第5章其他冷冲压成形工艺概论
《冷挤压成型工艺及模具设计》课程大纲

《冷挤压成型工艺及模具设计》课程教学大纲一、课程名称(中英文)中文名称:冷挤压成型工艺及模具设计英文名称:Cold Extrusion Processes and Die Design二、课程编码及性质课程编码:0817761课程性质:选修课三、学时与学分总学时:24学分:1.5四、先修课程机械设计、材料成形工艺、金属学及热处理和材料成形原理等五、授课对象本课程面向材料成型及控制工程专业学生开设,也可以供材料科学与工程专业和电子封装技术专业学生选修。
六、课程教学目的(对学生知识、能力、素质培养的贡献和作用)本课程是第七学期开设的一般选修课,其教学目的主要包括:1、掌握金属材料冷挤压的变形性质和成型规律,以及冷挤压模具设计的方法;2、掌握冷挤压成型工艺及模具设计的特点及国内外发展概况,查找并掌握冷挤压技术及模具设计发展前沿的新技术的特性;3、掌握挤压成形的各种方法,能独立编制工艺规程和设计冷挤压模具,分析和解决冷挤压生产问题,具有今后从事冷挤压成型工艺和复杂模具开发与设计的能力。
表1 课程目标对毕业要求的支撑关系七、教学重点与难点:教学重点:1)本课程以介绍冷挤压成型工艺与模具为主体、以讲述两者的设计为重点;2)在全面了解与掌握挤压成形的材料原理及力学原理的基础上,重点学习冷挤压加工工序和模具的设计;3)重点学习的章节内容包括:第2章“挤压基本原理”(6学时)、第5章“冷挤压加工工序设计”(4学时)、第6章“冷挤压模具设计”(6学时)。
教学难点:1)冷挤压成型工艺及模具设计是实践性极强的课程之一,本课程将密切结合学生的生产实习、课程设计、实验课等实践环节,培养学生对冷挤压成型工艺及模具的认识及设计能力,提高授课质量与效果。
2)通过本课程学习,要求掌握冷挤压成型工艺的变形特点、应用范围、质量控制方法等,具备合理设计冷挤压成型工艺和复杂模具的实践能力。
八、教学方法与手段:教学方法:(1)采用现代化教学方法(含PPT演示,工艺动画,视频资料等),讲授冷挤压工艺的变形特点及应用领域,以提高教学效果及效率;(2)采用课堂教学与学生PPT汇报、交流讨论等方式,进行课堂互动,吸引学生的注意力、激发学生的学习热情,提高学生的学习效果。
冷冲压工艺与模具设计冷冲压概论
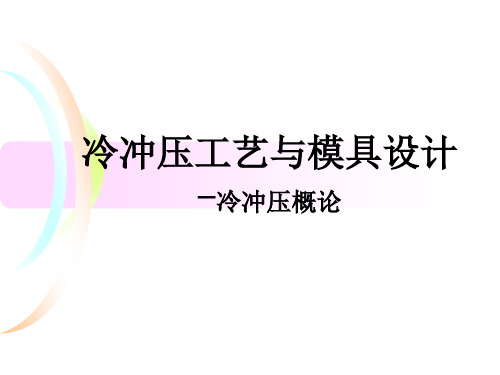
1.2.2 影响塑性及变形抗力的主要因素
• 2. 变形抗力 • 变形抗力一般来说反映了金属在外力作用下抵抗塑性变形的能力。 • 影响变形抗力的因素,也包括金属的内部性质和变形条件(即变形温度、变形速度和变
形程度)两个方面。 • 塑性和变形抗力是两个不同的概念。通常说某种材料的塑性好坏是指受力以后临近破
• 每种基本工序还包含有多种单一工序。冲压工序的具体分类及特点见表1-1和表1-2。
2 冲压工艺分类及模具
1.1.2 冲压工艺分类及模具
1.1.2 冲压工艺分类及模具
1.1.2 冲压工艺分类及模具
1.1.2 冲压工艺分类及模具
1.1.2 冲压工艺分类及模具
