太阳能光伏电池论文中英文资料对照外文翻译文献综述
光伏电池英文文献翻译

5.1太阳能电池材料理论效率和要求最大的太阳能辐射转换为电能的效率索取已经研究很透彻。
这种效率可以由两种方法得到:热力学定理和热力学平衡[67]。
热机极限效率可以由卡诺关系η= 1 - (T2/T1)得出,其中T1是热源温度和T2为散热器温度。
太阳频谱可以近似为5900黑体辐射谱。
如果考虑边界条件,最高效率可以达到85%。
细致平衡原理是基于太阳能电池中不同的粒子通量平衡和因为热力学极限而产生的相似结果。
Shockley和Queisser的一篇重要论文中介绍到这一定理[68]。
现在,实际效率远低于理论限制。
其原因是可以从以下方面得到:——太阳光谱非常宽,范围从紫外到近红外,而半导体只能以特定效率转换具备带隙能量的光子。
光子能量较低不可以被吸收,高能量光子的能量因为载流子的热化减少到带隙能量。
现在可以使用几种串联细胞半导体改善这种情况,正如我们在(图5.3.1)看到的。
——阳光在到达地球表面的能量和它离开太阳的表面时相比,已经是非常少了。
直射的阳光通过特定方式积聚,可以得到更高的转换效率。
首先我们看本征半导体,并考虑它的最高效率。
在图看到5.1我们看到,带隙的效率曲线有最高点。
并且可以看出,硅是不是最大,但比较接近。
该书的一大部份是有关硅,虽然从固体物理学我们知道,硅光伏并非理想转换材料。
一个非常严重的问题是,半导体硅是一种非直接半导体;最高价带和最低导带在晶体空间彼此不是相反的,正如图2.1描述的那样。
图。
5.1。
依赖的带隙的半导体转换效率光吸收远在间接半导体弱于直接半导体。
从材料的角度看这是一个严重的问题:对于90%的光吸收,只需要1微米的GaAs(直接半导体)与100微米的硅。
载流子必须达到前表面附近的PN结。
对少数载流子扩散长度要为200μm,或至少达到两次硅的厚度。
因此,材料要非常高的纯度和高结晶程度。
鉴于这些物理限制,但令人惊讶的是硅在市场上却起到主导角色作用。
最主要的原因是,光伏到来之前,硅技术已已经高度发达,微电子市场中,优质材料正在大量生产,并且成本相对较低。
光伏发电中英对照文献

外文参考文献译文及原文目录外文文献译文 (1)1.中国光伏发电的战略地位 (1)2.世界光伏产业现状和发展预测 (2)3.中国光伏发电市场和产业现状 (3)4.中国光复发电的市场预测和规划建议 (5)5.结论 (6)外文文献原文 (7)1.China's strategic position PV (7)2.The world's current situation and development of photovoltaic industryforecast (9)3.The Chinese PV market and industry statu s (10)4.China's PV market forecasting and planning proposals (13)5.Conclusions (15)外文文献译文1、中国光伏发电的战略地位1.1 中国的能源资源和可再生能源现状和预测;无论从世界还是从中国来看,常规能源都是很有限的,中国的一次能源储量远远低于世界的平均水平,大约只有世界总储量的10%。
从长远来看,可再生能源将是未来人类的主要能源来源,因此世界上多数发达国家和部分发展中国家都十分重视可再生能源对未来能源供应的重要作用。
在新的可再生能源中,光伏发电和风力发电是发展最快的,世界各国都把太阳能光伏发电的商业化开发和利用作为重要的发展方向。
根据欧洲JRC 的预测,到2030年太阳能发电将在世界电力的供应中显现其重要作用,达到10%以上,可再生能源在总能源结构中占到30%;2050 年太阳能发电将占总能耗的20%,可再生能源占到50%以上,到本世纪末太阳能发电将在能源结构中起到主导作用。
我国政府重视可再生能源技术的发展,主要有水能、风能、生物质能、太阳能、地热能和海洋能等。
我国目前可再生能源的发展现状如下:水能:我国经济可开发的水能资源量为3.9 亿千瓦,年发电量1.7 万亿千瓦时,其中5 万千瓦及以下的小水电资源量为1.25 亿千瓦。
光伏发电逆变器毕业论文中英文资料外文翻译文献

光伏发电逆变器毕业论文中英文资料外文翻译文献附录:文献翻译TMS320LF2407, TMS320LF2406, TMS320LF2402TMS320LC2406, TMS320LC2404, MS320LC2402DSP CONTROLLERSThe TMS320LF240x and TMS320LC240x devices, new members of the ‘24x family of digital signal processor (DSP) controllers, are part of the C2000 platform of fixed-point DSPs. The ‘240x devices offer the enhanced TMS320 architectural design of the ‘C2xx core CPU for low-cost, low-power, high-performance processing capabilities. Several advanced peripherals, optimized for digital motor and motion control applications, have been integrated to provide a true single chip DSP controller. While code-compatible with the existing ‘24x DSP controller devices, the ‘240x offers increased processing performance (30 MIPS) and a higher level of peripheral integration. See the TMS320x240x device summary section for device-specific features.The ‘240x family offers an array of memory sizes and different peripherals tailored to meet the specific price/performance points required by various applications. Flash-based devices of up to 32K words offer a reprogrammable solution useful for:◆Applications requiring field programmability upgrades.◆Development and initial prototyping of applications that migrate to ROM-baseddevices.Flash devices and corresponding ROM devices are fully pin-to-pin compatible. Note that flash-based devices contain a 256-word boot ROM to facilitate in-circuit programming.All ‘240x devices offer at least one event manager module which has been optimized for digital motor control and power conversion applications. Capabilities of this module include centered- and/or edge-aligned PWM generation, programmable deadband to prevent shoot-through faults, and synchronized analog-to-digital conversion. Devices with dual event managers enable multiple motor and/or converter control with a single ‗240x DSP controller.The high performance, 10-bit analog-to-digital converter (ADC) has a minimum conversion time of 500 ns and offers up to 16 channels of analog input. The auto sequencing capability of the ADC allows a maximum of 16 conversions to take place in a single conversion session without any CPU overhead.A serial communications interface (SCI) is integrated on all devices to provide asynchronous communication to other devices in the system. For systems requiring additional communication interfaces; the ‘2407, ‘2406, and ‘2404 offer a 16-bit synchronous serial peripheral interface (SPI). The ‘2407 and ‘2406 offer a controller area network (CAN) communications module that meets 2.0B specifications. To maximize device flexibility, functional pins are also configurable as general purpose inputs/outputs (GPIO).To streamline development time, JTAG-compliant scan-based emulation has been integrated into all devices. This provides non-intrusive real-time capabilities required to debug digital control systems. A complete suite of code generation tools from C compilers to the industry-standard Code Composerdebugger supports this family. Numerous third party developers not only offer device-level development tools, but also system-level design and development support.PERIPHERALSThe integrated peripherals of the TMS320x240x are described in the following subsections:●Two event-manager modules (EV A, EVB)●Enhanced analog-to-digital converter (ADC) module●Controller area network (CAN) module●Serial communications interface (SCI) module●Serial peripheral interface (SPI) module●PLL-based clock module●Digital I/O and shared pin functions●External memory interfaces (‘LF2407 only)●Watchdog (WD) timer moduleEvent manager modules (EV A, EVB)The event-manager modules include general-purpose (GP) timers, full-compare/PWM units, capture units, and quadrature-encoder pulse (QEP) circuits. EV A‘s and EVB‘s timers, compare units, and capture units function identically. However, timer/unit names differ for EV A and EVB. Table 1 shows the module and signal names used. Table 1 shows the features and functionality available for the event-manager modules and highlights EV A nomenclature.Event managers A and B have identical peripheral register sets with EV A starting at 7400h and EVB starting at 7500h. The paragraphs in this section describe the function of GP timers, compare units, capture units, and QEPs using EV A nomenclature. These paragraphs are applicable to EVB with regard to function—however, module/signal names would differ.Table 1. Module and Signal Names for EV A and EVBEVENT MANAGER MODULESEV AMODULESIGNALEVBMODULESIGNALGP Timers Timer 1Timer 2T1PWM/T1CMPT2PWM/T2CMPTimer 3Timer 4T3PWM/T3CMPT4PWM/T4CMPCompare Units Compare 1Compare 2Compare 3PWM1/2PWM3/4PWM5/6Compare 4Compare 5Compare 6PWM7/8PWM9/10PWM11/12Capture Units Capture 1Capture 2Capture 3CAP1CAP2CAP3Capture 4Capture 5Capture 6CAP4CAP5CAP6QEP QEP1QEP2QEP1QEP2QEP3QEP4QEP3QEP4External Inputs DirectionExternalClockTDIRATCLKINADirectionExternal ClockTDIRBTCLKINBGeneral-purpose (GP) timersThere are two GP timers: The GP timer x (x = 1 or 2 for EV A; x = 3 or 4 for EVB) includes:● A 16-bit timer, up-/down-counter, TxCNT, for reads or writes● A 16-bit timer-compare register, TxCMPR (double-buffered with shadow register), forreads or writes● A 16-bit timer-period register, TxPR (double-buffered with shadow register), forreads or writes● A 16-bit timer-control register,TxCON, for reads or writes●Selectable internal or external input clocks● A programmable prescaler for internal or external clock inputs●Control and interrupt logic, for four maskable interrupts: underflow, overflow, timercompare, and period interrupts● A selectable direction input pin (TDIR) (to count up or down when directionalup-/down-count mode is selected)The GP timers can be operated independently or synchronized with each other. The compare register associated with each GP timer can be used for compare function and PWM-waveform generation. There are three continuous modes of operations for each GP timer in up- or up/down-counting operations. Internal or external input clocks with programmable prescaler are used for each GP timer. GP timers also provide the time base for the other event-manager submodules: GP timer 1 for all the compares and PWM circuits, GP timer 2/1 for the capture units and the quadrature-pulse counting operations. Double-buffering of the period and compare registers allows programmable change of the timer (PWM) period and the compare/PWM pulse width as needed.Full-compare unitsThere are three full-compare units on each event manager. These compare units use GP timer1 as the time base and generate six outputs for compare and PWM-waveform generation using programmable deadband circuit. The state of each of the six outputs is configured independently. The compare registers of the compare units are double-buffered, allowing programmable change of the compare/PWM pulse widths as needed.Programmable deadband generatorThe deadband generator circuit includes three 8-bit counters and an 8-bit compare register. Desired deadband values (from 0 to 24 µs) can be programmed into the compare register for the outputs of the three compare units. The deadband generation can be enabled/disabled for each compare unit output individually. The deadband-generator circuit produces two outputs (with orwithout deadband zone) for each compare unit output signal. The output states of the deadband generator are configurable and changeable as needed by way of the double-buffered ACTR register.PWM waveform generationUp to eight PWM waveforms (outputs) can be generated simultaneously by each event manager: three independent pairs (six outputs) by the three full-compare units with programmable deadbands, and two independent PWMs by the GP-timer compares.PWM characteristicsCharacteristics of the PWMs are as follows:●16-bit registers●Programmable deadband for the PWM output pairs, from 0 to 24 µs●Minimum deadband width of 50 ns●Change of the PWM carrier frequency for PWM frequency wobbling as needed●Change of the PWM pulse widths within and after each PWM period as needed●External-maskable power and drive-protection interrupts●Pulse-pattern-generator circuit, for programmable generation of asymmetric,symmetric, and four-space vector PWM waveforms●Minimized CPU overhead using auto-reload of the compare and period registersCapture unitThe capture unit provides a logging function for different events or transitions. The values of the GP timer 2 counter are captured and stored in the two-level-deep FIFO stacks when selected transitions are detected on capture input pins, CAPx (x = 1, 2, or 3 for EV A; and x = 4, 5, or 6 for EVB). The capture unit consists of three capture circuits.Capture units include the following features:●One 16-bit capture control register, CAPCON (R/W)●One 16-bit capture FIFO status register, CAPFIFO (eight MSBs are read-only, eightLSBs are write-only)●Selection of GP timer 2 as the time base●Three 16-bit 2-level-deep FIFO stacks, one for each capture unit●Three Schmitt-triggered capture input pins (CAP1, CAP2, and CAP3)—one input pinper capture unit. [All inputs are synchronized with the device (CPU) clock. In order fora transition to be captured, the input must hold at its current level to meet two risingedges of the device clock. The input pins CAP1 and CAP2 can also be used as QEPinputs to the QEP circuit.]