转炉连铸新技术
连铸技术的发展状况及高效连铸

机作业率大大提高(≥80%)。
1.2高效连铸的主要作用
1.2.1
连铸坯产量大幅度提高
004
从1989年到2001年我国连铸坯产量由1
投资3~4亿元。
万t增加到12 000万t以上,连铸比由16.3%提高 到87.5%。如果只靠投资新建铸机,而没有连铸机 的高效化,新建和原有铸机都是那样的低生产率,要 想达到这样的总产量是不可想象的,无论资金投入、 场地占用等许多方面都是难以承受的。高教连铸技 术为钢铁行业的调整结构降低成本作出了贡献。 1.2.2 实现炼钢车间的炉机匹配 我国的转炉车间炉容从几吨到200 t都有小方坯 生产。由于小方坯铸机生产能力低,3台转炉配4、5 台甚至6台连铸机,匹配关系复杂混乱,工艺制度不 能保证。这反过来又影响了铸机生产和铸坯质量。 经过连铸机的高效化改造,设备可靠性增加,浇 铸速度提高,连铸机的台时产量大幅提高。实现了各 种模式的炉机匹配生产。如原3炉4、5机全连铸炼 钢车间只需要3台铸机.1炉对1机生产。原来炉容 较小的3炉2机加模铸的车间可实现3炉对2机的 全连铸生产。 炉机匹配后的最大好处全车间生产顺行,工艺制 度得以执行。钢水的温度、氧化性、到位时间都可保 证。这又促进了铸机生产的稳定、高速、优质。 1.2.3经济效益 实现高教连铸使各项技术指标提高,消耗下降, 铸坯质量改善,可使企业降低成本节省投资,获得很 大的经济效益。 连铸直接效盎首钢三炼钢厂统计,由于提高合 格坯收得率、节省备件费用、减少耐材消耗等可降低 连铸坯成本约7元/t。广钢转炉厂节省中间包材料 及提高铸坯收得率可降低连铸坯成本10元/t。 综合经济效益包括降低冶炼消耗、降低连铸成 本、提高综合成材率等,见表4。
450
mm,带厚度2.3~3.2
mm,拉速达35~70 m/rain,该生产线计划于2001年
连铸技术国内外现状及发展趋势

连铸技术国内外现状及发展趋势
连铸技术是钢铁工业中的重要技术之一,它可以实现高效连续生产,提高生产效率,降低成本。
目前,国内外的连铸技术都在不断发展和完善中。
在国内,连铸技术已经实现了从单流到双流、三流、四流等多流程的升级。
同时,还出现了带分段式结晶器、上下扫描式结晶器等新型结晶器,提高了连铸成材率和质量。
此外,国内的连铸技术还在不断推广智能化生产、绿色环保等方面的应用。
在国外,美国、日本等发达国家在连铸技术方面也有很多创新。
例如,美国的Hazelett连铸技术可以实现高品质的铝合金连铸,日本的CCS连铸技术则可以实现高浓度的钢水连铸。
此外,欧洲的一些连铸厂还在探索使用第三方能源进行加热,以实现更高的能源利用效率。
未来,随着新材料、新工艺、新技术的不断涌现,连铸技术将继续发展和创新。
同时,环保、智能化、自动化等方面也将成为连铸技术发展的重要方向。
- 1 -。
转炉精炼及连铸工艺设计答辩讲稿

转炉精炼工艺可根据不同的金属种类和用途,采用不同的精炼剂和工艺参数,以达 到最佳的精炼效果。
转炉精炼的重要性与应用
转炉精炼是现代工业中不可或缺 的一种金属加工工艺,尤其在钢 铁、有色金属等领域应用广泛。
通过转炉精炼,可以显著提高金 属材料的性能和品质,满足高端 制造业、航空航天、汽车、建筑
经济效益与社会效益的评估
总结词
经济效益与社会效益的评估是转炉精炼 及连铸工艺设计的最终目的,它决定了 企业的竞争力和市场地位。
VS
详细描述
