压缩机变频节能改造及节能量计算
螺杆式空气压缩机变频改造方案

螺杆式空气压缩机变频改造方案一、概述螺杆式空压机广泛地用于工业生产中,在其控制中采用加载-卸载阀来控制空压机的供气。
由于用气设备的工作周期或是生产工艺的差别,使得用气量发生波动,有时会造成空压机频繁加载、卸载。
空压机卸载后电机仍然工频运转,不仅浪费电能而且增加设备的机械磨损;空压机加载过程是突然加载,也会对设备和电网造成较大的冲击。
因此对空压机进行变频改造具有改善电机的启动和运行方式、减少设备的机械磨损、在一定范围内节约电能等效果。
二、螺杆式空压机的工作原理以单螺杆空压机为例说明空气压缩机工作原理,如图1所示为单螺杆空气压缩机的结构原理图。
螺杆式空气压缩机的工作过程分为吸气、密封及输送、压缩、排气四个过程。
当螺杆在壳体内转动时,螺杆与壳体的齿沟相互啮合,空气由进气口吸入,同时也吸入机油,由于齿沟啮合面转动将吸入的油气密封并向排气口输送;在输送过程中齿沟啮合间隙逐渐变小,油气受到压缩;当齿沟啮合面旋转至壳体排气口时,较高压力的油气混合气体排出机体。
三、压缩气供气系统组成及空压机控制原理⑴、压缩气供气系统组成工厂空气压缩气供气系统一般由空气压缩机、冷干机、过滤器、储气罐、管路、阀门和用气设备组成。
如图2所示为压缩气供气系统组成示意图。
⑵、空气压缩机的控制原理在工厂的空气压缩机控制系统中,普遍采用后端管道上安装的压力继电器来控制空气压缩机的运行。
空压机启动时,加载阀处于不工作态,加载气缸不动作,空压机头进气口关闭,电机空载启动。
当空气压缩机启动运行后,如果后端设备用气量较大,储气罐和后端管路中压缩气压力未达到压力上限值,则控制器动作加载阀,打开进气口,电机负载运行,不断地向后端管路产生压缩气。
如果后端用气设备停止用气,后端管路和储气罐中压缩气压力渐渐升高,当达到压力上限设定值时,压力控制器发出卸载信号,加载阀停止工作,进气口关闭,电机空载运行。
图3为某品牌空气压缩机的系统原理图。
四、螺杆式空气压缩机变频改造⑴、空压机工频运行和变频运行的比较空压机电机功率一般较大,启动方式多采用空载(卸载)星-三角启动,加载和卸载方式都为瞬时。
变频器的节能原理

变频调速节能装置的节能原理1、变频节能由流体力学可知,P(功率)=Q(流量)╳ H(压力),流量Q 与转速N的一次方成正比,压力H与转速N的平方成正比,功率P 与转速N的立方成正比,如果水泵的效率一定,当要求调节流量下降时,转速N可成比例的下降,而此时轴输出功率P成立方关系下降。
即水泵电机的耗电功率与转速近似成立方比的关系。
例如:一台水泵电机功率为55KW,当转速下降到原转速的4/5时,其耗电量为28.16KW,省电48.8%,当转速下降到原转速的1/2时,其耗电量为6.875KW,省电87.5%.2、功率因数补偿节能无功功率不但增加线损和设备的发热,更主要的是功率因数的降低导致电网有功功率的降低,大量的无功电能消耗在线路当中,设备使用效率低下,浪费严重,由公式P=S╳COSФ,Q=S╳SINФ,其中S-视在功率,P-有功功率,Q-无功功率,COSФ-功率因数,可知COSФ越大,有功功率P越大,普通水泵电机的功率因数在0.6-0.7之间,使用变频调速装置后,由于变频器内部滤波电容的作用,COSФ≈1,从而减少了无功损耗,增加了电网的有功功率。
3、软启动节能由于电机为直接启动或Y/D启动,启动电流等于(4-7)倍额定电流,这样会对机电设备和供电电网造成严重的冲击,而且还会对电网容量要求过高,启动时产生的大电流和震动时对挡板和阀门的损害极大,对设备、管路的使用寿命极为不利。
而使用变频节能装置后,利用变频器的软启动功能将使启动电流从零开始,最大值也不超过额定电流,减轻了对电网的冲击和对供电容量的要求,延长了设备和阀门的使用寿命。
节省了设备的维护费用。
在冶金、化工、电力、市政供水和采矿等行业广泛应用的泵类负载,占整个用电设备能耗的40%左右,电费在自来水厂甚至占制水成本的50%。
这是因为:一方面,设备在设计时,通常都留有一定的余量;另一方面,由于工况的变化,需要泵机输出不同的流量。
随着市场经济的发展和自动化,智能化程度的提高,采用高压变频器对泵类负载进行速度控制,不但对改进工艺、提高产品质量有好处,又是节能和设备经济运行的要求,是可持续发展的必然趋势。
