转炉炼钢脱氧技术的现发展状
炼钢转炉冶炼低碳钢脱氧合金化工艺优化
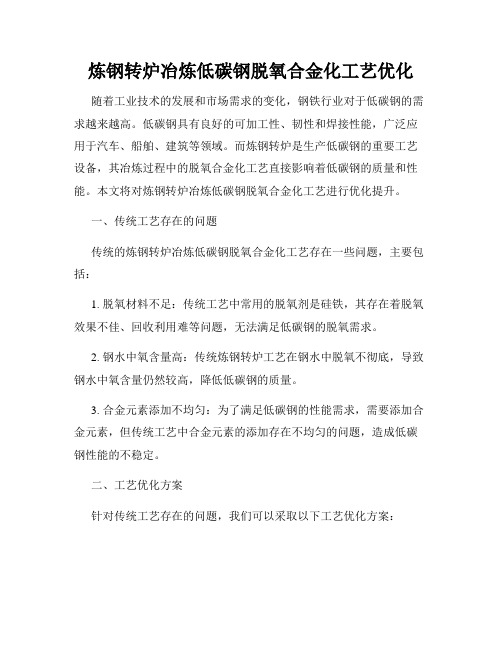
炼钢转炉冶炼低碳钢脱氧合金化工艺优化随着工业技术的发展和市场需求的变化,钢铁行业对于低碳钢的需求越来越高。
低碳钢具有良好的可加工性、韧性和焊接性能,广泛应用于汽车、船舶、建筑等领域。
而炼钢转炉是生产低碳钢的重要工艺设备,其冶炼过程中的脱氧合金化工艺直接影响着低碳钢的质量和性能。
本文将对炼钢转炉冶炼低碳钢脱氧合金化工艺进行优化提升。
一、传统工艺存在的问题传统的炼钢转炉冶炼低碳钢脱氧合金化工艺存在一些问题,主要包括:1. 脱氧材料不足:传统工艺中常用的脱氧剂是硅铁,其存在着脱氧效果不佳、回收利用难等问题,无法满足低碳钢的脱氧需求。
2. 钢水中氧含量高:传统炼钢转炉工艺在钢水中脱氧不彻底,导致钢水中氧含量仍然较高,降低低碳钢的质量。
3. 合金元素添加不均匀:为了满足低碳钢的性能需求,需要添加合金元素,但传统工艺中合金元素的添加存在不均匀的问题,造成低碳钢性能的不稳定。
二、工艺优化方案针对传统工艺存在的问题,我们可以采取以下工艺优化方案:1. 优化脱氧剂的选择:传统的硅铁脱氧剂可以通过其他脱氧剂进行替代,例如铝、锰等。
这些脱氧剂具有良好的脱氧效果和易回收利用的特点,可以提高低碳钢的质量。
2. 加强脱氧过程控制:通过提高脱氧剂的加入量和延长脱氧时间,确保炉料中的氧含量完全脱氧。
可以采用自动控制系统,实时监测钢水中氧含量,调整脱氧剂的加入量,实现钢水的有效脱氧。
3. 合金元素均匀添加:采用先进的合金元素添加技术,确保合金元素的均匀分布。
可以利用真空脱气设备将合金元素均匀加入钢水中,或者采用复合脱氧剂,使脱氧剂和合金元素同时添加,提高低碳钢的合金化效果。
4. 优化工艺参数:通过对炉温、转炉容量、吹氧时间等工艺参数的优化调整,提高低碳钢的冶炼效果。
可以利用计算机模拟技术对工艺参数进行优化设计,以实现低碳钢冶炼过程的最佳效果。
三、优化方案的效果及推广通过实施上述工艺优化方案,可以显著提高炼钢转炉冶炼低碳钢脱氧合金化的效果,进一步提升低碳钢的质量和性能。
试析转炉炼钢技术的发展与展望

试析转炉炼钢技术的发展与展望作者:黄勐来源:《名城绘》2020年第03期摘要:在我国占据主要地位的钢铁生产技术依然是转炉炼钢,这符合我国的国情,即废钢资源紧缺和巨大的人口红利,电费高昂等特点。
诸多因素促使之下,使得转炉炼钢技术在我国进一步发展。
本文主要分析探讨了转炉炼钢技术的发展与展望情况,以供同业者参考。
关键词:转炉炼钢技术;发展;展望转炉是主要用于生产碳钢、合金钢、铜、镍等金属材料的冶炼设备。
其主要原料有铁水、废钢和铁合金等,炼钢过程中的热量来源是靠铁液本身物理热以及铁液各组分间化学反应产生的热量,无需外界附加能源。
我国使用最为普遍的炼钢设备为碱性氧气顶吹和顶底复吹转炉,因其具有成本低、单炉产量高、投资少、生产速度快等优点,被我国钢铁企业所广泛应用。
1我国转炉炼钢技术的应用1.1洁净钢新流程的应用在21世纪的发展形势下,我国钢铁工业中对洁净钢的生产已经成为重点,而洁净钢的生产技术的发展目标就是采取最经济的手段来使生产效率大幅提高,从而形成大规模的生产。
当前我国已经创新出了新的炼钢流程来对洁净钢进行生产,并且已经在部分炼钢企业中得到了初步的应用。