• 在实际生产中,当冲压件的生产批量较大、尺寸较小而公差要求较小时,若用分散的单一工序来冲压是不经济的, 甚至难以达到要求。这时在工艺上多采用工序集中的方案,即把两种或两种以上的单一工序集中在一副模具内完成, 称为组合工序。根据工序组合的方法不同,又可将其分为复合、级进和“复合-级进”3种组合方式。
1.2.2 影响塑性及变形抗力的主要因素
• 1. 塑性 • 所谓塑性,是指金属材料在外力作用下产生永久变形而其完整性不被破
坏的能力。塑性指标可用材料在不被破坏的条件下能获得的塑性变形的 最大值来评定。对于同一种材料来说,在不同的变形条件下,其塑性是 不一样的。 • 影响金属塑性的因素包括两个方面:①金属本身的晶格类型、化学成分 和金相组织等;②变形时的外部条件,如变形温度、变形速度以及变形 方式等。
1.1.2 冲压工艺分类及模具
1.1.2 冲压工艺分类及模具
1.2 冲压变形的理论基础
1.2.1 金属塑性变形的概念 1.2.2 影响塑性及变形抗力的主要因素 1.2.3 成分与组织对金属塑性变形的影响 1.2.4 变形温度对金属塑性变形的影响 1.2.5 变形速度对金属塑性变形的影响 1.2.6 应力应变状态及其对金属塑性变形的影响
冷冲压工艺与模具设计绪论
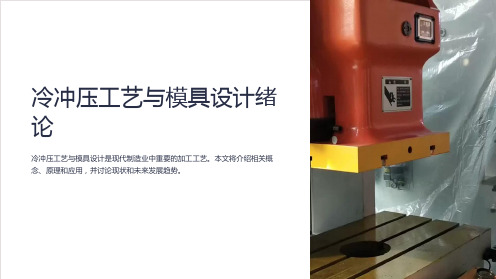
数字通信设备生产
冷冲压技术在数字通信设备生产中也非常常见, 例如手机中的精密零部件。
航空航天工业
冷冲压技术在航空航天工业领域也得到了广泛 的应用,例如飞机的外壳部件。
冷冲压的原理和过程
冷冲压是利用冲裁模和冲裁机械的压力,将金属板材加工成所需的形状。冷 冲压工艺一般包括五个过程:上料、定位、成形、冲裁、废料排除。
模具的精度要求是要达到国家标准,确保加工出来的零件精度和尺寸稳定一 致,能够达到设计要求。
模具的表面处理及涂层技术
1 石墨涂层
通过镀石墨涂层的方式能够大幅提高模具的防粘脱性、耐磨性。
2 表面喷涂处理
紫铜、白铜、硬铝等材料的表面处理,能够提高其的耐蚀性、耐磨性、耐高温性。
3 电镀处理
表面电镀是提高模具表面硬度、耐磨性的技术之一。
命,因此需要选择合适的模具材料。
3
确定零件
根据需要打造的元件和件装配关系,确定 加工零件型号和形状。
模具设计
按照所需的零件形状和要求,设计包括上 下模、上下模板、自动卡模等在内的模具 涉及的各项要素。
模具的分类
上下模式模具
上下模式模具是将一块板材放在 上模板上,再由下模板下压,实 现成型。
分段模具
3 材料利用率高
冷冲压能有效节约材料,使得原材料的利
冷冲压过程中不会产生废气废液,避免了对 环境的污染。
冷冲压工艺的应用领域
汽车零部件加工
冷冲压技术在汽车零部件生产中应用广泛,例 如车身、底盘等。
家电电器制造
冷冲压技术在家用电器生产中被广泛应用,例 如冰箱、洗衣机等。
2 卷料机
卷料机用于卷取成型后的金属板材,为后序加工做好准备。
3 切割机
切割机主要用于将冷卷板剪成所需的厚度及长度,并去除边缘毛刺。
冷冲压工艺及模具设计(绪论)页PPT文档

不多,而冷冲压的涵义要广泛些,包括 了立体冲压。
图0-l 冲压过程
绪论
1.基本概念(续)