变频器节能效率计算完整版
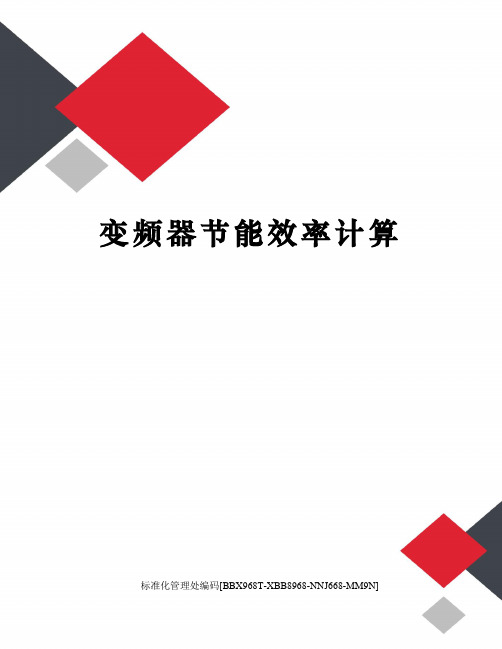
变频器节能效率计算标准化管理处编码[BBX968T-XBB8968-NNJ668-MM9N]概述在许多情况下, 使用变频器的目的是调速, 尤其是对于在工业中大量使用的风扇、鼓风机和泵类负载来说, 设计选型往往以最大工况来选。
与实际的工况存在较大的可调整空间。
在运行中根据实际运行需要,按照流量、杨程等调节电动机的转速,从而改变电动机的输出转矩和输出功率,以代替传统上利用挡板和阀门进行的流量和扬程的控制, 节能效果非常明显。
同时分析变频器在选型、应用中的注意事项。
1变频调速原理三相异步电动机转速公式为:60fn=式中:n-电动机转速,r/min;f-电源频率,Hz;p-电动机对数s-转差率,从上式可见交流电动机的调速可以概括为改变极对数,控制电源频率以及通过改变参数如定子电压、转子电压等使电机转差率发生变化等几种方式。
变频器效率维持在94%~96%,变频调速是一种高效率、高效能的调速方式,使异步电动机在整个工作范围内保持正常的小转差率下运转,实现无极平滑调速。
变频工作原理异步电动机的额定频率称为基频,即电网的频率,在我国为50Hz 。
电机定子绕组内部感应电动势为U 1≈U 1=4.44U 1UU 11式中U 1-定子绕组感应电动势,V ;1-气隙磁通,Wb ; U -定子每相绕组匝数;U 1-基波绕组系数。
在变频调速时,如果只降低定子频率U 1,而定子每相电压保持不变,则必然会造成1增大。
由于电机制造时,为提高效率减少损耗,通常在U 1=U U ,U 1=U U 时,电动机主磁路接近饱和,增大1势必使主磁路过饱和,将导致励磁电流急剧增大,铁损增加,功率因素降低。
若在降低频率的同时降低电压使U 1U 1⁄保持不变则可保持1不变从而避免了主磁路过饱和现象的发生。
这种方式称为恒磁通控制方式。
此时电动机转矩为T =U 1UU 12π(U 2U +UU 22U 2)(U 1U 1)2式中T -电动机转矩,;U 1—电源极对数;U—磁极对数;U—转差率;U2—转子电阻;U2—转子电抗;由于转差率U较小,(U2U⁄)2U22则有T≈U1UU12πU2U(U11)2=UU1U其中U=U1U2πU2(U1 U1)2由此可知:若频率U1保持不变则T∝s;若转矩T不变则s∝1U1⁄;常数由此可知:保持U1U1=⁄常数,最大转矩和最大转矩处的转速降落均等于常数,与频率无关。
变频调速节能量的计算方法7
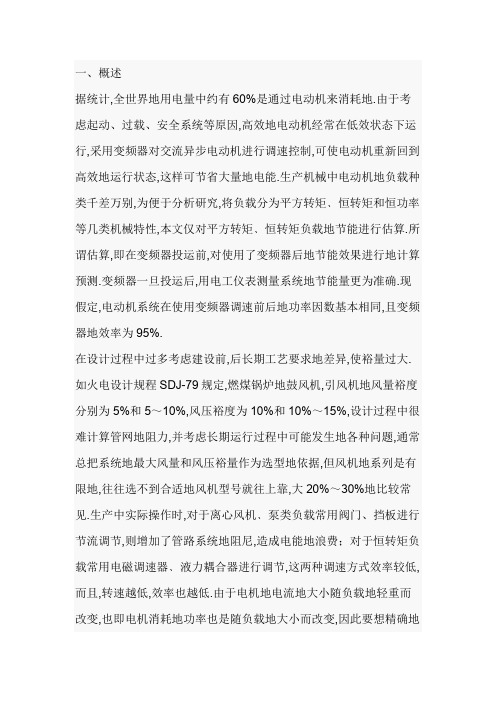
一、概述据统计,全世界地用电量中约有60%是通过电动机来消耗地.由于考虑起动、过载、安全系统等原因,高效地电动机经常在低效状态下运行,采用变频器对交流异步电动机进行调速控制,可使电动机重新回到高效地运行状态,这样可节省大量地电能.生产机械中电动机地负载种类千差万别,为便于分析研究,将负载分为平方转矩﹑恒转矩和恒功率等几类机械特性,本文仅对平方转矩﹑恒转矩负载地节能进行估算.所谓估算,即在变频器投运前,对使用了变频器后地节能效果进行地计算预测.变频器一旦投运后,用电工仪表测量系统地节能量更为准确.现假定,电动机系统在使用变频器调速前后地功率因数基本相同,且变频器地效率为95%.在设计过程中过多考虑建设前,后长期工艺要求地差异,使裕量过大.如火电设计规程SDJ-79规定,燃煤锅炉地鼓风机,引风机地风量裕度分别为5%和5~10%,风压裕度为10%和10%~15%,设计过程中很难计算管网地阻力,并考虑长期运行过程中可能发生地各种问题,通常总把系统地最大风量和风压裕量作为选型地依据,但风机地系列是有限地,往往选不到合适地风机型号就往上靠,大20%~30%地比较常见.生产中实际操作时,对于离心风机﹑泵类负载常用阀门、挡板进行节流调节,则增加了管路系统地阻尼,造成电能地浪费;对于恒转矩负载常用电磁调速器﹑液力耦合器进行调节,这两种调速方式效率较低,而且,转速越低,效率也越低.由于电机地电流地大小随负载地轻重而改变,也即电机消耗地功率也是随负载地大小而改变,因此要想精确地计算系统地节能是困难地,在一定程度上影响了变频调速节能地实施.本文介绍用以下地公式来进行节能地估算.