高炉炼铁工艺关键技术介绍
烧结及高炉炼铁基本原理及工艺

降低了煤气还原能力,影响还原速度.
CaCO3在低温区分解放出CO2进入煤气,降低了CO的 浓度,冲淡了还原气氛
在高温区分解出的CO2与焦炭发生反应, CO2+C焦=2CO 是吸热反应,而且直接消耗焦 炭,使焦比升高.
13
二、高炉还原过程
高炉冶炼用CO,H2和固体碳作还原剂. 氧化物的还原顺序: 高炉冶炼条件下,各种氧化物由易到难的还原 顺序. CuO→PbO→FeO→MnO→SiO2 →Al2O3→MgO→CaO
三元碱度:R3=(CaO+MgO)/SiO2,一般为1.3左 右
-Q -Q -Q -Q -Q
2.碳水反应的影响:
当温度大于1000℃时:
H2O汽 + C = H2 + CO
-Q
用H2还原铁氧化物在高温区时:
FeO+H2 = Fe+H2O
+ H2O+C = H2+CO
FeO+C = Fe+CO
在低温区时,用H2还原铁氧化物的产物与CO作用
FeO+H2 = Fe+H2O + H2O+CO = H2+CO2
0 400 500 600 700 800 900 1000 1200 0C
度随温度升高而降低,即温度升高,
CO的利用率提高,是吸热反应,
2.温度对反应的影响: 曲线3是FeO+CO=Fe+CO2的平衡 气相成分线,向上倾斜,与曲线2 正好相反,是放热反应,升温对反
应不利.
曲线4是Fe3O4+4CO=Fe+4CO2的 平衡气相成分线,向上倾斜,它在
%CO
Fe
高炉炼铁技术简介
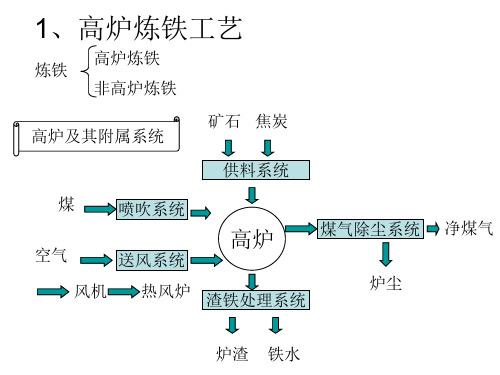
烧结 工艺 流程
精矿、粉矿 (0~10mm)
石灰石、白云石 (80~0mm)
碎焦、无烟煤 (25~0mm)
破碎
>3mm
• 炉渣中氧化物的种类:碱性氧化物、酸性氧化物 和中性氧化物。以碱性氧化物为主的炉渣称碱性 炉渣;以酸性氧化物为主的炉渣称酸性炉渣。
• 炉渣的碱度(R):炉渣中碱性氧化物和酸性氧化 物的质量百分数之比表示炉渣碱度:
• 高炉炉渣碱度一般表示式:R=w(CaO)/w (SiO2)
• 炉渣的碱度根据高炉原料和冶炼产品的不同,一 般在1.0~1.25之间。
消耗的(干)焦炭量(焦比一定的情况 下)
高炉每天消耗的焦炭量 I=
高炉的有效容积
• 生铁合格率:生铁化学成分符合国家标准的总量 占生铁总量的指标。
• 休风率:高炉休风时间(不包括计划大、中、小 修)占日历工作时间的百分数。
规定的日历作业时间=日历时间-计划大中修及
封炉时间
休风率=
高炉休风时间 规定的日历作业时间 ×100%
高炉炉渣与脱硫
• 高炉炉渣是铁矿石中的脉石和焦炭(燃料)中 的灰分等与熔剂相互作用生成低熔点的化 合物,形成非金属的液相。
– 高炉炉渣的成分 – 高炉炉渣作用 – 成渣过程 – 生铁去硫
• 高炉炉渣的来源:矿石中的脉石、焦炭(燃料)中 的灰分、熔剂中的氧化物、被侵蚀的炉衬等。
• 高炉炉渣的成分:氧化物为主,且含量最多的是 SiO2、CaO、Al2O3、MgO。
② 物理性能 包括机械强度和粒度组成等。高炉要求烧结矿机械 强度高,粉末少,粒度均匀。 烧结矿粒度小于5mm的称之为粉末。粉末含量对高 炉料柱透气性影响很大。粉末含量高,高炉透气性差, 导致炉况不顺,可能引起崩料或悬料。 反应机械强度的指标为:转鼓指数、抗磨指数、筛 分指数。 目前武钢烧结矿的转鼓强度大约在79%~80%左右。
高炉炼铁基本原理与工艺
