汽车覆盖件拉延模设计方法
汽车覆盖件拉伸模的设计及调试

汽车覆盖件拉伸模的设计及调试【摘要】介绍汽车覆盖件拉伸模的设计要点及主要的调试经验,并对汽车覆盖件在拉伸过程中容易出现的起皱和开裂现象进行了分析,从工艺分析、模具结构设计及调试等几个方面详细说明了拉伸模设计及调试的重要性。
1 大型覆盖件拉伸模的设计1.1 拉伸件冲压工艺方案的确定拉伸件的工艺性是编制覆盖件冲压工艺首先要考虑的问题,只有设计出一个合理的、工艺性好的拉伸件,才能保证在拉伸过程中不起皱、不开裂、少起皱、少开裂。
覆盖件拉伸工序的处理不仅是为拉伸工序 建立良好的变形条件,而且要为以后的工序提供方便。
所以在设计拉伸件时不但要考虑冲压方向、压料面的形状、拉延筋的形状及位置、工艺补充部分的合理性以及与下道工序之间的关系。
(1)冲压方向的确定。
正确地确定拉伸方向不仅是获得理想拉伸件的保证,而且将对后续工序的安排产生较大的影响,因此拉伸方向是确定拉伸件的第一要素。
确定拉伸方向时主要考虑:保证凸模能顺利进入凹模,且进入拉伸件的所有角落;开始拉伸时凸模与毛坯应尽量的使接触面大,且接触面应尽量位于冲模中心;压料面各进料阻力应均匀。
(2)合理增加工艺补充部分。
汽车覆盖件种类繁多,一些覆盖件形状复杂,结构不对称,直接成形较困难,设置必要的工艺补充部分有利于改善拉伸件的工艺性,提高拉伸件的质量。
工艺补充部分是拉伸件不可缺少的部分,在拉伸完成 后又需要将它切掉,因此,确定拉伸件工艺补充部分应遵循以下原则:使拉伸深度尽量浅;尽量利于垂直修边;工艺补充部分应尽量小。
(3)压料面形状的确定。
压料面是工艺补充的一部分,在增加工艺补充时必须正确确定压料面的形状,使压料面各部分的进料阻力均匀。
要做到这一点,必须保证 各方向的拉伸深度均匀,因为只有在压边圈将拉伸毛坯压紧在凹模压 料面上,不形成皱纹或折痕,才能保证拉伸件不皱不裂。
在确定压料面形状时要尽量降低拉伸深度,使形面平缓,由于凸模对拉伸毛坏要有一定的拉伸作用,所以必须保证压料面展开长度比凸模展开长度短,材料才能产生拉伸,如果压料面展开长度比凸模长,拉伸时可能会形成波纹或起皱。
汽车覆盖件拉延模设计方法

•
8.确定模具尺寸、导腿尺寸、导板尺寸位置
• 确定模具尺寸 (1)调入模板,调整闭合高(根据工艺卡),模具长宽 (2)确定模具吊耳、起重棒、翻转套大小及位置 • 确定导腿尺寸 (1)导腿长度至少占整体宽度2/5 (2)确定导腿刃入量,保证导腿导板在上模触料之前刃入40mm (3)导腿处导板保证同一高度且同时刃入 • 凸模导板尺寸及位置 (1)导板的安装位置约在凸模长度方向的1/6处 (2)导板导向面的宽度约为凸模长度的1/5-1/4 (3)导板高度〉压边圈行程+60~100mm (4)导板安装面要凸出分模线3~5mm便于加工 ( 5 ) 导板上端面与压边圈距离最好设计为40mm,因钳工调试时 不放墩死垫,容易发生异常。
9.布筋、挖夹持孔、减重孔、流水孔、出气 孔 • 布筋
(1)受力处必须布筋支撑,如调压垫、墩死垫 上下模底面筋要与机床的T槽错开,分模线以内上模本体、凸模、下 模座的筋要对应,导板后面最好有筋支撑 (2)两筋间隔最大350MM,一般控制在300MM以内 (3)为保证铸造清砂,底空不易过深过窄,底空型腔深度最好小于2.5 倍的底空宽度 (4)受力筋上尽量少挖减重孔 (5)尽量避免十字筋 • 夹持孔及减重孔的尺寸及形状,根据模具结构尺寸的不同而不同,但 其底边与模具底面间距至少100MM-150MM • 流水孔一般为直径Φ40的圆孔,设在模具型腔底部,并要保证每个型 腔的液体能流到模具外侧。 • 凸凹模的随型筋上挖Φ50的出气孔,不要存在封闭的型腔 凸凹模的型面上挖Φ4或Φ6的出气孔,打在凸凹模的凹形处