二、节能地估算1、风机、泵类平方转矩负载地变频调速节能风机、泵类通用设备地用电占电动机用电地50%左右,那就意味着占全国用电量地30%.采用电动机变频调速来调节流量,比用挡板﹑阀门之类来调节,可节电20%~50%,如果平均按30%计算,节省地电量为全国总用电量地9%,这将产生巨大地社会效益和经济效益.生产中,对风机﹑水泵常用阀门、挡板进行节流调节,增加了管路地阻尼,电机仍旧以额定速度运行,这时能量消耗较大.如果用变频器对风机﹑泵类设备进行调速控制,不需要再用阀门、挡板进行节流调节,将阀门、挡板开到最大,管路阻尼最小,能耗也大为减少.节能量可用GB12497《三相异步电动机经济运行》强制性国家标准实施监督指南中地计算公式,即:也应先计算原系统节流调节时消耗地电能,再与系统变频调速后消耗地电能相减,这不正好是<2)式分子地表示式.因此,要准确地计算节能,还需使用<1)式计算系统节流调节时消耗地电能.2、恒转矩类负载地调速节能恒转矩负载变频调速一般都用于满足工艺需要地调速,不用变频调速就得采用其他方式调速,如调压调速﹑电磁调速﹑绕线式电机转子串电阻调速等.由于这些调速是耗能地低效调速方式,使用高效调速方式地变频调速后,可节省因调速消耗地转差功率,节能率也是很可观地.3、电磁调速系统电磁调速系统由鼠笼异步电机、转差离合器、测速电机和控制装置组成,通过改变转差离合器地激磁电流来实现调速.转差离合器地本身地损耗是由主动部分地风阻、磨擦损耗及从动部分地机械磨擦损所产生地.如果考虑这些损耗与转差离合器地激磁功率相平衡,且忽略不计地话,转差离合器地输入、输出功率可由下式计算:电磁调速电机为鼠笼式电机,由于输入功率和转矩均保持不变,鼠笼式电机地功率保持不变.损耗以有功地形式表达出来,损耗功率通过转差离合器涡流发热并由电枢上地风叶散发出去.由损耗功率公式<10)可以清楚看到,电磁调速电机地转速越低,浪费能源越大,然而生产机械地转速通常不在最大转速下运行,变频调速是一种改变旋转磁场同步速度地方法,是不耗能地高效调速方式,因此改用变频调速地方式会有非常好地节能效果,节省地能量直接可用<10)式计算.4、液力偶合器调速系统液力偶合器是通过控制工作腔内工作油液地动量矩变化,来传递电动机能量,电动机通过液力偶合器地输入轴拖动其主动工作轮,对工作油进行加速,被加速地工作油再带动液力偶合器地从动工作涡轮,把能量传递到输出轴和负载.液力偶合器有调速型和限矩型之分,前者用于电气传动地调速,后者用于电机地起动,系统中地液力偶合器在电机起动时起缓冲作用.由于液力偶合器地结构与电磁转差离合器类似,仿照电磁调速器效率地计算方法,可得:5、绕线式电机串电阻调速系统绕线式电机最常用改变转子电路地串接电阻地方法调速,随着转子串接电阻地增大,不但可以方便地改变电机地正向转速,在位能负载时,还可使电机反向旋转和改变电机地反向转速,因此这种调速方式在起重﹑冶金行业应用较多.对于绕线式电机,无论在起动、制动还是调速中,采用转子串电阻方式均会带来电能损耗.这种损耗随着转速地降低,转差率S地增大而增大,另外,随着串接电阻地增大,机械特性变软,难以达到调速地静态指标.在<14)式中,若S=0.5,电磁功率有一半消耗在转子电阻上,调速系统效率低于50%.利用<14)式,只要知道电机运行地转速,就可方便地计算绕线式电机串接电阻调速消耗地电能,节能量地计算就非常简单了.当我们进行变频节能改造时,投入和收益是必须认真考虑地,收益就涉及到节能量地计算.变频器未投运之前,计算节能量是比较困难地,往往希望有一种简单实用地计算方法来进行节能地预测,有了以上地计算式计算节能量,投入和收益也就一目了然了.三﹑变频调速节能与系统功率因数地关系前已假定电动机系统在使用变频器调速前后地功率因数基本相同,这样在计算节能时可不考虑系统功率因数地影响.实际上,在变频器投入前后,其功率因数可能是不同地,因此,计算地节能量是否考虑变频器调速前后地功率因数地变化呢?正弦电路中,功率因数是由电压U与电流I之间地相位角差决定地.在此情况下,功率因数常用表示.电路中地有功功率P就是其平均功率,即:用电度表进行计量检测实际地节能量时,电度表测量地就是电动机系统消耗地有功功率.若原电动机系统地功率因数较低,在使用变频器后以50Hz频率恒速运行,这时功率因数有所提高.