洁净钢新流程能够对钢中的杂质进行有效的“三脱”处理,使其处理比例达到更高,并且转炉日产数也增加了将近一倍,极大提高了洁净钢的生产效率,相比于传统的洁净钢流程,生产成本也要低的多。
1.2转炉脱磷炼钢技术的应用在转炉炼钢生产中,常用脱磷技术方法包括结合铁水三脱预处理和转炉法、转炉双联法、双渣法。
其中双渣法是指操作一台转炉,实行2次造渣,转炉双联法是指操作2台转炉,一台脱磷,完成脱磷之后在另一台脱碳。
大型钢铁厂通过自主研发、应用脱磷脱碳新工艺,促使每一台转炉都可以脱磷、脱碳,应用双联技术炼钢。
一些炼钢厂由于缺乏铁水脱磷预处理的条件与设备,应用双渣法炼钢,但出钢量不高,且磷含量有较大变化,氧气含量较高。
通过不断优化转炉脱磷炼钢技术,提高出钢量与含碳量,保证出钢质量,提高转炉炼钢技术水平。
对炼钢生产中转炉炼钢脱氧工艺的分析

对炼钢生产中转炉炼钢脱氧工艺的分析摘要:随着我国经济的发展和社会的进步,我国的各行各业均均取得了令人瞩目的成就。
在目前的炼钢过程当中,转炉炼钢脱氧方式的应用越来越广泛,作为炼钢过程当中一项重要的内容,钢液脱氧效果控制能够最大限度地保证整个钢产品的质量。
本文主要是分析了炼钢生产中转炉炼钢脱氧工艺,以此为炼钢行业的发展提供些许的借鉴。
关键词:炼钢生产转炉炼钢脱氧工艺分析引言脱氧合金化是在炼钢生产中转炉炼钢过程当中非常重要的一个过程,其能够直接影响到钢产品的质量、产能以及生产成本等重要环节。
同时,脱氧合金化也是冶炼过程最后的一个步骤,通常来讲,脱氧与合金化过程是同步进行的。
一旦出现操作失误的情况,不仅对合金回收率会造成负面影响,还会提高精炼处理的难度,致使钢水混入较多的杂物,影响其可浇性,从而对铸坯的质量造成不利影响,更为严重的情况会产生废品甚至是铸机断浇。
所以,炼钢生产中转炉炼钢脱氧工艺水平的提升是炼钢生产最为关键的环节之一。
1转炉炼钢相关概述1.1转炉炼钢的原理转炉是转炉炼钢操作最为主要的设备。
其形状与鸭梨类似,内部的炉壁是由耐火砖制成,能够实现360°全方位任何角度旋转。
铁水和废钢是炼钢所需要的原材料,整个吹炼过程中的转炉炼钢是氧化反应,脱碳、脱磷、脱硫、脱氧去除有害气体和杂质,提高温度和调整成分是炼钢最基本的任务。
相关操作人员根据铁水的温度和成分和热平衡公式,再加上白灰和轻烧公式等促使炼钢渣的碱度适中,同时有效地去除氧化镁中的碳磷硫等杂物,并且确保在冶炼过程完成之后使得钢温度和成分符合要求。
吹炼过程所产出的钢水含氧量很难达到钢种质量的要求,主要是由于顶吹氧气与铁水、废钢等发生了氧化反应。
因此,在钢产出的过程中必须要加之脱氧工艺,以确保其能够达到钢种质量的要求。
1.2转炉炼钢中氧的产生及其危害钢液当中的氧气主要是以包括非金属杂物和溶解氧气两种形式存在的,而氧气主要产生自炼钢的原材料和吹氧炼钢的工序。
浅析炼钢生产的转炉炼钢脱氧工艺
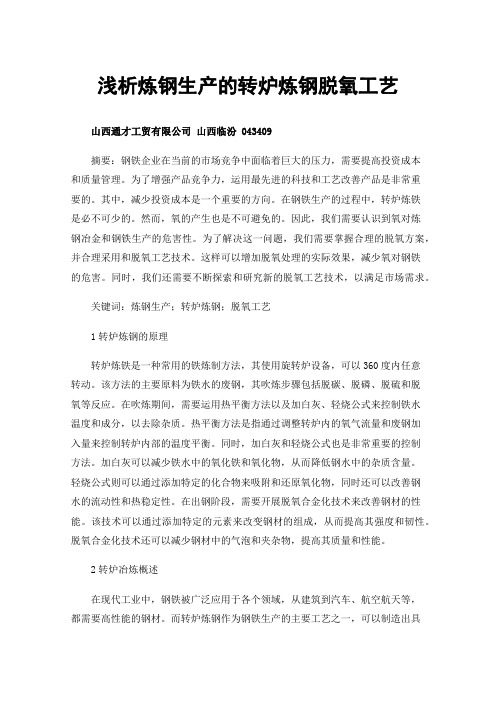
浅析炼钢生产的转炉炼钢脱氧工艺山西通才工贸有限公司山西临汾 043409摘要:钢铁企业在当前的市场竞争中面临着巨大的压力,需要提高投资成本和质量管理。
为了增强产品竞争力,运用最先进的科技和工艺改善产品是非常重要的。
其中,减少投资成本是一个重要的方向。
在钢铁生产的过程中,转炉炼铁是必不可少的。
然而,氧的产生也是不可避免的。
因此,我们需要认识到氧对炼钢冶金和钢铁生产的危害性。
为了解决这一问题,我们需要掌握合理的脱氧方案,并合理采用和脱氧工艺技术。
这样可以增加脱氧处理的实际效果,减少氧对钢铁的危害。