10.满足设计任务书及客户要求
• • • • • • • • • 活动件防护装置 在下模装防护板 压板槽、上模快卡、下模快速定位的要求 键槽及通键、加工基准孔的要求 起重形式的要求 气顶接柱上加钢垫、气顶躲空的要求 气路及电路位置的要求 模具防反、防侧向力的要求 客户及任务书对标准件的要求 客户的其他要求(如铸字、叉车过孔等)
汽车覆盖件数值模拟与拉延模设计

汽车覆盖件数值模拟与拉延模设计汽车覆盖件(简称覆盖件)是指覆盖汽车发动机、底盘、构成驾驶室和车身的薄钢板异形体的表面零件(外覆盖件)和(内部零件),与一般冲压件相比较,具有材料薄、形状复杂、结构尺寸大、表面质量要求高及生产成本高等特点。
在覆盖件的冲压工艺设计、模具设模具制造工艺上,也具有独自的特点【1】,一般需要经过多道工序(如拉延、冲孔修边、翻边、整形等)才能完成。
在其整个生产中,拉延成形则是一道关键的工序,而决定拉延成败和工件质量的,则是拉延成形的模具。
以前采取单件压制,生产效率、材料利用率和设备利用率均比较低。
将拉延工艺作了改进,采用中心对称一模两件的方法重新设计和制模,大大提高了设备利用率和生产效率[2]。
1冲压工艺分析(1)rember冲压工艺rember零件的材料为cr340,板料厚度为1mm, 抗拉强度750 mpa,延伸率16% 。
零件的结构外形如图1所示。
该零件的结构复杂,需要经过多道工序才能完成,根据该工件的工艺分析,工艺路线为:落料→拉延→冲孔、修边→cam修边→翻制→冲孔、分离。
具体工序图如图2所示。
该零件局部成形较多,是冲孔、拉延和翻边、修边复合的结果。
在拉延过程中,采用一模两件对称方式进行拉延,为保证能将拉延件的全部空间形状一次拉延出来,不应有凸模接触不到的“死区”,即既要保证凸模能全部进入,尽量使拉延深度差最小,以减小材料流动性和变形分布的不均匀性。
工艺补充是拉延工艺不可缺少的部分,但工艺补充部分应尽量减少,以提高材料的利用率。
工艺补充部分除考虑拉延工艺和压料面的需要外,还要考虑修边和翻边工序的要求。
该工件的工艺补充面和垂直修边线如图3所示:(2)拉延仿真结果与成形性分析。
拉延仿真选用的材料与上面相同,板坯尺寸为920mm×200mm,摩擦系数为0.1,压边力初定为95kn,冲头速度5000mm/s,在定义好模具各部分运动和边界条件后,提交工作到ls-dyna进行计算。
汽车覆盖件模具设计2.1拉延模本体设计

凸模(Punch)
分模线是凸模和压边圈的分界线,它是封闭的。凸模外围2D分模线与压边 圈内形2D分模线的间隙是1.5~2.0mm,大模具取2.0mm,中小模具取1.5mm。 本项目取1.5mm。
分模线(实际是面)通过数控机床2D加工出来,深度为40mm。
凸模分模线
凸模(Punch)
设计步骤: 1. 下模座构建,下模中不含凸模与下模座分开铸造,凸模材料为MoCr铸铁等,下模座材料为HT300 成本低,工艺复杂
拉延模的工作部分是凸模、凹模和压边圈三大件,工作部分材料全用MoCr铸 铁。另外GM241、GM246也是与MoCr铸铁相近的材料, GM246稍贵。
工作部分就是型面部分,型面部分需要上数控机床加工3D型面。 本项目是凸模与下模座共同铸造的,材质为MoCr铸铁。
本项目拉延模凹模为整体式,它的材料是MoCr铸设计。最终凹模实体图如 下。
(a) 正面
(b) 背面(左右翻转)
凹模(Die)
