外文翻译低热硅酸盐水泥混凝土的抗裂性能
混凝土中硅酸盐水泥的特性及应用

混凝土中硅酸盐水泥的特性及应用一、硅酸盐水泥的概述硅酸盐水泥(Silicate cement),又称水玻璃水泥、钠玻璃水泥、硅酸盐水泥、无机胶凝材料,是一种以硅酸盐为主要成分的水泥。
硅酸盐水泥是一种由硅酸盐水玻璃和硬化剂(如硫酸钠、磷酸钠、铝酸钠等)组成的胶凝材料。
硅酸盐水泥分为无机硅酸盐水泥和有机硅酸盐水泥两大类,其中无机硅酸盐水泥又分为钠硅酸盐水泥、钾硅酸盐水泥、铝硅酸盐水泥、铁硅酸盐水泥、钙硅酸盐水泥等。
二、硅酸盐水泥的特点1. 硬度高:硅酸盐水泥具有极高的硬度,是所有水泥中硬度最高的,因此在建筑中常用于制作高强度的地基、混凝土和砌体等。
2. 耐腐蚀:硅酸盐水泥具有很好的耐腐蚀性能,可以抵抗酸、碱等腐蚀物质,因此在化工、冶金等行业中应用广泛。
3. 抗渗性好:硅酸盐水泥中含有大量的硅酸盐,具有良好的抗渗性能,可以有效地防止水的渗透。
4. 抗压强度高:硅酸盐水泥的抗压强度很高,通常比普通水泥高出20%以上,因此在建筑中常用于制作各种高强度的混凝土和砌体等。
三、硅酸盐水泥的应用1. 混凝土制作:硅酸盐水泥在混凝土制作中有着广泛的应用,可以制作高强度的混凝土,因此在高层建筑、桥梁、隧道等建筑中应用较多。
2. 砌体制作:硅酸盐水泥可以制作高强度、高密度的砌体,因此在建筑墙体、隔墙等方面应用较多。
3. 防水涂料:硅酸盐水泥可以制作防水涂料,具有良好的抗渗性能,可以有效地防止水的渗透。
4. 耐酸碱砖:硅酸盐水泥可以制作耐酸碱砖,在化工、冶金等行业中应用广泛。
5. 硬化剂:硅酸盐水泥可以作为硬化剂使用,可以使混凝土、石材等材料硬化、增强强度。
四、硅酸盐水泥的生产工艺硅酸盐水泥的生产工艺主要包括原料准备、混合、成型、养护和检验等五个步骤。
1. 原料准备:硅酸盐水泥的主要原料是硅酸盐水玻璃和硬化剂。
硅酸盐水玻璃可以通过白砖石、石英石等矿物质熔炼得到,硬化剂可以选择硫酸钠、磷酸钠、铝酸钠等。
2. 混合:将硅酸盐水玻璃和硬化剂按一定比例混合,形成硅酸盐水泥浆。
外文翻译--混凝土结构使用的可靠性

Electronic Journal of Structural Engineering, 1 ( 2001)15 Shrinkage, Cracking and Deflection-the Serviceability of Concrete Structures R.I. GilbertProfessor and Head, School of Civil and Environmental EngineeringThe University of New South Wales, Sydney, NSW, 2052Email: ******************.auABSTRACT This paper addresses the effects of shrinkage on the serviceability of concrete structures. It outlines why shrinkage is important, its major influence on the final extent of cracking and the magnitude of deflection in structures, and what to do about it in design. A model is presented for predicting the shrinkage strain in normal and high strength concrete and the time-dependent behaviour of plain concrete and reinforced concrete, with and without external restraints, is explained. Analytical procedures are described for estimating the final width and spacing of both flexural cracks and direct tension cracks and a simplified procedure is presented for including the effects of shrinkage when calculating long-term deflection. The paper also contains an overview of the considerations currently being made by the working group established by Standards Australia to revise the serviceability provisions of AS3600-1994, particularly those clauses related to shrinkage.KEYWORDSCreep; Cracking; Deflection; Reinforced concrete; Serviceability; Shrinkage.1. IntroductionFor a concrete structure to be serviceable, cracking must be controlled and deflections must not be excessive. It must also not vibrate excessively. Concrete shrinkage plays a major role in each of these aspects of the service load behaviour of concrete structures.The design for serviceability is possibility the most difficult and least well understood aspect of the design of concrete structures. Service load behaviour depends primarily on the properties of the concrete and these are often not known reliably at the design stage. Moreover, concrete behaves in a non-linear and inelastic manner at service loads. The non-linear behaviour that complicates serviceability calculations is due to cracking, tension stiffening, creep, and shrinkage. Of these, shrinkage is the most problematic. Restraint to shrinkage causes time-dependent cracking and gradually reduces the beneficial effects of tension stiffening. It results in a gradual widening of existing cracks and, in flexural members, a significant increase in deflections with time.The control of cracking in a reinforced or prestressed concrete structure is usually achieved by limiting the stress increment in the bonded reinforcement to some appropriately low value and ensuring that the bonded reinforcement is suitably distributed. Many codes of practice specify maximum steel stress increments after cracking and maximum spacing requirements for the bonded reinforcement. However, few existing code procedures, if any, account adequately for the gradual increase in existing crack widths with time, due primarily to shrinkage, or the time-dependent development of new cracks resulting from tensile stresses caused by restraint to shrinkage.For deflection control, the structural designer should select maximum deflection limits that are appropriate to the structure and its intended use. The calculated deflection (or camber) must not exceed these limits. Codes of practice give general guidance for both the selection of the maximum deflection limits and the calculation of deflection. However, the simplified procedures for calculating e J S E Internationaldeflection in most codes were developed from tests on simply-supported reinforced concrete beams and often produce grossly inaccurate predictions when applied to more complex structures. Again, the existing code procedures do not provide real guidance on how to adequately model the time-dependent effects of creep and shrinkage in deflection calculations.Serviceability failures of concrete structures involving excessive cracking and/or excessive deflection are relatively common. Numerous cases have been reported, in Australia and elsewhere, of structures that complied with code requirements but still deflected or cracked excessively. In a large majority of these failures, shrinkage of concrete is primarily responsible. Clearly, the serviceability provisions embodied in our codes do not adequately model the in-service behaviour of structures and, in particular, fail to account adequately for shrinkage.The quest for serviceable concrete structures must involve the development of more reliable design procedures. It must also involve designers giving more attention to the specification of an appropriate concrete mix, particularly with regard to the creep and shrinkage characteristics of the mix, and sound engineering input is required in the construction procedures. High performance concrete structures require the specification of high performance concrete (not necessarily high strength concrete, but concrete with relatively low shrinkage, not prone to plastic shrinkage cracking) and a high standard of construction, involving suitably long stripping times, adequate propping, effective curing procedures and rigorous on-site supervision.This paper addresses some of these problems, particularly those related to designing for the effects of shrinkage. It outlines how shrinkage affects the in-service behaviour of structures and what to do about it in design. It also provides an overview of the considerations currently being made by the working group established by Standards Australia to revise the serviceability provisions of AS3600-1994 [1], particularly those clauses related to shrinkage.2. Designing for ServiceabilityWhen designing for serviceability, the designer must ensure that the structure can perform its intended function under the day to day service loads. Deflection must not be excessive, cracks must be adequately controlled and no portion of the structure should suffer excessive vibration. Shrinkage causes time-dependent cracking, thereby reducing the stiffness of a concrete structure, and is therefore a detrimental factor in all aspects of the design for serviceability.Deflection problems that may affect the serviceability of concrete structures can be classified into three main types:(a)Where excessive deflection causes either aesthetic or functional problems.(b)Where excessive deflection results in damage to either structural or non-structural elementattached to the member.(c)Where dynamics effects due to insufficient stiffness cause discomfort to occupants.3. Effects of ShrinkageIf concrete members were free to shrink, without restraint, shrinkage of concrete would not be a major concern to structural engineers. However, this is not the case. The contraction of a concrete member is often restrained by its supports or by the adjacent structure. Bonded reinforcement also restrains shrinkage. Each of these forms of restraint involve the imposition of a gradually increasing tensile force on the concrete which may lead to time-dependent cracking (in previously uncracked regions), increases in deflection and a widening of existing cracks. Restraint to shrinkage is probably the most common cause of unsightly cracking in concrete structures. In many cases, these problemsarise because shrinkage has not been adequately considered by the structural designer and the effects of shrinkage are not adequately modelled in the design procedures specified in codes of practice for crack control and deflection calculation.The advent of shrinkage cracking depends on the degree of restraint to shrinkage, the extensibility and strength of the concrete in tension, tensile creep and the load induced tension existing in the member. Cracking can only be avoided if the gradually increasing tensile stress induced by shrinkage, and reduced by creep, is at all times less than the tensile strength of the concrete. Although the tensile strength of concrete increases with time, so too does the elastic modulus and, therefore, so too does the tensile stress induced by shrinkage. Furthermore, the relief offered by creep decreases with age. The existence of load induced tension in uncracked regions accelerates the formation of time-dependent cracking. In many cases, therefore, shrinkage cracking is inevitable. The control of such cracking requires two important steps. First, the shrinkage-induced tension and the regions where shrinkage cracks are likely to develop must be recognised by the structural designer. Second, an adequate quantity and distribution of anchored reinforcement must be included in these regions to ensure that the cracks remain fine and the structure remains serviceable.3.1 What is Shrinkage?Shrinkage of concrete is the time-dependent strain measured in an unloaded and unrestrained specimen at constant temperature. It is important from the outset to distinguish between plastic shrinkage, chemical shrinkage and drying shrinkage. Some high strength concretes are prone to plastic shrinkage, which occurs in the wet concrete, and may result in significant cracking during the setting process. This cracking occurs due to capillary tension in the pore water. Since the bond between the plastic concrete and the reinforcement has not yet developed, the steel is ineffective in controlling such cracks. This problem may be severe in the case of low water content, silica fume concrete and the use of such concrete in elements such as slabs with large exposed surfaces is not recommended.Drying shrinkage is the reduction in volume caused principally by the loss of water during the drying process. Chemical (or endogenous) shrinkage results from various chemical reactions within the cement paste and includes hydration shrinkage, which is related to the degree of hydration of the binder in a sealed specimen. Concrete shrinkage strain, which is usually considered to be the sum of the drying and chemical shrinkage components, continues to increase with time at a decreasing rate.Shrinkage is assumed to approach a final value, *sc ε, as time approaches infinity and is dependent onall the factors which affect the drying of concrete, including the relative humidity and temperature, the mix characteristics (in particular, the type and quantity of the binder, the water content and water-to-cement ratio, the ratio of fine to coarse aggregate, and the type of aggregate), and the size and shape of the member.Drying shrinkage in high strength concrete is smaller than in normal strength concrete due to the smaller quantities of free water after hydration. However, endogenous shrinkage is significantly higher.For normal strength concrete (50≤'c f MPa), AS3600 suggests that the design shrinkage (which includes both drying and endogenous shrinkage) at any time after the commencement of drying may be estimated fromb cs cs k .1εε=(1)where b cs .ε is a basic shrinkage strain which, in the absence of measurements, may be taken to be 850 x 10-6 (note that this value was increased from 700 x 10-6 in the recent Amendment 2 of the Standard); k 1 is obtained by interpolation from Figure 6.1.7.2 in the Standard and depends on the time since the commencement of drying, the environment and the concrete surface area to volume ratio. A hypothetical thickness, t h = 2A / u e , is used to take this into account, where A is the cross-sectional area of the member and u e is that portion of the section perimeter exposed to the atmosphere plus half the total perimeter of any voids contained within the section.AS3600 states that the actual shrinkage strain may be within a range of plus or minus 40% of the value predicted (increased from ± 30% in Amendment 2 to AS3600-1994). In the writer’s opin ion, this range is still optimistically narrow, particularly when one considers the size of the country and the wide variation in shrinkage measured in concretes from the various geographical locations. Equation 1 does not include any of the effects related to the composition and quality of the concrete. The same value of εcs is predicted irrespective of the concrete strength, the water-cement ratio, the aggregate type and quantity, the type of admixtures, etc. In addition, the factor k 1 tends to overestimate the effect of member size and significantly underestimate the rate of shrinkage development at early ages.The method should be used only as a guide for concrete with a low water-cement ratio (<0.4) and with a well graded, good quality aggregate. Where a higher water-cement ratio is expected or when doubts exist concerning the type of aggregate to be used, the value of εcs predicted by AS3600 should be increased by at least 50%. The method in the Standard for the prediction of shrinkage strain is currently under revision and it is quite likely that significant changes will be proposed with the inclusion of high strength concretes.A proposal currently being considered by Standards Australia, and proposed by Gilbert (1998) [9], involves the total shrinkage strain, εcs , being divided into two components, endogenous shrinkage, εcse , (which is assumed to develop relatively rapidly and increases with concrete strength) and drying shrinkage, εcsd (which develops more slowly, but decreases with concrete strength). At any time t (in days) after pouring, the endogenous shrinkage is given byεcse = ε*cse (1.0 - e -0.1t ) (2) where ε*cse is the final endogenous shrinkage and may be taken as ε*cse 610)503(-⨯-'=c f , wherec f ' is in MPa. The basic drying shrinkage *csd ε is given by66*1025010)81100(--⨯≥⨯'-=c csd f ε(3) and at any time t (in days) after the commencement of drying, the drying shrinkage may be taken as*1csd csd k εε= (4)The variable 1k is given by )7/(8.08.0541h t t t k k k += (5) where h t e k 005.042.18.0-+= and 5k is equal to 0.7 for an arid environment, 0.6 for a temperate environment and 0.5 for a tropical/coastal environment. For an interior environment, k 5 may be taken as 0.65. The value of k 1 given by Equation 5 has the same general shape as that given in Figure6.1.7.2 in AS3600, except that shrinkage develops more rapidly at early ages and the reduction in drying shrinkage with increasing values of t h is not as great.The final shrinkage at any time is therefore the sum of the endogenous shrinkage (Equation 2) and the drying shrinkage (Equation 4). For example, for specimens in an interior environment with hypothetical thicknesses t h = 100 mm and t h = 400 mm, the shrinkage strains predicted