workinstructiontemplate作业指导书模板英文版
工作说明书 英文

Job Instruction ManualIntroductionThe purpose of this manual is to provide a comprehensive guide and instructions for performing tasks and responsibilities associated with the job. It aims to ensure consistency, efficiency, and standardization in job performance. It is essential for employees to follow this manual to carry out their duties effectively and efficiently.Job DescriptionThe job entails fulfilling a set of responsibilities and tasks assigned to the individual. The following is a brief description of the job:Job Title: [Specify job title] Department: [Specify department] Reporting to: [Specify job position] Working Hours: [Specify working hours]Duties and ResponsibilitiesThe following are the primary duties and responsibilities associated with the job. The employee should follow these guidelines to execute their tasks successfully:1.Task 1: [Provide a detailed description of the task, including anyspecific instructions or procedures that need to be followed]2.Task 2: [Provide a detailed description of the task, including anyspecific instructions or procedures that need to be followed]3.Task 3: [Provide a detailed description of the task, including anyspecific instructions or procedures that need to be followed]4.Task 4: [Provide a detailed description of the task, including anyspecific instructions or procedures that need to be followed]5.Task 5: [Provide a detailed description of the task, including anyspecific instructions or procedures that need to be followed]Standard Operating Procedures (SOPs)To ensure consistency and quality in job performance, the following standard operating procedures should be adhered to:1.Procedure 1: [Provide a step-by-step description of the procedure,including any specific guidelines or precautions to be taken]2.Procedure 3: [Provide a step-by-step description of the procedure,including any specific guidelines or precautions to be taken]3.Procedure 3: [Provide a step-by-step description of the procedure,including any specific guidelines or precautions to be taken]Safety GuidelinesTo ensure a safe work environment and prevent accidents or injuries, employees must adhere to the following safety guidelines:1.General Safety Guidelines:–Wear appropriate safety gear as required by the task.–Follow proper ergonomics to avoid strain or injury.–Keep workstations clean and organized to minimize hazards.2.Specific Safety Guidelines:–[Specify any task-specific safety guidelines]Communication ChannelsEffective communication within the organization is crucial for the smooth operation of tasks. The following communication channels should be utilized:1.Upward Communication: Report any issues, concerns, orsuggestions to the immediate supervisor or relevant authority.teral Communication: Collaborate and share information withcolleagues and peers to ensure efficient workflow.3.Downward Communication: Follow instructions and guidanceprovided by superiors.Performance EvaluationTo assess job performance, regular performance evaluations will be conducted. The evaluation will be based on the following criteria:1.Task Completion: Evaluate the completion of assigned tasks withinthe given timeframe.2.Accuracy: Assess the accuracy and quality of work performed.3.Productivity: Evaluate the employee’s productivity and ability tomeet deadlines.4.Adherence to Procedures: Assess the employee’s adherence tostandard operating procedures and guidelines.ConclusionThis Job Instruction Manual is intended to provide clear instructions and guidelines for effectively performing the job responsibilities. It is essential foremployees to familiarize themselves with the manual and adhere to the instructions provided. Regular consultation of this manual is encouraged to ensure consistency and standardization in job performance.。
工作说明书英文版word
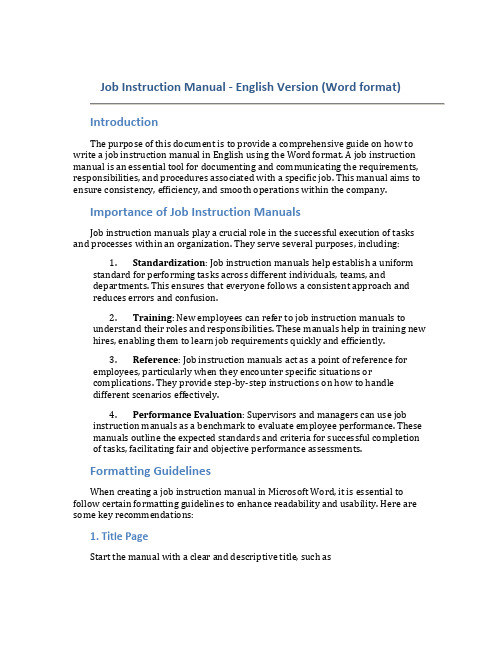
