象。
4.2.10 顶白———颜色泛白,常出现在顶出位置。
4.2.11 异色———局部与周围颜色有差异的缺陷。
4.2.12 斑点———与周围颜色有差异的点状缺陷。
4.2.13 油污———脱模剂、顶针油、防锈油造成的污染。
4.2.14 烧焦———塑胶燃烧变质,通常颜色发黄,严重时炭化发黑。
4.2.15 断裂———局部材料分离本体。
4.2.16 开裂———制件本体可见的裂纹。
4.2.17 气泡———透明制品内部形成的中空。
4.2.18 色差———实际颜色与标准颜色的差异。
4.2.19 修饰不良—修除制件毛边、浇口不良,过切或未修除干净。
4.3 喷油涂层外观缺陷4.3.1 泪油———油膜向下流动聚集的泪滴状突起。
注塑产品检验标准
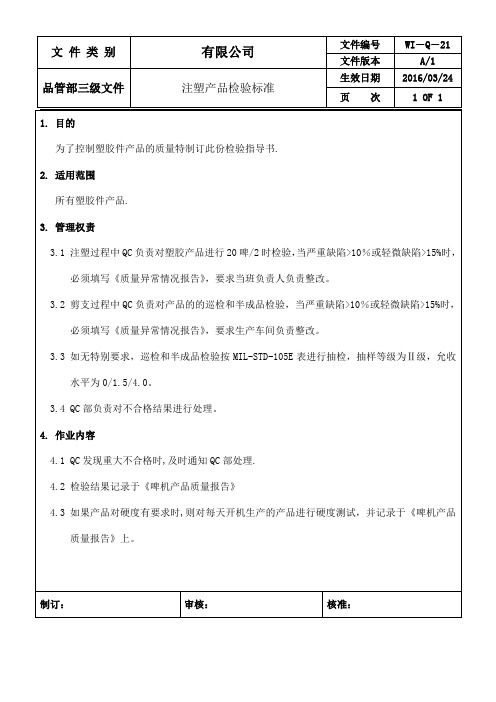
文件类别有限公司文件编号WI-Q-21
文件版本A/1
品管部三级文件注塑产品检验标准生效日期2016/03/24 页次 1 OF 1
1. 目的
为了控制塑胶件产品的质量特制订此份检验指导书.
2. 适用范围
所有塑胶件产品.
3. 管理权责
3.1 注塑过程中QC负责对塑胶产品进行20啤/2时检验,当严重缺陷>10%或轻微缺陷>15%时,
必须填写《质量异常情况报告》,要求当班负责人负责整改。
3.2 剪支过程中QC负责对产品的的巡检和半成品检验,当严重缺陷>10%或轻微缺陷>15%时,
必须填写《质量异常情况报告》,要求生产车间负责整改。
3.3 如无特别要求,巡检和半成品检验按MIL-STD-105E表进行抽检,抽样等级为Ⅱ级,允收
水平为0/1.5/4.0。
3.4 QC部负责对不合格结果进行处理。
4. 作业内容
4.1 QC发现重大不合格时,及时通知QC部处理.
4.2 检验结果记录于《啤机产品质量报告》
4.3如果产品对硬度有要求时,则对每天开机生产的产品进行硬度测试,并记录于《啤机产品
质量报告》上。
制订:审核:核准:。
塑胶件检验标准
★ XXX系列塑胶托盘管控重点: 1.外观可视面级别:序号①②③④⑤⑥⑦⑧⑨⑩备注:塑 胶 件检验标准书文件编号制定日期版 次页 次螺丝定位孔径、位置、强度1.重点管控尺寸2.强度以实配为准,3Kg扭力下不可出现裂纹等托盘面板外观、尺寸 1.托盘面板长、宽、高等尺寸2.如面板需喷漆或不需组装五金面板出货,则以A级面标准判定外观(如XXX抽屉托盘)锁孔位置 1.重点管控尺寸(依图面尺寸量测)管控内容硬币盒/现钞盒长、宽度1.重点管控尺寸(依图面尺寸量测)2.实配现钞隔板、硬币盒无手感顺畅3.其他部位之尺寸依图纸测量,不可超出公差允许之范围现钞隔板槽内宽1.重点管控尺寸,对比图面尺寸确认2.实配组装隔板手感顺畅,不可有较大阻力,不可将托盘侧壁顶变形.塑胶托盘滚轮运动轨道宽度 1.重点管控尺寸1.上述重点管控尺寸供参考,并不完全包括所有管控范围,且此文本会持续更新管控点滑轮固定座宽度1.重点管控尺寸2.客户要求、组装使用等特殊要求经工程师、供应商双方协商后定义落球测试1.使用重量为200g的钢球,50cm高度自由落下,产品背面选5个测试点,各测试3次,不可出现裂纹、破损等2.五个测试点:托盘四角、中心点位置2.相关重点管控尺寸塑胶直边 1.重点管控尺寸,弯曲变形不可超过0.50mm(依图面尺寸量测硬币槽、现钞槽、面板等尺寸)2.实配前面板、硬币盒、现钞隔板等组装顺畅名称⑨A 级面:1.如面板正面需喷漆或不需组装五金面板,则为A 级面(例如XXX 机型)2.如面板正面需组装五金面板,组装后不可见,则为B 级面(例如XXX 机型)B 级面:1.硬币及现钞槽底面,托盘底面、两侧、背面等A 级面B 级面⑧③④⑤⑥⑦②①。