同时,我们还需要不断探索和研究新的脱氧工艺技术,以满足市场需求。
关键词:炼钢生产;转炉炼钢;脱氧工艺1转炉炼钢的原理转炉炼铁是一种常用的铁炼制方法,其使用旋转炉设备,可以360度内任意转动。
该方法的主要原料为铁水的废钢,其吹炼步骤包括脱碳、脱磷、脱硫和脱氧等反应。
在吹炼期间,需要运用热平衡方法以及加白灰、轻烧公式来控制铁水温度和成分,以去除杂质。
热平衡方法是指通过调整转炉内的氧气流量和废钢加入量来控制转炉内部的温度平衡。
同时,加白灰和轻烧公式也是非常重要的控制方法。
加白灰可以减少铁水中的氧化铁和氧化物,从而降低钢水中的杂质含量。
轻烧公式则可以通过添加特定的化合物来吸附和还原氧化物,同时还可以改善钢水的流动性和热稳定性。
在出钢阶段,需要开展脱氧合金化技术来改善钢材的性能。
该技术可以通过添加特定的元素来改变钢材的组成,从而提高其强度和韧性。
脱氧合金化技术还可以减少钢材中的气泡和夹杂物,提高其质量和性能。
2转炉冶炼概述在现代工业中,钢铁被广泛应用于各个领域,从建筑到汽车、航空航天等,都需要高性能的钢材。
而转炉炼钢作为钢铁生产的主要工艺之一,可以制造出具备优良物理性能和化学性能的高性能钢铁,备受业界青睐。
转炉炼钢通过氧化生铁中的碳,制造出高性能钢铁。
其中,碳含量在2.1%范围内可以产生钢铁。
生钢铁中的铁元素和碳元素形成过饱和的固溶体,提高铁、碳含量可以提升钢的韧性和可塑性。
转炉氧枪发展现状

转炉氧枪发展现状转炉氧枪是冶金行业中一种重要的设备,用于向转炉内部喷射氧气,以提高钢水的温度和氧化反应速度,从而实现高效的炼钢过程。
近年来,转炉氧枪在设计和技术上取得了很大的进展,提高了炼钢过程的效率和质量。
在转炉氧枪的设计方面,目前最常见的设计是雾化型氧枪。
这种氧枪通过喷嘴将氧气雾化成细小的气泡,然后喷射到转炉内部。
雾化型氧枪具有喷射稳定、浸润性好、能量利用率高的特点,可以有效地提高转炉内部的温度和氧化速度。
同时,雾化型氧枪还可以根据钢水的质量要求进行自动控制,使得炼钢过程更加智能化。
此外,随着数控技术的发展,目前已经出现了自动化控制的转炉氧枪。
这些自动化控制的氧枪利用传感器感知转炉内部的温度、压力和氧含量等参数,通过计算机控制系统实现对氧枪的操作和调节。
这种自动化控制的转炉氧枪具有响应速度快、控制精度高的特点,能够更好地适应炼钢过程的变化。
另外,为了提高炼钢的能源利用率,目前一些新型的转炉氧枪开始采用燃气雾化技术。
与传统的氧气雾化相比,燃气雾化技术可以将氧气与燃料共同喷射,实现钢水的燃烧和加热。
这种新型的转炉氧枪不仅可以节约能源和氧气,还可以减少炉内的废气排放。
此外,为了改善转炉氧枪的工作环境和使用寿命,目前一些转炉氧枪开始采用耐高温材料和防腐蚀涂层。
这些耐高温材料可以在高温环境下保持良好的强度和稳定性,而防腐蚀涂层可以防止炉内的氧化物和腐蚀性介质对氧枪的侵蚀。
综上所述,转炉氧枪在设计和技术上的不断进步,使得炼钢过程更加高效和智能化。
通过采用雾化型氧枪、自动化控制、燃气雾化技术和耐高温材料等新技术,转炉氧枪能够更好地实现钢水的加热和氧化,从而提高钢水的温度和氧化速度,改善炼钢过程的质量和效率。
随着科技的不断发展,相信转炉氧枪在未来会有更大的突破和应用。
探讨炼钢生产中转炉炼钢脱氧工艺
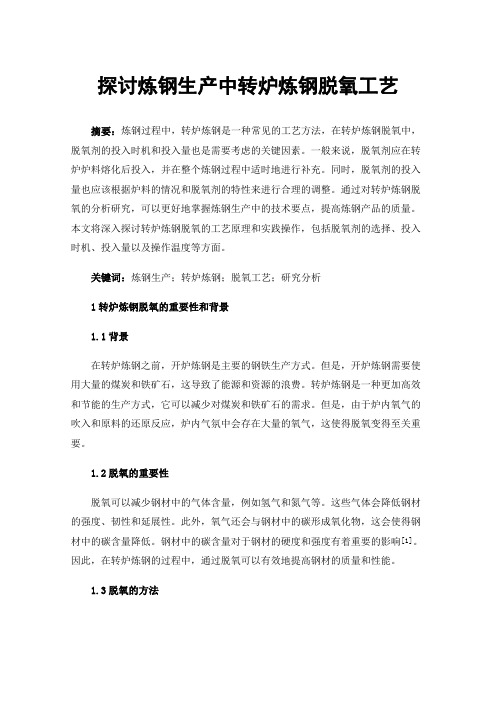
探讨炼钢生产中转炉炼钢脱氧工艺摘要:炼钢过程中,转炉炼钢是一种常见的工艺方法,在转炉炼钢脱氧中,脱氧剂的投入时机和投入量也是需要考虑的关键因素。