Job Instruction Manual - English Version (Word format)IntroductionThe purpose of this document is to provide a comprehensive guide on how to write a job instruction manual in English using the Word format. A job instruction manual is an essential tool for documenting and communicating the requirements, responsibilities, and procedures associated with a specific job. This manual aims to ensure consistency, efficiency, and smooth operations within the company.Importance of Job Instruction ManualsJob instruction manuals play a crucial role in the successful execution of tasks and processes within an organization. They serve several purposes, including:1.Standardization: Job instruction manuals help establish a uniformstandard for performing tasks across different individuals, teams, anddepartments. This ensures that everyone follows a consistent approach andreduces errors and confusion.2.Training: New employees can refer to job instruction manuals tounderstand their roles and responsibilities. These manuals help in training new hires, enabling them to learn job requirements quickly and efficiently.3.Reference: Job instruction manuals act as a point of reference foremployees, particularly when they encounter specific situations orcomplications. They provide step-by-step instructions on how to handledifferent scenarios effectively.4.Performance Evaluation: Supervisors and managers can use jobinstruction manuals as a benchmark to evaluate employee performance. These manuals outline the expected standards and criteria for successful completion of tasks, facilitating fair and objective performance assessments.Formatting GuidelinesWhen creating a job instruction manual in Microsoft Word, it is essential to follow certain formatting guidelines to enhance readability and usability. Here are some key recommendations:1. Title PageStart the manual with a clear and descriptive title, such as。
作业指导书(英文版)

Procedure :combine finished battery Procedure :encase battery into the PVC bProcedure :Heat-shrink the PVC bag Procedure :Stick the label Procedure:Combine the batteryPrepared by:Guan Xiao Jin Date:2007-08-23Approved by:Hu Zhong Bo Date:2007-08-231.According to the requirements of production , use the glass tape to cover the spot-weldedconnection nickel tab on the top .e the insulation tape to cover the spot-welded connection nickel tab both on the top andthe bottom .Check the battery carry and pass it to the next procedure .Procedure :stick glass tape and insulation tape 3.The insulation should not exceed the edge , distortion is not acceptable.Operation method:1.Encase the battery into the PVC bag according to the direction of the lead wire .2.Orient the exposed part by hand to keep the consistency .3.Pass the battery which has been encased into thePVC bag to the next procedure .H-AA1500J 3.6V PACKING METHOD1.Initialize the heat-blow equipment ;2.After the temperature rises , heat-shrink one batterand decide the time according to its heat-shrink effect .3.During heat-shrink process , the wire should beprevented from being damaged , and the batteries arenot allowed to be stacked .Operation method:Operation method:Operation method:1.Hold the battery with the left hand , and keep the label with the right hand .2.Wrap the label on to the right place according to the sample .3.Check it after finishing wrapping the label , it should be smoothly wrapped , no crinkle or floating is acceptable .insulation tape pvc paglabelheat-blow equipmentProcedure 1Procedure 4Procedure 5Procedure 6STEP 7glass tapeProcedure 2Procedure 3:encase battery into the PVC bag。
oqc作业指导书英文版模板

oqc作业指导书英文版模板OQC Work Instruction Template1. Purpose:The purpose of this work instruction is to provide guidelines and instructions for conducting the Outgoing Quality Control (OQC) process. OQC helps ensure that finished products meet the required quality standards before they are shipped to customers.2. Scope:This work instruction applies to all employees involved in the OQC process, including quality control inspectors, production personnel, and supervisors.3. Responsibilities:- Quality Control Inspectors:- Inspect finished products according to the specified quality standards.- Identify and report any deviations from the quality standards.- Record inspection results and maintain documentation.- Assist in identifying the root cause of any quality issues.- Production Personnel:- Ensure that finished products are ready for OQC inspection.- Provide necessary documentation, such as production records and test reports.