●User-specified transition (rising edge, falling edge, or both edges) detection●Three maskable interrupt flags, one for each capture unitEnhanced analog-to-digital converter (ADC) moduleA simplified functional block diagram of the ADC module is shown in Figure 1. The ADC module consists of a 10-bit ADC with a built-in sample-and-hold (S/H) circuit. Functions of the ADC module include:●10-bit ADC core with built-in S/H●Fast conversion time (S/H + Conversion) of 500 ns●16-channel, muxed inputs●Autosequencing capability provides up to 16 ―autoconversions‖ in a single session.Each conversion can be programmed to select any 1 of 16 input channels●Sequencer can be operated as two independent 8-state sequencers or as one large16-state sequencer (i.e., two cascaded 8-state sequencers)●Sixteen result registers (individually addressable) to store conversion values●Multiple triggers as sources for the start-of-conversion (SOC) sequence✧S/W – software immediate start✧EV A – Event manager A (multiple event sources within EV A)✧EVB – Event manager B (multiple event sources within EVB)✧Ext – External pin (ADCSOC)●Flexible interrupt control allows interrupt request on every end of sequence (EOS) orevery other EOS●Sequencer can operate in ―start/stop‖ mode, allowing multiple ―time-sequencedtriggers‖ to synchronize conv ersions●EV A and EVB triggers can operate independently in dual-sequencer mode●Sample-and-hold (S/H) acquisition time window has separate prescale control●Built-in calibration mode●Built-in self-test modeThe ADC module in the ‘240x has been enhanced to pro vide flexible interface to event managers A and B. The ADC interface is built around a fast, 10-bit ADC module with total conversion time of 500 ns (S/H + conversion). The ADC module has 16 channels, configurable as two independent 8-channel modules to service event managers A and B. The two independent 8-channel modules can be cascaded to form a 16-channel module. Figure 2 shows the block diagram of the ‘240x ADC module.The two 8-channel modules have the capability to autosequence a series of conversions,each module has the choice of selecting any one of the respective eight channels available through an analog mux. In the cascaded mode, the autosequencer functions as a single 16-channel sequencer. On each sequencer, once the conversion is complete, the selected channel value is stored in its respective RESULT register. Autosequencing allows the system to convert the same channel multiple times, allowing the user to perform oversampling algorithms. This gives increased resolution over traditional single-sampled conversion results.Figure 2. Block Diagram of the ‘240x ADC ModuleFrom TMS320LF2407, TMS320LF2406, TMS320LF2402TMS320LC2406, TMS320LC2404, MS320LC2402数字信号处理控制器TMS320LF240x和TMS320LC240x系列芯片作为’24x系列DSP控制器的新成员,是C2000平台下的一种定点DSP芯片。
毕业设计论文 外文文献翻译 光伏电力系统 中英文对照
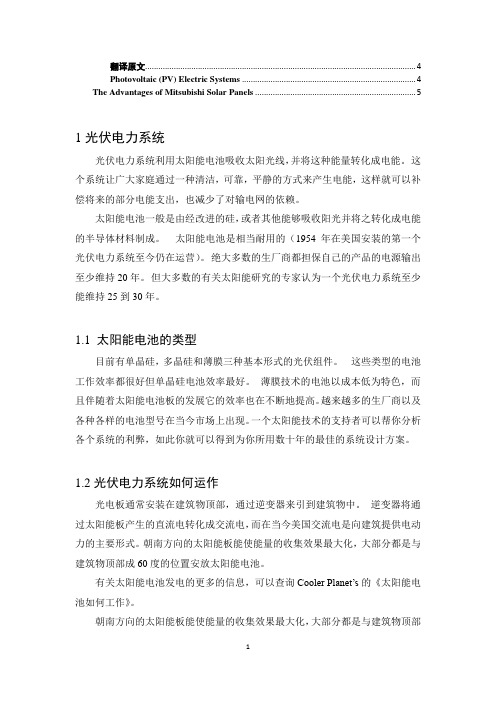
翻译原文 (4)Photovoltaic (PV) Electric Systems (4)The Advantages of Mitsubishi Solar Panels (5)1光伏电力系统光伏电力系统利用太阳能电池吸收太阳光线,并将这种能量转化成电能。
这个系统让广大家庭通过一种清洁,可靠,平静的方式来产生电能,这样就可以补偿将来的部分电能支出,也减少了对输电网的依赖。
太阳能电池一般是由经改进的硅,或者其他能够吸收阳光并将之转化成电能的半导体材料制成。
太阳能电池是相当耐用的(1954年在美国安装的第一个光伏电力系统至今仍在运营)。
绝大多数的生厂商都担保自己的产品的电源输出至少维持20年。
但大多数的有关太阳能研究的专家认为一个光伏电力系统至少能维持25到30年。
1.1 太阳能电池的类型目前有单晶硅,多晶硅和薄膜三种基本形式的光伏组件。
这些类型的电池工作效率都很好但单晶硅电池效率最好。
薄膜技术的电池以成本低为特色,而且伴随着太阳能电池板的发展它的效率也在不断地提高。
越来越多的生厂商以及各种各样的电池型号在当今市场上出现。
一个太阳能技术的支持者可以帮你分析各个系统的利弊,如此你就可以得到为你所用数十年的最佳的系统设计方案。
1.2光伏电力系统如何运作光电板通常安装在建筑物顶部,通过逆变器来引到建筑物中。
逆变器将通过太阳能板产生的直流电转化成交流电,而在当今美国交流电是向建筑提供电动力的主要形式。
朝南方向的太阳能板能使能量的收集效果最大化,大部分都是与建筑物顶部成60度的位置安放太阳能电池。
有关太阳能电池发电的更多的信息,可以查询Cooler Planet’s的《太阳能电池如何工作》。
朝南方向的太阳能板能使能量的收集效果最大化,大部分都是与建筑物顶部成60度的位置安放太阳能电池。
1.3 太阳能电池板与光伏建筑一体化太阳能电池板是用于捕获太阳光的平面板,他们以阵列的形式安装在建筑物顶部或者柱子上。
他们是传统的用于获得太阳能的阵列形式。
光伏发电介绍英文作文
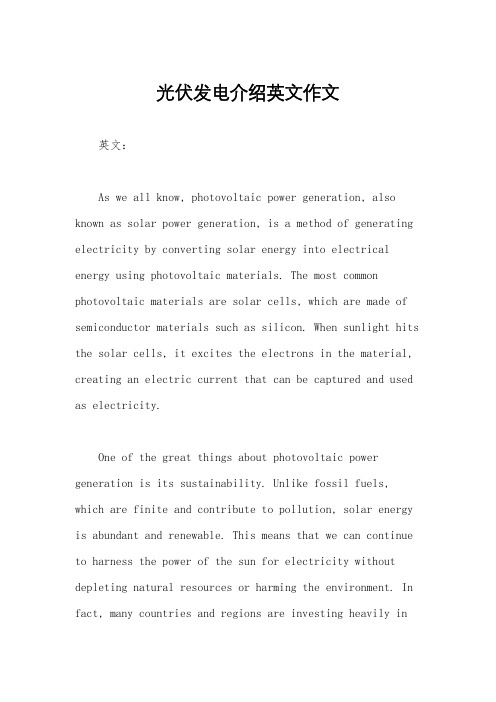
光伏发电介绍英文作文英文:As we all know, photovoltaic power generation, also known as solar power generation, is a method of generating electricity by converting solar energy into electrical energy using photovoltaic materials. The most common photovoltaic materials are solar cells, which are made of semiconductor materials such as silicon. When sunlight hits the solar cells, it excites the electrons in the material, creating an electric current that can be captured and used as electricity.One of the great things about photovoltaic power generation is its sustainability. Unlike fossil fuels, which are finite and contribute to pollution, solar energy is abundant and renewable. This means that we can continue to harness the power of the sun for electricity without depleting natural resources or harming the environment. In fact, many countries and regions are investing heavily insolar power as a clean and sustainable energy source.Another benefit of photovoltaic power generation is its versatility. Solar panels can be installed on a wide rangeof surfaces, from rooftops to open fields, making it a flexible option for generating electricity. In addition, solar panels can be used in both grid-connected and off-grid systems, providing power to remote areas that may not have access to traditional electricity sources.In my own experience, I have seen the impact of photovoltaic power generation firsthand. In my hometown, many households have installed solar panels on their roofsto generate electricity for their own use. This has notonly reduced their reliance on traditional power sources, but also saved them money on electricity bills. Furthermore, I have visited solar farms where vast fields of solarpanels are used to generate large amounts of electricityfor the local community. It's amazing to see how the powerof the sun can be harnessed to provide clean andsustainable energy for so many people.Overall, photovoltaic power generation is a promising and environmentally friendly method of generating electricity. With ongoing advancements in technology and increasing awareness of the importance of renewable energy, I believe that solar power will play an increasingly significant role in meeting our energy needs in the future.中文:众所周知,光伏发电,也被称为太阳能发电,是一种利用光伏材料将太阳能转换为电能的发电方法。
太阳能光伏系统蓄电池充电毕业论文中英文资料对照外文翻译文献综述

中英文资料对照外文翻译文献综述Design of a Lead-Acid Battery Charging and Protecting IC in Photovoltaic System1.IntroductionSolar energy as an inexhaustible, inexhaustible source of energy more and more attention. Solar power has become popular in many countries and regions, solar lighting has also been put into use in many cities in China. As a key part of the solar lighting, battery charging and protection is particularly important. Sealed maintenance-free lead-acid battery has a sealed, leak-free, pollution-free, maintenance-free, low-cost, reliable power supply during the entire life of the battery voltage is stable and no maintenance, the need for uninterrupted for the various types of has wide application in power electronic equipment, and portable instrumentation. Appropriate float voltage, in normal use (to prevent over-discharge, overcharge, over-current), maintenance-free lead-acid battery float life of up to 12 ~ 16 years float voltage deviation of 5% shorten the life of 1/2. Thus, the charge has a major impact on this type of battery life. Photovoltaic, battery does not need regular maintenance, the correct charge and reasonable protection, can effectively extend battery life. Charging and protection IC is the separation of the occupied area and the peripheral circuit complexity. Currently, the market has not yet real, charged with the protection function is integrated on a single chip. For this problem, design a set of battery charging and protection functions in one IC is very necessary.2.System design and considerationsThe system mainly includes two parts: the battery charger module and the protection module. Of great significance for the battery as standby power use of the occasion, It can ensure that the external power supply to the battery-powered, but also in the battery overcharge, over-current and an external power supply is disconnected the battery is to put the state to provide protection, the charge and protection rolled into one to make the circuit to simplify and reduce valuable product waste of resources. Figure 1 is a specific application of this Ic in the photovoltaic powergeneration system, but also the source of this design.Figure1 Photovoltaic circuit system block diagramMaintenance-free lead-acid battery life is usually the cycle life and float life factors affecting the life of the battery charge rate, discharge rate, and float voltage. Some manufacturers said that if the overcharge protection circuit, the charging rate can be achieved even more than 2C (C is the rated capacity of the battery), battery manufacturers recommend charging rate of C/20 ~ C/3. Battery voltage and temperature, the temperature is increased by 1 °C, single cell battery voltage drops 4 mV , negative temperature coefficient of -4 mV / ° C means that the battery float voltage. Ordinary charger for the best working condition at 25 °C; charge less than the ambient temperature of 0 °C; at 45 °C may shorten the battery life due to severe overcharge. To make the battery to extend the working life, have a certain understanding and analysis of the working status of the battery, in order to achieve the purpose of protection of the