型面部分比周边非型面部分高出至少20mm,可以沿型面偏置一定数值得到 非加工部分,也可以用几段折线拉伸作出比型面低下去的非加工面。 型面的范围比板料线周边大10mm。
设计步骤: 1. 构建中间型面部分
压边圈运动时通过耐磨板(或称导板)进行导向控制,一般情况下耐磨板装 在凸模上,在压边圈的相关部分作出导滑面,要求导向间隙在0.02 mm以内。导 向行程必须大于压边圈向上运动的行程,即当压边圈向上运行到最高点时,耐磨 板与导滑面至少保证接触深度不少于50 mm。
压边圈(PAD)
压边圈上部分 1. 上部中间是型面,需数控加工的工作部分,外轮廓二维尺寸比板料线外形轮廓 单边大10 mm;
1 整体结构 2 凸模(Punch) 3 压边圈(Pad/Binder) 4 凹模(Die)
汽车覆盖件拉延模具精确型面构建方法研究

P
d f Rj ( ) +( d f +t r c ) R , , ( “ )
,
图1汽车覆盖件拉延模具精确型面构建方法流程示意图
s
i  ̄ j = O
2 . 1模具型 面的面片构建 模具 型面的面片构建首先就要 规避对 NUR B S曲面 结构形 式 的改变 ,除此之外 ,要对汽 车覆 盖件精确 型面 的每 一个 曲面
c o o >O ,c o , >O ,根据 这两个权 因子 的关系 可 以得 出 0 ,所 以当有 S 个权 因子时 ,它们 不可 能同时为 0 ,而且为 了保证 曲 线 具有凸包性质 ,就必须防止公式 中出现分母为 0 的现象 ,这 样 就能保证 曲线不会退化成 点。 如果我们在 曲线中制定某一个 参数 “的点为 P,在所给 定 的曲线上进行 该点 P的沿方 向矢量位移 ,移动距 离为 C ,最终
相应曲面的控制定点偏移量 ,从而实现 曲面能够随着 网格 的模 的坐标数 值。然后 为每 个控制 定点 P 在 精确模 面 中寻找三 个 型变化而发生 自然形变 。只有这样才 能构建 出适合 于汽车覆盖 较它距离最近 的网格节 点,构成投影环 境下的三 角平 面。 件 厚度变化 的模具精确 型面来 。如果 能在 N UR BS曲线及其 曲 2 . 控制各个顶面 ,将上述 中的三角平面 投影 投射 到精 确模 线权 因子都不发生变化的情形下进行 网格模型 的节 点位移 ,进 面 的网格单元上 ,因为原始模面 网格模 型与精确模面 网格模 型 而修 正其对 应 曲面要控制的顶点位置 ,就要构建 出一种对应于 的单元节点是相 同的,所 以在此要建立单元节 点的对应 映射关 精确 型面网格模型的精确 曲面模型 。它 的具体构 建流程如 图 1 。 系, 再应用三角函数插值法对三角形上的投影点坐标进行计算 。 关于汽车覆盖件模具系统的具体应用 ,美 国国家标准局早 3计算 出原始模面 的控制顶 点后 ,利用 向 ( 下转第 1 7 1 页)
汽车覆盖件模具设计2.2拉延模顶杆布置设计

5. 顶杆垫块( Pin Block)
知识点
Knowledge Point
安装位置:装于压边圈顶杆凸台下
作用:降低顶杆对压边圈顶杆凸台的磨损
顶杆垫块样式
样式1 两个螺钉固定的圆形顶杆垫块,它 需用到2个M10内六角螺钉,外径D 一般有¢60 mm、¢70 mm等。
样式2 一个螺钉固定的圆形顶杆垫块,中 心用一个M12的内六角螺钉固定。外 径D一般有50 mm、60 mm、70 mm 三个系列。
一 知识点
Knowledge Point
二 设计步骤 Design Procedure
三 设计指导 Design Guide
知识点
Knowledge Point
