注塑部产品质量控制要求
注塑成型质量控制计划

注塑成型质量控制计划一、引言注塑成型是一种常用的创造工艺,广泛应用于塑料制品的生产。
为了确保注塑成型产品的质量,提高生产效率和产品一致性,制定注塑成型质量控制计划是必要的。
本文将详细介绍注塑成型质量控制计划的制定过程和相关内容。
二、质量控制目标1. 产品质量目标:确保注塑成型产品的尺寸精度、表面质量和物理性能符合设计要求。
2. 生产效率目标:提高注塑成型生产线的运行效率,降低生产成本,保证交货期的准时性。
三、质量控制流程1. 原料检验:a. 原料采购:选择可靠的供应商,确保原料的质量稳定性。
b. 原料检验:对每批原料进行外观检查、尺寸测量和物理性能测试,确保符合要求。
2. 模具检验:a. 模具维护:定期对模具进行清洁、润滑和维护,确保模具的正常运行。
b. 模具检验:在每次生产前对模具进行检查,确保无损伤、变形和磨损。
3. 注塑成型过程控制:a. 注塑参数设定:根据产品要求设定注塑机的注射速度、温度和压力等参数。
b. 注塑过程监控:通过实时监测注塑机的压力、温度和注射速度等参数,及时调整,确保注塑过程稳定。
4. 产品检验:a. 外观检查:对注塑成型产品的外观进行检查,包括表面光洁度、色泽和划痕等。
b. 尺寸测量:使用合适的测量工具对产品的尺寸进行测量,确保尺寸精度符合要求。
c. 物理性能测试:根据产品的要求进行拉伸、弯曲和冲击等物理性能测试。
5. 不良品处理:a. 不良品分类:将不合格的产品进行分类,如尺寸不合格、外观缺陷等。
b. 不良品原因分析:对不良品进行原因分析,找出问题的根源。
c. 不良品处理:对不良品进行返工、修复或者报废处理,确保不良品不进入市场。
6. 数据分析与改进:a. 数据采集:对每批产品进行记录,包括注塑参数、产品检验结果和不良品数量等。
b. 数据分析:对数据进行统计和分析,找出生产过程中存在的问题和改进的空间。
c. 改进措施:根据数据分析结果,制定改进措施,优化注塑成型质量控制计划。
注塑成型质量控制计划

注塑成型质量控制计划一、背景介绍注塑成型是一种常用的塑料创造工艺,广泛应用于各个行业。
为了确保注塑成型产品的质量,需要制定一份注塑成型质量控制计划,从而实现对整个生产过程的有效管理和控制。
二、质量目标1. 产品外观质量:确保产品表面光滑、无气泡、无瑕疵。
2. 尺寸精度:保证产品尺寸精确符合设计要求。
3. 材料质量:确保使用的塑料材料符合相关标准,无污染。
4. 模具质量:保证模具的使用寿命和精度,减少模具损耗。
5. 生产效率:提高生产效率,降低生产成本。
三、质量控制计划步骤1. 原材料检验在注塑成型过程中,原材料的质量直接影响产品的质量。
需要制定原材料检验标准,包括外观、密度、熔流速率、拉伸强度等指标。
每批原材料进厂时,进行抽样检验,确保原材料符合要求后方可使用。
2. 模具检验模具是注塑成型过程中的关键设备,模具的质量直接影响产品的尺寸精度和外观质量。
制定模具检验标准,包括尺寸精度、表面光洁度、模具寿命等指标。
每次使用新模具或者模具修复后,需要进行模具检验,确保模具质量符合要求。
3. 注塑工艺参数设定根据产品要求和模具特性,确定合适的注塑工艺参数,包括注射速度、保压时间、保压压力等。
通过试验和调整,找到最佳的工艺参数,确保产品尺寸精度和外观质量。