battery. Battery, there are four states: normal state, over-current state over the state of charge, over discharge state. However, due to the impact of the different discharge current over-capacity and lifetime of the battery is not the same, so the battery over discharge current detection should be treated separately. When the battery is charging the state a long time, would severely reduce the capacity of the battery and shorten battery life. When the battery is the time of discharge status exceeds the allotted time, the battery, the battery voltage is too low may not be able to recharge, making the battery life is lower.Based on the above, the charge on the life of maintenance-free lead-acid batteries have a significant impact, while the battery is always in good working condition, battery protection circuit must be able to detect the normal working condition of the battery and make the action the battery can never normal working state back to normal operation, in order to achieve the protection of the battery.3.Units modular design3.1The charging module Chip, charging module block diagram shown in Figure 2. The circuitry includes solar battery array Charge controller controller Discharge controller DC load accumulatorcurrent limiting, current sensing comparator, reference voltage source, under-voltage detection circuit, voltage sampling circuit and logic control circuit.Figure2 Charging module block diagramThe module contains a stand-alone limiting amplifier and voltage control circuit, it can control off-chip drive, 20 ~30 mA, provided by the drive output current can directly drive an external series of adjustment tube, so as to adjust the charger output voltage and current . V oltage and current detection comparator detects the battery charge status, and control the state of the input signal of the logic circuit. When the battery voltage or current is too low, the charge to start the comparator control the charging. Appliances into the trickle charge state when the cut-off of the drive, the comparator can output about 20 mA into the trickle charge current. Thus, when the battery short-circuit or reverse, the charger can only charge a small current, to avoid damage to the battery charging current is too large. This module constitutes a charging circuit charging process is divided into two charging status: high-current constant-current charge state, high-voltage charge status and low-voltage constant voltage floating state. The charging process from the constant current charging status, the constant charging current of the charger output in this state. And the charger continuously monitors the voltage across the battery pack, the battery power has been restored to 70% to 90% of the released capacity when the battery voltage reaches the switching voltage to charge conversion voltage Vsam charger moves to the state of charge. In this state, the charger output voltage is increased to overcharge pressure driverV oltage amplifierV oltage sampling comparatorStart amplifier State level control Charging indicator Logical module Undervoltage detection circuit R- powerCurrent sampling comparator Limiting amplifier Power indicatorV oc is due to the charger output voltage remains constant, so the charging current is a continuous decline. Current down to charge and suspend the current Ioct, the battery capacity has reached 100% of rated capacity, the charger output voltage drops to a lower float voltage VF.3.2 Protection ModuleChip block diagram of the internal protection circuit shown in Figure 3. The circuit includes control logic circuit, sampling circuit, overcharge detection circuit, over-discharge detection comparator, overcurrent detection comparator, load short-circuit detection circuit, level-shifting circuit and reference circuit (BGR).Figure3 Block diagram of battery protectionThis module constitutes a protection circuit shown in Figure 4. Under the chip supply voltage within the normal scope of work, and the VM pin voltage at the overcurrent detection voltage, the battery is in normal operation, the charge and discharge control of the chip high power end of the CO and DO are level, when the chip is in normal working mode. Larger when the battery discharge current will cause voltage rise of the VM pin at the VM pin voltage at above the current detection voltage Viov, then the battery is the current status, if this state to maintain the tiov overcurrent delay time, the chip ban on battery discharge, then the charge to control the end of CO is high, the discharge control side DO is low, the chip is in the current mode, general in order to play on the battery safer and more reasonable protection, the chip will battery over-discharge current to take over the discharge current delay time protection. The general rule is that the over-discharge current is larger, over the Sampling circuitOver discharge detection comparator Control logic circuitLevel conversion circuit Overcharge detection comparator Over-current detection comparator2 Over-current detection comparator1Over-current detection circuitLoad short detection circuitshorter the discharge current delay time. Above Overcharge detection voltage, the chip supply voltage (Vdd> Vcu), the battery is in overcharge state, this state is to maintain the corresponding overcharge delay time tcu chip will be prohibited from charging the battery, then discharge control end DO is high, and charging control terminal CO is low, the chip is in charging mode. When the supply voltage of the chip under the overdischarge detection voltage (Vdd <Vdl,), then the battery is discharged state, this state remains the overdischarge delay time tdl chip will be prohibited to discharge the battery at this time The charge control side CO is high, while the discharge control terminal DO is low, the chip is in discharge mode.ProtectionmoduleFigure4 Protection circuit application schematic diagram4.Circuit DesignTwo charge protection module structure diagram, the circuit can be divided into four parts: the power detection circuit (under-voltage detection circuit), part of the bias circuit (sampling circuit, the reference circuit and bias circuit), the comparator (including the overcharge detection /overdischarge detection comparator, over-current detection and load short-circuit detection circuit) and the logic control part.This paper describes the under-voltage detection circuit (Figure 5), and gives the bandgap reference circuit (Figure 6).Figure5 Under-voltage detection circuitFigure6 A reference power supply circuit diagramBattery charging, voltage stability is particularly important, undervoltage, overvoltage protection is essential, therefore integrated overvoltage, undervoltage protection circuit inside the chip, to improve power supply reliability and security. And protection circuit design should be simple, practical, here designed a CMOS process, the undervoltage protection circuit, this simple circuit structure, process and easy to implement and can be used as high-voltage power integrated circuits and other power protection circuit.Undervoltage protection circuit schematic shown in Figure 5, a total of five components: the bias circuit, reference voltage, the voltage divider circuit, differential amplifier, the output circuit. The circuit supply voltage is 10V; the M0, M1, M2, R0 is the offset portion of the circuit to provide bias to the post-stage circuit, the resistance, Ro, determine the circuit's operating point, the M0, M1, M2 form a current mirror; R1 M14 is the feedback loop of the undervoltage signal; the rest of the M3, M4 and M5, M6, M7, M8, M9, M10, M11, M12, M13, M14, composed of four amplification comparator; M15, DO, a reference voltage, the comparator input with the inverting Biasing circuit Reference circuit Bleeder circuit difference amplifier Output circuitAmplifierAmplifierinput is fixed (V+), partial pressure of the resistance R1, R2, R3, the input to the inverting input of the comparator, when the normal working of the power supply voltage, the inverting terminal of the voltage detection is lost to the inverting terminal voltage of the comparator is greater than V+. Comparator output is low, M14 cutoff, feedback circuit does not work; undervoltage occurs, the voltage divider of R1, R2, R3, reaction is more sensitive, lost to the inverting input voltage is less than V when the resistor divider, the comparator the output voltage is high, this signal will be M14 open, the voltage across R into M at both ends of the saturation voltage close to 0V, thereby further driving down the R1> R2, the partial pressure of the output voltage, the formation of the undervoltage positive feedback. Output, undervoltage lockout, and plays a protective role.5. Simulation results and analysisThe design of the circuit in CSMC 0.6 μm in digital CMOS process simulation and analysis of the circuit. In the overall simulation of the circuit, the main observation is that the protection module on the battery charge and discharge process by monitoring Vdd potential and Vm potential leaving chip CO side and DO-side changes accordingly. The simulation waveform diagram shown in Figure 7, the overall protection module with the battery voltage changes from the usual mode conversion into overcharge mode, and then return to normal working mode, and then into the discharge mode, and finally back to normal working mode. As the design in the early stages of the various parameters to be optimized, but to provide a preliminary simulation results.Figure7 Overvoltage and under-voltage protection circuit simulation waveform6.ConclusionDesigned a set of battery charging and protection functions in one IC. This design not only can reduce the product, they can reduce the peripheral circuit components. The circuit uses the low-power design. This project is underway to design optimization stage, a complete simulation can not meet the requirements, but also need to optimize the design of each module circuit.光伏系统中蓄电池的充电保护IC电路设计1.引言太阳能作为一种取之不尽、用之不竭的能源越来越受到重视。
光伏发电和风力发电混合发电系统论文中英文资料对照外文翻译文献综述
中英文资料对照外文翻译译文在混合光伏阵列中采用滑模技术的电源控制发电系统摘要变结构控制器来调节输出功率的一个独立的混合发电系统。
该系统包括光伏发电和风力发电,存储电池组和一个变量的单相负载。
控制律承认两种操作模式。