by the above model are given in Table 1. Table 1 Design shrinkage strains predicted by proposed model for an interior environment. h t c f ' *cse ε (x 10-6)*csd ε(x 10-6) Strain at 28 days (x 10-6) Strain at 10000 days (x 10-6) cse ε csd ε cs ε cse ε csd ε cs ε 100 2525 900 23 449 472 25 885 910 50100 700 94 349 443 100 690 790 75175 500 164 249 413 175 493 668 100250 300 235 150 385 250 296 546 4002525 900 23 114 137 25 543 568 50100 700 94 88 182 100 422 522 75175 500 164 63 227 175 303 478 100 250 300 235 38 273 250 182 4323.2 Shrinkage in Unrestrained and Unreinforced Concrete (Gilbert, 1988) [7]Drying shrinkage is greatest at the surfaces exposed to drying and decreases towards the interior of a concrete member. In Fig.1a , the shrinkage strains through the thickness of a plain concrete slab, drying on both the top and bottom surfaces, are shown. The slab is unloaded and unrestrained.The mean shrinkage strain, εcs in Fig. 1, is the average contraction. The non-linear strain labelled ∆εcs is that portion of the shrinkage strain that causes internal stresses to develop. These self-equilibrating stresses (called eigenstresses) produce the elastic and creep strains required to restore compatibility (ie. to ensure that plane sections remain plane). These stresses occur in all concrete structures and are tensile near the drying surfaces and compressive in the interior of the member. Because the shrinkage-induced stresses develop gradually with time, they are relieved by creep. Nevertheless, the tensile stresses near the drying surfaces often overcome the tensile strength of the immature concrete and result in surface cracking, soon after the commencement of drying. Moist curing delays the commencement of drying and may provide the concrete time to develop sufficient tensile strength to avoid unsightly surface cracking.Fig. 1 - Strain components caused by shrinkage in a plain concrete slab.The elastic plus creep strains caused by the eigenstresses are equal and opposite to ∆εcs and are shown in Fig. 1b. The total strain distribution, obtained by summing the elastic, creep and shrinkage strain components, is linear (Fig. 1c) thus satisfying compatibility. If the drying conditions are the same at both the top and bottom surfaces, the total strain is uniform over the depth of the slab and equal to the mean shrinkage strain, εcs . It is this quantity that is usually of significance in the analysis of concrete structures. If drying occurs at a different rate from the top and bottom surfaces, the total strain distribution becomes inclined and a warping of the member results.4. Control of deflectionThe control of deflections may be achieved by limiting the calculated deflection to an acceptably small value. Two alternative general approaches for deflection calculation are specified in AS3600 (1), namely ‘deflection by refined calculation’ (Clause 9.5.2 for beams and Clause 9.3.2 for slabs) and ‘deflection by simplified calculation’ (Clause 9.5.3 for beams and Clause 9.3.3 for slabs). The former is not specified in detail but allowance should be made for cracking and tension stiffening, the shrinkage and creep properties of the concrete, the expected load history and, for slabs, the two-way action of the slab. 呵呵The long-term or time-dependent behaviour of a beam or slab under sustained service loads can be determined using a variety of analytical procedures (Gilbert, 1988) [7], including the Age-Adjusted Effective Modulus Method (AEMM), described in detail by Gilbert and Mickleborough (1997) [12]. The use of the AEMM to determine the instantaneous and time-dependent deformation of the critical cross-sections in a beam or slab and then integrating the curvatures to obtain deflection, is a refined calculation method and is recommended.Using the AEMM, the strain and curvature on individual cross-sections at any time can be calculated, as can the stress in the concrete and bonded reinforcement or tendons. The routine use of the AEMM in the design of concrete structures for the serviceability limit states is strongly encouraged.5. Control of flexural crackingIn AS3600-1994, the control of flexural cracking is deemed to be satisfactory, providing the designer satisfies certain detailing requirements. These involve maximum limits on the centre-to-centre spacing of bars and on the distance from the side or soffit of the beam to the nearest longitudinal bar. These limits do not depend on the stress in the tensile steel under service loads and have been found to be unreliable when the steel stress exceeds about 240 MPa. The provisions of AS3600-1994 over-simplify the problem and do not always ensure adequate control of cracking.With the current move to higher strength reinforcing steels (characteristic strengths of 500 MPa and above), there is an urgent need to review the crack-control design rules in AS3600 for reinforced concrete beams and slabs. The existing design rules for reinforced concrete flexural elements are intended for use in the design of elements containing 400 MPa bars and are sometimes unconservative. They are unlikely to be satisfactory for members in which higher strength steels are used, where steel stresses at service loads are likely to be higher due to the reduced steel area required for strength.6. ConclusionsThe effects of shrinkage on the behaviour of reinforced and prestressed concrete members under sustained service loads has been discussed. In particular, the mechanisms of shrinkage warping in unsymmetrically reinforced elements and shrinkage cracking in restrained direct tension members has been described. Recent amendments to the serviceability provisions of AS3600 have beenoutlined and techniques for the control of deflection and cracking are presented. Reliable procedures for the prediction of long-term deflections and final crack widths in flexural members have also been proposed and illustrated by examples.收缩,开裂和变形–混凝土结构使用的可靠性里吉尔伯特土木及环境工程学校校长兼教授新南威尔士大学,悉尼,新南威尔士州 2052 号电子邮件:******************.au摘要本文讨论收缩对混凝土结构可靠性的影响,它概述了为什么收缩是重要的,它的主要影响,即对结构最终的开裂程度和挠度大小的影响,以及在设计中应该注意什么?有一种模型可以预测在普通混凝土、高强度混凝土、不稳定性普通混凝土和钢筋混凝土中的收缩应变,无论有没有外部约束的情况下,都可以用这种模型来解释。
新拌混凝土的性能中英文资料外文翻译文献

新拌混凝土的性能中英文资料外文翻译文献(文档含英文原文和中文翻译)Properties of Fresh ConcreteFresh concrete is a mixture of water, cement, aggregate and admixture (if any). After mixing, operations such as transporting, placing, compacting and finishing of fresh concrete can all considerably affect the properties of hardened concrete. It is important that the constituent materials remain uniformly distributed within the concrete mass during the various stages of its handling and that full compaction is achieved. When either of these conditions is not satisfied the properties of the resulting hardened concrete, for example, strength and durability, are adversely affected.The characteristics of fresh concrete which affect full compaction are its consistency, mobility and compactability. In concrete practice these are often collectively known as workability. The ability of concrete to maintain its uniformity is governed by its stability, which depends on its consistency and its cohesiveness. Since the methods employed for conveying, placing and consolidatingd a concrete mix, as well as the nature of the section to be cast, may vary from job to job it follows that the corresponding workability and stability requirements will also vary. The assessment of the suitability of a fresh concrete for a particular job will alwaysto some extent remain a matter of personal judgment.In spite of its importance, the behaviour of plastic concrete often tends to be overlooked. It is recommended that students should learn to appreciate the significance of the various characteristics of concrete in its plastic state and know how these may alter during operations involved in casting a concrete structure.13.1 WorkabilityWorkability of concrete has never been precisely defined. For practical purposes it generally implies the ease with which a concrete mix can be handled from the mixer to its finally compacted shape. The three main characteristics of the property are consistency, mobility and compactability. Consistency is a measure of wetness or fluidity. Mobility defines the ease with which a mix can flow into and completely fill the formwork or mould. Compactability is the ease with which a given mix can be fully compacted, all the trapped air being removed. In this context the required workability of a mix depends not only on the characteristics and relative proportions of the constituent materials but also on (1) the methods employed for conveyance and compaction, (2) the size, shape and surface roughness of formwork or moulds and (3) the quantity and spacing of reinforcement.Another commonly accepted definition of workability is related to the amount of useful internal work necessary to produce full compaction. It should be appreciated that the necessary work again depends on the nature of the section being cast. Measurement of internal work presents many difficulties and several methods have been developed for this purpose but none gives an absolute measure of workability.The tests commonly used for measuring workability do not measure the individual characteristics (consistency, mobility and compactability) of workability. However, they do provide useful and practical guidance on the workability of a mix. Workability affects the quality of concrete and has a direct bearing on cost so that, for example, an unworkable concrete mix requires more time and labour for full compaction. It is most important that a realistic assessment is made of the workability required for given site conditions before any decision is taken regarding suitable concrete mix proportions.13.2 Measurement of WorkabilityThree tests widely used for measuring workability are the slump, compacting factorand V-B consistometer tests (figure 13.1). These are standard tests in the United Kingdom and are described in detail in BS 1881: Part 2. Their use is also recommended in CP 110: Part 1. It is important to note that there is no single relationship between the slump, compacting factor and V-B results for different concretes. In the following sections the salient features of these tests together with their merits and limitations are discussed.Slump TestThis test was developed by Chapman in the United States in 1913. A 300 mm high concrete cone, prepared under standard conditions (BS 1881: Part 2) is allowed to subside and the slump or reduction in height of the cone is taken to be a measure of workability. The apparatus is inexpensive, portable and robustd and is the simplest of all the methods employed for measuring workability. It is not surprising that, in spite of its several limitations, the slump test has retained its popularity.Figure 13.1 Apparatus for workability measurement: (a) slump cone, (b) compacting factor and(c) V-B consistometerThe test primarily measures the consistency of plastic concrete and although it is difficult to see any significant relationship between slump and workability as defined previously, it is suitable for detecting changes in workability. For example, an increase in the water content or deficiency in the proportion of fine aggregate results in an increase in slump. Although the test is suitable for quality-controlpurposes it should be remembered that it is generally considered to be unsuitable formix design since concretes requiring varying amounts of work for compaction can have similar numerical values of slump. The sensitivity and reliability of the test for detecting variation in mixes of different workabilities is largely dependent on its sensitivity to consistency. The test is not suitable for very dry or wet mixes. For very dry mixes, with zero or near-zero slump, moderate variations in workability do not result in measurable changes in slump. For wet mixes, complete collapse of the concrete produces unreliable values of slump.Figure 13.2 Three main types of slumpThe three types of slump usually observed are true slump, shear slump and collapse slump, as illustrated in figure 13.2. A true slump is observed with cohesive and rich mixes for which the slump is generally sensitive to variations in workability.A collapse slump is usually associated with very wet mixes and is generally indicative of poor quality concrete and most frequently results from segregation of its constituent materials. Shear slump occurs more often in leaner mixes than in rich ones and indicates a lack of cohesion which is generally associated with harsh mixes (low mortar content). whenever a shear slump is obtained the test should be repeated and, if persistent, this fact should be recorded together with test results, because widely different values of slump can be obtained depending on whether the slump is of true or shear form.The standard slump apparatus is only suitable for concretes in which the maximum aggregate size does not exceed 37.5 mm. It should be noted that the value of slump changes with time after mixing owing to normal hydration processes and evaporation of some of the free water, and it is desirable therefore that tests are performed within a fixed period of time.Compacting Factor TestThis test, developed in the United Kingdom by Glanville et al. (1947), measures the degree of compaction for a standard amount of work and thus offers a direct and reasonably reliable assessment of the workability of concrete as previously defined. The apparatus is a relatively simple mechanical contrivance (figure 13.1) and is fully described in BS 1881: Part 2. The test requires measurement of the weights of the partially and fully compacted concrete and the ratio of the partially compacted weight to the fully compacted weight, which is always less than 1, is known as the compacting factor. For the normal range of concretes the compacting factor lies between 0.80 and 0.92. The test is particularly useful for drier mixes for which the slump test is not satisfactory. The sensitivity of the compacting factor is reduced outside the normal range of workability and is generally unsatisfactory for compacting factors greater than 0.92.It should also be appreciated that, strictly speaking, some of the basic assumptions of the test are not correct. The work done to overcome surface friction of the measuring cylinder probably varies with the characteristics of the mix. It has been shown by Cusens (1956) that for concretes with very low workability the actual work required to obtain full compaction depends on the richness of a mix while the compacting factor remains sensibly unaffected. Thus it follows that the generally held belief that concretes with the same compacting factor require the same amount of work for full compaction cannot always be justified. One further point to note is that the procedure for placing concrete in the measuring cylinder bears no resemblance to methods commonly employed on the site. As in the slump test, the measurement of compacting factor must be made within a certain specified period. The standard apparatus is suitable for concrete with a maximum aggregate size of up to 37.5 mm. V-B Consistometer TestThis test was developed in Sweden by B a hrner (1940) (see figure 13.1). Although generally regarded as a test primarily used in