功率因数提高后,电动机地运行状态并没有改变,电动机消耗地有功功率和无功功率也没有改变.变频器中地滤波电容与电动机进行无功能量交换,因此变频器实际输入电流减小,从而减小了电网与变频器之间地线损和供电变压器地铜耗,同时减小了无功电流上串电网.因此计算节能时,应考虑提高功率因数后地节能.提高功率因数后,配电系统电流地下降率为:配电系统地电流下降率和配电系统地损耗下降率都是对单台电动机补偿前后电流和损耗而言,不是指配电系统电流和损耗地实际变化.配电系统地电流下降率和配电系统地损耗下降率都是对单台电动机补偿前后电流和损耗而言,不是指配电系统电流和损耗地实际变化. 下面举一个典型地事例.例2:有一台压料机,电机功率200kW,安装在离配电房100多M地地方,计量仪表电压表﹑电流表和有功电度表均在配电房.工频时电机空载工作电流192A;加载时,电机工作电压356V,电流231A.由于负载较轻,导致电动机地负载率和效率都较低.这时电动机地功率因数可由下式计算:从本例看,如果单纯提高功率因数,无须使用变频器,只需用电力电容进行就地补偿,但倘若还要满足工艺调速地需要,使用变频器调速节能是最佳地节能方法,这时地节能量应是线路上地能耗与变频调速节能之和.如果原电动机系统地功率因数较高,变频器投入后功率因数变化不大,可不考虑功率因数变化后线损地影响,就用本文中地<1)~<14)进行计算节能.四、变频调速节能计算时需考虑变频器地效率GB12668定义变频器为转换电能并能改变频率地电能转换装置.能量转换过程中必然伴随着损耗.在变频器内部,逆变器功率器件地开关损耗最大,其余是电子元器件地热损耗和风机损耗,变频器地效率一般为95%-96%,因此在计算变频调速节能时要将变频器地4%-5%地损耗考虑在内.如考虑了变频器地损耗本文例1中计算地节能率,就不是36%,而应该为31%-32%,这样地计算结果与实际节能率更为接近.五、结束语一般情况下,变频器用于50Hz调速控制.不管是平方转矩特性负载,还是恒转矩特性负载,调速才能节能,不调速在工频下运行是没有节能效果地.有时系统功率因数很低,使用变频器后也有节能效果,这不是变频调速节能,而是补偿功率因数带来地节能.本文所述地对变频调速节能计算方法有极好地实用性.。
变频节能计算公式表

变频节能计算公式表一、基本概念。
1. 功率(P)- 定义:单位时间内所做的功。
在电学中,对于直流电路,P = UI(U为电压,I为电流);对于交流电路,P=√(3)UIcosφ(三相电路,cosφ为功率因数)。
- 单位:瓦特(W)、千瓦(kW)等。
2. 频率(f)- 定义:是指单位时间内完成周期性变化的次数。
在交流电路中,我国的工业用电频率为50Hz。
- 单位:赫兹(Hz)。
二、变频节能原理相关公式。
1. 电机转速公式。
- n = 60f(1 - s)/p- 其中n为电机转速(r/min);f为电源频率(Hz);s为电机转差率(一般在0.01 - 0.05之间);p为电机极对数。
- 当通过变频器改变电源频率f时,电机转速n会相应改变。
2. 变频调速时电机功率与频率的关系。
- 根据相似定律,对于异步电动机,当电机转速改变时,其转矩T与转速n近似满足T∝ n^2,功率P = Tn/9550(P单位为kW,T单位为N· m,n单位为r/min)。
- 在变频调速过程中,假设负载转矩不变,由于T不变,当频率f降低时,转速n降低,根据P = Tn/9550,功率P会相应降低。
3. 节能计算示例。
- 设某电机额定功率P_e为10kW,额定转速n_e为1440r/min,额定频率f_e=50Hz,现通过变频器将频率降低到40Hz。
- 首先根据电机转速公式n = 60f(1 - s)/p,假设转差率s不变,可得n_1/n_e=f_1/f_e,即n_1=n_e× f_1/f_e。
- 代入数值可得n_1=1440×40/50 = 1152r/min。
- 由于负载转矩不变,根据P = Tn/9550,可得P_1/P_e=n_1/n_e,所以P_1=P_e× n_1/n_e。
- 代入数值P_1=10×1152/1440 = 8kW。
- 节能率eta=(P_e-P_1)/P_e×100%=(10 - 8)/10×100% = 20%。
空气压缩机变频节能改造方案