4. 注塑成型过程监控在注塑成型过程中,需要对关键参数进行实时监控,确保生产过程稳定可控。
监控项包括注射压力、注射速度、保压时间、模具温度等。
通过监控,及时发现问题并进行调整,确保产品质量稳定。
5. 产品检验对注塑成型产品进行全面的检验,包括外观质量、尺寸精度、物理性能等。
制定产品检验标准,明确检验方法和标准。
每批产品进行抽样检验,确保产品符合质量要求。
6. 不良品处理对于不合格的产品,需要进行分类和处理。
可分为可修复和不可修复两类,可修复的产品进行修复后重新检验,不可修复的产品进行报废处理。
同时,分析不良品的原因,采取相应措施,防止类似问题再次发生。
7. 持续改进定期评估和分析注塑成型质量控制计划的实施效果,发现问题并制定改进措施。
注塑成型质量控制计划
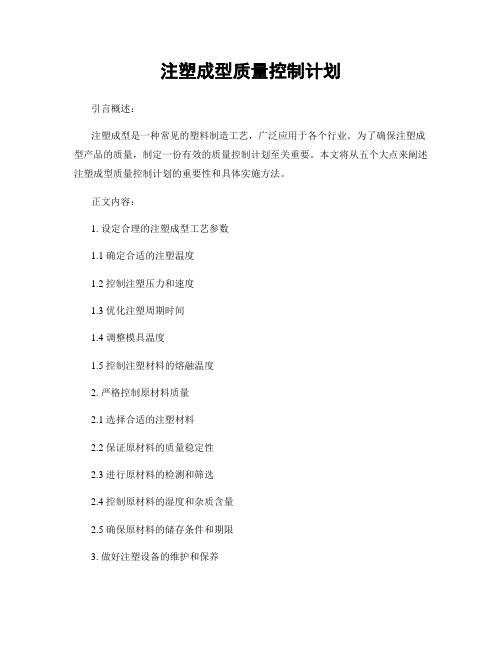
注塑成型质量控制计划引言概述:注塑成型是一种常见的塑料制造工艺,广泛应用于各个行业。
为了确保注塑成型产品的质量,制定一份有效的质量控制计划至关重要。
本文将从五个大点来阐述注塑成型质量控制计划的重要性和具体实施方法。
正文内容:1. 设定合理的注塑成型工艺参数1.1 确定合适的注塑温度1.2 控制注塑压力和速度1.3 优化注塑周期时间1.4 调整模具温度1.5 控制注塑材料的熔融温度2. 严格控制原材料质量2.1 选择合适的注塑材料2.2 保证原材料的质量稳定性2.3 进行原材料的检测和筛选2.4 控制原材料的湿度和杂质含量2.5 确保原材料的储存条件和期限3. 做好注塑设备的维护和保养3.1 定期检查设备的工作状态3.2 清洁注塑设备和模具3.3 确保注塑设备的稳定性和可靠性3.4 进行设备的定期保养和维修3.5 更新和升级设备以提高生产效率和质量4. 实施严格的注塑过程控制4.1 严格控制模具的开合速度和压力4.2 监控注塑过程中的温度和压力4.3 进行注塑过程中的实时监控和调整4.4 控制注塑过程中的注射速度和注射压力4.5 确保注塑过程中的注塑材料的充填和冷却均匀5. 进行注塑成型产品的质量检测5.1 进行外观质量的检查5.2 进行尺寸和尺寸偏差的测量5.3 进行物理性能和力学性能的测试5.4 进行耐热性和耐腐蚀性的测试5.5 进行可靠性和耐久性的测试总结:注塑成型质量控制计划的制定和执行对于保证注塑成型产品的质量至关重要。
通过设定合理的注塑工艺参数、严格控制原材料质量、做好设备的维护和保养、实施严格的注塑过程控制以及进行质量检测,可以有效地提高注塑成型产品的质量稳定性和一致性。
注塑成型企业应该重视质量控制计划的制定和执行,不断优化和改进质量控制措施,以满足市场和客户的需求。
注塑产品质量的控制

注塑产品质量的控制简介注塑是一种常用的塑料加工方法,广泛应用于各个行业中。
在注塑过程中,产品质量的控制是十分重要的,直接关系到产品的性能和可靠性。
本文将介绍注塑产品质量的控制方法和技术。
注塑工艺参数的控制注塑产品的质量控制要关注注塑工艺参数的控制。
注塑工艺参数包括注塑温度、保压时间、注射速度等等。
合理控制这些参数能够确保产品质量的稳定性和一致性。
特别是在大批量生产中,合理的工艺参数控制能够提高生产效率和产品的一致性。
原料的质量控制原料是注塑产品的基础,其质量直接影响产品的性能和使用寿命。
在注塑产品的质量控制中,原料的质量控制是至关重要的。