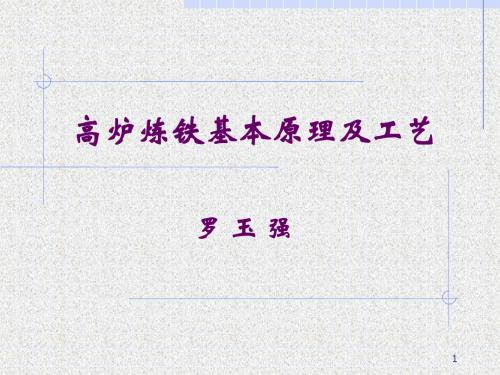
15
2.铁的间接还原与直接还原
(1)间接还原:用CO、H2为还原剂还原铁的氧化物,产物CO2、 H2O的还原反应。 特点:放热反应 反应可逆 (2)直接还原:用C作为还原剂,最终气体产物为CO的还原反应。 特点:强吸热反应 反应不可逆 (3)直接、间接还原区域划分:取决于焦碳的反应性 低温区 <800℃基本为间接还原 中温区 800~1100℃共存 高温区 > 1100℃全部为直接还原 (4)用直接还原度rd、间接还原度ri来衡量高炉C素利用好坏,评价 焦比。
9
2. (助)熔剂
(1)作用: 形成低熔点易流动的炉渣、脱S(碱性熔剂) (2)种类:
使用条件及作用
碱性
酸性
铁矿中脉石为酸性氧化物,包括:石灰石、白云石、石灰
铁矿中脉石为碱性氧化物,主要为:SiO2(只在炉况失常 时使用——(Al2O3)≥18%或排碱时) 高Al熔剂,主要为:含Al2O3高的铁矿(只在降低炉渣流动 性时使用)
24
五、高炉强化冶炼手段与方法
1.大风量 风量增加,炉内传热效果下降,ri降低,K 增加。风量应与还原性相适应 2.高风温 风温增加,传热推动力增加,但利用风温 的同时K势必降低,透气性将下降 3.富氧 富氧将使炉缸温度增加,但煤气总量下降, 不利于全厂能量平衡;富氧达到的效果与提高 风温相比,成本提高10倍。
10
中性
3 焦碳
①主要作用:
作为高炉热量主要来源的60~80%,其它热风提供 提供还原剂C、CO 料柱骨架,保证透气性、透液性
②质量要求:
含炭量:C↑ 灰份:10%左右,灰分低可使渣量↓ 含S量:<0.6% 生铁中[S]80%±来源于焦碳 强 度:M40 (kangsuiqd)、M10 (lmqd) 粒度组成:均匀 60mm 左右的 >80% ,大于 80mm 的 <10% ,大于 80mm的<10% 成分稳定(特指水分): 一般采用干熄焦 焦碳反应性: C+CO2=2CO开始反应的高低快慢→影响间接还原区的 范围从而影响焦比
高炉炼铁工艺技术标准

高炉炼铁工艺技术标准高炉炼铁是一项复杂的工艺过程,需要严格遵守一系列的技术标准来保证炼铁质量和生产效率。
下面将介绍一些关键的高炉炼铁工艺技术标准。
首先,高炉的炉料配比是一项非常重要的技术标准。
炉料主要包括铁矿石、焦炭和熔剂等。
合理的炉料配比可以保证炉内的物料成分符合要求,达到理想的还原效果。
配料时需要考虑铁矿石的品质、矿石的粒度、焦炭的品质和灰分等因素。
此外,还需要根据高炉运行情况进行及时调整,确保炉料配比的稳定性。
其次,高炉炉温的控制是非常关键的技术标准。
高炉的炉温直接影响到铁矿石还原的速度和产量。
过高的炉温会导致炉内的矿石过度还原,从而产生大量的炉渣。
过低的炉温则会使得还原反应缓慢,影响生产效率。
因此,需要通过调整空气和燃料的供给来控制炉温,确保在合适的范围内。
此外,高炉的风量控制也是一项重要的技术标准。
风量的大小直接影响到炉内氧气的供应和燃烧的强度。
过大的风量会导致过量的氧气进入炉内,从而引起废气中氧含量过高,浪费燃料。
过小的风量则会导致缺氧现象,影响还原反应的进行。
因此,需要根据高炉的情况调整风量,保持合适的氧气供应和燃烧强度。
最后,高炉炼铁还需要严格遵守安全操作规程,确保生产过程的安全性。
操作人员应该经过专业培训,了解高炉的工作原理和操作技术。
在操作过程中,要注意加强高炉的维修和保养工作,及时处理设备故障和热态问题,确保设备的正常运行。