加工对象:主要是金属板材 加工依据:板材冲压成形性能(主要是塑性) 加工设备:主要是压力机 加工工艺装备:冲压模具
冲压模具: 在冲压加工中,将材料加工成零件(或半成品)
的一种特殊工艺装备,称为冲压模具(俗称冲 模)。
绪论
冲压加工是制造业中最常用的一种材料成形加工方法。
冲压成形产品示例一——日常用品 冲压成形产品示例二——高科技产品
绪论
二、冲压工序的分类
根据材料的变形特点分:分离工序、成形工序
分离工序: 冲压成形时,变形材料内部的应力超过强度极限σ b,
使材料发生断裂而产生分离,从而成形零件。分离 工序主要有剪裁和冲裁等。
②模具标准化程度低; ③模具设计方法和手段、模具制造工艺及设备落后; ④模具专业化水平低。
所以,结果导致我国模具在寿命、效率、加工精度、生产周期
等方面与先进工业发达国家的模具相比差距相当大。
绪论
三、冲压技术现状与发展方向(续)
2.冲压技术发展方向 产品市场变化: 多品种、少批量,更新换代速度快
技术发展: 计算机技术、制造新技术
④材料利用率高,一般为70%-85%。
绪论
⑤生产率高,冲床冲一次一般可得 一个零件,而冲床一分钟的行程少 则几次,多则几百次。同时,毛坯 和零件形状规则,便于实现机械化 和自动化。
⑥冲压零件的质量主要靠冲模保证, 所以操作方便,要求的工人技术等 级不高,便于组织生产。
⑦在大量生产的条件下,产品的成本低。
绪论
1.基本概念(续)
冲
压 合理的冲压工艺 生
冷冲压工艺与模具设计
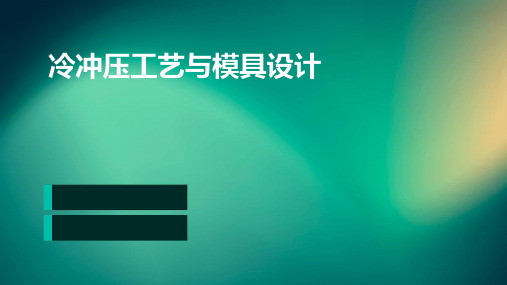
多工位级进模是一种高效率的冲模,可在一 副模具上完成多个工件的加工。设计时需考 虑工件的排列方式、送料方式、定位精度等 因素,确保生产效率和产品质量。
典型复合模和多工位级进模结构分析
典型复合模结构分析
以落料、冲孔复合模为例,其结构包括上模 、下模和导柱导套等部分。上模装有冲孔凸 模和落料凹模,下模装有卸料板、导料板和 定位销等。工作时,上模下行完成冲孔和落 料工序,废料从卸料板排出。
冷冲压工艺与模具设计
contents
目录
• 冷冲压工艺概述 • 冷冲压模具设计基础 • 冲裁工艺与模具设计 • 弯曲工艺与模具设计 • 拉深工艺与模具设计 • 其他冷冲压工艺与模具设计
01 冷冲压工艺概述
冷冲压定义及特点
冷冲压定义
冷冲压是在常温下利用冲模在压力机 上对材料施加压力,使其产生分离或 变形,从而获得一定形状、尺寸和性 能的产品零件的加工方法。
工序的冲裁模。生产效率高,但结构复杂,制造难度较大,适用于形状
复杂、精度要求高的零件生产。
Байду номын сангаас
04 弯曲工艺与模具设计
弯曲变形过程分析
01
02
03
弹性变形阶段
凸模开始接触坯料并下压, 坯料发生弹性压缩和弯曲。
塑性变形阶段
随着凸模继续下压,坯料 产生塑性变形,弯曲程度 逐渐增大。
校正阶段
弯曲变形完成后,凸模回 程,弯曲件在弹性恢复作 用下得到校正。
复合式拉深模
03
结合多种模具结构的特点,实现多工位连续拉深,提高生产效
率和产品质量。
06 其他冷冲压工艺与模具设 计
成形工艺原理及分类