对于不同种类的塑料原料,需要严格控制原料的成分、密度、流动性等参数,确保生产出的产品符合设计和标准要求。
模具的设计和制造注塑产品的模具是决定产品形状和尺寸的关键因素,对产品质量有着重要的影响。
在注塑产品质量控制中,模具的设计和制造是不可忽视的环节。
合理设计的模具能够确保产品的准确性和一致性,并且能够提高注塑过程的效率和稳定性。
注塑设备的维护和保养注塑设备的维护和保养对于产品质量的控制也是至关重要的。
定期检查和保养设备能够保证设备的正常运行,提高生产效率和产品的稳定性。
特别是在大批量生产中,设备的故障可能会导致产品质量的下降和生产延误。
检测和检验在注塑产品的质量控制中,检测和检验是必不可少的环节。
通过对产品的尺寸、外观、性能等进行检测和检验,能够及时发现和解决问题,确保产品的质量稳定和一致性。
常用的检测方法包括尺寸测量、外观检查、物性测试等等。
注塑产品质量的控制是一个复杂的过程,需要从注塑工艺参数的控制、原料的质量控制、模具的设计和制造、设备的维护和保养等多个方面进行考虑。
通过合理控制这些环节,能够保证注塑产品的质量稳定和一致性,提高产品的性能和可靠性。
在实际生产中,应根据具体情况制定相应的质量控制方案,并不断优化和改进,以提高产品的竞争力和市场占有率。
注塑车间产品质量控制要求

注塑车间产品质量控制要求1.原材料控制:在注塑生产中,原材料的质量是确保产品质量的基础。
因此,注塑车间需建立完善的原材料采购和质量控制体系。
要求供应商提供质量合格证明,并对进货原材料进行抽检,确保原材料符合技术要求。
2.注塑模具管理:注塑模具是生产注塑制品的重要工具,其质量直接关系到产品的质量。
注塑车间应对模具进行定期的维护保养和检修,确保模具的正常使用。
同时,在使用过程中,要对模具的使用进行记录和检查,发现问题及时解决。
3.设备维护保养:注塑车间的设备在生产过程中承受着较大的负荷,因此,设备的维护保养也是确保产品质量的重要环节。
要求设备操作人员按照操作规程进行操作,将设备安全工作放在首位,并定期对设备进行检修和维护,确保设备的正常运行。
4.工艺参数控制:注塑生产过程中,工艺参数的控制对产品质量有着重要的影响。
注塑车间应根据产品的要求,确定合理的工艺参数,并进行严格的控制。
要求操作人员按照工艺参数进行操作,并对工艺参数进行监测和调整,确保产品的一致性和稳定性。
5.过程监控:注塑车间应建立完善的过程监控体系,对注塑生产过程进行监控和控制。
要求操作人员对生产过程进行实时监测和记录,发现问题及时采取措施进行处理,确保产品质量的稳定性和可控性。
6.成品检验:成品检验是确保产品质量的最后一道关口。
注塑车间应建立完善的成品检验制度,进行成品的外观检查和尺寸检测,并对成品抽样进行性能测试,确保产品达到客户的质量要求。
7.异常处理:在注塑生产过程中,可能会出现一些异常情况,如工艺参数偏差、设备故障等。
注塑车间应建立异常处理制度,对异常情况进行记录和分析,并及时采取措施进行处理,避免对产品质量的影响。
8.员工培训:注塑车间的产品质量控制还需要依赖于员工的素质和技能。
注塑车间应对员工进行定期的培训和考核,提高员工的工作技能和质量意识,确保产品质量的稳定性和一致性。