第一条用在当日晒度足够满足对电力的需求的情况下。
第二运作模式应用在日晒度不足的时候。
后者致使系统在最大功率操作点(MPOP)操作下存储尽可能多的能量。
根据IncCo nd算法开发的一种新方法。
滑模控制用于技术设计的控制律。
这些技术提供了一个简单的控制律设计框架,并有助于它们自带的鲁棒性。
最后,指导方针根据考虑为实际系统的设计。
1引言可再生能源,如风力和太阳能被认为是非常前途的能源。
它们拥有可以满足不断增加的世界能源需求的特点。
另一方面,他们是基于无公害转换流程,它们需要的主要资源是取之不尽,用之不竭,并且免费的。
对于远程、远离电网的地方,它往往是比用输电线路[1] 提供一个独立的电力来源拥有可行性。
在这些电网中,在混合动力系统结合模块的基础上,可再生能源发电以柴油为动力的备用发电机已考虑ERED等效为一个可行的选择[2, 3]。
然而,柴油发电机在孤立的燃料供应和其运作领域是相当麻烦,相比较可再生能源,显得不划算[4]。
为了取代柴油备用发电机,独立的混合动力系统经常采用结合可再生能源来源的TARY 型材,如风力和光伏发电,合适的存储设备,如电池。
自存储成本仍然是一个重大的经济约束,通常光伏/风能/电池系统是用“适当”的大小以减少资本成本。
本文提出了一种控制策略,以规范的混合动力系统,包括光伏发电和风力发电,蓄电池组和可变负载的输出功率作为研究。
控制可调整的光伏发电、风力发电,以满足负载和电池充电的电源要求。
系统以在独立控制下的最大发电的主要目标。
该控制器的设计开发,在之前的文献[5]中提过。
因此,根据不同的大气条件,不同的光伏阵列控制律使用的范围不同。
第一条用在暴晒的地方,运作模式足以提供的总功率需求,和风力发电一起适用。
多晶硅太阳能电池 毕业论文文献翻译 中英文对照
英文翻译Polycrystalline silicon solar cellsAs we all know, solar energy has many advantages, photovoltaic power generation will provide the main energy of mankind, but at present it, to make solar power a large market, is the general consumer acceptance, increased solar cell efficiency and reduce production costs should be our overriding goal, from the current development of the international solar cell can see the trend of its silicon, polycrystalline silicon, ribbon silicon, thin film materials (including trend of its silicon, polycrystalline silicon, ribbon silicon, thin film materials (including microcrystalline silicon thin films, compound-based thin film and dye film).From industrial development, it has been the focus of the direction of single crystal to polycrystalline, mainly due to;(1)the beginning and end of solar cell materials can supply less and less;(2)in terms of the solar cell, a square substrate is more cost-effective, by direct coagulation casting method and obtained direct access to a square polysilicon materials;(3)of polysilicon production technology continue to make progress, casting furnace automatic production cycle of each (50 hours) can produce over 200 kg ingots, grain size to achieve centimeter level;(4)in recent years as research and development of silicon technology quickly, in which technology has been applied to the production of polycrystalline silicon cells, such as selective etching the emitter, back surface field, corrosion suede , surface and bulk passivation, thin metal gate electrode, using screen-printing technology enables the gate electrode width down to 50 microns to 15 microns high, rapid thermal annealing technology for polysilicon production process can significantly shorten the time, single time of thermal process can be completed within a minute using this technology in the 100 square centimeters of silicon chip to make the cell conversion efficiency of over 14%. It was reported in 50 to 60 micron silicon substrate produced more than 16% cell efficiency.Mechanical groove, screen printing technology in polycrystalline on the efficiency of more than 17%, no mechanical groove in the same area on the efficiency of 16%, with buried gate structure, mechanical groove 130 on a square centimeter of polycrystalline cell efficiency of 15.8%.The following two aspects of the polysilicon to discuss battery technology.Laboratory efficient battery technology Laboratory techniques often do not consider the cost of battery production and mass production can only achieve maximum efficiency of the method and means to provide specific materials and processes that can achieve the limit.1.On the absorption of lightFor the optical absorption is mainly:(1)reduce the surface reflection;(2)Change the path of light in the cell body;(3)using the back reflection.For silicon, anisotropic chemical etching method applied in (100) surfaceproduced textured pyramid-shaped, lower surface light reflection. But silicon crystal to deviate from the (100) surface, using the above methods can not make even the suede, the current use of the following methods:(1)laser grooveGroove with a laser method can be produced in the polysilicon surface, inverted pyramid structure, in 500~900nm wavelength range, reflectance was 4 to 6%, with double-layer antireflection coating surface produced considerable. In the (100) reflection of silicon chemical production rate of 11% of the flock. Produced by laser textured surface than in the smooth double-layer antireflection coating film (ZnS/MgF2) short circuit current to increase by about 4%, mainly long-wave light (wavelength greater than 800nm) the reasons for slanting into the battery. Laser production of suede problems in etching, surface damage caused by the introduction of a number of impurities at the same time, through chemical treatment to remove surface damage layer. Solar cells made by this method are usually higher short circuit current, open circuit voltage is not high, mainly due to cell surface area increased, the recombination current increase.(2)Chemical grooveApplication of mask (Si3N4or SiO2) isotropic corrosion, etching solutions for acid etching solutions, but also for the higher concentration of sodium hydroxide or potassium hydroxide solution, the method can not create the kind formed by anisotropic etching cone-like structure. According to reports, the approach down the face of the formation of micron spectral range 700 to 1030 significantly reduced reflex. But the mask layer will be formed at higher temperatures, causing decreased performance polysilicon materials, especially for lower quality polycrystalline materials, reduce the minority carrier lifetime. Application of the technology made of polysilicon in cell conversion efficiency of 16.4%. Mask layer screen printing method can also be formed.(3)reactive ion corrosion (RIE)This method is a non-mask etching process, the formation of suede particularly low reflectivity in the spectral range 450 to 1000 micron reflectivity can be less than 2%. Only from the optical point of view, is an ideal method, but problem is serious silicon surface damage, the battery open circuit voltage and fill factor decreased.(4)produced antireflection filmFor efficient solar cells, the most common and most effective way is to double-layer antireflection coatings deposited ZnS/MgF2, its optimal thickness depends on the thickness of the oxide layer below the surface characteristics and battery, for example, the surface is smooth or textured surface,anti-reflection technology has evaporated Ta2O5, PECVD deposition Si3N3 so. ZnO conductive film can be used as anti-reflective material.2.MetallizationIn the efficient production of the battery, the metal electrode to the battery design parameters such as surface doping concentration, PN junction depth, the metal material to match. General area of small laboratory cell (area less than 4cm2), so they need small metal gate line (less than 10 microns), the general approach to lithography,electron beam evaporation, rge-scale production of industrial plating process is also used, but the combination of evaporation and lithography, do not belong to low-cost technology.3.PN junction formation technology(1)emitter formation and phosphorus getteringFor efficient solar cells, emitter diffusion formation of choice commonly used in the formation of heavy metal impurities in the region below the electrode in the spread between the electrodes to achieve light levels, the shallow emitter diffusion is increased concentration of cell response to blue light, and also allows silicon surface easily passivated. Two-step diffusion method diffusion process, diffusion process and increase corrosion buried diffusion process. Currently used selection proliferation, 15 × 15 cell conversion efficiency of 16.4%, n + +, n + sheet resistance of the surface region were 20Ω and 80Ω.For Mc-Si materials, expansion of phosphorus gettering effect on the battery has been widely studied, a longer period of phosphorus gettering process (usually 3 to 4 hours), make some of Mc-Si of the minority carrier diffusion length increase of two orders of magnitude.(2)the formation of back surface field and aluminum getteringIn Mc-Si cell, the back p + p junction by the formation of uniform diffusion of aluminum or boron, boron source is generally BN, BBr, APCVD SiO2: B2O8 such as evaporation or diffusion of aluminum screen printing of aluminum, 800 degrees completed sintering , on the role of aluminum gettering carried out extensive research, and in different phosphorus diffusion gettering, aluminum gettering at a relatively low temperature. Physical defects which also involved the dissolution and deposition of impurities, while in higher temperatures, the deposition of impurities easily dissolve into the silicon, on the Mc-Si have a negative impact. Far, to the regional background field has been applied to silicon solar cell technology, but in the polysilicon, the application of aluminum or the back surface field structure.(3)Double Mc-Si cellsMc-Si double the battery positive side for the conventional structure, on the back for the N + and P + cross-cutting structure, so that generated a positive light, but in the back of the photo birth rate near the back electrode can be effectively absorbed. Back electrode as an effective complement to the positive electrode, also planted as an independent flow of sub-collector on the back of the light and the scattered light to be effective, it was reported in the AM1.5 conditions, the conversion efficiency of over 19%.360毕业设计网4.Surface and bulk passivationFor Mc-Si, due to higher grain boundary exist, point defects (vacancies, interstitial atoms, metal impurities, oxygen and nitrogen and their compounds) and in vivo defect on the surface passivation is particularly important, in addition to the previously mentioned The gettering, the passivation process has a number of ways, by thermal oxidation to silicon dangling bonds saturated is a relatively common method, make Si-SiO2interface recombination velocity greatly decreased, the passivation effect depends on the launching area surfaceconcentration, the interface state density and the electron and hole cross sections were floating. Annealed in hydrogen atmosphere can passivation effect is more obvious. Nitride deposited by PECVD the recent positive is very effective because the process of film has the effect of hydrogenation. The process can also be applied to large scale production. Application of Remote PECVD Si3N4 surface recombination velocity is less than can 20cm / s.多晶硅太阳能电池众所周知,利用太阳能有许多优点,光伏发电将为人类提供主要的能源,但目前来讲,要使太阳能发电具有较大的市场,被广大的消费者接受,提高太阳电池的光电转换效率,降低生产成本应该是我们追求的最大目标,从目前国际太阳电池的发展过程可以看出其发展趋势为单晶硅、多晶硅、带状硅、薄膜材料(包括微晶硅基薄膜、化合物基薄膜及染料薄膜)。