成形工艺原理
冷冲压成形工艺是利用模具使金属板 材在室温下产生塑性变形,从而获得 所需形状、尺寸和性能的零件的加工 方法。
冷冲压加工工艺简介

冲压加工工艺与其他加工工艺方法相比 的优越性
a、生产效率高,在冷冲压工艺中,压力机的一次行程可完 成一道工序,而压力机的行程次数是每分钟几次或几百 次,所以在最短的时间内完成一道工序的工作。
b、材料利用率高,冷冲压加工能以较少的废料,而得到强 度大、刚性好,重量轻的机械零件。
c、同一产品的形状和尺寸一致性好:用模具冲压加工如同 复制,使零件的形状和尺寸非常接近模具工作部分,使 零件的具有良好互换性。
• 弯曲零件由于弯曲区的应力和应变存在, 材料的展开长度计算既不能按外层圆弧也 不能按内层圆弧,而是以计算中性层的长 度为准,中性层的位置随弯曲内半径不同 而有差异。
2.3 弯曲模具工作部分尺寸
• 弯曲件 的成型 尺寸依 据要求 的差异 可分为 四种表 注方法:
模具工作部分尺寸
• 其尺寸给定以零件尺寸标注形式来确定U型 件模具尺寸,标注零件内形尺寸时则以凸 模为模具尺寸基准,凹模按此基础加材料 厚度为间隙值(凹模尺寸),反之,当标 注零件外形尺寸时则以凹模为模具尺寸基 准,凸模按此基础加材料厚度为间隙值 (凸模尺寸),同时也可以根据加工方式 进行模具尺寸标注,加工方式分为配作法 和分作法。
裂缝扩展与重合
随着凸模继续挤入凸 模刀口处材料应力随 之达到并超过σb 最终 到达抗剪强度τ,当凸 模、凹模间隙Z/2合适 时,凸、凹模刀口处 出现的裂缝扩展重合 而使材料分离成零件 与废料。
冲裁零件端面构成部分
• 冲裁所得的零件表面(端 面)有几部分构成,微园 角部分(塌角)、光亮带 部分(挤压带)、断裂部 分(断裂带或粗糙带)。
2)冷冲压加工所针对的材料可以是金属、也可以是非金属, 可以是板材,也可以是条料、棒料、块料和型材。
3)冷冲压加工是许多加工方法中最重要的加工方法之一, 其在实际加工作业量中也是最大的几种之一。
《冷冲压工艺及模具设计》教案
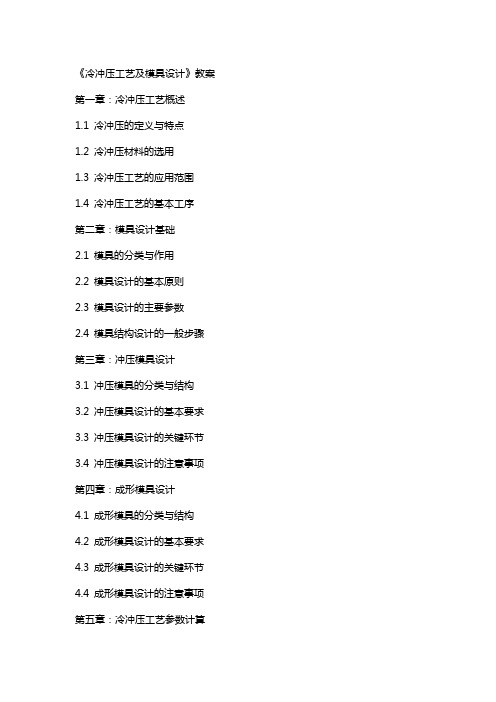
《冷冲压工艺及模具设计》教案第一章:冷冲压工艺概述1.1 冷冲压的定义与特点1.2 冷冲压材料的选用1.3 冷冲压工艺的应用范围1.4 冷冲压工艺的基本工序第二章:模具设计基础2.1 模具的分类与作用2.2 模具设计的基本原则2.3 模具设计的主要参数2.4 模具结构设计的一般步骤第三章:冲压模具设计3.1 冲压模具的分类与结构3.2 冲压模具设计的基本要求3.3 冲压模具设计的关键环节3.4 冲压模具设计的注意事项第四章:成形模具设计4.1 成形模具的分类与结构4.2 成形模具设计的基本要求4.3 成形模具设计的关键环节4.4 成形模具设计的注意事项第五章:冷冲压工艺参数计算5.1 冲压力的计算5.2 模具工作零件尺寸的计算5.3 冲压力的估算5.4 模具强度校核第六章:冲压设备及选用6.1 冲压设备的类型与性能6.2 冲压设备的选择原则6.3 冲压设备的使用与维护6.4 冲压设备的安全操作规程第七章:冷冲压工艺参数优化7.1 冲压工艺参数的影响因素7.2 