以上是注塑车间产品质量控制的一些要求,注塑车间需要建立完善的质量控制系统,从原材料控制到成品检验,全面监控和控制产品的质量,不断提升产品的质量水平,满足客户的需求。
注塑部质量控制标准
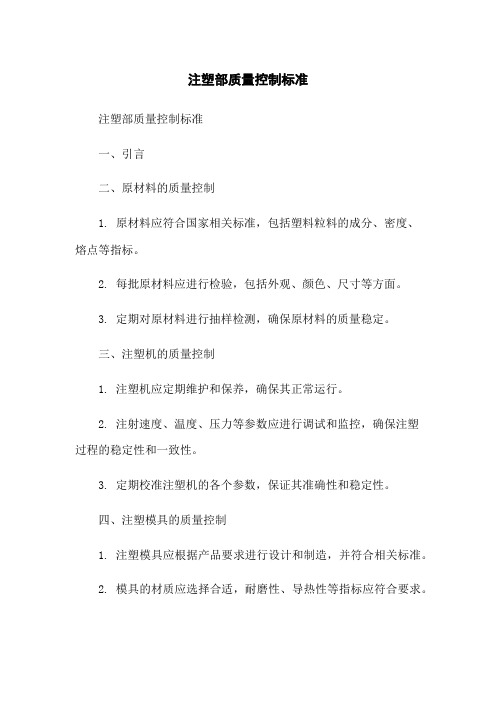
注塑部质量控制标准注塑部质量控制标准一、引言二、原材料的质量控制1. 原材料应符合国家相关标准,包括塑料粒料的成分、密度、熔点等指标。
2. 每批原材料应进行检验,包括外观、颜色、尺寸等方面。
3. 定期对原材料进行抽样检测,确保原材料的质量稳定。
三、注塑机的质量控制1. 注塑机应定期维护和保养,确保其正常运行。
2. 注射速度、温度、压力等参数应进行调试和监控,确保注塑过程的稳定性和一致性。
3. 定期校准注塑机的各个参数,保证其准确性和稳定性。
四、注塑模具的质量控制1. 注塑模具应根据产品要求进行设计和制造,并符合相关标准。
2. 模具的材质应选择合适,耐磨性、导热性等指标应符合要求。
3. 模具的使用寿命应进行监控和记录,定期维护和更换损坏的部件。
五、注塑工艺的质量控制1. 首件检测:在生产开始前,应进行首件检测,确保模具、注塑机和工艺参数的正确性。
2. 在注塑过程中,应进行在线检测,包括尺寸、外观等方面。
3. 定期抽样进行产品检测,包括物理性能、可靠性等方面。
六、产品的质量控制1. 对产品外观进行检查,包括色差、气泡、瑕疵等。
2. 对产品尺寸进行检测,确保尺寸的准确性和一致性。
3. 对产品的物理性能进行测试,包括强度、硬度等方面。
七、质量记录与反馈1. 每批产品应有相应的质量记录,包括检验结果、返工情况等。
2. 对产品质量问题的处理过程和结果应进行记录和分析,以便不断改进和提升质量。
八、通过以上质量控制标准,注塑部门可以确保产品质量的稳定性和一致性,满足客户的需求和要求。
注塑成型质量控制计划
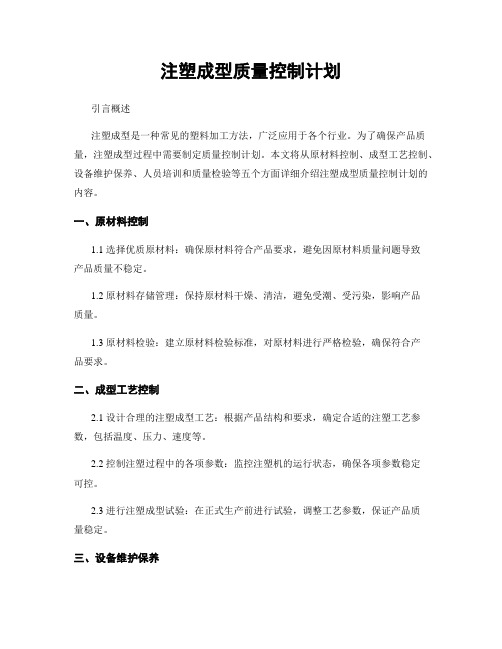
注塑成型质量控制计划引言概述注塑成型是一种常见的塑料加工方法,广泛应用于各个行业。
为了确保产品质量,注塑成型过程中需要制定质量控制计划。
本文将从原材料控制、成型工艺控制、设备维护保养、人员培训和质量检验等五个方面详细介绍注塑成型质量控制计划的内容。
一、原材料控制1.1 选择优质原材料:确保原材料符合产品要求,避免因原材料质量问题导致产品质量不稳定。
1.2 原材料存储管理:保持原材料干燥、清洁,避免受潮、受污染,影响产品质量。
1.3 原材料检验:建立原材料检验标准,对原材料进行严格检验,确保符合产品要求。
二、成型工艺控制2.1 设计合理的注塑成型工艺:根据产品结构和要求,确定合适的注塑工艺参数,包括温度、压力、速度等。
2.2 控制注塑过程中的各项参数:监控注塑机的运行状态,确保各项参数稳定可控。
2.3 进行注塑成型试验:在正式生产前进行试验,调整工艺参数,保证产品质量稳定。
三、设备维护保养3.1 定期检查注塑机设备:定期对注塑机进行检查,保证设备运行正常。
3.2 及时维护设备:发现设备故障及时维修,避免因设备故障导致产品质量问题。
3.3 建立设备维护记录:记录设备维护情况,为设备维护提供依据。
四、人员培训4.1 培训员工操作技能:对操作人员进行培训,提高其操作技能和质量意识。
4.2 培训员工质量检验知识:培训员工对产品质量的判断标准和检验方法,提高产品质量控制能力。