在经济效益方面,应关注投资回报率、成 本效益比、产品附加值等方面。在社会效 益方面,应关注产品的市场需求、用户满 意度、企业社会责任等方面。通过对经济 效益和社会效益的综合评估,可以为企业 的发展战略和市场定位提供有力支持。
03
转炉精炼与连铸工艺的结合
转炉精炼与连铸工艺的关系
转炉精炼是炼钢工艺中的重要 环节,通过控制温度、成分和 熔池搅拌等手段,实现钢液的 净化和合金化。
连铸工艺则是将转炉精炼后的 钢液连续铸造成各种规格的钢 坯或钢材,以满足不同需求。
转炉精炼与连铸工艺的结合, 能够实现炼钢工艺的高效、连 续和自动化生产。
连铸工艺的重要性与应用
连铸工艺是现代钢铁生产中的 重要环节,对于提高产品质量 、降低生产成本、节能减排等
方面具有重要作用。
通过连铸工艺,可以生产出各 种规格、不同材质的钢材和铸
件,满足不同领域的需求。
连铸工艺在钢铁、有色金属、 机械、汽车、船舶、建筑等行 业中得到了广泛应用。
随着科技的不断发展,连铸工 艺的应用前景将更加广阔。
连铸工艺流程与原理
连铸工作中的改进方案和总结
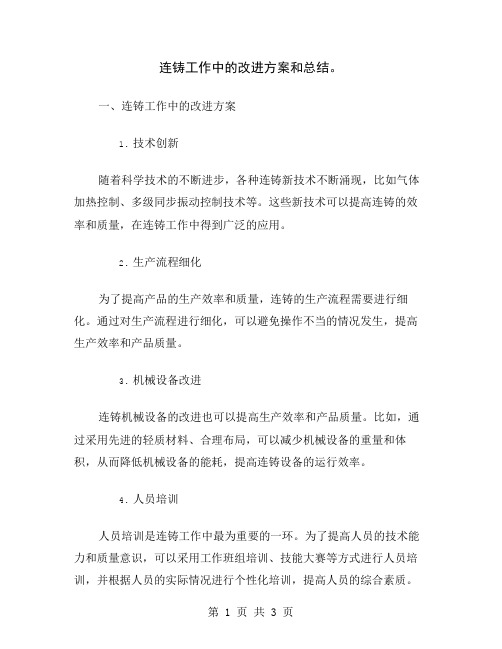
连铸工作中的改进方案和总结。
一、连铸工作中的改进方案1.技术创新随着科学技术的不断进步,各种连铸新技术不断涌现,比如气体加热控制、多级同步振动控制技术等。
这些新技术可以提高连铸的效率和质量,在连铸工作中得到广泛的应用。
2.生产流程细化为了提高产品的生产效率和质量,连铸的生产流程需要进行细化。
通过对生产流程进行细化,可以避免操作不当的情况发生,提高生产效率和产品质量。
3.机械设备改进连铸机械设备的改进也可以提高生产效率和产品质量。
比如,通过采用先进的轻质材料、合理布局,可以减少机械设备的重量和体积,从而降低机械设备的能耗,提高连铸设备的运行效率。
4.人员培训人员培训是连铸工作中最为重要的一环。
为了提高人员的技术能力和质量意识,可以采用工作班组培训、技能大赛等方式进行人员培训,并根据人员的实际情况进行个性化培训,提高人员的综合素质。
二、连铸工作中的总结1.高品质的原材料在连铸工作中,高品质的原材料是保证产品质量的基础。
因此,在原材料采购时,一定要选择质量好、纯度高的原材料。
2.加强管理和监控为了确保连铸工作的正常进行,必须要加强对生产过程的管理和监控。
通过实时监测,可以及时发现和解决生产过程中的问题,避免问题扩大并影响生产效率和产品质量。
3.用先进技术提升质量为了确保连铸生产的高效率和高质量,必须使用先进技术。
只有掌握了先进技术,才能不断提升连铸生产的效率和质量。
4.确保生产安全安全是连铸工作中最为重要的一环。
为了确保生产过程的安全,必须严格遵守生产规程,在工作过程中注意安全,提高员工的安全意识,加强设备的安全保障。
连铸工作中的改进方案和总结可以提高生产效率和产品质量,以适应市场需求的不断增长。
通过不断探索和发展,连铸技术和生产工艺将会得到更加广泛的应用,为实现精准制造和高质量发展做出贡献。
连铸新技术_PPT幻灯片
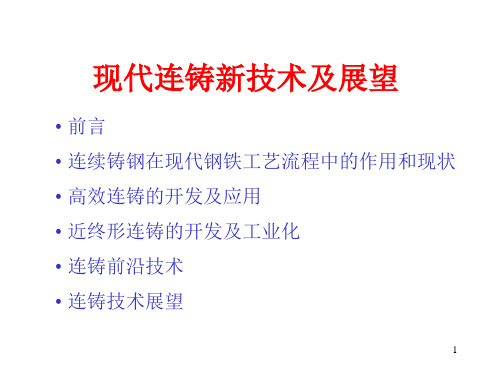
三、 高效连铸的开发及应用
• 高效连铸技术是20世纪80年代中后期发展起 来的,是连铸技术优化发展的方向。所谓高 效连铸通常是指比常规连铸生产效率更高, 以高拉速为核心,以高质量、无缺陷铸坯生 产为基础,实现高连浇率、高作业率的连铸 系统技术。其核心是高拉速技术。
17
三、 高效连铸的开发及应用