太阳能发电-中英文翻译Solarelectricalenergygeneration文献翻译
文献翻译英文原文:Solar electrical energy generationAlong with economical development, society's progress, the people to the energy proposed that more and more high request, seeks for the new energy to become the urgent topic which the current humanity faces. The existing energy mainly has 3 kinds, namely thermal power, water and electricity and nuclear power.The thermal power needs to burn fossil fuels and so on bunker coal, petroleum. On the one hand the fossil fuel reserves limited, the fever are less, is facing the danger which dries up. It is estimated that the world oil resource will have 30 years then to dry up again. On the other hand the combustion fuel will discharge CO2 and the sulfur oxide compound, will therefore cause the greenhouse effect and the acid rain, will worsen the terrestrial environment.The water and electricity must submerge the massive lands, has the possibility to cause the ecological environment to destroy, moreover large reservoir, once collapses, the consequence will be inconceivable. Moreover, country's hydro-electric resources are also limited, moreover must receive the season influence.The nuclear power in the normal condition no doubt is clean, but has the nuclear leakage accidentally, the consequence is similarly fearful. The former Soviet Union Chernobyl Nuclear Power Station accident, has caused 9,000,000 people to receive the varying degree harm, moreover this influence has not terminated.These force the people to seek for the new energy. The new energy must simultaneously meet two conditions: First, the implication rich will not dry up; Second, is safe, is clean, will not threaten the humanity and the destruction environment. At present found the new energy mainly had two kinds:first, solar energy; second, fuel cell. Moreover, the wind power generation may also be the auxiliary new energy. And, the most ideal new energy is greatly positive energy.1. The solar electrical energy generation is the most ideal new energyShines is huge on Earth's solar energy, about 40 minutes shine on Earth's solar energy, then sufficiently supplies global humanity one year energy the expense. It can be said that the solar energy is true inexhaustible, the inexhaustible energy. Moreover the solar electrical energy generation is absolutely clean, does not have the environmental damage. Therefore the solar electrical energy generation is honored asis the ideal energy.Obtains the electric power from the solar energy, must carry on the electro-optical transformation through the greatly positive battery to realize. It completely was formerly different with other power source electricity generation principle, has the following characteristic: ①Non-depletion danger; ②Clean (does not have environmental damage) absolutely; ③It is not distributed the resources the region the limit; ④But is using electricity place nearby generates electricity; ⑤The energy quality is high; ⑥The user easy to accept from the sentiment; ⑦The gain energy expenditure's time is short. The deficiency is:①The illumination energy distribution density is small, namely must take the huge area; ②Obtains the energy with four seasons, the day and nights and cloudy clear and so on meteorological conditions concerns. But generally speaking, the flaw does not cover the fine jade, takes the new energy, the solar energy has the enormous merit, therefore receives various countries the value.Must enable the solar electrical energy generation to achieve the practical level truly; first, must raise the solar energy electro-optic conversion efficiency and reduce its cost; second, must realize the solar electrical energy generation with present's electrical network networking.At present, solar panels mainly has the mono-crystalline silicon, the polycrystalline silicon, the amorphous state silicon three kinds. The mono-crystalline silicon solar cell conversion efficiency is highest, has reached above 20%, but the price is also the most expensive. The amorphous state silicon solar cell conversion efficiency is lowest, but the price is the cheapest, from now on most will be hopeful uses in generally generating electricity will be this kind of battery. Once its big area module electro-optic conversion efficiency achieves 10%, each watt generating set price falls to 1-2 US dollars, then sufficiently compete with present's electricity generation way. It is estimated that at the end of this century it may achieve this level.Certainly, in the special use and the laboratory uses the solar cell efficiency must be much higher, if the US Boeing develops by the gallium arsenic semiconductor with the positive electricity place which too the stibium gallium semiconductor overlaps becomes, the electro-optic conversion efficiency may reach 36%, has caught up with the coal-burning electricity generation efficiency quickly. But because it is too expensive, at present can only be restricted on the satellite uses.2. Solar electrical energy generation applicationAlthough solar electrical energy generation day and nights, clear and rain, season influence, but may carry on scattered, therefore it is suitable for various each household minute to carry on the electricity generation severally, moreover must join in the power supply network, causes each family when the electric power is wealthy may sold it to the Electricity company, when the insufficiency be possible from the Electricity company to buy up. Realizes this point’s technology not to be difficult to solve, the key lies in must have the corresponding legal safeguard. Now the US, Japan and so on developed country has made the corresponding law, guaranteed that carries on the solar electrical energy generation the family benefit, encourages the family to carry on the solar electrical energy generation.Japan has realized the solar electrical energy generation system the same electricity company electrical network's networking in April, 1992, had some families to start to install the solar electrical energy generation equipment. The Japanese Ministry of International Trade and Industry started from 1994 take individual housing as an object, implemented to purchases the solar electrical energy generation equipment's expense to subsidize 2/3 systems. Requests the first year had 1000 households families, when 2000 to have 70,000 households families to install the solar electrical energy generation equipment.According to the Japanese Department concerned estimates in the Japanese 21,000,000 households individual housing, if has 80% to install the solar electrical energy generation equipment, then may satisfy 14% which the national total power needs, if units and so on factory and office building also carry on the solar electrical energy generation with the room, then the solar electrical energy generation will occupy the national electric power 30%-40%. The current hindrance solar electrical energy generation popular most primary factor is the expense is expensive In order to satisfy the general family power requirement 3 kilowatt generating system, needs 6,000,000 to 7,000,000 Japanese Yen, has not included the installment wages. The concerned expert believed that when must fall at least to 1,000,000 to 2,000,000 Japanese Yen, the solar electrical energy generation only then can popularize truly. The key to reduce the expense lie in the solar cell to raise the conversion efficiency and to reduce the cost.Some time ago, the US Texas Instruments Company and SCE Corporation announced that they develop one kind of new solar cell, each unit is the diameter less than 1 millimeter bead, they distribute regularly densely and numerously on the softaluminum foil, looks like many silkworm eggs to cling on the paper is the same. Then distributes in about 50 square centimeters area has 1,700 such units. This kind of new battery's characteristic is, although the conversion efficiency has 8%-10%, but the price is cheap. Moreover aluminum foil bottom bush soft solid, may look like the cloth to fold equally at will, and durable, hangs in toward the sun place then may generate electricity, is convenient. It is said that uses this kind of new solar cell, so long as each watt power capacity equipment 1.5 to 2 US dollars, moreover each round of once electricity's expense might also fall to 14 cents about, definitely may compete with the ordinary power plant. Each family hangs this kind of battery on the roof, the wall toward the sun, every year may obtain 1,000-2,000 degrees electric powers.3. Solar electrical energy generation prospectThe solar electrical energy generation has a more exciting plan. First, Japan proposes creates the century plan. Prepares the desert and the sea area carries on the electricity generation using the ground, and through superconducting cable whole world solar power station connection unification electrical network in order to global. According to reckoning, to 2000, in 2050, in 2100, even if all uses the solar electrical energy generation supplies the whole world energy, the occupying land area is also 651,100 square kilometer, 1,867,900 square kilometer, 8,291,900 square kilometers. 