1. 顶杆(Pin)的作用 2. 认识冲压设备工作台(Machine Table) 3. 模具偏心(Die off-centre) 4. 顶杆孔( Pin Hole)布置的原则 5. 顶杆垫块( Pin Block)
4. 压边圈上顶杆凸台设计
设计步骤
Design Procedure
(1)确定压边圈顶杆凸台高度。
压边圈行程:压边圈从模具闭合(镦底)状 态到向上顶到最高点时的高度差。
在模具中运动部件的行程在图纸中简写为St, 全称为Stroke。拉延开始压边圈顶到最高点时, 应保证所放坯料只接触压边圈工作部分,不接触 凸模,顶杆行程应保证压边圈的压料面高于凸模 即工件最高点5 mm以上,这就是对压边圈行程 的要求。
4. 顶杆孔布置的原则
知识点
Knowledge Point
① 顶杆在气垫下死点时不应高出下工作台面;
② 顶杆接杆长度小于200 mm,可与压边圈一体铸出。使用寿命≥30 万次的 模具,顶杆承接面不允许为铸铁基体材料 ,应使用顶杆垫块;
汽车覆盖件成形中拉延筋的设计与数值模拟
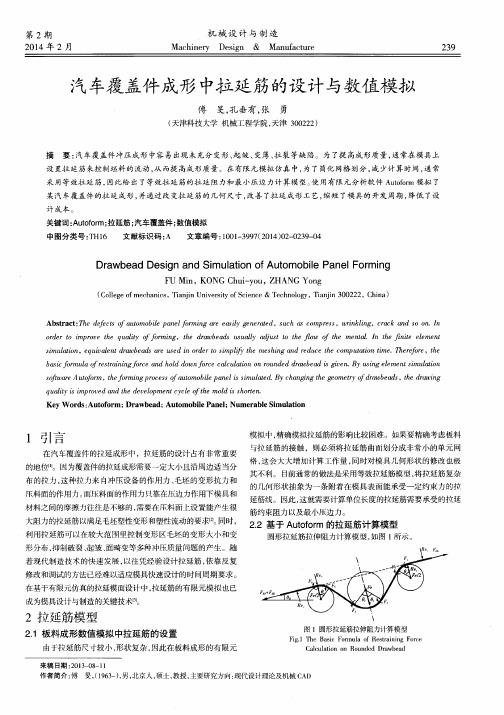
( C o l l e g e o f m e c h a n i c s , T i a n j i n U n i v e r s i t y o f S c i e n c e &T e c h n o l o g y , T i a n j i n 3 0 0 2 2 2 , C h i n a )
摘
要: 汽车覆盖件 冲压成形 中容 易出现 未充分 变形 、 起皱 、 变薄 、 拉 裂等缺 陷。 为 了提 高成形 质量 , 通常在模 具上
设置拉延 筋来控制坯料 的流动 , 从 而提 高成形 质量。在有 限元模 拟仿真 中, 为 了简化 网格 划分 , 减 少计 算时 间, 通常 采 用等效拉 延筋 , 因此给 出了等效拉 延筋 的拉延 阻力和 最小压边力计 算模 型。 使 用有限元分析软件 A u t o  ̄r m模拟 了
第 2期 2 0 1 4年 2月 ຫໍສະໝຸດ 机 械 设 计 与 制 造
Ma c hi n e r y De s i g n & Ma nu f a c t u r e 2 3 9
汽车覆 盖件成形 中拉 延 筋的设 计与数值模 拟
傅 曼, 孔垂有 , 张 勇
( 天津科技 大学 机械工程学 院, 天津 3 0 0 2 2 2 )
某汽 车覆 盖件的拉延成形 , 并通过 改 变拉延 筋的几何尺 寸 , 改善 了拉 延成形 工艺 , 缩短 了模具 的开发周期 , 降低 了设
计成 本。
关键词: Au t o f o r m; 拉延筋 ; 汽车覆盖件 ; 数值模拟 中图分类号 : T H1 6 文献标识码 : A 文章编号 : 1 0 0 1 — 3 9 9 7 ( 2 0 1 4 ) 0 2 — 0 2 3 9 — 0 4
汽车覆盖件模具设计2.2拉延模顶杆布置设计

5. 顶杆垫块( Pin Block)
知识点
Knowledge Point
安装位置:装于压边圈顶杆凸台下
作用:降低顶杆对压边圈顶杆凸台的磨损
顶杆垫块样式
样式1 两个螺钉固定的圆形顶杆垫块,它 需用到2个M10内六角螺钉,外径D 一般有¢60 mm、¢70 mm等。
样式2 一个螺钉固定的圆形顶杆垫块,中 心用一个M12的内六角螺钉固定。外 径D一般有50 mm、60 mm、70 mm 三个系列。
(a) T型槽断面图(上下工作台同)
(b) 下工作台垫板上顶杆过孔断面图
知识点
Knowledge Point
3. 模具偏心(Die off-centre)