塑胶件外观通用检验标准
5.缺点分类:
5.1一般检验中,缺陷主要分为:极严重、严重、轻微三种。
5.1.1极严重:是指产品的缺陷被买主发现一定退货或一定不接受的情况(与安全、
行规和法律法规有关的缺陷)。
5.1.2严重:是指产品功能主面达不到要求和外观不合要求,被买方很容易发现,且发现后一定不接受之缺陷(与功能和严重外观有关的缺陷).
页数:2 OF 4
1.目的:旨在规定塑胶件的接收标准,更好地满足客户的要求。
2.范围:本标准适用于本公司塑胶件,喷油件,丝(移)件产品的检验。
3.职责:品质部门负责执行并根据客户的要求进行修改。
4.检查方法:
4.1在正常照明条件:两盏40W光灯下,双眼距产品60CM。
4.2身体坐正,以肉眼观察或指导的测量工具检查。
工作指引
文件编号:CQAI-IQ-001-99
页数:1 OF 4
文件名称:塑胶件外观通用检验标准
编写日期
修订版本
修订内容/历史
编写员
2004.12.23
00
初版
吴伟栋
编写员:吴伟栋审核:
修订版本
00
01
02
03
04
05
06
07
08
09
发放印章
工作指引
文件编号:CQAI-IQ-001-99
塑胶件外观通用性检验标准
何掉油脱油的迹象.
●
3M600胶纸测试
用3M600胶纸贴牢固丝(移)印件和喷油件的表面需
测试的位置两端各留1CM左右,双手拉住同时猛然
地拉起胶纸,贴牢距离大于5CM,如此重复5次,(胶纸
不可重复使用),有任何脱油反底的迹象.
塑料产品检验标准(通用)
外观检验标准页版别B.01. 目的为了对塑胶件外观进行有效控制、检验及判定有依据而制定本标准。
2. 适用范围适用于注塑、喷油、丝印、烫金件的外观检验及判定。
3. 检验条件3.1照明应保证40W-60W 的日光灯2支(或相应光源),灯管的高度约为160CM 。
3.2眼睛与产品的距离应保持在30CM 左右,视线与产品被测面(约100cm²)呈60°±30°角,目视时间为5-8秒。
A 级面在检测时应转动,以获得最大反光效果。
B 级面和C 级面在检测期间不必转动。
4.产品外观面的划分A 级面:正面、顶面B 级面:侧面、后盖面正常使用时可见面C 级面:底面D 级面:正常使用时不可见面 5. 划分标准A .杂点、黑点、冷胶、混色斑在直径为50mm 圆以内的个数、大小判定标准如下:各级别划分标准表异物大小 A 级 B 级C 级D 级 0.05-0.10mm 2≦2个 ≦2个≦3个 ≦3个 0.11-0.20mm 2≦1个 ≦2个≦2个 ≦2个 0.21-0.30mm 2≦1个 ≦1个≦2个 ≦2个 0.31-0.35mm 2NG≦1个≦1个 ≦1个 0.35-.050mm 2NG ≥0.51mm 2NGNG同色点判定标准:指颜色与部品颜色相接近的点。
(A级面允许≦1个直径0.35-.050mm 2;B级面允许≦1个直径0.51-0.7mm 2;C 级面允许≦1个直径0.7-1.0 mm 2)光源=40W 日光零件表面人眼(转动视角) 30-90°目视距离30cm被测面(约100cm²)核准:审核:制定:。
塑胶类检验标准
塑胶类检验标准
为控制塑胶产品的质量,同时为检验人员提供依据,特制定此规范。
2适用范围
适用于本公司对a级、b级和c级塑胶物料的检验。
3职责和权限
3.1iqc依照此标准继续执行塑胶物料的外观检验。
3.2qe负责管理此文件的撰写与升
级保护。
4工作环境及所用设备
4.1检验环境
4.1.1被检验物料距离光源高度在1米左右。
4.1.2人眼距离被检验物料的距离为30cm-40cm,±45度角目视。