8,291,900 square kilometers only occupy the complete sea area 2.3% or the complete desert area 51.4%, even is the Sahara area 91.5%. Therefore this plan has the possibility to realize.Another one is the space electricity generation plan. As early as in 1980 the NASA and Department of Energy proposed that in the spatial construction solar power station tentative plan, prepares on the synchronous orbit to put one long 10 kilometers, to extend 5 kilometer big plates, above covers entirely the solar cell, like this then may provide 5,000,000 kilowatts electric powers. But this needs to solve to the ground wireless electric transmission question. Already proposed with the micro wave beam, the laser beam and so on each kind of plan. At present although has realized the short distance, the short time, the low power microwave wireless electric transmission with the mockup, but to true practical also has the long distance.Along with our country technology's development, in 2006, China had three enterprises to enter global first ten, symbolizes that China will become one of global new energy science and technology central, in the world the solar energy light bends down widespread application, what caused present to be deficient was raw materialsupply and the price rise, we needed dissemination of technology at the same time, to use the new technology, with the aim of reducing the cost large scale, was this new energy long-term development provides the driving force!The solar energy use mainly divides into several aspects: The family with the small solar energy power plant, the large-scale incorporation power plant, the building integration light bends down the glass curtain wall, the solar energy street light, the scenery supplementary street light, the scenery supplementary power supply system and so on, now main application way for construction integration and scenery supplementary system.The world present had the nearly 200 companies to produce the solar cell, but produces the plants mainly hand in the Japanese business.Recent years the South Korean Tri-star, LG expressed the positive participation's desire, China two sides across the Taiwan Strait are similarly very warm-hearted. It is reported that our country Taiwan in 2008 crystallizes the silicon solar cell productivity to reach 2.2GW, later will expand by every year 1GW productivity in the past and started to produce the thin film solar cell, this year will strengthen vigorously, Taiwan anticipated that “the solar cell great nation” emulated to Europe. in 2010 various countries and the area have above 1GW the productive plan solar cell manufacturer to have Japanese Sharp, German Q-Cells, Scho~Solar, turns 5 prestige RWE Solar, Chinese Suntech Power and so on 5 companies, above other 7 500MW productivity company.Recent years the world solar cell market advanced triumphantly, an excellence, but the rare financial storm brought the economic crisis, was similarly presses in solar cell market on dark clouds, the Major enterprise like Germany Q-Cells achievement declined accordingly, because pre-year the world too positive electricity market also the demand will be this year worn out, the petroleum price dropped, but the competitive power counter-promotion and so on disadvantage factor lowered But at the same time, the people also see the US. After the Obama comes on stage, soon applies the Green New Deal policy, may have 150,000,000,000 US dollar subsidy funds including the among them green energy program, Japan will also carry out the subsidy system to continue to popularize solar cell's application4. Solar cell electricity generation principle:The solar cell is pair of light has the response and can transform the energy of light the electric power the component. Many kinds of materials can produce the lightto bend down the effect, for example: Mono-crystalline silicon, polycrystalline silicon, amorphous silicon, gallium arsenic, selenium indium copper and so on. Their electricity generation principle basic same, presently take crystal as example description light electricity generation process. The P crystalline silicon may result in the N silicon after the doping phosphorus, forms the P-N knot.When light illumination solar cell surface, part of photons by silicon material absorption; The photon energy transfer has given the silicon atom, caused the electron to occur more moved, becomes the free electron to tie the both sides in P-N to gather has formed the potential difference, when exterior key-on, under this voltage's function, will have the electric current to wind through the exterior electric circuit to have certain output. This process's essence is: The photon energy transforms the electrical energy the process.5. Crystalline silicon solar cell's manufacture process:The silicon is on our star preserves one of most abundant quantity materials. Had discovered after the 19th century scientists crystalline silicon semiconductor characteristic, it changed all nearly, even humanity's thought. 20 century's ends, in our life everywhere obviously “silicon” the f orm and the function, the crystalline silicon solar cell is in the recent 15 years forms the industrial production to be quickest. The production process may divide into five steps approximately: a、depuration process.b、pulls good process.c、slice process.d、system battery process.e、and the seal process.6. Solar cell's application:In the 1960s, the scientists already applied the solar cells in the spatial technology-communication satellite power supply, on the century's end, in the human self-introspection's process, bends down unceasingly regarding the light generates electricity this kind so clean and the direct energy form already even more kind, not only in the spatial application, but also gives full play in the numerous domains.For example: The solar energy garden lamp, the solar electrical energy generation household with the system, the stockaded village power supply's independent system, the light bends down the water pump (potable water or irrigation), the correspondence power source, the petroleum oil pipeline cathodic protection, the fiber optic cable communications pumping station power source, in the seawater desalination system, the cities the guidepost, the highway guidepost and so on. Europe and America and so on advanced countries bend down the electricitygeneration the light to merge the city to use electricity the system and the remote border district nature village power supply system integrate the development direction. The solar cell and the building system's union already formed the industrial production tendency.参考译文:太阳能发电随着经济的发展、社会的进步,人们对能源提出越来越高的要求,寻找新能源成为当前人类面临的迫切课题。
光伏发电系统外文翻译文献
文献信息:文献标题:A New Controller Scheme for Photovoltaics Power Generation Systems(光伏发电系统的一种新的控制方案)国外作者:Tamer T.N.Khatib,Azah Mohamed,Nowshad Amin文献出处:《European Journal of Scientific Research》,2009,Vol.33 No.3, pp515-524字数统计:英文1337单词,7006字符;中文2149汉字外文文献:A New Controller Scheme for Photovoltaics PowerGeneration SystemsAbstract:This paper presents a new controller scheme for photovoltaic (PV) power generation systems. The proposed PV controller scheme controls both the boost converter and the battery charger by using a microcontroller in order to extract maximum power from the PV array and control the charging process of the battery. The objective of the paper is to present a cost effective boost converter design and an improved maximum power point tracking algorithm for the PV system. A MATLAB based simulation model of the proposed standalone PV system has been developed to evaluate the feasibility of the system in ensuring maximum power point operation.1.IntroductionRecently, the installation of PV generation systems is rapidly growing due to concerns related to environment, global warming, energy security, technology improvements and decreasing costs. PV generation system is considered as a clean and environmentally-friendly source of energy. The main applications of PV systems are in either standalone or grid connected configurations. Standalone PV generationsystems are attractive as indispensable electricity source for remote areas. However, PV generation systems have two major problems which are related to low conversion efficiency of about 9 to 12 % especially in low irradiation conditions and the amount of electric power generated by PV arrays varies continuously with weather conditions. Therefore, many research works are done to increase the efficiency of the energy produced from the PV arrays.The solar cell V-I characteristics is nonlinear and varies with irradiation and temperature. But there is a unique point on the V-I and P-V curves, called as the maximum power point (MPP), at which at this point the PV system is said to operate with maximum efficiency and produces its maximum power output. The location of the MPP is not known but can be traced by either through calculation models or search algorithms. Thus, maximum power point tracking (MPPT) techniques are needed to maintain the PV array’s operating point at its MPP. Many MPPT techniques have been proposed in the literature in which the techniques vary in many aspects, including simplicity, convergence speed, hardware implementation and range of effectiveness. However, the most widely used MPPT technique is the perturbation and observation (P&O) method. This paper presents a simple MPPT algorithm which can be easily implemented and adopted for low cost PV applications. The objective of this paper is to design a novel PV controller scheme with improved MPPT method.The proposed standalone PV controller implementation takes into account mathematical model of each component as well as actual component specification. The dc–dc or boost converter is the front-end component connected between the PV array and the load. The conventional boost converter may cause serious reverse recovery problem and increase the rating of all devices. As a result, the conversion efficiency is degraded and the electromagnetic interference problem becomes severe under this situation. To increase the conversion efficiency, many modified step-up converter topologies have been investigated by several researchers. V oltage clamped techniques have been incorporated in the converter design to overcome the severe reverse-recovery problem of the output diodes. In this paper, focus is also given in the boost converter design. Another important component in the standalone PV systemsis the charge controller which is used to save the battery from possible damage due to over-charging and over-discharging. Studies showed that the life time of a battery can be degraded without using a charge controller.The proposed new controller scheme for the standalone PV system controls both the boost converter and the charge