- Alert quality control inspectors if there are any known issues with the product.- Supervisors:- Ensure that all necessary resources and equipment are available for OQC inspection.- Oversee the OQC process and provide support to quality control inspectors.- Review and analyze OQC inspection results to identify trends or recurring issues.- Take corrective actions to address any quality issues identified in OQC.4. Procedure:- Personnel involved in the OQC process should receive appropriate training and be familiar with the specified quality standards.- Quality control inspectors should follow these steps during the OQC process:1. Receive finished products for inspection.2. Review the specified quality standards and inspection criteria.3. Inspect the product for any visible defects, such as scratches, dents, or discoloration.4. Use appropriate measuring equipment to check dimensions, tolerances, and functionality.5. Conduct any required tests, such as electrical or mechanical performance testing.6. Record inspection results accurately and legibly.7. Identify any non-conforming products and segregate them for further analysis and disposition.8. Report any deviations from the quality standards to the supervisor.- Supervisors should review the inspection results and take appropriate actions based on the findings: - If there are non-conforming products, investigate the root cause and take corrective actions.- Communicate with production personnel to address any issues identified during the inspection.- Regularly review OQC inspection data to identify trends or patterns that require attention.5. Records:- All OQC inspection results should be recorded and maintained as per the company's record-keeping requirements.- Records should include the date, product details, inspection results, and any actions taken based on the inspection findings.Note: This OQC Work Instruction Template is a general guideline and should be customized to fit the specific requirements of the organization and its products.。
WORK INSTRUCTION 工作指导书

Page 1 of 2FORWARD—DELETE AFTER READING[Use of this format is mandatory for all QMS documentation to comply with the requirements of ISO 9001. Work instructions shall be prepared in instances where the lack of such directions may adversely affect the quality of a product. Work Instructions shall be prepared as a procedure containing the following sections when the instructions will reasonably conform to the format. Some sections may be designated as "not applicable" in a particular instruction. Employee directions or instructions that do not reasonably conform to this format, such as drawings, forms, or checklists shall be identified and controlled as Work Instructions.[This document template is prepared in two sections. This forward is designed for the document author’s use. It provides general information about using the template. The forward section must be deleted from the document and then the remainder of the template can be used. The body of the document contains section headings and writing instructions , which are enclosed in brackets [ ], as follows: [This is an instruction on what should be written.] DELETE ALL BRACKETED TEXT AND REPLACE WITH WORK INSTRUCTION SPECIFIC DETAIL.[Fill out the title block on page 1, along with the header on page 2, which contains the document number and title. The “Effective Date” is the earliest possible date after a pproval the document will be effective. If this date occurs before final approval, the release date will supersede the effective date as the date of implementation.]1. PURPOSE[Short statement of the purpose of the Work Instruction]2. SCOPE[Short statement of the scope of the Work Instruction.]3. DEFINITIONSGE-XXXXX-A [Fill in Document Title] Page 2 of 2 [This paragraph is optional. Unless otherwise defined, the quality management terms that are used in this procedure will be as defined in ISO 8402. When definitions are included, they should be assigned sequential lower-case letters, beginning with a.]4. REFERENCES[List and identify documents which are either referenced in the body of the procedure or employ the subject procedure as a reference. Also, record forms that are applicable to the implementation of the procedure.]5. TOOLS and