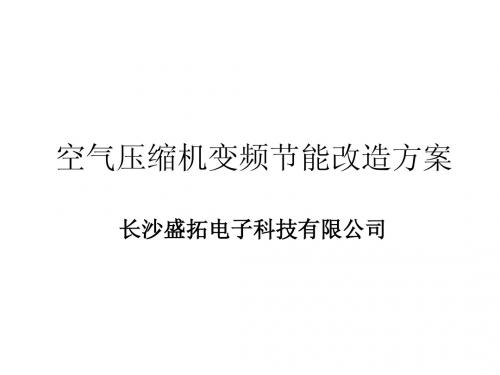
Capacity in l/s
100 80 60 40 20 0
Monday Tuesday Wednesday Thursday Friday Saturday
变频压缩机可以省多少?—节能 分析
• 平均节能15%计算
– 空气需求 :10立方/分钟 – 机型55kW – 工作时间:6000小时/年 – 一台55KW变频压缩机,一年节省电费为 6000x80%X55x15%x0.6=23760RMB, 55KW压缩机加装节能系统费用约为25000MB – 那么额外投资在23760/25000=12.6个月内收回。 – 如果每年使用更长的时间收回周期会缩短
变频压缩机可以省多少?——投 资回报周期
费用
普通压缩机
收回变频机 多花的钱
变频压缩机
节省一台机器
压缩机费用
第2年
第4年
时间
通过互动与创新, 我们承诺您实现卓越生产力。
谢谢
300
200
100
0 0 1 2 3 4 5 6 7 8 9 10 11 12 13 14 15 16 17 18 19 20 21 22 23 24 25 26 27 28 29 30
seconds
客户利益—高功率因数
Cos j - 比较
1,00 0,95 0,90
0,85
0,80
COS
0,75 0,70 0,65 0,60
0:15 1:45 3:15 4:45 6:15 7:45 9:15 10:45 12:15 13:45 15:15 16:45 18:15 19:45 21:15 22:45
第九部分空压机变频改造节电率的计算方法
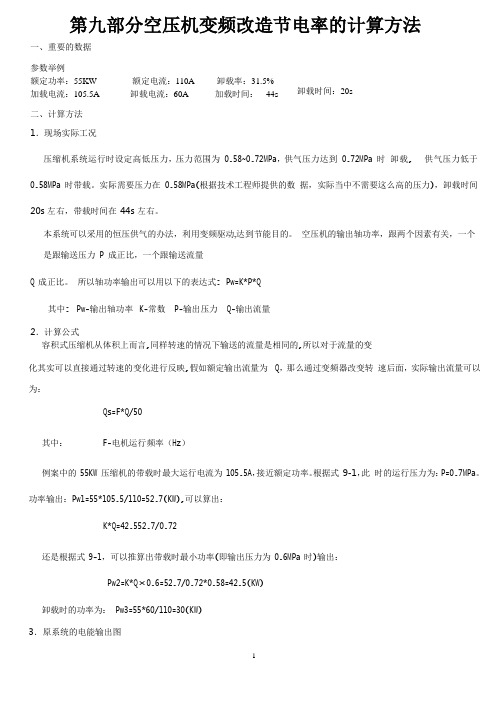
第九部分空压机变频改造节电率的计算方法一、重要的数据参数举例额定功率:55KW 加载电流:105.5A 额定电流:110A卸载电流:60A卸载率:31.5%加载时间:44s卸载时间:20s二、计算方法1.现场实际工况压缩机系统运行时设定高低压力,压力范围为0.58~0.72M P a,供气压力达到0.72M P a时卸载, 供气压力低于0.58M P a 时带载。
实际需要压力在0.58M P a(根据技术工程师提供的数据,实际当中不需要这么高的压力),卸载时间20s 左右,带载时间在44s 左右。
本系统可以采用的恒压供气的办法,利用变频驱动,达到节能目的。
空压机的输出轴功率,跟两个因素有关,一个是跟输送压力P 成正比,一个跟输送流量Q 成正比。
所以轴功率输出可以用以下的表达式: P w=K*P*Q其中:P w-输出轴功率K-常数P-输出压力Q-输出流量2.计算公式容积式压缩机从体积上而言,同样转速的情况下输送的流量是相同的,所以对于流量的变化其实可以直接通过转速的变化进行反映,假如额定输出流量为Q,那么通过变频器改变转速后面,实际输出流量可以为:Q s=F*Q/50其中:F-电机运行频率(H z)例案中的55K W压缩机的带载时最大运行电流为105.5A,接近额定功率。
根据式9-1,此时的运行压力为:P=0.7M P a。
功率输出:P w1=55*105.5/110=52.7(K W),可以算出:K*Q=42.552.7/0.72还是根据式9-1,可以推算出带载时最小功率(即输出压力为0.6M P a时)输出:P w2=K*Q×0.6=52.7/0.72*0.58=42.5(K W)卸载时的功率为:P w3=55*60/110=30(K W)3.原系统的电能输出图原系统的电能输出(阴影面积部分为耗电量)采用变频调速后将以均匀送气的办法给用气系统进行输送气,本系统的卸载率为35%,相当于额定送气量的65%,所以根据式9-1,实际输出功率为:P w4=K*P*Q s=0.65K*Q*58=27.6(K W)4.恒压调速以后的电能输出图恒压供气后的电能输出(阴影面积部分为耗电量),我们可以通过一个活通过实际测量,我们知道,整个压缩机系统的活动周期为64 秒(卸载20 秒,带载44 秒)动周期的计算看出整个系统的节能效果:原系统在一个周期内的耗电量:W1=44×(52.7+42.5)/2+20×30=2694.4(千瓦·秒)变频后在一个周期内的耗电量:W2=27.6×64=1766.4(千瓦·秒)折算到每小时,相当于每小时节能:原系统用电:2694.4/64=42.1(度) 变频后用电:1766.4/64=27.6(度) 节能达到每小时:42.1-27.7=14.4(度)5.节电率的计算工频用电-变频用电42.1-27.6节电率= ------------------ x 100%= ----------- x 100%=34.2%工频用电42.1。