一般来说,脱氧剂应在转炉炉料熔化后投入,并在整个炼钢过程中适时地进行补充。
同时,脱氧剂的投入量也应该根据炉料的情况和脱氧剂的特性来进行合理的调整。
通过对转炉炼钢脱氧的分析研究,可以更好地掌握炼钢生产中的技术要点,提高炼钢产品的质量。
本文将深入探讨转炉炼钢脱氧的工艺原理和实践操作,包括脱氧剂的选择、投入时机、投入量以及操作温度等方面。
关键词:炼钢生产;转炉炼钢;脱氧工艺;研究分析1转炉炼钢脱氧的重要性和背景1.1背景在转炉炼钢之前,开炉炼钢是主要的钢铁生产方式。
但是,开炉炼钢需要使用大量的煤炭和铁矿石,这导致了能源和资源的浪费。
转炉炼钢是一种更加高效和节能的生产方式,它可以减少对煤炭和铁矿石的需求。
但是,由于炉内氧气的吹入和原料的还原反应,炉内气氛中会存在大量的氧气,这使得脱氧变得至关重要。
1.2脱氧的重要性脱氧可以减少钢材中的气体含量,例如氢气和氮气等。
这些气体会降低钢材的强度、韧性和延展性。
此外,氧气还会与钢材中的碳形成氧化物,这会使得钢材中的碳含量降低。
钢材中的碳含量对于钢材的硬度和强度有着重要的影响[1]。
因此,在转炉炼钢的过程中,通过脱氧可以有效地提高钢材的质量和性能。
1.3脱氧的方法转炉炼钢中有两种主要的脱氧方法,即硅脱氧和铝脱氧。
硅脱氧是最常用的方法,它通过在炉内加入硅来将氧气与硅反应,从而减少炉内氧气含量。
硅脱氧可以有效地减少氧气含量,但同时也会增加钢材中硅的含量。
铝脱氧则是一种更加高效的脱氧方法,它可以将氧气与铝反应,从而减少氧气含量,同时不会增加钢材中其他元素的含量。
铝脱氧可以生产出更加纯净的钢材。
2氧化铝脱氧法在转炉炼钢中的应用2.1背景在传统的转炉炼钢过程中,气氛中存在大量的氧气,这会使钢中存在过多的气体,如氮气、氧气和氢气等。
这些气体会导致钢中的气孔和夹杂物增多,从而降低钢的质量和性能。
转炉冶炼低碳钢脱氧工艺的改进
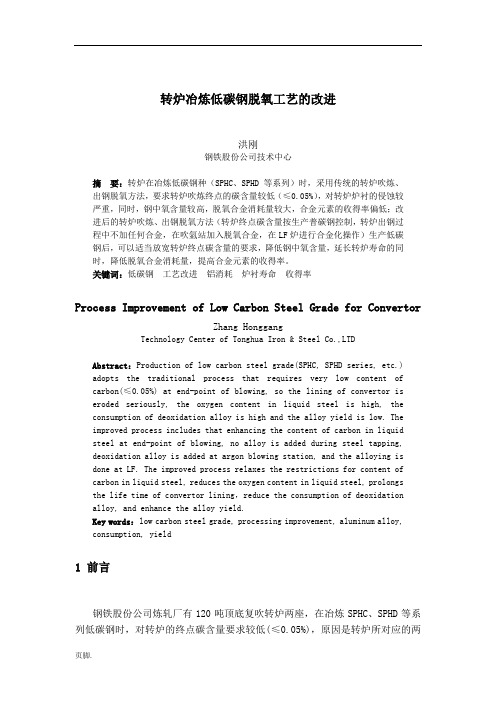
转炉冶炼低碳钢脱氧工艺的改进洪刚钢铁股份公司技术中心摘要:转炉在冶炼低碳钢种(SPHC、SPHD等系列)时,采用传统的转炉吹炼、出钢脱氧方法,要求转炉吹炼终点的碳含量较低(≤0.05%),对转炉炉衬的侵蚀较严重,同时,钢中氧含量较高,脱氧合金消耗量较大,合金元素的收得率偏低;改进后的转炉吹炼、出钢脱氧方法(转炉终点碳含量按生产普碳钢控制,转炉出钢过程中不加任何合金,在吹氩站加入脱氧合金,在LF炉进行合金化操作)生产低碳钢后,可以适当放宽转炉终点碳含量的要求,降低钢中氧含量,延长转炉寿命的同时,降低脱氧合金消耗量,提高合金元素的收得率。
关键词:低碳钢工艺改进铝消耗炉衬寿命收得率Process Improvement of Low Carbon Steel Grade for ConvertorZhang HonggangTechnology Center of Tonghua Iron & Steel Co.,LTDAbstract:Production of low carbon steel grade(SPHC, SPHD series, etc.)adopts the traditional process that requires very low content ofcarbon(≤0.05%) at end-point of blowing, so the