research its potential is now more widely acknowledged in industry and the test is gradually being accepted. In this test (BS 1881: Part 2) the time taken to transform, by means of vibration, a standard cone of concrete to a compacted flat cylindrical mass is recorded. This is known as the V-B time, in seconds, and is stated to the nearest 0.5 s. Unlike the two previous tests, the treatment of concrete in this test is comparable to the method of compacting concrete in practice. Moreover, the test is sensitive to change inconsistency, mobility and compactability, and therefore a reasonable correlation between the test results and site assessment of workability can be expected.The test is suitable for a wide range of mixes and, unlike the slump and compacting factor tests, it is sensitive to variations in workability of very dry and also air-entrained concretes. It is also more sensitive to variation in aggregate characteristics such as shape and surface texture. The reproducibility of results is good. As for other tests its accuracy tends to decrease with increasing maximum size of aggregate; above 19.0 mm the test results become somewhat unreliable. For concretes requiring very little vibration for compaction the V-B time is only about 3 s. Such results are likely to be less reliable than for larger V-B times because of the difficulty in estimating the time of the end point (concrete in contact withd the whole of the underside of the plastic disc). At the other end of the workability range, such as with very dry mixes, the recorded V-B times are likely to be in excess of their true workability since prolonged vibration is required to remove the entrapped air bubbles under the transparent disc. To overcome this difficulty an automatic device which records the vertical settlement of the disc with respect to time can be attached to the apparatus. This recording device can also assist in eliminating human error in judging the end point. The apparatus for the V-B test is more expensive than that for the slump and compacting factor tests, requiring an electric power supply and greater experience in handling; all these factors make it more suitable for the precast concrete industry and ready-mixed concrete plants than for general site use.13.3 Factors Affecting WorkabilityVarious factors known to influence the workability of a freshly mixed concrete are shown in figure 13.3. From the following discussion it will be apparent that a change in workability associated with the constituent materials is mainly affected by water content and specific surface of cement and aggregate.Cement and WaterFigure 13.3 Factors affecting workability of fresh conreteTypical relationships between the cement-water ratio (by volume) and the volume fraction of cement for different workabilities are shown in figure 15.5. The change in workability for a given change in cement-water ratio is greater when the water content is changed than when only the cement content is changed. In general theeffect of the cement content is greater for richer mixes. Hughes (1971) has shown that similar linear relationships exist irrespective of the properties of the constituent materials.For a given mix, the workability of the concrete decreases as the fineness of the cement increases as a result of the increased specific surface, this effect being more marked in rich mixtures. It should also be noted that the finer cements improve the cohesiveness of a mix. With the exception of gypsum, the composition of cement has no apparent effect on workability. Unstable gypsum is responsible for false set, which can impair workability unless prolonged mixing or remixing of the fresh concrete is carried out. Variations in quality of water suitable for making concrete have no significant effect on workability.AdmixturesThe principal admixtures affecting improvement in the workability of concrete are water-reducing and air-entraining agents. The extent of the increase in workability is dependent on the type and amount of admixture used and the general characteristics of the fresh concrete.Workability admixtures are used to increase workability while the mix proportions are kept constant or to reduce the water content while maintaining constant workability. The former results in a slight reduction in concrete strength.Air-entraining agents are by far the most commonly used workability admixtures because they also improve both the cohesiveness of the plastic concrete and the frost resistance of the resulting hardened concrete. Two points of practical importance concerning air-entrained concrete are that for a given amount of entrained air, the increase in workability tends to be smaller for concretes containing rounded aggregates or low cement-water ratios (by volume) and, in general, the rate of increase in workability tends to decrease with increasing air content. However, as a guide it may be assumed that every 1 per cent increase in air content will increase the compacting factor by 0.01 and reduce the V-B time by 10 per cent.AggregateFor given cement, water and aggregate contents, the workability of concrete is mainly influenced by the total surface area of the aggregate. The surface area is governed by the maximum size, grading and shape of the aggregate. Workability decreases as the specific surface increases, since this requires a greater proportion of cement paste to wet the aggregate particles, thus leaving a smaller amount of paste for lubrication. It follows that, all other conditions being equal, the workability will be increased when the maximum size of aggregate increases, the aggregate particles become rounded or the overall grading becomes coarser. However, the magnitude of this change inworkability depends on the mix proportions, the effect of the aggregate being negligible for very rich mixes (aggregate-cement ratios approaching 2). The practical significance of this is that for a given workability and cement-water ratio the amount of aggregate which can be used in a mix varies depending on the shape, maximum size and grading of the aggregate, as shown in figure 13.4 and tables 13.1 and 13.2. The influence of air-entrainment (4.5 per cent) on workability is shown also in figure 13.4.TABLE 13.1Effect of maximum size of aggregate of similar grading zone on aggregate-cement ratio of concrete having water-cement ratio of 0.55 by weight, based on McIntosh(1964)Maximum aggregatesize(mm)Aggregate-cement ratio (by weight)Low workability Medium workability High workability IrregulargravelCrushed rockIrregulargravelCrushed rockIrregulargravelCrushed rock9.5 19.0 37.5 5.36.27.64.85.56.44.75.46.54.24.75.54.44.95.93.74.45.2TABLE 13.2Effect of aggregate grading (maximum size 19.0 mm) on aggregate-cement ratio of concrete having medium workability and water-cement ratio of 0.55 by weight, basedon McIntosh (1964)Type of aggregateAggregate-cement ratioCoarse grading Fine gradingRounded gravel Irregular gravel Crushed rock 7.35.54.76.35.14.3Figure 13.4 Effect of aggregate shape on aggregate-cement ratio of concretes for different workabilities, based on Cornelius (1970)Several methods have been developed for evaluating the shape of aggregate, a subject discussed in chapter 12. Angularity factors together with grading modulus and equivalent mean diameter provide a means of considering the respective effects of shape, size and grading of aggregate (see chapter 15). Since the strength of a fully compacted concrete, for given materials and cement-water ratio, is not dependent on the ratio of coarse to fine aggregate, maximum economy can be obtained by using the coarse aggregate content producing the maximum workability for a given cement content (Hughes, 1960) (see figure 13.5). The use of optimum coarse aggregate content in concrete mix design is described in chapter 15. It should be noted that it is the volume fraction of an aggregate, rather than its weight, which is important.Figure 13.5 A typical relationship between workability and coarse aggregate content of concrete, based on Hughes (1960)The effect of surface texture on workability is shown in figure 13.6. It can be seen that aggregates with a smooth texture result in higher workabilities than aggregates with a rough texture. Absorption characteristics of aggregate also affect workability where dry or partially dry aggregates are used. In such a case workability drops, the extent of the reduction being dependent on the aggregate content and its absorption capacity.Ambient ConditionsEnvironmental factors that may cause a reduction in workability are temperature, humidity and wind velocityd. For a given concrete, changes in workability are governed by the rate of hydration of the cement and the rate of evaporation of water. Therefore both the time interval from the commencement of mixing to compaction and the conditions of exposure influence the reduction in workability. An increase in the temperature speeds up the rate at which water is used for hydration as well as its loss through evaporation. Likewise wind velocity and humidity influence the workability as they affect the rate of evaporation. It is worth remembering that in practice these factors depend on weather conditions and cannot be controlled.Figure 13.6 Effect of aggregate surface texture on aggregate-cement ratio of concretes for different workabilities, based on Cornelius (1970)TimeThe time that elapses between mixing of concrete and its final compaction depends on the general conditions of work such as the distance between the mixer and the point of placing, site procedures and general management. The associated reduction in workability is a direct result of loss of free water with time through evaporation, aggregate absorption and initial hydration of the cement. The rate of loss of workability is affected by certain characteristics of the constituent materials, for example, hydration and heat development characteristics of the cement, initial moisture content and porosity of the aggregate, as well as the ambient conditions.For a given concrete and set of ambient conditions, the rate of loss of workability with time depends on the conditions of handling. Where concrete remains undisturbed after mixing until it is placed, the loss of workability during the first hour can be substantial, the rate of loss of workability decreasing with time as illustrated by curve A in figure 13.7. On the other hand, if it is continuously agitated, as in the case of ready-mixed concrete, the loss of workability is reduced, particularly during the first hour or so (see curve B in figure 13.7). However,prolonged agitation during transportation may increase the fineness of the solidparticles through abrasion and produce a further reduction in workability. For concretes continuously agitated and undisturbed during transportation, the time intervals permitted (BS 1926) between the commencement of mixing and delivery on site are 2 hours and 1 hour respectively.For practical purposes, loss of workability assumes importance when concrete becomes so unworkable that it cannot be effectively compacted, with the result that its strength and other properties become adversely affected. Corrective measures frequently taken to ensure that concrete at the time of placing has the desired workability are either an initial increase in the water content or an increase in the water content with further mixing shortly before the concrete is discharged. When this results in a water content greater than that originally intended, some reduction in strength and durability of the hardened concrete is to be expected unless the cement content is increased accordingly. This important fact is frequently overlooked on site. It should be recalled that the loss of workability varies with the mix, the ambient conditions, the handling conditions and the delivery time. No restriction on delivery time is given in CP 110: Part 1 but the concrete must be capable of being placed and effectively compacted without the addition of further water. For detailed information on the use of ready-mixed concrete the reader is advised to consult the work of Dewar (1973).Figure 13.7 Loss of workability of concrete with time: (A) no agitation and (B)continuously agitated after mixing13.4 StabilityApart from being sufficiently workable, fresh concrete should have a composition such that its constituent materials remain uniformly distributed in the concrete during both the period between mixing and compaction and the period following compaction before the concrete stiffens. Because of differences in the particle size and specific gravities of the constituent materials there exists a natural tendency for them to separate. Concrete capable of maintaining the required uniformity is said to be stable and most cohesive mixes belong to this category. For an unstable mix the extent towhich the constituent materials will separate depends on the methods of transportation, placing and compaction. The two most common features of an unstable concrete are segregation and bleeding.SegregationWhen there is a significant tendency for the large and fine particles in a mix to become separated, segregation is said to have occurred. In general, the less cohesive the mix the greater the tendency for segregation to occur. Segregation is governed by the total specific surface of the solid particles including cement and the quantity of mortar in the mix. Harsh, extremely wet and dry mixes as well as those deficient in sand, particularly the finer particles, are prone to segregation. As far as possible, conditions conducive to segregation such as jolting of concrete during transportation, dropping from excessive heights during placing and over-vibration during compaction should be avoided.Blemishes, sand streaks, porous layers and honeycombing are a direct result of segregation. These features are not only unsightly but also adversely affect strength, durability and other properties of the hardened concrete. It is important to realize that the effects of segregation may not be indicated by the routine strength tests on control specimens since the conditions of placing and compaction of the specimens differ from those in the actual structure. There are no specific rules for suspecting possible segregation but after some experience of mixing and handling concrete it is not difficult to recognize mixes where this is likely to occur. For example, if a handful of concrete is squeezed in the hand and then released so that it lies in the palm, a cohesive concrete will be seen to retain its shape. A concrete which does not retain its shape under these conditions may well be prone to segregation and this is particularly so far wet mixes.BleedingDuring compaction and until the cement paste has hardened there is a natural tendency for the solid particles, depending on size and specific gravity, to exhibit a downward movement. Where the consistency of a mix is such that it is unable to hold all its water some of it is gradually displaced and rises to the surface, and some may also leak through the joints of the formwork. Separation of water from a mix in this manner is known as bleeding. While some of the water reaches the top surface some may become trapped under the larger particles and under the reinforcing bars. The resulting variations in the effective water content within a concrete massproduce corresponding changes in its properties. For example, the strength of the concrete immediately underneath the reinforcing bars and coarse aggregate particles may be much less than the average strength and the resistance to percolation of water in these areas is reduced. In general, the concrete strength tends to increase with depth below the top surface. The water which reaches the top surface presents the most serious practical problems. If it is not removed, the concrete at and near the top surface will be much weaker and less durable than the remainder of the concrete. This can be particularly troublesome in slabs which have a large surface area. On the other hand, removal of the surface water will unduly delay the finishing operation on the site.The risk of bleeding increases when concrete is compacted by vibration although this may be minimized by using a correctly designed mix and ensuring that the concrete is not over-vibrated. Rich mixes tend to bleed less than lean mixes. The type of cement employed is also important, the tendency for bleeding to occur decreasing as the fineness of the cement or its alkaline and tricalcium aluminate (C3A) content increases. Air-entrainment provides another very effective means of controlling bleeding in, for example, wet lean mixes where both segregation and bleeding are frequently troublesome.新拌混凝土的性能新拌混凝土为水、水泥、集料和外加剂(如果有的话)的混合物。