4.1.3外观检验时
间为5s-10s。
4.1.4光源为黑萤日光灯管(60w)。
4.1.5如右图:
4.2检测设备:游标卡尺、直尺、工具显微镜、检验规、高度计、高度尺、针规、r规、塞规、介刀、
3m胶纸(600)、2h铅笔、95%酒精、橡皮、耐酒精测试架、硬度测试架、耐热测试
架等。
5.1材料级别的定义:
5.1.1a级材料:指高质量标准,以及制作成高档产品所用的原材料(例如:手机、手表、平板等)。
5.1.2b级材料:指普通质量标准,适用于于通常客户所用的原材料。
(例如:电视盒等)5.1.3c级材料:指礼品订单、送来样产品、模具样机及零散客户产品所用原材料。
6抽样检验标准
a级检验标准:
ii:b级检验标准:
iii:c级检验标准:。
- 1、下载文档前请自行甄别文档内容的完整性,平台不提供额外的编辑、内容补充、找答案等附加服务。
- 2、"仅部分预览"的文档,不可在线预览部分如存在完整性等问题,可反馈申请退款(可完整预览的文档不适用该条件!)。
- 3、如文档侵犯您的权益,请联系客服反馈,我们会尽快为您处理(人工客服工作时间:9:00-18:30)。
塑胶产品通用检验标准书Ceneral inspection standard book plastic products2015-06-15发布2015-06-15 实施深圳巴斯巴科技发展有限公司SHEN ZHEN BUSBAR SCIENCE &TECHNOLLGY DEVELOPMENT CO. ,LTD修订履历一、范围:本标准适用于供应商来料(塑胶件)、塑胶部制程检验、组装部生产自检及出货检验等各个阶段。
二、缺陷定义:以下定义适用于本标准2.1 塑胶件不良缺陷定义:2.1.1 点:具有点形状的缺陷(黑点、异色点、碰伤点),测量尺寸时以其最大直径为准。
2.1.2 深划伤(有手感划伤):由于硬物摩擦而造成产品表面有深度的划伤,任一角度目视产品均可见不良缺陷。
2.1.3 浅划伤(无手感划伤):指产品表面没有深度的划伤,视线与被检查物体表面成90°夹角目视产品,缺陷不明显或不可见的不良缺陷。
2.1.4 批锋:由于注塑参数或模具原因,造成在产品分型面、顶针孔、镶件及滑块处等溢出的多余胶料,有刮手的感觉。
2.1.5 缩水:壁厚处表面的原料由于体积收缩,固化成型后在产品表面形成凹陷痕迹。
2.1.6 熔接线:塑胶熔体在型腔中流动时,遇到阻物(型芯等物体)时,熔体在绕过阻碍物后不能很好融合,于是在塑胶件表面形成一条明显的结合线。
2.1.7 气纹:因气体干扰使塑胶件表面形成雾状发暗、发白的痕迹。
2.1.8 流纹:因冷料被射入,在塑胶件表面形成雾色或亮色痕迹。
2.1.9 银纹:指塑胶件表面树脂流动方向所呈现出的银白色条纹,主要集中在浇口处。
2.1.10 烧焦:指局部高温而在塑胶件表面留下发黄或碳化的痕迹。
2.1.11 顶白/顶凸:由于塑胶件包紧力大,顶杆区域受到强大的顶出力所产生的白印或凸起现象。
2.1.12 拉伤(拖花):因注射压力过大或型腔不平滑,脱模时造成塑胶件边缘擦伤,主要出现在模具分模位和滑块位。
2.1.13 缺料:因注射压力不足或模腔内排气不良等原因,使熔料无法达到模腔内的某一角落而造成射料不足现象。
2.1.14 翘曲变形:模具内的材料受到高压而产生的内部应力,脱模后产品收缩导致弯曲变形。
2.1.15 杂质:有异物混入原料中,成型后在产品表面呈现出斑点。
2.1.16 气泡:由于原料未充分干燥,造成成型后产品内部有缩孔。
2.1.17 多胶:因模具方面的损伤或镶件断裂而造成塑胶件表面有塑胶凸起。