此外,还要定期进行安全检查,防止因设备老化和工程安全漏洞引发事故。
总之,高炉炼铁工艺技术标准包括炉料配比、炉温控制、风量控制以及安全操作等方面。
只有严格遵守这些标准,才能保证高炉的正常运行和炼铁的质量。
高炉炼铁的主要工艺流程

高炉炼铁的主要工艺流程
《高炉炼铁的主要工艺流程》
高炉是钢铁企业中用于炼铁的主要设备,其工艺流程是将铁矿石和焦炭加入高炉内,经过一系列的化学和物理反应,最终得到熔融的生铁。
下面将介绍高炉炼铁的主要工艺流程。
1. 搅拌坩埚法:将原铁矿石和焦炭按一定的比例混合,放入高炉的上部,即炉料层。
在高炉内,炉料层受到高温和高压的影响,发生一系列的物理和化学反应。
2. 燃烧:通过给炉料层加入空气或者氧气,点燃炉料层的顶部,使其燃烧。
燃烧产生的热量使炉料层内的焦炭燃烧,并提供高温条件,促进各种反应的进行。
3. 还原反应:当焦炭燃烧释放出一定量的一氧化碳时,与高炉内的铁矿石发生还原反应,使氧化铁还原为生铁。
4. 精炼:在高温下,生铁中的杂质和一些有害元素(如硫、磷等)会被氧化成气体,并通过炉顶排出。
这一过程称为精炼,是炉料中杂质清除的重要环节。
5. 收得生铁:经过一定时间的冶炼,高炉内的炉料最终产生了熔融的生铁。
生铁通过炉口排除,并进入铁水槽中,成为炼铁的产物。
通过上述简单介绍,可以看出高炉炼铁的主要工艺流程是一个
复杂的过程,包括搅拌坩埚法、燃烧、还原反应、精炼和收得生铁等环节。
这一流程不仅需要科学合理的原料比例和控制方法,还需要高炉操作者的丰富经验和技巧。
只有合理的工艺流程和专业的操作技术,才能保证高炉炼铁的顺利进行和生产出优质的生铁产品。
高炉炼铁工艺介绍

斜桥卷扬
斜桥卷扬是向 炉顶输送原燃 料的设备。由 交流变频电动 卷扬机、指令 控制器、斜料 料车组成。左 右两台料车, 将矿槽下配好 矿集中称量后 装入料车,按 高炉指令;准 确、平稳,不 间断地送入炉 顶料罐。
斜桥上料
高炉本体
高炉炉体,巍然屹立,如钢铁巨人。炉 口由密封的双料罐和流槽将炉料布入炉喉, 下部风口鼓入一千多度的富氧风和煤粉进行 燃烧,使炉料在高温高压中进行一系列热化 学变化,最后还原出生铁,分离的渣铁从铁 口定期排出。炉顶高压高温煤气经上升管、 下降管送去除尘系统处理。
高炉出铁
铁水流入铁水罐,火花飞溅。铁水罐由火车牵引送到炼钢厂炼钢。
高 炉 炼 铁 概 论
高炉炼铁工艺
高炉炼铁是以烧结、球团为原料,焦碳,煤 粉为燃料,配加溶剂,鼓入热风熔炼出铁水的工 艺。高炉是逆反应式竖炉,下降的炉料和上升的 煤气流进行传热,传质和动力的传递,使炉料熔 化、还原,进尔渣铁分离。高炉是电气化、连续 化、机械化和自动化程度非常高的大型装备。也 是钢铁企业核心装备。高炉有十大系统:上料系 统、炉体系统、渣铁处理系统、热风系统、喷煤 系统、煤气处理系统、冷却系统、余压发电系统、 除尘系统、控制系统。
高炉炼带运输来 的原料,及焦炭与 溶剂进行储存、筛 分、称量,并按高 炉设计的料批料制 进行配料。包括料 仓、震动给料器、 矿焦筛、称量漏斗 和皮带。矿焦由皮 带输送到槽下料坑 的称量矿斗。有自 动给料称量及自动 重量补偿等功能。
原料筛分
高炉炉体
高炉风口
通过高炉风口,鼓入富氧热风和喷吹煤粉,在炉内燃烧。
炉前出铁场
炉前出铁场是 对高炉定期排 放渣铁,并进 行分离的场所, 有开铁口机、 堵铁口泥炮、 铁沟和渣铁分 离的撇渣器。 使喷射的高温 渣铁溶液分离 后静静的流向 铁水包和渣沟。
高炉炼铁的主要工艺流程