一般情况下,模具中心与机械中心是重合的,但在拉延模设计中有可能出现 模具中心与机械中心不重合的情况,这就是偏心现象。拉延模设计时,顶杆孔应 尽量靠近分模线,为此会出现模具中心与机床中心不重合的情况。这种情况下, 要注意压板槽的位置要与机床中心一致, Y向可以偏心,X向一般不偏心,避免 压板槽布置出错。
一 知识点
Knowledge Point
二 设计步骤 Design Procedure
三 设计指导 Design Guide
知识点
Knowledge Point
1. 顶杆(Pin)的作用 2. 认识冲压设备工作台(Machine Table) 3. 模具偏心(Die off-centre) 4. 顶杆孔( Pin Hole)布置的原则 5. 顶杆垫块( Pin Block)
1. 顶杆的作用
知识点
Knowledge Point
顶杆的样式
知识点
Knowledge Point
观看顶杆运动了解其工作状态
- 1、下载文档前请自行甄别文档内容的完整性,平台不提供额外的编辑、内容补充、找答案等附加服务。
- 2、"仅部分预览"的文档,不可在线预览部分如存在完整性等问题,可反馈申请退款(可完整预览的文档不适用该条件!)。
- 3、如文档侵犯您的权益,请联系客服反馈,我们会尽快为您处理(人工客服工作时间:9:00-18:30)。
•
7.确定压边圈限程及坯料送料定位装置
• 确定压边圈限程 (1)内导向一般采用退料螺钉限程 外导向模具多用限程板或是侧销限程 (2)限程距离=压边圈行程 +20mm(安全距离) 确定送料制件定位 (1)多采用定位板定位 (2)定位板高度根据重力坯料线确定,直边至少高于重力坯料线20mm (3)当制件起伏比较大时,要采用配重式定位板 (4)当重力坯料线和定位坯料线在板料流入方向上有偏差时,要将定位板设计 为随型式,即沿着坯料的下落轨迹线(由CAE算出) (5)自动线时要布置传感器定位板,注意传感器定位板要保证放料时能有感应 同时还要保证取件时不干涉 (6)定位板的安装位置不能与拉延筋干涉
单动拉延模结构设计标准
个人经验总结
单动拉延模设计过程
工艺分析 • 分模线决定了凸模的外圈轮廓大小 • 坯料线决定了压料面的大小 • 拉延前后坯料线可以反映板料在压料面上的流入情况 • 重力坯料线决定了定位板定位位置和高度 • 拉延筋可以控制板料的流入量 • 到底标记用来检测是否拉伸到位(设计在废料区) • 左右标记是产品左右件的标识,来实现焊装白车身的目 的 • CH孔是在拉延(序)模上的拉延件上冲制的两个模具制 造调试用的研模(定位)工艺孔。是带件研合各序模具型 面(和形状)的基准
10.满足设计任务书及客户要求
• • • • • • • • • 活动件防护装置 在下模装防护板 压板槽、上模快卡、下模快速定位的要求 键槽及通键、加工基准孔的要求 起重形式的要求 气顶接柱上加钢垫、气顶躲空的要求 气路及电路位置的要求 模具防反、防侧向力的要求 客户及任务书对标准件的要求 客户的其他要求(如铸字、叉车过孔等)
•
8.确定模具尺寸、导腿尺寸、导板尺寸位置
• 确定模具尺寸 (1)调入模板,调整闭合高(根据工艺卡),模具长宽 (2)确定模具吊耳、起重棒、翻转套大小及位置 • 确定导腿尺寸 (1)导腿长度至少占整体宽度2/5 (2)确定导腿刃入量,保证导腿导板在上模触料之前刃入40mm (3)导腿处导板保证同一高度且同时刃入 • 凸模导板尺寸及位置 (1)导板的安装位置约在凸模长度方向的1/6处 (2)导板导向面的宽度约为凸模长度的1/5-1/4 (3)导板高度〉压边圈行程+60~100mm (4)导板安装面要凸出分模线3~5mm便于加工 ( 5 ) 导板上端面与压边圈距离最好设计为40mm,因钳工调试时 不放墩死垫,容易发生异常。