controller in two control steps. The first step is to control the boost converter so as to extract the maximum power point of the PV modules. Here, a high step-up converter is considered for the purpose of stepping up the PV voltage and consequently reducing the number of series-connected PV modules and to maintain a constant dc bus voltage. A microcontroller is used for data acquisition that gets PV module operating current and voltage and is also used to program the MPPT algorithm. The controller adopts the pulse width modulation (PWM) technique to increase the duty cycle of the generated pulses as the PV voltage decreases so as to obtain a stable output voltage and current close to the maximum power point. The second control step is to control the charge controller for the purpose of protecting the batteries. By controlling the charging current using the PWM technique and controlling the battery voltage during charging, voltages higher than the gassing voltage can be avoided.2.Design of the Proposed Photovoltaic SystemMost of the standalone PV systems operate in one mode only such that the PV system charges the battery which in turns supply power to the load. In this mode of operation, the life cycle time of the battery may be reduced due to continuous charging and discharging of the battery. The proposed standalone PV system as shown in terms of a block diagram in Figure 1 is designed to operate in two modes: PV system supplies power directly to loads and when the radiation goes down and the produced energy is not enough, the PV system will charge the battery which in turns supply power to the load. To manage these modes of operation, a controller is connected to the boost converter by observing the PV output power.3.MethodologyFor the purpose of estimating the mathematical models developed for the proposed standalone PV system, simulations were carried in terms of the MATLAB codes. Each PV module considered in the simulation has a rating of 80 Watt at 1000 W/m2, 21.2 V open circuit voltage, 5A short circuit current. The PV module is connected to a block of batteries with of sizing 60 Ah, 48 V.4.Results and DiscussionThe simulation results of the standalone PV system using a simple MPPT algorithm and an improved boost converter design are described in this section. Simulations were carried out for the PV system operating above 30o C ambient temperature and under different values of irradiation. Figure 9 shows the PV array I-V characteristic curve at various irradiation values. From the figure, it is observed that the PV current increase linearly as the irradiation value is increased. However, the PV voltage increases in logarithmic pattern as the irradiation increases. Figure 10 shows the PV array I-V characteristic curve at various temperature values. It is noted from the figure that, the PV voltage decreases as the ambient temperature is increased.Figure 4 compares the PV array P-V characteristics obtained from using the proposed MPPT algorithm and the classical MPPT P&O algorithm. From this figure, it can be seen that by using the proposed MPPT algorithm, the operating point of PV array is much closer to the MPP compared to the using the classical P&O algorithm.In addition, the proposed boost converter is able to give a stable output voltage as shown in Figure 5. In terms of PV array current, it can be seen from Figure 6 that the PV current is closer to the MPP current when using the improved MPPT algorithm. Thus, the track operating point is improved by using the proposed MPPT algorithm. In terms of efficiency of the standalone PV system which is calculated by dividing the load power with the maximum power of PV array, it is noted that the efficiency of the system is better with the proposed MPPT algorithm as compared to using the classical P&O algorithm as shown in Figure 7.5.ConclusionThis paper has presented an efficient standalone PV controller by incorporating an improved boost converter design and a new controller scheme which incorporates both a simple MPPT algorithm and a battery charging algorithm. The simulation results show that the PV controller using the simple MPPT algorithm has provided more power and better efficiency (91%) than the classical P&O algorithm. In addition, the proposed boost converter design gives a better converter efficiency of about 93%. Such a PV controller design can provide efficient and stable power supply for remote mobile applications.中文译文:光伏发电系统的一种新的控制方案摘要:本文提出了一种新的光伏(PV)发电系统控制器方案。
- 1、下载文档前请自行甄别文档内容的完整性,平台不提供额外的编辑、内容补充、找答案等附加服务。
- 2、"仅部分预览"的文档,不可在线预览部分如存在完整性等问题,可反馈申请退款(可完整预览的文档不适用该条件!)。
- 3、如文档侵犯您的权益,请联系客服反馈,我们会尽快为您处理(人工客服工作时间:9:00-18:30)。
光伏系统中蓄电池的充电保护IC电路设计1.引言太阳能作为一种取之不尽、用之不竭的能源越来越受到重视。
太阳能发电已经在很多国家和地区开始普及,太阳能照明也已经在我国很多城市开始投入使用。
作为太阳能照明的一个关键部分,蓄电池的充电以及保护显得尤为重要。
由于密封免维护铅酸蓄电池具有密封好、无泄漏、无污染、免维护、价格低廉、供电可靠,在电池的整个寿命期间电压稳定且不需要维护等优点,所以在各类需要不间断供电的电子设备和便携式仪器仪表中有着广泛的应用。
采用适当的浮充电压,在正常使用(防止过放、过充、过流)时,免维护铅酸蓄电池的浮充寿命可达12~16年,如果浮充电压偏差5%则使用寿命缩短1/2。
由此可见,充电方式对这类电池的使用寿命有着重大的影响。
由于在光伏发电中,蓄电池无需经常维护,因此采用正确的充电方式并采用合理的保护方式,能有效延长蓄电池的使用寿命。
传统的充电和保护IC是分立的,占用而积大并且外围电路复杂。
目前,市场上还没有真正的将充电与保护功能集成于单一芯片。
针对这个问题,设计一种集蓄电池充电和保护功能于一身的IC是十分必要的。
2.系统设计与考虑系统主要包括两大部分:蓄电池充电模块和保护模块。
这对于将蓄电池作为备用电源使用的场合具有重要意义,它既可以保证外部电源给蓄电池供电,又可以在蓄电池过充、过流以及外部电源断开蓄电池处于过放状态时提供保护,将充电和保护功能集于一身使得电路简化,并且减少宝贵的而积资源浪费。
图1是此Ic在光伏发电系统中的具体应用,也是此设计的来源。
免维护铅酸蓄电池的寿命通常为循环寿命和浮充寿命,影响蓄电池寿命的因素有充电速率、放电速率和浮充电压。
某些厂家称如果有过充保护电路,充电率可以达到甚至超过2C(C为蓄电池的额定容量),但是电池厂商推荐的充电率是C/20~C/3。
电池的电压与温度有关,温度每升高1℃,单格电池电压下降4 mV,也就是说电池的浮充电压有负的温度系数-4 mV/℃。
普通充电器在25℃处为最佳工作状态;在环境温度为0℃时充电不足;在45℃时可能因严重过充电缩短电池的使用寿命。
要使得蓄电池延长工作寿命,对蓄电池的工作状态要有一定的了解和分析,从而实现对蓄电池进行保护的目的。
蓄电池有四种工作状态:通常状态、过电流状态、过充电状态、过放电状态。
但是由于不同的过放电电流对蓄电池的容量和寿命所产生的影响不尽相同,所以对蓄电池的过放电电流检测也要分别对待。
当电池处于过充电状态的时间较长,则会严重降低电池的容量,缩短电池的寿命。
当电池处于过放电状态的时间超过规定时间,则电池由于电池电压过低可能无法再充电使用,从而使得电池寿命降低。
根据以上所述,充电方式对免维护铅酸蓄电池的寿命有很大影响,同时为了使电池始终处于良好的工作状态,蓄电池保护电路必须能够对电池的非正常工作状态进行检测,并作出动作以使电池能够从不正常的工作状态回到通常工作状态,从而实现对电池的保护。
3.单元模块设计3.1充电模块芯片的充电模块框图如图2所示。
该电路包括限流比较器、电流取样比较器、基准电压源、欠压检测电路、电压取样电路和逻辑控制电路。
该模块内含有独立的限流放大器和电压控制电路,它可以控制芯片外驱动器,驱动器提供的输出电流为20~30 mA,可直接驱动外部串联的调整管,从而调整充电器的输出电压与电流。
电压和电流检测比较器检测蓄电池的充电状态,并控制状态逻辑电路的输入信号。
当电池电压或电流过低时,充电启动比较器控制充电。
电器进入涓流充电状态,当驱动器截止时,该比较器还能输出20 mA左右,进入涓流充电电流。
这样,当电池短路或反接时,充电器只能以小电流充电,避免了因充电电流过大而损坏电池。
此模块构成的充电电路充电过程分为二个充电状态:大电流恒流充电状态、高电压过充电状态和低电压恒压浮充状态。
充电过程从大电流恒流充电状态开始,在这种状态下充电器输出恒定的充电电流。
同时充电器连续监控电池组的两端电压,当电池电压达到转换电压过充转换电压V sam时,电池的电量己恢复到放出容量的70%~90%,充电器转入过充电状态。
在此状态下,充电器输出电压升高到过充电压V oc,由于充电器输出电压保持恒定不变,所以充电电流连续下降。
当电流下降到过充中止电流I oct时,电池的容量己达到额定容量的100%,充电器输出电压下降到较低的浮充电压V F。
3.2保护模块芯片内部保护电路模块框图如图3所示。
该电路包括控制逻辑电路、取样电路、过充电检测电路、过放电检测比较器、过电流检测比较器、负载短路检测电路、电平转换电路和基准电路(BGR)。
此模块构成的保护电路如图4所示。
当芯片的供电电压在正常工作范围内,且VM管脚处的电压在过电流I检测电压之下,则此时电池处于通常工作状态,芯片的充放电控制端CO和DO均为高电平,这时芯片处于通常工作模式。
而当电池放电电流变大,会引起VM管脚处的电压上升,若VM管脚处的电压在过电流检测电压V iov之上,则此时电池处于过电流状态,如果这种状态保持相应的过电流延时时间t iov,芯片禁止电池放电,这时充电控制端CO为高电平,而放电控制端DO为低电平,芯片处于过电流模式,一般为了对电池起到更加安全合理的保护,芯片会对电池的不同过放电电流采取不同的过放电电流延时时间保护。
一般规律是过放电电流越大,则过放电电流延时时间越短。
当芯片的供电电压在过充电检测电压之上(V dd>V cu)时,则电池处于过充电状态,如果这种状态保持相应的过充电延时时间t cu芯片将禁止电池充电,此时放电控制端DO为高电平,而充电控制端CO为低电平,芯片处于过充电模式。
当芯片的供电电压在过放电检测电压之下(V dd<V dl),则此时电池处于过放电状态,如果这种状态保持相应的过放电延时时间t dl,芯片将禁止电池放电,此时充电控制端CO为高电平,而放电控制端DO为低电平,芯片处于过放电模式。
4.电路设计由两个充电与保护模块结构图可将电路分为四部分:电源检测电路(欠压检测电路)、偏置电路(取样电路、基准电路以及偏置电路)、比较器部分(包括过充电检测比较器/过放电检测比较器、过流检测比较器和负载短路检测电路)及逻辑控制部分。
文中主要介绍欠压检测电路设计(图5) ,并给出带隙基准电路(图6) 。
蓄电池的充电、电压的稳定尤为重要,欠压、过压保护是必不可少的,因此通过在芯片内部集成过压、欠压保护电路来提高电源的可靠性和安全性。
并且保护电路的设计要简单、实用,此处设计了一种CMOS工艺下的欠压保护电路,此电路结构简单,工艺实现容易,可用做高压或功率集成电路等的电源保护电路。
欠压保护的电路原理图如图5所示,共由五部分组成:偏置电路、基准电压、分压电路、差分放大器、输出电路。
本电路的电源电压是10V;M0,M1,M2,R0是电路的偏置部分,给后级电路提供偏置,电阻Ro决定了电路的工作点,M0,M1,M2组成电流镜;R1,M14是欠压信号的反馈回路;其余M3,M4,M5,M6,M7,M8,M9,M10,M11,M12,M13,M14组成四级放大比较器;M15,DO产生基准电压,输入比较器的同相端,固定不变(V+),分压电阻R1,R2,R3输入到比较器的反相端,当电源电压正常工作时,反相端的欠压检测输给比较器的反相端的电压大于V+。
比较器输出为低,M14截止,反馈电路不起作用;当欠压发生时,分压电阻R1,R2,R3反应比较敏感,当电阻分压后输给反相端的电压小于V,比较器的输出电压为高,此信号将M14开启,使得R两端的电压变为M两端的饱和电压,趋近于0V,从而进一步拉低了R1>R2分压后的输出电压,形成了欠压的正反馈。
输出为高,欠压锁定,起到了保护作用。
5.仿真模拟结果与分析本设计电路采用CSMC 0.6 μm数字CMOS工艺对电路进行仿真分析。
在对电路做整体仿真时,主要观察的是保护模块对电池的充放电过程是否通过监测V dd电位和V m电位而使芯片的CO端和DO端发生相应的变化。
图7所示的整体仿真波形图是保护模块随着电池电压的变化从通常工作模式转换到过充电模式,然后回到通常工作模式,接着进入过放电模式,最后再回到通常工作模式。
由于本设计处于前期阶段,各个参数还需要优化,只是提供初步的仿真结果。
6.结论设计了一种集蓄电池充电与保护功能于一身的IC。
利用此设计既可以减小而积,又可以减少外围电路元器件。
电路同时采用了低功耗设计。
由于此项目正在进行设计优化阶段,完整的仿真还不能达到要求,还需要对各个模块电路进行优化设计。
英语原文Design of a Lead-Acid Battery Charging and Protecting IC in Photovoltaic System1.IntroductionSolar energy as an inexhaustible, inexhaustible source of energy more and more attention. Solar power has become popular in many countries and regions, solar lighting has also been put into use in many cities in China. As a key part of the solar lighting, battery charging and protection is particularly important. Sealed maintenance-free lead-acid battery has a sealed, leak-free, pollution-free, maintenance-free, low-cost, reliable power supply during the entire life of the battery voltage is stable and no maintenance, the need for uninterrupted for the various types of has wide application in power electronic equipment, and portable instrumentation. Appropriate float voltage, in normal use (to prevent over-discharge, overcharge, over-current), maintenance-free lead-acid battery float life of up to 12 ~ 16 years float voltage deviation of 5% shorten the life of 1/2. Thus, the charge has a major impact on this type of battery life. Photovoltaic, battery does not need regular maintenance, the correct charge and reasonable protection, can effectively extend battery life. Charging and protection IC is the separation of the occupied area and the peripheral circuit complexity. Currently, the market has not yet real, charged with the protection function is integrated on a singlechip. For this problem, design a set of battery charging and protection functions in one IC is very necessary.2.System design and considerationsThe system mainly includes two parts: the battery charger module and the protection module. Of great significance for the battery as standby power use of the occasion, It can ensure that the external power supply to the battery-powered, but also in the battery overcharge, over-current and an external power supply is disconnected the battery is to put the state to provide protection, the charge and protection rolled into one to make the circuit to