连铸机高的作业率和高的铸坯质量是与钢水在连铸机 凝固过程紧密相连的,这样就需要不断改进连铸机设备、 工艺技术和过程控制技术以实现优化配置,使连铸机生产 达到高产量、高质量、低成本的目的。
因此,今天简要介绍为实现这一目标,目前连铸生产 中所采用的先进技术和今后的发展趋势。
3
2.1 连续铸钢技术的发展历程
量扩张到结构优化的战略转移。突出的贡献之一在于连 续铸钢技术的工业化,取代了用钢锭模铸钢、初轧机开 坯的第一代钢液成形技术,从而使从炼钢到轧制成材的 工艺生产线连续化成为可能。而今,随着相关行业科学
技术的进步,特别是控制技术的发展,传统连铸技术已 无竞争能力可言,即将为以高效连铸、近终形连铸为代 表的新一代连铸技术所代替。目前,连铸技术水平的高 低已成为一个国家钢铁工业技术水平的重要指标之一。
—出结晶器均匀的坯壳厚度; —液相穴的长度; —铸坯的冷却强度。
• 第一阶段(1840—1930年)
连续浇铸金属液思想的启蒙阶段。 最早 (1887年)提出与现代连铸机相似的连铸设备建议 的是德国人R.M.Daelen,在其开发的设 备中已包括了上下敞开的结晶器、液态金属注入、 二次冷却段、引锭杆和铸坯切割装置等。
6
2.1 连续铸钢技术的发展历程
• 第二阶段(1940—1949年)
高 效
20
3.1 高效连铸的应用
钢铁冶金新工艺技术目录

钢铁冶金新工艺技术目录钢铁冶金是现代工业中应用最广泛的材料之一,其技术不断发展和创新,推动了钢铁行业的高效生产和质量提升。
下面是一份钢铁冶金新工艺技术目录。
一、高炉冶炼新技术1. 高效节能热风炉技术:采用高效燃烧器和余热回收装置,提高燃烧效率和热风温度,降低燃料消耗和排放。
2. 富氧预处理技术:通过对冶炼矿石进行富氧预处理,提高还原效率和高炉产能,减少煤耗和焦耗。
3. 燃料灰渣精煤技术:通过对燃料灰渣中的可燃物质进行精煤,提高燃烧效率和热量利用率,降低煤耗和废气排放。
二、转炉冶炼新技术1. 高效氧枪技术:采用高效氧枪和透氧技术,提高氧枪吹氧效率和转炉熔化过程中的氧气利用率,降低氧气消耗和炉渣中的氧化铁含量。
2. 喷吹粉煤技术:通过将粉煤喷吹到转炉中,在燃烧过程中释放高热值的挥发分,提高炉内温度和燃烧效率,减少焦耗和燃料消耗。
3. 渣液脱锰技术:通过添加适量的石灰和石膏等物质,控制转炉渣中的碱度和碳酸锰含量,降低转炉渣锰损失和锰冶炼成本。
三、连铸新技术1. 水模连铸技术:采用水模铸坯,提高结晶器冷却效果和铸坯的表面质量,降低铸坯变形和裂损率,提高铸坯质量和连铸效率。
2. 轧辊调整技术:通过轧辊调整系统自动化控制,实现辊型调整和轧件形状控制,提高轧件尺寸精度和表面质量,降低轧制能耗和加工成本。
3. 涂层技术:在连铸过程中,对铸坯和轧件表面进行涂层处理,减少表面氧化、脱碳和损伤,提高产品质量和附加值。
四、高温热处理新技术1. 连续退火技术:采用连续退火设备,对钢材进行高温退火处理,实现均匀结构和优良性能,提高钢材的塑性和韧性。
2. 淬火技术:采用先进的淬火设备和工艺,快速冷却钢材,形成细小、均匀的马氏体组织,提高钢材的硬度和耐磨性。
3. 氮化处理技术:通过将钢材置于含氮气氛中,在高温下进行氮化处理,提高钢材的表面硬度和耐腐蚀性。
五、环保技术1. 高效除尘技术:采用先进的除尘设备和技术,减少钢铁冶炼过程中的烟尘和废气排放,改善环境污染问题。
现代连铸新工艺、新技术与铸坯质量控制

现代连铸新工艺、新技术与铸坯质量控制下载提示:该文档是本店铺精心编制而成的,希望大家下载后,能够帮助大家解决实际问题。