EQUIPMENT[List specific/special tools, equipment and materials required to perform the instruction. The list shall be detailed (e.g. serial numbers, lot date code, etc.) to the degree necessary to perform the instructions in a satisfactory manner.]6. INSTRUCTIONS[In a step-by-step sequence, identify each action required to perform the task. For each step description, the following guidelines shall be considered:1. Identify special working conditions2. Identify requirements/specifications such as pressure, temperature, voltage settings, etc.3. Identify accept/reject criteria4. Identify data records and/or forms that must be completed.5. Include aids that will help the user such as flow diagrams, checklists, diagrams, schematics, tables, etc.]7. QUALITY RECORDS[This section is used to identify quality records. Quality Records are the objective evidence of the fulfillment of project requirements for quality and the effectiveness of the operation the Project Quality System.[Not all documents created as a result of carrying out a process are quality records. You should identify those quality records that result from key steps in the process.[It is recommended that the owner and location sections contain information that will generally guide employees to the record but not be so detailed that an office reorganization or relocation will necessitate the update of this table.[The Record Media column refers to the official record and whether it is in electronic or hard copy format. Generally, the official file copy is either the electronic copy or the hard copy but not both. [NPG 1441.1, the NASA Records Retention Schedule, is the official procedure governing the retention, retirement, and destruction of Agency records and should be used to determine schedule, retention, and disposition.]。
ENG-7.5-010 Creating work Instruction operation guide 制作作业指导书的操作指导 中英双语

标题:制作作业指导书的操作指导Page 1 of 14Revision History更改记录REV 版本CHANGE更改内容WRITTEN编写DA TE日期A B C D ENewAdd Training; Update record and Limited timeUpdate AllUpdate AllUpdate document format/Revise 4.7/6.1.3/6.1.4、6.2.6-6.2.8/6.6.3/6.6.4/6.6.5/6.5/6.6.6/6.7/part7/part 10January 26,2006February 1,2007Aug.17, 2007June 10, 2008Aug,14.2013Check & Approval检查和批准栏SIGNATURE DATE SIGNA TURE DA TE 签名日期签名日期Originator Program/Project起案者 xxx 2013-8-14 项目部 N/A N/A AQuality Materials质量部 xxx 2013-8-20 物料部 N/A N/A AIT/IS HR 资讯部 N/A N/A 人事部 N/A N/A A Ops. Eng.运作部 xxx 2013-8-20 工程部 xxx 2013-8-21 AFacility Logistics厂务 N/A N/A 物流部 N/A N/A A BE Finance卓越运营部 N/A N/A 财务部 N/A N/A___A GM总经理 N/A N/A AChecked by DCC: Date:文控审核: xxx A 日期: 2013-8-21 A标题:制作作业指导书的操作指导Page 2 of 141.Purpose目的To establish the appropriate flow of Work Instruction creation and maintenance of Flextronics (Nanjing).制定公司作业指导书的建立和维护的流程2. Scope 范围This procedure is applicable to all Work Instruction and Loading list creation of xxx适用于xxx所有项目作业指导书和装料清单的制作.3. Definitions 定义WI – Work Instruction作业指导书BOM – Bill of materialLoading list –装料清单TQC – Total Quality Control 全面质量控制4. Responsibility 职责4.1 Process Engineer –工艺工程师4.1.1 All Work Instruction owner expect for Test, Rework, OBA station and Loading List.除了测试,维修, 质量开箱检查和装料清单以外所有作业指导的主导者.4.1.2 Define process flow chart.定义产品的工艺流程.4.1.3 All the process parameters owner (eg: silk-screen; reflow oven and wave soldering parameters and so on).所有工艺参数的主导者( 例如:印刷机,回流炉和波峰焊等的参数等).4.1.4 Process parameters optimization owner所有工艺参数优化的主导者.4.1.5 Training operators to follow WI requirements培训作业员按照作业指导书进行操作.4.2 Test Engineer –测试工程师4.2.1 Work Instruction owner of test station.所有测试工位作业指导书的主导者.4.2.2 Training operators to follow WI requirements培训作业员按照作业指导书进行操作.4.3 Rework Engineer –维修工程师4.3.1 Work Instruction owner of rework station.所有维修工位作业指导书的主导者.4.3.2 Training operators to follow WI requirements培训作业员按照作业指导书进行操作.4.4 Quality Engineer –质量工程师4.4.1 Work Instruction owner of related quality control station (such as OBA, solder paste thickness measure and so on.)有关质量控制工位 (例如:OBA,锡膏厚度测量等) 作业指导书的主导者.4.4.2 Verify whether the Work Instruction suitable for production before approval.在作业指导书受控批准前确认作业指导书是否适用于生产.4.4.3 Supervise operators to follow WI requirements监督作业员按照作业指导书的要求进行操作.标题:制作作业指导书的操作指导Page 3 of 144.5 Equipment Engineer –设备工程师4.5.1 Loading List owner of machine.