冲压工艺参数的优化方法7.3 冲压工艺参数的实验研究7.4 冲压工艺参数优化的应用实例第八章:模具制造与维护8.1 模具制造工艺流程8.2 模具制造的材料选择8.3 模具制造的注意事项8.4 模具的维护与保养第九章:冷冲压工艺质量控制9.1 冲压质量问题及原因分析9.2 冲压质量控制方法9.3 冲压质量的检测与评估9.4 提高冲压质量的途径第十章:冷冲压工艺应用实例10.1 汽车覆盖件的冲压工艺10.2 家用电器的冲压工艺10.3 金属结构件的冲压工艺10.4 其他行业冲压工艺应用案例重点和难点解析一、冷冲压工艺概述补充说明:冷冲压材料的选用对于冲压成品的质量、模具寿命和生产效率具有重要影响。
需要根据成品的要求,选择合适的材料牌号和状态。
冷冲压工艺的基本工序包括剪切、弯曲、拉伸、成形等,了解各工序的特点和适用范围对于合理选择模具和工艺参数至关重要。
冷冲压概述

模块一冷冲压概述一、冲压加工概况1.冷冲压概念冷冲压是在室温下,利用安装在压力机上的模具对材料施加压力,使其产生分离或塑性变形,从而获得所需冲件的一种压力加工方法。
冷冲压加工实施条件:压力机、模具、材料性能冷冲压加工的性质:压力加工授课要点:比较压力加工与切削加工;举例说明冷冲压加工的条件和性质(例子为脸盆的生产)2.冷冲压加工的特点优点:1)冷冲压加工属于少、无废料加工,省能、低耗、高效所以冲件的成本低.2)质量稳定、互换性好。
3)适于加工壁薄、重量轻、形状复杂、表面质量好、刚性好的零件。
4)操作简单、生产效率高,对操作工人的技术要求低.缺点:1)生产环境差、噪音大、危险性高。
2)生产零件精度较低,经济精度等级为IT11~IT14。
3.冷冲压加工的应用:应用广泛,但要求有一定的批量性.二、冲压工序的分类1。
分离工序分离工序是指坯料在模具刃口作用下,沿一定的轮廓线分离而获得冲件的加工方法.主要包括落料、冲孔、分离等。
2。
成形工序成形工序是指坯料在模具压力作用下,使坯料产生塑性变形,但不产生分离而获得的具有一定形状和尺寸的冲件的加工方法。
主要有弯曲、拉深、翻边等.三、压力机简介机械压力机:曲柄压力机、摩擦压力机等1.压力机的分类液压机专用设备:折弯机、弯管机等2.曲柄压力机基本原理主要技术参数:1.公称压力:主要反应滑块下行时冲击力的大小。
2.滑块行程:滑块最高位置与最低位置之间的距离.3.装模高度:滑块位于下止点时,其下表面到工作台垫板上表面之间的距离。
4.模柄孔尺寸5.工作台尺寸6.行程次数四、冲模简介1。
模具的分类简单模(单工序模):在压力机的一次行程中,只能完成一道冲压工序的模具。
单工序、单工位级进模(连续模):在压力机的一次行程中,在模具的不同工位上同时完成多道工序的模具。
多工序、多工位复合模:在压力机的一次行程中,在模具的同一工位上同时完成多道工序的模具。
多工序、单工位例:垫圈的生产使用简单模生产,需要两套模具—-落料模、冲孔模.使用级进模生产,需要一套模具——在模具的第一个位置上冲孔,第二个位置上落料.使用复合模生产,需要一套模具-—在模具的同一个位置上同时完成落料和冲孔工序.2.模具组成零件简介工作零件:对材料直接施加压力,完成冲压工作的零件。