1.核对拉延模行程并确定气顶数量及位置
• 拉延模压边圈行程以工艺卡提供的行程为准 工艺卡提供行程有2种形式: (1)ST=XX 表示凸模担料 (2)ST=XX+40mm(TQM安全值)表示凸模不担料 • 气顶数量=压边力/单个气顶所受力(4T)+安全个数(0-4) • 气顶位置的布置 (1)保证气顶均布在分模线外侧并尽量接近分模线 (2)尽量保证受力平衡,以模具中心划分4个象限,保证每个象限气 顶个数相同 (3)有时为了保证上述条件可能要将机床偏心,这时就要看任务书 是否允许偏心 (4) 注意设备是否要求气顶全躲开 (5)气顶位置要注意同时满足客户设备和TQM设备要求
2. 确认模具材质
• 模具材质以任务书为标准 注意:下模是否可以做成分体式看材质要求
3 根据制件形状确定模具的导向形式, 大致 分为外导向拉延,内导向拉延,四角导向 拉延
4 确认凸凹模和压边圈的基准高
5.设计凸模、凹模及压边圈工作部分
筋厚要求:型面60MM.受力筋50MM.其他筋 40MM • 凸模工作部分的设计 (1)用分模线和型面裁出凸模的形状 (2)确定刃口高度 压料面为二维曲面时高度一般为40MM 压料面为三维曲面时高度一般为50MM (3)做出受力筋
刃口高度 (3)确定刃口高度 压料面为二维曲面是高度一般为50MM 压料面为三维曲面是高度一般为60MM 压边圈刃口距凸模刃口距离为3mm (4)做出受力筋
50
6.布置调整垫块及镦死垫块
• 调整垫块布置(凹模与压边圈之间) (1)在坯料流入量大的地方要布置调整垫块 (2)沿着压料面周圈300mm-400mm均布 (3)调整垫块安装台的位置高于压料面时,距离压料面至少30mm, 低于压料面时,距离10~20mm即可 (4)手动线时尽量保证垫块的上表面在坯料面以下 镦死垫块布置(压边圈与凸模之间) (1)靠近分模线,尽量保证400MM均布 (2)四角要布置4个墩死垫,保证模具受力平衡 (3)有产品在压料面上时,必须布置墩死垫块,产品在分模线以里不 在压料面上时,压料面下可不布置墩死垫块,但仍然需要看客户要求
9.布筋、挖夹持孔、减重孔、流水孔、出气 孔 • 布筋
(1)受力处必须布筋支撑,如调压垫、墩死垫 上下模底面筋要与机床的T槽错开,分模线以内上模本体、凸模、下 模座的筋要对应,导板后面最好有筋支撑 (2)两筋间隔最大350MM,一般控制在300MM以内 (3)为保证铸造清砂,底空不易过深过窄,底空型腔深度最好小于2.5 倍的底空宽度 (4)受力筋上尽量少挖减重孔 (5)尽量避免十字筋 • 夹持孔及减重孔的尺寸及形状,根据模具结构尺寸的不同而不同,但 其底边与模具底面间距至少100MM-150MM • 流水孔一般为直径Φ40的圆孔,设在模具型腔底部,并要保证每个型 腔的液体能流到模具外侧。 • 凸凹模的随型筋上挖Φ50的出气孔,不要存在封闭的型腔 凸凹模的型面上挖Φ4或Φ6的出气孔,打在凸凹模的凹形处
刃口高度
10
60
50
•
凹模工作部分的设计 (1)用型面裁出凹模的形状
分模线
(2)用坯料线外偏20MM确定凹模 工作部分的轮廓,即压料面的大小
50
(3)分模线里外各偏25MM 做出受力筋
拉延筋中心线 凹模轮廓
10-20MM 坯料线 分模线
60
• 压边圈工作部分的设计 (1)用型面和分模线裁出压边圈 工作部分的形状 (2)用坯料线外偏10-20MM确定压边圈 工作