所有机器装料清单的主导者.4.5.2 Training operators to follow Loading List requirements培训作业员按照装料清单进行操作.4.6 Production department –生产部4.6.1 Perform job with the Work Instruction and consult with interrelated engineer for any suggestion and improvement.生产操作人员要严格按照作业指导书进行工作. 如有好的建议可与相关的工程师联系进行改善.4.6.2 Ensure operators passed the station training before their on line operate independently生产操作人员在进行独立操作前必须通过相关岗位培训.4.6.3 Use the correct WI according production plan and well keep all the controlled WI from DCC根据生产安排使用正确的作业指导并妥善保管好文控发放的作业指导书.4.6.4 WI preserve place must easy to get and see for operations when line production.产线生产时对应作业指导书保存处需在生产操作人员便于读取范围内.4.6.5 Transportation box or rack required in WI was numbering and managed by Production Dep. Appendix 4:Transportation numbering作业指导书里要求的周转箱, 货架等由产线统一编号管理. 附件4: 周转箱的编号4.7 DCC–文控中心Check WI& Loading list follow FIFO and make them release with 48 hours and call back the old revision on time.根据接收文件时间的先后顺序审查作业指导书和装料清单并使其在接收后的48小时内发行,及时的回收旧的文件版本.5. Process Flow Chart 流程图Work instruction Creating Process标题:制作作业指导书的操作指导Page 4 of 146. Procedure程序6.1 The standard format of the Work Instruction in Flex Factory as appendix 2 below.伟创力工厂里作业指导书的标准格式如下面附件2所示.6.1.1 All Work Instruction must include the TQC, Work content and Verify sections. This is on the left hand side of themethod sheet. The TQC is Represent by a Red triangle while the Work content is represented by a Yellow square and finally the Blue circle represents Verify.所有的工作指导书都必须包括三个部分,依次是: 质量检查, 操作内容和校对.这三个部分应写在工作指导书的左手边. 质量检查部分用红色三角形表示, 操作内容部分用黄色四边形表示, 校对部分用蓝色圆形表示.6.1.2 The TQC information allows the Operator of the station to validate product from the previous work content / stationand the part. As a guide, it is to highlight inspection points for operate problems, frequent defects etc.标题:制作作业指导书的操作指导Page 5 of 14质量检查是要求该工位的操作员检查来自上工位的操作和本工位所用到的物料是否有缺陷.这部分的检查主要是针对操作问题和经常出现的缺陷.6.1.3 The Work Content contains a block that details direct materials used in this workstation (use graphics as possible).The Work Content also details information on the sequence of work activities. The tools, fixtures and process parameter should be included in the work content. For example, the hands solder iron, soldering fixture and the soldering temperature. And follow FEHSP-4.4.6-12 Personal Protection Equipment Management Procedure to define the PPE for each station.操作内容包括该工位上所要用到的直接物料(尽可能使用表格), 工作内容要按照实际操作的顺序编写。
作业指导书标准范文英语(3篇精选)

作业指导书标准范文英语(3篇精选)作业指导书标准范文英语(篇1)1. IntroductionThis Standard Operating Procedure (SOP) outlines the detailed steps for completing a specific task within our organization. It ensures consistency, safety, and compliance with industry standards. This document is to be followed by all personnel involved in the task.2. Job OverviewProvide a brief overview of the task, including its purpose, importance, and the expected outcome. Identify the key objectives and the overall workflow.3. Tools and MaterialsList all the necessary tools, equipment, and materials required to complete the task. Specify the type, model, and any specific requirements for each item. Ensure that all necessary safety certifications and approvals are met.4. Job StepsProvide a detailed, step-by-step guide to completing the task. Each step should be clearly written and easy to understand. Include any specific techniques, procedures, or measurements required. Reference any diagrams, sketches, or images that may aid in understanding.5. Safety PrecautionsOutline all the necessary safety measures to be taken during the task. This should include personal protective equipment, environmental controls, and any specific safety procedures or protocols. Emphasize the importance of adhering to these measures to prevent accidents or injuries.6. Quality StandardsDefine the expected quality outcomes for the task. Include any specific metrics, tolerances, or performance criteria. Identify any quality control measures or testing procedures that will be used to ensure compliance.7. Common Issues and TroubleshootingIdentify common problems or issues that may arise during the task. For each issue, provide a troubleshooting guide with steps to resolve the problem. Include any specific tools or techniques that may be required.8. AppendicesInclude any additional information or references that may be useful for completing the task. This could include technical specifications, drawings, diagrams, safety data sheets, or any other relevant documents.Remember to review and update this SOP periodically to ensure it remains accurate and compliant with industry standards.