文档下载后可定制修改,请根据实际需要进行调整和使用,谢谢!本店铺为大家提供各种类型的实用资料,如教育随笔、日记赏析、句子摘抄、古诗大全、经典美文、话题作文、工作总结、词语解析、文案摘录、其他资料等等,想了解不同资料格式和写法,敬请关注!Download tips: This document is carefully compiled by this editor. I hope that after you download it, it can help you solve practical problems. The document can be customized and modified after downloading, please adjust and use it according to actual needs, thank you! In addition, this shop provides you with various types of practical materials, such as educational essays, diary appreciation, sentence excerpts, ancient poems, classic articles, topic composition, work summary, word parsing, copy excerpts, other materials and so on, want to know different data formats and writing methods, please pay attention!一、引言随着现代工业的发展,连铸技术作为一种高效、节能的铸造工艺,逐渐成为铸造行业的主流技术之一。
炼钢与连铸若干新技术
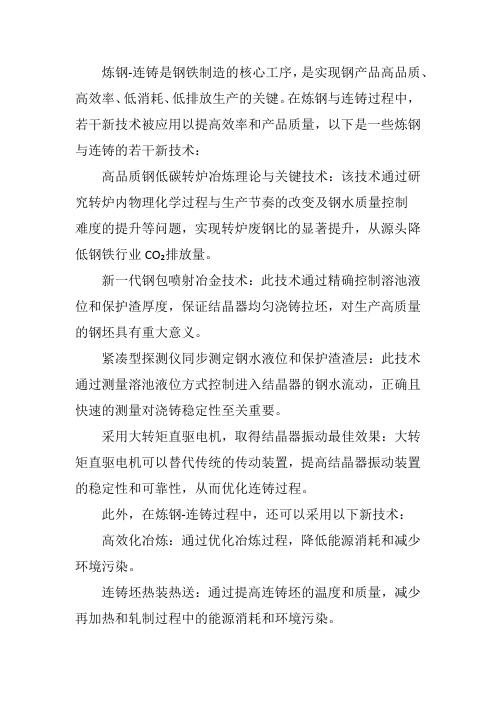
炼钢-连铸是钢铁制造的核心工序,是实现钢产品高品质、高效率、低消耗、低排放生产的关键。
在炼钢与连铸过程中,若干新技术被应用以提高效率和产品质量,以下是一些炼钢与连铸的若干新技术:高品质钢低碳转炉冶炼理论与关键技术:该技术通过研究转炉内物理化学过程与生产节奏的改变及钢水质量控制难度的提升等问题,实现转炉废钢比的显著提升,从源头降低钢铁行业CO₂排放量。
新一代钢包喷射冶金技术:此技术通过精确控制溶池液位和保护渣厚度,保证结晶器均匀浇铸拉坯,对生产高质量的钢坯具有重大意义。
紧凑型探测仪同步测定钢水液位和保护渣渣层:此技术通过测量溶池液位方式控制进入结晶器的钢水流动,正确且快速的测量对浇铸稳定性至关重要。
采用大转矩直驱电机,取得结晶器振动最佳效果:大转矩直驱电机可以替代传统的传动装置,提高结晶器振动装置的稳定性和可靠性,从而优化连铸过程。
此外,在炼钢-连铸过程中,还可以采用以下新技术:高效化冶炼:通过优化冶炼过程,降低能源消耗和减少环境污染。
连铸坯热装热送:通过提高连铸坯的温度和质量,减少再加热和轧制过程中的能源消耗和环境污染。
近终形化生产:通过采用先进的工艺和技术,生产更小断面的连铸坯,提高成材率和生产效率。
精确控制结晶器液面和保护渣厚度:通过精确控制结晶器液面和保护渣厚度,提高连铸坯的质量和稳定性。
电磁搅拌技术:通过采用电磁搅拌技术,改善连铸坯的凝固过程,提高产品质量和生产效率。