lining of convertor iseroded seriously, the oxygen content in liquid steel is high, theconsumption of deoxidation alloy is high and the alloy yield is low. Theimproved process includes that enhancing the content of carbon in liquidsteel at end-point of blowing, no alloy is added during steel tapping,deoxidation alloy is added at argon blowing station, and the alloying isdone at LF. The improved process relaxes the restrictions for content ofcarbon in liquid steel, reduces the oxygen content in liquid steel, prolongsthe life time of convertor lining,reduce the consumption of deoxidationalloy, and enhance the alloy yield.Key words:low carbon steel grade, processing improvement, aluminum alloy,consumption, yield1 前言钢铁股份公司炼轧厂有120吨顶底复吹转炉两座,在冶炼SPHC、SPHD等系列低碳钢时,对转炉的终点碳含量要求较低(≤0.05%),原因是转炉所对应的两台薄板坯连铸机(意大利达涅利公司的FTSC型)对钢水的质量要求较严格,考虑精炼处理过程中的增碳及尽量避开钢种成份的包晶区需要成品钢水的碳含量≤0.06%,这使转炉终点的氧含量偏高,尤其是在转炉炉役的后期,转炉的复吹效果变差,终点的碳氧浓度积较高,一般情况下转炉终点的氧含量要达到800PPm 以上,对转炉炉衬的侵蚀较严重,而且脱氧及合金化所消耗的合金成本较高,我厂的此类钢种产量比例约占薄板坯产量的30%左右,每月约5万吨,因此,需要对现有的冶炼及脱氧合金化工艺进行优化,以降低生产成本。
我国转炉复吹技术的发展和现状

我国转炉复吹技术的发展和现状
转炉复吹技术是指在钢水净化过程中,在转炉内部进行二次喷吹氧气,以增强钢水中的氧化反应,从而提高钢水净化效果的一种技术。
我国的转炉复吹技术始于上世纪80年代,随着技术的发展,该技术已经得到了广泛应用。
目前,我国大多数钢厂都采用了转炉复吹技术,其中大型钢铁企业的复吹技术水平已达到国际先进水平。
转炉复吹技术的发展与现状主要有以下几点:
1. 技术改进:随着科技的不断进步,转炉复吹技术得到了不断改进和完善,特别是在喷吹氧气的位置、角度、流量等方面做出了不少创新,从而提高了钢水净化效果。
2. 技术水平提高:我国大多数钢厂都拥有较为先进的复吹技术设备,能够更好地掌握复吹技术,提高钢水净化效率,降低生产成本,提高钢铁产品质量。
3. 实现绿色环保:转炉复吹技术可有效净化钢水中的杂质,减少废气排放,达到了绿色环保的效果。
我国的钢铁企业也在积极推广清洁生产,不断提高环保水平。