作业指导书标准范文英语(篇2)1. Purpose and ScopeThis Standard Operating Procedure (SOP) outlines the specific steps and guidelines for performing a particular task within our organization. It aims to ensure consistency, safety, and quality in the execution of the task. The scope of this SOP covers all necessary steps, tools, materials, and safety measures required for the successful completion of the task.2. Safety PrecautionsBefore commencing the task, it is crucial to ensure the safety of all personnel involved. Appropriate safety gear, such as gloves, eye protection, and safety shoes, must be worn at all times. Ensure the workspace is clean, organized, and free of any hazards. Familiarize yourself with the safety measures outlined in the relevant safety data sheets and follow them strictly.3. Tools and MaterialsGather all the necessary tools and materials required for the task. Verify their condition and ensure they are suitable for the job. Keep them organized and easily accessible throughout the task. Refer to the tool and material list provided in the appendix for a detailed inventory.4. Step-by-Step GuideFollow the step-by-step guide provided below to ensure the task is completed accurately and efficiently. Read each step carefully and perform the task in the order provided. Do not skip any steps or deviate from the guidelines without explicit authorization.Step 1: [Description of step 1]Step 2: [Description of step 2]Step 3: [Description of step 3]...Final Step: [Description of the final step]5. TroubleshootingIn case of any issues or problems encountered during the task, refer to the troubleshooting section below. It provides solutions and workarounds for common problems that may arise. If the issue persists, contact the designated support team or supervisor for assistance.Issue 1: [Description of issue 1]Solution: [Description of solution for issue 1]Issue 2: [Description of issue2]Solution: [Description of solution for issue 2]...6. Quality ControlQuality is paramount in our organization. Therefore, itis essential to perform quality checks throughout the task to ensure the desired outcomes are achieved. Follow the quality control measures outlined below and record the results for future reference.Quality Check 1: [Description of quality check 1]Quality Check 2: [Description of quality check 2]...7. Post-Task ActionsUpon completion of the task, it is crucial to perform certain post-task actions to ensure the workspace is left in a safe and organized condition. This includes cleaning up any debris, storing tools and materials properly, and verifying that all safety measures are in place.8. ReferencesFor further information or additional guidance, refer to the following references:[Reference 1: Title or Description][Reference 2: Title or Description]...Appendices:Tool and Material ListSafety Data SheetsRelevant Technical DocumentsRemember to adhere strictly to this SOP to ensure the safety, quality, and efficiency of the task. Regular updates and reviews are recommended to reflect any changes or improvements.作业指导书标准范文英语(篇3)1. Assignment ObjectivesThe primary objective of this assignment is to achieve [specific goal or objectives of the assignment]. This SOPoutlines the necessary steps, tools, and precautions to ensure a smooth and safe completion of the task.2. Tool PreparationBefore starting the assignment, ensure that you have all the necessary tools and materials prepared. This includes but is not limited to:[List of tools and materials required for the assignment]It is essential to have these tools ready and functioning properly to avoid any delays or issues during the assignment.3. Step-by-Step GuideFollow the step-by-step guide below to complete the assignment effectively:Step 1: [Description of Step 1]Step 2: [Description of Step 2]...Step N: [Description of the final step]Refer to the diagrams, screenshots, or additional resources