simplify and reduce valuable product waste of resources. Figure 1 is a specific application of this Ic in the photovoltaic power generation system, but also the source of this design.Maintenance-free lead-acid battery life is usually the cycle life and float life factors affecting the life of the battery charge rate, discharge rate, and float voltage. Some manufacturers said that if the overcharge protection circuit, the charging rate can be achieved even more than 2C (C is the rated capacity of the battery), battery manufacturers recommend charging rate of C/20 ~ C/3. Battery voltage and temperature, the temperature is increased by 1 °C, single cell battery voltage drops 4 mV, negative temperature coefficient of -4 mV / °C means that the battery float voltage. Ordinary charger for the bestworking condition at 25 °C; charge less than the ambient temperature of 0 °C; at 45 °C may shorten the battery life due to severe overcharge. To make the battery to extend the working life, have a certain understanding and analysis of the working status of the battery, in order to achieve the purpose of protection of the battery. Battery, there are four states: normal state, over-current state over the state of charge, over discharge state. However, due to the impact of the different discharge current over-capacity and lifetime of the battery is not the same, so the battery over discharge current detection should be treated separately. When the battery is charging the state a long time, would severely reduce the capacity of the battery and shorten battery life. When the battery is the time of discharge status exceeds the allotted time, the battery, the battery voltage is too low may not be able to recharge, making the battery life is lower.Based on the above, the charge on the life of maintenance-free lead-acid batteries have a significant impact, while the battery is always in good working condition, battery protection circuit must be able to detect the normal working condition of the battery and make the action the battery can never normal working state back to normal operation, in order to achieve the protection of the battery.3.Units modular design3.1The charging moduleChip, charging module block diagram shown in Figure 2. The circuitry includes current limiting, current sensing comparator, reference voltage source, under-voltage detection circuit, voltage sampling circuit and logic control circuit.The module contains a stand-alone limiting amplifier and voltage control circuit, it can control off-chip drive, 20 ~30 mA, provided by the drive output current can directly drive an external series of adjustment tube, so as to adjust the charger output voltage and current . Voltage and current detection comparator detects the battery charge status, and control the state of the input signal of the logic circuit. When the battery voltage or current is too low, the charge to start the comparator control the charging. Appliances into the trickle charge state when the cut-off of the drive, the comparator can output about 20 mA into the trickle charge current. Thus, when the battery short-circuit or reverse, the charger can only charge a small current, to avoid damage to the battery charging current is too large. This module constitutes a charging circuit charging process is divided into two charging status: high-current constant-current charge state, high-voltage charge status and low-voltage constant voltage floating state. The charging process from the constant current charging status, the constant charging current of the charger output in this state. And the charger continuously monitors the voltage across the battery pack, the battery power has been restoredto 70% to 90% of the released capacity when the battery voltage reaches the switching voltage to charge conversion voltage V sam charger moves to the state of charge. In this state, the charger output voltage is increased to overcharge pressure V oc is due to the charger output voltage remains constant, so the charging current is a continuous decline. Current down to charge and suspend the current Ioct, the battery capacity has reached 100% of rated capacity, the charger output voltage drops to a lower float voltage V F.3.2 Protection ModuleChip block diagram of the internal protection circuit shown in Figure 3. The circuit includes control logic circuit, sampling circuit, overcharge detection circuit, over-discharge detection comparator, overcurrent detection comparator, load short-circuit detection circuit, level-shifting circuit and reference circuit (BGR).This module constitutes a protection circuit shown in Figure 4. Under the chip supply voltage within the normal scope of work, and the VM pin voltage at the overcurrent detection voltage, the battery is in normal operation, the charge and discharge control of the chip high power end of the CO and DO are level, when the chip is in normal working mode. Larger when the battery discharge current will cause voltage rise of the VM pin at the VM pin voltage at above the current detection voltage V iov, then the battery is the current status, if this state to maintain the tiovovercurrent delay time, the chip ban on battery discharge, then the charge to control the end of CO is high, the discharge control side DO is low, the chip is in the current mode, general in order to play on the battery safer and more reasonable protection, the chip will battery over-discharge current to take over the discharge current delay time protection. The general rule is that the over-discharge current is larger, over the shorter the discharge current delay time. Above Overcharge detection voltage, the chip supply voltage (V dd> V cu), the battery is in overcharge state, this state is to maintain the corresponding overcharge delay time tcu chip will be prohibited from charging the battery, then discharge control end DO is high, and charging control terminal CO is low, the chip is in charging mode. When the supply voltage of the chip under the overdischarge detection voltage (V dd <V dl,), then the battery is discharged state, this state remains the overdischarge delay time tdl chip will be prohibited to discharge the battery at this time The charge control side CO is high, while the discharge control terminal DO is low, the chip is in discharge mode.4.Circuit DesignTwo charge protection module structure diagram, the circuit can be divided into four parts: the power detection circuit (under-voltage detection circuit), part of the bias circuit (sampling circuit, the reference circuit and bias circuit), the comparator (including the overchargedetection /overdischarge detection comparator, over-current detection and load short-circuit detection circuit) and the logic control part.This paper describes the under-voltage detection circuit (Figure 5), and gives the bandgap reference circuit (Figure 6).Battery charging, voltage stability is particularly important, undervoltage, overvoltage protection is essential, therefore integrated overvoltage, undervoltage protection circuit inside the chip, to improve power supply reliability and security. And protection circuit design should be simple, practical, here designed a CMOS process, the undervoltage protection circuit, this simple circuit structure, process and easy to implement and can be used as high-voltage power integrated circuits and other power protection circuit.Undervoltage protection circuit schematic shown in Figure 5, a total of five components: the bias circuit, reference voltage, the voltage divider circuit, differential amplifier, the output circuit. The circuit supply voltage is 10V; the M0, M1, M2, R0 is the offset portion of the circuit to provide bias to the post-stage circuit, the resistance, Ro, determine the circuit's operating point, the M0, M1, M2 form a current mirror; R1 M14 is the feedback loop of the undervoltage signal; the rest of the M3, M4 and M5, M6, M7, M8, M9, M10, M11, M12, M13, M14, composed of four amplification comparator; M15, DO, a reference voltage, the comparator input with the inverting input is fixed (V+), partial pressure of theresistance R1, R2, R3, the input to the inverting input of the comparator, when the normal working of the power supply voltage, the inverting terminal of the voltage detection is lost to the inverting terminal voltage of the comparator is greater than V+. Comparator output is low, M14 cutoff, feedback circuit does not work; undervoltage occurs, the voltage divider of R1, R2, R3, reaction is more sensitive, lost to the inverting input voltage is less than V when the resistor divider, the comparator the output voltage is high, this signal will be M14 open, the voltage across R into M at both ends of the saturation voltage close to 0V, thereby further driving down the R1> R2, the partial pressure of the output voltage, the formation of the undervoltage positive feedback. Output, undervoltage lockout, and plays a protective role.5. Simulation results and analysisThe design of the circuit in CSMC 0.6 μm in digital CMOS process simulation and analysis of the circuit. In the overall simulation of the circuit, the main observation is that the protection module on the battery charge and discharge process by monitoring V dd potential and V m potential leaving chip CO side and DO-side changes accordingly. The simulation waveform diagram shown in Figure 7, the overall protection module with the battery voltage changes from the usual mode conversion into overcharge mode, and then return to normal working mode, and then into the discharge mode, and finally back to normalworking mode. As the design in the early stages of the various parameters to be optimized, but to provide a preliminary simulation results.6.ConclusionDesigned a set of battery charging and protection functions in one IC. This design not only can reduce the product, they can reduce the peripheral circuit components. The circuit uses the low-power design. This project is underway to design optimization stage, a complete simulation can not meet the requirements, but also need to optimize the design of each module circuit.THANKS !!!致力为企业和个人提供合同协议,策划案计划书,学习课件等等打造全网一站式需求欢迎您的下载,资料仅供参考。