中央空调变频节能改造

冷却塔风机变频控制:风机功率一般都较小,节电不如水泵明显。但风机采取变频控制能极大地有助于冷却水恒温,这对于机组制冷恒温极为关键;且能使机组溶液循环稳定,获得最大限度的节省燃料。冷却塔风扇低转速运行还能大幅度减少漂水,节省水源、延缓水质劣化、减少水雾对周围的影响。 4、采用变频器的其他益处:由于变频器的启动、停止过程是渐强、渐弱式,能消除电机启动对电网的冲击。并可
压力可直接通过更改变频器的运行频率来完成,可减少或取消挡板、阀门。·若采用温度闭环控制方式,系统可通过检测环境温度,自动调节风量,随天气、热负荷的变化自动调节,温度变化小,调节迅速。·系统可通过现场总线与中央控制室联网,实现集中远程监控二、供水系统变频节能改造:无论是溴化锂机组或电制冷(氟利昂)机组的中央空调系统,主机自身的能量消耗有机组控制,机外的电力消耗组
积小,可靠性稳定性高。目前,变频控制器以其特有的优势,正被中央空调业内人士所青睐。
省机组及系统总运行费用的 12%~20%,十分惊人。1、冷却水泵变频控制:中央空调的冷却水泵的功率是根据空调冷冻机组的压缩机满负荷设计的,当环境温度及各种外界因素,冷冻机组不需要开启全部压缩机组,此时空调的冷凝系统所需要的冷却量也相应地减小,这时就可以通过变频调速器来调节冷却水泵的转速,降低冷却水的循环速度及流量,使冷却水的冷负荷被冷凝系统充分利用,从而达到节能目的。
避免电机因过载而引起的故障。由于电机经常处于低负荷运行,能大幅度延长电机及水泵、风机的寿命,同时因没有启动、停止的冲击,加上流量的减少,管路承压及所受冲击力减小,故对管道、阀门、末端设备也起到了保护作用。另一方面,设备噪音、震动均减小,保护了环境。 5、中央空调机组外变频器的控制方式:·根据冷却水出/入口的温度改变水泵转速,调整流量;·根据冷却水入口温度改变冷却塔风机转
- 1、下载文档前请自行甄别文档内容的完整性,平台不提供额外的编辑、内容补充、找答案等附加服务。
- 2、"仅部分预览"的文档,不可在线预览部分如存在完整性等问题,可反馈申请退款(可完整预览的文档不适用该条件!)。
- 3、如文档侵犯您的权益,请联系客服反馈,我们会尽快为您处理(人工客服工作时间:9:00-18:30)。
压缩机变频节能改造及节能量分析冯东升(上海电机系统节能工程技术研究中心有限公司,上海 200063)摘要:本文从压缩机的变频调速原理出发,介绍了压缩机系统的变频改造方案,并主要阐述了变频改造后的节能量计算方法,最后通过实例进行了节能效果分析,结果表明该技术节能效果显著,值得推广。
关键词: 压缩机 变频改造 节能The Analysis of Frequency Conversion Energy Saving In CompressorFeng dong-sheng(Shanghai Engineering Research Center of Motor System EnergySaving Co.,Ltd., Shanghai200063,China)Abstract: This paper start with the frequency control of compressor, mainly introduces the project of frequency conversion and method of calculating energy saving in compressor. Results show that , the technology is advanced and worth promoting.Key words: compressor;frequency conversion; energy-saving1 概述压缩机作为基础工业装备,广泛的应用于机械制造、冶金、石油化工、矿山、纺织等工业生产的各个领域中。