混凝土工艺中英文对照外文翻译文献
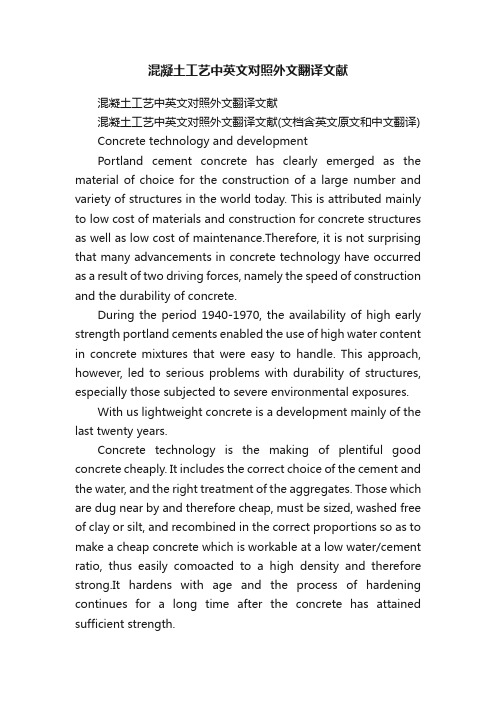
混凝土工艺中英文对照外文翻译文献混凝土工艺中英文对照外文翻译文献混凝土工艺中英文对照外文翻译文献(文档含英文原文和中文翻译) Concrete technology and developmentPortland cement concrete has clearly emerged as the material of choice for the construction of a large number and variety of structures in the world today. This is attributed mainly to low cost of materials and construction for concrete structures as well as low cost of maintenance.Therefore, it is not surprising that many advancements in concrete technology have occurred as a result of two driving forces, namely the speed of construction and the durability of concrete.During the period 1940-1970, the availability of high early strength portland cements enabled the use of high water content in concrete mixtures that were easy to handle. This approach, however, led to serious problems with durability of structures, especially those subjected to severe environmental exposures.With us lightweight concrete is a development mainly of the last twenty years.Concrete technology is the making of plentiful good concrete cheaply. It includes the correct choice of the cement and the water, and the right treatment of the aggregates. Those which are dug near by and therefore cheap, must be sized, washed free of clay or silt, and recombined in the correct proportions so as to make a cheap concrete which is workable at a low water/cement ratio, thus easily comoacted to a high density and therefore strong.It hardens with age and the process of hardening continues for a long time after the concrete has attained sufficient strength.Abrams’law, perhaps the oldest law of concrete technology, states that the strength of a concrete varies inversely with its water cement ratio. This means that the sand content (particularly the fine sand which needs much water) must be reduced so far as possible. The fact that the sand “drinks” large quantities of water can easily be established by mixing several batches of x kg of cement with y kg of stone and the same amount of water but increasing amounts of sand. However if there is no sand the concrete will be so stiff that it will be unworkable thereforw porous and weak. The same will be true if the sand is too coarse. Therefore for each set of aggregates, the correct mix must not be changed without good reason. This applied particularly to the water content.Any drinkable and many undrinkable waters can be used for making concrete, including most clear waters from the sea or rivers. It is important that clay should be kept out of the concrete. The cement if fresh can usually be chosen on the basis of the maker’s certificates of tensile or crushing tests, but these are always made with fresh cement. Where strength is important , and the cement at the site is old, it should be tested.This stress , causing breakage,will be a tension since concretes are from 9 to 11times as strong in compression as in tension, This stress, the modulus of rupture, will be roughly double the direct tensile breaking stress obtained in a tensile testing machine,so a very rough guess at the conpressive strength can be made by multiplying the modulus of rupture by 4.5. The method can be used in combination with the strength results of machine-crushed cubes or cylinders or tensile test pieces but cannot otherwise be regarded as reliable. With these comparisons,however, it is suitable for comparing concretes on the same site made from the same aggregates and cement, with beams cast and tested in the same way.Extreme care is necessary for preparation,transport,plating and finish of concrete in construction works.It is important to note that only a bit of care and supervision make a great difference between good and bad concrete.The following factors may be kept in mind in concreting works.MixingThe mixing of ingredients shall be done in a mixer as specified in the contract.Handling and ConveyingThe handling&conveying of concrete from the mixer to the place of final deposit shall be done as rapidly as practicable and without any objectionable separation or loss of ingredients.Whenever the length of haul from the mixing plant to the place of deposit is such that the concrete unduly compacts or segregates,suitable agitators shall be installed in the conveying system.Where concrete is being conveyed on chutes or on belts,the free fall or drop shall be limited to 5ft.(or 150cm.) unless otherwise permitted.The concrete shall be placed in position within 30 minutes of its removal from the mixer.Placing ConcreteNo concrete shall be placed until the place of deposit has been thoroughly inspected and approved,all reinforcement,inserts and embedded metal properly security in position and checked,and forms thoroughly wetted(expect in freezing weather)or oiled.Placing shall be continued without avoidable interruption while the section is completed or satisfactory construction joint made.Within FormsConcrete shall be systematically deposited in shallow layers and at such rate as to maintain,until the completion of the unit,a plastic surface approximately horizontal throughout.Each layer shall be thoroughly compacted before placing the succeeding layer.CompactingMethod. Concrete shall be thoroughly compacted by means of suitable tools during and immediately after depositing.The concrete shall be worked around all reinforcement,embedded fixtures,and into the comers of the forms.Every precaution shall be taken to keep the reinforcement and embedded metal in proper position and to prevent distortion.Vibrating. Wherever practicable,concrete shall be internally vibrated within the forms,or in the mass,in order to increase the plasticity as to compact effectively to improve the surface texture and appearance,and to facilitate placing of the concrete.Vibration shall be continued the entire batch melts to a uniform appearance and the surface just starts to glisten.A minute film of cement paste shall be discernible between the concrete and the form and around the reinforcement.Over vibration causing segregation,unnecessary bleeding or formation of laitance shall be avoided.The effect spent on careful grading, mixing and compaction of concrete will be largely wasted if the concrete is badly cured. Curing means keeping the concretethoroughly damp for some time, usually a week, until it has reached the desired strength. So long as concrete is kept wet it will continue to gain strength, though more slowly as it grows older.Admixtures or additives to concrete are materials arematerials which are added to it or to the cement so as to improve one or more of the properties of the concrete. The main types are:1. Accelerators of set or hardening,2. Retarders of set or hardening,3. Air-entraining agents, including frothing or foaming agents,4. Gassing agents,5. Pozzolanas, blast-furnace slag cement, pulverized coal ash,6. Inhibitors of the chemical reaction between cement and aggregate, which might cause the aggregate to expand7. Agents for damp-proofing a concrete or reducing its permeability to water,8. Workability agents, often called plasticizers,9. Grouting agents and expanding cements.Wherever possible, admixtures should be avouded, particularly those that are added on site. Small variations in the quantity added may greatly affect the concrete properties in an undesiraale way. An accelerator can often be avoided by using a rapid-hardening cement or a richer mix with ordinary cement, or for very rapid gain of strength, high-alumina cement, though this is very much more expensive, in Britain about three times as costly as ordinary Portland cement. But in twenty-four hours its strength is equal to that reached with ordinary Portland cement in thirty days.A retarder may have to be used in warm weather when a large quantity of concrete has to be cast in one piece of formwork, and it is important that the concrete cast early in the day does not set before the last concrete. This occurs with bridges when they are cast in place, and the formwork necessarily bends underthe heavy load of the wet concrete. Some retarders permanently weaken the concrete and should not be used without good technical advice.A somewhat similar effect,milder than that of retarders, is obtained with low-heat cement. These may be sold by the cement maker or mixed by the civil engineering contractor. They give out less heat on setting and hardening, partly because they harden more slowly, and they are used in large casts such as gravity dams, where the concrete may take years to cool down to the temperature of the surrounding air. In countries like Britain or France, where pulverized coal is burnt in the power stations, the ash, which is very fine, has been mixed with cement to reduce its production of heat and its cost without reducing its long-term strength. Up to about 20 per cent ash by weight of the cement has been successfully used, with considerable savings in cement costs.In countries where air-entraining cement cement can be bought from the cement maker, no air-entraining agent needs to be mixed in .When air-entraining agents draw into the wet cement and concrete some 3-8 percent of air in the form of very small bubbles, they plasticize the concrete, making it more easily workable and therefore enable the water |cement ratio to be reduced. They reduce the strength of the concrete slightly but so little that in the United States their use is now standard practice in road-building where heavy frost occur. They greatly improve the frost resistance of the concrete.Pozzolane is a volcanic ash found near the Italian town of Puzzuoli, which is a natural cement. The name has been given to all natural mineral cements, as well as to the ash from coal or the slag from blast furnaces, both of which may become cementswhen ground and mixed with water. Pozzolanas of either the industrial or the mineral type are important to civil engineers because they have been added to oridinary Portland cement in proportions up to about 20 percent without loss of strength in the cement and with great savings in cement cost. Their main interest is in large dams, where they may reduce the heat given out by the cement during hardening. Some pozzolanas have been known to prevent the action between cement and certain aggregates which causes the aggregate to expand, and weaken or burst the concrete.The best way of waterproof a concrete is to reduce its permeability by careful mix design and manufacture of the concrete, with correct placing and tighr compaction in strong formwork ar a low water|cement ratio. Even an air-entraining agent can be used because the minute pores are discontinuous. Slow, careful curing of the concrete improves the hydration of the cement, which helps to block the capillary passages through the concrete mass. An asphalt or other waterproofing means the waterproofing of concrete by any method concerned with the quality of the concrete but not by a waterproof skin.Workability agents, water-reducing agents and plasticizers are three names for the same thing, mentioned under air-entraining agents. Their use can sometimes be avoided by adding more cement or fine sand, or even water, but of course only with great care.The rapid growth from 1945 onwards in the prestressing of concrete shows that there was a real need for this high-quality structural material. The quality must be high because the worst conditions of loading normally occur at the beginning of the life of the member, at the transfer of stress from the steel to theconcrete. Failure is therefore more likely then than later, when the concrete has become stronger and the stress in the steel has decreased because of creep in the steel and concrete, and shrinkage of the concrete. Faulty members are therefore observed and thrown out early, before they enter the structure, or at least before it The main advantages of prestressed concrete in comparison with reinforced concrete are :①The whole concrete cross-section resists load. In reinforced concrete about half the section, the cracked area below the neutral axis, does no useful work. Working deflections are smaller.②High working stresses are possible. In reinforced concrete they are not usually possible because they result in severe cracking which is always ugly and may be dangerous if it causes rusting of the steel.