高炉炼铁的主要工艺流程高炉炼铁是一种传统的冶炼工艺,通过将铁矿石、焦炭和石灰石等原料投入高炉,经过化学反应和物理过程,最终得到铁水和副产品。
下面将介绍高炉炼铁的主要工艺流程。
1. 原料准备:高炉炼铁的主要原料包括铁矿石、焦炭和石灰石。
首先,铁矿石要经过破碎、磨细的过程,使得颗粒大小适合投入高炉。
焦炭也需要经过破碎、筛分,去除杂质,以提高燃烧效率。
石灰石用于炉渣的形成,防止高炉壁被侵蚀。
2. 加料混合:将经过准备的铁矿石、焦炭和石灰石按一定比例投入到高炉的料斗中。
同时,还需要添加一定的烧结矿和再生焦,以增加炉料的活性和燃烧效率。
混合的原料进入高炉,开始炼铁过程。
3. 预热干燥:原料混合进入高炉后,从上部加入的燃烧空气通过炉体底部的风口喷吹,使混合料堆温度迅速升高。
在预热的同时,水分和挥发物被蒸发除去,使料堆达到干燥状态。
4. 还原反应:当料堆升温到一定程度时,焦炭开始燃烧,释放大量的热能,同时产生一氧化碳(CO)。
在高炉中,一氧化碳与铁矿石中的氧发生还原反应,将铁矿石中的氧还原成金属铁。
这是炼铁过程的关键步骤。
5. 炉渣形成:在还原反应过程中,石灰石与其他杂质反应生成衍生石灰,与铁矿石中的硅和磷等杂质形成炉渣。
炉渣既可以保护高炉炉壁不受侵蚀,还可以促进还原反应的进行,提高金属铁的产率。
6. 铁水收集:经过还原反应后,金属铁被熔化并沉积在高炉底部的铁水中。
在铁水收集器中,铁水与炉渣通过不同的密度分层,并通过铁水口和渣口分别排出。
铁水经过冷却和预处理后,可作为原料用于制造钢铁。
7. 副产品处理:除了铁水以外,高炉炼铁还能产生大量的副产品,如煤气、炉渣和飞灰等。
煤气作为一种重要的燃料和能源资源,可用于发电、加热和炼化等。
炉渣可以用于建筑材料的生产,而飞灰则可以通过处理和综合利用,减少环境污染。
综上所述,高炉炼铁的主要工艺流程包括原料准备、加料混合、预热干燥、还原反应、炉渣形成、铁水收集和副产品处理。
这个工艺流程经过长时间的发展和改进,已经成为一种效率高、成本低、能源利用率较高的冶炼工艺。
高炉炼铁工艺介绍

高炉炼铁工艺介绍1. 简介高炉炼铁是一种重要的冶金工艺,用于将铁矿石转化为生铁的过程。
它是钢铁工业的核心环节之一,用于生产各种钢材。
2. 高炉炼铁的基本原理高炉炼铁的基本原理是将铁矿石与焦炭等还原剂混合后,在高温下进行还原反应,将铁矿石中的氧化铁还原为金属铁。
同时,炉内的温度和化学反应条件还可以使一部分其他有害物质被除去。
3. 高炉炼铁的工艺流程3.1 高炉炉缸高炉炉缸是高炉的主要部分,通常由炉壳、炉缸和炉缸衬板组成。
炉缸衬板由耐火材料制成,以承受高温和化学侵蚀。
3.2 上料系统上料系统的主要作用是将矿石、焦炭、燃料及其他辅助材料送入高炉。
通常,这些原料需要经过破碎、筛分、称重等处理。
3.3 炉冰炉冰是指在高炉顶部装置的冷却设备,用于冷却进入高炉的热气体。
这样可以减少热能的损失,并为高炉提供所需的煤气流动动力。
3.4 高炉通气系统高炉通气系统主要包括风机和风口。
高炉顶部的风机通过送风管将空气送入高炉,从而维持高炉的氧气供应。
风口是位于炉缸底部的通气装置,用于引入煤气和空气,同时也是控制和调节高炉燃烧的关键。
3.5 高炉冷却系统高炉冷却系统主要用于冷却高炉的各个部位,包括炉缸、炉壁和炉顶。
这些部位会受到高温的侵蚀,而冷却系统可以降低温度,延长高炉使用寿命。
3.6 出铁系统出铁系统用于从高炉底部将生铁和渣铁分离出来。
通常通过出铁口将液态金属铁和渣铁分别引出,然后进一步处理。