4.3 定期进行培训考核:定期组织培训,对员工进行考核,确保培训效果。
五、质量检验5.1 制定质量检验标准:根据产品要求,制定质量检验标准,明确各项检验内容和标准。
5.2 定期进行产品质量检验:对生产出的产品进行定期检验,确保产品质量稳定。
5.3 处理不合格品:对不合格品进行处理,找出问题原因并采取措施,避免类似问题再次发生。
结语通过以上五个方面的质量控制计划,可以有效提高注塑成型产品的质量稳定性和生产效率,确保产品符合客户要求,提升企业竞争力。
注塑成型质量控制计划
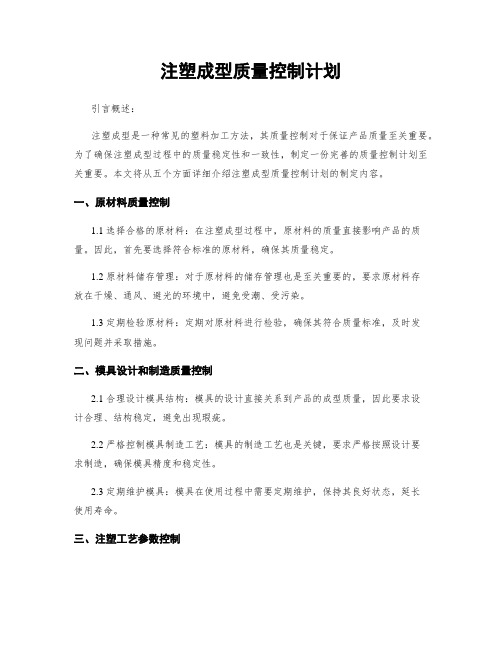
注塑成型质量控制计划引言概述:注塑成型是一种常见的塑料加工方法,其质量控制对于保证产品质量至关重要。
为了确保注塑成型过程中的质量稳定性和一致性,制定一份完善的质量控制计划至关重要。
本文将从五个方面详细介绍注塑成型质量控制计划的制定内容。
一、原材料质量控制1.1 选择合格的原材料:在注塑成型过程中,原材料的质量直接影响产品的质量。
因此,首先要选择符合标准的原材料,确保其质量稳定。
1.2 原材料储存管理:对于原材料的储存管理也是至关重要的,要求原材料存放在干燥、通风、避光的环境中,避免受潮、受污染。
1.3 定期检验原材料:定期对原材料进行检验,确保其符合质量标准,及时发现问题并采取措施。
二、模具设计和制造质量控制2.1 合理设计模具结构:模具的设计直接关系到产品的成型质量,因此要求设计合理、结构稳定,避免出现瑕疵。
2.2 严格控制模具制造工艺:模具的制造工艺也是关键,要求严格按照设计要求制造,确保模具精度和稳定性。
2.3 定期维护模具:模具在使用过程中需要定期维护,保持其良好状态,延长使用寿命。
三、注塑工艺参数控制3.1 确定合适的注塑工艺参数:注塑成型的工艺参数包括温度、压力、速度等多个方面,需要根据产品要求确定合适的参数。
3.2 实时监控注塑工艺参数:在注塑成型过程中,需要实时监控各项工艺参数,及时调整,确保产品质量稳定。
3.3 记录和分析注塑过程数据:对注塑过程中的数据进行记录和分析,找出问题原因并改进,提高生产效率和产品质量。
四、成型产品质量检验4.1 制定产品质量检验标准:制定符合产品要求的质量检验标准,确保产品质量符合标准。
4.2 定期进行产品质量检验:对成型产品进行定期的质量检验,及时发现问题并采取措施,避免不良品流入市场。
4.3 进行产品质量统计分析:对产品质量数据进行统计分析,找出问题的根源并采取改进措施,提高产品质量。
五、持续改进和优化5.1 定期召开质量改进会议:定期召开质量改进会议,对生产过程中出现的问题进行讨论和改进,持续提高产品质量。
- 1、下载文档前请自行甄别文档内容的完整性,平台不提供额外的编辑、内容补充、找答案等附加服务。
- 2、"仅部分预览"的文档,不可在线预览部分如存在完整性等问题,可反馈申请退款(可完整预览的文档不适用该条件!)。
- 3、如文档侵犯您的权益,请联系客服反馈,我们会尽快为您处理(人工客服工作时间:9:00-18:30)。
注塑部产品质量控制要求
“产品质量,人人有责”,优质产品是生产制造和管理出来的,而不是检验出来的。
目标是品质优异,客户满意,一次成型合格率达98%以上。
要达到上述目标,全体员工必须提高质量意识和工作责任心,并按如下要求做好各项工作。