provided for further clarification if needed.4. Safety PrecautionsWhile performing the assignment, it is crucial to prioritize safety. Therefore, adhere to the following safety guidelines:Wear protective gear as recommended.Handle tools and materials with caution to avoid accidents.Follow the correct procedures and do not take shortcuts that may compromise safety.Immediately stop the assignment and seek assistance if any unsafe conditions are observed.5. Assignment Check Upon completion of the assignment, conduct a thorough check to ensure the desired results are achieved. Verify that all steps have been followed correctly, and there are no errors or omissions. It is recommended to refer to the assignment rubric or criteria for guidance.6. Problem HandlingIf any issues or challenges arise during the assignment, take the following steps to address them:Refer to the troubleshooting section or relevant resources for solutions.Seek assistance from classmates, mentors, or teachers if needed.Be proactive in seeking help and communicating any issues to ensure timely resolution.7. Assignment SubmissionOnce you have completed the assignment, follow the submission guidelines provided:Ensure all work is saved and backed up.Submit the assignment through the designated platform or system.Adhere to the submission deadline and any additional instructions provided.By following this SOP, you will be able to completethe assignment effectively, safely, and in a timely manner. Remember to refer to the resources and additional guidance provided throughout the assignment process.。
PFMEA作业指导书(中英文)

PFMEA作业指导书1 PURPOSE(目的)The purpose of this work instruction is to provide a method for continuous improvement through the use of PFMEAs.此作业指导书的目的是为运用制程失效模式及效果分析达到持续改善目的提供方法。
2 SCOUPE(范围)This work instruction applies to any manufacturing process that has a customer requirement for failure mode effect analysis or any process at FLEX (Doumen) where management requires a PFMEA.适用于客户要求或管理要求而需要做失效模式及效果分析的所有制程。
3 DEFINITIONS(定义)3.1 PFMEA: Process Failure Mode and Effect Analysis. It should describe all thepotential failure modes which may occur in process and their corresponding failure effects; evaluate and rank the severity, occurrence and detection of the failures. It should also describe the current control method, recommend corrective action, person responsible responsibility and due date.PFMEA--制程失效模式及效果分析。
- 1、下载文档前请自行甄别文档内容的完整性,平台不提供额外的编辑、内容补充、找答案等附加服务。
- 2、"仅部分预览"的文档,不可在线预览部分如存在完整性等问题,可反馈申请退款(可完整预览的文档不适用该条件!)。
- 3、如文档侵犯您的权益,请联系客服反馈,我们会尽快为您处理(人工客服工作时间:9:00-18:30)。
TITLE of ELEMENT
Revision: A Page 1 of 2
WORK INSTRUCTION
01-01-01
1.0 PURPOSE
1.1(What is the reason for writing this work instruction) Start with the following statement:
purpose of this document is to provide instructions for - - - - - - - - .”
1.2Be as specific as you need to be to define the purpose of the document.
2.0 SCOPE
2.1(Define the area or process that this instruction applies to)
3.0 RECORDS
3.1(Indicate specific type of records to be maintained and where they will be maintained)
4.0 ASSOCIATED DOCUMENTS
4.1(Reference upward to the procedures that the work instruction is controlled by and
reference forms by control number used to create records. Also, reference other documents, standards or information that are relevant.)
5.0 DEFINITIONS
5.1(Define any terms and phrases that might be unique to this instruction or to this particular
industry)
6.0 RESPONSIBILITY
6.1(List department(s) or functions responsible for maintaining these instructions)
7.0 TOOLS, GAGES, FIXTURES
7.1(List all unique tools required to perform tasks as indicated in this work instruction)
8.0 SAFETY REQUIREMENTS
8.1(List all necessary safety precautions that employees must comply with and all safety
equipment that must be used while following the operations specified in this work instruction)
9.0 INSTRUCTIONS
9.1(List all steps to be taken to complete the scope of this work instruction, in the exact
sequence necessary. Work instructions may be in the form of flow charts, bullet
instructions, text, photos, digitized images, numbered instructions or any combination of all, as long as the instructions are clear, crisp and do the job as intended)。