③Cracking is almost completely avoided in prestressed concrete.The main disadvantage of prestressed concrete is that much more care is needed to make it than reinforced concrete and it is therefore more expensive, but because it is of higher quality less of it needs to be needs to be used. It can therefore happen that a solution of a structural problem may be cheaper in prestressed concrete than in reinforced concrete, and it does often happen that a solution is possible with prestressing but impossible without it.Prestressing of the concrete means that it is placed under compression before it carries any working load. This means that the section can be designed so that it takes no tension or very little under the full design load. It therefore has theoretically no cracks and in practice very few. The prestress is usually applied by tensioning the steel before the concrete in which it isembedded has hardened. After the concrete has hardened enough to take the stress from the steel to the concrete. In a bridge with abutments able to resist thrust, the prestress can be applied without steel in the concrete. It is applied by jacks forcing the bridge inwards from the abutments. This methods has the advantage that the jacking force, or prestress, can be varied during the life of the structure as required.In the ten years from 1950 to 1960 prestressed concrete ceased to be an experinmental material and engineers won confidence in its use. With this confidence came an increase in the use of precast prestressed concrete particularly for long-span floors or the decks of motorways. Whereever the quantity to be made was large enough, for example in a motorway bridge 500 m kong , provided that most of the spans could be made the same and not much longer than 18m, it became economical to usefactory-precast prestressed beams, at least in industrial areas near a precasting factory prestressed beams, at least in industrial areas near a precasting factory. Most of these beams are heat-cured so as to free the forms quickly for re-use.In this period also, in the United States, precast prestressed roof beams and floor beams were used in many school buildings, occasionally 32 m long or more. Such long beams over a single span could not possibly be successful in reinforced concrete unless they were cast on site because they would have to be much deeper and much heavier than prestressed concrete beams. They would certainlly be less pleasing to the eye and often more expensive than the prestressed concrete beams. These school buildings have a strong, simple architectural appeal and will be a pleasure to look at for many years.The most important parts of a precast prestressed concrete beam are the tendons and the concrete. The tendons, as the name implies, are the cables, rods or wires of steel which are under tension in the concrete.Before the concrete has hardened (before transfer of stress), the tendons are either unstressed (post-tensioned prestressing) or are stressed and held by abutments outside the concrete ( pre-tensioned prestressing). While the concrete is hardening it grips each tendon more and more tightly by bond along its full length. End anchorages consisting of plates or blocks are placed on the ends of the tendons of post-tensioned prestressed units, and such tendons are stressed up at the time of transfer, when the concrete has hardened sufficiently. In the other type of pretressing, with pre-tensioned tendons, the tendons are released from external abutments at the moment of transfer, and act on the concrete through bond or archorage or both, shortening it by compression, and themselves also shortening and losing some tension.Further shortening of the concrete (and therefore of the steel) takes place with time. The concrete is said to creep. This means that it shortens permanently under load and spreads the stresses more uniformly and thus more safely across its section. Steel also creeps, but rather less. The result of these two effects ( and of the concrete shrinking when it dries ) is that prestressed concrete beams are never more highly stressed than at the moment of transfer.The factory precasting of long prestressed concrete beams is likely to become more and more popular in the future, but one difficulty will be road transport. As the length of the beam increases, the lorry becomes less and less manoeuvrable untileventually the only suitable time for it to travel is in the middle of the night when traffic in the district and the route, whether the roads are straight or curved. Precasting at the site avoids these difficulties; it may be expensive, but it has often been used for large bridge beams.混凝土工艺及发展波特兰水泥混凝土在当今世界已成为建造数量繁多、种类复杂结构的首选材料。
低热硅酸盐水泥
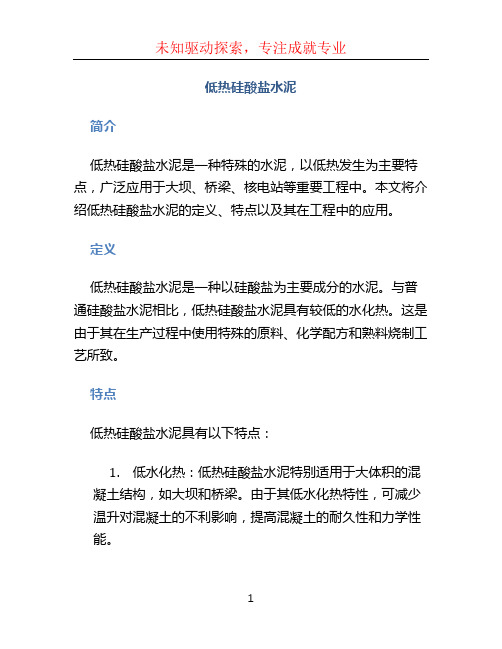
低热硅酸盐水泥简介低热硅酸盐水泥是一种特殊的水泥,以低热发生为主要特点,广泛应用于大坝、桥梁、核电站等重要工程中。
本文将介绍低热硅酸盐水泥的定义、特点以及其在工程中的应用。
定义低热硅酸盐水泥是一种以硅酸盐为主要成分的水泥。
与普通硅酸盐水泥相比,低热硅酸盐水泥具有较低的水化热。
这是由于其在生产过程中使用特殊的原料、化学配方和熟料烧制工艺所致。
特点低热硅酸盐水泥具有以下特点:1.低水化热:低热硅酸盐水泥特别适用于大体积的混凝土结构,如大坝和桥梁。
由于其低水化热特性,可减少温升对混凝土的不利影响,提高混凝土的耐久性和力学性能。
2.早强:低热硅酸盐水泥在水化过程中,能够产生更多的早期强度。
这使得低热硅酸盐水泥尤其适用于需要早期脱模或早期使用的工程项目。
3.抗裂性能:由于低热硅酸盐水泥具有较低的水化热,减少了温度应力的产生和累积,从而提高了混凝土的抗裂性能。
4.环境友好:低热硅酸盐水泥生产过程中采用特殊的原料和化学配方,减少了环境污染和资源消耗。
同时,由于其低热发生特性,也减少了对周围环境和工人的不良影响。
应用低热硅酸盐水泥广泛应用于以下工程项目中:1.大坝:大坝工程对混凝土的性能要求较高。
由于低热硅酸盐水泥具有低热发生和早强的特点,可避免大坝在水化过程中的温度应力积累,从而提高大坝的耐久性和稳定性。
2.桥梁:桥梁是承受车辆重载和气候变化等因素的工程项目。
低热硅酸盐水泥能够提供较高的早期强度,确保桥梁在早期使用阶段的安全性和稳定性。
3.核电站:核电站是对混凝土性能要求极高的工程项目。
低热硅酸盐水泥具有较低的水化热和优良的抗裂性能,能够减少混凝土在核电站运行期间的温度应力和裂缝产生,确保核电站的安全性和稳定性。
除了以上工程项目外,低热硅酸盐水泥还可以应用于需要较低水化热和高早期强度的其他工程项目中,如高速公路、隧道、海洋工程等。
结论低热硅酸盐水泥以其低水化热、早强、抗裂等特点,成为重要工程项目中的首选材料。
论混凝土的施工温度与结构裂缝外文翻译17页word
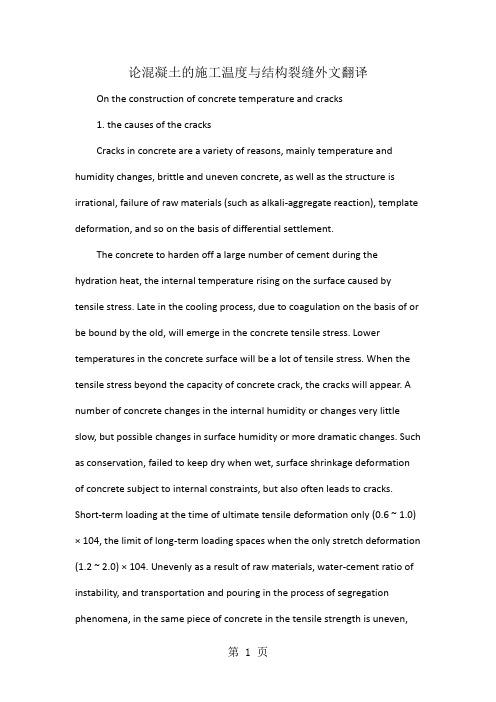
论混凝土的施工温度与结构裂缝外文翻译On the construction of concrete temperature and cracks1. the causes of the cracksCracks in concrete are a variety of reasons, mainly temperature and humidity changes, brittle and uneven concrete, as well as the structure is irrational, failure of raw materials (such as alkali-aggregate reaction), template deformation, and so on the basis of differential settlement.The concrete to harden off a large number of cement during the hydration heat, the internal temperature rising on the surface caused by tensile stress. Late in the cooling process, due to coagulation on the basis of or be bound by the old, will emerge in the concrete tensile stress. Lower temperatures in the concrete surface will be a lot of tensile stress. When the tensile stress beyond the capacity of concrete crack, the cracks will appear. A number of concrete changes in the internal humidity or changes very little slow, but possible changes in surface humidity or more dramatic changes. Such as conservation, failed to keep dry when wet, surface shrinkage deformation of concrete subject to internal constraints, but also often leads to cracks. Short-term loading at the time of ultimate tensile deformation only (0.6 ~ 1.0) × 104, the limit of long-term loading spaces when the only stretch deformation (1.2 ~ 2.0) × 104. Unevenly as a result of raw materials, water-cement ratio of instability, and transportation and pouring in the process of segregation phenomena, in the same piece of concrete in the tensile strength is uneven,there are many low tensile capacity, easy to fracture in a weak position. In reinforced concrete, the tensile stress is mainly borne by the steel, concrete is subject to compressive stress. In plain concrete or reinforced coagulation on the edge of the site if the structure of the tensile stress appears to be relying on its own concrete共12 页commitment.2. thermal stress analysisAccording to the formation of thermal stress can be divided into the following three stages:(1)early: Since the beginning of pouring concrete to cement the end of exothermic basic general about 30 days. Two characteristics of this stage, first, to release a large number of cement hydration heat, and the other is the elastic modulus of coagulation dramatic changes. Modulus of elasticity as a result of changes within this period in the formation of residual stress in the concrete.(2) medium-term: from the basic role of cement heat until the end of the stable temperature of the concrete cooling time, during this period, the temperature stress was mainly due to cooling and the outside concrete caused by temperature changes, stress and early formation of these residual stress superposition phase, during which the coagulation of the elastic modulus changed little.(3) late: concrete completely cooling period after the operation. Thermal stress is mainly caused by external temperature changes, the stress and the first two-phase superposition of residual stress.Under the thermal stress caused by the reasons can be divided into two categories:(1) self-stress: there is no constraint on the border or completely static structure, if the internal temperature distribution is nonlinear, due to structural constraints arising from their co-temperature stress. For example, the conversion layer of its relatively larger size, concrete cooling surface temperature low, the internal temperatures are high, the surface tensile stress, compressive stress appears in the middle.(2) bound by stress: the structure of all or part of the boundary bound by the outside world can not be free-form deformation caused by stress. Roof box,共12 页such as concrete and concrete barrier.Both the temperature and the concrete stress is often caused by shrinkage of the combined effect of stress.Known to be in accordance with an accurate analysis of the temperature of the thermal stress distribution, size is a more complex task. In most cases, the need to rely on model test or numerical calculation. Creep of concrete so that the temperature there is considerable stress relaxation, thermal stresscalculation, we must consider the effects of creep, is no longer calculated in detail here.3. temperature control and measures to prevent the cracksIn order to prevent cracking, reduce the thermal stress can control the conditions of temperature and to improve the binding of two aspects.Temperature control measures are as follows:(1) used to improve the aggregate gradation, dry hard concrete, mixed mixture, add air-entraining agent or plasticizer, etc. measures to reduce the amount of cement concrete;(2) mixing concrete by adding water or cooling water will be gravel and pouring concrete to reduce the temperature;(3) pouring hot days to reduce the pouring of concrete thickness, the use of pouring heat levels;(4) laid in concrete water pipes, access to cold water to cool;(5) the provisions of reasonable time, the temperature drop when the surface insulation, concrete surface in order to avoid a sharp temperature gradient;(6) Construction of long-term exposure to block the surface of the concrete pouring, or thin-walled structures, thermal insulation in the cold season to take measures;Measures to improve the constraints are:共12 页(1) a reasonable sub-block joints;(2) basis to avoid too much ups and downs;(3) reasonable arrangements for the construction process, to avoid excessive side elevation and long-term exposure;In addition, to improve the performance of concrete to improve theanti-cracking ability, to strengthen the conservation, to prevent surface drying, in particular, is to ensure the quality of concrete is very important to prevent cracks, should pay special attention to avoid cross-cracks appears to restore the integrity of its structure it is very difficult, so the construction should be to prevent the occurrence of cross-cutting the main crack.In concrete construction, in order to increase the turnover rate of the template, often require new pouring concrete as soon as possible. When the concrete temperature is higher than the temperature should be appropriate to consider time, so as to avoid the early cracks in the concrete surface. New pouring early, a lot of the surface tensile stress, a "temperature shock" phenomenon. Concrete pouring in the early heat of hydration as a result of the dissemination of the surface caused by a large tensile stress, when the surface temperature is higher than the temperature at this time to remove the template, a sharp fall in surface temperature is bound to lead to temperature gradient, so an additional one on the surface tensile stress, thermal stress superposition and hydration, coupled with the shrinkage of concrete, Tensile stress to reach the surface of great value, there is the danger oflead to cracks, but if in a timely manner after the removal of the template on the surface coverage of a light insulating material, such as foam sponge and so on, have a concrete surface to prevent excessive tensile stress, with significant results.Reinforced concrete on the large volume of thermal stress has little effect because the large volume of concrete reinforced with a very low rate. Only on 共12 页the general impact of reinforced concrete. Not too high in temperature and stress below the yield limit under the condition of the properties of steel is stable, and with the stress, time and temperature has nothing to do. Linear expansion coefficient of steel and concrete linear expansion coefficient difference between the small changes in temperature between the two with only a very small stress. Since the modulus of elasticity of steel to concrete elastic modulus of 7 ~ 15-fold, when the stress reached the tensile strength of concrete and cracking, the steel stress will not exceed 100 ~ 200kg/cm2 .. So , Want to use in reinforced concrete to prevent the emergence of small cracks is difficult. However, after the reinforced structure of the number of cracks in general has become more than a small distance, a smaller width and depth. And if the diameter of steel thin and close spacing, the crack resistance of concrete to enhance the effect of better. Concrete and reinforced concrete structure of the surface often occur cracks in thin and shallow, most of them belonging to shrinkage cracks. While this is generally shallow cracks, but itsstrength and durability of the structure is still a certain impact.In order to ensure the quality of concrete to prevent cracking and improve the durability of concrete, the proper use of admixtures is also one of the measures to reduce cracking. Such as the use of anti-cracking agent and water, in practice, its major role in concluding as follows:(1) the existence of a large number of pores in the concrete that, after evaporation of water generated by capillary capillary tension, deformation of the concrete shrinkage. Pores increased capillary diameter can reduce the surface tension, but would reduce the strength of concrete.(2) the impact of water-cement ratio is an important factor for concrete shrinkage, the use of anti-cracking agent can reduce water consumption reduced by 25% concrete.(3) the amount of cement concrete is also an important factor in shrinkage,共12 页water addition and subtraction mixed concrete cracking agent in maintaining the strength of concrete under the condition of 15 percent can reduce the amount of cement, aggregate size, by increasing the amount to supplement.(4) anti-cracking agent and water can improve the consistency of cement slurry to reduce the bleeding of concrete, reduce shrinkage deformation Shen.(5) to improve and cement bonded aggregate, and enhance theanti-cracking performance of concrete.(6) concrete bound in the contraction produced by tensile stress, when the tensile stress is greater than the tensile strength of concrete will be produced when the cracks. Water-reducing agent can be an effectiveanti-cracking of the concrete tensile strength to increase, a substantial increase in anti-cracking performance of concrete.(7) mixing-compacting concrete admixtures can, and can effectively improve the carbonation resistance of concrete to reduce the carbonation shrinkage.(8)-doped water-reducing agent after the concrete cracking retardation time due, in the effective prevention of the rapid hydration heat of cement based on cement to avoid long-term result of non-condensable increase plastic shrinkage.(9)-doped workability of concrete admixtures, and easy to find flat surfaces to form a micro-membrane to reduce evaporation and reduce drying shrinkage.Many have a retarding admixture to increase the workability and improve the function of plasticity, we in engineering practice in this area should be more contrast and research experiments than simply relying on external conditions to improve may be even more simple and economic.4. early concrete conservationPractice has proved that the common concrete cracks, the majority ofsurface cracks at different depths, mainly because of the temperature gradient caused by the cold temperature region is also vulnerable to a sharp fall in the formation共12 页of cracks. Insulation so that the concrete surface to prevent early cracking is particularly important.Thermal stress from the point of view, the insulation should meet the following requirements:(1) to prevent the concrete inside and outside the concrete surface temperature difference and gradient, to prevent surface cracks.