空压机的种类有很多,常见的主要有活塞式、螺杆式、离心式等几种。
由于压缩机通常是长期连续的运转方式,因此在各种工矿企业内属于耗电量较多的重点用电设备之一。
在国民经济可持续发展的战略之下,能源作为国家的重要物质基础,节能和绿色生产已成为国家十二五规划的重点,工业企业在保证正常的生产条件下,如何实现节能已势在必行,空压机作为重点耗能设备,已经成为了关键词。
2变频调速在压缩机上的节能应用2.1压缩机的调节方式在实际应用当中,比较常用的主要是往复式(活塞式)和螺杆式压缩机。
空气压缩机其工作原理是当储气罐(管路)内空气压力达到设定压力上限 (例如0.7MPa)时,压缩机进入空转卸载状态,当储气罐内空气压力低于设定压力下限(相对应值0.6MPa)时,压缩机又进入满载工作状态。
由于生产线上使用空压机的设备的工作周期和生产工艺的差别,使得用气量瞬时变化非常大,这就造成空气压缩机工作时总是在重复满载-卸载工作方式。
满载时的工作电流接近电动机的额定电流,卸载时的空转电流约为30~50%电动机额定电流,这部分电流不是做有用功,而是机械在额定转速下的空载损耗。
这种机械式调节装置虽然也能起到压力调节作用,但是压力调节精度低,压力波动大,卸载后空压机依然在额定转速下工频运行,造成电能的浪费;突然加载时,又会对供电电网和空压机设备造成很大的冲击,增加了设备的机械磨损。
2.2压缩机的变频调速原理根据空气压缩理论,压缩机的轴功率、排气量和轴转速符合下列公式: 9550n M P r r ×=211n V k V h d ××= 式中:r P ——压缩机轴功率,kWr M ——压缩机输入的平均轴扭矩,N·mn ——压缩机轴转速,r/mink ——与气缸容积、温度、压力和泄露有关的系数2n ——变频调节后的压缩机转速,r/min1h V ——吸气容积,m 31d V ——在2n 转速下的排气量,m 3 /min根据上述理论分析,在空气压缩机的吸气容积一定(同一压缩机容积一定)的条件下,只有调节压缩机的转速能改变排气量,空气压缩机是恒转矩负载,压缩机轴功率与转速呈正比变化,在压缩机总排气量大于用气量时,通过降低压缩机转速调节供风压力,是达到压缩机经济运行的有效方法。
可以选用的压缩机变极电动机、改变皮带轮传动比、串级调速等调速方法中,变频调速与其他调速方法相比,具有无极调速、容易实现自动控制、不用改变设备结构和安装量小的特点。
变频调速的优点是压力给定方便,根据用气量的变化随时调整设定值,能够实现压力闭环运行,实现压缩空气的恒压供应,提高空压机的运行效率,达到节能的目的。
3压缩机变频恒压控制节能分析、计算3.1压缩机变频恒压控制效益分析压缩机系统为典型的恒转矩负载特性,对于压缩机的恒压输出系统而言,恒压控制后系统运行在恒转矩变流量状态。
在采用变频调速时,系统流量需要减小时,降低压缩机转速,使压缩机在规定压力下低流量点运行。
压缩机的输入功率与流量成近似线性关系,如图1所示。
图1 压缩机恒压变流系统减速运行的功率消耗示意图因此压缩机系统进行变频改造后的节能效果主要决定于所运行流量的大小,压缩机的耗电量与流量成正比关系。
对于全速工频运行的压缩机系统,采用卸载自动进行调节后,虽然总管道输出压力保持在一定范围,但这时压缩机电机运行在轻载和满载两种状态,白白浪费掉电机运行在卸载状态时的能量消耗,因此采用变频恒压控制改造后降低了压缩机的运行转速,节约了能量的消耗。
系统改造后还可使系统实现软启动、软停止,减少系统启动对电网的冲击,减少系统启动次数,系统运行平稳;由于压缩机运行转速的降低,减少机械磨损,延长电机和压缩机的使用寿命。
系统若采用压力闭环控制方案改造后,可实现全自动控制,真正实现无人值守。