3.7 气体处理系统高炉产生的煤气会通过气体处理系统进行处理。
其中一种常见的处理方法是将煤气用作燃料,同时采用高炉煤气洗涤的方式除去其中的尘埃和硫化物等有害物质。
4. 高炉炼铁的优缺点4.1 优点•高炉炼铁工艺稳定,适合大规模生产。
•可以利用多种铁矿石和煤炭,适应不同的原料条件。
•高炉炼铁可以同时除去一部分有害物质,对环境保护有一定的效果。
4.2 缺点•高炉炼铁能耗较高,对资源消耗较大。
•高炉炼铁产生的煤气和废渣需要进一步处理,处理过程中会产生一定的环境污染物。
- 1、下载文档前请自行甄别文档内容的完整性,平台不提供额外的编辑、内容补充、找答案等附加服务。
- 2、"仅部分预览"的文档,不可在线预览部分如存在完整性等问题,可反馈申请退款(可完整预览的文档不适用该条件!)。
- 3、如文档侵犯您的权益,请联系客服反馈,我们会尽快为您处理(人工客服工作时间:9:00-18:30)。
7)成熟、先进、经济的烧结烟气综合治理技术<脱硫、脱硝、除二噁英、除尘等)。
<2)需积极探索、研发、加快烧结工程化的关键技术
1)新型低漏风率、长寿命、高质量和高效节能型大型烧结机、带式焙烧机、链箅机-回转窑氧化球团成套设备设计和制造技术;
2)新型烧结机偏析布料、双层布料铺料、液压调速梭式和摆头布料、改善料层透气性技术。
高炉炼铁是以精料为基础。精料水平对炼铁指标的影响率在70%,高炉操作占10%,企业管理占10%,设备运行状态占5%,外界因素占5%。当前,铁矿石品位下降是国内外大趋势,适度使用低品位矿;我们应在“稳”、“均”、“少”、“好”等方面下功夫。
炼铁系统的关键生产技术介绍:
1.烧结、球团工序
低质矿预处理、预混合和强力混合技术、烧结机厚料层、防漏风、余热回收利用和高效低成本烟气净化技术。烧结机大型化、现代化的集成技术。
3 高炉炼铁关键技术
<1) 加快推广的关键技术
1)针对不同容积的高炉,合理的高球团比、低块矿比及进一步提高入炉铁品位的低成本精料技术;
2)适应大喷煤量强富氧率、大喷煤量条件下的低焦比,高炉长寿、稳定顺行冶炼操作技术;
4)高流动性、高硫容量渣系的低硅生铁冶炼技术;
7)球团升温-焙烧-冷却的热工工艺(物料平衡、热平衡和风流图>数学模型和控制技术;
8)最低原、燃料消耗的途径的烧结球团过程“物质流”、“能量流”分析技术;
9)造球混合原料水分、粒径、球团生产过程工艺参数在线测定和自动调节;烧结、球团生产终点精确控制、模糊控制技术和智能化操作管理专家系统等先进的自动化技术;
目前,铁矿石的价值与价格发生严重扭曲,铁矿石价格高居不下和钢材价格下跌,使钢铁企业微利或亏损。这种态势将会维持较长时间。为此,企业要加快技术改造、产品升级、结构调整,进行精细化管理,用系统工程<技术、经济、管理向结合,统筹规划等),科学地、可持续地发展企业。
炼铁系统能耗、污染物排放、生产成本约占钢铁联合企业的70%。所以,炼铁系统要完成钢铁企业节能减排,降低生产成本的重任。高炉的能耗占钢铁企业总能耗的近50%。高炉炼铁所需能源78%是由碳素<焦炭和煤粉=燃料比)燃烧提供的,热风提供19%的能量,炉料化学反应热占3%。因此,降低燃料比是炼铁节能减排、降低生产成本的主攻方向。
10)赤铁矿、褐铁矿、菱铁矿球团、熔剂性球团、低膨胀和低还原粉化球团矿生产技术;
11)还原性烧结矿、复合烧结等新烧结法的生产技术。
2 炼焦关键技术
<1)加快推广的关键技术
1)6.25M大型捣固炼焦技术
2)7M大型顶装焦炉工艺和装备技术