(2) to prevent the concrete super-cold, it should be possible to make concrete the construction period of not less than the minimum temperature of concrete used for the stability of the temperature.(3) to prevent cold-old concrete in order to reduce the concrete between the old and new constraints.Early concrete conservation, the main objective is to maintain the appropriate temperature and humidity conditions in order to achieve the effect of two aspects, on the one hand, the concrete from adverse temperature and humidity deformation invasion to prevent the harmful and drying shrinkage. On the one hand, to enable the smooth progress of cement hydration, with a view to meet the design capacity of the strength and crack resistance.Appropriate conditions of temperature and humidity are interrelated. Coagulation on the insulation often has the effect of moisture.Theoretical analysis of fresh concrete contained in the water fully meets the requirements of cement hydration and more than. However, due to evaporation and other factors often cause water loss, thereby delay or prevent the hydration of cement, concrete surface and most likely to be directly affected by such a negative impact. Concrete pouring, therefore the first few days after the critical period of conservation in the construction should pay attention to.5. concluding remarksAbove the temperature of concrete and cracks in the construction of the 共12 页relation between theory and practice of the preliminary study, although the academic community about the causes of cracks in concrete and calculation methods are different theories, but specific measures to prevent and improve the opinion it is quite uniform At the same time, the application in practice is also a relatively good effect, concrete construction and more depends on our observation, and more, when compared to multi-issue analysis, and more sum up, combined with a wide range of prevention measures, the cracks in the concrete is completely avoided.论混凝土的施工温度与结构裂缝1.裂缝的原因混凝土中产生裂缝有多种原因,主要是温度和湿度的变化,混凝土的脆性和不均匀性,以及结构不合理,原材料不合格(如碱骨料反应),模板变形,基础不均匀沉降等。
低热硅酸盐水泥改善大体积混凝土抗裂性能研究

金属 的体 积大 得多 , 铁锈 体积膨 胀 , 对周 围混凝 土产 生 挤压 , 使混 凝土 胀裂 。 ( )有 的混凝 土虽 然 设 计抗 裂 强 度 高 , 由于 原 8 但
超 出混凝 土 的抗 裂 能力 时 , 就会 出现 裂缝 。 ( )混凝 土塑性 塌落 引起 的裂缝 。 2
1 大 体 积 混 凝 土 出现 裂 缝 的 原 因及 处 理 措 施
1 1 出现 裂 缝 的原 因 。
( )温 度 应 力 产 生 的 裂 缝 。混 凝 土 在 硬 化 期 间 经 1
( )当结构 的基 础 出 现不 均 匀 沉 陷 , 有 可 能产 6 就
生 裂缝 , 随着 沉 陷的进一 步 发展 , 裂缝会 进 一步扩 大 。
第4 卷 第 l l 8期 2 0 10 年 9 月 文 章 编 号 :0 1— 1 9 2 1 ) 8— 0 3— 3 10 47 (0 0 1 0 7 0
人 民 长 江
Ya g z Rie n te vr
Vo . 1 41. No. 8 1 S p., e 2 0 01
( )混凝 土加 水 拌 和后 , 泥 中 的碱 性 物质 与 骨 3 水 料 中活性 氧化 硅 等起 反应 , 出 的胶 状 碱 一硅胶 从 周 析 围介 质 中吸水膨 涨 , 体积 增大 3倍 , 而使混 凝土涨 裂 从 产生 裂缝 。
复杂 、 资大 、 投 一旦 发 生 质 量 问题 , 果 严 重 。而 目前 后 大 体积混 凝土 由于施 工 中 的各种 原 因易 产 生 裂缝 , 严 重 危害工 程质 量 , 大体 积混凝 土施 工 的技 术难 点 。 是 本文结 合 四川大 渡 河 深溪 沟 水 电站 工程 , 大体 就
收 稿 日期 :0 0— 7— 0 2 1 0 3
外文翻译---浅谈混凝土的施工过程中温度与裂缝控制
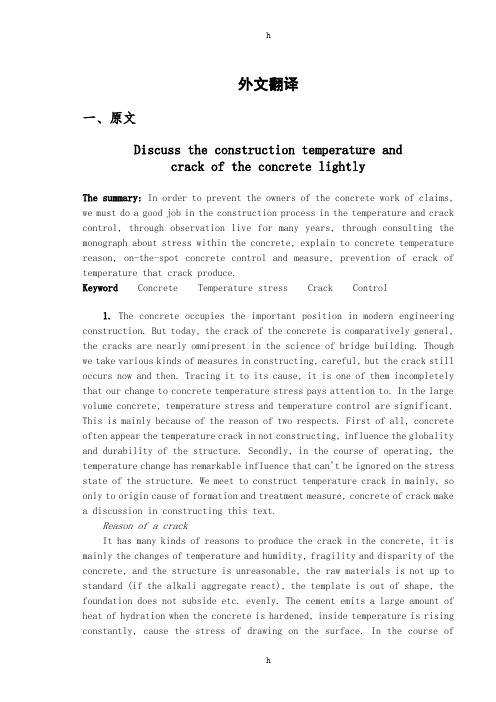
外文翻译一、原文Discuss the construction temperature andcrack of the concrete lightlyThe summary: In order to prevent the owners of the concrete work of claims, we must do a good job in the construction process in the temperature and crack control, through observation live for many years, through consulting the monograph about stress within the concrete, explain to concrete temperature reason, on-the-spot concrete control and measure, prevention of crack of temperature that crack produce.Keyword Concrete Temperature stress Crack Control1. The concrete occupies the important position in modern engineering construction. But today, the crack of the concrete is comparatively general, the cracks are nearly omnipresent in the science of bridge building. Though we take various kinds of measures in constructing, careful, but the crack still occurs now and then. Tracing it to its cause, it is one of them incompletely that our change to concrete temperature stress pays attention to. In the large volume concrete, temperature stress and temperature control are significant. This is mainly because of the reason of two respects. First of all, concrete often appear the temperature crack in not constructing, influence the globality and durability of the structure. Secondly, in the course of operating, the temperature change has remarkable influence that can't be ignored on the stress state of the structure. We meet to construct temperature crack in mainly, so only to origin cause of formation and treatment measure, concrete of crack make a discussion in constructing this text.Reason of a crackIt has many kinds of reasons to produce the crack in the concrete, it is mainly the changes of temperature and humidity, fragility and disparity of the concrete, and the structure is unreasonable, the raw materials is not up to standard (if the alkali aggregate react), the template is out of shape, the foundation does not subside etc. evenly. The cement emits a large amount of heat of hydration when the concrete is hardened, inside temperature is rising constantly, cause the stress of drawing on the surface. In the course oflowering the temperature, is it congeal foundation pay restrain to mix always later stage, will present the stress of drawing within the concrete. Reducing of temperature can surface cause heavy stress of drawing very in concrete too. When these draw the stress and go beyond resisting the ability of splitting of concrete, namely will present the crack. A lot of inside humidity ofconcrete change very light or change relatively slow, surface humidity might change heavy the violent change takes placing. Such as maintaining thoroughly, when getting wetter when not doing, contract surface there aren't deformation doing, often cause the crack too. The concrete is a kind of fragility material, tensile strength is about 1/10 of the compression strength, is it carry on one's shoulder or back limit when draw out of shape to have (0.6~1.0)×104 only, is it carry on one's shoulder or back limit location when stretch out of shape to there is(1.2~2.0)×104 to add for a long time to add a short time. Because raw materials even, water dust than unstable, transport and build phenomenon of emanating of course, its tensile strength is not even in the same concrete, a lot of resist the ability of drawing very low, it is apt to present the weak position of the crack. Among armored concrete, draw stress to undertake by reinforcing bar mainly, concrete bear stress of keeping just. Or reinforcing bar mix if edge position gone to congeal presents the stress of drawing in the structure in plain concrete must rely on the concrete oneself to bear. Require avoiding the stress of drawing or only very small stress of drawing appears of the general design. But the concrete is cooled from maximum temperature to the steady temperature of operating period in constructing, often cause sizable to draw the stress within the concrete. The temperature stress can exceed other outsides and load the stresses caused sometimes, know change law, temperature of stress for carry on reasonable structural design and construct extremely important.Analysis of 2 temperature stressesIt can be divided into following three stages according to the forming process of the temperature stress:(1)It is early: It needs generally 30 day from beginning building concrete to finishing sending out heat basically by cement. There are two characteristics at this stage, first, the cement emits a large amount of heat of hydration, second, mix and congeal the changing sharply of elastic model quantity. Because of the change of elastic model quantity, form the remaining stress in the concrete in this period.(2)Middle period: Up till the concrete is cooled until stability temperature from cement send out heat function basically when expiring, in this period, the temperature stress is mainly because the cooling of the concrete and external temperature change cause, these stresses and remnants stresses that is formed in early days are superposed, mix and congeal the elastic mould amount that goes to and does not change much during this period.(3)Later period: Operation period after the complete cooling of concrete. Temperature stress whether external temperature change causes mainly, these stresses and first two kinds of remnants stresses are changed and added.It can be divided into two kinds according to the reason why the temperature stress causes:(1)Spontaneous stress: There are not any restraints or totally static structure at the border, if inside temperature is non-linear distribution, temperature stress appearing because structure restrains from each other. For example, the body of mound of the bridge, the physical dimension is relatively large, surface temperature is low when the concrete is cooled, inside temperature is high, present the stress of drawing on the surface, present the stress of pressing in the middle.(2)Restrain the stress: All of the structure ones or it restrain external one some border, can't out of shape and stress not cause not free. Such as case beam roof concrete and guardrail concrete.These two kinds of temperature stresses draw back stresses caused to act on with the doing of concrete together frequently. It is a more complicated job to want to analyse the distribution, size of the temperature stress accurately according to known temperature. In case of great majority, need to rely on the model test or the number value to calculate. To is it make temperature stress have sizable limp to creep concrete, at the stress accounting temperature, must consider the influence that creep, calculate concretely that no longer states thinly here.Control and preventing the measure of the crack of 3 temperatureFor prevent crack, lighten temperature stress can from control temperature and is it is it set about to restrain terms from two to improve.The measure of controlling temperature is as follows:(1)Is it improve aggregate grade mix, is it do rigid concrete to spend, mix mixture to adopt, is it guide angry pharmaceutical or plastification pharmaceutical, etc. measure in order to reduce cement consumption of concrete to add;(2)Add water or the water to cool the broken stone in order to reduce the temperature of building of the concrete while mixing and shutting the concrete;(3)Reduce the thickness of building while building the concrete on hot day, utilize and build the aspect to dispel the heat;(4)Bury the water pipe underground in the concrete, enter the cold water to lower the temperature openly;(5)Stipulate rational form removal time, the temperature keeps warm the surface while lowering suddenly, in case that the rapid temperature gradient takes place in the concrete surface;(6)The concrete with medium and long-term and exposed construction buildsa piece of surface or thin wall structure, take the measure of keeping warm in cold season;The measure of improving condition of restraining is:(1)Divide and sew and divide one rationally;(2)Prevent the foundation from rising and falling too big;(3)Rational arrangement construction process, prevent the too big discrepancy in elevation and side from exposing for a long time;In addition, improve the performance of the concrete and improve and resist the ability of splitting, strengthen maintenance, prevent the surface from being done and contracted, especially guarantee the quality of the concrete is very important to preventing the crack, should pay special attention to avoiding producing and running through the crack, the globality resumed its structure after appearing is very difficult, so should rely mainly on preventing the emergence of the running through crack while constructing.In construction of concrete, for raise turnover rate of template, demand concrete form removal as soon as possible that build newly often. Should consider form removal time properly when concrete temperature is higher than the temperature, so as not to cause the superficial early crack of concrete. Building the early form removal newly, cause very large stress of drawing on the surface, the phenomenon that "temperature is assaulted" appears. Build initial stage in concrete, because heat of hydration is sent out, the surface causes sizable to draw the stress, surface temperature is also higher than temperature at this moment, remove the template at this moment, surface temperature is lowered suddenly, must cause temperature gradient, thus add and draw the stress on the surface, change and add with the heat of hydration stress, in addition, the concrete dries and contracts, the superficial stress of drawing reaches very great number value, have danger of causing the crack, but cover a light-duty heat insulator with on the surface in time after removing the template, for instance foam sponge, etc. , for prevent concrete surfacefrom produce the too big stress of drawing, have remarkable results.Add muscle influence to large volume temperature stress of concrete very light, because large volume concrete include muscle to be rate very much low. Just have influence on the general armored concrete. On terms that temperature is not very high and the stress is less than limit of surrendering, every performance of the steel is steady, and have nothing to do with stress state, time and temperature. Line bloated coefficient of steel and concrete line bloated coefficient difference very light, take place little internal stress very only between the two while changing in temperature. Because elastic mould amount of steel concrete elastic mould 7~15 of quantity, reach as interior concrete stress tensile strength and when fracturing, the stress of the reinforcing bar will not exceed 10000kg/cm2. So is it is it prevent tiny appearance difficulty very much of crack from to make use of reinforcing bar to want among concrete. But the crack in the structure generally becomes numerous, the interval is little, the width and depth are smaller after adding the muscle. And if diameter of reinforcing bar detailed and when interval dense, to improve concrete resist result of person who split better. Concrete and surface, armored concrete of structure can take place detailed and shallow crack often, among them the great majority belong to and do and draw back the crack. Though this kind of crack is generally all relatively light, it stills have certain influence on the intensity and durability of the structure.In order to guarantee concrete project quality, prevent fracturing, improve the durability of the concrete, use the admixture to reduce one of the measures that fractures correctly. Whether is it reduce water is it split pharmaceutical to defend, I summarize his main function in practice to use.(1)There is a large number of capillary in the concrete, produce capillary tension in the capillary after water is evaporated, make concrete is it contract out of shape to do. Increasing the thin aperture of hair can reduce the capillary surface tension, but will make the intensity of concrete reduce. This surface tension theory has already been confirmed in the world as far back as the sixties.