自动化的物流系统:通过采用先进的物流系统和技术,实现生产过程中物料的自动化运输和跟踪管理,提高生产效率和产品质量。
高效节能的轧制技术:通过采用高效节能的轧制技术,降低轧钢过程中的能源消耗和提高产品质量。
环保型轧制工艺:通过采用环保型轧制工艺和技术,减少轧钢过程中的环境污染和资源浪费。
集成化工艺控制技术:通过采用集成化工艺控制技术,将炼钢、连铸和轧制等工艺过程进行优化和控制,提高生产效率和产品质量。
这些新技术的应用可以显著提高炼钢-连铸生产的效率和产品质量,同时降低能源消耗和环境污染。
- 1、下载文档前请自行甄别文档内容的完整性,平台不提供额外的编辑、内容补充、找答案等附加服务。
- 2、"仅部分预览"的文档,不可在线预览部分如存在完整性等问题,可反馈申请退款(可完整预览的文档不适用该条件!)。
- 3、如文档侵犯您的权益,请联系客服反馈,我们会尽快为您处理(人工客服工作时间:9:00-18:30)。
溅渣护炉与复吹转炉的关系 对于采用溅渣护炉与复吹冶炼并存的转炉,随着溅渣后 炉龄的提高,炉底相应上涨,影响了底吹透气砖的工作。此时, 底吹透气砖的寿命约为3000 炉,这意味着从2000炉以后,复 吹效果大大减弱,甚至消失。 而溅渣护炉的炉龄远远大于 2000炉(现在达2万多炉),这就是一贯注重高纯净钢,普遍 采用复吹技术的日本不愿意采用溅渣护炉技术的原因。
1)铁水脱硫预处理的工艺方法
1
投掷法—将脱硫剂投入铁水中。 喷吹法—将脱硫剂喷入铁水中。 搅拌法(KR法)—将通过中空机械搅拌器向铁水内加入脱硫 剂,搅拌脱硫。
2
2)铁水脱硫剂的选择 元素的脱硫能力由高到低依次为:CaC2、NaO2、Mg、BaO、 CaO、MnO、MgO。 工业中常用的脱硫剂有:CaO系、CaO+CaC2系、CaC2、 CaO+Mg系、Mg系。几种脱硫剂的特点见表2。
溅渣护炉技术是利用高MgO 含量的炉渣,用高压氮气将炉渣喷 吹到转炉炉衬上,进而凝固到炉衬上,减缓炉衬砖的侵蚀速度,从 而提高转炉的炉龄。 技术要点
炉内合理的留渣量,通常控制在80~120kg/t 较合适; 炉渣特性控制: 终渣MgO≥8%为宜(特别对镁碳砖转炉); FeO12~18%为宜; 合适的炉渣粘度:易溅起、挂渣均匀。
烟气分析:
根据炉气变化情况动态计算脱碳速率和钢水C含量,特别在吹炼末期 炉内[C][O]反应趋于平衡后,动态计算、校正熔池温度,准确预报吹炼末 期熔池的碳、温度值,根据动态计算、预报的终点[C]、T并结合转炉烟气 变化曲线确定吹炼终点并自动提枪结束吹炼,实现转炉不倒炉直接出钢自 动化炼钢技术。
11
静态控制
依据初始条件、铁水重量、成分、温度、废钢重量、 分类)。要求的终点目标(终点温度,化学成分)以及参 考炉次的参考数据,计算出本炉次的氧耗量,确定各种副原料 的加入量和吹炼过程氧枪的高度。静态控制包括三个模型:氧 量模型,枪位模型和副原料模型。这样可基本命中终点的含碳 量和温度目标。
动态控制
当转炉供氧量达到氧耗量的85%左右时,降低吹氧流量,副枪 开始测温、定碳,并把测得的温度值及碳含量送入过程计算机。 过程计算机则计算出达到目标温度和目标碳含量所需补吹的氧 量及冷却剂加入量,并以副枪测到的实际值作为初值,以后每 吹4秒的氧气量,启动一次动态计算,预测熔池内温度和目标 碳含量。当温度和碳含量都进入目标范围时,发出停吹命令, 10 终点C和温度T的命中率可达80以上。
3)在氧化条件下,脱磷反应是阳极反应([P]→P5++5e) ,脱硫反应是阴极反应([S]+2e→S2-),所以铁水间同时脱 磷脱硫是可行的,只是需采用较大脱硫能力的熔剂。