2.1.18 色差:产品表面呈现出与原样件颜色的差异或同一套外壳之间呈现出颜色的差异;2.1.19 纤花:尼龙料中的白色玻纤在塑料熔体充模流动过程中浮露于外表,待冷凝成型后便在塑胶表面形成放射状白色痕迹。
当塑胶件为黑色时因色泽的差异大而更加明显。
2.1.20 破裂:由于模具原因导致产品表面拉裂现象。
2.1.21 掉纹:模具用久后局部纹路不一致现象;2.1.22 台阶:镶件、滑块位置与主体之间不平齐的高度2.2 喷涂件不良缺陷定义:2.2.1 毛絮:油漆本身带有的或油漆未干燥时落在油漆表面形成的纤维状毛絮。
2.2.2 积漆:由于油漆的流平性较好,容易在喷漆件表面出现局部的油漆堆积现象。
2.2.3 缩水:由于塑胶件表面存在缩水,在喷涂后没有盖住反而更加明显。
2.2.4 桔皮纹:在喷涂件表面出现大面积细小的像桔子皮形状的起伏不平。
2.2.5 漏底:在喷涂件表面出现局部的油漆层过薄而露出基体颜色的现象。
2.2.6 手印:在油漆层未干时,用手摸产品而在产品表面留下的手指印痕。
2.2.7 油漆脱落:喷涂件表面出现涂层脱落的现象。
2.2.8 尘点:在喷涂件表面附着的细小尘粒或杂质。
2.2.9 鱼眼:由于溶剂挥发速度不适而造成在喷涂件表面有凹陷或小坑。
2.2.10 雾状:整个产品表面光洁度不好,表面呈雾状。
2.2.11 气泡:在涂层表面呈现的小鼓包,受外力挤压易破裂。
2.2.12 光泽不良:喷涂件表面呈现出与原样件(色板)光泽不一致的情况。
2.3 丝印字体不良缺陷定义:2.3.1 色薄:丝印字体颜色偏淡。
2.3.2 重影:二次印刷整体错位。
2.3.3 锯齿:字体边缘呈现锯齿状。
2.3.4 扩散:字体边缘呈现模糊状。
2.3.5 针孔:在应该有印刷的地方出现点状的缺少油墨。
2.3.6 溅点:在无印刷的区域出现点状油墨。
2.3.7 花斑:对于大面积印刷不均匀而出现的局部斑状不良,此区域与别的区域看上去明显不同。
2.3.8 粗细不均匀:字体各个笔画之间出现粗细不一样的现象。
2.3.9 字体倾斜:各字体或同一字体的底部不在同一水平线上。
2.3.10 字体偏位:字体偏移图纸尺寸位置。
2.4 电镀件不良缺陷定义:2.4.1 漏镀:在应该电镀的地方没有电镀,导致露出基材。
2.4.2 镀层脱落:电镀件表面出现电镀层起皮脱落的现象。
2.4.3 污渍:在电镀件表面所残留的油污、印渍。
2.4.4 局部发黄:由于电镀时电流过大等原因造成产品颜色发黄。
2.4.5 暗斑:电镀件表面局部发暗。
2.4.6 麻点:电镀件表面出现的颗粒状缺陷。
2.4.7 针孔:电镀件表面出现针孔状不良。
2.4.8 雾状:电镀件表面出现局部发白或模糊的现象。
2.4.9 粗糙:由于塑胶件的模具没有抛好光,造成电镀件表面不光滑。
2.4.10 色泽不均匀:电镀件表面出现的颜色及光泽不均匀的现象。
2.5 缺陷分类的定义:2.5.1 严重(致命)缺陷(CR):可能对使用者造成伤害或有安全隐患的缺陷,或造成产品不能使用或主要功能不能实现的缺陷;影响机械或电气性能,产品在组装后或在客户使用时会发生重大品质事件的。
2.5.2 重要(主要)缺陷(MA):性能不能达到预期的目标,但不至于引起危险或不安全现象;导致最终影响产品使用性能和装配;客户很难接受或存在客户抱怨风险的。
2.5.3 轻微(次要)缺陷(MI):不满足规定的要求但不会影响产品使用功能的;客户不易发现,发现后通过沟通能使客户接受的。
2.6 外观面的定义:2.6.1 A级面:产品在客户组装过程中或终端用户正常使用过程中可直接看到产品正面;2.6.2 B级面:产品在客户组装过程中或在终端用户正常使用过程中可直接看到的产品侧面及底面。