总之,转炉复吹技术在我国的发展和应用已经取得了显著成果,随着科技的不断进步和环保要求的不断提高,该技术将会得到更广泛的应用。
- 1、下载文档前请自行甄别文档内容的完整性,平台不提供额外的编辑、内容补充、找答案等附加服务。
- 2、"仅部分预览"的文档,不可在线预览部分如存在完整性等问题,可反馈申请退款(可完整预览的文档不适用该条件!)。
- 3、如文档侵犯您的权益,请联系客服反馈,我们会尽快为您处理(人工客服工作时间:9:00-18:30)。
转炉炼钢脱氧技术的现发展状摘要:介绍了沉淀脱氧、扩散脱氧、真空脱氧和复合脱氧法对钢水脱氧的影响以及各种脱氧工艺效果之间的比较。
关键词:脱氧工艺,效果分析The Present Situation Of BOF Purging ProcessAbstract:The present paper introduces settling purging and spread purging and vacuum purging and composite purging and the comparison to all kinds of purging process.Key word:purging process;effect analyse前言当钢液中大量元素,特别是碳被氧化到较低浓度时,钢液内就存在着较高量的氧(ω[ O ]=0.02%~0.08%)。
这种饱含氧的钢液在冷凝固时,不仅在晶界上析出FeO及FeO-FeS,使钢的塑性降低及发生热脆,而且其中的[ C ]及[ O ]将继续反应,甚至强烈反应。
因为其内的氧在冷却的钢液中溶解度减小,出现偏析时,毗连于凝固层的母体钢液的含氧量增高,超过了ω[ C ]·ω[ O ]平衡值,于是CO 气泡形成,使钢锭饱含气泡,组织疏松,质量下降。
因此,只有在控制沸腾(沸腾钢)或不出现沸腾(镇静钢)时,才可能获得成分及组织合格的优质钢锭或钢坯。
为此,对于沸腾钢,ω[ O ]需降到0.025%~0.030%,对于镇静钢,ω[ O ]应小于0.005%。
【1】2 脱氧原理2.1 钢液的脱氧不管是哪种炼钢方法,都需要在熔池中供氧去除C、Si、Mn、P等杂质元素,氧化精炼结束后,钢液达到了一定成分和温度。
如果钢水不进行脱氧,连铸胚就得不到正确的凝固组织结构。
钢中氧含量高,还会产生皮下气泡、疏松等缺陷,并加剧硫的危害作用。
而且还会生成过多的氧化物杂质,降低钢的塑性、冲击韧性等力学性能。
因此,必须在出钢或浇注过程中,加脱氧剂适当减少钢液含氧量,除去钢中的过剩氧。
2.2 脱氧剂和脱氧能力炼钢常用的脱氧元素有:硅、锰和铝。
硅:硅的脱氧生成物位SiO2或硅酸铁(FeO·SiO2)。
硅脱氧反应式为:[ Si ] + 2[ O ] = SiO2∆G=—576440+218.2T J/molK=在ω[ O ] [Si]<2%,·值接近1,于是可得ω[Si]%·ω≈a Si ·炉渣碱度越高,SiO 2的活度越小,残余量越低,硅的脱氧效果越好。
各种牌号的Fe-Si 是常用的脱氧剂锰:锰是弱脱氧剂,常用于沸腾钢脱氧,其脱氧产物并不是纯的MnO ,而是MnO 与FeO 的熔体。
锰脱氧反应式可表示为:[Mn]+[O] =(MnO)(l) ∆G θ=—244300+107.6T J/mol[Fe]+[O] =(FeO)[Mn]+ (FeO)= (MnO)+Fe (l)实验测得上述反应的平衡常数: lglg =k MnO ][%)(Mn N N W FeO l MnO ∙=T 6440—2.95 k Mn lg =a Mn N o l MnO W ∙][%)(lg =T12760—5.62 当金属含锰增加时,与之平衡的脱氧产物中的N MnO 也是随之增大。