- 1、下载文档前请自行甄别文档内容的完整性,平台不提供额外的编辑、内容补充、找答案等附加服务。
- 2、"仅部分预览"的文档,不可在线预览部分如存在完整性等问题,可反馈申请退款(可完整预览的文档不适用该条件!)。
- 3、如文档侵犯您的权益,请联系客服反馈,我们会尽快为您处理(人工客服工作时间:9:00-18:30)。
第5章其他冷冲压成形工艺与模具设计本章内容:学习目的与要求:1.了解翻边、胀形、缩口、校形等工序的变形特点;2.了解胀形模、翻边模、缩口模、校形模的结构特点。
重点:翻边、胀形工序的变形特点、工艺性和模具结构特点。
难点:翻边工序的变形特点。
在掌握冲裁、弯曲、拉深成形工艺与模具设计的基础之上,本章介绍其它成形工艺特点和模具结构特点。
涉及翻边、胀形、缩口、校形等成形工序的变形特点、工艺与模具设计特点。
成形工艺:用各种局部变形的方式来改变零件或坯料形状的各种加工工艺方法。
按塑性变形特点,分为➢压缩类成形:缩口、外翻边➢主应力为压应力,材料变厚,易失稳➢伸长类变形:翻孔、内翻边、起伏、胀形等➢主应力为拉应力,材料变薄,易破裂5.1成形工艺与模具设计教学要点【目的要求】1、起伏成形工艺与模具设计2、圆柱形空心毛坯的胀形3、翻孔和翻边4、缩口5、校平与整形6、压印教学要点【重点】1、起伏成形的定义、主要目的及主要形式2、胀形的定义3、翻孔、翻边的定义,主要变形部位及易出现的质量问题;极限翻边系数及影响因素4、缩口的定义、受力特点5、校平与整形的定义、工艺特点【难点】1、翻孔、翻边的主要变形部位及易出现的质量问题;2、极限翻边系数及影响因素当坯料外径与成形直径的比值D/d>3时,其成形完全依赖于直径为d的圆周以内金属厚度的变薄实现表面积的增大而成形。
问题:与拉深的差别在哪?胀形的变形区及其应力应变示意图:5.1.1起伏成形工艺与模具设计局部起伏成形:是材料的局部发生拉深而形成部分的凹进或凸出,借以改变零件或坯料形状的一种冲压方法。
1. 加强肋(beading)2. 加强窝(swaging)3. 起伏成形的压力计算4. 百页窗口的冲压5.1.1起伏成形工艺与模具设计起伏成形目的:主要用于增加工件的刚度和强度以及使零件美观图5-1起伏成形的零件示意图1. 加强肋(beading)表5-1加强肋的尺寸图5-2加强肋的形式能够一次成形加强肋的条件为δε)75.0~7.0(00≤-=l l l 式中ε——许用断面变形程度;l 0——变形区横断面的原始长度(mm );l ——成形后加强肋断面的曲线轮廓长度(mm );δ——材料伸长率;0.7~0.75——视加强肋形状而定,半球形肋取上限值,梯形肋取下限值。
两道工序成形的加强肋a)首次成形b)最后成形如果ε>0.75δ,采用两道工序成形加强肋,如上图所示。
当加强肋与边缘距离小于(3~3.5)t时,需加大制件外形尺寸,压形后增加切边工序。