2.6.3 C级面:产品的内部面为C级面(即除了A、B级以外的面)。
2.7 缺陷代码对照表:(表一)三、检验条件及检验环境要求:3.1 距离:眼睛与被检测的物体表面距离为300mm~450mm。
3.2 时间:每件外观检查时间不超过5秒。
(如果5秒内看不出问题缺陷可以不算在内)3.3 检查角度:以垂直正视为准±45度角。
3.4 照明条件:光照度达600~800LUX。
3.5 检查视力:不低于1.0,且视觉正常,不可色盲、斜视、散光。
3.6 检查顺序:先正面、顶部、侧门、底部、反面。
四、塑胶产品外观检验:5.1 塑胶原料检验:5.1.1 塑胶原料的质量直接影响塑胶产品的外观、尺寸精度及物理机械性能,所以必须对原材料进行外观(色泽、颗粒大小及均匀性等)和工艺性能(熔融指数)进行检验,要求原材料厂家每批送货时附材质证明书,在材质证明书中注明塑胶材料制造商、牌号、型号、阻燃级别、着色方式、添加剂种类等各项说明。
5.1.2 塑胶阻燃级别测试(图纸无规定按V0级标准执行):V-0:对样品进行两次10秒的燃烧测试后,火焰在30秒内熄灭。
不能有燃烧物掉下;V-1:对样品进行两次10秒的燃烧测试后,火焰在60秒内熄灭。
不能有燃烧物掉下;V-2:对样品进行两次10秒的燃烧测试后,火焰在60秒内熄灭。
可以有燃烧物掉下。
5.1.3 除了结构图纸中允许使用替代材料外,在任何材料变更时均须重新进行样品试制确认工作后方可生产。
5.2 塑胶件螺纹性能测试(镶螺母产品):5.2.1 按照开发图面要求对镶母扭矩进行测试;5.2.2 如开发图纸未作明确规定时,则按照下表6.8级VW标准执行;5.3 产品信赖性测试(表面喷油产品):序号测试项目测试方法测试结果备注1百格测试划好1mm×1mm 的方格后,用3M 600#胶带测试3次(每次用新胶带),并用橡皮擦擦拭胶带,加大胶带与被测区域的接触面积及力度,停留5秒钟后用手抓住胶带的一端,以90度角方向迅速拉起胶带,同一位置测试三次,同一产品测试三处不同位置。
100%不脱落为OK图纸有明确规定按图纸要求执行2铅笔测试三菱”HB铅笔,负重1000g,以45度角匀速划5条线(不同位置),再用橡皮擦将铅笔痕擦拭干净。
任何一条有划痕判定为NG3耐油测试用猪毛刷将化学药剂刷到产品表面并到室温下自然干燥。
(猪毛刷的握手部分为铝,长宽分别为25*6mm).a.润滑油(刷后室温保持24小时);b.制动液(刷后室温保持24小时);c.汽油(刷后室温保持24小时);d.柴油(刷后室温保持24小时);e.机油(刷后室温保持24小时);f.液压油(刷后室温保持24小时)表面无变色、起泡为OK4高低温零件在85℃静止4H,转至-40℃静止4H,共6个循环涂层无裂纹为OK;5盐雾测试按照中性盐雾测试条件,在盐雾测试箱内连续喷雾96H涂层无变色、脱落、龟裂等不良六、塑胶产品结构、尺寸检验:6.1 所有塑胶产品的结构及尺寸均以开发(客户)提供的样板和标准图纸(尺寸公差)为准来进行检验判定。
七、实配检验标准:7.1 配套相应的装配件,配件要求配合良好、错位(断差)≦0.20mm。
7.2 产品实配后间隙正常不大于0.2mm(图纸。
7.3 产品实配后转动部位,无干涉或受阻的现象。
7.4 如客户有特殊要求,依客户要求标准执行。
八、包装检查:8.1 产品的包装应与对应的《作业指导书S0P》上所注明的包装方式、包装数量一致。
8.2 产品的外箱标签须填写正确规范、无少填、错填现象,标签内容必须与箱内的产品一致。
8.3 产品外箱无明显破损、脏污等现象。
8.4 所有的包装以不影响品质(包括搬运/储存等过程环节)为原则,客户有特殊要求依要求执行。