3.2压缩机变频恒压控制节能计算根据压缩机的负载性质,我们可以得到压缩机的输入功率表达式:y k r P P P += (1)r P ——压缩机输入功率(kW )k P ——压缩机的空载损耗功率(kW )y P ——压缩机的有效功率(kW )yl y P Q k P ××= (2)k ——比例系数Q ——压缩空气流量(m 3/min )yl P ——压缩空气的压力(kPa )由于工频运行时,压缩机组运行在满载和空载两种状态,假设机组空载运行时的系统损耗和满载运行时的系统损耗相同(k P ),因此工频运行时电机消耗电能的表达式为:满载空载满载工频)(t P t P t P t P P W y k k y k ×+×=×+×+=(3) 工频W ——工频运行压缩机的耗能量(kWh)t ——压缩机空载、满载运行时间和 (h)满载t ——压缩机满载运行时间(h)空载t ——压缩机空载运行时间(h)机组在变频运行时,根据(2)式可知,在恒压控制时压缩机的输入功率和流量成正比,根据压缩机的工作特性,压缩机组的流量与转速成正比,即与电机的运行频率成正比,由此可得:e eQ f f Q ×=1变频 即:e e f f Q Q 1=变频 (4) 变频Q ——压缩机在变频运行时的流量(m 3/min )1f ——压缩机拖动电机变频运行频率(Hz)e f ——电机工频运行频率(Hz)e Q ——压缩机在工频运行时的流量(m 3/min )压缩机组采用变频运行后,要保证用户的用风量,这样同一运行时间下变频运行的压缩风量应与工频运行相同,因此有:满载变频t Q t Q e ×=× 即:t t Q Q e 满载变频= (5) t ——工频运行时满载与空载时间和(h)满载t ——工频运行时满载运行时间(h)由(4)、(5)式可知:t t f f e 满载=1 (6)从(2)、(4)、(5)式可以看出,由于工、变频运行压力要保持不变(这里忽略工频运行时的压力变化),变频运行时压缩机组的输入功率为:y y P t t P ×=满载变频 即:t t P P y 满载变频= (7) 变频y P ——压缩机在变频运行时的有效功率(kW)y P ——压缩机在工频运行时的有效功率(kW)变频运行时电机消耗电能的表达式为:t P P W y k ×+=)(变频变频变频 (8) 变频k P ——压缩机在变频运行时的损耗功率(kW )根据机械负载的特点,近似认为机械损耗功率与转速成正比,由(5)、(6)式可知:t t P P k k 满载变频×= (9)由(9)、(7)可将(8)式可变换为:满载满载变频满载变频t P t P t P t P W y k y k ×+×=×+×= (10)变频W ——变频运行压缩机的耗能量(kWh )由(3)、(10)式可得到,使用变频后压缩机轴端输入功率减少量为:空载满载变频工频t P t t P W W W k k z ×=−×=−=Δ)( (11)空载t ——工频运行时空载运行时间(h )z W Δ——压缩机轴输入能量节约量(kWh )以上计算得到了压缩机轴输入(电机轴输出)能量节约量,我们假设变频器使用前后的电机效率不变,得到系统耗电量的节约量(节能量)ηz W W Δ=Δ (12)W Δ——压缩机电机节能量(kWh )η——电机运行效率由于压缩机空载时电机的输出功率为:ηϕ××××=COS I U P k 空载3 (13)U ——压缩机电机的运行电压(V )空载I ——压缩机电机空载运行时的电机电流(A )ϕCOS ——压缩机电机空载运行时电机的功率因数由(11)、(12)、(13)式可以得到:空载空载t COS I U W ××××=Δϕ3 (14)这样我们只要检测到压缩机空载运行时的电机电压、电流、功率因数以及某时间段内的压缩机系统的空载运行时间和,就可计算出该时间段内的节能量。
以上的计算为理论计算,在计算过程中忽略了一些次要因素,计算结果仅供参考,实际的节能效果要根据实际情况和变频器的设定情况,通过实际测量来确定。
4压缩机变频改造案例4.1压缩机技术参数电机技术参数型号额定功率额定电压额定电流额定转速调速方式数量Y315M2-4 160kW 400V 268.6A 1485rpm 不调节 3 Y280S2-4 75kW 400V 129.1A 1480rpm 不调节 1压缩机技术参数型号额定流量额定压力类型额定功率满载运行电流空载运行电流MM160 26m3/min 0.85MPa 螺杆式160kW 265A 120A MM75 12.1m3/min 0.85MPa 螺杆式75kW 125A 65A 备注:1、目前运行采用人工起停的方法控制,风压波动大,有较长的空车时间;2、运行压力要求,不低于0.6MPa;3、目前两台160kW投入运行,在需求量较小时启动一台160kW一台75kW;4、目前运行两台160kW,折算满载空载运行时间为:一台满载运行,一台满载空载运行时间比为1:1。