表5-2加强窝的尺寸和间距(mm)3. 起伏成形的压力计算bKLt P σ=冲压加强肋的变形力:若在曲柄压力机上用薄料(t <1.5mm )对小制件(面积小于200mm 2)压肋或压肋间校正工序时,变形力:2KFt P =4. 百页窗口的冲压胀形:将空心件或管状毛坯沿径向向外扩张的冲压工序1. 刚性凸模胀形2. 软模胀形3. 波纹管零件胀形4. 罩盖胀形模设计示例1. 刚性凸模胀形1-分瓣凸模2-型芯3-零件4-气垫顶杆图5-7钢模胀形2. 软模胀形图5-8软体凸模胀形a )橡胶凸模胀形b )倾注液体法胀形c )冲液橡胶囊法胀形3. 波纹管零件胀形4. 罩盖胀形模设计示例工件名称:罩盖生产批量:中批量材料:10钢料厚:0.5㎜(1)工件的工艺性分析(2)工艺计算(1)工件的工艺性分析由图可知,其侧壁由空心毛坯胀形而成,底部为起伏成形(2)工艺计算1)底部起伏成形计算起伏成形的计算:2) 侧壁胀形计算。
NNFKFtP110395.0154250222=⨯⨯⨯==π2.1398.46max===ddK表5-3极限胀形系数和切向许用伸长率3) 胀形毛坯的计算。
4) 侧壁胀形力计算。
(3) 模具结构设计胀形力:总成形力:P=P 起+P 胀=11039kN+54078kN=65.117kNNN Fp P 540782.9408.46=⨯⨯⨯==π图5-13罩盖胀形模装配图5.1.3翻孔和翻边1. 内孔翻边(hole-flanging)2. 螺纹底孔的变薄翻边3. 外缘翻边(flaring)4. 固定套翻边模设计实例图5-14翻边形式翻孔是指沿内孔周围将材料翻成侧立凸缘的冲压工序。
翻边是指沿外形曲线周围将材料翻成竖立短边的冲压工序。
注意:翻孔前必须有预冲孔!所以:一个零件有翻孔就必须有冲孔工序!翻边成形典型案例(1)固定套生产批量:中批量材料:08钢料厚:1mm工件工序:落料、拉深、冲孔、翻边工件工艺性分析:Ф40mm 处由内孔翻边成形,Ф80mm 是圆筒形拉深件,可一次拉深成形。
工序安排为落料→拉深→预冲孔→翻边。
固定套零件图(2)防尘盖生产批量:大批量材料:10钢料厚:0.3mm防尘盖工件简图工艺性分析:该工件需内孔翻边和浅拉深起伏因为该工件是轴对称工件,材料厚度仅为0.3mm,冲裁性能较好。
为减少工序数,可采用复合模一次压制成形。
一次压制成形的特点是首先进行冲孔,再翻边成形,最后落料。
(1) 内孔翻边的变形特点及变形系数变形特点----坯料受切向和径向拉伸,接近预孔边缘变形大,易拉裂。
表示:变形程度用翻边系数K内孔翻边表5-4各种材料的翻边系数极限翻边系数:圆孔翻边时孔边不破裂所能达到的最小翻边系数称为极限翻边系数1. 内孔翻边(hole-flanging)1)材料的塑性。
塑性越好的材料,其极限翻边系数越小2) 孔的边缘状况。
孔的表面质量越好,极限翻边系数越小3) 材料的相对厚度。
相对厚度越小,极限翻边系数越小4) 凸模的形状。
球形、抛物面形、锥形凸模极限翻边系数比平底凸模小2. 螺纹底孔的变薄翻边图5-15小孔翻边模翻边预冲孔直径:翻边孔外径:翻边高度:图5-16外缘翻边外凸外缘翻边变形程度:内凹外缘翻边变形程度:沿毛坯的曲边,使材料的拉伸或压缩,形成高度不大的竖边。
分类---(1)外凸外缘翻边(相当于拉深的一小部分):属压缩类翻边,近似于局部浅拉深,易起皱。