4
铁水脱硅工艺技术 1)脱硅是脱磷的必要条件。换言之。铁水须先脱硅,然 后再同时脱磷脱硫,脱硅易于减少转炉石灰用量和渣量。 2)铁水脱硅可在高炉的铁水沟连续进行,也可在铁水罐 脱硅。
3
铁水脱磷工艺技术 1)铁水脱磷可在四种容器中进行:混铁车同时脱硫脱磷、 铁水罐同时脱硫脱磷、铁水包同时脱硫脱磷、转炉铁水脱磷。 2)铁水预处理脱磷反应温度低,热力学条件好,易于脱 磷。铁水中C、Si含量高,提高了铁水磷的活度,有利于脱磷。 由于铁水预处理脱磷具备良好的化学热力学条件,渣钢间 磷的分配系数是炼钢脱磷的5-10倍,因而渣量小,可以控制较 低的渣中FeO含量,脱磷成本低。
复吹转炉的经济效益
渣中含铁量降低2.5~5.0%; 金属收得率提高0.5~1.5%,残Mn 提高0.02%~0.06%; 磷含量降低0.002%。
6
石灰消耗降低3-10kg/t, 氧气消耗减少4NM3/t~6NM3/t; 提高炉龄,减少耐火材料消耗,综合经济效益约为6~15元/吨。 1.3 溅渣护炉技术
1.2 顶底复合吹炼技术
顶底复合吹炼法可分为两类 顶吹氧、底吹惰性气体法,全世界广泛采用此法。 顶底复合吹氧法,日本和欧洲多为采用。 工艺特点 反应速度快,热效率高,可实现炉内二次燃烧。
5
碳氧反应更趋平衡。当吹炼终点[C]=0.04复吹的终点[O]约 为900ppm,而进行复吹的炉次则为550ppm左右, 说明钢渣 的氧化性大为降低。吹炼终点残Mn明显提高,合金收得率明 显提高% 吹炼后期强化熔池搅拌,使钢-渣反应接近平衡,利于脱磷 脱硫反应的进行。 保持顶吹转炉成渣速度快和底吹转炉吹炼平稳的双重优点。 冶炼低碳钢(C=0.01-0.02%)时,避免了钢渣过氧化。
目前,炼钢工作者正努力开发底吹喷嘴长寿技术,要点 如下:
利用底吹喷嘴前蘑菇头的生长和控制技术,实现喷嘴长寿化; 炉役前期,利用粘渣、挂渣和溅渣迅速在喷嘴前端生成透气 蘑菇头,避免喷嘴烧损; 炉役中后期注意控制蘑菇头高度,防止堵塞; 对堵塞喷嘴采用复通技术。
9
1.4 转炉炼钢自动控制技术 转炉吹炼自动控制分为三个阶段:
7Байду номын сангаас
溅渣操作参数控制 氮气压力与流量与氧气压力和 流量相接近时,效果较 好。 枪位高度要根据企业实际摸索,可在1~2.5m之间变化。 溅渣时间通常为2.5~4min,枪位夹角多数企业的实践证明 12°比较理想。 溅渣护炉的经济效益 提高炉龄3~4 倍以上; 提高转炉利用系数2~4%; 降低炉衬砖消耗0.2~1.0kg/t。 降低补炉料消耗0.5~1.0kg/t; 减轻工人劳动强度; 投资回报率高。我国63座转炉测算投资回收期为1.3年。 溅 渣护炉的综合经济效益大约为2~10年/吨钢。
全自动控制
在静态、动态控制基础上,通过对炉渣的在线检测,控制喷溅, 并全面预报终点C、P、S、T,实现闭环控制。
2)脱碳速度加快、终点控制容易、氧效率提高、提高生产率。 3)锰的回收率提高,可进行锰矿熔融还原,降低成本。 4)转炉煤气成分稳定,煤气回收控制更加容易,以利实现转 炉负能炼钢、节能、降成本。 5)有利于扩大品种(高碳、高锰钢系列)。 铁水脱硫工艺技术 铁水脱硫法是指在铁水罐、铁水包、混铁车中进行脱硫。 在高炉、炉外精炼炉和转炉内每脱除1kg硫的成本分别是 铁水脱硫法的2.6倍、6.1倍、16.9倍。铁水脱硫法的成本低效 率高。