1.产品开啤时,需参照“成型工艺记录表”内的工艺参数调机,开啤样板需经QC检查确认OK板后方可批量生产。
2.操作工开机前必须向管理人员或品检人员问清楚有关产品开机要求、质量要求、加工要求、包装要求及留意事项,严禁在不熟悉产品质量标准的情况下开机操作。
3.新工人上班或转班啤新产品时,领班/组长和品检人员必须向操作工讲清楚其产品质量标准、开机要求、包装要求及注意事项。
4.操作工开机时必须严格按机位“作业指导书”的要求去操作和控制产品质量,不15得将不合格流入成品箱中。
5.生产过程中,注塑领班/组长每3小时必须认真仔细地检查一次产品质量(如:外观、结构、颜色等)。
6.操作工需按要求对每啤产品的外观质量进行自检,每30分钟对照一次机位OK样板,对其内部结构进行认真检查,留意是否有断柱、盲孔、缺胶等不良现象,发现问题应立即停机通知管理人员改善。
7.保持工作台面干净整洁,产品要轻拿轻放,并将产品外表面朝上摆放(不可倒置)于台面上,且工作台上不可堆积过多产品。
产品从模具中取出时需小心操作,勿让产品碰到模具上或产品互相碰撞,防止碰伤或刮伤产品。
8.严格按包装资料要求对产品进行包装与摆放,并注意入箱方式和包装数量,防止擦伤、碰伤产品和受压变形。
9.剪水口、批披峰时需小心操作,水口位应剪平,勿剪伤或批伤产品。
产品周边轻微披峰用铜棒或顶针杆滚压毛边,用力不可过大,且要均匀一致,防止碰伤或刮伤产品。
10.生产过程中若发现正品内有不良品时,应予以分开摆放(隔开),并标识清楚,
11.领班/组长需及时安排人手对其进行返工处理。
12.管理人员及操作工均需做好交接班工作,交班人员需将产品质量要求、操作方式、包装要求及当班出现的问题和留意事项向接班人员交接清楚,接班人员应主动向交班人员问清楚有关情况。
13.因工作失职,造成产品质量问题而需返工的,由当班管理人员及有关操作工下班后自行处理。
14.严格按要求使用夹具(不可随意调整夹具高度),定时检查夹具定位情况和使用效果,留意产品是否变形?并注意产品摆在夹具中的位置和受力情况。
15.努力熟悉胶件质量标准和加工要求,做到举一反三、触类旁通。
并积极参加有关品质培训和操作和操作培训,不断提高工作质量。
D.白色或透明胶件黑点问题的控制措施
为严格控制塑胶件表面黑点,提高产品质量、减少原料和人工浪费,降低成本,现制定预防措施如下:
1.打料或混料前应将打料机或混料机内的剩料或粉尘彻底清理干净后,才能开机打料或混料。
2.打料时,若发现有被污染或有黑点的水口料之废品,必须挑出来经处理后(如:清洁油污、气枪吹掉灰尘等),才能打碎,严禁打错料、打混料。
3.所有打好或混好的料,装入料袋后,必须及时将料袋口封存严并做好标识。
4.所有装料的胶袋或加料的工具必须彻底清理干净。
5.保持打料、混料场所清洁无尘,混料机需随时盖好盖子,下料后料闸口处的料应及时清理干净,并关好料闸。
6.机位烘料桶必须清理干净,进风口需用防尘布包住,防止灰尘进入烘料桶内。
7.加料前需先将料袋外面及底部的灰尘清理干净,方可加料,加料后若料袋中剩有原料,应及时将料袋口封好。
8.料斗中的料不准加得太满,并要随时盖严料斗盖,防止空气中的灰尘落入料斗中。
9.将水口胶桶(箱)内的异物和灰尘清理干净后,方可装水口料或废品。
10.开啤调机时,严禁用脏手去拿产品及水口,必须戴上干净手套去拿。