(2)内凹外缘翻边(相当于翻孔的一小部分):属伸长类翻边,近似于局部孔翻边,易开裂。
表5-5外缘翻边允许的极限变形程度表5-5外缘翻边允许的极限变形程度4. 固定套翻边模设计实例(1) 工件工艺性分析(2) 固定套翻边件工艺计算1) 平板毛坯内孔翻边时预孔直径及翻边高度在内孔翻边工艺计算中有两方面内容,一是根据翻边零件的尺寸,计算毛坯预孔的尺寸d;二是根据允许的极限翻边系数,校核一次翻边可能达到的翻边高度H(如图5-19所示)。
工艺计算与翻边力(1)平板毛坯内孔翻边时预孔直径及翻边高度内孔的翻边极限高度:t r K D H 72.043.0)1(2min max ++-=⎥⎦⎤⎢⎣⎡+⎪⎭⎫ ⎝⎛+-=h t r D d 2210πt r d D H 72.043.020++-=(2)在拉深件的底部冲孔翻边允许的翻边高度:拉深高度:预孔直径:式中D —翻边直径;r —翻边件半径;t —材料厚度。
0(1)0.57()22D t h K r =-++h t r D d D K d 2)2(14.1000-++==或r h H h +-='2) 计算翻边系数3) 计算翻边力由附录1查得σs =200MPa (3) 翻边模(planging die )结构设计kNkN t d D P s 628.42201)3.3239(1.1)(1.10=⨯⨯-⨯=-=πσπ1)计算预孔尺寸D =39mm ,H =4.5mmD 1=D +2r +t =39+2×1+1=42mm h =H -r -t =4.5-1-1=2.5mmmm h t r D d 3.325.22211422210=⎥⎦⎤⎢⎣⎡⨯+⎪⎭⎫ ⎝⎛+-=⎥⎦⎤⎢⎣⎡+⎪⎭⎫ ⎝⎛+-=ππ(3)翻边模结构设计图5-20翻边凸模结构形式4. 固定套翻边模设计实例翻边模1—卸料螺钉2—顶杆3、16—螺钉4—下模座5、11—销钉6—翻边凸模固定板7—翻边凸模8—托料板9—定位钉10—翻边凹模12—上模座13—打件器14—模柄15—打料杆17—导套18—导柱5.1.4缩口1.缩口变形程度2.缩口工艺计算3.气瓶缩口模设计示例缩口:将预先拉深好的圆筒或管状坯料,通过缩口模将其口部缩小的一种成形工艺。
工件名称:气瓶生产批量:中批量材料:08钢料厚:1mm气瓶零件图●缩口成形的特点缩口属于压缩类成形工序,缩口端材料在凹模的压力下向凹模滑动,直径缩小,壁厚和高度增加。
在缩口时,缩口端承受切向压力,筒壁坯料承受全部缩口压力而易于失稳起皱,所以防止失稳是缩口工艺的主要问题。
1.缩口变形程度表5-6各种材料的缩口系数m 缩口系数:Ddm=多次缩口时,首次缩口系数:以后各次缩口系数:均mm9.01=均m mn)10.105.1(-=1)缩口坯料尺寸。
表5-7缩口坯料计算公式2)缩口所需的压力。
图5-22缩口模结构无支承时:有支承时:P133式5-22⎥⎦⎤⎢⎣⎡+-=ααμσπcos 1)1)(1(1.10ctg D d Dt k P b(1) 工件工艺分析(2)工艺计算1)计算缩口系数。
2)计算缩口前毛坯高度。
3)计算缩口力。
图5-23气瓶零件图71.0==Ddm(3)缩口模结构设计图5-24气瓶缩口模装配图。