(2)Water dust than influence important factor that concrete shrink, is it reduce water is it split pharmaceutical can make concrete water consumption reduce by 25% to defend to use.(3)Cement consumption important factor, concrete of person who shrink too, is it add and subtract water is it split concrete reducible 15% of the cement consumption on terms that keep the intensity of concrete of pharmaceutical to defend to mix, its volume is supplemented by increasing aggregate consumption.(4)Reduce water is it split pharmaceutical can improve consistency of grout, reduce concrete secrete ink to defend, reduce and sink and draw back deforming.(5)Improve gluing the strength of forming of the grout and aggregate, the concrete improved resists the performance of splitting.(6)Concrete is it produce stress of drawing to restrain from while shrinking, crack when drawing the stress and is greater than concrete tensile strength can produce. Reduce water is it split pharmaceutical effective concrete tensile strength of improvement very to defend, improve resisting the performance of splitting of concrete by a wide margin.(7)It can make the concrete density good to add the admixture to mix, can improve resisting carbonization of concrete effectively, reduce carbonization to shrink.(8)Is it reduce water is it split slow coagulation time proper concrete under pharmaceutical to defend, on the basis of preventing the fast water of cement from sending out heat effectively to mix, prevent the plasticity shrink that brings because the cement is not congealed for a long time from increasing.(9)Mix admixture concrete and getting easy and kind, surface easy to feel flat, form little membrane, reduce the moisture to evaporate, reduce drily and shrink. A lot of admixtures all have the functions of slow coagulation, increasing and apt, improvement plasticity, the experiment that we should carry on in this respect more in the project practice is compared with and studied, than lean against not improving terms more simple, may getting simple and more direct, economy.Early maintenance of 4 concretePractice has proved, the common crack of concrete , most is the surface crack of different depth, main reason its whether temperature gradient cause cold temperature of area lower too easy to form crack suddenly. So say the warm-keeping of the concrete is especially important to preventing the early crack of surface.From the viewpoint of temperature stress, should reach and require keeping warm following:1)Prevent concrete internal and external temperature poor and concrete surface gradient from, prevent the surface crack.2)Prevent concrete from to be ultra and cold , should is it is it make the minimum temperature is not lower than the steady temperature of concrete service time construction time in concrete to try to try one's best.3)Prevent the old concrete subcooling, in order to reduce the restraint among the old and new concrete.The early maintenance of the concrete, the main purpose lies in keeping the suitable warm and humid condition, in order to get the result of two respects, on the other hand make the concrete avoid the invasion and attack of the unfavorable and warm, humidity out of shape, the ones that prevent from harmfully are cold to contract and do to contract. On one hand make cement water function go on smoothly, is in the hope of reaching the intensity designed and resisting the ability of splitting.The suitable warm damp condition is interrelated. Mix warm-keeping measure paid to congeal often protects wet results too. Analyse, water concrete include moisture can meet demand, cement of water have enough and to spare newly theoretically. But because the reason of evaporating etc. often causes losses of the moisture, thus postpone or hinder water of the cement from, the surface concrete receives this kind of adverse effect easiestly and directly. Key period when maintained in initial a few days after so the concrete is built should pay attention to conscientiously in constructing.2. Quality control of waterproof concrete constructionCombined with experience, from formwork design, fabrication and installation, assembling reinforcement, pouring and curing of concrete and other aspects construction technology of fair-faced concrete is introduced as well as quality control measures and standards in order to reduce engineering cost to acquire satisfied economic and social benefits.The factors of influencing waterproof-concrete quality are very many. Any links does not pay attention to the water-proof concrete of field loss hinders the water function without exception jointly with degree. Engineering construction in the basement adopts secondary form board fabrication and installation, reinforced bar fabrication and bind, concrete stirring and mixing system and transport, concrete covibration beat with a stick, construction joint practice, concrete curing and dismantle model and being ready for backfill and so on aspects. These are very critical to quality method to ensure that water-proof concrete self water-proof, and the way of practicehas wan out.Method being under construction2.1 Fabrication and InstallationAccording to the concert of closely knit, demand of reason why to form board since the water-proof also concrete have made and have assembled corresponding rise is special, be to require that not leaving out thick fluid, firm closely knit block of wood deformation, water absorption Character should be small and ought to give priority to select and using bamboo slab rubber form board or the steel form.. Strict control form board room gap size, necessary exceeding 2 mms uses foam rubber or plastic to squeeze a crack in, porous form board nonutility without exception to board face Be ready for wall post at the same time rotting the prevention and cure job adopt the cement mortar pouring same, indicia in before the root segment sticking the foam rubber or plastic strip, the bottom puts on a cement mortar, concrete a concrete, first 5cm~10cm. Since water-proof, concrete structure wall thickness is mostly more infertile. Be to ensure that component geometry dimension, Chang adopt the inside and outside bolt to pull the measure meeting attention to, responds to on play receive bolt centre interpose stop water iron plate, to prevent water from forming pilotage passage along bolt leakage.2.2 Assembling reinforcementWater-proof concrete structure has demanding as follows to the reinforced bar:1)Reinforced bar should adopt twisted steel as far as possible, increases by hold wrap a force composing in reply a water ability2)Reinforced bars connect should try one's best to adopt to solder connection, stop using and being needless to bind connection to the full3)When binding a reinforced bar, the iron wire head responds to inner bending.4)Strict control reinforced bars protective layer thickness.Minimal thickness of water-proof concrete reinforced bar protective layer is not smaller than 25mms, the protective layer welcoming water surface especially inadmissibility to disappoint error. The iron wire and reinforced bar that application buries in advance within mortar piece while using mortar heel block as protective layer, are bound solid. When the cavalry puts up the fixed reinforced bar if adopt a reinforced bar, also need to increase solders water iron plate or fixation just goes ahead, to strengthen water-proof effect in the heel block. This project uses new materials nylon to have fixed there is an effect's had guarded against reinforced bar protective layer deviation piece big mass common failings.2.3 The concrete stirring and mixing makes and transportsSince the water-proof concrete requires that higher closely knit, reason why stir and mix system also need to have the fairly good homogeneity, should be ready for burning as follows almost for this purpose:1)Ensures that mixing time, mixing at every time are secondary jump intoa expect the general ejection of compact block of wood less than 2mins.2)Should use the apposition agent, the solution queen who should manufacture certain thickness from apposition agent adds the mixer inner, the dried powder or high concentration solution will add an agent extra not to adds the mixer inner directly, prevent from mixing is uneven but part concentrates, both lose the apposition agent effect, and affect concrete mass.3)Responds to the assured source of life degree having a spot test on the admeasurement concrete at the regular intervals collapsing in the process being under construction, construction is middle if Yu rains or other cause, respond to the ratio determining whose water ratio, and adjusting the composition being under construction in time when change happened in sandstone moisture content.4)Project uses the commodity concrete, has boundary have raised a concrete stirring mass and of all kinds effect apposition agent adulterating falls when amounts, the water ash having controlled a concrete strictly collapsing.5)Concretes adopt a pump to have given handicraft, effective avoiding a concrete producing the phenomenon isolating bleeding and leaving out thick fluid in the process of transportation.2.4 Matters needing attention in being under construction1)Construction school assignment soft and floury is divided. Water-proof concreting should stratify strictly being in progress, and a continuous construction is completed The front and back and high and low connect between the tier should subjugate within the cement initial setting time, For this purpose, with handling a worker dividing into several, at the same time each other, school assignment group faces or it is all right for each other, carry on the back.2)Achieve strictly fixed point determines the amounts of the components of a substance material down According to the vehicle capacities stratifying concrete altitude and the means of transport, the quantify carrying out fixed point strictly is able to go down one important ring expecting that this is to improve water-proof concreting mass.3)Concretes vibrating beat one important ring being to ensure that the concrete is closely knit, defend against to seep with a stick. Also, should adopt fixed point vibrating, handle meticulously on basis expecting that under determining the amounts of the components of a substance homogeneously in fixed point. Pay attention to high and low tier of linking up. Now that needing to prevent from miss and vibrating, not vibrating enough, being going to prevent a fault from vibrating again, Need to forbid using prying the method coming to aid to vibrate moving a reinforced bar or shaking a reinforced bar especially, such separates to making the front already concrete the reinforced bar and concrete shaking the reality part, causes serious consequences.4)Being ready for the assured source of life degree taking over thick fluid measure, and adjusting in time to collapse seriously. Average water-proof concrete structure construction, the construction joint being under construction respectively, composing namely on erecting wall sells be bottom board and vertical wall at reduced prices. Should irrigate thick a layer of 5cm~10cms surname indicia cement mortars in seam place first linking up closely knitting tier, in order to ensuring that the seam place vibrates when concrete vertical wall. Simultaneous, improve step by step with concrete an altitude, should fall off step by step with the water yield, diminish collapsing to fall degree prevent from concrete insist to be short but the cement paste is partial to much phenomenon to aggregate appearing on upper part.2.5 Dismantling model and curing of concreteThe water-proof concreting queen maintains goodness and badness working, not only affecting the intensity arriving at a concrete, moreover the impervious function affecting to the concrete. Evidence, water-proof concrete early phase dehydration or curing process lack for water, will reduce whose impervious function by a wide margin. Water-proof concrete curing responds to the block of wood less than 14ds. The water-proof concrete dismantles a model demanding to be unable to compare high, dismantle model time unsuitable untimely, respond to when dismantling a model handle meticulously, prevent an iron rod from using to pry stiffly, that the sledgehammer is knocked suddenly and forcibly pries, uses a concrete meet with destroy.2.6 Do good well at backfillWater-proof architectural backfill is a final working procedure, it be sometimes ignored, this is a very big faults in fact under the ground. When the water-proof structure job is over queen responds to the construction carrying out backfill immediately. Most important, we should take backfill seriously self mass; Secondly, backfill varia and ponding should clear up the pit bottom in the front, respond to densification with layers when backfill. Water-proof structure vicinity layer pounds true backfill, self is a reliable and economical as well water proofing drapery under the ground. In project basement engineering construction Shanghai, since organizing water proofing down to earth strictly with all above seven passes, the concrete is under construction, effect is comparatively ideal. The percolating water phenomenon does not appear.ConclusionsConstruction temperature and relation of crack in concrete the above carry on preliminary discussion of theory and practice, though the academia has different theories to origin cause of formation and computing technology of the concrete crack, but to concrete prevention and improving the measure suggestion to relatively unify, application in practice result fine too at the same time, concrete to is it observe, compare more by us to want in constructing, analyse more, summarize more after going wrong, combine many kinds of prevention and deal with the measure, the crack of the concrete can be avoided.一、翻译浅谈混凝土的施工过程中温度与裂缝控制摘要为了防止业主对混凝土工程的索要赔偿,我们就必须做好过程中的温度与裂缝控制。
- 1、下载文档前请自行甄别文档内容的完整性,平台不提供额外的编辑、内容补充、找答案等附加服务。
- 2、"仅部分预览"的文档,不可在线预览部分如存在完整性等问题,可反馈申请退款(可完整预览的文档不适用该条件!)。
- 3、如文档侵犯您的权益,请联系客服反馈,我们会尽快为您处理(人工客服工作时间:9:00-18:30)。