当N MnO 增大到一定的浓度时,脱氧产物开始有固态的FeO ·MnO 出现铝:铝是强脱氧剂,常用于镇静钢的终脱氧,铝脱氧反应为:2[Al]+3[O] =Al2O3 ∆G θ=—1242400+394.93T J /mol复合脱氧剂:使用两种或多种脱氧元素制成的复合脱氧剂,例如硅锰、硅钙、硅锰铝等复合脱氧剂,复合脱氧剂有以下优点:(1)可以提高脱氧元素的脱氧能力;(2)有利于形成液态的脱氧产物,便于产物的分离和上浮;(3)有利于提高易挥发元素在钢中的溶解度,减少元素的损失,提高脱氧元素的脱氧效率。
【2】3 三种不同脱氧工艺比较3.1 沉淀脱氧沉淀脱氧法是指将脱氧剂加到钢液中,它直接与钢液中的氧反应生成稳定的氧化物,即直接脱氧。
沉淀脱氧效率高,操作简单,成本低,对冶炼时间无影响,但沉淀脱氧的脱氧程度取决于脱氧剂能力和脱氧产物的排除条件。
向钢液中加人与氧的亲和力比铁大的元素,使溶解于钢液中的氧化铁还原,用公式表示如下:x[ M ] + y[ Fe0 ] = ( M x O y ) + yFe这种脱氧法的缺点是随着氧化铁的还原,在钢液中产生了新的氧化物Fe x0y,因此采用这种方法脱氧时,必须创造夹杂物上浮的良好条件。
【3】图3.1成品钢锭氧含量的趋势图3.2 扩散脱氧扩散脱氧是根据氧分定律建立起来的,一般用于电炉还原期,或钢液的炉外精炼。
随着钢液中氧向炉渣中扩散,炉渣中(FeO)逐渐增多,为了使(FeO)保持在低水平,需在渣中加脱氧剂来还原渣中的(FeO),这样可以保证钢液中的氧不断向渣中扩散。
扩散脱氧的产物存在于熔渣中,这样有利于提高钢液个纯洁度,但扩散脱氧的速度慢,时间长,可以通过吹氩搅拌或钢渣混冲等方式加速脱氧进程。
另外,进行扩散脱氧操作前,需换新榨,以防止回磷。
将脱氧剂加入到炉渣中,直接降低炉渣中的氧化铁含量,借分配定律的作用使钢液中的氧化铁逐渐转移到炉渣中来。
平衡状态下,氧在炉渣和钢液之间的分配服从分配定律为:L FeO=,即[%FeO]= L FeO×a(FeO)由上式可见,如人为降低(Fe0),则钢液中的[Fe0]就会扩散进人炉渣。
因此,决定熔池中氧含量的主要因素不是钢液中的含碳量,而是炉渣中的氧化铁含量。
将含氧化铁较低的合成渣置于盛钢桶内与钢液混合,也能得到相同效果。
【4】表3.2 各种钢扩散脱氧工艺优化前后的技术指标对比从表2可以看出,经扩散脱氧工艺优化后,各钢种Si、Mn等成分的收得率提高,Als 损失量降低了0.005%以上,脱氧合金成本大大降低,平均达到3元/t钢以上。
按年产420万t钢计算,年可创效益1 000万元以上。
3.3 真空脱氧真空脱氧法是将钢包内钢液置于真空条件下,通过抽真空打破原有的碳氧平衡,促使碳与氧的反应,达到通过钢中碳除去氧的目的。
此法的优点为脱氧产物是CO,不会污染钢液;CO气泡具有去气和吸附夹杂的作用;CO气泡逸出时,可起到搅拌钢液的作用。
在根本改善钢的质量方面,应用真空脱氧有很大意义,这是因为采用其他脱氧方法不可能完全去除钢中的夹杂物。
真空碳脱氧服从以下热力学规律:[C] + {O} = COlgK=lg==2.003[%O] =如果根据上式近似评价碳在1873 K下的脱氧能力,则当P CO =10-3 Pa时,碳就具有比铝还强的脱氧能力。