11.有油污或黑点的产品及水口料,必须与干净废品或水口料分开摆放,严禁混装在一起。
12.所有被污染或黑点多的不良产品(包括水口料)必须做黑色料或废料处理,
13.较大胶件中的黑点应用刀挑出,才能放入水口桶中。
14.水口料或废品(包括产品)落在地面上时,应及时拣起来并将其擦干净(或吹干净),严禁任何人将被污染(黑点多)的水口料或产品扔进干净的水口胶桶中。
15.水口或废品满一筐/桶时,应及时拉到水口房碎成水口料,来不及粉碎时,应盖上塑料薄膜袋。
16.做好开机/停机时的清机、洗炮工作,防止料筒中原料因料温过高或受热时间过长而出现碳化现象。
E.机位水口料的控制措施
目前,很多注塑部未对机位水口料进行严格控制与管理,既缺乏检查/监督,又无管理处罚措施。
甚至一些员工将盛装水口料的胶桶视为“垃圾桶”,任何东西都往里面扔,胶桶中常有不同原料产品的水口、胶头、碎布、废纸、喉管、水口剪、刀片、螺丝批、铜喉嘴、生力布、油污的胶件、烧焦的胶头等异物。
为防止水口污染和碎料时损坏刀片,杜绝回用水口料中有异物,确保生产正常运行,必需按以下要求去控制:
1.盛装水口料的胶桶使用前需检查一下,如有油污、灰尘、异物等应清理干净。
2.盛装水口料的胶桶需分类使用,新胶桶专用于剩装透明或白色产品的水口。
3.严禁向盛装水口料的胶桶中扔异物(如:不同色/不同料的胶件或水口、纸片、污染的胶头及五金工具等)。
4.接班时机位啤工、技工、组长均需检查确认机位水口料中是否有异物。
5.生产过程中机位啤工、技工、组长、助理员(班长)、领班等均需严格控制水口料、防止水口料污染或混有杂物。
6.各级管理人员平时巡机时均需检查机位水口料胶桶中是否有异物、发现问题及时调查产生的原因,并追查相关人员之责任。
7.胶桶装满水口料/废品时,需贴上标签(标识纸),注明日期、班别、机台及原料/色粉编号,以便发现问题时,能追查相关人员之责任。
8.水口房人员需对生产过程中机位水口料进行巡查,发现问题及时上报处理。
9.碎料人员在碎料前需仔细检查水口料中是否有异物(如:不同22.料的产品/水口、胶头、碎布、纸片及五金工具等),水口料中若有异物,必须及时查明责任人并上报处理。
F.水口料添加比例的规定
1.透明产品之水口料不可回用(只能做为它用)。
2.结构简单(无扣脚、无螺丝柱)的内装件可用全水口料啤。
3.结构较复杂且需受力的内装件,可加30%左右的水口料(需检测其强度)。
4.外观要求较高、结构复杂的产品,最好不加水口料,最多可考虑加25%以内的水口料。
5.外观要求一般,结构较简单且非受力的产品,可加50%左右的水口料。
6.白色产品要视水口料干净情况来添加(最好不加),无黑点的水口料在结构简单的产品中可加25%,复杂结构的白色产品加15%的水口料。
7.水口料的添加要视产品的功能、作用、受力情况及外观要求而定。
8.添加水口料的比例超过40%时,必须交样板给品管部测试强度和功能,并检查颜色是否一致。
9.可以添加水口料的产品,在啤货过程中(开始一个班生产的产品用全原料外),所加入的水口料用量应均匀一致,避免添加的水口料量忽多忽少,影响产品质量的稳定性。
10.严禁随意添加水口料或更改水口料比例。
11.改变水口料添加的比例时,必须经过工程部门批准,品管部确认。
12.已被污染(含有其它颜色、原料或黑点、油污)的水口料严禁加入浅色料中啤货。