外文翻译Anti-Crack Performance of Low-HeatPortland Cement ConcreteAbstract: The properties of low-heat Portland cement concrete(LHC) were studied in detail. The experimental results show that the LHC concrete has characteristics of a higher physical mechanical behavior, deformation and durability. Compared with moderate-heat Portland cement(MHC), the average hydration heat of LHC concrete is reduced by about 17.5%. Under same mixing proportion, the adiabatic temperature rise of LHC concrete was reduced by 2 ℃-3℃,and the limits tension of LHC concrete was increased by 10×10-6-15×10-6than that of MHC. Moreover, it is indicated that LHC concrete has a better anti-crack behavior than MHC concrete. Key words: low-heat portland cement; mass concrete; high crack resistance; moderate-heat portland cement1 IntroductionThe investigation on crack of mass concrete is a hot problem to which attention has been paid for a long time. The cracks of the concrete are formed by multi-factors, but they are mainly caused by thermal displacements in mass concrete[1-3]. So the key technology on mass concrete is how to reduce thermal displacements and enhance the crack resistance of concrete.As well known, the hydration heat of bonding materials is the main reason that results in the temperature difference between outside and inside of mass concrete[4,5]. In order to reduce the inner temperature of hydroelectric concrete, several methods have been proposed in mix proportion design. These include using moderate-heat portland cement (MHC), reducing the content of cement, and increasing the Portland cement (OPC), MHC has advantages such as low heat of hydration, high growth rate of long-term strength, etc[6,7]. So it is more reasonable to use MHC in application of mass concrete.Low-heat portland cement (LHC), namely highbelite cement is currently attracting a great deal of interest worldwide. This is largely due to its lower energy consumption and CO2 emission in manufacture than conventional Portland cements.LHC has a lot of noticeable properties, such as low heat of hydration excellent durability,etc, so the further study continues to be important[8-10]. The long-term strength of C2S can approach to or even exceed that of C3S[11]. In addition, C2S has a series of characteristics superior to C3S. These include the low content of CaO, low hydration heat, good toughness, compact hydration products, excellent resistances to chemical corrosion, little dry shrinkage, etc[12,13].For hydroelectric concrete , the design requirements have some characteristics, such as long design age, low design strength, low hydration temperature rise, and low temperature gradient[14]. All these requirements agree with the characteristics of LHC. Furthermore, LHC has a high hydration activity at later ages, the effect of which can improve the inner micro-crack. Based on above-mentioned analyses, the properties of low-heat Portland cement concrete were studied in detail in this paper. Compared with the moderate-heat Portland cement (MHC) concrete, the anti-crack behavior of LHC concrete was analyzed.2 ExperimentalMHC was produced in Gezhouba Holding Company Cement Plant, China; and LHC was produced in Hunan Shimen Special Cement Co. Ltd., China. The chemical compositions and mineral compositions of cement are listed in Table 1 and Table 2 respectively, and the physical and mechanical properties of cement are listed in Table 3.In spite of a little difference in chemical compositions, there is an obvious dissimilarity between the mineral component of LHC and that of MHC because of the different burning schedule. The C3S (Alite) content of MHC is higher than that of LHC, and the C2S (Belite) content of LHC is higher than that of MHC. Alite is formed at temperatures of about 1 450 ℃, while Belite is formed at around 1 200 ℃. Therefore, LHC can be manufactured at lower kiln temperatures than MHC. And the amount of energy theoretically required to manufacture LHC is lower than that of MHC.Belite hydrates comparatively slowly, and the early compressive strengths of pastes, mortars, and concretes containing LHC are generally lower as a result. The long-term strength and durability of concrete made from LHC can potentially exceed those of MHC. The results from Table 3 show that the early strength of LHC pastes is lower than that of MHC pastes, and that the strength growth rate of LHC is higher than that of MHC.The hydration heat of bonding materials was tested. Class I fly ash of bonding materials came from Shandong Zhouxian Power Plant, China. The experimental results shown in Table 4 indicate that the hydration heat of LHC is much lower than that of MHC. The 1-day, 3-day and 7-day hydration heat of LHC without fly ash is 143 kJ/kg, 205 kJ/kg, 227 kJ/kg, respectively. The 1-day, 3-day and 7-day hydration heat of MHC without fly ash is 179 kJ/kg, 239 kJ/kg, 278 kJ/kg, respectively. Compared with MHC, the average hydration heat of LHC concrete is reduced by about 17.5%. Obviously, low hydration is of advantage to abate the pressure to temperature control, and to reduce the crack probability due to the temperature gradients. The adiabatic temperature of LHC concrete and MHC concrete was tested. As a result, the adiabatic temperature rise of LHC concrete is lower than that of MHC concrete and the different value ranges from 2 ℃to 3 ℃in general.After adding fly ash, all specimens show a lower hydration heat, and it decreases with increasing fly ash content. For MHC with 30% fly ash, the 1 d, 3 d, 7d accumulative hydration heat is reduced by 14.5%, 20.5%, 21.9%, respectively; and for LHC with 30% fly ash, the 1 d, 3 d, 7 d accumulative hydration heat is reduced by 21.7%, 26.3%, 23.3%, respectively. Obviously, the effect of fly ash on the hydration heat of LHC is more than that of MHC. It is well known that the fly ash activation could be activated by Ca(OH)2. LHC has a lower content of C3S and a higher content of C2S than MHC, so the Ca(OH)2, namely the exciter content in hydration products of LHC pastes is lower. Decreasing the hydration activation of fly ash reduces the hydration heat of bonding materials.3 Results and DiscussionIn this experiment, ZB-1A type retarding superplasticizer and DH9 air-entraining agent were used. The dosage of ZB-1 was 0.7% by the weight of the blending, and the dosage of DH9 was adjusted to give an air-containing of 4.5% to 6.0%. The parameters that affected the dosage included the composition and the fineness of thecement used, and whether the fly ash was used. Four gradations of aggregate were used,120 mm-80 mm: 80 mm-40 mm: 40 mm-20 mm: 20 mm-5 mm=30:30:20:20.The term water-to-cementitious was used instead of water-to-cement, and the water-to-cementitious ratio was maintained at 0.50 for all the blending. The slump of concrete was maintained at about 40 mm, and the air content was maintained at about 5.0% in the experimental. After being demoulded, all the specimens were in a standard curing chamber. The mix proportion parameter of concrete is listed in Table 5.3.1 Physical and mechanical propertiesThe physical and mechanical properties include strength, elastic modulus, limits tension, and so on. The results of strength shown in Table 6 indicate the early strength (7 d curing ages) of LHC (odd samples) concrete increases slowly. The ratio between 7 d compressive strength and 28 d compressive strength of LHC concrete is about 0.4, while for MHC concrete the ratio is about 0.6. Compared with MHC concrete, the growth rate of strength of LHC concrete becomes faster after 7 d curing ages. The compressive strength for 28 d, 90 d, 180 d curing ages of LHC concrete containing 20% of fly ash is 30.2 MPa, 43.8 MPa, 48.5 MPa, respectively, while that of MHC concrete containing 20% of fly ash is 28.3 MPa, 35.6 MPa, 39.8 MPa, respectively. The content of C2S in LHC is higher than that in MHC, which results in the above-mentioned difference.Table 6 shows that the strength growth rate of concrete made with fly ash blended cements is higher than that of blank specimens; the more the dosage of fly ash, the higher the growth rate. Fly ash has a glassy nature, which can react with Ca(OH)2. Since Ca(OH)2 is a hydration product of cement, the reaction between fly ash and Ca(OH)2, called “secondary hydration”, will happen at latish ages. The magnitude of Ca(OH)2 is affected by some factors, such as the water-to-cementitious, the dosage of cement.The elastic modulus and the limits tension of concrete are given in Table 7. Under same mixing proportion, the elastic modulus of LHC concrete is approximately equal to that of MHC; the 28-day limits tension of LHC concrete is increased by 10×10-6 to 15 ×10-6 than that of MHC, and the 90-day limits tension of LHC concrete is increased by 12×10-6 than that of MHC concrete. The above results show that the use of LHC improves the limits tension of concrete. Increasing the limits tension of concrete will be benefit to the crack resistance of concrete.3.2 Deformation characteristicsDeformation characteristics of concrete include drying shrinkage, autogenous deformation, creep, etc. The drying shrinkage of concrete is shown in Fig.1. The drying shrinkage increases with age. At early ages a up to 90 days, all the LHC concrete specimens show a lower drying shrinkage; and it decreases with increasingthe fly ash content. When containing 30% of fly ash, the drying shrinkage of LHC concrete is 363 ×10-6 at 90 days, while for MHC concrete the value is 408×10-6. As a result, the volume stability of LHC concrete is better than that of MHC concrete in drying environment.Experiment results of autogenous deformation of concrete are given in Fig.2. There is an obvious difference between the development of autogenous deformation of LHC concrete and that of MHC concrete. The autogenous deformation of LHC concrete has an expansive tendency. At early ages up to 14 days, the autogenous deformation of pure LHC samples increases with age, and the 14-day value reaches a peak of 20×10-6. The autogenous deformation of pure LHC samples decreases with age at 14 days to 90 days, and the 90-day value is 10×10-6. After adding 30% of fly ash, the autogenous deformation of LHC concrete increases with age, and the 90-day value is 61×10-6. The autogenous deformation of MHC concrete has a tendency to shrink, especially without fly ash.3.3. DurabilityThe durability of concrete is evaluated by antipenetrability grade and frost-resistant level. Under the pressure of 1.2 MPa, the permeability height of pure LHC samples is 3.1 cm, while that of pure MHC samples is 2.0 cm. The test data indicate that the LHC concrete has an excellent performance in anti-penetrability, as well as MHC concrete. The permeability of concrete increases somewhat with addition of fly ash. At the end of the 250 freezing and thawing cycling, there is a little difference in both mass and resonant frequency. Both LHC concrete and MHC concrete show an excellent frost-resistant behavior. The results of this work confirmthat LHC concrete systems have an adequate anti-penetrability and frost-resistance to adapting design requirement.3.4 Analysis of crack resistanceIn order to control the crack phenomena, it is important to accurately evaluate the anti-crack behavior.As well known, concrete is a kind of typical brittle materials, and its brittleness is associated with the anti-crack behavior[15]. The brittleness is measured by the ratio of tension strength to compressive strength. With the increase of the ratio, concrete has a less brittleness, better crack resistance and toughness. It is indicated from the experiment results shown in Table 6 that the ratio of LHC concrete at all stages of hydration is higher than that of MHC concrete, which shows that LHC concrete has a better anti-crack behavior.In the crack control and design of hydroelectric mass concrete, the original evaluation of crack resistance behavior of concrete is using the utmost tensile strength which is shown in the following expression of Eq.1.σ=εP E (1)where, εP is the limits tension of concrete, and E is the elastic modulus of tension, which is assumed to be equal to the elastic modulus of compression[16].It is indicated from the calculation results shown in Table 8 that the utmost tensile strength of LHC concrete at all stages of hydration is higher than that of MHC cncrete.The research on materials crack resistance which is the basis for esign, constr uction and the choice of raw materials, has been popular in today’s world. Through a great deal of research, it is widely thought that concrete with a better crack resistance has a higher tension strength and limits tension, lower elastic odulus and adiabatic temperature rise and better volume stability[17,18].Based on above-mentioned results, the LHC concrete has a higher tension strength and limits tension, lower elastic modulus and adiabatic temperature rise, and lower drying shrinkage than MHC concrete. Compared with MHC concrete, the autogenous deformation of LHC concrete has an expansive tendency. Although the early strength of LHC concrete is lower than that of MHC concrete, its later strength has approached to or even exceed that of MHC concrete.4 Conclusionsa) The early compressive strength (7 d curing ages) of LHC is lower, but its later strength (28 d, 90 d curing ages) has approached to or even exceed that of MHC.b) Compared with MHC, the average hydration heat of LHC concrete is reduced by about 17.5%.c) Under the same mixing proportion, the elastic modulus of LHC concrete is approximately equal to that of MHC, and the limits tension of LHC concrete is increased by 10×10-6-15×10-6 than that of MHC.d) The drying shrinkage of LHC concrete is obviously smaller than that of MHC concrete, and the autogenous deformation of LHC concrete has a tendency to expand.e ) The LHC concrete has a better anti-penetrability and frost resistance, as well as the MHC concrete.f) At all stages of hydration, the anti-crack strength of LHC concrete is higher than that of MHC concrete, and the former has a higher ratio of tension strength to compressive strength.References[1] C X Yu, Z Kong. Research on the Causes of Cracks in Mass Concrete and Control Measures [J]. Low Temperature Architecture Technology (China), 2005 (5): 112-113 [2] A A Almusallam, M Maslehuddin. Effect of Mix Proportions on Plastic Shrinkage Cracking of Concrete in Hot Environments[J].Construction and Building Materials, 1998 (12): 353-358[3] Xu Jing’an, An Zhiwen. Countermeasure of Temperature Crack of Mass Concrete[J]. Journal of Hebie Institute of Architectural Engineering, 2005,23(3):36-40[4] Peng Weibing, Ren Aizhu. Effects and Evaluation on Cracking of Concrete Incorporating Supplementary Cementitious Materials[J]. Concrete (China), 2005 (6): 50-64[5] Xiao Reimin, Zhang Xiong. Effect of Binder on Drying Shrinkage of Concrete [J].China Concrete and Cement Products, 2002 (5): 11-13[6] Ye Qing, Chen Xin. Research on the Expansive Mechanism of Moderate Heat Portland Cement with Slight Expansion [J].Journal of the Chinese Ceramic Society, 2000, 128 (4):335-347[7] Shi Xun. Application of Slight Expansion Cement on Concrete of Stage II Works of the Three Gorges Project [J]. Cement (China). 2002 (5): 12-14[8] Nagaokas, Mizukosui M. Property of Concrete Using Beliterich Cement and Ternary Blended Cement [J]. Journal of the Society of Materials Science, Japan, 1994, 43 (491): 488-492[9] Ge Juncai. Technology Progress of Cement and Concrete [M]. Beijing: China Building Material Industry Press , 1993:275-276[10] Metha P K. Investigation on Energy-saving Cement[J]. World Cement Technology, 1980, 1(3): 166-177[11] Taylor. Cement Chemistry[M]. London: Academic Press, 1990:142-152[12] Sui Tongba, Liu Kezhong. A Study on Properties of High Belite Cement [J]. Journal of the Chinese Ceramic Society, 1999, 127 (4): 488-492[13] Yang Nanru, Zhong Baixi. Study on Active -C2S[C]. Symposium on Cement,1983:180-185[14] Yang Huanquan, Li Wenwei. Research and Application of Hydroelectric Concrete[M]. Beijing, China Water Power Press,2004:393-394[15] E Ringot, A Bascoul. About the Analysis of Micro-cracking in Concrete[J]. Cement and Concrete Composites, 2001 (23):261-266[16] Li Guangwei. Assessment for Anti-Crack Performance of Concrete [J]. Advances in Science and Technology of Water Resources (China), 2001, 21 (2): 33-36[17] Liu Shuhua, Fang Kunhe. Summarization of Norm of Crack Resistance of Concrete[J]. Highway (China), 2004 (4): e[J] 105-107低热硅酸盐水泥混凝土的抗裂性能摘要:低热硅酸盐水泥混凝土(LHC)的特性详细地被研究。