前苏联的研究表明,1873 K时,P CO =0.006687 Pa,[O] =(18.2±2.07)×10-5%,[C]×[O] =1.3×10-10。
在真空碳脱氧的过程中吹入100~200 L/min的氩气进行搅拌,为产生CO气泡创造了条件,真空度达0.5乇时解除真空,可以达到钢中游离氧含量100×10-6以下。
初炼炉出钢不加合金及预脱氧剂,钢水中游离氧在500×10-6左右,大包温度在1580℃以上直接入真空位,根据钢液碳含量增碳至0.13%,然后进行真空碳脱氧处理约8 min,真空度达到0.5乇后解除真空,取样吊至LF炉精炼,根据钢种不同直接加入相应量的硅锰合金,后步工序同正常炉次操作。
每炉钢(120 t/炉)降低脱氧剂及石灰消耗量,见下表:【5】表3.3.1 每炉钢降低脱氧剂及石灰消耗情况表3.3.2 每炉钢增加的成本从表3.3.1和表3.3.2可以看出,采用真空碳脱氧工艺后,非过氧化炉次每炉钢可降低成本2229元,对过氧化炉次,由于铝线用量比此工艺多消耗300 m以上,故每炉钢成本可以降低3000元左右。
3.4 复合脱氧依据钢的电弧炉冶炼原理,经过对铁合金炉渣的筛选再处理,采用“SC复合脱氧剂”,它是铁合金生产中的副产品(炉渣),主要成分正是电石渣所需的成分CaC2。
SC复合脱氧剂的化学成分见表3.4.1。
表3.4.1 SC复合脱氧剂的化学成分(%)其中SiCa脱氧反应的自由能变化远低于C的氧化反应:SiCa+3FeO=3Fe+CaSiO3△G1873K=﹣1032.9 KJ 这样,就可以使用复合脱氧剂的方法解决难以获得电石渣或类似电石渣脱氧剂的问题。
表3.4.2 SC复合脱氧剂与Si-Fe-C脱氧剂脱氧效果比较表3.4.2是在冶炼12Mn和ZG230—450钢中使用SC复合脱氧剂和Si-Fe-C粉两种脱氧剂的脱氧效果比较。
可以看出,与Si-Fe-C相比,SC脱氧剂不仅有横好的脱氧效果,而且脱氧速度快、脱氧率高,每炉可缩短冶炼时间。
【6】4 三种脱氧工艺的对比沉淀脱氧法,是目前应用得最广泛的方法。
相当于扩散脱氧和真空扩散法,设备简单,工艺流程也不复杂。
图4 3种脱氧方法的特点对于扩散脱氧法,由于脱氧剂加在渣层内,脱氧反应在渣钢液界面进行,脱氧产物不进入钢液中,就不会沾污钢液,因而在原则上说是冶炼优质钢最好的脱氧方法。
真空脱氧法,对于机器设备和操作精良有较高的要求,可以得到脱氧效果较好的钢液。
复合脱氧法,相对于单一脱氧剂而言,效率有很大的提升。
5 总结通过比较沉淀脱氧、扩散脱氧、真空脱氧以及复合脱氧法,可见不同的工艺各有其优缺点。
应当在生产实践中,有机的结合这4种脱氧工艺。
有效的将复合脱氧剂应用到沉淀、扩散、真空脱氧工艺中。
这样可以大大减少脱氧剂的使用量,同时能加快脱氧速度,降低工人的劳动强度。
结合各种脱氧工艺生产,还可以减低电能消耗,提升钢液质量。
参考文献:【1】钢铁冶金原理(第三版),黄希古,主编,冶金工业出版社.【2】现代冶金学(钢铁冶金卷),朱苗勇,主编,钢铁工业出版社.【3】沉淀脱氧和柔性吹氩搅拌对于提高钢锭质量的分析,姚国平,太原科技,2008.12.【4】炼钢厂150t转炉出钢过程脱氧工艺研究,范启兴,梅山科技,2008增刊(1).【5】精炼过程中的真空碳脱氧试验,李慧勇,宽厚板,2009.8.【6】复合脱氧粉剂在电炉炼钢扩散脱氧中的应用,吉仁龙,铁合金,1996.7.。