3)采用高温高压锅炉的CDQ技术
4)煤调湿和型煤炼焦技术
5)焦炉煤气高附加值资源化利用技术
10)科学调剂炉况,优化布料,高煤气利用率<>50%),低燃料比技术。
<2)需积极探索、研发、加快高炉炼铁工程化的关键技术
1)≥1280℃的高风温热风炉技术;
2)≥0.28MPa高压炉顶设备和生产操作技术;
3)高炉煤气脱除CO2和循环利用技术;
4)≥1350℃的高风温,富氧10%-20%并加热、喷煤≥230kg/t、焦比≤260kg/t、生产率≥3.0t/m3.d的大型高炉低能耗高效生产技术;
5)大型高炉一代炉役≥22年<或单位容积产铁1.5万t)综合技术;
6)每5秒钟更新一次、类似多层CT的高炉炉缸耐材侵蚀及炉内温度和压力分布曲线实时在线监视技术;
7)喷吹焦炉煤气量≥100m3/吨铁,煤比≥120kg/吨铁的低炭冶炼技术;
8)高炉煤气深度净化系统技术<≥4000Nm3/h,硫、砷和氯等杂质含量≤1ppm,金属氧化物粉尘含量≤5mg/Nm3);
3)厚料层烧结(>800mm>和高球层焙烧技术;低能耗点火、低水、低碳、低风量的烧结工艺技术;
4)减少烟气排放量的热废气返回循环利用烧结新工艺技术,烧结废气脱硫脱硝(NOx、二恶英>、余热发电一体化的烧结技术;
5)先进的烧结矿整粒、分级技术;
6)可大幅度降低烧结燃耗、提高烧结矿的产质量的新型添加剂、催化助燃剂技术;
5)≥5000m3特大型高炉高效、低耗、长寿、稳定生产的操作工艺技术;
6)高炉寿命≥18年的冷却器、耐火材料的使用、维护及快速修复综合技术;
7)高炉操作智能专家系统软件平台及相关信息的在线监测预报技术;
8)高炉煤气干式除尘、余热回收、发电量≥40kWh/t铁的TRT压差发电技术;
9)大型高炉的炉型<炉腹角、高径比、薄炉衬、深炉缸等方面合理性)合理优化技术。
<1)加快推广的关键技术
1)原料综合技术经济评价技术(采购、物流、贮运和钢铁冶炼最终效益>和管理技术;
2)原、燃、辅料的高效加工(破碎、细磨、干燥、再细磨>技术;
3)高精度及微量精确自动称量配料设备及技术;
4)高效强力混合、高效强化造球和大型圆盘造球机高效強化造球、生球筛分、破碎技术;
5)高配比褐铁矿、高铁、低硅烧结技术;
9)高炉煤气资源化利用制甲醇技术<规模≥1000t/a,总碳单程转化率≥25%,综合转化率≥50%,正常运行≥2000h);
10)焦炭、烧结矿、球团矿炉料及炉渣显热高效回收利用及≤400℃中低温烟气、低压蒸汽的低能余热回收利用的装备技术;
6)废气循环与多段加热相结合、降低NOx排放的焦炉加热组合燃烧技术。
<2)积极探索、研发、加快焦炉工程化的关键技术
1)低NOX排放的焦炉加热燃烧技术
2)特大型现代化焦炉<炭化室高8m)的设计和装备制造技术
3)焦炉荒煤气上升管余热回收技术
4)多用弱粘结煤生产高强度焦炭技术
5)配加废塑料炼焦技术
6)关注和及时调研日本SCOPE21、美国CASP等国际新型炼焦技术
高炉炼铁工艺关键技术介绍
王维兴<中国金属学会北京100711)
136****2795***************
钢铁工业是国民经济的基础产业,也是能源消耗的大户,约占我国总能耗的16.3%,占全国GDP的3.2%。随着我国工业化进程的快速发展,钢铁需求量还要增长,随之带来能耗的急剧增加,污染物排放加剧,产业发展与资源环境的矛盾日趋尖锐。因此,推进钢铁行业节能减排,对加快钢铁工业结构调整,切实转变钢铁工业发展方式,促进节约、清洁和可持续发展具有重要意义。